Les presses à 4 colonnes sont un type de presse hydraulique ou mécanique, caractérisé par la présence de quatre colonnes qui supportent la structure de la presse. Ces colonnes assurent une distribution uniforme de la force sur la surface de travail, ce qui permet une précision et une stabilité accrues lors du processus de pressage. Les presses à 4 colonnes sont couramment utilisées dans les industries où des forces de pressage importantes et une grande précision sont nécessaires, telles que l’automobile, l’aéronautique, la métallurgie, et la fabrication de plastiques et de composites.
Caractéristiques principales des presses à 4 colonnes :
- Uniformité de la pression : Les quatre colonnes assurent une répartition homogène de la pression sur toute la surface de travail.
- Précision : La stabilité et la rigidité de la structure permettent un contrôle précis des opérations de pressage.
- Polyvalence : Elles peuvent être utilisées pour une variété d’applications, y compris le moulage, le forgeage, l’estampage, et le formage.
- Capacité de charge : Elles sont capables de gérer des charges très élevées, ce qui les rend adaptées aux tâches industrielles lourdes.
- Sécurité : Les systèmes modernes de presse à 4 colonnes sont souvent équipés de dispositifs de sécurité avancés pour protéger les opérateurs et les machines.
Applications courantes :
- Fabrication automobile : Pour le formage et l’assemblage des pièces de carrosserie et des composants.
- Industrie aéronautique : Pour le formage des pièces structurelles et des composants en alliages légers.
- Industrie métallurgique : Pour le forgeage, le formage et l’estampage des métaux.
- Fabrication de plastiques et composites : Pour le moulage sous pression et l’assemblage de pièces composites.
Uniformité de la pression
L’uniformité de la pression est une caractéristique cruciale des presses à 4 colonnes, car elle assure que la force appliquée est distribuée de manière homogène sur toute la surface de travail. Voici comment cela se réalise et pourquoi c’est important :
Comment l’uniformité de la pression est-elle assurée ?
- Structure Symétrique :
- Les quatre colonnes de la presse créent une structure symétrique qui maintient la platine supérieure parfaitement parallèle à la platine inférieure, même sous de fortes charges. Cela garantit que la pression est uniformément appliquée.
- Guidage Précis :
- Les colonnes servent de guides pour les mouvements de la platine supérieure, réduisant les déviations latérales et assurant un mouvement vertical précis. Cela aide à maintenir une distribution uniforme de la pression sur toute la surface de la pièce.
- Contrôle Hydraulique ou Mécanique :
- Les systèmes de contrôle modernes, qu’ils soient hydrauliques ou mécaniques, permettent de réguler avec précision la force appliquée. Les capteurs et les dispositifs de rétroaction surveillent constamment la pression et ajustent automatiquement les paramètres pour maintenir l’uniformité.
Importance de l’uniformité de la pression
- Qualité des Pièces :
- Une pression uniformément répartie assure une qualité de produit supérieure en évitant les défauts tels que les déformations, les fissures, ou les variations d’épaisseur. Cela est particulièrement critique dans des industries comme l’automobile et l’aéronautique, où la précision et la qualité sont primordiales.
- Durabilité des Outils :
- En évitant les points de pression excessifs, l’usure des outils est minimisée. Cela prolonge la durée de vie des matrices et autres composants de la presse, réduisant ainsi les coûts de maintenance et les interruptions de production.
- Sécurité :
- Une pression uniforme réduit les risques de défaillance de la machine ou de l’outil, contribuant ainsi à un environnement de travail plus sûr pour les opérateurs.
- Efficacité :
- Avec une répartition uniforme de la pression, les opérations de pressage peuvent être effectuées plus rapidement et de manière plus fiable, augmentant ainsi l’efficacité globale du processus de production.
Conclusion
L’uniformité de la pression dans une presse à 4 colonnes est essentielle pour assurer des opérations de pressage précises, fiables et de haute qualité. Les avantages en termes de qualité des pièces, durabilité des outils, sécurité et efficacité justifient largement l’investissement dans ce type de presse pour les applications industrielles exigeantes.
Contrôle Hydraulique

Le contrôle hydraulique est un aspect crucial des presses à 4 colonnes, offrant des avantages significatifs en termes de précision, de force, et de régulation. Voici une vue d’ensemble de comment fonctionne le contrôle hydraulique et pourquoi il est essentiel pour ces types de presses.
Fonctionnement du contrôle hydraulique
- Système de Pompe Hydraulique :
- Une pompe hydraulique génère la pression nécessaire pour faire fonctionner la presse. Cette pompe peut être à déplacement fixe ou variable, selon les besoins spécifiques de la presse.
- Fluides Hydrauliques :
- Le fluide hydraulique, généralement de l’huile, est utilisé pour transmettre la force. Il circule dans un circuit fermé, alimentant les cylindres hydrauliques de la presse.
- Cylindres Hydrauliques :
- Les cylindres hydrauliques convertissent l’énergie hydraulique en énergie mécanique. La pression du fluide pousse le piston dans le cylindre, créant la force nécessaire pour effectuer le pressage.
- Valves de Contrôle :
- Des valves de contrôle, y compris des valves de décharge, des valves directionnelles, et des valves de régulation de débit, sont utilisées pour contrôler le flux et la pression du fluide hydraulique. Elles permettent un contrôle précis du mouvement et de la force appliquée par la presse.
- Capteurs et Contrôle Électronique :
- Des capteurs surveillent les paramètres tels que la pression, la position du piston, et la vitesse. Ces informations sont transmises à un système de contrôle électronique qui ajuste les valves et la pompe pour maintenir les conditions de pressage souhaitées.
Avantages du contrôle hydraulique
- Force et Puissance :
- Les systèmes hydrauliques peuvent générer des forces très élevées, permettant à la presse de manipuler des matériaux robustes et épais. Cela est essentiel pour les applications industrielles lourdes.
- Précision :
- Le contrôle hydraulique permet une régulation très précise de la force et de la position, ce qui est crucial pour obtenir des tolérances serrées et des finitions de haute qualité sur les pièces pressées.
- Flexibilité :
- Les presses hydrauliques peuvent être facilement ajustées pour différents types de pressage en modifiant la pression, le débit, et les cycles de travail. Cela les rend adaptées à une large gamme d’applications.
- Uniformité de la Pression :
- Comme mentionné précédemment, le contrôle hydraulique aide à assurer une distribution uniforme de la pression sur toute la surface de travail, ce qui améliore la qualité et la consistance des produits finis.
- Sécurité :
- Les systèmes hydrauliques modernes sont équipés de dispositifs de sécurité avancés, comme des soupapes de surpression et des contrôles de surcharge, qui protègent à la fois la machine et les opérateurs.
Applications du contrôle hydraulique
- Formage de Métaux :
- Pour le formage, le forgeage, l’estampage et l’emboutissage de pièces métalliques.
- Moulage de Plastiques et Composites :
- Utilisé dans les presses pour le moulage par injection ou compression des plastiques et des composites.
- Assemblage :
- Pour l’assemblage de composants dans des industries telles que l’automobile et l’aéronautique.
Conclusion
Le contrôle hydraulique est une technologie clé qui permet aux presses à 4 colonnes de fonctionner avec une grande efficacité, précision et sécurité. Il offre la flexibilité nécessaire pour répondre aux exigences variées des applications industrielles modernes, tout en assurant une qualité et une uniformité exceptionnelles des produits finis.
Système de Pompe Hydraulique
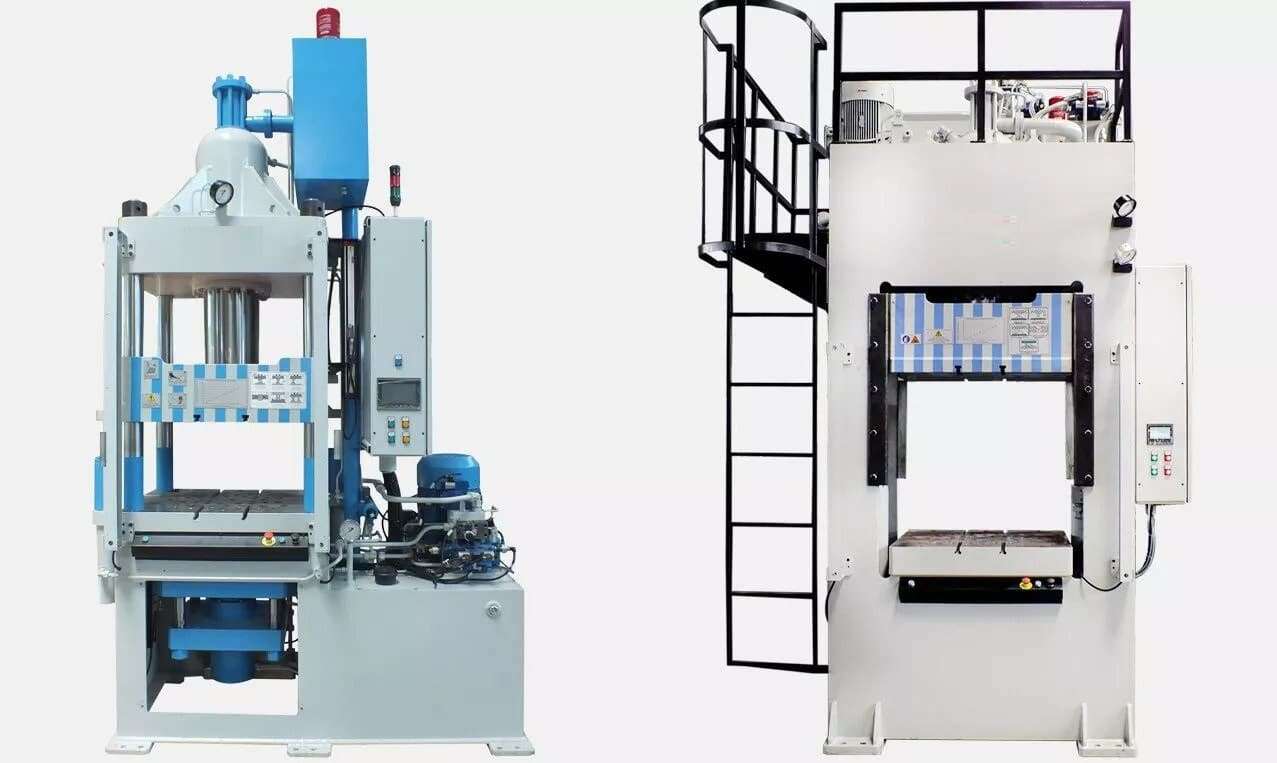
Le système de pompe hydraulique est un composant fondamental des presses à 4 colonnes, jouant un rôle crucial dans la génération et la régulation de la pression hydraulique nécessaire au fonctionnement de la presse. Voici une description détaillée du fonctionnement et des types de systèmes de pompes hydrauliques, ainsi que leurs avantages et applications.
Fonctionnement du Système de Pompe Hydraulique
- Génération de la Pression :
- La pompe hydraulique convertit l’énergie mécanique, généralement fournie par un moteur électrique, en énergie hydraulique en déplaçant le fluide hydraulique (souvent de l’huile) à travers le système. La pompe crée un flux de fluide à une certaine pression, ce qui permet de transmettre la force nécessaire pour faire fonctionner les cylindres hydrauliques de la presse.
- Circulation du Fluide :
- Le fluide hydraulique est aspiré dans la pompe depuis un réservoir, puis pompé à haute pression dans le circuit hydraulique. Le fluide circule ensuite vers les cylindres hydrauliques, où il exerce une force sur les pistons pour effectuer le travail de pressage.
- Contrôle de la Pression et du Débit :
- Des valves et des régulateurs de débit sont utilisés pour contrôler la pression et le débit du fluide hydraulique, permettant une régulation précise de la force et de la vitesse des cylindres hydrauliques.
Types de Pompes Hydrauliques
- Pompes à Engrenages :
- Les pompes à engrenages sont simples et robustes, souvent utilisées pour des applications nécessitant une pression modérée. Elles sont constituées de deux engrenages qui tournent en sens opposé pour déplacer le fluide hydraulique.
- Pompes à Piston :
- Les pompes à piston sont capables de générer des pressions très élevées et sont utilisées dans des applications nécessitant une force importante. Elles fonctionnent en utilisant des pistons alternatifs pour déplacer le fluide.
- Pompes à Palette :
- Les pompes à palette offrent un débit régulier et sont souvent utilisées dans des applications où un contrôle précis du débit est nécessaire. Elles utilisent des palettes montées sur un rotor pour déplacer le fluide.
- Pompes à Déplacement Variable :
- Ces pompes peuvent ajuster automatiquement le volume de fluide déplacé en fonction des besoins du système, permettant une efficacité énergétique accrue et une meilleure régulation de la pression.
Avantages des Systèmes de Pompes Hydrauliques
- Haute Pression et Force :
- Les pompes hydrauliques peuvent générer des forces considérables, ce qui est essentiel pour les applications industrielles lourdes.
- Précision :
- Les systèmes de pompes hydrauliques permettent un contrôle précis de la force et de la vitesse, ce qui est crucial pour des opérations de pressage délicates.
- Efficacité Énergétique :
- Les pompes à déplacement variable et les systèmes de régulation avancés permettent une utilisation efficace de l’énergie, réduisant les coûts opérationnels.
- Flexibilité :
- Les systèmes hydrauliques peuvent être facilement ajustés pour différentes applications et conditions de travail, offrant une grande polyvalence.
Applications des Systèmes de Pompes Hydrauliques
- Industrie Automobile :
- Utilisés pour le formage et l’assemblage des pièces de carrosserie et des composants mécaniques.
- Aéronautique :
- Pour le formage de pièces structurelles et de composants en alliages légers.
- Métallurgie :
- Pour le forgeage, l’estampage et le formage des métaux.
- Fabrication de Plastiques et Composites :
- Pour le moulage sous pression et l’assemblage de pièces composites.
Conclusion
Le système de pompe hydraulique est essentiel pour le fonctionnement des presses à 4 colonnes, offrant la puissance, la précision et la flexibilité nécessaires pour répondre aux exigences des applications industrielles modernes. Grâce à la variété des types de pompes et aux technologies de contrôle avancées, ces systèmes permettent de réaliser des opérations de pressage efficaces et de haute qualité.
Machines de Formage
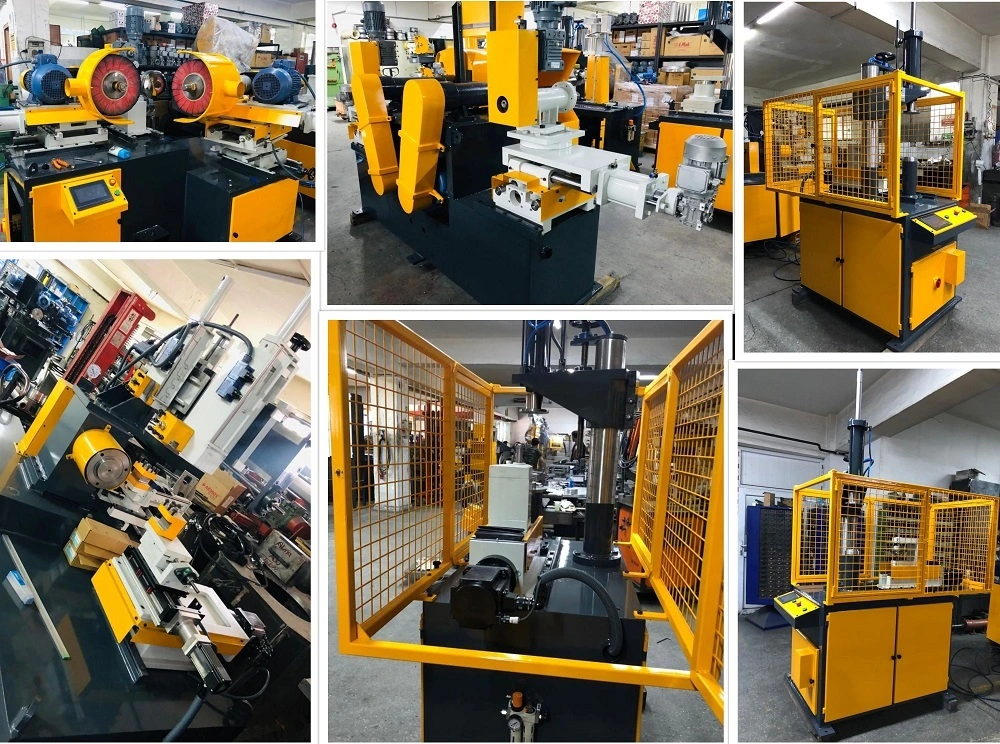
Dans l’industrie moderne, les machines de formage jouent un rôle essentiel dans la production de composants et de structures variées. Qu’il s’agisse de l’industrie automobile, aéronautique, électronique ou encore de la fabrication de biens de consommation, le formage des matériaux est un processus incontournable pour assurer la précision, la robustesse et la qualité des produits finis.
Les technologies industrielles de transformation des matériaux sont au cœur de l’évolution des secteurs manufacturiers modernes. Parmi ces technologies, les machines de formage et les presses occupent une place centrale dans les processus de fabrication et de production en masse. Ces machines permettent la transformation de matières premières en produits finis ou semi-finis, utilisés dans divers secteurs comme l’automobile, l’aérospatial, l’électroménager, et bien plus encore.
Les avancées technologiques dans ces équipements ont considérablement amélioré la précision, la rapidité et l’efficacité des procédés de production, répondant aux besoins croissants de l’industrie pour des produits de qualité supérieure, à des coûts compétitifs. Que ce soit pour des applications de formage, de découpe, de pliage ou d’emboutissage, ces machines constituent un maillon essentiel dans la chaîne de production industrielle. Dans ce contexte, ce guide vous présente en détail diverses catégories de machines et presses utilisées dans l’industrie métallurgique et manufacturière. Chaque section abordera un type spécifique de machine, ses caractéristiques, ses avantages et ses principales applications.
Le contenu suivant couvre des équipements allant des machines de formage aux presses hydrauliques, en passant par les machines de polissage et d’ébavurage, offrant ainsi une vue d’ensemble complète des technologies disponibles pour la transformation des métaux.
Machine de Formage
Les machines de formage jouent un rôle clé dans la transformation des métaux et d’autres matériaux à travers des procédés mécaniques, thermiques ou hydrauliques. Leur objectif principal est de façonner une pièce en lui donnant une forme prédéfinie, souvent sans enlever de matière, ce qui les distingue des procédés d’usinage ou de découpe.
Fonctionnement des Machines de Formage
Le principe de base d’une machine de formage repose sur l’application d’une force mécanique ou hydraulique pour déformer un matériau, généralement un métal, jusqu’à obtenir la forme désirée. Ce processus peut se dérouler à chaud ou à froid, selon la nature du matériau et le type de formage souhaité. Les machines de formage comprennent diverses catégories d’équipements, chacune adaptée à un type spécifique de transformation, comme le pliage, l’étirage, le cintrage ou le laminage.
Parmi les technologies de formage les plus utilisées, on trouve :
- Le formage à froid : utilisé principalement pour les métaux fins et ductiles, cette technique permet de déformer le matériau à température ambiante sans le chauffer, conservant ainsi ses propriétés mécaniques.
- Le formage à chaud : dans ce cas, le matériau est chauffé au-dessus de sa température de recristallisation, ce qui permet de faciliter sa déformation tout en limitant les contraintes internes.
Types de Machines de Formage
Il existe plusieurs types de machines de formage, en fonction de l’application spécifique :
- Machines de formage par étirage : ces machines sont souvent utilisées pour la production de grandes pièces, comme les panneaux de carrosserie dans l’industrie automobile.
- Machines de formage par pliage : adaptées au pliage de tôles métalliques, ces machines permettent de réaliser des angles précis sur des matériaux rigides.
- Machines de formage par laminage : elles servent principalement à réduire l’épaisseur d’un matériau, tout en augmentant sa longueur, très utilisées dans la production de feuilles de métal.
Avantages des Machines de Formage
Les machines de formage offrent plusieurs avantages dans le processus de fabrication industrielle :
- Efficacité : Elles permettent de transformer rapidement des matières premières en pièces finies ou semi-finies, réduisant ainsi les délais de production.
- Précision : Grâce aux innovations technologiques, ces machines peuvent produire des pièces aux tolérances très précises, même dans des matériaux difficiles à travailler.
- Réduction des pertes de matière : Contrairement à d’autres procédés comme l’usinage, le formage ne produit que très peu de déchets, ce qui en fait un processus plus économique et respectueux de l’environnement.
Applications Industrielles
Les machines de formage sont largement utilisées dans divers secteurs industriels :
- Automobile : pour la fabrication de châssis, de pièces de carrosserie, et autres composants critiques.
- Aéronautique : des pièces complexes et légères, telles que les structures d’aile et les panneaux de fuselage, sont souvent formées à l’aide de ces machines.
- Construction : dans la production de poutres, de barres et d’autres composants structurels utilisés dans les bâtiments et les infrastructures.
Presse à Emboutir

La presse à emboutir est une machine utilisée dans l’industrie pour transformer une feuille de métal en une forme tridimensionnelle complexe, grâce à un processus de déformation appelé emboutissage. Ce procédé est couramment utilisé dans la fabrication de pièces métalliques pour des industries telles que l’automobile, l’aéronautique, et l’électroménager.
Fonctionnement de la Presse à Emboutir
L’emboutissage est un processus de formage à froid, où une feuille métallique, appelée flan, est pressée entre une matrice et un poinçon. Le poinçon descend, déformant la feuille en lui donnant la forme souhaitée, généralement en une seule étape ou à travers une série de coups successifs pour des pièces plus complexes. Ce procédé permet de produire des formes précises et détaillées, souvent avec des géométries qui seraient difficiles, voire impossibles, à obtenir avec d’autres méthodes de fabrication.
Les presses à emboutir peuvent être actionnées mécaniquement, hydrauliquement ou via une combinaison des deux. Les presses hydrauliques sont couramment utilisées pour les opérations d’emboutissage profond, où de grandes forces sont nécessaires pour former des pièces aux formes complexes sans risque de déformation ou de fissuration du matériau.
Types de Presses à Emboutir
Il existe plusieurs types de presses à emboutir, chacune étant adaptée à des applications spécifiques :
- Presse mécanique : Utilisée pour des processus à grande vitesse, elle est plus adaptée à des opérations répétitives où la précision de chaque coup est essentielle.
- Presse hydraulique : Permet de mieux contrôler la pression et est plus adaptée pour les opérations nécessitant une grande force de formage, comme l’emboutissage profond.
- Presse servo-électrique : Combine la précision et le contrôle des presses hydrauliques avec la rapidité des presses mécaniques. Elle est idéale pour les opérations nécessitant à la fois rapidité et précision.
Avantages des Presses à Emboutir
Les presses à emboutir sont largement utilisées dans l’industrie pour plusieurs raisons :
- Productivité élevée : Ces machines permettent la production rapide de pièces complexes, souvent en une seule opération, ce qui augmente considérablement la cadence de fabrication.
- Flexibilité : Elles peuvent traiter une grande variété de matériaux, des métaux plus légers comme l’aluminium aux matériaux plus résistants comme l’acier inoxydable.
- Réduction des coûts : Grâce à leur efficacité et à leur capacité à produire des formes complexes en une seule opération, elles permettent de réduire les coûts de production par pièce, surtout dans les grandes séries.
- Précision et qualité : Les presses à emboutir modernes sont capables de produire des pièces avec des tolérances très serrées, minimisant ainsi les défauts et les rebuts.
Applications des Presses à Emboutir
L’emboutissage est un procédé essentiel dans diverses industries, notamment :
- Automobile : La fabrication des carrosseries de voitures, des portes, des capots, et d’autres pièces structurelles repose largement sur des presses à emboutir. La rapidité de production et la précision sont des atouts majeurs pour ce secteur.
- Aéronautique : Dans ce secteur, des pièces légères et complexes, telles que les carénages et les composants de structure d’aéronefs, sont souvent fabriquées par emboutissage pour assurer des tolérances strictes tout en minimisant le poids.
- Électroménager : Des composants tels que les coques extérieures des machines à laver, les tambours et les panneaux sont fréquemment produits par emboutissage, en raison de la précision et de la vitesse du processus.
Innovations Technologiques
Les presses à emboutir ont connu plusieurs évolutions ces dernières années, avec l’introduction de technologies avancées comme :
- L’emboutissage numérique : Des logiciels de simulation permettent désormais de prévoir et d’optimiser le processus d’emboutissage avant même de commencer la production, réduisant ainsi les erreurs et améliorant la qualité du produit fini.
- Presses à emboutissage automatique : Ces presses automatisées augmentent la cadence de production tout en minimisant les erreurs humaines, ce qui est crucial dans des industries où la précision est primordiale.
- Emboutissage à chaud : Cette technique consiste à chauffer la feuille de métal avant de l’emboutir, ce qui permet de créer des pièces encore plus complexes tout en limitant le risque de fissuration.
Machines à Filer les Métaux
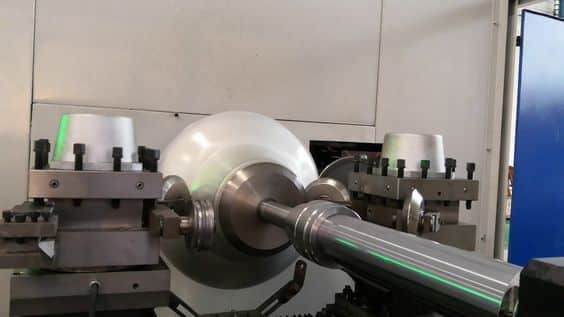
Les machines à filer les métaux sont des équipements industriels spécialisés dans la transformation de métaux à l’aide d’un procédé appelé le filage. Ce procédé consiste à déformer une pièce métallique en la faisant tourner rapidement tout en exerçant une pression contrôlée, permettant ainsi de créer des formes symétriques et précises. Le filage des métaux est utilisé principalement pour la production de pièces de forme cylindrique, conique ou de révolution.
Fonctionnement du Filage des Métaux
Le filage des métaux est un procédé de formage à froid ou à chaud, selon le type de matériau et les spécifications de la pièce à fabriquer. Le processus commence par la fixation d’un disque ou d’un tube de métal sur un mandrin rotatif. Ce mandrin sert de support pour former le métal en utilisant un outil de formage qui applique une pression pendant que le métal tourne à grande vitesse.
- Filage manuel : Bien que ce procédé soit souvent automatisé dans les grandes industries, il existe encore des opérations de filage manuel, où un opérateur guide l’outil de filage pour donner au métal la forme souhaitée. Ce type de filage est souvent réservé à des pièces complexes ou de petites séries.
- Filage automatique : Les machines à filer automatiques sont capables de produire des pièces à grande échelle avec une grande précision et constance. L’ensemble du processus est contrôlé par un système informatique qui régule la pression, la vitesse de rotation et la forme de l’outil.
Types de Filage
Il existe plusieurs types de procédés de filage selon le résultat souhaité :
- Filage conventionnel : Le procédé le plus courant, utilisé pour créer des formes simples comme des cônes ou des cylindres.
- Filage à compression : Ce procédé consiste à réduire l’épaisseur du métal tout en formant la pièce, ce qui est souvent utilisé pour les pièces nécessitant une résistance accrue.
- Filage assisté par ordinateur (CNC) : Utilisé pour des pièces complexes nécessitant une grande précision, ce procédé fait appel à des commandes numériques pour ajuster en temps réel la pression et la vitesse du processus.
Avantages du Filage des Métaux
Le filage des métaux présente plusieurs avantages distincts par rapport à d’autres procédés de formage :
- Production sans soudure : Le filage permet de créer des pièces creuses sans nécessiter de soudure, ce qui est essentiel pour la production de pièces de haute intégrité, notamment dans les secteurs de l’aéronautique ou de la chimie.
- Faible coût de production : En comparaison avec des procédés comme l’emboutissage profond, le filage nécessite des outillages relativement simples, ce qui réduit les coûts pour des productions de petites à moyennes séries.
- Haute précision : Les machines à filer modernes, surtout celles assistées par ordinateur, permettent d’obtenir des tolérances extrêmement serrées, indispensables dans des secteurs exigeants comme l’automobile ou la défense.
- Flexibilité : Le filage peut être utilisé pour une large gamme de matériaux, y compris l’aluminium, le cuivre, l’acier inoxydable, et même certains alliages exotiques utilisés dans l’aéronautique.
Applications des Machines à Filer
Les machines à filer les métaux trouvent des applications dans plusieurs industries :
- Aéronautique : Dans ce secteur, le filage est utilisé pour fabriquer des pièces légères et résistantes telles que des cônes de nez, des fuselages ou des réservoirs de carburant. La capacité du filage à produire des pièces sans soudure est un avantage majeur dans la fabrication d’équipements aéronautiques où la sécurité et la fiabilité sont primordiales.
- Automobile : Les composants tels que les roues, les jantes, les réservoirs et certains éléments de châssis sont souvent produits par filage en raison de la précision et de la solidité des pièces obtenues.
- Éclairage et mobilier : Le filage est également utilisé pour produire des luminaires, des abat-jours et des éléments décoratifs en métal, où la combinaison de formes complexes et de finitions lisses est très appréciée.
- Industrie chimique et pétrochimique : Des récipients sous pression et des réservoirs utilisés pour le stockage et le transport de produits chimiques dangereux sont souvent fabriqués par filage pour garantir une haute résistance et une étanchéité parfaite.
Innovations Récentes
L’évolution des machines à filer les métaux a suivi les avancées technologiques dans l’automatisation et la robotique :
- Machines CNC à filage : Ces machines à commande numérique permettent une précision accrue et la possibilité de fabriquer des pièces complexes en une seule opération, tout en optimisant les temps de cycle.
- Filage assisté par robot : Certaines machines sont équipées de bras robotiques capables de manipuler des pièces volumineuses ou complexes, ce qui augmente la flexibilité du procédé tout en réduisant les besoins en main-d’œuvre qualifiée.
- Matériaux avancés : Avec la montée en popularité des matériaux composites et des alliages exotiques, les machines à filer se sont adaptées pour être capables de traiter ces matériaux difficiles tout en conservant la précision et la qualité des pièces produites.
Presses de Formage des Métaux

Les presses de formage des métaux sont des machines industrielles utilisées pour déformer des matériaux métalliques afin de leur donner une forme spécifique. Ce processus de formage peut impliquer des actions telles que le pliage, l’emboutissage, l’étirage ou la découpe. Les presses de formage jouent un rôle essentiel dans la production de pièces métalliques, que ce soit dans l’automobile, l’aéronautique, ou les secteurs de la construction et de l’électroménager.
Fonctionnement des Presses de Formage
Le fonctionnement d’une presse de formage repose sur l’application d’une grande force mécanique ou hydraulique pour déformer un morceau de métal. Le métal est placé sur une matrice ou un moule, puis une presse applique une pression contrôlée, soit en une seule fois, soit de manière progressive, afin de lui donner la forme désirée.
- Presses mécaniques : Ce type de presse utilise un moteur et des engrenages pour générer la force nécessaire au formage du métal. Les presses mécaniques sont souvent préférées pour les opérations rapides et répétitives.
- Presses hydrauliques : Elles fonctionnent à l’aide d’un fluide sous pression pour générer la force. Ce type de presse est souvent utilisé pour des opérations de formage nécessitant un contrôle précis de la pression, notamment dans les applications complexes comme l’emboutissage profond.
Les presses peuvent être classées selon leur mode d’action :
- Presses à simple action : Une seule pression est appliquée au matériau pour réaliser le formage. Cela convient à des pièces plus simples.
- Presses à double action : Ce type de presse comporte deux opérations simultanées, avec une première pression pour maintenir la pièce et une seconde pour la déformer. Elle est souvent utilisée pour des formes plus complexes.
- Presses progressives : Elles effectuent plusieurs étapes de formage en une seule séquence, avec chaque coup de la presse apportant une déformation supplémentaire. Ce processus est largement utilisé pour des pièces complexes nécessitant plusieurs opérations de formage.
Types de Presses de Formage
Il existe plusieurs types de presses de formage, chacune étant adaptée à des besoins industriels spécifiques :
- Presse à friction : Utilisée pour des opérations nécessitant un contrôle précis de la vitesse et de la force, comme le forgeage ou l’estampage.
- Presse de formage à chaud : Utilisée pour former des métaux chauffés à haute température, souvent pour des alliages qui sont difficiles à travailler à froid.
- Presse à col de cygne (C-frame) : Souvent utilisée dans des opérations plus légères, elle permet un accès facile à la zone de formage, ce qui est utile pour des pièces de petite taille.
- Presse à cadre en H (H-frame) : Plus robuste, elle est utilisée pour des opérations nécessitant une grande stabilité et une force de formage élevée.
Avantages des Presses de Formage des Métaux
Les presses de formage offrent des avantages significatifs dans les processus de fabrication industrielle :
- Précision : Grâce à la régularité de la force appliquée, les presses de formage peuvent produire des pièces avec des tolérances très serrées, ce qui est crucial dans des industries comme l’automobile ou l’électronique.
- Efficacité de production : Les presses modernes permettent un formage rapide et répétitif, assurant une productivité élevée tout en réduisant les coûts par pièce.
- Flexibilité : Ces machines peuvent traiter différents types de métaux, allant des aciers aux alliages légers comme l’aluminium, et peuvent être ajustées pour produire des pièces de formes variées.
- Adaptabilité : Que ce soit pour le formage à chaud ou à froid, les presses de formage sont capables de s’adapter aux différents besoins de production selon le type de matériau et la forme désirée.
Applications des Presses de Formage
Les presses de formage sont essentielles dans de nombreux secteurs industriels :
- Automobile : Les composants critiques comme les panneaux de carrosserie, les châssis, et d’autres pièces structurelles sont fréquemment fabriqués à l’aide de presses de formage. Leur capacité à produire des pièces légères mais solides est un atout majeur dans la réduction du poids des véhicules tout en assurant leur robustesse.
- Aéronautique : Dans ce secteur, la précision et la qualité des pièces sont primordiales. Les presses de formage sont utilisées pour créer des pièces légères et résistantes, indispensables à la sécurité et à l’efficacité des avions.
- Industrie électrique : Les boîtiers métalliques pour appareils électriques, ainsi que d’autres composants en métal, sont souvent fabriqués par le biais de presses de formage, grâce à leur capacité à produire des pièces avec une grande précision.
- Construction : Les poutres, supports et autres éléments structurels métalliques utilisés dans les bâtiments et les infrastructures sont souvent produits à l’aide de ces presses, permettant d’obtenir des pièces standardisées et robustes.
Innovations Technologiques dans les Presses de Formage
L’industrie des presses de formage a vu de nombreuses innovations au fil des ans, améliorant l’efficacité et la précision des machines :
- Contrôle numérique : Les presses modernes sont souvent équipées de systèmes CNC (Commande Numérique par Calculateur) qui permettent de programmer et d’ajuster avec précision les paramètres de formage, garantissant une production plus rapide et moins d’erreurs.
- Automatisation : Les presses automatisées permettent d’augmenter la productivité tout en réduisant les besoins en main-d’œuvre. Des robots peuvent être intégrés pour alimenter la presse et retirer les pièces finies, accélérant ainsi les temps de cycle.
- Technologie écoénergétique : Certaines presses sont maintenant conçues pour utiliser moins d’énergie, tout en offrant une puissance de formage équivalente, réduisant ainsi les coûts opérationnels et l’empreinte carbone des usines.
Presse de Découpe Rapide

La presse de découpe rapide est un équipement industriel spécialisé dans la découpe de matériaux, principalement métalliques, à grande vitesse et avec une extrême précision. Ce type de presse est essentiel dans les environnements de production où des volumes élevés de pièces découpées avec précision sont nécessaires, notamment dans les secteurs de l’automobile, de l’électronique, de l’emballage, et de l’aérospatiale.
Fonctionnement de la Presse de Découpe Rapide
Le processus de découpe rapide repose sur l’utilisation d’une presse pour exercer une force sur une matrice, dans laquelle le matériau est positionné. Sous cette pression, le matériau est découpé à la forme désirée en un temps extrêmement court. Contrairement aux processus de découpe traditionnels, qui peuvent être plus lents ou moins précis, la presse de découpe rapide permet de traiter de grandes quantités de matériaux tout en assurant une qualité constante.
- Presse mécanique : Ce type de presse utilise un mécanisme à volant pour générer la force de découpe. Elle est idéale pour des cadences de production très élevées, pouvant réaliser des milliers de découpes à l’heure.
- Presse hydraulique : Les presses hydrauliques, bien que généralement plus lentes, offrent un contrôle plus précis de la force et sont utilisées pour des découpes nécessitant une extrême précision, ou pour des matériaux plus difficiles à découper.
- Presse servo-électrique : Ce type de presse combine la rapidité des presses mécaniques et la précision des presses hydrauliques. Elle utilise un moteur servo-électrique pour générer la force nécessaire, offrant ainsi une grande flexibilité dans le contrôle des paramètres de découpe.
Types de Découpe
Les presses de découpe rapide peuvent réaliser différents types de découpe, en fonction de la forme finale souhaitée et du type de matériau utilisé :
- Découpe à blanc : Une opération qui consiste à séparer une pièce d’un matériau plus grand sans formation supplémentaire. Cela est couramment utilisé pour produire des composants plats ou des pièces prêtes pour un autre processus de formage.
- Découpe progressive : Le matériau passe à travers plusieurs étapes de découpe successives pour aboutir à une pièce finale plus complexe. Chaque étape enlève une partie spécifique du matériau.
- Découpe fine : Utilisée pour des tolérances très serrées, notamment dans des applications où une haute précision et une finition de bord lisse sont essentielles, comme dans l’industrie de l’électronique ou l’horlogerie.
Avantages de la Presse de Découpe Rapide
Les presses de découpe rapide offrent plusieurs avantages qui en font un choix privilégié dans l’industrie moderne :
- Vitesse de production : Grâce à leur capacité à effectuer des découpes rapidement et en continu, ces presses permettent de produire un grand nombre de pièces dans un laps de temps réduit, augmentant ainsi la productivité de l’usine.
- Précision : Ces presses sont capables de réaliser des découpes d’une précision exceptionnelle, même à grande vitesse, ce qui est crucial pour des pièces nécessitant des tolérances serrées.
- Réduction des coûts : En automatisant le processus de découpe et en augmentant la cadence de production, les presses de découpe rapide contribuent à réduire les coûts de production par pièce, particulièrement dans les productions en série.
- Flexibilité : Certaines presses de découpe rapide peuvent être configurées pour réaliser différents types de découpes sur un même matériau, offrant ainsi une grande flexibilité dans les lignes de production.
Applications des Presses de Découpe Rapide
Ces presses sont largement utilisées dans plusieurs secteurs industriels en raison de leur capacité à traiter des volumes élevés de matériaux avec précision :
- Automobile : La découpe des tôles utilisées pour les carrosseries, les châssis, et autres pièces structurelles est souvent réalisée avec des presses de découpe rapide pour répondre aux besoins de production de masse du secteur.
- Aéronautique : Dans ce secteur, la précision et la qualité des composants sont primordiales. Les presses de découpe rapide sont utilisées pour découper des pièces métalliques légères et complexes qui nécessitent des tolérances strictes.
- Électronique : Les composants en métal de petite taille, comme les connecteurs ou les circuits imprimés, sont souvent découpés à l’aide de presses rapides, car ces pièces nécessitent une précision extrême.
- Emballage : Le secteur de l’emballage utilise souvent des presses de découpe rapide pour produire des emballages en métal ou en plastique à haute vitesse, répondant ainsi aux besoins du marché de masse.
Innovations et Évolutions Technologiques
Les presses de découpe rapide bénéficient des avancées technologiques qui optimisent leurs performances :
- Systèmes CNC et automatisation : Les presses modernes sont souvent équipées de commandes numériques par calculateur (CNC) permettant une programmation précise de chaque opération de découpe. Cela permet un ajustement rapide et précis des paramètres de découpe pour différentes pièces, ce qui est essentiel dans des environnements de production variés.
- Presses intelligentes : Certaines machines sont dotées de capteurs et de systèmes de surveillance en temps réel qui peuvent ajuster les paramètres en fonction des conditions réelles du matériau ou de l’usure des outils, garantissant ainsi une qualité constante.
- Économies d’énergie : De plus en plus de presses sont conçues pour être plus efficaces sur le plan énergétique, réduisant ainsi les coûts d’exploitation et contribuant à une production plus durable.
Presses à Rogner

Les presses à rogner sont des machines industrielles utilisées pour enlever l’excédent de matière autour d’une pièce après un processus de formage, d’emboutissage ou de moulage. Ce procédé de rognage permet d’obtenir des pièces finales avec des contours précis et nets, en supprimant toute bavure ou excès de métal qui pourrait affecter la qualité et l’esthétique de la pièce.
Fonctionnement des Presses à Rogner
Le processus de rognage consiste à placer la pièce formée dans une matrice et à utiliser une presse pour couper ou retirer les parties excédentaires. Le rognage est souvent l’étape finale après des opérations de formage comme l’emboutissage ou le moulage, où le matériau est déformé pour créer une forme spécifique, mais laisse généralement des bords irréguliers ou du surplus de matière.
- Presses mécaniques : Ce type de presse est couramment utilisé pour des opérations de rognage à haute vitesse. Les presses mécaniques sont particulièrement adaptées à des séries de production où un grand nombre de pièces doivent être rognées en un minimum de temps.
- Presses hydrauliques : Les presses hydrauliques sont privilégiées dans les cas où une grande force de rognage est nécessaire ou lorsque des matériaux plus durs doivent être traités. Elles permettent également un meilleur contrôle de la pression, ce qui est utile pour des pièces plus complexes.
- Presses de rognage automatiques : Dans les environnements de production moderne, les presses à rogner automatiques intègrent des systèmes robotisés et des capteurs pour une opération continue sans intervention humaine, ce qui augmente la productivité tout en garantissant une qualité constante.
Types de Processus de Rognage
Il existe plusieurs types de rognage en fonction de la nature de la pièce et du type de matériau utilisé :
- Rognage mécanique : Ce type de rognage utilise une force mécanique pour découper les excédents de matériau. Il est couramment utilisé pour des pièces en métal formées par emboutissage ou forgeage.
- Rognage par cisaillement : Un procédé où la pièce est cisaillée pour enlever les excédents de matière, souvent utilisé pour des matériaux plus épais ou plus durs.
- Rognage manuel : Dans certains cas, des opérations manuelles sont nécessaires pour rogner des pièces particulièrement complexes ou lorsque la production n’est pas adaptée à une automatisation complète.
- Rognage par usinage : Des outils de coupe rotatifs sont utilisés pour enlever les bavures ou excès de métal, ce qui permet d’obtenir une finition plus lisse, particulièrement dans les pièces qui nécessitent une précision accrue.
Avantages des Presses à Rogner
Les presses à rogner sont essentielles dans les processus de fabrication industrielle pour plusieurs raisons :
- Finition de haute qualité : Le rognage permet d’obtenir des bords propres et lisses, essentiels dans les secteurs où l’esthétique et la précision sont primordiales, comme l’automobile et l’aéronautique.
- Productivité accrue : Les presses à rogner automatiques ou à grande vitesse permettent de traiter un grand nombre de pièces en peu de temps, augmentant ainsi le rendement de la production.
- Réduction des déchets : En enlevant uniquement l’excédent de matière nécessaire, le rognage réduit les déchets et maximise l’utilisation des matériaux, contribuant à une production plus rentable et durable.
- Flexibilité : Les presses à rogner peuvent être adaptées pour traiter divers types de matériaux, des métaux légers comme l’aluminium aux alliages plus durs, rendant ce procédé polyvalent dans de nombreux secteurs.
Applications des Presses à Rogner
Le rognage est une étape essentielle dans la fabrication de nombreuses pièces industrielles, et il est utilisé dans plusieurs secteurs :
- Automobile : Dans la fabrication de pièces de carrosserie, d’éléments de moteur ou de composants structurels, le rognage permet d’éliminer les bavures ou excédents de métal résultant des processus d’emboutissage ou de moulage, garantissant ainsi une finition parfaite.
- Aéronautique : Les pièces utilisées dans les avions doivent souvent répondre à des normes strictes en matière de précision et de sécurité. Le rognage est utilisé pour éliminer les irrégularités après le formage des pièces métalliques, notamment pour les ailes, les carénages et autres composants critiques.
- Électronique : Dans la fabrication de petits composants métalliques, comme les connecteurs ou les boîtiers, le rognage permet de garantir des tolérances serrées et des contours précis, indispensables pour l’assemblage de circuits électroniques.
- Électroménager : Les pièces métalliques utilisées dans les appareils électroménagers, comme les tambours de machines à laver ou les coques de réfrigérateurs, doivent souvent être rognées pour garantir une finition soignée et sécurisée.
Innovations dans le Rognage Industriel
Les avancées technologiques dans le domaine des presses à rogner ont conduit à des innovations majeures, améliorant à la fois l’efficacité et la précision du processus :
- Rognage automatisé : L’intégration de robots et de systèmes de capteurs dans les presses permet un rognage entièrement automatisé, augmentant ainsi la productivité tout en réduisant les risques d’erreur humaine.
- Systèmes CNC : Les commandes numériques permettent de programmer précisément chaque opération de rognage, garantissant une uniformité parfaite d’une pièce à l’autre, même à grande échelle.
- Machines multi-processus : Certaines machines combinent le rognage avec d’autres opérations, comme l’emboutissage ou l’ébavurage, permettant ainsi de réduire les temps de manipulation et d’optimiser les processus de production.
Presses de Formage à Froid

Les presses de formage à froid sont des machines industrielles utilisées pour déformer des métaux sans les chauffer, contrairement au formage à chaud. Ce processus consiste à appliquer une pression intense à température ambiante pour plier, étirer, emboutir ou découper le matériau, tout en préservant ses propriétés mécaniques. Le formage à froid est particulièrement apprécié dans les secteurs où la précision, la résistance et la durabilité des pièces sont essentielles.
Fonctionnement des Presses de Formage à Froid
Le principe du formage à froid repose sur l’application d’une force mécanique ou hydraulique sur une pièce métallique pour lui donner une forme spécifique. Contrairement au formage à chaud, où le métal est chauffé pour faciliter sa déformation, le formage à froid exige des machines plus puissantes pour surmonter la résistance naturelle du métal. Ce procédé est couramment utilisé pour des métaux ductiles, comme l’acier doux, l’aluminium et le cuivre, qui peuvent être déformés sans rupture même à température ambiante.
Les presses de formage à froid se distinguent en fonction de leur méthode d’application de la pression :
- Presses mécaniques : Utilisées pour des opérations de formage à grande vitesse, ces presses sont souvent privilégiées pour des productions en série, comme l’emboutissage rapide de pièces simples.
- Presses hydrauliques : Ces machines offrent un contrôle précis de la pression appliquée, permettant de former des pièces plus complexes et d’utiliser des matériaux plus résistants. Elles sont idéales pour des opérations nécessitant une force continue.
- Presses servo-électriques : Elles combinent la rapidité des presses mécaniques avec la précision des presses hydrauliques, tout en réduisant la consommation d’énergie et les bruits générés.
Types de Processus de Formage à Froid
Le formage à froid regroupe plusieurs techniques en fonction de la pièce et de la géométrie à obtenir :
- Emboutissage : Une pièce est déformée à froid pour lui donner une forme tridimensionnelle. L’emboutissage à froid est utilisé pour fabriquer des composants tels que les boîtiers, les réservoirs et les coques de véhicules.
- Pliage : La presse applique une force sur une feuille de métal pour la plier à un angle spécifique, généralement à l’aide d’une matrice de pliage. Ce procédé est utilisé pour fabriquer des pièces structurelles comme des poutres et des panneaux.
- Extrusion à froid : Une pièce est forcée à travers une matrice pour lui donner une forme allongée. Ce procédé permet de fabriquer des tubes, des barres ou des profils métalliques complexes avec des tolérances très serrées.
- Forgeage à froid : Une pression est appliquée sur une pièce métallique pour la comprimer et la façonner sans la chauffer. Ce procédé est souvent utilisé pour produire des pièces mécaniques résistantes comme des boulons et des engrenages.
Avantages du Formage à Froid
Le formage à froid présente plusieurs avantages par rapport au formage à chaud :
- Précision accrue : Comme le métal n’est pas chauffé, il conserve mieux ses dimensions d’origine, permettant d’obtenir des pièces avec des tolérances plus serrées et des formes plus précises.
- Meilleure résistance des pièces : Le formage à froid améliore les propriétés mécaniques du métal, en augmentant sa résistance et sa dureté par écrouissage, ce qui rend les pièces plus robustes et durables.
- Efficacité énergétique : Contrairement au formage à chaud, le formage à froid ne nécessite pas de chauffer le métal, ce qui réduit la consommation d’énergie et les coûts associés.
- Qualité de surface améliorée : Les pièces formées à froid ont généralement une surface plus lisse et ne nécessitent pas de finitions supplémentaires, ce qui permet de réduire les étapes de post-traitement.
Applications des Presses de Formage à Froid
Le formage à froid est utilisé dans divers secteurs industriels en raison de sa capacité à produire des pièces de haute précision et à grande échelle :
- Automobile : De nombreuses pièces automobiles, comme les composants de châssis, les supports et les pièces structurelles, sont fabriquées par formage à froid en raison de leur robustesse et de leur précision.
- Aéronautique : Dans l’industrie aéronautique, où la qualité et la sécurité sont primordiales, le formage à froid est utilisé pour fabriquer des pièces légères et résistantes, comme des supports, des ferrures et des pièces de fuselage.
- Électronique : Le formage à froid permet de produire des composants métalliques fins et précis, comme des connecteurs et des boîtiers, indispensables dans la fabrication de circuits électroniques.
- Industrie des outils et machines : De nombreux outils, boulons, écrous et pièces mécaniques sont fabriqués par formage à froid, car ce procédé permet de produire des pièces solides et résistantes aux contraintes mécaniques.
Innovations dans le Formage à Froid
Les presses de formage à froid ont connu des avancées technologiques significatives ces dernières années, améliorant leur efficacité et leurs performances :
- Commandes numériques (CNC) : L’intégration de systèmes CNC permet un contrôle précis de chaque étape du processus de formage, garantissant une uniformité parfaite des pièces produites, même à grande échelle.
- Automatisation : Les presses de formage à froid sont de plus en plus automatisées, avec des systèmes robotisés qui alimentent et retirent les pièces, augmentant ainsi la productivité tout en réduisant les besoins en main-d’œuvre.
- Matériaux avancés : Le formage à froid de nouveaux alliages et matériaux composites permet d’obtenir des pièces plus légères, plus résistantes et plus adaptées aux applications modernes, notamment dans les secteurs de la défense et de l’aéronautique.
- Presses hybrides : Combinant les avantages des presses mécaniques, hydrauliques et servo-électriques, ces machines permettent de s’adapter à une large gamme de matériaux et de processus, tout en optimisant l’efficacité énergétique.
Presse Hydraulique d’Emboutissage
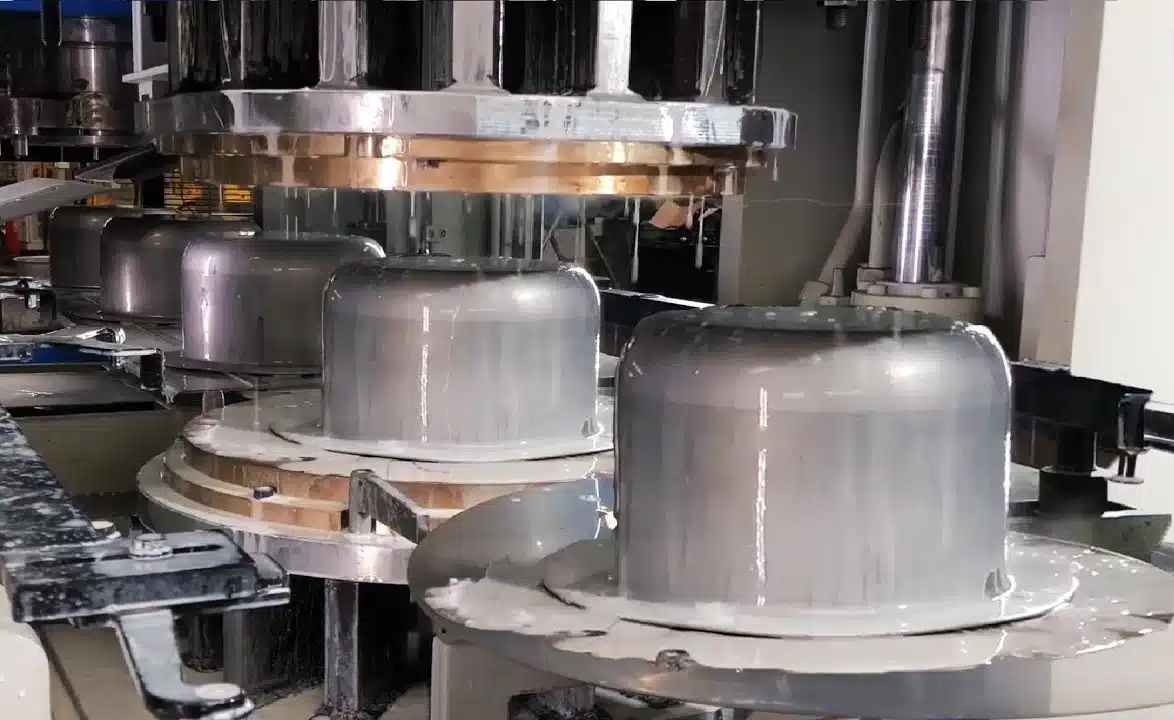
La presse hydraulique d’emboutissage est une machine industrielle puissante utilisée pour transformer des feuilles de métal en des formes tridimensionnelles complexes. L’emboutissage, processus de formage du métal par déformation, nécessite des forces importantes pour obtenir des pièces avec des géométries précises. Grâce à leur capacité à générer une force de pression continue et élevée, les presses hydrauliques sont idéales pour ce type d’opération.
Fonctionnement des Presses Hydrauliques d’Emboutissage
Les presses hydrauliques fonctionnent en utilisant un fluide sous pression pour générer une force capable de déformer des matériaux métalliques. Lors du processus d’emboutissage, une feuille métallique, appelée flan, est placée entre une matrice et un poinçon. La presse hydraulique applique ensuite une force uniforme sur le poinçon pour pousser la feuille à travers la matrice, créant ainsi une pièce avec des formes détaillées et complexes.
Contrairement aux presses mécaniques, qui génèrent une force maximale à un point donné, les presses hydrauliques peuvent appliquer une force constante tout au long du cycle de travail, ce qui est particulièrement important dans des processus comme l’emboutissage profond, où le matériau est fortement déformé.
Types de Presses Hydrauliques d’Emboutissage
Il existe plusieurs types de presses hydrauliques adaptées à l’emboutissage, chacune ayant des caractéristiques spécifiques selon les applications :
- Presse à action simple : Ce type de presse hydraulique est utilisé pour des opérations d’emboutissage de base, où une seule force est appliquée pour déformer le métal.
- Presse à double action : Ces presses sont équipées de deux vérins hydrauliques : l’un pour maintenir la feuille de métal en place pendant le processus, et l’autre pour appliquer la force de déformation. Elles sont couramment utilisées pour l’emboutissage profond.
- Presse à triple action : Ce type de presse est utilisé pour des processus de formage encore plus complexes, nécessitant un contrôle précis des forces appliquées sur différentes parties de la pièce.
Avantages des Presses Hydrauliques d’Emboutissage
Les presses hydrauliques sont largement utilisées dans l’industrie pour de nombreuses raisons :
- Capacité à générer des forces élevées : Les presses hydrauliques peuvent appliquer des forces très importantes, ce qui les rend idéales pour le formage de pièces épaisses ou de grandes dimensions.
- Précision et contrôle : Grâce à la régulation de la pression hydraulique, il est possible de contrôler précisément la force appliquée, ce qui garantit des tolérances plus serrées et des pièces de haute qualité.
- Adaptabilité : Les presses hydrauliques peuvent être ajustées pour diverses opérations, allant de l’emboutissage superficiel à l’emboutissage profond, permettant une grande flexibilité dans la production.
- Longueur de course ajustable : Les presses hydrauliques peuvent avoir une course plus longue, ce qui les rend particulièrement adaptées à des opérations nécessitant des déformations importantes, comme l’emboutissage profond.
Applications des Presses Hydrauliques d’Emboutissage
Les presses hydrauliques d’emboutissage sont utilisées dans une large gamme de secteurs industriels pour fabriquer des pièces complexes et volumineuses :
- Automobile : Dans l’industrie automobile, les presses hydrauliques sont utilisées pour fabriquer des composants structurels comme les capots, les portes, les panneaux latéraux, et d’autres pièces de carrosserie. Ces pièces nécessitent une grande précision et doivent être produites en masse.
- Aéronautique : Dans ce secteur, l’emboutissage profond est utilisé pour fabriquer des pièces légères et résistantes, comme les réservoirs de carburant, les carénages et les éléments de fuselage. L’utilisation de presses hydrauliques permet d’obtenir des pièces d’une qualité irréprochable, tout en respectant les normes de sécurité strictes de l’aéronautique.
- Électroménager : De nombreuses pièces métalliques utilisées dans les appareils électroménagers, comme les tambours de machines à laver, les coques extérieures et les composants de moteurs, sont fabriquées par emboutissage avec des presses hydrauliques.
- Industrie énergétique : Les presses hydrauliques d’emboutissage sont également utilisées pour produire des composants utilisés dans l’industrie énergétique, comme des enveloppes de batteries ou des pièces pour panneaux solaires.
Innovations et Évolutions Technologiques
Les presses hydrauliques d’emboutissage ont bénéficié de nombreuses innovations au fil des années, améliorant leurs performances et leurs capacités :
- Automatisation avancée : L’intégration de robots et de systèmes automatisés permet aux presses hydrauliques modernes de fonctionner de manière continue et sans interruption, augmentant ainsi la productivité tout en réduisant les coûts de production.
- Contrôles numériques : Grâce aux systèmes CNC, les presses hydrauliques peuvent être programmées avec une précision extrême, permettant un contrôle minutieux de chaque étape du processus d’emboutissage, garantissant ainsi la constance de la qualité des pièces produites.
- Économies d’énergie : Certaines presses hydrauliques sont conçues pour utiliser moins d’énergie tout en maintenant des niveaux de performance élevés. Cela contribue à la réduction des coûts d’exploitation et à une production plus respectueuse de l’environnement.
- Technologie de fluide à haute pression : Les nouvelles presses hydrauliques sont capables d’utiliser des fluides à haute pression, augmentant ainsi la force générée sans avoir besoin de moteurs plus puissants, ce qui améliore l’efficacité énergétique.
Presses Hydrauliques pour Formage
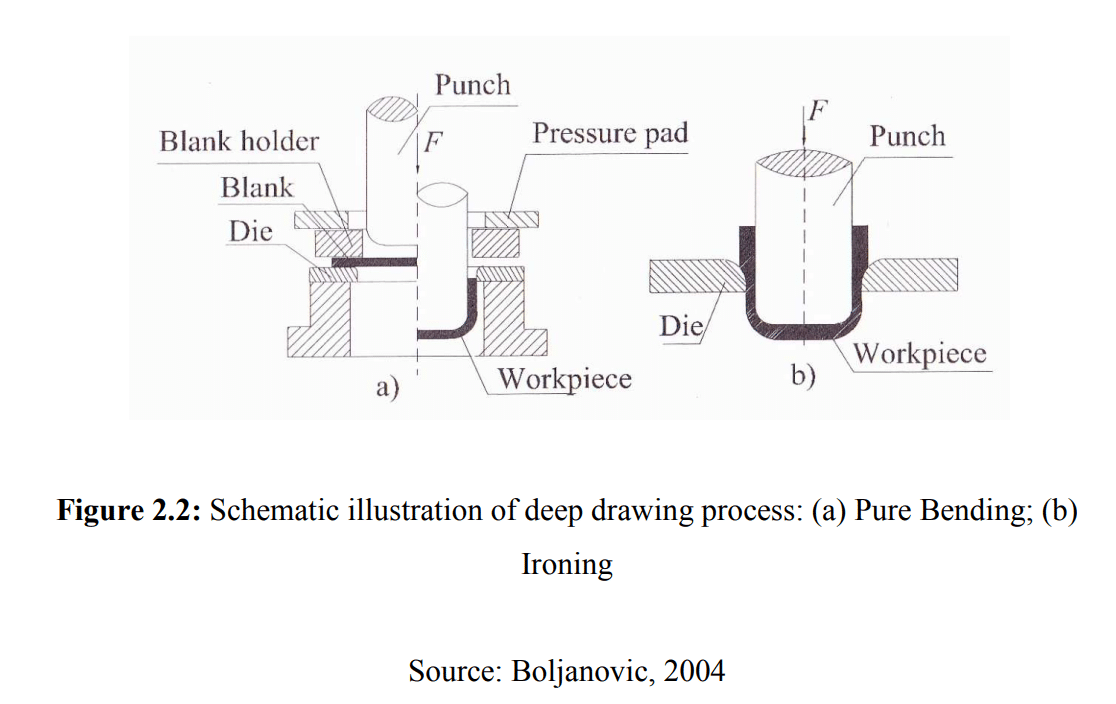
Les presses hydrauliques pour formage sont des machines industrielles polyvalentes, utilisées pour façonner des matériaux métalliques et non métalliques en appliquant une force élevée via un fluide hydraulique. Ces presses sont essentielles dans les processus de formage, car elles permettent de réaliser des opérations complexes avec une grande précision. Elles sont couramment employées dans divers secteurs industriels, comme l’automobile, l’aéronautique, la construction, et bien d’autres.
Fonctionnement des Presses Hydrauliques pour Formage
Les presses hydrauliques fonctionnent sur un principe simple mais puissant : un fluide, généralement de l’huile, est pressurisé à l’intérieur d’un cylindre pour générer une force de compression qui déforme le matériau placé entre la matrice et le poinçon. La force générée par la presse hydraulique est constante tout au long du cycle de travail, ce qui permet un formage progressif et uniforme.
Contrairement aux presses mécaniques, qui appliquent une force maximale à un moment précis du cycle, les presses hydrauliques offrent une pression contrôlée et ajustable, ce qui est essentiel pour des opérations de formage plus complexes. Elles peuvent également être utilisées pour plusieurs types de formage, comme le pliage, l’emboutissage, l’étirage, et l’extrusion.
Types de Presses Hydrauliques pour Formage
Il existe plusieurs types de presses hydrauliques, chacune étant adaptée à un type particulier de formage :
- Presses à cadre en H : Ces presses sont très robustes et offrent une grande stabilité lors des opérations de formage, ce qui les rend adaptées aux applications nécessitant des forces de pression élevées.
- Presses à 4 colonnes : Ces presses hydrauliques sont idéales pour les opérations nécessitant une répartition uniforme de la force sur la pièce. Elles sont souvent utilisées pour l’emboutissage et le formage de grandes pièces plates.
- Presses à double action : Elles sont équipées de deux vérins permettant de contrôler la pression de manière indépendante, ce qui est utile pour les opérations de formage à plusieurs étapes, telles que le formage profond ou l’étirage.
- Presses de transfert : Elles sont intégrées à des lignes de production automatisées pour déplacer la pièce d’une station à une autre, réalisant plusieurs étapes de formage en une seule séquence.
Avantages des Presses Hydrauliques pour Formage
Les presses hydrauliques offrent de nombreux avantages, notamment :
- Force ajustable : La pression générée par une presse hydraulique peut être ajustée avec précision en fonction des exigences du matériau et du processus de formage, permettant ainsi une flexibilité maximale.
- Capacité à travailler des matériaux variés : Ces presses peuvent être utilisées pour former une large gamme de matériaux, allant des métaux légers comme l’aluminium aux alliages plus durs, ainsi que des matériaux composites et plastiques.
- Formage de pièces complexes : Grâce à la répartition uniforme de la force, ces presses permettent de former des pièces aux géométries complexes, même avec des tolérances très strictes.
- Économie d’énergie : Certaines presses hydrauliques modernes sont conçues pour être plus écoénergétiques, réduisant la consommation tout en maintenant des performances élevées, ce qui en fait des solutions plus durables.
Applications des Presses Hydrauliques pour Formage
Les presses hydrauliques sont essentielles dans de nombreuses industries pour le formage de pièces métalliques et non métalliques :
- Automobile : Dans l’industrie automobile, ces presses sont utilisées pour la fabrication de nombreuses pièces, allant des panneaux de carrosserie aux composants structurels comme les montants, les longerons et les supports. Elles permettent de former des pièces légères mais solides, essentielles pour réduire le poids des véhicules tout en améliorant leur performance.
- Aéronautique : Le formage de pièces aéronautiques, comme les cadres de fuselage, les ailes et autres composants, nécessite une grande précision et une force importante. Les presses hydrauliques sont couramment utilisées pour former des alliages légers comme le titane ou l’aluminium.
- Construction : Les presses hydrauliques sont utilisées pour produire des poutres, des colonnes et d’autres éléments structurels dans la construction de bâtiments, d’infrastructures et de ponts. Elles permettent de former des pièces résistantes aux contraintes mécaniques tout en assurant leur durabilité.
- Électronique : Les composants métalliques des appareils électroniques, comme les boîtiers, les connecteurs et autres pièces de petite taille, sont souvent formés à l’aide de presses hydrauliques. Ces machines permettent d’obtenir des tolérances serrées et des finitions de haute qualité.
Innovations dans les Presses Hydrauliques pour Formage
Les presses hydrauliques ont évolué avec l’intégration de nouvelles technologies, rendant leur utilisation plus efficace et plus précise :
- Commandes numériques (CNC) : Les systèmes CNC permettent de contrôler chaque aspect du processus de formage, de la pression à la vitesse de compression, assurant ainsi une répétabilité et une précision exceptionnelles.
- Automatisation : L’intégration de robots et de systèmes automatisés dans les presses hydrauliques a révolutionné les lignes de production, augmentant la productivité tout en réduisant les coûts liés à la main-d’œuvre et aux erreurs humaines.
- Technologie à faible consommation d’énergie : Les presses hydrauliques modernes sont de plus en plus conçues pour réduire la consommation d’énergie. L’utilisation de systèmes hybrides, combinant hydraulique et électrique, permet d’améliorer l’efficacité énergétique sans compromettre la puissance de formage.
- Maintenance prédictive : Grâce à des capteurs intelligents, les presses hydrauliques peuvent maintenant surveiller en temps réel l’usure des composants, permettant une maintenance prédictive et ainsi minimiser les temps d’arrêt.
Les machines de formage englobent une large gamme d’équipements conçus pour transformer les matières premières, telles que les métaux, en produits finis de formes spécifiques. Ces machines permettent de manipuler les matériaux avec une grande précision, en utilisant diverses techniques telles que le pliage, le découpage, l’emboutissage, et bien d’autres. Parmi ces équipements, on trouve des outils spécialisés comme la machine de formage de précision, la bordeuse pour tôle, ou encore la machine de formage verticale.
Les industries d’aujourd’hui dépendent fortement de ces machines pour maintenir des niveaux élevés de production et de qualité. L’évolution technologique a conduit à la création de machines de formage de plus en plus sophistiquées, intégrant des systèmes de contrôle numériques avancés et des automatismes qui améliorent non seulement la précision mais aussi l’efficacité des processus de production.
Les machines de formage multistations sont un exemple de ces avancées. Elles permettent la réalisation de plusieurs opérations de formage sur une seule pièce, sans nécessiter de transfert entre différentes machines. Ce gain de temps et de précision se traduit par une réduction des coûts de production et une amélioration de la qualité des produits.
Dans le contexte de la fabrication de tôles, les machines telles que la bordeuse pour tôle ou la cintreuse sont essentielles. Elles permettent de donner aux feuilles de métal des formes spécifiques, souvent complexes, tout en conservant leurs propriétés mécaniques. Le pliage de tôle est une opération courante dans de nombreux secteurs, et les machines modernes permettent d’effectuer ces opérations avec une précision micrométrique.
En plus du formage, le découpage est une autre opération cruciale dans l’industrie. Les lignes de presses de découpe sont utilisées pour découper des pièces à partir de tôles ou d’autres matériaux plats. Ces machines, telles que la poinçonneuse de découpe et la presse de découpe, sont conçues pour exécuter des découpes complexes avec une grande rapidité et une précision extrême. L’intégration de ces machines dans une ligne de production robotisée permet une automatisation complète du processus, de la découpe initiale au formage final.
L’évolution des machines de formage ne se limite pas aux opérations de pliage et de découpe. La machine à moulurer, par exemple, est un équipement essentiel pour la création de moulures décoratives ou fonctionnelles sur des matériaux métalliques. Ces machines sont souvent utilisées dans la fabrication de panneaux routiers et autres équipements de signalisation, où la précision et la durabilité sont cruciales.
L’automatisation joue un rôle de plus en plus important dans l’industrie du formage. Les bordeur moulureuse automatique et autres machines de formage automatiques permettent de réduire les erreurs humaines et d’augmenter la productivité. Les machines pour la fabrication de panneaux de signalisation, par exemple, sont souvent équipées de systèmes automatisés qui garantissent une production rapide et sans défaut des panneaux routiers.
L’intégration de technologies hydrauliques dans les machines de formage a également permis de réaliser des avancées significatives. Les poinçonneuses semi-automatiques et les presses hydrauliques pour la transformation des métaux sont désormais courantes dans les usines modernes. Ces machines offrent une puissance et une précision inégalées, ce qui les rend idéales pour des opérations complexes telles que l’emboutissage cylindrique ou la mise en forme des tubes.
Enfin, les machines de polissage industriel jouent un rôle crucial dans la finition des pièces formées. Ces machines, qu’elles soient manuelles ou automatisées, permettent d’obtenir des surfaces parfaitement lisses et prêtes à être utilisées dans des applications critiques.
Dans cette introduction, nous avons exploré l’importance des machines de formage dans l’industrie moderne, en soulignant les différents types de machines et leurs applications. Dans les sections suivantes, nous examinerons en détail chaque catégorie de machines de formage, en mettant en lumière leurs caractéristiques spécifiques, leurs applications industrielles, et les innovations récentes qui continuent de transformer ce domaine essentiel de la production industrielle.
Les Machines de Formage et leur Application
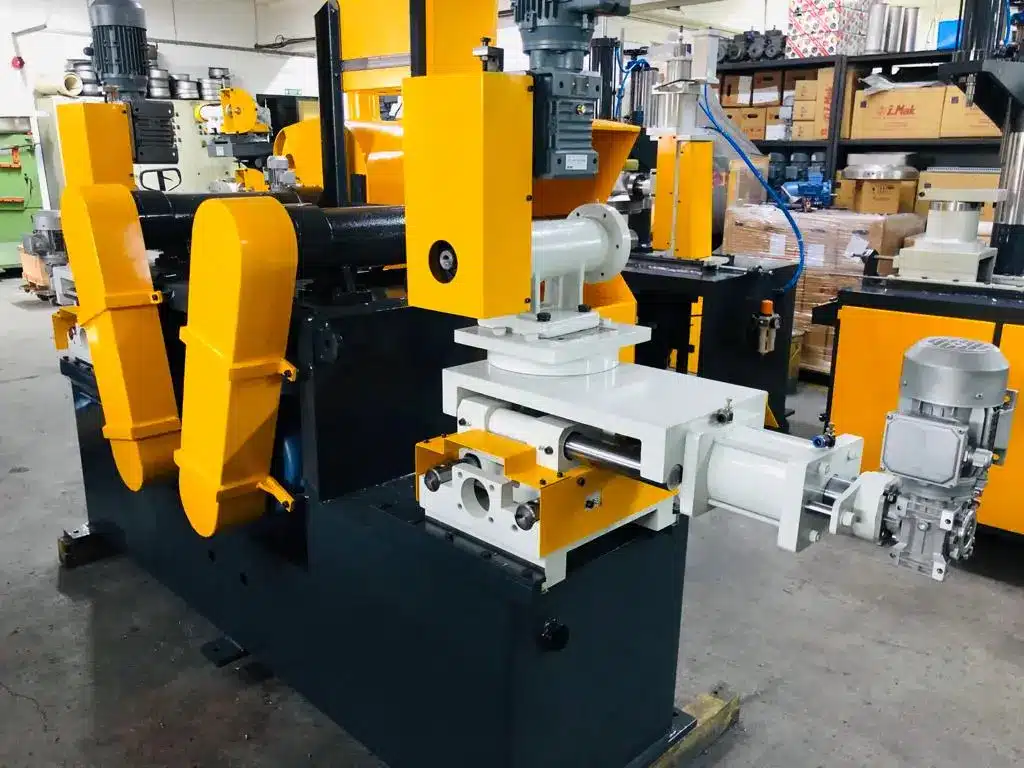
Les machines de formage de précision sont au cœur de la production industrielle, offrant des solutions de formage ultra-précises pour des secteurs nécessitant une grande exactitude, comme l’aéronautique, l’automobile ou l’électronique. Ces machines sont conçues pour manipuler divers matériaux avec une précision allant jusqu’à quelques micromètres, ce qui est essentiel pour la fabrication de composants critiques.
L’utilisation de ces machines est cruciale dans des industries où les tolérances dimensionnelles sont extrêmement strictes. Par exemple, dans l’industrie automobile, les composants tels que les châssis, les panneaux de carrosserie, ou les pièces de moteur doivent être fabriqués avec une précision impeccable pour assurer non seulement la performance mais aussi la sécurité des véhicules.
La machine de formage verticale est une autre innovation clé dans le domaine du formage de précision. Contrairement aux machines traditionnelles qui fonctionnent sur un plan horizontal, ces machines opèrent sur un axe vertical, offrant des avantages significatifs en termes de contrôle et de stabilité des pièces pendant le formage. Cela est particulièrement utile pour les pièces complexes qui nécessitent une manipulation délicate ou un formage en plusieurs étapes.
Les machines de formage multistations représentent une autre avancée technologique majeure. Ces équipements sont capables de réaliser plusieurs opérations de formage successives sur une même pièce sans nécessiter de transfert manuel entre différentes machines. Cela permet non seulement de gagner du temps, mais aussi d’assurer une précision constante à chaque étape du processus.
Les applications des machines de formage de précision sont vastes et variées. Elles sont utilisées pour la fabrication de composants électroniques miniaturisés, de pièces de moteurs à haute performance, ainsi que pour la production de structures complexes dans l’industrie aéronautique. Le développement de machines toujours plus précises et rapides est essentiel pour répondre aux exigences croissantes de ces industries.
2. Bordeuses et Cintreuses pour Tôle
Dans le travail de la tôle, les bordeuses et cintreuses sont des équipements indispensables. Elles permettent de façonner les feuilles de métal en leur donnant des formes spécifiques, telles que des angles, des courbes ou des bords renforcés. Ces opérations sont essentielles pour la production de pièces de carrosserie, de panneaux structurels, et d’autres composants utilisés dans une multitude d’industries.
La bordeuse pour tôle est particulièrement utile pour renforcer les bords des tôles, les rendant plus résistantes à la déformation et aux dommages. Ces machines sont couramment utilisées dans la production de carrosseries automobiles, où chaque pièce doit répondre à des normes strictes de durabilité et de sécurité.
La cintreuse quant à elle, est utilisée pour plier les tôles en formes spécifiques. Le pliage de tôle est une opération qui requiert une grande précision, car toute erreur peut compromettre l’intégrité de la pièce finale. Les machines modernes sont équipées de systèmes de contrôle avancés qui assurent un pliage précis, même pour des formes complexes.
Les innovations récentes dans ces machines ont permis d’améliorer la vitesse et la précision des opérations, tout en réduisant les déchets de matériaux. Par exemple, les cintreuses de découpe intègrent désormais des systèmes de découpe qui permettent de réaliser des plis et des découpes en une seule opération, ce qui accélère considérablement le processus de production.
3. Avantages des Machines de Formage de Précision
Les machines de formage de précision offrent de nombreux avantages aux entreprises industrielles. L’un des principaux avantages est la réduction des coûts de production grâce à la diminution des erreurs et des déchets de matériaux. En utilisant des machines de formage précises, les entreprises peuvent produire des pièces conformes aux spécifications avec un minimum de rebuts, ce qui se traduit par une économie substantielle.
En outre, la précision accrue permet de produire des pièces plus complexes, qui répondent aux exigences des industries modernes en matière de performance et de durabilité. Cela est particulièrement important dans des secteurs tels que l’aéronautique et l’automobile, où les pièces doivent non seulement être précises, mais aussi légères et résistantes.
L’intégration de technologies numériques dans les machines de formage de précision a également ouvert de nouvelles possibilités en matière de contrôle et de surveillance des processus. Les systèmes de contrôle numérique permettent de suivre en temps réel les opérations de formage, d’ajuster les paramètres en fonction des conditions de production, et d’assurer une qualité constante tout au long du processus.
Enfin, l’utilisation de ces machines permet également de réduire les temps de production, ce qui est essentiel pour répondre aux demandes croissantes du marché. En optimisant chaque étape du processus de formage, les entreprises peuvent produire plus rapidement, tout en maintenant des standards élevés de qualité.
Avec ces deux sections rédigées, nous avons couvert l’introduction générale des machines de formage et les applications des machines de formage de précision, ainsi que les machines utilisées pour le travail de la tôle. Les prochaines sections se concentreront sur les lignes de production et l’automatisation, ainsi que sur les machines spécifiques pour la fabrication. Je vous invite à lire cette première partie et à me donner vos retours ou suggestions pour continuer sur la lancée.
Lignes de Production et Automation
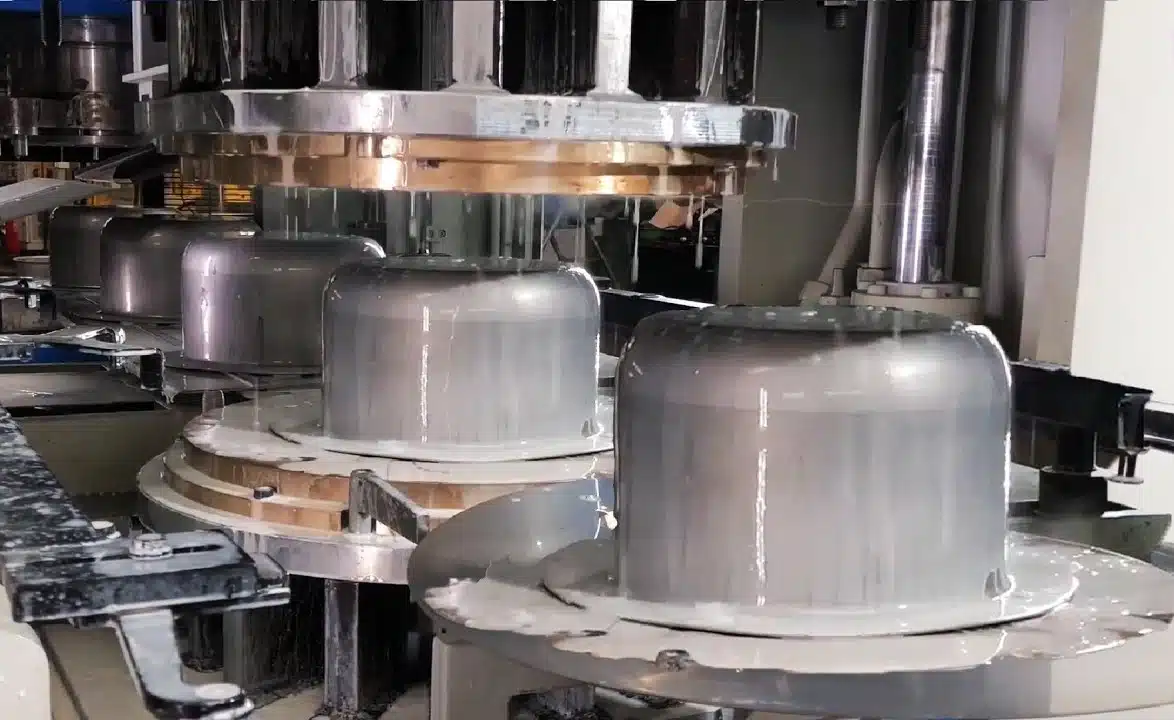
Importance de l’Automatisation dans les Lignes de Production: L’automatisation a révolutionné l’industrie manufacturière, permettant d’améliorer la productivité, de réduire les coûts de production et d’augmenter la qualité des produits finis. L’intégration de lignes de presses de découpe, de lignes de production robotisées, et de machines de formage dans des systèmes automatisés a permis de transformer les usines traditionnelles en unités de production hautement efficaces et sophistiquées.
Les lignes de production robotisées sont conçues pour automatiser entièrement le processus de fabrication, de la manipulation des matières premières à l’assemblage final des produits. Elles permettent non seulement de réduire la dépendance à la main-d’œuvre humaine, mais aussi d’augmenter la précision et la répétabilité des opérations. Cela est particulièrement crucial dans les industries où des tolérances strictes et des volumes de production élevés sont requis.
2. Lignes de Presses de Découpe
Les lignes de presses de découpe sont essentielles pour la production de pièces en métal à grande échelle. Ces lignes comprennent plusieurs machines interconnectées qui travaillent en synergie pour transformer les tôles ou autres matériaux plats en pièces finies. Les presses de découpe sont généralement utilisées pour des opérations telles que le découpage, le poinçonnage, l’emboutissage, et le pliage.
Ces lignes sont souvent équipées de poinçonneuses de découpe, qui permettent de réaliser des trous ou des découpes complexes avec une grande précision. L’intégration de systèmes de contrôle numérique dans ces machines a permis de simplifier les processus de configuration et d’améliorer la précision des découpes. De plus, les presses industrielles modernes peuvent être programmées pour exécuter plusieurs opérations en séquence, ce qui réduit le besoin de manipulations manuelles et augmente la productivité.
3. Lignes de Production de Pièces en Métal
Les lignes de production de pièces en métal sont couramment utilisées dans l’industrie automobile, aéronautique, et de la construction. Ces lignes intègrent diverses machines de formage, de découpe, et d’assemblage pour produire des composants métalliques de haute qualité. L’automatisation de ces lignes permet de garantir une production continue et de haute précision, essentielle pour répondre aux normes rigoureuses de ces secteurs.
Un exemple concret est l’utilisation de lignes de presses hydrauliques dans la production de pièces automobiles. Ces lignes permettent de former, découper, et assembler des pièces avec une grande précision, tout en assurant une haute répétabilité et une productivité élevée. Les presses hydrauliques sont particulièrement adaptées à l’emboutissage de grandes pièces, telles que les panneaux de carrosserie, grâce à leur capacité à exercer une force importante de manière contrôlée.
4. Avantages des Lignes de Production Automatisées
Les lignes de production automatisées offrent de nombreux avantages aux entreprises manufacturières. Parmi ces avantages, on peut citer :
- Réduction des coûts de main-d’œuvre : En automatisant les processus de production, les entreprises peuvent réduire leur dépendance à la main-d’œuvre humaine, ce qui permet de diminuer les coûts de production.
- Augmentation de la productivité : Les machines automatisées peuvent fonctionner sans interruption, ce qui permet d’augmenter les volumes de production.
- Amélioration de la qualité : L’automatisation permet de réduire les erreurs humaines et d’assurer une qualité constante des produits finis.
- Flexibilité de production : Les systèmes automatisés peuvent être facilement reconfigurés pour produire différentes pièces ou répondre à des besoins spécifiques.
5. Étude de Cas : Automatisation dans une Ligne de Production
Prenons l’exemple d’une entreprise manufacturière spécialisée dans la production de pièces pour l’industrie automobile. Cette entreprise a récemment investi dans une ligne de production robotisée comprenant plusieurs machines de formage de précision, presses de découpe, et bordeur moulureuse automatique.
Avant l’automatisation, la production nécessitait une intervention humaine à chaque étape, ce qui entraînait des temps d’arrêt fréquents et une variabilité dans la qualité des produits finis. Avec l’introduction de la ligne de production automatisée, l’entreprise a pu augmenter sa capacité de production de 30%, réduire les déchets de matériaux de 20%, et améliorer la qualité des pièces produites grâce à une précision accrue.
L’intégration de machines de formage hydraulique et de presses pour tôle a également permis de réaliser des opérations complexes en un seul passage, réduisant ainsi le temps de production global et améliorant l’efficacité énergétique de l’usine. Cette automatisation a non seulement permis à l’entreprise de répondre plus rapidement aux commandes clients, mais aussi de réduire ses coûts opérationnels et d’améliorer sa compétitivité sur le marché mondial.
Machines Spécifiques pour la Fabrication
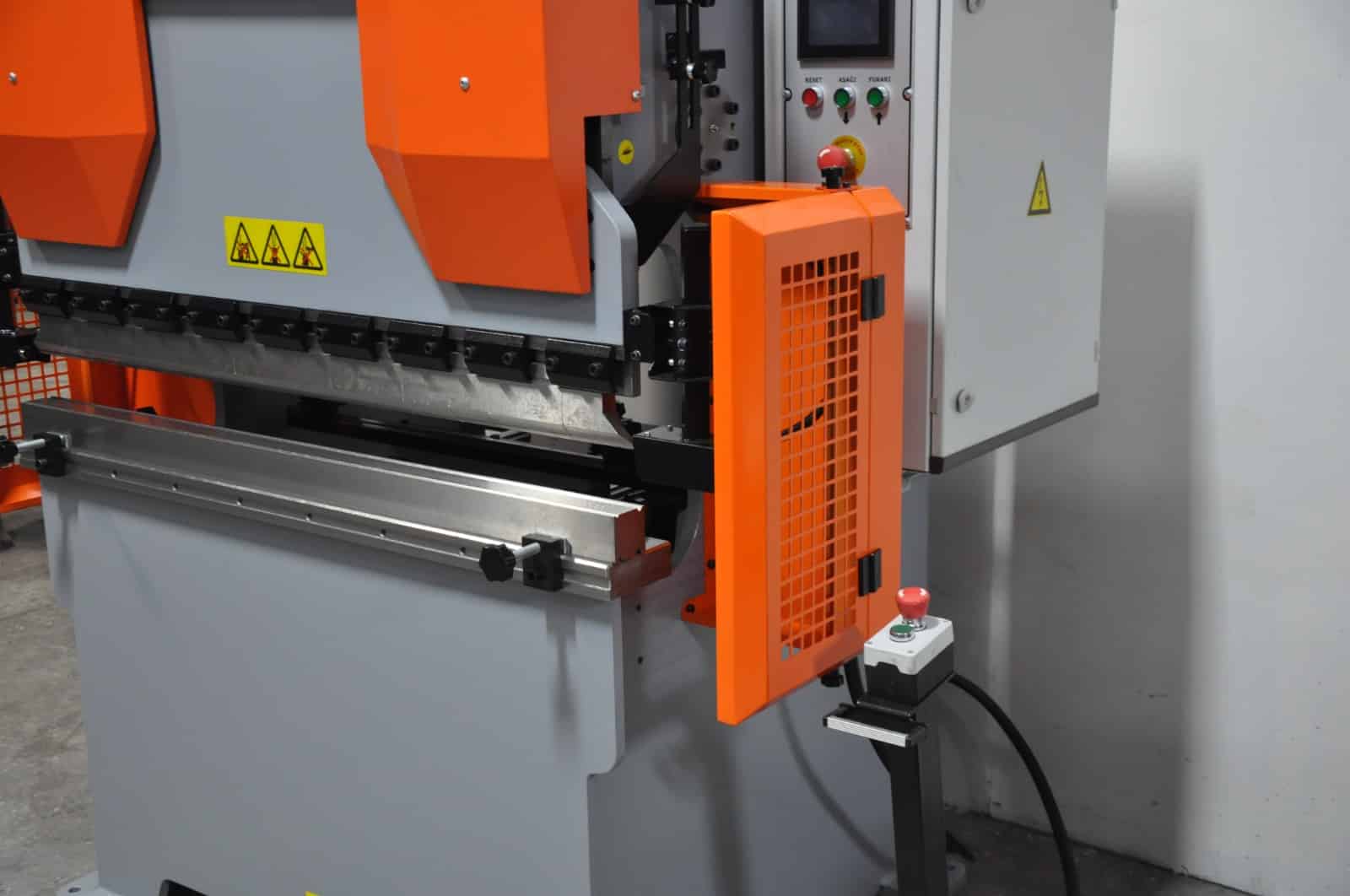
Les machines de fabrication de panneaux routiers sont des équipements spécialisés conçus pour produire des panneaux de signalisation de haute qualité. Ces machines utilisent des techniques de formage, de découpe, et de moulurage pour créer des panneaux routiers qui répondent aux normes de sécurité et de durabilité.
La bordeuse moulureuse automatique est un exemple clé de ce type de machine. Elle permet de façonner et de renforcer les bords des panneaux routiers, garantissant leur résistance aux intempéries et à l’usure. Cette machine est souvent utilisée en tandem avec des machines à moulurer qui créent des motifs ou des textes en relief sur les panneaux, améliorant leur visibilité et leur lisibilité.
2. Machines de Formage de Tuyaux
Les machines de formage de tuyaux sont essentielles dans la production de conduites pour diverses industries, y compris le pétrole, le gaz, et la construction. Ces machines permettent de former des tuyaux à partir de feuilles de métal ou de barres en appliquant des forces de pliage, de torsion, et d’emboutissage.
Les techniques de mise en forme des tubes impliquent souvent des opérations de cintrage et d’emboutissage pour créer des courbes et des angles précis. Les machines de formage hydraulique sont couramment utilisées pour ces opérations en raison de leur capacité à exercer une pression uniforme sur le matériau, assurant ainsi une forme constante et sans défaut.
3. Bordeur Moulureuse Automatique
La bordeuse moulureuse automatique est une machine spécialisée utilisée principalement dans l’industrie de la signalisation et de la fabrication de panneaux. Cette machine combine les fonctions de bordage et de moulurage, permettant de créer des panneaux avec des bords renforcés et des motifs moulés en une seule opération. L’automatisation de cette machine permet de produire des panneaux à grande échelle avec une qualité constante.
4. Machines pour la Fabrication de Panneaux de Signalisation
Les machines pour la fabrication de panneaux de signalisation sont conçues pour produire des panneaux routiers, des panneaux d’avertissement, et d’autres types de signalisation utilisés dans les infrastructures publiques. Ces machines intègrent des technologies de formage, de découpe, et de marquage pour créer des panneaux résistants et conformes aux normes de sécurité.
L’intégration de bordeuses hydrauliques dans ces machines permet de renforcer les bords des panneaux, tandis que les systèmes de marquage automatisés assurent une application précise et durable des textes et des symboles. Ces machines sont essentielles pour répondre aux besoins croissants en matière de signalisation dans les infrastructures modernes.
5. Impact sur la Qualité et la Durabilité des Produits
Les machines spécialisées telles que les machines de fabrication de panneaux routiers et les machines de formage de tuyaux jouent un rôle crucial dans l’amélioration de la qualité et de la durabilité des produits finis. En utilisant des techniques de formage précises et en intégrant des systèmes de contrôle avancés, ces machines permettent de produire des pièces qui non seulement répondent aux spécifications techniques, mais qui sont également résistantes aux conditions d’utilisation difficiles.
Par exemple, les panneaux routiers fabriqués à l’aide de bordeuses moulureuses automatiques et de machines à moulurer présentent une durabilité accrue, leur permettant de résister à des conditions météorologiques extrêmes sans compromettre leur lisibilité ou leur intégrité structurale.
De même, les tuyaux formés par des machines de formage de tuyaux montrent une résistance supérieure à la pression et aux contraintes mécaniques, ce qui est essentiel pour leur utilisation dans des applications critiques telles que le transport de fluides sous haute pression ou la construction de structures souterraines.
Avec ces nouvelles sections, nous avons maintenant couvert l’importance de l’automatisation dans les lignes de production et les machines spécifiques pour la fabrication de produits particuliers. Les sections restantes se concentreront sur les machines de polissage et d’emboutissage, ainsi que sur les dernières innovations dans le domaine des machines de formage.
Machines de Polissage et d’Emboutissage
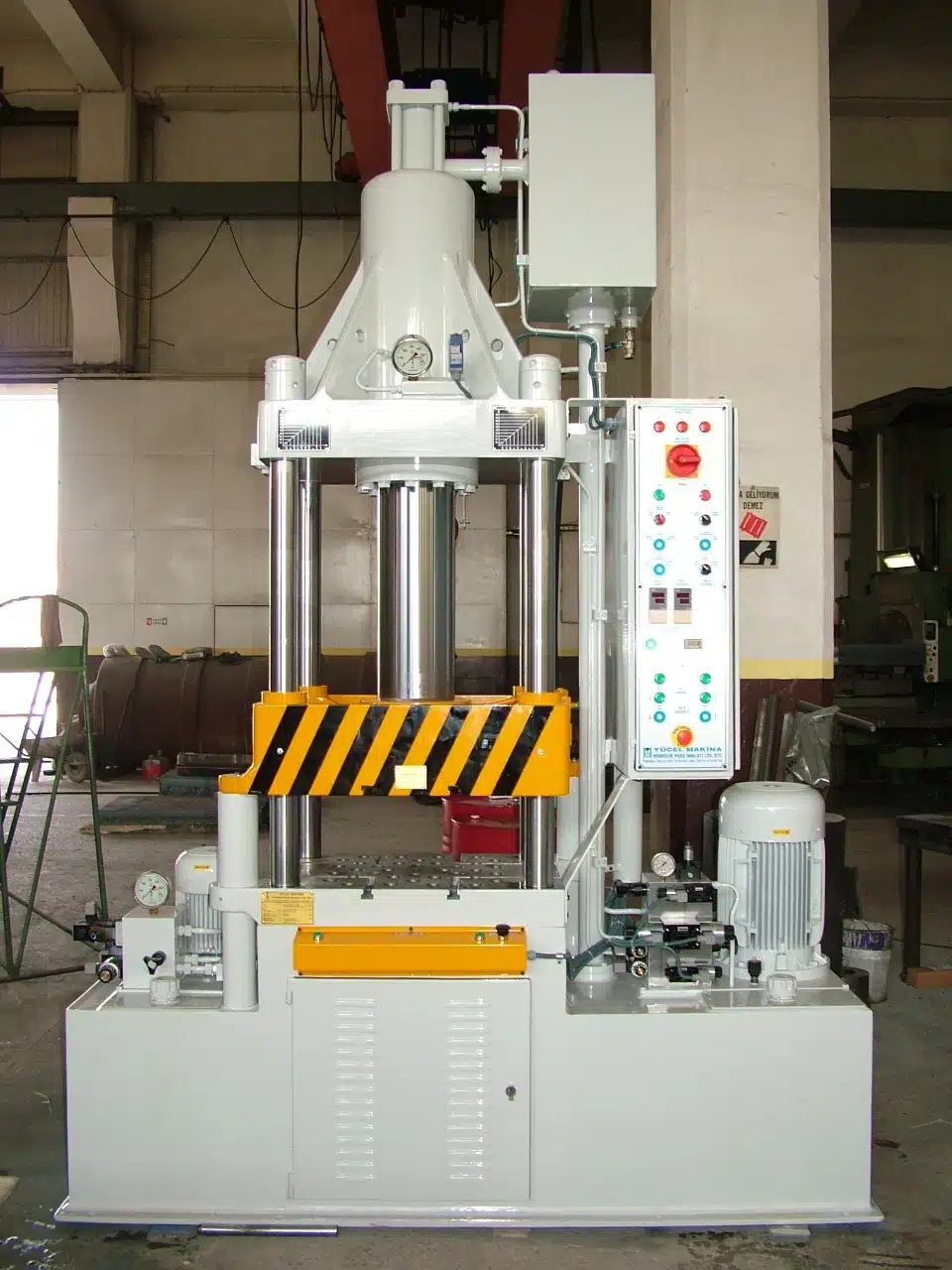
Le polissage est une étape cruciale dans de nombreux processus de fabrication, en particulier pour les pièces métalliques qui nécessitent une finition lisse et sans défaut. Les machines de polissage industriel sont conçues pour effectuer ce travail avec une grande précision, en éliminant les imperfections de surface telles que les rayures, les bosses ou les marques laissées par d’autres processus de fabrication.
Les machines de polissage industrielles peuvent être manuelles ou automatisées, et elles sont équipées de divers types d’abrasifs qui permettent de traiter différentes surfaces métalliques. Par exemple, une mini presse hydraulique peut être utilisée pour le polissage de petites pièces avec des exigences de finition élevées. Les machines de polissage industrielle sont particulièrement importantes dans des industries telles que l’automobile, l’aéronautique, et la bijouterie, où l’apparence et la finition des pièces jouent un rôle crucial.
Le polissage industriel ne se limite pas à l’amélioration esthétique; il peut également améliorer les propriétés mécaniques des pièces, telles que la résistance à la corrosion ou à l’usure. Par exemple, un polissage minutieux peut réduire la rugosité de surface, ce qui minimise les points de stress et prolonge la durée de vie de la pièce.
2. Techniques d’Emboutissage
L’emboutissage est une technique de formage dans laquelle une feuille de métal est transformée en une forme tridimensionnelle à l’aide d’une presse. Cette technique est largement utilisée pour produire des pièces creuses, telles que des réservoirs, des boîtiers, et des composants automobiles. L’emboutissage cylindrique et l’emboutissage à froid sont deux méthodes courantes qui permettent de former des pièces avec des contours complexes.
Les presses hydrauliques pour la transformation des métaux sont souvent utilisées pour l’emboutissage, car elles peuvent exercer une force importante sur le métal, tout en permettant un contrôle précis du processus. Ces presses sont capables de produire des pièces avec des tolérances très strictes, ce qui est essentiel pour des applications où la précision est primordiale.
L’emboutissage à froid est une méthode particulièrement avantageuse pour la production de grandes quantités de pièces. En raison de l’absence de chaleur dans le processus, le métal conserve ses propriétés mécaniques, ce qui permet de produire des pièces solides et résistantes. Cette technique est souvent utilisée dans l’industrie automobile pour la fabrication de pièces de châssis et de carrosserie.
3. Avantages des Machines de Polissage et d’Emboutissage
Les machines de polissage et d’emboutissage offrent plusieurs avantages clés pour les fabricants. Premièrement, elles permettent d’améliorer la qualité des produits finis en assurant des surfaces lisses et des formes précises. Deuxièmement, elles augmentent l’efficacité de la production en réduisant les temps de cycle et en minimisant les erreurs.
Les machines de polissage industriel sont particulièrement utiles pour atteindre une finition uniforme sur des pièces complexes, ce qui est essentiel dans des secteurs où l’esthétique et la performance sont cruciales. De plus, les machines de polissage industrielles automatisées peuvent fonctionner sans interruption, ce qui permet de produire de grandes quantités de pièces en un temps réduit.
En ce qui concerne l’emboutissage, les presses hydrauliques permettent de réaliser des opérations de formage complexes avec une grande précision. Cela réduit la nécessité de retouches manuelles et augmente la productivité. L’utilisation de presses pour l’emboutissage permet également de produire des pièces avec des formes difficiles à obtenir par d’autres méthodes, ce qui ouvre de nouvelles possibilités pour les concepteurs et les ingénieurs.
4. Innovations Récentes dans les Machines de Polissage et d’Emboutissage
Les innovations dans les machines de polissage et d’emboutissage continuent d’améliorer les capacités de production et la qualité des produits. Par exemple, l’intégration de systèmes de vision et de capteurs dans les machines de polissage permet d’automatiser le contrôle qualité, en détectant et en corrigeant les défauts de surface en temps réel.
Dans le domaine de l’emboutissage, l’avènement des presses hydrauliques à contrôle numérique a révolutionné le processus en permettant une programmation précise des opérations. Cela permet non seulement de réduire les temps de configuration, mais aussi d’optimiser les cycles de production en fonction des caractéristiques spécifiques des matériaux utilisés.
De plus, les nouvelles technologies de lubrification et de refroidissement des outillages ont permis d’augmenter la durabilité des outils utilisés dans les machines d’emboutissage, réduisant ainsi les coûts d’entretien et prolongeant la durée de vie des équipements.
Innovations et Avancées Technologiques
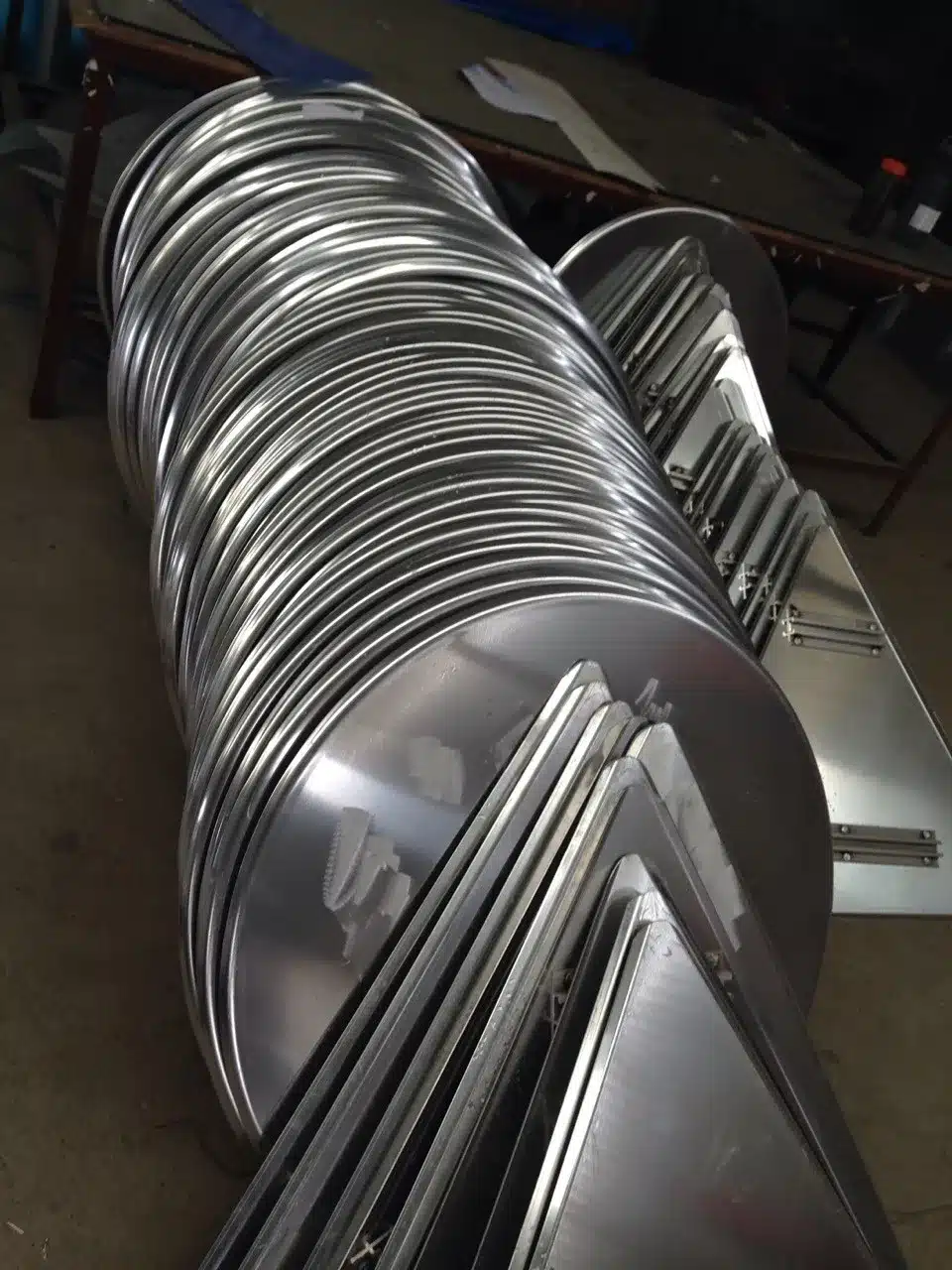
1. Nouvelles Tendances dans les Machines de Formage de Métal L’industrie du formage de métal est en constante évolution, avec des innovations technologiques qui permettent d’améliorer l’efficacité, la précision, et la flexibilité des processus de production. Parmi les tendances les plus marquantes, on trouve l’intégration de technologies numériques avancées dans les machines de formage de métal et les machines de formage hydraulique.
Les machines de formage hydraulique sont maintenant équipées de systèmes de contrôle intelligent qui ajustent automatiquement les paramètres de formage en fonction des propriétés du matériau et des spécifications du produit final. Ces systèmes permettent de réduire les temps de cycle, d’améliorer la qualité des pièces, et de minimiser les déchets de matériaux.
Une autre tendance importante est l’augmentation de l’utilisation des technologies de simulation dans le développement des processus de formage. Les logiciels de simulation permettent aux ingénieurs de modéliser les processus de formage avant la production, en identifiant les potentiels problèmes et en optimisant les paramètres de formage. Cela réduit les coûts de développement et accélère le temps de mise sur le marché des nouveaux produits.
2. Impact de l’Innovation sur la Compétitivité
L’adoption des nouvelles technologies de formage a un impact direct sur la compétitivité des entreprises industrielles. En intégrant des machines de formage de précision et des presses hydrauliques à haute performance, les entreprises peuvent améliorer la qualité de leurs produits, réduire les coûts de production, et répondre plus rapidement aux demandes du marché.
Les machines de formage multistations, par exemple, permettent d’effectuer plusieurs opérations de formage en une seule passe, ce qui réduit les besoins en équipements et en espace, tout en augmentant la vitesse de production. De plus, les systèmes de contrôle avancés permettent de réduire les temps d’arrêt en détectant et en corrigeant automatiquement les problèmes de production.
En outre, l’intégration des technologies de l’Internet des objets (IoT) dans les lignes de presses hydrauliques et autres machines de formage permet une surveillance en temps réel des performances des machines, ce qui aide à anticiper les pannes et à optimiser la maintenance. Cette approche proactive permet de maximiser l’utilisation des machines et de minimiser les interruptions de production, augmentant ainsi la compétitivité de l’entreprise.
3. Évolutions Futures dans le Domaine des Machines de Formage
Les évolutions futures dans le domaine des machines de formage seront probablement orientées vers une automatisation encore plus poussée et une personnalisation accrue des processus de production. Les machines de formage de précision deviendront de plus en plus intelligentes, capables de s’adapter automatiquement à des variations dans les matériaux ou les spécifications des produits.
Les lignes de production robotisées continueront de se développer, avec des robots de plus en plus polyvalents capables de manipuler des pièces complexes et d’effectuer plusieurs opérations de formage et d’assemblage. Ces développements permettront aux fabricants de produire des pièces de haute qualité à des coûts réduits, tout en augmentant leur flexibilité pour répondre à des demandes spécifiques des clients.
De plus, l’utilisation de l’intelligence artificielle dans l’optimisation des processus de formage ouvrira de nouvelles perspectives pour l’amélioration continue des performances des machines. L’IA pourra analyser des données en temps réel pour ajuster les paramètres de production, anticiper les besoins en maintenance, et proposer des améliorations pour augmenter l’efficacité et la qualité.
Conclusion
En conclusion, l’industrie du formage est en pleine mutation, portée par les innovations technologiques qui permettent d’améliorer continuellement la précision, la rapidité, et l’efficacité des processus de production. Les machines de formage de précision, les presses hydrauliques, et les lignes de production robotisées sont au cœur de cette transformation, offrant aux entreprises industrielles des outils puissants pour rester compétitives dans un marché globalisé.
L’intégration de technologies numériques avancées, telles que l’IoT et l’IA, dans les machines de formage ouvre de nouvelles possibilités pour l’automatisation et l’optimisation des processus de production. Ces technologies permettent de maximiser l’utilisation des ressources, de minimiser les coûts, et de produire des pièces de haute qualité qui répondent aux exigences croissantes des industries modernes.
Les perspectives d’avenir pour l’industrie du formage sont prometteuses, avec des machines de plus en plus intelligentes et des processus de production de plus en plus flexibles. Les entreprises qui investiront dans ces technologies seront en mesure de répondre plus rapidement aux évolutions du marché et de maintenir leur compétitivité à long terme.
Pour conclure, il est essentiel que les entreprises continuent d’explorer et d’adopter les nouvelles technologies de formage pour rester à la pointe de l’innovation industrielle. Les machines de formage et les presses hydrauliques de nouvelle génération représentent une opportunité majeure pour améliorer les performances des processus de production, réduire les coûts et répondre aux besoins croissants des industries mondiales.
Introduction Générale
Dans l’industrie moderne, la fabrication et la transformation des matériaux nécessitent l’utilisation d’équipements de plus en plus sophistiqués. Les machines de formage et autres outils industriels jouent un rôle crucial dans la création de produits de haute précision, durables et conformes aux spécifications rigoureuses de différents secteurs tels que l’automobile, l’aéronautique, et l’électronique. Ce texte explore en détail les différents types de machines et leurs applications industrielles.
Machine de Formage
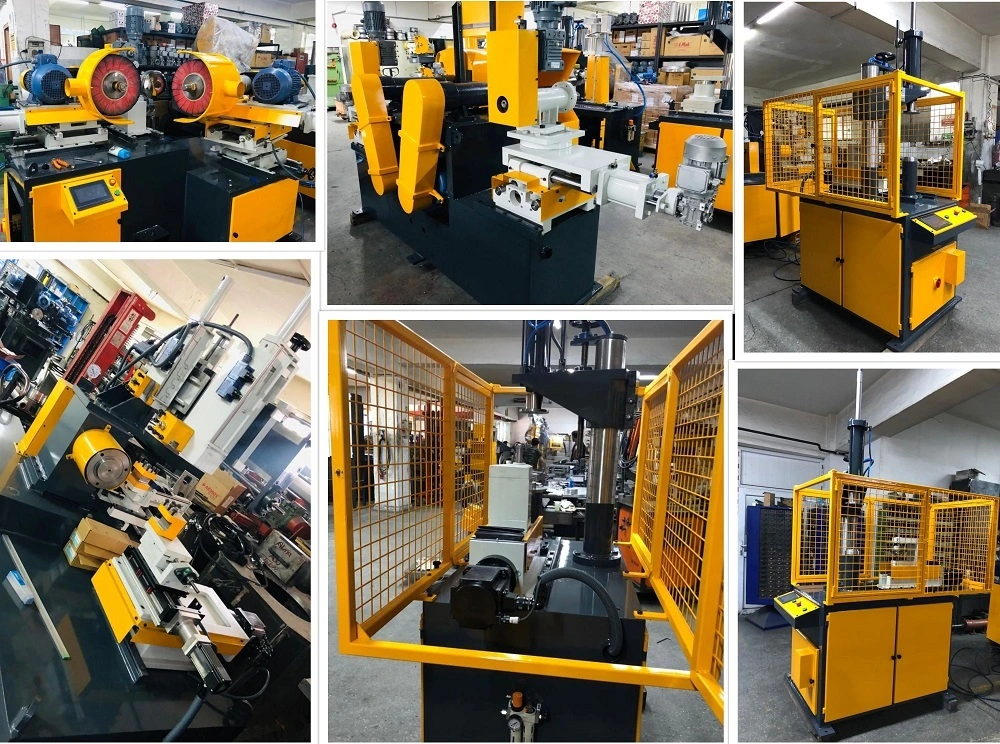
La machine de formage est un appareil essentiel dans de nombreux processus de fabrication. Elle permet de donner à un matériau, souvent du métal, une forme spécifique en appliquant des forces mécaniques. Ce type de machine est utilisé pour créer des pièces aux géométries précises, répondant à des spécifications techniques strictes.
Machine de Formage de Précision
Les machines de formage de précision sont des équipements spécialisés capables de produire des pièces avec des tolérances extrêmement faibles. Ces machines sont essentielles dans les secteurs où la précision est critique, comme dans la fabrication de composants électroniques ou dans l’industrie médicale. Elles permettent d’obtenir des pièces aux dimensions exactes, avec une finition impeccable.
Bordeuse pour Tôle
La bordeuse pour tôle est un outil utilisé pour façonner les bords des tôles métalliques. Elle est souvent utilisée dans l’industrie automobile pour produire des panneaux de carrosserie ou d’autres composants métalliques nécessitant des bords renforcés ou des formes complexes. La précision de ces machines est cruciale pour assurer la durabilité et la fonctionnalité des pièces.
Machine de Formage Verticale
La machine de formage verticale est conçue pour effectuer des opérations de formage sur un axe vertical. Ce type de machine est idéal pour les pièces nécessitant une manipulation précise et un contrôle accru pendant le processus de formage. Les machines de formage verticales sont largement utilisées dans la production de pièces complexes, comme les composants aéronautiques.
Machine de Formage Multistations
Les machines de formage multistations sont des systèmes avancés qui permettent de réaliser plusieurs opérations de formage successives sur une même pièce sans la déplacer d’une station à une autre. Ces machines sont utilisées dans des processus de production en série où la précision et l’efficacité sont cruciales.
Cintreuse
La cintreuse est une machine utilisée pour plier ou cintrer des tubes, des barres ou des tôles métalliques en leur donnant la forme souhaitée. Ces machines sont essentielles dans la fabrication de structures métalliques, de châssis, et de composants industriels où la forme précise du métal est critique pour l’intégrité structurelle.
Ligne de Presses de Découpe
Les lignes de presses de découpe sont des systèmes intégrés utilisés pour découper des pièces à partir de feuilles de métal ou d’autres matériaux. Ces lignes combinent plusieurs presses et outils de découpe pour produire des pièces de manière rapide et précise, réduisant ainsi les temps de cycle et augmentant la productivité.
Machine de Formage de Découpe
La machine de formage de découpe combine des opérations de formage et de découpe en un seul processus. Elle est particulièrement utile dans les chaînes de production où il est nécessaire de découper et de former des pièces en une seule étape, optimisant ainsi le flux de production et réduisant les besoins en manipulations.
Cintreuse de Découpe
La cintreuse de découpe est une machine qui combine les fonctions de cintrage et de découpe. Elle est utilisée pour former des pièces avec des courbes et des angles complexes tout en réalisant des découpes précises. Cette machine est souvent employée dans la fabrication de composants tubulaires et de structures métalliques.
Poinçonneuse de Découpe
La poinçonneuse de découpe est une machine qui utilise des poinçons pour perforer ou découper des trous et des formes spécifiques dans des matériaux métalliques. Ces machines sont essentielles dans la fabrication de pièces qui nécessitent des ouvertures précises, comme les grilles, les panneaux perforés ou les pièces d’assemblage.
Ligne de Presses
Les lignes de presses sont des installations complexes qui regroupent plusieurs presses pour effectuer différentes opérations de formage, de découpe ou d’emboutissage en séquence. Ces lignes sont couramment utilisées dans les usines de production de masse, où l’efficacité et la précision sont cruciales.
Presse Industrielle
La presse industrielle est une machine utilisée pour appliquer une force importante sur un matériau afin de le former, le découper ou l’assembler. Ces presses sont utilisées dans divers processus industriels, allant de l’emboutissage à la compression, et sont disponibles en différents types, y compris mécaniques, hydrauliques et pneumatiques.
Presse de Découpe
La presse de découpe est un type spécifique de presse industrielle utilisée pour découper des formes dans des matériaux comme le métal, le plastique ou le tissu. Ces presses sont équipées de matrices de découpe qui permettent de produire des pièces avec des contours précis et nets, essentiels pour l’assemblage ou la fabrication de produits finis.
Bordeuse Motorisée
La bordeuse motorisée est une machine utilisée pour façonner les bords des tôles ou des plaques métalliques. Contrairement à une bordeuse manuelle, elle est équipée d’un moteur qui automatise le processus, permettant ainsi un travail plus rapide et précis. Elle est couramment utilisée dans la fabrication de pièces automobiles et aéronautiques.
Ligne de Production Robotisée
Les lignes de production robotisées intègrent des robots dans les processus de fabrication pour automatiser des tâches répétitives ou complexes. Ces lignes sont particulièrement utiles pour les industries nécessitant une production de masse avec une grande précision, comme l’automobile ou l’électronique. Les robots peuvent manipuler des pièces, effectuer des opérations de formage, de découpe, ou d’assemblage, avec une efficacité inégalée.
Ligne de Production de Pièces en Métal
Les lignes de production de pièces en métal sont conçues pour transformer des matières premières métalliques en pièces finies prêtes à être assemblées ou utilisées. Ces lignes intègrent plusieurs machines, telles que des presses, des cintreuses, et des machines de formage, pour créer des pièces métalliques précises et conformes aux spécifications techniques.
Machine à Moulurer
La machine à moulurer est utilisée pour créer des motifs en relief ou des formes complexes sur des matériaux, souvent utilisés pour des applications décoratives ou fonctionnelles. Ces machines sont couramment utilisées dans la fabrication de moulures, de cadres et de panneaux décoratifs pour l’industrie du bâtiment et de la signalisation.
Machine de Fabrication de Panneaux Routiers
Les machines de fabrication de panneaux routiers sont spécialisées dans la production de panneaux de signalisation routière. Ces machines combinent des opérations de découpe, de moulage et de marquage pour produire des panneaux durables, conformes aux normes de sécurité routière.
Bordeuse Moulureuse Automatique
La bordeuse moulureuse automatique est une machine combinant les fonctions de bordage et de moulage en une seule opération. Elle est utilisée pour produire des pièces avec des bords moulés et renforcés, souvent utilisées dans les industries de la signalisation et de l’automobile. L’automatisation de cette machine permet une production rapide et uniforme de pièces complexes.
Machines pour la Fabrication de Panneaux de Signalisation
Les machines pour la fabrication de panneaux de signalisation sont des systèmes complets qui incluent des machines de découpe, de formage, et de marquage. Elles permettent de produire des panneaux de signalisation de haute qualité en respectant les normes en vigueur pour la visibilité, la durabilité et la sécurité.
Bordeuse Hydraulique
La bordeuse hydraulique est un type de bordeuse qui utilise la pression hydraulique pour former les bords des tôles ou plaques métalliques. Ce système offre une force plus importante et une plus grande précision, rendant cette machine idéale pour les opérations nécessitant un formage rigoureux des bords.
Machine de Formage de Tuyau
Les machines de formage de tuyau sont utilisées pour former des tuyaux à partir de tubes ou de plaques métalliques. Elles sont essentielles dans la production de conduites pour le pétrole, le gaz, et les systèmes de plomberie, où la précision du formage est cruciale pour assurer l’intégrité des tuyaux sous pression.
Pliage de Tôle
Le pliage de tôle est un processus dans lequel une tôle métallique est pliée pour créer des angles, des courbes, ou des formes spécifiques. Cette opération est réalisée à l’aide de presses plieuses ou de cintreuses, et est essentielle dans la fabrication de pièces de structure ou de carrosserie.
Mise en Forme des Tubes
La mise en forme des tubes est une opération qui consiste à plier, cintrer, ou emboutir des tubes métalliques pour leur donner la forme souhaitée. Ces techniques sont utilisées dans la fabrication de cadres, de conduites, et d’autres structures tubulaires nécessitant une précision élevée.
Ligne de Presses Hydraulique
Les lignes de presses hydrauliques sont des installations industrielles qui utilisent la force hydraulique pour effectuer des opérations de formage, de découpe, ou d’emboutissage sur des matériaux métalliques. Ces lignes sont particulièrement efficaces pour les grandes séries de production, où la constance et la puissance sont essentielles.
Machine de Formage Hydraulique
La machine de formage hydraulique est un équipement qui utilise la pression hydraulique pour former des matériaux en appliquant une force contrôlée. Ces machines sont couramment utilisées dans l’emboutissage, le cintrage, et d’autres opérations de formage où une force importante est nécessaire pour façonner des pièces métalliques.
Machine de Formage de Métal
Les machines de formage de métal englobent une large gamme d’équipements conçus pour transformer les métaux en formes spécifiques. Ces machines utilisent des techniques variées, comme le pliage, l’emboutissage, et la découpe, pour produire des pièces métalliques conformes aux exigences des industries modernes.
Bordeuse Automatique
La bordeuse automatique est une machine qui automatise le processus de formage des bords des tôles. Elle est souvent utilisée dans des lignes de production en série, où la rapidité et la précision sont essentielles pour produire des pièces conformes aux spécifications.
Poinçonneuse Semi-automatique
La poinçonneuse semi-automatique combine des éléments de contrôle manuel et automatique pour perforer ou découper des formes dans des matériaux. Ce type de machine est utilisé dans des opérations de production où un certain degré de flexibilité est nécessaire, permettant à l’opérateur de contrôler certaines étapes du processus.
Poinçonneuse de Formage
La poinçonneuse de formage est un outil utilisé pour perforer et former des matériaux métalliques en une seule opération. Elle est couramment utilisée pour produire des pièces qui nécessitent à la fois des trous et des contours spécifiques, comme les pièces de carrosserie ou les panneaux perforés.
Presse pour Tôle
La presse pour tôle est une machine industrielle utilisée pour appliquer une force sur une tôle afin de la découper, de la plier ou de l’emboutir en une forme précise. Ces presses sont essentielles dans la fabrication de pièces de structure, de panneaux, et d’autres composants en tôle.
Machine Polissage Industriel
La machine de polissage industriel est utilisée pour améliorer la finition de surfaces métalliques en éliminant les imperfections et en produisant une surface lisse et brillante. Ces machines sont essentielles dans la production de pièces où l’esthétique et la résistance à la corrosion sont des critères importants.
Mini Presse Hydraulique
La mini presse hydraulique est une version compacte de la presse hydraulique, utilisée pour des opérations de formage ou d’emboutissage sur des pièces de petite taille. Elle est idéale pour les ateliers ou les lignes de production nécessitant des presses polyvalentes et faciles à intégrer.
Emboutissage Cylindrique
L’emboutissage cylindrique est une technique de formage utilisée pour créer des formes cylindriques ou coniques à partir de feuilles de métal. Cette technique est couramment utilisée dans la fabrication de réservoirs, de tubes, et d’autres composants creux.
Machine de Polissage Industrielle
La machine de polissage industrielle est un équipement spécialisé conçu pour le polissage en masse de pièces métalliques. Elle est souvent utilisée dans des secteurs comme l’automobile ou l’aéronautique, où la qualité de la finition de surface est essentielle.
Emboutissage à Froid
L’emboutissage à froid est une méthode de formage qui permet de transformer une tôle en une forme tridimensionnelle sans chauffer le matériau. Ce procédé est largement utilisé dans l’industrie pour produire des pièces solides et précises, notamment dans le secteur automobile.
Conclusion
Les machines de formage et autres équipements industriels mentionnés ici sont essentiels pour la production de pièces et de structures métalliques précises, durables et conformes aux exigences modernes. Chaque machine ou technique a son rôle spécifique dans le processus de fabrication, contribuant à la création de produits de haute qualité dans divers secteurs industriels. L’innovation continue dans ces technologies garantit que les industries peuvent répondre aux défis futurs avec efficacité et précision.
Machine de Formage
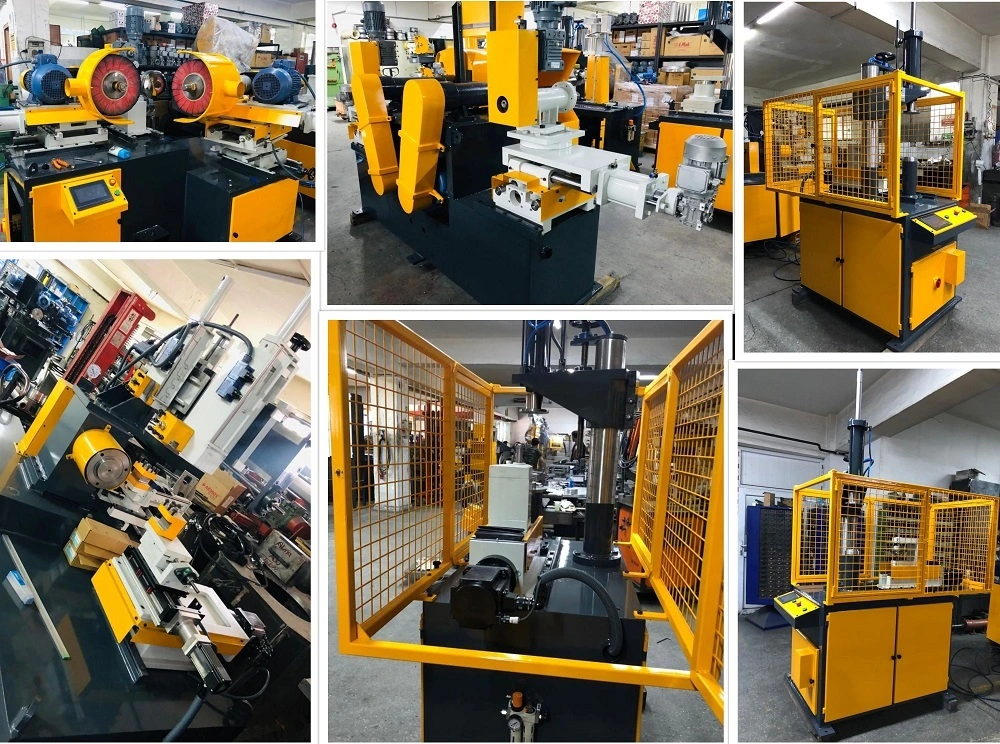
La machine de formage est un équipement essentiel dans l’industrie de la transformation des matériaux, particulièrement des métaux. Le formage désigne un ensemble de procédés par lesquels un matériau est déformé pour adopter une nouvelle forme sous l’effet de forces mécaniques. Ces machines sont utilisées pour produire une grande variété de pièces, allant des composants de carrosserie automobile aux structures métalliques pour l’aéronautique, en passant par des pièces pour l’électronique et les biens de consommation.
Fonctionnement et Types
Les machines de formage fonctionnent généralement en appliquant une pression sur le matériau à l’aide de moules ou de matrices. Cette pression peut être exercée par des outils mécaniques, hydrauliques ou pneumatiques. Parmi les types de machines de formage, on trouve :
- Les presses mécaniques : Elles utilisent des systèmes d’engrenages ou des volants pour appliquer une force de formage.
- Les presses hydrauliques : Elles utilisent la pression hydraulique pour exercer une force importante sur le matériau, permettant ainsi de former des pièces plus grandes ou plus complexes.
- Les machines de formage par étirage : Utilisées pour les tôles métalliques, elles étirent le matériau au-dessus d’un moule pour lui donner une forme spécifique.
Applications
Les machines de formage sont omniprésentes dans de nombreux secteurs industriels. Dans l’industrie automobile, elles sont utilisées pour produire des panneaux de carrosserie, des composants de châssis, et d’autres pièces critiques. Dans l’aéronautique, elles permettent de fabriquer des éléments structurels légers mais robustes, capables de résister à des conditions extrêmes. Les industries de l’électronique utilisent également ces machines pour la fabrication de boîtiers et de composants nécessitant une haute précision.
Avantages et Innovations
L’un des principaux avantages des machines de formage est leur capacité à produire des pièces en grande série avec une précision constante. Les innovations récentes, telles que l’intégration de systèmes de contrôle numériques et de technologies de simulation, ont permis d’améliorer encore plus la précision et l’efficacité de ces machines. Ces technologies permettent aux fabricants de simuler les processus de formage avant de les réaliser, ce qui réduit les erreurs et optimise les performances.
Machine de Formage de Précision
Les machines de formage de précision sont des outils essentiels pour les industries où la précision est critique, comme l’aéronautique, l’automobile, ou encore l’électronique. Ces machines sont conçues pour produire des pièces avec des tolérances extrêmement faibles, souvent de l’ordre du micromètre. Elles permettent de réaliser des opérations de formage très précises, répondant aux exigences rigoureuses des secteurs qui les utilisent.
Caractéristiques Techniques
Les machines de formage de précision se distinguent par leur capacité à contrôler avec exactitude les paramètres de formage, tels que la force appliquée, la vitesse, et la température. Elles sont souvent équipées de systèmes de contrôle numérique (CNC) qui permettent de programmer et d’automatiser les processus de formage avec une grande précision.
Ces machines peuvent réaliser diverses opérations, notamment le pliage, l’emboutissage, le découpage et l’étirage de matériaux. Elles sont capables de travailler avec des métaux aussi bien qu’avec des matériaux composites, des plastiques, et d’autres matériaux de haute technologie.
Applications
Les applications des machines de formage de précision sont variées et couvrent plusieurs secteurs industriels. Dans l’industrie aérospatiale, elles sont utilisées pour produire des pièces structurelles légères mais résistantes, essentielles pour la performance des avions. Dans l’automobile, ces machines permettent de fabriquer des composants critiques tels que les pièces de moteur, les boîtiers de transmission, et les structures de châssis, où la précision est indispensable pour garantir la sécurité et la performance.
Dans le domaine de l’électronique, les machines de formage de précision sont utilisées pour produire des boîtiers miniaturisés, des circuits imprimés, et d’autres composants nécessitant une extrême précision. Les progrès dans les technologies de formage de précision ont également permis de répondre aux besoins de l’industrie médicale, où des pièces complexes et petites, comme les implants et les instruments chirurgicaux, sont fabriquées avec ces machines.
Avantages et Défis
L’un des principaux avantages des machines de formage de précision est leur capacité à produire des pièces complexes avec une qualité constante. Cependant, ces machines sont souvent coûteuses et nécessitent des compétences spécialisées pour leur programmation et leur maintenance. Les innovations récentes dans les domaines de l’intelligence artificielle et du contrôle automatisé promettent d’améliorer encore l’efficacité de ces machines, en réduisant les coûts et en augmentant la flexibilité des processus de production.
Bordeuse pour Tôle
La bordeuse pour tôle est un outil spécialisé utilisé dans le travail des métaux, notamment pour façonner les bords des tôles. Ce type de machine est particulièrement utile dans les industries où les tôles métalliques doivent être renforcées ou façonnées pour créer des pièces aux bords lisses et réguliers.
Principe de Fonctionnement
La bordeuse pour tôle fonctionne en plaçant une tôle entre deux rouleaux ou matrices, qui appliquent une pression uniforme sur les bords pour les façonner. Ce processus peut être effectué manuellement ou être automatisé dans des versions motorisées de la machine. Le but est de créer un bord lisse et sans bavure, souvent avec un pli ou une courbure spécifique pour renforcer la pièce ou faciliter son assemblage avec d’autres composants.
Applications
Les bordeuses pour tôle sont couramment utilisées dans l’industrie automobile pour la fabrication de panneaux de carrosserie, de portes, de capots, et d’autres composants nécessitant des bords renforcés ou décoratifs. Elles sont également utilisées dans la fabrication d’appareils électroménagers, où les bords des pièces doivent être esthétiques et sûrs pour une manipulation quotidienne.
Dans le secteur de la construction, ces machines sont utilisées pour produire des éléments de toiture, des gouttières, et d’autres pièces métalliques qui nécessitent un bord propre et durable. Elles jouent également un rôle crucial dans la fabrication de meubles en métal et de structures architecturales, où la précision et la finition des bords sont essentielles pour l’assemblage et l’apparence finale.
Avantages et Innovations
L’utilisation d’une bordeuse pour tôle permet de renforcer les bords des pièces métalliques, améliorant ainsi leur durabilité et leur résistance aux chocs et à la corrosion. Les versions motorisées de ces machines offrent une productivité accrue et une qualité constante des pièces produites.
Les innovations récentes dans ce domaine incluent l’intégration de systèmes de contrôle numérique, permettant une programmation précise des opérations de bordage et une adaptation rapide aux différentes spécifications de production. Cela permet également de réduire les temps de réglage et d’améliorer la répétabilité des processus, assurant ainsi une qualité constante.
Machine de Formage Verticale

La machine de formage verticale est un type d’équipement de formage qui opère sur un axe vertical, offrant des avantages particuliers en termes de contrôle et de précision. Ces machines sont particulièrement adaptées pour les pièces qui nécessitent une manipulation délicate ou des opérations de formage complexes.
Fonctionnement
Contrairement aux machines de formage traditionnelles qui fonctionnent sur un plan horizontal, les machines de formage verticales appliquent la force de formage dans une direction verticale. Cela permet de mieux contrôler la position et le mouvement du matériau pendant le formage, réduisant ainsi les risques de distorsion ou de déformation indésirable.
Ces machines sont souvent utilisées pour le formage de pièces cylindriques ou coniques, ainsi que pour des opérations où la précision de l’alignement est cruciale. Elles peuvent être équipées de diverses matrices et outils interchangeables pour réaliser des opérations de pliage, d’emboutissage, et de découpe.
Applications
Les machines de formage verticales sont largement utilisées dans l’industrie aéronautique pour la production de composants structurels complexes, tels que des cadres, des cônes d’ailes, ou des carénages. Elles sont également utilisées dans l’industrie automobile pour la fabrication de pièces telles que des réservoirs, des carters, et d’autres composants nécessitant un formage précis.
Dans le domaine médical, ces machines sont employées pour produire des implants et des instruments chirurgicaux de haute précision, où le contrôle exact du formage est essentiel pour assurer la conformité aux normes strictes de l’industrie.
Avantages
L’un des principaux avantages des machines de formage verticales est leur capacité à réaliser des opérations de formage complexes avec une grande précision. L’orientation verticale permet une meilleure distribution des forces de formage, ce qui réduit les déformations indésirables et améliore la qualité des pièces produites.
De plus, ces machines sont souvent équipées de systèmes de contrôle automatisés qui permettent de programmer et d’ajuster les opérations de formage en fonction des spécifications exactes des pièces à produire. Cela permet une plus grande flexibilité dans la production et une réduction des temps de réglage, augmentant ainsi l’efficacité et la productivité globale.
Machine de Formage Multistations
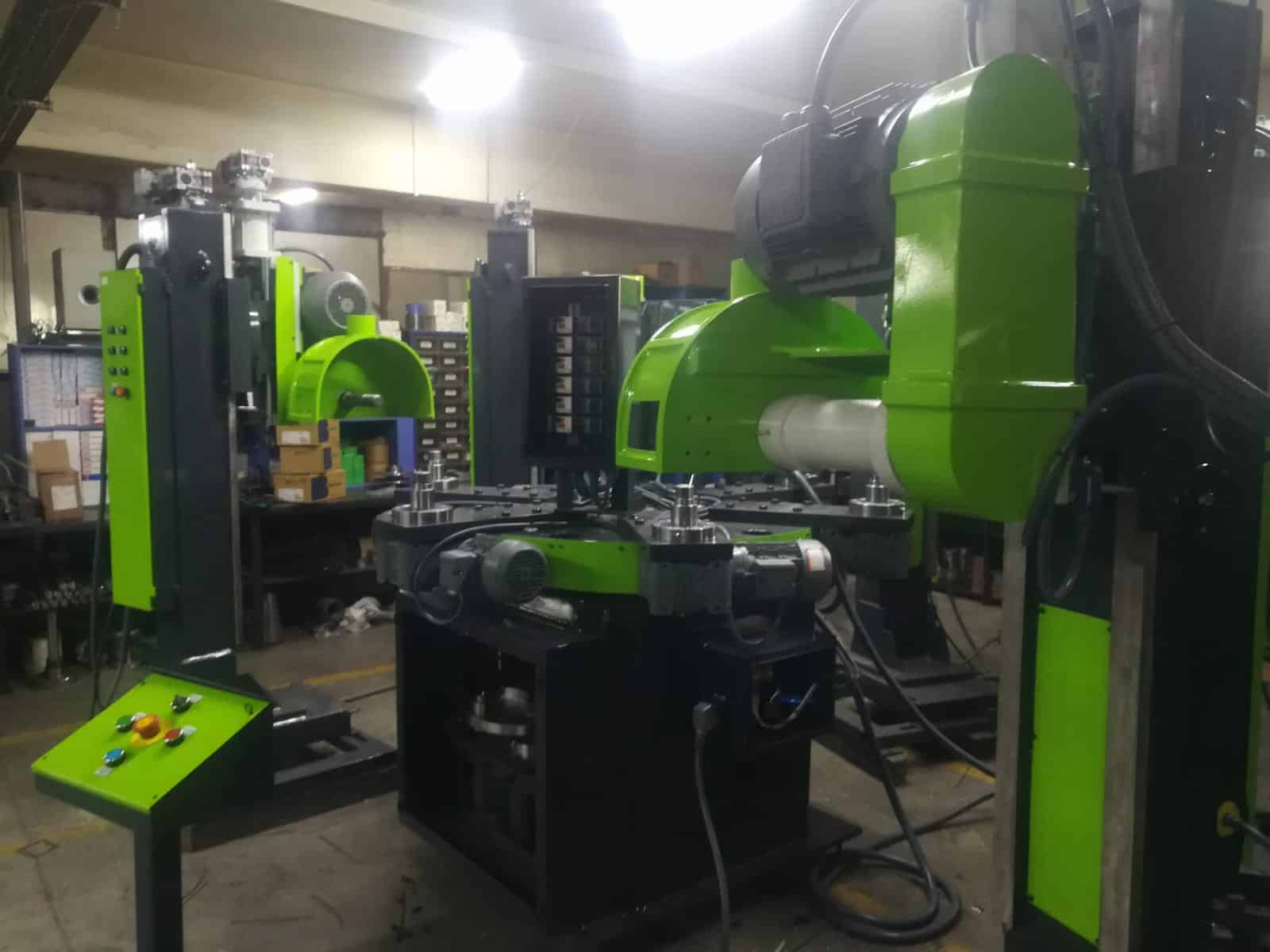
La machine de formage multistations est un système avancé conçu pour effectuer plusieurs opérations de formage successives sur une même pièce sans avoir besoin de la déplacer d’une station à une autre. Ce type de machine est particulièrement utile dans les processus de production en série, où la précision, la rapidité, et l’efficacité sont essentielles.
Fonctionnement
Les machines de formage multistations sont composées de plusieurs unités de travail, chacune dédiée à une opération spécifique de formage, comme le pliage, l’emboutissage, la découpe ou le poinçonnage. La pièce à usiner est déplacée automatiquement d’une station à l’autre, chaque station effectuant une opération différente jusqu’à ce que la pièce soit complètement formée.
Ces machines sont souvent contrôlées par un système centralisé qui synchronise les différentes opérations pour optimiser le flux de production et minimiser les temps d’arrêt. Les outils et les matrices peuvent être changés rapidement pour adapter la machine à la production de différentes pièces, ce qui en fait un outil extrêmement polyvalent pour la production en série.
Applications
Les machines de formage multistations sont largement utilisées dans l’industrie automobile pour la fabrication de composants complexes nécessitant plusieurs opérations de formage, tels que les pièces de carrosserie, les supports de moteur, et les éléments structurels. Elles sont également utilisées dans la production d’appareils électroménagers, de pièces de machines, et de composants électroniques, où la précision et la rapidité sont cruciales.
Dans l’industrie de l’emballage, ces machines permettent de produire des boîtiers métalliques, des canettes, et d’autres conteneurs avec des formes complexes en une seule séquence de production, ce qui réduit considérablement les coûts de fabrication et améliore l’efficacité.
Avantages
L’un des principaux avantages des machines de formage multistations est leur capacité à réaliser des opérations de formage complexes en une seule étape, sans nécessiter de transfert manuel de la pièce d’une machine à une autre. Cela réduit non seulement les temps de cycle, mais améliore également la précision et la répétabilité des processus de production.
Ces machines permettent également une grande flexibilité dans la production, car elles peuvent être rapidement reconfigurées pour produire différents types de pièces. Cela est particulièrement important dans les environnements de production modernes, où les besoins peuvent changer rapidement en fonction de la demande du marché.
Cintreuse
La cintreuse est une machine industrielle utilisée pour plier ou courber des barres, des tubes, des profilés ou des tôles en métal. Cette opération est essentielle dans la fabrication de structures métalliques, d’équipements industriels, et de nombreux produits où la forme précise du matériau est critique pour l’intégrité structurelle et la fonctionnalité.
Types de Cintreuses
Il existe plusieurs types de cintreuses, chacune conçue pour des applications spécifiques :
- Cintreuse manuelle : Utilisée pour les travaux simples ou les petites séries, elle fonctionne par action mécanique directe, souvent à l’aide d’une manivelle.
- Cintreuse hydraulique : Elle utilise la pression hydraulique pour courber le matériau, ce qui permet de plier des pièces plus épaisses ou plus résistantes.
- Cintreuse CNC : Équipée d’un système de contrôle numérique (CNC), elle permet de programmer des courbures précises et répétitives, idéale pour les productions en série où une grande précision est requise.
Applications
Les cintreuses sont couramment utilisées dans de nombreux secteurs industriels :
- Construction : Pour la création de structures métalliques telles que des poutres, des colonnes, ou des cadres.
- Automobile : Pour la fabrication de châssis, de conduites de carburant, de systèmes d’échappement, et d’autres composants nécessitant des courbes précises.
- Aéronautique : Pour produire des pièces légères mais résistantes, comme les cadres de soutien ou les conduits d’air.
Avantages et Défis
L’utilisation d’une cintreuse permet de créer des formes complexes à partir de matériaux métalliques tout en maintenant l’intégrité du matériau. Les cintreuses modernes, particulièrement celles équipées de CNC, offrent une précision élevée et une répétabilité, ce qui est crucial pour les industries nécessitant des normes de qualité strictes.
Cependant, le cintrage de matériaux épais ou durs peut présenter des défis, notamment le risque de fissuration ou de rupture du matériau. Les innovations dans les technologies de cintrage, comme l’introduction de logiciels de simulation, permettent de mieux anticiper ces problèmes et d’optimiser les paramètres de cintrage pour éviter les défauts.
Ligne de Presses de Découpe
Une ligne de presses de découpe est un système automatisé qui combine plusieurs presses pour réaliser des opérations de découpe successives sur des feuilles de métal ou d’autres matériaux plats. Ces lignes sont conçues pour maximiser l’efficacité de la production en permettant un flux continu de matière première à travers plusieurs étapes de découpe.
Fonctionnement
Dans une ligne de presses de découpe, le matériau est introduit sous forme de bobines ou de feuilles, puis est automatiquement alimenté dans une série de presses. Chaque presse est équipée d’outils de découpe spécifiques qui réalisent des découpes précises selon les spécifications requises.
Les presses peuvent être mécaniques ou hydrauliques, en fonction des besoins de force et de précision. Les lignes modernes sont souvent équipées de systèmes de contrôle numérique (CNC) qui permettent de programmer et de surveiller chaque étape du processus, garantissant ainsi une production cohérente et de haute qualité.
Applications
Les lignes de presses de découpe sont largement utilisées dans :
- L’industrie automobile : Pour la fabrication de pièces de carrosserie, de supports, et d’autres composants métalliques nécessitant des découpes précises.
- L’industrie de l’électronique : Pour découper des boîtiers, des châssis, et d’autres pièces métalliques avec des tolérances très strictes.
- L’industrie de l’emballage : Pour produire des emballages métalliques, comme les boîtes de conserve, avec des formes spécifiques et des découpes complexes.
Avantages
L’avantage principal d’une ligne de presses de découpe est sa capacité à produire de grandes quantités de pièces découpées avec une précision et une rapidité élevées. Cela permet de répondre aux exigences de production en série tout en maintenant des coûts de production compétitifs.
De plus, l’automatisation des lignes de découpe permet de réduire les erreurs humaines, d’optimiser l’utilisation des matériaux, et de minimiser les déchets, ce qui est particulièrement important dans les industries où la gestion des ressources est cruciale.
Machine de Formage de Découpe

La machine de formage de découpe est un équipement polyvalent qui combine les opérations de formage et de découpe en un seul processus. Ce type de machine est idéal pour les chaînes de production où il est nécessaire de transformer des matériaux en pièces finies en une seule étape, optimisant ainsi le flux de production.
Principe de Fonctionnement
Une machine de formage de découpe fonctionne en utilisant des matrices ou des moules pour donner au matériau la forme désirée, tout en réalisant simultanément des découpes précises. Cela permet de créer des pièces aux contours complexes et aux formes précises sans avoir besoin de transferts entre différentes machines.
Ces machines sont souvent équipées de systèmes de contrôle CNC qui permettent de programmer les opérations de formage et de découpe avec une grande précision, garantissant ainsi une qualité constante des pièces produites.
Applications
Les machines de formage de découpe sont utilisées dans de nombreux secteurs industriels, notamment :
- Automobile : Pour la production de pièces de carrosserie, de supports, et de composants structurels.
- Aéronautique : Pour fabriquer des éléments légers mais résistants, tels que des cadres et des panneaux.
- Électronique : Pour produire des boîtiers, des châssis, et d’autres composants nécessitant des découpes précises et un formage complexe.
Avantages
L’un des principaux avantages d’une machine de formage de découpe est sa capacité à combiner plusieurs opérations en une seule étape, ce qui réduit les temps de cycle et améliore l’efficacité globale de la production. Cela permet également de réduire les coûts de main-d’œuvre et de minimiser les erreurs associées aux transferts manuels entre différentes machines.
Les innovations récentes dans ce domaine incluent l’intégration de technologies de vision et de capteurs qui permettent de surveiller en temps réel la qualité des pièces produites et d’ajuster automatiquement les paramètres de formage et de découpe pour corriger les défauts.
Cintreuse de Découpe

La cintreuse de découpe est une machine qui combine les fonctions de cintrage et de découpe en un seul équipement. Ce type de machine est particulièrement utile dans la fabrication de pièces nécessitant à la fois des courbures précises et des découpes complexes, optimisant ainsi les processus de production.
Fonctionnement
La cintreuse de découpe fonctionne en utilisant des matrices ou des outils spécifiques pour plier et découper des pièces de métal en une seule opération. Le matériau est alimenté dans la machine, où il est d’abord cintré pour obtenir la forme désirée, puis découpé selon les spécifications requises.
Ces machines sont souvent équipées de systèmes CNC qui permettent de programmer des séquences de cintrage et de découpe complexes, assurant ainsi une production précise et répétitive. Les cintreuses de découpe peuvent traiter différents types de matériaux, y compris les tubes, les barres, et les tôles métalliques.
Applications
Les cintreuses de découpe sont couramment utilisées dans plusieurs industries :
- Automobile : Pour la fabrication de cadres, de systèmes d’échappement, et de conduites de carburant où des courbes précises et des découpes spécifiques sont nécessaires.
- Construction : Pour produire des éléments structurels métalliques, tels que des poutres et des colonnes avec des formes spécifiques.
- Mobilier en métal : Pour créer des cadres et des structures avec des courbures et des découpes décoratives ou fonctionnelles.
Avantages
L’utilisation d’une cintreuse de découpe permet de réduire le nombre de machines et d’opérations nécessaires pour produire des pièces complexes, ce qui se traduit par une augmentation de l’efficacité et une réduction des coûts de production. De plus, la capacité de la machine à réaliser des opérations de cintrage et de découpe en une seule étape réduit le risque d’erreurs associées à la manipulation manuelle et aux transferts entre machines.
Les machines modernes intègrent également des technologies de contrôle en boucle fermée qui ajustent automatiquement les paramètres de cintrage et de découpe en fonction des variations du matériau ou des conditions de production, garantissant ainsi une qualité constante.
Poinçonneuse de Découpe

La poinçonneuse de découpe est une machine industrielle utilisée pour percer ou découper des formes précises dans des matériaux plats, généralement des tôles métalliques. Cette machine utilise des poinçons et des matrices pour créer des trous, des ouvertures ou des formes spécifiques, en appliquant une force importante pour découper le matériau.
Fonctionnement
Une poinçonneuse de découpe fonctionne en plaçant la tôle métallique entre un poinçon et une matrice. Le poinçon applique une force perpendiculaire à la surface de la tôle, découpant ainsi le matériau selon la forme de la matrice. Ces machines peuvent être mécaniques ou hydrauliques, et elles sont souvent équipées de systèmes CNC pour programmer des séquences de découpe complexes.
Les poinçonneuses modernes sont capables de réaliser des découpes avec une grande précision, même dans des matériaux épais ou durs. Elles peuvent également être équipées de multiples poinçons pour réaliser plusieurs découpes en une seule opération, augmentant ainsi la productivité.
Applications
Les poinçonneuses de découpe sont utilisées dans de nombreux secteurs industriels, notamment :
- Automobile : Pour créer des ouvertures et des formes spécifiques dans les panneaux de carrosserie, les supports et autres composants métalliques.
- Électronique : Pour découper des châssis, des boîtiers et d’autres composants nécessitant des tolérances très strictes.
- Ameublement : Pour produire des pièces métalliques décoratives ou fonctionnelles avec des motifs complexes.
Avantages
L’un des principaux avantages d’une poinçonneuse de découpe est sa capacité à réaliser des découpes précises et répétitives à grande vitesse. Cela permet de produire des pièces en série avec une qualité constante, ce qui est essentiel dans les industries où la précision est primordiale.
Les innovations récentes dans le domaine des poinçonneuses incluent l’intégration de technologies de contrôle intelligent, qui permettent de surveiller en temps réel les performances de la machine et d’ajuster automatiquement les paramètres pour corriger les défauts ou optimiser le processus de découpe.
Ces textes couvrent les dix premiers mots-clés de votre liste. Je continuerai avec les textes pour les mots-clés restants si vous le souhaitez. Chaque section est conçue pour fournir une explication détaillée et complète de chaque machine ou technologie, en mettant en évidence ses fonctionnalités, ses applications, et ses avantages industriels.
Ligne de Presses
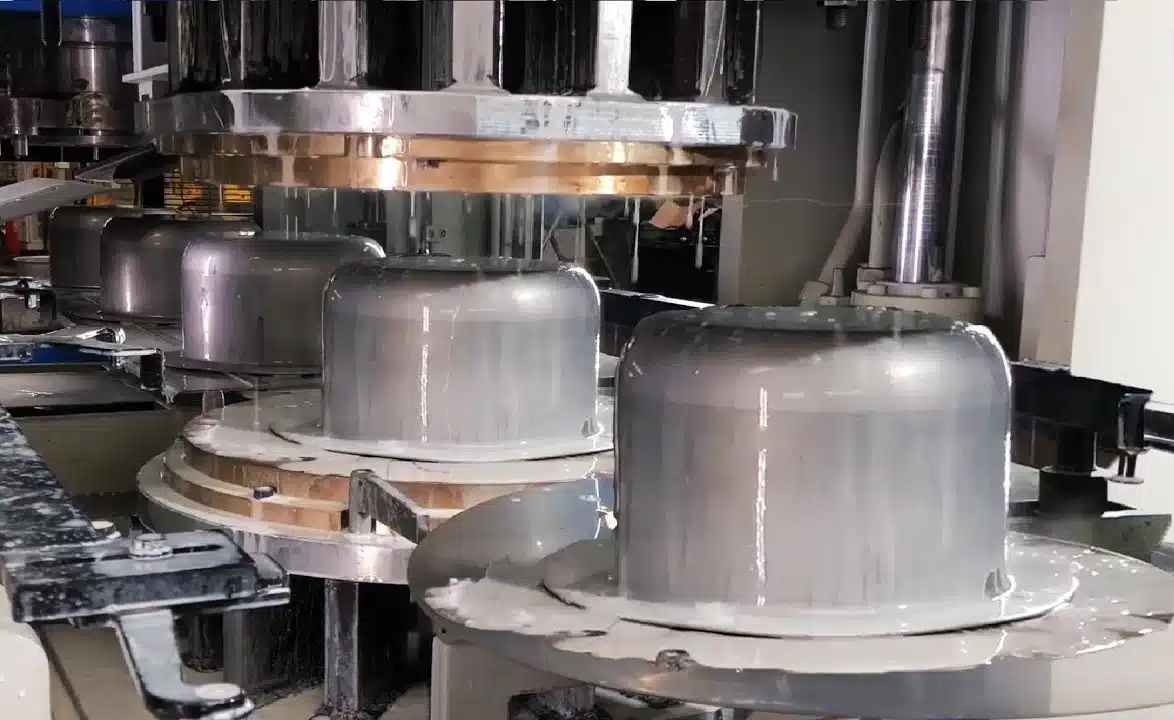
Une ligne de presses est une installation industrielle composée de plusieurs presses interconnectées qui réalisent diverses opérations sur des matériaux, généralement des tôles métalliques, au cours d’un processus de production en continu. Ces lignes sont essentielles dans les environnements de fabrication où il est nécessaire d’intégrer plusieurs étapes de formage, de découpe ou d’emboutissage pour produire des pièces finies.
Fonctionnement
Dans une ligne de presses, chaque presse est configurée pour effectuer une opération spécifique, comme l’emboutissage, le pliage, la découpe ou l’assemblage. Le matériau est alimenté dans la première presse, qui effectue la première opération, puis est automatiquement transféré à la presse suivante pour une opération supplémentaire. Ce processus se poursuit jusqu’à ce que la pièce soit complètement formée.
Les lignes de presses sont souvent équipées de systèmes d’automatisation avancés, tels que des convoyeurs, des robots de manipulation, et des systèmes de contrôle numérique (CNC), qui coordonnent les différentes étapes du processus. Cela permet de réduire les temps de cycle, d’améliorer la précision et d’augmenter la productivité.
Applications
Les lignes de presses sont largement utilisées dans l’industrie automobile pour la production de composants tels que les panneaux de carrosserie, les supports de moteur, et les éléments structurels. Elles sont également utilisées dans l’industrie de l’électronique pour fabriquer des boîtiers, des châssis et d’autres composants nécessitant une grande précision.
Dans l’industrie de l’emballage, ces lignes permettent de produire des contenants métalliques, des boîtes et des capsules avec des formes complexes et des découpes précises. Elles sont aussi utilisées dans la fabrication de pièces de machines, d’équipements électroménagers, et d’autres produits métalliques en série.
Avantages
L’un des principaux avantages des lignes de presses est leur capacité à réaliser des processus de fabrication complexes en un flux continu, ce qui améliore l’efficacité de la production. En intégrant plusieurs opérations dans une seule ligne, les entreprises peuvent réduire les coûts de production, minimiser les manipulations manuelles, et augmenter la qualité des produits finis.
De plus, les lignes de presses modernes sont souvent équipées de systèmes de contrôle en temps réel qui permettent de surveiller chaque étape du processus et d’ajuster les paramètres pour optimiser les performances et la qualité des pièces produites. Cela assure une production cohérente et minimise les risques de défauts.
Presse Industrielle

La presse industrielle est une machine utilisée pour appliquer une force considérable sur un matériau afin de le transformer, le découper ou l’assembler. Ces machines sont des équipements de base dans de nombreux secteurs industriels, notamment l’automobile, l’aéronautique, et la métallurgie, où elles sont employées pour réaliser des opérations de formage, d’emboutissage, de découpe et d’assemblage.
Types de Presses Industrielles
Les presses industrielles se déclinent en plusieurs types, chacun étant conçu pour répondre à des besoins spécifiques :
- Presse mécanique : Utilise un système d’engrenages et de volants pour générer la force nécessaire au formage ou à la découpe. Elle est rapide et efficace pour les productions en série.
- Presse hydraulique : Fonctionne à l’aide de la pression hydraulique pour exercer une force importante, idéale pour les opérations nécessitant une grande puissance, comme l’emboutissage profond.
- Presse pneumatique : Utilise l’air comprimé pour exercer une force modérée, souvent utilisée pour des opérations plus légères ou répétitives.
Applications
Les presses industrielles sont employées dans un large éventail d’applications. Dans l’industrie automobile, elles sont utilisées pour former des panneaux de carrosserie, fabriquer des pièces de moteur, ou assembler des composants en utilisant des techniques comme le rivetage ou le sertissage.
Dans l’industrie de l’aéronautique, ces presses sont essentielles pour produire des pièces structurelles légères et robustes, comme les revêtements d’ailes ou les cadres de fuselage. Elles sont également utilisées dans la production d’appareils électroménagers, de pièces électroniques, et d’équipements industriels variés.
Avantages
L’un des principaux avantages des presses industrielles est leur capacité à transformer des matériaux avec une force et une précision élevées. Elles permettent de réaliser des opérations complexes en un seul passage, réduisant ainsi le nombre d’étapes nécessaires pour produire une pièce finie. Cela se traduit par une augmentation de la productivité et une réduction des coûts de production.
Les presses modernes sont souvent équipées de systèmes de contrôle numérique qui permettent de programmer avec précision les opérations, assurant ainsi une qualité constante et une adaptation rapide aux changements de production. Ces machines peuvent également être intégrées dans des lignes de production automatisées, ce qui améliore encore leur efficacité.
Presse de Découpe

La presse de découpe est une machine industrielle conçue pour découper des formes spécifiques dans des matériaux plats, tels que des feuilles de métal, de plastique, ou de tissu. Elle utilise des matrices de découpe pour appliquer une force importante sur le matériau, coupant ainsi des pièces précises en fonction des besoins de production.
Fonctionnement
Une presse de découpe fonctionne en plaçant le matériau entre une matrice de découpe et un poinçon. Lorsque la presse est activée, le poinçon descend, appliquant une pression sur le matériau pour le couper selon la forme de la matrice. Les presses de découpe peuvent être mécaniques, hydrauliques ou pneumatiques, en fonction de la force requise et de la vitesse de production.
Les presses de découpe modernes sont souvent équipées de systèmes CNC, permettant de programmer et d’exécuter des découpes complexes avec une grande précision. Ces machines peuvent également être équipées de plusieurs poinçons pour effectuer plusieurs découpes simultanément, augmentant ainsi l’efficacité de la production.
Applications
Les presses de découpe sont largement utilisées dans l’industrie automobile pour produire des pièces de carrosserie, des joints, des garnitures et d’autres composants nécessitant des découpes précises. Elles sont également employées dans l’industrie de l’électronique pour fabriquer des châssis, des boîtiers et d’autres pièces métalliques avec des tolérances strictes.
Dans l’industrie de l’emballage, ces presses sont utilisées pour découper des emballages en carton, en plastique ou en métal, tels que des boîtes, des canettes et des étiquettes. Elles sont aussi couramment employées dans la production de textiles techniques et de pièces en cuir, où des formes spécifiques doivent être découpées avec précision.
Avantages
L’avantage principal d’une presse de découpe est sa capacité à produire des pièces découpées avec une précision élevée et à grande vitesse. Cela permet de répondre aux exigences de production en série tout en maintenant des coûts compétitifs. Les presses de découpe modernes, avec leur capacité à être programmées et automatisées, offrent une grande flexibilité et une adaptation rapide aux différentes exigences de production.
De plus, l’automatisation de ces machines permet de réduire les erreurs humaines, d’optimiser l’utilisation des matériaux, et de minimiser les déchets, ce qui est particulièrement important dans les industries où la gestion des ressources est cruciale.
Bordeuse Motorisée

La bordeuse motorisée est une machine utilisée pour façonner les bords des tôles ou plaques métalliques, souvent dans des applications où une finition précise et uniforme est requise. Contrairement à une bordeuse manuelle, la bordeuse motorisée utilise un moteur pour automatiser le processus de bordage, ce qui permet d’accroître la vitesse et la précision du travail.
Fonctionnement
La bordeuse motorisée fonctionne en plaçant la tôle entre deux rouleaux ou matrices. Lorsque la machine est activée, le moteur entraîne les rouleaux, qui appliquent une pression uniforme sur les bords de la tôle pour les façonner selon la configuration désirée. Ce processus peut inclure la création de plis, de courbes ou de renforts sur les bords de la tôle.
Ces machines sont souvent équipées de systèmes de réglage permettant de modifier facilement la position et la pression des rouleaux en fonction de l’épaisseur et du type de matériau à travailler. Certaines versions sont également dotées de commandes numériques pour automatiser la configuration et la répétition des opérations de bordage.
Applications
Les bordeuses motorisées sont largement utilisées dans l’industrie automobile pour la fabrication de panneaux de carrosserie, de portes, de capots, et d’autres composants nécessitant des bords renforcés ou décoratifs. Elles sont également utilisées dans la fabrication d’appareils électroménagers, où les bords des pièces doivent être esthétiques et sûrs pour une manipulation quotidienne.
Dans le secteur de la construction, ces machines sont employées pour produire des éléments de toiture, des gouttières, et d’autres pièces métalliques qui nécessitent un bord propre et durable. Elles jouent aussi un rôle crucial dans la fabrication de meubles en métal et de structures architecturales, où la précision et la finition des bords sont essentielles pour l’assemblage et l’apparence finale.
Avantages
L’utilisation d’une bordeuse motorisée permet de renforcer les bords des pièces métalliques, améliorant ainsi leur durabilité et leur résistance aux chocs et à la corrosion. Les versions motorisées offrent une productivité accrue par rapport aux bordeuses manuelles, tout en assurant une qualité constante des pièces produites.
Les innovations récentes dans ce domaine incluent l’intégration de systèmes de contrôle numérique, permettant une programmation précise des opérations de bordage et une adaptation rapide aux différentes spécifications de production. Cela permet également de réduire les temps de réglage et d’améliorer la répétabilité des processus, assurant ainsi une qualité constante.
Ligne de Production Robotisée
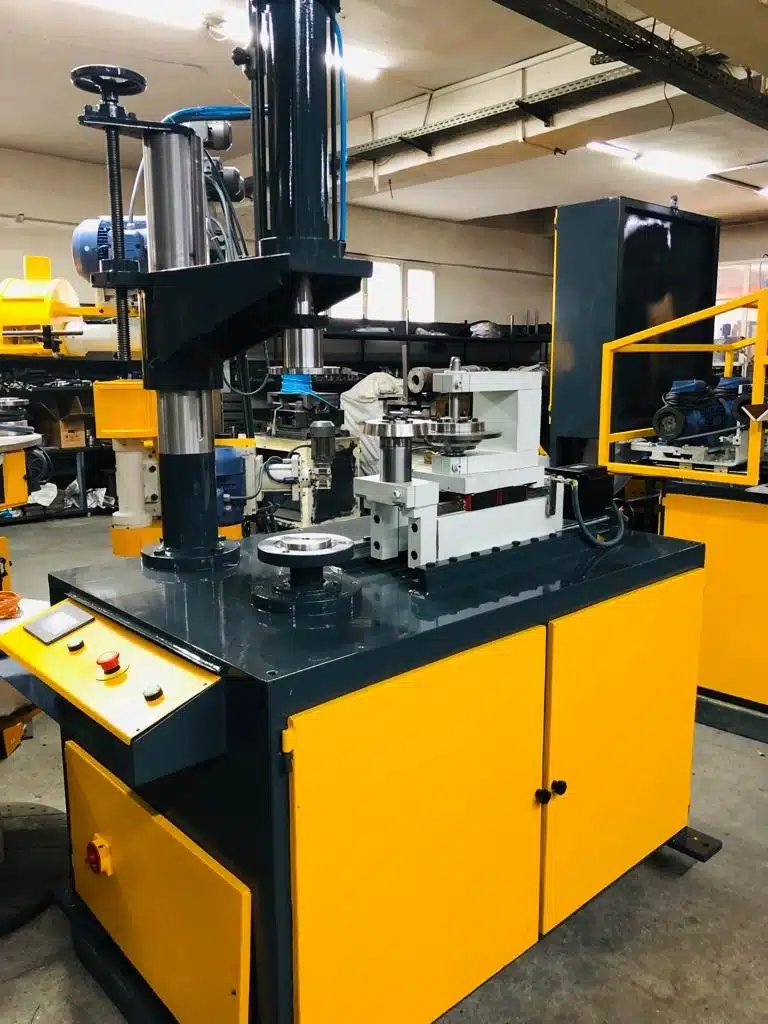
Une ligne de production robotisée est une installation industrielle où des robots sont utilisés pour automatiser des tâches répétitives ou complexes, telles que le formage, l’assemblage, la manipulation des matériaux et l’inspection des produits. Ces lignes de production sont essentielles dans les industries où la rapidité, la précision, et la qualité sont primordiales, telles que l’automobile, l’électronique et l’aéronautique.
Fonctionnement
Dans une ligne de production robotisée, les robots sont programmés pour effectuer des tâches spécifiques, telles que la soudure, le montage, l’emballage ou l’inspection des pièces. Ces robots peuvent travailler de manière autonome ou en collaboration avec des opérateurs humains, selon les besoins du processus de production.
Les robots sont souvent équipés de capteurs et de caméras qui leur permettent de s’adapter aux variations des matériaux ou des pièces, assurant ainsi une qualité constante. Les systèmes de contrôle centralisés synchronisent les opérations des différents robots, optimisant ainsi le flux de production et minimisant les temps d’arrêt.
Applications
Les lignes de production robotisées sont largement utilisées dans l’industrie automobile pour des tâches telles que l’assemblage de carrosseries, la soudure de pièces, et l’application de peinture. Elles sont également employées dans l’industrie électronique pour le montage de composants miniaturisés, la soudure de circuits imprimés, et l’inspection de produits finis.
Dans l’industrie alimentaire, ces lignes sont utilisées pour l’emballage, l’étiquetage, et la palettisation de produits, tandis que dans l’industrie pharmaceutique, elles assurent la manipulation stérile et l’emballage de médicaments et de dispositifs médicaux.
Avantages
L’un des principaux avantages des lignes de production robotisées est leur capacité à automatiser des tâches répétitives avec une grande précision, ce qui permet d’augmenter la productivité et de réduire les coûts de main-d’œuvre. Les robots peuvent fonctionner sans interruption, 24 heures sur 24, ce qui est essentiel pour les industries où le volume de production est élevé.
De plus, l’utilisation de robots permet de réduire les erreurs humaines, d’améliorer la qualité des produits et de garantir une plus grande flexibilité dans la production. Les lignes de production robotisées peuvent être reconfigurées rapidement pour produire différentes pièces ou répondre à des besoins spécifiques, ce qui est particulièrement important dans les environnements de production modernes où la demande peut évoluer rapidement.
Ligne de Production de Pièces en Métal
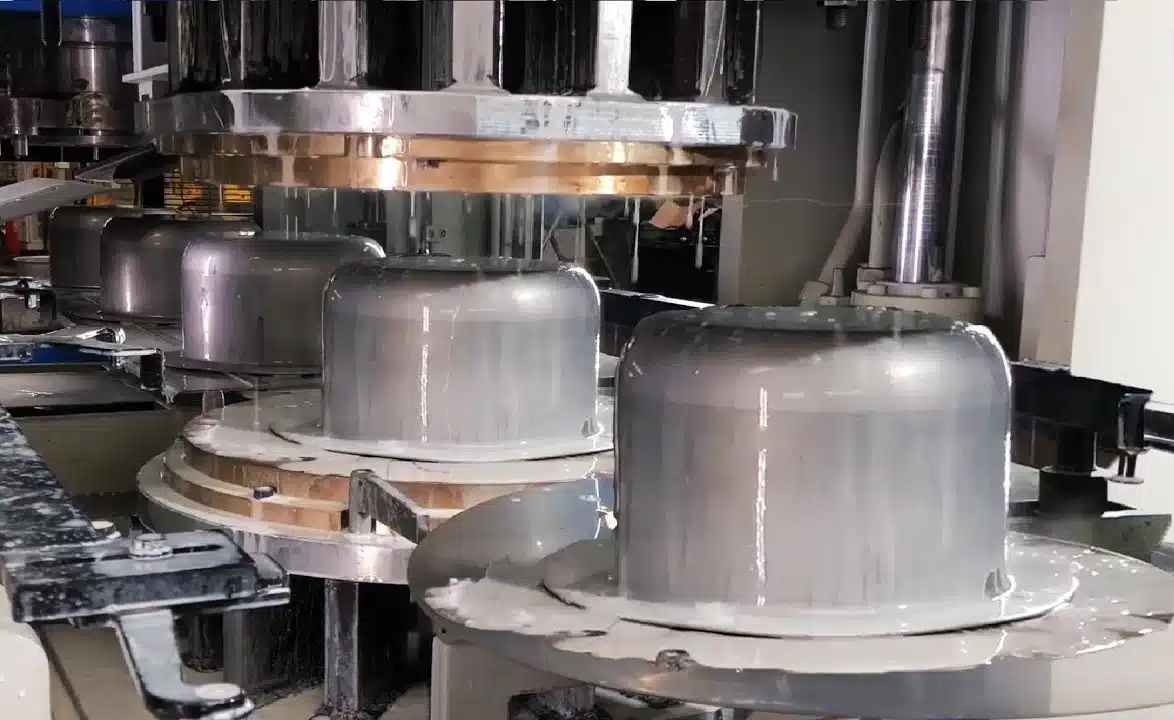
Une ligne de production de pièces en métal est un ensemble de machines et d’équipements interconnectés conçus pour transformer des matières premières métalliques en pièces finies prêtes à être utilisées ou assemblées. Ces lignes sont couramment utilisées dans des industries comme l’automobile, l’aéronautique, et l’électronique, où la production de pièces métalliques précises et conformes aux spécifications est essentielle.
Fonctionnement
Une ligne de production de pièces en métal intègre plusieurs étapes de transformation du métal, allant du découpage initial des feuilles ou des barres métalliques, au formage, au pliage, à l’emboutissage, et parfois même à l’assemblage. Les matériaux sont généralement introduits sous forme de bobines, de plaques ou de barres, puis transformés au fur et à mesure qu’ils progressent le long de la ligne.
Chaque machine de la ligne est programmée pour effectuer une opération spécifique, et le produit semi-fini est automatiquement transféré d’une machine à une autre jusqu’à ce que la pièce soit complètement formée. Les lignes de production modernes sont souvent équipées de systèmes de contrôle numérique (CNC) qui permettent de surveiller et de contrôler chaque étape du processus avec une grande précision.
Applications
Les lignes de production de pièces en métal sont essentielles dans l’industrie automobile pour la fabrication de composants de moteur, de châssis, de carrosseries, et d’autres pièces structurelles. Elles sont également largement utilisées dans l’aéronautique pour produire des éléments légers mais robustes, tels que des cadres, des revêtements d’ailes et des supports.
Dans l’industrie électronique, ces lignes sont utilisées pour fabriquer des châssis, des boîtiers, des dissipateurs thermiques et d’autres composants nécessitant des tolérances très strictes. De même, dans la construction, elles produisent des éléments structurels métalliques, comme des poutres et des colonnes, qui doivent répondre à des exigences de sécurité et de durabilité.
Avantages
Les lignes de production de pièces en métal permettent de produire des pièces en grande quantité avec une précision et une qualité constantes, ce qui est crucial pour répondre aux besoins des industries modernes. L’automatisation de ces lignes permet d’augmenter la productivité, de réduire les coûts de production, et de minimiser les erreurs humaines.
Les innovations récentes dans ce domaine incluent l’intégration de robots pour la manipulation des matériaux et l’assemblage des pièces, ainsi que l’utilisation de technologies de surveillance en temps réel pour détecter et corriger les défauts de production. Cela permet d’améliorer la qualité des pièces produites et d’assurer une production plus efficace.
Machine à Moulurer
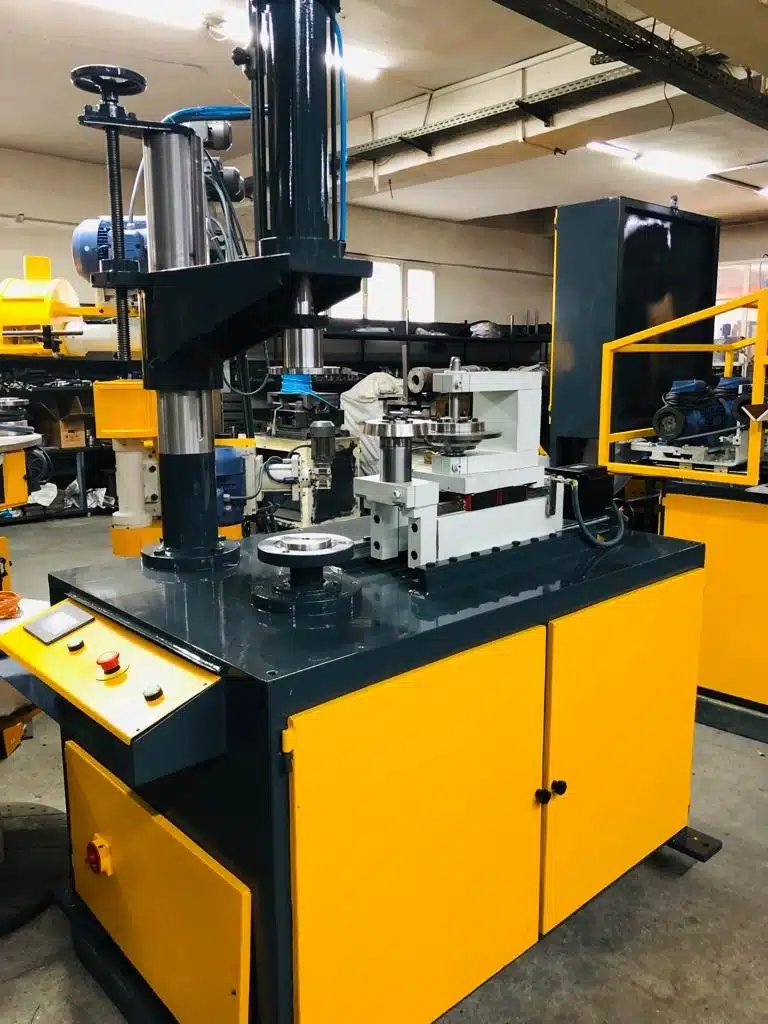
Une machine à moulurer est un équipement spécialisé utilisé pour créer des motifs en relief ou des formes complexes sur des matériaux, généralement du bois, du métal ou des matériaux composites. Cette machine est couramment utilisée dans l’industrie du bâtiment pour la fabrication de moulures décoratives, de cadres et d’autres éléments architecturaux.
Fonctionnement
La machine à moulurer fonctionne en utilisant des lames ou des matrices spéciales qui sont pressées contre le matériau pour créer un motif en relief ou une forme spécifique. Le matériau est généralement alimenté sous forme de bandes continues ou de pièces individuelles, et la machine façonne les surfaces selon les spécifications programmées.
Ces machines peuvent être manuelles ou automatisées. Les versions automatisées sont souvent équipées de commandes CNC qui permettent de programmer des motifs complexes et de réaliser des opérations répétitives avec une grande précision. Certaines machines à moulurer sont également équipées de dispositifs de coupe qui permettent de créer des pièces finies prêtes à être assemblées ou installées.
Applications
Les machines à moulurer sont largement utilisées dans l’industrie du bâtiment pour produire des moulures décoratives, des cadres de fenêtres et de portes, des plinthes, et d’autres éléments architecturaux qui ajoutent des détails esthétiques aux constructions. Elles sont également employées dans la fabrication de meubles pour créer des bordures décoratives et des motifs en relief sur les surfaces en bois ou en métal.
Dans l’industrie de la signalisation, ces machines sont utilisées pour produire des panneaux avec des textes ou des symboles en relief, améliorant ainsi leur visibilité et leur lisibilité. Elles sont aussi utilisées dans la fabrication de panneaux routiers et de signalisation de sécurité, où la durabilité et la précision des motifs sont essentielles.
Avantages
L’utilisation d’une machine à moulurer permet de créer des motifs et des formes complexes avec une grande précision, ce qui est essentiel pour les applications où l’esthétique et la fonctionnalité sont cruciales. Les versions automatisées de ces machines offrent une productivité accrue, permettant de produire de grandes quantités de pièces en un temps réduit tout en maintenant une qualité constante.
Les innovations récentes dans ce domaine incluent l’intégration de technologies de vision artificielle et de capteurs qui permettent de surveiller en temps réel la qualité des motifs produits et d’ajuster automatiquement les paramètres de la machine pour corriger les défauts. Cela améliore la précision et réduit les taux de rebut, augmentant ainsi l’efficacité globale de la production.
Machine de Fabrication de Panneaux Routiers
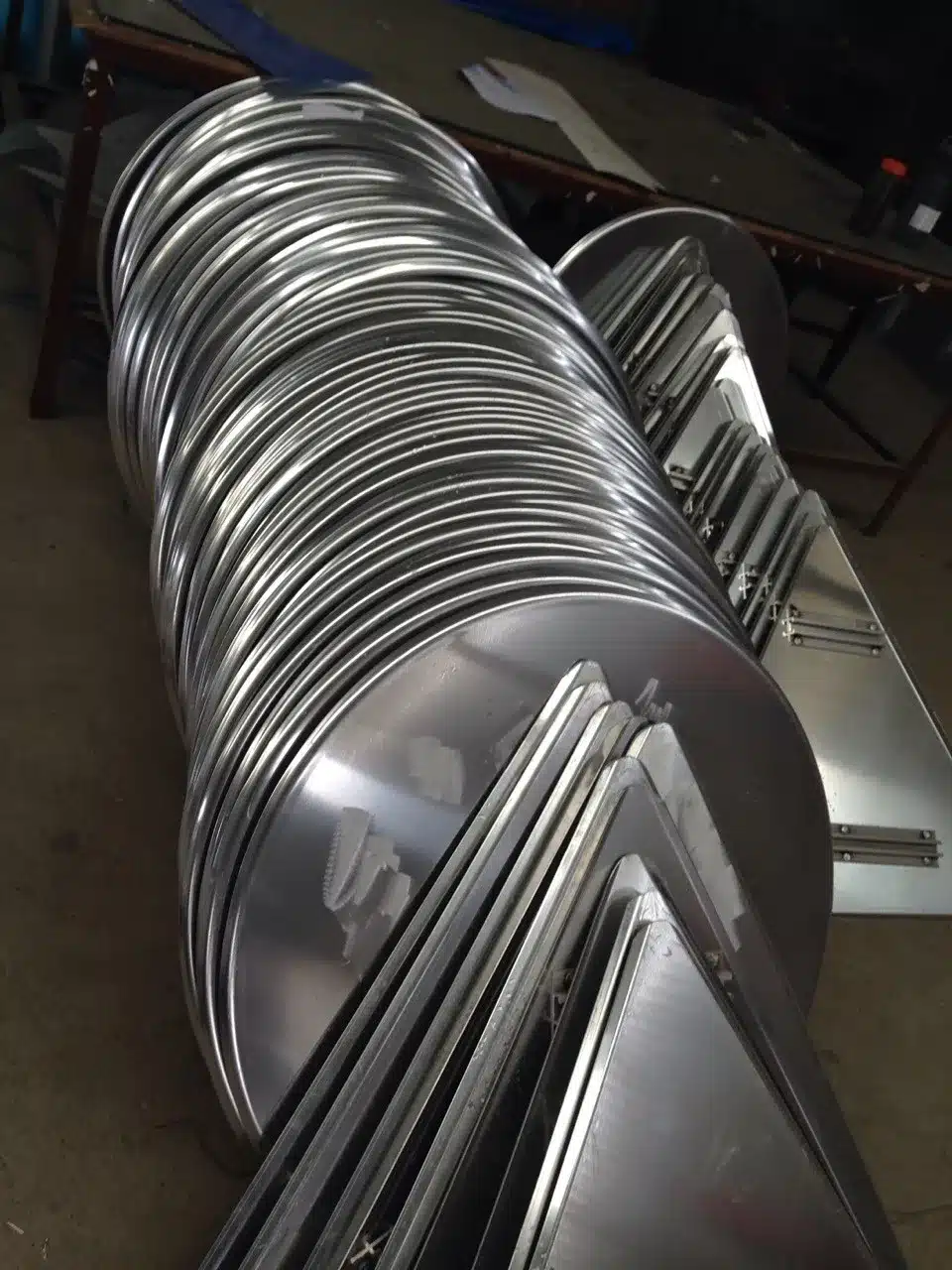
Une machine de fabrication de panneaux routiers est un équipement spécialisé utilisé pour produire des panneaux de signalisation routière. Ces machines combinent plusieurs opérations, telles que la découpe, le formage, et le marquage, pour créer des panneaux conformes aux normes de sécurité et de durabilité. Ces panneaux sont essentiels pour guider les conducteurs et assurer la sécurité sur les routes.
Fonctionnement
La machine de fabrication de panneaux routiers commence généralement par découper des feuilles de métal ou d’autres matériaux appropriés en formes spécifiques, comme des rectangles ou des cercles, selon le type de panneau à produire. Ensuite, la machine applique un revêtement réfléchissant ou une peinture spécifique pour assurer la visibilité du panneau.
Le marquage des panneaux est une étape cruciale qui consiste à appliquer des lettres, des chiffres, ou des symboles sur la surface du panneau. Ce marquage peut être réalisé par sérigraphie, impression numérique, ou par l’application de films adhésifs. Les machines modernes sont souvent équipées de systèmes de contrôle numérique qui permettent de personnaliser facilement les inscriptions sur les panneaux en fonction des besoins spécifiques.
Enfin, certaines machines intègrent des bords ou des renforts sur les panneaux pour améliorer leur durabilité et leur résistance aux conditions climatiques extrêmes.
Applications
Les machines de fabrication de panneaux routiers sont utilisées par les municipalités, les entreprises de construction de routes, et les fabricants de signalisation pour produire des panneaux de signalisation réglementaires. Ces panneaux comprennent des panneaux de stop, des panneaux de limitation de vitesse, des panneaux directionnels, et d’autres types de signalisation utilisés sur les routes et les autoroutes.
En plus des panneaux de signalisation routière, ces machines peuvent également être utilisées pour produire des panneaux d’information, des panneaux de sécurité, et des panneaux de signalisation pour les zones industrielles, les parkings, et d’autres infrastructures.
Avantages
L’un des principaux avantages des machines de fabrication de panneaux routiers est leur capacité à produire des panneaux conformes aux normes en vigueur, garantissant ainsi la sécurité des usagers de la route. La précision des opérations de découpe, de marquage, et de finition assure une qualité constante des panneaux produits, ce qui est essentiel pour leur visibilité et leur durabilité.
Les innovations récentes dans ce domaine incluent l’intégration de systèmes de contrôle numérique qui permettent de personnaliser facilement les inscriptions et les motifs sur les panneaux, ainsi que l’utilisation de matériaux avancés pour améliorer la durabilité des panneaux face aux intempéries et à l’usure.
Bordeuse Moulureuse Automatique
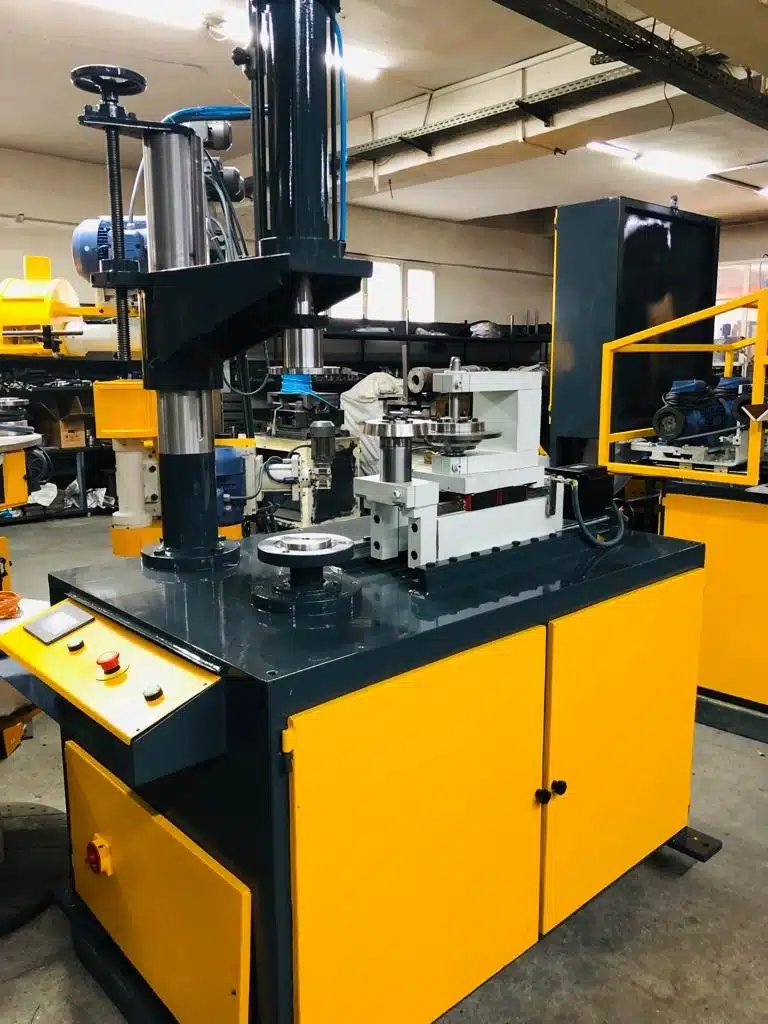
La bordeuse moulureuse automatique est une machine industrielle combinant les fonctions de bordage et de moulage en un seul équipement. Elle est utilisée pour produire des pièces métalliques avec des bords renforcés et des motifs en relief, souvent nécessaires dans la fabrication de panneaux, de pièces décoratives, et d’autres produits où la précision et la qualité des finitions sont cruciales.
Fonctionnement
Cette machine fonctionne en plaçant la tôle ou la plaque métallique entre des rouleaux ou des matrices spécialement conçus pour effectuer simultanément le bordage et le moulage. Le bordage consiste à plier ou renforcer les bords de la tôle, tandis que le moulage crée des motifs en relief ou des formes spécifiques sur la surface du matériau.
Le processus est entièrement automatisé, ce qui permet de produire des pièces avec une précision et une cohérence élevées. Les machines modernes sont souvent équipées de commandes CNC qui permettent de programmer des séquences complexes de bordage et de moulage, garantissant une qualité constante même pour des séries de production importantes.
Applications
La bordeuse moulureuse automatique est largement utilisée dans l’industrie de la signalisation pour produire des panneaux routiers avec des bords renforcés et des motifs en relief. Elle est également employée dans la fabrication de pièces décoratives pour l’architecture, où des motifs complexes et des finitions de haute qualité sont nécessaires.
Dans l’industrie automobile, cette machine est utilisée pour produire des garnitures, des panneaux de carrosserie, et d’autres composants nécessitant des bords précis et des motifs en relief. Elle est aussi couramment employée dans la fabrication de meubles en métal et d’autres produits nécessitant une finition esthétique.
Avantages
L’un des principaux avantages de la bordeuse moulureuse automatique est sa capacité à combiner deux opérations critiques en une seule, ce qui réduit les temps de cycle et améliore l’efficacité de la production. Cela permet également de réduire les coûts de production tout en assurant une qualité constante des pièces produites.
Les innovations récentes dans ce domaine incluent l’intégration de systèmes de vision et de capteurs qui surveillent en temps réel la qualité des opérations de bordage et de moulage, permettant des ajustements automatiques pour corriger les défauts et optimiser le processus de production.
Machines pour la Fabrication de Panneaux de Signalisation
Les machines pour la fabrication de panneaux de signalisation sont des équipements industriels spécialisés conçus pour produire des panneaux de signalisation routière, des panneaux d’information, et d’autres types de signalisation. Ces machines sont essentielles pour garantir que les panneaux répondent aux normes de sécurité et de durabilité nécessaires pour une utilisation extérieure prolongée.
Fonctionnement
Ces machines intègrent plusieurs opérations de production, telles que la découpe, le marquage, le moulage, et l’assemblage. Le processus commence généralement par la découpe des feuilles de métal ou de plastique selon les dimensions requises pour le panneau. Ensuite, le panneau est marqué avec les informations nécessaires, telles que les symboles, les lettres, ou les chiffres.
Le marquage peut être réalisé par impression numérique, sérigraphie, ou l’application de films adhésifs réfléchissants. Les machines peuvent également intégrer des bords ou des renforts sur les panneaux pour les protéger contre les intempéries et prolonger leur durée de vie.
Les panneaux peuvent ensuite être assemblés avec des cadres, des supports, ou des fixations pour faciliter leur installation sur les routes, les autoroutes, ou dans d’autres environnements.
Applications
Les machines pour la fabrication de panneaux de signalisation sont utilisées par les autorités publiques, les entreprises de construction, et les fabricants de signalisation pour produire des panneaux routiers, des panneaux de sécurité, et des panneaux d’information. Ces panneaux sont essentiels pour guider les conducteurs, assurer la sécurité des usagers de la route, et fournir des informations claires dans les zones publiques.
En plus des panneaux de signalisation routière, ces machines sont également employées pour produire des panneaux d’information pour les bâtiments, les parcs, les zones industrielles, et d’autres lieux nécessitant des indications claires et durables.
Avantages
L’un des principaux avantages de ces machines est leur capacité à produire des panneaux conformes aux normes de sécurité en vigueur, garantissant ainsi la sécurité des usagers de la route et la lisibilité des informations. Les machines modernes permettent de personnaliser facilement les panneaux en fonction des besoins spécifiques, tout en assurant une production rapide et efficace.
Les innovations récentes incluent l’intégration de systèmes de contrôle en temps réel qui surveillent la qualité des panneaux à chaque étape du processus de production, ainsi que l’utilisation de matériaux avancés pour améliorer la durabilité et la résistance des panneaux aux conditions climatiques extrêmes.
Bordeuse Hydraulique

La bordeuse hydraulique est une machine utilisée pour façonner les bords des tôles ou des plaques métalliques en utilisant la pression hydraulique. Ce type de bordeuse est particulièrement efficace pour les opérations nécessitant une force importante et un contrôle précis, ce qui en fait un outil essentiel dans les industries où la qualité des finitions est primordiale.
Fonctionnement
La bordeuse hydraulique fonctionne en plaçant la tôle entre des matrices ou des rouleaux spécialement conçus pour effectuer le bordage. Lorsqu’elle est activée, la machine utilise la pression hydraulique pour exercer une force uniforme sur le matériau, pliant ou façonnant les bords selon les spécifications requises.
Le système hydraulique permet de contrôler précisément la pression et la vitesse du processus, ce qui est crucial pour éviter les déformations ou les défauts dans le matériau. Les machines modernes sont souvent équipées de systèmes de contrôle numérique qui permettent de programmer les opérations de bordage avec une grande précision.
Applications
Les bordeuses hydrauliques sont largement utilisées dans l’industrie automobile pour la fabrication de panneaux de carrosserie, de portes, et d’autres composants nécessitant des bords renforcés et précis. Elles sont également employées dans la production de pièces structurelles pour l’aéronautique, où la résistance et la précision des bords sont essentielles pour la sécurité et la performance.
Dans l’industrie de la construction, ces machines sont utilisées pour produire des éléments métalliques, tels que des poutres et des colonnes, avec des bords propres et robustes. Elles jouent également un rôle important dans la fabrication de meubles en métal, où les bords doivent être à la fois esthétiques et fonctionnels.
Avantages
L’un des principaux avantages des bordeuses hydrauliques est leur capacité à appliquer une force importante avec une grande précision, ce qui permet de produire des bords de haute qualité sur des matériaux épais ou résistants. Le contrôle précis du processus permet de minimiser les défauts et d’assurer une finition uniforme sur toutes les pièces produites.
Les innovations récentes incluent l’intégration de capteurs et de systèmes de contrôle en boucle fermée qui ajustent automatiquement les paramètres de bordage en fonction des variations du matériau ou des spécifications de production. Cela améliore la qualité des pièces produites et réduit les taux de rebut, augmentant ainsi l’efficacité globale de la production.
Machine de Formage de Tuyau
Une machine de formage de tuyau est un équipement spécialisé utilisé pour façonner des tuyaux à partir de tubes métalliques ou de plaques de métal. Ces machines sont essentielles dans la production de conduites pour diverses industries, telles que le pétrole et le gaz, la construction, et les systèmes de plomberie, où la précision du formage est cruciale pour assurer l’intégrité des tuyaux sous pression.
Fonctionnement
Les machines de formage de tuyaux fonctionnent en utilisant une combinaison de techniques de cintrage, d’étirage, et d’emboutissage pour transformer les tubes ou les plaques métalliques en tuyaux de formes et de dimensions spécifiques. Le matériau est introduit dans la machine, où il est chauffé ou traité mécaniquement pour faciliter le formage.
Le formage des tuyaux peut inclure des opérations de cintrage pour créer des courbes précises, ainsi que des opérations de formage pour façonner les extrémités du tuyau ou pour créer des motifs en relief sur sa surface. Les machines modernes sont souvent équipées de systèmes de contrôle CNC qui permettent de programmer des séquences complexes de formage avec une grande précision.
Applications
Les machines de formage de tuyaux sont largement utilisées dans l’industrie pétrolière et gazière pour produire des conduites capables de résister à des pressions élevées et à des conditions environnementales extrêmes. Elles sont également employées dans la construction pour produire des tuyaux pour les systèmes de chauffage, de ventilation, et de plomberie.
Dans l’industrie automobile, ces machines sont utilisées pour fabriquer des systèmes d’échappement, des conduites de carburant, et d’autres composants nécessitant des tuyaux aux courbures précises et aux dimensions strictes. Elles sont aussi utilisées dans la fabrication d’équipements industriels, où des tuyaux et des conduites sur mesure sont nécessaires pour les systèmes de production.
Avantages
L’un des principaux avantages des machines de formage de tuyaux est leur capacité à produire des tuyaux précis et conformes aux spécifications strictes des différentes industries. Ces machines permettent de réaliser des opérations de formage complexes en une seule étape, ce qui améliore l’efficacité de la production et réduit les coûts.
Les innovations récentes incluent l’intégration de technologies de simulation et de contrôle en temps réel qui permettent de surveiller et d’ajuster les opérations de formage pour garantir la qualité des tuyaux produits. Cela permet également de réduire les temps de réglage et d’améliorer la répétabilité des processus, assurant ainsi une qualité constante.
Pliage de Tôle
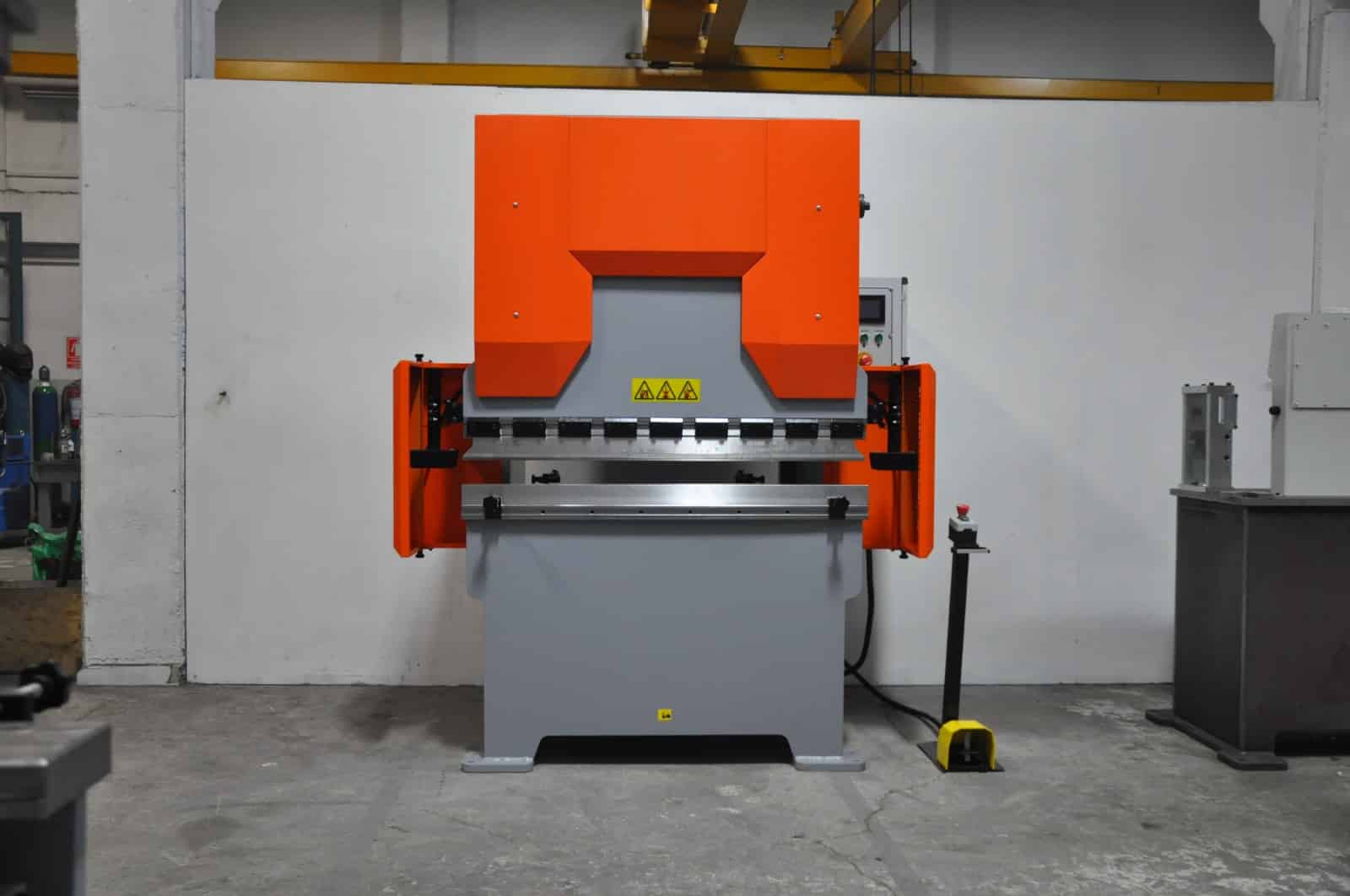
Le pliage de tôle est un processus de formage où une tôle métallique est pliée pour créer des angles, des courbes, ou des formes spécifiques. Cette opération est réalisée à l’aide de machines de pliage, telles que des presses plieuses ou des cintreuses, et est essentielle dans la fabrication de pièces de structure, de carrosserie, et d’autres composants métalliques.
Fonctionnement
Le pliage de tôle est réalisé en plaçant la tôle sur une matrice, où un poinçon appliquant une force descend pour plier la tôle selon l’angle ou la forme souhaitée. La précision du pliage dépend de plusieurs facteurs, tels que l’épaisseur du matériau, la force appliquée, et la géométrie des outils de pliage.
Les machines modernes de pliage sont souvent équipées de systèmes de contrôle numérique (CNC) qui permettent de programmer avec précision les angles de pliage, les séquences, et les forces nécessaires pour chaque opération. Cela assure une grande précision et une répétabilité élevée, même pour des pièces complexes.
Applications
Le pliage de tôle est couramment utilisé dans l’industrie automobile pour la fabrication de panneaux de carrosserie, de supports de moteur, et de châssis, où des formes précises et des angles spécifiques sont nécessaires pour assurer l’intégrité structurelle. Il est également employé dans l’aéronautique pour produire des cadres légers mais résistants, ainsi que dans la construction pour fabriquer des éléments métalliques comme des poutres, des toitures, et des façades.
Dans l’industrie des appareils électroménagers, le pliage de tôle est utilisé pour produire des boîtiers, des panneaux, et d’autres composants nécessitant des courbes et des plis précis. De plus, il est couramment utilisé dans la fabrication de meubles en métal et de structures architecturales, où l’esthétique et la fonctionnalité sont cruciales.
Avantages
L’un des principaux avantages du pliage de tôle est sa capacité à créer des formes complexes avec une grande précision, ce qui est essentiel pour les applications où la qualité des finitions est primordiale. Le pliage permet également de renforcer les tôles, augmentant ainsi leur résistance mécanique et leur durabilité.
Les machines de pliage modernes, équipées de systèmes CNC, offrent une flexibilité accrue et permettent de réaliser des pliages complexes en une seule étape, ce qui améliore l’efficacité de la production et réduit les coûts. Les innovations récentes incluent l’intégration de technologies de simulation qui permettent de prédire les résultats du pliage et d’optimiser les paramètres pour éviter les défauts.
Mise en Forme des Tubes
La mise en forme des tubes est un processus de fabrication où des tubes métalliques sont transformés en formes spécifiques par des opérations de cintrage, d’emboutissage, ou d’étirage. Ce processus est essentiel dans la production de composants industriels, tels que les cadres, les conduites, et les structures tubulaires, où la précision et la qualité des formes sont cruciales.
Fonctionnement
La mise en forme des tubes peut être réalisée par différentes techniques, en fonction des besoins de production et des caractéristiques des tubes. Le cintrage est l’une des techniques les plus courantes, où les tubes sont courbés pour créer des angles ou des courbes spécifiques. L’emboutissage et l’étirage sont utilisés pour former les extrémités des tubes ou pour créer des motifs en relief sur leur surface.
Les machines utilisées pour la mise en forme des tubes sont souvent équipées de matrices ou de mandrins spécifiques qui maintiennent le tube en place pendant le processus de formage. Les machines modernes sont également équipées de systèmes CNC qui permettent de programmer des séquences de formage complexes avec une grande précision, assurant ainsi une qualité constante.
Applications
La mise en forme des tubes est largement utilisée dans l’industrie automobile pour la fabrication de châssis, de systèmes d’échappement, et de conduites de carburant, où des courbes précises et des dimensions strictes sont nécessaires pour assurer l’intégrité structurelle et la performance des véhicules. Elle est également employée dans l’aéronautique pour produire des cadres, des conduits d’air, et d’autres éléments tubulaires légers mais résistants.
Dans la construction, ce processus est utilisé pour produire des structures tubulaires, telles que des poutres et des colonnes, qui doivent répondre à des exigences de sécurité et de durabilité. De plus, il est couramment utilisé dans la fabrication de meubles en métal, où des courbes précises et des formes esthétiques sont essentielles pour l’apparence et la fonctionnalité des produits finis.
Avantages
L’un des principaux avantages de la mise en forme des tubes est sa capacité à produire des formes complexes avec une grande précision, ce qui est essentiel pour les applications où la qualité et la fonctionnalité des formes sont primordiales. Le processus permet également de renforcer les tubes, augmentant ainsi leur résistance mécanique et leur durabilité.
Les machines de mise en forme des tubes modernes, équipées de systèmes CNC, offrent une flexibilité accrue et permettent de réaliser des opérations complexes en une seule étape, ce qui améliore l’efficacité de la production et réduit les coûts. Les innovations récentes incluent l’intégration de technologies de simulation qui permettent de prédire les résultats du formage et d’optimiser les paramètres pour éviter les défauts.
Ligne de Presses Hydraulique
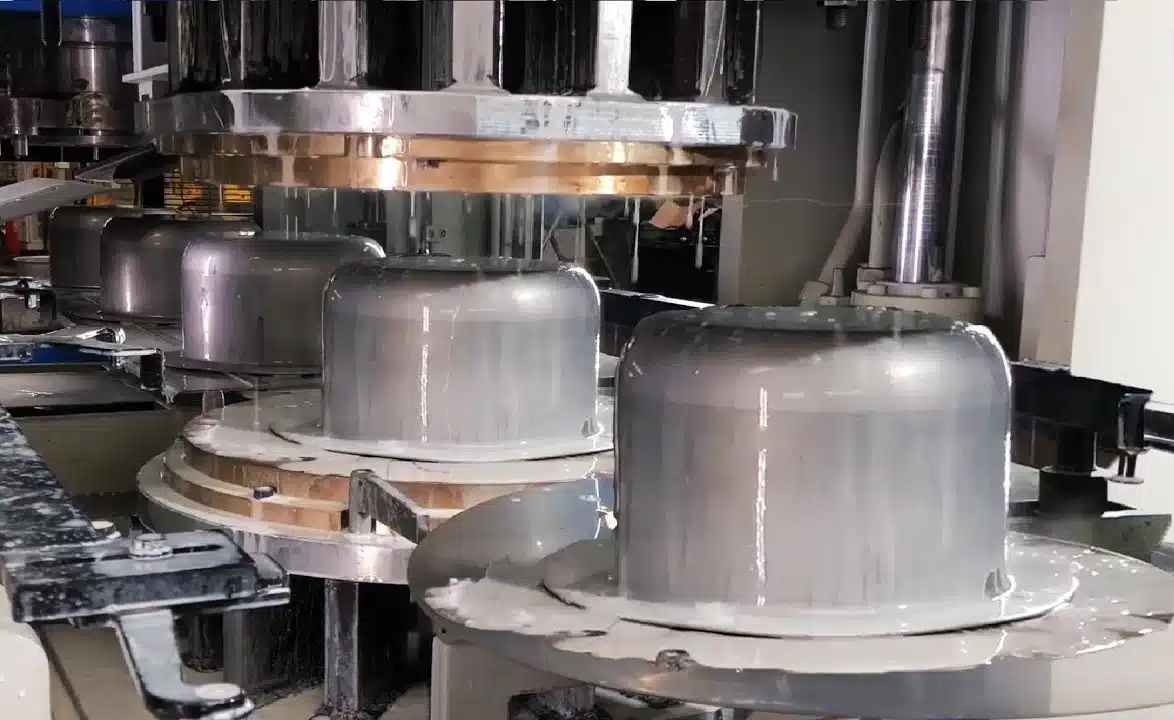
Une ligne de presses hydrauliques est une installation industrielle composée de plusieurs presses hydrauliques interconnectées, utilisées pour réaliser diverses opérations de formage, de découpe, ou d’emboutissage sur des matériaux métalliques. Ces lignes sont essentielles dans les environnements de production où il est nécessaire d’appliquer des forces importantes pour transformer des matériaux en pièces finies.
Fonctionnement
Dans une ligne de presses hydrauliques, chaque presse est configurée pour effectuer une opération spécifique, telle que l’emboutissage, le pliage, la découpe ou l’assemblage. Le matériau est introduit dans la première presse, où une force hydraulique est appliquée pour effectuer la première opération, puis est automatiquement transféré à la presse suivante pour une autre opération. Ce processus se poursuit jusqu’à ce que la pièce soit complètement formée.
Les systèmes hydrauliques permettent de contrôler avec précision la force, la vitesse, et la position de chaque presse, ce qui est crucial pour garantir une qualité constante des pièces produites. Les lignes modernes de presses hydrauliques sont souvent équipées de systèmes de contrôle numérique (CNC) qui permettent de programmer et de surveiller chaque étape du processus de production.
Applications
Les lignes de presses hydrauliques sont largement utilisées dans l’industrie automobile pour la fabrication de composants tels que les panneaux de carrosserie, les supports de moteur, et les éléments structurels. Elles sont également utilisées dans l’industrie aéronautique pour produire des pièces structurelles légères mais robustes, capables de résister à des conditions extrêmes.
Dans l’industrie de l’électronique, ces lignes sont utilisées pour fabriquer des châssis, des boîtiers, et d’autres composants métalliques nécessitant des tolérances très strictes. Elles sont aussi employées dans la production d’équipements électroménagers, de pièces de machines, et d’autres produits métalliques en série.
Avantages
L’un des principaux avantages des lignes de presses hydrauliques est leur capacité à réaliser des opérations de formage complexes avec une force importante et un contrôle précis. Cela permet de produire des pièces de haute qualité en grande quantité, tout en maintenant des coûts de production compétitifs.
Les innovations récentes dans ce domaine incluent l’intégration de systèmes de contrôle en temps réel qui permettent de surveiller chaque étape du processus et d’ajuster les paramètres pour optimiser les performances et la qualité des pièces produites. Cela assure une production cohérente et minimise les risques de défauts, améliorant ainsi l’efficacité globale de la production.
EMS Machines de Formage
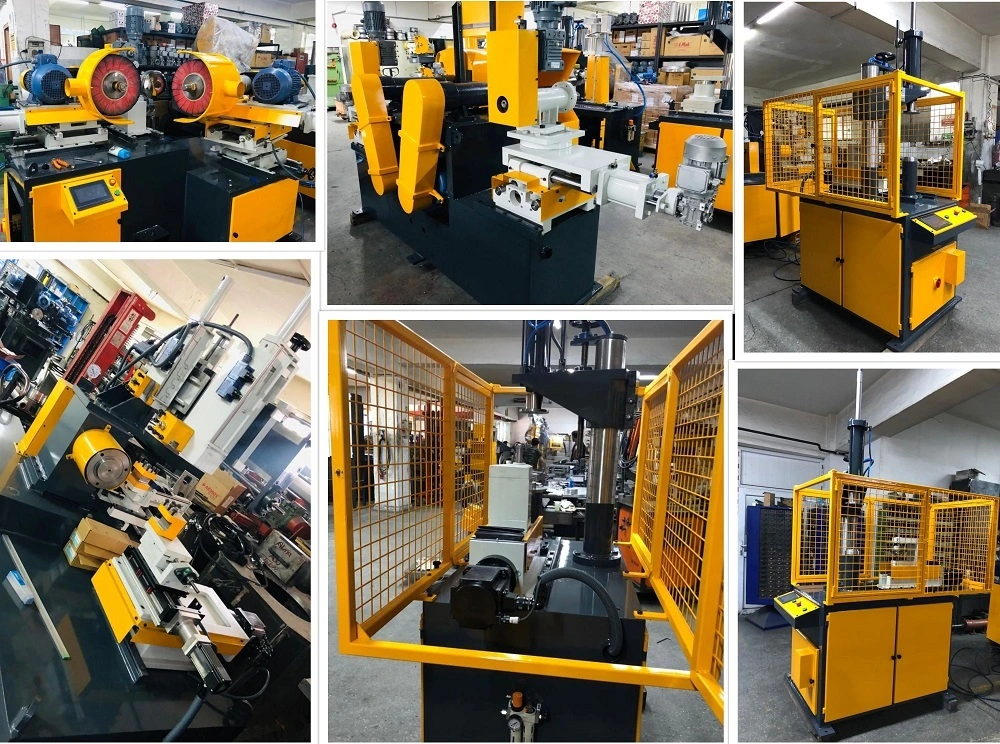
Le formage du métal est un processus consistant à façonner le métal dans la forme et la taille souhaitées à l’aide de diverses techniques. Il s’agit d’un processus crucial dans l’industrie manufacturière car il permet la production de différents produits tels que des pièces automobiles, des composants d’avion, des appareils électroménagers et bien d’autres encore.
Le processus de formage du métal consiste à appliquer une force sur le métal pour changer sa forme sans enlever aucune matière. La force peut être appliquée par diverses méthodes telles que le forgeage, le laminage, l’extrusion, l’étirage et l’estampage. Chaque méthode a ses propres avantages et inconvénients, et le choix de la méthode dépend du matériau formé et de la forme souhaitée.
Le forgeage est l’une des techniques de formage des métaux les plus anciennes. Il s’agit de chauffer le métal à haute température, puis d’appliquer une force de compression à l’aide d’un marteau ou d’une presse pour donner au métal la forme souhaitée. Le forgeage est couramment utilisé pour produire de grandes pièces telles que des engrenages, des essieux et des bielles.
Le laminage est une autre technique de formage du métal qui consiste à faire passer le métal à travers une paire de rouleaux pour réduire son épaisseur ou modifier sa forme. Les rouleaux peuvent être lisses ou texturés selon la finition souhaitée. Le laminage est couramment utilisé pour produire des tôles plates, des plaques et des barres.
L’extrusion est une technique de formage du métal qui consiste à pousser une billette ou une tige métallique à travers une matrice pour créer une forme spécifique. L’extrusion peut être utilisée pour produire des formes complexes telles que des tubes, des canaux et des angles.
L’emboutissage est une technique de formage des métaux utilisée pour réaliser des pièces de forme cylindrique, comme des tubes ou des tuyaux. Le processus consiste à tirer le métal à travers une matrice pour réduire son diamètre et augmenter sa longueur. Le tréfilage est couramment utilisé dans la production de fils, de tiges et de tubes.
L’emboutissage est une technique de formage du métal qui consiste à couper, poinçonner ou plier le métal dans une forme spécifique à l’aide d’une matrice. Le processus peut être utilisé pour produire des pièces avec une grande précision et répétabilité. L’estampage est couramment utilisé dans la production de pièces automobiles, d’appareils électroménagers et d’appareils électroniques.
En plus de ces techniques, il existe de nombreuses autres méthodes de formage des métaux telles que le filage, l’emboutissage profond et l’hydroformage. Chaque méthode a ses propres avantages et inconvénients, et le choix de la méthode dépend des exigences spécifiques du produit fabriqué.
Le formage des métaux est un processus complexe qui nécessite un haut niveau de compétence et d’expertise. Le succès du processus dépend de nombreux facteurs tels que le type de matériau formé, l’équipement utilisé et l’expérience de l’opérateur. En comprenant les différentes techniques de formage des métaux et en choisissant la méthode adaptée au travail, les fabricants peuvent produire des pièces de haute qualité qui répondent aux besoins spécifiques de leurs clients.
La presse hydraulique est une machine industrielle utilisée pour appliquer une force importante sur un matériau dans le but de le déformer, le compacter, ou le découper. Elle tire son nom du principe de fonctionnement basé sur l’hydraulique, c’est-à-dire l’utilisation d’un fluide (généralement de l’huile) pour générer une pression et exercer une force mécanique sur une pièce. Grâce à ce procédé, les presses hydrauliques sont capables de produire des forces considérables, bien supérieures à celles générées par des presses mécaniques ou manuelles, ce qui les rend indispensables dans de nombreuses industries.
Inventée au 18ème siècle par Joseph Bramah, la presse hydraulique a révolutionné les méthodes de fabrication industrielle. Elle est aujourd’hui utilisée dans un large éventail de secteurs, notamment l’industrie automobile, la métallurgie, la fabrication de plastique, et bien d’autres. Cette machine offre une flexibilité inégalée pour de nombreuses applications, telles que le formage des métaux, l’emboutissage, le pliage, le poinçonnage et l’extrusion. Les presses hydrauliques sont également essentielles pour des processus nécessitant une force constante et bien contrôlée.
Cet article explore en détail le fonctionnement des presses hydrauliques, leurs différents types, leurs applications industrielles, ainsi que leurs avantages et inconvénients. Nous aborderons également les exigences de maintenance et l’avenir de cette technologie dans l’industrie moderne.
Historique et Principe de Fonctionnement
2.1 Historique de la Presse Hydraulique
L’invention de la presse hydraulique est attribuée à l’ingénieur britannique Joseph Bramah, qui a déposé un brevet en 1795. Bramah cherchait à développer une machine capable d’exercer une pression beaucoup plus élevée que celle des presses mécaniques utilisées à l’époque. Son invention reposait sur le principe de Pascal, selon lequel une pression appliquée à un fluide incompressible est transmise uniformément dans toutes les directions. Ce principe simple mais révolutionnaire a permis de multiplier la force appliquée sur une surface donnée, ouvrant ainsi la voie à des applications industrielles plus performantes.
À l’origine, la presse hydraulique était utilisée pour des tâches simples comme le pressage des huiles et des textiles. Cependant, avec l’évolution des technologies industrielles, son utilisation s’est étendue à des domaines aussi variés que le formage des métaux, la production de composants électroniques et même le compactage des déchets. Aujourd’hui, les presses hydrauliques sont des machines omniprésentes dans de nombreuses usines modernes et jouent un rôle clé dans la fabrication de produits de haute précision. affirme que la pression appliquée à un fluide incompressible dans un système fermé est transmise de manière égale dans toutes les directions. Cette loi est à la base du mécanisme de la presse hydraulique, qui amplifie une force relativement faible en une force considérablement plus grande à l’aide de pistons et de vérins hydrauliques.
Le composant clé d’une presse hydraulique est son système de cylindres. Ce système se compose généralement de deux cylindres : un petit, appelé cylindre maître, et un plus grand, appelé cylindre esclave. Le cylindre maître est rempli de fluide hydraulique (souvent de l’huile), et une force est appliquée sur ce cylindre. En appliquant cette force sur un fluide incompressible, la pression générée est transmise de manière égale au cylindre esclave, qui a une surface plus grande, amplifiant ainsi la force appliquée. Le cylindre esclave pousse ensuite un poinçon ou une plaque contre la pièce à travailler, permettant ainsi la déformation ou la découpe de celle-ci.
Par exemple, si une petite force est appliquée sur un cylindre maître avec une petite surface, cette force est multipliée en fonction de la différence de surface entre les deux cylindres. Cela signifie que même une pression faible peut générer une force immense dans le cylindre esclave. Le fluide hydraulique joue un rôle crucial en tant que médium qui transmet la pression à travers le système.
2.3 Composants d’une Presse Hydraulique
Les presses hydrauliques sont constituées de plusieurs composants essentiels :
- Cylindre hydraulique : Le cylindre hydraulique est la pièce maîtresse d’une presse hydraulique. Il est composé d’un piston et d’un cylindre dans lequel circule le fluide hydraulique. Le cylindre transforme la pression hydraulique en force mécanique pour presser la pièce.
- Vérin : Le vérin est l’élément qui exerce la force directement sur la pièce à travailler. Le mouvement du vérin est contrôlé par la pression du fluide dans le cylindre. Il peut se déplacer verticalement ou horizontalement selon la conception de la machine.
- Pompe hydraulique : La pompe hydraulique est utilisée pour déplacer le fluide dans le système sous pression. Elle fournit l’énergie nécessaire pour faire fonctionner le système hydraulique.
- Réservoir de fluide : Ce réservoir contient le fluide hydraulique (souvent de l’huile) qui est utilisé pour alimenter le système. Le fluide est pompé dans le cylindre sous pression puis renvoyé au réservoir après chaque cycle.
- Soupapes de contrôle : Les soupapes sont utilisées pour réguler le débit et la pression du fluide hydraulique dans le système. Elles garantissent un contrôle précis de la force et de la vitesse de la presse.
- Châssis : Le châssis d’une presse hydraulique est une structure robuste qui supporte l’ensemble de la machine. Il est conçu pour absorber les forces générées pendant le processus de pressage.
Types de Presses Hydrauliques

Il existe plusieurs types de presses hydrauliques, chacun étant conçu pour des applications spécifiques. Voici quelques-uns des types les plus courants :
3.1 Presse Hydraulique à Col de Cygne
La presse hydraulique à col de cygne, également appelée presse en “C”, est caractérisée par un cadre en forme de “C”, offrant un accès facile à la zone de travail. Cette configuration est idéale pour les petites opérations de formage, de poinçonnage ou de montage où la taille de la pièce est relativement petite. Ce type de presse est couramment utilisé dans les ateliers de réparation et pour les opérations nécessitant un accès rapide à la pièce.
Avantages :
- Facilité d’accès à la zone de travail.
- Idéal pour les petites séries de production.
- Structure compacte, adaptée aux petits ateliers.
Inconvénients :
- Force de pressage limitée par la conception en “C”, moins robuste que d’autres types de presses.
- Moins adapté aux pièces volumineuses ou aux matériaux épais.
3.2 Presse Hydraulique à Cadre H
La presse hydraulique à cadre H, parfois appelée presse à cadre en portique, est l’un des types les plus robustes. Elle est utilisée pour les applications nécessitant une force de pressage importante. La structure en forme de “H” permet une distribution égale de la force sur la pièce, ce qui la rend idéale pour les travaux de formage lourd, d’extrusion et d’emboutissage profond.
Avantages :
- Capacité de générer une force importante pour des opérations lourdes.
- Structure robuste, adaptée aux matériaux épais et aux grandes pièces.
- Haute précision dans les opérations de formage et d’emboutissage.
Inconvénients :
- Encombrante, prend plus de place dans un atelier.
- Coût plus élevé en raison de la complexité de la machine.
3.3 Presse Hydraulique Multicolonne
La presse multicolonne est équipée de plusieurs colonnes verticales qui soutiennent la plaque de pression et guident le vérin. Ce type de presse est conçu pour des opérations nécessitant une précision très élevée et une force de pressage uniforme sur toute la surface de la pièce. Elle est souvent utilisée dans des applications de fabrication nécessitant une très grande précision, comme l’aérospatiale, où chaque millimètre compte.
Avantages :
- Force de pressage très bien répartie, idéale pour des pièces grandes et complexes.
- Très haute précision dans le formage des métaux.
- Permet d’exercer une pression constante et uniforme.
Inconvénients :
- Complexe à entretenir en raison de la multiplicité des colonnes.
- Généralement plus coûteuse que les autres types de presses.
3.4 Presse Hydraulique à Plaques Chauffantes
La presse hydraulique à plaques chauffantes est conçue pour travailler avec des matériaux qui nécessitent une chaleur contrôlée lors du formage, comme les plastiques, les composites ou certains métaux. Les plaques chauffantes permettent de maintenir la température de la pièce tout au long du processus de pressage, ce qui est crucial pour éviter les fissures ou les défauts dans les matériaux sensibles à la température.
Avantages :
- Contrôle précis de la température, idéal pour le travail des matériaux sensibles à la chaleur.
- Permet un formage de haute qualité pour des produits nécessitant des températures précises.
- Réduction des défauts dus aux variations de température.
Inconvénients :
- Nécessite une maintenance accrue pour les éléments chauffants.
- Consommation d’énergie plus élevée en raison du chauffage des plaques.
3.5 Presse Hydraulique à Vérins Multiples
Ce type de presse est équipé de plusieurs vérins hydrauliques, ce qui permet de répartir la force sur plusieurs points de la pièce. Cela est particulièrement utile pour les opérations complexes où la pièce doit être pressée de manière uniforme sur plusieurs zones. Les presses à vérins multiples sont couramment utilisées dans les processus d’assemblage, de collage, et pour les pièces nécessitant une grande uniformité de pression.
Avantages :
- Répartition uniforme de la force sur la pièce.
- Adapté aux opérations complexes nécessitant plusieurs points de pression.
- Haute précision et répétabilité.
Inconvénients :
- Complexité accrue en termes de maintenance et de contrôle des vérins.
- Coût d’acquisition élevé.
Applications Industrielles des Presses Hydrauliques
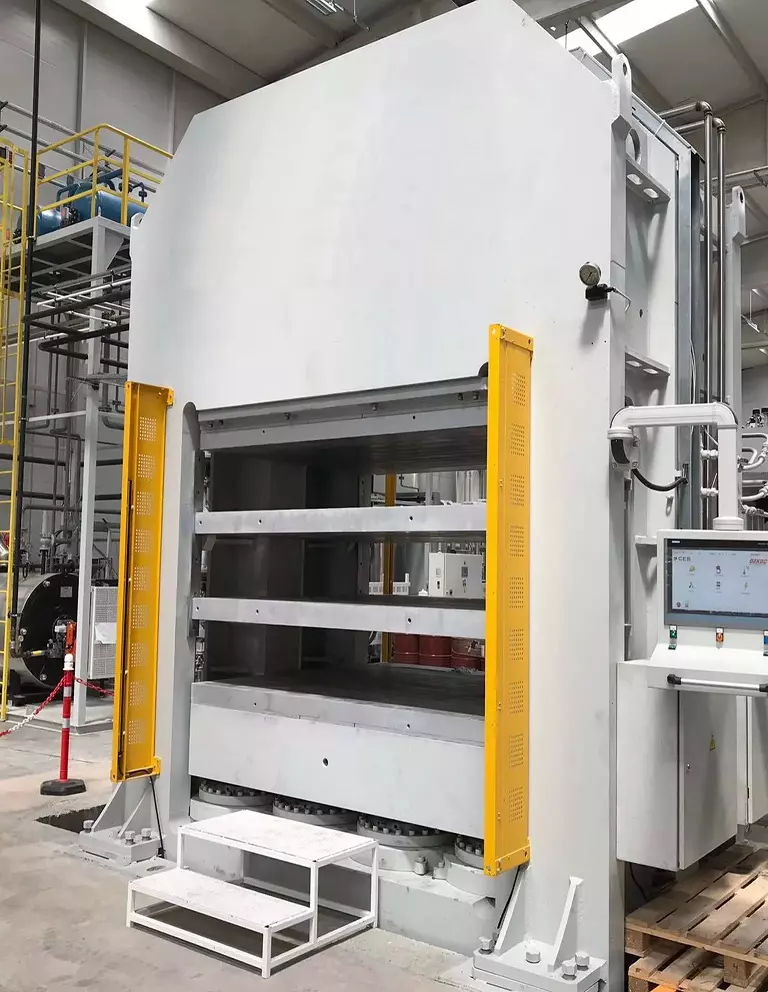
Les presses hydrauliques sont utilisées dans une multitude d’industries, chacune tirant parti des avantages uniques offerts par cette technologie. Voici quelques exemples d’applications typiques.
4.1 Formage des Métaux
L’une des applications les plus courantes des presses hydrauliques est le formage des métaux. Ce processus implique la déformation des métaux à froid ou à chaud pour créer des pièces de formes spécifiques. Les presses hydrauliques sont particulièrement adaptées à ce type d’opération car elles permettent d’exercer une pression constante et contrôlée, même sur des matériaux épais et résistants.
Dans l’industrie automobile, par exemple, les presses hydrauliques sont largement utilisées pour former des composants de carrosserie, des châssis, et d’autres pièces structurelles. La capacité des presses hydrauliques à générer des forces considérables permet de plier, étirer ou emboutir des pièces métalliques avec une grande précision, réduisant ainsi les défauts et augmentant la qualité du produit final.
4.2 Emboutissage
L’emboutissage est un autre processus de fabrication qui tire parti des capacités des presses hydrauliques. Dans ce procédé, une feuille de métal est placée dans une matrice, puis pressée pour prendre une forme tridimensionnelle. Ce processus est utilisé pour créer des pièces telles que des capots de voitures, des portes ou des réservoirs de carburant.
Les presses hydrauliques sont particulièrement efficaces pour l’emboutissage en raison de leur capacité à appliquer une force constante et bien répartie sur toute la pièce, réduisant ainsi le risque de fissures ou de défauts dans les matériaux.
4.3 Extrusion
L’extrusion est un processus dans lequel un matériau est forcé à travers une matrice pour créer des profils de forme continue, comme des tubes, des tiges ou des barres. Les presses hydrauliques sont souvent utilisées pour l’extrusion de matériaux métalliques, plastiques ou composites, car elles peuvent fournir la pression nécessaire pour pousser le matériau à travers la matrice.
L’industrie des matériaux de construction utilise régulièrement ce procédé pour fabriquer des profils en aluminium ou en PVC destinés à être utilisés dans les fenêtres, les portes ou les cadres de bâtiment.
4.4 Poinçonnage et Découpe
Le poinçonnage et la découpe sont des opérations qui consistent à retirer des sections d’un matériau à l’aide d’une presse hydraulique équipée d’un poinçon et d’une matrice. Ces processus sont utilisés pour créer des trous, des ouvertures ou des formes complexes dans des pièces métalliques ou en plastique.
Les presses hydrauliques sont particulièrement adaptées au poinçonnage et à la découpe, car elles peuvent générer des forces très précises et répétitives, garantissant ainsi la constance des dimensions des pièces produites.
4.5 Compactage et Compression
Les presses hydrauliques sont également utilisées pour des opérations de compactage ou de compression. Par exemple, dans le secteur des matériaux composites, elles servent à compacter les couches de fibre de verre, de carbone ou d’autres matériaux dans des moules pour créer des composants robustes. Elles sont aussi couramment utilisées pour compacter des matériaux pulvérulents ou des déchets métalliques en blocs.
Avantages des Presses Hydrauliques
Les presses hydrauliques présentent de nombreux avantages par rapport à d’autres types de machines de pressage, notamment les presses mécaniques. Voici quelques-uns des principaux avantages :
5.1 Force de Pression Élevée et Constante
L’un des principaux atouts des presses hydrauliques est leur capacité à générer des forces de pression extrêmement élevées tout en maintenant une pression constante tout au long du processus. Cette caractéristique est essentielle pour des opérations telles que l’emboutissage profond, le formage et l’extrusion, où une force stable est cruciale pour obtenir des résultats de haute qualité.
5.2 Flexibilité et Polyvalence
Les presses hydrauliques sont extrêmement polyvalentes et peuvent être utilisées pour une large gamme de tâches, de la découpe au formage, en passant par l’extrusion et l’emboutissage. Elles peuvent être facilement ajustées pour traiter différents matériaux et réaliser des opérations complexes sur des pièces de formes variées.
5.3 Précision et Contrôle
Les presses hydrauliques offrent un niveau de contrôle très élevé, notamment grâce à leur capacité à réguler précisément la force et la vitesse de pressage. Cela permet aux opérateurs de produire des pièces avec une grande précision et répétabilité, ce qui est particulièrement important dans les industries où la qualité des produits est essentielle.
5.4 Sécurité
Les presses hydrauliques sont généralement plus sûres à utiliser que les presses mécaniques car elles ne présentent pas les mêmes risques de surcharge ou de blocage. Les systèmes hydrauliques sont équipés de soupapes de sécurité et de régulateurs de pression, garantissant que la machine ne dépasse pas ses limites de fonctionnement.
5.5 Rentabilité
Bien que le coût initial d’une presse hydraulique puisse être plus élevé que celui d’une presse mécanique, son entretien plus simple et sa durée de vie plus longue compensent souvent cet investissement initial. De plus, les presses hydrauliques nécessitent généralement moins d’énergie pour fonctionner, ce qui contribue à réduire les coûts d’exploitation sur le long terme.
Inconvénients des Presses Hydrauliques
Malgré leurs nombreux avantages, les presses hydrauliques présentent également certains inconvénients qu’il convient de prendre en compte.
6.1 Vitesse Relativement Lente
Les presses hydrauliques ont tendance à être plus lentes que les presses mécaniques, en particulier pour les opérations nécessitant des cycles de production rapides. Cela peut être un inconvénient dans les environnements de fabrication où la vitesse est un facteur crucial pour répondre aux exigences de production.
6.2 Besoins de Maintenance Accrus
Le système hydraulique d’une presse nécessite un entretien régulier, en particulier en ce qui concerne la vérification des fuites de fluide, la lubrification et le remplacement des joints d’étanchéité. Les pannes dans le système hydraulique peuvent entraîner des temps d’arrêt coûteux, surtout si des réparations majeures sont nécessaires.
6.3 Consommation d’Énergie
Certaines presses hydrauliques peuvent consommer une quantité importante d’énergie, en particulier celles équipées de grands vérins ou travaillant avec des matériaux très épais. Cependant, cette consommation dépend du modèle de la presse et des exigences spécifiques de l’opération en cours.
Maintenance des Presses Hydrauliques
Pour garantir un fonctionnement optimal et prolonger la durée de vie des presses hydrauliques, il est essentiel de suivre un programme de maintenance régulier. Voici quelques éléments clés à prendre en compte pour assurer une maintenance efficace des presses hydrauliques.
7.1 Vérification du Niveau de Fluide Hydraulique
Le fluide hydraulique est l’élément central du fonctionnement d’une presse hydraulique, car il transmet la pression nécessaire pour générer la force de pressage. Il est donc crucial de vérifier régulièrement le niveau de fluide et de s’assurer qu’il n’y a pas de fuites. Le remplacement régulier du fluide est également important pour éviter la contamination et maintenir l’efficacité de la machine.
7.2 Inspection des Joints et des Éléments d’Étanchéité
Les joints et les éléments d’étanchéité doivent être inspectés régulièrement pour s’assurer qu’ils ne sont pas usés ou endommagés. Des fuites de fluide dues à des joints défectueux peuvent non seulement entraîner une perte d’efficacité de la machine, mais également endommager d’autres composants internes.
7.3 Lubrification des Composants Mobiles
Les composants mobiles de la presse hydraulique, tels que les vérins et les pistons, doivent être correctement lubrifiés pour garantir un mouvement fluide et minimiser l’usure mécanique. Une lubrification insuffisante peut provoquer des frottements excessifs et, à terme, des pannes mécaniques.
7.4 Contrôle des Soupapes et Régulateurs de Pression
Les soupapes de sécurité et les régulateurs de pression sont des éléments cruciaux pour le bon fonctionnement de la presse hydraulique. Ces composants doivent être vérifiés régulièrement pour s’assurer qu’ils fonctionnent correctement et qu’ils régulent la pression conformément aux spécifications du fabricant.
L’Avenir des Presses Hydrauliques dans l’Industrie
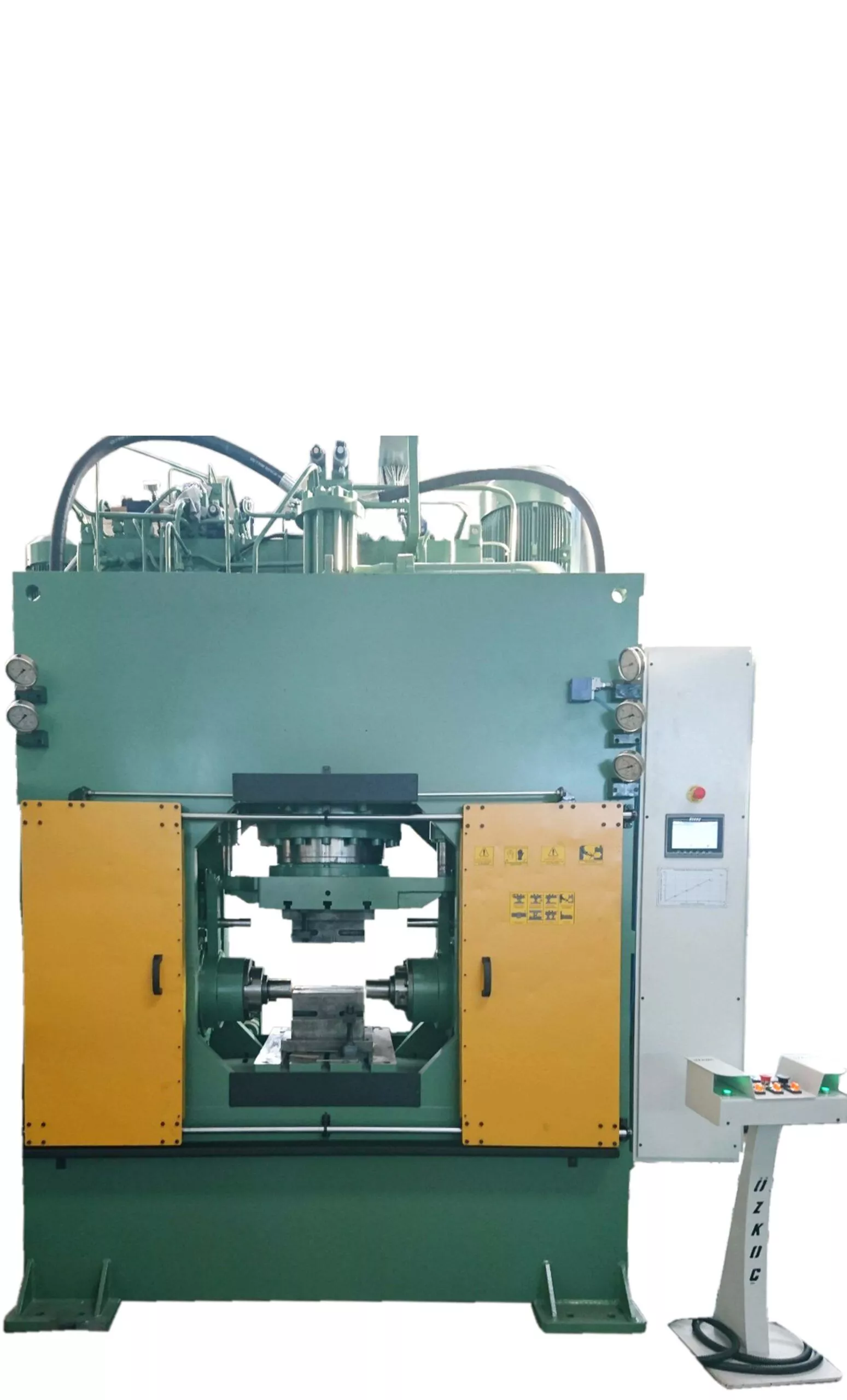
Alors que l’industrie manufacturière évolue vers des technologies plus automatisées et plus durables, les presses hydrauliques continuent de jouer un rôle crucial dans de nombreuses applications. Cependant, les innovations récentes, telles que les systèmes hydrauliques intelligents et les solutions énergétiquement efficaces, contribuent à améliorer les performances des presses hydrauliques tout en réduisant leur empreinte écologique.
Les avancées dans le domaine de la commande numérique (CNC) permettent également aux presses hydrauliques de devenir plus précises et plus adaptables aux processus de fabrication modernes. Ces technologies permettent aux fabricants d’ajuster en temps réel les paramètres de pressage et de surveiller les performances de la machine, optimisant ainsi la production.
En outre, la pression croissante pour adopter des pratiques industrielles plus écologiques pousse les fabricants de presses hydrauliques à développer des solutions plus économes en énergie, en particulier pour réduire la consommation d’énergie des systèmes de fluide hydraulique et les pertes dues à la chaleur.
Conclusion
La presse hydraulique est une machine polyvalente et puissante qui joue un rôle central dans l’industrie manufacturière. Grâce à sa capacité à générer des forces considérables et à sa précision inégalée, elle est utilisée dans une multitude d’applications, allant du formage des métaux à l’emboutissage, en passant par l’extrusion et le poinçonnage. Bien que son fonctionnement repose sur un principe relativement simple, la presse hydraulique offre une flexibilité et une fiabilité qui en font un choix de prédilection pour de nombreuses industries.
Malgré certains inconvénients, comme la nécessité d’une maintenance régulière et une vitesse de fonctionnement parfois plus lente que celle des presses mécaniques, les avantages des presses hydrauliques en termes de puissance, de précision et de sécurité en font un investissement judicieux pour les fabricants cherchant à améliorer leurs processus de production.
Pour ceux qui envisagent d’acquérir une presse hydraulique de haute qualité, EMS Machines de Formage est un fournisseur réputé qui propose une gamme complète de presses adaptées à divers besoins industriels, ainsi qu’un service client exceptionnel pour garantir un fonctionnement optimal de vos machines.
Composants d’une Presse Hydraulique : Une Analyse Approfondie

1. Introduction
La presse hydraulique est une machine essentielle dans le domaine de la fabrication industrielle, largement utilisée pour une multitude d’opérations telles que le formage des métaux, l’emboutissage, le poinçonnage et la découpe. Ce dispositif puissant repose sur le principe de l’hydraulique, où la pression générée par un fluide (souvent de l’huile hydraulique) est utilisée pour appliquer une force massive sur une pièce. Mais derrière cette apparente simplicité se cache un système complexe, composé de nombreux éléments interconnectés.
Dans cet article, nous explorerons en profondeur les composants principaux d’une presse hydraulique. Chacun de ces éléments joue un rôle crucial dans le fonctionnement global de la machine, et leur interaction permet de réaliser des tâches de formage complexes avec une grande précision et puissance. De la pompe hydraulique aux systèmes de commande, en passant par les vérins, les soupapes et les réservoirs de fluide, nous passerons en revue ces composants pour comprendre leur importance, leur fonctionnement et leur contribution à l’efficacité globale de la presse hydraulique.
Les Composants Clés d’une Presse Hydraulique
2.1 Cylindre Hydraulique
Le cylindre hydraulique est sans doute le composant central de toute presse hydraulique. Il s’agit de l’élément qui convertit l’énergie hydraulique en force mécanique, permettant ainsi d’exercer une pression considérable sur la pièce à travailler. Le cylindre est constitué de plusieurs sous-composants, notamment le piston, le fût du cylindre, et les joints d’étanchéité.
- Piston : Le piston est un composant mobile situé à l’intérieur du cylindre. Lorsqu’une pression est appliquée sur le fluide hydraulique, le piston se déplace et transmet cette pression au poinçon ou à la plaque de pression, réalisant ainsi l’opération de formage ou de découpe.
- Fût du cylindre : Il s’agit de la partie extérieure du cylindre qui contient le piston et le fluide hydraulique. Le fût doit être extrêmement robuste, car il est soumis à des pressions très élevées. Il est souvent fabriqué en acier ou dans d’autres matériaux très résistants pour éviter toute déformation ou rupture.
- Joints d’étanchéité : Les joints jouent un rôle crucial dans l’étanchéité du cylindre hydraulique. Ils empêchent les fuites de fluide et garantissent que la pression à l’intérieur du cylindre reste constante. Un mauvais fonctionnement ou l’usure des joints peuvent entraîner une perte de pression, réduisant ainsi l’efficacité globale de la presse.
Les cylindres hydrauliques existent en différentes tailles, en fonction des besoins spécifiques de la presse. Certains cylindres peuvent générer des forces de plusieurs tonnes, ce qui est essentiel pour les opérations de formage de matériaux épais ou durs.
2.2 Vérin
Le vérin est un autre élément clé de la presse hydraulique, souvent confondu avec le cylindre. Le vérin est la partie qui transforme la pression hydraulique en mouvement linéaire. Il est directement relié au cylindre hydraulique et se déplace en réponse à la pression du fluide pour appliquer la force nécessaire au processus de formage, d’emboutissage ou de découpe.
Les vérins sont de deux types principaux :
- Vérin à simple effet : Ce type de vérin n’exerce une force que dans une direction (généralement vers le bas), grâce à la pression hydraulique. Le retour du vérin à sa position initiale est généralement assuré par un ressort ou par le poids de l’outil.
- Vérin à double effet : Contrairement aux vérins à simple effet, les vérins à double effet peuvent appliquer une force dans deux directions (montée et descente). Ils utilisent la pression hydraulique des deux côtés du piston, ce qui permet un contrôle plus précis du mouvement. Ce type de vérin est souvent utilisé dans les applications nécessitant une grande précision, ou lorsque la pièce à travailler doit être pressée dans les deux directions.
Les vérins jouent un rôle fondamental dans le bon fonctionnement de la presse hydraulique. Un dysfonctionnement au niveau du vérin peut entraîner des erreurs dans le processus de fabrication, affectant la qualité des produits finis.
2.3 Pompe Hydraulique
La pompe hydraulique est l’élément qui fournit la pression nécessaire pour faire fonctionner le système. Elle est responsable du déplacement du fluide hydraulique à travers le circuit, générant ainsi la force nécessaire pour actionner les vérins et les pistons. La pompe doit être capable de maintenir une pression constante, car toute fluctuation de la pression pourrait affecter la précision du processus de pressage.
Les pompes hydrauliques existent en plusieurs types, chacun ayant des applications spécifiques :
- Pompe à pistons : Il s’agit de la pompe la plus couramment utilisée dans les presses hydrauliques. Elle est particulièrement efficace pour générer des pressions élevées, ce qui est essentiel pour les opérations nécessitant une grande force de pressage.
- Pompe à engrenages : Ce type de pompe est plus simple et généralement moins coûteux que la pompe à pistons. Elle est souvent utilisée pour des presses hydrauliques de plus petite taille ou pour des applications nécessitant des pressions modérées.
- Pompe à palettes : Les pompes à palettes sont également utilisées dans certaines presses hydrauliques. Elles sont appréciées pour leur fonctionnement silencieux et leur capacité à fournir des débits constants.
Le choix de la pompe dépend largement des besoins spécifiques de la presse hydraulique en termes de pression et de débit. Les systèmes plus complexes peuvent même intégrer plusieurs pompes pour répondre à des besoins variés en matière de force et de précision.
2.4 Réservoir de Fluide Hydraulique
Le réservoir de fluide hydraulique est un composant essentiel de la presse hydraulique, car il contient l’huile hydraulique utilisée pour générer la pression. Ce réservoir permet de stocker et de réguler le fluide, tout en garantissant que celui-ci reste propre et exempt de contaminants. La qualité du fluide hydraulique est primordiale pour garantir le bon fonctionnement du système.
Le réservoir a plusieurs fonctions importantes :
- Stockage du fluide : Le réservoir contient une quantité suffisante de fluide pour alimenter le système hydraulique en continu. Il doit être dimensionné de manière à pouvoir fournir le fluide nécessaire sans que le système soit sous-alimenté.
- Régulation de la température : Pendant le fonctionnement de la presse, le fluide hydraulique peut chauffer en raison de la friction et de la pression élevée. Le réservoir aide à dissiper cette chaleur, maintenant ainsi la température du fluide à des niveaux sûrs et efficaces.
- Filtration du fluide : Le réservoir est souvent équipé de filtres qui permettent de purifier le fluide hydraulique en éliminant les particules et les impuretés qui pourraient endommager les composants du système, comme les soupapes ou les pistons.
Le fluide hydraulique doit être surveillé et remplacé régulièrement pour garantir que le système fonctionne correctement et pour éviter l’usure prématurée des composants internes.
2.5 Soupapes de Contrôle
Les soupapes de contrôle jouent un rôle crucial dans la régulation de la pression et du débit du fluide hydraulique au sein du système. Elles permettent de contrôler le flux de fluide, de maintenir la pression adéquate dans le circuit, et de garantir que chaque composant reçoit la quantité de fluide nécessaire pour fonctionner correctement. Dans une presse hydraulique, les soupapes assurent la sécurité, la précision, et l’efficacité des opérations.
Il existe plusieurs types de soupapes utilisées dans les presses hydrauliques, chacune ayant une fonction spécifique :
2.5.1 Soupape de Décharge (ou Régulateur de Pression)
La soupape de décharge est l’une des soupapes les plus importantes dans une presse hydraulique. Elle est conçue pour limiter la pression maximale dans le système. Si la pression dépasse un certain seuil, la soupape de décharge s’ouvre pour libérer une partie du fluide dans le réservoir, ce qui réduit la pression et empêche d’endommager les composants du système.
Cela est crucial pour la sécurité de l’opérateur et pour la protection des équipements, car une surpression peut entraîner une défaillance catastrophique, notamment une rupture des tuyaux, des fuites importantes, ou même une explosion dans des cas extrêmes.
Avantages :
- Assure la sécurité du système en limitant la pression maximale.
- Prévient les dommages aux composants sensibles à la surpression.
- Contribue à la régulation de la force appliquée lors des opérations de pressage.
2.5.2 Soupape de Sécurité
La soupape de sécurité est une autre soupape critique qui agit comme un mécanisme de secours si la pression dans le système devient trop élevée. Contrairement à la soupape de décharge, qui contrôle la pression dans des conditions normales de fonctionnement, la soupape de sécurité est activée uniquement en cas d’urgence, lorsque les autres dispositifs de régulation de pression échouent. Une fois la pression excessive détectée, la soupape s’ouvre pour relâcher une partie du fluide et rétablir un niveau de sécurité dans le circuit.
2.5.3 Soupape de Régulation du Débit
La soupape de régulation du débit contrôle la quantité de fluide qui circule à travers le système, régulant ainsi la vitesse à laquelle les vérins ou les pistons se déplacent. En ajustant le débit, l’opérateur peut contrôler avec précision la vitesse à laquelle la presse applique une pression sur la pièce à travailler.
Ces soupapes sont particulièrement utiles pour les applications qui nécessitent un contrôle fin de la vitesse, telles que le formage de précision, l’emboutissage ou les processus de compression. En régulant le débit, les presses hydrauliques peuvent réaliser des opérations complexes qui exigent une coordination précise entre la force et la vitesse.
Avantages :
- Permet un contrôle précis de la vitesse des vérins et des pistons.
- Améliore la précision des opérations de formage et d’emboutissage.
- Contribue à l’efficacité énergétique en optimisant le débit de fluide.
2.5.4 Soupape Directionnelle
La soupape directionnelle détermine le chemin que le fluide hydraulique doit suivre à l’intérieur du système. Elle permet de diriger le fluide vers différentes parties du système en fonction des besoins de l’opération en cours. Par exemple, dans une presse hydraulique à double effet, la soupape directionnelle peut inverser le flux de fluide, permettant ainsi au vérin de se déplacer dans les deux directions (montée et descente).
Cette capacité à contrôler la direction du fluide est essentielle pour les opérations nécessitant des cycles complexes, où la presse doit appliquer une force dans plusieurs directions.
Avantages :
- Offre un contrôle total de la direction du fluide hydraulique.
- Permet des opérations à double effet, optimisant l’utilisation du vérin.
- Essentiel pour les cycles de pressage complexes.
2.6 Système de Filtration
Le système de filtration est un autre composant clé de toute presse hydraulique. Il joue un rôle crucial dans la protection des composants internes en filtrant les impuretés présentes dans le fluide hydraulique. Des particules, des débris ou de la saleté peuvent entrer dans le système hydraulique, provoquant une usure prématurée des composants tels que les vérins, les pistons et les soupapes.
Le système de filtration utilise des filtres qui capturent ces impuretés avant qu’elles n’atteignent les parties sensibles du système. Un fluide hydraulique propre est essentiel pour maintenir la performance de la machine, minimiser l’usure et prolonger la durée de vie des composants.
Avantages :
- Protège les composants contre l’usure prématurée due aux impuretés.
- Améliore l’efficacité du système hydraulique en réduisant la résistance interne.
- Réduit les coûts de maintenance en minimisant les risques de pannes.
2.7 Réchauffeurs et Refroidisseurs
Dans certaines presses hydrauliques, le fluide hydraulique doit être maintenu à une température spécifique pour assurer un fonctionnement optimal. Les réchauffeurs et refroidisseurs sont des composants utilisés pour contrôler la température du fluide.
- Réchauffeurs : Les réchauffeurs sont utilisés dans des environnements froids où le fluide peut devenir trop visqueux à basse température, réduisant ainsi son efficacité. En réchauffant le fluide, la viscosité est abaissée, ce qui permet une meilleure circulation et une transmission de pression plus efficace.
- Refroidisseurs : À l’inverse, les refroidisseurs sont utilisés dans les presses hydrauliques où le fluide hydraulique peut surchauffer en raison des pressions élevées ou d’une utilisation prolongée. Un excès de chaleur peut endommager les composants internes et entraîner une dégradation prématurée du fluide. Le refroidissement du fluide aide à maintenir une température optimale, garantissant ainsi une performance constante.
Avantages :
- Maintient une température optimale du fluide hydraulique.
- Protège le système contre les effets néfastes de la surchauffe ou du refroidissement excessif.
- Prolonge la durée de vie du fluide et des composants internes.
2.8 Table de Travail et Châssis
La table de travail et le châssis d’une presse hydraulique constituent la structure physique sur laquelle les opérations de pressage sont effectuées. Le châssis doit être suffisamment solide pour supporter les forces massives générées par la presse hydraulique sans fléchir ni se déformer.
- Table de travail : La table de travail est la surface sur laquelle la pièce à travailler est placée pendant le processus de pressage. Elle est souvent équipée de dispositifs de fixation pour maintenir la pièce en place. Les tables peuvent être fixes ou mobiles, en fonction du type de presse et des opérations spécifiques à réaliser.
- Châssis : Le châssis de la presse est généralement fabriqué en acier robuste ou dans d’autres matériaux résistants pour absorber les forces de pressage. Il existe plusieurs configurations de châssis, telles que le cadre en “C” ou le cadre en “H”, qui offrent différents avantages en termes de force et d’accessibilité à la zone de travail.
Avantages :
- Fournit une structure stable pour supporter les forces de pressage.
- Peut être conçu pour répondre à des besoins spécifiques en termes d’accessibilité ou de force.
- Essentiel pour garantir la précision et la sécurité des opérations de pressage.
2.9 Système de Commande
Le système de commande est le cerveau de la presse hydraulique. Dans les presses modernes, ce système est souvent informatisé et permet un contrôle précis des paramètres de pressage, tels que la force appliquée, la vitesse de pressage, et la position du vérin. Les systèmes de commande peuvent varier du simple contrôle manuel à des systèmes entièrement automatisés, comme les systèmes CNC (Commande Numérique par Ordinateur).
- Commande manuelle : Dans les presses hydrauliques de base, l’opérateur contrôle manuellement les soupapes et les commandes pour ajuster la pression et la vitesse de pressage. Ce type de commande est souvent utilisé dans les petits ateliers ou pour des opérations simples.
- Commande numérique (CNC) : Les presses hydrauliques plus avancées sont équipées de systèmes CNC qui permettent de programmer des séquences complexes de pressage avec une grande précision. Ces systèmes permettent de réaliser des opérations répétitives avec une grande exactitude, ce qui est particulièrement utile pour la production en série.
Avantages :
- Permet un contrôle précis des paramètres de pressage.
- Réduit les erreurs humaines en automatisant le processus.
- Améliore la qualité et la répétabilité des pièces produites.
Maintenance des Composants d’une Presse Hydraulique
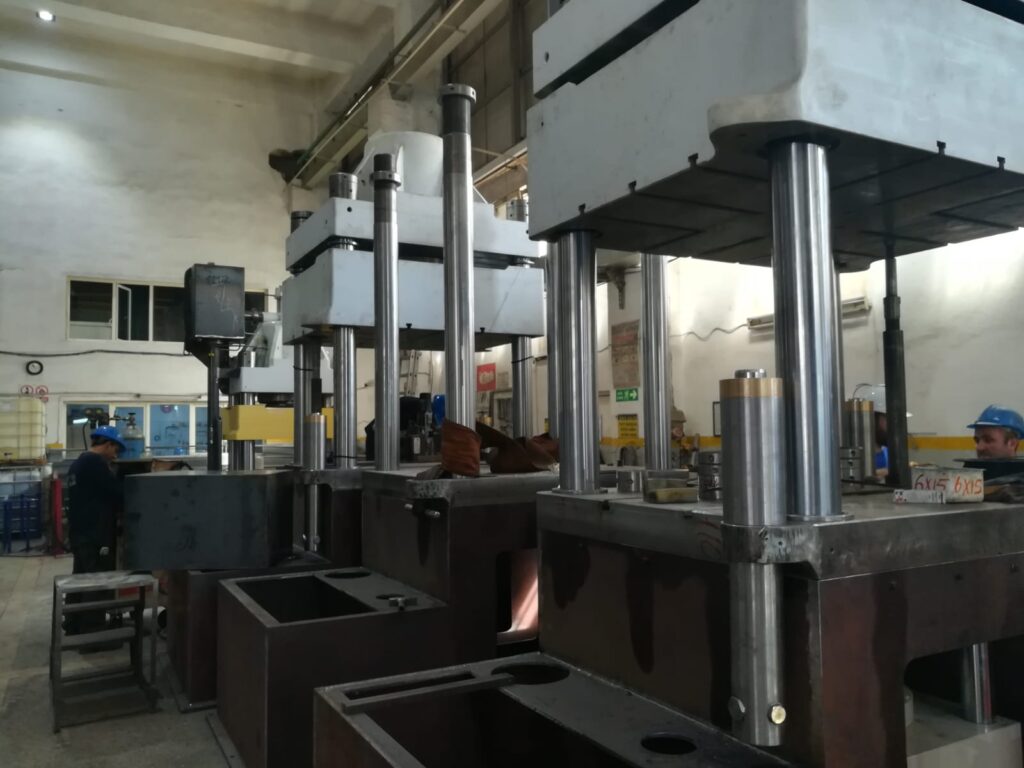
Pour assurer le bon fonctionnement et prolonger la durée de vie des composants d’une presse hydraulique, un programme de maintenance régulier est indispensable. Voici quelques pratiques de maintenance courantes :
3.1 Entretien du Fluide Hydraulique
Le fluide hydraulique doit être régulièrement contrôlé et remplacé pour garantir que le système fonctionne de manière optimale. Les filtres doivent également être nettoyés ou remplacés pour éviter la contamination du fluide.
3.2 Inspection des Vérins et Cylindres
Les vérins et cylindres doivent être inspectés régulièrement pour détecter des signes d’usure ou de fuite. Les joints d’étanchéité doivent être remplacés dès qu’ils montrent des signes de défaillance pour éviter les fuites de fluide.
3.3 Vérification des Soupapes
Les soupapes de contrôle doivent être vérifiées et nettoyées régulièrement pour garantir qu’elles fonctionnent correctement. Des soupapes défectueuses peuvent entraîner une perte de pression et affecter les performances de la presse.
3.4 Contrôle du Système de Commande
Le système de commande, qu’il soit manuel ou CNC, doit être régulièrement testé pour s’assurer qu’il fonctionne correctement. Les composants électroniques doivent être protégés de la poussière et des environnements humides pour éviter les dysfonctionnements.
Conclusion
Les composants d’une presse hydraulique travaillent ensemble pour permettre la création de pièces complexes avec une grande force et précision. Des vérins aux soupapes, en passant par la pompe hydraulique et le réservoir de fluide, chaque élément joue un rôle crucial dans le fonctionnement global de la machine. Une bonne compréhension de ces composants et de leur entretien est essentielle pour maximiser l’efficacité de la presse et prolonger sa durée de vie. Pour ceux qui cherchent à investir dans des presses hydrauliques de haute qualité, EMS Machines de Formage est un partenaire fiable, offrant une large gamme de machines et de composants adaptés aux besoins industriels.
Types de Presses Hydrauliques : Une Analyse Approfondie

1. Introduction
Les presses hydrauliques jouent un rôle crucial dans de nombreuses industries modernes, où elles sont utilisées pour diverses opérations telles que le formage des métaux, l’emboutissage, le pliage, la découpe et bien plus encore. En raison de leur capacité à générer des forces importantes avec une grande précision, elles sont omniprésentes dans des secteurs tels que l’automobile, l’aéronautique, la construction, et l’électronique. Mais derrière leur apparente simplicité se cache une large gamme de types de presses hydrauliques, chacune adaptée à des applications spécifiques. Le choix du bon type de presse dépend de nombreux facteurs, tels que la nature des matériaux à travailler, le niveau de précision requis, et la cadence de production.
Dans cet article, nous explorerons en détail les différents types de presses hydrauliques disponibles sur le marché, leurs caractéristiques, leurs avantages, et leurs applications spécifiques. Nous examinerons également les innovations récentes dans le domaine des presses hydrauliques et leur impact sur l’industrie manufacturière moderne.
Presses Hydraulique à Col de Cygne (ou Presse en “C”)

La presse hydraulique à col de cygne, également appelée presse en “C”, tire son nom de la forme distinctive de son châssis, qui ressemble à un “C”. Ce type de presse est conçu pour offrir un accès facile à la zone de travail grâce à sa structure ouverte. Cela permet à l’opérateur d’insérer et de retirer des pièces rapidement, ce qui en fait un choix populaire dans les ateliers de réparation et les petites séries de production. Le cadre en forme de “C” est cependant limité en termes de robustesse, ce qui signifie qu’il est mieux adapté aux applications de formage léger.
2.1 Caractéristiques et Fonctionnement
La presse à col de cygne se caractérise par une construction relativement simple. Le vérin hydraulique, qui génère la force de pressage, est monté au sommet de la structure en “C”. Lorsqu’une pression est appliquée, le vérin pousse le poinçon contre la pièce à travailler, la déformant ou la découpant selon les besoins de l’opération.
Avantages :
- Accessibilité : L’un des principaux avantages de la presse à col de cygne est son accès facile à la zone de travail. Cela permet aux opérateurs de manipuler facilement les pièces, rendant cette presse idéale pour des opérations rapides et fréquentes.
- Compacte : Sa conception en “C” rend cette presse plus compacte que d’autres types de presses hydrauliques, ce qui est un atout pour les petits ateliers ou les espaces de travail restreints.
- Coût réduit : Comparée à des presses plus lourdes, la presse à col de cygne est relativement peu coûteuse à fabriquer, ce qui la rend abordable pour les petites entreprises ou les ateliers spécialisés.
Inconvénients :
- Limites de force : En raison de la conception ouverte du cadre en “C”, ce type de presse est limité en termes de force maximale. Le cadre peut se déformer sous des charges élevées, ce qui le rend moins adapté aux opérations nécessitant une grande puissance.
- Risque de désalignement : La structure ouverte peut également entraîner un désalignement entre le poinçon et la matrice, affectant la précision des opérations.
2.2 Applications de la Presse à Col de Cygne
Les presses à col de cygne sont couramment utilisées dans les opérations de formage léger, telles que :
- Montage et démontage de pièces : En raison de sa facilité d’accès, cette presse est souvent utilisée pour assembler ou démonter des composants mécaniques.
- Redressage : Le redressage de pièces métalliques déformées est une autre application courante, car la presse à col de cygne permet d’appliquer des forces contrôlées à des zones spécifiques.
- Pliage et formage léger : Elle est également utilisée pour plier et former des pièces de métal de petite à moyenne taille, en particulier dans les ateliers de fabrication sur mesure.
Presse Hydraulique à Cadre H (Presse en Portique)
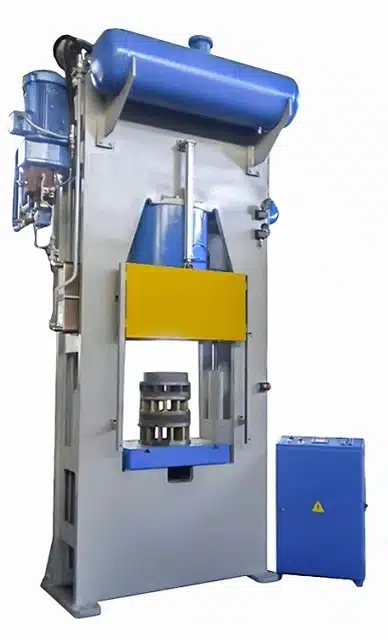
La presse hydraulique à cadre H, également appelée presse en portique, est l’une des presses hydrauliques les plus robustes et polyvalentes disponibles sur le marché. Contrairement à la presse à col de cygne, qui est limitée par la rigidité de son cadre, la presse à cadre H est conçue pour des opérations nécessitant des forces importantes. Son cadre est composé de deux montants verticaux reliés par une traverse supérieure et inférieure, formant ainsi une structure en forme de “H”. Cette conception confère à la machine une grande stabilité et permet d’appliquer des forces importantes sans risque de déformation du cadre.
3.1 Caractéristiques et Fonctionnement
Le cadre robuste de la presse à cadre H permet une répartition uniforme des forces, ce qui est crucial pour les opérations de formage, d’emboutissage, et d’extrusion de matériaux épais ou résistants. Le vérin hydraulique est généralement monté sur la traverse supérieure, tandis que la pièce à travailler est placée sur la table située sur la traverse inférieure. Lorsque la presse est activée, le vérin pousse le poinçon contre la pièce, appliquant une force uniforme sur toute la surface de la pièce.
Avantages :
- Grande capacité de force : La presse à cadre H est capable de générer des forces considérables, ce qui la rend idéale pour les opérations de formage et d’emboutissage des métaux lourds.
- Répartition uniforme de la force : Grâce à sa conception symétrique, la force appliquée est uniformément répartie sur la pièce, garantissant une meilleure précision dans les opérations de formage.
- Adaptabilité : La presse à cadre H peut être équipée de plusieurs vérins hydrauliques pour des applications complexes nécessitant des forces variables.
Inconvénients :
- Encombrement : En raison de sa taille, la presse à cadre H prend plus de place dans un atelier que les presses à col de cygne ou à cadre en “C”. Elle nécessite donc un espace de travail plus important.
- Coût élevé : Les presses à cadre H sont plus coûteuses à fabriquer en raison de leur structure robuste et de leur capacité à générer des forces élevées.
3.2 Applications de la Presse à Cadre H
Les presses hydrauliques à cadre H sont largement utilisées dans des secteurs industriels où des forces de pressage importantes sont requises, notamment :
- Emboutissage profond : Ce processus, qui consiste à former des pièces métalliques en trois dimensions à partir de tôles, nécessite des forces considérables que seule une presse à cadre H peut générer.
- Formage à chaud : Le formage des métaux à haute température, qui nécessite des forces importantes et une distribution uniforme de la pression, est une application idéale pour la presse à cadre H.
- Réparation de châssis automobiles : Dans l’industrie automobile, les presses à cadre H sont souvent utilisées pour réparer ou ajuster les châssis, car elles permettent d’exercer des forces importantes avec une grande précision.
Presse Hydraulique à Double Effet
La presse hydraulique à double effet est un type de presse spécialement conçu pour exercer une pression dans deux directions. Contrairement aux presses à simple effet, où la force est appliquée uniquement dans une direction (généralement vers le bas), les presses à double effet utilisent deux vérins distincts qui permettent de contrôler à la fois la descente et la montée du poinçon. Ce type de presse est particulièrement utile pour les opérations nécessitant un contrôle précis de la force et du mouvement, comme l’emboutissage profond ou le formage complexe.
4.1 Caractéristiques et Fonctionnement
Dans une presse à double effet, un vérin est utilisé pour appliquer une pression vers le bas, tandis qu’un second vérin est utilisé pour contrôler le mouvement de retour. Ce système à double vérin permet un contrôle très précis de la force de pressage, ce qui est crucial pour les opérations nécessitant une pression uniforme et continue sur la pièce à travailler. En outre, la presse à double effet permet d’ajuster indépendamment la vitesse et la force de chaque mouvement (descente et remontée), offrant ainsi une grande flexibilité dans les processus de fabrication.
Avantages :
- Contrôle précis : Le système à double vérin permet un contrôle très fin de la pression et du mouvement, ce qui est essentiel pour les opérations de formage complexes.
- Flexibilité : La possibilité d’ajuster la force et la vitesse dans les deux directions permet de traiter une large gamme de matériaux et de formes.
- Précision dans les opérations d’emboutissage profond : Grâce à sa capacité à contrôler le mouvement de retour, la presse à double effet réduit le risque de déformations ou de fissures dans les matériaux emboutis.
Inconvénients :
- Complexité accrue : En raison de la présence de deux vérins, la presse à double effet est plus complexe à entretenir et à utiliser que les presses à simple effet.
- Coût plus élevé : La conception à double vérin entraîne un coût d’acquisition plus élevé par rapport aux presses hydrauliques traditionnelles.
4.2 Applications de la Presse à Double Effet
Les presses à double effet sont particulièrement prisées dans les industries où la précision et la flexibilité sont cruciales. Elles sont utilisées pour :
- Emboutissage profond : Ce processus, qui consiste à former des pièces métalliques en trois dimensions à partir de tôles, nécessite un contrôle précis de la force et du mouvement pour éviter les déformations et garantir la qualité des pièces.
- Formage de précision : Dans des secteurs comme l’aéronautique et l’électronique, où des pièces complexes doivent être formées avec une grande précision, la presse à double effet offre une flexibilité inégalée.
- Moulage de plastique : Ce type de presse est également utilisé dans le moulage de plastiques où la pression doit être appliquée de manière uniforme et contrôlée dans les deux directions pour garantir une distribution homogène du matériau dans le moule.
Presse Hydraulique Multicolonne
La presse hydraulique multicolonne est une machine conçue pour offrir une répartition uniforme de la pression sur la pièce à travailler. Contrairement aux presses classiques qui utilisent un seul vérin centralisé, la presse multicolonne est équipée de plusieurs vérins disposés autour de la zone de travail, généralement soutenus par plusieurs colonnes. Cette configuration permet de maintenir une grande précision et une stabilité lors du formage de grandes pièces ou de composants nécessitant une force uniforme sur toute la surface.
5.1 Caractéristiques et Fonctionnement
Le châssis d’une presse multicolonne est renforcé par plusieurs colonnes qui encadrent la zone de travail, offrant ainsi un support et une stabilité supplémentaires. Les vérins hydrauliques sont disposés de manière à appliquer une pression équilibrée sur l’ensemble de la pièce, ce qui permet d’éviter les déformations et d’assurer une finition de haute qualité. Ces presses sont particulièrement utilisées pour les opérations qui nécessitent des tolérances très serrées, où même de légères variations de pression peuvent entraîner des défauts dans le produit final.
Avantages :
- Répartition uniforme de la pression : La présence de plusieurs vérins garantit que la pression est appliquée de manière homogène sur la pièce, réduisant ainsi le risque de déformations et de défauts.
- Stabilité accrue : Le cadre multicolonne assure une stabilité exceptionnelle, même lors de l’application de forces importantes, ce qui est crucial pour les grandes pièces ou les matériaux épais.
- Haute précision : Les presses multicolonne sont idéales pour les opérations nécessitant une grande précision, telles que le formage de pièces d’aéronefs ou de composants électroniques.
Inconvénients :
- Coût élevé : En raison de leur complexité et de leur capacité à appliquer des forces importantes de manière uniforme, les presses multicolonne sont généralement plus coûteuses que les presses classiques.
- Encombrement : Ces machines prennent plus de place dans un atelier en raison de leur structure complexe, nécessitant ainsi un espace de travail plus important.
5.2 Applications de la Presse Multicolonne
Les presses multicolonne sont couramment utilisées dans des secteurs où la précision et la stabilité sont essentielles, notamment :
- Industrie aérospatiale : La fabrication de composants d’aéronefs nécessite une précision extrême et des forces de pressage uniformes pour éviter les déformations et garantir la sécurité des pièces.
- Fabrication de grandes plaques métalliques : Les presses multicolonne sont également utilisées pour former de grandes plaques métalliques, où une répartition uniforme de la pression est essentielle pour éviter les déformations.
- Industrie électronique : Dans la production de composants électroniques, où les tolérances sont très serrées, la capacité des presses multicolonne à appliquer des forces précises et uniformes est cruciale pour garantir la qualité des produits.
Presse Hydraulique à Vérins Multiples
La presse hydraulique à vérins multiples est une machine spécialisée qui utilise plusieurs vérins hydrauliques pour appliquer une force sur la pièce à travailler. Ce type de presse est conçu pour les opérations complexes qui nécessitent une application de force sur plusieurs points simultanément. En utilisant plusieurs vérins, la presse à vérins multiples permet de répartir la pression de manière contrôlée sur l’ensemble de la pièce, offrant ainsi une grande flexibilité et précision dans les opérations de formage, d’assemblage et d’emboutissage.
6.1 Caractéristiques et Fonctionnement
Le fonctionnement de la presse à vérins multiples repose sur l’utilisation de plusieurs vérins hydrauliques, chacun étant contrôlé indépendamment pour appliquer une force à un point spécifique de la pièce. Cette capacité à ajuster la force de chaque vérin permet de créer des pièces complexes avec des formes variées et des tolérances précises.
Avantages :
- Flexibilité : La presse à vérins multiples permet de contrôler chaque vérin individuellement, offrant ainsi une flexibilité inégalée dans les opérations de formage complexes.
- Répartition précise de la force : En utilisant plusieurs vérins, cette presse permet une répartition précise de la force sur des points spécifiques de la pièce, réduisant ainsi le risque de déformations.
- Adaptée aux grandes pièces : Ce type de presse est idéal pour les grandes pièces ou les composants qui nécessitent une application de force sur plusieurs zones en même temps.
Inconvénients :
- Complexité accrue : La présence de plusieurs vérins rend cette presse plus complexe à entretenir et à utiliser. Chaque vérin doit être contrôlé et ajusté de manière précise pour garantir un fonctionnement optimal.
- Coût élevé : En raison de la complexité du système, la presse à vérins multiples est plus coûteuse que les presses hydrauliques traditionnelles.
6.2 Applications de la Presse à Vérins Multiples
Les presses à vérins multiples sont largement utilisées dans des industries nécessitant un contrôle précis et une flexibilité maximale dans les opérations de formage et d’assemblage, telles que :
- Assemblage de composants automobiles : Dans l’industrie automobile, où des forces doivent être appliquées sur plusieurs points simultanément pour l’assemblage de pièces complexes, la presse à vérins multiples est un choix idéal.
- Industrie de l’électroménager : La fabrication d’appareils électroménagers nécessite souvent des opérations de formage et d’emboutissage qui impliquent des forces appliquées de manière répartie sur plusieurs zones de la pièce.
- Industrie du bâtiment : La presse à vérins multiples est également utilisée dans la production de composants de construction, tels que des poutres en acier, où une répartition uniforme de la pression est cruciale.
Presse Hydraulique à Table Mobile
La presse hydraulique à table mobile est une machine qui combine la puissance d’une presse hydraulique avec la flexibilité d’une table mobile. Ce type de presse est conçu pour les opérations nécessitant une grande accessibilité et une manipulation facile des pièces à travailler. La table mobile permet de déplacer la pièce dans et hors de la zone de pressage, ce qui est particulièrement utile pour les grandes pièces ou les opérations nécessitant un chargement et un déchargement fréquents.
7.1 Caractéristiques et Fonctionnement
La presse à table mobile est équipée d’une table de travail qui peut se déplacer horizontalement, permettant ainsi à l’opérateur de positionner facilement la pièce sous le poinçon ou la matrice. Une fois la pièce en place, le vérin hydraulique applique la force de pressage. Après l’opération, la table peut être déplacée pour retirer la pièce finie.
Avantages :
- Accessibilité améliorée : La table mobile permet un accès facile à la zone de travail, ce qui facilite le chargement et le déchargement des pièces, en particulier pour les grandes ou lourdes.
- Flexibilité opérationnelle : Ce type de presse est idéal pour les opérations nécessitant un repositionnement fréquent des pièces.
- Idéal pour les grandes pièces : La possibilité de déplacer la table rend cette presse particulièrement adaptée aux grandes pièces ou aux matériaux lourds qui seraient difficiles à manipuler avec une presse fixe.
Inconvénients :
- Complexité mécanique : La table mobile ajoute un niveau de complexité mécanique qui nécessite une maintenance régulière pour garantir un fonctionnement fluide.
- Coût plus élevé : Le mécanisme de table mobile entraîne un coût supplémentaire par rapport aux presses fixes.
7.2 Applications de la Presse à Table Mobile
Les presses à table mobile sont largement utilisées dans les industries où la manipulation facile des pièces est essentielle, notamment :
- Industrie du métal : Le formage et l’emboutissage de grandes pièces métalliques nécessitent souvent une presse à table mobile pour faciliter le chargement et le déchargement des pièces.
- Fabrication de moules : Dans la fabrication de moules pour le plastique ou les composites, la table mobile permet de manipuler facilement des moules de grande taille.
- Industrie de la construction : Les presses à table mobile sont également utilisées pour produire des composants de construction de grande taille, tels que des poutres ou des panneaux en métal.
Conclusion
Les presses hydrauliques sont des outils indispensables dans de nombreuses industries modernes. Chaque type de presse hydraulique possède des caractéristiques spécifiques qui le rendent adapté à des applications particulières. Des presses à col de cygne compactes et abordables aux puissantes presses à cadre H et aux presses à vérins multiples complexes, il existe une solution pour chaque besoin industriel.
Le choix du bon type de presse hydraulique dépend de nombreux facteurs, tels que la nature des matériaux à travailler, la force requise, la précision nécessaire, et l’espace disponible dans l’atelier. Les progrès technologiques, tels que les systèmes hydrauliques automatisés et les presses à contrôle numérique, permettent d’élargir encore les possibilités offertes par ces machines puissantes et polyvalentes.
Pour les entreprises à la recherche de solutions performantes en matière de presses hydrauliques, EMS Machines de Formage est un fournisseur de confiance. Avec une gamme complète de presses adaptées à divers besoins industriels, EMS offre des machines robustes, fiables, et soutenues par un service client de qualité pour garantir une productivité optimale.
EMS Machines de Formage
Le formage du métal est un processus consistant à façonner le métal dans la forme et la taille souhaitées à l’aide de diverses techniques. Il s’agit d’un processus crucial dans l’industrie manufacturière car il permet la production de différents produits tels que des pièces automobiles, des composants d’avion, des appareils électroménagers et bien d’autres encore.
Le processus de formage du métal consiste à appliquer une force sur le métal pour changer sa forme sans enlever aucune matière. La force peut être appliquée par diverses méthodes telles que le forgeage, le laminage, l’extrusion, l’étirage et l’estampage. Chaque méthode a ses propres avantages et inconvénients, et le choix de la méthode dépend du matériau formé et de la forme souhaitée.
Le forgeage est l’une des techniques de formage des métaux les plus anciennes. Il s’agit de chauffer le métal à haute température, puis d’appliquer une force de compression à l’aide d’un marteau ou d’une presse pour donner au métal la forme souhaitée. Le forgeage est couramment utilisé pour produire de grandes pièces telles que des engrenages, des essieux et des bielles.
Le laminage est une autre technique de formage du métal qui consiste à faire passer le métal à travers une paire de rouleaux pour réduire son épaisseur ou modifier sa forme. Les rouleaux peuvent être lisses ou texturés selon la finition souhaitée. Le laminage est couramment utilisé pour produire des tôles plates, des plaques et des barres.
L’extrusion est une technique de formage du métal qui consiste à pousser une billette ou une tige métallique à travers une matrice pour créer une forme spécifique. L’extrusion peut être utilisée pour produire des formes complexes telles que des tubes, des canaux et des angles.
L’emboutissage est une technique de formage des métaux utilisée pour réaliser des pièces de forme cylindrique, comme des tubes ou des tuyaux. Le processus consiste à tirer le métal à travers une matrice pour réduire son diamètre et augmenter sa longueur. Le tréfilage est couramment utilisé dans la production de fils, de tiges et de tubes.
L’emboutissage est une technique de formage du métal qui consiste à couper, poinçonner ou plier le métal dans une forme spécifique à l’aide d’une matrice. Le processus peut être utilisé pour produire des pièces avec une grande précision et répétabilité. L’estampage est couramment utilisé dans la production de pièces automobiles, d’appareils électroménagers et d’appareils électroniques.
En plus de ces techniques, il existe de nombreuses autres méthodes de formage des métaux telles que le filage, l’emboutissage profond et l’hydroformage. Chaque méthode a ses propres avantages et inconvénients, et le choix de la méthode dépend des exigences spécifiques du produit fabriqué.
Le formage des métaux est un processus complexe qui nécessite un haut niveau de compétence et d’expertise. Le succès du processus dépend de nombreux facteurs tels que le type de matériau formé, l’équipement utilisé et l’expérience de l’opérateur. En comprenant les différentes techniques de formage des métaux et en choisissant la méthode adaptée au travail, les fabricants peuvent produire des pièces de haute qualité qui répondent aux besoins spécifiques de leurs clients.