
Presses Hydrauliques: Les presses hydrauliques sont des équipements indispensables dans le domaine de la fabrication industrielle. Elles permettent de transformer, de déformer et de manipuler des matériaux, en particulier des métaux, à l’aide de la puissance hydraulique. Ce mécanisme repose sur les principes de la dynamique des fluides et de la mécanique des solides, rendant ces machines à la fois efficaces et polyvalentes.
Principes de Fonctionnement
Le fonctionnement d’une presse hydraulique repose sur le principe de Pascal, qui stipule que dans un fluide incompressible, une pression appliquée se transmet de manière uniforme à toutes les parties du fluide. Cela signifie qu’une petite force appliquée sur un petit piston peut être amplifiée pour soulever ou déplacer des charges beaucoup plus lourdes sur un piston plus grand.
Une presse hydraulique se compose principalement des éléments suivants :
- Cylindre hydraulique : Contient le fluide hydraulique qui transmet la pression.
- Piston : Se déplace à l’intérieur du cylindre pour exercer une force sur la pièce à travailler.
- Pompe hydraulique : Injecte le fluide dans le cylindre pour provoquer le mouvement du piston.
- Vannes : Régulent le flux de fluide pour contrôler le mouvement du piston.
Applications des Presses Hydrauliques
Les presses hydrauliques sont utilisées dans divers domaines, notamment :
- Emboutissage : Ce processus consiste à former des pièces métalliques à partir de tôles. Les presses hydrauliques appliquent une force qui déforme la tôle, créant des formes complexes.
- Pliage : Les presses sont utilisées pour plier des tôles métalliques, ce qui est essentiel dans la fabrication de structures en métal et de composants pour l’industrie automobile.
- Soudage : Les presses peuvent également être utilisées pour le soudage à point, où elles exercent une pression sur les pièces métalliques à assembler.
- Découpage : Elles sont employées pour découper des formes spécifiques dans des tôles, facilitant la création de pièces pour diverses applications industrielles.
Types de Presses Hydrauliques
Il existe plusieurs types de presses hydrauliques, chacune adaptée à des besoins spécifiques :
- Presses à cadre : Idéales pour des opérations de pressage général, elles sont souvent utilisées dans les ateliers de mécanique.
- Presses à plat : Conçues pour le formage de tôles, elles offrent une large surface de travail, permettant de traiter de grandes pièces.
- Presses à cliquet : Ces presses sont équipées d’un mécanisme qui permet un cycle de pressage automatique, ce qui améliore l’efficacité de la production.
- Presses multi-étages : Utilisées pour les opérations complexes, elles permettent de réaliser plusieurs opérations de formage en une seule séquence, réduisant ainsi le temps de production.
Avantages des Presses Hydrauliques
Les presses hydrauliques offrent plusieurs avantages notables :
- Force Élevée : Elles peuvent générer des forces considérables, rendant possible le travail de matériaux très résistants.
- Précision et Contrôle : Grâce à la nature du système hydraulique, il est possible de contrôler avec précision la force appliquée, garantissant des résultats uniformes et de haute qualité.
- Polyvalence : Elles peuvent être adaptées à une grande variété d’applications, de la production de pièces simples à des opérations plus complexes.
- Efficacité Energétique : Les systèmes hydrauliques modernes sont conçus pour être écoénergétiques, minimisant la consommation d’énergie tout en maximisant la performance.
Entretien des Presses Hydrauliques
L’entretien régulier des presses hydrauliques est crucial pour garantir leur bon fonctionnement et leur longévité. Cela comprend :
- Vérification des Niveaux de Fluide : Un niveau d’huile approprié est nécessaire pour éviter la surchauffe et garantir la sécurité.
- Inspection des Joints et des Tuyaux : Les fuites peuvent entraîner des pertes de pression et affecter le fonctionnement de la presse.
- Nettoyage : Maintenir la machine propre est essentiel pour éviter l’accumulation de débris qui pourrait affecter son fonctionnement.
- Calibration et Réglages : Les machines doivent être régulièrement calibrées pour garantir une précision optimale.
Conclusion
Les presses hydrauliques représentent un élément fondamental de l’industrie moderne. Leur capacité à exercer une force considérable avec précision et leur polyvalence en font des outils incontournables dans divers secteurs. En investissant dans des presses hydrauliques de qualité et en s’assurant de leur entretien régulier, les entreprises peuvent améliorer leur efficacité et la qualité de leurs produits.
Presses Hydrauliques

Les presses hydrauliques sont des machines industrielles essentielles qui jouent un rôle clé dans divers secteurs de fabrication. Leur conception repose sur des principes physiques fondamentaux, et elles sont utilisées pour une multitude d’applications, allant de l’emboutissage à la fabrication de pièces complexes. Grâce à leur capacité à exercer d’énormes forces sur des matériaux variés, elles ont révolutionné les processus de production et continuent d’être au cœur de l’innovation industrielle.
Principes de Fonctionnement
Le fonctionnement d’une presse hydraulique repose sur le principe de Pascal, qui énonce que la pression appliquée à un fluide incompressible dans un espace clos se transmet uniformément dans toutes les directions. Cela signifie qu’une force relativement faible appliquée sur un petit piston peut être amplifiée pour déplacer ou soulever des objets beaucoup plus lourds sur un piston de plus grande taille. Ce mécanisme de multiplication de la force est fondamental pour le fonctionnement des presses hydrauliques.
Composants Principaux
Les presses hydrauliques se composent de plusieurs éléments clés :
- Cylindre Hydraulique : C’est le cœur de la presse, où se produit la transformation de l’énergie hydraulique en énergie mécanique. Il contient le fluide hydraulique qui transmet la pression.
- Piston : Il se déplace à l’intérieur du cylindre et exerce une force sur la pièce à travailler. La taille du piston détermine la capacité de charge de la presse.
- Pompe Hydraulique : Elle est responsable de l’injection du fluide dans le cylindre. La pompe peut être manuelle ou électrique, selon la conception de la machine.
- Vannes de Contrôle : Ces vannes régulent le flux de fluide, permettant un contrôle précis du mouvement du piston et de la force appliquée.
- Réservoir de Fluide : Un réservoir est nécessaire pour stocker le fluide hydraulique, qui est généralement de l’huile spéciale conçue pour résister à la chaleur et à la pression.
Applications des Presses Hydrauliques
Les presses hydrauliques ont des applications variées dans de nombreux secteurs :
- Emboutissage : Dans l’industrie automobile, l’emboutissage est crucial pour produire des pièces de carrosserie. Les presses hydrauliques peuvent former des panneaux de porte, des coques de voiture, et d’autres composants complexes à partir de tôles métalliques. Ce processus est essentiel pour garantir des tolérances précises et des formes complexes.
- Pliage : Elles sont largement utilisées pour plier des tôles métalliques. Les presses hydrauliques à plier permettent de créer des angles et des formes spécifiques, essentielles pour la fabrication de structures en métal.
- Soudage : Dans le processus de soudage, les presses hydrauliques peuvent exercer une pression sur les pièces à assembler, garantissant un contact optimal et une soudure de qualité. Cela est particulièrement important dans les applications où la résistance et la durabilité des joints sont critiques.
- Découpage et Formage : Les presses peuvent également être utilisées pour découper des formes spécifiques dans des tôles. Grâce à la force hydraulique, elles peuvent produire des pièces avec une grande précision et un minimum de déchets.
- Forgeage : Le forgeage à chaud utilise des presses hydrauliques pour former des pièces en métal à haute température. Cela permet de modifier les propriétés mécaniques du métal tout en créant des formes complexes.
Types de Presses Hydrauliques
Il existe différents types de presses hydrauliques, chacune adaptée à des besoins spécifiques :
- Presses à Cadre : Ces presses sont souvent utilisées pour des opérations de pressage général. Leur structure ouverte permet d’accéder facilement à la zone de travail, ce qui est pratique pour des opérations variées.
- Presses à Plat : Conçues pour le formage de tôles, ces presses offrent une large surface de travail, idéale pour traiter de grandes pièces ou effectuer des opérations de formage à grande échelle.
- Presses à Cliquet : Équipées d’un mécanisme de cliquet, ces presses permettent un cycle de pressage automatique. Cela améliore considérablement l’efficacité de la production en réduisant les temps d’arrêt.
- Presses Multi-Étages : Ces presses complexes permettent de réaliser plusieurs opérations de formage en une seule séquence. Elles sont particulièrement utiles pour des applications où le temps de production doit être minimisé.
- Presses de Forge : Spécialisées pour le forgeage, elles sont utilisées pour travailler des métaux à haute température, permettant de créer des pièces avec des propriétés mécaniques optimisées.
Avantages des Presses Hydrauliques
Les presses hydrauliques présentent plusieurs avantages significatifs :
- Force Élevée : Elles peuvent générer des forces considérables, rendant possible le travail de matériaux très résistants. Cette capacité est cruciale pour les applications où une force élevée est nécessaire pour former ou déformer des pièces.
- Précision et Contrôle : Grâce à la nature du système hydraulique, il est possible de contrôler avec précision la force appliquée, garantissant des résultats uniformes et de haute qualité. Les vannes de contrôle permettent d’ajuster la pression selon les besoins spécifiques de chaque opération.
- Polyvalence : Les presses hydrauliques peuvent être adaptées à une grande variété d’applications. Que ce soit pour l’emboutissage, le pliage ou le découpage, elles peuvent traiter différents types de matériaux et de formes.
- Efficacité Énergétique : Les systèmes hydrauliques modernes sont conçus pour être écoénergétiques, minimisant la consommation d’énergie tout en maximisant la performance. Cela en fait une option attrayante pour les entreprises soucieuses de l’environnement.
- Durabilité : Les presses hydrauliques sont généralement conçues pour durer, avec des composants robustes capables de résister à des conditions de fonctionnement exigeantes.
Entretien des Presses Hydrauliques
L’entretien régulier des presses hydrauliques est crucial pour garantir leur bon fonctionnement et leur longévité. Cela comprend :
- Vérification des Niveaux de Fluide : Un niveau d’huile approprié est nécessaire pour éviter la surchauffe et garantir la sécurité de l’opération.
- Inspection des Joints et des Tuyaux : Les fuites peuvent entraîner des pertes de pression et affecter le fonctionnement de la presse. Une inspection régulière permet de détecter et de résoudre ces problèmes rapidement.
- Nettoyage : Maintenir la machine propre est essentiel pour éviter l’accumulation de débris qui pourrait affecter son fonctionnement. Un nettoyage régulier aide également à prolonger la durée de vie des composants.
- Calibration et Réglages : Les machines doivent être régulièrement calibrées pour garantir une précision optimale dans le formage des pièces. Cela implique des réglages des vannes et des composants hydrauliques.
- Formation des Opérateurs : Assurer que les opérateurs sont correctement formés à l’utilisation des presses hydrauliques est essentiel pour minimiser les erreurs et garantir un environnement de travail sûr.
Conclusion
Les presses hydrauliques représentent un élément fondamental de l’industrie moderne. Leur capacité à exercer une force considérable avec précision et leur polyvalence en font des outils incontournables dans divers secteurs. Que ce soit dans l’industrie automobile, l’aéronautique, ou l’électroménager, ces machines continuent d’évoluer et de s’améliorer, intégrant de nouvelles technologies pour répondre aux exigences croissantes de l’innovation industrielle. En investissant dans des presses hydrauliques de qualité et en s’assurant de leur entretien régulier, les entreprises peuvent améliorer leur efficacité, la qualité de leurs produits, et leur compétitivité sur le marché.
Emboutissage

L’emboutissage est un procédé de fabrication qui consiste à former des pièces métalliques à partir de tôles en utilisant des presses hydrauliques. Ce processus est largement employé dans des secteurs tels que l’industrie automobile, l’aéronautique, et l’électroménager, où la précision et l’efficacité sont primordiales. Grâce à son efficacité et à sa capacité à produire des pièces complexes, l’emboutissage est devenu un pilier de la fabrication moderne.
Processus d’Emboutissage
L’emboutissage se déroule en plusieurs étapes clés :
- Préparation de la Tôle : La première étape consiste à découper la tôle métallique aux dimensions nécessaires. Cette étape peut impliquer des techniques de découpage au laser ou à l’eau, assurant des bords nets et précis.
- Insertion dans la Presse : La tôle découpée est ensuite placée dans la presse hydraulique. Le choix de la presse et de l’outil de formage est crucial, car cela déterminera la forme finale de la pièce.
- Application de la Force : La presse applique une force sur la tôle à l’aide d’un outil de formage. Ce processus peut se faire à froid, à température ambiante, ou à chaud, selon le type de métal et la complexité de la forme à réaliser.
- Finition : Après l’emboutissage, les pièces peuvent nécessiter des opérations supplémentaires telles que le découpage, le pliage, ou le traitement de surface pour améliorer l’apparence et la résistance des pièces.
Applications de l’Emboutissage
L’emboutissage est utilisé dans une grande variété d’applications :
- Industrie Automobile : L’une des applications les plus courantes de l’emboutissage est la fabrication de composants automobiles, tels que les panneaux de carrosserie, les supports de moteur, et les structures internes des véhicules. Ces pièces doivent être précises et robustes pour garantir la sécurité et la performance.
- Appareils Électroménagers : L’emboutissage est également utilisé pour produire des châssis et des composants internes pour des appareils tels que réfrigérateurs, lave-linge, et cuisinières. Les pièces embouties contribuent à la solidité et à la fonctionnalité des appareils.
- Équipements Électriques : De nombreux équipements électriques contiennent des pièces embouties, notamment des boîtiers, des supports, et des connecteurs. L’emboutissage permet de produire ces éléments avec des tolérances serrées et des formes spécifiques.
- Industrie Aéronautique : Dans l’aéronautique, l’emboutissage est utilisé pour créer des pièces légères et résistantes, essentielles pour la performance des aéronefs. Les techniques de formage avancées permettent de répondre aux exigences strictes de sécurité et de performance.
Types d’Emboutissage
L’emboutissage peut être classé en plusieurs types, chacun ayant ses spécificités :
- Emboutissage à Froid : Réalisé à température ambiante, ce procédé convient aux matériaux ductiles et permet de conserver les propriétés mécaniques du métal. Il est souvent utilisé pour des pièces nécessitant une grande précision.
- Emboutissage à Chaud : Impliquant un préchauffage de la tôle, ce type d’emboutissage est utilisé pour des matériaux plus difficiles à travailler, augmentant la ductilité du métal. Cela permet de réaliser des formes plus complexes sans risquer la rupture du matériau.
- Emboutissage Progressif : Cette technique permet de réaliser plusieurs étapes de formage dans une seule opération. Les outils sont configurés pour effectuer différents processus de formage successifs, ce qui augmente l’efficacité et réduit le temps de production.
- Emboutissage Multicouche : Utilisé pour des applications spécifiques, ce type permet de former des pièces à partir de plusieurs couches de matériau, offrant ainsi des propriétés mécaniques améliorées et une résistance accrue.
Matériaux Utilisés dans l’Emboutissage
L’emboutissage peut être effectué avec divers matériaux, notamment :
- Acier : L’acier est le matériau le plus couramment utilisé en raison de sa résistance, de sa durabilité, et de sa capacité à être formé en différentes formes. L’acier inoxydable est également utilisé pour des applications nécessitant une résistance à la corrosion.
- Aluminium : L’aluminium est apprécié pour sa légèreté et sa résistance à la corrosion. Il est souvent utilisé dans l’industrie automobile et aéronautique pour réduire le poids des véhicules tout en maintenant la résistance.
- Métaux Alliés : Des alliages spécifiques peuvent être utilisés pour des applications qui nécessitent des propriétés particulières, comme la résistance à des températures élevées ou à la corrosion.
Avantages de l’Emboutissage
L’emboutissage présente plusieurs avantages clés :
- Précision : Ce processus permet de produire des pièces avec des tolérances très serrées, ce qui est crucial pour des applications industrielles où la qualité est essentielle.
- Efficacité : L’emboutissage en série permet de produire de grandes quantités de pièces en un temps réduit, ce qui est particulièrement bénéfique pour les industries qui nécessitent une production en masse.
- Économie de Matériaux : L’emboutissage réduit les déchets de matériaux en maximisant l’utilisation des tôles, ce qui contribue à des processus de fabrication plus durables et rentables.
- Flexibilité : Les techniques d’emboutissage peuvent être adaptées pour répondre à des besoins spécifiques, permettant ainsi la production de pièces variées et personnalisées.
Défis de l’Emboutissage
Malgré ses nombreux avantages, l’emboutissage présente des défis :
- Déformation Incontrôlée : La déformation du métal peut se produire de manière imprévisible si les paramètres de formage ne sont pas correctement réglés. Cela peut entraîner des défauts dans les pièces finies.
- Coûts d’Outillage : La fabrication des outils de formage peut être coûteuse, surtout pour des productions à faible volume. Les entreprises doivent évaluer la rentabilité de l’investissement dans des outils spécialisés.
- Contrôle de Qualité : Assurer un contrôle qualité rigoureux est essentiel pour garantir que les pièces produites répondent aux normes requises. Cela nécessite des investissements en équipements de test et en personnel qualifié.
Conclusion
L’emboutissage est un procédé essentiel dans la fabrication moderne, permettant de produire des pièces complexes avec une grande précision et efficacité. Grâce à ses applications variées dans de nombreux secteurs, il continue de jouer un rôle clé dans l’innovation industrielle. En comprenant les techniques, les matériaux, et les défis associés à l’emboutissage, les entreprises peuvent optimiser leur production, améliorer la qualité de leurs produits, et rester compétitives sur le marché mondial.
Outils de Formage

Les outils de formage sont des dispositifs essentiels dans le processus d’emboutissage et de transformation des métaux. Ils sont conçus pour appliquer des forces spécifiques aux matériaux afin de les façonner, de les couper ou de les assembler. La qualité et la précision des outils de formage influencent directement la qualité des pièces produites et l’efficacité des opérations de fabrication.
Types d’Outils de Formage
Il existe plusieurs types d’outils de formage, chacun conçu pour des applications spécifiques :
- Matrices de Formage : Ces outils sont utilisés pour donner une forme spécifique à la tôle métallique. Elles peuvent être de simples formes planes ou des designs plus complexes. Les matrices sont souvent fabriquées en acier trempé pour résister à l’usure.
- Coupelles et Poinçons : Utilisés pour découper des formes dans la tôle, les poinçons travaillent en tandem avec les matrices pour créer des pièces spécifiques. Les poinçons doivent être conçus avec précision pour éviter l’ovalisation ou d’autres déformations.
- Outils de Pliage : Ces outils permettent de plier des tôles à des angles précis. Ils peuvent inclure des bords arrondis ou des formes personnalisées pour répondre aux besoins spécifiques des pièces à produire.
- Outils de Soudage : Dans certains cas, les outils de formage sont également utilisés pour assembler des pièces par soudage. Ces outils appliquent une pression sur les pièces à souder, garantissant un contact optimal pour une soudure solide.
- Outils de Contrôle de Qualité : Bien que non directement impliqués dans le formage, ces outils assurent que les pièces produites respectent les tolérances et les spécifications requises. Ils peuvent inclure des instruments de mesure, des gabarits, et d’autres dispositifs de vérification.
Matériaux des Outils de Formage
Les outils de formage doivent être fabriqués à partir de matériaux résistants et durables pour résister aux contraintes et à l’usure. Les matériaux couramment utilisés comprennent :
- Acier Trempé : L’acier trempé est souvent choisi pour sa résistance à l’usure et sa durabilité. Il peut supporter des charges lourdes et résister aux déformations.
- Acier à Haute Résistance : Utilisé pour des applications spécifiques nécessitant une robustesse accrue, ce type d’acier est souvent utilisé dans des environnements de production intensifs.
- Carbures : Les outils en carbure sont utilisés pour leur dureté exceptionnelle. Ils sont idéaux pour les applications de découpe où la précision est essentielle.
Processus de Conception des Outils de Formage
La conception d’outils de formage est une étape cruciale qui nécessite une expertise technique et une compréhension approfondie du matériau à travailler. Les étapes typiques comprennent :
- Analyse des Besoins : Avant la conception, il est important de déterminer les spécifications de la pièce à produire, y compris les dimensions, les tolérances, et le type de matériau.
- Conception Assistée par Ordinateur (CAO) : Les logiciels de CAO sont utilisés pour créer des modèles numériques des outils de formage. Cela permet de visualiser le produit final et d’apporter des ajustements avant la fabrication.
- Prototypage : Dans de nombreux cas, un prototype de l’outil est fabriqué pour tester son efficacité avant la production en série. Cela permet d’identifier d’éventuels problèmes et d’apporter des modifications nécessaires.
- Fabrication : Une fois le design finalisé, les outils de formage sont fabriqués à l’aide de machines de haute précision, garantissant que les dimensions et les spécifications sont respectées.
- Tests et Validation : Après la fabrication, les outils sont soumis à des tests pour s’assurer qu’ils fonctionnent correctement et qu’ils produisent les pièces souhaitées avec la précision requise.
Avantages de l’Utilisation d’Outils de Formage de Qualité
L’utilisation d’outils de formage de haute qualité présente plusieurs avantages :
- Précision Accrue : Des outils bien conçus garantissent que les pièces sont produites avec des tolérances précises, ce qui est crucial pour des applications où la qualité est essentielle.
- Durabilité : Des matériaux résistants augmentent la durée de vie des outils, réduisant ainsi les coûts de remplacement et de maintenance.
- Efficacité de Production : Des outils optimisés permettent d’accélérer le processus de production, augmentant ainsi la productivité globale de l’usine.
- Flexibilité : Des outils de formage bien conçus peuvent être adaptés pour différents types de matériaux ou de formes, ce qui permet une plus grande variété dans les productions.
Défis dans la Fabrication d’Outils de Formage
Malgré les nombreux avantages, la fabrication d’outils de formage présente également des défis :
- Coûts Initiaux : La conception et la fabrication d’outils de formage peuvent être coûteuses, en particulier pour des pièces complexes. Cela peut représenter un obstacle pour les petites entreprises.
- Maintenance : Les outils de formage nécessitent un entretien régulier pour garantir leur performance. Cela inclut l’affûtage, le nettoyage et la vérification des pièces usées.
- Formation des Opérateurs : Les opérateurs doivent être formés pour utiliser les outils de manière efficace et sûre. Cela nécessite un investissement en temps et en ressources.
Conclusion
Les outils de formage jouent un rôle fondamental dans le processus de fabrication moderne, en permettant de créer des pièces métalliques avec précision et efficacité. Grâce à des avancées technologiques dans la conception et la fabrication, les outils de formage continuent d’évoluer pour répondre aux exigences croissantes des industries. En investissant dans des outils de qualité et en garantissant leur entretien adéquat, les entreprises peuvent améliorer leur efficacité opérationnelle et la qualité de leurs produits, assurant ainsi leur compétitivité sur le marché.
Presses à Emboutir

Les presses à emboutir sont des machines industrielles spécialement conçues pour effectuer le processus d’emboutissage, qui consiste à former des pièces à partir de tôles métalliques. Elles jouent un rôle crucial dans l’industrie manufacturière, en particulier dans les secteurs automobile, aéronautique et électroménager. Leur capacité à transformer des matériaux en pièces finies avec précision et efficacité en fait un équipement indispensable pour les fabricants.
Fonctionnement des Presses à Emboutir
Le fonctionnement des presses à emboutir repose sur plusieurs principes clés :
- Force Appliquée : Les presses à emboutir exercent une force importante sur la tôle en utilisant un piston hydraulique. Cette force est nécessaire pour déformer la tôle sans la rompre, permettant ainsi de créer des formes complexes.
- Cycle de Pressage : Le processus d’emboutissage implique un cycle de pressage, où la tôle est placée dans un moule et la pression est appliquée. Le cycle peut être automatique ou semi-automatique, selon la configuration de la presse.
- Réglage de la Pression : La pression appliquée peut être ajustée en fonction du type de matériau et de la complexité de la pièce à produire. Cela nécessite une connaissance approfondie des propriétés des matériaux et des techniques d’emboutissage.
Types de Presses à Emboutir
Il existe plusieurs types de presses à emboutir, chacune adaptée à des besoins spécifiques :
- Presses Hydraulique : Ces presses utilisent un système hydraulique pour générer la force nécessaire à l’emboutissage. Elles sont polyvalentes et peuvent être utilisées pour une grande variété de formes et de matériaux.
- Presses Mécaniques : Utilisant des moteurs et des systèmes de bielle pour appliquer la force, ces presses sont généralement plus rapides que les presses hydrauliques. Elles sont souvent utilisées pour des productions en série où la vitesse est essentielle.
- Presses Électriques : Ces presses, de plus en plus populaires, utilisent des moteurs électriques pour générer la force de pressage. Elles offrent un meilleur contrôle de la pression et sont souvent plus silencieuses et plus efficaces énergétiquement.
- Presses à Cadre : Conçues pour des opérations d’emboutissage général, elles ont une structure ouverte qui permet un accès facile aux pièces à travailler.
Applications des Presses à Emboutir
Les presses à emboutir sont utilisées dans divers domaines industriels :
- Industrie Automobile : Elles sont utilisées pour produire des panneaux de carrosserie, des supports de moteur, et d’autres composants essentiels. L’emboutissage permet de créer des formes complexes tout en garantissant la résistance et la durabilité des pièces.
- Électroménager : Dans le secteur des appareils électroménagers, les presses à emboutir fabriquent des pièces telles que des châssis et des couvercles. Ces composants doivent être robustes et esthétiques.
- Aéronautique : Les presses à emboutir jouent un rôle crucial dans la fabrication de pièces légères et résistantes pour les aéronefs. Les exigences strictes en matière de sécurité et de performance rendent ce processus particulièrement important.
- Construction : Dans le secteur de la construction, elles sont utilisées pour produire des éléments métalliques tels que des poutres et des supports, contribuant à la structure et à la stabilité des bâtiments.
Avantages des Presses à Emboutir
L’utilisation de presses à emboutir présente plusieurs avantages :
- Précision et Qualité : Ces presses permettent de produire des pièces avec des tolérances très serrées, garantissant que les produits finaux répondent aux normes de qualité les plus élevées.
- Efficacité : Les presses à emboutir sont capables de produire de grandes quantités de pièces en peu de temps, augmentant ainsi la productivité des usines.
- Réduction des Déchets : L’emboutissage optimise l’utilisation des matériaux, réduisant ainsi le gaspillage et contribuant à des processus de fabrication plus durables.
- Flexibilité : Les presses peuvent être configurées pour traiter différents types de matériaux et de formes, ce qui permet une grande variété de productions.
Défis des Presses à Emboutir
Bien que les presses à emboutir présentent de nombreux avantages, elles sont également confrontées à certains défis :
- Coûts d’Investissement : L’achat de presses à emboutir, en particulier celles de haute capacité, peut représenter un investissement considérable pour les entreprises, ce qui peut être un obstacle pour les petites entreprises.
- Formation et Compétences : L’utilisation efficace de ces machines nécessite des compétences techniques spécifiques. Les entreprises doivent investir dans la formation de leur personnel pour garantir un fonctionnement optimal.
- Entretien Régulier : Comme toute machine industrielle, les presses à emboutir nécessitent un entretien régulier pour garantir leur performance et leur longévité. Cela implique la vérification des composants, l’huile des pièces mobiles, et le nettoyage.
Conclusion
Les presses à emboutir sont des machines essentielles dans le paysage manufacturier moderne, permettant la production de pièces métalliques complexes avec précision et efficacité. Leur rôle dans des secteurs clés tels que l’automobile, l’aéronautique et l’électroménager souligne leur importance dans l’innovation et l’évolution des procédés de fabrication. En investissant dans des presses de haute qualité et en s’assurant d’une maintenance adéquate, les entreprises peuvent optimiser leur production et maintenir leur compétitivité sur le marché mondial.
Déformation Plastique
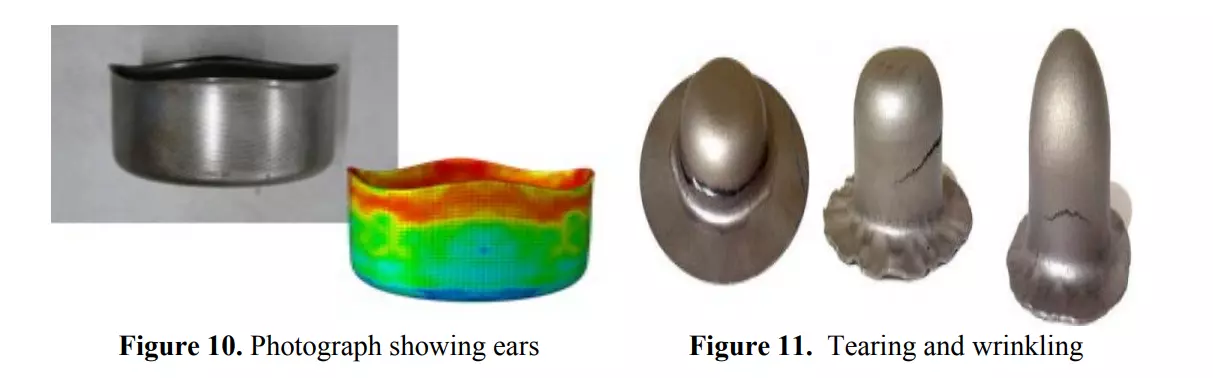
La déformation plastique est un phénomène fondamental dans le domaine de la métallurgie et de l’ingénierie des matériaux. Elle se réfère au processus par lequel un matériau, lorsqu’il est soumis à une contrainte, subit une déformation permanente, contrairement à la déformation élastique où le matériau retrouve sa forme initiale après la suppression de la contrainte. Ce processus est crucial dans des applications telles que l’emboutissage, le forgeage et d’autres méthodes de transformation des métaux.
Mécanismes de Déformation Plastique
La déformation plastique se produit lorsque la contrainte appliquée dépasse une certaine limite, appelée limite d’élasticité. Les principaux mécanismes de déformation plastique incluent :
- Glissement : Ce mécanisme implique le mouvement des dislocations à travers le réseau cristallin du matériau. Lorsque la contrainte appliquée est suffisante, des plans de glissement se forment, permettant aux atomes de se déplacer les uns par rapport aux autres, entraînant une déformation.
- Jouissance de Déformation : Ce phénomène se produit lorsque des dislocations se rencontrent et se regroupent, créant des zones de contraintes qui facilitent le mouvement des dislocations. Cela conduit à une déformation plus importante du matériau.
- Frappe de Déformation : Ce mécanisme implique la déformation du matériau par impact. Dans certaines applications, une force d’impact peut provoquer une déformation plastique rapide, qui est souvent utilisée dans le forgeage.
Types de Déformation Plastique
La déformation plastique peut être classée en plusieurs types, selon le mode d’application des forces :
- Déformation à Froid : Réalisée à température ambiante, cette forme de déformation plastiques permet de travailler les matériaux sans les chauffer. Elle est couramment utilisée dans les applications d’emboutissage où des tolérances serrées et une finition de surface de haute qualité sont requises.
- Déformation à Chaud : Dans ce cas, les matériaux sont chauffés avant d’être déformés, ce qui augmente leur ductilité et réduit la résistance à la déformation. Cette méthode est couramment utilisée dans le forgeage et la fabrication de pièces complexes.
- Déformation à Pression : Ce type de déformation se produit lorsque des forces sont appliquées de manière concentrée sur un matériau, comme dans le cas de l’emboutissage. Cela permet de créer des formes spécifiques sans rompre le matériau.
Applications de la Déformation Plastique
La déformation plastique est largement utilisée dans divers secteurs industriels, notamment :
- Industrie Automobile : Dans l’automobile, la déformation plastique est essentielle pour la fabrication de pièces de carrosserie, de supports et d’autres composants critiques. Les techniques de déformation permettent de produire des pièces légères et résistantes.
- Fabrication de Métaux : Dans l’industrie métallurgique, la déformation plastique est utilisée pour façonner des métaux en barres, plaques et autres formes. Les processus tels que le laminage et le forgeage reposent sur ce phénomène.
- Aéronautique : La déformation plastique est cruciale dans la fabrication de pièces pour l’aéronautique, où des propriétés spécifiques de résistance et de légèreté sont nécessaires.
- Construction : Dans le secteur de la construction, la déformation plastique est utilisée pour façonner des matériaux en acier pour des poutres et des structures, contribuant ainsi à la durabilité et à la stabilité des bâtiments.
Avantages de la Déformation Plastique
La déformation plastique présente plusieurs avantages significatifs :
- Amélioration des Propriétés Mécaniques : La déformation plastique peut améliorer la résistance et la ductilité des matériaux, les rendant plus adaptés à des applications spécifiques.
- Flexibilité de Conception : Ce processus permet de créer des formes complexes et variées, répondant ainsi à des exigences de conception spécifiques dans divers secteurs.
- Efficacité de Production : La déformation plastique peut être réalisée en série, augmentant ainsi l’efficacité de la production et réduisant les coûts.
- Économie de Matériaux : Les techniques de déformation plastique permettent d’optimiser l’utilisation des matériaux, réduisant ainsi les déchets et les coûts associés.
Défis de la Déformation Plastique
Malgré ses nombreux avantages, la déformation plastique présente également des défis :
- Contrôle des Propriétés : Assurer des propriétés mécaniques uniformes dans les pièces produites peut être difficile, surtout lorsque les matériaux ont des hétérogénéités.
- Formation de Défauts : La déformation plastique peut entraîner la formation de défauts, tels que des fissures ou des inclusions, qui peuvent compromettre l’intégrité des pièces.
- Coûts d’Investissement : Les équipements nécessaires pour réaliser des déformations plastiques de haute qualité peuvent être coûteux, représentant un obstacle pour certaines entreprises.
Conclusion
La déformation plastique est un processus fondamental dans l’industrie moderne, permettant de transformer les matériaux en pièces fonctionnelles avec des propriétés mécaniques optimisées. Grâce à ses nombreuses applications et à ses avantages significatifs, elle continue de jouer un rôle clé dans l’innovation et l’efficacité des procédés de fabrication. En comprenant les mécanismes, les avantages et les défis associés à la déformation plastique, les entreprises peuvent mieux exploiter ce phénomène pour améliorer leurs processus de production et la qualité de leurs produits.
Matériaux Métalliques

Les matériaux métalliques jouent un rôle fondamental dans l’ingénierie et la fabrication modernes. Leur capacité à être formés, renforcés et assemblés en fait des éléments clés dans de nombreux secteurs, allant de l’automobile à l’aéronautique, en passant par l’électroménager et la construction. Comprendre les propriétés, les types et les applications des matériaux métalliques est essentiel pour optimiser les processus de fabrication et garantir la qualité des produits finis.
Propriétés des Matériaux Métalliques
Les matériaux métalliques présentent un certain nombre de propriétés qui les rendent particulièrement adaptés à des applications industrielles :
- Ductilité : La ductilité est la capacité d’un matériau à se déformer plastiquement sans se rompre. Cela permet de former des pièces complexes par emboutissage ou forgeage.
- Résistance : Les métaux présentent une résistance élevée, ce qui leur permet de supporter des charges importantes sans se déformer de manière permanente. Cette propriété est cruciale dans les structures et les composants soumis à des contraintes mécaniques.
- Conductivité : Les métaux sont généralement de bons conducteurs de chaleur et d’électricité, ce qui les rend indispensables dans les applications électriques et thermiques.
- Malléabilité : La malléabilité est la capacité d’un métal à être façonné sous forme de feuilles ou de plaques. Cela permet une grande variété d’applications dans la fabrication de composants.
- Résistance à la Corrosion : Certains métaux, tels que l’acier inoxydable, présentent une excellente résistance à la corrosion, ce qui est essentiel dans des environnements humides ou corrosifs.
Types de Matériaux Métalliques
Les matériaux métalliques peuvent être classés en plusieurs catégories, chacune ayant ses caractéristiques et ses applications spécifiques :
- Acier : L’acier est un alliage de fer et de carbone, largement utilisé en raison de sa résistance, de sa durabilité et de sa polyvalence. Il est souvent utilisé dans la construction, l’automobile et les appareils électroménagers.
- Aluminium : Ce métal léger et résistant à la corrosion est utilisé dans des applications où le poids est un facteur critique, comme dans l’aéronautique et l’automobile. Son excellente conductivité thermique et électrique en fait également un choix privilégié pour les applications électriques.
- Cuivre : Connu pour sa conductivité électrique exceptionnelle, le cuivre est largement utilisé dans les câbles électriques, les tuyauteries et les équipements électroniques. Sa résistance à la corrosion en fait un matériau durable pour de nombreuses applications.
- Titane : Le titane est un métal léger et très résistant, souvent utilisé dans des applications aéronautiques et médicales. Sa résistance à la corrosion et sa biocompatibilité en font un choix idéal pour des implants et des dispositifs médicaux.
- Alliages Métalliques : Les alliages, tels que les alliages d’aluminium ou de cuivre, combinent les propriétés de différents métaux pour créer des matériaux aux caractéristiques optimisées pour des applications spécifiques.
Applications des Matériaux Métalliques
Les matériaux métalliques sont utilisés dans une grande variété d’applications industrielles :
- Industrie Automobile : Les métaux sont essentiels dans la fabrication de véhicules, des châssis aux moteurs, en passant par les systèmes de suspension et les panneaux de carrosserie.
- Aéronautique : Dans ce secteur, les matériaux métalliques doivent répondre à des exigences strictes en matière de résistance, de légèreté et de résistance à la corrosion. Les alliages de titane et d’aluminium sont couramment utilisés.
- Électronique : Les métaux sont cruciaux dans la fabrication de composants électroniques, y compris les circuits imprimés, les connecteurs et les dissipateurs thermiques.
- Construction : Dans le secteur de la construction, l’acier est largement utilisé pour les structures des bâtiments, des ponts et des infrastructures en raison de sa résistance et de sa durabilité.
- Électroménager : Les appareils électroménagers, tels que les réfrigérateurs et les lave-linge, contiennent de nombreux composants en métal, notamment des châssis et des moteurs, qui assurent leur fonctionnement efficace.
Avantages des Matériaux Métalliques
Les matériaux métalliques présentent plusieurs avantages significatifs :
- Durabilité : La longévité des matériaux métalliques en fait un choix idéal pour des applications nécessitant des produits robustes et résistants à l’usure.
- Polyvalence : Les métaux peuvent être transformés de diverses manières, y compris le découpage, le pliage et l’emboutissage, permettant une grande flexibilité dans le design et la fabrication.
- Recyclabilité : La plupart des matériaux métalliques sont recyclables, ce qui contribue à la durabilité et à la réduction des déchets dans l’industrie.
- Coût-efficacité : Les matériaux métalliques, en particulier l’acier, sont souvent disponibles à un coût relativement faible par rapport à d’autres matériaux, ce qui les rend économiquement attractifs pour les fabricants.
Défis des Matériaux Métalliques
Malgré leurs nombreux avantages, les matériaux métalliques présentent également des défis :
- Corrosion : Bien que certains métaux soient résistants à la corrosion, d’autres peuvent se détériorer lorsqu’ils sont exposés à des environnements agressifs, nécessitant des traitements de surface ou des alliages spécialisés.
- Poids : Dans certaines applications, le poids des matériaux métalliques peut être un inconvénient, notamment dans le secteur aéronautique, où la légèreté est cruciale.
- Fabrication : Les processus de fabrication des métaux peuvent nécessiter des équipements coûteux et une expertise technique, ce qui peut représenter un obstacle pour certaines entreprises.
Conclusion
Les matériaux métalliques sont au cœur de l’innovation industrielle moderne, permettant de créer des produits durables, performants et polyvalents. En comprenant les propriétés, les types et les applications des métaux, les fabricants peuvent optimiser leurs processus de production et garantir la qualité des pièces produites. Avec les avancées technologiques et une attention croissante à la durabilité, les matériaux métalliques continueront de jouer un rôle essentiel dans l’avenir de la fabrication.
Conception Assistée par Ordinateur (CAO)
La conception assistée par ordinateur (CAO) est une technologie essentielle dans le domaine de l’ingénierie et de la fabrication. Elle permet aux concepteurs et aux ingénieurs de créer des modèles numériques de pièces et d’assemblages, facilitant ainsi le processus de conception, d’analyse et de fabrication. La CAO a révolutionné la manière dont les produits sont développés, offrant une précision, une efficacité et une flexibilité inégalées.
Histoire de la CAO
La CAO a émergé dans les années 1960 avec l’apparition des premiers logiciels de conception. À l’origine, ces outils étaient principalement utilisés pour la conception architecturale et l’ingénierie. Au fil des décennies, la technologie a évolué, et les logiciels de CAO sont devenus de plus en plus sophistiqués, intégrant des fonctionnalités avancées telles que la modélisation 3D, l’analyse par éléments finis (AEF) et la simulation.
Fonctionnalités de la CAO
Les logiciels de CAO modernes offrent une multitude de fonctionnalités qui améliorent le processus de conception :
- Modélisation 2D et 3D : Les utilisateurs peuvent créer des dessins en deux dimensions et des modèles en trois dimensions, permettant une visualisation réaliste des pièces et des assemblages.
- Bibliothèques de Composants : La plupart des logiciels de CAO incluent des bibliothèques de composants standardisés, facilitant l’insertion de pièces courantes dans les conceptions.
- Simulation et Analyse : Les outils de CAO permettent de simuler le comportement des pièces sous différentes conditions, ce qui aide à identifier les problèmes potentiels avant la fabrication.
- Dessin Technique : Les logiciels de CAO génèrent automatiquement des dessins techniques à partir des modèles 3D, incluant les cotes et les annotations nécessaires pour la fabrication.
- Interopérabilité : Les logiciels de CAO modernes sont souvent compatibles avec d’autres outils de conception et de fabrication, facilitant l’échange d’informations entre les différentes étapes du processus de production.
Applications de la CAO
La CAO est utilisée dans divers secteurs industriels, notamment :
- Industrie Automobile : Les fabricants automobiles utilisent la CAO pour concevoir des pièces de moteur, des châssis et des systèmes de sécurité. La capacité à simuler le comportement des pièces sous contrainte est essentielle pour garantir la sécurité et la performance des véhicules.
- Aéronautique : Dans ce secteur, la CAO est utilisée pour concevoir des composants légers et résistants, tels que des ailes et des moteurs. La précision des modèles CAO est cruciale pour répondre aux exigences strictes de l’aviation.
- Ingénierie Mécanique : Les ingénieurs mécaniques utilisent la CAO pour concevoir des machines, des outils et des systèmes mécaniques. La modélisation 3D permet de visualiser les interactions entre les différentes pièces.
- Architecture : Les architectes utilisent des logiciels de CAO pour créer des plans et des modèles de bâtiments. La visualisation 3D aide à communiquer les concepts aux clients et aux parties prenantes.
- Design de Produits : Dans le design industriel, la CAO est utilisée pour créer des prototypes de produits, facilitant l’itération et l’amélioration des conceptions avant la fabrication.
Avantages de la CAO
L’utilisation de la CAO présente de nombreux avantages :
- Précision et Exactitude : La CAO permet de créer des modèles numériques précis, réduisant ainsi les erreurs de conception et améliorant la qualité des produits finis.
- Efficacité : Les outils de CAO accélèrent le processus de conception en automatisant de nombreuses tâches, permettant ainsi aux ingénieurs de se concentrer sur des aspects plus critiques de la conception.
- Flexibilité : La CAO permet d’apporter des modifications rapides aux conceptions, facilitant l’itération et l’optimisation des produits.
- Collaboration : Les outils de CAO permettent à plusieurs utilisateurs de travailler simultanément sur un projet, favorisant la collaboration entre les équipes de conception et de fabrication.
- Documentation : La CAO génère automatiquement la documentation nécessaire pour la fabrication, y compris les dessins techniques et les spécifications.
Défis de la CAO
Malgré ses nombreux avantages, la CAO présente également des défis :
- Coûts des Logiciels : Les logiciels de CAO peuvent être coûteux, ce qui peut représenter un obstacle pour les petites entreprises.
- Formation Nécessaire : L’utilisation efficace de la CAO nécessite une formation spécialisée, et les entreprises doivent investir du temps et des ressources pour former leur personnel.
- Complexité des Outils : Les fonctionnalités avancées des logiciels de CAO peuvent être complexes à maîtriser, ce qui peut ralentir le processus de conception pour les utilisateurs novices.
Conclusion
La conception assistée par ordinateur (CAO) est une technologie indispensable dans le monde de l’ingénierie et de la fabrication. Elle améliore la précision, l’efficacité et la collaboration dans le processus de conception, permettant aux entreprises de développer des produits de haute qualité de manière rapide et flexible. Avec les avancées continues dans les logiciels de CAO et l’intégration de nouvelles technologies, telles que la réalité augmentée et l’intelligence artificielle, l’avenir de la CAO s’annonce prometteur, offrant encore plus de possibilités aux concepteurs et aux ingénieurs du monde entier.
Simulation Numérique
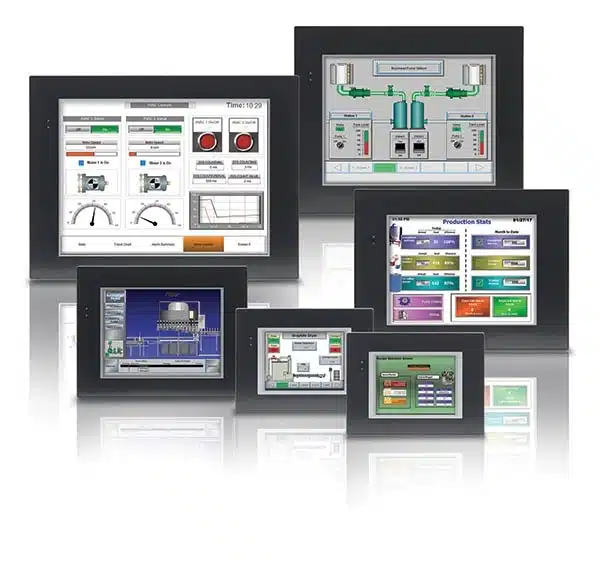
La simulation numérique est une technique informatique qui permet de reproduire le comportement de systèmes physiques, mécaniques, ou chimiques à l’aide de modèles mathématiques. En ingénierie et dans de nombreux autres domaines industriels, cette approche est devenue un outil incontournable pour analyser, prévoir et optimiser les performances des produits et des processus avant leur réalisation concrète. En plus d’améliorer l’efficacité du développement, la simulation numérique réduit considérablement les coûts et le temps liés à la fabrication de prototypes physiques.
Principes de la Simulation Numérique
Le principe de base de la simulation numérique est la modélisation d’un phénomène réel à l’aide d’un ensemble d’équations mathématiques qui décrivent son comportement. Ces modèles sont ensuite résolus par des méthodes numériques, à l’aide d’ordinateurs puissants capables de traiter d’énormes quantités de données. Voici les principales étapes d’une simulation numérique :
- Modélisation : Cette étape consiste à définir un modèle mathématique qui représente le système ou le phénomène que l’on souhaite étudier. Le modèle peut être aussi simple qu’une équation décrivant la chute d’un objet, ou aussi complexe qu’un ensemble d’équations différentielles décrivant le comportement d’un fluide en mouvement.
- Discrétisation : Une fois le modèle établi, il est nécessaire de discrétiser l’espace et le temps afin de résoudre les équations de manière numérique. Cela signifie que l’on divise le domaine du problème en un nombre fini de points ou d’éléments, ce qui permet de traiter les calculs de manière informatique.
- Résolution Numérique : À cette étape, les équations discrétisées sont résolues à l’aide de méthodes numériques, telles que les méthodes des éléments finis (MEF) ou des volumes finis (MVF). Ces techniques permettent de calculer les résultats en fonction des conditions initiales et des paramètres du modèle.
- Validation et Vérification : Après avoir obtenu les résultats de la simulation, il est essentiel de vérifier leur validité en les comparant à des données expérimentales ou à des résultats théoriques pour s’assurer que le modèle fonctionne correctement.
Types de Simulations Numériques
Il existe plusieurs types de simulations numériques, chacune adaptée à un type spécifique de problème ou de domaine d’application :
- Simulation Mécanique : Cette simulation est couramment utilisée pour analyser les déformations, les tensions et les forces dans les structures et les matériaux. Les ingénieurs utilisent la simulation mécanique pour tester la résistance de ponts, de bâtiments ou de pièces de machines.
- Dynamique des Fluides Numérique (CFD) : La CFD est une branche de la simulation numérique qui modélise le comportement des fluides (liquides et gaz) et leurs interactions avec leur environnement. Elle est largement utilisée dans des domaines tels que l’aéronautique, l’automobile, et l’énergie.
- Simulation Thermique : La simulation thermique permet de prédire la distribution de la chaleur dans un système ou un matériau. Ce type de simulation est utilisé dans des applications allant du refroidissement des circuits électroniques à la conception de systèmes de chauffage pour les bâtiments.
- Simulation de Réaction Chimique : Ce type de simulation permet de modéliser et d’analyser les réactions chimiques, y compris la cinétique des réactions, les transferts de masse et d’énergie. Elle est couramment utilisée dans l’industrie chimique et pharmaceutique.
- Simulation de Systèmes Multiphysiques : Les systèmes multiphysiques impliquent des interactions entre plusieurs phénomènes physiques, tels que la mécanique, la thermique, et la dynamique des fluides. La simulation de ces systèmes complexes permet de mieux comprendre les interactions entre différentes disciplines.
Applications de la Simulation Numérique
La simulation numérique est utilisée dans une grande variété de secteurs, chacun exploitant cette technologie pour résoudre des problèmes complexes et optimiser ses produits :
- Industrie Automobile : Dans l’automobile, la simulation est utilisée pour concevoir des véhicules plus sûrs, plus économes en carburant et plus performants. La dynamique des fluides, la simulation d’impact et la simulation thermique sont couramment utilisées pour analyser le comportement des voitures sous diverses conditions.
- Aéronautique et Spatial : Les ingénieurs aéronautiques utilisent des simulations pour concevoir des avions et des engins spatiaux plus légers, plus rapides et plus sûrs. La CFD est particulièrement utile pour modéliser le flux d’air autour des ailes d’un avion et optimiser son aérodynamisme.
- Santé et Biomécanique : Les simulations numériques sont de plus en plus utilisées dans la médecine pour modéliser des organes humains, simuler des interventions chirurgicales et concevoir des dispositifs médicaux. En biomécanique, les chercheurs simulent le mouvement et les forces appliquées aux muscles et aux os.
- Énergie : Dans le domaine de l’énergie, la simulation est utilisée pour optimiser les processus de production d’énergie, qu’il s’agisse de l’extraction de pétrole, de la production d’électricité ou de la gestion de réseaux électriques. La simulation thermique et la modélisation des fluides sont particulièrement pertinentes dans ces applications.
- Environnement : La simulation numérique aide les chercheurs à modéliser des phénomènes environnementaux tels que les changements climatiques, la dispersion des polluants dans l’atmosphère, et les flux d’eau dans les rivières et les océans.
Avantages de la Simulation Numérique
Les avantages de la simulation numérique sont nombreux et contribuent à améliorer la conception, la sécurité et la performance des produits et des systèmes :
- Réduction des Coûts : En remplaçant les prototypes physiques par des simulations numériques, les entreprises peuvent réduire considérablement les coûts associés à la fabrication et au test de prototypes. La simulation permet de détecter et de corriger les erreurs de conception avant la production.
- Gain de Temps : La simulation permet de raccourcir les délais de développement des produits en accélérant les tests et les analyses, ce qui permet de commercialiser les produits plus rapidement.
- Amélioration des Performances : En simulant différentes conditions et scénarios, les ingénieurs peuvent optimiser les conceptions pour maximiser la performance, la durabilité et la sécurité des produits.
- Réduction des Risques : La simulation permet d’évaluer le comportement des systèmes dans des situations critiques, ce qui aide à prévenir les défaillances et à améliorer la sécurité.
- Flexibilité et Innovation : Les outils de simulation permettent de tester rapidement différentes configurations et concepts, favorisant ainsi l’innovation et la créativité dans la conception.
Défis de la Simulation Numérique
Malgré ses nombreux avantages, la simulation numérique présente certains défis :
- Complexité des Modèles : La création de modèles précis et réalistes nécessite une expertise avancée, et certains phénomènes physiques complexes peuvent être difficiles à modéliser.
- Puissance de Calcul : Les simulations complexes, en particulier celles qui impliquent des systèmes multiphysiques ou des simulations à grande échelle, nécessitent des ressources de calcul importantes, ce qui peut entraîner des coûts élevés en termes d’infrastructure informatique.
- Validation : La simulation numérique est basée sur des modèles mathématiques, et il est essentiel de valider ces modèles en les comparant à des données expérimentales pour s’assurer qu’ils reflètent fidèlement la réalité.
Conclusion
La simulation numérique est un outil puissant qui transforme la manière dont les ingénieurs et les concepteurs abordent le développement de produits et la résolution de problèmes. En permettant de tester virtuellement des scénarios et des conditions variées, la simulation numérique améliore la qualité des produits, réduit les coûts et les délais, et favorise l’innovation. Avec l’évolution continue des technologies informatiques et des algorithmes de simulation, cette technique continuera de jouer un rôle clé dans l’ingénierie et dans de nombreux autres domaines.
Analyse par Éléments Finis (AEF)

L’Analyse par Éléments Finis (AEF) est une méthode numérique utilisée pour résoudre des problèmes complexes en ingénierie, physique, et autres disciplines scientifiques. Elle permet de modéliser et de comprendre comment des structures ou des matériaux se comportent sous diverses contraintes, telles que des forces, des vibrations, des charges thermiques, ou des pressions. L’AEF est devenue un outil indispensable pour les ingénieurs et les concepteurs, leur permettant de simuler des phénomènes physiques complexes sans recourir à des essais coûteux ou à la fabrication de prototypes physiques.
Fondements Théoriques de l’AEF
L’AEF repose sur une technique de modélisation mathématique qui divise un problème complexe en un grand nombre d’éléments finis plus petits et plus simples. Ces éléments sont interconnectés par des nœuds, formant un maillage qui couvre toute la surface ou le volume du modèle étudié. Une fois que le modèle est discretisé en éléments finis, des équations algébriques sont utilisées pour décrire les comportements mécaniques ou physiques de chaque élément. Ces équations sont ensuite résolues pour calculer les réponses du système aux contraintes imposées.
- Discrétisation du Domaine : La première étape de l’AEF consiste à diviser le domaine d’analyse (par exemple, une pièce mécanique) en un grand nombre de petits éléments. Ces éléments peuvent être de différentes formes géométriques : triangles, quadrilatères, tétraèdres, etc. Ce maillage est essentiel pour que les équations différentielles qui régissent le comportement du système puissent être résolues de manière numérique.
- Équations du Problème : Les équations différentielles partielles (EDP) qui régissent le phénomène étudié (déformations, vibrations, écoulement de fluides, etc.) sont transformées en équations algébriques grâce à la discrétisation par éléments finis. Chaque élément du maillage est alors analysé individuellement.
- Résolution : Une fois les équations algébriques établies pour chaque élément, le système global d’équations est résolu pour obtenir les déformations, contraintes, températures ou autres variables pertinentes à chaque nœud du modèle.
- Post-Traitement : Après avoir obtenu les résultats de la résolution, ces données sont analysées et interprétées pour évaluer les performances de la structure ou du système. Le post-traitement inclut souvent des visualisations graphiques, telles que des cartes de déformation, de contraintes ou de température, qui permettent de visualiser clairement les zones critiques.
Applications de l’AEF
L’AEF est utilisée dans une grande variété de domaines où la simulation de structures complexes ou de phénomènes physiques est nécessaire :
- Mécanique des Structures : L’AEF est largement utilisée pour analyser la résistance et la stabilité des structures. Par exemple, dans l’industrie de la construction, elle permet de simuler le comportement des ponts, des bâtiments et des infrastructures sous l’effet des charges et des forces environnementales, telles que les tremblements de terre ou les vents violents.
- Industrie Automobile : Dans l’automobile, l’AEF est utilisée pour concevoir des véhicules plus légers, plus sûrs et plus performants. Elle permet de simuler des crash-tests virtuels, d’analyser le comportement des composants sous différentes charges et de prévoir les défaillances potentielles avant la production.
- Aéronautique et Spatial : Les structures des avions et des engins spatiaux doivent répondre à des exigences strictes en termes de poids, de résistance et de sécurité. L’AEF est utilisée pour simuler le comportement des ailes, des fuselages et des moteurs d’avion sous des conditions de vol extrêmes, optimisant ainsi la conception tout en respectant des contraintes de légèreté.
- Électronique : L’AEF est utilisée dans l’industrie électronique pour modéliser les déformations thermiques et mécaniques des composants, tels que les circuits imprimés et les boîtiers de puces. Cela permet de garantir que les dispositifs électroniques fonctionnent correctement dans des conditions de température et de vibration variables.
- Biomécanique : En médecine, l’AEF est utilisée pour simuler le comportement des os, des implants, et des prothèses sous l’effet des forces mécaniques. Cela aide les ingénieurs biomédicaux à concevoir des dispositifs médicaux qui s’adaptent parfaitement au corps humain et répondent aux besoins des patients.
Avantages de l’AEF
L’AEF présente plusieurs avantages majeurs par rapport à d’autres méthodes d’analyse :
- Précision : L’AEF permet de modéliser et de simuler des phénomènes très complexes avec une grande précision, en particulier dans les cas où les géométries, les matériaux et les conditions de chargement sont difficiles à analyser à l’aide de méthodes analytiques traditionnelles.
- Flexibilité : L’AEF peut être appliquée à une large gamme de problèmes dans différents domaines, qu’il s’agisse de la mécanique des structures, de la dynamique des fluides, de la thermique, ou même de la propagation d’ondes.
- Réduction des Coûts : L’une des plus grandes contributions de l’AEF est la réduction des coûts de développement. En effectuant des simulations numériques au lieu de tests physiques, les entreprises peuvent économiser sur la fabrication de prototypes et sur les tests destructifs.
- Optimisation : En utilisant l’AEF, il est possible de tester virtuellement de multiples conceptions et configurations avant de choisir la solution optimale. Cela permet d’améliorer les performances des produits, tout en réduisant les coûts de développement et les délais de mise sur le marché.
Défis de l’AEF
Malgré ses avantages, l’AEF présente également plusieurs défis qu’il est important de prendre en compte :
- Complexité de la Modélisation : Créer un modèle précis et valide peut être une tâche complexe, surtout lorsque des phénomènes physiques non linéaires, comme les grands déplacements ou les matériaux non homogènes, sont impliqués.
- Puissance de Calcul : Les simulations AEF peuvent être très gourmandes en ressources informatiques, en particulier lorsqu’il s’agit de grandes structures ou de systèmes complexes. L’accès à des ordinateurs performants et à des logiciels spécialisés est souvent nécessaire pour résoudre ces problèmes.
- Validation des Modèles : L’AEF repose sur des hypothèses et des simplifications qui peuvent parfois ne pas refléter exactement la réalité. Il est donc essentiel de valider les résultats des simulations par des tests expérimentaux pour garantir leur fiabilité.
- Formation et Compétences : La mise en œuvre de l’AEF nécessite des compétences spécialisées en ingénierie, en mathématiques et en informatique. Les ingénieurs doivent être formés à l’utilisation des logiciels de simulation et à l’interprétation des résultats.
Logiciels d’Analyse par Éléments Finis
De nombreux logiciels spécialisés dans l’AEF sont disponibles sur le marché, chacun offrant des fonctionnalités adaptées à des industries et des applications spécifiques. Parmi les logiciels les plus couramment utilisés, on trouve :
- ANSYS : ANSYS est l’un des logiciels AEF les plus populaires, utilisé dans une large gamme d’industries pour la mécanique des structures, la thermique, la dynamique des fluides, et la simulation électromagnétique.
- Abaqus : Utilisé principalement dans les secteurs de l’automobile, de l’aéronautique et de la biomécanique, Abaqus est reconnu pour sa capacité à résoudre des problèmes complexes impliquant des matériaux non linéaires et des conditions de chargement dynamiques.
- SolidWorks Simulation : Ce logiciel est souvent utilisé pour la conception de produits industriels. Il propose des fonctionnalités d’AEF intégrées à un environnement de CAO, facilitant ainsi l’analyse des pièces et des assemblages directement à partir des modèles 3D.
- COMSOL Multiphysics : COMSOL est un outil multiphysique qui permet de résoudre des problèmes impliquant plusieurs phénomènes physiques simultanés, comme la mécanique, la thermique, et l’électromagnétisme.
Conclusion
L’Analyse par Éléments Finis (AEF) est une méthode puissante et polyvalente qui permet aux ingénieurs et aux concepteurs de résoudre des problèmes complexes en simulant numériquement des phénomènes physiques variés. Elle améliore la précision des analyses, réduit les coûts et les délais de développement, et permet d’optimiser les performances des produits. Cependant, la mise en œuvre de l’AEF nécessite des compétences spécialisées et une validation rigoureuse des modèles pour garantir des résultats fiables. Avec l’évolution des technologies informatiques et des logiciels de simulation, l’AEF continuera de jouer un rôle clé dans l’innovation et l’amélioration des produits dans de nombreux secteurs industriels.
Fabrication Assistée par Ordinateur (FAO)
Introduction
La Fabrication Assistée par Ordinateur (FAO) est un ensemble de techniques et de logiciels qui permettent de contrôler et d’automatiser les machines-outils utilisées dans les processus de production. La FAO est souvent associée à la Conception Assistée par Ordinateur (CAO), car les deux processus sont intimement liés : après avoir conçu un produit en 3D avec un logiciel de CAO, les ingénieurs utilisent un logiciel de FAO pour programmer les machines qui fabriqueront la pièce. L’objectif de la FAO est d’améliorer la précision, l’efficacité et la rapidité des processus de fabrication, tout en minimisant les erreurs humaines.
Principe de la FAO
La FAO repose sur l’utilisation de logiciels capables de convertir les conceptions numériques en instructions spécifiques destinées aux machines-outils, telles que les fraiseuses, les tours, et les machines de découpe laser. Ces instructions sont souvent sous la forme de code G, un langage de programmation standard utilisé pour contrôler les mouvements et les actions des machines.
- Étape de Conception (CAO) : Le processus commence par la création d’un modèle 3D de la pièce à fabriquer à l’aide d’un logiciel de Conception Assistée par Ordinateur (CAO). Le modèle est précis et inclut toutes les dimensions et spécifications nécessaires à la fabrication.
- Conversion en Code G : Le logiciel de FAO traduit ensuite le modèle 3D en instructions compréhensibles par les machines-outils. Ces instructions incluent des détails sur les trajectoires des outils, la vitesse de coupe, et les conditions de fonctionnement de la machine.
- Simulation et Validation : Avant d’envoyer les instructions aux machines, une simulation numérique du processus est effectuée. Cette simulation permet de vérifier que la machine suivra correctement les étapes de fabrication et de s’assurer qu’il n’y aura pas de collisions ou d’erreurs de programmation.
- Fabrication : Une fois validées, les instructions sont envoyées à la machine-outil, qui exécute les opérations nécessaires pour transformer le matériau brut en produit final.
Histoire de la FAO
L’histoire de la FAO remonte aux années 1950, avec l’émergence des premières machines-outils à commande numérique (CNC) aux États-Unis. Ces machines étaient programmées à l’aide de cartes perforées pour effectuer des tâches répétitives. À mesure que les ordinateurs ont évolué, la FAO a suivi, permettant des niveaux croissants d’automatisation et de précision dans les processus de fabrication.
Dans les années 1970, les avancées en CAO ont permis l’intégration de ces logiciels avec des systèmes FAO, ce qui a marqué le début d’une nouvelle ère pour la production industrielle. Depuis lors, la FAO n’a cessé de progresser, et aujourd’hui, elle est utilisée dans presque tous les secteurs de fabrication, allant de l’industrie aérospatiale à la production de biens de consommation.
Types de Machines Utilisées en FAO
La FAO est utilisée pour contrôler une grande variété de machines-outils, chacune adaptée à des tâches spécifiques. Voici quelques exemples des machines les plus couramment utilisées dans les systèmes FAO :
- Fraiseuses CNC : Les fraiseuses sont utilisées pour enlever de la matière d’un bloc en métal ou en plastique afin de créer des formes et des contours complexes. Les fraiseuses CNC (à commande numérique) peuvent effectuer des mouvements dans plusieurs directions simultanément, ce qui permet de créer des géométries tridimensionnelles très complexes.
- Tours CNC : Les tours sont principalement utilisés pour produire des pièces cylindriques ou coniques. Ils fonctionnent en faisant tourner la pièce tandis qu’un outil de coupe enlève la matière. Les tours CNC permettent de contrôler avec précision la vitesse de rotation et les mouvements de coupe pour produire des pièces très précises.
- Découpeuses Laser et Jet d’Eau : Ces machines utilisent des faisceaux laser ou des jets d’eau à haute pression pour découper des matériaux. Elles sont idéales pour les matériaux qui seraient difficiles à usiner avec des outils traditionnels, comme les métaux durs, les céramiques, ou même certains matériaux composites.
- Imprimantes 3D : Bien que traditionnellement associée à la FAO soustractive (qui enlève de la matière), la FAO peut aussi inclure des techniques additives, comme l’impression 3D. Les imprimantes 3D construisent des objets couche par couche à partir de matériaux plastiques, métalliques ou composites.
Applications de la FAO
La FAO est utilisée dans une multitude d’industries, offrant des avantages en termes de précision, d’efficacité, et de contrôle qualité.
- Aéronautique et Aérospatial : Dans l’industrie aéronautique, la précision est primordiale. La FAO est utilisée pour fabriquer des pièces d’avions, telles que des ailettes de turbine, des composants de moteur, et des structures en aluminium et en titane. Ces pièces doivent respecter des tolérances extrêmement strictes et être fabriquées à partir de matériaux avancés et légers.
- Automobile : L’industrie automobile utilise la FAO pour produire une grande variété de composants, des pièces de moteur aux carrosseries de voitures. En plus de garantir la précision, la FAO permet de produire des pièces en grande série avec des variations minimales d’une pièce à l’autre.
- Médical : Dans le secteur médical, la FAO est utilisée pour fabriquer des implants sur mesure, des prothèses et des outils chirurgicaux. Les machines-outils à commande numérique permettent de produire des dispositifs médicaux complexes, comme des implants dentaires ou des prothèses de hanches, avec une précision très élevée.
- Électronique : Les fabricants d’électronique utilisent la FAO pour fabriquer des boîtiers et des composants de précision pour des dispositifs tels que les smartphones, les ordinateurs, et autres appareils électroniques. Ces produits nécessitent souvent une miniaturisation extrême et des tolérances strictes.
- Énergie : Dans l’industrie de l’énergie, la FAO est utilisée pour produire des composants critiques pour les centrales électriques, telles que des aubes de turbine et des pompes haute performance. La FAO permet également de fabriquer des pièces pour l’industrie pétrolière et gazière, où la résistance et la durabilité des matériaux sont essentielles.
Avantages de la FAO
La FAO offre plusieurs avantages par rapport aux méthodes de fabrication traditionnelles :
- Précision et Répétabilité : Grâce à la FAO, les machines-outils peuvent réaliser des opérations complexes avec une précision très élevée, souvent jusqu’à des tolérances de quelques microns. En outre, cette précision est maintenue sur de grandes séries de production, assurant une qualité constante d’une pièce à l’autre.
- Efficacité et Réduction des Coûts : La FAO permet de réduire le temps de fabrication en automatisant les opérations et en réduisant la nécessité d’une intervention humaine. Cela se traduit par une diminution des coûts de production et une augmentation de la productivité.
- Flexibilité : La FAO permet de produire une grande variété de pièces complexes sans avoir besoin de changer fréquemment les outils ou les machines. Cela permet aux fabricants de répondre rapidement aux demandes du marché et d’adapter les processus de production.
- Réduction des Erreurs : En réduisant l’intervention humaine dans le processus de fabrication, la FAO diminue les risques d’erreurs, augmentant ainsi la fiabilité des produits finaux.
Défis de la FAO
Malgré ses nombreux avantages, la FAO présente également des défis qu’il est essentiel de prendre en compte :
- Investissement Initial : Les machines CNC et les logiciels de FAO peuvent représenter un investissement initial important, notamment pour les petites entreprises. Cependant, cet investissement est souvent rapidement amorti grâce aux gains de productivité.
- Compétences Techniques : L’utilisation de la FAO nécessite des compétences techniques spécialisées, tant pour la programmation des machines que pour la maintenance des équipements. Les opérateurs doivent être formés à la compréhension des logiciels et des processus.
- Maintenance : Les machines à commande numérique nécessitent un entretien régulier pour fonctionner correctement. Une panne de machine peut entraîner des arrêts de production coûteux.
Conclusion
La Fabrication Assistée par Ordinateur (FAO) est un outil essentiel dans l’industrie moderne, permettant de produire des pièces avec une précision et une efficacité inégalées. Grâce à l’automatisation et à la programmation numérique, les entreprises peuvent réduire leurs coûts de production, améliorer la qualité des produits et répondre aux exigences toujours croissantes du marché. Avec l’évolution des technologies et l’intégration de nouvelles méthodes, telles que l’impression 3D, la FAO continuera d’évoluer, jouant un rôle central dans l’avenir de la fabrication.
Contrôle de la Qualité
Introduction
Le contrôle de la qualité est un processus essentiel dans l’industrie de la fabrication, visant à assurer que les produits répondent aux exigences spécifiées en termes de performance, de sécurité, de fiabilité, et d’uniformité. Ce processus couvre toutes les étapes de production, de la conception à la fabrication, en passant par les essais, les inspections et la vérification finale. Le contrôle de la qualité est fondamental pour garantir que les produits fabriqués respectent les normes industrielles et les attentes des clients, tout en réduisant les coûts de production liés aux défauts ou aux reprises.
L’importance du contrôle de la qualité s’est accrue avec la montée en puissance des industries modernes, notamment dans les secteurs de l’automobile, de l’aéronautique, de la santé et de l’électronique, où la moindre défaillance peut avoir des conséquences graves. Aujourd’hui, le contrôle de la qualité s’appuie sur une gamme d’outils et de méthodologies avancées pour détecter les erreurs de production avant qu’elles ne se propagent et pour optimiser les processus.
Concepts Fondamentaux du Contrôle de la Qualité
Le contrôle de la qualité repose sur plusieurs concepts clés qui guident son application dans les divers secteurs industriels.
- Normes de Qualité : Les normes de qualité définissent les caractéristiques spécifiques que les produits doivent respecter. Ces normes peuvent être internes à une entreprise ou imposées par des organismes de normalisation internationaux, tels que l’Organisation internationale de normalisation (ISO) ou des régulateurs sectoriels. Les normes de qualité incluent des critères sur la sécurité, la durabilité, la taille, la forme, la fonctionnalité et l’esthétique du produit.
- Tolérance et Précision : Dans la fabrication, la tolérance fait référence à la plage de variation acceptable des dimensions d’un produit par rapport à ses spécifications. La précision concerne la capacité à fabriquer des pièces qui se rapprochent le plus possible des dimensions idéales. Un contrôle strict des tolérances est crucial pour les produits qui doivent s’assembler parfaitement ou répondre à des exigences strictes de performance.
- Prévention des Défauts : L’une des approches modernes du contrôle de la qualité est axée sur la prévention des défauts plutôt que sur la simple détection. Cela se traduit par la mise en place de processus de contrôle proactifs tout au long de la chaîne de production afin d’identifier et d’éliminer les sources potentielles d’erreurs avant qu’elles ne se produisent.
- Amélioration Continue : Le contrôle de la qualité est un processus évolutif. Les entreprises cherchent constamment à améliorer la qualité de leurs produits et de leurs processus de fabrication. L’amélioration continue, souvent associée aux méthodes comme le Kaizen ou le Six Sigma, vise à analyser régulièrement les performances et à mettre en œuvre des ajustements pour accroître l’efficacité et la qualité globale.
Méthodes et Techniques de Contrôle de la Qualité
Le contrôle de la qualité englobe une variété de méthodes et de techniques pour s’assurer que les produits répondent aux normes requises.
- Inspection Visuelle : C’est la méthode la plus simple et la plus directe pour contrôler la qualité. Les opérateurs inspectent les produits à l’œil nu ou à l’aide d’outils simples pour vérifier s’ils présentent des défauts visibles, comme des rayures, des fissures, ou des déformations. Bien que cette méthode soit utile pour détecter les défauts évidents, elle peut être sujette à des erreurs humaines, surtout dans le cadre de productions à grande échelle.
- Contrôle Dimensionnel : Ce contrôle consiste à vérifier que les dimensions des pièces produites correspondent aux spécifications définies. Des instruments tels que des pieds à coulisse, des micromètres, ou des machines de mesure tridimensionnelle (CMM) sont utilisés pour mesurer les dimensions critiques des pièces.
- Contrôle Non Destructif (CND) : Les méthodes de contrôle non destructif sont utilisées pour détecter les défauts internes ou invisibles à l’œil nu sans endommager les produits. Ces techniques incluent les ultrasons, les rayons X, la radiographie, et les tests magnétiques. Elles sont particulièrement utiles dans les industries où les produits doivent conserver leur intégrité après l’inspection, comme dans l’aérospatiale ou l’industrie pétrolière.
- Contrôle Statistique : Le contrôle statistique de la qualité repose sur l’utilisation de données pour surveiller et contrôler les processus de fabrication. Des échantillons de produits sont régulièrement prélevés, et les mesures sont comparées aux spécifications pour détecter toute variation anormale. Les outils statistiques, tels que les cartes de contrôle ou les diagrammes de Pareto, permettent d’identifier les tendances et de prendre des décisions informées pour corriger les processus.
- Contrôle Fonctionnel : Ce type de contrôle implique de tester les produits dans des conditions d’utilisation réelles ou simulées pour s’assurer qu’ils fonctionnent comme prévu. Cela peut inclure des tests de performance, de résistance, ou de durabilité. Par exemple, dans l’industrie automobile, les composants de freinage sont soumis à des tests rigoureux pour vérifier leur efficacité dans différentes conditions de conduite.
- Essais Destructifs : Contrairement au contrôle non destructif, les essais destructifs consistent à soumettre les produits à des conditions extrêmes jusqu’à ce qu’ils échouent. Ces essais permettent de déterminer les limites des produits et de s’assurer qu’ils sont suffisamment résistants pour répondre aux attentes des utilisateurs finaux.
Outils de Contrôle de la Qualité
Pour mettre en œuvre efficacement le contrôle de la qualité, plusieurs outils et méthodologies sont couramment utilisés dans l’industrie.
- Diagrammes de Contrôle : Les diagrammes de contrôle sont utilisés pour surveiller les variations dans les processus de production. Ils permettent aux ingénieurs d’identifier les variations normales (inhérentes au processus) et anormales (dus à des erreurs ou des dysfonctionnements). Cela permet d’anticiper les problèmes avant qu’ils ne deviennent critiques.
- Diagramme d’Ishikawa : Aussi appelé diagramme de causes et effets ou diagramme en arête de poisson, cet outil permet de visualiser les différentes causes potentielles d’un problème de qualité. Il aide les équipes à identifier les sources possibles de défauts et à développer des solutions correctives.
- Analyse PARETO : Cette technique est basée sur le principe 80/20, qui stipule que 80 % des problèmes de qualité proviennent de 20 % des causes. L’analyse Pareto permet d’identifier et de prioriser les problèmes qui ont le plus grand impact sur la qualité, afin de concentrer les efforts de correction sur les domaines les plus critiques.
- Six Sigma : Six Sigma est une méthodologie de gestion de la qualité qui vise à réduire les défauts et les variations dans les processus de production. En utilisant des outils statistiques, Six Sigma permet d’optimiser les processus et d’améliorer la qualité globale des produits. Il repose sur une approche structurée de résolution de problèmes appelée DMAIC (Définir, Mesurer, Analyser, Innover et Contrôler).
Normes et Certifications de Qualité
De nombreuses industries sont soumises à des normes de qualité strictes, et les entreprises doivent souvent obtenir des certifications pour prouver leur conformité.
- ISO 9001 : La norme ISO 9001 est une norme internationale qui définit les exigences d’un système de management de la qualité. Elle est applicable à tout type d’organisation, quelle que soit sa taille ou son secteur d’activité. Cette certification permet de démontrer que l’entreprise est engagée dans une démarche de qualité et qu’elle est en mesure de fournir des produits ou des services conformes aux exigences des clients.
- ISO/TS 16949 : Cette norme est spécifique à l’industrie automobile et vise à garantir que les produits respectent les exigences des clients et les réglementations applicables. Elle englobe les processus de production, de conception, et de contrôle de la qualité.
- AS9100 : Utilisée principalement dans l’industrie aérospatiale, la norme AS9100 impose des exigences spécifiques pour assurer la qualité et la sécurité des produits utilisés dans les avions et autres appareils aérospatiaux.
- Certifications Médicales (ISO 13485) : Dans l’industrie des dispositifs médicaux, la norme ISO 13485 établit les critères pour un système de management de la qualité spécifiquement adapté à la fabrication de produits médicaux. Cette norme assure que les produits répondent aux réglementations strictes en matière de santé et de sécurité.
Avantages du Contrôle de la Qualité
La mise en œuvre d’un système de contrôle de la qualité rigoureux présente de nombreux avantages pour les entreprises.
- Amélioration de la Satisfaction Client : En garantissant que les produits répondent ou dépassent les attentes des clients, le contrôle de la qualité contribue à augmenter la satisfaction client, renforcer la fidélité, et améliorer la réputation de l’entreprise.
- Réduction des Coûts : Les défauts de production peuvent entraîner des coûts élevés, notamment en termes de retours de produits, de remplacements, et de pertes de production. Un bon système de contrôle de la qualité permet de minimiser ces défauts et de réduire les coûts associés aux produits défectueux.
- Augmentation de l’Efficacité : En identifiant et en éliminant les sources d’erreurs, le contrôle de la qualité permet d’optimiser les processus de production, ce qui se traduit par une amélioration de l’efficacité opérationnelle.
- Conformité Réglementaire : De nombreuses industries sont soumises à des réglementations strictes en matière de qualité. Un contrôle de la qualité efficace permet aux entreprises de se conformer à ces réglementations, évitant ainsi des sanctions potentielles.
Défis du Contrôle de la Qualité
Malgré ses nombreux avantages, le contrôle de la qualité peut présenter certains défis pour les entreprises.
- Coût Initial : La mise en place d’un système de contrôle de la qualité peut être coûteuse, en particulier pour les petites entreprises. Cela inclut l’achat d’équipements de test, la formation du personnel, et la mise en œuvre de processus de contrôle rigoureux.
- Complexité : Dans certaines industries, les processus de contrôle de la qualité peuvent être très complexes et nécessiter des compétences techniques spécialisées. Cela peut rendre difficile la gestion du contrôle de la qualité pour certaines entreprises.
- Ressources Humaines : Le contrôle de la qualité nécessite du personnel qualifié capable de réaliser des tests, des inspections, et des analyses. Trouver et former ce personnel peut représenter un défi, notamment dans les secteurs où les compétences spécialisées sont rares.
Conclusion
Le contrôle de la qualité est un élément clé de tout processus de fabrication réussi, garantissant que les produits respectent les normes attendues et que les entreprises peuvent maintenir leur compétitivité sur le marché mondial. En intégrant des outils avancés, des techniques d’amélioration continue, et des normes rigoureuses, les entreprises peuvent non seulement assurer la satisfaction de leurs clients, mais aussi réduire les coûts de production et améliorer l’efficacité globale.
- Presses Mécaniques
- Fonctionnement: Utilisent l’énergie cinétique générée par un volant d’inertie pour produire la force nécessaire à l’emboutissage.
- Caractéristiques: Vitesse élevée, adaptées aux opérations de production en grande série.
- Applications: Principalement utilisées pour les opérations nécessitant des cadences de production rapides.
- Presses Hydrauliques
- Fonctionnement: Utilisent un fluide hydraulique pour générer la force d’emboutissage.
- Caractéristiques: Force de pression constante, capacité à gérer des opérations complexes avec des forces de formage élevées.
- Applications: Adaptées pour les pièces de grande taille, les matériaux épais et les opérations nécessitant une grande précision.
- Presses Servo-électriques
- Fonctionnement: Utilisent des moteurs électriques et des vis à billes pour générer la force de formage.
- Caractéristiques: Haute précision et contrôle de la vitesse, efficacité énergétique.
- Applications: Idéales pour les opérations nécessitant un contrôle précis des paramètres de formage.
Processus de Fonctionnement des Presses d’Emboutissage
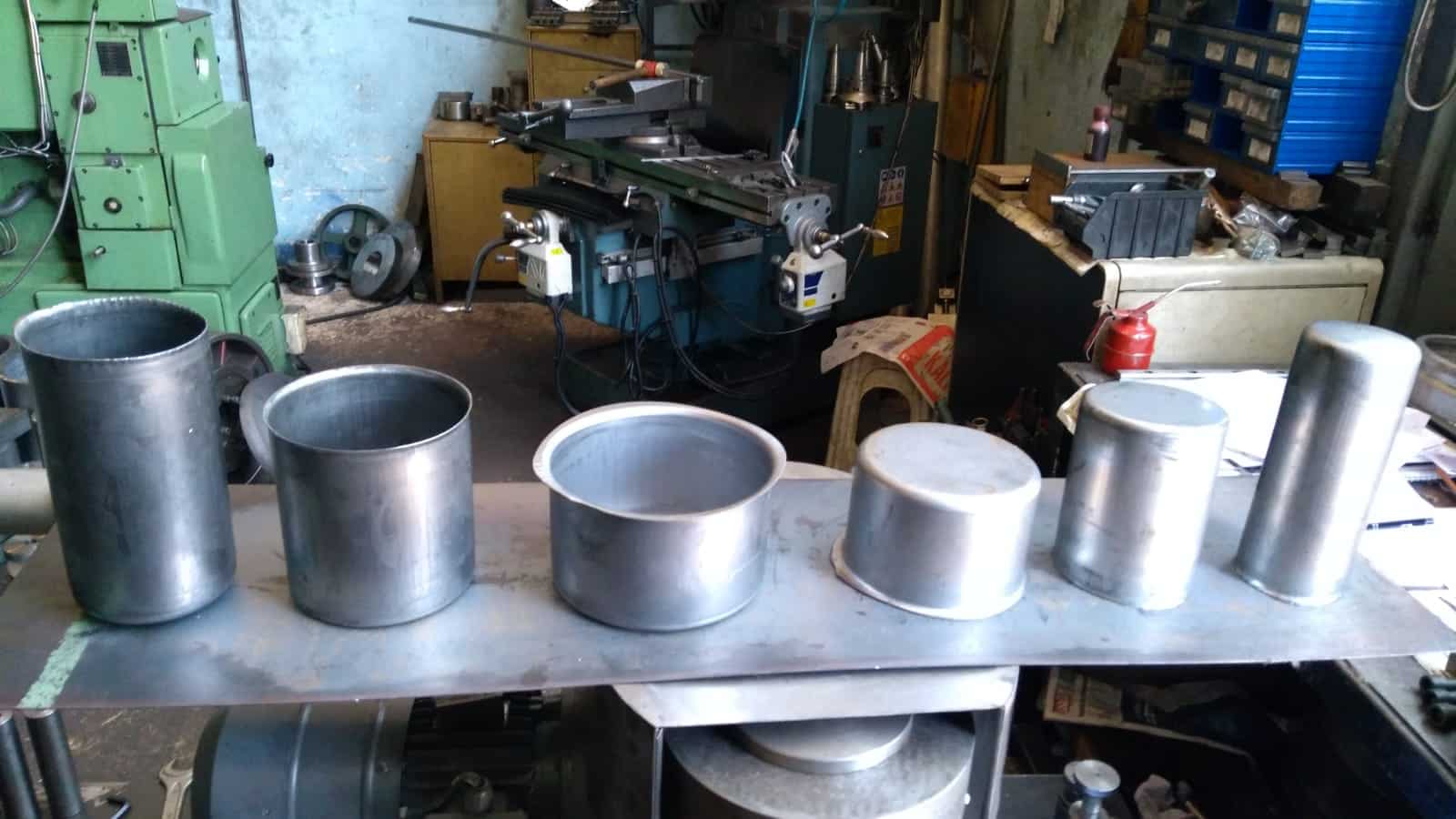
- Préparation de la Feuille de Métal: La feuille de métal est positionnée sur la matrice inférieure de la presse.
- Mise en Place du Poinçon: Le poinçon descend pour entrer en contact avec la feuille de métal.
- Déformation de la Feuille: La pression appliquée par le poinçon déforme la feuille selon la forme de la matrice.
- Éjection de la Pièce: Après l’emboutissage, la pièce formée est éjectée de la matrice.
Presse hydraulique d’emboutissage Double Action et Triple Action

Presse à Emboutir Double Action
- Caractéristiques: Comprend deux pistons ou vérins indépendants.
- Piston de Serrage: Maintient la feuille de métal en place.
- Piston d’Emboutissage: Effectue l’opération d’emboutissage.
- Avantages: Permet de contrôler le serrage et l’emboutissage séparément, réduisant les risques de plis et de déformations indésirables.
- Applications: Utilisée pour des pièces nécessitant un contrôle précis de la pression de serrage et de formage, comme dans l’industrie automobile pour les grandes pièces de carrosserie.
Presse hydraulique d’emboutissage Triple Action
- Caractéristiques: Comprend trois pistons ou vérins indépendants.
- Premier Piston: Maintient la feuille de métal.
- Deuxième Piston: Réalise un pré-emboutissage.
- Troisième Piston: Finalise la forme de la pièce.
- Avantages: Offre un contrôle encore plus précis et permet de réaliser des formes très complexes avec une répartition uniforme de la pression.
- Applications: Utilisée pour des pièces très détaillées nécessitant plusieurs étapes de formage, comme les panneaux de carrosserie avec des caractéristiques spécifiques.
Applications des Presses d’Emboutissage
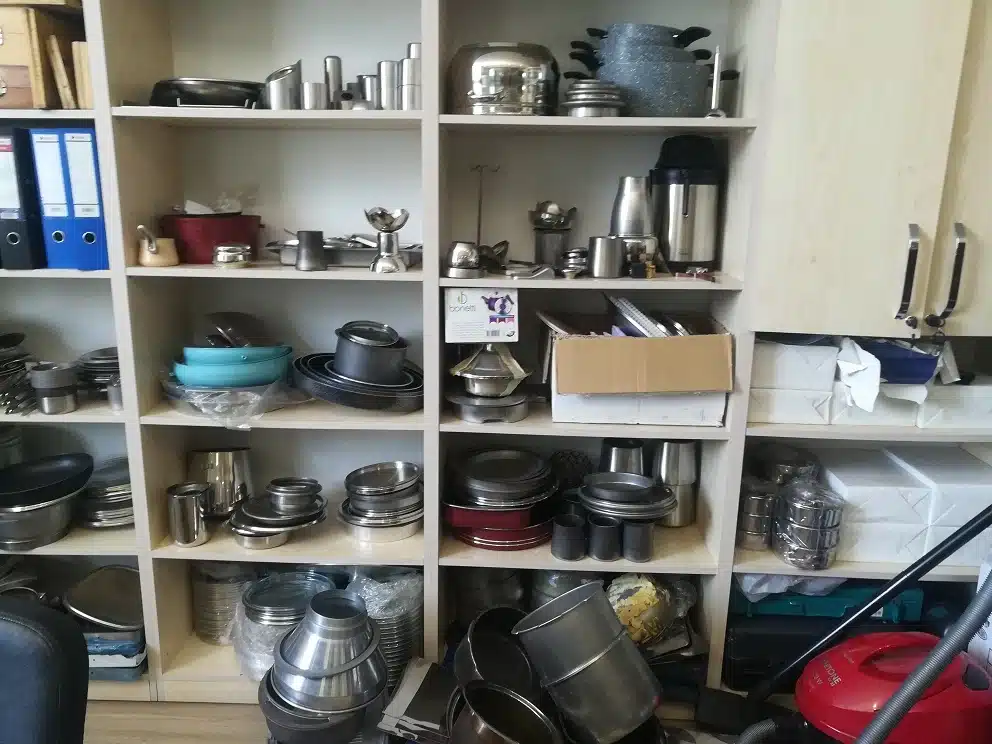
- Industrie Automobile
- Fabrication de panneaux de carrosserie, de capots, de portes et d’autres composants structurels.
- Utilisation de presses double action et triple action pour des pièces complexes et de grande taille.
- Aéronautique
- Production de composants structurels légers et résistants, tels que des panneaux de fuselage.
- Utilisation de presses hydrauliques et servo-électriques pour la précision et le contrôle.
- Électroménager
- Fabrication de pièces pour des appareils ménagers, comme des boîtiers de réfrigérateurs et de lave-linge.
- Utilisation de presses mécaniques pour les opérations de grande série.
- Électronique
- Production de boîtiers et de composants électroniques nécessitant des formes précises.
- Utilisation de presses servo-électriques pour un contrôle précis.
Conclusion
Les presses d’emboutissage jouent un rôle crucial dans la fabrication de pièces métalliques complexes et précises. Le choix du type de presse dépend de la complexité des pièces à fabriquer, des exigences de production et des matériaux utilisés. Les presses double action et triple action offrent des capacités avancées pour les opérations de formage nécessitant un contrôle précis et une répartition uniforme de la pression, permettant ainsi de répondre aux besoins exigeants des industries modernes.
Presse hydraulique d’emboutissage
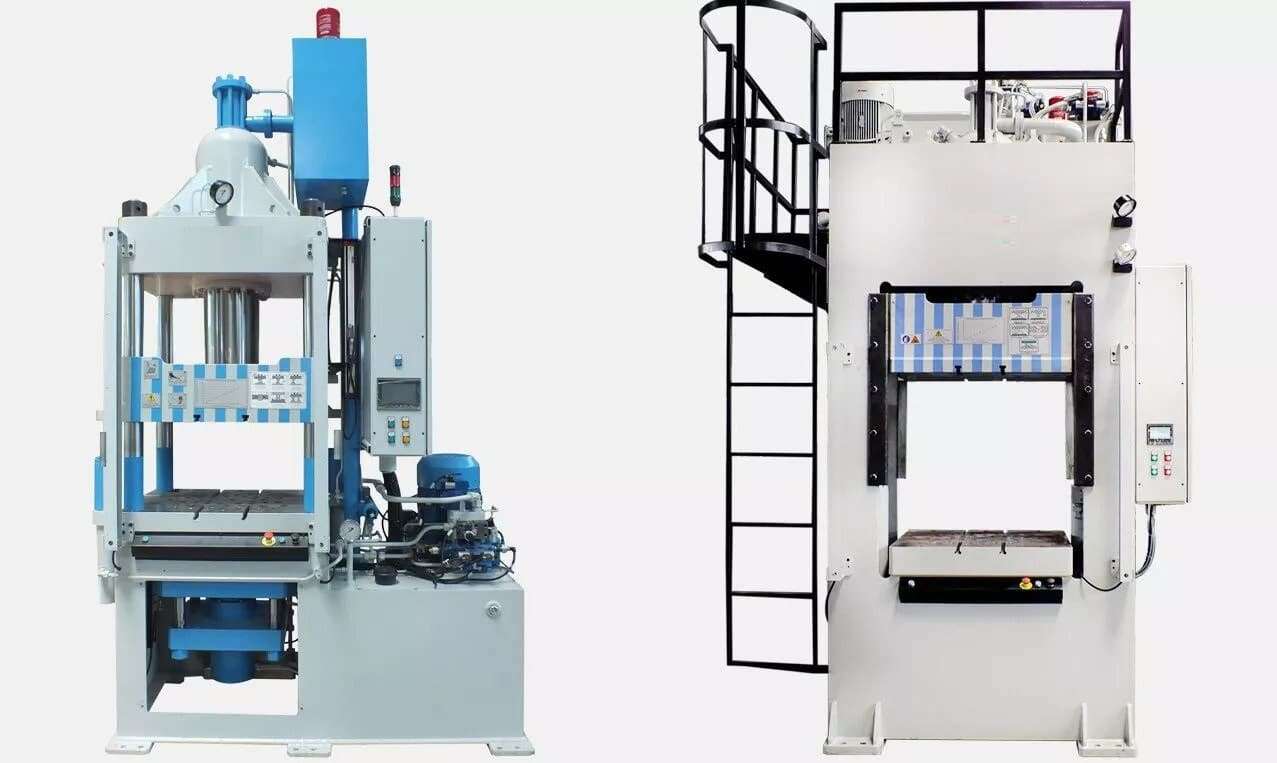
La presse hydraulique d’emboutissage est une machine industrielle essentielle pour transformer des feuilles de métal en pièces tridimensionnelles par déformation plastique. Utilisant la puissance de l’hydraulique, elle offre une grande précision, une force de formage élevée et une flexibilité dans les opérations de fabrication.
Caractéristiques et Fonctionnement
Caractéristiques
- Force de Pression Élevée: Les presses hydrauliques peuvent générer une force de pression très élevée, adaptée aux matériaux épais et durs.
- Contrôle Précis: La force et la vitesse de pressage peuvent être contrôlées précisément, permettant des opérations de formage complexes.
- Flexibilité: Les presses hydrauliques sont polyvalentes et peuvent être utilisées pour une variété d’opérations telles que le pliage, l’emboutissage, le découpage et le formage.
- Uniformité de la Force: La pression appliquée est uniforme, ce qui est crucial pour éviter les défauts de formage.
Fonctionnement
- Cylindres Hydrauliques: La presse comprend des cylindres hydrauliques remplis de fluide sous pression.
- Pistons: Les pistons à l’intérieur des cylindres appliquent la force nécessaire pour déformer la feuille de métal.
- Contrôle de la Pression: Un système de contrôle régule la pression et la vitesse du fluide hydraulique pour assurer une force constante et précise.
- Cycle de Formage:
- Chargement: La feuille de métal est placée sur la matrice inférieure.
- Serrage: La presse descend pour serrer la feuille en place.
- Emboutissage: Le piston applique la force hydraulique pour déformer la feuille selon la forme de la matrice.
- Retour: Après l’emboutissage, le piston remonte, et la pièce formée est éjectée.
Types de Presses Hydrauliques d’Emboutissage
Presses Hydrauliques Simple Action
https://www.youtube.com/embed/bT9ytRxlVtI?feature=oembedPresses Hydrauliques Simple Action
- Description: Utilisent un seul cylindre hydraulique.
- Applications: Utilisées pour des opérations d’emboutissage de base et de formage simple.
Presses Hydrauliques Double Action
https://www.youtube.com/embed/o3teYKvRcGk?feature=oembedPresses Hydrauliques Double Action
- Description: Comprennent deux cylindres hydrauliques, l’un pour le serrage et l’autre pour l’emboutissage.
- Avantages: Offrent un meilleur contrôle de la feuille de métal pendant le formage, réduisant les risques de plis et de déformations.
- Applications: Idéales pour les pièces complexes nécessitant un contrôle précis de la pression de serrage et de formage.
Presses Hydrauliques Triple Action
- Description: Comprennent trois cylindres hydrauliques, permettant un processus d’emboutissage en plusieurs étapes.
- Avantages: Permettent de réaliser des formes très complexes et détaillées grâce à un contrôle encore plus précis de la répartition de la pression.
- Applications: Utilisées pour des pièces de haute précision dans des industries comme l’automobile et l’aéronautique.
Applications des Presses Hydrauliques d’Emboutissage
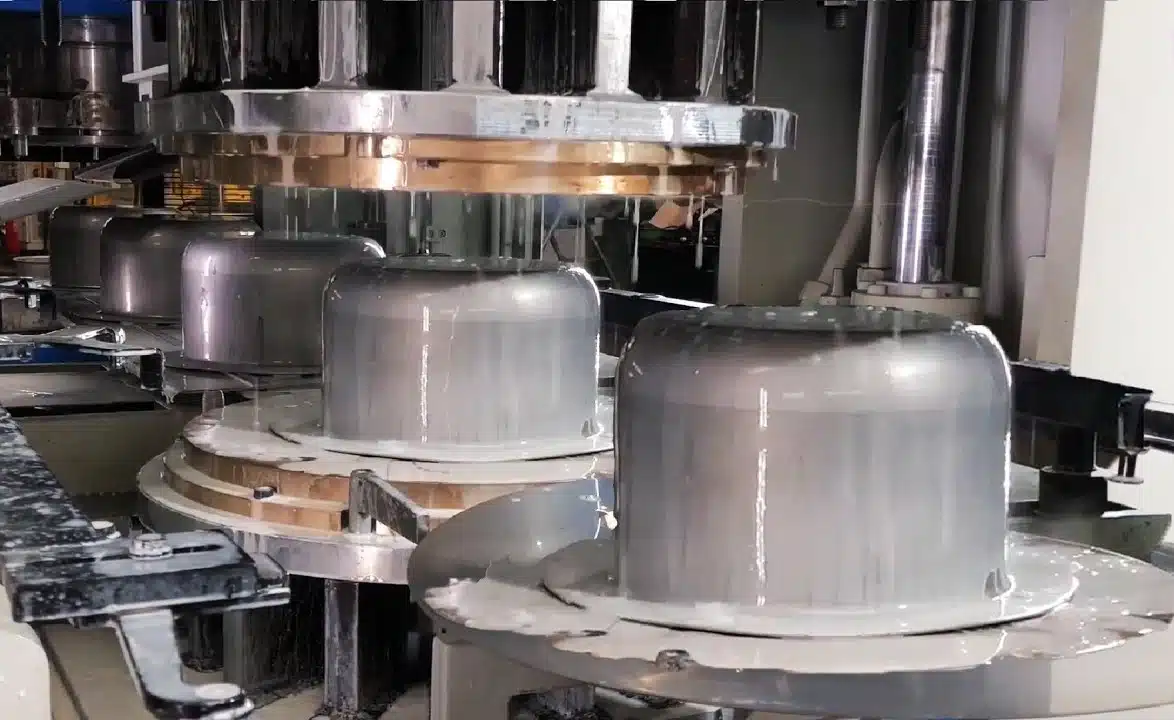
- Industrie Automobile
- Fabrication de panneaux de carrosserie, de capots, de portes et d’autres composants structurels.
- Utilisation de presses double et triple action pour des pièces complexes et de grande taille.
- Industrie Aéronautique
- Production de composants structurels légers et résistants, tels que des panneaux de fuselage.
- Précision et contrôle sont cruciaux pour les pièces utilisées dans l’aéronautique.
- Électroménager
- Fabrication de pièces pour des appareils ménagers, comme des boîtiers de réfrigérateurs et de lave-linge.
- Presses hydrauliques offrent la force nécessaire pour former des pièces de grande taille.
- Électronique
- Production de boîtiers et de composants électroniques nécessitant des formes précises.
- Contrôle précis de la force et de la vitesse est essentiel pour les pièces délicates.
Avantages des Presses Hydrauliques d’Emboutissage
- Force Puissante: Capacité de générer des forces de pressage très élevées, adaptées aux matériaux difficiles à travailler.
- Précision: Contrôle précis de la pression et de la vitesse, essentiel pour les opérations de formage complexe.
- Flexibilité: Polyvalence dans les opérations de formage, permettant une large gamme d’applications industrielles.
- Fiabilité: Moins de risques de surchauffe ou d’usure rapide par rapport aux presses mécaniques.
Conclusion
Les presses hydrauliques d’emboutissage sont des outils indispensables dans la fabrication industrielle, offrant une combinaison de puissance, de précision et de flexibilité. Elles permettent de réaliser des pièces complexes avec une grande uniformité et sont essentielles dans des industries où la qualité et la précision sont cruciales. Le choix entre une presse simple, double ou triple action dépend des exigences spécifiques de l’application et du niveau de complexité des pièces à fabriquer.
Emboutissage sur presses hydrauliques
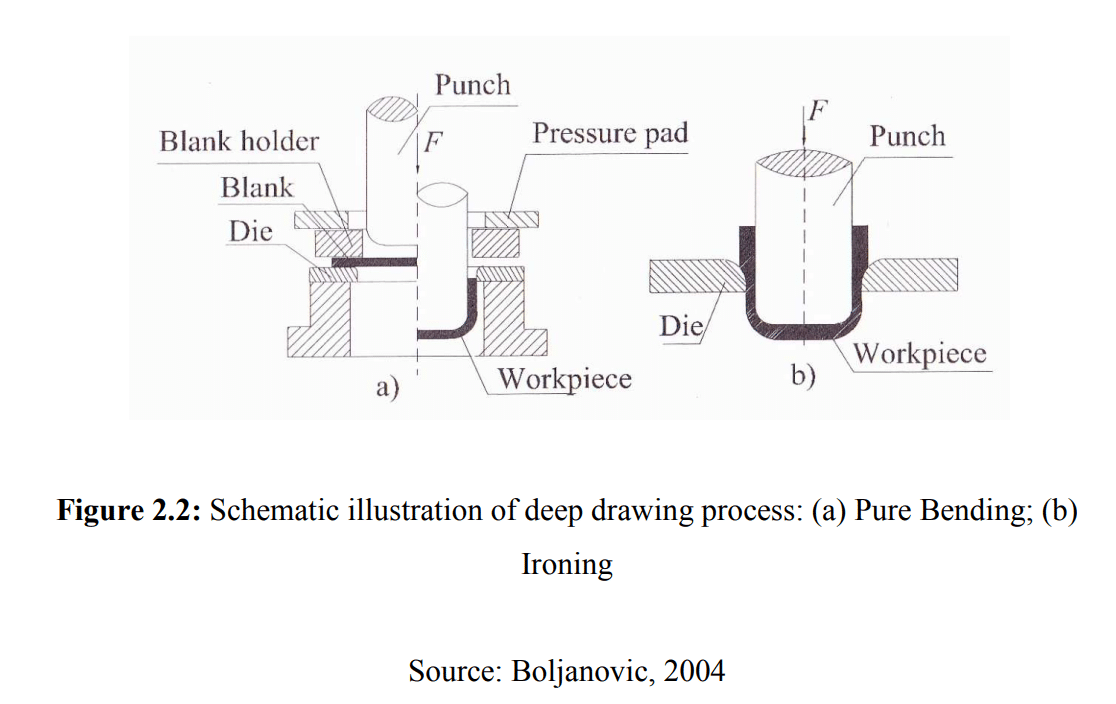
L’emboutissage sur presses hydrauliques est une technique couramment utilisée dans l’industrie pour transformer des feuilles de métal en pièces tridimensionnelles complexes. Les presses hydrauliques d’emboutissage exploitent la puissance des systèmes hydrauliques pour réaliser ces opérations avec précision et efficacité. Voici un aperçu détaillé de cette technologie et de ses applications.
Emboutissage sur Presses Hydrauliques

Principes de Base
- Pression Hydraulique: Utilise un fluide hydraulique (souvent de l’huile) pour générer la force nécessaire à l’emboutissage. La pression exercée par le fluide est transmise uniformément, permettant un contrôle précis de la force appliquée.
- Déformation Plastique: La feuille de métal est déformée de manière permanente pour prendre la forme de la matrice. Cette déformation est réalisée sans rupture du matériau, grâce à la répartition uniforme de la pression.
- Cycle de Travail:
- Chargement de la Feuille: La feuille de métal est positionnée sur la matrice inférieure.
- Serrage: La feuille est maintenue en place par le serre-flan pour éviter tout déplacement ou pliage involontaire.
- Emboutissage: Le poinçon descend et applique une pression contrôlée sur la feuille pour la former selon la matrice.
- Retour et Éjection: Le poinçon remonte, et la pièce formée est éjectée de la matrice.
Types de Presses Hydrauliques d’Emboutissage
Presse Simple Action
- Description: Utilise un seul vérin hydraulique pour l’emboutissage.
- Applications: Convient pour des opérations d’emboutissage simples et des pièces peu complexes.
Presse Double Action
- Description: Comprend deux vérins hydrauliques, un pour le serrage (serre-flan) et un pour l’emboutissage.
- Avantages: Meilleur contrôle sur le processus de formage, réduction des risques de plis et de déformations indésirables.
- Applications: Utilisée pour des pièces plus complexes, comme les panneaux de carrosserie automobile.
Presse Triple Action
- Description: Comprend trois vérins hydrauliques, ajoutant une troisième action pour des opérations de formage encore plus complexes.
- Avantages: Permet de réaliser des pièces très complexes avec une grande précision et un contrôle optimal de la répartition de la pression.
- Applications: Idéale pour des pièces de haute précision nécessitant plusieurs étapes de formage.
Applications
- Industrie Automobile
- Fabrication de composants de carrosserie tels que les portes, les capots et les panneaux latéraux.
- Utilisation de presses double et triple action pour des pièces aux formes complexes et de grande taille.
- Industrie Aéronautique
- Production de pièces structurelles légères et résistantes comme les panneaux de fuselage.
- Presses hydrauliques permettent une grande précision et une uniformité des pièces.
- Électroménager
- Création de composants pour des appareils ménagers tels que les tambours de lave-linge et les panneaux de réfrigérateurs.
- Nécessite une force de formage élevée pour des pièces robustes et durables.
- Électronique
- Fabrication de boîtiers et de composants pour appareils électroniques.
- Précision nécessaire pour des pièces délicates et complexes.
Avantages des Presses Hydrauliques d’Emboutissage
- Force et Précision: Les presses hydrauliques offrent une force de pression constante et contrôlée, essentielle pour les opérations de formage complexes.
- Flexibilité: Elles peuvent être ajustées pour une variété d’opérations, permettant une grande polyvalence dans la production.
- Uniformité de la Pression: Assure une répartition homogène de la pression sur la feuille de métal, évitant les déformations et les défauts.
- Efficacité Énergétique: Les systèmes hydrauliques peuvent être plus efficaces énergétiquement comparés à d’autres types de presses, en particulier pour les cycles de travail longs et continus.
- Durabilité: Les composants des presses hydrauliques sont robustes et conçus pour une utilisation intensive, réduisant les coûts de maintenance et les temps d’arrêt.
Conclusion
Les presses hydrauliques d’emboutissage sont des outils essentiels dans de nombreuses industries pour la fabrication de pièces métalliques complexes. Leur capacité à exercer une force élevée et contrôlée avec précision les rend idéales pour des applications nécessitant une grande qualité et une uniformité des pièces produites. Que ce soit pour des composants automobiles, aéronautiques, électroménagers ou électroniques, les presses hydrauliques d’emboutissage offrent des solutions flexibles et efficaces pour répondre aux exigences modernes de fabrication.
Machines pour le formage de tôles
Les machines pour le formage de tôles sont des équipements industriels utilisés pour transformer des feuilles métalliques en différentes formes et dimensions. Ces machines jouent un rôle crucial dans de nombreuses industries telles que l’automobile, l’aérospatiale, la construction, et l’électronique. Voici une description détaillée des principaux types de machines de formage de tôles, leurs fonctions, et leurs applications :
Types de Machines de Formage de Tôles
1. Presse-Plieuse
La presse-plieuse est une machine essentielle pour plier les tôles selon des angles précis. Elle utilise un poinçon et une matrice pour appliquer une force sur la tôle, créant ainsi des plis droits ou courbés.
Composants principaux :
- Bâti : Structure solide qui supporte la machine.
- Vérin hydraulique ou mécanique : Génère la force nécessaire pour plier la tôle.
- Poinçon et matrice : Outils interchangeables qui déterminent la forme du pli.
Applications :
- Fabrication de pièces de carrosserie automobile.
- Production de composants de construction métallique.
- Création de boîtiers et de châssis pour équipements électroniques.
2. Cisaille Guillotine
La cisaille guillotine est utilisée pour couper les tôles en morceaux de dimensions spécifiques. Elle utilise une lame supérieure mobile et une lame inférieure fixe pour effectuer des coupes nettes.
Composants principaux :
- Cadre : Structure qui maintient les lames en place.
- Lame supérieure et inférieure : Lames tranchantes qui coupent la tôle.
- Système hydraulique ou mécanique : Fournit la force de coupe.
Applications :
- Découpage de tôles pour la fabrication de pièces.
- Préparation de matériaux pour des opérations de pliage ou de formage ultérieures.
- Fabrication de panneaux et de plaques métalliques.
3. Presse à Emboutir
La presse à emboutir est utilisée pour former des pièces tridimensionnelles à partir de tôles plates en utilisant des matrices et des poinçons. Elle est particulièrement utile pour créer des formes complexes et profondes.
Composants principaux :
- Cadre : Structure solide qui supporte la machine.
- Vérin hydraulique ou mécanique : Génère la force nécessaire pour l’emboutissage.
- Poinçon et matrice : Outils qui forment la tôle en la pressant dans la forme souhaitée.
Applications :
- Fabrication de pièces automobiles telles que des réservoirs et des capots.
- Production de pièces pour appareils électroménagers.
- Création de composants aérospatiaux.
4. Rouleuse
La rouleuse est une machine qui utilise des rouleaux pour courber les tôles en formes cylindriques ou coniques. Elle est essentielle pour la fabrication de tubes, de cylindres, et de réservoirs.
Composants principaux :
- Rouleaux : Cylindres en acier qui plient la tôle en la faisant passer entre eux.
- Système de réglage : Permet d’ajuster la distance entre les rouleaux pour contrôler le rayon de courbure.
- Moteur : Fournit la puissance nécessaire pour faire tourner les rouleaux.
Applications :
- Fabrication de conduits et de tuyaux.
- Production de réservoirs et de cylindres.
- Création de structures métalliques courbes pour la construction.
5. Presse de Formage à Chaud
La presse de formage à chaud utilise la chaleur et la pression pour former des tôles en matériaux difficiles à travailler à froid, comme certains aciers et alliages.
Composants principaux :
- Four de chauffage : Utilisé pour chauffer la tôle à la température de formage.
- Presse hydraulique ou mécanique : Applique la force nécessaire pour former la tôle chauffée.
- Matrice et poinçon : Déterminent la forme finale de la pièce.
Applications :
- Fabrication de composants de haute résistance pour l’automobile et l’aérospatiale.
- Production de pièces structurelles pour le bâtiment.
- Formage de matériaux réfractaires et difficiles à travailler.
Avantages des Machines de Formage de Tôles
- Précision : Ces machines permettent de réaliser des formes complexes avec une grande précision.
- Efficacité : Elles augmentent la vitesse de production et réduisent les coûts de main-d’œuvre.
- Flexibilité : Les outils interchangeables permettent de produire une grande variété de formes et de tailles.
- Qualité : Elles assurent une qualité constante des pièces produites, réduisant ainsi les erreurs et les déchets.
Conclusion
Les machines pour le formage de tôles sont essentielles pour de nombreuses industries manufacturières. Elles offrent des solutions efficaces et précises pour transformer des tôles en composants utilisables, répondant ainsi aux besoins variés des secteurs de l’automobile, de l’aérospatiale, de la construction, et bien d’autres. Avec l’évolution technologique, ces machines continuent de s’améliorer, offrant des capacités de production encore plus avancées et diversifiées.
Machines de Formage
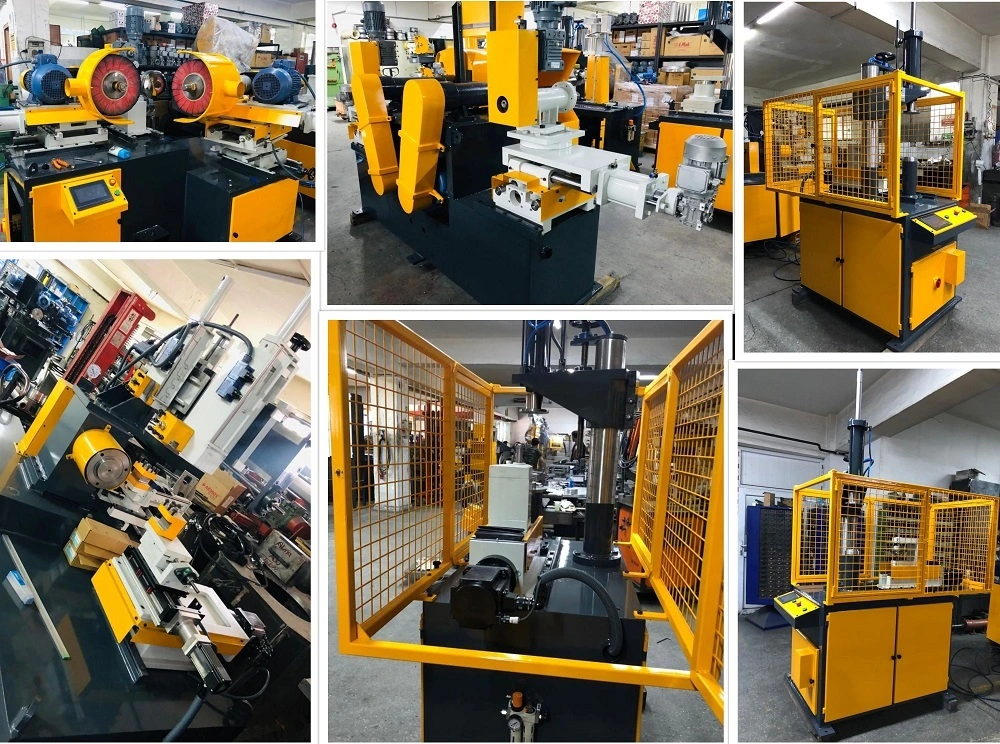
Dans l’industrie moderne, les machines de formage jouent un rôle essentiel dans la production de composants et de structures variées. Qu’il s’agisse de l’industrie automobile, aéronautique, électronique ou encore de la fabrication de biens de consommation, le formage des matériaux est un processus incontournable pour assurer la précision, la robustesse et la qualité des produits finis.
Les technologies industrielles de transformation des matériaux sont au cœur de l’évolution des secteurs manufacturiers modernes. Parmi ces technologies, les machines de formage et les presses occupent une place centrale dans les processus de fabrication et de production en masse. Ces machines permettent la transformation de matières premières en produits finis ou semi-finis, utilisés dans divers secteurs comme l’automobile, l’aérospatial, l’électroménager, et bien plus encore.
Les avancées technologiques dans ces équipements ont considérablement amélioré la précision, la rapidité et l’efficacité des procédés de production, répondant aux besoins croissants de l’industrie pour des produits de qualité supérieure, à des coûts compétitifs. Que ce soit pour des applications de formage, de découpe, de pliage ou d’emboutissage, ces machines constituent un maillon essentiel dans la chaîne de production industrielle. Dans ce contexte, ce guide vous présente en détail diverses catégories de machines et presses utilisées dans l’industrie métallurgique et manufacturière. Chaque section abordera un type spécifique de machine, ses caractéristiques, ses avantages et ses principales applications.
Le contenu suivant couvre des équipements allant des machines de formage aux presses hydrauliques, en passant par les machines de polissage et d’ébavurage, offrant ainsi une vue d’ensemble complète des technologies disponibles pour la transformation des métaux.
Machine de Formage
Les machines de formage jouent un rôle clé dans la transformation des métaux et d’autres matériaux à travers des procédés mécaniques, thermiques ou hydrauliques. Leur objectif principal est de façonner une pièce en lui donnant une forme prédéfinie, souvent sans enlever de matière, ce qui les distingue des procédés d’usinage ou de découpe.
Fonctionnement des Machines de Formage
Le principe de base d’une machine de formage repose sur l’application d’une force mécanique ou hydraulique pour déformer un matériau, généralement un métal, jusqu’à obtenir la forme désirée. Ce processus peut se dérouler à chaud ou à froid, selon la nature du matériau et le type de formage souhaité. Les machines de formage comprennent diverses catégories d’équipements, chacune adaptée à un type spécifique de transformation, comme le pliage, l’étirage, le cintrage ou le laminage.
Parmi les technologies de formage les plus utilisées, on trouve :
- Le formage à froid : utilisé principalement pour les métaux fins et ductiles, cette technique permet de déformer le matériau à température ambiante sans le chauffer, conservant ainsi ses propriétés mécaniques.
- Le formage à chaud : dans ce cas, le matériau est chauffé au-dessus de sa température de recristallisation, ce qui permet de faciliter sa déformation tout en limitant les contraintes internes.
Types de Machines de Formage
Il existe plusieurs types de machines de formage, en fonction de l’application spécifique :
- Machines de formage par étirage : ces machines sont souvent utilisées pour la production de grandes pièces, comme les panneaux de carrosserie dans l’industrie automobile.
- Machines de formage par pliage : adaptées au pliage de tôles métalliques, ces machines permettent de réaliser des angles précis sur des matériaux rigides.
- Machines de formage par laminage : elles servent principalement à réduire l’épaisseur d’un matériau, tout en augmentant sa longueur, très utilisées dans la production de feuilles de métal.
Avantages des Machines de Formage
Les machines de formage offrent plusieurs avantages dans le processus de fabrication industrielle :
- Efficacité : Elles permettent de transformer rapidement des matières premières en pièces finies ou semi-finies, réduisant ainsi les délais de production.
- Précision : Grâce aux innovations technologiques, ces machines peuvent produire des pièces aux tolérances très précises, même dans des matériaux difficiles à travailler.
- Réduction des pertes de matière : Contrairement à d’autres procédés comme l’usinage, le formage ne produit que très peu de déchets, ce qui en fait un processus plus économique et respectueux de l’environnement.
Applications Industrielles
Les machines de formage sont largement utilisées dans divers secteurs industriels :
- Automobile : pour la fabrication de châssis, de pièces de carrosserie, et autres composants critiques.
- Aéronautique : des pièces complexes et légères, telles que les structures d’aile et les panneaux de fuselage, sont souvent formées à l’aide de ces machines.
- Construction : dans la production de poutres, de barres et d’autres composants structurels utilisés dans les bâtiments et les infrastructures.
Presse à Emboutir

La presse à emboutir est une machine utilisée dans l’industrie pour transformer une feuille de métal en une forme tridimensionnelle complexe, grâce à un processus de déformation appelé emboutissage. Ce procédé est couramment utilisé dans la fabrication de pièces métalliques pour des industries telles que l’automobile, l’aéronautique, et l’électroménager.
Fonctionnement de la Presse à Emboutir
L’emboutissage est un processus de formage à froid, où une feuille métallique, appelée flan, est pressée entre une matrice et un poinçon. Le poinçon descend, déformant la feuille en lui donnant la forme souhaitée, généralement en une seule étape ou à travers une série de coups successifs pour des pièces plus complexes. Ce procédé permet de produire des formes précises et détaillées, souvent avec des géométries qui seraient difficiles, voire impossibles, à obtenir avec d’autres méthodes de fabrication.
Les presses à emboutir peuvent être actionnées mécaniquement, hydrauliquement ou via une combinaison des deux. Les presses hydrauliques sont couramment utilisées pour les opérations d’emboutissage profond, où de grandes forces sont nécessaires pour former des pièces aux formes complexes sans risque de déformation ou de fissuration du matériau.
Types de Presses à Emboutir
Il existe plusieurs types de presses à emboutir, chacune étant adaptée à des applications spécifiques :
- Presse mécanique : Utilisée pour des processus à grande vitesse, elle est plus adaptée à des opérations répétitives où la précision de chaque coup est essentielle.
- Presse hydraulique : Permet de mieux contrôler la pression et est plus adaptée pour les opérations nécessitant une grande force de formage, comme l’emboutissage profond.
- Presse servo-électrique : Combine la précision et le contrôle des presses hydrauliques avec la rapidité des presses mécaniques. Elle est idéale pour les opérations nécessitant à la fois rapidité et précision.
Avantages des Presses à Emboutir
Les presses à emboutir sont largement utilisées dans l’industrie pour plusieurs raisons :
- Productivité élevée : Ces machines permettent la production rapide de pièces complexes, souvent en une seule opération, ce qui augmente considérablement la cadence de fabrication.
- Flexibilité : Elles peuvent traiter une grande variété de matériaux, des métaux plus légers comme l’aluminium aux matériaux plus résistants comme l’acier inoxydable.
- Réduction des coûts : Grâce à leur efficacité et à leur capacité à produire des formes complexes en une seule opération, elles permettent de réduire les coûts de production par pièce, surtout dans les grandes séries.
- Précision et qualité : Les presses à emboutir modernes sont capables de produire des pièces avec des tolérances très serrées, minimisant ainsi les défauts et les rebuts.
Applications des Presses à Emboutir
L’emboutissage est un procédé essentiel dans diverses industries, notamment :
- Automobile : La fabrication des carrosseries de voitures, des portes, des capots, et d’autres pièces structurelles repose largement sur des presses à emboutir. La rapidité de production et la précision sont des atouts majeurs pour ce secteur.
- Aéronautique : Dans ce secteur, des pièces légères et complexes, telles que les carénages et les composants de structure d’aéronefs, sont souvent fabriquées par emboutissage pour assurer des tolérances strictes tout en minimisant le poids.
- Électroménager : Des composants tels que les coques extérieures des machines à laver, les tambours et les panneaux sont fréquemment produits par emboutissage, en raison de la précision et de la vitesse du processus.
Innovations Technologiques
Les presses à emboutir ont connu plusieurs évolutions ces dernières années, avec l’introduction de technologies avancées comme :
Emboutissage à chaud : Cette technique consiste à chauffer la feuille de métal avant de l’emboutir, ce qui permet de créer des pièces encore plus complexes tout en limitant le risque de fissuration.
L’emboutissage numérique : Des logiciels de simulation permettent désormais de prévoir et d’optimiser le processus d’emboutissage avant même de commencer la production, réduisant ainsi les erreurs et améliorant la qualité du produit fini.
Presses à emboutissage automatique : Ces presses automatisées augmentent la cadence de production tout en minimisant les erreurs humaines, ce qui est crucial dans des industries où la précision est primordiale.
EMS Machines de Formage
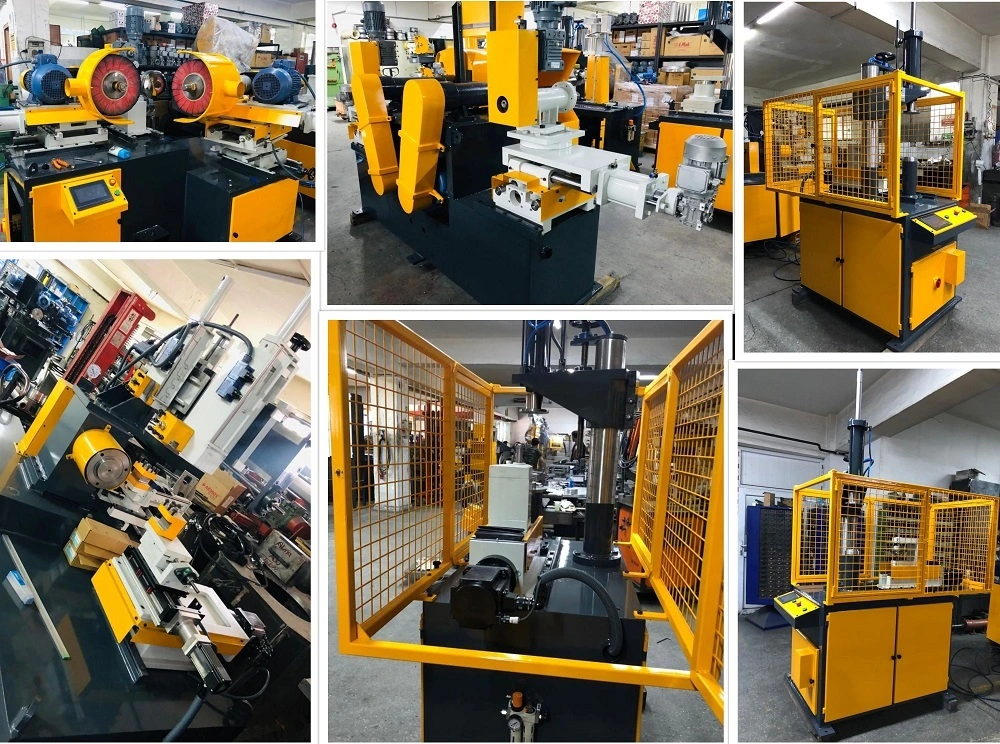
Le formage du métal est un processus consistant à façonner le métal dans la forme et la taille souhaitées à l’aide de diverses techniques. Il s’agit d’un processus crucial dans l’industrie manufacturière car il permet la production de différents produits tels que des pièces automobiles, des composants d’avion, des appareils électroménagers et bien d’autres encore.
Le processus de formage du métal consiste à appliquer une force sur le métal pour changer sa forme sans enlever aucune matière. La force peut être appliquée par diverses méthodes telles que le forgeage, le laminage, l’extrusion, l’étirage et l’estampage. Chaque méthode a ses propres avantages et inconvénients, et le choix de la méthode dépend du matériau formé et de la forme souhaitée.
Le forgeage est l’une des techniques de formage des métaux les plus anciennes. Il s’agit de chauffer le métal à haute température, puis d’appliquer une force de compression à l’aide d’un marteau ou d’une presse pour donner au métal la forme souhaitée. Le forgeage est couramment utilisé pour produire de grandes pièces telles que des engrenages, des essieux et des bielles.
Le laminage est une autre technique de formage du métal qui consiste à faire passer le métal à travers une paire de rouleaux pour réduire son épaisseur ou modifier sa forme. Les rouleaux peuvent être lisses ou texturés selon la finition souhaitée. Le laminage est couramment utilisé pour produire des tôles plates, des plaques et des barres.
L’extrusion est une technique de formage du métal qui consiste à pousser une billette ou une tige métallique à travers une matrice pour créer une forme spécifique. L’extrusion peut être utilisée pour produire des formes complexes telles que des tubes, des canaux et des angles.
L’emboutissage est une technique de formage des métaux utilisée pour réaliser des pièces de forme cylindrique, comme des tubes ou des tuyaux. Le processus consiste à tirer le métal à travers une matrice pour réduire son diamètre et augmenter sa longueur. Le tréfilage est couramment utilisé dans la production de fils, de tiges et de tubes.
L’emboutissage est une technique de formage du métal qui consiste à couper, poinçonner ou plier le métal dans une forme spécifique à l’aide d’une matrice. Le processus peut être utilisé pour produire des pièces avec une grande précision et répétabilité. L’estampage est couramment utilisé dans la production de pièces automobiles, d’appareils électroménagers et d’appareils électroniques.
En plus de ces techniques, il existe de nombreuses autres méthodes de formage des métaux telles que le filage, l’emboutissage profond et l’hydroformage. Chaque méthode a ses propres avantages et inconvénients, et le choix de la méthode dépend des exigences spécifiques du produit fabriqué.
Le formage des métaux est un processus complexe qui nécessite un haut niveau de compétence et d’expertise. Le succès du processus dépend de nombreux facteurs tels que le type de matériau formé, l’équipement utilisé et l’expérience de l’opérateur. En comprenant les différentes techniques de formage des métaux et en choisissant la méthode adaptée au travail, les fabricants peuvent produire des pièces de haute qualité qui répondent aux besoins spécifiques de leurs clients.
EMS Machines de Formage
Le formage du métal est un processus consistant à façonner le métal dans la forme et la taille souhaitées à l’aide de diverses techniques. Il s’agit d’un processus crucial dans l’industrie manufacturière car il permet la production de différents produits tels que des pièces automobiles, des composants d’avion, des appareils électroménagers et bien d’autres encore.
Le processus de formage du métal consiste à appliquer une force sur le métal pour changer sa forme sans enlever aucune matière. La force peut être appliquée par diverses méthodes telles que le forgeage, le laminage, l’extrusion, l’étirage et l’estampage. Chaque méthode a ses propres avantages et inconvénients, et le choix de la méthode dépend du matériau formé et de la forme souhaitée.
Le forgeage est l’une des techniques de formage des métaux les plus anciennes. Il s’agit de chauffer le métal à haute température, puis d’appliquer une force de compression à l’aide d’un marteau ou d’une presse pour donner au métal la forme souhaitée. Le forgeage est couramment utilisé pour produire de grandes pièces telles que des engrenages, des essieux et des bielles.
Le laminage est une autre technique de formage du métal qui consiste à faire passer le métal à travers une paire de rouleaux pour réduire son épaisseur ou modifier sa forme. Les rouleaux peuvent être lisses ou texturés selon la finition souhaitée. Le laminage est couramment utilisé pour produire des tôles plates, des plaques et des barres.
L’extrusion est une technique de formage du métal qui consiste à pousser une billette ou une tige métallique à travers une matrice pour créer une forme spécifique. L’extrusion peut être utilisée pour produire des formes complexes telles que des tubes, des canaux et des angles.
L’emboutissage est une technique de formage des métaux utilisée pour réaliser des pièces de forme cylindrique, comme des tubes ou des tuyaux. Le processus consiste à tirer le métal à travers une matrice pour réduire son diamètre et augmenter sa longueur. Le tréfilage est couramment utilisé dans la production de fils, de tiges et de tubes.
L’emboutissage est une technique de formage du métal qui consiste à couper, poinçonner ou plier le métal dans une forme spécifique à l’aide d’une matrice. Le processus peut être utilisé pour produire des pièces avec une grande précision et répétabilité. L’estampage est couramment utilisé dans la production de pièces automobiles, d’appareils électroménagers et d’appareils électroniques.
En plus de ces techniques, il existe de nombreuses autres méthodes de formage des métaux telles que le filage, l’emboutissage profond et l’hydroformage. Chaque méthode a ses propres avantages et inconvénients, et le choix de la méthode dépend des exigences spécifiques du produit fabriqué.
Le formage des métaux est un processus complexe qui nécessite un haut niveau de compétence et d’expertise. Le succès du processus dépend de nombreux facteurs tels que le type de matériau formé, l’équipement utilisé et l’expérience de l’opérateur. En comprenant les différentes techniques de formage des métaux et en choisissant la méthode adaptée au travail, les fabricants peuvent produire des pièces de haute qualité qui répondent aux besoins spécifiques de leurs clients.