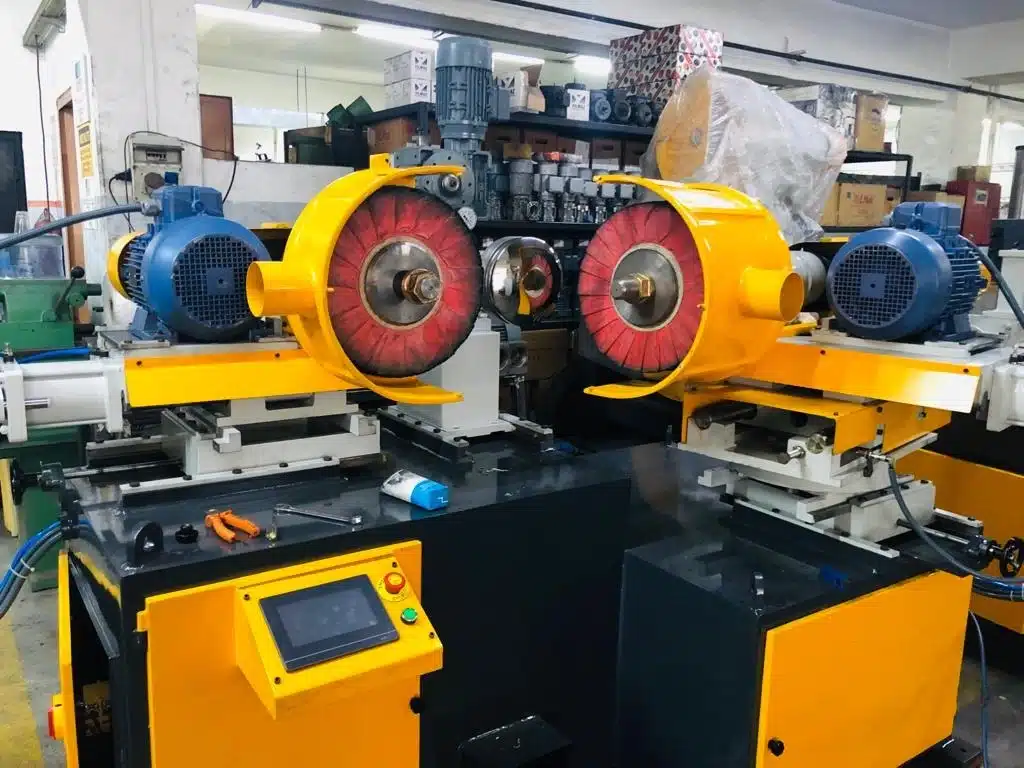
Machine à Polir Professionnel: Les technologies industrielles de transformation des matériaux sont au cœur de l’évolution des secteurs manufacturiers modernes. Parmi ces technologies, les machines de formage et les presses occupent une place centrale dans les processus de fabrication et de production en masse. Ces machines permettent la transformation de matières premières en produits finis ou semi-finis, utilisés dans divers secteurs comme l’automobile, l’aérospatial, l’électroménager, et bien plus encore.
Les avancées technologiques dans ces équipements ont considérablement amélioré la précision, la rapidité et l’efficacité des procédés de production, répondant aux besoins croissants de l’industrie pour des produits de qualité supérieure, à des coûts compétitifs. Que ce soit pour des applications de formage, de découpe, de pliage ou d’emboutissage, ces machines constituent un maillon essentiel dans la chaîne de production industrielle. Dans ce contexte, ce guide vous présente en détail diverses catégories de machines et presses utilisées dans l’industrie métallurgique et manufacturière. Chaque section abordera un type spécifique de machine, ses caractéristiques, ses avantages et ses principales applications.
Le contenu suivant couvre des équipements allant des machines de formage aux presses hydrauliques, en passant par les machines de polissage et d’ébavurage, offrant ainsi une vue d’ensemble complète des technologies disponibles pour la transformation des métaux.
Machine de Formage
Les machines de formage jouent un rôle clé dans la transformation des métaux et d’autres matériaux à travers des procédés mécaniques, thermiques ou hydrauliques. Leur objectif principal est de façonner une pièce en lui donnant une forme prédéfinie, souvent sans enlever de matière, ce qui les distingue des procédés d’usinage ou de découpe.
Fonctionnement des Machines de Formage
Le principe de base d’une machine de formage repose sur l’application d’une force mécanique ou hydraulique pour déformer un matériau, généralement un métal, jusqu’à obtenir la forme désirée. Ce processus peut se dérouler à chaud ou à froid, selon la nature du matériau et le type de formage souhaité. Les machines de formage comprennent diverses catégories d’équipements, chacune adaptée à un type spécifique de transformation, comme le pliage, l’étirage, le cintrage ou le laminage.
Parmi les technologies de formage les plus utilisées, on trouve :
- Le formage à froid : utilisé principalement pour les métaux fins et ductiles, cette technique permet de déformer le matériau à température ambiante sans le chauffer, conservant ainsi ses propriétés mécaniques.
- Le formage à chaud : dans ce cas, le matériau est chauffé au-dessus de sa température de recristallisation, ce qui permet de faciliter sa déformation tout en limitant les contraintes internes.
Types de Machines de Formage
Il existe plusieurs types de machines de formage, en fonction de l’application spécifique :
- Machines de formage par étirage : ces machines sont souvent utilisées pour la production de grandes pièces, comme les panneaux de carrosserie dans l’industrie automobile.
- Machines de formage par pliage : adaptées au pliage de tôles métalliques, ces machines permettent de réaliser des angles précis sur des matériaux rigides.
- Machines de formage par laminage : elles servent principalement à réduire l’épaisseur d’un matériau, tout en augmentant sa longueur, très utilisées dans la production de feuilles de métal.
Avantages des Machines de Formage
Les machines de formage offrent plusieurs avantages dans le processus de fabrication industrielle :
- Efficacité : Elles permettent de transformer rapidement des matières premières en pièces finies ou semi-finies, réduisant ainsi les délais de production.
- Précision : Grâce aux innovations technologiques, ces machines peuvent produire des pièces aux tolérances très précises, même dans des matériaux difficiles à travailler.
- Réduction des pertes de matière : Contrairement à d’autres procédés comme l’usinage, le formage ne produit que très peu de déchets, ce qui en fait un processus plus économique et respectueux de l’environnement.
Applications Industrielles
Les machines de formage sont largement utilisées dans divers secteurs industriels :
- Automobile : pour la fabrication de châssis, de pièces de carrosserie, et autres composants critiques.
- Aéronautique : des pièces complexes et légères, telles que les structures d’aile et les panneaux de fuselage, sont souvent formées à l’aide de ces machines.
- Construction : dans la production de poutres, de barres et d’autres composants structurels utilisés dans les bâtiments et les infrastructures.
Presse à Emboutir

La presse à emboutir est une machine utilisée dans l’industrie pour transformer une feuille de métal en une forme tridimensionnelle complexe, grâce à un processus de déformation appelé emboutissage. Ce procédé est couramment utilisé dans la fabrication de pièces métalliques pour des industries telles que l’automobile, l’aéronautique, et l’électroménager.
Fonctionnement de la Presse à Emboutir
L’emboutissage est un processus de formage à froid, où une feuille métallique, appelée flan, est pressée entre une matrice et un poinçon. Le poinçon descend, déformant la feuille en lui donnant la forme souhaitée, généralement en une seule étape ou à travers une série de coups successifs pour des pièces plus complexes. Ce procédé permet de produire des formes précises et détaillées, souvent avec des géométries qui seraient difficiles, voire impossibles, à obtenir avec d’autres méthodes de fabrication.
Les presses à emboutir peuvent être actionnées mécaniquement, hydrauliquement ou via une combinaison des deux. Les presses hydrauliques sont couramment utilisées pour les opérations d’emboutissage profond, où de grandes forces sont nécessaires pour former des pièces aux formes complexes sans risque de déformation ou de fissuration du matériau.
Types de Presses à Emboutir
Il existe plusieurs types de presses à emboutir, chacune étant adaptée à des applications spécifiques :
- Presse mécanique : Utilisée pour des processus à grande vitesse, elle est plus adaptée à des opérations répétitives où la précision de chaque coup est essentielle.
- Presse hydraulique : Permet de mieux contrôler la pression et est plus adaptée pour les opérations nécessitant une grande force de formage, comme l’emboutissage profond.
- Presse servo-électrique : Combine la précision et le contrôle des presses hydrauliques avec la rapidité des presses mécaniques. Elle est idéale pour les opérations nécessitant à la fois rapidité et précision.
Avantages des Presses à Emboutir
Les presses à emboutir sont largement utilisées dans l’industrie pour plusieurs raisons :
- Productivité élevée : Ces machines permettent la production rapide de pièces complexes, souvent en une seule opération, ce qui augmente considérablement la cadence de fabrication.
- Flexibilité : Elles peuvent traiter une grande variété de matériaux, des métaux plus légers comme l’aluminium aux matériaux plus résistants comme l’acier inoxydable.
- Réduction des coûts : Grâce à leur efficacité et à leur capacité à produire des formes complexes en une seule opération, elles permettent de réduire les coûts de production par pièce, surtout dans les grandes séries.
- Précision et qualité : Les presses à emboutir modernes sont capables de produire des pièces avec des tolérances très serrées, minimisant ainsi les défauts et les rebuts.
Applications des Presses à Emboutir
L’emboutissage est un procédé essentiel dans diverses industries, notamment :
- Automobile : La fabrication des carrosseries de voitures, des portes, des capots, et d’autres pièces structurelles repose largement sur des presses à emboutir. La rapidité de production et la précision sont des atouts majeurs pour ce secteur.
- Aéronautique : Dans ce secteur, des pièces légères et complexes, telles que les carénages et les composants de structure d’aéronefs, sont souvent fabriquées par emboutissage pour assurer des tolérances strictes tout en minimisant le poids.
- Électroménager : Des composants tels que les coques extérieures des machines à laver, les tambours et les panneaux sont fréquemment produits par emboutissage, en raison de la précision et de la vitesse du processus.
Innovations Technologiques
Les presses à emboutir ont connu plusieurs évolutions ces dernières années, avec l’introduction de technologies avancées comme :
- L’emboutissage numérique : Des logiciels de simulation permettent désormais de prévoir et d’optimiser le processus d’emboutissage avant même de commencer la production, réduisant ainsi les erreurs et améliorant la qualité du produit fini.
- Presses à emboutissage automatique : Ces presses automatisées augmentent la cadence de production tout en minimisant les erreurs humaines, ce qui est crucial dans des industries où la précision est primordiale.
- Emboutissage à chaud : Cette technique consiste à chauffer la feuille de métal avant de l’emboutir, ce qui permet de créer des pièces encore plus complexes tout en limitant le risque de fissuration.
Machines à Filer les Métaux
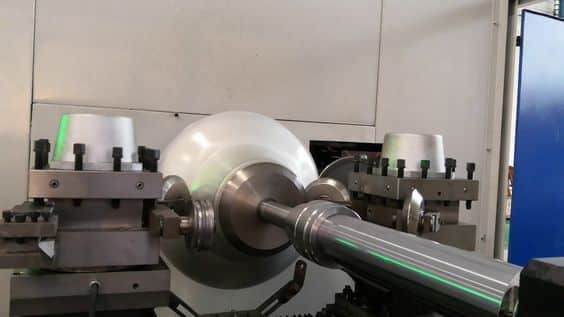
Les machines à filer les métaux sont des équipements industriels spécialisés dans la transformation de métaux à l’aide d’un procédé appelé le filage. Ce procédé consiste à déformer une pièce métallique en la faisant tourner rapidement tout en exerçant une pression contrôlée, permettant ainsi de créer des formes symétriques et précises. Le filage des métaux est utilisé principalement pour la production de pièces de forme cylindrique, conique ou de révolution.
Fonctionnement du Filage des Métaux
Le filage des métaux est un procédé de formage à froid ou à chaud, selon le type de matériau et les spécifications de la pièce à fabriquer. Le processus commence par la fixation d’un disque ou d’un tube de métal sur un mandrin rotatif. Ce mandrin sert de support pour former le métal en utilisant un outil de formage qui applique une pression pendant que le métal tourne à grande vitesse.
- Filage manuel : Bien que ce procédé soit souvent automatisé dans les grandes industries, il existe encore des opérations de filage manuel, où un opérateur guide l’outil de filage pour donner au métal la forme souhaitée. Ce type de filage est souvent réservé à des pièces complexes ou de petites séries.
- Filage automatique : Les machines à filer automatiques sont capables de produire des pièces à grande échelle avec une grande précision et constance. L’ensemble du processus est contrôlé par un système informatique qui régule la pression, la vitesse de rotation et la forme de l’outil.
Types de Filage
Il existe plusieurs types de procédés de filage selon le résultat souhaité :
- Filage conventionnel : Le procédé le plus courant, utilisé pour créer des formes simples comme des cônes ou des cylindres.
- Filage à compression : Ce procédé consiste à réduire l’épaisseur du métal tout en formant la pièce, ce qui est souvent utilisé pour les pièces nécessitant une résistance accrue.
- Filage assisté par ordinateur (CNC) : Utilisé pour des pièces complexes nécessitant une grande précision, ce procédé fait appel à des commandes numériques pour ajuster en temps réel la pression et la vitesse du processus.
Avantages du Filage des Métaux
Le filage des métaux présente plusieurs avantages distincts par rapport à d’autres procédés de formage :
- Production sans soudure : Le filage permet de créer des pièces creuses sans nécessiter de soudure, ce qui est essentiel pour la production de pièces de haute intégrité, notamment dans les secteurs de l’aéronautique ou de la chimie.
- Faible coût de production : En comparaison avec des procédés comme l’emboutissage profond, le filage nécessite des outillages relativement simples, ce qui réduit les coûts pour des productions de petites à moyennes séries.
- Haute précision : Les machines à filer modernes, surtout celles assistées par ordinateur, permettent d’obtenir des tolérances extrêmement serrées, indispensables dans des secteurs exigeants comme l’automobile ou la défense.
- Flexibilité : Le filage peut être utilisé pour une large gamme de matériaux, y compris l’aluminium, le cuivre, l’acier inoxydable, et même certains alliages exotiques utilisés dans l’aéronautique.
Applications des Machines à Filer
Les machines à filer les métaux trouvent des applications dans plusieurs industries :
- Aéronautique : Dans ce secteur, le filage est utilisé pour fabriquer des pièces légères et résistantes telles que des cônes de nez, des fuselages ou des réservoirs de carburant. La capacité du filage à produire des pièces sans soudure est un avantage majeur dans la fabrication d’équipements aéronautiques où la sécurité et la fiabilité sont primordiales.
- Automobile : Les composants tels que les roues, les jantes, les réservoirs et certains éléments de châssis sont souvent produits par filage en raison de la précision et de la solidité des pièces obtenues.
- Éclairage et mobilier : Le filage est également utilisé pour produire des luminaires, des abat-jours et des éléments décoratifs en métal, où la combinaison de formes complexes et de finitions lisses est très appréciée.
- Industrie chimique et pétrochimique : Des récipients sous pression et des réservoirs utilisés pour le stockage et le transport de produits chimiques dangereux sont souvent fabriqués par filage pour garantir une haute résistance et une étanchéité parfaite.
Innovations Récentes
L’évolution des machines à filer les métaux a suivi les avancées technologiques dans l’automatisation et la robotique :
- Machines CNC à filage : Ces machines à commande numérique permettent une précision accrue et la possibilité de fabriquer des pièces complexes en une seule opération, tout en optimisant les temps de cycle.
- Filage assisté par robot : Certaines machines sont équipées de bras robotiques capables de manipuler des pièces volumineuses ou complexes, ce qui augmente la flexibilité du procédé tout en réduisant les besoins en main-d’œuvre qualifiée.
- Matériaux avancés : Avec la montée en popularité des matériaux composites et des alliages exotiques, les machines à filer se sont adaptées pour être capables de traiter ces matériaux difficiles tout en conservant la précision et la qualité des pièces produites.
Presses de Formage des Métaux

Les presses de formage des métaux sont des machines industrielles utilisées pour déformer des matériaux métalliques afin de leur donner une forme spécifique. Ce processus de formage peut impliquer des actions telles que le pliage, l’emboutissage, l’étirage ou la découpe. Les presses de formage jouent un rôle essentiel dans la production de pièces métalliques, que ce soit dans l’automobile, l’aéronautique, ou les secteurs de la construction et de l’électroménager.
Fonctionnement des Presses de Formage
Le fonctionnement d’une presse de formage repose sur l’application d’une grande force mécanique ou hydraulique pour déformer un morceau de métal. Le métal est placé sur une matrice ou un moule, puis une presse applique une pression contrôlée, soit en une seule fois, soit de manière progressive, afin de lui donner la forme désirée.
- Presses mécaniques : Ce type de presse utilise un moteur et des engrenages pour générer la force nécessaire au formage du métal. Les presses mécaniques sont souvent préférées pour les opérations rapides et répétitives.
- Presses hydrauliques : Elles fonctionnent à l’aide d’un fluide sous pression pour générer la force. Ce type de presse est souvent utilisé pour des opérations de formage nécessitant un contrôle précis de la pression, notamment dans les applications complexes comme l’emboutissage profond.
Les presses peuvent être classées selon leur mode d’action :
- Presses à simple action : Une seule pression est appliquée au matériau pour réaliser le formage. Cela convient à des pièces plus simples.
- Presses à double action : Ce type de presse comporte deux opérations simultanées, avec une première pression pour maintenir la pièce et une seconde pour la déformer. Elle est souvent utilisée pour des formes plus complexes.
- Presses progressives : Elles effectuent plusieurs étapes de formage en une seule séquence, avec chaque coup de la presse apportant une déformation supplémentaire. Ce processus est largement utilisé pour des pièces complexes nécessitant plusieurs opérations de formage.
Types de Presses de Formage
Il existe plusieurs types de presses de formage, chacune étant adaptée à des besoins industriels spécifiques :
- Presse à friction : Utilisée pour des opérations nécessitant un contrôle précis de la vitesse et de la force, comme le forgeage ou l’estampage.
- Presse de formage à chaud : Utilisée pour former des métaux chauffés à haute température, souvent pour des alliages qui sont difficiles à travailler à froid.
- Presse à col de cygne (C-frame) : Souvent utilisée dans des opérations plus légères, elle permet un accès facile à la zone de formage, ce qui est utile pour des pièces de petite taille.
- Presse à cadre en H (H-frame) : Plus robuste, elle est utilisée pour des opérations nécessitant une grande stabilité et une force de formage élevée.
Avantages des Presses de Formage des Métaux
Les presses de formage offrent des avantages significatifs dans les processus de fabrication industrielle :
- Précision : Grâce à la régularité de la force appliquée, les presses de formage peuvent produire des pièces avec des tolérances très serrées, ce qui est crucial dans des industries comme l’automobile ou l’électronique.
- Efficacité de production : Les presses modernes permettent un formage rapide et répétitif, assurant une productivité élevée tout en réduisant les coûts par pièce.
- Flexibilité : Ces machines peuvent traiter différents types de métaux, allant des aciers aux alliages légers comme l’aluminium, et peuvent être ajustées pour produire des pièces de formes variées.
- Adaptabilité : Que ce soit pour le formage à chaud ou à froid, les presses de formage sont capables de s’adapter aux différents besoins de production selon le type de matériau et la forme désirée.
Applications des Presses de Formage
Les presses de formage sont essentielles dans de nombreux secteurs industriels :
- Automobile : Les composants critiques comme les panneaux de carrosserie, les châssis, et d’autres pièces structurelles sont fréquemment fabriqués à l’aide de presses de formage. Leur capacité à produire des pièces légères mais solides est un atout majeur dans la réduction du poids des véhicules tout en assurant leur robustesse.
- Aéronautique : Dans ce secteur, la précision et la qualité des pièces sont primordiales. Les presses de formage sont utilisées pour créer des pièces légères et résistantes, indispensables à la sécurité et à l’efficacité des avions.
- Industrie électrique : Les boîtiers métalliques pour appareils électriques, ainsi que d’autres composants en métal, sont souvent fabriqués par le biais de presses de formage, grâce à leur capacité à produire des pièces avec une grande précision.
- Construction : Les poutres, supports et autres éléments structurels métalliques utilisés dans les bâtiments et les infrastructures sont souvent produits à l’aide de ces presses, permettant d’obtenir des pièces standardisées et robustes.
Innovations Technologiques dans les Presses de Formage
L’industrie des presses de formage a vu de nombreuses innovations au fil des ans, améliorant l’efficacité et la précision des machines :
- Contrôle numérique : Les presses modernes sont souvent équipées de systèmes CNC (Commande Numérique par Calculateur) qui permettent de programmer et d’ajuster avec précision les paramètres de formage, garantissant une production plus rapide et moins d’erreurs.
- Automatisation : Les presses automatisées permettent d’augmenter la productivité tout en réduisant les besoins en main-d’œuvre. Des robots peuvent être intégrés pour alimenter la presse et retirer les pièces finies, accélérant ainsi les temps de cycle.
- Technologie écoénergétique : Certaines presses sont maintenant conçues pour utiliser moins d’énergie, tout en offrant une puissance de formage équivalente, réduisant ainsi les coûts opérationnels et l’empreinte carbone des usines.
Presse de Découpe Rapide

La presse de découpe rapide est un équipement industriel spécialisé dans la découpe de matériaux, principalement métalliques, à grande vitesse et avec une extrême précision. Ce type de presse est essentiel dans les environnements de production où des volumes élevés de pièces découpées avec précision sont nécessaires, notamment dans les secteurs de l’automobile, de l’électronique, de l’emballage, et de l’aérospatiale.
Fonctionnement de la Presse de Découpe Rapide
Le processus de découpe rapide repose sur l’utilisation d’une presse pour exercer une force sur une matrice, dans laquelle le matériau est positionné. Sous cette pression, le matériau est découpé à la forme désirée en un temps extrêmement court. Contrairement aux processus de découpe traditionnels, qui peuvent être plus lents ou moins précis, la presse de découpe rapide permet de traiter de grandes quantités de matériaux tout en assurant une qualité constante.
- Presse mécanique : Ce type de presse utilise un mécanisme à volant pour générer la force de découpe. Elle est idéale pour des cadences de production très élevées, pouvant réaliser des milliers de découpes à l’heure.
- Presse hydraulique : Les presses hydrauliques, bien que généralement plus lentes, offrent un contrôle plus précis de la force et sont utilisées pour des découpes nécessitant une extrême précision, ou pour des matériaux plus difficiles à découper.
- Presse servo-électrique : Ce type de presse combine la rapidité des presses mécaniques et la précision des presses hydrauliques. Elle utilise un moteur servo-électrique pour générer la force nécessaire, offrant ainsi une grande flexibilité dans le contrôle des paramètres de découpe.
Types de Découpe
Les presses de découpe rapide peuvent réaliser différents types de découpe, en fonction de la forme finale souhaitée et du type de matériau utilisé :
- Découpe à blanc : Une opération qui consiste à séparer une pièce d’un matériau plus grand sans formation supplémentaire. Cela est couramment utilisé pour produire des composants plats ou des pièces prêtes pour un autre processus de formage.
- Découpe progressive : Le matériau passe à travers plusieurs étapes de découpe successives pour aboutir à une pièce finale plus complexe. Chaque étape enlève une partie spécifique du matériau.
- Découpe fine : Utilisée pour des tolérances très serrées, notamment dans des applications où une haute précision et une finition de bord lisse sont essentielles, comme dans l’industrie de l’électronique ou l’horlogerie.
Avantages de la Presse de Découpe Rapide
Les presses de découpe rapide offrent plusieurs avantages qui en font un choix privilégié dans l’industrie moderne :
- Vitesse de production : Grâce à leur capacité à effectuer des découpes rapidement et en continu, ces presses permettent de produire un grand nombre de pièces dans un laps de temps réduit, augmentant ainsi la productivité de l’usine.
- Précision : Ces presses sont capables de réaliser des découpes d’une précision exceptionnelle, même à grande vitesse, ce qui est crucial pour des pièces nécessitant des tolérances serrées.
- Réduction des coûts : En automatisant le processus de découpe et en augmentant la cadence de production, les presses de découpe rapide contribuent à réduire les coûts de production par pièce, particulièrement dans les productions en série.
- Flexibilité : Certaines presses de découpe rapide peuvent être configurées pour réaliser différents types de découpes sur un même matériau, offrant ainsi une grande flexibilité dans les lignes de production.
Applications des Presses de Découpe Rapide
Ces presses sont largement utilisées dans plusieurs secteurs industriels en raison de leur capacité à traiter des volumes élevés de matériaux avec précision :
- Automobile : La découpe des tôles utilisées pour les carrosseries, les châssis, et autres pièces structurelles est souvent réalisée avec des presses de découpe rapide pour répondre aux besoins de production de masse du secteur.
- Aéronautique : Dans ce secteur, la précision et la qualité des composants sont primordiales. Les presses de découpe rapide sont utilisées pour découper des pièces métalliques légères et complexes qui nécessitent des tolérances strictes.
- Électronique : Les composants en métal de petite taille, comme les connecteurs ou les circuits imprimés, sont souvent découpés à l’aide de presses rapides, car ces pièces nécessitent une précision extrême.
- Emballage : Le secteur de l’emballage utilise souvent des presses de découpe rapide pour produire des emballages en métal ou en plastique à haute vitesse, répondant ainsi aux besoins du marché de masse.
Innovations et Évolutions Technologiques
Les presses de découpe rapide bénéficient des avancées technologiques qui optimisent leurs performances :
- Systèmes CNC et automatisation : Les presses modernes sont souvent équipées de commandes numériques par calculateur (CNC) permettant une programmation précise de chaque opération de découpe. Cela permet un ajustement rapide et précis des paramètres de découpe pour différentes pièces, ce qui est essentiel dans des environnements de production variés.
- Presses intelligentes : Certaines machines sont dotées de capteurs et de systèmes de surveillance en temps réel qui peuvent ajuster les paramètres en fonction des conditions réelles du matériau ou de l’usure des outils, garantissant ainsi une qualité constante.
- Économies d’énergie : De plus en plus de presses sont conçues pour être plus efficaces sur le plan énergétique, réduisant ainsi les coûts d’exploitation et contribuant à une production plus durable.
Presses à Rogner

Les presses à rogner sont des machines industrielles utilisées pour enlever l’excédent de matière autour d’une pièce après un processus de formage, d’emboutissage ou de moulage. Ce procédé de rognage permet d’obtenir des pièces finales avec des contours précis et nets, en supprimant toute bavure ou excès de métal qui pourrait affecter la qualité et l’esthétique de la pièce.
Fonctionnement des Presses à Rogner
Le processus de rognage consiste à placer la pièce formée dans une matrice et à utiliser une presse pour couper ou retirer les parties excédentaires. Le rognage est souvent l’étape finale après des opérations de formage comme l’emboutissage ou le moulage, où le matériau est déformé pour créer une forme spécifique, mais laisse généralement des bords irréguliers ou du surplus de matière.
- Presses mécaniques : Ce type de presse est couramment utilisé pour des opérations de rognage à haute vitesse. Les presses mécaniques sont particulièrement adaptées à des séries de production où un grand nombre de pièces doivent être rognées en un minimum de temps.
- Presses hydrauliques : Les presses hydrauliques sont privilégiées dans les cas où une grande force de rognage est nécessaire ou lorsque des matériaux plus durs doivent être traités. Elles permettent également un meilleur contrôle de la pression, ce qui est utile pour des pièces plus complexes.
- Presses de rognage automatiques : Dans les environnements de production moderne, les presses à rogner automatiques intègrent des systèmes robotisés et des capteurs pour une opération continue sans intervention humaine, ce qui augmente la productivité tout en garantissant une qualité constante.
Types de Processus de Rognage
Il existe plusieurs types de rognage en fonction de la nature de la pièce et du type de matériau utilisé :
- Rognage mécanique : Ce type de rognage utilise une force mécanique pour découper les excédents de matériau. Il est couramment utilisé pour des pièces en métal formées par emboutissage ou forgeage.
- Rognage par cisaillement : Un procédé où la pièce est cisaillée pour enlever les excédents de matière, souvent utilisé pour des matériaux plus épais ou plus durs.
- Rognage manuel : Dans certains cas, des opérations manuelles sont nécessaires pour rogner des pièces particulièrement complexes ou lorsque la production n’est pas adaptée à une automatisation complète.
- Rognage par usinage : Des outils de coupe rotatifs sont utilisés pour enlever les bavures ou excès de métal, ce qui permet d’obtenir une finition plus lisse, particulièrement dans les pièces qui nécessitent une précision accrue.
Avantages des Presses à Rogner
Les presses à rogner sont essentielles dans les processus de fabrication industrielle pour plusieurs raisons :
- Finition de haute qualité : Le rognage permet d’obtenir des bords propres et lisses, essentiels dans les secteurs où l’esthétique et la précision sont primordiales, comme l’automobile et l’aéronautique.
- Productivité accrue : Les presses à rogner automatiques ou à grande vitesse permettent de traiter un grand nombre de pièces en peu de temps, augmentant ainsi le rendement de la production.
- Réduction des déchets : En enlevant uniquement l’excédent de matière nécessaire, le rognage réduit les déchets et maximise l’utilisation des matériaux, contribuant à une production plus rentable et durable.
- Flexibilité : Les presses à rogner peuvent être adaptées pour traiter divers types de matériaux, des métaux légers comme l’aluminium aux alliages plus durs, rendant ce procédé polyvalent dans de nombreux secteurs.
Applications des Presses à Rogner
Le rognage est une étape essentielle dans la fabrication de nombreuses pièces industrielles, et il est utilisé dans plusieurs secteurs :
- Automobile : Dans la fabrication de pièces de carrosserie, d’éléments de moteur ou de composants structurels, le rognage permet d’éliminer les bavures ou excédents de métal résultant des processus d’emboutissage ou de moulage, garantissant ainsi une finition parfaite.
- Aéronautique : Les pièces utilisées dans les avions doivent souvent répondre à des normes strictes en matière de précision et de sécurité. Le rognage est utilisé pour éliminer les irrégularités après le formage des pièces métalliques, notamment pour les ailes, les carénages et autres composants critiques.
- Électronique : Dans la fabrication de petits composants métalliques, comme les connecteurs ou les boîtiers, le rognage permet de garantir des tolérances serrées et des contours précis, indispensables pour l’assemblage de circuits électroniques.
- Électroménager : Les pièces métalliques utilisées dans les appareils électroménagers, comme les tambours de machines à laver ou les coques de réfrigérateurs, doivent souvent être rognées pour garantir une finition soignée et sécurisée.
Innovations dans le Rognage Industriel
Les avancées technologiques dans le domaine des presses à rogner ont conduit à des innovations majeures, améliorant à la fois l’efficacité et la précision du processus :
- Rognage automatisé : L’intégration de robots et de systèmes de capteurs dans les presses permet un rognage entièrement automatisé, augmentant ainsi la productivité tout en réduisant les risques d’erreur humaine.
- Systèmes CNC : Les commandes numériques permettent de programmer précisément chaque opération de rognage, garantissant une uniformité parfaite d’une pièce à l’autre, même à grande échelle.
- Machines multi-processus : Certaines machines combinent le rognage avec d’autres opérations, comme l’emboutissage ou l’ébavurage, permettant ainsi de réduire les temps de manipulation et d’optimiser les processus de production.
Presses de Formage à Froid

Les presses de formage à froid sont des machines industrielles utilisées pour déformer des métaux sans les chauffer, contrairement au formage à chaud. Ce processus consiste à appliquer une pression intense à température ambiante pour plier, étirer, emboutir ou découper le matériau, tout en préservant ses propriétés mécaniques. Le formage à froid est particulièrement apprécié dans les secteurs où la précision, la résistance et la durabilité des pièces sont essentielles.
Fonctionnement des Presses de Formage à Froid
Le principe du formage à froid repose sur l’application d’une force mécanique ou hydraulique sur une pièce métallique pour lui donner une forme spécifique. Contrairement au formage à chaud, où le métal est chauffé pour faciliter sa déformation, le formage à froid exige des machines plus puissantes pour surmonter la résistance naturelle du métal. Ce procédé est couramment utilisé pour des métaux ductiles, comme l’acier doux, l’aluminium et le cuivre, qui peuvent être déformés sans rupture même à température ambiante.
Les presses de formage à froid se distinguent en fonction de leur méthode d’application de la pression :
- Presses mécaniques : Utilisées pour des opérations de formage à grande vitesse, ces presses sont souvent privilégiées pour des productions en série, comme l’emboutissage rapide de pièces simples.
- Presses hydrauliques : Ces machines offrent un contrôle précis de la pression appliquée, permettant de former des pièces plus complexes et d’utiliser des matériaux plus résistants. Elles sont idéales pour des opérations nécessitant une force continue.
- Presses servo-électriques : Elles combinent la rapidité des presses mécaniques avec la précision des presses hydrauliques, tout en réduisant la consommation d’énergie et les bruits générés.
Types de Processus de Formage à Froid
Le formage à froid regroupe plusieurs techniques en fonction de la pièce et de la géométrie à obtenir :
- Emboutissage : Une pièce est déformée à froid pour lui donner une forme tridimensionnelle. L’emboutissage à froid est utilisé pour fabriquer des composants tels que les boîtiers, les réservoirs et les coques de véhicules.
- Pliage : La presse applique une force sur une feuille de métal pour la plier à un angle spécifique, généralement à l’aide d’une matrice de pliage. Ce procédé est utilisé pour fabriquer des pièces structurelles comme des poutres et des panneaux.
- Extrusion à froid : Une pièce est forcée à travers une matrice pour lui donner une forme allongée. Ce procédé permet de fabriquer des tubes, des barres ou des profils métalliques complexes avec des tolérances très serrées.
- Forgeage à froid : Une pression est appliquée sur une pièce métallique pour la comprimer et la façonner sans la chauffer. Ce procédé est souvent utilisé pour produire des pièces mécaniques résistantes comme des boulons et des engrenages.
Avantages du Formage à Froid
Le formage à froid présente plusieurs avantages par rapport au formage à chaud :
- Précision accrue : Comme le métal n’est pas chauffé, il conserve mieux ses dimensions d’origine, permettant d’obtenir des pièces avec des tolérances plus serrées et des formes plus précises.
- Meilleure résistance des pièces : Le formage à froid améliore les propriétés mécaniques du métal, en augmentant sa résistance et sa dureté par écrouissage, ce qui rend les pièces plus robustes et durables.
- Efficacité énergétique : Contrairement au formage à chaud, le formage à froid ne nécessite pas de chauffer le métal, ce qui réduit la consommation d’énergie et les coûts associés.
- Qualité de surface améliorée : Les pièces formées à froid ont généralement une surface plus lisse et ne nécessitent pas de finitions supplémentaires, ce qui permet de réduire les étapes de post-traitement.
Applications des Presses de Formage à Froid
Le formage à froid est utilisé dans divers secteurs industriels en raison de sa capacité à produire des pièces de haute précision et à grande échelle :
- Automobile : De nombreuses pièces automobiles, comme les composants de châssis, les supports et les pièces structurelles, sont fabriquées par formage à froid en raison de leur robustesse et de leur précision.
- Aéronautique : Dans l’industrie aéronautique, où la qualité et la sécurité sont primordiales, le formage à froid est utilisé pour fabriquer des pièces légères et résistantes, comme des supports, des ferrures et des pièces de fuselage.
- Électronique : Le formage à froid permet de produire des composants métalliques fins et précis, comme des connecteurs et des boîtiers, indispensables dans la fabrication de circuits électroniques.
- Industrie des outils et machines : De nombreux outils, boulons, écrous et pièces mécaniques sont fabriqués par formage à froid, car ce procédé permet de produire des pièces solides et résistantes aux contraintes mécaniques.
Innovations dans le Formage à Froid
Les presses de formage à froid ont connu des avancées technologiques significatives ces dernières années, améliorant leur efficacité et leurs performances :
- Commandes numériques (CNC) : L’intégration de systèmes CNC permet un contrôle précis de chaque étape du processus de formage, garantissant une uniformité parfaite des pièces produites, même à grande échelle.
- Automatisation : Les presses de formage à froid sont de plus en plus automatisées, avec des systèmes robotisés qui alimentent et retirent les pièces, augmentant ainsi la productivité tout en réduisant les besoins en main-d’œuvre.
- Matériaux avancés : Le formage à froid de nouveaux alliages et matériaux composites permet d’obtenir des pièces plus légères, plus résistantes et plus adaptées aux applications modernes, notamment dans les secteurs de la défense et de l’aéronautique.
- Presses hybrides : Combinant les avantages des presses mécaniques, hydrauliques et servo-électriques, ces machines permettent de s’adapter à une large gamme de matériaux et de processus, tout en optimisant l’efficacité énergétique.
Presse Hydraulique d’Emboutissage
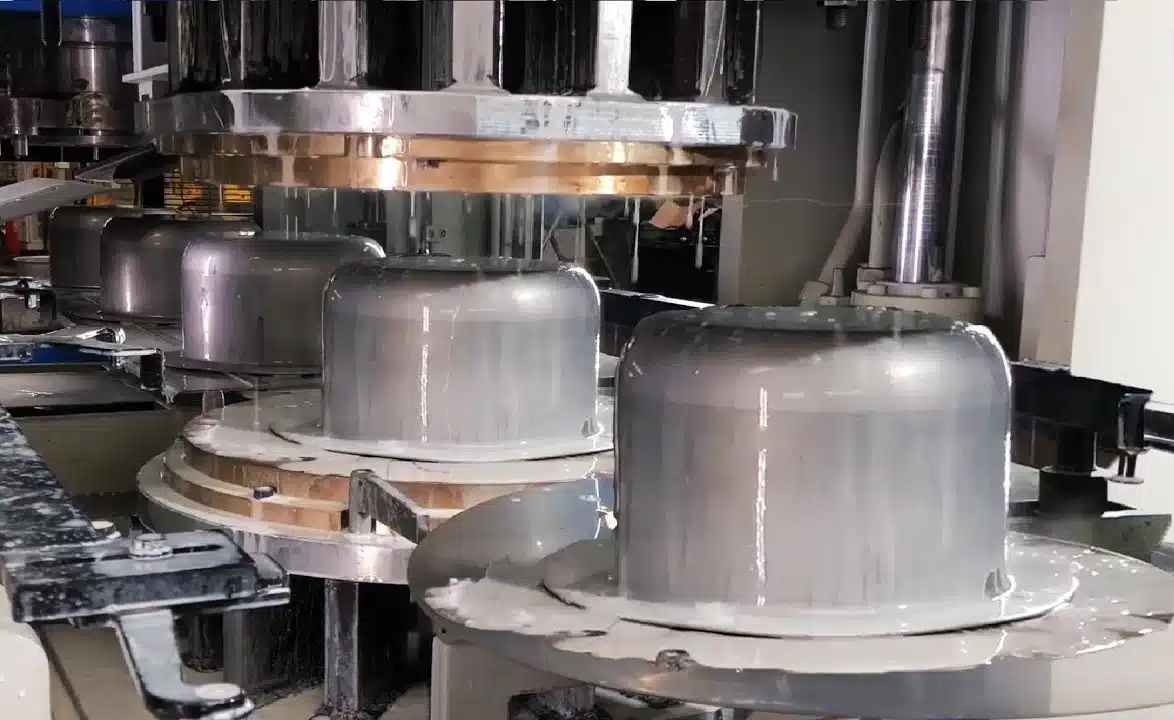
La presse hydraulique d’emboutissage est une machine industrielle puissante utilisée pour transformer des feuilles de métal en des formes tridimensionnelles complexes. L’emboutissage, processus de formage du métal par déformation, nécessite des forces importantes pour obtenir des pièces avec des géométries précises. Grâce à leur capacité à générer une force de pression continue et élevée, les presses hydrauliques sont idéales pour ce type d’opération.
Fonctionnement des Presses Hydrauliques d’Emboutissage
Les presses hydrauliques fonctionnent en utilisant un fluide sous pression pour générer une force capable de déformer des matériaux métalliques. Lors du processus d’emboutissage, une feuille métallique, appelée flan, est placée entre une matrice et un poinçon. La presse hydraulique applique ensuite une force uniforme sur le poinçon pour pousser la feuille à travers la matrice, créant ainsi une pièce avec des formes détaillées et complexes.
Contrairement aux presses mécaniques, qui génèrent une force maximale à un point donné, les presses hydrauliques peuvent appliquer une force constante tout au long du cycle de travail, ce qui est particulièrement important dans des processus comme l’emboutissage profond, où le matériau est fortement déformé.
Types de Presses Hydrauliques d’Emboutissage
Il existe plusieurs types de presses hydrauliques adaptées à l’emboutissage, chacune ayant des caractéristiques spécifiques selon les applications :
- Presse à action simple : Ce type de presse hydraulique est utilisé pour des opérations d’emboutissage de base, où une seule force est appliquée pour déformer le métal.
- Presse à double action : Ces presses sont équipées de deux vérins hydrauliques : l’un pour maintenir la feuille de métal en place pendant le processus, et l’autre pour appliquer la force de déformation. Elles sont couramment utilisées pour l’emboutissage profond.
- Presse à triple action : Ce type de presse est utilisé pour des processus de formage encore plus complexes, nécessitant un contrôle précis des forces appliquées sur différentes parties de la pièce.
Avantages des Presses Hydrauliques d’Emboutissage
Les presses hydrauliques sont largement utilisées dans l’industrie pour de nombreuses raisons :
- Capacité à générer des forces élevées : Les presses hydrauliques peuvent appliquer des forces très importantes, ce qui les rend idéales pour le formage de pièces épaisses ou de grandes dimensions.
- Précision et contrôle : Grâce à la régulation de la pression hydraulique, il est possible de contrôler précisément la force appliquée, ce qui garantit des tolérances plus serrées et des pièces de haute qualité.
- Adaptabilité : Les presses hydrauliques peuvent être ajustées pour diverses opérations, allant de l’emboutissage superficiel à l’emboutissage profond, permettant une grande flexibilité dans la production.
- Longueur de course ajustable : Les presses hydrauliques peuvent avoir une course plus longue, ce qui les rend particulièrement adaptées à des opérations nécessitant des déformations importantes, comme l’emboutissage profond.
Applications des Presses Hydrauliques d’Emboutissage
Les presses hydrauliques d’emboutissage sont utilisées dans une large gamme de secteurs industriels pour fabriquer des pièces complexes et volumineuses :
- Automobile : Dans l’industrie automobile, les presses hydrauliques sont utilisées pour fabriquer des composants structurels comme les capots, les portes, les panneaux latéraux, et d’autres pièces de carrosserie. Ces pièces nécessitent une grande précision et doivent être produites en masse.
- Aéronautique : Dans ce secteur, l’emboutissage profond est utilisé pour fabriquer des pièces légères et résistantes, comme les réservoirs de carburant, les carénages et les éléments de fuselage. L’utilisation de presses hydrauliques permet d’obtenir des pièces d’une qualité irréprochable, tout en respectant les normes de sécurité strictes de l’aéronautique.
- Électroménager : De nombreuses pièces métalliques utilisées dans les appareils électroménagers, comme les tambours de machines à laver, les coques extérieures et les composants de moteurs, sont fabriquées par emboutissage avec des presses hydrauliques.
- Industrie énergétique : Les presses hydrauliques d’emboutissage sont également utilisées pour produire des composants utilisés dans l’industrie énergétique, comme des enveloppes de batteries ou des pièces pour panneaux solaires.
Innovations et Évolutions Technologiques
Les presses hydrauliques d’emboutissage ont bénéficié de nombreuses innovations au fil des années, améliorant leurs performances et leurs capacités :
- Automatisation avancée : L’intégration de robots et de systèmes automatisés permet aux presses hydrauliques modernes de fonctionner de manière continue et sans interruption, augmentant ainsi la productivité tout en réduisant les coûts de production.
- Contrôles numériques : Grâce aux systèmes CNC, les presses hydrauliques peuvent être programmées avec une précision extrême, permettant un contrôle minutieux de chaque étape du processus d’emboutissage, garantissant ainsi la constance de la qualité des pièces produites.
- Économies d’énergie : Certaines presses hydrauliques sont conçues pour utiliser moins d’énergie tout en maintenant des niveaux de performance élevés. Cela contribue à la réduction des coûts d’exploitation et à une production plus respectueuse de l’environnement.
- Technologie de fluide à haute pression : Les nouvelles presses hydrauliques sont capables d’utiliser des fluides à haute pression, augmentant ainsi la force générée sans avoir besoin de moteurs plus puissants, ce qui améliore l’efficacité énergétique.
Presses Hydrauliques pour Formage
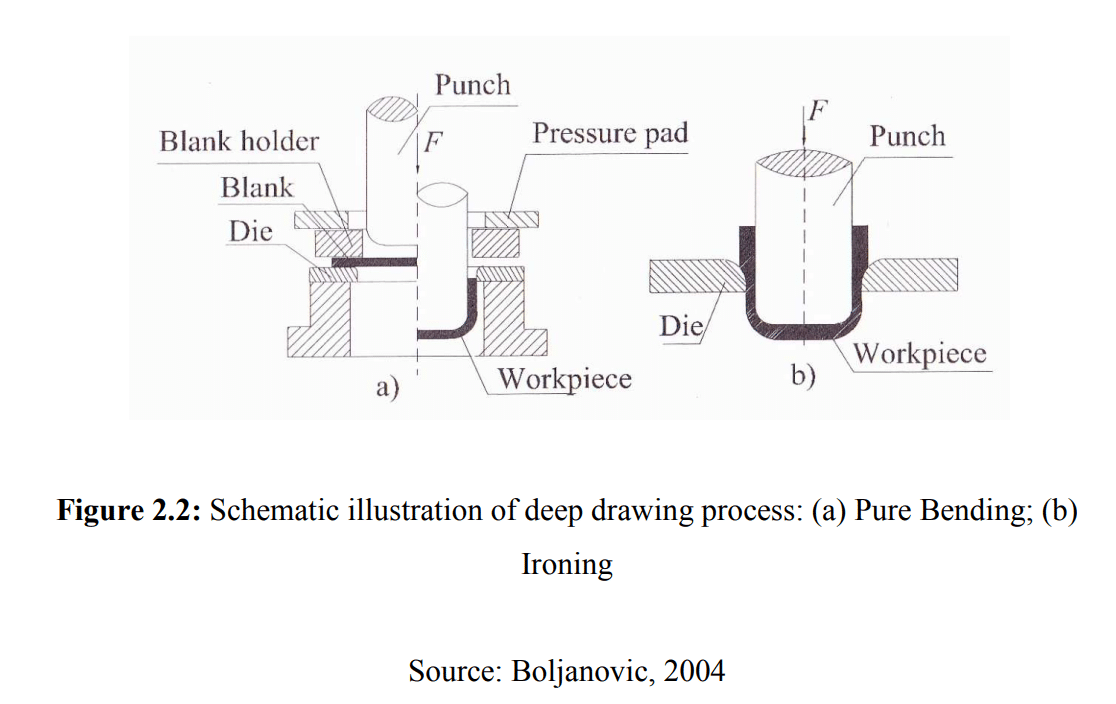
Les presses hydrauliques pour formage sont des machines industrielles polyvalentes, utilisées pour façonner des matériaux métalliques et non métalliques en appliquant une force élevée via un fluide hydraulique. Ces presses sont essentielles dans les processus de formage, car elles permettent de réaliser des opérations complexes avec une grande précision. Elles sont couramment employées dans divers secteurs industriels, comme l’automobile, l’aéronautique, la construction, et bien d’autres.
Fonctionnement des Presses Hydrauliques pour Formage
Les presses hydrauliques fonctionnent sur un principe simple mais puissant : un fluide, généralement de l’huile, est pressurisé à l’intérieur d’un cylindre pour générer une force de compression qui déforme le matériau placé entre la matrice et le poinçon. La force générée par la presse hydraulique est constante tout au long du cycle de travail, ce qui permet un formage progressif et uniforme.
Contrairement aux presses mécaniques, qui appliquent une force maximale à un moment précis du cycle, les presses hydrauliques offrent une pression contrôlée et ajustable, ce qui est essentiel pour des opérations de formage plus complexes. Elles peuvent également être utilisées pour plusieurs types de formage, comme le pliage, l’emboutissage, l’étirage, et l’extrusion.
Types de Presses Hydrauliques pour Formage
Il existe plusieurs types de presses hydrauliques, chacune étant adaptée à un type particulier de formage :
- Presses à cadre en H : Ces presses sont très robustes et offrent une grande stabilité lors des opérations de formage, ce qui les rend adaptées aux applications nécessitant des forces de pression élevées.
- Presses à 4 colonnes : Ces presses hydrauliques sont idéales pour les opérations nécessitant une répartition uniforme de la force sur la pièce. Elles sont souvent utilisées pour l’emboutissage et le formage de grandes pièces plates.
- Presses à double action : Elles sont équipées de deux vérins permettant de contrôler la pression de manière indépendante, ce qui est utile pour les opérations de formage à plusieurs étapes, telles que le formage profond ou l’étirage.
- Presses de transfert : Elles sont intégrées à des lignes de production automatisées pour déplacer la pièce d’une station à une autre, réalisant plusieurs étapes de formage en une seule séquence.
Avantages des Presses Hydrauliques pour Formage
Les presses hydrauliques offrent de nombreux avantages, notamment :
- Force ajustable : La pression générée par une presse hydraulique peut être ajustée avec précision en fonction des exigences du matériau et du processus de formage, permettant ainsi une flexibilité maximale.
- Capacité à travailler des matériaux variés : Ces presses peuvent être utilisées pour former une large gamme de matériaux, allant des métaux légers comme l’aluminium aux alliages plus durs, ainsi que des matériaux composites et plastiques.
- Formage de pièces complexes : Grâce à la répartition uniforme de la force, ces presses permettent de former des pièces aux géométries complexes, même avec des tolérances très strictes.
- Économie d’énergie : Certaines presses hydrauliques modernes sont conçues pour être plus écoénergétiques, réduisant la consommation tout en maintenant des performances élevées, ce qui en fait des solutions plus durables.
Applications des Presses Hydrauliques pour Formage
Les presses hydrauliques sont essentielles dans de nombreuses industries pour le formage de pièces métalliques et non métalliques :
- Automobile : Dans l’industrie automobile, ces presses sont utilisées pour la fabrication de nombreuses pièces, allant des panneaux de carrosserie aux composants structurels comme les montants, les longerons et les supports. Elles permettent de former des pièces légères mais solides, essentielles pour réduire le poids des véhicules tout en améliorant leur performance.
- Aéronautique : Le formage de pièces aéronautiques, comme les cadres de fuselage, les ailes et autres composants, nécessite une grande précision et une force importante. Les presses hydrauliques sont couramment utilisées pour former des alliages légers comme le titane ou l’aluminium.
- Construction : Les presses hydrauliques sont utilisées pour produire des poutres, des colonnes et d’autres éléments structurels dans la construction de bâtiments, d’infrastructures et de ponts. Elles permettent de former des pièces résistantes aux contraintes mécaniques tout en assurant leur durabilité.
- Électronique : Les composants métalliques des appareils électroniques, comme les boîtiers, les connecteurs et autres pièces de petite taille, sont souvent formés à l’aide de presses hydrauliques. Ces machines permettent d’obtenir des tolérances serrées et des finitions de haute qualité.
Innovations dans les Presses Hydrauliques pour Formage
Les presses hydrauliques ont évolué avec l’intégration de nouvelles technologies, rendant leur utilisation plus efficace et plus précise :
Maintenance prédictive : Grâce à des capteurs intelligents, les presses hydrauliques peuvent maintenant surveiller en temps réel l’usure des composants, permettant une maintenance prédictive et ainsi minimiser les temps d’arrêt.
Commandes numériques (CNC) : Les systèmes CNC permettent de contrôler chaque aspect du processus de formage, de la pression à la vitesse de compression, assurant ainsi une répétabilité et une précision exceptionnelles.
Automatisation : L’intégration de robots et de systèmes automatisés dans les presses hydrauliques a révolutionné les lignes de production, augmentant la productivité tout en réduisant les coûts liés à la main-d’œuvre et aux erreurs humaines.
Technologie à faible consommation d’énergie : Les presses hydrauliques modernes sont de plus en plus conçues pour réduire la consommation d’énergie. L’utilisation de systèmes hybrides, combinant hydraulique et électrique, permet d’améliorer l’efficacité énergétique sans compromettre la puissance de formage.
EMS Machines de Formage
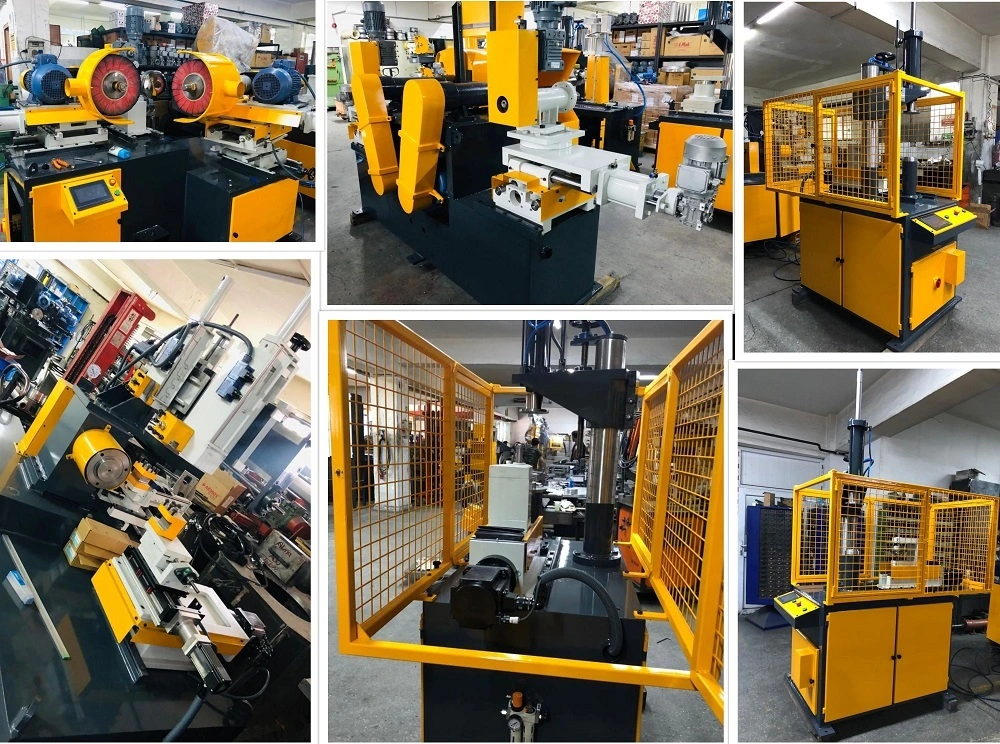
Le formage du métal est un processus consistant à façonner le métal dans la forme et la taille souhaitées à l’aide de diverses techniques. Il s’agit d’un processus crucial dans l’industrie manufacturière car il permet la production de différents produits tels que des pièces automobiles, des composants d’avion, des appareils électroménagers et bien d’autres encore.
Le processus de formage du métal consiste à appliquer une force sur le métal pour changer sa forme sans enlever aucune matière. La force peut être appliquée par diverses méthodes telles que le forgeage, le laminage, l’extrusion, l’étirage et l’estampage. Chaque méthode a ses propres avantages et inconvénients, et le choix de la méthode dépend du matériau formé et de la forme souhaitée.
Le forgeage est l’une des techniques de formage des métaux les plus anciennes. Il s’agit de chauffer le métal à haute température, puis d’appliquer une force de compression à l’aide d’un marteau ou d’une presse pour donner au métal la forme souhaitée. Le forgeage est couramment utilisé pour produire de grandes pièces telles que des engrenages, des essieux et des bielles.
Le laminage est une autre technique de formage du métal qui consiste à faire passer le métal à travers une paire de rouleaux pour réduire son épaisseur ou modifier sa forme. Les rouleaux peuvent être lisses ou texturés selon la finition souhaitée. Le laminage est couramment utilisé pour produire des tôles plates, des plaques et des barres.
L’extrusion est une technique de formage du métal qui consiste à pousser une billette ou une tige métallique à travers une matrice pour créer une forme spécifique. L’extrusion peut être utilisée pour produire des formes complexes telles que des tubes, des canaux et des angles.
L’emboutissage est une technique de formage des métaux utilisée pour réaliser des pièces de forme cylindrique, comme des tubes ou des tuyaux. Le processus consiste à tirer le métal à travers une matrice pour réduire son diamètre et augmenter sa longueur. Le tréfilage est couramment utilisé dans la production de fils, de tiges et de tubes.
L’emboutissage est une technique de formage du métal qui consiste à couper, poinçonner ou plier le métal dans une forme spécifique à l’aide d’une matrice. Le processus peut être utilisé pour produire des pièces avec une grande précision et répétabilité. L’estampage est couramment utilisé dans la production de pièces automobiles, d’appareils électroménagers et d’appareils électroniques.
En plus de ces techniques, il existe de nombreuses autres méthodes de formage des métaux telles que le filage, l’emboutissage profond et l’hydroformage. Chaque méthode a ses propres avantages et inconvénients, et le choix de la méthode dépend des exigences spécifiques du produit fabriqué.
Le formage des métaux est un processus complexe qui nécessite un haut niveau de compétence et d’expertise. Le succès du processus dépend de nombreux facteurs tels que le type de matériau formé, l’équipement utilisé et l’expérience de l’opérateur. En comprenant les différentes techniques de formage des métaux et en choisissant la méthode adaptée au travail, les fabricants peuvent produire des pièces de haute qualité qui répondent aux besoins spécifiques de leurs clients.