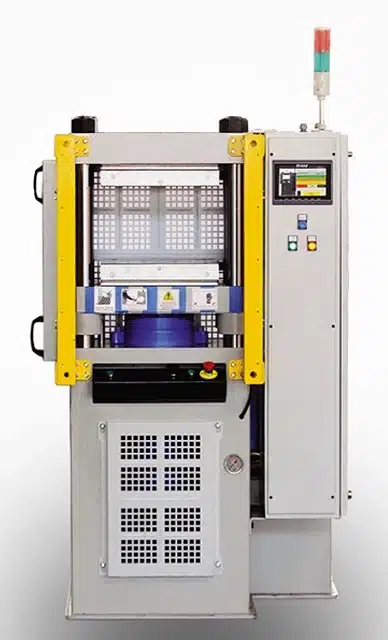
Presse de Laboratoire: Les presses de laboratoire, bien que moins connues que les équipements tels que les microscopes ou les centrifugeuses, jouent un rôle crucial dans de nombreux domaines de la recherche scientifique et industrielle. Ces appareils sont utilisés pour appliquer une pression contrôlée sur des échantillons, afin de réaliser diverses opérations comme la formation de matériaux, la préparation d’échantillons pour des analyses ou encore des tests de résistance. Ce type d’équipement est indispensable pour garantir la répétabilité des expériences et l’uniformité des résultats.
Les presses de laboratoire sont particulièrement importantes dans des secteurs comme l’industrie pharmaceutique, la recherche sur les matériaux, la chimie ou encore les biotechnologies. Elles permettent de simuler des conditions réelles de production ou d’expérimenter des méthodes à petite échelle avant de passer à des processus à plus grande échelle. Par exemple, dans le domaine pharmaceutique, elles sont utilisées pour comprimer des poudres et des granules en comprimés, tandis que dans le domaine des matériaux, elles sont utilisées pour former et tester des polymères, des métaux ou des céramiques.
L’un des principaux avantages des presses de laboratoire est leur capacité à contrôler précisément les paramètres tels que la force appliquée, la température et la durée de l’application de la pression. Cela permet d’obtenir des résultats très spécifiques et de reproduire des conditions expérimentales avec précision. De plus, les presses modernes intègrent souvent des systèmes de contrôle automatisés qui augmentent encore la précision et l’efficacité des processus.
Cependant, il est également important de noter que l’utilisation des presses de laboratoire nécessite une certaine expertise technique. Les utilisateurs doivent être formés non seulement à l’utilisation des appareils, mais aussi à la compréhension des matériaux et des réactions physiques qui peuvent survenir sous pression. De plus, le choix d’une presse doit être fait en fonction des besoins spécifiques de l’expérience, du type de matériau et des conditions de l’environnement de laboratoire.
Cette introduction met en lumière l’importance des presses de laboratoire dans le contexte scientifique et industriel moderne. Dans les sections suivantes, nous examinerons plus en détail les différents types de presses, leurs applications, les avantages et les limites de leur utilisation, ainsi que les innovations récentes dans ce domaine.
Presse hydraulique

Les presses hydrauliques sont sans doute les plus couramment utilisées dans les laboratoires en raison de leur polyvalence et de leur capacité à générer des forces considérables. Elles fonctionnent en utilisant un liquide, généralement de l’huile hydraulique, pour transmettre la force d’un piston à un autre, générant ainsi une pression élevée sur l’échantillon placé dans la presse. L’avantage principal de ces presses est leur capacité à produire une pression constante et uniforme, même pour de grandes charges, ce qui les rend idéales pour la compression de matériaux résistants comme les métaux ou les polymères durs.
Le fonctionnement d’une presse hydraulique repose sur le principe de Pascal, qui stipule que la pression appliquée à un fluide dans un système fermé est transmise uniformément dans toutes les directions. Ce principe permet de générer de grandes forces avec un effort relativement faible, ce qui est particulièrement utile dans les environnements de laboratoire où des pressions très précises sont souvent requises.
Les presses hydrauliques de laboratoire sont souvent équipées de fonctionnalités avancées, telles que des contrôles de température intégrés, qui permettent de chauffer les échantillons pendant la compression. Cela est particulièrement utile pour des expériences nécessitant des conditions de température spécifiques, comme la production de composites thermodurcissables ou la synthèse de nouveaux matériaux. Cependant, malgré leur polyvalence, les presses hydrauliques peuvent être coûteuses et nécessitent un entretien régulier, en particulier au niveau des systèmes de fluide et des joints.
Presse manuelle
Les presses manuelles, bien que souvent perçues comme dépassées dans un monde dominé par l’automatisation, conservent leur utilité dans de nombreux laboratoires. Elles sont particulièrement adaptées aux environnements où les budgets sont limités ou où la simplicité d’utilisation est prioritaire. Ces presses sont actionnées manuellement par une manivelle ou un levier, ce qui permet un contrôle direct de la pression appliquée.
Un des avantages majeurs des presses manuelles est leur portabilité. Contrairement aux presses hydrauliques ou automatiques, qui nécessitent souvent une installation fixe et un entretien plus sophistiqué, les presses manuelles peuvent être utilisées dans une grande variété de contextes expérimentaux. De plus, elles sont moins chères à l’achat et à l’entretien, ce qui en fait une solution idéale pour des laboratoires plus petits ou pour des expériences nécessitant moins de précision.
Cependant, les presses manuelles présentent également certaines limites. Le contrôle de la pression est moins précis que dans les presses automatiques ou hydrauliques, ce qui peut poser problème pour des expériences où la répétabilité est essentielle. En outre, elles sont généralement limitées à des applications de faible force, ce qui les rend moins adaptées à des matériaux durs ou à des expérimentations à grande échelle.
Presse automatique
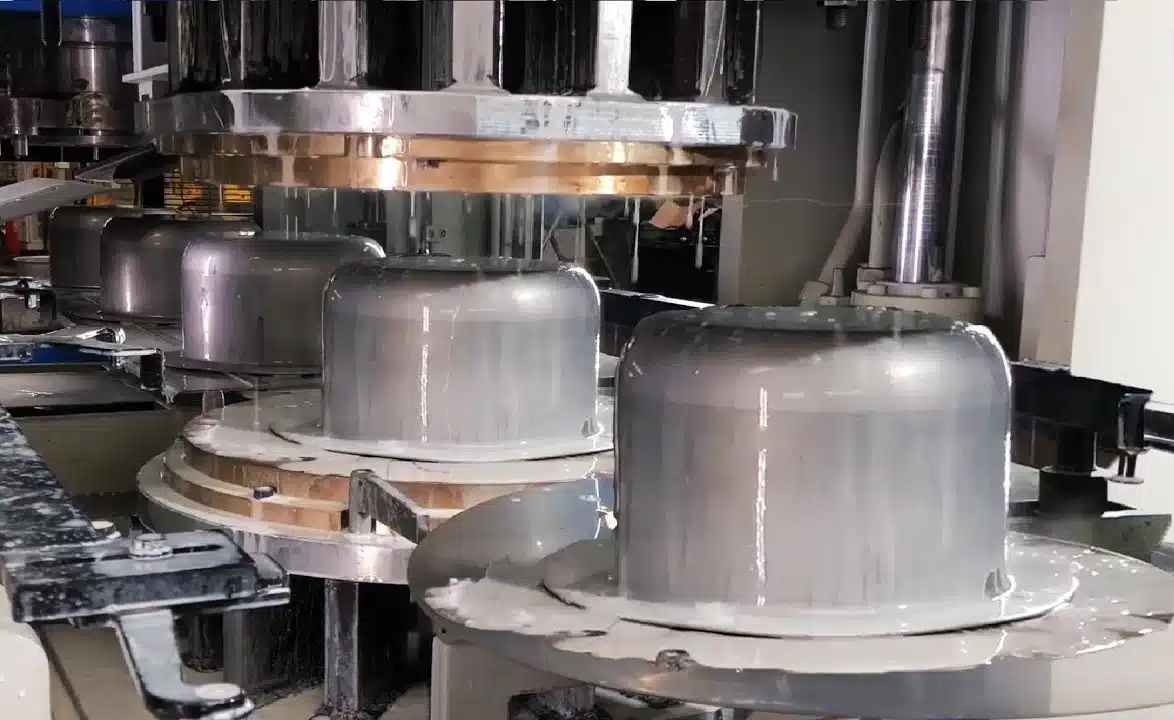
Les presses automatiques de laboratoire représentent une évolution majeure en termes de précision, de rapidité et d’efficacité. Ces machines, contrôlées par des systèmes électroniques et informatiques, permettent d’appliquer une pression prédéterminée de manière répétée et uniforme, sans intervention manuelle. Cela élimine le facteur humain, souvent source de variations et d’erreurs, et garantit une reproductibilité optimale des résultats expérimentaux.
Les presses automatiques sont équipées de capteurs avancés qui surveillent en temps réel la pression, la température, et d’autres paramètres critiques, et qui ajustent automatiquement ces variables selon les spécifications définies. Grâce à ces fonctionnalités, elles sont particulièrement prisées dans des environnements où des essais répétitifs et précis sont nécessaires, comme dans l’industrie pharmaceutique ou la recherche sur les matériaux.
Un autre avantage important de ces presses réside dans la possibilité de programmer des cycles de pressage complexes. Les utilisateurs peuvent définir des étapes multiples, avec des augmentations ou des réductions de pression à des intervalles spécifiques, ce qui permet de simuler des processus de production complexes à petite échelle. Cela est particulièrement utile dans le développement de matériaux composites ou dans la fabrication de dispositifs électroniques où plusieurs couches de matériaux sont pressées successivement.
Toutefois, le coût élevé des presses automatiques, ainsi que la nécessité d’une formation technique pour leur utilisation et leur maintenance, représentent des défis pour certains laboratoires. Malgré cela, les bénéfices en termes de précision et d’automatisation justifient souvent cet investissement, surtout dans les laboratoires à forte cadence ou dans des environnements industriels.
Presse à vide
Les presses à vide se distinguent par leur capacité à effectuer des opérations de pressage dans une chambre dépourvue d’air. Cela est essentiel dans des domaines où la présence d’oxygène ou d’autres gaz pourrait affecter la qualité des résultats ou des matériaux produits. En retirant l’air de la chambre de pressage, ces presses éliminent la possibilité de contamination par l’air ambiant et permettent de travailler avec des matériaux sensibles à l’oxygène, comme certains métaux ou polymères.
L’un des principaux avantages des presses à vide est qu’elles garantissent une homogénéité parfaite dans les matériaux comprimés. Sans poches d’air ou autres impuretés, les produits finaux sont d’une qualité supérieure, tant en termes de densité que de résistance mécanique. Cela est particulièrement crucial dans des domaines comme l’industrie aéronautique, où des composites solides et légers doivent être produits sans défauts internes.
Les presses à vide sont également fréquemment utilisées dans la fabrication de dispositifs électroniques, où même une infime quantité de contaminants peut compromettre les performances d’un circuit ou d’un composant. En éliminant l’air, ces presses assurent que les matériaux conducteurs et isolants sont compressés de manière uniforme et sans interférence externe.
Cependant, l’entretien des presses à vide est plus exigeant que celui des autres types de presses, notamment en raison des systèmes de pompe à vide, qui doivent être maintenus en bon état de fonctionnement. De plus, le coût de ces presses est souvent plus élevé en raison des technologies spécialisées qu’elles intègrent.
Autres types de presses
Outre les presses hydrauliques, manuelles, automatiques et à vide, il existe une multitude d’autres types de presses de laboratoire, chacune étant conçue pour répondre à des besoins spécifiques.
- Presse électrique : Ces presses utilisent l’énergie électrique pour générer la force de compression, ce qui les rend plus écologiques que les presses hydrauliques ou pneumatiques, qui nécessitent des fluides. Elles offrent une bonne précision et sont souvent utilisées dans des applications nécessitant des forces modérées.
- Presse pneumatique : Similaire aux presses hydrauliques, les presses pneumatiques utilisent l’air comprimé comme source de pression. Elles sont légères et faciles à utiliser, mais leur capacité de pression est limitée par rapport aux autres types de presses. Elles sont idéales pour des applications légères où une force modérée suffit.
- Presse chauffante : Ces presses sont équipées de plaques chauffantes, permettant de travailler à des températures élevées. Elles sont utilisées pour les tests sur des matériaux thermoplastiques ou thermodurcissables, où la chaleur est nécessaire pour modifier la structure du matériau sous pression.
Chaque type de presse de laboratoire possède des caractéristiques spécifiques qui le rendent plus adapté à certaines applications que d’autres. Le choix d’une presse dépend des besoins de l’expérience, du type de matériaux utilisés et des conditions expérimentales.
Fonctionnement d’une Presse de Laboratoire
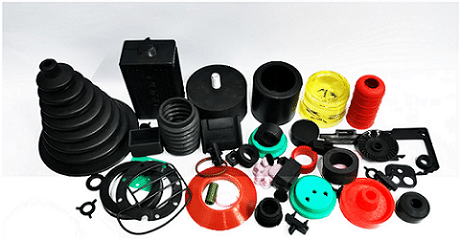
Le fonctionnement d’une presse de laboratoire repose sur des principes mécaniques de base, mais l’intégration de technologies modernes permet d’en améliorer la précision et la fiabilité. Qu’il s’agisse d’une presse hydraulique, manuelle ou automatique, le but est toujours d’appliquer une pression contrôlée sur un échantillon, que ce soit pour le transformer, le tester ou le préparer en vue d’autres analyses.
3.1. Les composants essentiels
Chaque presse de laboratoire est composée de plusieurs composants clés :
- Le bâti : Il s’agit de la structure qui supporte l’ensemble de la presse. Elle doit être suffisamment robuste pour résister à la force exercée sans déformation.
- Le piston ou le vérin : C’est l’élément qui applique directement la force sur l’échantillon. Dans une presse hydraulique, il est actionné par un fluide sous pression, tandis que dans une presse manuelle, il est activé par un levier.
- Le système de pression : Ce système contrôle la quantité de pression appliquée à l’échantillon. Dans les presses modernes, ce système est souvent automatisé et contrôlé par des capteurs qui assurent une pression constante et précise.
- Les plaques de compression : Ce sont les surfaces entre lesquelles l’échantillon est placé. Elles peuvent être chauffées ou refroidies, selon les besoins de l’expérience.
- Le manomètre : Ce dispositif mesure la pression appliquée et permet de l’ajuster en temps réel pour atteindre le niveau souhaité.
3.2. Pression appliquée et maintenue
Le mécanisme d’application de la pression varie selon le type de presse. Dans une presse hydraulique, par exemple, la pression est générée par un fluide sous pression qui pousse un piston contre l’échantillon. Ce fluide, généralement de l’huile, permet une pression stable et constante, et son utilisation garantit également une distribution uniforme de la force sur toute la surface de l’échantillon.
Dans une presse manuelle, la pression est appliquée par l’utilisateur à l’aide d’un levier ou d’une manivelle. Cela offre un contrôle direct mais moins précis, car la force dépend de l’effort exercé par l’utilisateur. Dans les presses automatiques, la pression est générée et contrôlée électroniquement, ce qui permet une plus grande précision et une répétabilité optimale.
Une fois la pression appliquée, elle peut être maintenue pendant une durée déterminée. Cela est crucial pour certaines expériences, où une pression constante doit être maintenue pour observer les effets sur l’échantillon. Dans les presses automatiques, ce maintien de la pression est géré automatiquement par des programmes préétablis, tandis que dans les presses manuelles, cela dépend de la constance de l’opérateur.
3.3. Presses à chaud et à froid
Une distinction importante dans le fonctionnement des presses de laboratoire est la différence entre les presses à chaud et les presses à froid. Chacune de ces configurations offre des avantages spécifiques en fonction des matériaux et des résultats attendus.
- Presses à chaud : Les presses à chaud sont équipées de plaques chauffantes qui permettent de chauffer les matériaux pendant l’application de la pression. Elles sont couramment utilisées pour des matériaux thermoplastiques, qui nécessitent de la chaleur pour se ramollir et se former sous pression. Ces presses sont aussi essentielles pour les tests de polymérisation, où la chaleur et la pression combinées provoquent des réactions chimiques qui modifient la structure du matériau.La température peut atteindre plusieurs centaines de degrés Celsius, selon les besoins de l’expérience. Les presses à chaud permettent ainsi la fabrication de composants composites dans des domaines comme l’aéronautique, l’automobile et la microélectronique, où les matériaux doivent être moulés sous des conditions précises de température et de pression.
- Presses à froid : À l’inverse, les presses à froid n’incluent pas de source de chaleur et sont utilisées pour compresser des matériaux à température ambiante. Elles sont idéales pour les matériaux qui pourraient être dégradés ou endommagés par la chaleur, comme certains produits pharmaceutiques ou des échantillons biologiques. L’application de la pression à froid permet de tester la résistance des matériaux, de former des poudres compactes ou d’extraire des composants sans risque de modifications thermiques.
Les presses à chaud et à froid, bien qu’utilisées dans des contextes très différents, s’inscrivent dans des processus où la précision des paramètres de pression est essentielle.
Applications des Presses de Laboratoire
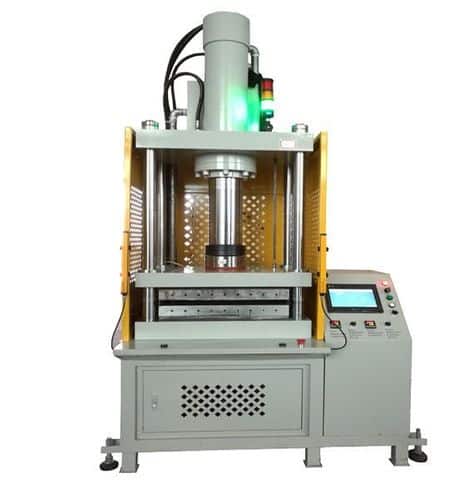
Les presses de laboratoire trouvent des applications dans de nombreux secteurs scientifiques et industriels. Chacune de ces applications tire parti des caractéristiques spécifiques des presses, telles que le contrôle précis de la pression et de la température. Voici un tour d’horizon des principales applications.
4.1. Secteur pharmaceutique
Dans l’industrie pharmaceutique, les presses de laboratoire jouent un rôle essentiel dans la fabrication et l’analyse des formes galéniques solides comme les comprimés.
- Compression des poudres : Les poudres de principes actifs et d’excipients sont comprimées sous une pression élevée pour former des comprimés. Les presses de laboratoire permettent de tester la faisabilité des formulations avant la production à grande échelle. Cela aide à évaluer des paramètres tels que la dureté, la friabilité et la désintégration des comprimés.
- Contrôle qualité : Les presses sont également utilisées dans le contrôle de la qualité des produits finis. La capacité à compresser les échantillons sous des conditions contrôlées permet de tester la stabilité des médicaments et de vérifier la cohérence des lots de production.
- Recherche et développement : Avant la mise sur le marché d’un nouveau médicament, les presses de laboratoire permettent aux scientifiques de tester des prototypes et d’optimiser les formulations. Elles jouent un rôle crucial dans la simulation des processus industriels à petite échelle.
4.2. Recherche sur les matériaux
Les presses de laboratoire sont couramment utilisées pour étudier et former des matériaux dans le domaine de la science des matériaux.
- Polymères : Dans les laboratoires de recherche sur les polymères, les presses sont utilisées pour former des feuilles ou des films à partir de résines polymères sous l’effet de la chaleur et de la pression. Cela permet d’étudier les propriétés mécaniques et thermiques des polymères ainsi que leur comportement sous différentes conditions.
- Métaux et céramiques : La formation de pièces en métal ou en céramique via le pressage est un autre domaine clé. La pression permet de compacter des poudres métalliques ou céramiques pour créer des échantillons solides qui seront ensuite analysés ou sintrés. Les presses à haute température sont essentielles pour cette application.
- Matériaux composites : Dans des secteurs comme l’aéronautique ou l’automobile, les matériaux composites sont pressés à chaud pour combiner plusieurs couches de matériaux aux propriétés différentes. Cela permet de créer des composants légers, résistants et adaptés aux exigences de ces industries.
4.3. Industrie chimique
Dans l’industrie chimique, les presses de laboratoire sont utilisées pour effectuer des tests sur des formulations chimiques complexes.
- Test de stabilité : La compression de substances chimiques permet de simuler des conditions de stress mécanique. Cela est utile pour évaluer la stabilité des formulations sous pression et pour comprendre comment elles réagissent à différents niveaux de compression.
- Pressage de catalyseurs : Les catalyseurs, qui accélèrent les réactions chimiques, sont souvent pressés en pellets pour augmenter leur surface active. Les presses de laboratoire permettent de former ces pellets avec une densité et une structure spécifiques, garantissant ainsi des performances optimales.
4.4. Biotechnologie
Les presses de laboratoire jouent également un rôle dans le domaine des biotechnologies, notamment dans la préparation et l’analyse des échantillons biologiques.
- Préparation d’échantillons biologiques : Pour des analyses telles que la spectroscopie ou la chromatographie, les échantillons doivent parfois être pressés en pastilles. Les presses permettent d’obtenir des échantillons uniformes et denses, prêts à être analysés sous des conditions spécifiques.
- Extraction de substances : Dans certaines applications biotechnologiques, des presses à haute pression sont utilisées pour extraire des substances d’échantillons biologiques, comme des huiles ou des composés actifs à partir de plantes ou d’organismes vivants.
4.5. Applications dans d’autres industries
Les presses de laboratoire trouvent également des applications dans d’autres secteurs industriels.
- Industrie alimentaire : Elles sont utilisées pour la compression des produits alimentaires, par exemple dans l’étude de la texture des aliments ou dans l’extraction d’huiles et de jus.
- Électronique et énergie : Dans la fabrication des dispositifs électroniques, les presses permettent de comprimer des composants miniatures ou de créer des couches minces de matériaux conducteurs ou isolants. Elles sont également utilisées dans le domaine des batteries et des supercondensateurs pour former les électrodes sous pression.
Avantages et Limites des Presses de Laboratoire
5.1. Avantages
Les presses de laboratoire présentent plusieurs avantages significatifs :
- Précision : Les presses modernes permettent de contrôler précisément la pression, la température et la durée, garantissant des résultats fiables et reproductibles.
- Polyvalence : Les presses peuvent être utilisées pour une grande variété de matériaux et d’applications, allant de la formation de matériaux composites à la fabrication de comprimés pharmaceutiques.
- Réduction des déchets : En simulant des processus industriels à petite échelle, les presses de laboratoire permettent de limiter les quantités de matériaux utilisés, réduisant ainsi les coûts et les déchets.
- Amélioration des processus : Elles permettent d’optimiser les processus de fabrication avant la mise en production à grande échelle, en identifiant les conditions optimales de pression et de température.
5.2. Limites
Malgré leurs nombreux avantages, les presses de laboratoire présentent aussi certaines limites :
- Coût : Les presses, en particulier les modèles automatisés ou spécialisés, peuvent être coûteuses, tant à l’achat qu’à l’entretien.
- Complexité : Certaines presses nécessitent une formation spécifique pour être utilisées correctement, en particulier celles dotées de systèmes automatisés ou chauffants.
- Entretien : Les systèmes de pressage, notamment les presses hydrauliques ou à vide, nécessitent un entretien régulier pour garantir leur bon fonctionnement. Des fuites de fluide ou des défaillances dans le système de vide peuvent compromettre la qualité des résultats.
6. Critères de Sélection d’une Presse de Laboratoire
Le choix d’une presse de laboratoire dépend de nombreux critères qui doivent être soigneusement considérés pour répondre aux besoins spécifiques des expériences ou des processus industriels. La sélection appropriée de l’équipement garantit non seulement la précision des résultats, mais aussi la durabilité de l’appareil et la sécurité des opérateurs. Voici les principaux critères à prendre en compte lors du choix d’une presse de laboratoire.
6.1. Plage de force et de pression
La force de compression maximale qu’une presse peut exercer est l’un des premiers éléments à considérer. Cette force, généralement exprimée en tonnes, doit correspondre à la résistance du matériau à traiter et aux exigences de l’application.
- Presses à faible force (généralement moins de 1 tonne) : Idéales pour des applications légères comme la compression de poudres pharmaceutiques ou d’échantillons biologiques fragiles.
- Presses à force moyenne (1 à 10 tonnes) : Utilisées dans les laboratoires pour la compression de matériaux de densité moyenne, tels que les polymères ou les produits chimiques.
- Presses à haute force (plus de 10 tonnes) : Nécessaires pour les matériaux plus durs, comme les métaux ou les céramiques, où une forte pression est indispensable pour assurer une densité uniforme.
Il est essentiel de sélectionner une presse capable de fournir la force appropriée à l’application souhaitée, sans dépasser les limites mécaniques de l’appareil ou du matériau testé.
6.2. Contrôle de la température
Le contrôle de la température est un critère essentiel pour les presses destinées à des applications spécifiques, comme le traitement des matériaux thermoplastiques ou des composites. Il existe deux grandes catégories de presses selon la gestion de la température :
- Presses à température ambiante : Adaptées pour des matériaux qui ne nécessitent pas de traitement thermique, comme certaines poudres pharmaceutiques ou échantillons biologiques.
- Presses chauffantes : Dotées de plaques chauffantes pour des applications où la chaleur est nécessaire pour modifier la structure du matériau, comme dans le moulage de polymères. Les températures peuvent atteindre plusieurs centaines de degrés Celsius.
Certaines presses offrent également un contrôle de la température sur les deux plaques de manière indépendante, ce qui permet des applications où une différence de température entre les deux côtés de l’échantillon est nécessaire. Cette capacité peut s’avérer cruciale dans des procédés complexes de fabrication de matériaux.
6.3. Automatisation et systèmes de contrôle
L’intégration de systèmes automatisés dans une presse de laboratoire est un facteur déterminant pour la précision et la reproductibilité des expériences. Une presse manuelle peut être suffisante pour des expériences simples, mais pour des applications plus complexes nécessitant des cycles de pressage répétitifs ou des changements progressifs de pression et de température, une presse automatique est préférable.
- Presses manuelles : Adaptées pour des expériences où le contrôle direct est suffisant et où le budget est limité. Elles permettent un ajustement manuel de la pression et sont souvent utilisées dans les laboratoires où la simplicité d’utilisation prime.
- Presses automatiques : Équipées de commandes électroniques qui permettent de programmer des cycles complexes. Ces presses permettent de définir des pressions et des températures précises et de les appliquer de manière répétée. Elles intègrent souvent des capteurs pour surveiller et ajuster les paramètres en temps réel, garantissant une plus grande précision.
- Presses semi-automatiques : Offrent un compromis entre les deux, où certains paramètres sont automatisés tandis que d’autres nécessitent une intervention manuelle. Elles sont idéales pour des laboratoires souhaitant combiner flexibilité et précision.
6.4. Compatibilité avec les matériaux
Un autre critère important est la compatibilité de la presse avec les matériaux qui seront traités. Chaque matériau, qu’il s’agisse de métaux, de céramiques, de polymères ou de poudres pharmaceutiques, présente des propriétés physiques et chimiques uniques. Il est crucial de choisir une presse qui peut exercer la pression nécessaire tout en conservant l’intégrité de l’échantillon.
- Matériaux métalliques : Nécessitent souvent une pression plus élevée pour être formés correctement, ainsi que des plaques de compression capables de supporter ces forces sans se déformer.
- Polymères et composites : Ces matériaux peuvent nécessiter des températures spécifiques et des cycles de pression pour être correctement moulés. Les presses chauffantes avec un contrôle précis de la température sont recommandées.
- Poudres pharmaceutiques : La compatibilité avec des matrices de compression spécifiques est essentielle pour garantir la consistance des comprimés sans affecter la biodisponibilité des principes actifs.
6.5. Sécurité et conformité aux normes
Dans tout laboratoire, la sécurité est primordiale, en particulier lorsqu’il s’agit d’équipements capables de générer de fortes pressions et températures. Les presses modernes intègrent généralement des dispositifs de sécurité pour protéger les utilisateurs.
- Capteurs de sécurité : Les presses automatiques peuvent être équipées de capteurs qui arrêtent immédiatement le processus en cas de détection d’une anomalie (par exemple, une surpression ou une surchauffe).
- Verrouillage de sécurité : Certaines presses sont dotées de systèmes de verrouillage empêchant l’ouverture des plaques tant que la pression ou la température n’est pas redescendue à des niveaux sûrs.
Enfin, il est important de vérifier que la presse sélectionnée est conforme aux normes industrielles et aux réglementations locales en matière de sécurité et de qualité, comme les normes ISO ou CE, particulièrement dans des secteurs sensibles comme la pharmacie ou les biotechnologies.
6.6. Maintenance et longévité
La durabilité d’une presse de laboratoire est un aspect à ne pas négliger, surtout pour des équipements coûteux. Une presse bien conçue doit être robuste et capable de résister à des utilisations répétées sans subir de déformations ou de pannes.
- Entretien régulier : Certaines presses, comme les presses hydrauliques, nécessitent un entretien régulier, notamment en ce qui concerne les fluides et les joints. Il est important de choisir un modèle pour lequel l’entretien peut être effectué facilement.
- Garantie et service après-vente : Un autre critère à prendre en compte est la qualité du service après-vente, ainsi que la disponibilité des pièces de rechange et des techniciens pour l’entretien.
Innovations et Développements Récents dans les Presses de Laboratoire
L’industrie des presses de laboratoire, comme beaucoup d’autres secteurs, évolue constamment grâce à l’intégration de nouvelles technologies qui augmentent la précision, l’efficacité et la durabilité de ces équipements. Ces innovations visent à répondre aux exigences croissantes des laboratoires modernes, où la précision et la reproductibilité des résultats sont de plus en plus cruciales. Voici quelques-unes des tendances récentes dans le domaine.
7.1. Intégration de l’Internet des objets (IoT)
Avec l’essor des technologies numériques, les presses de laboratoire peuvent désormais être équipées de capteurs intelligents connectés à des réseaux informatiques. Cela permet un suivi en temps réel des paramètres de pression, de température et de durée via des interfaces numériques.
- Suivi en temps réel : Les opérateurs peuvent surveiller à distance les performances des presses, enregistrer les données pour analyse, et ajuster les paramètres en temps réel. Cela permet d’éviter des erreurs de manipulation et d’assurer un contrôle optimal de l’expérience.
- Maintenance prédictive : Grâce à l’IoT, les presses peuvent signaler des anomalies avant qu’elles ne deviennent des pannes graves, permettant ainsi une maintenance préventive et réduisant les temps d’arrêt imprévus.
7.2. Presses éco-énergétiques
La réduction de l’empreinte énergétique des équipements de laboratoire est devenue une priorité dans de nombreux secteurs. De nouvelles presses sont désormais conçues pour consommer moins d’énergie tout en maintenant leur efficacité.
- Systèmes de récupération d’énergie : Certaines presses modernes récupèrent l’énergie produite lors des cycles de pressage et la réutilisent pour d’autres phases du processus, réduisant ainsi la consommation énergétique globale.
- Matériaux durables : L’utilisation de matériaux plus légers et plus résistants dans la construction des presses contribue également à améliorer l’efficacité énergétique en réduisant les pertes thermiques.
7.3. Presses intelligentes et automatisées
Les progrès dans l’automatisation ont permis de créer des presses capables de gérer des processus de plus en plus complexes sans intervention humaine.
- Programmation avancée : Les presses intelligentes peuvent être programmées pour exécuter des cycles multiples de pression et de température, ajustant les paramètres selon les besoins spécifiques de chaque étape du processus.
- Apprentissage automatique : L’intégration de l’intelligence artificielle dans certaines presses permet d’optimiser les paramètres de pressage en fonction des données collectées lors des expériences précédentes, améliorant ainsi la précision et réduisant les erreurs humaines.
7.4. Évolution des matériaux de presse
Les matériaux utilisés dans la fabrication des presses, notamment pour les plaques de compression, ont également évolué.
- Matériaux composites : Certains fabricants intègrent des matériaux composites plus légers et plus résistants pour réduire le poids des presses tout en augmentant leur durabilité. Cela permet d’améliorer la longévité de l’équipement et de réduire la nécessité d’entretien.
- Plaques de compression en céramique : Les plaques de compression en céramique, plus résistantes aux températures élevées et à l’usure, sont désormais plus couramment utilisées, notamment pour les applications nécessitant des conditions extrêmes de chaleur.
7.5. Interfaces utilisateurs améliorées
L’expérience utilisateur a également été améliorée grâce à des interfaces plus intuitives et des systèmes de commande avancés.
- Écrans tactiles : De nombreuses presses automatiques modernes sont équipées d’écrans tactiles intuitifs qui permettent de configurer rapidement et facilement les paramètres, même pour les utilisateurs non spécialisés.
- Enregistrement et analyse des données : Les presses peuvent désormais enregistrer toutes les données de pressage, ce qui permet une analyse détaillée post-expérimentation et une traçabilité complète des résultats.
8. Utilisation et Entretien des Presses de Laboratoire
L’utilisation et l’entretien des presses de laboratoire sont essentiels pour garantir leur bon fonctionnement à long terme, leur sécurité, ainsi que la précision des expériences ou des processus de production. Une mauvaise manipulation ou un entretien insuffisant peut entraîner des pannes, des résultats expérimentaux erronés, ou des risques pour les opérateurs. Cette section propose un guide pratique sur les meilleures pratiques d’utilisation, les stratégies de maintenance préventive et les mesures de sécurité à suivre dans un environnement de laboratoire.
8.1. Bonnes pratiques d’utilisation des presses de laboratoire
8.1.1. Formation des opérateurs
Il est primordial que les opérateurs de presses de laboratoire aient reçu une formation adéquate. Même les presses les plus simples, comme les presses manuelles, peuvent présenter des risques si elles ne sont pas correctement utilisées. La formation doit couvrir les aspects suivants :
- Manipulation des commandes : Les opérateurs doivent savoir comment configurer la presse pour les cycles spécifiques, y compris l’ajustement de la pression, de la température (pour les presses chauffantes) et de la durée.
- Réglage des paramètres : Comprendre comment calibrer la presse pour chaque type d’échantillon et ajuster les variables en fonction des besoins expérimentaux.
- Inspection préliminaire : Savoir inspecter la presse avant chaque utilisation pour s’assurer qu’elle fonctionne correctement (vérification des plaques, du manomètre, des composants électriques ou hydrauliques).
8.1.2. Préparation des échantillons
Une partie cruciale de l’utilisation efficace d’une presse de laboratoire réside dans la préparation correcte des échantillons. Les échantillons doivent être soigneusement préparés pour assurer une répartition uniforme de la pression. Voici quelques conseils pratiques :
- Uniformité de l’échantillon : Les échantillons doivent être découpés ou moulés de manière à avoir une épaisseur et une forme homogènes. Cela garantit une distribution uniforme de la pression lors du pressage.
- Placement correct : L’échantillon doit être placé exactement au centre des plaques de la presse pour éviter les pressions inégales qui pourraient endommager l’échantillon ou la presse.
- Utilisation de matrices : Lorsque cela est nécessaire, utiliser des matrices spécifiques adaptées à l’échantillon et à l’application. Par exemple, les matrices en acier inoxydable sont souvent utilisées pour les échantillons de poudres pharmaceutiques.
8.1.3. Utilisation des fonctionnalités avancées
Les presses de laboratoire modernes offrent une variété de fonctionnalités avancées pour optimiser les résultats, en particulier les modèles automatiques et semi-automatiques :
- Programmer des cycles complexes : Les utilisateurs peuvent créer des séquences de pressage spécifiques, ajustant la pression ou la température à plusieurs étapes pour simuler des processus de fabrication industriels.
- Monitoring en temps réel : Les presses équipées de capteurs et d’écrans de contrôle permettent une surveillance en direct des variables expérimentales. Les données collectées peuvent être utilisées pour ajuster le processus en temps réel et garantir une pression constante.
8.1.4. Considérations de sécurité
Les presses de laboratoire exercent des pressions considérables, et la sécurité doit être une priorité pour éviter tout accident :
- Équipement de protection individuelle (EPI) : Les opérateurs doivent porter des gants, des lunettes de protection et des vêtements appropriés pour éviter tout risque de blessure en cas de défaillance de la presse.
- Dispositifs de verrouillage : Utiliser les dispositifs de verrouillage de sécurité présents sur les presses automatiques ou hydrauliques pour empêcher toute ouverture prématurée des plaques sous pression.
- Signalisation des dangers : Les zones autour des presses doivent être bien signalées, et l’accès restreint aux personnes non autorisées pour éviter tout accident.
8.2. Maintenance et entretien des presses de laboratoire
La maintenance régulière des presses de laboratoire est indispensable pour prolonger leur durée de vie et garantir leur bon fonctionnement. L’entretien préventif permet également de détecter les anomalies avant qu’elles ne provoquent des pannes coûteuses.
8.2.1. Maintenance préventive régulière
Certaines tâches de maintenance doivent être effectuées régulièrement, que la presse soit utilisée fréquemment ou non. Voici les principaux aspects à surveiller :
- Inspection des joints et des systèmes hydrauliques : Pour les presses hydrauliques, vérifier régulièrement l’état des joints et des tuyaux. Les fuites d’huile peuvent affecter les performances de la presse et provoquer une baisse de pression.
- Lubrification des composants mécaniques : Les parties mobiles de la presse, telles que le piston ou les charnières, doivent être lubrifiées selon les recommandations du fabricant pour réduire l’usure due à la friction.
- Nettoyage des plaques : Les plaques de compression doivent être nettoyées après chaque utilisation pour éviter l’accumulation de résidus qui pourraient compromettre la qualité des pressions futures.
8.2.2. Calibrage régulier
Le calibrage des instruments de mesure (pression, température) de la presse est essentiel pour garantir l’exactitude des résultats. Un mauvais calibrage peut entraîner des erreurs significatives dans les expériences.
- Manomètres : Les manomètres doivent être calibrés régulièrement pour s’assurer qu’ils indiquent la bonne pression. Un manomètre défectueux peut fausser les résultats.
- Capteurs de température : Les presses chauffantes doivent être équipées de capteurs de température fiables, calibrés pour garantir une régulation thermique précise.
8.2.3. Remplacement des pièces usées
Les composants de la presse s’usent avec le temps, en particulier si la presse est utilisée fréquemment ou dans des conditions exigeantes (hautes températures, forte pression).
- Plaques de compression : Si elles sont trop usées ou déformées, les plaques de compression peuvent entraîner des pressions inégales, affectant la qualité des échantillons. Les plaques doivent être remplacées dès qu’elles montrent des signes d’usure.
- Pompes hydrauliques : Pour les presses hydrauliques, les pompes doivent être entretenues et, si nécessaire, remplacées en cas de baisse de performance.
8.2.4. Consignes spécifiques des fabricants
Il est essentiel de suivre les recommandations spécifiques du fabricant de la presse pour l’entretien et le remplacement des pièces. Les manuels d’entretien fournis par les fabricants doivent être respectés pour assurer la sécurité et la longévité de l’équipement.
8.3. Dépannage des problèmes courants
Même avec une maintenance préventive rigoureuse, certaines pannes peuvent survenir. Voici une liste des problèmes courants rencontrés avec les presses de laboratoire et leurs solutions possibles :
- Perte de pression : Cela peut être dû à une fuite dans le système hydraulique ou à une défaillance du manomètre. Vérifier les tuyaux, les joints et calibrer le manomètre.
- Chauffage insuffisant : Dans les presses chauffantes, un problème de chauffage peut être lié à une défaillance des éléments chauffants ou des capteurs. Vérifier l’état des éléments et recalibrer les capteurs si nécessaire.
- Usure des plaques : Si les plaques montrent des signes d’usure prématurée, il peut s’agir d’un problème de lubrification ou d’une mauvaise répartition de la pression. Veiller à ce que les échantillons soient correctement placés et que les pièces mobiles soient bien lubrifiées.
8.4. Gestion des risques et régulations
L’utilisation de presses dans des environnements de laboratoire implique le respect de normes de sécurité et de réglementation. Selon le secteur, il peut être nécessaire de se conformer à des règles spécifiques, notamment dans les domaines pharmaceutiques ou chimiques.
- Normes de sécurité : Respecter les réglementations locales ou internationales, comme les directives de l’OSHA (Occupational Safety and Health Administration) ou les normes ISO, pour garantir un environnement de travail sûr.
- Formation continue : Mettre en place des formations continues pour les opérateurs, surtout lorsqu’il s’agit de presses complexes ou de nouvelles technologies.
- Audit et contrôle qualité : Effectuer régulièrement des audits de sécurité et des contrôles de qualité sur les presses pour s’assurer qu’elles fonctionnent conformément aux normes et aux spécifications.
Études de Cas et Exemples Pratiques
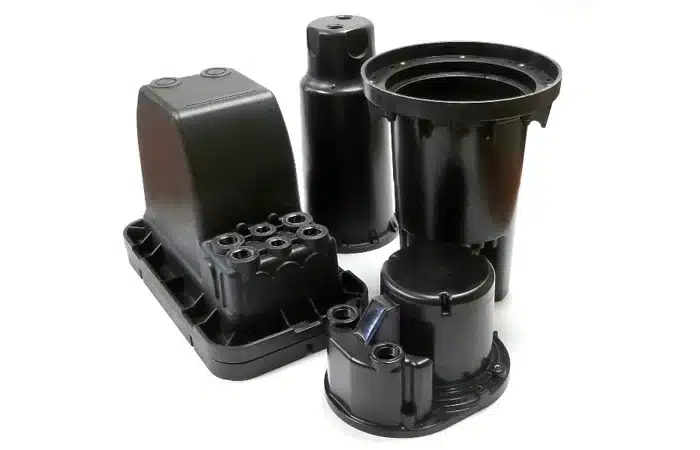
L’utilisation des presses de laboratoire peut être illustrée par des exemples concrets issus de différents secteurs. Ces études de cas montrent comment ces appareils ont été utilisés avec succès pour répondre à des défis spécifiques, que ce soit dans le domaine pharmaceutique, industriel, ou de la recherche sur les matériaux.
9.1. Fabrication de comprimés pharmaceutiques
Dans un laboratoire pharmaceutique, une presse hydraulique a été utilisée pour développer un nouveau comprimé à libération prolongée. Le défi consistait à comprimer une combinaison de principes actifs et d’excipients, tout en garantissant une libération contrôlée du médicament sur une période de 12 heures.
- Problème : La composition chimique des ingrédients rendait difficile la compression à température ambiante, car elle entraînait une désintégration prématurée du comprimé.
- Solution : En utilisant une presse chauffante, les chercheurs ont pu augmenter la température des plaques, ce qui a permis de stabiliser les composants pendant la compression. Le résultat a été une formulation qui répondait aux normes de libération prolongée et offrait une meilleure bio-disponibilité du médicament.
9.2. Test de résistance des matériaux dans l’aéronautique
Un fabricant de matériaux composites pour l’industrie aéronautique a utilisé des presses automatiques pour tester la résistance mécanique de nouveaux matériaux composites destinés à des structures d’avions.
- Problème : Les composites testés devaient résister à des conditions de pression et de température extrêmes, simulant les contraintes rencontrées en vol.
- Solution : La presse automatique a été programmée pour appliquer une pression croissante jusqu’à la rupture du matériau. Les résultats ont permis d’identifier les meilleures combinaisons de fibres et de matrices pour produire des matériaux légers et résistants.
9.3. Production de plaques de polymères dans l’industrie électronique
Dans un laboratoire de recherche en électronique, une presse à vide a été utilisée pour fabriquer des plaques de polymère à haute densité, utilisées comme isolants dans les circuits imprimés.
- Problème : La présence d’impuretés et de bulles d’air dans les plaques de polymère affectait leurs propriétés isolantes, entraînant des pannes dans les circuits.
- Solution : La presse à vide a permis d’éliminer l’air et les contaminants pendant le pressage, garantissant ainsi une production homogène de plaques avec des propriétés isolantes optimales.
10. Conclusion
Les presses de laboratoire occupent une place essentielle dans de nombreux domaines scientifiques et industriels, notamment dans la recherche sur les matériaux, l’industrie pharmaceutique, la chimie, et les biotechnologies. Leur capacité à appliquer des forces précises et contrôlées permet d’effectuer des tests critiques, de former des matériaux, ou de fabriquer des produits à petite échelle, avant une mise en production industrielle. Ces équipements, bien que souvent complexes, garantissent des résultats fiables et reproductibles, qui sont fondamentaux pour le développement de nouvelles technologies et de nouvelles formulations.
Les différents types de presses, allant des modèles hydrauliques aux presses automatiques et manuelles, permettent de répondre à des besoins spécifiques en fonction du type de matériau ou de l’expérience à mener. Les presses à vide, à chaud ou encore les presses spécialisées comme les modèles pneumatiques ou électriques, apportent des solutions variées et adaptées à des environnements de laboratoire où la précision est une priorité absolue.
En outre, le choix d’une presse de laboratoire doit tenir compte de plusieurs critères tels que la plage de pression, la température de fonctionnement, le degré d’automatisation et la compatibilité avec les matériaux utilisés. L’émergence des technologies intelligentes, comme l’intégration de l’Internet des objets (IoT) et les systèmes d’automatisation avancés, ouvre de nouvelles possibilités pour optimiser les processus de pressage et améliorer la reproductibilité des expériences.
Cependant, bien que ces machines offrent des avantages considérables, leur entretien régulier et une utilisation sécurisée sont des aspects cruciaux à ne pas négliger. Un entretien préventif adéquat, combiné à un calibrage régulier des capteurs de pression et de température, est indispensable pour prolonger la durée de vie des presses et garantir leur bon fonctionnement. En parallèle, la sécurité des opérateurs doit être assurée par le respect des consignes d’utilisation et des dispositifs de sécurité présents sur les appareils.
Les études de cas présentées montrent comment les presses de laboratoire jouent un rôle stratégique dans des secteurs variés, que ce soit pour améliorer la fabrication de médicaments, optimiser les matériaux destinés à l’industrie aéronautique, ou encore garantir la qualité des composants électroniques. Ces exemples concrets illustrent l’importance de ces équipements dans le développement de technologies et de produits innovants.
Enfin, les développements technologiques récents ouvrent des perspectives prometteuses. Avec l’essor des presses intelligentes et éco-énergétiques, les laboratoires pourront continuer à repousser les limites de l’innovation tout en optimisant leurs processus de production. La flexibilité et la précision des presses de laboratoire en font des outils indispensables dans un monde où la recherche et le développement sont en constante évolution.
Résumé des points clés :
- Les presses de laboratoire sont essentielles dans des secteurs variés, de la recherche scientifique à la production industrielle.
- Les différents types de presses, y compris hydrauliques, manuelles, automatiques, et à vide, offrent des solutions adaptées à des besoins spécifiques.
- Le choix d’une presse dépend de plusieurs critères comme la force de compression, la température de fonctionnement et le degré d’automatisation.
- L’entretien régulier et la sécurité sont indispensables pour assurer la longévité et l’efficacité des presses.
- Les innovations récentes, comme l’intégration de l’IoT et des presses éco-énergétiques, apportent de nouvelles opportunités d’optimisation des processus expérimentaux.
Fonctionnement d’une Presse de Laboratoire
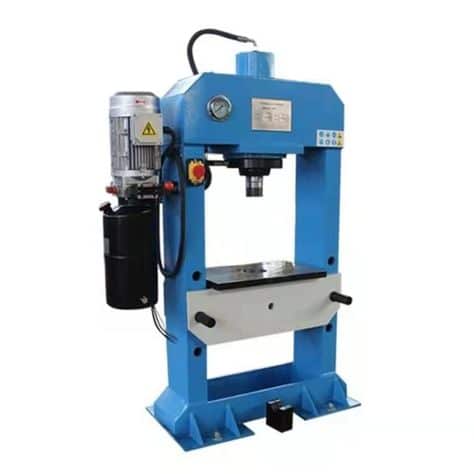
Le fonctionnement d’une presse de laboratoire repose sur des principes mécaniques qui permettent d’exercer une pression contrôlée sur un échantillon. Ces appareils sont conçus pour effectuer des tâches telles que la compression, le formage, ou la fabrication de matériaux à petite échelle, ainsi que la préparation d’échantillons pour des analyses. Le mécanisme de chaque type de presse, qu’il soit hydraulique, manuel, automatique ou à vide, varie en fonction des besoins spécifiques de l’expérience, mais les bases restent similaires.
Voici les éléments clés qui composent le fonctionnement d’une presse de laboratoire, ainsi que les processus associés à son utilisation.
3.1. Composants essentiels d’une presse de laboratoire
Une presse de laboratoire se compose de plusieurs éléments principaux qui fonctionnent ensemble pour appliquer une pression uniforme sur un échantillon. Chaque composant joue un rôle déterminant dans la performance et la précision de l’appareil.
- Le bâti (ou châssis) : Il s’agit de la structure principale de la presse, souvent en acier robuste, qui maintient l’intégrité de l’appareil sous pression. Le bâti doit être capable de supporter les forces générées sans se déformer.
- Les plaques de compression : Ce sont les surfaces entre lesquelles l’échantillon est placé. Elles peuvent être fixes ou mobiles, et dans certaines presses, elles peuvent être chauffées ou refroidies selon les besoins de l’expérience. Ces plaques transmettent directement la force de compression à l’échantillon.
- Le piston ou vérin : Dans une presse hydraulique, un piston, actionné par un fluide sous pression, pousse contre l’échantillon. C’est le composant qui applique la force mécanique nécessaire au processus de compression.
- Le système de pression : Ce système permet de réguler la pression exercée sur l’échantillon. Dans les presses manuelles, la pression est contrôlée par l’utilisateur via un levier ou une manivelle, tandis que dans les presses hydrauliques ou automatiques, un fluide (comme l’huile) ou un moteur applique la pression de manière plus précise.
- Les capteurs et manomètres : Ces instruments mesurent la pression appliquée en temps réel. Dans les presses automatiques, ils sont souvent reliés à un système de contrôle qui ajuste la pression pour correspondre exactement aux paramètres définis par l’utilisateur.
- Systèmes de chauffage (pour les presses chauffantes) : Les presses chauffantes disposent de plaques de compression chauffées qui permettent d’appliquer une chaleur simultanée à la pression. Cela est utile pour les matériaux qui nécessitent une chaleur pour être déformés ou pour les polymérisations.
3.2. Étapes de fonctionnement d’une presse de laboratoire
Le processus d’utilisation d’une presse de laboratoire peut varier légèrement en fonction du type d’appareil, mais voici les étapes générales suivies lors d’un cycle de pressage.
Étape 1 : Préparation de l’échantillon
La première étape consiste à préparer l’échantillon à compresser. L’échantillon doit être propre, sec et de taille uniforme pour garantir une distribution homogène de la pression. Des matrices peuvent être utilisées pour contenir les poudres ou pour donner une forme spécifique aux échantillons.
Étape 2 : Placement dans la presse
L’échantillon est placé entre les plaques de compression. Il est essentiel de s’assurer que l’échantillon est bien centré, car une mauvaise position peut entraîner une répartition inégale de la pression, ce qui pourrait fausser les résultats ou endommager l’échantillon.
Étape 3 : Application de la pression
Une fois l’échantillon en place, la presse est activée pour appliquer la pression. Le système de pression varie selon le type de presse :
- Presses hydrauliques : Dans ces presses, l’huile hydraulique est pompée pour pousser un piston contre l’échantillon, générant ainsi une pression contrôlée. Cette méthode permet d’appliquer des pressions très élevées de manière stable et continue.
- Presses manuelles : Ici, la pression est générée par un levier ou une manivelle, ce qui permet un contrôle manuel direct. La pression est ajustée par l’utilisateur en fonction des besoins spécifiques de l’expérience.
- Presses automatiques : La pression est générée et contrôlée par un moteur ou un système électronique. L’utilisateur programme la presse pour appliquer une pression précise pendant une durée déterminée, souvent en plusieurs étapes, avec des augmentations ou des relâchements progressifs de la force.
Étape 4 : Maintien de la pression
Une fois que la pression souhaitée est atteinte, elle est maintenue pendant un temps prédéfini. Cette phase est cruciale dans de nombreuses expériences, en particulier celles impliquant des réactions chimiques ou des modifications structurales sous pression. La presse garde les paramètres stables pendant cette période, ce qui permet d’obtenir des résultats reproductibles.
Étape 5 : Relâchement de la pression
Après le maintien de la pression pendant la durée souhaitée, celle-ci est lentement relâchée pour éviter d’endommager l’échantillon. Dans les presses hydrauliques ou automatiques, cette étape est généralement programmée pour se dérouler de manière contrôlée, tandis que dans les presses manuelles, elle est réalisée progressivement par l’opérateur.
Étape 6 : Retrait de l’échantillon
Une fois la pression relâchée, les plaques de compression s’écartent et l’échantillon peut être retiré de la presse. Il est ensuite inspecté pour vérifier si les propriétés souhaitées (densité, forme, réaction chimique) ont été atteintes.
3.3. Presses à chaud et à froid
Les presses de laboratoire peuvent être classées en deux grandes catégories selon qu’elles appliquent ou non de la chaleur en plus de la pression :
- Presses à chaud : Ces presses sont équipées de plaques chauffantes qui permettent de chauffer les matériaux pendant la compression. Elles sont couramment utilisées pour les polymères et autres matériaux thermoplastiques, qui nécessitent de la chaleur pour se ramollir et se transformer sous pression. Les températures peuvent être contrôlées avec précision, atteignant parfois plusieurs centaines de degrés Celsius.
- Presses à froid : Dans ces presses, seule la pression est appliquée à température ambiante. Elles sont utilisées pour les matériaux qui pourraient être endommagés par la chaleur ou qui n’en nécessitent pas, comme certains produits pharmaceutiques ou échantillons biologiques.
3.4. Contrôle de la pression et de la température
Le contrôle des paramètres dans une presse de laboratoire est crucial pour la précision des expériences. Voici les principaux paramètres qui doivent être surveillés et contrôlés :
- Pression : La plupart des presses modernes sont équipées de capteurs de pression qui mesurent en temps réel la force exercée. La pression doit être ajustée pour correspondre aux propriétés spécifiques de l’échantillon. Par exemple, les matériaux durs nécessitent des pressions élevées, tandis que les échantillons fragiles ou en poudre nécessitent des pressions plus douces.
- Température : Dans les presses chauffantes, la température est un facteur clé. La capacité à ajuster et à maintenir une température stable est essentielle pour les processus comme la polymérisation ou le formage de composites. Les capteurs de température doivent être régulièrement calibrés pour garantir leur exactitude.
3.5. Cycles de pressage programmables
Dans les presses automatiques, un des grands avantages est la possibilité de programmer des cycles de pressage complexes. Ces cycles permettent de contrôler précisément :
- La montée en pression : Le taux auquel la pression augmente peut être contrôlé pour éviter des chocs trop brutaux à l’échantillon.
- Le maintien de la pression : Une fois la pression maximale atteinte, elle peut être maintenue pour une durée précise, indispensable dans certaines réactions chimiques.
- La libération progressive de la pression : Un relâchement trop rapide de la pression peut endommager l’échantillon. Les presses automatiques permettent de programmer un relâchement progressif, évitant ainsi des dégradations.
3.6. Sécurité dans le fonctionnement d’une presse
L’utilisation de presses de laboratoire implique de respecter des mesures de sécurité rigoureuses pour éviter les accidents. Les presses modernes sont équipées de dispositifs de sécurité tels que :
- Capteurs de surcharge : Ces capteurs arrêtent automatiquement la machine en cas de pression excessive qui pourrait entraîner un dysfonctionnement ou un accident.
- Systèmes de verrouillage : Ils empêchent l’ouverture des plaques tant que la pression ou la température n’est pas revenue à des niveaux sûrs, protégeant ainsi l’utilisateur.
- Arrêts d’urgence : Les presses sont souvent équipées de boutons d’arrêt d’urgence pour permettre un arrêt immédiat en cas de problème.
Préparation de l’échantillon pour une presse de laboratoire
La préparation adéquate de l’échantillon avant son passage dans une presse de laboratoire est une étape cruciale pour garantir des résultats fiables, reproductibles et conformes aux objectifs de l’expérience. Une mauvaise préparation peut non seulement fausser les résultats, mais aussi endommager la presse ou l’échantillon lui-même. Voici un guide détaillé sur les aspects essentiels à prendre en compte pour la préparation d’un échantillon avant l’utilisation d’une presse de laboratoire.
1. Nature de l’échantillon
La première étape dans la préparation de l’échantillon est de bien comprendre ses caractéristiques physiques et chimiques, car ces propriétés détermineront la manière dont il doit être manipulé et pressé.
- Solide : Les échantillons solides (comme les poudres, les granulés, ou les matériaux compacts) nécessitent généralement une compression pour évaluer leur résistance ou pour les transformer en une forme plus dense, comme des comprimés ou des pastilles.
- Liquide ou semi-liquide : Pour les échantillons liquides ou visqueux, une préparation particulière est nécessaire pour les contenir dans un moule ou une matrice avant compression. Ils peuvent aussi nécessiter une température contrôlée pour être pressés correctement.
- Matériaux sensibles à la chaleur : Certains échantillons peuvent être sensibles à la chaleur, ce qui rend essentiel le choix d’une presse à froid. Si une chaleur est nécessaire, il est important de déterminer la température maximale que l’échantillon peut supporter sans se dégrader.
- Matériaux réactifs : Pour les matériaux qui réagissent facilement avec l’air ou d’autres substances, comme les métaux sensibles à l’oxygène, il peut être nécessaire d’utiliser une presse à vide pour empêcher l’oxydation ou d’autres réactions indésirables.
2. Taille et forme de l’échantillon
La taille et la forme de l’échantillon doivent être standardisées autant que possible pour garantir des résultats uniformes. Il est recommandé de découper ou de préparer les échantillons de manière homogène, en tenant compte des dimensions de la presse et des matrices utilisées.
- Épaisseur uniforme : L’échantillon doit avoir une épaisseur uniforme sur toute sa surface pour garantir que la pression appliquée soit répartie de manière homogène. Un échantillon trop épais ou irrégulier pourrait entraîner une déformation ou une pression inégale, compromettant ainsi la qualité du pressage.
- Taille appropriée : L’échantillon ne doit pas dépasser les dimensions des plaques de compression ou des matrices. Un échantillon trop grand pourrait entraîner une distribution inégale de la pression ou endommager la presse.
3. Utilisation de matrices et moules
Dans de nombreux cas, les matrices ou les moules sont utilisés pour guider la forme et la taille de l’échantillon pendant le pressage. Ces outils permettent de compacter des poudres ou des granulés dans une forme définie, comme des comprimés, des disques ou des pastilles.
- Matrice en acier inoxydable : Les matrices en acier inoxydable sont couramment utilisées pour les poudres pharmaceutiques et chimiques. Elles permettent d’obtenir des comprimés de haute densité et de formes uniformes.
- Moules spécifiques : Pour certaines expériences, il peut être nécessaire d’utiliser des moules personnalisés, en fonction des exigences de l’expérience, par exemple pour créer des échantillons cylindriques, cubiques ou de formes complexes.
- Compatibilité des matériaux : Il est crucial de s’assurer que le matériau de la matrice ne réagit pas chimiquement avec l’échantillon. Par exemple, dans le cas de substances corrosives, il peut être nécessaire d’utiliser des matrices en céramique ou en plastique résistant à la corrosion.
4. Conditions spécifiques de l’échantillon
Il est également essentiel de vérifier que l’échantillon est dans des conditions optimales avant d’être placé dans la presse.
- Sec ou humide : Les échantillons doivent être secs, à moins que l’expérience ne nécessite un pressage d’échantillons humides ou visqueux. Un échantillon humide pourrait modifier la densité finale obtenue et provoquer des effets indésirables lors de la compression.
- Nettoyage préalable : L’échantillon doit être exempt de toute impureté ou particule étrangère qui pourrait altérer les résultats de l’expérience ou endommager les plaques de la presse.
- Homogénéité : Dans le cas des poudres, il est recommandé de s’assurer que l’échantillon est bien homogène avant le pressage, en le mélangeant soigneusement pour éviter toute ségrégation des composants.
5. Placement de l’échantillon dans la presse
Le placement correct de l’échantillon entre les plaques de la presse est essentiel pour garantir une application uniforme de la pression. Voici quelques étapes à suivre pour un placement optimal :
- Centrage de l’échantillon : L’échantillon doit être placé exactement au centre des plaques de compression ou de la matrice. Un mauvais centrage peut entraîner une distribution inégale de la pression, ce qui peut endommager l’échantillon ou la presse elle-même.
- Utilisation de films de protection : Dans certaines situations, l’utilisation de films protecteurs (en plastique ou en aluminium, par exemple) entre les plaques de compression et l’échantillon peut être nécessaire pour éviter que l’échantillon n’adhère aux plaques, ou pour le protéger de toute contamination.
- Ajustement de la pression initiale : Avant d’appliquer la pleine pression, il est recommandé de commencer par une pression légère pour s’assurer que l’échantillon est bien positionné et stable. Cela permet également de vérifier que les plaques sont correctement alignées avant de procéder à l’application de la pression maximale.
6. Considérations de sécurité
La préparation de l’échantillon doit toujours se faire en respectant des règles de sécurité strictes, surtout lorsque des matériaux potentiellement dangereux sont manipulés ou lorsque la presse génère des forces importantes.
- Port de protections : Il est recommandé de porter des gants de protection, des lunettes et des vêtements de laboratoire pour manipuler l’échantillon, surtout lorsqu’il s’agit de matériaux corrosifs, réactifs ou de haute densité.
- Matériaux inflammables ou explosifs : Certains matériaux peuvent présenter des risques lors du pressage sous haute pression, notamment les matériaux inflammables ou explosifs. Il est important de vérifier que les caractéristiques de l’échantillon ne présentent aucun risque sous pression et que des mesures de sécurité supplémentaires sont prises.
Résumé de la préparation d’un échantillon pour une presse de laboratoire :
- Comprendre la nature de l’échantillon : S’assurer que les propriétés physiques et chimiques de l’échantillon sont compatibles avec le processus de pressage.
- Préparer l’échantillon de manière uniforme : Couper ou former l’échantillon avec des dimensions standardisées pour une pression homogène.
- Utiliser des matrices ou moules adaptés : Employer des outils appropriés pour garantir la forme et la taille de l’échantillon.
- Placer correctement l’échantillon dans la presse : Centrer l’échantillon sur les plaques et vérifier son alignement avant d’appliquer la pleine pression.
- Suivre des consignes de sécurité strictes : Porter un équipement de protection et respecter les protocoles pour garantir la sécurité lors de la manipulation et du pressage des échantillons.
Placement de l’échantillon dans la presse
Le placement correct de l’échantillon dans une presse de laboratoire est une étape cruciale qui influence directement la qualité et la fiabilité des résultats. Un mauvais positionnement peut entraîner une répartition inégale de la pression, faussant ainsi les données expérimentales ou endommageant l’échantillon, voire la presse elle-même. Suivre des protocoles précis permet d’assurer un fonctionnement optimal de la presse et de garantir la sécurité des opérateurs. Voici les étapes et considérations clés pour un placement adéquat de l’échantillon dans une presse de laboratoire.
1. Centrage de l’échantillon
La première règle à respecter lors du placement d’un échantillon est de s’assurer qu’il est bien centré entre les plaques de compression de la presse. Ce centrage est essentiel pour garantir que la pression appliquée soit répartie de manière uniforme sur toute la surface de l’échantillon.
- Répartition égale de la pression : Un échantillon mal centré peut subir une pression inégale, ce qui peut entraîner une compression irrégulière, des déformations de l’échantillon, ou même la défaillance de l’expérience.
- Stabilité du processus : Un bon centrage permet également de maintenir la stabilité de la presse pendant l’application de la pression, minimisant les risques de dérapage ou d’endommagement des composants de la presse.
- Plaques d’alignement : Certaines presses de laboratoire sont équipées de plaques d’alignement qui facilitent le centrage automatique de l’échantillon. Cela peut s’avérer utile pour des échantillons complexes ou des expériences répétitives nécessitant un haut degré de précision.
2. Surface de contact optimale
La surface de contact entre l’échantillon et les plaques de compression doit être aussi uniforme que possible pour éviter des points de pression inégaux.
- Surface plane : Assurez-vous que l’échantillon présente des surfaces planes sur les zones qui entreront en contact avec les plaques. Si l’échantillon est irrégulier ou présente des aspérités, il est recommandé de le lisser ou de l’ajuster avant le pressage.
- Utilisation de films protecteurs : Dans certains cas, il est nécessaire d’interposer un film protecteur entre les plaques de la presse et l’échantillon. Cela peut éviter des contaminations croisées ou empêcher que l’échantillon ne colle aux plaques, surtout lorsqu’on travaille avec des poudres, des matériaux collants ou des produits chimiques sensibles.
- Adaptation de la taille des plaques : Si l’échantillon est de petite taille par rapport à la surface des plaques de compression, il peut être nécessaire d’utiliser des inserts ou des entretoises pour garantir que la pression est appliquée uniformément sur l’échantillon et non sur les zones vides autour de celui-ci.
3. Alignement des matrices et moules
Dans de nombreuses applications, les échantillons sont placés dans des matrices ou des moules qui leur donnent une forme spécifique pendant le pressage (par exemple, pour la fabrication de comprimés ou la formation de disques de polymère). L’alignement de ces matrices dans la presse est tout aussi important que le placement de l’échantillon lui-même.
- Alignement correct de la matrice : La matrice ou le moule doit être bien aligné entre les plaques de compression pour éviter des pressions inégales ou des déformations du moule. L’utilisation de matrices mal alignées peut entraîner des résultats incohérents ou endommager le moule et la presse.
- Équilibrage de la pression : S’assurer que la matrice est stable avant l’application de la pression. Si la matrice est instable ou mal fixée, elle pourrait se déplacer sous la pression, entraînant un pressage inégal.
- Support de la matrice : Dans certaines presses, des supports spéciaux ou des guides sont disponibles pour maintenir les matrices parfaitement en place pendant l’expérience, garantissant ainsi un alignement parfait et une répartition homogène de la pression.
4. Réglage initial de la pression
Avant d’appliquer la pression maximale, il est recommandé de commencer par une pression légère pour vérifier l’alignement et la stabilité de l’échantillon.
- Test de pression initiale : Une légère pression initiale permet de s’assurer que l’échantillon est bien positionné et que les plaques de compression exercent une force uniforme. Cela réduit le risque d’une compression inégale ou d’un glissement de l’échantillon.
- Ajustement de l’échantillon : Si l’échantillon semble mal positionné après l’application de la pression initiale, il peut être ajusté à ce stade sans risquer de l’endommager.
- Stabilisation de l’échantillon : Pour les échantillons particulièrement fragiles ou sensibles, cette étape permet de stabiliser l’échantillon avant d’exercer une forte pression, garantissant ainsi une compression contrôlée.
5. Utilisation de cales et entretoises
Dans certaines situations, surtout lorsque l’échantillon est de petite taille par rapport à la presse, il peut être nécessaire d’utiliser des cales ou des entretoises pour garantir une application correcte de la pression.
- Cales d’espacement : Ces éléments permettent de réduire l’espace entre l’échantillon et les plaques de compression, garantissant une pression uniforme même sur de petits échantillons. Ils sont souvent utilisés lorsque les plaques de la presse sont trop éloignées pour exercer une pression efficace directement sur l’échantillon.
- Supports d’échantillon : Dans certains cas, des supports spécifiques sont utilisés pour maintenir l’échantillon en place pendant le pressage. Cela est particulièrement important pour les échantillons de formes irrégulières ou fragiles qui risquent de se désaligner sous pression.
6. Mesures de sécurité lors du placement de l’échantillon
Le placement de l’échantillon dans une presse, en particulier lorsque des forces élevées sont en jeu, doit toujours être effectué en tenant compte des mesures de sécurité appropriées.
- Port d’équipement de protection : Avant de placer l’échantillon dans la presse, les opérateurs doivent s’assurer de porter des gants, des lunettes de protection, et d’autres équipements de sécurité requis, notamment lorsque des échantillons chimiques ou biologiques dangereux sont manipulés.
- Vérification des plaques de compression : Avant chaque utilisation, les plaques de compression doivent être inspectées pour s’assurer qu’elles sont propres, sans défauts ou usures visibles. Des plaques endommagées ou sales peuvent entraîner une répartition inégale de la pression ou contaminer l’échantillon.
- Zones sécurisées autour de la presse : Pendant l’application de la pression, il est recommandé de se tenir à distance de la presse et de ne pas manipuler l’échantillon ou les commandes sans s’assurer que la presse est correctement verrouillée ou que la pression est relâchée.
7. Vérification post-pressage
Après le cycle de pressage, il est important de retirer l’échantillon avec précaution et d’inspecter à nouveau la presse.
- Relâchement contrôlé de la pression : Dans les presses automatiques ou hydrauliques, le relâchement de la pression est généralement programmé pour être progressif. Cependant, dans les presses manuelles, il est important de relâcher la pression doucement pour éviter tout choc à l’échantillon.
- Inspection de l’échantillon : Une fois l’échantillon retiré, il doit être inspecté pour vérifier qu’il a bien conservé sa forme et ses propriétés attendues (uniformité de la densité, absence de fissures ou de déformations).
- Nettoyage des plaques : Après chaque pressage, les plaques de la presse doivent être nettoyées pour éviter l’accumulation de résidus d’échantillons, en particulier lorsqu’on travaille avec des poudres ou des substances chimiques.
Résumé du placement de l’échantillon dans la presse :
- Centrer l’échantillon pour garantir une répartition uniforme de la pression.
- S’assurer que la surface de contact est plane et uniforme pour éviter des points de pression inégaux.
- Aligner les matrices ou moules avec précision pour éviter des déformations ou des résultats incohérents.
- Commencer par une pression légère pour vérifier le positionnement avant d’appliquer la pleine pression.
- Utiliser des cales ou entretoises si nécessaire pour garantir une compression homogène.
- Respecter les mesures de sécurité lors du placement et du retrait de l’échantillon.
- Inspecter l’échantillon et les plaques après chaque utilisation pour maintenir des conditions optimales.
Maintien de la pression dans une presse de laboratoire
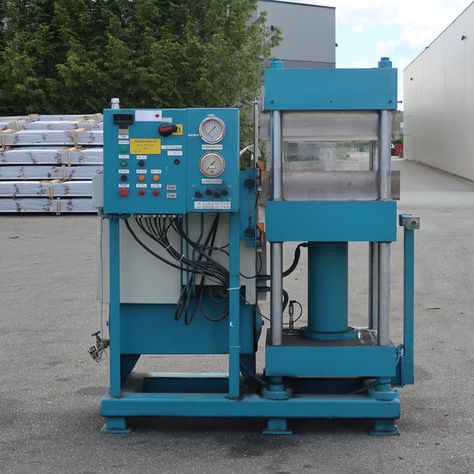
Le maintien de la pression est une étape critique dans le fonctionnement d’une presse de laboratoire. Cette phase consiste à appliquer une pression constante et uniforme sur l’échantillon pendant une durée définie. Elle est indispensable pour garantir que les matériaux subissent le traitement nécessaire, que ce soit pour les compacter, les transformer, ou les tester dans des conditions spécifiques. Le maintien de la pression doit être soigneusement contrôlé pour assurer des résultats précis et reproductibles, en évitant tout choc ou variation de force pouvant affecter l’échantillon ou les résultats de l’expérience.
1. Importance du maintien de la pression
Dans de nombreuses applications de laboratoire, maintenir la pression pendant une période donnée est aussi important que l’application initiale de la pression. Voici quelques raisons pour lesquelles cette phase est essentielle :
- Homogénéité et uniformité : En maintenant une pression constante, on s’assure que l’échantillon est comprimé de manière homogène. Cela est crucial pour obtenir une densité uniforme dans des matériaux comme les comprimés pharmaceutiques, les polymères ou les céramiques.
- Réactions chimiques : Dans certains processus, comme la polymérisation ou la formation de composites, maintenir la pression est nécessaire pour que les réactions chimiques se déroulent correctement sous des conditions contrôlées de température et de pression.
- Test de résistance : Lors des tests de résistance ou d’endurance de matériaux, comme les métaux ou les composites, la pression doit être maintenue pendant un certain temps pour évaluer leur comportement et leur déformation sous stress.
2. Durée du maintien de la pression
La durée pendant laquelle la pression doit être maintenue dépend de l’application spécifique et du matériau traité. Les paramètres de temps doivent être définis en fonction des objectifs de l’expérience.
- Compression rapide : Certaines applications, comme la fabrication de comprimés pharmaceutiques, peuvent ne nécessiter qu’un maintien de la pression pendant quelques secondes à quelques minutes pour compacter efficacement les poudres.
- Maintien prolongé : Pour les matériaux plus complexes ou les processus chimiques, le maintien de la pression peut durer plusieurs heures. Par exemple, dans le cas des polymères thermoplastiques ou des matériaux composites, il peut être nécessaire de maintenir la pression et la température pendant plusieurs heures pour garantir que la réaction chimique se déroule entièrement.
- Cycles de pression : Certaines presses automatiques permettent de programmer des cycles de montée et de descente de la pression sur une période prolongée. Cela permet de simuler des conditions de stress répétées ou de vérifier comment un matériau réagit à des pressions fluctuantes.
3. Presses automatiques vs manuelles : contrôle du maintien
Le maintien de la pression varie en fonction du type de presse utilisé. Les presses automatiques et hydrauliques offrent un contrôle précis et programmable, tandis que les presses manuelles nécessitent une surveillance plus active de l’opérateur.
3.1. Presses automatiques et hydrauliques
Les presses automatiques et hydrauliques permettent de programmer et de maintenir précisément la pression appliquée sans intervention humaine constante. Ces systèmes offrent de nombreux avantages :
- Précision : Grâce à des capteurs intégrés et des systèmes de contrôle électroniques, la pression peut être surveillée en temps réel et maintenue à un niveau constant sans variation. Cela garantit que la force appliquée reste stable tout au long de la période de maintien.
- Programmabilité : Dans les presses automatiques, il est possible de prédéfinir des durées spécifiques pour le maintien de la pression. L’opérateur peut programmer la machine pour augmenter la pression, la maintenir pendant un temps donné, puis la relâcher progressivement.
- Adaptabilité : En fonction du matériau ou du processus, ces presses permettent de maintenir une pression et, si nécessaire, une température constante, ce qui est essentiel pour des processus tels que le moulage sous pression ou la fabrication de matériaux composites.
3.2. Presses manuelles
Dans les presses manuelles, le maintien de la pression dépend de l’opérateur, qui doit ajuster le levier ou la manivelle pour maintenir une pression constante. Cela nécessite une attention particulière et peut entraîner une légère variation de la force appliquée.
- Suivi constant : L’opérateur doit surveiller en permanence le manomètre pour s’assurer que la pression reste au niveau souhaité. Cela peut être plus difficile à réaliser de manière précise, en particulier sur de longues périodes.
- Variations de pression : Contrairement aux systèmes automatisés, les variations de pression sont plus fréquentes dans les presses manuelles. Cela peut entraîner des résultats moins homogènes ou moins précis si le maintien de la pression n’est pas rigoureusement surveillé.
4. Relâchement progressif de la pression
Une fois la période de maintien terminée, la pression doit être relâchée de manière contrôlée pour éviter d’endommager l’échantillon ou de provoquer un choc mécanique.
- Relâchement lent : Le relâchement progressif de la pression permet à l’échantillon de retrouver sa forme initiale sans subir de déformation excessive. Dans les presses automatiques, cette étape peut être programmée pour se dérouler à une vitesse contrôlée.
- Risques d’un relâchement brutal : Un relâchement trop rapide de la pression peut endommager l’échantillon, surtout s’il est fragile ou soumis à des forces importantes. Dans certains cas, cela peut même entraîner la rupture ou la fissuration de l’échantillon, notamment dans les matériaux composites ou céramiques.
- Contrôle manuel : Dans les presses manuelles, l’opérateur doit veiller à libérer la pression progressivement en ajustant le levier ou la manivelle avec soin. Cela demande une attention particulière pour éviter un relâchement soudain.
5. Précautions pendant le maintien de la pression
Le maintien de la pression implique de respecter certaines précautions pour garantir la sécurité et la précision des résultats.
- Surveillance des paramètres : Pendant la période de maintien, il est essentiel de surveiller les paramètres tels que la pression et, si applicable, la température. Les capteurs et les systèmes de contrôle des presses modernes peuvent alerter l’opérateur en cas d’anomalie.
- Stabilité de la presse : La presse doit être installée sur une surface stable et à niveau pour éviter tout mouvement ou vibration qui pourrait affecter la répartition de la pression.
- Consignes de sécurité : Ne pas tenter de modifier l’échantillon ou d’ajuster la position de la presse pendant le maintien de la pression. Cela pourrait entraîner des accidents ou compromettre l’intégrité de l’échantillon.
6. Effets du maintien prolongé de la pression
Dans certains cas, maintenir la pression sur une longue période peut entraîner des effets bénéfiques ou, au contraire, des effets indésirables sur l’échantillon.
6.1. Effets bénéfiques
- Consolidation des matériaux : Le maintien prolongé de la pression permet une consolidation plus uniforme des matériaux, en particulier pour les poudres ou les matériaux composites. Cela garantit une densité homogène et une résistance accrue.
- Réactions chimiques complètes : Dans les processus nécessitant des réactions chimiques, comme la polymérisation ou le durcissement, le maintien de la pression permet à ces réactions de se dérouler complètement, sans interruption.
6.2. Effets indésirables
- Déformation excessive : Dans certains cas, une pression maintenue trop longtemps peut entraîner une déformation excessive ou permanente de l’échantillon, surtout pour des matériaux plus fragiles ou sensibles.
- Stress mécanique : Le stress prolongé sur certains matériaux peut entraîner des microfissures ou des faiblesses internes, qui pourraient ne pas être visibles immédiatement mais qui affecteront les propriétés mécaniques à long terme.
Résumé du maintien de la pression dans une presse de laboratoire :
- Importance du maintien de la pression : Garantir l’uniformité, permettre des réactions chimiques ou tester la résistance des matériaux.
- Durée du maintien : Dépend du matériau et de l’objectif de l’expérience, allant de quelques secondes à plusieurs heures.
- Presses automatiques vs manuelles : Les presses automatiques offrent un contrôle précis et programmable, tandis que les presses manuelles nécessitent une surveillance active par l’opérateur.
- Relâchement progressif de la pression : Essentiel pour éviter d’endommager l’échantillon ou de provoquer un choc mécanique.
- Précautions à prendre : Surveiller les paramètres et garantir la stabilité de la presse pendant toute la durée de la compression.
- Effets du maintien prolongé : Consolidation des matériaux et réactions chimiques complètes, mais attention aux risques de déformation excessive ou de stress mécanique.
Le maintien de la pression, correctement exécuté, est crucial pour garantir des résultats précis et fiables lors de l’utilisation d’une presse de laboratoire, tout en assurant la sécurité et l’intégrité des échantillons.
Relâchement de la pression dans une presse de laboratoire
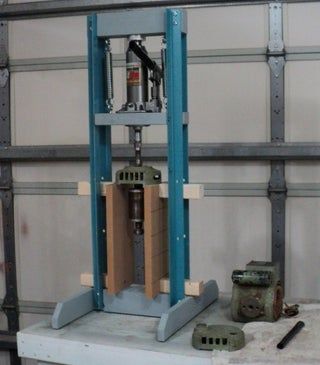
Le relâchement de la pression est une étape critique dans le processus de pressage d’un échantillon en laboratoire. Une fois la pression maintenue pendant la durée requise, elle doit être réduite de manière contrôlée pour éviter d’endommager l’échantillon ou de provoquer un choc mécanique pouvant altérer les résultats. Le relâchement de la pression, s’il est mal géré, peut entraîner des fissures, des déformations ou des ruptures, surtout avec des matériaux fragiles ou complexes. Cette phase doit être effectuée avec soin et selon les exigences spécifiques de chaque expérience.
1. Importance du relâchement progressif de la pression
Le relâchement progressif de la pression permet à l’échantillon de se stabiliser après avoir subi un cycle de compression intense. Si la pression est relâchée trop rapidement, cela peut causer des déformations irréversibles ou altérer les propriétés mécaniques ou chimiques de l’échantillon.
- Prévenir les dommages : Les matériaux fragiles ou composites peuvent être particulièrement sensibles à un relâchement soudain de la pression. En effet, une réduction brutale de la force appliquée peut créer des contraintes internes, entraînant des microfissures, des ruptures ou une délamination dans le cas de matériaux stratifiés.
- Maintenir l’intégrité structurelle : Dans les matériaux pressés à haute pression, comme les céramiques ou les métaux, un relâchement trop rapide peut provoquer une relaxation brutale, perturbant ainsi l’homogénéité de la densité ou la structure cristalline.
- Prévenir les chocs thermiques : Si l’échantillon est chauffé pendant la compression (presse à chaud), un relâchement trop rapide de la pression, surtout lorsque la température est encore élevée, peut provoquer un choc thermique qui pourrait déformer ou fissurer l’échantillon.
2. Méthodes de relâchement de la pression
Le processus de relâchement de la pression varie selon le type de presse utilisé et les caractéristiques de l’échantillon. Il peut être contrôlé manuellement ou automatisé, selon l’équipement disponible.
2.1. Relâchement dans les presses automatiques
Dans les presses automatiques, le relâchement de la pression est généralement programmé pour être progressif et se dérouler de manière contrôlée.
- Programmation du cycle de relâchement : Les presses automatiques permettent de définir un taux de réduction de la pression, qui peut être constant ou par paliers successifs. Cela permet de s’assurer que la force appliquée sur l’échantillon diminue lentement et uniformément.
- Capteurs de pression : Ces presses sont souvent équipées de capteurs qui surveillent la pression en temps réel. Ils permettent de garantir que la pression diminue à la vitesse prévue et alertent en cas de variation anormale ou d’erreur.
- Systèmes de contrôle électronique : Grâce aux systèmes de commande électroniques, le relâchement peut être réglé avec une grande précision, en fonction des besoins spécifiques de l’expérience. L’opérateur peut programmer différents niveaux de relâchement en fonction du type de matériau ou de la complexité de l’échantillon.
2.2. Relâchement dans les presses manuelles
Dans les presses manuelles, le relâchement de la pression doit être effectué directement par l’opérateur. Cela nécessite une attention particulière pour éviter une chute soudaine de la pression.
- Réglage manuel du levier ou de la manivelle : L’opérateur doit desserrer progressivement le levier ou la manivelle pour permettre à la pression de diminuer lentement. Cela demande un bon contrôle et une précision dans le geste pour éviter une baisse trop rapide de la force appliquée.
- Surveillance constante : Il est important de surveiller le manomètre pendant le relâchement pour s’assurer que la pression descend à un rythme constant. Un ajustement progressif du relâchement peut être nécessaire pour éviter un effondrement soudain de la pression.
2.3. Relâchement contrôlé par étapes
Dans certaines expériences, il peut être avantageux de relâcher la pression par étapes, avec des pauses à des niveaux intermédiaires. Cela permet à l’échantillon de se stabiliser avant que la pression ne soit complètement relâchée.
- Relâchement par paliers : Ce processus consiste à réduire la pression en plusieurs étapes. Par exemple, on peut diminuer la pression de 10 % à la fois, en marquant une pause à chaque niveau avant de continuer à relâcher la force.
- Stabilisation intermédiaire : Cette méthode est particulièrement utile pour les matériaux qui sont susceptibles de se fissurer ou de se déformer si la pression est relâchée trop rapidement. En stabilisant l’échantillon entre chaque palier, on lui permet de retrouver un équilibre interne avant de continuer la décompression.
3. Conséquences d’un relâchement brutal
Un relâchement trop rapide de la pression peut entraîner plusieurs effets indésirables qui affectent la qualité et l’intégrité de l’échantillon.
3.1. Fissures et ruptures
Dans les matériaux solides ou rigides, tels que les céramiques, les métaux ou les composites, une chute soudaine de la pression peut provoquer des microfissures internes ou des ruptures. Ces fissures peuvent ne pas être visibles immédiatement mais affaiblir considérablement le matériau et compromettre les résultats de l’expérience.
- Fragilité des matériaux : Les matériaux compressés sous haute pression sont souvent sous tension. Si la pression est libérée trop rapidement, ces tensions se libèrent brutalement, créant des défauts structurels.
- Tests destructifs : Dans certains tests de résistance des matériaux, un relâchement trop rapide de la pression peut fausser les résultats en endommageant prématurément l’échantillon.
3.2. Déformation de l’échantillon
Un relâchement soudain de la pression peut entraîner une déformation plastique de l’échantillon, surtout s’il s’agit de matériaux plus souples, comme certains polymères ou métaux. Cela peut affecter la forme finale ou les propriétés mécaniques de l’échantillon.
- Perte de forme : Les matériaux compressés de manière uniforme peuvent se déformer irrégulièrement lorsque la pression est relâchée trop rapidement, compromettant ainsi les mesures finales.
- Non-conformité des résultats : Une déformation inattendue peut rendre les résultats non reproductibles ou inutilisables, en particulier dans les essais où l’uniformité de la forme et de la densité est primordiale.
3.3. Stress interne
Le relâchement rapide de la pression peut induire des contraintes internes dans les matériaux qui, bien qu’invisibles immédiatement, peuvent affecter leur durabilité à long terme. Ces contraintes peuvent provoquer des ruptures ou des fissures ultérieures lors de tests de fatigue ou d’usure.
4. Relâchement de la pression et contrôle de la température
Dans les presses à chaud, où la température joue un rôle aussi important que la pression, il est essentiel de synchroniser le relâchement de la pression avec le refroidissement de l’échantillon.
- Relâchement progressif pendant le refroidissement : Si la température est encore élevée au moment de relâcher la pression, l’échantillon peut subir un choc thermique. Il est donc recommandé de relâcher la pression lentement, en accord avec la diminution progressive de la température.
- Impact des gradients thermiques : Les matériaux chauffés peuvent se comporter différemment lors du relâchement de la pression. Des gradients de température internes peuvent exacerber les tensions mécaniques si la pression est relâchée trop rapidement.
5. Précautions de sécurité lors du relâchement de la pression
La sécurité est un élément crucial lors du relâchement de la pression, surtout lorsque des forces importantes sont en jeu.
- Éviter de manipuler la presse pendant le relâchement de la pression. Tout ajustement ou manipulation de la presse pendant cette phase pourrait entraîner un choc mécanique dangereux.
- Utilisation des dispositifs de sécurité : Les presses automatiques modernes sont souvent équipées de systèmes de verrouillage qui empêchent l’ouverture des plaques tant que la pression n’est pas complètement relâchée. Il est important de s’assurer que ces dispositifs sont activés et fonctionnent correctement.
- Surveillance constante : Dans le cas des presses manuelles, l’opérateur doit rester attentif au manomètre pour éviter tout relâchement soudain, en maintenant un contrôle total sur la manivelle ou le levier de relâchement.
Résumé du relâchement de la pression dans une presse de laboratoire :
- Relâchement progressif de la pression : Essentiel pour éviter les dommages matériels, les déformations et les fissures dans l’échantillon.
- Méthodes de relâchement : Dans les presses automatiques, le processus est programmable et précis, tandis que dans les presses manuelles, il demande une attention continue de l’opérateur.
- Relâchement par étapes : Utile pour stabiliser l’échantillon à différents niveaux de pression avant de la relâcher complètement.
- Conséquences d’un relâchement brutal : Risque de fissures, de déformations et de stress interne dans l’échantillon, affectant la qualité des résultats.
- Précautions de sécurité : Toujours surveiller le processus et utiliser les dispositifs de sécurité pour éviter tout accident ou dommage lors du relâchement.
Le relâchement contrôlé de la pression est une étape aussi importante que l’application initiale de celle-ci. Une gestion soignée de cette phase garantit l’intégrité de l’échantillon et des résultats expérimentaux, tout en assurant la sécurité de l’opérateur et de l’équipement.
Retrait de l’échantillon d’une presse de laboratoire
Le retrait de l’échantillon après un cycle de pressage est une étape importante qui doit être réalisée avec soin pour éviter d’endommager l’échantillon et garantir la sécurité de l’opérateur. Cette phase intervient une fois que la pression a été complètement relâchée et que l’échantillon est prêt à être retiré des plaques de compression ou de la matrice. Un retrait incorrect ou précipité peut non seulement altérer les propriétés de l’échantillon, mais aussi causer des accidents ou des dommages à la presse.
1. Importance du retrait correct de l’échantillon
Le retrait de l’échantillon, bien que simple en apparence, doit être effectué de manière méthodique pour plusieurs raisons :
- Préserver l’intégrité de l’échantillon : Si l’échantillon est fragile, récemment formé ou compacté, il peut être sensible aux forces externes. Un retrait brusque ou mal exécuté pourrait entraîner des fissures, des cassures ou des déformations.
- Éviter les accidents : L’opérateur doit s’assurer que toutes les mesures de sécurité sont respectées avant d’ouvrir la presse ou de manipuler l’échantillon. Un retrait hâtif sans s’assurer que la pression est entièrement relâchée peut provoquer des blessures graves.
- Assurer la reproductibilité : Dans les expériences scientifiques ou les processus industriels, il est essentiel de retirer l’échantillon sans l’endommager pour garantir que les résultats obtenus soient reproductibles et fiables.
2. Vérifications avant le retrait de l’échantillon
Avant de retirer l’échantillon de la presse, plusieurs vérifications doivent être effectuées pour s’assurer que les conditions sont sûres et optimales.
2.1. Relâchement complet de la pression
La pression doit être complètement relâchée avant d’ouvrir la presse et de manipuler l’échantillon.
- Manomètre à zéro : Il est essentiel de vérifier que le manomètre de la presse indique zéro avant de commencer le retrait. Dans une presse hydraulique ou manuelle, un manomètre encore sous pression indique que la presse n’est pas entièrement décompressée.
- Systèmes de verrouillage : Dans les presses automatiques, les plaques de compression restent souvent verrouillées tant que la pression n’est pas entièrement relâchée. Ce système de sécurité doit être vérifié pour éviter tout accident.
2.2. Vérification de la température
Dans les presses à chaud, la température des plaques et de l’échantillon peut encore être élevée juste après le relâchement de la pression. Il est important de s’assurer que l’échantillon est suffisamment refroidi avant de le manipuler pour éviter les risques de brûlures ou de déformation thermique.
- Capteurs de température : Certains systèmes sont équipés de capteurs qui indiquent quand la température est revenue à un niveau sûr. Si ce n’est pas le cas, l’opérateur doit attendre que l’échantillon refroidisse à une température appropriée avant de le manipuler.
- Utilisation de gants thermorésistants : Si l’échantillon ou les plaques sont encore légèrement chauds, il est recommandé de porter des gants thermorésistants pour éviter tout contact direct avec des surfaces brûlantes.
2.3. Inspection visuelle des plaques et de l’échantillon
Avant de retirer l’échantillon, un examen visuel rapide des plaques et de l’échantillon est recommandé pour vérifier que rien ne gêne le retrait.
- Résidus sur les plaques : Les plaques de compression doivent être propres et exemptes de résidus qui pourraient rendre difficile le retrait de l’échantillon ou compromettre l’intégrité des échantillons suivants.
- Intégrité de l’échantillon : L’échantillon doit être inspecté visuellement pour s’assurer qu’il n’est ni fissuré ni déformé avant de tenter de le retirer. Si des dommages sont constatés, il convient d’examiner de plus près la cause possible avant de le retirer complètement.
3. Méthodes de retrait de l’échantillon
Selon le type de presse utilisée et la nature de l’échantillon, différentes méthodes peuvent être employées pour retirer l’échantillon en toute sécurité et de manière efficace.
3.1. Retrait manuel direct
Dans les cas où l’échantillon est simplement placé entre les plaques de compression sans être inséré dans une matrice ou un moule, un retrait manuel direct peut être effectué après le relâchement de la pression.
- Utilisation d’outils adaptés : Si l’échantillon est difficile à saisir, des pinces ou des outils spécialisés peuvent être utilisés pour le retirer délicatement sans l’endommager. Les outils en plastique ou en silicone sont souvent préférés pour éviter de rayer ou de fissurer des matériaux fragiles.
- Éviter de forcer : Si l’échantillon semble coller aux plaques, il est recommandé de ne pas forcer son retrait. Dans certains cas, un léger tapotement sur les plaques peut suffire à le détacher, ou l’utilisation d’un jet d’air comprimé peut aider à le libérer.
3.2. Retrait d’un échantillon dans une matrice
Lorsque l’échantillon est comprimé dans une matrice ou un moule, son retrait nécessite plus de précautions, surtout si l’échantillon a pris une forme spécifique et doit être maintenu intact.
- Démoulage progressif : Pour retirer un échantillon moulé, il peut être nécessaire de tapoter légèrement sur les bords de la matrice avec un maillet en caoutchouc ou en bois pour le libérer. Cela évite de fracturer l’échantillon lors du retrait.
- Utilisation de lubrifiants : Dans certaines applications, des lubrifiants spécifiques sont appliqués sur la matrice avant le pressage pour faciliter le démoulage. Si un lubrifiant a été utilisé, s’assurer qu’il n’a pas affecté la surface ou les propriétés chimiques de l’échantillon.
- Presses à éjecteurs automatiques : Certaines presses sont équipées de systèmes d’éjection qui facilitent le retrait automatique de l’échantillon une fois la pression relâchée. Ces systèmes sont particulièrement utiles pour les échantillons comprimés dans des matrices étroites ou complexes.
4. Précautions lors du retrait
Lors du retrait de l’échantillon, il est important de suivre certaines précautions pour garantir la sécurité et préserver l’intégrité de l’échantillon.
4.1. Protéger l’échantillon
Si l’échantillon est fragile ou a subi une compression sous haute pression, il peut être susceptible de se fissurer ou de se casser lors de son retrait.
- Manipulation délicate : Utiliser des outils qui ne risquent pas de rayer, fissurer ou briser l’échantillon. Si nécessaire, soutenir l’échantillon avec les deux mains lors du retrait pour répartir uniformément la pression.
- Utilisation de supports : Pour les échantillons volumineux ou complexes, il est recommandé d’utiliser des supports spécialement conçus pour les maintenir en place pendant le retrait, évitant ainsi tout mouvement ou chute accidentelle.
4.2. Prévenir les accidents
La sécurité de l’opérateur doit être assurée à chaque étape du retrait de l’échantillon, notamment lors de la manipulation de matériaux sous haute pression ou de températures élevées.
- Port de gants et de lunettes de protection : Pour se prémunir des risques liés à la manipulation de matériaux chauds, abrasifs ou dangereux, l’opérateur doit porter des gants thermorésistants ou des gants adaptés à la manipulation de substances chimiques. Des lunettes de protection sont également recommandées.
- Attention aux systèmes de verrouillage : Si la presse est équipée d’un système de verrouillage de sécurité, s’assurer que celui-ci est désactivé avant de tenter de retirer l’échantillon.
5. Nettoyage des plaques et de la matrice
Après le retrait de l’échantillon, il est essentiel de nettoyer les plaques de compression et la matrice pour les préparer aux prochaines expériences ou cycles de production.
- Nettoyage immédiat : Les résidus laissés par l’échantillon, qu’il s’agisse de poudres, de liquides ou de matériaux polymérisés, doivent être retirés immédiatement pour éviter qu’ils ne durcissent ou n’endommagent les plaques lors du prochain cycle.
- Produits de nettoyage appropriés : Utiliser des produits de nettoyage compatibles avec les matériaux des plaques et des matrices, en évitant les solvants qui pourraient corroder ou endommager les surfaces. Des brosses non abrasives ou des chiffons doux peuvent être utilisés pour éliminer les résidus sans rayer la surface.
6. Inspection finale de l’échantillon
Après avoir retiré l’échantillon, il est important de l’inspecter pour s’assurer qu’il répond aux attentes de l’expérience.
- Vérification de la forme et de la densité : S’assurer que l’échantillon a conservé sa forme prévue sans déformation visible. Pour certains échantillons, un contrôle de la densité ou du poids peut être effectué pour vérifier la qualité de la compression.
- Observation des fissures ou des défauts : Rechercher toute fissure,
Presses à chaud et à froid
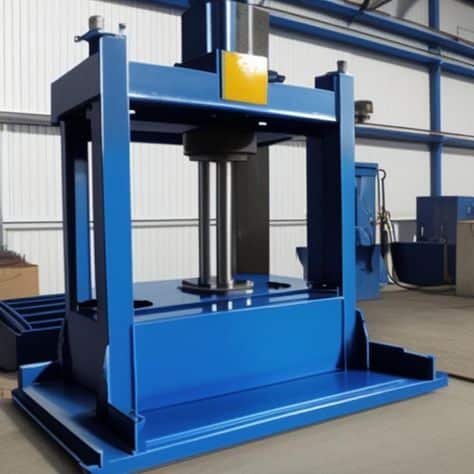
Les presses de laboratoire se divisent principalement en deux catégories selon l’utilisation ou non de la chaleur lors du processus de pressage : les presses à chaud et les presses à froid. Chaque type de presse a des applications spécifiques, des avantages et des inconvénients en fonction des matériaux à traiter et des résultats attendus. Le choix entre une presse à chaud ou à froid dépend des propriétés thermiques des matériaux utilisés, ainsi que des objectifs de l’expérience ou du processus industriel.
1. Presses à chaud
Les presses à chaud sont équipées de plaques chauffantes qui permettent d’appliquer de la chaleur, en plus de la pression, sur l’échantillon. Elles sont particulièrement utilisées pour les matériaux thermoplastiques, les polymères, les composites, et dans certains processus chimiques ou pharmaceutiques où la chaleur est nécessaire pour activer des réactions ou modifier la structure des matériaux.
1.1. Principe de fonctionnement
Le fonctionnement d’une presse à chaud repose sur l’application simultanée de pression et de chaleur. Les plaques de compression sont chauffées à une température prédéfinie et l’échantillon est placé entre ces plaques. La combinaison de la pression et de la chaleur permet de former, compacter, ou déclencher des réactions chimiques dans les matériaux.
- Plaques chauffantes : Ces plaques peuvent être chauffées par des résistances électriques internes ou d’autres systèmes de chauffage intégrés. La température est contrôlée via un thermostat ou un système de régulation électronique, avec une plage de température pouvant atteindre plusieurs centaines de degrés Celsius.
- Contrôle de la température : Les presses à chaud permettent un contrôle précis de la température, parfois avec une régulation indépendante de chaque plaque pour offrir une flexibilité accrue dans les expériences.
- Pression appliquée : La pression est exercée de manière classique, soit via un système hydraulique, manuel, ou automatique. L’application de chaleur pendant le pressage peut faciliter la déformation ou la réaction des matériaux sous pression.
1.2. Applications des presses à chaud
Les presses à chaud sont utilisées dans des domaines variés, notamment pour le formage de matériaux, les réactions chimiques sous pression, et la consolidation de matériaux composites.
- Moulage des polymères : Les polymères thermoplastiques sont souvent pressés à chaud pour être moulés ou pour obtenir des feuilles, des films ou des formes spécifiques. La chaleur ramollit les polymères, permettant leur transformation sous pression.
- Consolidation de composites : Les matériaux composites, tels que les fibres de carbone ou de verre renforcées de résine, sont souvent pressés à chaud pour créer des structures solides et légères. La chaleur permet à la résine de durcir, tout en maintenant la forme sous pression.
- Fabrication de circuits électroniques : Les presses à chaud sont également utilisées pour la fabrication de circuits imprimés multicouches, où des couches de matériaux conducteurs et isolants sont compressées sous chaleur pour créer des connexions stables.
- Polymérisation : Dans certaines réactions chimiques, la chaleur permet d’activer des processus de polymérisation. Cela est crucial pour la fabrication de certains types de plastiques ou de caoutchoucs.
1.3. Avantages des presses à chaud
- Réactions activées par la chaleur : La combinaison de la chaleur et de la pression permet de réaliser des transformations que la pression seule ne peut pas accomplir, comme le ramollissement des thermoplastiques ou la durcification des résines.
- Accélération des processus : La chaleur réduit le temps nécessaire pour certaines transformations, notamment dans les processus de moulage ou de consolidation de matériaux composites, où le durcissement sous chaleur est essentiel.
- Flexibilité des paramètres : Les presses à chaud permettent de contrôler à la fois la pression et la température, ce qui offre une grande flexibilité pour ajuster les conditions en fonction des besoins spécifiques des expériences.
1.4. Limites des presses à chaud
- Coût et complexité : Les presses à chaud sont généralement plus coûteuses que les presses à froid en raison de leur mécanisme de chauffage et de contrôle de la température.
- Maintenance : Le système de chauffage nécessite un entretien régulier pour garantir des performances optimales. De plus, les plaques chauffantes peuvent s’user plus rapidement en raison des cycles répétés de chauffage et de refroidissement.
- Risques thermiques : La manipulation de matériaux à haute température nécessite des précautions supplémentaires, notamment l’utilisation d’équipements de protection pour éviter les brûlures.
Presses à froid
Les presses à froid sont des presses qui appliquent uniquement de la pression sans aucune intervention thermique. Elles sont principalement utilisées pour les matériaux qui ne nécessitent pas de chaleur pour être déformés ou consolidés, ou pour les échantillons qui pourraient être dégradés par la chaleur. Elles sont courantes dans la préparation de poudres, le test de résistance des matériaux, et dans certaines applications pharmaceutiques ou chimiques.
2.1. Principe de fonctionnement
Dans une presse à froid, seule la force mécanique est utilisée pour comprimer l’échantillon. La pression est appliquée via un système hydraulique, pneumatique ou manuel, en fonction du type de presse.
- Plaques de compression : Les plaques restent à température ambiante pendant tout le processus. Cela garantit que la structure chimique et physique de l’échantillon n’est pas modifiée par des facteurs thermiques.
- Pression appliquée : Comme pour les presses à chaud, la pression est exercée par un piston, qui peut être actionné manuellement ou automatiquement. Les forces appliquées peuvent varier de quelques tonnes à plusieurs dizaines de tonnes, selon la presse.
2.2. Applications des presses à froid
Les presses à froid sont largement utilisées dans des secteurs où la chaleur pourrait altérer ou dégrader l’échantillon ou lorsque seule la pression est nécessaire pour obtenir le résultat souhaité.
- Compression des poudres : Dans les laboratoires pharmaceutiques, les poudres de médicaments sont souvent comprimées en comprimés sans chaleur pour préserver l’intégrité des ingrédients actifs. Cela permet de former des comprimés denses et uniformes tout en préservant les propriétés pharmacologiques du produit.
- Test de résistance des matériaux : Les presses à froid sont utilisées pour tester la résistance mécanique des matériaux, comme les métaux, les plastiques, ou les céramiques. La pression est appliquée pour simuler des conditions de charge et mesurer la capacité du matériau à supporter ces forces.
- Formation de pastilles pour l’analyse : Dans les laboratoires chimiques, des échantillons en poudre sont souvent compressés en pastilles pour les analyses spectroscopiques. L’application de la pression suffit pour obtenir des échantillons denses et homogènes, prêts à être analysés.
- Préparation de produits alimentaires : Dans l’industrie alimentaire, certaines techniques de compression à froid sont utilisées pour préparer des produits alimentaires, comme la fabrication de comprimés alimentaires ou l’extraction d’huiles et de jus sans chaleur.
2.3. Avantages des presses à froid
- Simplicité et coût : Les presses à froid sont souvent moins coûteuses et plus simples à entretenir que les presses à chaud, car elles n’ont pas de systèmes de chauffage complexes.
- Préservation des matériaux sensibles : Certains matériaux peuvent être dégradés ou modifiés par la chaleur. Les presses à froid sont donc idéales pour les substances thermosensibles ou fragiles.
- Moins de risques thermiques : Comme aucune chaleur n’est appliquée, les risques de brûlures pour l’opérateur sont éliminés, et les conditions de travail sont plus sûres.
2.4. Limites des presses à froid
- Pas de transformation thermique : Contrairement aux presses à chaud, les presses à froid ne permettent pas de transformations nécessitant de la chaleur, comme la fusion ou le durcissement des polymères ou des composites.
- Résultats limités pour certains matériaux : Pour les matériaux thermoplastiques ou certains polymères, la pression seule peut ne pas suffire pour obtenir les résultats souhaités, car ils nécessitent de la chaleur pour se ramollir ou se transformer.
Comparaison des presses à chaud et à froid
Caractéristique | Presse à chaud | Presse à froid |
---|---|---|
Température | Utilisation de la chaleur (jusqu’à plusieurs centaines de degrés Celsius). | Pas de chaleur, température ambiante. |
Applications | Moulage de polymères, consolidation de composites, réactions chimiques. | Compression de poudres, tests mécaniques, formation de pastilles. |
Coût et complexité | Plus coûteuses et complexes (systèmes de chauffage et de contrôle). | Moins coûteuses, plus simples à utiliser. |
Maintenance | Entretien régulier des plaques chauffantes. | Moins de maintenance, pas de systèmes de chauffage à gérer. |
Risques thermiques | Précautions nécessaires pour éviter les brûlures et les accidents liés à la chaleur. | Aucune précaution thermique requise. |
Utilisation | Transformation thermique et pressage simultanés. | Pressage uniquement, sans transformation thermique. |
Conclusion
Le choix entre une presse à chaud et une presse à froid dépend entièrement des besoins spécifiques de l’application. Si le processus nécessite de la chaleur pour ramollir, former, ou déclencher des réactions chimiques dans les matériaux, une presse à chaud sera indispensable. En revanche, si l’échantillon est thermosensible ou que seule la pression est nécessaire, une presse à froid sera plus appropriée.
Applications des presses de laboratoire
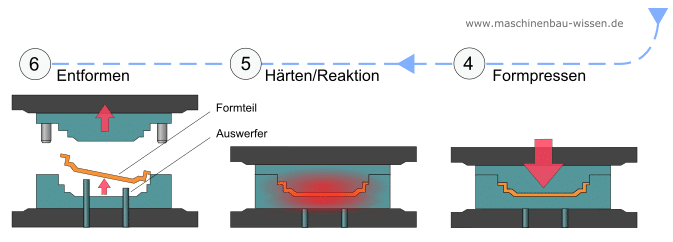
Les presses de laboratoire sont utilisées dans une vaste gamme d’industries et de secteurs scientifiques. Leur capacité à appliquer une pression précise et contrôlée sur des échantillons en fait des outils polyvalents pour diverses applications, allant de la recherche à la production industrielle. Les principales applications concernent les secteurs pharmaceutique, chimique, des matériaux, électronique, et bien d’autres. Voici un aperçu détaillé des principales applications des presses de laboratoire.
1. Secteur pharmaceutique
Les presses de laboratoire sont largement utilisées dans l’industrie pharmaceutique pour diverses tâches liées à la recherche, au développement, et à la fabrication de médicaments. Elles sont indispensables dans les processus de préparation des formes solides, comme les comprimés, et pour le contrôle qualité des produits.
1.1. Compression de poudres pour la fabrication de comprimés
L’une des principales applications des presses dans l’industrie pharmaceutique est la compression de poudres pour former des comprimés solides.
- Formulation de comprimés : Les poudres de principes actifs et d’excipients sont comprimées sous une pression contrôlée pour former des comprimés uniformes en taille, forme et densité. Cette étape est cruciale pour garantir que chaque comprimé contient la bonne dose de médicament et qu’il est mécaniquement stable.
- Tests de faisabilité : Avant la production à grande échelle, les presses de laboratoire permettent de réaliser des tests de faisabilité pour évaluer la compressibilité des formulations. Cela permet de s’assurer que les ingrédients se lient correctement sous pression, sans se désintégrer ou s’effriter.
1.2. Fabrication de pilules à libération contrôlée
Les presses sont utilisées pour fabriquer des comprimés à libération prolongée ou contrôlée. Ces formulations spéciales permettent de libérer le principe actif sur une période prolongée, garantissant ainsi une action durable du médicament.
- Contrôle de la porosité : Le pressage sous conditions contrôlées permet de réguler la porosité du comprimé, influençant ainsi la vitesse de dissolution et de libération du principe actif dans l’organisme.
1.3. Contrôle qualité
Les presses de laboratoire jouent un rôle clé dans le contrôle qualité des médicaments. Elles sont utilisées pour tester la dureté, la friabilité, et la dissolution des comprimés sous pression. Ces tests garantissent que les comprimés fabriqués répondent aux normes strictes de qualité et de sécurité avant leur mise sur le marché.
2. Recherche sur les matériaux
Les presses de laboratoire sont largement employées dans les laboratoires de recherche sur les matériaux pour étudier les propriétés des matériaux et pour fabriquer des échantillons de test à petite échelle. Elles sont essentielles dans la mise au point de nouveaux matériaux composites, de métaux, de polymères, et de céramiques.
2.1. Moulage de polymères et composites
Les presses de laboratoire sont utilisées pour transformer des polymères sous pression, souvent avec l’aide de la chaleur (presses à chaud), afin de former des films, des feuilles, ou des pièces spécifiques. Elles sont aussi utilisées pour les matériaux composites qui nécessitent un pressage sous haute pression pour être consolidés.
- Moulage de polymères thermoplastiques : Les polymères thermoplastiques peuvent être formés à chaud sous pression pour fabriquer des pièces ou des films. Ce processus est couramment utilisé dans l’industrie des plastiques pour fabriquer des prototypes avant une production à grande échelle.
- Consolidation de matériaux composites : Les composites, comme les fibres de verre ou de carbone, renforcées par des résines thermodurcissables, sont pressés à chaud pour former des structures solides et légères. Ces matériaux sont utilisés dans les secteurs de l’aéronautique, de l’automobile et de la construction.
2.2. Tests de résistance et de dureté des matériaux
Les presses de laboratoire sont également utilisées pour évaluer la résistance à la compression de divers matériaux, y compris les métaux, les céramiques et les matériaux composites.
- Tests de dureté : La capacité d’un matériau à résister à la pression est mesurée par des tests de dureté sous pression. Ces tests permettent d’évaluer la qualité mécanique des matériaux et leur capacité à supporter des charges importantes.
- Tests de déformation plastique : Les presses de laboratoire sont utilisées pour tester la plasticité des métaux et des composites, c’est-à-dire leur capacité à se déformer de manière permanente sous l’effet d’une contrainte, sans se rompre.
2.3. Compression des poudres métalliques et céramiques
Les poudres métalliques et céramiques sont souvent pressées sous haute pression dans des moules pour former des échantillons solides qui seront ensuite sintrés ou testés.
- Métallurgie des poudres : Dans la métallurgie des poudres, des particules métalliques sont compactées sous pression pour former des pièces solides. Ces pièces sont ensuite sintrées pour obtenir des propriétés mécaniques comparables à celles des métaux fondus.
- Formation de céramiques : Les presses permettent de former des céramiques en comprimant des poudres fines dans des moules, créant ainsi des pièces solides prêtes pour des processus de cuisson ou de sintrage.
3. Industrie chimique
Les presses de laboratoire trouvent également des applications variées dans l’industrie chimique, où elles sont utilisées pour compacter des produits chimiques ou pour préparer des échantillons pour analyse.
3.1. Pressage de catalyseurs
Les catalyseurs utilisés dans l’industrie chimique sont souvent pressés sous forme de pellets pour augmenter leur surface active. Les presses de laboratoire permettent de compacter ces catalyseurs de manière uniforme, assurant ainsi une réactivité maximale dans les réactions chimiques.
- Pelletisation des catalyseurs : En pressant les catalyseurs sous forme de petits pellets, on augmente leur surface de contact avec les réactifs, améliorant ainsi l’efficacité des réactions chimiques dans des processus comme le raffinage du pétrole ou la production de produits chimiques fins.
3.2. Préparation d’échantillons pour analyse chimique
Les presses sont souvent utilisées pour préparer des échantillons en comprimant des poudres chimiques dans des pastilles denses et homogènes, prêtes pour des analyses par spectroscopie ou d’autres méthodes.
- Compression en pastilles : Dans la spectroscopie infrarouge (IR), par exemple, les échantillons en poudre sont souvent pressés en pastilles avec du bromure de potassium (KBr) pour obtenir des échantillons transparents et uniformes, facilitant ainsi l’analyse.
3.3. Test de stabilité des formulations
Dans l’industrie chimique, des formulations sous forme de poudre ou de comprimés sont souvent testées sous pression pour évaluer leur stabilité mécanique et chimique. Ces tests garantissent que les produits restent intacts pendant leur stockage, leur transport et leur utilisation.
4. Biotechnologie
Dans le domaine de la biotechnologie, les presses de laboratoire sont utilisées pour la préparation et l’analyse des échantillons biologiques, ainsi que dans la fabrication de dispositifs biomédicaux.
4.1. Préparation des échantillons biologiques
Les presses sont souvent utilisées pour préparer des échantillons biologiques à analyser par des méthodes comme la spectrométrie ou la chromatographie.
- Pressage d’échantillons pour spectrométrie : Les échantillons biologiques, comme les tissus ou les cellules, peuvent être pressés en pastilles pour être analysés en spectrométrie, facilitant ainsi la détection des éléments chimiques présents dans les échantillons.
4.2. Fabrication de dispositifs médicaux
Dans certaines applications biomédicales, les presses sont utilisées pour compacter des matériaux biocompatibles qui serviront à fabriquer des implants ou des dispositifs médicaux. La compression sous pression permet de former des dispositifs solides et stériles prêts à être utilisés en milieu médical.
5. Industrie alimentaire
Dans l’industrie alimentaire, les presses de laboratoire sont utilisées pour compacter des aliments ou extraire des composants tels que les huiles ou les jus.
5.1. Compression des produits alimentaires
Certaines techniques de compression sont utilisées pour former des produits alimentaires sous forme de comprimés ou de galettes. Cela permet de créer des produits alimentaires faciles à manipuler ou à conditionner.
- Comprimés alimentaires : Dans l’industrie des compléments alimentaires, des poudres de vitamines ou de minéraux sont comprimées sous forme de comprimés solides, prêts à la consommation.
5.2. Extraction de jus et d’huiles
Les presses sont également utilisées pour extraire des huiles ou des jus à partir de matières premières alimentaires, telles que les fruits, les graines ou les noix.
- Extraction d’huiles à froid : Les presses à froid sont utilisées pour extraire des huiles sans chaleur, préservant ainsi la qualité nutritionnelle des huiles, comme l’huile d’olive ou l’huile de noix.
6. Autres applications industrielles
Les presses de laboratoire trouvent également des applications dans d’autres industries, notamment l’électronique, l’énergie et les matériaux de construction.
6.1. Fabrication de composants électroniques
Dans l’industrie électronique, les presses sont utilisées pour compacter et laminer des matériaux dans la fabrication de dispositifs électroniques, comme les circuits imprimés.
- Circuits multicouches : Les matériaux isolants et conducteurs sont laminés sous pression pour former des circuits imprimés multicouches, utilisés dans les ordinateurs, les téléphones portables et d’autres dispositifs électroniques.
6.2. Production d’électrodes et de batteries
Les presses sont également utilisées dans la fabrication de composants pour les batteries, comme les électrodes. Ces composants doivent être compactés sous haute pression pour garantir une densité et une efficacité énergétique optimales.
- Fabrication d’électrodes : Les électrodes pour batteries au lithium sont souvent pressées sous haute pression pour assurer une bonne conductivité électrique et une capacité de charge optimale.
Conclusion
Les presses de laboratoire sont des outils polyvalents et indispensables dans de nombreuses industries et secteurs de recherche. Que ce soit pour la compression de poudres, la fabrication de matériaux composites, le test de résistance ou la préparation d’échantillons pour analyse, ces presses offrent un contrôle précis de la pression (et parfois de la température) pour répondre aux exigences spécifiques des expériences et des processus industriels. Leur rôle est crucial dans le développement de nouvelles technologies, la mise au point de matériaux innovants et la fabrication de produits de haute qualité.
Introduction à la Presse de Laboratoire
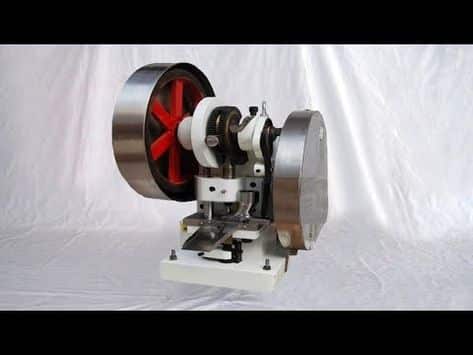
Les presses de laboratoire sont des équipements essentiels dans de nombreuses disciplines scientifiques et industrielles. Ces appareils permettent l’application contrôlée de pressions sur divers matériaux, avec des utilisations dans des domaines tels que la recherche sur les matériaux, la chimie, l’industrie pharmaceutique, l’électronique et bien d’autres. Leur rôle est crucial dans la transformation, la compression et la caractérisation des échantillons à des fins de recherche, de fabrication ou d’analyse.
Cet article vise à fournir une vue d’ensemble exhaustive des presses de laboratoire, en explorant leur fonctionnement, les différents types, leurs applications variées et leur importance dans l’avancement des technologies et des produits modernes. Dans le cadre de cette introduction, nous allons d’abord examiner le concept général des presses de laboratoire, puis analyser en détail les nombreux aspects techniques et pratiques liés à leur utilisation.
1. Qu’est-ce qu’une presse de laboratoire ?
Une presse de laboratoire est un appareil conçu pour appliquer une pression contrôlée sur un échantillon, généralement en vue de le comprimer, de le former, ou de l’analyser. Ces appareils sont largement utilisés dans des laboratoires de recherche ou des environnements industriels pour des tâches de transformation de matériaux, la fabrication de petites pièces, ou la préparation d’échantillons pour des analyses plus approfondies.
Les presses de laboratoire sont disponibles dans une gamme variée de types et de configurations, allant des presses manuelles simples aux presses automatiques et hydrauliques sophistiquées. Elles peuvent être utilisées à température ambiante (presses à froid) ou à haute température (presses à chaud), en fonction des besoins spécifiques de l’application. La précision avec laquelle ces presses peuvent exercer et maintenir la pression est l’un des aspects qui les rendent si précieuses dans des environnements où la reproductibilité des expériences est essentielle.
1.1. Rôle et importance des presses de laboratoire
Les presses de laboratoire jouent un rôle fondamental dans des processus qui nécessitent une application de pression rigoureuse et précise. Parmi les exemples de leur utilisation, on peut citer :
- Compression des poudres : Dans l’industrie pharmaceutique, elles sont utilisées pour transformer des poudres en comprimés solides, assurant ainsi une dose précise et uniforme de médicament.
- Formage de matériaux : Elles servent à façonner des matériaux, comme les métaux, les polymères et les céramiques, sous forme de films, de pastilles ou de disques, souvent à des fins de test ou de recherche.
- Préparation d’échantillons pour analyse : Les laboratoires de chimie et de matériaux utilisent des presses pour préparer des échantillons denses et homogènes, nécessaires pour des analyses par spectrométrie, diffraction des rayons X, etc.
- Fabrication de composants : En électronique et dans l’industrie des matériaux avancés, les presses sont indispensables pour fabriquer des composants complexes, tels que des circuits imprimés multicouches, des matériaux composites, ou encore des électrodes pour batteries.
1.2. Évolution des presses de laboratoire
Au fil du temps, les presses de laboratoire ont évolué pour s’adapter aux besoins de plus en plus sophistiqués des chercheurs et des industriels. Des presses mécaniques manuelles aux presses hydrauliques automatisées actuelles, cette évolution s’est accompagnée d’une amélioration de la précision, de la reproductibilité et de la sécurité.
L’introduction des presses automatiques, avec des systèmes de contrôle numérique, a permis d’augmenter considérablement la précision et la régularité des processus de pressage. Les capteurs et les systèmes de contrôle permettent aujourd’hui de surveiller la pression, la température et d’autres paramètres critiques en temps réel, garantissant ainsi des résultats cohérents et fiables.
Par ailleurs, les innovations récentes, telles que l’intégration de technologies intelligentes et l’utilisation de matériaux durables, continuent d’améliorer les performances et l’efficacité des presses de laboratoire. L’intégration de l’Internet des objets (IoT) permet aux presses modernes de se connecter à des systèmes d’analyse de données, ce qui ouvre de nouvelles perspectives en termes de contrôle de qualité, de maintenance prédictive et d’optimisation des processus.
2. Types de presses de laboratoire
Il existe plusieurs types de presses de laboratoire, chacune adaptée à des besoins spécifiques en termes de pression, de température, de taille et de précision. Ces presses sont classées selon divers critères, tels que la méthode d’application de la pression, le niveau d’automatisation et la présence ou non d’un système de chauffage.
2.1. Presses manuelles
Les presses manuelles sont actionnées par l’utilisateur à l’aide d’un levier ou d’une manivelle pour générer la pression nécessaire. Elles sont souvent utilisées pour des applications simples ou lorsque le budget est limité, car elles sont plus économiques et faciles à entretenir.
- Avantages : Facilité d’utilisation, coût faible, entretien minimal.
- Inconvénients : Moins de précision, application de la pression moins constante, et effort manuel nécessaire.
Les presses manuelles sont souvent utilisées dans les petits laboratoires ou pour des expériences où une précision extrême n’est pas requise.
2.2. Presses hydrauliques
Les presses hydrauliques sont parmi les plus couramment utilisées dans les laboratoires. Elles fonctionnent grâce à un système hydraulique qui utilise un fluide (généralement de l’huile) pour exercer une pression sur l’échantillon.
- Avantages : Excellente capacité de pression, application uniforme de la force, grande précision. Elles peuvent générer des forces très élevées (jusqu’à plusieurs centaines de tonnes).
- Inconvénients : Coût plus élevé que les presses manuelles, besoin d’entretien régulier du système hydraulique.
Les presses hydrauliques sont essentielles dans les environnements où des forces élevées et une grande précision sont nécessaires, comme dans le moulage de polymères ou les tests de matériaux durs.
2.3. Presses automatiques
Les presses automatiques offrent un contrôle précis et programmable de la pression, ainsi que des cycles de pressage complexes. Elles sont équipées de capteurs et de systèmes électroniques qui permettent de programmer des paramètres tels que la force appliquée, la température, et la durée du pressage.
- Avantages : Grande précision, capacité à programmer des cycles complexes, automatisation réduisant l’intervention humaine, pression constante et reproductibilité accrue.
- Inconvénients : Coût élevé, besoin de formation technique pour l’utilisation et la maintenance.
Ces presses sont couramment utilisées dans les laboratoires de recherche et les environnements de production où la reproductibilité et l’efficacité sont cruciales.
2.4. Presses à chaud
Les presses à chaud disposent de plaques chauffantes qui permettent de chauffer l’échantillon pendant le processus de pressage. Elles sont largement utilisées pour des matériaux nécessitant de la chaleur pour se déformer ou réagir, comme les polymères thermoplastiques et les composites.
- Avantages : Permet le formage et la consolidation de matériaux sous pression et chaleur, idéale pour la fabrication de composites et le moulage de polymères.
- Inconvénients : Coût et complexité plus élevés en raison du système de chauffage, et entretien plus fréquent nécessaire.
2.5. Presses à vide
Les presses à vide permettent d’éliminer l’air autour de l’échantillon avant et pendant la compression, ce qui est essentiel pour éviter la formation de bulles ou de contaminations. Elles sont souvent utilisées dans la fabrication de dispositifs électroniques ou pour le moulage de matériaux sensibles à l’oxygène.
- Avantages : Élimine l’air et prévient la contamination, idéal pour les matériaux sensibles ou la fabrication de composants électroniques.
- Inconvénients : Complexité et coût plus élevés, nécessite un entretien spécifique du système de vide.
3. Fonctionnement d’une presse de laboratoire
Le fonctionnement d’une presse de laboratoire repose sur des principes mécaniques et, parfois, hydrauliques. Ces appareils appliquent une pression contrôlée sur un échantillon pour modifier ses propriétés physiques ou pour le préparer à une analyse ou à une étape de production.
3.1. Étapes de base du pressage
Le processus de pressage dans un laboratoire suit généralement ces étapes :
- Préparation de l’échantillon : L’échantillon est préparé et placé entre les plaques de compression.
- Positionnement dans la presse : L’échantillon est soigneusement centré dans la presse pour garantir une application uniforme de la pression.
- Application de la pression : La presse est activée pour appliquer la pression prédéfinie. Dans le cas des presses automatiques, la pression, la température, et la durée du pressage sont programmées à l’avance.
- Maintien de la pression : Une fois la pression atteinte, elle est maintenue pendant la durée nécessaire pour que le processus souhaité se déroule (comme la compression ou la polymérisation).
- Relâchement de la pression : La pression est ensuite relâchée de manière contrôlée pour éviter de brusques changements qui pourraient endommager l’échantillon.
- Retrait de l’échantillon : L’échantillon est retiré et inspecté pour vérifier que les objectifs du pressage ont été atteints.
3.2. Variables critiques à contrôler
Lors de l’utilisation d’une presse de laboratoire, il est essentiel de contrôler plusieurs variables pour assurer la réussite du processus.
- Pression : La pression appliquée doit être précise et uniforme pour garantir des résultats homogènes. Elle est mesurée en tonnes ou en pascals (Pa).
- Température (pour les presses à chaud) : La température doit être rigoureusement contrôlée, surtout dans les processus impliquant des matériaux thermosensibles ou des réactions chimiques.
- Durée de pressage : Le temps pendant lequel la pression est appliquée est une variable critique qui peut affecter les propriétés mécaniques de l’échantillon. Une pression trop longue ou trop courte peut produire des résultats sous-optimaux.
- Taux de relâchement de la pression : Un relâchement trop rapide peut entraîner des fissures ou des déformations, en particulier pour les matériaux fragiles ou composites.
4. Applications des presses de laboratoire
Les presses de laboratoire trouvent des applications dans de nombreux secteurs, notamment dans l’industrie pharmaceutique, la recherche sur les matériaux, la chimie, l’électronique et les biotechnologies.
4.1. Secteur pharmaceutique
Dans l’industrie pharmaceutique, les presses de laboratoire sont cruciales pour la fabrication de comprimés solides et pour tester la stabilité des formulations. Elles sont également utilisées dans la recherche sur la libération prolongée des médicaments et dans le contrôle qualité des produits finis.
4.2. Recherche sur les matériaux
Dans le domaine des matériaux, les presses sont utilisées pour former et tester des échantillons de polymères, de composites, de métaux, et de céramiques. Elles sont indispensables pour étudier les propriétés mécaniques des matériaux sous pression, ainsi que pour les tests de résistance, de dureté, et de durabilité.
4.3. Industrie chimique
Les presses sont utilisées pour la compression de catalyseurs, la préparation d’échantillons pour analyses chimiques, et pour tester la stabilité des formulations chimiques sous différentes conditions de pression et de température.
4.4. Biotechnologie
Dans les biotechnologies, les presses sont utilisées pour préparer des échantillons biologiques à analyser, ainsi que pour compacter des matériaux biocompatibles qui serviront à la fabrication de dispositifs médicaux.
4.5. Industrie alimentaire
Dans l’industrie alimentaire, les presses de laboratoire sont utilisées pour compacter des aliments ou pour extraire des composants tels que les huiles ou les jus.
5. Innovations et tendances dans les presses de laboratoire
L’innovation dans les presses de laboratoire se concentre principalement sur l’amélioration de la précision, de l’automatisation et de la connectivité. Voici quelques-unes des tendances récentes dans ce domaine.
5.1. Intégration de l’Internet des objets (IoT)
Les presses de laboratoire modernes intègrent des capteurs et des systèmes de contrôle connectés à des réseaux. Cela permet un suivi en temps réel des paramètres de pression et de température, ainsi que la maintenance prédictive des appareils.
5.2. Presses éco-énergétiques
Les presses sont de plus en plus conçues pour minimiser la consommation d’énergie, notamment en récupérant la chaleur générée par le processus de pressage. Cela répond à la demande croissante pour des équipements plus écologiques dans les laboratoires.
5.3. Presses intelligentes et automatisées
Les nouvelles générations de presses automatiques permettent de programmer des cycles complexes et d’ajuster automatiquement les paramètres en fonction des données collectées lors des expériences précédentes. Elles offrent également une interface utilisateur intuitive pour simplifier les opérations.
5.4. Utilisation de matériaux durables
Les presses modernes sont fabriquées avec des matériaux plus durables et résistants à l’usure, ce qui augmente leur longévité tout en réduisant les coûts d’entretien.
6. Avantages et limites des presses de laboratoire
6.1. Avantages
- Précision : Les presses modernes permettent de contrôler précisément la pression, la température, et la durée du pressage, garantissant des résultats cohérents.
- Polyvalence : Elles peuvent être utilisées pour une variété de matériaux et d’applications, allant de la fabrication de comprimés à la consolidation de matériaux composites.
- Automatisation : Les presses automatiques permettent de réduire l’intervention humaine, ce qui améliore la reproductibilité des expériences et la productivité.
6.2. Limites
- Coût : Les presses, en particulier les modèles hydrauliques ou automatiques, peuvent être coûteuses, et leur entretien peut représenter un investissement important.
- Complexité d’utilisation : Certaines presses nécessitent une formation spécifique pour être utilisées correctement, et leur configuration peut prendre du temps.
- Maintenance : Les presses doivent être entretenues régulièrement pour éviter les pannes et garantir une pression précise. Cela est particulièrement vrai pour les presses hydrauliques ou à vide.
Conclusion
Les presses de laboratoire sont des outils incontournables dans les environnements scientifiques et industriels. Elles permettent de réaliser une multitude de tâches, allant de la compression de poudres et la fabrication de matériaux composites à la préparation d’échantillons pour des analyses. Grâce à leur capacité à appliquer des pressions précises et contrôlées, ces appareils jouent un rôle crucial dans de nombreux secteurs, notamment la pharmacie, la recherche sur les matériaux, la chimie et les biotechnologies.
Qu’est-ce qu’une presse de laboratoire ?
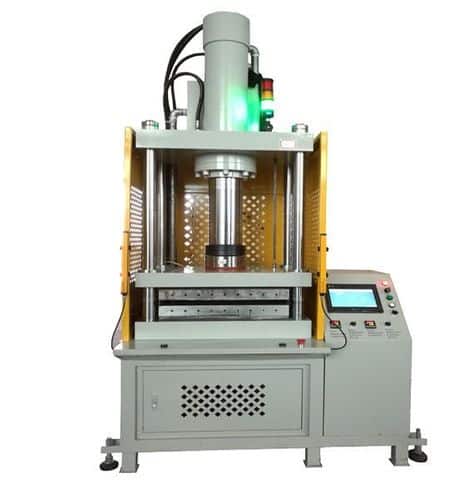
Une presse de laboratoire est un appareil conçu pour appliquer une pression contrôlée sur un échantillon dans le but de le compresser, de le former, ou de le transformer, généralement pour des recherches scientifiques, des analyses ou des procédés industriels. Utilisées dans une large gamme de domaines, notamment la chimie, la science des matériaux, la pharmacie, et l’électronique, les presses de laboratoire jouent un rôle clé dans des processus où la précision et la répétabilité sont cruciales.
Ces machines peuvent appliquer des forces qui varient de quelques kilos à plusieurs centaines de tonnes, selon le type de presse et les besoins spécifiques. Elles sont souvent utilisées pour :
- Compacter des poudres : par exemple, pour transformer des poudres en comprimés ou pastilles.
- Mouler des matériaux : comme les polymères ou les composites.
- Tester des matériaux : en évaluant leur résistance ou leur déformation sous pression.
- Préparer des échantillons pour des analyses physiques, chimiques ou spectroscopiques.
Fonctionnalité principale : l’application de la pression
L’objectif principal d’une presse de laboratoire est d’appliquer une pression uniforme sur un échantillon placé entre des plaques de compression. Cette pression peut être exercée de différentes manières, selon le type de presse (manuel, hydraulique, automatique), et peut être combinée à d’autres paramètres tels que la chaleur (dans les presses à chaud).
- Pression contrôlée : Les presses de laboratoire permettent un contrôle précis de la pression appliquée sur l’échantillon, souvent mesurée en tonnes ou en pascals (Pa), afin de répondre aux exigences spécifiques des processus expérimentaux ou industriels.
- Paramètres programmables : Dans les presses automatiques, les utilisateurs peuvent définir des cycles de pressage avec des paramètres programmables comme la durée, la pression, et la température.
Types de presses de laboratoire
Les presses de laboratoire se déclinent en plusieurs types en fonction des méthodes utilisées pour générer la pression et des spécificités liées à chaque application. Les principaux types incluent :
- Presses manuelles : Utilisées pour des applications simples, elles nécessitent l’intervention directe de l’utilisateur pour appliquer la pression à l’aide d’un levier.
- Presses hydrauliques : Elles utilisent un système hydraulique pour générer une pression plus importante et plus uniforme, sans effort manuel.
- Presses automatiques : Ces presses permettent une programmation complète et sont capables de maintenir une pression précise et stable pendant une durée déterminée, avec un contrôle électronique intégré.
- Presses à chaud : Équipées de plaques chauffantes, elles appliquent de la chaleur en plus de la pression, ce qui est particulièrement utile pour des matériaux comme les polymères qui nécessitent une température élevée pour être formés ou consolidés.
- Presses à vide : Elles permettent d’éliminer l’air et les gaz avant de compresser l’échantillon, utile dans la fabrication de composants électroniques ou pour des matériaux sensibles à l’oxygène.
Applications courantes
Les presses de laboratoire sont utilisées dans de nombreux secteurs industriels et scientifiques pour répondre à des besoins variés :
- Industrie pharmaceutique : Les presses sont utilisées pour comprimer des poudres afin de fabriquer des comprimés solides, en garantissant une dose précise et une stabilité mécanique.
- Science des matériaux : Elles permettent de mouler et de tester des matériaux comme les polymères, les métaux, et les céramiques, en étudiant leur comportement sous pression.
- Recherche chimique : Elles servent à compacter des échantillons pour des analyses chimiques ou physiques, et à tester la stabilité des formulations sous pression.
- Électronique : Les presses à chaud et à vide sont utilisées pour fabriquer des composants électroniques tels que les circuits imprimés multicouches ou des électrodes pour batteries.
Évolution des presses de laboratoire
Les presses de laboratoire ont considérablement évolué au fil du temps, en passant des simples dispositifs manuels à des équipements automatisés et programmables dotés de technologies avancées. L’intégration de systèmes intelligents et de capteurs permet aujourd’hui un contrôle en temps réel des paramètres tels que la pression et la température, garantissant des résultats plus précis et reproductibles.
Les presses modernes sont également équipées de systèmes de sécurité et de verrouillage pour protéger les opérateurs, en particulier lors de l’utilisation de fortes pressions ou de températures élevées.
Conclusion
En résumé, une presse de laboratoire est un outil essentiel dans de nombreux domaines pour appliquer une pression précise et contrôlée à des matériaux variés, qu’il s’agisse de compacter des poudres, de tester la résistance des matériaux, ou de former des échantillons pour des analyses ultérieures. Grâce à leur polyvalence et à leurs performances, elles occupent une place centrale dans les laboratoires de recherche et les processus de fabrication industrielle.
Types de presses de laboratoire
Les presses de laboratoire sont des équipements variés conçus pour appliquer une pression contrôlée sur des matériaux à des fins spécifiques. En fonction des besoins et des applications, plusieurs types de presses sont disponibles, chacune avec ses caractéristiques, avantages, et inconvénients. Ces presses peuvent être classées en fonction de leur mécanisme d’action, de leur niveau d’automatisation, de l’utilisation de chaleur ou de vide, ainsi que des matériaux pour lesquels elles sont adaptées.
Presses manuelles
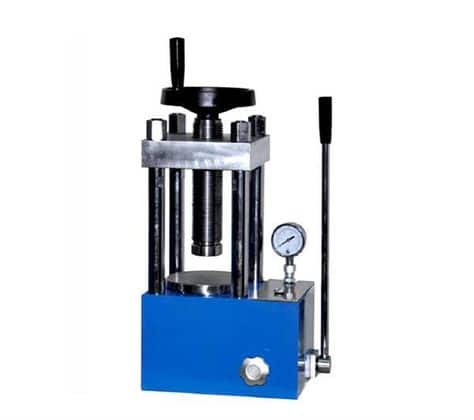
Les presses manuelles sont des dispositifs simples qui nécessitent une intervention humaine pour générer et appliquer la pression à l’aide d’un levier ou d’une manivelle. Ces presses sont utilisées dans des applications qui ne nécessitent pas des niveaux de pression très élevés ou un contrôle complexe.
1.1. Fonctionnement
Les presses manuelles fonctionnent par un mécanisme mécanique qui utilise la force appliquée manuellement pour comprimer l’échantillon. L’opérateur ajuste la pression en manipulant le levier jusqu’à ce que l’échantillon atteigne la densité ou la forme désirée.
1.2. Applications
- Compression de petites quantités de matériaux : Les presses manuelles sont idéales pour des expériences à petite échelle où l’application de la pression peut être gérée de manière directe par l’opérateur.
- Laboratoires pédagogiques : Elles sont souvent utilisées dans des environnements éducatifs ou des laboratoires de recherche pour enseigner les principes de base du pressage sans investissement lourd.
1.3. Avantages
- Coût faible : Les presses manuelles sont généralement moins coûteuses à l’achat que leurs homologues automatiques ou hydrauliques.
- Simplicité d’utilisation : Elles ne nécessitent pas de formation spécifique ou de compétences techniques poussées.
- Portabilité : Leur petite taille et leur faible poids permettent de les déplacer facilement entre différents postes de travail.
1.4. Inconvénients
- Manque de précision : La force appliquée dépend de la constance et de la force de l’opérateur, ce qui peut entraîner des variations dans les résultats.
- Limitation de la pression : Elles sont moins adaptées aux applications nécessitant des pressions élevées ou une pression constante sur une longue durée.
Presses hydrauliques
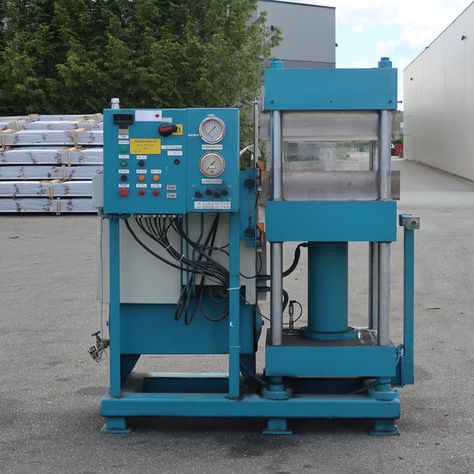
Les presses hydrauliques utilisent un système hydraulique pour générer et appliquer la pression. Un fluide hydraulique (souvent de l’huile) est pompé dans un cylindre pour créer une force qui applique une pression sur l’échantillon. Ce type de presse est couramment utilisé dans les laboratoires où des pressions plus élevées sont nécessaires.
2.1. Fonctionnement
Les presses hydrauliques fonctionnent en utilisant un piston actionné par un fluide sous pression. La force est appliquée de manière constante et homogène, ce qui permet d’obtenir des résultats reproductibles et précis. L’opérateur peut ajuster la pression en réglant la pompe hydraulique.
2.2. Applications
- Compression de matériaux à haute pression : Ces presses sont idéales pour les matériaux nécessitant de fortes pressions, comme les métaux ou les céramiques.
- Fabrication de composants solides : Elles sont largement utilisées pour compacter des poudres métalliques, fabriquer des matériaux composites ou presser des échantillons de matériaux résistants.
2.3. Avantages
- Grande capacité de pression : Elles peuvent générer des pressions très élevées, souvent nécessaires pour les matériaux durs et les processus industriels complexes.
- Précision accrue : Le système hydraulique assure une pression constante et uniformément répartie, ce qui garantit une grande reproductibilité des résultats.
- Polyvalence : Elles peuvent être utilisées pour une large gamme d’applications et de matériaux.
2.4. Inconvénients
- Coût plus élevé : Les presses hydrauliques sont plus coûteuses que les presses manuelles, en raison de leur technologie plus avancée.
- Entretien nécessaire : Le système hydraulique nécessite un entretien régulier pour éviter les fuites et garantir une pression précise.
Presses automatiques
Les presses automatiques sont équipées de systèmes électroniques qui permettent de programmer les cycles de pressage avec un contrôle précis et automatisé de la pression, de la température (si nécessaire) et du temps de compression. Elles sont largement utilisées dans les environnements de recherche ou industriels où la répétabilité et la précision sont essentielles.
3.1. Fonctionnement
Les presses automatiques sont entièrement programmables. L’utilisateur peut définir des cycles spécifiques avec des paramètres prédéfinis de pression, de durée et, dans certains cas, de température. Ces presses sont souvent équipées de capteurs qui surveillent en temps réel les conditions du processus de pressage.
3.2. Applications
- Fabrication de matériaux composites : Les cycles programmés permettent de compresser des matériaux composites de manière précise, en ajustant les paramètres de manière optimale pour la fabrication de composants.
- Recherche scientifique : Elles sont utilisées dans des laboratoires où des cycles répétitifs et une haute précision sont nécessaires, notamment dans la recherche sur les polymères et les métaux.
3.3. Avantages
- Précision extrême : Les presses automatiques garantissent une grande répétabilité des résultats grâce à des paramètres programmables qui assurent un contrôle rigoureux de la pression, du temps et de la température.
- Facilité d’utilisation : Une fois programmées, ces presses peuvent fonctionner de manière autonome, ce qui réduit la nécessité d’une surveillance constante par l’opérateur.
- Reproductibilité : Elles offrent une grande reproductibilité, ce qui est essentiel dans les environnements de recherche où des résultats cohérents sont requis.
3.4. Inconvénients
- Coût élevé : Les presses automatiques sont plus coûteuses à l’achat et à l’entretien, en raison de leur technologie avancée.
- Formation nécessaire : Leur utilisation nécessite une formation technique, en particulier pour la programmation des cycles et la maintenance des systèmes électroniques.
Presses à chaud
Les presses à chaud sont équipées de plaques chauffantes qui permettent d’appliquer de la chaleur en plus de la pression. Ces presses sont particulièrement utiles dans les processus qui nécessitent une combinaison de chaleur et de pression, tels que le formage des polymères, la consolidation de matériaux composites, ou l’activation de réactions chimiques.
4.1. Fonctionnement
Les presses à chaud combinent pression et chaleur pour faciliter la transformation des matériaux. La température est contrôlée via un thermostat intégré, et les plaques chauffantes peuvent atteindre plusieurs centaines de degrés Celsius. L’échantillon est placé entre les plaques, où il subit à la fois une compression et une montée en température.
4.2. Applications
- Moulage des polymères thermoplastiques : Ces presses sont couramment utilisées pour mouler des polymères sous l’effet de la chaleur, ce qui permet de créer des pièces solides ou des films fins.
- Consolidation de matériaux composites : Les matériaux composites, comme les fibres de verre ou de carbone, nécessitent souvent un pressage sous chaleur pour permettre à la résine de durcir et de former une structure solide.
4.3. Avantages
- Transformation thermique : Les presses à chaud permettent d’activer des réactions chimiques ou des transformations physiques qui ne seraient pas possibles uniquement avec de la pression.
- Polyvalence : Elles sont largement utilisées dans l’industrie des plastiques, des composites, et même de la microélectronique pour fabriquer des dispositifs sous pression et chaleur.
4.4. Inconvénients
- Complexité : Elles nécessitent un contrôle précis de la température et de la pression, et leur utilisation peut être plus complexe que celle des presses à froid.
- Entretien : Le système de chauffage et les plaques chauffantes nécessitent un entretien régulier pour garantir une performance optimale.
Presses à froid
Les presses à froid sont conçues pour appliquer une pression à température ambiante, sans chauffer l’échantillon. Elles sont utilisées dans les applications où la chaleur pourrait altérer ou dégrader le matériau ou lorsque la chaleur n’est tout simplement pas nécessaire.
5.1. Fonctionnement
Les presses à froid fonctionnent comme les autres types de presses mais sans utiliser de système de chauffage. La pression est appliquée via un système hydraulique, manuel ou automatique, et maintenue à une température ambiante pour préserver l’intégrité thermique des échantillons.
5.2. Applications
- Compression des poudres : Elles sont couramment utilisées dans l’industrie pharmaceutique pour comprimer des poudres de médicaments en comprimés sans modifier leurs propriétés chimiques par la chaleur.
- Tests mécaniques : Les matériaux tels que les métaux ou les plastiques peuvent être testés sous pression pour évaluer leur résistance ou leur déformation sans affecter leur structure chimique.
5.3. Avantages
- Simplicité : Elles sont plus simples à utiliser que les presses à chaud puisqu’il n’est pas nécessaire de gérer un système de chauffage.
- Préservation des matériaux : Elles sont adaptées aux matériaux sensibles à la chaleur ou aux échantillons qui doivent être analysés sans être chauffés.
5.4. Inconvénients
- Transformation limitée : Les presses à froid ne peuvent pas être utilisées pour des matériaux ou des processus qui nécessitent de la chaleur, limitant ainsi leur champ d’application.
Presses à vide
Les presses à vide permettent d’éliminer l’air autour de l’échantillon avant et pendant la compression. Cela est crucial pour éviter l’oxydation, les bulles d’air ou les contaminations par des gaz lors du pressage, notamment dans la fabrication de dispositifs électroniques ou de matériaux très sensibles.
6.1. Fonctionnement
Avant le pressage, un système de vide élimine l’air ou les gaz présents dans la chambre de compression, garantissant un environnement totalement étanche. Ensuite, la pression est appliquée pour compacter l’échantillon sans aucune présence d’air.
6.2. Applications
- Fabrication de dispositifs électroniques : Elles sont utilisées dans la production de composants électroniques où la présence d’air ou d’humidité pourrait altérer la qualité ou la performance des dispositifs.
- Moulage de matériaux sensibles : Les matériaux sensibles à l’oxygène, comme certains métaux ou polymères, peuvent être pressés sans être exposés à l’air pour éviter l’oxydation.
6.3. Avantages
- Prévention des bulles d’air : Elles éliminent les poches d’air qui pourraient affaiblir les matériaux ou compromettre les résultats des expériences.
- Propriétés optimales des matériaux : En éliminant l’air, elles permettent de maintenir les propriétés chimiques et physiques des échantillons sous pression.
6.4. Inconvénients
- Coût élevé : Les systèmes de vide rendent ces presses plus coûteuses que les presses traditionnelles.
- Complexité d’utilisation : Leur manipulation et leur entretien sont plus complexes en raison du besoin de maintenir un environnement sous vide constant.
Conclusion
Les presses de laboratoire, qu’elles soient manuelles, hydrauliques, automatiques, à chaud, à froid, ou à vide, sont des outils essentiels dans une grande variété de secteurs scientifiques et industriels. Chaque type de presse présente des avantages spécifiques en fonction des matériaux et des processus impliqués. Le choix de la presse dépendra donc des exigences techniques, du budget, ainsi que des résultats attendus en termes de précision, de reproductibilité, et de transformation des matériaux.
Applications courantes des presses de laboratoire
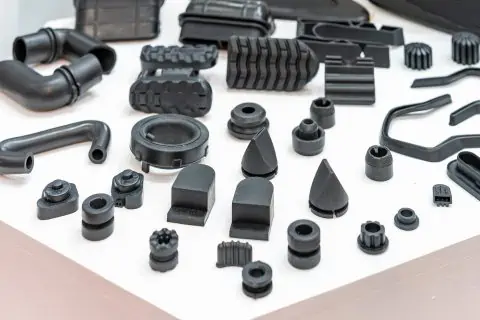
Les presses de laboratoire jouent un rôle fondamental dans divers secteurs industriels et scientifiques. Elles sont utilisées pour tester des matériaux, fabriquer des composants, préparer des échantillons pour des analyses, et effectuer des procédés de transformation. Ces applications se retrouvent dans des domaines variés, allant de la pharmacie à l’électronique, en passant par la science des matériaux et l’industrie chimique. Voici une exploration des applications courantes des presses de laboratoire dans différents secteurs.
1. Secteur pharmaceutique
Dans l’industrie pharmaceutique, les presses de laboratoire sont largement utilisées pour la fabrication et la recherche liées aux formes solides des médicaments, comme les comprimés et les capsules.
1.1. Compression de poudres pour la fabrication de comprimés
La principale utilisation des presses dans le secteur pharmaceutique est la compression des poudres pour fabriquer des comprimés. La presse permet de compacter des poudres de principes actifs et d’excipients sous forme de comprimés uniformes en termes de taille et de densité.
- Fabrication de comprimés : Les poudres de médicaments sont comprimées pour produire des formes solides qui sont faciles à administrer, tout en assurant une homogénéité de dosage.
- Test de formulation : Les presses permettent de tester et d’optimiser les formulations avant leur production à grande échelle, garantissant que les comprimés conservent leur forme et leur efficacité.
1.2. Comprimés à libération contrôlée
Les presses de laboratoire sont utilisées pour créer des comprimés à libération prolongée ou contrôlée. Ces comprimés sont conçus pour libérer le principe actif de manière graduelle sur une période de temps définie, permettant un effet thérapeutique plus long.
- Contrôle de la porosité : Grâce aux presses, la densité et la porosité des comprimés peuvent être contrôlées, ce qui influence la vitesse de libération du médicament.
1.3. Test de résistance et de friabilité
Les comprimés fabriqués sont soumis à des tests de résistance mécanique, où les presses sont utilisées pour appliquer une pression et mesurer la capacité du comprimé à résister à l’écrasement ou à la rupture.
- Test de dureté : Les presses testent la dureté des comprimés pour garantir qu’ils peuvent supporter les conditions de transport et de manipulation sans se briser.
- Test de friabilité : Les comprimés sont également testés pour s’assurer qu’ils ne se désintègrent pas en poudre lorsqu’ils sont soumis à des forces de frottement.
2. Science des matériaux
Dans les laboratoires de recherche sur les matériaux, les presses de laboratoire sont utilisées pour fabriquer des échantillons, tester des matériaux et développer de nouvelles technologies.
2.1. Compression des poudres métalliques et céramiques
Dans la métallurgie des poudres et la fabrication de céramiques, les presses sont utilisées pour compacter des poudres fines en des formes solides avant le processus de frittage ou de cuisson.
- Métallurgie des poudres : Les poudres métalliques sont pressées pour former des pièces compactes qui seront ensuite soumises à un processus de frittage pour obtenir des pièces solides aux propriétés mécaniques comparables à celles des métaux fondus.
- Fabrication de céramiques : Les poudres de céramiques sont compressées dans des moules pour former des formes solides, comme des disques ou des plaques, qui seront ensuite cuites à haute température pour obtenir des pièces céramiques denses.
2.2. Moulage et formage de polymères
Les presses sont couramment utilisées pour transformer des polymères thermoplastiques et créer des pièces ou des films sous pression et chaleur (presses à chaud).
- Moulage de polymères : Les polymères thermoplastiques sont pressés sous haute pression pour obtenir des formes spécifiques. Ce processus est utilisé dans l’industrie des plastiques pour fabriquer des prototypes avant la production à grande échelle.
- Fabrication de composites : Les presses sont utilisées pour fabriquer des matériaux composites en compressant des fibres (comme la fibre de carbone) avec une matrice de résine thermodurcissable, formant des pièces solides et légères utilisées dans l’aéronautique et l’automobile.
2.3. Tests de résistance mécanique
Les presses sont utilisées pour tester la résistance à la compression et la dureté des matériaux tels que les métaux, les polymères, et les composites.
- Test de résistance à la compression : Les matériaux sont soumis à une pression croissante pour évaluer leur résistance avant la rupture, ce qui est crucial dans le développement de nouveaux matériaux ou la validation des matériaux utilisés dans des constructions.
- Test de dureté : Les presses appliquent une pression pour tester la dureté des matériaux, c’est-à-dire leur capacité à résister aux rayures, aux impacts ou à la déformation.
3. Industrie chimique
Dans l’industrie chimique, les presses sont utilisées pour compacter des produits chimiques, préparer des échantillons pour des analyses, et tester la stabilité des formulations.
3.1. Pelletisation des catalyseurs
Les catalyseurs utilisés dans les procédés chimiques sont souvent pressés sous forme de pellets pour améliorer leur efficacité. Les presses permettent de compacter les catalyseurs sous des formes uniformes, augmentant leur surface active et optimisant les réactions chimiques.
- Pelletisation des catalyseurs : Les catalyseurs, sous forme de poudre, sont comprimés en petites pastilles ou pellets pour augmenter leur surface de contact avec les réactifs dans les procédés de raffinage ou de production chimique.
3.2. Préparation d’échantillons pour analyses chimiques
Les presses sont souvent utilisées pour préparer des échantillons en comprimant des poudres chimiques sous forme de pastilles denses et homogènes. Ces pastilles sont ensuite analysées par des techniques comme la spectroscopie infrarouge ou la diffraction des rayons X.
- Compression pour spectroscopie : Les échantillons sont compressés pour obtenir des pastilles transparentes, prêtes pour des analyses spectroscopiques qui permettent de détecter les éléments chimiques présents dans l’échantillon.
3.3. Tests de stabilité des formulations chimiques
Les presses permettent de tester la stabilité mécanique et chimique des formulations sous pression. Cela garantit que les produits chimiques comprimés conservent leur intégrité pendant leur stockage et leur utilisation.
4. Électronique
Dans l’industrie électronique, les presses sont utilisées pour fabriquer des composants électroniques, tels que les circuits imprimés multicouches, ainsi que pour compacter des matériaux destinés aux dispositifs de stockage d’énergie.
4.1. Fabrication de circuits imprimés multicouches
Les presses à chaud et à vide sont utilisées pour laminer des couches de matériaux conducteurs et isolants afin de former des circuits imprimés (PCB) multicouches.
- Laminage sous pression et chaleur : Les différentes couches d’un circuit imprimé sont pressées ensemble sous haute température pour créer des connexions stables et assurer l’intégrité électrique du dispositif.
4.2. Fabrication de composants pour batteries
Les presses sont utilisées dans la fabrication des électrodes pour batteries, où les matériaux actifs des électrodes sont pressés sous haute pression pour améliorer la densité énergétique et la performance des batteries.
- Pressage des électrodes : Les matériaux conducteurs sont compressés pour former des électrodes fines et denses, essentielles pour les batteries au lithium-ion et autres dispositifs de stockage d’énergie.
5. Biotechnologie
Dans le domaine de la biotechnologie, les presses sont utilisées pour la préparation d’échantillons biologiques, ainsi que pour la fabrication de dispositifs médicaux et d’implants biocompatibles.
5.1. Préparation d’échantillons biologiques
Les presses de laboratoire sont souvent utilisées pour compacter des échantillons biologiques, tels que des tissus ou des cellules, en pastilles denses qui seront ensuite analysées par des méthodes telles que la spectrométrie ou la chromatographie.
- Pressage pour spectrométrie : Les échantillons biologiques peuvent être compressés pour être analysés par des techniques de spectrométrie, permettant de détecter et quantifier des biomolécules.
5.2. Fabrication de dispositifs biomédicaux
Les matériaux biocompatibles sont compressés à l’aide de presses pour former des dispositifs médicaux ou des implants, comme les prothèses ou les supports osseux.
- Pressage de biomatériaux : Les presses permettent de transformer des matériaux biocompatibles, tels que les polymères ou les céramiques bioactives, en dispositifs médicaux stériles et fonctionnels.
6. Industrie alimentaire
Les presses de laboratoire sont également utilisées dans l’industrie alimentaire pour compacter des produits alimentaires ou extraire des huiles et des jus à partir de matières premières.
6.1. Compression des produits alimentaires
Les presses sont utilisées pour former des comprimés alimentaires ou des galettes à partir de poudres de nutriments ou de compléments alimentaires, facilitant ainsi la consommation et le dosage.
- Comprimés alimentaires : Les poudres de vitamines, de minéraux ou de suppléments sont comprimées en comprimés solides, ce qui permet de les conditionner de manière pratique.
6.2. Extraction de jus et d’huiles
Les presses à froid sont utilisées pour extraire des huiles végétales ou des jus de fruits sans chauffer les matières premières, préservant ainsi leurs qualités nutritionnelles et organoleptiques.
- Extraction à froid : L’extraction à froid permet de conserver les propriétés nutritionnelles des huiles, comme l’huile d’olive ou de noix, en évitant la dégradation due à la chaleur.
Conclusion
Les presses de laboratoire sont des outils polyvalents, indispensables dans de nombreux secteurs industriels et scientifiques. De la compression des poudres pharmaceutiques à la fabrication de matériaux composites ou de composants électroniques, elles offrent une grande flexibilité et précision pour répondre aux exigences variées des différents domaines d’application. Leur rôle est fondamental pour la recherche, la production et l’analyse, contribuant ainsi à l’innovation technologique et à l’amélioration des processus industriels.
Presses hydrauliques de laboratoire
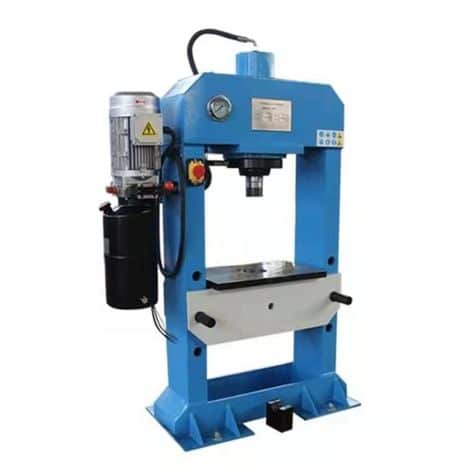
Les presses hydrauliques sont des équipements largement utilisés dans les laboratoires et les industries en raison de leur capacité à générer des forces importantes et à appliquer une pression de manière précise et constante. Ces presses exploitent la puissance des fluides hydrauliques pour comprimer, façonner ou tester divers matériaux, et sont adaptées à une grande variété d’applications, de la métallurgie des poudres à la fabrication de composites, en passant par les tests de résistance mécanique.
1. Principe de fonctionnement d’une presse hydraulique
Le fonctionnement d’une presse hydraulique repose sur le principe de Pascal, selon lequel une pression appliquée sur un fluide incompressible est transmise uniformément dans toutes les directions. Ce principe permet à un système hydraulique de multiplier la force initiale et de l’appliquer sur un échantillon via un piston.
1.1. Système hydraulique
Les presses hydrauliques se composent de plusieurs éléments essentiels qui travaillent ensemble pour générer et contrôler la pression exercée sur l’échantillon :
- Cylindre et piston : Le cœur de la presse hydraulique est le cylindre dans lequel se trouve un piston. Lorsque l’huile hydraulique est pompée dans le cylindre, elle pousse le piston vers le bas, ce qui applique une pression sur l’échantillon placé entre les plaques de compression.
- Pompe hydraulique : Cette pompe est utilisée pour déplacer le fluide (généralement de l’huile) à haute pression vers le cylindre. La force de pression est déterminée par la pression de l’huile et la surface du piston.
- Réservoir de fluide : Le fluide hydraulique est stocké dans un réservoir, puis pompé dans le système lorsque la presse est activée.
- Manomètre et régulateur de pression : Ces composants permettent de mesurer et de contrôler la pression exercée sur l’échantillon, garantissant que la pression appliquée est exacte et constante pendant toute la durée du processus.
1.2. Application de la pression
Lorsque la pompe pousse le fluide dans le cylindre, la pression exercée sur le piston est transmise aux plaques de compression qui appliquent la force directement sur l’échantillon. La pression peut être ajustée en fonction des besoins, et dans les presses hydrauliques modernes, elle est souvent régulée automatiquement pour garantir une constance et une précision optimales.
1.3. Relâchement de la pression
Une fois le processus de pressage terminé, la pression est relâchée de manière contrôlée pour éviter d’endommager l’échantillon. Le fluide hydraulique est renvoyé dans le réservoir, permettant au piston de remonter et de libérer l’échantillon.
2. Avantages des presses hydrauliques
Les presses hydrauliques présentent plusieurs avantages par rapport aux autres types de presses (manuelles ou mécaniques), ce qui explique leur utilisation répandue dans les environnements de laboratoire et industriels.
2.1. Capacité à générer des pressions élevées
Les presses hydrauliques sont capables de générer des forces très importantes, généralement supérieures à celles des presses manuelles ou mécaniques. Elles peuvent appliquer des pressions allant de quelques tonnes à plusieurs centaines de tonnes, selon la taille et la puissance de la machine. Cela permet de compresser des matériaux très résistants comme les métaux, les composites ou les céramiques.
- Pressions élevées : Les presses hydrauliques sont idéales pour les matériaux qui nécessitent une pression extrême pour être compressés ou testés.
2.2. Application uniforme et précise de la pression
L’un des principaux atouts des presses hydrauliques est leur capacité à appliquer une pression uniforme sur toute la surface de l’échantillon. Grâce au fluide hydraulique, la force est distribuée de manière homogène, ce qui est crucial pour garantir l’uniformité du matériau compressé.
- Répartition homogène de la pression : Cela est particulièrement important pour les tests de matériaux ou la fabrication de composants qui nécessitent une uniformité de densité et de structure.
2.3. Contrôle de la pression
Les presses hydrauliques offrent un contrôle précis de la pression appliquée, souvent régulé par un manomètre et un système de commande électronique. Cela permet d’ajuster la pression en fonction des besoins spécifiques, avec une grande précision.
- Pression contrôlée : Le contrôle permet d’appliquer une pression stable pendant la durée du processus, avec la possibilité d’ajuster en temps réel selon l’évolution du comportement de l’échantillon.
2.4. Polyvalence
Les presses hydrauliques sont extrêmement polyvalentes et peuvent être utilisées pour une variété d’applications, y compris le formage de matériaux, la compression de poudres, les tests de résistance mécanique, et la fabrication de composants à petite échelle.
3. Applications des presses hydrauliques
Les presses hydrauliques sont utilisées dans de nombreux secteurs industriels et scientifiques. Voici quelques-unes des applications courantes de ces presses dans différents domaines :
3.1. Métallurgie des poudres et fabrication de céramiques
Les presses hydrauliques sont largement utilisées dans la métallurgie des poudres et la fabrication de céramiques, où elles permettent de comprimer des poudres métalliques ou céramiques en des formes compactes avant un processus de frittage ou de cuisson.
- Compaction des poudres : Les poudres métalliques sont compressées sous haute pression pour créer des pièces solides qui sont ensuite chauffées pour obtenir leur résistance mécanique finale.
- Fabrication de céramiques : Des presses hydrauliques sont utilisées pour former des pièces de céramique compactes qui sont ensuite cuites pour créer des objets solides tels que des plaques ou des disques.
3.2. Moulage et formage de polymères
Dans l’industrie des polymères et des matériaux composites, les presses hydrauliques sont utilisées pour mouler et former des matériaux sous pression. Cela permet de créer des pièces complexes ou de consolider des matériaux composites.
- Moulage de polymères thermoplastiques : Les polymères sont pressés sous haute pression pour prendre la forme de moules et créer des pièces ou des films.
- Consolidation de matériaux composites : Les presses hydrauliques sont utilisées pour combiner des fibres (comme la fibre de carbone ou de verre) avec des résines pour créer des matériaux composites solides et légers, utilisés dans des secteurs tels que l’aéronautique et l’automobile.
3.3. Tests de résistance et de dureté des matériaux
Les presses hydrauliques sont souvent utilisées pour évaluer la résistance mécanique des matériaux, en simulant des conditions de stress ou de compression auxquelles ces matériaux seront soumis dans leur usage final.
- Tests de compression : Les matériaux sont soumis à une pression croissante pour mesurer leur résistance avant leur rupture.
- Tests de dureté : Ces presses peuvent être utilisées pour mesurer la dureté des matériaux, en appliquant une pression définie et en observant la déformation.
3.4. Compression de poudres pharmaceutiques
Dans l’industrie pharmaceutique, les presses hydrauliques sont utilisées pour compresser des poudres de médicaments afin de former des comprimés solides.
- Fabrication de comprimés : Les poudres de médicaments sont compactées pour former des comprimés qui sont homogènes en taille, forme, et dosage, ce qui est essentiel pour garantir l’efficacité du médicament.
4. Limites des presses hydrauliques
Bien que les presses hydrauliques soient extrêmement utiles et polyvalentes, elles présentent également certaines limites qu’il convient de prendre en compte.
4.1. Entretien régulier
Le système hydraulique nécessite un entretien régulier pour garantir que la presse fonctionne de manière optimale. Cela inclut la vérification des fuites d’huile, le nettoyage des conduites, et le remplacement des joints et des filtres.
- Fuites de fluide hydraulique : Les fuites peuvent entraîner une perte de pression et endommager la machine.
4.2. Coût d’acquisition et d’entretien
Les presses hydrauliques sont généralement plus coûteuses à l’achat et à l’entretien par rapport aux presses manuelles ou mécaniques. Le système hydraulique, avec ses composants spécifiques comme les pompes et les pistons, augmente les coûts globaux.
4.3. Température du fluide hydraulique
Lors d’une utilisation prolongée ou intensive, la température du fluide hydraulique peut augmenter, ce qui peut affecter les performances de la presse si le fluide devient trop chaud. Un système de refroidissement peut être nécessaire pour éviter cette surchauffe.
5. Presses hydrauliques automatiques et avancées
Les presses hydrauliques modernes intègrent souvent des systèmes automatisés et des capteurs qui permettent un contrôle encore plus précis du processus de pressage. Ces presses automatiques peuvent être programmées pour réaliser des cycles complexes, où la pression est appliquée à différents niveaux pendant des périodes spécifiques.
5.1. Automatisation et programmabilité
Les presses hydrauliques automatiques permettent de programmer les cycles de pressage pour une précision optimale. Les utilisateurs peuvent définir des paramètres programmables, tels que la montée en pression, le maintien de la pression à un certain niveau, et le relâchement de la pression.
- Programmation des cycles : Cela est particulièrement utile dans des environnements de production ou de recherche où des cycles complexes sont nécessaires pour répondre à des exigences spécifiques.
5.2. Intégration de capteurs et de systèmes de surveillance
Les capteurs intégrés permettent de surveiller en temps réel la pression, la température et d’autres paramètres critiques pendant le processus de pressage. Ces systèmes garantissent que les conditions restent constantes et permettent d’effectuer des ajustements si nécessaire.
- Systèmes de rétroaction : Ces systèmes permettent à la presse de s’ajuster automatiquement si des variations de pression ou de température sont détectées, garantissant ainsi des résultats reproductibles et fiables.
Conclusion
Les presses hydrauliques de laboratoire sont des outils indispensables dans de nombreux secteurs, en raison de leur capacité à appliquer une pression élevée de manière précise et constante. Elles sont largement utilisées pour la compression de matériaux, la fabrication de composants, et les tests de résistance. Leur polyvalence et leur capacité à gérer des pressions élevées en font un choix privilégié pour les industries qui nécessitent une application homogène et répétable de la pression.
Cependant, elles nécessitent un entretien régulier pour garantir leur bon fonctionnement, et leur coût est généralement plus élevé que celui des presses manuelles ou mécaniques. Avec l’évolution des technologies automatiques, les presses hydrauliques deviennent de plus en plus performantes et intégrées, ce qui permet une plus grande précision et une meilleure efficacité dans les processus de laboratoire et de production.
EMS Machines de Formage
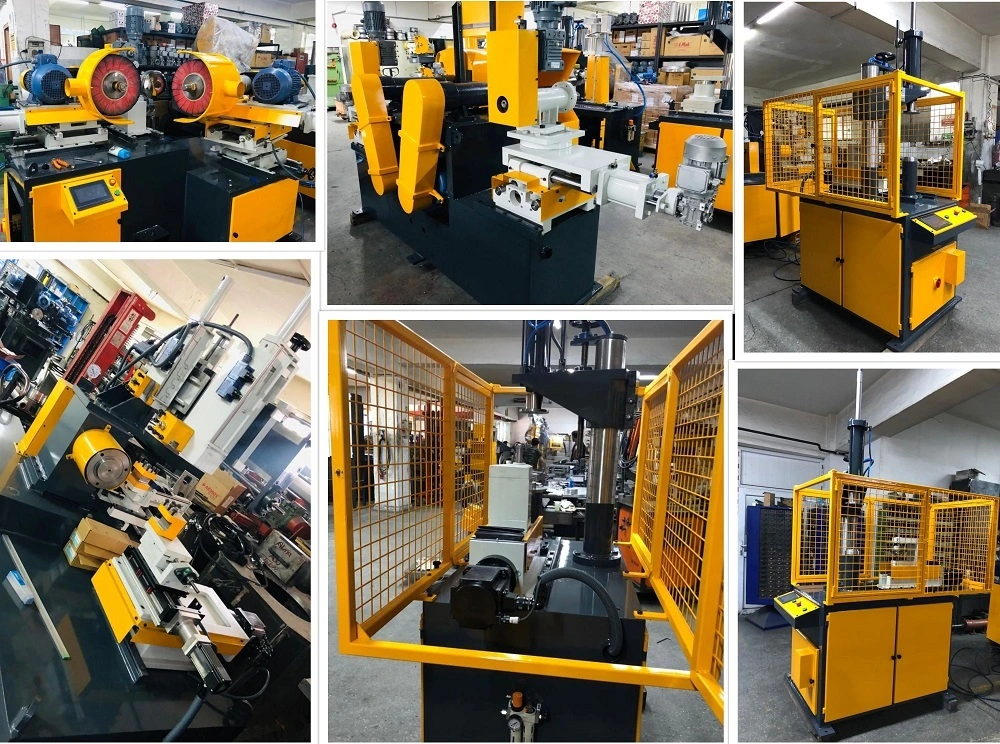
Le formage du métal est un processus consistant à façonner le métal dans la forme et la taille souhaitées à l’aide de diverses techniques. Il s’agit d’un processus crucial dans l’industrie manufacturière car il permet la production de différents produits tels que des pièces automobiles, des composants d’avion, des appareils électroménagers et bien d’autres encore.
Le processus de formage du métal consiste à appliquer une force sur le métal pour changer sa forme sans enlever aucune matière. La force peut être appliquée par diverses méthodes telles que le forgeage, le laminage, l’extrusion, l’étirage et l’estampage. Chaque méthode a ses propres avantages et inconvénients, et le choix de la méthode dépend du matériau formé et de la forme souhaitée.
Le forgeage est l’une des techniques de formage des métaux les plus anciennes. Il s’agit de chauffer le métal à haute température, puis d’appliquer une force de compression à l’aide d’un marteau ou d’une presse pour donner au métal la forme souhaitée. Le forgeage est couramment utilisé pour produire de grandes pièces telles que des engrenages, des essieux et des bielles.
Le laminage est une autre technique de formage du métal qui consiste à faire passer le métal à travers une paire de rouleaux pour réduire son épaisseur ou modifier sa forme. Les rouleaux peuvent être lisses ou texturés selon la finition souhaitée. Le laminage est couramment utilisé pour produire des tôles plates, des plaques et des barres.
L’extrusion est une technique de formage du métal qui consiste à pousser une billette ou une tige métallique à travers une matrice pour créer une forme spécifique. L’extrusion peut être utilisée pour produire des formes complexes telles que des tubes, des canaux et des angles.
L’emboutissage est une technique de formage des métaux utilisée pour réaliser des pièces de forme cylindrique, comme des tubes ou des tuyaux. Le processus consiste à tirer le métal à travers une matrice pour réduire son diamètre et augmenter sa longueur. Le tréfilage est couramment utilisé dans la production de fils, de tiges et de tubes.
L’emboutissage est une technique de formage du métal qui consiste à couper, poinçonner ou plier le métal dans une forme spécifique à l’aide d’une matrice. Le processus peut être utilisé pour produire des pièces avec une grande précision et répétabilité. L’estampage est couramment utilisé dans la production de pièces automobiles, d’appareils électroménagers et d’appareils électroniques.
En plus de ces techniques, il existe de nombreuses autres méthodes de formage des métaux telles que le filage, l’emboutissage profond et l’hydroformage. Chaque méthode a ses propres avantages et inconvénients, et le choix de la méthode dépend des exigences spécifiques du produit fabriqué.
Le formage des métaux est un processus complexe qui nécessite un haut niveau de compétence et d’expertise. Le succès du processus dépend de nombreux facteurs tels que le type de matériau formé, l’équipement utilisé et l’expérience de l’opérateur. En comprenant les différentes techniques de formage des métaux et en choisissant la méthode adaptée au travail, les fabricants peuvent produire des pièces de haute qualité qui répondent aux besoins spécifiques de leurs clients.
EMS Machines de Formage
Le formage du métal est un processus consistant à façonner le métal dans la forme et la taille souhaitées à l’aide de diverses techniques. Il s’agit d’un processus crucial dans l’industrie manufacturière car il permet la production de différents produits tels que des pièces automobiles, des composants d’avion, des appareils électroménagers et bien d’autres encore.
Le processus de formage du métal consiste à appliquer une force sur le métal pour changer sa forme sans enlever aucune matière. La force peut être appliquée par diverses méthodes telles que le forgeage, le laminage, l’extrusion, l’étirage et l’estampage. Chaque méthode a ses propres avantages et inconvénients, et le choix de la méthode dépend du matériau formé et de la forme souhaitée.
Le forgeage est l’une des techniques de formage des métaux les plus anciennes. Il s’agit de chauffer le métal à haute température, puis d’appliquer une force de compression à l’aide d’un marteau ou d’une presse pour donner au métal la forme souhaitée. Le forgeage est couramment utilisé pour produire de grandes pièces telles que des engrenages, des essieux et des bielles.
Le laminage est une autre technique de formage du métal qui consiste à faire passer le métal à travers une paire de rouleaux pour réduire son épaisseur ou modifier sa forme. Les rouleaux peuvent être lisses ou texturés selon la finition souhaitée. Le laminage est couramment utilisé pour produire des tôles plates, des plaques et des barres.
L’extrusion est une technique de formage du métal qui consiste à pousser une billette ou une tige métallique à travers une matrice pour créer une forme spécifique. L’extrusion peut être utilisée pour produire des formes complexes telles que des tubes, des canaux et des angles.
L’emboutissage est une technique de formage des métaux utilisée pour réaliser des pièces de forme cylindrique, comme des tubes ou des tuyaux. Le processus consiste à tirer le métal à travers une matrice pour réduire son diamètre et augmenter sa longueur. Le tréfilage est couramment utilisé dans la production de fils, de tiges et de tubes.
L’emboutissage est une technique de formage du métal qui consiste à couper, poinçonner ou plier le métal dans une forme spécifique à l’aide d’une matrice. Le processus peut être utilisé pour produire des pièces avec une grande précision et répétabilité. L’estampage est couramment utilisé dans la production de pièces automobiles, d’appareils électroménagers et d’appareils électroniques.
En plus de ces techniques, il existe de nombreuses autres méthodes de formage des métaux telles que le filage, l’emboutissage profond et l’hydroformage. Chaque méthode a ses propres avantages et inconvénients, et le choix de la méthode dépend des exigences spécifiques du produit fabriqué.
Le formage des métaux est un processus complexe qui nécessite un haut niveau de compétence et d’expertise. Le succès du processus dépend de nombreux facteurs tels que le type de matériau formé, l’équipement utilisé et l’expérience de l’opérateur. En comprenant les différentes techniques de formage des métaux et en choisissant la méthode adaptée au travail, les fabricants peuvent produire des pièces de haute qualité qui répondent aux besoins spécifiques de leurs clients.