Le système de transfert de presses à presses est une technologie utilisée dans l’industrie de la fabrication pour transférer automatiquement des pièces d’une presse à une autre au cours du processus de production. Ce système est crucial pour les lignes de production qui nécessitent plusieurs étapes de formage, de découpage ou d’emboutissage, chaque étape étant réalisée par une presse différente.
Système de transfert de presses à presses
Le système de transfert est une technologie utilisée dans de nombreux secteurs industriels pour déplacer des matériaux, des pièces ou des produits d’un point à un autre au sein d’un processus de fabrication ou d’assemblage. Ces systèmes sont essentiels pour automatiser et rationaliser les opérations, augmentant ainsi l’efficacité et réduisant les coûts. Voici une vue d’ensemble des principaux types de systèmes de transfert, leurs composants, et leurs applications :
Types de Systèmes de Transfert
- Systèmes de Transfert Linéaires :
- Convoyeurs : Utilisés pour transporter des matériaux ou des pièces sur des distances linéaires. Les convoyeurs peuvent être à bande, à rouleaux, à chaîne, ou à vis, selon le type de matériaux à transporter.
- Chariots Automatisés : Des véhicules guidés automatisés (AGV) qui se déplacent sur des trajectoires prédéfinies pour transporter des charges.
- Systèmes de Transfert Rotatifs :
- Tables Rotatives : Utilisées pour déplacer des pièces d’une station de travail à une autre dans un mouvement circulaire. Elles sont souvent utilisées dans les processus d’assemblage.
- Systèmes de Transfert Robotisés :
- Bras Robotisés : Utilisés pour manipuler des pièces dans des mouvements tridimensionnels complexes. Ils sont particulièrement utiles pour les tâches nécessitant une grande précision et flexibilité.
- Robots de Transfert à Portique : Des systèmes de robots qui se déplacent sur des rails pour transférer des pièces lourdes ou volumineuses entre différentes zones de travail.
Composants Clés
- Mécaniques :
- Supports et Cadres : Structures qui supportent le poids des pièces et des équipements de transfert.
- Mécanismes de Préhension : Pinces, ventouses, ou aimants utilisés pour saisir et relâcher les pièces.
- Électriques et Électroniques :
- Moteurs et Actionneurs : Fournissent la puissance nécessaire pour le mouvement.
- Capteurs : Utilisés pour détecter la position, la présence, et l’orientation des pièces.
- Contrôle et Automatisation :
- PLC (Contrôleurs Logiques Programmables) : Gèrent les séquences de mouvement et assurent la coordination avec les autres équipements de la ligne de production.
- Systèmes de Vision : Utilisés pour inspecter les pièces et guider les robots dans leurs mouvements.
Applications
- Industrie Automobile :
- Transfert de pièces entre différentes étapes de fabrication et d’assemblage.
- Transfert de moteurs, de châssis, et de composants volumineux.
- Industrie Alimentaire :
- Transport de produits alimentaires entre les différentes étapes de traitement, de cuisson et de conditionnement.
- Transfert de produits fragiles nécessitant une manipulation délicate.
- Électronique et Assemblage de Précision :
- Manipulation de composants électroniques sensibles.
- Assemblage de produits nécessitant une grande précision.
- Industrie Pharmaceutique :
- Transport de médicaments et de produits chimiques entre les différentes étapes de production.
- Manipulation de produits stériles en environnements contrôlés.
Avantages
- Augmentation de l’Efficacité :
- Réduction des temps de cycle et augmentation de la cadence de production.
- Amélioration de la précision et de la répétabilité des opérations.
- Réduction des Coûts :
- Réduction des coûts de main-d’œuvre grâce à l’automatisation.
- Réduction des erreurs et des déchets.
- Flexibilité :
- Possibilité de reconfigurer les systèmes pour s’adapter à différents produits et processus.
Défis
- Coût Initial :
- Investissement initial élevé pour l’installation et la mise en place des systèmes automatisés.
- Maintenance :
- Besoin de maintenance régulière pour assurer la fiabilité et la longévité des systèmes.
- Complexité technique nécessitant du personnel qualifié pour l’entretien et les réparations.
Conclusion
Les systèmes de transfert jouent un rôle crucial dans la modernisation des processus industriels, permettant d’atteindre des niveaux élevés d’efficacité, de précision et de flexibilité. En automatisant le déplacement des pièces et des produits, ils réduisent les coûts et améliorent la qualité, tout en répondant aux exigences croissantes des marchés modernes.
Composants et Fonctionnement
- Unités de Transfert :
- Robots de Transfert : Ces robots sont souvent utilisés pour déplacer les pièces entre les presses. Ils peuvent être des robots à axes multiples capables de manipuler des pièces complexes et lourdes.
- Convoyeurs : Utilisés pour le déplacement de pièces sur des trajets linéaires entre les presses. Ils sont adaptés aux pièces moins complexes et de poids modéré.
- Systèmes de Préhenstion :
- Pinces : Utilisées pour saisir et relâcher les pièces. Les pinces doivent être adaptées à la forme et à la taille des pièces pour assurer une manipulation précise.
- Ventouses : Utilisées pour les pièces plus légères ou fragiles où une pression uniforme est nécessaire pour éviter d’endommager les pièces.
- Systèmes de Contrôle :
- Contrôleurs Programmables (PLC) : Ils gèrent et synchronisent les mouvements des unités de transfert et les presses.
- Capteurs : Utilisés pour détecter la position des pièces, la présence ou l’absence des pièces, et assurer la sécurité et la précision du transfert.
- Sécurité :
- Barrières de Sécurité : Elles empêchent l’accès humain aux zones dangereuses pendant le fonctionnement du système.
- Systèmes de Surveillance : Assurent le bon fonctionnement et détectent les anomalies pour prévenir les accidents.
Avantages du Système de Transfert de Presses à Presses
- Efficacité Accrue :
- Réduction des Temps de Cycle : En automatisant le transfert, le temps entre chaque opération est réduit, augmentant ainsi la cadence de production.
- Augmentation de la Précision : Les erreurs humaines sont minimisées, assurant une meilleure qualité des pièces produites.
- Flexibilité :
- Adaptabilité : Les systèmes de transfert peuvent être reprogrammés et ajustés pour différentes tailles et formes de pièces, ainsi que pour différents processus de production.
- Sécurité :
- Réduction des Risques : L’automatisation réduit les risques de blessures pour les opérateurs en les éloignant des zones dangereuses.
Défis et Considérations
- Investissement Initial :
- Le coût d’installation et de mise en place d’un système de transfert automatisé peut être élevé, mais il est généralement amorti par les gains en efficacité et en réduction des coûts de main-d’œuvre.
- Maintenance et Fiabilité :
- Un entretien régulier est nécessaire pour assurer le bon fonctionnement des robots et des systèmes de transfert.
- Les systèmes doivent être robustes et capables de fonctionner en continu dans des environnements industriels exigeants.
En résumé, un système de transfert de presses à presses est une solution technologique avancée qui améliore l’efficacité, la précision et la sécurité des lignes de production industrielles, bien qu’il nécessite un investissement initial significatif et une maintenance continue.
Les technologies industrielles de transformation des matériaux sont au cœur de l’évolution des secteurs manufacturiers modernes. Parmi ces technologies, les machines de formage et les presses occupent une place centrale dans les processus de fabrication et de production en masse. Ces machines permettent la transformation de matières premières en produits finis ou semi-finis, utilisés dans divers secteurs comme l’automobile, l’aérospatial, l’électroménager, et bien plus encore.
Les avancées technologiques dans ces équipements ont considérablement amélioré la précision, la rapidité et l’efficacité des procédés de production, répondant aux besoins croissants de l’industrie pour des produits de qualité supérieure, à des coûts compétitifs. Que ce soit pour des applications de formage, de découpe, de pliage ou d’emboutissage, ces machines constituent un maillon essentiel dans la chaîne de production industrielle. Dans ce contexte, ce guide vous présente en détail diverses catégories de machines et presses utilisées dans l’industrie métallurgique et manufacturière. Chaque section abordera un type spécifique de machine, ses caractéristiques, ses avantages et ses principales applications.
Le contenu suivant couvre des équipements allant des machines de formage aux presses hydrauliques, en passant par les machines de polissage et d’ébavurage, offrant ainsi une vue d’ensemble complète des technologies disponibles pour la transformation des métaux.
Machine de Formage
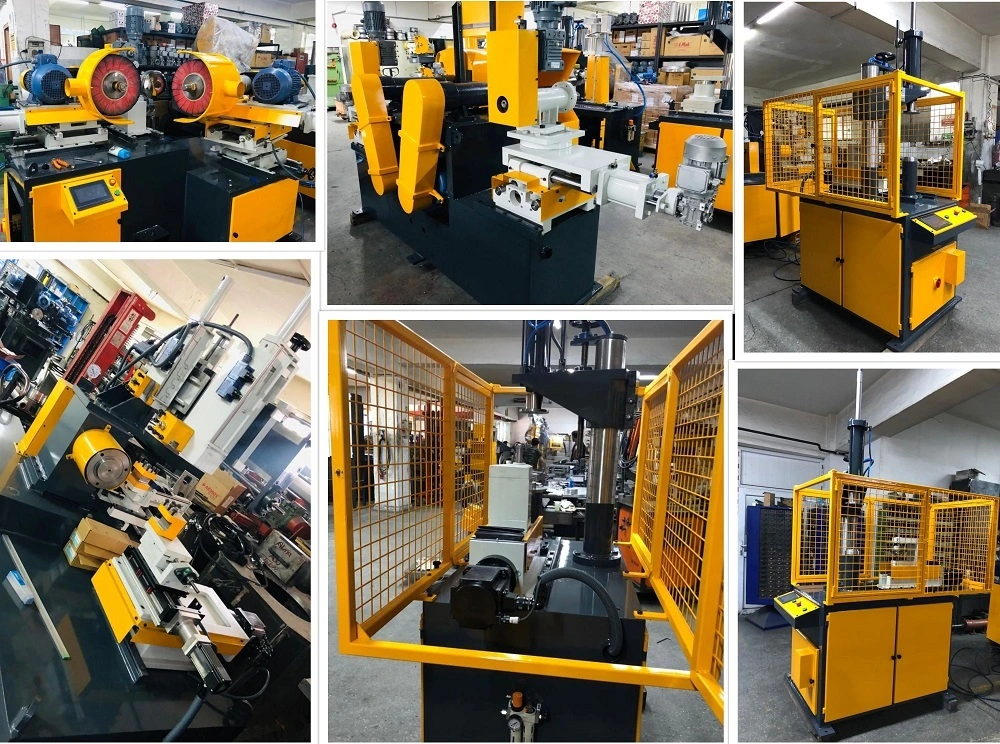
Les machines de formage jouent un rôle clé dans la transformation des métaux et d’autres matériaux à travers des procédés mécaniques, thermiques ou hydrauliques. Leur objectif principal est de façonner une pièce en lui donnant une forme prédéfinie, souvent sans enlever de matière, ce qui les distingue des procédés d’usinage ou de découpe.
Fonctionnement des Machines de Formage
Le principe de base d’une machine de formage repose sur l’application d’une force mécanique ou hydraulique pour déformer un matériau, généralement un métal, jusqu’à obtenir la forme désirée. Ce processus peut se dérouler à chaud ou à froid, selon la nature du matériau et le type de formage souhaité. Les machines de formage comprennent diverses catégories d’équipements, chacune adaptée à un type spécifique de transformation, comme le pliage, l’étirage, le cintrage ou le laminage.
Parmi les technologies de formage les plus utilisées, on trouve :
- Le formage à froid : utilisé principalement pour les métaux fins et ductiles, cette technique permet de déformer le matériau à température ambiante sans le chauffer, conservant ainsi ses propriétés mécaniques.
- Le formage à chaud : dans ce cas, le matériau est chauffé au-dessus de sa température de recristallisation, ce qui permet de faciliter sa déformation tout en limitant les contraintes internes.
Types de Machines de Formage
Il existe plusieurs types de machines de formage, en fonction de l’application spécifique :
- Machines de formage par étirage : ces machines sont souvent utilisées pour la production de grandes pièces, comme les panneaux de carrosserie dans l’industrie automobile.
- Machines de formage par pliage : adaptées au pliage de tôles métalliques, ces machines permettent de réaliser des angles précis sur des matériaux rigides.
- Machines de formage par laminage : elles servent principalement à réduire l’épaisseur d’un matériau, tout en augmentant sa longueur, très utilisées dans la production de feuilles de métal.
Avantages des Machines de Formage
Les machines de formage offrent plusieurs avantages dans le processus de fabrication industrielle :
- Efficacité : Elles permettent de transformer rapidement des matières premières en pièces finies ou semi-finies, réduisant ainsi les délais de production.
- Précision : Grâce aux innovations technologiques, ces machines peuvent produire des pièces aux tolérances très précises, même dans des matériaux difficiles à travailler.
- Réduction des pertes de matière : Contrairement à d’autres procédés comme l’usinage, le formage ne produit que très peu de déchets, ce qui en fait un processus plus économique et respectueux de l’environnement.
Applications Industrielles
Les machines de formage sont largement utilisées dans divers secteurs industriels :
- Automobile : pour la fabrication de châssis, de pièces de carrosserie, et autres composants critiques.
- Aéronautique : des pièces complexes et légères, telles que les structures d’aile et les panneaux de fuselage, sont souvent formées à l’aide de ces machines.
- Construction : dans la production de poutres, de barres et d’autres composants structurels utilisés dans les bâtiments et les infrastructures.
Presse à Emboutir

La presse à emboutir est une machine utilisée dans l’industrie pour transformer une feuille de métal en une forme tridimensionnelle complexe, grâce à un processus de déformation appelé emboutissage. Ce procédé est couramment utilisé dans la fabrication de pièces métalliques pour des industries telles que l’automobile, l’aéronautique, et l’électroménager.
Fonctionnement de la Presse à Emboutir
L’emboutissage est un processus de formage à froid, où une feuille métallique, appelée flan, est pressée entre une matrice et un poinçon. Le poinçon descend, déformant la feuille en lui donnant la forme souhaitée, généralement en une seule étape ou à travers une série de coups successifs pour des pièces plus complexes. Ce procédé permet de produire des formes précises et détaillées, souvent avec des géométries qui seraient difficiles, voire impossibles, à obtenir avec d’autres méthodes de fabrication.
Les presses à emboutir peuvent être actionnées mécaniquement, hydrauliquement ou via une combinaison des deux. Les presses hydrauliques sont couramment utilisées pour les opérations d’emboutissage profond, où de grandes forces sont nécessaires pour former des pièces aux formes complexes sans risque de déformation ou de fissuration du matériau.
Types de Presses à Emboutir
Il existe plusieurs types de presses à emboutir, chacune étant adaptée à des applications spécifiques :
- Presse mécanique : Utilisée pour des processus à grande vitesse, elle est plus adaptée à des opérations répétitives où la précision de chaque coup est essentielle.
- Presse hydraulique : Permet de mieux contrôler la pression et est plus adaptée pour les opérations nécessitant une grande force de formage, comme l’emboutissage profond.
- Presse servo-électrique : Combine la précision et le contrôle des presses hydrauliques avec la rapidité des presses mécaniques. Elle est idéale pour les opérations nécessitant à la fois rapidité et précision.
Avantages des Presses à Emboutir
Les presses à emboutir sont largement utilisées dans l’industrie pour plusieurs raisons :
- Productivité élevée : Ces machines permettent la production rapide de pièces complexes, souvent en une seule opération, ce qui augmente considérablement la cadence de fabrication.
- Flexibilité : Elles peuvent traiter une grande variété de matériaux, des métaux plus légers comme l’aluminium aux matériaux plus résistants comme l’acier inoxydable.
- Réduction des coûts : Grâce à leur efficacité et à leur capacité à produire des formes complexes en une seule opération, elles permettent de réduire les coûts de production par pièce, surtout dans les grandes séries.
- Précision et qualité : Les presses à emboutir modernes sont capables de produire des pièces avec des tolérances très serrées, minimisant ainsi les défauts et les rebuts.
Applications des Presses à Emboutir
L’emboutissage est un procédé essentiel dans diverses industries, notamment :
- Automobile : La fabrication des carrosseries de voitures, des portes, des capots, et d’autres pièces structurelles repose largement sur des presses à emboutir. La rapidité de production et la précision sont des atouts majeurs pour ce secteur.
- Aéronautique : Dans ce secteur, des pièces légères et complexes, telles que les carénages et les composants de structure d’aéronefs, sont souvent fabriquées par emboutissage pour assurer des tolérances strictes tout en minimisant le poids.
- Électroménager : Des composants tels que les coques extérieures des machines à laver, les tambours et les panneaux sont fréquemment produits par emboutissage, en raison de la précision et de la vitesse du processus.
Innovations Technologiques
Les presses à emboutir ont connu plusieurs évolutions ces dernières années, avec l’introduction de technologies avancées comme :
- L’emboutissage numérique : Des logiciels de simulation permettent désormais de prévoir et d’optimiser le processus d’emboutissage avant même de commencer la production, réduisant ainsi les erreurs et améliorant la qualité du produit fini.
- Presses à emboutissage automatique : Ces presses automatisées augmentent la cadence de production tout en minimisant les erreurs humaines, ce qui est crucial dans des industries où la précision est primordiale.
- Emboutissage à chaud : Cette technique consiste à chauffer la feuille de métal avant de l’emboutir, ce qui permet de créer des pièces encore plus complexes tout en limitant le risque de fissuration.
Machines à Filer les Métaux
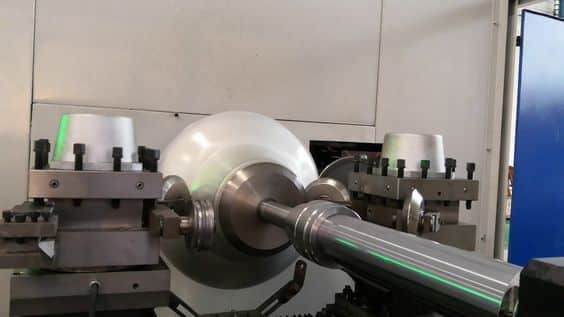
Les machines à filer les métaux sont des équipements industriels spécialisés dans la transformation de métaux à l’aide d’un procédé appelé le filage. Ce procédé consiste à déformer une pièce métallique en la faisant tourner rapidement tout en exerçant une pression contrôlée, permettant ainsi de créer des formes symétriques et précises. Le filage des métaux est utilisé principalement pour la production de pièces de forme cylindrique, conique ou de révolution.
Fonctionnement du Filage des Métaux
Le filage des métaux est un procédé de formage à froid ou à chaud, selon le type de matériau et les spécifications de la pièce à fabriquer. Le processus commence par la fixation d’un disque ou d’un tube de métal sur un mandrin rotatif. Ce mandrin sert de support pour former le métal en utilisant un outil de formage qui applique une pression pendant que le métal tourne à grande vitesse.
- Filage manuel : Bien que ce procédé soit souvent automatisé dans les grandes industries, il existe encore des opérations de filage manuel, où un opérateur guide l’outil de filage pour donner au métal la forme souhaitée. Ce type de filage est souvent réservé à des pièces complexes ou de petites séries.
- Filage automatique : Les machines à filer automatiques sont capables de produire des pièces à grande échelle avec une grande précision et constance. L’ensemble du processus est contrôlé par un système informatique qui régule la pression, la vitesse de rotation et la forme de l’outil.
Types de Filage
Il existe plusieurs types de procédés de filage selon le résultat souhaité :
- Filage conventionnel : Le procédé le plus courant, utilisé pour créer des formes simples comme des cônes ou des cylindres.
- Filage à compression : Ce procédé consiste à réduire l’épaisseur du métal tout en formant la pièce, ce qui est souvent utilisé pour les pièces nécessitant une résistance accrue.
- Filage assisté par ordinateur (CNC) : Utilisé pour des pièces complexes nécessitant une grande précision, ce procédé fait appel à des commandes numériques pour ajuster en temps réel la pression et la vitesse du processus.
Avantages du Filage des Métaux
Le filage des métaux présente plusieurs avantages distincts par rapport à d’autres procédés de formage :
- Production sans soudure : Le filage permet de créer des pièces creuses sans nécessiter de soudure, ce qui est essentiel pour la production de pièces de haute intégrité, notamment dans les secteurs de l’aéronautique ou de la chimie.
- Faible coût de production : En comparaison avec des procédés comme l’emboutissage profond, le filage nécessite des outillages relativement simples, ce qui réduit les coûts pour des productions de petites à moyennes séries.
- Haute précision : Les machines à filer modernes, surtout celles assistées par ordinateur, permettent d’obtenir des tolérances extrêmement serrées, indispensables dans des secteurs exigeants comme l’automobile ou la défense.
- Flexibilité : Le filage peut être utilisé pour une large gamme de matériaux, y compris l’aluminium, le cuivre, l’acier inoxydable, et même certains alliages exotiques utilisés dans l’aéronautique.
Applications des Machines à Filer
Les machines à filer les métaux trouvent des applications dans plusieurs industries :
- Aéronautique : Dans ce secteur, le filage est utilisé pour fabriquer des pièces légères et résistantes telles que des cônes de nez, des fuselages ou des réservoirs de carburant. La capacité du filage à produire des pièces sans soudure est un avantage majeur dans la fabrication d’équipements aéronautiques où la sécurité et la fiabilité sont primordiales.
- Automobile : Les composants tels que les roues, les jantes, les réservoirs et certains éléments de châssis sont souvent produits par filage en raison de la précision et de la solidité des pièces obtenues.
- Éclairage et mobilier : Le filage est également utilisé pour produire des luminaires, des abat-jours et des éléments décoratifs en métal, où la combinaison de formes complexes et de finitions lisses est très appréciée.
- Industrie chimique et pétrochimique : Des récipients sous pression et des réservoirs utilisés pour le stockage et le transport de produits chimiques dangereux sont souvent fabriqués par filage pour garantir une haute résistance et une étanchéité parfaite.
Innovations Récentes
L’évolution des machines à filer les métaux a suivi les avancées technologiques dans l’automatisation et la robotique :
- Machines CNC à filage : Ces machines à commande numérique permettent une précision accrue et la possibilité de fabriquer des pièces complexes en une seule opération, tout en optimisant les temps de cycle.
- Filage assisté par robot : Certaines machines sont équipées de bras robotiques capables de manipuler des pièces volumineuses ou complexes, ce qui augmente la flexibilité du procédé tout en réduisant les besoins en main-d’œuvre qualifiée.
- Matériaux avancés : Avec la montée en popularité des matériaux composites et des alliages exotiques, les machines à filer se sont adaptées pour être capables de traiter ces matériaux difficiles tout en conservant la précision et la qualité des pièces produites.
Presses de Formage des Métaux
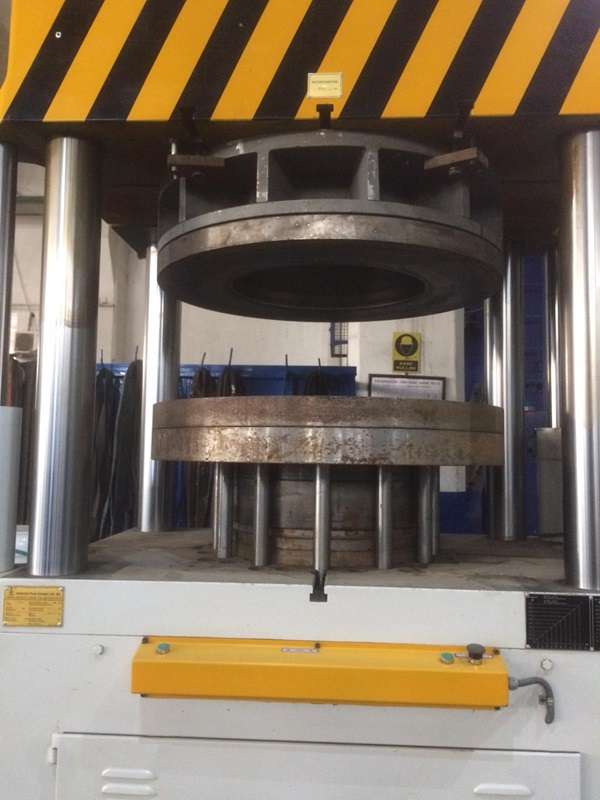
Les presses de formage des métaux sont des machines industrielles utilisées pour déformer des matériaux métalliques afin de leur donner une forme spécifique. Ce processus de formage peut impliquer des actions telles que le pliage, l’emboutissage, l’étirage ou la découpe. Les presses de formage jouent un rôle essentiel dans la production de pièces métalliques, que ce soit dans l’automobile, l’aéronautique, ou les secteurs de la construction et de l’électroménager.
Fonctionnement des Presses de Formage
Le fonctionnement d’une presse de formage repose sur l’application d’une grande force mécanique ou hydraulique pour déformer un morceau de métal. Le métal est placé sur une matrice ou un moule, puis une presse applique une pression contrôlée, soit en une seule fois, soit de manière progressive, afin de lui donner la forme désirée.
- Presses mécaniques : Ce type de presse utilise un moteur et des engrenages pour générer la force nécessaire au formage du métal. Les presses mécaniques sont souvent préférées pour les opérations rapides et répétitives.
- Presses hydrauliques : Elles fonctionnent à l’aide d’un fluide sous pression pour générer la force. Ce type de presse est souvent utilisé pour des opérations de formage nécessitant un contrôle précis de la pression, notamment dans les applications complexes comme l’emboutissage profond.
Les presses peuvent être classées selon leur mode d’action :
- Presses à simple action : Une seule pression est appliquée au matériau pour réaliser le formage. Cela convient à des pièces plus simples.
- Presses à double action : Ce type de presse comporte deux opérations simultanées, avec une première pression pour maintenir la pièce et une seconde pour la déformer. Elle est souvent utilisée pour des formes plus complexes.
- Presses progressives : Elles effectuent plusieurs étapes de formage en une seule séquence, avec chaque coup de la presse apportant une déformation supplémentaire. Ce processus est largement utilisé pour des pièces complexes nécessitant plusieurs opérations de formage.
Types de Presses de Formage
Il existe plusieurs types de presses de formage, chacune étant adaptée à des besoins industriels spécifiques :
- Presse à friction : Utilisée pour des opérations nécessitant un contrôle précis de la vitesse et de la force, comme le forgeage ou l’estampage.
- Presse de formage à chaud : Utilisée pour former des métaux chauffés à haute température, souvent pour des alliages qui sont difficiles à travailler à froid.
- Presse à col de cygne (C-frame) : Souvent utilisée dans des opérations plus légères, elle permet un accès facile à la zone de formage, ce qui est utile pour des pièces de petite taille.
- Presse à cadre en H (H-frame) : Plus robuste, elle est utilisée pour des opérations nécessitant une grande stabilité et une force de formage élevée.
Avantages des Presses de Formage des Métaux
Les presses de formage offrent des avantages significatifs dans les processus de fabrication industrielle :
- Précision : Grâce à la régularité de la force appliquée, les presses de formage peuvent produire des pièces avec des tolérances très serrées, ce qui est crucial dans des industries comme l’automobile ou l’électronique.
- Efficacité de production : Les presses modernes permettent un formage rapide et répétitif, assurant une productivité élevée tout en réduisant les coûts par pièce.
- Flexibilité : Ces machines peuvent traiter différents types de métaux, allant des aciers aux alliages légers comme l’aluminium, et peuvent être ajustées pour produire des pièces de formes variées.
- Adaptabilité : Que ce soit pour le formage à chaud ou à froid, les presses de formage sont capables de s’adapter aux différents besoins de production selon le type de matériau et la forme désirée.
Applications des Presses de Formage
Les presses de formage sont essentielles dans de nombreux secteurs industriels :
- Automobile : Les composants critiques comme les panneaux de carrosserie, les châssis, et d’autres pièces structurelles sont fréquemment fabriqués à l’aide de presses de formage. Leur capacité à produire des pièces légères mais solides est un atout majeur dans la réduction du poids des véhicules tout en assurant leur robustesse.
- Aéronautique : Dans ce secteur, la précision et la qualité des pièces sont primordiales. Les presses de formage sont utilisées pour créer des pièces légères et résistantes, indispensables à la sécurité et à l’efficacité des avions.
- Industrie électrique : Les boîtiers métalliques pour appareils électriques, ainsi que d’autres composants en métal, sont souvent fabriqués par le biais de presses de formage, grâce à leur capacité à produire des pièces avec une grande précision.
- Construction : Les poutres, supports et autres éléments structurels métalliques utilisés dans les bâtiments et les infrastructures sont souvent produits à l’aide de ces presses, permettant d’obtenir des pièces standardisées et robustes.
Innovations Technologiques dans les Presses de Formage
L’industrie des presses de formage a vu de nombreuses innovations au fil des ans, améliorant l’efficacité et la précision des machines :
- Contrôle numérique : Les presses modernes sont souvent équipées de systèmes CNC (Commande Numérique par Calculateur) qui permettent de programmer et d’ajuster avec précision les paramètres de formage, garantissant une production plus rapide et moins d’erreurs.
- Automatisation : Les presses automatisées permettent d’augmenter la productivité tout en réduisant les besoins en main-d’œuvre. Des robots peuvent être intégrés pour alimenter la presse et retirer les pièces finies, accélérant ainsi les temps de cycle.
- Technologie écoénergétique : Certaines presses sont maintenant conçues pour utiliser moins d’énergie, tout en offrant une puissance de formage équivalente, réduisant ainsi les coûts opérationnels et l’empreinte carbone des usines.
Presse de Découpe Rapide

La presse de découpe rapide est un équipement industriel spécialisé dans la découpe de matériaux, principalement métalliques, à grande vitesse et avec une extrême précision. Ce type de presse est essentiel dans les environnements de production où des volumes élevés de pièces découpées avec précision sont nécessaires, notamment dans les secteurs de l’automobile, de l’électronique, de l’emballage, et de l’aérospatiale.
Fonctionnement de la Presse de Découpe Rapide
Le processus de découpe rapide repose sur l’utilisation d’une presse pour exercer une force sur une matrice, dans laquelle le matériau est positionné. Sous cette pression, le matériau est découpé à la forme désirée en un temps extrêmement court. Contrairement aux processus de découpe traditionnels, qui peuvent être plus lents ou moins précis, la presse de découpe rapide permet de traiter de grandes quantités de matériaux tout en assurant une qualité constante.
- Presse mécanique : Ce type de presse utilise un mécanisme à volant pour générer la force de découpe. Elle est idéale pour des cadences de production très élevées, pouvant réaliser des milliers de découpes à l’heure.
- Presse hydraulique : Les presses hydrauliques, bien que généralement plus lentes, offrent un contrôle plus précis de la force et sont utilisées pour des découpes nécessitant une extrême précision, ou pour des matériaux plus difficiles à découper.
- Presse servo-électrique : Ce type de presse combine la rapidité des presses mécaniques et la précision des presses hydrauliques. Elle utilise un moteur servo-électrique pour générer la force nécessaire, offrant ainsi une grande flexibilité dans le contrôle des paramètres de découpe.
Types de Découpe
Les presses de découpe rapide peuvent réaliser différents types de découpe, en fonction de la forme finale souhaitée et du type de matériau utilisé :
- Découpe à blanc : Une opération qui consiste à séparer une pièce d’un matériau plus grand sans formation supplémentaire. Cela est couramment utilisé pour produire des composants plats ou des pièces prêtes pour un autre processus de formage.
- Découpe progressive : Le matériau passe à travers plusieurs étapes de découpe successives pour aboutir à une pièce finale plus complexe. Chaque étape enlève une partie spécifique du matériau.
- Découpe fine : Utilisée pour des tolérances très serrées, notamment dans des applications où une haute précision et une finition de bord lisse sont essentielles, comme dans l’industrie de l’électronique ou l’horlogerie.
Avantages de la Presse de Découpe Rapide
Les presses de découpe rapide offrent plusieurs avantages qui en font un choix privilégié dans l’industrie moderne :
- Vitesse de production : Grâce à leur capacité à effectuer des découpes rapidement et en continu, ces presses permettent de produire un grand nombre de pièces dans un laps de temps réduit, augmentant ainsi la productivité de l’usine.
- Précision : Ces presses sont capables de réaliser des découpes d’une précision exceptionnelle, même à grande vitesse, ce qui est crucial pour des pièces nécessitant des tolérances serrées.
- Réduction des coûts : En automatisant le processus de découpe et en augmentant la cadence de production, les presses de découpe rapide contribuent à réduire les coûts de production par pièce, particulièrement dans les productions en série.
- Flexibilité : Certaines presses de découpe rapide peuvent être configurées pour réaliser différents types de découpes sur un même matériau, offrant ainsi une grande flexibilité dans les lignes de production.
Applications des Presses de Découpe Rapide
Ces presses sont largement utilisées dans plusieurs secteurs industriels en raison de leur capacité à traiter des volumes élevés de matériaux avec précision :
- Automobile : La découpe des tôles utilisées pour les carrosseries, les châssis, et autres pièces structurelles est souvent réalisée avec des presses de découpe rapide pour répondre aux besoins de production de masse du secteur.
- Aéronautique : Dans ce secteur, la précision et la qualité des composants sont primordiales. Les presses de découpe rapide sont utilisées pour découper des pièces métalliques légères et complexes qui nécessitent des tolérances strictes.
- Électronique : Les composants en métal de petite taille, comme les connecteurs ou les circuits imprimés, sont souvent découpés à l’aide de presses rapides, car ces pièces nécessitent une précision extrême.
- Emballage : Le secteur de l’emballage utilise souvent des presses de découpe rapide pour produire des emballages en métal ou en plastique à haute vitesse, répondant ainsi aux besoins du marché de masse.
Innovations et Évolutions Technologiques
Les presses de découpe rapide bénéficient des avancées technologiques qui optimisent leurs performances :
- Systèmes CNC et automatisation : Les presses modernes sont souvent équipées de commandes numériques par calculateur (CNC) permettant une programmation précise de chaque opération de découpe. Cela permet un ajustement rapide et précis des paramètres de découpe pour différentes pièces, ce qui est essentiel dans des environnements de production variés.
- Presses intelligentes : Certaines machines sont dotées de capteurs et de systèmes de surveillance en temps réel qui peuvent ajuster les paramètres en fonction des conditions réelles du matériau ou de l’usure des outils, garantissant ainsi une qualité constante.
- Économies d’énergie : De plus en plus de presses sont conçues pour être plus efficaces sur le plan énergétique, réduisant ainsi les coûts d’exploitation et contribuant à une production plus durable.
Presses à Rogner
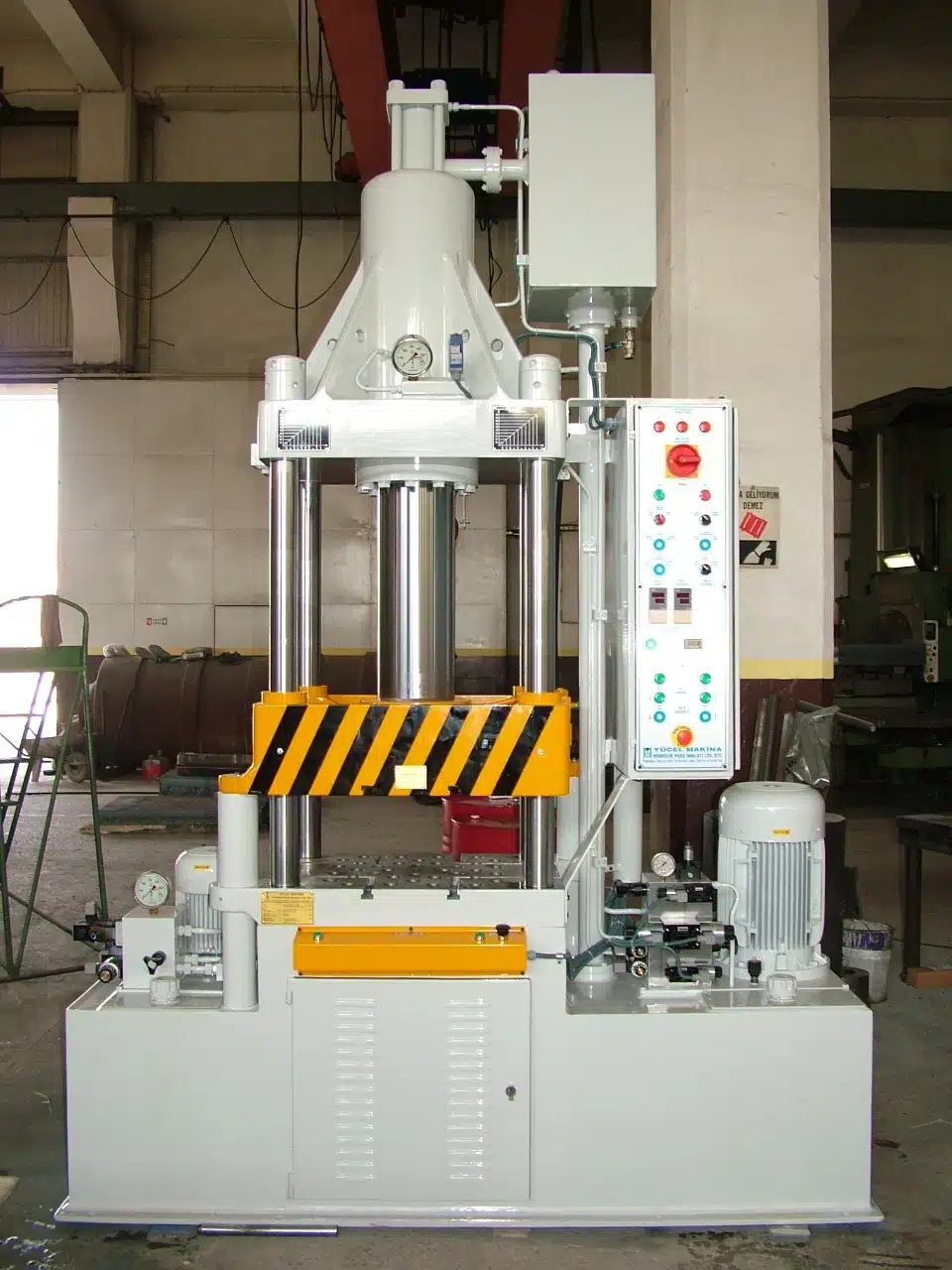
Les presses à rogner sont des machines industrielles utilisées pour enlever l’excédent de matière autour d’une pièce après un processus de formage, d’emboutissage ou de moulage. Ce procédé de rognage permet d’obtenir des pièces finales avec des contours précis et nets, en supprimant toute bavure ou excès de métal qui pourrait affecter la qualité et l’esthétique de la pièce.
Fonctionnement des Presses à Rogner
Le processus de rognage consiste à placer la pièce formée dans une matrice et à utiliser une presse pour couper ou retirer les parties excédentaires. Le rognage est souvent l’étape finale après des opérations de formage comme l’emboutissage ou le moulage, où le matériau est déformé pour créer une forme spécifique, mais laisse généralement des bords irréguliers ou du surplus de matière.
- Presses mécaniques : Ce type de presse est couramment utilisé pour des opérations de rognage à haute vitesse. Les presses mécaniques sont particulièrement adaptées à des séries de production où un grand nombre de pièces doivent être rognées en un minimum de temps.
- Presses hydrauliques : Les presses hydrauliques sont privilégiées dans les cas où une grande force de rognage est nécessaire ou lorsque des matériaux plus durs doivent être traités. Elles permettent également un meilleur contrôle de la pression, ce qui est utile pour des pièces plus complexes.
- Presses de rognage automatiques : Dans les environnements de production moderne, les presses à rogner automatiques intègrent des systèmes robotisés et des capteurs pour une opération continue sans intervention humaine, ce qui augmente la productivité tout en garantissant une qualité constante.
Types de Processus de Rognage
Il existe plusieurs types de rognage en fonction de la nature de la pièce et du type de matériau utilisé :
- Rognage mécanique : Ce type de rognage utilise une force mécanique pour découper les excédents de matériau. Il est couramment utilisé pour des pièces en métal formées par emboutissage ou forgeage.
- Rognage par cisaillement : Un procédé où la pièce est cisaillée pour enlever les excédents de matière, souvent utilisé pour des matériaux plus épais ou plus durs.
- Rognage manuel : Dans certains cas, des opérations manuelles sont nécessaires pour rogner des pièces particulièrement complexes ou lorsque la production n’est pas adaptée à une automatisation complète.
- Rognage par usinage : Des outils de coupe rotatifs sont utilisés pour enlever les bavures ou excès de métal, ce qui permet d’obtenir une finition plus lisse, particulièrement dans les pièces qui nécessitent une précision accrue.
Avantages des Presses à Rogner
Les presses à rogner sont essentielles dans les processus de fabrication industrielle pour plusieurs raisons :
- Finition de haute qualité : Le rognage permet d’obtenir des bords propres et lisses, essentiels dans les secteurs où l’esthétique et la précision sont primordiales, comme l’automobile et l’aéronautique.
- Productivité accrue : Les presses à rogner automatiques ou à grande vitesse permettent de traiter un grand nombre de pièces en peu de temps, augmentant ainsi le rendement de la production.
- Réduction des déchets : En enlevant uniquement l’excédent de matière nécessaire, le rognage réduit les déchets et maximise l’utilisation des matériaux, contribuant à une production plus rentable et durable.
- Flexibilité : Les presses à rogner peuvent être adaptées pour traiter divers types de matériaux, des métaux légers comme l’aluminium aux alliages plus durs, rendant ce procédé polyvalent dans de nombreux secteurs.
Applications des Presses à Rogner
Le rognage est une étape essentielle dans la fabrication de nombreuses pièces industrielles, et il est utilisé dans plusieurs secteurs :
- Automobile : Dans la fabrication de pièces de carrosserie, d’éléments de moteur ou de composants structurels, le rognage permet d’éliminer les bavures ou excédents de métal résultant des processus d’emboutissage ou de moulage, garantissant ainsi une finition parfaite.
- Aéronautique : Les pièces utilisées dans les avions doivent souvent répondre à des normes strictes en matière de précision et de sécurité. Le rognage est utilisé pour éliminer les irrégularités après le formage des pièces métalliques, notamment pour les ailes, les carénages et autres composants critiques.
- Électronique : Dans la fabrication de petits composants métalliques, comme les connecteurs ou les boîtiers, le rognage permet de garantir des tolérances serrées et des contours précis, indispensables pour l’assemblage de circuits électroniques.
- Électroménager : Les pièces métalliques utilisées dans les appareils électroménagers, comme les tambours de machines à laver ou les coques de réfrigérateurs, doivent souvent être rognées pour garantir une finition soignée et sécurisée.
Innovations dans le Rognage Industriel
Les avancées technologiques dans le domaine des presses à rogner ont conduit à des innovations majeures, améliorant à la fois l’efficacité et la précision du processus :
- Rognage automatisé : L’intégration de robots et de systèmes de capteurs dans les presses permet un rognage entièrement automatisé, augmentant ainsi la productivité tout en réduisant les risques d’erreur humaine.
- Systèmes CNC : Les commandes numériques permettent de programmer précisément chaque opération de rognage, garantissant une uniformité parfaite d’une pièce à l’autre, même à grande échelle.
- Machines multi-processus : Certaines machines combinent le rognage avec d’autres opérations, comme l’emboutissage ou l’ébavurage, permettant ainsi de réduire les temps de manipulation et d’optimiser les processus de production.
Presses de Formage à Froid

Les presses de formage à froid sont des machines industrielles utilisées pour déformer des métaux sans les chauffer, contrairement au formage à chaud. Ce processus consiste à appliquer une pression intense à température ambiante pour plier, étirer, emboutir ou découper le matériau, tout en préservant ses propriétés mécaniques. Le formage à froid est particulièrement apprécié dans les secteurs où la précision, la résistance et la durabilité des pièces sont essentielles.
Fonctionnement des Presses de Formage à Froid
Le principe du formage à froid repose sur l’application d’une force mécanique ou hydraulique sur une pièce métallique pour lui donner une forme spécifique. Contrairement au formage à chaud, où le métal est chauffé pour faciliter sa déformation, le formage à froid exige des machines plus puissantes pour surmonter la résistance naturelle du métal. Ce procédé est couramment utilisé pour des métaux ductiles, comme l’acier doux, l’aluminium et le cuivre, qui peuvent être déformés sans rupture même à température ambiante.
Les presses de formage à froid se distinguent en fonction de leur méthode d’application de la pression :
- Presses mécaniques : Utilisées pour des opérations de formage à grande vitesse, ces presses sont souvent privilégiées pour des productions en série, comme l’emboutissage rapide de pièces simples.
- Presses hydrauliques : Ces machines offrent un contrôle précis de la pression appliquée, permettant de former des pièces plus complexes et d’utiliser des matériaux plus résistants. Elles sont idéales pour des opérations nécessitant une force continue.
- Presses servo-électriques : Elles combinent la rapidité des presses mécaniques avec la précision des presses hydrauliques, tout en réduisant la consommation d’énergie et les bruits générés.
Types de Processus de Formage à Froid
Le formage à froid regroupe plusieurs techniques en fonction de la pièce et de la géométrie à obtenir :
- Emboutissage : Une pièce est déformée à froid pour lui donner une forme tridimensionnelle. L’emboutissage à froid est utilisé pour fabriquer des composants tels que les boîtiers, les réservoirs et les coques de véhicules.
- Pliage : La presse applique une force sur une feuille de métal pour la plier à un angle spécifique, généralement à l’aide d’une matrice de pliage. Ce procédé est utilisé pour fabriquer des pièces structurelles comme des poutres et des panneaux.
- Extrusion à froid : Une pièce est forcée à travers une matrice pour lui donner une forme allongée. Ce procédé permet de fabriquer des tubes, des barres ou des profils métalliques complexes avec des tolérances très serrées.
- Forgeage à froid : Une pression est appliquée sur une pièce métallique pour la comprimer et la façonner sans la chauffer. Ce procédé est souvent utilisé pour produire des pièces mécaniques résistantes comme des boulons et des engrenages.
Avantages du Formage à Froid
Le formage à froid présente plusieurs avantages par rapport au formage à chaud :
- Précision accrue : Comme le métal n’est pas chauffé, il conserve mieux ses dimensions d’origine, permettant d’obtenir des pièces avec des tolérances plus serrées et des formes plus précises.
- Meilleure résistance des pièces : Le formage à froid améliore les propriétés mécaniques du métal, en augmentant sa résistance et sa dureté par écrouissage, ce qui rend les pièces plus robustes et durables.
- Efficacité énergétique : Contrairement au formage à chaud, le formage à froid ne nécessite pas de chauffer le métal, ce qui réduit la consommation d’énergie et les coûts associés.
- Qualité de surface améliorée : Les pièces formées à froid ont généralement une surface plus lisse et ne nécessitent pas de finitions supplémentaires, ce qui permet de réduire les étapes de post-traitement.
Applications des Presses de Formage à Froid
Le formage à froid est utilisé dans divers secteurs industriels en raison de sa capacité à produire des pièces de haute précision et à grande échelle :
- Automobile : De nombreuses pièces automobiles, comme les composants de châssis, les supports et les pièces structurelles, sont fabriquées par formage à froid en raison de leur robustesse et de leur précision.
- Aéronautique : Dans l’industrie aéronautique, où la qualité et la sécurité sont primordiales, le formage à froid est utilisé pour fabriquer des pièces légères et résistantes, comme des supports, des ferrures et des pièces de fuselage.
- Électronique : Le formage à froid permet de produire des composants métalliques fins et précis, comme des connecteurs et des boîtiers, indispensables dans la fabrication de circuits électroniques.
- Industrie des outils et machines : De nombreux outils, boulons, écrous et pièces mécaniques sont fabriqués par formage à froid, car ce procédé permet de produire des pièces solides et résistantes aux contraintes mécaniques.
Innovations dans le Formage à Froid
Les presses de formage à froid ont connu des avancées technologiques significatives ces dernières années, améliorant leur efficacité et leurs performances :
- Commandes numériques (CNC) : L’intégration de systèmes CNC permet un contrôle précis de chaque étape du processus de formage, garantissant une uniformité parfaite des pièces produites, même à grande échelle.
- Automatisation : Les presses de formage à froid sont de plus en plus automatisées, avec des systèmes robotisés qui alimentent et retirent les pièces, augmentant ainsi la productivité tout en réduisant les besoins en main-d’œuvre.
- Matériaux avancés : Le formage à froid de nouveaux alliages et matériaux composites permet d’obtenir des pièces plus légères, plus résistantes et plus adaptées aux applications modernes, notamment dans les secteurs de la défense et de l’aéronautique.
- Presses hybrides : Combinant les avantages des presses mécaniques, hydrauliques et servo-électriques, ces machines permettent de s’adapter à une large gamme de matériaux et de processus, tout en optimisant l’efficacité énergétique.
Presse Hydraulique d’Emboutissage
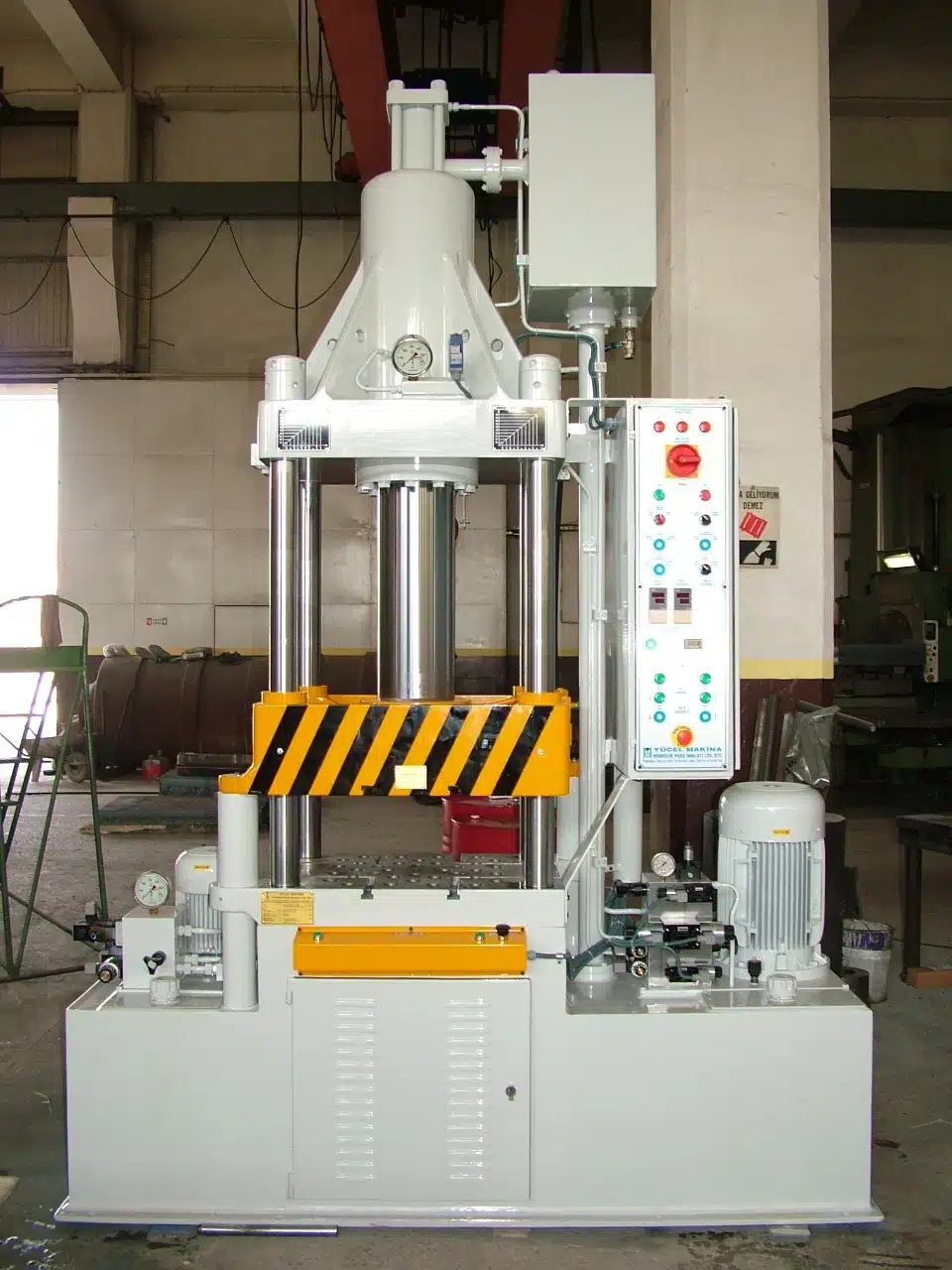
La presse hydraulique d’emboutissage est une machine industrielle puissante utilisée pour transformer des feuilles de métal en des formes tridimensionnelles complexes. L’emboutissage, processus de formage du métal par déformation, nécessite des forces importantes pour obtenir des pièces avec des géométries précises. Grâce à leur capacité à générer une force de pression continue et élevée, les presses hydrauliques sont idéales pour ce type d’opération.
Fonctionnement des Presses Hydrauliques d’Emboutissage
Les presses hydrauliques fonctionnent en utilisant un fluide sous pression pour générer une force capable de déformer des matériaux métalliques. Lors du processus d’emboutissage, une feuille métallique, appelée flan, est placée entre une matrice et un poinçon. La presse hydraulique applique ensuite une force uniforme sur le poinçon pour pousser la feuille à travers la matrice, créant ainsi une pièce avec des formes détaillées et complexes.
Contrairement aux presses mécaniques, qui génèrent une force maximale à un point donné, les presses hydrauliques peuvent appliquer une force constante tout au long du cycle de travail, ce qui est particulièrement important dans des processus comme l’emboutissage profond, où le matériau est fortement déformé.
Types de Presses Hydrauliques d’Emboutissage
Il existe plusieurs types de presses hydrauliques adaptées à l’emboutissage, chacune ayant des caractéristiques spécifiques selon les applications :
- Presse à action simple : Ce type de presse hydraulique est utilisé pour des opérations d’emboutissage de base, où une seule force est appliquée pour déformer le métal.
- Presse à double action : Ces presses sont équipées de deux vérins hydrauliques : l’un pour maintenir la feuille de métal en place pendant le processus, et l’autre pour appliquer la force de déformation. Elles sont couramment utilisées pour l’emboutissage profond.
- Presse à triple action : Ce type de presse est utilisé pour des processus de formage encore plus complexes, nécessitant un contrôle précis des forces appliquées sur différentes parties de la pièce.
Avantages des Presses Hydrauliques d’Emboutissage
Les presses hydrauliques sont largement utilisées dans l’industrie pour de nombreuses raisons :
- Capacité à générer des forces élevées : Les presses hydrauliques peuvent appliquer des forces très importantes, ce qui les rend idéales pour le formage de pièces épaisses ou de grandes dimensions.
- Précision et contrôle : Grâce à la régulation de la pression hydraulique, il est possible de contrôler précisément la force appliquée, ce qui garantit des tolérances plus serrées et des pièces de haute qualité.
- Adaptabilité : Les presses hydrauliques peuvent être ajustées pour diverses opérations, allant de l’emboutissage superficiel à l’emboutissage profond, permettant une grande flexibilité dans la production.
- Longueur de course ajustable : Les presses hydrauliques peuvent avoir une course plus longue, ce qui les rend particulièrement adaptées à des opérations nécessitant des déformations importantes, comme l’emboutissage profond.
Applications des Presses Hydrauliques d’Emboutissage
Les presses hydrauliques d’emboutissage sont utilisées dans une large gamme de secteurs industriels pour fabriquer des pièces complexes et volumineuses :
- Automobile : Dans l’industrie automobile, les presses hydrauliques sont utilisées pour fabriquer des composants structurels comme les capots, les portes, les panneaux latéraux, et d’autres pièces de carrosserie. Ces pièces nécessitent une grande précision et doivent être produites en masse.
- Aéronautique : Dans ce secteur, l’emboutissage profond est utilisé pour fabriquer des pièces légères et résistantes, comme les réservoirs de carburant, les carénages et les éléments de fuselage. L’utilisation de presses hydrauliques permet d’obtenir des pièces d’une qualité irréprochable, tout en respectant les normes de sécurité strictes de l’aéronautique.
- Électroménager : De nombreuses pièces métalliques utilisées dans les appareils électroménagers, comme les tambours de machines à laver, les coques extérieures et les composants de moteurs, sont fabriquées par emboutissage avec des presses hydrauliques.
- Industrie énergétique : Les presses hydrauliques d’emboutissage sont également utilisées pour produire des composants utilisés dans l’industrie énergétique, comme des enveloppes de batteries ou des pièces pour panneaux solaires.
Innovations et Évolutions Technologiques
Les presses hydrauliques d’emboutissage ont bénéficié de nombreuses innovations au fil des années, améliorant leurs performances et leurs capacités :
- Automatisation avancée : L’intégration de robots et de systèmes automatisés permet aux presses hydrauliques modernes de fonctionner de manière continue et sans interruption, augmentant ainsi la productivité tout en réduisant les coûts de production.
- Contrôles numériques : Grâce aux systèmes CNC, les presses hydrauliques peuvent être programmées avec une précision extrême, permettant un contrôle minutieux de chaque étape du processus d’emboutissage, garantissant ainsi la constance de la qualité des pièces produites.
- Économies d’énergie : Certaines presses hydrauliques sont conçues pour utiliser moins d’énergie tout en maintenant des niveaux de performance élevés. Cela contribue à la réduction des coûts d’exploitation et à une production plus respectueuse de l’environnement.
- Technologie de fluide à haute pression : Les nouvelles presses hydrauliques sont capables d’utiliser des fluides à haute pression, augmentant ainsi la force générée sans avoir besoin de moteurs plus puissants, ce qui améliore l’efficacité énergétique.
Presses Hydrauliques pour Formage
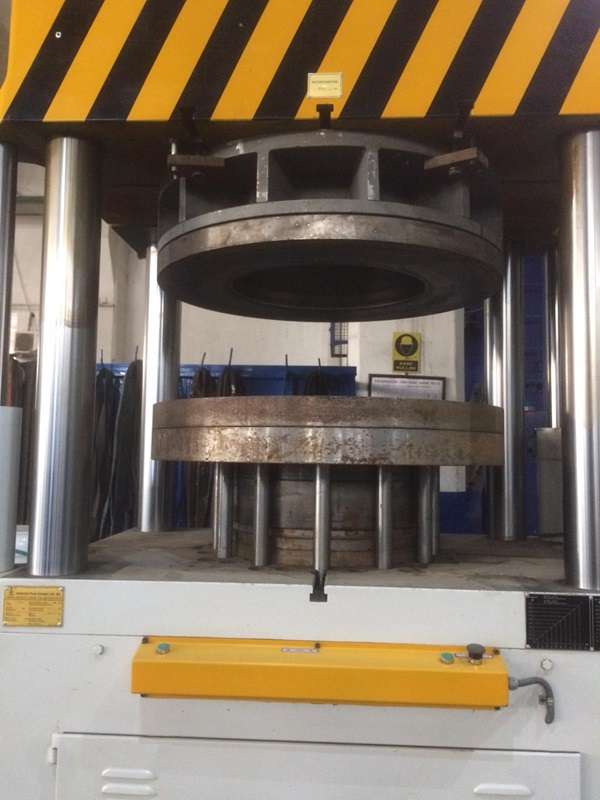
Les presses hydrauliques pour formage sont des machines industrielles polyvalentes, utilisées pour façonner des matériaux métalliques et non métalliques en appliquant une force élevée via un fluide hydraulique. Ces presses sont essentielles dans les processus de formage, car elles permettent de réaliser des opérations complexes avec une grande précision. Elles sont couramment employées dans divers secteurs industriels, comme l’automobile, l’aéronautique, la construction, et bien d’autres.
Fonctionnement des Presses Hydrauliques pour Formage
Les presses hydrauliques fonctionnent sur un principe simple mais puissant : un fluide, généralement de l’huile, est pressurisé à l’intérieur d’un cylindre pour générer une force de compression qui déforme le matériau placé entre la matrice et le poinçon. La force générée par la presse hydraulique est constante tout au long du cycle de travail, ce qui permet un formage progressif et uniforme.
Contrairement aux presses mécaniques, qui appliquent une force maximale à un moment précis du cycle, les presses hydrauliques offrent une pression contrôlée et ajustable, ce qui est essentiel pour des opérations de formage plus complexes. Elles peuvent également être utilisées pour plusieurs types de formage, comme le pliage, l’emboutissage, l’étirage, et l’extrusion.
Types de Presses Hydrauliques pour Formage
Il existe plusieurs types de presses hydrauliques, chacune étant adaptée à un type particulier de formage :
- Presses à cadre en H : Ces presses sont très robustes et offrent une grande stabilité lors des opérations de formage, ce qui les rend adaptées aux applications nécessitant des forces de pression élevées.
- Presses à 4 colonnes : Ces presses hydrauliques sont idéales pour les opérations nécessitant une répartition uniforme de la force sur la pièce. Elles sont souvent utilisées pour l’emboutissage et le formage de grandes pièces plates.
- Presses à double action : Elles sont équipées de deux vérins permettant de contrôler la pression de manière indépendante, ce qui est utile pour les opérations de formage à plusieurs étapes, telles que le formage profond ou l’étirage.
- Presses de transfert : Elles sont intégrées à des lignes de production automatisées pour déplacer la pièce d’une station à une autre, réalisant plusieurs étapes de formage en une seule séquence.
Avantages des Presses Hydrauliques pour Formage
Les presses hydrauliques offrent de nombreux avantages, notamment :
- Force ajustable : La pression générée par une presse hydraulique peut être ajustée avec précision en fonction des exigences du matériau et du processus de formage, permettant ainsi une flexibilité maximale.
- Capacité à travailler des matériaux variés : Ces presses peuvent être utilisées pour former une large gamme de matériaux, allant des métaux légers comme l’aluminium aux alliages plus durs, ainsi que des matériaux composites et plastiques.
- Formage de pièces complexes : Grâce à la répartition uniforme de la force, ces presses permettent de former des pièces aux géométries complexes, même avec des tolérances très strictes.
- Économie d’énergie : Certaines presses hydrauliques modernes sont conçues pour être plus écoénergétiques, réduisant la consommation tout en maintenant des performances élevées, ce qui en fait des solutions plus durables.
Applications des Presses Hydrauliques pour Formage
Les presses hydrauliques sont essentielles dans de nombreuses industries pour le formage de pièces métalliques et non métalliques :
- Automobile : Dans l’industrie automobile, ces presses sont utilisées pour la fabrication de nombreuses pièces, allant des panneaux de carrosserie aux composants structurels comme les montants, les longerons et les supports. Elles permettent de former des pièces légères mais solides, essentielles pour réduire le poids des véhicules tout en améliorant leur performance.
- Aéronautique : Le formage de pièces aéronautiques, comme les cadres de fuselage, les ailes et autres composants, nécessite une grande précision et une force importante. Les presses hydrauliques sont couramment utilisées pour former des alliages légers comme le titane ou l’aluminium.
- Construction : Les presses hydrauliques sont utilisées pour produire des poutres, des colonnes et d’autres éléments structurels dans la construction de bâtiments, d’infrastructures et de ponts. Elles permettent de former des pièces résistantes aux contraintes mécaniques tout en assurant leur durabilité.
- Électronique : Les composants métalliques des appareils électroniques, comme les boîtiers, les connecteurs et autres pièces de petite taille, sont souvent formés à l’aide de presses hydrauliques. Ces machines permettent d’obtenir des tolérances serrées et des finitions de haute qualité.
Innovations dans les Presses Hydrauliques pour Formage
Les presses hydrauliques ont évolué avec l’intégration de nouvelles technologies, rendant leur utilisation plus efficace et plus précise :
- Commandes numériques (CNC) : Les systèmes CNC permettent de contrôler chaque aspect du processus de formage, de la pression à la vitesse de compression, assurant ainsi une répétabilité et une précision exceptionnelles.
- Automatisation : L’intégration de robots et de systèmes automatisés dans les presses hydrauliques a révolutionné les lignes de production, augmentant la productivité tout en réduisant les coûts liés à la main-d’œuvre et aux erreurs humaines.
- Technologie à faible consommation d’énergie : Les presses hydrauliques modernes sont de plus en plus conçues pour réduire la consommation d’énergie. L’utilisation de systèmes hybrides, combinant hydraulique et électrique, permet d’améliorer l’efficacité énergétique sans compromettre la puissance de formage.
- Maintenance prédictive : Grâce à des capteurs intelligents, les presses hydrauliques peuvent maintenant surveiller en temps réel l’usure des composants, permettant une maintenance prédictive et ainsi minimiser les temps d’arrêt.
Presse à Transfert Hydraulique
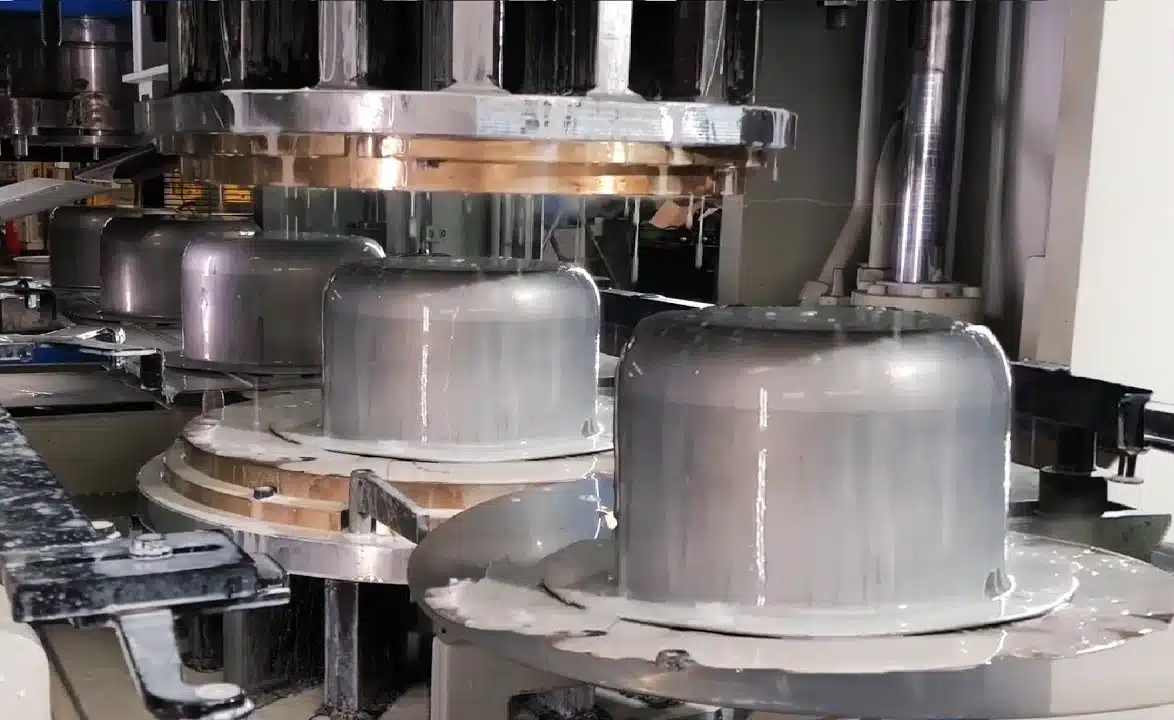
La presse à transfert hydraulique est une machine industrielle conçue pour réaliser des opérations de formage des métaux sur plusieurs étapes, en déplaçant automatiquement la pièce d’une station à une autre au sein de la presse. Ce type de presse est particulièrement adapté aux lignes de production automatisées où chaque pièce doit subir une série d’opérations de formage, telles que l’emboutissage, le pliage, la découpe ou l’étirage, dans un processus continu. Les presses à transfert hydraulique combinent la puissance des systèmes hydrauliques avec la flexibilité du transfert automatisé, offrant des avantages significatifs en termes de productivité, de précision et de réduction des coûts.
Fonctionnement de la Presse à Transfert Hydraulique
Une presse à transfert hydraulique est composée de plusieurs stations de travail où chaque étape du processus de formage est effectuée. La pièce brute est introduite dans la presse, puis elle est transférée automatiquement d’une station à l’autre grâce à un système de bras mécaniques ou de convoyeurs. Chaque station applique une force hydraulique pour accomplir une opération spécifique, comme le découpage ou l’emboutissage. L’intégration d’un système de transfert permet d’accélérer le processus, car chaque pièce est formée de manière continue et sans interruption.
- Transfert mécanique : Le transfert de la pièce se fait via des bras mécaniques qui saisissent la pièce et la déplacent d’une station à l’autre. Cela permet une synchronisation parfaite entre les différentes étapes de formage.
- Transfert par convoyeur : Dans certaines configurations, la pièce est transportée d’une station à une autre via un convoyeur intégré, permettant ainsi une automatisation complète de la chaîne de production.
Avantages de la Presse à Transfert Hydraulique
Les presses à transfert hydraulique offrent plusieurs avantages pour les processus de production industrielle :
- Productivité élevée : En automatisant le transfert des pièces entre les stations de formage, les presses à transfert hydraulique permettent de réaliser plusieurs opérations dans un seul cycle, ce qui réduit considérablement les temps de production.
- Précision et uniformité : La force hydraulique permet un contrôle précis de chaque opération de formage, garantissant des tolérances serrées et des pièces uniformes, même sur de grandes séries.
- Réduction des coûts de main-d’œuvre : L’automatisation du processus de transfert réduit la nécessité d’une intervention humaine, ce qui diminue les coûts de production tout en améliorant la sécurité des opérateurs.
- Flexibilité des opérations : Ces presses peuvent être configurées pour réaliser plusieurs types d’opérations de formage sur une même pièce, ce qui en fait des solutions polyvalentes pour des productions complexes nécessitant plusieurs étapes de transformation.
Types de Presses à Transfert Hydraulique
Il existe différents types de presses à transfert hydraulique, chacune étant adaptée à des processus industriels spécifiques :
- Presses à transfert à double action : Ces presses sont équipées de deux vérins hydrauliques qui permettent de réaliser deux opérations de formage simultanément sur une même pièce, ce qui réduit encore plus les temps de cycle.
- Presses de transfert modulaires : Ces presses permettent d’ajouter ou de retirer des stations de formage selon les besoins de production. Elles offrent une flexibilité accrue et peuvent être adaptées à des séries de production de tailles variées.
- Presses à transfert multi-étages : Utilisées pour des processus complexes, elles réalisent plusieurs opérations successives, comme l’emboutissage, le rognage et la découpe, en un seul passage à travers la presse.
Applications des Presses à Transfert Hydraulique
Les presses à transfert hydraulique sont utilisées dans divers secteurs industriels où la rapidité et la précision sont essentielles :
- Automobile : Dans l’industrie automobile, ces presses sont couramment utilisées pour produire des pièces de carrosserie, des panneaux, des cadres et d’autres composants structurels qui nécessitent plusieurs étapes de formage. La capacité des presses à transfert à réaliser plusieurs opérations en une seule séquence réduit les coûts de production et augmente la cadence.
- Aéronautique : Les presses à transfert hydraulique sont utilisées pour la fabrication de pièces aéronautiques légères et complexes, telles que les réservoirs de carburant, les éléments de fuselage et les supports de moteur. Ces presses permettent de former des pièces résistantes tout en respectant des tolérances très strictes.
- Électroménager : Les pièces métalliques utilisées dans les appareils électroménagers, comme les tambours de machines à laver, les coques et les composants de moteur, sont souvent produites avec des presses à transfert hydraulique, en raison de leur capacité à réaliser plusieurs opérations en continu.
- Électronique : Les petites pièces métalliques complexes utilisées dans les appareils électroniques, telles que les connecteurs, les boîtiers et les contacts, peuvent être produites en masse avec ces presses, assurant une haute précision et une productivité élevée.
Innovations Technologiques
Les presses à transfert hydraulique ont bénéficié de nombreuses avancées technologiques, augmentant leur efficacité et leur précision :
- Automatisation avancée : Les presses modernes sont souvent entièrement automatisées, avec des systèmes de transfert robotisés qui déplacent les pièces d’une station à l’autre de manière rapide et fluide. Cela permet de réduire les erreurs et d’augmenter la cadence de production.
- Systèmes de surveillance en temps réel : Des capteurs intelligents peuvent surveiller les paramètres critiques comme la pression hydraulique et la vitesse de transfert, assurant une régulation en temps réel pour éviter les erreurs et garantir la qualité des pièces produites.
- Contrôles numériques (CNC) : Les systèmes CNC permettent de programmer chaque étape du processus de formage, garantissant une répétabilité parfaite et une grande flexibilité dans les opérations de formage complexes. Cela facilite également le changement de série pour différents types de production.
- Maintenance prédictive : Les presses sont de plus en plus équipées de technologies de maintenance prédictive qui permettent de détecter les signes d’usure des composants avant qu’ils ne tombent en panne, réduisant ainsi les temps d’arrêt et augmentant la durée de vie des machines.
Presse Plieuse Hydraulique Horizontale
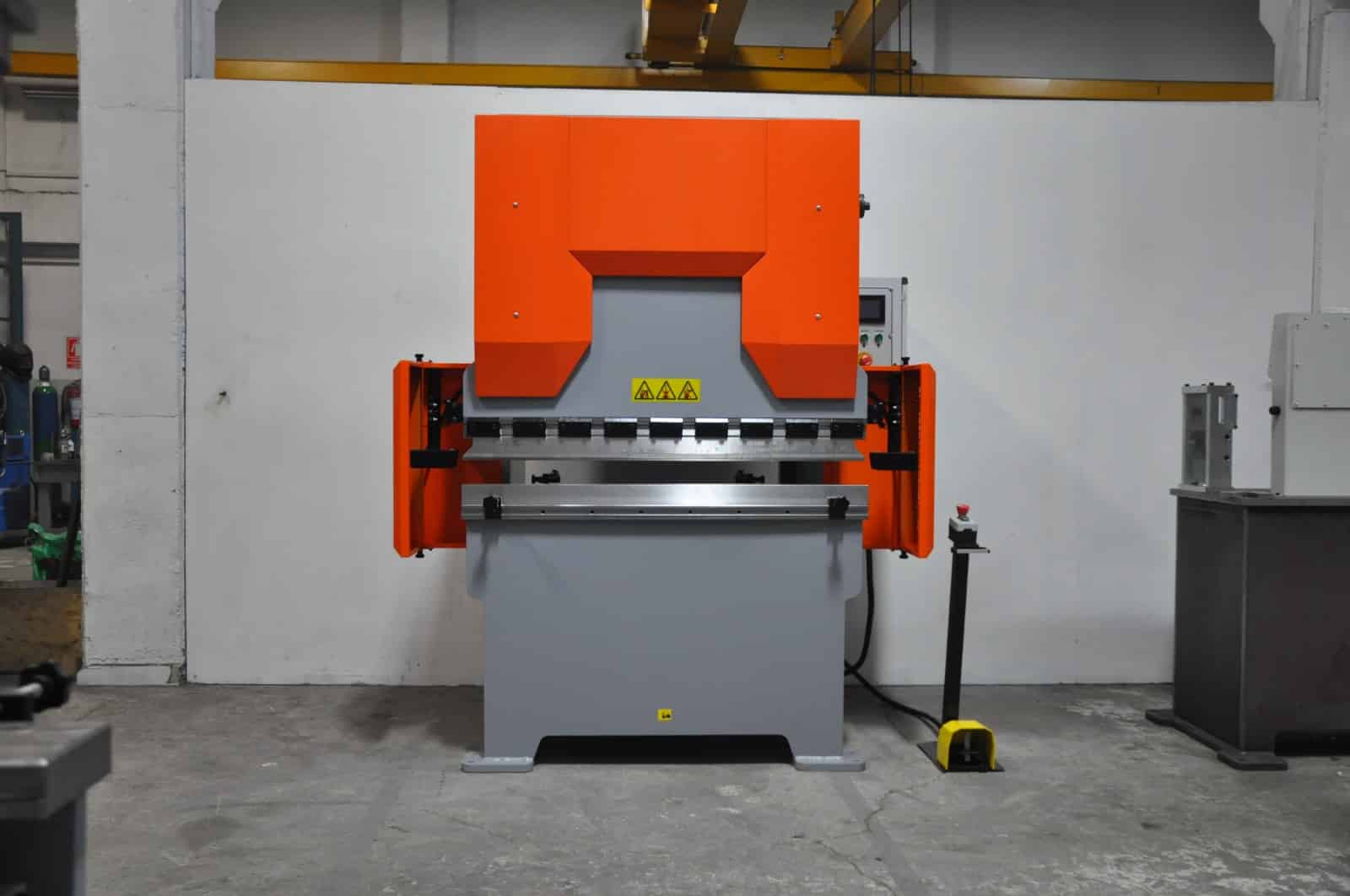
La presse plieuse hydraulique horizontale est une machine industrielle conçue spécifiquement pour plier des pièces métalliques de manière précise et répétitive. Contrairement aux presses plieuses verticales, les modèles horizontaux permettent une plus grande flexibilité dans les types de pliage et offrent des avantages particuliers dans certaines applications où un pliage horizontal est requis. Ces presses sont largement utilisées dans les secteurs de la métallurgie, de la construction, et de la fabrication d’équipements industriels.
Fonctionnement de la Presse Plieuse Hydraulique Horizontale
La presse plieuse hydraulique horizontale fonctionne en appliquant une pression hydraulique sur une pièce métallique placée entre une matrice et un poinçon. Le mouvement de la presse est horizontal, ce qui diffère des presses plieuses verticales qui déplacent le poinçon de haut en bas. La force appliquée par le système hydraulique permet de plier la pièce à l’angle souhaité avec une grande précision.
La presse hydraulique horizontale se distingue par sa capacité à effectuer des opérations de pliage dans des positions spécifiques où l’accès est limité pour les presses verticales. De plus, certaines configurations permettent de réaliser des opérations supplémentaires telles que la coupe, l’évasement et le formage, offrant une polyvalence accrue.
Types de Presses Plieuses Hydrauliques Horizontales
Il existe plusieurs types de presses plieuses hydrauliques horizontales adaptées aux besoins spécifiques des industries :
- Presses plieuses à usage général : Ces presses sont utilisées pour des opérations de pliage standard, comme le formage de barres, de tôles et de profilés. Elles sont souvent configurées pour réaliser des angles de pliage précis sur des matériaux variés, tels que l’acier ou l’aluminium.
- Presses plieuses multi-usage : Ces machines sont conçues pour exécuter plusieurs types d’opérations, telles que le pliage, la découpe et le cintrage. Elles sont idéales pour des ateliers où la flexibilité est essentielle, car elles permettent de réduire les temps de changement d’outillage et d’améliorer l’efficacité globale de production.
- Presses plieuses de haute précision : Utilisées dans des industries exigeant des tolérances serrées, ces presses sont souvent équipées de systèmes de commande numérique (CNC) pour garantir une précision extrême et une répétabilité parfaite dans chaque cycle de pliage.
Avantages des Presses Plieuses Hydrauliques Horizontales
Les presses plieuses hydrauliques horizontales offrent de nombreux avantages pour le pliage des métaux :
- Flexibilité des opérations : Grâce à leur conception horizontale, ces presses peuvent être utilisées dans des espaces restreints où le pliage vertical n’est pas pratique. Elles sont également capables de réaliser des formes complexes avec une grande précision.
- Puissance et précision : Les systèmes hydrauliques permettent d’appliquer une pression constante et contrôlée, garantissant une qualité de pliage supérieure, même pour des matériaux épais ou résistants.
- Polyvalence : En plus du pliage, certaines presses plieuses hydrauliques horizontales sont équipées pour effectuer des opérations comme le formage, la découpe, et même l’assemblage de pièces, ce qui les rend particulièrement utiles dans les environnements de production variée.
- Sécurité : Les presses horizontales sont souvent perçues comme plus sûres que les presses verticales pour certaines opérations, car elles permettent un meilleur contrôle visuel de la pièce tout au long du processus.
Applications des Presses Plieuses Hydrauliques Horizontales
Les presses plieuses hydrauliques horizontales sont largement utilisées dans de nombreux secteurs industriels :
- Construction métallique : Ces presses sont utilisées pour former des poutres, des barres d’armature et d’autres composants structurels dans la construction de bâtiments, de ponts et d’infrastructures. Elles permettent de plier des pièces volumineuses à des angles précis sans compromettre leur intégrité structurelle.
- Fabrication de machines : Dans les ateliers de fabrication, ces presses sont utilisées pour plier et former des pièces destinées aux équipements industriels, notamment dans la construction de machines-outils et de structures mécaniques.
- Industrie automobile : Les presses plieuses hydrauliques horizontales sont utilisées pour former des composants automobiles comme les supports, les barres de renfort, et autres pièces structurelles. Leur capacité à plier des matériaux résistants avec une grande précision est essentielle pour garantir la qualité des pièces produites.
- Mobilier métallique : Dans la fabrication de meubles et d’éléments de mobilier en métal, les presses plieuses hydrauliques horizontales permettent de créer des pièces aux formes complexes, comme des cadres, des structures de sièges et des pieds de tables.
Innovations Technologiques
Les presses plieuses hydrauliques horizontales ont évolué grâce à l’intégration de technologies modernes, améliorant à la fois leur efficacité et leur polyvalence :
- Commandes numériques (CNC) : Les presses équipées de systèmes CNC permettent de programmer avec précision chaque opération de pliage, garantissant des résultats constants et une répétabilité parfaite sur des séries de production importantes. Cela facilite également les changements rapides entre différentes opérations.
- Systèmes de sécurité avancés : Les presses modernes intègrent des dispositifs de sécurité tels que des barrières lumineuses et des capteurs pour protéger les opérateurs et réduire les risques d’accidents en cas de manipulation incorrecte.
- Efficacité énergétique : De plus en plus de presses plieuses hydrauliques horizontales sont conçues pour utiliser moins d’énergie tout en offrant des performances optimales. L’utilisation de systèmes hydrauliques à faible consommation et d’électronique intelligente permet de réduire les coûts d’exploitation.
- Automatisation : Les presses plieuses hydrauliques horizontales peuvent être intégrées à des lignes de production automatisées, avec des robots manipulant les pièces avant et après le pliage. Cela améliore non seulement la cadence de production, mais réduit également les erreurs humaines et les temps d’arrêt.
Presse en Ligne pour Moulage Composite
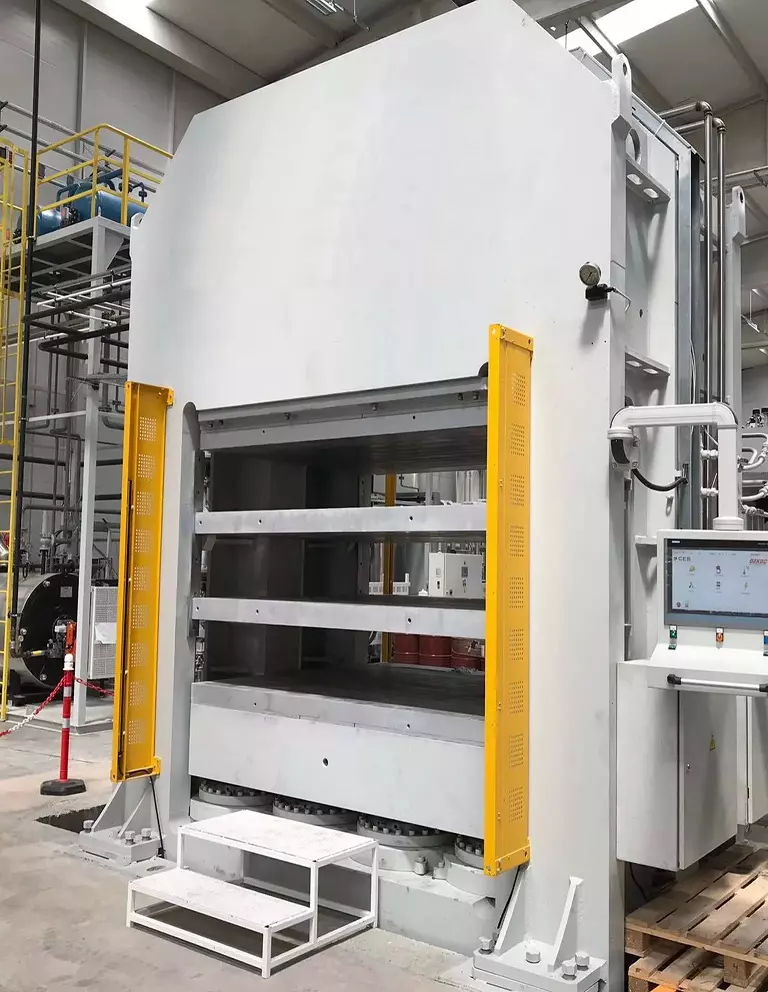
La presse en ligne pour moulage composite est une machine spécialement conçue pour la fabrication de pièces en matériaux composites, utilisés dans des industries comme l’aéronautique, l’automobile, et les énergies renouvelables. Ces matériaux composites, qui associent deux ou plusieurs matériaux distincts pour créer un produit plus résistant et léger, nécessitent un processus de moulage complexe. La presse en ligne pour moulage composite permet de produire des pièces de haute précision et de qualité grâce à un procédé de compression ou de transfert automatisé.
Fonctionnement de la Presse en Ligne pour Moulage Composite
Le moulage composite repose sur l’application de chaleur et de pression pour former des matériaux composites dans des moules spécifiques. La presse en ligne pour moulage composite utilise un système hydraulique ou mécanique pour appliquer une force uniforme sur le matériau composite, souvent constitué de fibres (comme le carbone, le verre ou le Kevlar) et d’une résine thermodurcissable ou thermoplastique.
Le processus commence par le placement des couches de matériau composite dans un moule chauffé. Une fois en place, la presse applique une pression contrôlée, qui force les couches de matériaux à prendre la forme du moule. La chaleur permet de catalyser la résine, qui durcit et forme une pièce rigide et solide. Le principal avantage des presses en ligne est qu’elles sont intégrées à une chaîne de production automatisée, où plusieurs étapes de moulage peuvent être réalisées sans interruption, augmentant ainsi l’efficacité et la productivité.
Types de Processus de Moulage Composite
Il existe plusieurs méthodes de moulage composite adaptées à la fabrication de différentes pièces, chacune étant optimisée pour des types de matériaux et des exigences spécifiques :
- Moulage par compression : Le processus le plus couramment utilisé, où les couches de matériaux sont placées dans un moule chauffé et une pression est appliquée pour former la pièce. Il est particulièrement adapté aux pièces plates ou légèrement courbées.
- Moulage par transfert de résine (RTM) : Cette méthode consiste à injecter la résine dans un moule préalablement rempli de fibres, sous pression. Elle permet de produire des pièces complexes avec une finition de surface de haute qualité.
- Moulage par injection : Dans ce processus, des granulés de matériau thermoplastique sont chauffés et injectés dans un moule sous haute pression, permettant de créer des pièces avec des géométries complexes en une seule étape.
- Moulage SMC/BMC (Sheet/Bulk Molding Compound) : Cette technique utilise des matériaux composites sous forme de feuilles (SMC) ou de masses (BMC) qui sont placées dans le moule avant d’être pressées et durcies. Elle est idéale pour les pièces à haut volume de production.
Avantages des Presses en Ligne pour Moulage Composite
Les presses en ligne pour moulage composite apportent de nombreux avantages dans le processus de fabrication des pièces composites :
- Légèreté et résistance : Les matériaux composites formés par ces presses sont à la fois légers et extrêmement résistants, ce qui en fait un choix idéal pour des secteurs comme l’aéronautique et l’automobile, où la réduction du poids est cruciale pour améliorer l’efficacité énergétique.
- Précision et contrôle : Les presses en ligne offrent un contrôle précis sur la pression, la température et le temps de cycle, garantissant ainsi une qualité constante et des tolérances serrées pour chaque pièce fabriquée.
- Cycle de production rapide : Grâce à l’automatisation et à la capacité de la presse en ligne à fonctionner sans interruption, le processus de moulage est accéléré, permettant de produire un grand nombre de pièces en peu de temps.
- Réduction des coûts : La fabrication de pièces composites en une seule opération permet de réduire le nombre de traitements post-production, diminuant ainsi les coûts de main-d’œuvre et de production.
Applications des Presses en Ligne pour Moulage Composite
Les matériaux composites sont de plus en plus utilisés dans une grande variété de secteurs industriels, et les presses en ligne pour moulage composite permettent de répondre aux exigences de production de ces secteurs :
- Aéronautique : L’utilisation de matériaux composites dans l’aéronautique est en forte augmentation, notamment pour des pièces structurelles comme les ailes, les carénages et les empennages. Les composites offrent une résistance mécanique élevée tout en réduisant le poids des avions, ce qui améliore l’efficacité énergétique et réduit les émissions.
- Automobile : Dans l’industrie automobile, les pièces en composite, telles que les panneaux de carrosserie, les châssis et les composants de suspension, sont utilisées pour réduire le poids des véhicules tout en conservant une résistance accrue. Les presses en ligne pour moulage composite permettent de produire ces pièces en série, garantissant une production rapide et à grande échelle.
- Énergies renouvelables : Les composites sont largement utilisés dans la fabrication des pales d’éoliennes et autres équipements liés aux énergies renouvelables, où la légèreté et la durabilité sont des facteurs clés. Les presses en ligne permettent de produire des composants de grande taille tout en maintenant une qualité de fabrication irréprochable.
- Industrie des sports et loisirs : Les matériaux composites sont également utilisés dans la fabrication d’équipements sportifs de haute performance, tels que les cadres de vélos, les skis, et les bateaux. Les presses en ligne permettent de produire ces pièces avec des propriétés spécifiques telles que la rigidité, la légèreté, et la résistance aux chocs.
Innovations Technologiques dans le Moulage Composite
Les presses en ligne pour moulage composite ont évolué avec l’introduction de nouvelles technologies qui améliorent la qualité des produits et augmentent l’efficacité des processus :
- Automatisation complète : De nombreuses presses modernes sont entièrement automatisées, avec des robots intégrés qui manipulent les matériaux, alimentent les moules et retirent les pièces finies. Cela permet d’améliorer la productivité et de réduire les erreurs humaines.
- Contrôle numérique avancé (CNC) : Les systèmes CNC permettent de programmer chaque aspect du processus de moulage, y compris la température, la pression et le temps de cure. Cela garantit des résultats constants et précis à chaque cycle de production.
- Technologies de surveillance en temps réel : Grâce à des capteurs intégrés, les presses en ligne peuvent surveiller en temps réel des paramètres critiques tels que la température du moule et la pression, permettant des ajustements automatiques pour optimiser la qualité des pièces produites.
- Moulage à cycle court : Les nouvelles technologies de moulage permettent de réduire considérablement les temps de cycle, notamment en utilisant des résines à durcissement rapide, ce qui améliore encore l’efficacité de la production en série.
Emboutissage Métallique pour Aéronautique
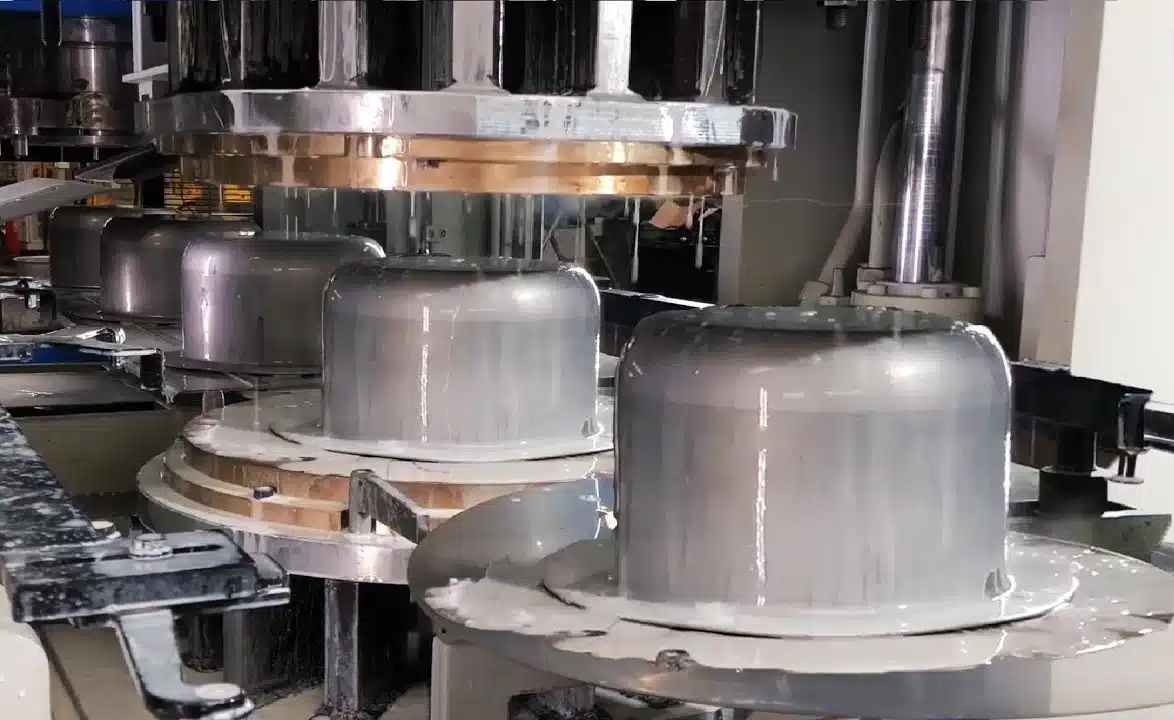
L’emboutissage métallique est une technique de formage utilisée dans l’industrie aéronautique pour fabriquer des pièces complexes à partir de tôles métalliques. Ce procédé est essentiel pour la production de composants structurels légers et robustes, indispensables à la performance et à la sécurité des avions. Dans le secteur aéronautique, l’emboutissage métallique permet de produire des pièces aux tolérances serrées, tout en optimisant le poids et la résistance des matériaux, ce qui est crucial pour améliorer l’efficacité énergétique et réduire les coûts d’exploitation.
Fonctionnement de l’Emboutissage Métallique
L’emboutissage consiste à déformer une feuille métallique (appelée flan) en la plaçant dans une matrice, puis en exerçant une pression à l’aide d’un poinçon pour lui donner la forme souhaitée. Ce processus de déformation plastique se fait souvent à froid dans l’aéronautique, pour préserver les propriétés mécaniques du matériau. Le processus peut inclure des étapes supplémentaires telles que le découpage, le pliage ou l’étirage, selon la complexité de la pièce.
Les matériaux utilisés pour l’emboutissage dans l’aéronautique sont souvent des alliages légers comme l’aluminium ou des alliages exotiques comme le titane et les composites renforcés, qui allient légèreté et haute résistance. Ces matériaux permettent de fabriquer des composants critiques tels que les fuselages, les carénages et les cadres internes, tout en respectant les exigences strictes en matière de sécurité aéronautique.
Types de Processus d’Emboutissage Métallique
Il existe plusieurs méthodes d’emboutissage utilisées dans l’industrie aéronautique pour répondre aux besoins spécifiques de la production de pièces :
- Emboutissage profond : Ce procédé est utilisé pour former des pièces profondes et complexes, telles que les réservoirs de carburant ou les carénages. Il permet de produire des pièces creuses sans joint, ce qui améliore leur résistance structurelle.
- Emboutissage à froid : Il est souvent privilégié pour former des alliages d’aluminium, car il permet de conserver la résistance du matériau tout en assurant une haute précision dans le processus.
- Emboutissage à chaud : Utilisé pour des matériaux plus difficiles à former, comme le titane ou les alliages à haute température, l’emboutissage à chaud consiste à chauffer le matériau avant de l’emboutir, ce qui facilite sa déformation tout en prévenant les risques de fissuration.
- Emboutissage progressif : Dans ce processus, la feuille métallique passe par plusieurs étapes de formage successives dans un outillage progressif, permettant de réaliser des pièces complexes en une seule séquence automatisée.
Avantages de l’Emboutissage Métallique dans l’Aéronautique
L’emboutissage est une technique privilégiée dans l’industrie aéronautique pour de nombreuses raisons :
- Légèreté et résistance : L’emboutissage permet de produire des pièces légères avec des géométries complexes, tout en conservant une grande résistance mécanique. Cela est essentiel pour optimiser les performances des aéronefs et réduire leur consommation de carburant.
- Haute précision : Les pièces embouties répondent aux tolérances très strictes exigées par les normes de l’aéronautique, garantissant ainsi une qualité uniforme, même pour des pièces de grande taille.
- Réduction des assemblages : L’emboutissage permet de fabriquer des pièces monoblocs, ce qui réduit le besoin d’assemblages et de soudures, diminuant ainsi les points de faiblesse et améliorant la fiabilité structurelle.
- Efficacité de production : Le processus d’emboutissage est adapté à la production en série, avec des cycles de production rapides et une automatisation accrue, ce qui permet de répondre aux besoins massifs de l’industrie aéronautique tout en optimisant les coûts de fabrication.
Applications de l’Emboutissage Métallique dans l’Aéronautique
L’emboutissage est utilisé pour produire une grande variété de pièces aéronautiques, allant des composants structurels aux éléments de carénage :
- Fuselage : Les panneaux et les cadres du fuselage, qui forment la structure externe de l’avion, sont souvent produits par emboutissage. Ces pièces doivent être légères pour minimiser le poids de l’avion, tout en étant suffisamment résistantes pour supporter les contraintes mécaniques et les pressions en vol.
- Carénages : Les carénages sont des pièces profilées qui couvrent les parties mobiles ou mécaniques de l’avion, comme les trains d’atterrissage ou les moteurs. L’emboutissage permet de produire ces composants avec des formes aérodynamiques complexes, réduisant ainsi la traînée et améliorant l’efficacité énergétique.
- Cadres internes : Les pièces structurelles internes, telles que les nervures et les supports des ailes ou des réservoirs de carburant, sont souvent embouties pour garantir une haute résistance tout en optimisant l’utilisation de l’espace.
- Composants des moteurs : Certaines pièces utilisées dans la fabrication des moteurs d’avion, notamment les ailettes de turbines et les enveloppes, sont fabriquées par emboutissage, en raison des exigences de haute précision et de résistance à la chaleur.
Innovations dans l’Emboutissage Métallique pour l’Aéronautique
Les technologies d’emboutissage dans l’aéronautique ont évolué avec l’introduction de nouveaux matériaux et de procédés avancés :
- Matériaux composites : Bien que les matériaux composites soient plus difficiles à former que les métaux, des innovations récentes permettent de les emboutir en combinaison avec des alliages métalliques, améliorant ainsi les performances mécaniques des pièces tout en réduisant leur poids.
- Simulation numérique : Avant de commencer la production, des logiciels de simulation numérique permettent de tester et d’optimiser le processus d’emboutissage, réduisant ainsi les risques d’erreurs et les coûts liés aux essais physiques. Cela garantit que chaque pièce sera fabriquée selon les spécifications exactes requises par l’industrie aéronautique.
- Emboutissage avec assistance robotique : Les presses d’emboutissage modernes sont souvent équipées de bras robotisés pour automatiser le processus de manipulation des pièces, augmentant ainsi la productivité et la précision tout en minimisant les erreurs humaines.
- Emboutissage en ligne : Cette méthode intègre plusieurs étapes de formage dans une seule ligne de production automatisée, permettant de réaliser des opérations d’emboutissage, de découpe et d’assemblage en une seule séquence, ce qui améliore l’efficacité de la production.
Machine à Polir
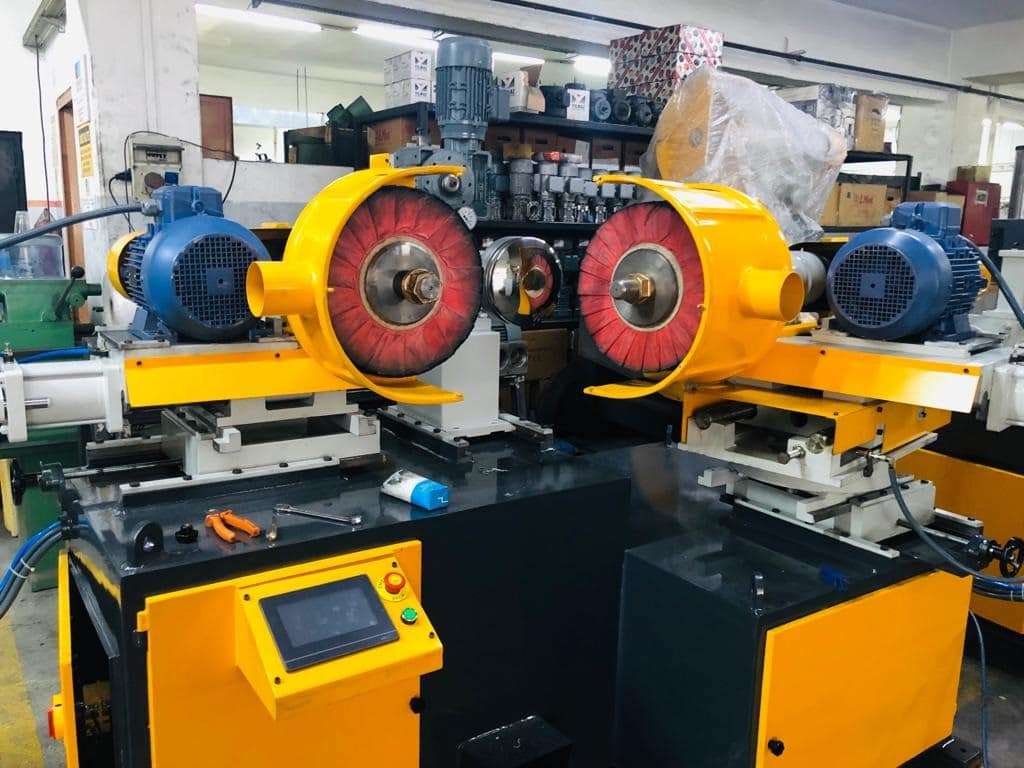
La machine à polir est un équipement industriel utilisé pour améliorer la finition des surfaces métalliques ou autres matériaux. Ce processus de polissage consiste à rendre une surface lisse et brillante, éliminant ainsi les rugosités, les défauts mineurs et les marques laissées par les procédés de fabrication précédents. Les machines à polir sont essentielles dans de nombreux secteurs, notamment la métallurgie, l’automobile, l’aéronautique, la bijouterie, et bien d’autres, où l’apparence, la précision et la qualité de la finition jouent un rôle crucial.
Fonctionnement des Machines à Polir
Le polissage est un processus mécanique dans lequel un abrasif est utilisé pour enlever une fine couche de matériau sur la surface à traiter, créant ainsi une finition plus lisse et plus brillante. Les machines à polir peuvent être manuelles, semi-automatiques ou entièrement automatisées, selon les exigences de production et le niveau de précision souhaité.
Les principales composantes d’une machine à polir incluent :
- Disques de polissage : Ces disques abrasifs, souvent fabriqués en feutre, en tissu ou en caoutchouc, sont utilisés pour frotter la surface de la pièce. Différents types de disques sont utilisés en fonction du matériau à polir et du niveau de finition souhaité.
- Abrasifs : Des abrasifs, tels que des pâtes de polissage ou des grains fins, sont appliqués sur les disques pour améliorer le processus de lissage.
- Moteur rotatif : Les machines à polir sont équipées d’un moteur qui fait tourner les disques à grande vitesse, permettant d’éliminer efficacement les imperfections de surface.
Types de Machines à Polir
Il existe plusieurs types de machines à polir, adaptées aux différents matériaux et applications :
- Machines à polir manuelles : Utilisées principalement pour des opérations de polissage plus fines ou des travaux sur des pièces uniques, ces machines nécessitent l’intervention d’un opérateur pour guider la pièce et ajuster la pression et le mouvement.
- Machines à polir semi-automatiques : Ces machines nécessitent moins d’intervention manuelle, car elles sont équipées de bras articulés ou de supports de pièces qui déplacent les objets sous le disque de polissage. Elles sont idéales pour les moyennes séries de production.
- Machines à polir automatiques : Utilisées pour les grandes productions, ces machines sont entièrement automatisées et peuvent polir un grand nombre de pièces de manière répétitive et rapide. Elles sont souvent équipées de capteurs et de systèmes de contrôle numérique pour ajuster le polissage en fonction des spécificités de chaque pièce.
- Polisseuses portatives : Ces machines plus petites sont souvent utilisées pour des retouches sur des surfaces déjà finies ou dans des endroits difficiles d’accès.
Avantages des Machines à Polir
L’utilisation de machines à polir dans les processus industriels présente plusieurs avantages significatifs :
- Amélioration de l’apparence : Le polissage permet d’obtenir des surfaces brillantes et esthétiquement plaisantes, essentielles dans des industries comme la bijouterie, l’horlogerie et l’automobile, où l’apparence du produit est cruciale.
- Réduction des imperfections : Les machines à polir éliminent efficacement les rayures, les marques de soudure et autres défauts de surface, offrant ainsi une meilleure finition et une durée de vie accrue des pièces.
- Préparation des surfaces : Le polissage est souvent utilisé avant d’autres traitements de surface, comme la galvanisation ou le chromage, pour garantir une adhérence optimale du revêtement et une finition de haute qualité.
- Uniformité et précision : Les machines à polir automatisées permettent d’obtenir des finitions constantes sur un grand nombre de pièces, tout en assurant des tolérances serrées.
Applications des Machines à Polir
Les machines à polir sont largement utilisées dans plusieurs secteurs pour améliorer la qualité et la finition des produits :
- Automobile : Dans l’industrie automobile, les machines à polir sont utilisées pour donner une finition lisse aux carrosseries, aux jantes et aux autres composants visibles. Elles sont également essentielles pour polir les pièces mécaniques internes, telles que les pistons et les arbres de transmission, afin d’améliorer les performances et de réduire l’usure.
- Aéronautique : Dans l’industrie aéronautique, le polissage est utilisé pour améliorer la finition des composants métalliques tels que les ailes, les panneaux de fuselage et les pièces de moteur. Un polissage précis permet de réduire la résistance à l’air, d’améliorer l’efficacité aérodynamique et de garantir des performances optimales en vol. De plus, la finition des pièces métalliques assure une durabilité accrue, en minimisant les risques de corrosion et de fatigue des matériaux.
- Bijouterie et horlogerie : Le polissage est essentiel pour obtenir des surfaces lisses et brillantes sur les bijoux et les montres. Les machines à polir permettent d’éliminer les imperfections et d’obtenir une finition parfaite, ce qui est crucial dans ces industries où l’esthétique joue un rôle primordial.
- Équipements médicaux : Les machines à polir sont également utilisées pour la finition des instruments chirurgicaux et des implants, où des surfaces lisses sont nécessaires pour prévenir les infections et faciliter l’utilisation des dispositifs médicaux.
- Électronique : Dans la fabrication de boîtiers métalliques et d’autres composants électroniques, le polissage est utilisé pour améliorer l’apparence et la résistance des pièces, garantissant ainsi une meilleure durée de vie et une protection accrue contre l’usure et les agressions extérieures.
Innovations Technologiques dans les Machines à Polir
Les machines à polir ont évolué avec l’introduction de nouvelles technologies qui améliorent leur efficacité et leur polyvalence :
- Systèmes de contrôle numérique (CNC) : Les machines à polir CNC permettent de programmer et d’automatiser le processus de polissage, garantissant des résultats constants et de haute précision, même sur des formes complexes.
- Polissage robotisé : Les robots de polissage automatisent totalement le processus et sont utilisés pour des pièces de grande taille ou difficiles à manipuler manuellement, augmentant ainsi la productivité tout en réduisant les erreurs humaines.
- Polissage écologique : De plus en plus de machines à polir sont conçues pour être plus respectueuses de l’environnement, en utilisant des abrasifs et des techniques qui réduisent les déchets et l’impact environnemental.
Machine à Polir Professionnel
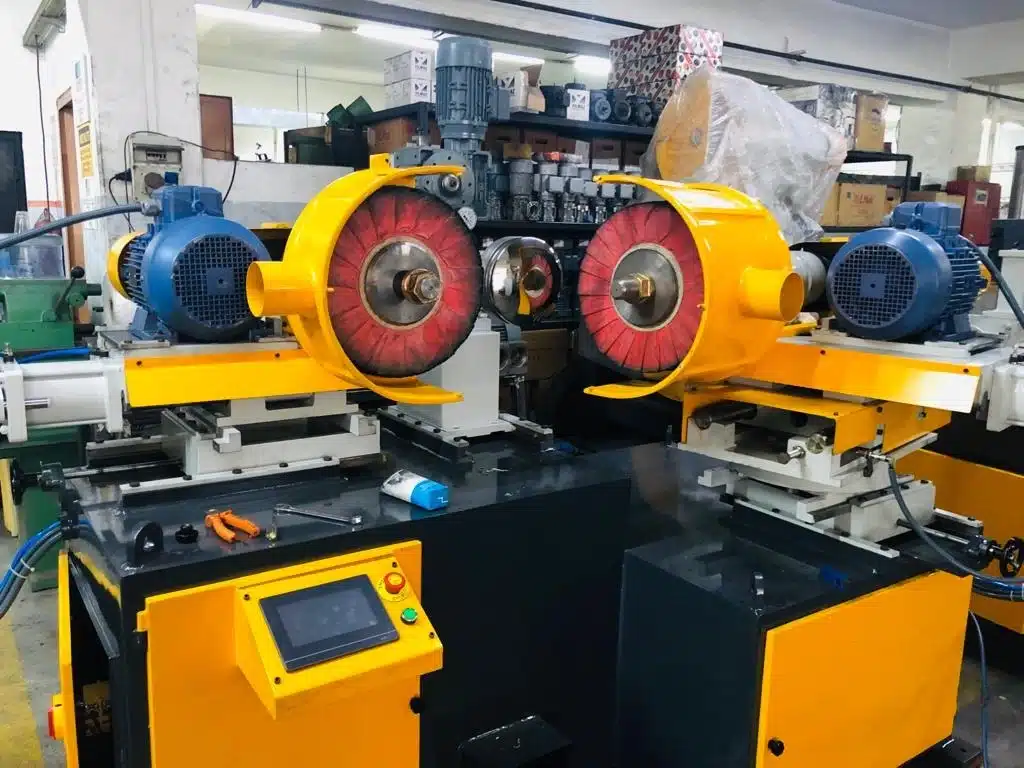
La machine à polir professionnel est un équipement destiné aux industries et ateliers spécialisés qui nécessitent des finitions de haute précision et une surface lisse parfaite. Contrairement aux machines de polissage standard, les modèles professionnels sont conçus pour offrir une qualité de polissage supérieure, essentielle dans des secteurs où la précision, l’apparence et la durabilité sont des critères majeurs, comme la bijouterie, l’horlogerie, la métallurgie fine, et l’artisanat de luxe.
Fonctionnement des Machines à Polir Professionnel
Les machines à polir professionnel fonctionnent sur le même principe que les machines standard, mais elles sont optimisées pour les besoins de précision accrue. Elles utilisent des disques de polissage rotatifs ou vibrants, auxquels des abrasifs de différentes granulométries sont appliqués pour enlever les imperfections et créer une surface lisse et brillante.
- Disques et abrasifs : Ces machines sont équipées de disques de polissage spécifiques en feutre, coton, ou matériaux composites, avec l’utilisation d’abrasifs fins tels que des pâtes de polissage ou des poudres spéciales. Les disques peuvent être interchangeables pour différentes étapes du polissage, allant de l’ébauche à la finition.
- Commandes précises : Les machines professionnelles offrent souvent un contrôle précis de la vitesse et de la pression, permettant de polir délicatement les surfaces les plus sensibles, sans risque de les abîmer.
Types de Machines à Polir Professionnel
Il existe plusieurs types de machines à polir professionnel, adaptées aux besoins spécifiques des différentes industries :
- Machines à polir rotatives : Celles-ci sont idéales pour polir des pièces circulaires ou courbes. Elles permettent de travailler sur des angles complexes et des géométries détaillées, comme celles trouvées dans la fabrication de bijoux ou de montres.
- Machines à polir vibrantes : Utilisées pour des pièces plus petites ou des travaux fins, ces machines exercent une vibration douce qui déplace l’abrasif uniformément sur la surface de la pièce. Elles sont couramment utilisées dans la bijouterie pour polir des pierres précieuses ou des métaux fins.
- Machines de polissage à commande numérique (CNC) : Ces machines sont entièrement automatisées et permettent de programmer avec précision chaque étape du processus de polissage. Elles sont particulièrement utilisées pour des pièces complexes nécessitant des tolérances serrées, comme dans l’horlogerie ou les instruments médicaux.
Avantages des Machines à Polir Professionnel
Les machines à polir professionnel offrent de nombreux avantages pour les industries nécessitant une finition de haute qualité :
- Précision maximale : Grâce à leur capacité à ajuster la pression et la vitesse de polissage, ces machines permettent de travailler des matériaux délicats, comme les métaux précieux ou les composites, sans risque de les endommager.
- Résultats de qualité supérieure : Les machines professionnelles garantissent une finition impeccable, sans rayures ni défauts, ce qui est essentiel pour des produits de luxe ou des composants techniques de haute précision.
- Durabilité accrue des pièces : En obtenant une surface parfaitement lisse, le polissage professionnel augmente la durabilité des pièces en réduisant les zones de friction, ce qui limite l’usure et la corrosion à long terme.
- Adaptabilité à différents matériaux : Ces machines peuvent être utilisées pour polir divers types de matériaux, des métaux précieux comme l’or et l’argent, aux matériaux industriels comme l’acier inoxydable et les alliages d’aluminium.
Applications des Machines à Polir Professionnel
Les machines à polir professionnel sont indispensables dans plusieurs secteurs industriels et artisanaux :
- Bijouterie et horlogerie : Dans ces secteurs, la finition des surfaces est cruciale pour obtenir un éclat et une brillance irréprochables. Le polissage permet d’éliminer les imperfections et d’améliorer l’esthétique des bijoux et des montres, qu’il s’agisse de métaux précieux ou de pierres.
- Médical : Les instruments chirurgicaux, les implants et autres dispositifs médicaux nécessitent un polissage de haute précision pour garantir une hygiène parfaite et une fonctionnalité optimale. Le polissage améliore également la biocompatibilité des implants.
- Luxe et design : Dans la fabrication de pièces de luxe ou de mobilier design, le polissage joue un rôle essentiel pour obtenir des surfaces parfaites et reflétant la lumière de manière esthétique. Le souci du détail dans la finition est essentiel dans ces domaines.
Innovations Technologiques
Les machines à polir professionnel bénéficient également des avancées technologiques récentes :
- Systèmes de contrôle numérique avancés : Les machines à polir professionnel sont souvent équipées de commandes numériques qui permettent de personnaliser chaque étape du processus, assurant une précision et une répétabilité parfaites.
- Robotique intégrée : Dans les grandes productions, des robots sont intégrés pour automatiser le polissage des pièces complexes ou répétitives. Cela permet d’augmenter la cadence tout en maintenant une qualité constante.
- Techniques de polissage écologique : De plus en plus d’industries utilisent des abrasifs et des procédés moins polluants pour réduire l’impact environnemental du polissage, tout en maintenant des standards de qualité élevés.
Presses à 4 Colonnes

Les presses à 4 colonnes sont des machines industrielles robustes et polyvalentes, utilisées principalement pour des opérations de formage, d’emboutissage, de découpe, et d’assemblage de matériaux métalliques. Comme leur nom l’indique, ces presses disposent de quatre colonnes verticales qui supportent le plateau supérieur et répartissent la pression exercée sur la pièce de manière uniforme. Grâce à cette structure, les presses à 4 colonnes sont particulièrement appréciées pour leur stabilité, leur précision et leur capacité à exercer des forces de compression élevées, même sur de grandes pièces.
Fonctionnement des Presses à 4 Colonnes
Les presses à 4 colonnes fonctionnent en appliquant une pression verticale sur une pièce de métal ou de tout autre matériau placé entre un poinçon et une matrice. La pression est générée soit par un système hydraulique, soit par un mécanisme mécanique, en fonction du type de presse. Les quatre colonnes supportent le plateau supérieur, ce qui permet de maintenir une distribution homogène de la force sur toute la surface de la pièce. Ce cadre assure une grande stabilité et réduit les déformations des composants pendant le processus de formage.
Les presses à 4 colonnes peuvent être utilisées pour des opérations variées telles que l’emboutissage, la découpe, le pliage et même le moulage de matériaux composites ou plastiques. Elles sont conçues pour offrir une grande précision tout en pouvant traiter des matériaux épais et résistants.
Types de Presses à 4 Colonnes
Les presses à 4 colonnes existent en plusieurs configurations, chacune adaptée à des besoins spécifiques :
- Presses hydrauliques à 4 colonnes : Utilisées pour les opérations de formage nécessitant une force contrôlée et constante, ces presses sont largement utilisées dans le formage des métaux et l’emboutissage profond. Elles permettent d’ajuster précisément la pression, ce qui est essentiel pour obtenir des pièces aux tolérances serrées.
- Presses mécaniques à 4 colonnes : Celles-ci utilisent un moteur pour générer la force et sont plus rapides que les presses hydrauliques. Elles sont principalement utilisées dans des opérations nécessitant des cadences élevées, comme la découpe de pièces métalliques ou le pliage.
- Presses à 4 colonnes avec système CNC : Ces presses sont équipées de commandes numériques par calculateur (CNC), permettant de programmer avec précision chaque étape du processus de formage. Elles sont idéales pour des productions en série nécessitant une qualité constante.
Avantages des Presses à 4 Colonnes
Les presses à 4 colonnes offrent plusieurs avantages, notamment en termes de robustesse et de polyvalence :
- Stabilité et répartition uniforme de la pression : Grâce à leur structure à quatre colonnes, ces presses répartissent la pression de manière homogène, ce qui réduit le risque de déformation des pièces et garantit une précision optimale.
- Grande capacité de charge : Les presses à 4 colonnes peuvent supporter de lourdes charges et appliquer des forces très élevées, ce qui les rend adaptées à des matériaux épais ou résistants, comme l’acier et les alliages métalliques.
- Polyvalence : Ces machines peuvent être utilisées pour une large gamme d’opérations, du formage à l’emboutissage, en passant par le pliage, la découpe, et le moulage. Elles sont couramment employées dans des industries diverses telles que l’automobile, l’aéronautique, et la métallurgie.
- Facilité d’entretien : En raison de leur conception robuste et modulaire, les presses à 4 colonnes sont relativement faciles à entretenir et à réparer, ce qui les rend rentables sur le long terme.
Applications des Presses à 4 Colonnes
Les presses à 4 colonnes sont utilisées dans divers secteurs industriels en raison de leur capacité à manipuler des pièces volumineuses et complexes :
- Automobile : Dans l’industrie automobile, ces presses sont utilisées pour l’emboutissage de pièces de carrosserie, la fabrication de châssis, et la production de composants structurels. Leur capacité à former des matériaux épais et résistants tout en maintenant des tolérances strictes est essentielle pour garantir la sécurité et la durabilité des véhicules.
- Aéronautique : Les composants d’aéronefs, tels que les panneaux de fuselage, les ailes et les supports de moteurs, sont souvent formés à l’aide de presses à 4 colonnes, en raison de leur précision et de leur capacité à traiter des alliages métalliques légers mais résistants.
- Industrie des appareils électroménagers : Les presses à 4 colonnes sont utilisées pour emboutir et former des pièces métalliques utilisées dans les appareils électroménagers, comme les coques de lave-linge, les tambours et autres composants en métal.
- Moulage et formage de matériaux composites : Dans la production de pièces en matériaux composites, les presses à 4 colonnes sont souvent utilisées pour comprimer les fibres et la résine dans des moules chauffés, permettant ainsi de former des pièces légères et résistantes, utilisées dans des secteurs comme l’aéronautique et l’automobile.
Innovations Technologiques
Les presses à 4 colonnes ont bénéficié d’innovations technologiques qui ont considérablement amélioré leur performance et leur efficacité :
- Intégration des commandes numériques (CNC) : Les systèmes CNC permettent de programmer avec précision chaque étape du processus de formage, garantissant une qualité constante et une réduction des erreurs humaines. Cela facilite également le changement rapide d’outillage et de paramètres pour différents types de production.
- Systèmes de surveillance en temps réel : Les presses modernes sont équipées de capteurs qui surveillent en continu les paramètres tels que la pression, la température et la position des composants, permettant des ajustements en temps réel pour garantir une qualité optimale des pièces.
- Économies d’énergie : De plus en plus de presses à 4 colonnes sont conçues pour réduire la consommation d’énergie, notamment grâce à des systèmes hydrauliques plus efficaces et à des moteurs à faible consommation. Cela contribue à diminuer les coûts d’exploitation tout en maintenant des niveaux de performance élevés.
- Automatisation et robotisation : Les presses à 4 colonnes peuvent être intégrées à des lignes de production entièrement automatisées, où des robots manipulent les pièces avant et après le formage, augmentant ainsi la productivité et réduisant les temps d’arrêt.
Presses à Cadre en H
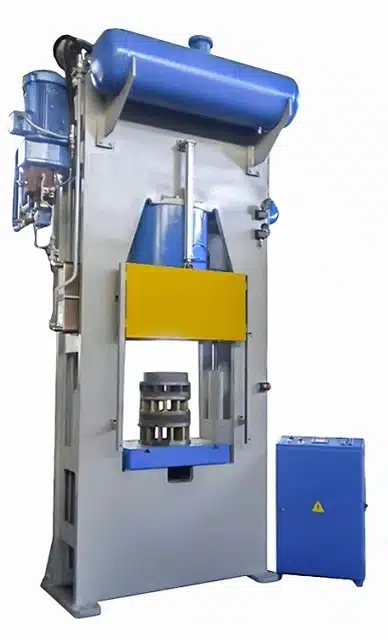
Les presses à cadre en H sont des machines industrielles robustes et puissantes, conçues pour des opérations de formage des métaux, telles que l’emboutissage, le pliage, le découpage et l’assemblage. Ces presses, également appelées presses à cadre fermé, se distinguent par leur structure en forme de « H », où deux poutres horizontales soutiennent la presse sur deux colonnes latérales. Cette conception assure une grande stabilité, une distribution uniforme de la force, et permet d’appliquer des pressions très élevées sans déformation du cadre, même sur des pièces volumineuses ou épaisses.
Fonctionnement des Presses à Cadre en H
Les presses à cadre en H fonctionnent en appliquant une pression verticale sur la pièce à traiter, qui est placée entre une matrice et un poinçon. La pression est généralement générée par un système hydraulique ou mécanique, selon le modèle de presse. Grâce à la rigidité de leur cadre, ces presses peuvent appliquer une force importante de manière homogène, ce qui réduit le risque de déformation de la pièce et garantit des résultats précis.
- Système hydraulique : Les presses à cadre en H hydraulique permettent un contrôle fin de la pression et de la vitesse, offrant ainsi une grande précision dans le formage des pièces.
- Système mécanique : Les presses mécaniques sont plus rapides et conviennent aux opérations nécessitant des cadences élevées, comme la découpe rapide ou le pliage de tôles fines.
Types de Presses à Cadre en H
Il existe plusieurs types de presses à cadre en H, adaptées aux différents besoins de production :
- Presses hydrauliques à cadre en H : Ces presses sont utilisées pour des opérations nécessitant une grande force de compression, telles que l’emboutissage profond et le formage de matériaux épais ou résistants. Elles permettent un contrôle précis de la pression et sont idéales pour le traitement de pièces volumineuses.
- Presses mécaniques à cadre en H : Utilisées principalement pour des opérations de découpe et de pliage à haute vitesse, ces presses sont adaptées aux productions en série de pièces plus simples nécessitant une répétabilité rapide et précise.
- Presses à cadre en H avec CNC : Ces presses sont équipées de commandes numériques, permettant de programmer chaque étape du processus de formage, garantissant ainsi une qualité constante et une grande flexibilité dans la production.
Avantages des Presses à Cadre en H
Les presses à cadre en H offrent plusieurs avantages qui en font un choix privilégié dans de nombreuses industries :
- Stabilité accrue : Grâce à leur conception en cadre fermé, ces presses sont extrêmement stables, même sous des forces de pression élevées. Cela réduit les vibrations et permet un formage plus précis.
- Distribution uniforme de la force : La structure en H permet une répartition homogène de la pression sur toute la surface de la pièce, ce qui est essentiel pour obtenir des tolérances serrées, en particulier lors du formage de grandes pièces.
- Grande capacité de charge : Les presses à cadre en H sont capables de supporter des forces de compression très élevées, ce qui les rend adaptées au traitement de matériaux épais, résistants, ou difficiles à former, comme l’acier ou les alliages spéciaux.
- Adaptabilité à divers procédés : Ces presses peuvent être utilisées pour une large gamme d’opérations, allant du simple découpage au formage complexe de pièces embouties. Leur conception modulaire permet de les adapter facilement aux besoins de production spécifiques.
Applications des Presses à Cadre en H
Les presses à cadre en H sont utilisées dans plusieurs secteurs industriels pour des opérations de formage, d’emboutissage et de découpe :
- Automobile : Ces presses sont largement utilisées pour fabriquer des composants structurels et des pièces de carrosserie, comme les portes, les capots et les châssis. Leur capacité à former des matériaux épais et résistants est essentielle pour garantir la sécurité et la durabilité des véhicules.
- Aéronautique : Dans l’industrie aéronautique, les presses à cadre en H sont utilisées pour produire des pièces légères et résistantes, comme les éléments de fuselage, les ailes et les composants internes. Leur stabilité et leur précision permettent de respecter les normes strictes de qualité et de sécurité requises dans ce secteur.
- Métallurgie : Ces presses sont également employées dans les aciéries et les usines de transformation des métaux pour la fabrication de poutres, de tubes et d’autres composants structurels utilisés dans la construction et les infrastructures.
- Fabrication d’équipements industriels : Dans la production de machines-outils, les presses à cadre en H sont utilisées pour assembler et former des composants volumineux, nécessitant une grande précision et une répartition uniforme de la pression.
Innovations Technologiques
Les presses à cadre en H ont bénéficié de nombreuses innovations qui ont amélioré leur performance et leur polyvalence :
- Commandes numériques avancées (CNC) : Les systèmes CNC permettent de programmer chaque étape du processus de formage, assurant une répétabilité parfaite et une qualité constante, même dans des productions en série. Cela facilite également les changements d’outils pour des productions variées.
- Surveillance en temps réel : Des capteurs intelligents sont intégrés dans les presses à cadre en H pour surveiller des paramètres tels que la pression et la position des composants, permettant des ajustements automatiques pour optimiser la qualité du formage.
- Réduction de la consommation énergétique : Grâce à des moteurs et systèmes hydrauliques plus efficaces, les presses modernes à cadre en H consomment moins d’énergie tout en maintenant des performances élevées, ce qui réduit les coûts d’exploitation et améliore l’empreinte écologique des installations.
- Automatisation : De nombreuses presses à cadre en H sont désormais intégrées à des lignes de production entièrement automatisées, où des robots assurent l’alimentation des pièces et l’évacuation des produits finis. Cela permet d’augmenter la cadence de production tout en minimisant les risques d’erreurs et les coûts liés à la main-d’œuvre.
Presses Composites
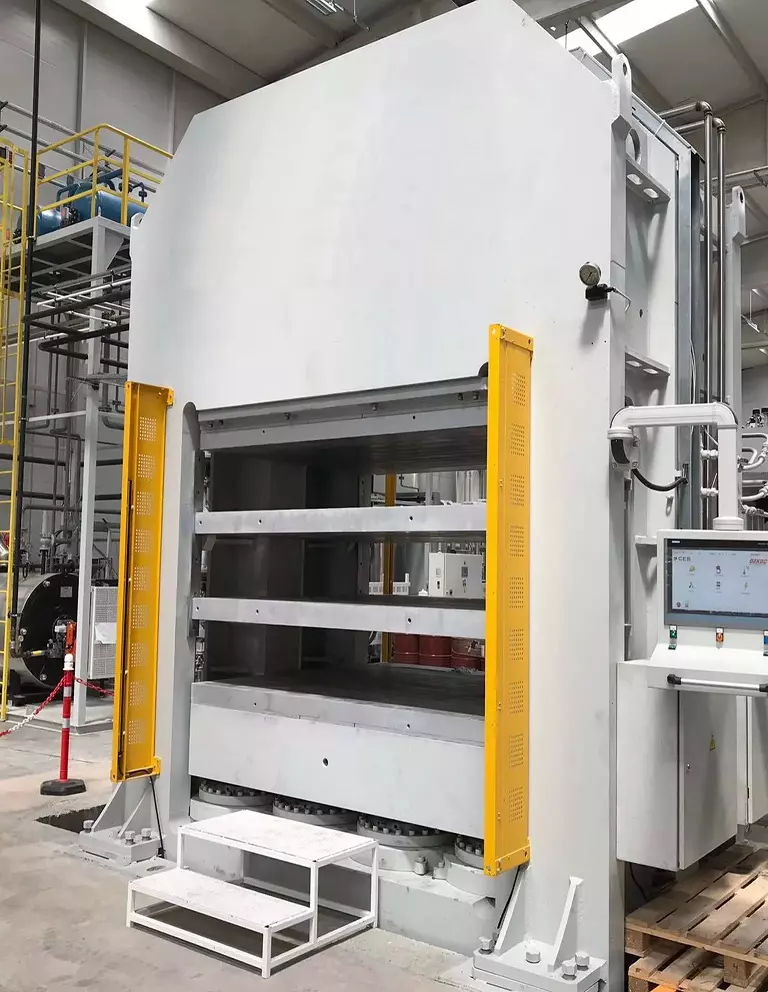
Les presses composites sont des machines spécialement conçues pour la fabrication de pièces à partir de matériaux composites, qui combinent deux ou plusieurs matériaux distincts pour obtenir des propriétés mécaniques optimisées. Ces presses sont essentielles dans des industries telles que l’aéronautique, l’automobile, et les énergies renouvelables, où les matériaux composites offrent une combinaison de légèreté et de résistance exceptionnelle. Les presses composites permettent de comprimer ces matériaux sous haute pression et chaleur, garantissant ainsi des pièces robustes et durables.
Fonctionnement des Presses Composites
Les presses composites fonctionnent en appliquant une force de compression sur des couches de fibres renforcées (telles que la fibre de carbone, de verre, ou d’aramide) imprégnées de résine thermoplastique ou thermodurcissable. Le processus commence par le placement du matériau composite dans un moule, souvent chauffé, puis la presse applique une pression élevée pour comprimer et former la pièce. La chaleur permet à la résine de durcir et de lier les fibres, créant ainsi une pièce solide et légère.
Le processus de pressage composite peut inclure plusieurs techniques :
- Moulage par compression : Un des procédés les plus courants, où les couches de matériau composite sont placées dans un moule chauffé, puis comprimées pour créer des pièces de forme complexe.
- Moulage par transfert de résine (RTM) : Dans cette technique, les fibres sont d’abord placées dans un moule, et la résine est injectée sous pression pour remplir l’espace entre les fibres, avant que la presse n’applique la compression nécessaire à la formation de la pièce.
Types de Presses Composites
Les presses composites peuvent varier en fonction des types de matériaux et des processus utilisés :
- Presses à compression à chaud : Utilisées pour les thermoplastiques et les thermodurcissables, ces presses appliquent à la fois de la chaleur et de la pression pour former des pièces solides et légères. Elles sont très populaires dans l’aéronautique et l’automobile.
- Presses de moulage par transfert de résine (RTM) : Ce type de presse est conçu pour injecter la résine dans les fibres tout en maintenant une pression constante pour garantir une distribution uniforme de la résine et un durcissement optimal.
- Presses composites avec CNC : Ces presses sont équipées de commandes numériques qui permettent de contrôler précisément la température, la pression et le temps de cycle, garantissant une production de haute qualité et répétable pour des pièces complexes.
Avantages des Presses Composites
Les presses composites apportent de nombreux avantages dans la fabrication de pièces en matériaux composites :
- Légèreté et résistance : Les matériaux composites sont connus pour leur rapport résistance/poids élevé, ce qui permet de fabriquer des pièces légères mais extrêmement résistantes, idéales pour des applications dans les secteurs de l’aéronautique et de l’automobile.
- Flexibilité de conception : Le processus de moulage composite permet de créer des pièces avec des géométries complexes, qui seraient difficiles ou impossibles à produire avec des matériaux métalliques traditionnels.
- Haute précision : Grâce aux systèmes CNC et à la régulation précise de la pression et de la température, les presses composites permettent de fabriquer des pièces aux tolérances serrées et avec une finition de surface de qualité.
- Réduction des coûts d’assemblage : Les pièces composites peuvent souvent être fabriquées en une seule étape, sans avoir besoin d’assemblages complexes ou de soudures, réduisant ainsi les coûts de fabrication et améliorant la durabilité des produits.
Applications des Presses Composites
Les presses composites sont utilisées dans divers secteurs où la légèreté, la résistance et la durabilité des pièces sont essentielles :
- Aéronautique : Les matériaux composites sont largement utilisés pour la fabrication de pièces structurelles légères, telles que les ailes, les carénages et les cadres d’avions. Grâce à leur résistance exceptionnelle et leur légèreté, les composites permettent d’améliorer l’efficacité énergétique des aéronefs tout en réduisant les émissions de carbone.
- Automobile : Dans l’industrie automobile, les composites sont utilisés pour la fabrication de châssis, de panneaux de carrosserie et de composants de suspension, contribuant à réduire le poids des véhicules et à améliorer leur performance. Les presses composites permettent de produire ces pièces en série tout en maintenant des normes de sécurité et de qualité élevées.
- Énergies renouvelables : Les presses composites sont également utilisées dans la fabrication de pales d’éoliennes, où la légèreté et la résistance sont des facteurs clés pour garantir une efficacité maximale des turbines éoliennes.
- Sports et loisirs : Dans la fabrication d’équipements sportifs de haute performance, tels que les cadres de vélos, les raquettes de tennis et les cannes à pêche, les matériaux composites offrent une combinaison de légèreté, de flexibilité et de résistance aux chocs.
Innovations Technologiques
Les presses composites ont évolué pour répondre aux exigences croissantes des industries en matière de qualité et d’efficacité :
- Commandes numériques avancées (CNC) : Les presses composites modernes sont équipées de systèmes CNC qui permettent un contrôle précis de chaque étape du processus, y compris la pression, la température et le temps de durcissement, garantissant ainsi des résultats de haute qualité et répétables.
- Automatisation : Les lignes de production automatisées intégrant des presses composites permettent de produire en série des pièces complexes avec une intervention humaine minimale. Les robots sont souvent utilisés pour manipuler les matériaux composites et les moules, ce qui augmente la cadence de production tout en maintenant une qualité constante.
- Matériaux composites à durcissement rapide : De nouveaux composites et résines thermodurcissables ont été développés pour accélérer le processus de durcissement, réduisant ainsi les temps de cycle et augmentant la productivité.
- Techniques de moulage sous vide : En utilisant des techniques de moulage sous vide, les presses composites peuvent réduire le nombre de bulles d’air dans la résine, ce qui améliore la qualité et la résistance des pièces finies.
Machine de Bordage Automatique
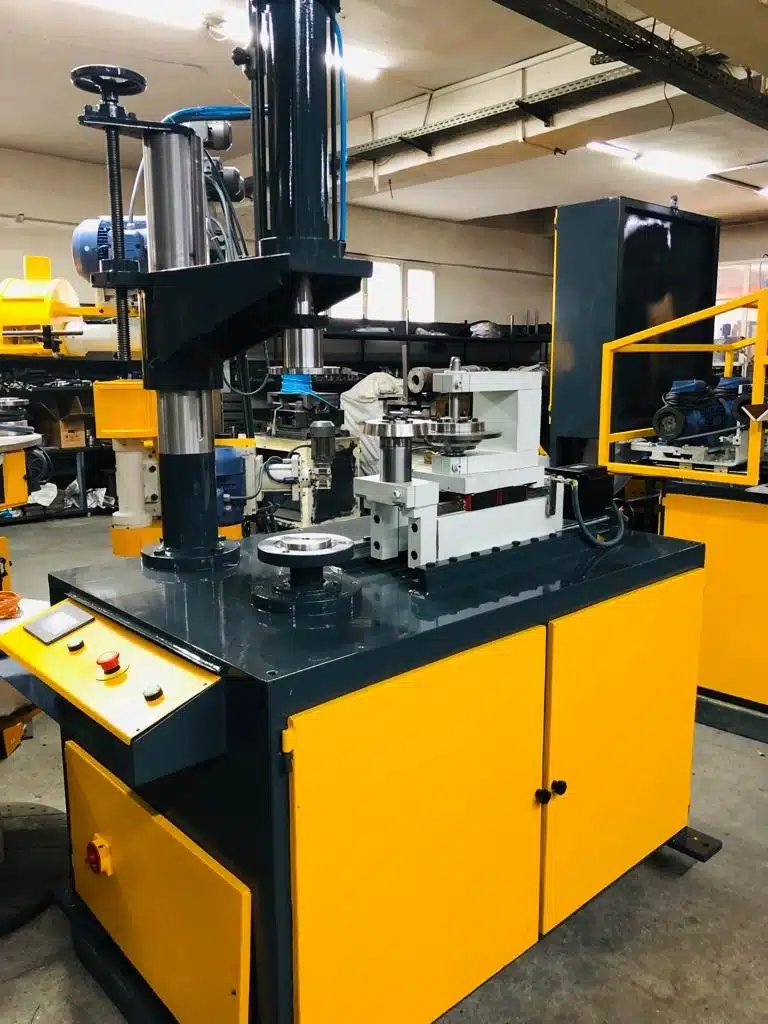
La machine de bordage automatique est un équipement industriel spécialisé utilisé pour former les bords des pièces métalliques ou d’autres matériaux. Ce procédé est essentiel pour renforcer la structure des pièces, améliorer leur résistance mécanique et préparer les composants à des opérations d’assemblage ou de sertissage. Les machines de bordage automatiques sont couramment utilisées dans des industries comme l’automobile, l’électroménager, l’aéronautique, et dans la fabrication de récipients métalliques tels que les cuves ou les réservoirs.
Fonctionnement des Machines de Bordage Automatique
Le bordage est un processus qui consiste à plier ou enrouler le bord d’une pièce métallique, souvent dans le but de renforcer la pièce, de la rendre plus sécurisée ou d’ajouter une esthétique lisse. Une machine de bordage automatique réalise cette opération de manière continue et avec précision, en utilisant des outils rotatifs ou des rouleaux pour former les bords de la pièce à des angles spécifiques.
Le fonctionnement de la machine repose sur les étapes suivantes :
- Fixation de la pièce : La pièce métallique est placée et fixée dans la machine. Un bras ou un support robotisé maintient la pièce en place pour éviter tout mouvement pendant l’opération de bordage.
- Action de bordage : Les outils de bordage, généralement constitués de rouleaux ou de matrices rotatives, appliquent une force sur les bords de la pièce pour les enrouler ou les plier à l’angle souhaité.
- Contrôle automatique : La machine est équipée d’un système de contrôle numérique qui ajuste la pression, la vitesse de rotation et le positionnement des rouleaux pour garantir une précision constante tout au long du processus. Des capteurs surveillent la qualité du bord formé.
Types de Bordage
Les machines de bordage automatique peuvent réaliser différents types de bordage selon les besoins spécifiques :
- Bordage simple : Il consiste à plier le bord d’une pièce de manière perpendiculaire pour renforcer le matériau ou préparer la pièce à l’assemblage.
- Bordage enroulé : Ce type de bordage enroule complètement le bord sur lui-même pour créer une finition lisse, couramment utilisée dans la fabrication de récipients comme les réservoirs ou les bidons.
- Bordage à double pli : Utilisé pour des applications nécessitant une résistance accrue, ce type de bordage consiste à plier et enrouler le bord de la pièce plusieurs fois.
- Bordage conique : Spécifique aux pièces de forme conique ou circulaire, où le bord est plié progressivement en suivant la forme de la pièce.
Avantages des Machines de Bordage Automatique
Les machines de bordage automatique offrent plusieurs avantages dans la production industrielle :
- Précision et répétabilité : Grâce à l’automatisation et aux systèmes de contrôle numérique, les machines de bordage assurent une qualité constante et uniforme sur chaque pièce produite, même pour des séries importantes.
- Rapidité de production : Les machines automatiques augmentent la cadence de production en éliminant les étapes manuelles et en permettant de traiter plusieurs pièces en continu.
- Réduction des coûts de main-d’œuvre : L’automatisation du bordage réduit les besoins en intervention humaine, ce qui permet d’économiser sur les coûts de production tout en améliorant la sécurité des opérateurs.
- Polyvalence : Ces machines peuvent être programmées pour réaliser une large gamme de types de bordage et s’adapter à différentes tailles et formes de pièces, ce qui les rend idéales pour des productions variées.
Applications des Machines de Bordage Automatique
Les machines de bordage automatique sont largement utilisées dans plusieurs secteurs industriels pour créer des pièces métalliques à bords robustes et précis :
- Automobile : Le bordage est essentiel dans la fabrication de nombreuses pièces automobiles, comme les portes, les capots et les panneaux de carrosserie. Le bordage renforce les bords de ces pièces tout en améliorant leur aspect esthétique et leur sécurité lors de l’assemblage.
- Aéronautique : Les composants d’aéronefs, tels que les panneaux d’aile et les éléments de fuselage, nécessitent un bordage précis pour garantir leur intégrité structurelle et réduire la résistance à l’air. Les machines de bordage automatiques sont utilisées pour former ces bords avec une grande précision.
- Fabrication de récipients : Les réservoirs, bidons et autres types de récipients métalliques doivent souvent être bordés pour éviter les fuites et améliorer la solidité de la structure. Le bordage permet également de créer des finitions lisses et sûres pour les récipients destinés aux industries alimentaires ou chimiques.
- Électroménager : Dans la fabrication d’appareils tels que les lave-linge ou les cuisinières, le bordage est utilisé pour renforcer les bords des coques métalliques et des tambours, garantissant ainsi la durabilité et la sécurité des produits.
Innovations Technologiques dans les Machines de Bordage
Les machines de bordage automatique ont évolué avec l’introduction de nouvelles technologies qui améliorent la qualité et l’efficacité du processus :
- Commandes numériques (CNC) : Les machines de bordage équipées de systèmes CNC permettent de programmer chaque étape du processus, garantissant une précision absolue et une répétabilité parfaite, même pour des pièces aux formes complexes.
- Automatisation avancée : Les machines modernes sont souvent entièrement automatisées, permettant de réduire l’intervention humaine et d’augmenter la cadence de production. Les systèmes robotisés peuvent charger et décharger les pièces, optimisant ainsi l’efficacité.
- Surveillance en temps réel : Des capteurs intelligents surveillent en continu des paramètres critiques comme la pression appliquée sur les bords, la vitesse de rotation des rouleaux et la position de la pièce, assurant ainsi une qualité constante et des ajustements automatiques en cas de besoin.
- Réduction du bruit et des vibrations : De nouvelles technologies ont été introduites pour réduire les niveaux de bruit et de vibrations lors du processus de bordage, améliorant ainsi le confort de travail pour les opérateurs tout en augmentant la précision du processus.
Cintreuse de Tubes Sans Mandrin
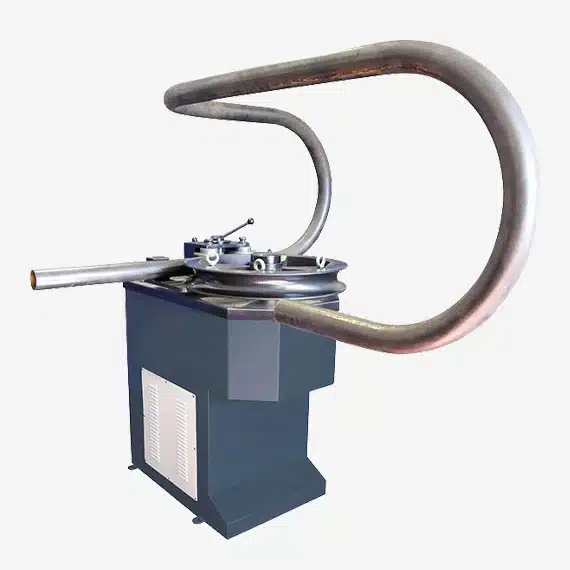
La cintreuse de tubes sans mandrin est une machine industrielle utilisée pour cintrer des tubes métalliques ou en plastique sans utiliser de mandrin interne. Ce procédé est largement employé dans des secteurs comme l’automobile, la construction, la plomberie, et l’ameublement. Contrairement aux cintreuses classiques, qui nécessitent un mandrin pour maintenir la forme intérieure du tube, les cintreuses sans mandrin utilisent des techniques avancées pour plier les tubes avec précision, tout en minimisant les déformations et les plis.
Fonctionnement des Cintreuses de Tubes Sans Mandrin
Le cintrage de tubes sans mandrin repose sur l’application d’une force extérieure pour plier le tube autour d’un gabarit ou d’une matrice, sans avoir besoin d’un support interne (mandrin). Ce procédé est particulièrement adapté aux tubes de grand diamètre ou aux matériaux qui ne nécessitent pas de maintien interne pour éviter le flambage.
- Cintrage rotatif : Dans cette méthode, le tube est placé entre un gabarit rotatif et des galets de maintien. Lorsque la machine active le cintrage, le tube est plié autour du gabarit, avec les galets qui l’empêchent de se déplacer ou de se déformer. Ce type de cintrage est rapide et efficace, adapté aux tubes de petite et moyenne épaisseur.
- Cintrage par enroulement : Cette technique consiste à enrouler le tube autour d’un gabarit fixe, en appliquant une force pour le plier de manière continue. Elle est idéale pour les grandes longueurs de tubes ou les matériaux plus souples, comme l’aluminium ou le cuivre.
Avantages des Cintreuses de Tubes Sans Mandrin
Les cintreuses de tubes sans mandrin offrent plusieurs avantages, notamment pour les tubes où un mandrin interne n’est pas nécessaire :
- Rapidité et efficacité : En éliminant l’étape de mise en place du mandrin, ces machines permettent d’accélérer le processus de cintrage et de réduire les temps de cycle, augmentant ainsi la productivité.
- Polyvalence : Ces machines peuvent cintrer une large variété de matériaux, y compris l’acier, l’aluminium, le cuivre, et même certains plastiques, avec différents diamètres et épaisseurs de tubes.
- Faible coût de maintenance : L’absence de mandrin réduit l’usure des outils et diminue les besoins en maintenance, ce qui en fait un choix économique pour de nombreuses applications industrielles.
- Cintrage de grandes pièces : Les cintreuses sans mandrin sont capables de plier de grands tubes ou des tubes épais qui ne nécessitent pas de soutien interne, comme dans la construction de structures métalliques ou de conduits.
Applications des Cintreuses de Tubes Sans Mandrin
Les cintreuses de tubes sans mandrin sont utilisées dans une multitude de secteurs industriels en raison de leur polyvalence et de leur capacité à cintrer des tubes sans nécessiter un mandrin interne :
- Construction : Dans le secteur de la construction, les cintreuses de tubes sont utilisées pour créer des structures métalliques, des échafaudages, des conduits, ou des éléments architecturaux courbés. Le cintrage sans mandrin permet de travailler des tubes de grand diamètre utilisés dans les bâtiments et les infrastructures.
- Automobile : Ces machines sont essentielles dans la fabrication de systèmes d’échappement, de cadres de véhicules, et de pièces structurelles. Le cintrage de tubes est crucial pour créer des formes précises sans compromettre la résistance des composants.
- Plomberie : Les cintreuses sans mandrin sont largement utilisées pour cintrer des tubes en cuivre ou en acier destinés aux systèmes de plomberie, garantissant un bon ajustement dans les installations sans nécessiter de jonctions supplémentaires.
- Mobilier : Dans l’industrie du mobilier métallique, le cintrage de tubes est utilisé pour créer des cadres et des structures esthétiques, comme les chaises, les tables et les luminaires. Ces machines permettent de réaliser des courbes douces et précises, sans risque de plisser le tube.
Innovations dans les Cintreuses de Tubes Sans Mandrin
Les cintreuses de tubes sans mandrin ont évolué avec l’introduction de nouvelles technologies, améliorant leur précision et leur efficacité :
- Contrôle numérique (CNC) : Les cintreuses CNC permettent de programmer avec précision chaque courbe et chaque angle de cintrage, garantissant des résultats parfaits, même sur des pièces complexes. Cela assure également une répétabilité optimale pour les grandes séries de production.
- Automatisation : De nombreuses cintreuses sans mandrin modernes sont entièrement automatisées, avec des systèmes de chargement et de déchargement automatiques, ce qui permet de traiter de grandes quantités de tubes sans intervention humaine et d’améliorer la productivité.
- Techniques de cintrage sans déformation : Grâce à des innovations dans le contrôle de la pression et de la vitesse de cintrage, les cintreuses sans mandrin modernes peuvent minimiser les risques de déformation des tubes, garantissant des résultats de haute qualité sans défauts.
- Capteurs de surveillance en temps réel : Les machines équipées de capteurs peuvent surveiller des paramètres comme la force de cintrage et la déformation du tube, permettant d’ajuster automatiquement le processus pour maintenir la qualité.
Limites du Cintrage Sans Mandrin
Bien que les cintreuses sans mandrin offrent une grande polyvalence et rapidité, elles présentent certaines limitations :
- Cintrage de petits rayons : Les tubes nécessitant des rayons de courbure très petits peuvent nécessiter un mandrin pour maintenir la forme intérieure du tube et éviter l’écrasement ou la déformation.
- Matériaux plus épais : Le cintrage de tubes très épais ou de matériaux particulièrement durs peut parfois nécessiter un mandrin pour garantir un contrôle précis de la forme, en particulier sur des courbes complexes.
Machine à Polir l’Acier

La machine à polir l’acier est un équipement industriel utilisé pour améliorer la surface des pièces en acier en les rendant lisses, brillantes et exemptes d’imperfections. Le polissage de l’acier est essentiel dans de nombreux secteurs industriels, notamment la métallurgie, l’automobile, l’aéronautique, et la construction, où la qualité des surfaces métalliques influe directement sur la durabilité, la performance et l’esthétique des produits finis.
Fonctionnement des Machines à Polir l’Acier
Les machines à polir l’acier utilisent des disques abrasifs, des roues en feutre, ou des brosses métalliques rotatives pour éliminer les défauts de surface, comme les rayures, les bavures et les marques d’usinage, et pour obtenir une finition lisse et brillante. Le processus de polissage peut être effectué en plusieurs étapes, avec l’utilisation d’abrasifs de granulométrie de plus en plus fine.
- Phase de dégrossissage : L’acier est d’abord poli avec des abrasifs grossiers pour enlever les imperfections majeures et les irrégularités de la surface.
- Phase de finition : Une fois la surface lissée, des disques plus fins sont utilisés pour obtenir une finition plus brillante et homogène.
- Phase de polissage miroir : Pour des applications esthétiques ou techniques de haute précision, une pâte de polissage peut être appliquée pour créer une surface d’acier avec un effet miroir.
Types de Machines à Polir l’Acier
Il existe plusieurs types de machines adaptées au polissage de l’acier, en fonction de la taille des pièces et du niveau de finition requis :
- Machines à polir manuelles : Ces machines sont utilisées pour les travaux de finition fine et permettent à l’opérateur de contrôler directement la pression et l’angle de polissage. Elles sont idéales pour des pièces uniques ou des travaux de précision.
- Machines à polir automatiques : Ces machines permettent de polir des pièces en série avec une précision constante. Elles sont équipées de bras articulés ou de systèmes robotisés qui réalisent le polissage de manière automatique, sans intervention humaine.
- Polisseuses portatives : Utilisées pour les travaux de retouche ou les petites pièces, ces machines portatives offrent une grande flexibilité pour accéder à des zones difficiles ou pour polir des objets de formes complexes.
- Machines à polir industrielles : Ces machines sont conçues pour traiter de grandes surfaces d’acier, comme des tôles ou des plaques, et sont utilisées dans des industries où la finition de surface est cruciale pour la performance, comme dans la construction de navires ou de machines lourdes.
Avantages des Machines à Polir l’Acier
L’utilisation de machines à polir l’acier présente de nombreux avantages dans l’industrie :
- Amélioration de l’apparence : Le polissage de l’acier permet d’obtenir une surface lisse et brillante, améliorant l’esthétique des pièces, en particulier pour des produits de haute qualité dans l’automobile ou l’architecture.
- Durabilité accrue : En éliminant les microfissures et les défauts de surface, le polissage renforce la résistance de l’acier à la corrosion et à l’usure, augmentant ainsi la durée de vie des pièces.
- Préparation des surfaces : Le polissage est souvent utilisé pour préparer les surfaces avant des traitements supplémentaires, comme le chromage ou la peinture, garantissant une adhérence optimale et une finition uniforme.
- Réduction des frottements : Dans des secteurs comme la mécanique et l’aéronautique, le polissage de l’acier permet de réduire les frottements entre les pièces mobiles, améliorant ainsi l’efficacité des machines et des équipements.
Applications des Machines à Polir l’Acier
Les machines à polir l’acier sont utilisées dans de nombreux secteurs industriels :
- Automobile : Le polissage des pièces automobiles, telles que les carrosseries, les jantes et les éléments chromés, est essentiel pour obtenir une finition brillante et durable. Les moteurs et les pièces internes peuvent également être polis pour améliorer leurs performances mécaniques.
- Aéronautique : Dans l’industrie aéronautique, les pièces en acier inoxydable, comme les composants de moteur ou les structures d’avion, sont souvent polies pour améliorer leur résistance à la corrosion et optimiser leurs performances en vol.
- Construction métallique : Dans la fabrication de structures en acier, telles que les poutres, les colonnes et les revêtements, le polissage permet de créer des surfaces esthétiques et résistantes aux intempéries, idéales pour des projets architecturaux de grande envergure.
- Industrie alimentaire : Les équipements en acier inoxydable utilisés dans la transformation des aliments sont souvent polis pour éviter l’accumulation de résidus et garantir un nettoyage facile, améliorant ainsi l’hygiène et la sécurité des produits alimentaires.
Innovations dans les Machines à Polir l’Acier
Les technologies de polissage ont évolué avec l’introduction de nouvelles innovations pour améliorer l’efficacité et la précision :
- Contrôle numérique (CNC) : Les machines à polir CNC permettent de programmer avec précision les mouvements de polissage, garantissant une qualité constante et une finition uniforme sur chaque pièce. Cela est particulièrement utile pour les séries de production où des tolérances strictes sont requises.
- Polissage robotisé : Les robots de polissage automatisent totalement le processus, augmentant la productivité et réduisant le besoin de main-d’œuvre qualifiée. Ils sont utilisés pour polir de grandes pièces complexes, comme des panneaux métalliques ou des composants de machines.
- Technologies de polissage écologique : Les nouvelles techniques de polissage utilisent des produits abrasifs plus respectueux de l’environnement, réduisant l’impact écologique du processus tout en garantissant des finitions de haute qualité.
- Systèmes de surveillance intelligents : Les machines à polir modernes intègrent des capteurs qui surveillent la pression, la vitesse et la température de la surface, permettant des ajustements en temps réel pour assurer un polissage optimal.
Machine d’Ébavurage
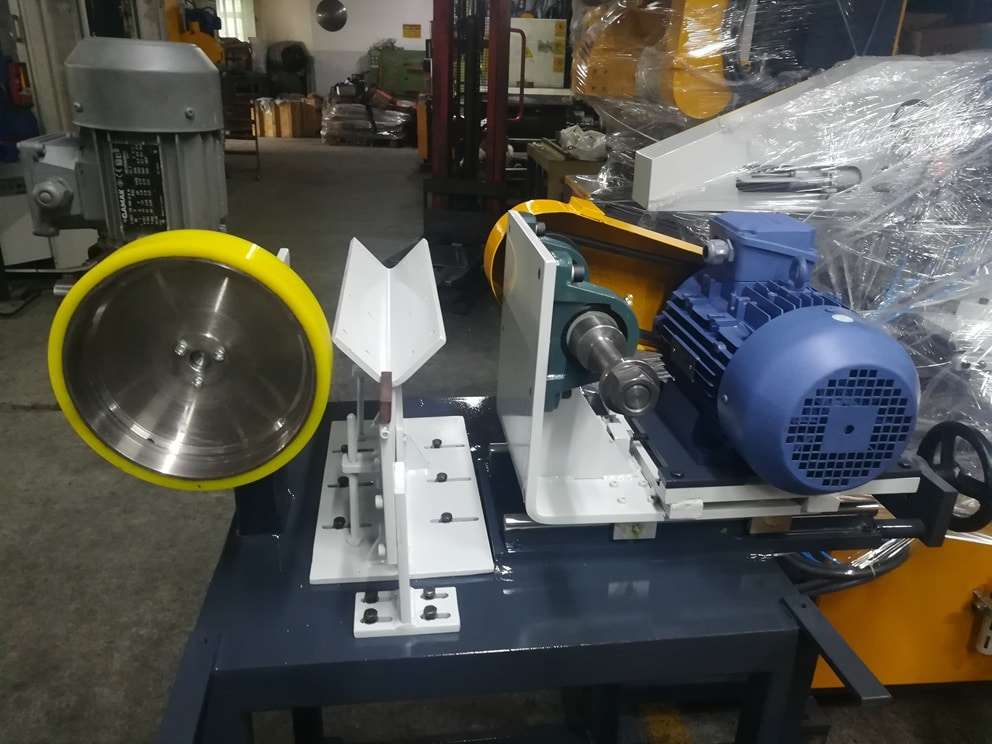
La machine d’ébavurage est un équipement industriel utilisé pour éliminer les bavures, qui sont des irrégularités ou des excroissances métalliques formées sur les bords des pièces lors de leur fabrication. Ces bavures apparaissent souvent après des opérations de découpe, de fraisage, d’usinage, ou de moulage et peuvent nuire à la qualité, à la précision et à la sécurité des pièces. L’ébavurage est donc une étape essentielle pour garantir que les pièces soient prêtes à être assemblées ou à recevoir d’autres traitements de surface.
Fonctionnement des Machines d’Ébavurage
Les machines d’ébavurage fonctionnent en utilisant des outils abrasifs, des brosses ou des rouleaux qui viennent frotter les bords des pièces pour enlever les bavures. Le processus d’ébavurage peut être mécanique, thermique, chimique ou électrochimique, en fonction du type de matériau et de l’application.
- Ébavurage mécanique : Ce procédé utilise des brosses métalliques ou des bandes abrasives pour lisser les bords des pièces. C’est l’une des méthodes les plus couramment utilisées, particulièrement pour les métaux.
- Ébavurage thermique : Il consiste à exposer brièvement la pièce à une chaleur intense, brûlant ainsi les bavures sans affecter les propriétés de la pièce. Ce procédé est souvent utilisé pour les pièces complexes et difficiles à traiter mécaniquement.
- Ébavurage chimique : Une solution chimique est appliquée pour dissoudre les bavures. Ce procédé est idéal pour les pièces de petite taille ou délicates, où les méthodes mécaniques risqueraient d’endommager la pièce.
- Ébavurage électrochimique : Un courant électrique est utilisé pour éroder les bavures à partir d’une pièce métallique, un procédé précis qui permet de traiter des pièces avec des tolérances serrées.
Types de Machines d’Ébavurage
Il existe plusieurs types de machines d’ébavurage adaptées à différents matériaux et types de production :
- Machines d’ébavurage à brosses rotatives : Ces machines utilisent des brosses rotatives pour éliminer les bavures et polir les bords des pièces. Elles sont souvent utilisées dans l’industrie de la métallurgie pour traiter des pièces de grande taille ou des tôles.
- Ébavureuses vibrantes : Ces machines utilisent un mouvement vibratoire pour déplacer les pièces en vrac à travers un abrasif, éliminant ainsi les bavures. Elles sont couramment utilisées pour des séries de petites pièces.
- Machines d’ébavurage CNC : Ces machines sont équipées de commandes numériques qui permettent de programmer précisément l’ébavurage des pièces, garantissant une qualité constante et des résultats reproductibles, même pour des pièces complexes.
- Ébavureuses thermiques : Utilisées pour les métaux et les plastiques, ces machines exposent les pièces à une chaleur contrôlée qui brûle les bavures tout en préservant l’intégrité des matériaux.
Avantages des Machines d’Ébavurage
L’utilisation de machines d’ébavurage dans les processus de fabrication offre de nombreux avantages :
- Amélioration de la qualité des pièces : L’ébavurage élimine les bords tranchants et irréguliers, garantissant ainsi que les pièces soient plus sûres à manipuler et prêtes pour les étapes suivantes du processus de production.
- Préparation pour les traitements de surface : Les bavures peuvent gêner l’application de revêtements ou de traitements de surface, comme le chromage ou la peinture. L’ébavurage permet d’obtenir une surface propre et lisse, garantissant une meilleure adhérence des revêtements.
- Précision accrue : En éliminant les excroissances métalliques, l’ébavurage permet de respecter les tolérances dimensionnelles requises, ce qui est crucial pour les pièces destinées à être assemblées avec d’autres composants.
- Réduction de l’usure des outils : Les bavures sur les pièces peuvent causer une usure prématurée des outils et des équipements lors des étapes suivantes de production. L’ébavurage contribue à prolonger la durée de vie des équipements en éliminant ces défauts.
Applications des Machines d’Ébavurage
Les machines d’ébavurage sont utilisées dans une grande variété de secteurs industriels où la qualité et la précision des pièces sont essentielles :
- Automobile : Dans l’industrie automobile, les pièces de moteur, les engrenages et les éléments structurels en métal doivent être ébavurés pour garantir un assemblage précis et éviter les risques de défaillance. L’ébavurage mécanique et thermique est largement utilisé pour traiter ces pièces avant leur intégration dans les véhicules.
- Aéronautique : Les composants d’avion, comme les structures en aluminium et les pièces de moteur, doivent être parfaitement lisses pour minimiser la résistance à l’air et garantir des performances optimales. Les machines d’ébavurage sont utilisées pour éliminer les irrégularités et préparer ces pièces à des traitements de surface supplémentaires.
- Électronique : Dans la fabrication des boîtiers et des circuits imprimés, l’ébavurage est crucial pour éviter les courts-circuits et les défauts de connexion. Les ébavureuses CNC sont souvent utilisées pour garantir la précision des petites pièces électroniques.
- Métallurgie : L’ébavurage des tôles et des barres métalliques est nécessaire pour garantir une manipulation sûre et une qualité de surface optimale. Les machines d’ébavurage à brosses rotatives ou vibrantes sont utilisées dans ce secteur pour traiter de grandes quantités de matériaux.
Innovations Technologiques dans les Machines d’Ébavurage
Les technologies d’ébavurage ont évolué pour répondre aux exigences croissantes de l’industrie moderne :
- Ébavurage automatisé : Les machines d’ébavurage modernes sont souvent entièrement automatisées, permettant de traiter de grandes quantités de pièces sans intervention humaine. Cela améliore la productivité et réduit les erreurs liées à la manipulation manuelle.
- Contrôle numérique (CNC) : Les ébavureuses CNC permettent de programmer avec précision les étapes d’ébavurage, garantissant une qualité constante sur chaque pièce et une adaptabilité à des pièces de formes complexes.
- Techniques d’ébavurage écologiques : Des technologies plus respectueuses de l’environnement, comme l’ébavurage à haute pression d’eau ou l’utilisation de produits chimiques non toxiques, sont de plus en plus adoptées pour réduire l’impact environnemental des procédés d’ébavurage.
- Ébavurage intelligent : Les machines équipées de capteurs intelligents permettent de surveiller en temps réel l’état des pièces et d’ajuster automatiquement les paramètres d’ébavurage pour maintenir une qualité optimale.
Machine de Ponçage
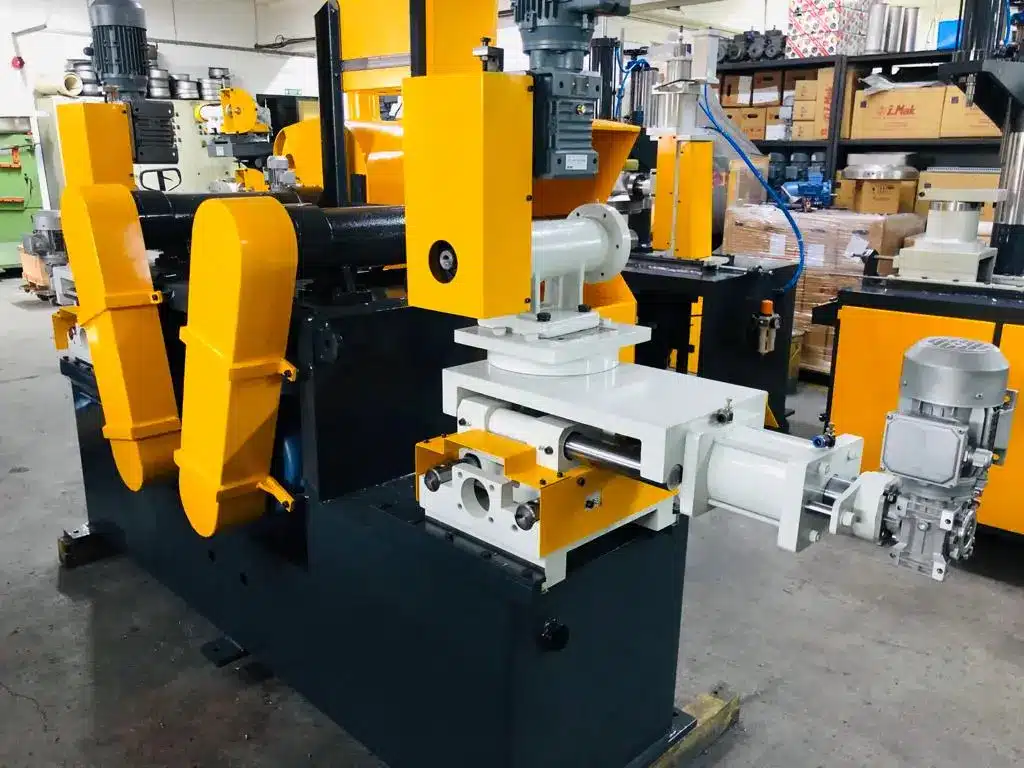
La machine de ponçage est un équipement industriel utilisé pour lisser et préparer les surfaces de divers matériaux, notamment le métal, le bois, le plastique et les composites. Le ponçage est une étape essentielle pour éliminer les imperfections, les rugosités et les traces de fabrication avant d’appliquer des finitions comme la peinture, le vernis ou le polissage. Les machines de ponçage sont largement utilisées dans de nombreux secteurs, tels que la métallurgie, l’automobile, l’aéronautique, l’ébénisterie et la construction.
Fonctionnement des Machines de Ponçage
Les machines de ponçage fonctionnent en utilisant des bandes abrasives ou des disques rotatifs pour frotter la surface de la pièce, réduisant ainsi les irrégularités et créant une surface lisse et uniforme. Le choix du type d’abrasif, de la taille des grains et de la méthode de ponçage dépend de la nature du matériau et du niveau de finition souhaité.
- Ponçage à bande : Ce type de machine utilise une bande abrasive en mouvement continu qui ponce la pièce au fur et à mesure qu’elle passe à travers la machine. Il est couramment utilisé pour des surfaces planes ou de grandes dimensions, comme des tôles métalliques ou des panneaux de bois.
- Ponçage orbital : Les machines à ponçage orbitales utilisent des disques abrasifs rotatifs qui effectuent des mouvements circulaires et oscillants pour éliminer les imperfections de la surface. Elles sont idéales pour des surfaces courbes ou complexes.
- Ponçage à tambour : Ce procédé utilise un tambour rotatif recouvert d’un abrasif pour poncer les pièces de manière uniforme. Il est souvent utilisé dans la métallurgie pour polir les bords des pièces après découpe ou emboutissage.
Types de Machines de Ponçage
Il existe plusieurs types de machines de ponçage adaptées à des applications spécifiques :
- Ponceuses à bande industrielle : Ces machines utilisent une large bande abrasive en mouvement pour poncer des plaques de métal, des panneaux de bois ou des pièces volumineuses. Elles sont idéales pour des travaux nécessitant un enlèvement rapide de matière sur des surfaces planes.
- Ponceuses orbitales : Elles sont principalement utilisées pour des finitions plus fines sur des surfaces complexes, grâce à leur mouvement rotatif qui réduit les risques de rayures visibles.
- Ponceuses à disque : Ces machines utilisent un disque abrasif rotatif pour poncer des bords ou des surfaces plus petites. Elles sont souvent utilisées pour des travaux de précision ou pour traiter des zones difficiles d’accès.
- Ponceuses portatives : Ces machines manuelles sont utilisées pour des travaux de retouche ou des petites pièces. Leur légèreté et leur maniabilité en font un outil polyvalent pour une variété de matériaux.
Avantages des Machines de Ponçage
Les machines de ponçage apportent de nombreux avantages dans les processus de fabrication industrielle :
- Amélioration de la qualité de surface : Le ponçage élimine les défauts de surface, comme les rayures, les bavures ou les irrégularités, garantissant ainsi une finition lisse et uniforme prête pour des étapes de finition ultérieures, comme le polissage ou la peinture.
- Préparation avant traitement : Le ponçage est souvent utilisé avant l’application de traitements de surface, tels que le revêtement en poudre ou la peinture, pour assurer une bonne adhérence et une finition de haute qualité.
- Flexibilité d’utilisation : Les machines de ponçage peuvent être utilisées pour une large gamme de matériaux et de formes, offrant ainsi une grande polyvalence dans les processus de fabrication.
- Rapidité et efficacité : Le ponçage mécanique permet de traiter de grandes surfaces en un minimum de temps, accélérant ainsi le processus de production tout en garantissant des résultats cohérents.
Applications des Machines de Ponçage
Les machines de ponçage sont utilisées dans de nombreux secteurs industriels pour améliorer la qualité de surface des pièces et préparer les matériaux pour d’autres traitements :
- Automobile : Le ponçage est essentiel pour la préparation des carrosseries avant la peinture. Les ponceuses à bande sont largement utilisées pour lisser les surfaces métalliques, tandis que les ponceuses orbitales servent à traiter les zones courbes et les joints.
- Métallurgie : Dans la fabrication de pièces métalliques, le ponçage est utilisé pour éliminer les bavures après découpe ou formage, ainsi que pour polir les surfaces avant l’application de revêtements ou de traitements thermiques.
- Aéronautique : Le ponçage est couramment utilisé pour lisser les pièces d’avion en aluminium et en composites avant le montage. Les ponceuses orbitales et à bande sont largement employées pour garantir une finition impeccable et minimiser la traînée aérodynamique.
- Ébénisterie et mobilier : Dans la fabrication de meubles, le ponçage est essentiel pour créer des surfaces lisses avant l’application de vernis ou de peinture. Les ponceuses à bande et orbitales sont utilisées pour traiter les panneaux en bois et les surfaces complexes.
Innovations Technologiques dans les Machines de Ponçage
Les machines de ponçage ont bénéficié de plusieurs innovations récentes qui ont amélioré leur efficacité et leur précision :
- Contrôle numérique (CNC) : Les machines de ponçage CNC permettent de programmer chaque étape du processus, garantissant ainsi une uniformité parfaite et une finition précise, même pour des pièces complexes ou des surfaces de grande dimension.
- Systèmes de surveillance intelligents : Les machines modernes sont équipées de capteurs qui surveillent la pression appliquée, la vitesse de rotation et la température des surfaces poncées, permettant des ajustements en temps réel pour assurer une qualité de finition constante.
- Papiers abrasifs haute performance : Les machines utilisent désormais des abrasifs plus durables et plus efficaces, tels que les abrasifs en céramique ou les composites, qui offrent une meilleure coupe tout en réduisant la chaleur générée lors du ponçage.
- Ponçage sans poussière : De nombreuses machines de ponçage sont maintenant équipées de systèmes d’extraction de poussière, réduisant les particules en suspension dans l’air et améliorant la sécurité des opérateurs tout en maintenant un environnement de travail plus propre.
Machine de Polissage
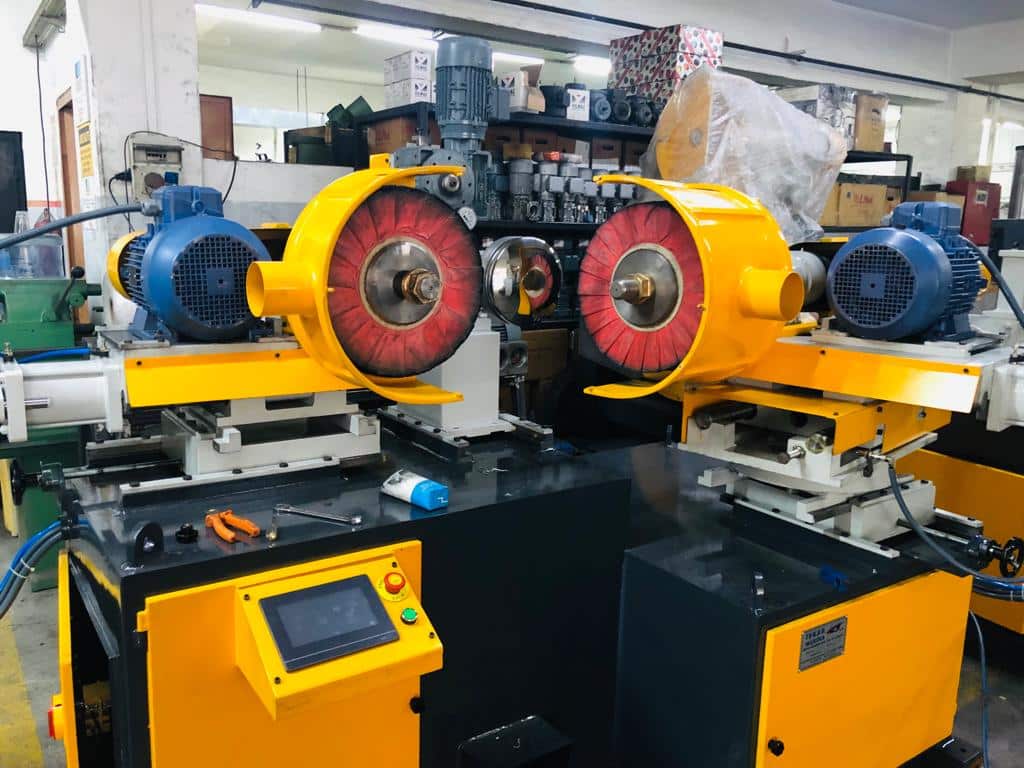
La machine de polissage est un équipement industriel utilisé pour obtenir des surfaces lisses, brillantes et esthétiquement parfaites sur des pièces métalliques, en plastique ou en verre. Le polissage est une étape cruciale dans de nombreuses industries, notamment l’automobile, l’aéronautique, la bijouterie, et la métallurgie, car il permet d’améliorer l’apparence des pièces tout en augmentant leur résistance à la corrosion, à l’usure et à la friction. Les machines de polissage sont conçues pour éliminer les imperfections superficielles laissées par les processus de fabrication antérieurs, comme le ponçage ou l’usinage, et pour préparer les pièces à des traitements de finition comme le chromage ou la peinture.
Fonctionnement des Machines de Polissage
Les machines de polissage fonctionnent en frottant la surface d’une pièce avec des disques ou des roues de polissage enduits de pâtes abrasives. Ces disques rotatifs lissent la surface de la pièce en éliminant les micro-rayures et les aspérités, créant ainsi une finition brillante et homogène. Le choix de l’abrasif et de la vitesse de rotation dépend du matériau de la pièce et du niveau de brillance souhaité.
- Polissage rotatif : Utilise des disques ou des brosses rotatives pour polir la pièce. Ce type de polissage est idéal pour des surfaces planes ou légèrement courbes.
- Polissage vibratoire : La pièce est placée dans un récipient contenant des abrasifs, qui sont agités par des vibrations pour polir uniformément les surfaces, particulièrement utile pour les petites pièces en vrac.
- Polissage miroir : Utilisé pour obtenir une finition extrêmement brillante, ce procédé combine des disques en tissu ou en feutre et des pâtes abrasives très fines.
Types de Machines de Polissage
Il existe plusieurs types de machines de polissage adaptées aux besoins spécifiques des industries :
- Machines à polir rotatives : Utilisées pour polir de grandes surfaces ou des pièces volumineuses, ces machines fonctionnent à l’aide de disques rotatifs abrasifs pour obtenir une finition lisse et brillante. Elles sont couramment utilisées dans la métallurgie et l’automobile.
- Polisseuses vibratoires : Employées pour le polissage de petites pièces en vrac, ces machines utilisent des vibrations pour faire circuler les abrasifs autour des pièces, assurant un polissage uniforme.
- Polisseuses manuelles : Ces machines sont utilisées pour des opérations de précision ou de retouche sur des pièces délicates, comme dans la bijouterie ou l’horlogerie, où le contrôle de l’opérateur est essentiel.
- Polisseuses CNC : Des machines à polir programmées par commande numérique (CNC) qui permettent de polir des pièces complexes avec une précision et une répétabilité parfaites, souvent utilisées dans l’aéronautique et l’automobile.
Avantages des Machines de Polissage
Les machines de polissage offrent de nombreux avantages pour l’amélioration de la qualité de surface des pièces industrielles :
- Amélioration de l’esthétique : Le polissage donne aux surfaces métalliques une brillance et un éclat esthétique, ce qui est essentiel pour des industries comme la bijouterie, l’automobile ou la décoration intérieure.
- Résistance accrue à la corrosion : En éliminant les microfissures et les défauts de surface, le polissage rend les pièces plus résistantes à la corrosion et à l’oxydation, prolongeant ainsi leur durée de vie.
- Réduction des frottements : Le polissage réduit la friction entre les surfaces en contact, ce qui améliore l’efficacité des pièces mobiles et diminue l’usure dans les moteurs, les roulements et les engrenages.
- Préparation des surfaces : Le polissage est souvent utilisé avant l’application de traitements de surface, comme le chromage ou la peinture, pour garantir une adhérence optimale et une finition lisse.
Applications des Machines de Polissage
Les machines de polissage sont utilisées dans divers secteurs industriels pour améliorer la qualité et l’apparence des pièces :
- Automobile : Dans l’industrie automobile, les machines de polissage sont utilisées pour donner aux carrosseries, aux jantes et aux pièces chromées une finition brillante et esthétique. Elles sont également essentielles pour polir les pièces mécaniques internes, telles que les pistons et les vilebrequins, afin de réduire les frottements et d’améliorer les performances du moteur.
- Aéronautique : Le polissage des pièces en aluminium et en titane, telles que les composants de moteur et les éléments de structure, est crucial pour améliorer leur résistance à la corrosion et réduire la traînée aérodynamique.
- Bijouterie et horlogerie : Le polissage est une étape clé dans la finition des bijoux en or, argent et autres métaux précieux, ainsi que dans la fabrication des montres. Il permet d’obtenir des surfaces sans défauts, offrant une brillance et un éclat exceptionnels.
- Équipements médicaux : Les instruments chirurgicaux et les implants en acier inoxydable ou en titane doivent être parfaitement polis pour garantir une utilisation sûre et hygiénique, tout en minimisant les risques d’infection.
Innovations Technologiques dans les Machines de Polissage
Les machines de polissage ont évolué grâce à l’introduction de nouvelles technologies, qui améliorent leur précision et leur efficacité :
- Polissage robotisé : Les robots de polissage automatisent totalement le processus et permettent de traiter de grandes pièces complexes avec une précision constante, tout en réduisant les temps de production.
- Polissage sans pâte abrasive : De nouvelles technologies utilisent des systèmes de polissage sans pâte, réduisant ainsi les déchets et facilitant le nettoyage des pièces après le polissage.
- Polissage écologique : L’utilisation de matériaux abrasifs non toxiques et de techniques de polissage respectueuses de l’environnement réduit l’impact écologique tout en garantissant une finition de haute qualité.
- Systèmes de contrôle numérique (CNC) : Les polisseuses CNC permettent de programmer chaque étape du processus de polissage avec une extrême précision, garantissant une finition uniforme sur des pièces de forme complexe ou des surfaces irrégulières.
Machine de Ponçage de Cordons de Soudure
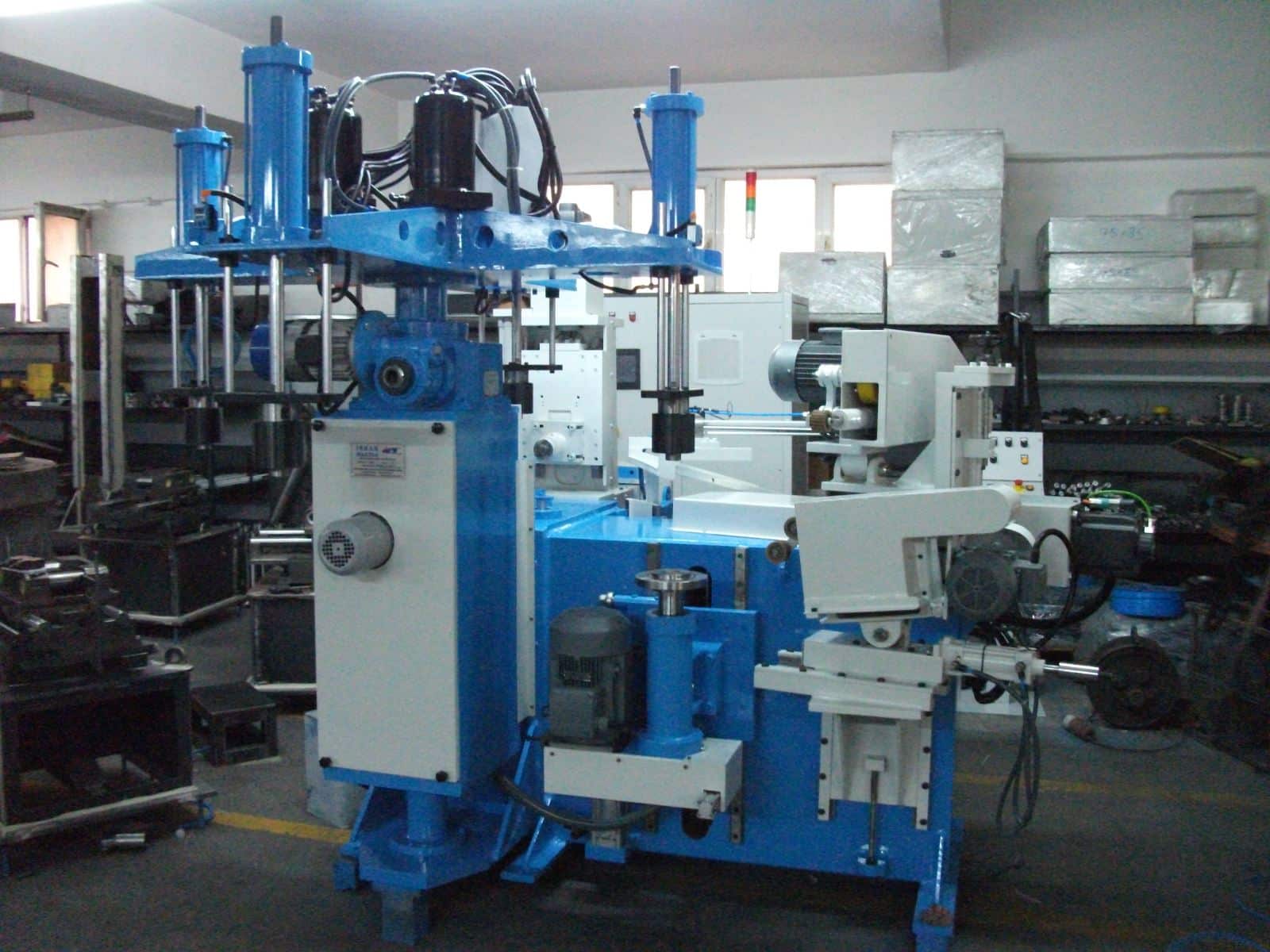
La machine de ponçage de cordons de soudure est un équipement industriel utilisé pour lisser et éliminer les excédents de soudure après l’assemblage de pièces métalliques. Le ponçage des cordons de soudure est essentiel pour obtenir une finition lisse et propre, et pour préparer les surfaces métalliques avant les traitements de surface ou la peinture. Ce processus est couramment utilisé dans la fabrication de structures métalliques, de réservoirs, de châssis automobiles, et dans de nombreuses autres industries où la qualité des soudures doit être optimale pour des raisons esthétiques, de sécurité et de performance.
Fonctionnement des Machines de Ponçage de Cordons de Soudure
Les machines de ponçage de cordons de soudure fonctionnent en utilisant des disques abrasifs, des bandes ou des meules pour enlever l’excédent de métal des soudures et lisser les surfaces environnantes. Le ponçage permet d’obtenir un aspect homogène tout en garantissant que les soudures sont solides et exemptes de défauts.
Le processus de ponçage de soudure peut inclure les étapes suivantes :
- Élimination des excédents : Les excédents de soudure sont retirés avec des meules ou des disques abrasifs de gros grains pour enlever rapidement la matière et lisser le cordon de soudure.
- Ponçage de finition : Une fois les excédents enlevés, des abrasifs plus fins sont utilisés pour obtenir une finition plus lisse et uniforme, surtout si la pièce est destinée à être peinte ou polie par la suite.
- Finition miroir (facultatif) : Dans certains cas, comme pour des soudures visibles sur des pièces décoratives, la finition peut être poussée jusqu’à un niveau miroir, en utilisant des disques en feutre et des pâtes de polissage.
Types de Machines de Ponçage de Cordons de Soudure
Il existe plusieurs types de machines de ponçage conçues pour traiter les cordons de soudure :
- Ponceuses à bande : Utilisées pour poncer des surfaces plates et étendues, elles permettent de traiter rapidement les soudures sur de grandes pièces métalliques. La bande abrasive permet d’enlever l’excédent de soudure et de lisser les surfaces environnantes.
- Ponceuses à disque : Équipées de disques abrasifs rotatifs, ces machines sont idéales pour poncer les soudures dans des zones plus restreintes ou courbes, telles que les tuyaux ou les coins.
- Meuleuses d’angle : Très couramment utilisées dans les ateliers de soudure, ces machines portatives permettent d’ébavurer et de lisser les cordons de soudure sur des structures complexes et des assemblages difficiles d’accès.
- Ponceuses orbitales : Ces machines sont principalement utilisées pour la finition après l’enlèvement de l’excédent de soudure. Elles offrent un mouvement orbital qui garantit un ponçage uniforme, sans risque de rayures profondes.
Avantages des Machines de Ponçage de Cordons de Soudure
Les machines de ponçage de cordons de soudure offrent plusieurs avantages pour améliorer la qualité des soudures et la finition des pièces métalliques :
- Amélioration de l’apparence : Le ponçage des soudures permet d’obtenir une surface lisse et homogène, essentielle pour des pièces visibles ou des structures décoratives où l’esthétique est cruciale.
- Renforcement des soudures : En éliminant les excédents et les imperfections, le ponçage réduit les points faibles dans les soudures, améliorant ainsi leur solidité et leur résistance à la fatigue.
- Préparation pour la peinture ou le revêtement : Une surface lisse est essentielle pour garantir une bonne adhérence des peintures ou des revêtements protecteurs, en particulier dans des environnements corrosifs ou soumis à des conditions sévères.
- Sécurité accrue : Les soudures brutes peuvent avoir des arêtes vives ou des points d’accrochage qui présentent des risques pour la sécurité. Le ponçage élimine ces dangers et rend la pièce plus sûre à manipuler.
Applications des Machines de Ponçage de Cordons de Soudure
Les machines de ponçage de cordons de soudure sont utilisées dans de nombreux secteurs industriels où les soudures doivent être solides, sécurisées et esthétiquement acceptables :
- Construction métallique : Dans les structures en acier et les bâtiments, les cordons de soudure doivent être lissés pour garantir la résistance et l’intégrité des assemblages, ainsi que pour des raisons esthétiques.
- Automobile : Le ponçage des soudures est essentiel dans la fabrication des châssis et des composants de carrosserie, car une finition lisse améliore l’apparence et la durabilité des pièces avant la peinture ou le revêtement.
- Réservoirs et conduites : Dans la fabrication de réservoirs, de cuves et de pipelines, le ponçage des soudures garantit l’absence de défauts qui pourraient provoquer des fuites ou des points de faiblesse sous pression.
- Aéronautique : Les pièces d’avion, en particulier celles en aluminium et en acier inoxydable, nécessitent un ponçage des soudures pour garantir des performances optimales et réduire la traînée aérodynamique.
Innovations Technologiques dans les Machines de Ponçage de Cordons de Soudure
Les technologies de ponçage ont évolué avec l’introduction de nouvelles innovations qui améliorent l’efficacité, la précision et la sécurité :
- Contrôle numérique (CNC) : Les machines de ponçage CNC permettent de programmer avec précision les mouvements de ponçage, garantissant une finition uniforme et une réduction des erreurs humaines.
- Ponçage robotisé : Les robots de ponçage automatisent complètement le processus pour des applications de soudure en série, augmentant ainsi la productivité tout en réduisant les coûts de main-d’œuvre.
- Technologies de réduction de la poussière : Les machines modernes sont souvent équipées de systèmes d’aspiration de poussière pour améliorer les conditions de travail et minimiser l’exposition des opérateurs aux particules métalliques.
- Disques abrasifs de nouvelle génération : Les matériaux abrasifs, comme les céramiques ou les composites, offrent une meilleure durabilité et une efficacité accrue, permettant d’effectuer le ponçage plus rapidement tout en générant moins de chaleur.
EMS Machines de Formage
Le formage du métal est un processus consistant à façonner le métal dans la forme et la taille souhaitées à l’aide de diverses techniques. Il s’agit d’un processus crucial dans l’industrie manufacturière car il permet la production de différents produits tels que des pièces automobiles, des composants d’avion, des appareils électroménagers et bien d’autres encore.
Le processus de formage du métal consiste à appliquer une force sur le métal pour changer sa forme sans enlever aucune matière. La force peut être appliquée par diverses méthodes telles que le forgeage, le laminage, l’extrusion, l’étirage et l’estampage. Chaque méthode a ses propres avantages et inconvénients, et le choix de la méthode dépend du matériau formé et de la forme souhaitée.
Le forgeage est l’une des techniques de formage des métaux les plus anciennes. Il s’agit de chauffer le métal à haute température, puis d’appliquer une force de compression à l’aide d’un marteau ou d’une presse pour donner au métal la forme souhaitée. Le forgeage est couramment utilisé pour produire de grandes pièces telles que des engrenages, des essieux et des bielles.
Le laminage est une autre technique de formage du métal qui consiste à faire passer le métal à travers une paire de rouleaux pour réduire son épaisseur ou modifier sa forme. Les rouleaux peuvent être lisses ou texturés selon la finition souhaitée. Le laminage est couramment utilisé pour produire des tôles plates, des plaques et des barres.
L’extrusion est une technique de formage du métal qui consiste à pousser une billette ou une tige métallique à travers une matrice pour créer une forme spécifique. L’extrusion peut être utilisée pour produire des formes complexes telles que des tubes, des canaux et des angles.
L’emboutissage est une technique de formage des métaux utilisée pour réaliser des pièces de forme cylindrique, comme des tubes ou des tuyaux. Le processus consiste à tirer le métal à travers une matrice pour réduire son diamètre et augmenter sa longueur. Le tréfilage est couramment utilisé dans la production de fils, de tiges et de tubes.
L’emboutissage est une technique de formage du métal qui consiste à couper, poinçonner ou plier le métal dans une forme spécifique à l’aide d’une matrice. Le processus peut être utilisé pour produire des pièces avec une grande précision et répétabilité. L’estampage est couramment utilisé dans la production de pièces automobiles, d’appareils électroménagers et d’appareils électroniques.
En plus de ces techniques, il existe de nombreuses autres méthodes de formage des métaux telles que le filage, l’emboutissage profond et l’hydroformage. Chaque méthode a ses propres avantages et inconvénients, et le choix de la méthode dépend des exigences spécifiques du produit fabriqué.
Le formage des métaux est un processus complexe qui nécessite un haut niveau de compétence et d’expertise. Le succès du processus dépend de nombreux facteurs tels que le type de matériau formé, l’équipement utilisé et l’expérience de l’opérateur. En comprenant les différentes techniques de formage des métaux et en choisissant la méthode adaptée au travail, les fabricants peuvent produire des pièces de haute qualité qui répondent aux besoins spécifiques de leurs clients.