
Équipements industriels de formage de tôle: Le formage de tôles métalliques est un procédé de fabrication qui consiste à transformer des tôles métalliques en différentes formes ou géométries par l’application de forces mécaniques. Ce procédé est largement utilisé dans l’industrie pour produire des pièces en métal qui sont ensuite assemblées pour former des produits finis.
Voici quelques techniques courantes de formage des tôles métalliques :
- Le découpage : Il s’agit de couper la tôle métallique à la taille désirée. Les méthodes comprennent la découpe au laser, la découpe au jet d’eau, la découpe au plasma et le poinçonnage.
- Le pliage : Cette méthode consiste à plier la tôle selon un angle donné pour obtenir la forme souhaitée. Elle est souvent utilisée pour créer des éléments comme des boîtiers, des bords ou des flans.
- L’emboutissage : C’est un processus où une tôle est formée dans un moule pour obtenir une pièce en forme de cuvette ou de coque. Ce procédé est couramment utilisé pour fabriquer des pièces automobile comme les panneaux de carrosserie.
- Le roulage : Cette technique consiste à faire passer la tôle à travers des rouleaux pour lui donner une forme courbée. Elle est souvent utilisée pour produire des cylindres ou des sections circulaires.
- Le matriçage : Cette méthode est utilisée pour créer des formes complexes en appliquant une pression sur la tôle à l’aide de matrices et de poinçons.
- Le laminage : Un procédé de formage à chaud ou à froid où la tôle est passée entre des rouleaux pour réduire son épaisseur ou la façonner en une forme spécifique.
- Le forgeage : Bien que ce soit un procédé traditionnellement plus utilisé pour les pièces solides, il peut aussi être adapté au formage de tôles, particulièrement pour des pièces de grandes tailles.
Ces procédés peuvent être réalisés à chaud (avec la tôle chauffée avant l’opération) ou à froid (avec la tôle à température ambiante). Le choix de la méthode dépend de plusieurs facteurs comme la forme finale, les propriétés mécaniques requises et le matériau utilisé.
Le formage de tôles métalliques est crucial dans l’industrie pour la fabrication de pièces aux formes spécifiques. Cela inclut des techniques variées adaptées à différents types de métal et exigences de production. Par exemple, pour des métaux comme l’acier inoxydable ou l’aluminium, des outils et des procédés spéciaux sont nécessaires pour optimiser la résistance tout en maintenant une efficacité de production élevée. Une fois formées, ces pièces subissent souvent des traitements thermiques ou de surface pour améliorer leur durabilité, leur finition ou leur résistance à la corrosion. Le choix de la méthode de formage dépend de nombreux paramètres, y compris la géométrie complexe de la pièce, les contraintes mécaniques, la vitesse de production et les coûts associés à chaque procédé.
Le formage de tôles métalliques joue un rôle fondamental dans la production industrielle de composants métalliques de diverses formes et tailles. Ce processus est largement utilisé dans des secteurs tels que l’automobile, l’aérospatiale, la construction, l’électronique et bien d’autres. Les tôles métalliques sont des feuilles fines et plates de métal, qui, par le biais de différentes techniques de formage, peuvent être transformées en produits finaux aux formes complexes et précises.
Le formage des tôles métalliques peut se diviser en deux catégories principales : le formage à chaud et le formage à froid. Le choix entre ces deux méthodes dépend de plusieurs facteurs tels que les propriétés du matériau, la forme finale requise et les coûts de production.
- Formage à chaud : Ce processus implique le chauffage de la tôle métallique à une température élevée avant qu’elle ne soit travaillée. La chaleur facilite la déformation du métal, ce qui permet de produire des pièces avec des géométries plus complexes et plus grandes. Le formage à chaud est particulièrement utile pour les métaux qui sont difficiles à travailler à température ambiante, comme l’acier inoxydable ou certains alliages d’aluminium. Parmi les techniques utilisées en formage à chaud, on retrouve le matriçage, où le métal est placé dans un moule chauffé, et le laminage, qui réduit l’épaisseur de la tôle tout en la façonnant.
- Formage à froid : Dans cette méthode, la tôle est travaillée à température ambiante, ce qui peut offrir des avantages en termes de précision et de finition de surface. Le formage à froid est souvent plus économique, car il nécessite moins d’énergie, mais il peut entraîner des contraintes internes dans le métal, rendant certaines pièces plus fragiles. Les techniques de formage à froid incluent le poinçonnage, où des trous ou des formes spécifiques sont découpés dans la tôle, le pliage, qui permet de modifier l’angle de la tôle, et l’emboutissage, où une tôle est formée en une forme profonde ou une coque en la plaçant dans un moule.
Le découpage est également un procédé clé dans le formage des tôles métalliques. Il permet de découper des tôles aux dimensions exactes ou de produire des formes spécifiques avant d’effectuer d’autres opérations de formage. Cette étape peut être réalisée à l’aide de laser, de jet d’eau, de plasma, ou de poinçonneuses, selon les besoins en matière de précision, de vitesse et de coût. Le découpage au laser, par exemple, est particulièrement apprécié pour sa capacité à offrir une précision extrême, tout en permettant de couper des tôles d’épaisseurs variées sans contact direct, réduisant ainsi les risques de déformation.
Les assemblages de pièces formées sont ensuite réalisés, souvent par soudage, rivetage ou vissage. Une fois ces assemblages effectués, il est possible que les pièces subissent des traitements de surface, comme la peinture, le chromage ou le galvanisage, pour les protéger contre la corrosion, améliorer leur aspect esthétique ou augmenter leur résistance à l’usure.
L’industrie moderne de formage de tôles métalliques utilise aussi des technologies avancées telles que les robots de formage et les machines à commande numérique pour automatiser les processus. Ces technologies permettent de réduire les erreurs humaines, d’augmenter la production et de garantir une qualité constante, même pour des productions en série de pièces complexes.
Le choix de la méthode de formage la mieux adaptée dépend donc d’un certain nombre de critères techniques et économiques. Par exemple, pour des productions en grande série, des méthodes comme l’emboutissage ou le pliage automatisé peuvent être privilégiées pour leur rapidité et leur efficacité. D’autre part, pour des petites séries de pièces très spécifiques ou de haute précision, des procédés comme le découpage au laser ou le poinçonnage peuvent être plus appropriés.
En conclusion, le formage des tôles métalliques est un processus essentiel pour de nombreuses industries modernes. Son efficacité dépend de la capacité à choisir les bons procédés, outils et techniques en fonction des exigences spécifiques de chaque projet, tout en intégrant les considérations de coût, de performance et de délais. Les avancées technologiques, notamment l’automatisation et l’intégration de solutions numériques, ont permis de rendre ces processus de plus en plus rapides, précis et adaptés aux besoins complexes de l’industrie actuelle.
Le formage de tôles métalliques a une grande importance dans l’industrie de fabrication moderne en raison de sa flexibilité et de sa capacité à produire des pièces aux formes et aux dimensions variées. Ce processus permet de répondre à des besoins très spécifiques dans des secteurs très divers, allant de l’automobile à l’aéronautique, en passant par la construction métallique et la production d’équipements électroniques.
La fabrication de composants automobiles en tôle métallique est un exemple frappant de l’utilisation de ces techniques. Les pièces telles que les panneaux de carrosserie, les châssis, les supports et même les composants internes, sont souvent fabriquées à l’aide de techniques de formage. Cela permet de produire des pièces légères mais résistantes, tout en respectant des critères stricts de sécurité, de performance et de coûts. Les techniques comme l’emboutissage et l’assemblage par soudure sont particulièrement courantes dans la fabrication automobile. Ces processus permettent non seulement de façonner la tôle mais aussi de l’assembler de manière robuste, tout en maintenant une production rapide et de haute qualité.
En aérospatiale, les matériaux utilisés sont souvent des alliages légers mais résistants, comme l’aluminium, pour minimiser le poids des aéronefs tout en maintenant une résistance structurelle élevée. Le formage de tôles métalliques dans ce secteur doit répondre à des exigences strictes en termes de précision, de résistance et de résistance à la fatigue. Les tôles d’aluminium sont fréquemment soumises à des procédés de pliage et d’emboutissage pour créer des pièces comme des panneaux de fuselage, des ailes ou des éléments de moteurs. La résistance aux températures extrêmes, aux contraintes de pression et aux conditions climatiques sévères est essentielle, ce qui nécessite des procédés de formage qui préservent les propriétés des matériaux tout en les transformant en formes complexes.
La construction métallique repose également largement sur les procédés de formage de tôles métalliques. Des structures comme les ponts, les bâtiments ou les installations industrielles nécessitent une combinaison de pièces en acier ou en alliages métalliques. Par exemple, le formage de tôles est utilisé pour produire des éléments de charpente métallique, des panneaux de façade, des éléments de toiture et des bardages. Dans ce secteur, les procédés comme le découpage, le pliage et le roulage sont utilisés pour adapter les tôles aux dimensions et aux géométries des structures. Le formage à chaud et à froid joue également un rôle essentiel pour garantir la solidité et la durabilité des composants tout en réduisant les coûts de production.
Le secteur de l’électronique bénéficie également des procédés de formage de tôles métalliques, notamment pour la fabrication de boîtiers, de supports et de châssis pour des appareils tels que des ordinateurs, des téléviseurs et des équipements de communication. Ici, la précision est primordiale, car les pièces doivent non seulement s’assembler correctement mais aussi répondre aux critères de conductivité thermique, de protection contre les interférences électromagnétiques et de dissipation thermique. Le découpage laser et le poinçonnage sont souvent utilisés pour produire des composants de précision, tandis que le pliage permet de donner aux boîtiers la forme requise.
Au-delà de la production de pièces industrielles, le formage des tôles métalliques est également crucial dans la fabrication d’équipements ménagers, tels que des réfrigérateurs, des cuisinières, des lave-linges et autres appareils. Ces appareils nécessitent des pièces métalliques spécifiques, souvent découpées et pliées selon des formes précises pour une meilleure fonctionnalité et un design esthétique. Le poinçonnage et le pliage sont utilisés pour réaliser les éléments extérieurs de ces appareils, tandis que des traitements de surface comme la peinture ou le revêtement en poudre sont appliqués pour donner une finition attrayante et résistante à l’usure.
Un aspect clé du formage de tôles métalliques moderne est l’automatisation. L’utilisation de machines à commande numérique (CNC) et de robots industriels a révolutionné le secteur en permettant des productions de haute précision à des vitesses beaucoup plus élevées. Ces technologies permettent de réduire les erreurs humaines, d’optimiser l’utilisation des matériaux et d’augmenter la productivité tout en conservant une qualité constante. Les systèmes de gestion assistée par ordinateur permettent également de planifier et de suivre les différentes étapes de production, ce qui améliore la gestion de la chaîne de production et réduit les coûts.
En outre, la durabilité et l’efficacité énergétique deviennent de plus en plus des critères décisifs dans le formage des tôles métalliques. Avec la montée en puissance de l’industrie verte et des réglementations de plus en plus strictes en matière de réduction des émissions de CO₂, les fabricants recherchent des solutions qui minimisent l’impact environnemental des procédés de formage. Cela inclut la réduction des consommations d’énergie, l’optimisation des matériaux utilisés, la gestion des déchets de production et la mise en place de processus de recyclage des métaux. L’industrie est ainsi amenée à développer des technologies plus durables tout en répondant aux exigences de productivité et de rentabilité.
En somme, le formage des tôles métalliques est une discipline industrielle en constante évolution, soutenue par les avancées technologiques et l’innovation dans les matériaux et les procédés. Il est essentiel à la production de nombreuses pièces industrielles et de consommables, et il continue de se perfectionner pour répondre aux défis de l’industrie moderne, tout en intégrant des solutions plus écologiques et efficaces.
Dispositifs de formage de tôles métalliques
Les dispositifs de formage de tôles métalliques sont des machines et équipements utilisés pour transformer des tôles métalliques en formes spécifiques en appliquant différentes méthodes mécaniques. Ces dispositifs peuvent être utilisés pour découper, plier, emboutir, rouler, ou façonner des tôles métalliques dans des formes géométriques complexes. Voici un aperçu des principaux dispositifs utilisés dans le formage des tôles métalliques, chacun étant conçu pour un type particulier de transformation :
1. Presse plieuse (ou plieuse)
La presse plieuse est un dispositif utilisé pour plier des tôles métalliques. Ce processus permet de donner à la tôle un angle précis en la soumettant à une force appliquée par un poinçon et une matrice. La presse plieuse peut être manuelle ou équipée de commandes numériques pour assurer une précision optimale.
- Utilisation : Pliage de tôles pour créer des angles, des bords et des formes complexes.
- Exemple : Fabrication de boîtiers métalliques, panneaux de carrosserie.
2. Presse à emboutir (ou presse d’emboutissage)
La presse à emboutir est utilisée pour former des pièces de forme complexe en plaçant la tôle entre un poinçon et une matrice. Sous l’effet de la pression, la tôle prend la forme de la cavité de la matrice.
- Utilisation : Fabrication de pièces profondes ou de formes incurvées, comme les coques et les composants automobiles.
- Exemple : Emboutissage de panneaux de carrosserie pour l’industrie automobile.
3. Poinçonneuse
La poinçonneuse est un dispositif utilisé pour effectuer des découpes, des trous, ou des formes spécifiques dans une tôle métallique. Cette machine est équipée d’un poinçon qui exerce une pression sur la tôle pour créer la forme souhaitée.
- Utilisation : Découpe de trous, de motifs ou de formes dans des tôles métalliques pour des applications diverses.
- Exemple : Fabrication de boîtiers ou de pièces avec des découpes complexes.
4. Découpeuse laser
La découpeuse laser est une machine de haute précision qui utilise un faisceau laser pour découper ou graver des tôles métalliques. Ce dispositif est particulièrement adapté pour des découpes de formes complexes avec une grande précision.
- Utilisation : Découpe de tôles métalliques avec des formes précises, sans contact direct.
- Exemple : Fabrication de composants électroniques ou de pièces automobiles.
5. Machine de découpe plasma
La découpe plasma utilise un jet de plasma à haute température pour couper des tôles métalliques. Ce procédé est particulièrement adapté pour couper des métaux de faible à moyenne épaisseur.
- Utilisation : Découpe de tôles métalliques de manière rapide, avec moins de précision que la découpe laser.
- Exemple : Découpe de tôles pour des applications industrielles lourdes, telles que la construction de structures métalliques.
6. Machine de découpe au jet d’eau
Le découpage au jet d’eau utilise un jet d’eau à haute pression, souvent mélangé avec un abrasif, pour découper les tôles métalliques. Ce procédé est sans chaleur, ce qui empêche la déformation thermique de la tôle.
- Utilisation : Découpe de tôles métalliques épaisses ou de matériaux sensibles à la chaleur.
- Exemple : Découpe de matériaux composites ou de métaux durs.
7. Rouleuse (ou machine de roulage)
La rouleuse est utilisée pour courber ou arrondir des tôles métalliques en les faisant passer entre des rouleaux. Ce procédé est couramment utilisé pour créer des pièces de forme circulaire ou cylindrique.
- Utilisation : Façonnage de tôles métalliques en formes cylindriques ou coniques.
- Exemple : Fabrication de tuyaux, réservoirs ou structures cylindriques.
8. Lamineuse (ou laminage)
Le laminage est un procédé de déformation qui consiste à réduire l’épaisseur de la tôle métallique en la faisant passer entre deux rouleaux. Il peut être effectué à chaud ou à froid, selon le type de métal et la précision requise.
- Utilisation : Réduction de l’épaisseur des tôles et formation de pièces plates.
- Exemple : Fabrication de tôles minces utilisées dans la production de composants automobiles ou de matériaux de construction.
9. Machine à emboutir à froid (ou matrice à emboutir)
Les machines à emboutir à froid sont utilisées pour créer des formes profondes dans des tôles métalliques sans chauffer le matériau. Cette méthode est souvent utilisée pour produire des pièces en métal à partir de tôles de faible épaisseur.
- Utilisation : Création de formes profondes ou complexes à partir de tôles métalliques minces.
- Exemple : Fabrication de pièces pour l’industrie de la consommation, comme les canettes en métal.
10. Machine à cintrer (ou cintreuse)
La cintreuse est utilisée pour donner des courbes spécifiques à une tôle métallique. Elle peut être utilisée pour créer des pièces de forme sinusoïdale ou de petites courbures.
- Utilisation : Façonnage de tôles métalliques pour des courbes douces ou serrées.
- Exemple : Fabrication de cadres ou de tuyaux en métal.
11. Ligne de production de tôles embouties (ou presses de découpe et de formage)
Ces lignes sont des installations automatisées qui combinent plusieurs étapes de formage, allant du découpage à l’emboutissage, dans un processus continu. Elles sont utilisées pour produire en série de grandes quantités de pièces.
- Utilisation : Fabrication en série de pièces métalliques complexes pour des secteurs comme l’automobile ou l’électroménager.
- Exemple : Production de panneaux de carrosserie pour l’industrie automobile.
12. Plieuse hydraulique
La plieuse hydraulique utilise un système hydraulique pour appliquer la force de pliage. Elle permet une grande flexibilité et est adaptée à des tôles métalliques de différentes épaisseurs.
- Utilisation : Pliage de tôles métalliques de manière précise, particulièrement pour des séries de production.
- Exemple : Fabrication de composants pour la construction ou l’industrie électronique.
Conclusion
Les dispositifs de formage de tôles métalliques sont essentiels pour la production de pièces métalliques utilisées dans une grande variété d’applications industrielles. Le choix de l’équipement dépend du type de forme souhaitée, du matériau utilisé, et des caractéristiques de production telles que la précision et le volume. Ces machines permettent de transformer les tôles métalliques en pièces finales robustes, légères et adaptées aux besoins spécifiques de chaque secteur industriel.
Les dispositifs de formage de tôles métalliques sont essentiels pour la transformation de matériaux en pièces de plus en plus complexes et précises. Ces machines sont utilisées pour manipuler les tôles métalliques, souvent sous forme de grandes feuilles plates, afin de les transformer en composants utilisés dans de nombreuses industries, telles que l’automobile, l’aéronautique, la construction, et bien d’autres. La diversité des procédés et des machines disponibles permet de répondre à des besoins très spécifiques, allant de la simple découpe à des formes plus complexes nécessitant de l’emboutissage ou du pliage.
Les presses plieuses et les presses à emboutir sont des équipements incontournables pour façonner des tôles métalliques. La presse plieuse est particulièrement utile pour obtenir des angles précis et réaliser des plis dans la tôle, ce qui est essentiel pour des pièces comme les boîtiers ou les supports. La presse à emboutir, quant à elle, est utilisée pour créer des formes plus profondes et complexes, comme les panneaux de carrosserie automobile, en appliquant une force importante sur la tôle pour la faire prendre la forme du moule.
Les machines de découpe, telles que les découpeuses laser, à plasma ou au jet d’eau, jouent également un rôle crucial dans la fabrication des pièces. Ces technologies permettent une découpe très précise et rapide des tôles métalliques, tout en minimisant les risques de déformation. La découpe au laser, en particulier, est idéale pour les découpes complexes et fines, tandis que la découpe plasma est utilisée pour des matériaux plus épais ou des applications où la rapidité est essentielle. La découpe au jet d’eau, quant à elle, offre l’avantage de ne pas générer de chaleur, ce qui permet d’éviter des déformations thermiques qui peuvent altérer les propriétés du matériau.
Les rouleuses et les machines de laminage sont utilisées pour donner des courbes aux tôles métalliques. Ces dispositifs permettent de transformer des tôles plates en formes circulaires ou cylindriques, ce qui est indispensable dans des applications comme la fabrication de tuyaux ou de réservoirs. Le laminage, qu’il soit à chaud ou à froid, permet également de réduire l’épaisseur des tôles et d’améliorer leurs propriétés mécaniques, ce qui les rend plus adaptées à des applications nécessitant une grande résistance à la traction.
Les machines de poinçonnage et les machines à emboutir à froid, de leur côté, sont utilisées pour créer des trous ou des motifs dans les tôles métalliques. Ces procédés sont particulièrement efficaces lorsqu’il est nécessaire de produire des formes répétitives à grande échelle. Les poinçonneuses à commande numérique permettent d’optimiser les cycles de production et d’assurer une précision élevée lors de la fabrication de pièces complexes. Ces machines sont idéales pour des applications où la rapidité et la répétabilité sont essentielles, comme dans la production de pièces automobiles ou électroménagères.
Les lignes de production automatisées, qui combinent plusieurs procédés de formage comme la découpe, l’emboutissage, et le pliage, sont également de plus en plus courantes. Ces lignes permettent une production en série de composants métalliques complexes, tout en garantissant une qualité constante et une grande efficacité. Ce type d’équipement est essentiel pour des industries telles que l’automobile, où des milliers de pièces doivent être produites en un temps record.
L’intégration de technologies avancées, telles que la commande numérique par ordinateur (CNC), dans ces machines permet de guider avec une précision extrême chaque étape du processus de fabrication. La CNC permet de programmer les mouvements de la machine avec une exactitude millimétrique, ce qui est indispensable pour la production de pièces à géométrie complexe. L’automatisation de ces procédés permet également d’améliorer la productivité et de réduire les coûts en minimisant les erreurs humaines et en maximisant l’efficacité de la production.
De plus, avec les préoccupations environnementales croissantes, les dispositifs de formage sont de plus en plus conçus pour être écoénergétiques et pour optimiser l’utilisation des matériaux. Le recyclage des tôles métalliques, la réduction des émissions de CO2 et la gestion efficace des déchets de production sont désormais des priorités dans la conception de ces équipements. Cela conduit à une plus grande durabilité dans les procédés industriels tout en maintenant une rentabilité.
En résumé, les dispositifs de formage de tôles métalliques sont au cœur de la fabrication moderne, permettant la production de pièces essentielles pour une variété d’industries. L’innovation continue dans ces machines, notamment avec l’automatisation, la commande numérique et l’intégration de technologies plus respectueuses de l’environnement, continue de transformer ce secteur, permettant de répondre aux exigences croissantes en matière de précision, de rapidité et de durabilité.
Les avancées technologiques et l’optimisation des processus de production dans le formage des tôles métalliques ont permis de répondre à des exigences toujours plus strictes, tant en termes de performance que de respect des normes environnementales. L’automatisation, couplée à des dispositifs de haute précision, permet aujourd’hui de fabriquer des pièces de plus en plus complexes tout en améliorant la productivité et en réduisant les coûts de fabrication.
Les machines à commande numérique (CNC), par exemple, ont révolutionné la manière dont les tôles métalliques sont formées. Ces machines permettent de programmer les mouvements des outils de manière précise et répétitive, assurant ainsi une qualité constante, même pour des séries de production en grande quantité. Cela est particulièrement avantageux dans des secteurs où la précision est essentielle, comme l’aéronautique ou l’industrie automobile, où chaque pièce doit correspondre parfaitement à des spécifications strictes.
Le développement des technologies de simulation est également un facteur clé dans l’évolution des procédés de formage. Avant même que la production ne commence, les ingénieurs peuvent simuler les processus de formage à l’aide de logiciels spécialisés. Ces outils permettent d’optimiser la conception des outils et des matrices, d’identifier les problèmes potentiels de déformation ou de fissuration des matériaux, et d’ajuster les paramètres de production pour éviter des erreurs coûteuses. La simulation numérique permet également de prédire le comportement du métal sous différentes contraintes, facilitant ainsi l’adaptation des procédés de formage aux matériaux les plus complexes.
L’intégration des systèmes de vision artificielle et de contrôle de qualité automatisé permet également d’améliorer la précision des processus de formage. Ces systèmes peuvent analyser en temps réel la qualité des pièces produites, détectant des défauts invisibles à l’œil nu, tels que des fissures microscopiques ou des défauts de surface. Grâce à cela, les fabricants peuvent corriger immédiatement toute anomalie, minimisant ainsi les risques de pièces défectueuses et améliorant l’efficacité globale de la production.
Les matériaux utilisés dans le formage des tôles métalliques ont également évolué. De nouveaux alliages plus résistants mais plus légers sont constamment développés, ce qui permet de répondre à des besoins spécifiques dans des secteurs comme l’aéronautique, l’automobile ou la construction. Par exemple, l’utilisation de tôles d’acier à haute résistance ou d’alliages d’aluminium permet de réduire le poids des composants tout en augmentant leur solidité, ce qui est essentiel pour améliorer les performances énergétiques des véhicules ou des structures métalliques.
En outre, l’optimisation des matériaux est devenue une priorité dans le formage des tôles métalliques. De nouvelles techniques permettent de réduire les pertes de matière lors des étapes de découpe ou de formage. Par exemple, les logiciels de gestion des matériaux peuvent être utilisés pour planifier le découpage des tôles de manière à minimiser les chutes, ce qui réduit les coûts et l’impact environnemental. De plus, ces chutes peuvent être recyclées et réutilisées dans d’autres processus, contribuant à une production plus durable.
Une tendance croissante dans l’industrie est l’intégration de la fabrication additive, ou impression 3D, avec les techniques de formage des tôles métalliques. Bien que la fabrication additive soit souvent associée à des matériaux plastiques, elle peut également être utilisée pour produire des pièces métalliques complexes, qui peuvent ensuite être intégrées dans un processus de formage plus traditionnel. Cette combinaison permet de produire des prototypes rapides, des pièces de rechange sur demande ou des composants très complexes qu’il serait difficile de produire avec des méthodes conventionnelles.
Les défis environnementaux ont conduit l’industrie à repenser ses procédés de fabrication. Par exemple, le formage de tôles métalliques peut générer des émissions de chaleur, de gaz ou d’autres polluants. Les fabricants sont donc de plus en plus soumis à des régulations strictes pour minimiser leur empreinte carbone. L’introduction de procédés plus « verts », comme le recyclage des métaux et l’utilisation d’énergies renouvelables pour alimenter les machines de formage, devient une priorité. Ces initiatives contribuent non seulement à la réduction des émissions, mais permettent aussi de réaliser des économies d’énergie sur le long terme.
En parallèle, la recherche et développement dans le domaine des matériaux continue de croître. Les tôles métalliques sont désormais disponibles dans une gamme de matériaux spécifiques adaptés à des applications de plus en plus variées. Des alliages d’aluminium ultra-légers aux matériaux composites métalliques, ces innovations permettent de répondre aux besoins croissants de réduction de poids dans des industries comme l’automobile et l’aéronautique, tout en assurant une résistance accrue. Les métaux à haute résistance à la corrosion ou à l’usure sont également en forte demande, notamment pour les environnements marins, industriels ou chimiques.
Les processus de formage de tôles métalliques continuent donc de se diversifier et de se perfectionner. De nouvelles technologies, telles que l’intelligence artificielle et l’analyse de données, permettent aux machines de s’adapter en temps réel aux conditions de production, ce qui offre encore plus de précision, d’efficacité et de flexibilité. En intégrant ces technologies dans des systèmes de production intelligents et automatisés, l’industrie du formage de tôles métalliques est en train de se transformer pour répondre aux défis futurs, qu’il s’agisse de durabilité, de performance ou de réduction des coûts.
Machines de travail de la tôle

Les machines de travail de la tôle sont des équipements utilisés dans l’industrie pour transformer des tôles métalliques en pièces finies ou semi-finies, en utilisant une variété de procédés mécaniques. Ces machines sont essentielles dans des secteurs tels que la fabrication automobile, la construction métallique, l’aéronautique, l’électroménager, et bien d’autres, où la production de pièces métalliques spécifiques est nécessaire. Voici un aperçu des machines couramment utilisées dans le travail de la tôle, chacune ayant un rôle bien défini selon le type de transformation souhaitée.
1. Presse plieuse (Plieuse)
La presse plieuse est l’une des machines les plus courantes pour le travail de la tôle. Elle permet de plier des tôles métalliques en appliquant une pression sur la tôle entre une matrice et un poinçon. Ce type de machine est essentiel pour réaliser des angles précis ou des courbes dans des tôles métalliques de différentes épaisseurs.
- Applications : Fabrication de boîtiers, supports, composants de charpente métallique, etc.
- Caractéristiques : Peut être équipée de commandes numériques (CNC) pour une plus grande précision et répétabilité.
2. Poinçonneuse
La poinçonneuse est une machine utilisée pour effectuer des trous ou des découpes dans une tôle métallique. Elle fonctionne en exerçant une pression sur la tôle à travers un poinçon qui va percer la matière. Cette machine peut également être utilisée pour effectuer des découpes complexes ou des motifs dans les tôles métalliques.
- Applications : Découpe de trous pour vis, rivets, ou autres fixations, fabrication de motifs décoratifs ou de pièces avec des ouvertures.
- Caractéristiques : Poinçonnage rapide et efficace pour des séries de production en grande quantité.
3. Découpeuse laser
La découpeuse laser utilise un faisceau laser pour couper avec une précision extrême des tôles métalliques, notamment celles de faibles à moyennes épaisseurs. Elle offre un avantage de haute précision sans contact direct, ce qui permet de réduire les risques de déformation ou de marquage.
- Applications : Découpe de formes complexes pour des pièces d’une grande précision, idéale pour des prototypes ou des petites séries.
- Caractéristiques : Utilisation d’un faisceau de lumière concentré qui fond, brûle ou vaporise le métal, avec un contrôle informatique pour des découpes complexes.
4. Découpeuse plasma
La découpe plasma utilise un jet de gaz ionisé à haute température pour découper des tôles métalliques. Cette machine est plus rapide que la découpe au laser, mais elle est souvent moins précise. Elle est particulièrement efficace pour couper des métaux de moyenne à grande épaisseur.
- Applications : Découpe rapide de tôles métalliques épaisses dans l’industrie de la construction, de la production de structures métalliques et du secteur naval.
- Caractéristiques : Peut couper des matériaux conducteurs d’électricité comme l’acier, l’aluminium, le cuivre, etc.
5. Découpe au jet d’eau
Le découpage au jet d’eau utilise un jet d’eau à très haute pression, souvent avec un abrasif, pour couper les tôles métalliques. Ce procédé ne génère pas de chaleur, ce qui évite les déformations thermiques. Il est particulièrement adapté pour couper des matériaux sensibles à la chaleur.
- Applications : Découpe de tôles métalliques épaisses, matériaux composites, ou métaux durs sans risque de modification des propriétés matérielles.
- Caractéristiques : Aucune chaleur n’est générée, ce qui permet de conserver les propriétés du matériau sans déformation.
6. Rouleuse
La rouleuse est utilisée pour courber ou former des tôles métalliques en leur donnant une forme cylindrique ou conique. Ce type de machine fonctionne en faisant passer la tôle entre des rouleaux qui exercent une pression sur la tôle pour la plier.
- Applications : Fabrication de tuyaux, réservoirs, structures métalliques circulaires, ou côniques.
- Caractéristiques : Permet de créer des formes géométriques complexes avec une précision élevée.
7. Laminoir (ou machine de laminage)
Les machines de laminage sont utilisées pour réduire l’épaisseur des tôles métalliques, les rendre plus fines ou obtenir des propriétés mécaniques améliorées. Le laminage peut se faire à chaud ou à froid, selon les besoins du processus.
- Applications : Fabrication de tôles minces, produits en acier ou en aluminium pour des applications variées (automobile, construction, etc.).
- Caractéristiques : Permet de transformer des métaux de grande épaisseur en feuilles minces tout en modifiant leurs propriétés mécaniques, telles que la résistance à la traction.
8. Machine à emboutir
La machine à emboutir est utilisée pour fabriquer des pièces métalliques en forme de cuve, de coque, ou de toute autre forme complexe à partir d’une tôle. Ce procédé est généralement réalisé à froid, mais il peut également être effectué à chaud pour certains matériaux.
- Applications : Fabrication de composants de carrosserie automobile, réservoirs, cuves, et autres pièces nécessitant une forme profonde.
- Caractéristiques : Permet de transformer une tôle plate en une forme complexe à l’aide d’un poinçon et d’une matrice.
9. Cintreuse
La cintreuse est une machine utilisée pour créer des courbes ou des arcs dans des tôles métalliques, permettant de réaliser des pièces avec des formes sinusoïdales ou des arcs complexes. Ce processus est souvent utilisé dans les secteurs de la construction et de l’industrie navale.
- Applications : Fabrication de supports cintrés, cadres, tuyaux et autres composants à forme courbe.
- Caractéristiques : Capacité à plier des tôles métalliques sans compromettre leur résistance.
10. Plieuse hydraulique
Une plieuse hydraulique est une machine de pliage qui utilise un système hydraulique pour appliquer une pression sur la tôle métallique et obtenir des plis précis. Elle est couramment utilisée pour les tôles d’épaisseur variable et offre une grande flexibilité et précision.
- Applications : Pliage de tôles pour créer des supports, boîtiers, et autres structures métalliques.
- Caractéristiques : Permet un contrôle précis de la force appliquée et est idéale pour des productions en série.
11. Meuleuse ou meuleuse d’angle
Les meuleuses sont des machines utilisées pour meuler, polir ou finir les bords des tôles métalliques. Elles sont souvent utilisées pour éliminer les bavures ou ajuster les formes des pièces après leur découpe ou leur emboutissage.
- Applications : Finition de pièces métalliques, ébarbage, et préparation de surfaces pour le soudage ou la peinture.
- Caractéristiques : Équipée de disques abrasifs pour traiter les surfaces métalliques de manière rapide et efficace.
12. Ligne de production automatique (Systèmes intégrés)
Les lignes de production automatisées sont des ensembles de machines reliées entre elles pour exécuter une série de processus de transformation de la tôle métallique, allant de la découpe à l’assemblage, en passant par le pliage, l’emboutissage, etc. Ces systèmes sont souvent utilisés dans les grandes productions industrielles pour produire des pièces en grande quantité avec un minimum d’intervention humaine.
- Applications : Production de pièces automobile, composants électroniques, et autres articles nécessitant une production de masse.
- Caractéristiques : Intégration de plusieurs machines pour une efficacité maximale, réduisant le temps de cycle et augmentant la productivité.
En résumé, ces machines de travail de la tôle couvrent une gamme de procédés permettant de transformer les tôles métalliques en une multitude de formes et de produits finis pour des applications variées. Les avancées technologiques dans les domaines de l’automatisation, de la précision et de l’efficacité énergétique continuent de façonner l’industrie du travail de la tôle, rendant ces machines essentielles à la production moderne.
Les machines de travail de la tôle jouent un rôle crucial dans la fabrication industrielle, offrant une variété de solutions pour transformer les tôles métalliques en produits finis ou semi-finis. Ces équipements sont utilisés dans plusieurs secteurs, notamment l’automobile, la construction, l’électroménager, l’aéronautique, et bien d’autres, où la précision et l’efficacité sont des critères primordiaux. Ces machines permettent de réaliser une large gamme de transformations, du pliage à la découpe, en passant par l’emboutissage, le cintrage et le laminage.
Une des caractéristiques majeures des machines de travail de la tôle modernes est leur capacité à être intégrées dans des lignes de production automatisées. Ces systèmes peuvent inclure plusieurs machines reliées entre elles, chacune accomplissant une tâche spécifique, comme le découpage, le formage, et l’assemblage, créant ainsi un flux de production continu et sans faille. L’automatisation permet d’augmenter la productivité tout en réduisant les erreurs humaines et les temps d’arrêt. Les systèmes de contrôle par commande numérique (CNC) et les robots industriels jouent également un rôle clé dans la précision et la répétabilité des processus de transformation.
Les machines de découpe laser, plasma et jet d’eau sont souvent utilisées pour réaliser des découpes nettes et précises dans les tôles métalliques. Le découpage au laser, par exemple, est idéal pour des formes complexes et des détails fins, offrant une grande flexibilité. De son côté, le découpage au plasma est plus adapté aux matériaux d’épaisseur moyenne à épaisse et est souvent privilégié pour des applications nécessitant une production rapide. Quant au découpage au jet d’eau, il permet d’éviter les déformations thermiques et est utilisé pour couper des matériaux sensibles à la chaleur ou des matériaux composites.
Les machines de pliage, comme la presse plieuse, sont capables de réaliser des plis très précis dans les tôles, permettant de créer des angles spécifiques pour des pièces telles que des boîtiers, des supports ou des structures. Ces machines peuvent être équipées de commandes numériques pour une précision accrue et une plus grande flexibilité, ce qui permet de plier des tôles de différentes épaisseurs et de géométries variées. Les presses hydrauliques, par exemple, offrent un contrôle précis de la force appliquée et sont souvent utilisées dans des productions de grandes séries.
Les poinçonneuses sont utilisées pour réaliser des trous dans les tôles métalliques. Ces machines exercent une pression sur la tôle à travers un poinçon, créant ainsi des ouvertures ou des motifs dans la matière. Les poinçonneuses modernes, équipées de systèmes CNC, permettent de produire des pièces complexes et des perforations multiples avec une grande rapidité et une précision élevée.
Le formage des tôles à l’aide de machines comme les rouleuses et les machines à emboutir est également un aspect fondamental du travail de la tôle. Les rouleuses permettent de créer des formes cylindriques ou coniques, en transformant des tôles plates en pièces courbes ou arrondies, comme des tuyaux ou des réservoirs. Les machines à emboutir, quant à elles, sont utilisées pour transformer une tôle plane en une forme plus complexe, souvent utilisée dans la fabrication de pièces automobiles, de réservoirs ou d’autres structures métalliques.
L’intégration de nouvelles technologies, telles que les systèmes de vision artificielle et le contrôle de qualité automatisé, contribue à améliorer encore la précision des processus de travail de la tôle. Ces systèmes peuvent détecter des défauts microscopiques dans les pièces finies, comme des fissures ou des irrégularités de surface, assurant ainsi une qualité constante et une conformité aux normes de production. Ces outils sont utilisés non seulement pour améliorer la qualité des pièces mais aussi pour optimiser l’efficacité des processus, permettant ainsi une détection en temps réel des défauts et une correction immédiate.
Les machines de travail de la tôle modernes sont également conçues pour répondre à des critères de durabilité et d’efficacité énergétique. L’optimisation de la consommation d’énergie, la réduction des émissions de gaz à effet de serre, et l’utilisation de matériaux recyclés sont des priorités dans le développement de ces équipements. De plus, l’utilisation accrue de l’intelligence artificielle et de l’analyse de données permet une gestion en temps réel des machines, ce qui permet d’adapter instantanément les paramètres de production pour maximiser la performance tout en réduisant les coûts.
En somme, les machines de travail de la tôle constituent le fondement de nombreuses industries modernes, en permettant la fabrication de pièces métalliques avec une précision et une rapidité exceptionnelles. L’innovation technologique continue d’améliorer ces équipements, rendant leur utilisation plus flexible, plus efficace, et plus respectueuse de l’environnement, tout en répondant aux exigences toujours croissantes de qualité, de production en série et de coûts réduits. Ces évolutions ouvrent la voie à une production industrielle plus automatisée, plus durable, et plus rapide, en réponse aux défis économiques et écologiques du 21e siècle.
L’évolution continue des machines de travail de la tôle repose également sur l’adoption de matériaux avancés et l’intégration de nouveaux procédés de fabrication. Par exemple, l’utilisation de matériaux composites et d’alliages métalliques spéciaux est devenue courante dans de nombreuses industries, en particulier dans l’automobile et l’aéronautique, où la légèreté et la résistance sont cruciales. Les machines de travail de la tôle doivent être capables de traiter ces matériaux spécifiques tout en maintenant la précision et la qualité des pièces finies.
Une autre avancée significative concerne la modularité des machines. De plus en plus de machines de travail de la tôle sont conçues pour être modulaires, permettant aux utilisateurs de les adapter à des besoins spécifiques. Cela comprend des fonctionnalités comme l’ajout ou le retrait de différents outils ou modules de transformation (poinçonnage, découpe, emboutissage, etc.) selon les exigences de production. Cette flexibilité permet non seulement de s’adapter à un large éventail de tâches, mais aussi de réduire les coûts de production, car les fabricants n’ont pas besoin de machines distinctes pour chaque tâche.
L’intégration de la robotique et de l’automatisation avancée a également modifié le paysage des machines de travail de la tôle. Les robots peuvent effectuer des tâches telles que le chargement et le déchargement des tôles, le contrôle de qualité, ou même la gestion des flux de production, ce qui permet de libérer les opérateurs pour des tâches plus complexes. L’automatisation permet d’atteindre des vitesses de production plus élevées et d’améliorer la cohérence des pièces produites, tout en réduisant les risques d’erreurs humaines. Cela contribue également à la sécurité, car les opérateurs sont moins souvent en contact direct avec les machines.
De plus, les systèmes de gestion de production intelligents (ERP, MES) sont de plus en plus utilisés pour suivre et contrôler le flux de travail à travers les différentes étapes du processus de fabrication. Ces systèmes permettent de collecter et d’analyser des données en temps réel sur la production, permettant ainsi une prise de décision plus éclairée. Par exemple, en surveillant les temps d’arrêt, les pannes de machine, ou les défauts de qualité, ces systèmes peuvent prédire quand une machine nécessitera une maintenance préventive, ce qui minimise les arrêts non planifiés et optimise l’efficacité globale de la production.
Un autre aspect important est l’optimisation des ressources. Avec la pression croissante sur les entreprises pour qu’elles réduisent les coûts et les déchets, les machines modernes de travail de la tôle intègrent des fonctionnalités qui permettent de mieux utiliser les matériaux, de réduire les déchets et d’optimiser les processus de production. Par exemple, la gestion intelligente des chutes de tôle, qui peuvent être réutilisées ou recyclées, permet non seulement de réduire les coûts des matières premières, mais aussi de diminuer l’impact environnemental des opérations de fabrication.
Dans un contexte de soutenabilité environnementale renforcée, les machines de travail de la tôle sont également de plus en plus conçues pour être économes en énergie. Cela inclut l’utilisation de technologies écoénergétiques dans les moteurs, les systèmes hydrauliques et les dispositifs de commande. L’optimisation de l’efficacité énergétique non seulement aide les entreprises à réduire leur empreinte carbone, mais elle permet également de diminuer les coûts opérationnels liés à la consommation d’énergie.
Les normes de sécurité et les réglementations industrielles continuent de se renforcer, obligeant les fabricants de machines de travail de la tôle à intégrer des dispositifs de sécurité sophistiqués. Cela inclut des systèmes de détection de proximité, des protections automatiques, des arrêts d’urgence instantanés, ainsi que des interfaces utilisateur qui minimisent les risques d’erreurs humaines. L’évolution de ces technologies contribue à créer un environnement de travail plus sûr et à réduire les risques d’accidents industriels.
Enfin, le futur du travail de la tôle est fortement influencé par l’intelligence artificielle (IA) et l’apprentissage automatique. Ces technologies permettent aux machines de s’adapter et d’optimiser automatiquement les paramètres de production en fonction des conditions de fabrication en temps réel. Par exemple, des systèmes intelligents peuvent ajuster les vitesses de coupe ou de formage, ou encore détecter des défauts avant même qu’ils n’apparaissent visuellement, en analysant les données générées par les machines.
Les progrès dans le domaine des logiciels de conception et de simulation jouent également un rôle clé. Aujourd’hui, avant de lancer la production, les ingénieurs peuvent simuler chaque étape du processus de fabrication, des découpe et formage jusqu’aux opérations de finition, pour détecter d’éventuels problèmes et optimiser les cycles de production. Ces simulations sont devenues essentielles pour garantir une production efficace et pour réduire les erreurs humaines dans la phase de conception.
Dans l’ensemble, l’industrie du travail de la tôle est en pleine transformation, avec des machines plus intelligentes, plus écologiques et plus flexibles. L’intégration de nouvelles technologies, la recherche continue d’innovations matérielles et la montée en puissance de l’automatisation et de la robotique permettent aux entreprises de répondre à des demandes de plus en plus complexes tout en réduisant leur impact environnemental et leurs coûts de production. Les machines de travail de la tôle de demain seront non seulement plus efficaces, mais aussi plus polyvalentes et adaptées aux défis économiques et écologiques du futur.
Machines de transformation de tôle
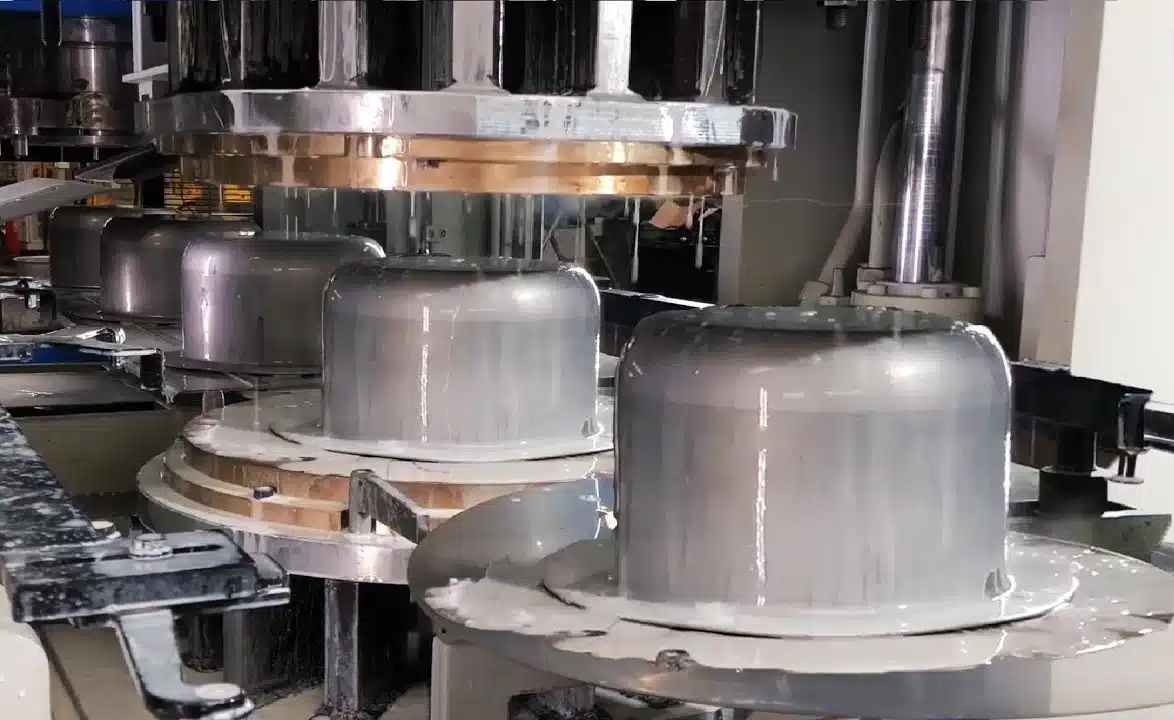
Les machines de transformation de tôle sont des équipements utilisés dans l’industrie pour modifier la forme, la taille, et les caractéristiques des tôles métalliques afin de produire des pièces spécifiques qui répondent aux besoins des différentes industries. Ces machines couvrent une gamme de procédés allant de la découpe, au formage, au pliage, jusqu’à l’emboutissage et au soudage. Chaque machine est conçue pour effectuer une tâche particulière dans la chaîne de production, et leur évolution technologique permet d’améliorer la productivité, la précision et la flexibilité des processus industriels.
1. Machines de découpe
Les machines de découpe de tôle sont essentielles pour créer des pièces métalliques à partir de tôles plates en effectuant des découpes nettes et précises.
- Découpe au laser : Utilise un faisceau laser pour couper avec une grande précision. Cette méthode est idéale pour des formes complexes et des découpes très fines. Elle est utilisée dans des industries comme l’aéronautique, l’automobile, et la fabrication de prototypes.
- Découpe au plasma : Utilise un jet de gaz ionisé à haute température pour découper des tôles métalliques. Ce procédé est plus rapide que le découpage au laser, mais moins précis. Il est particulièrement utilisé pour couper des tôles plus épaisses.
- Découpe au jet d’eau : Utilise un jet d’eau à haute pression pour couper des tôles métalliques, souvent en ajoutant un abrasif pour augmenter l’efficacité. Ce procédé est idéal pour les matériaux sensibles à la chaleur.
- Poinçonnage : Utilise un poinçon et une matrice pour créer des trous, des découpes ou des formes spécifiques dans la tôle. Les poinçonneuses modernes sont souvent automatisées et contrôlées par des systèmes CNC pour une précision optimale.
- Scie à ruban : Utilisée pour couper des tôles métalliques de manière plus linéaire, cette machine est idéale pour des découpes simples et régulières.
2. Machines de formage
Les machines de formage sont utilisées pour changer la forme des tôles métalliques sans en modifier leur volume.
- Plieuse : Utilise une pression pour plier des tôles métalliques à des angles spécifiques. Ce procédé est utilisé pour produire des pièces comme des boîtiers, des panneaux ou des supports.
- Rouleuse : Permet de courber des tôles métalliques pour obtenir des formes cylindriques ou coniques. Cette machine est utilisée pour fabriquer des réservoirs, des tuyaux, et d’autres formes courbes.
- Machine à emboutir : Utilisée pour créer des formes profondes à partir d’une tôle métallique, l’emboutissage permet de produire des pièces comme des cuves, des coques, ou des composants automobiles.
- Cintreuse : Utilisée pour produire des courbes ou des arcs dans les tôles, cette machine est fréquemment utilisée pour la fabrication de supports cintrés et de structures métalliques.
3. Machines de laminage
Le laminage est un processus qui consiste à réduire l’épaisseur d’une tôle métallique tout en améliorant ses propriétés mécaniques. Il peut être effectué à chaud ou à froid, selon les besoins du processus.
- Laminoir à chaud : Permet de réduire l’épaisseur des tôles métalliques à des températures élevées, souvent utilisées pour produire des tôles fines ou des feuilles d’acier.
- Laminoir à froid : Utilisé pour former des tôles métalliques à température ambiante, ce procédé permet de produire des tôles d’une grande précision, avec des surfaces lisses et des propriétés mécaniques améliorées.
4. Machines d’emboutissage et d’estampage
Ces machines sont utilisées pour effectuer des transformations complexes dans les tôles métalliques, telles que la création de pièces profondes ou des formes spécifiques.
- Presses à emboutir : Utilisent un poinçon et une matrice pour effectuer des transformations complexes de la tôle, comme l’emboutissage, l’étirage ou l’extrusion. Ce processus est utilisé dans des industries comme l’automobile et l’électroménager pour créer des pièces comme des carrosseries, des réservoirs, des coques, etc.
- Machines à estampage : Similaires aux presses à emboutir, mais elles sont spécialement conçues pour effectuer des frappes à haute pression, permettant de former des pièces complexes et de grandes dimensions à partir de tôles métalliques.
5. Machines de soudage
Le soudage des tôles métalliques est souvent nécessaire pour assembler plusieurs pièces ou pour renforcer une structure. Plusieurs types de machines de soudage sont utilisés dans l’industrie de transformation de la tôle.
- Soudage MIG/MAG : Utilise un fil électrode et un gaz pour souder les tôles métalliques. Ce procédé est souvent utilisé dans l’industrie automobile, aéronautique et navale.
- Soudage TIG : Utilise une électrode en tungstène non consommable et un gaz inerte pour souder les tôles métalliques. Il est particulièrement adapté pour les métaux légers et les alliages, offrant une grande précision.
- Soudage par résistance : Utilisé principalement pour souder des tôles métalliques fines, ce procédé est couramment utilisé dans les lignes de production automobile pour assembler des pièces de carrosserie.
- Soudage laser : Utilise un faisceau laser pour effectuer des soudures de haute précision sans nécessité d’ajout de matériau. Ce procédé est utilisé pour des applications où une faible déformation est souhaitée.
6. Machines de finition et de traitement de surface
Une fois que la tôle a été formée, découpée ou soudée, elle passe souvent par des machines de finition pour améliorer la qualité de la surface et préparer la pièce pour le revêtement ou l’assemblage final.
- Meuleuses et polisseuses : Utilisées pour affiner les bords des tôles, éliminer les bavures, et polir la surface des pièces métalliques. Ces machines sont importantes pour garantir une finition lisse et esthétique.
- Machines de grenaillage : Utilisent des billes d’acier pour nettoyer la surface des tôles métalliques et éliminer les impuretés, ce qui est particulièrement important avant l’application de peintures ou de traitements de surface.
- Laveuses de pièces métalliques : Utilisées pour nettoyer les tôles métalliques avant ou après la transformation, afin d’éliminer les huiles, les débris, et les contaminants de la surface.
7. Machines de contrôle et de mesure
Les machines de contrôle et de mesure permettent de vérifier la précision et la qualité des pièces produites. Elles peuvent être utilisées pour mesurer les dimensions des pièces, détecter les défauts, ou contrôler la qualité des soudures.
- Machines de contrôle tridimensionnel (CMM) : Permettent de mesurer avec précision les dimensions des pièces en trois dimensions, garantissant leur conformité avec les spécifications techniques.
- Systèmes de vision industrielle : Utilisent des caméras et des logiciels de traitement d’image pour inspecter les pièces et détecter les défauts visibles, tels que des fissures ou des imperfections de surface.
Les machines de transformation de tôle constituent ainsi un élément clé dans l’industrie moderne, permettant une grande variété de processus allant de la découpe à la finition. Leur rôle dans l’optimisation des processus industriels, la réduction des coûts et la maximisation de la productivité est crucial dans des secteurs tels que l’automobile, l’aéronautique, la construction, et bien d’autres.
Les machines de transformation de tôle jouent un rôle essentiel dans l’industrie manufacturière moderne. Elles permettent de transformer des tôles métalliques brutes en pièces finies ou semi-finies qui sont ensuite utilisées dans des secteurs variés, comme l’automobile, l’aéronautique, la construction, et la fabrication d’équipements industriels. L’innovation technologique continue dans ce domaine a permis de rendre ces machines plus efficaces, plus précises et plus flexibles, répondant ainsi aux exigences croissantes en termes de productivité, de coût et de qualité.
Les avancées dans les systèmes de commande numérique par ordinateur (CNC) et dans l’automatisation ont grandement contribué à améliorer l’efficacité de ces machines. Grâce à ces technologies, les machines peuvent être programmées pour effectuer une large gamme de tâches avec une grande précision, réduisant ainsi le besoin d’intervention humaine et permettant une production à grande échelle avec moins d’erreurs et de déchets. La numérisation a aussi permis une gestion plus fine des processus, permettant d’adapter en temps réel les paramètres de production pour optimiser la qualité et la vitesse de fabrication.
L’un des aspects clés de ces machines est leur capacité à s’adapter à différents types de matériaux et d’épaisseurs de tôles. En fonction de la tâche à accomplir, les machines peuvent être équipées de divers outils et modules interchangeables pour découper, plier, emboutir, ou souder, offrant ainsi une polyvalence qui est essentielle pour répondre aux besoins spécifiques de chaque production. Cette adaptabilité est cruciale dans les environnements industriels où la diversité des pièces à produire peut varier considérablement, exigeant des machines capables de traiter un large éventail de matériaux et de géométries.
Les machines de transformation de tôle ont également évolué pour devenir plus écologiques et économes en énergie. En raison de la pression croissante pour réduire l’impact environnemental des processus de fabrication, de nombreuses machines sont désormais conçues pour minimiser leur consommation énergétique, réduire les émissions et limiter la production de déchets. L’utilisation de technologies plus vertes, comme les systèmes de récupération de chaleur et l’optimisation des processus pour réduire la consommation de matières premières, fait partie de l’engagement de nombreuses entreprises à se conformer aux normes environnementales et à répondre à la demande croissante de production durable.
Les exigences en matière de qualité sont également un moteur important de l’innovation dans ce domaine. Les machines modernes de transformation de tôle intègrent des systèmes de contrôle qualité avancés, comme les capteurs et les caméras de vision, pour détecter en temps réel toute anomalie ou défaut sur les pièces produites. Cela permet d’assurer que les produits finis respectent des tolérances strictes et sont exempts de défauts visibles ou de déformations, garantissant ainsi leur performance et leur durabilité dans des applications finales telles que les composants automobiles ou aéronautiques.
Avec la mondialisation de la production et l’augmentation des volumes de fabrication, la flexibilité et l’optimisation des processus deviennent des priorités majeures. Les machines de transformation de tôle doivent non seulement être capables de produire à grande échelle, mais aussi de s’adapter rapidement à des demandes de production changeantes, de nouvelles conceptions et des exigences strictes en matière de délais. Cela exige des solutions de production qui peuvent être facilement reconfigurées ou modifiées en fonction des besoins du marché, tout en maintenant des niveaux élevés de productivité et de rentabilité.
La mise en réseau de ces machines, souvent dans des systèmes de production automatisée, facilite également la gestion de la chaîne de production. Les machines interconnectées peuvent échanger des informations en temps réel, permettant un suivi continu de la production, une maintenance prédictive, et des ajustements instantanés pour éviter les erreurs et les arrêts de production. Ce type d’intégration fait partie d’une tendance plus large vers la Industrie 4.0, où les machines sont non seulement plus intelligentes, mais aussi capables de fonctionner de manière autonome dans des environnements interconnectés, améliorant ainsi l’efficacité globale des usines.
L’avenir des machines de transformation de tôle semble prometteur, avec des technologies de plus en plus avancées qui permettent une personnalisation poussée, une efficacité accrue et un respect plus strict des normes environnementales. Les progrès dans les domaines de l’intelligence artificielle, du machine learning et de l’Internet des objets (IoT) offriront encore plus d’opportunités pour la surveillance en temps réel, l’automatisation et la personnalisation des processus de fabrication, rendant les machines de transformation de tôle encore plus adaptées aux besoins spécifiques des fabricants du futur.
L’évolution future des machines de transformation de tôle s’oriente également vers une plus grande interconnectivité et intégration des systèmes. Cela signifie que, d’ici quelques années, les machines de transformation de tôle pourront communiquer en temps réel avec d’autres équipements de production, des logiciels de gestion de production, et même des fournisseurs ou des clients. Cette interconnectivité permettra de collecter une quantité massive de données qui pourront être utilisées pour optimiser non seulement la production, mais aussi la chaîne d’approvisionnement et la gestion des stocks. Les usines seront de plus en plus intelligentes, capables de s’ajuster automatiquement aux fluctuations de la demande et aux conditions de production.
Le recours croissant à l’intelligence artificielle (IA) et à l’apprentissage automatique dans ces machines pourrait également transformer la manière dont les défauts sont détectés et corrigés. Par exemple, des systèmes basés sur l’IA pourraient analyser les données en temps réel collectées par les capteurs et les caméras de vision pour identifier les anomalies avant même qu’elles ne deviennent visibles à l’œil nu, et ajuster instantanément les paramètres de production. Cela pourrait conduire à une réduction drastique des défauts de fabrication et des retours de produits, tout en augmentant l’efficacité et la rentabilité de l’ensemble de la chaîne de production.
L’adoption de technologies de fabrication additive (impression 3D) pourrait également avoir un impact significatif sur les machines de transformation de tôle dans les années à venir. L’impression 3D permet de créer des pièces métalliques complexes qui étaient auparavant difficiles à fabriquer par des procédés de fabrication traditionnels. Cette technologie pourrait être combinée avec des procédés de formage de tôle pour permettre des designs encore plus complexes et personnalisés. Par exemple, des structures métalliques légères, des composants de machines ou même des pièces d’outillage de production pourraient être fabriqués à la fois par formage traditionnel et impression 3D, ouvrant la voie à des solutions plus créatives et efficaces.
Un autre domaine d’évolution est le développement de machines plus écologiques. L’optimisation des procédés de fabrication pour minimiser l’impact environnemental va devenir un axe de plus en plus important. Par exemple, les machines de transformation de tôle pourraient intégrer des systèmes de recyclage internes pour récupérer les chutes de métal et les réutiliser immédiatement dans le processus de production. De même, les technologies de réduction de la consommation d’énergie, telles que les moteurs à haut rendement, les systèmes de récupération d’énergie et la réduction des émissions de CO2, deviendront des priorités pour les fabricants qui cherchent à se conformer aux normes environnementales strictes tout en maintenant une production compétitive.
En parallèle, les machines de transformation de tôle deviendront plus modulaires et flexibles. Cette modularité permettra aux entreprises d’adapter rapidement leurs lignes de production à des demandes changeantes sans avoir besoin de remplacer ou d’investir massivement dans de nouvelles machines. Par exemple, un fabricant de pièces automobiles pourrait facilement changer une presse à emboutir pour l’adapter à de nouvelles conceptions de pièces, ou ajuster une machine de découpe pour traiter un nouveau matériau ou une nouvelle épaisseur de tôle. Cette flexibilité réduira les coûts d’investissement et de mise à jour des équipements, tout en augmentant la réactivité de la production.
L’automatisation et l’intelligence collaborative seront également des éléments clés dans le développement des machines de transformation de tôle. L’utilisation de robots collaboratifs (cobots) intégrés aux lignes de production permettra aux machines de travailler de manière plus fluide avec des opérateurs humains. Ces cobots pourraient effectuer des tâches répétitives ou dangereuses, laissant les opérateurs se concentrer sur des fonctions plus créatives et de gestion. Cela permettra de maximiser l’efficacité de la production tout en garantissant la sécurité des travailleurs.
En somme, les machines de transformation de tôle continueront d’évoluer pour devenir des outils plus intelligents, flexibles, et écologiques. Les progrès technologiques permettront non seulement d’améliorer la productivité et la qualité, mais aussi de répondre à des défis industriels plus complexes, comme l’intégration de matériaux composites et la fabrication de pièces de plus en plus complexes et personnalisées. Le futur de la transformation de tôle est donc un avenir où l’automatisation, la connectivité, l’intelligence artificielle et les préoccupations environnementales guideront les innovations, rendant les processus de production plus efficaces, plus durables, et plus adaptés aux exigences du marché mondial.
Machines-outils pour le formage de tôle
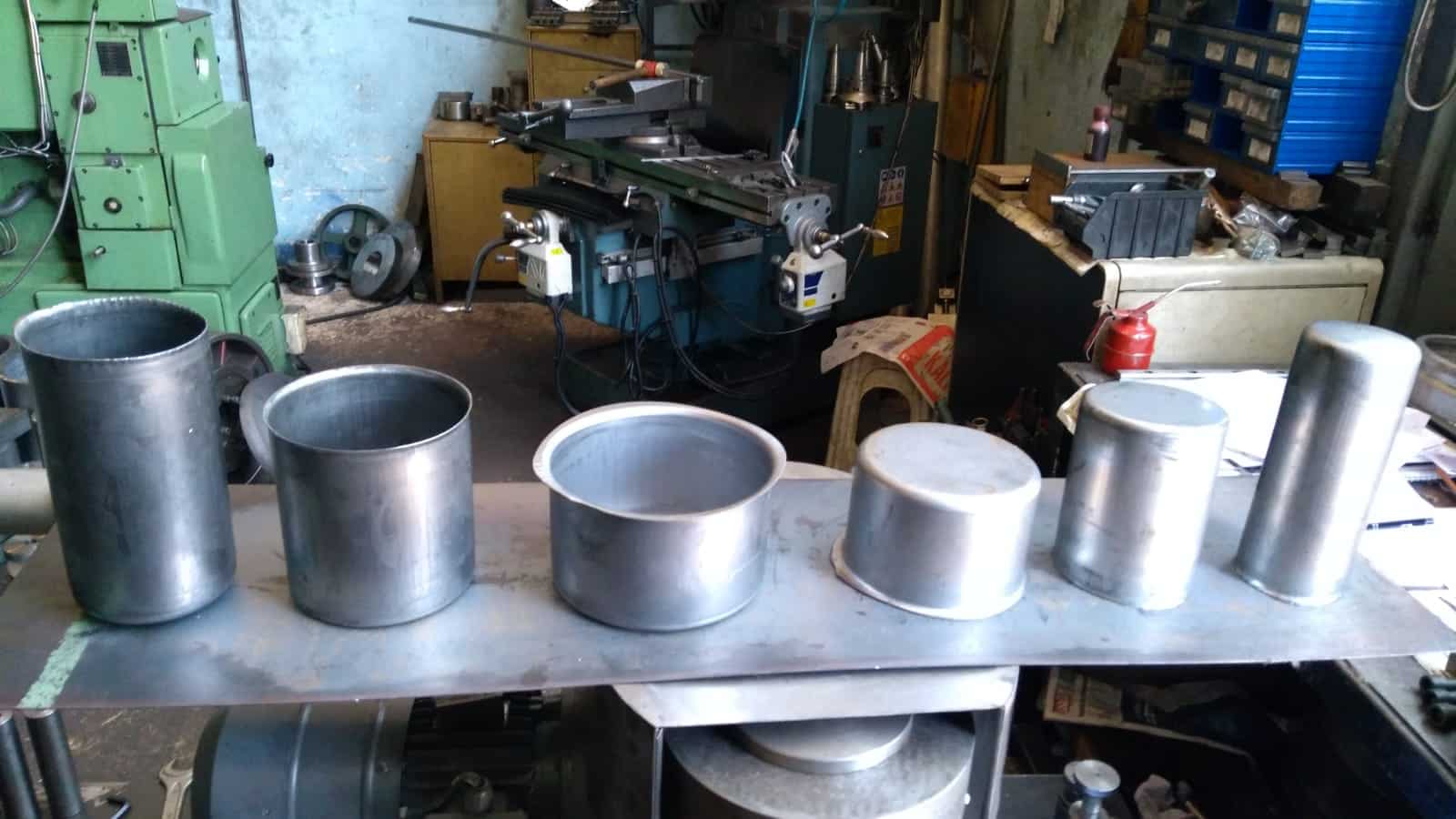
Les machines-outils pour le formage de tôle sont utilisées pour transformer des tôles métalliques en pièces de formes spécifiques, en utilisant des procédés tels que le pliage, l’emboutissage, le roulage ou le découpage. Ces machines sont essentielles pour une large gamme d’industries, telles que l’automobile, l’aéronautique, la construction, et l’électroménager. Ces machines sont équipées de divers systèmes de commande et de contrôle qui permettent de garantir une grande précision et une grande efficacité dans la production de pièces métalliques.
1. Plieuses
Les plieuses sont des machines-outils utilisées pour plier les tôles métalliques à des angles précis. Elles sont couramment utilisées pour fabriquer des pièces comme des boîtiers, des panneaux, des supports ou des cadres. Les plieuses sont souvent équipées de commandes numériques (CNC) pour offrir une flexibilité maximale et permettre des ajustements fins pour des plis de haute précision. Ce type de machine est souvent utilisé dans la fabrication de petites séries de pièces ou dans des environnements nécessitant des variations complexes dans la géométrie de la pièce.
- Plieuses mécaniques : Utilisent un système mécanique pour plier la tôle. Elles sont relativement simples et adaptées aux productions à faible volume.
- Plieuses hydrauliques : Utilisent un système hydraulique pour exercer une pression uniforme sur la tôle, permettant un meilleur contrôle de la force et de la précision. Ce type de plieuse est plus courant pour les productions de plus grande envergure.
- Plieuses CNC : Ces machines sont contrôlées numériquement, permettant des ajustements précis du processus de pliage et la création de géométries complexes. Elles sont idéales pour des productions de haute précision et des séries de pièces complexes.
2. Rouleurs
Les rouleurs sont utilisés pour courber les tôles métalliques et les transformer en formes cylindriques, coniques ou courbes. Ils sont principalement utilisés pour produire des tubes, des réservoirs, des tuyaux, des silos, ou des composants structuraux.
- Rouleurs à 3 rouleaux : Utilisent trois rouleaux pour enrouler la tôle métallique. Ce type de rouleuse est idéal pour la fabrication de formes simples et cylindriques.
- Rouleurs à 4 rouleaux : Ce type de machine est plus précis et permet de courber des tôles plus épaisses avec un contrôle accru de la forme et de l’épaisseur de la courbure. Les rouleaux à quatre canaux permettent un réglage plus précis de la courbure finale.
3. Emboutisseuses
Les emboutisseuses sont utilisées pour effectuer des transformations profondes de la tôle, créant des pièces comme des coques, des cuves, des réservoirs, des boîtiers de machines ou des composants automobiles. Ces machines sont capables de créer des formes complexes en exerçant une pression à l’aide d’un poinçon et d’une matrice.
- Presses à emboutir : Utilisent un poinçon pour pousser la tôle dans une matrice afin de lui donner une forme spécifique. Ce processus peut être effectué avec une presse manuelle ou automatisée, en fonction de la complexité de la pièce.
- Emboutissage profond : Utilisé pour créer des pièces avec des formes plus profondes et complexes, comme des réservoirs ou des pièces automobiles. Cette opération demande des presses particulièrement puissantes et des outils adaptés aux épaisseurs des tôles.
4. Cintreuses
Les cintreuses sont utilisées pour créer des courbures précises dans les tôles métalliques, souvent pour des applications dans la fabrication de structures métalliques ou de composants incurvés. Elles sont utilisées dans la production de supports cintrés, de rails, de tuyaux ou de parties de bâtiments.
- Cintreuses manuelles : Utilisées pour des tâches de cintrage simples, souvent adaptées aux petites productions ou aux ajustements spécifiques.
- Cintreuses automatiques : Ces machines utilisent des commandes CNC pour réaliser des courbures plus complexes avec une grande précision, idéales pour la production de pièces en série.
5. Machines de découpe
La découpe de tôle est une opération courante dans le formage des tôles, et plusieurs types de machines sont utilisés en fonction des spécifications de la production.
- Poinçonneuses : Ces machines utilisent un poinçon pour découper des trous ou des formes spécifiques dans la tôle. Les poinçonneuses modernes sont souvent contrôlées par des systèmes CNC, permettant une grande flexibilité dans la fabrication de pièces complexes.
- Scies à ruban : Utilisées pour couper des tôles métalliques de manière linéaire. Ce type de machine est couramment utilisé pour des découpes simples ou pour la préparation des tôles avant d’autres opérations de formage.
- Découpe laser : Utilise un faisceau laser pour découper des tôles métalliques avec une grande précision. Ce procédé est idéal pour des pièces de formes complexes et est utilisé pour des matériaux fins ou épais. La découpe laser est particulièrement avantageuse pour obtenir une qualité de coupe parfaite sans déformation du matériau.
- Découpe plasma : Utilise un jet de gaz ionisé pour couper des tôles métalliques plus épaisses. Bien que ce procédé soit plus rapide que la découpe laser, il est moins précis et est donc généralement utilisé pour des applications où la vitesse prime sur la précision.
6. Machines de repoussage
Le repoussage est un procédé de formage qui consiste à étirer la tôle dans une matrice à l’aide d’une presse, créant ainsi des pièces de forme ronde ou d’autres formes complexes. Ce procédé est souvent utilisé pour fabriquer des pièces profondes et très précises, comme des réservoirs ou des carters de moteurs.
7. Presses à découper et à emboutir
Les presses à découper et à emboutir sont utilisées pour transformer les tôles métalliques en pièces plates ou semi-finies. Elles fonctionnent en utilisant une matrice et un poinçon qui exercent une pression sur la tôle pour la découper, l’emboutir ou la plier selon le design requis.
- Presses mécaniques : Utilisent un mécanisme mécanique pour exercer une pression sur la tôle, elles sont plus rapides et sont souvent utilisées pour des productions à grande échelle.
- Presses hydrauliques : Utilisent un système hydraulique pour fournir une force de pression plus uniforme et contrôlée, permettant un travail plus précis et plus adapté à des tâches plus complexes.
Les machines-outils pour le formage de tôle sont au cœur de nombreuses chaînes de production industrielles modernes. Elles permettent une flexibilité, une productivité et une précision accrues dans la transformation des tôles métalliques, tout en répondant à des exigences de plus en plus complexes dans des secteurs variés. Grâce à l’intégration de la commande numérique (CNC), de la robotique et des technologies de vision, ces machines continueront d’évoluer pour s’adapter aux besoins croissants de personnalisation, de productivité et de durabilité dans l’industrie.
Les machines-outils pour le formage de tôle ont évolué au fil des ans pour répondre aux demandes croissantes d’efficacité, de précision et de flexibilité dans la production industrielle. Elles permettent non seulement de transformer la tôle en différentes formes, mais aussi de traiter une large gamme de matériaux, allant des métaux ferreux aux alliages non ferreux, et même des métaux très résistants ou légers. L’introduction de la commande numérique (CNC) a permis de programmer des machines avec une grande précision, offrant ainsi des possibilités de production sur mesure et une réduction des erreurs humaines.
Les machines de formage de tôle sont de plus en plus sophistiquées, intégrant des technologies avancées qui permettent une gestion optimisée de l’énergie, une amélioration de la précision de fabrication et une réduction des déchets. Par exemple, les systèmes de récupération de chaleur, les moteurs à haute efficacité énergétique et les technologies de gestion des matériaux ont permis de réduire l’empreinte environnementale de la production de tôles métalliques. Ces machines peuvent également s’intégrer dans des lignes de production automatisées où plusieurs opérations de transformation sont effectuées de manière séquentielle, réduisant ainsi les besoins d’intervention manuelle et augmentant la vitesse de production.
L’innovation en matière de matériaux et de technologie de formage continue également de transformer ce secteur. L’introduction de nouveaux alliages, comme les composites métalliques ou les métaux à haute résistance, a poussé les fabricants à développer des machines capables de traiter ces matériaux avec des tolérances plus strictes et des méthodes de formage plus avancées. Ces matériaux, souvent utilisés dans des secteurs exigeants tels que l’aéronautique ou l’automobile, nécessitent des équipements capables de supporter des contraintes plus importantes et de garantir une qualité irréprochable.
Les machines-outils pour le formage de tôle intègrent également de plus en plus de systèmes de maintenance prédictive, permettant de détecter et de prévenir les pannes avant qu’elles ne surviennent. Ces systèmes utilisent des capteurs pour surveiller en temps réel l’état des machines et collecter des données sur les vibrations, la température, la pression et d’autres paramètres. Cette approche permet non seulement de réduire les arrêts imprévus, mais aussi d’optimiser la durée de vie des machines et de minimiser les coûts de maintenance.
L’automatisation a permis d’introduire des robots collaboratifs (cobots) qui travaillent aux côtés des opérateurs humains pour accomplir des tâches répétitives ou dangereuses, telles que la manipulation de tôles lourdes ou l’alimentation des machines. Cette collaboration entre robots et opérateurs humains augmente la sécurité, tout en permettant une plus grande efficacité dans la production. De plus, l’utilisation des systèmes de vision artificielle dans les machines de formage de tôle aide à contrôler la qualité des pièces en temps réel, détectant les défauts et permettant des ajustements instantanés pour éviter les erreurs avant qu’elles ne se propagent tout au long du processus de production.
Les machines de formage de tôle sont également de plus en plus connectées, dans le cadre de la transition vers l’Industrie 4.0. Les machines interconnectées échangent des informations sur l’état de la production, les besoins de maintenance, et les ajustements nécessaires, permettant ainsi une gestion plus fluide et réactive de la chaîne de production. Cela offre des possibilités de personnalisation à grande échelle, avec des ajustements rapides en fonction des besoins du marché ou des commandes spécifiques. Cette connectivité améliore également la traçabilité des pièces, offrant des informations détaillées sur chaque étape du processus de fabrication, ce qui peut être crucial pour des industries réglementées ou pour garantir la conformité aux normes de qualité.
Avec l’intégration de l’intelligence artificielle (IA) et du machine learning, les machines de formage de tôle pourront apprendre de leurs expériences passées pour optimiser en temps réel les paramètres de production, réduisant ainsi les erreurs et améliorant la qualité des produits finis. Ces technologies pourraient même permettre une gestion proactive des processus, en prédisant les tendances de consommation et en ajustant les opérations en conséquence.
Les défis de demain pour ces machines incluront également l’adaptation aux demandes de production plus petites et plus flexibles, avec des séries de pièces de plus en plus personnalisées et des délais de fabrication de plus en plus courts. Les machines devront être capables de traiter une grande variété de pièces avec une grande réactivité, tout en maintenant des coûts compétitifs. Cela implique également une adaptation aux nouvelles tendances en matière de conception, comme les pièces légères ou à géométrie complexe, qui nécessitent des processus de formage plus sophistiqués.
Enfin, la durabilité sera un facteur clé dans le développement futur des machines de formage de tôle. La réduction de l’impact environnemental à toutes les étapes de la production, du recyclage des matériaux à l’optimisation des consommations d’énergie et des ressources, sera au cœur des préoccupations des fabricants de ces équipements. Les matériaux eux-mêmes devront aussi répondre à des exigences de plus en plus strictes en matière de recyclabilité et de durabilité, tout en restant compétitifs sur le plan des performances.
Ainsi, les machines-outils pour le formage de tôle ne cessent d’évoluer pour répondre aux défis techniques, économiques et environnementaux de l’industrie moderne. Grâce à l’intégration de technologies de pointe, de nouveaux matériaux et de processus de production plus intelligents et plus durables, ces machines continueront de jouer un rôle essentiel dans la transformation des tôles métalliques en pièces de haute qualité et à la pointe de l’innovation industrielle.
L’avenir des machines-outils pour le formage de tôle semble extrêmement prometteur avec les nouvelles tendances technologiques qui façonnent l’industrie. L’une des avancées majeures réside dans l’intégration croissante de la fabrication additive (impression 3D) avec les procédés de formage traditionnels. Bien que l’impression 3D soit généralement associée à la création de prototypes ou à des pièces complexes à géométrie variable, son potentiel dans le formage de tôle pourrait ouvrir de nouvelles possibilités pour la production de pièces uniques ou personnalisées, tout en optimisant les délais et les coûts de fabrication. Par exemple, des structures métalliques légères ou des pièces à géométrie complexe pourraient être fabriquées en combinant des techniques d’emboutissage ou de découpe avec l’impression 3D pour créer des composants de qualité et de plus en plus adaptés aux besoins spécifiques des industries.
Les machines pourraient également s’orienter vers une plus grande intégration avec les technologies d’Internet des objets (IoT). Cela permettrait non seulement de suivre l’état de chaque machine en temps réel, mais aussi de collecter des données détaillées sur les performances de chaque opération de formage, facilitant ainsi la maintenance prédictive et l’amélioration continue des processus. Les usines intelligentes seront ainsi capables d’ajuster instantanément les paramètres de production pour maximiser l’efficacité tout en réduisant les coûts et en améliorant la qualité. Les données collectées peuvent être utilisées pour analyser la performance des matériaux, le comportement des machines et les variations du processus de production, créant ainsi une boucle de rétroaction constante qui alimente les décisions en temps réel.
Les défis de la personnalisation à grande échelle joueront également un rôle clé dans le futur des machines de formage de tôle. Avec l’augmentation de la demande pour des pièces plus petites, personnalisées et à haute précision, ces machines devront être capables de produire rapidement des séries plus petites, tout en maintenant une rentabilité élevée. Les machines devront pouvoir s’adapter facilement à différents types de matériaux et de géométries tout en réduisant les coûts de mise en production. Cela pourrait se traduire par des machines modulaires, facilement reconfigurables, qui peuvent être rapidement adaptées aux exigences spécifiques d’un nouveau projet ou produit.
L’une des avancées les plus prometteuses réside dans l’utilisation des intelligences artificielles et des algorithmes d’optimisation. Ces outils pourraient non seulement prédire et optimiser la qualité des produits finis, mais aussi anticiper les besoins futurs en ajustant les configurations des machines en fonction de l’analyse des données récoltées au fil du temps. Grâce à l’intelligence artificielle, les machines pourraient identifier les tendances de production, prévenir les défaillances et proposer des solutions d’optimisation avant même qu’un problème ne survienne. Cela permettrait d’améliorer la qualité des pièces et de réduire les coûts de production.
Dans un contexte où la durabilité devient une priorité de plus en plus marquée pour les entreprises, les machines de formage de tôle seront conçues pour maximiser le recyclage des matériaux et l’efficacité énergétique. De plus en plus de machines seront dotées de systèmes de gestion énergétique intelligents, capables de réduire les consommations électriques, de récupérer l’énergie excédentaire et de minimiser les déchets produits lors des processus de formage. Ce changement est également lié à une législation de plus en plus stricte en matière d’émissions de CO2 et d’empreinte écologique. L’optimisation des processus pour minimiser l’impact environnemental est donc une tendance qui va se renforcer dans les années à venir.
La digitalisation des processus de fabrication, en particulier dans le domaine du formage de tôle, sera également un facteur clé d’innovation. Grâce à des technologies comme la réalité virtuelle (VR) et la réalité augmentée (AR), les opérateurs pourront non seulement simuler les processus de formage avant la mise en production, mais aussi interagir avec des données et des modèles 3D pour optimiser la fabrication en temps réel. Les formations et la maintenance à distance pourraient aussi être facilitées par ces technologies, permettant aux techniciens de résoudre des problèmes rapidement sans nécessiter de déplacements physiques.
La sécurisation des processus et l’amélioration des conditions de travail des opérateurs seront également des priorités majeures pour les fabricants de machines. Les systèmes de sécurité intégrés aux machines, comme les capteurs de proximité, les dispositifs de détection de risques et les mécanismes de protection automatisés, réduiront les risques d’accidents liés à l’utilisation des machines, garantissant ainsi un environnement de travail plus sûr. De plus, l’intégration de l’intelligence collaborative, permettant aux opérateurs humains et aux robots de travailler ensemble, contribuera également à rendre le processus de production plus ergonomique et plus sécurisé.
Enfin, l’évolution des matériaux sera un facteur déterminant pour le développement des machines de formage de tôle. De nouveaux alliages, de plus en plus légers et résistants, seront utilisés pour répondre aux besoins de l’industrie automobile et aéronautique en matière de légèreté et de résistance à la chaleur. Les machines devront être adaptées pour traiter ces matériaux plus complexes, souvent plus difficiles à travailler avec les méthodes traditionnelles, et offrir des performances accrues dans des conditions de formage plus extrêmes.
Dans l’ensemble, les machines-outils pour le formage de tôle continueront à évoluer pour devenir plus intelligentes, plus durables et plus flexibles. Elles intégreront des technologies avancées, telles que l’intelligence artificielle, les systèmes IoT, la fabrication additive et la digitalisation, pour répondre aux besoins croissants de personnalisation, de réduction des coûts et d’amélioration de la productivité dans des environnements industriels de plus en plus exigeants. Le développement de machines plus efficaces, plus écologiques et plus sûres constituera un pilier central de l’industrie manufacturière du futur.
Appareils de formage de tôle
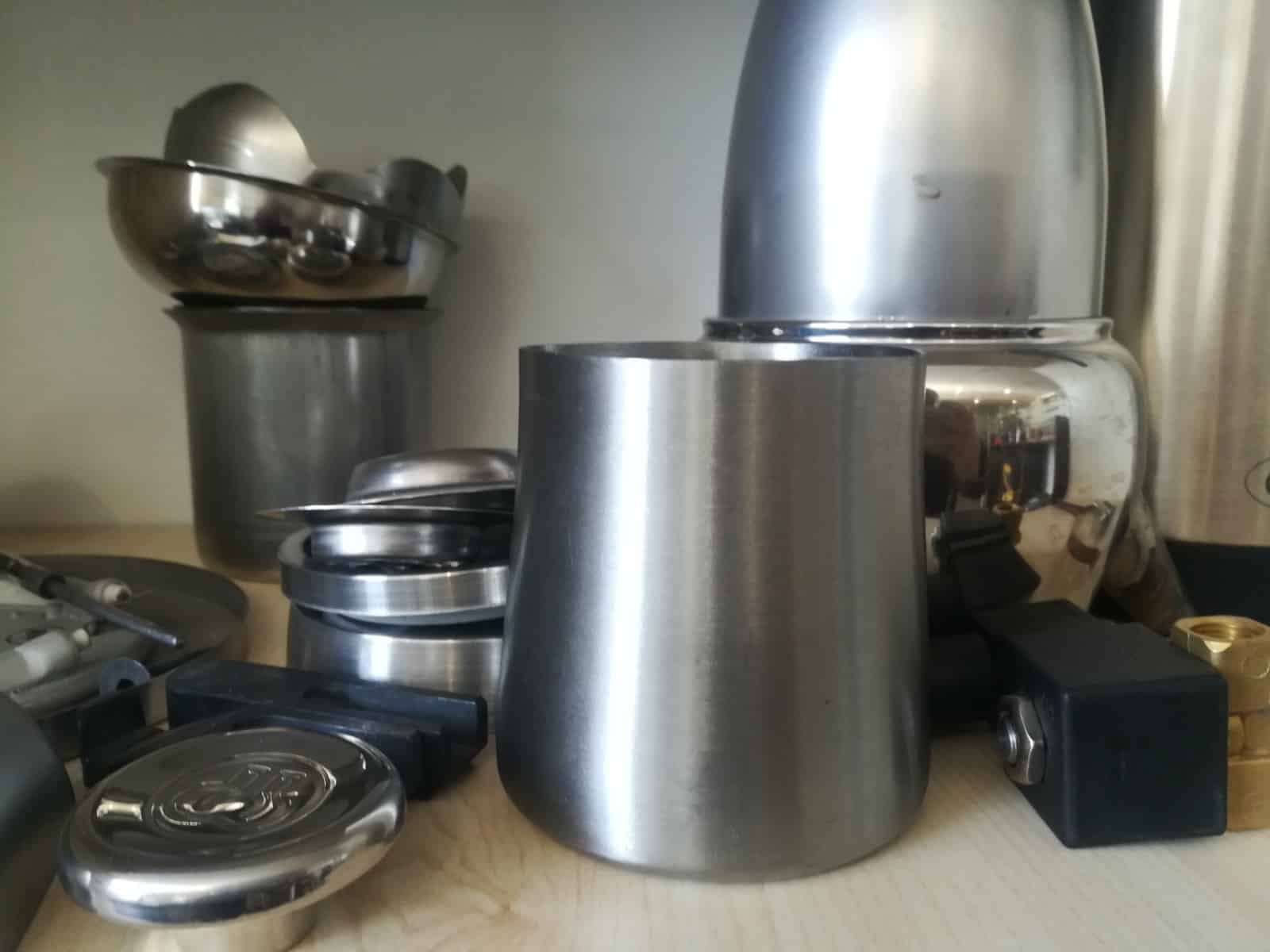
Les appareils de formage de tôle sont des machines utilisées dans l’industrie pour transformer des tôles métalliques en pièces ou composants de formes spécifiques. Ces appareils sont essentiels pour la fabrication de produits finis dans une grande variété de secteurs, tels que l’automobile, l’aéronautique, la construction, et l’électroménager. Leur rôle principal est de modifier les tôles métalliques par des techniques de pliage, d’emboutissage, de découpe, de cintrage, de roulage, et autres opérations de formage pour répondre à des spécifications de design.
Voici un aperçu des différents types d’appareils de formage de tôle utilisés dans l’industrie :
1. Plieuses
Les plieuses sont des machines utilisées pour plier les tôles métalliques à des angles spécifiques, en fonction des besoins de production. Ces appareils utilisent des presses hydrauliques ou mécaniques pour plier les tôles contre une matrice. Les types les plus courants incluent :
- Plieuses mécaniques : Utilisent un système mécanique pour réaliser le pliage. Elles sont adaptées aux applications de faible à moyenne complexité.
- Plieuses hydrauliques : Utilisent des vérins hydrauliques pour appliquer une pression, offrant un meilleur contrôle de la force de pliage et de la précision.
- Plieuses CNC : Contrôlées par un système informatique, permettant de réaliser des plis complexes avec une haute précision et de produire des pièces personnalisées.
2. Rouleurs
Les rouleurs sont utilisés pour courber les tôles métalliques en formes cylindriques, coniques ou autres courbes. Ils sont utilisés pour produire des pièces comme des tuyaux, des réservoirs ou des structures métalliques.
- Rouleurs à 3 rouleaux : Utilisent trois rouleaux pour courber la tôle. Ce type est adapté pour des courbures simples.
- Rouleurs à 4 rouleaux : Permettent une plus grande précision et sont utilisés pour des courbures complexes ou des tôles plus épaisses.
3. Emboutisseuses
Les emboutisseuses sont des appareils utilisés pour transformer les tôles métalliques en pièces profondes, comme des coques ou des réservoirs. Le processus consiste à pousser la tôle dans une matrice pour lui donner une forme spécifique. Les emboutisseuses sont particulièrement utilisées pour la production en série de pièces complexes.
- Presses à emboutir : Ces presses sont adaptées pour réaliser des emboutissages peu profonds.
- Emboutissage profond : Permet de former des pièces plus profondes, souvent utilisées dans l’industrie automobile ou aéronautique.
4. Poinçonneuses
Les poinçonneuses sont utilisées pour perforer des tôles métalliques, créant des trous ou des motifs spécifiques dans les pièces. Elles sont généralement équipées de matrices et de poinçons qui perforent la tôle sous haute pression.
- Poinçonneuses manuelles : Utilisées pour des tâches simples, comme la perforation de petits trous.
- Poinçonneuses CNC : Plus complexes, elles permettent de réaliser des perforations très précises et de découper des formes complexes, contrôlées par un système numérique.
5. Découpeurs Laser
Les découpeurs laser utilisent un faisceau laser intense pour découper des tôles métalliques avec une grande précision. Ils sont utilisés pour la production de pièces aux formes complexes, souvent dans des secteurs où la qualité de coupe est primordiale, comme l’aéronautique ou l’automobile.
- Découpe laser CO2 : Utilise un faisceau laser pour fondre et vaporiser la matière, idéal pour les matériaux fins et moyens.
- Découpe laser fibre : Plus rapide et efficace que le CO2 pour certaines tôles, offrant une coupe plus nette et une consommation d’énergie plus faible.
6. Découpe Plasma
Les découpeurs plasma utilisent un jet de gaz ionisé (plasma) pour couper des tôles métalliques. Ils sont souvent utilisés pour couper des tôles plus épaisses et sont appréciés pour leur rapidité et leur flexibilité dans les environnements industriels.
7. Cintreuses
Les cintreuses sont des appareils utilisés pour courber ou plier des tôles métalliques dans des formes spécifiques. Contrairement aux rouleuses, qui créent des courbes uniformes, les cintreuses sont souvent utilisées pour des applications nécessitant une courbure plus précise.
- Cintreuses manuelles : Utilisées pour des cintrages simples et à faible volume de production.
- Cintreuses hydrauliques et CNC : Offrent une plus grande précision et sont adaptées pour des pièces plus complexes ou pour des séries de production plus importantes.
8. Machines de Découpe à Jet d’Eau
Les découpeurs à jet d’eau utilisent un jet d’eau haute pression mélangé avec un abrasif pour découper des tôles métalliques, principalement utilisées pour des matériaux sensibles à la chaleur ou pour des découpes de grande précision. Ils sont adaptés pour les matériaux épais et offrent une coupe sans chaleur, ce qui évite la déformation thermique.
9. Machines à Repli de Tôle (Formage à froid)
Les machines à repli ou machines de formage à froid sont utilisées pour plier, emboutir, ou étirer des tôles à température ambiante. Elles ne nécessitent pas de chauffage préalable des matériaux, ce qui réduit la consommation d’énergie et permet un travail rapide et efficace, particulièrement dans les secteurs de la construction ou de l’électroménager.
10. Machines à Profilé
Les machines à profilé sont des appareils utilisés pour fabriquer des profilés métalliques en roulant des tôles. Ces machines sont capables de transformer les tôles en différentes formes profilées comme des poutres, des rails ou des tôles ondulées. Elles sont couramment utilisées dans la construction de structures métalliques et d’éléments de toiture.
11. Machines de Formage Rotatif
Les machines de formage rotatif sont utilisées pour produire des pièces métalliques à partir de tôles en utilisant une technique de déformation contrôlée par la rotation. Ce type de machine est souvent utilisé dans la fabrication de pièces à géométrie complexe ou avec des bords incurvés, telles que les cuves, réservoirs ou composants cylindriques.
12. Machines de Repliage et de Roulage (Stretch Forming)
Les machines de repliage et de roulage (ou machines de “stretch forming”) sont utilisées pour former des tôles métalliques en les étirant sur un moule pour obtenir des pièces légères à géométrie complexe, comme des panneaux de carrosserie pour l’automobile ou des éléments décoratifs. Ce procédé permet de créer des formes sans soudures et avec une grande précision dimensionnelle.
Les appareils de formage de tôle jouent un rôle crucial dans la production industrielle moderne. Leur capacité à transformer des tôles métalliques en une large gamme de pièces précises et fonctionnelles permet aux industries de répondre aux exigences de qualité, de performance et de coût des produits finis. Grâce à l’évolution constante des technologies, tels que les systèmes de commande numériques (CNC) et les innovations dans les matériaux, ces appareils deviennent de plus en plus efficaces, flexibles et écologiques, ouvrant la voie à une production industrielle plus intelligente et durable.
Les appareils de formage de tôle continuent de jouer un rôle essentiel dans l’industrie, avec des innovations constantes visant à améliorer la précision, l’efficacité et la flexibilité des processus de fabrication. L’évolution technologique a conduit à la création de machines plus sophistiquées, capables de travailler avec des matériaux de plus en plus complexes, tout en répondant aux exigences strictes en termes de qualité et de coûts.
L’essor de l’automatisation et de la robotisation a également eu un impact considérable sur le formage de tôle. Les robots industriels, souvent équipés de systèmes de vision et d’intelligence artificielle, peuvent maintenant effectuer des tâches telles que le chargement et le déchargement des tôles, le contrôle de qualité en temps réel ou même l’ajustement des paramètres de machines pour optimiser la production. Cette automatisation permet non seulement d’augmenter la productivité, mais aussi de réduire les risques d’erreurs humaines et d’améliorer la sécurité sur les lignes de production.
Les avancées dans les systèmes de commande numérique (CNC) ont transformé le formage de tôle en rendant les machines plus flexibles et plus faciles à programmer. Avec la possibilité de changer rapidement les paramètres de production, ces machines peuvent répondre à des demandes de production personnalisées, réduire les temps de préparation et offrir une grande précision dans le traitement des tôles. Cela permet d’adapter les processus de fabrication à des séries plus petites et plus diversifiées, une tendance particulièrement importante dans des secteurs comme l’automobile ou la fabrication de produits électroniques où la personnalisation à grande échelle devient de plus en plus courante.
En parallèle, l’intégration de la simulation 3D dans le processus de conception et de formage de tôle permet aux fabricants de simuler les processus de production avant même de lancer une série de fabrication. Cela réduit les risques de défauts, optimise la consommation des matériaux et assure un meilleur contrôle des coûts. Les ingénieurs peuvent ainsi prédire le comportement des matériaux et ajuster les paramètres des machines pour garantir que les pièces finies respectent les spécifications requises.
La durabilité devient également une priorité pour les fabricants d’appareils de formage de tôle. L’introduction de solutions plus écologiques, telles que les technologies de réduction de consommation d’énergie, de recyclage des matériaux ou de réduction des émissions de CO2, est devenue essentielle dans le développement de nouvelles machines. En réduisant la consommation énergétique et les déchets de matériaux, ces machines contribuent à rendre la production industrielle plus respectueuse de l’environnement.
L’intégration des technologies Internet des objets (IoT) dans les machines de formage de tôle permet également d’optimiser la gestion de la production. Ces machines, connectées entre elles, peuvent échanger des données en temps réel concernant l’état de la production, la consommation des matériaux, et la performance des machines. Cela permet une gestion proactive des processus de fabrication, facilitant la maintenance prédictive et améliorant la réactivité face aux éventuels problèmes de production.
Enfin, avec l’essor de l’industrie 4.0, les appareils de formage de tôle sont de plus en plus conçus pour être intégrés dans des chaînes de production entièrement automatisées, où la gestion des machines, des matériaux et des produits est centralisée et optimisée. Ces machines de formage de tôle deviennent ainsi des éléments clés de l’usine intelligente du futur, où l’interconnexion, l’analyse de données et l’automatisation se combinent pour créer une production plus flexible, plus rapide et plus rentable.
Les appareils de formage de tôle sont ainsi en constante évolution, intégrant de nouvelles technologies et s’adaptant aux besoins d’une industrie de plus en plus exigeante. Leur rôle dans la transformation des tôles métalliques continue de croître, avec des machines de plus en plus performantes, plus écologiques et plus adaptées aux défis industriels du XXIe siècle.
L’avenir des appareils de formage de tôle se dirige vers une intégration accrue des technologies intelligentes, où les systèmes de contrôle et de supervision basés sur des algorithmes d’intelligence artificielle (IA) joueront un rôle de plus en plus important. Ces algorithmes permettront de prédire, d’analyser et d’optimiser les performances des machines en temps réel, rendant le processus de production plus autonome et efficace. Par exemple, des systèmes d’IA pourront ajuster automatiquement les paramètres des machines en fonction des variations de matériaux ou des erreurs détectées pendant le processus de formage, améliorant ainsi la précision et réduisant les coûts de production.
Les appareils de formage de tôle de demain seront également de plus en plus connectés à des systèmes de gestion de production avancés (ERP) et à des plateformes de gestion des données pour permettre une surveillance complète du cycle de vie de la production. Les données générées par ces machines seront utilisées pour anticiper les pannes, optimiser les horaires de maintenance et même ajuster la chaîne de production en fonction des besoins en temps réel. Cette évolution facilitera une gestion plus agile et réactive des usines, offrant ainsi une meilleure adaptabilité aux fluctuations de la demande et aux changements du marché.
L’automatisation collaborative deviendra un autre facteur clé de l’avenir des machines de formage de tôle. L’usage de robots collaboratifs, ou cobots, travaillant en harmonie avec les opérateurs humains, est appelé à se développer. Ces cobots pourront effectuer des tâches répétitives ou dangereuses tout en permettant aux travailleurs de se concentrer sur des missions à plus forte valeur ajoutée, comme le contrôle qualité ou la gestion des ajustements complexes des machines. L’interaction homme-machine sera optimisée pour garantir une productivité accrue tout en assurant la sécurité des opérateurs.
En termes de matériaux, la tendance s’oriente vers l’utilisation de nouvelles alliages et composites qui nécessitent des techniques de formage de tôle adaptées. Par exemple, des matériaux à base de fibres composites ou des alliages légers sont de plus en plus utilisés dans les industries automobile et aérospatiale pour réduire le poids des véhicules ou des avions, tout en maintenant une résistance élevée. Ces matériaux, souvent plus difficiles à former que les métaux traditionnels, nécessiteront des machines de formage plus sophistiquées, capables de traiter des matériaux plus fragiles ou plus résistants.
L’une des principales tendances dans l’industrie du formage de tôle est la recherche de solutions de fabrication durables. Les normes environnementales et les régulations de plus en plus strictes sur les émissions de CO2 et les déchets imposent aux fabricants de repenser leurs procédés pour réduire leur empreinte écologique. Les machines modernes sont ainsi conçues pour être plus écoénergétiques, avec des moteurs et des systèmes plus efficaces qui réduisent la consommation d’énergie. De plus, la réduction des déchets de matière est un enjeu central, avec l’introduction de procédés de recyclage intégrés dans les machines elles-mêmes, permettant de récupérer les chutes de métal pour les réutiliser dans la production.
Un autre aspect de cette évolution concerne les matériaux intelligents. Ceux-ci pourraient être utilisés pour fabriquer des tôles dont les propriétés changent en fonction des conditions de leur environnement ou de leur utilisation. Par exemple, des tôles qui changent de forme ou de résistance sous certaines températures ou pressions pourraient offrir de nouvelles possibilités de conception pour des applications spécifiques dans l’aéronautique ou l’automobile. Ces matériaux intelligents nécessiteront des machines capables de traiter des tôle dont les caractéristiques changent au cours du processus de formage, ajoutant une couche de complexité à la fabrication.
Les machines de formage de tôle automatisées deviendront également plus adaptables, avec des systèmes modulaire et flexibles. Ces machines seront capables de passer facilement d’une production à l’autre, ajustant les configurations pour produire des pièces différentes sans nécessiter de longues périodes de reconfiguration. La flexibilité des lignes de production permettra une meilleure gestion des petites séries et de la production à la demande, répondant ainsi aux besoins du marché de plus en plus orienté vers la personnalisation et la production flexible.
Enfin, la cyber-sécurité sera un aspect crucial du développement des machines de formage de tôle. À mesure que ces machines deviennent de plus en plus connectées et interconnectées, la protection des données et des processus industriels contre les cyberattaques deviendra un enjeu majeur. Les fabricants devront intégrer des systèmes de sécurité avancés pour protéger les informations sensibles, les plans de production et les données liées aux performances des machines.
Dans l’ensemble, l’avenir des appareils de formage de tôle sera marqué par une convergence technologique. Les machines deviendront non seulement plus intelligentes et plus flexibles, mais aussi plus écologiques et plus collaboratives, répondant à la fois aux exigences de production modernes et aux préoccupations environnementales. Elles joueront un rôle central dans l’évolution de l’industrie 4.0, contribuant à la création d’usines plus intelligentes, plus efficaces et plus résilientes face aux défis futurs.
Systèmes de formage de tôle

Les systèmes de formage de tôle regroupent l’ensemble des technologies, machines et équipements utilisés pour transformer des tôles métalliques en produits finis ou semi-finis, tout en contrôlant les paramètres de production pour garantir la qualité et la précision des pièces obtenues. Ces systèmes permettent de réaliser une variété de formes, d’angles et de structures à partir de tôles plates, en utilisant des techniques de déformation, de coupe, de pliage et de formage sous pression. Ils sont largement utilisés dans de nombreuses industries, comme l’automobile, l’aéronautique, la construction, et la fabrication de biens de consommation.
Voici un aperçu des principaux systèmes de formage de tôle :
1. Système de Formage par Pliage
Le pliage est l’une des techniques les plus courantes de formage de tôle. Elle consiste à appliquer une force pour courber la tôle métallique autour d’un outil spécifique, comme une matrice et une lame. Ce procédé peut être réalisé à l’aide de plieuses hydrauliques ou mécaniques. Les systèmes de pliage modernes utilisent souvent des plieuses à commande numérique (CNC) qui permettent une flexibilité accrue, une meilleure précision et une adaptation facile à différents types de tôles et d’angles de pliage.
Les plieuses à commande numérique (CNC) intègrent des systèmes automatisés de contrôle des axes, des outils et des paramètres de déformation. Cela permet de produire des pièces de manière plus rapide et avec une plus grande précision. Les plieuses CNC sont adaptées à la production de pièces complexes, en particulier lorsque des séries de production varient ou qu’un travail de haute précision est requis.
2. Système de Formage par Emboutissage
L’emboutissage est un procédé de formage à froid qui permet de transformer une tôle métallique plate en une pièce en trois dimensions. Il s’agit d’une déformation de la tôle, généralement sous l’effet d’une pression exercée par une presse et une matrice. Les systèmes d’emboutissage sont principalement utilisés pour la production de pièces profondes, comme les carrosseries de véhicules, les réservoirs, et autres composants complexes.
Les presses à emboutir peuvent être hydrauliques, mécaniques, ou pneumatiques, chacune étant adaptée à différents types de production. Les presses à emboutir CNC permettent également une meilleure répétabilité et une grande précision, en automatisant et en ajustant les forces appliquées selon les spécifications.
3. Système de Formage par Découpe
Les systèmes de découpe sont utilisés pour couper des tôles métalliques en différentes formes. La découpe peut être réalisée à l’aide de plusieurs technologies, notamment :
- Découpe au laser : Un faisceau laser intense est utilisé pour fondre et vaporiser la tôle, offrant une grande précision et permettant de découper des formes complexes. Ce type de découpe est souvent utilisé dans des applications nécessitant une finition nette, comme dans l’aéronautique ou l’industrie automobile.
- Découpe plasma : Un jet de plasma chaud est utilisé pour découper la tôle, en particulier pour les matériaux plus épais. La découpe plasma est rapide et relativement économique pour des matériaux plus grossiers.
- Découpe à jet d’eau : Ce procédé utilise un jet d’eau haute pression, souvent mélangé à un abrasif, pour découper les tôles sans générer de chaleur. Il est idéal pour des matériaux sensibles à la chaleur ou lorsqu’une coupe précise est nécessaire.
Ces systèmes permettent d’obtenir une grande variété de découpes, de motifs et de dimensions pour répondre aux besoins de la production industrielle.
4. Système de Formage par Rouleau
Le formage par rouleau est utilisé pour donner aux tôles des formes courbes, telles que des cylindres, des cônes ou des courbes complexes. Il existe plusieurs types de machines pour cette opération :
- Rouleuses à trois rouleaux : Ce type de système utilise trois rouleaux pour déformer la tôle en une forme courbe. Il est adapté pour des courbures simples.
- Rouleuses à quatre rouleaux : Permettent une plus grande précision et sont utilisées pour des formes plus complexes, comme des arcs plus précis ou des courbures plus serrées.
Le formage par rouleau est couramment utilisé dans la production de tubes, réservoirs, ou éléments de toiture en métal.
5. Système de Formage par Roulage et Profilage
Le profilage est une technique de formage utilisée pour produire des profils métalliques, comme des poutres, des rails ou des éléments de toiture en tôle. Les machines de profilage, également appelées machines à rouleaux de profilé, déforment une tôle en la faisant passer successivement sous plusieurs rouleaux qui lui donnent sa forme finale.
Les systèmes de profilage sont souvent utilisés dans la construction pour fabriquer des éléments comme des tôles ondulées, des profilés de charpente, ou des bardeaux métalliques. Ces systèmes sont souvent modulaires, permettant de produire une large gamme de formes en fonction des besoins de la production.
6. Système de Formage à Froid
Le formage à froid est un procédé où la tôle métallique est déformée à température ambiante, sans être chauffée préalablement. Ce procédé est utilisé pour des applications de production à grande échelle et est couramment employé pour des pièces qui ne nécessitent pas de températures élevées pour être formées, comme dans l’électroménager, la construction, et la fabrication de composants automobiles.
Les machines de formage à froid incluent des presse-plieuses, des emboutisseuses, des rouleuses et des profilées, qui utilisent des forces mécaniques ou hydrauliques pour façonner la tôle selon les spécifications.
7. Système de Formage Magnétique
Les systèmes de formage magnétique utilisent des champs magnétiques pour déformer des tôles métalliques. Bien que moins courants, ces systèmes offrent des avantages uniques dans certaines applications, notamment pour des formes complexes et pour éviter les déformations thermiques ou les risques d’endommagement mécanique. Ce type de système est utilisé dans des applications de niche, comme la production de composants dans des environnements sensibles.
8. Système de Formage en Continu
Les systèmes de formage en continu sont utilisés pour la production de grandes quantités de pièces, comme des profilés métalliques, des tôles ondulées ou des tubes. Ce procédé permet de former des tôles sur une ligne de production automatisée, en utilisant des rouleaux, des presses et des systèmes de coupe pour réaliser une série de déformations sans interruption. Ces systèmes sont souvent utilisés dans les industries de la construction et de l’automobile, où de grandes quantités de pièces homogènes doivent être produites à un coût réduit.
9. Systèmes de Formage à Haute Pression
Les systèmes de formage à haute pression, comme le moulage à haute pression, utilisent une force extrêmement élevée pour déformer la tôle métallique. Ce procédé est particulièrement adapté pour les matériaux durs ou très épais, où d’autres méthodes de formage, comme le pliage ou l’emboutissage, ne sont pas efficaces. Les machines utilisées pour ces procédés sont souvent équipées de presses hydrauliques capables d’appliquer une force immense de manière contrôlée.
10. Systèmes de Contrôle et de Surveillance
Les systèmes de contrôle et de surveillance sont essentiels pour garantir la qualité et la précision du processus de formage de tôle. Ces systèmes comprennent des capteurs, des caméras de vision, et des logiciels de contrôle qui surveillent en temps réel la déformation des tôles, les dimensions des pièces finies, et l’usure des outils. L’intégration de la commande numérique (CNC) dans les systèmes de formage permet d’automatiser et de contrôler de manière précise les différents paramètres du processus.
En résumé, les systèmes de formage de tôle incluent une gamme variée de technologies et de machines adaptées aux différents types de déformation et aux spécifications des pièces à produire. Ces systèmes sont au cœur de la fabrication industrielle moderne, contribuant à la production de pièces métalliques complexes et de haute précision dans de nombreux secteurs. L’évolution constante des technologies permet de répondre aux exigences croissantes en matière de productivité, de flexibilité, de qualité et de durabilité.
Les systèmes de formage de tôle sont essentiels pour transformer des tôles métalliques plates en produits finis ou semi-finis, utilisés dans des secteurs variés tels que l’automobile, l’aéronautique, la construction, et l’industrie électroménager. Ces systèmes incluent des machines et des procédés qui permettent de façonner, découper, plier et transformer les tôles métalliques en produits aux formes et aux dimensions spécifiques.
Le formage de tôle repose sur différentes techniques telles que le pliage, l’emboutissage, la découpe, le roulage, le profilage, et bien d’autres. Chaque technique répond à des besoins de production spécifiques et est adaptée à différents types de matériaux et de formes. Par exemple, le pliage consiste à appliquer une force pour courber une tôle métallique à un angle précis, et est utilisé pour des pièces telles que des panneaux ou des supports. Ce processus est souvent effectué à l’aide de plieuses hydrauliques ou mécaniques, parfois avec commande numérique pour une plus grande précision et flexibilité.
L’emboutissage est un autre procédé populaire, où une presse exerce une force sur la tôle pour lui donner une forme tridimensionnelle, comme des carters, des coques ou des composants automobiles. Ce procédé est généralement effectué à froid, mais peut aussi être combiné avec un chauffage pour certains matériaux. L’emboutissage est une méthode idéale pour les pièces de formes complexes nécessitant de grandes séries de production.
La découpe, qu’elle soit au laser, plasma ou jet d’eau, permet de réaliser des formes précises et complexes dans les tôles métalliques. Chaque technologie de découpe a ses avantages, comme la découpe au laser qui offre une précision exceptionnelle pour des pièces complexes, tandis que la découpe plasma est plus rapide et plus économique pour les matériaux plus épais. La découpe à jet d’eau est idéale pour des matériaux sensibles à la chaleur, car elle ne génère pas de chaleur pendant le processus.
Le formage par rouleau et le profilage sont utilisés pour créer des formes courbes ou profilées dans des tôles. Les rouleuses à trois ou quatre rouleaux sont couramment utilisées pour créer des cylindres, des cônes ou d’autres formes arrondies. Les machines de profilage, quant à elles, permettent de produire des éléments de construction tels que des tôles ondulées ou des profilés de charpente, grâce à une série de rouleaux qui déforment la tôle selon le profil souhaité.
Le formage à froid, quant à lui, est largement utilisé pour des applications qui ne nécessitent pas de chaleur pour la déformation du métal, ce qui permet de maintenir les propriétés mécaniques du matériau intactes. Ce processus est particulièrement adapté pour la production à grande échelle de composants simples comme des pièces automobiles ou des équipements de construction.
Les systèmes de formage en continu et les presses à haute pression sont des solutions efficaces pour la production de grandes quantités de pièces. Dans le formage en continu, la tôle est déformée de manière continue sur une ligne de production, souvent pour des produits comme les profilés métalliques. Les presses à haute pression, qui exercent une force extrême sur la tôle, sont utilisées pour les matériaux plus épais ou résistants qui nécessitent une déformation plus importante.
Les systèmes modernes de formage intègrent des technologies de commande numérique (CNC) et des systèmes de contrôle automatisés qui permettent de contrôler avec précision les paramètres du processus de fabrication, garantissant ainsi la qualité et la constance des pièces produites. Les machines CNC sont capables d’ajuster automatiquement les paramètres de production en fonction des variations de matériaux ou des exigences spécifiques des pièces.
L’intégration de technologies telles que la robotique, l’intelligence artificielle et l’Internet des objets (IoT) dans les systèmes de formage de tôle permet d’optimiser la gestion des processus de production. Ces technologies permettent une surveillance en temps réel, une gestion proactive des pannes, une maintenance prédictive et un contrôle de la qualité tout au long de la chaîne de production.
De plus, la durabilité devient une priorité dans le développement des machines de formage de tôle. Les efforts visant à réduire l’empreinte écologique de la production passent par l’adoption de technologies plus écoénergétiques, la réduction des déchets de matériaux et l’optimisation des processus pour minimiser la consommation d’énergie.
En somme, les systèmes de formage de tôle sont de plus en plus sophistiqués, intégrant des solutions intelligentes, écologiques et hautement automatisées pour répondre aux exigences de l’industrie moderne. Ils jouent un rôle fondamental dans la fabrication de produits métalliques diversifiés et de haute précision, tout en contribuant à l’évolution vers des usines plus intelligentes et durables.
Les systèmes de formage de tôle continuent d’évoluer pour répondre aux besoins croissants de flexibilité, de personnalisation et de réduction des coûts dans les processus de fabrication. À mesure que la demande pour des produits plus légers, plus résistants et plus complexes augmente, les machines et les technologies de formage de tôle doivent s’adapter pour traiter une variété de matériaux et de configurations.
L’introduction de matériaux innovants comme les alliages à haute résistance, les composites et les matériaux légers, comme l’aluminium et le titane, crée de nouveaux défis pour les systèmes de formage de tôle. Ces matériaux, bien que plus légers, sont souvent plus difficiles à façonner en raison de leur résistance accrue ou de leurs propriétés particulières. Par exemple, l’aluminium, tout en étant léger, a des propriétés de ductilité et de résistance qui diffèrent de celles de l’acier, nécessitant des ajustements spécifiques dans les processus de formage. Les presses à emboutir, les rouleuses et les machines de découpe doivent donc être adaptées pour traiter ces matériaux plus complexes tout en garantissant une qualité constante.
Le formage de tôle à haute température est également en développement pour certains matériaux, comme les superalliages utilisés dans l’aéronautique. Ces matériaux sont souvent formés à des températures élevées pour garantir leur malléabilité et leur résistance aux conditions extrêmes. Le contrôle thermique devient un élément clé pour éviter la déformation ou la rupture du matériau lors du processus. Des systèmes de chauffage intégrés aux machines de formage peuvent être utilisés pour atteindre et maintenir la température idéale, tandis que des technologies de refroidissement permettent d’assurer un contrôle de la qualité des pièces formées.
La technologie additive a aussi un impact significatif sur l’industrie du formage de tôle. Bien qu’elle soit plus couramment utilisée dans la fabrication de prototypes et la production de petites séries, l’impression 3D métallique est de plus en plus appliquée dans la création de pièces complexes qui ne peuvent pas être obtenues par les méthodes de formage classiques. Les systèmes de formage de tôle sont désormais capables de travailler en synergie avec des imprimantes 3D pour fabriquer des composants métalliques à partir de tôles, en les combinant avec des techniques de soudage ou d’assemblage pour offrir des solutions plus flexibles et plus personnalisées.
En matière de production flexible, les avancées récentes dans les technologies de robotique et d’automatisation permettent aux systèmes de formage de tôle de s’adapter rapidement à des changements de design ou de spécifications sans nécessiter de reconfiguration lourde des machines. Cela est particulièrement important dans des industries où les demandes peuvent varier considérablement, comme dans l’automobile ou la production de matériel électronique, où les conceptions de produits évoluent fréquemment et où les petites séries doivent être produites efficacement.
Un autre domaine clé de l’innovation réside dans la maintenance prédictive. Avec l’augmentation de la numérisation des processus industriels, les systèmes de formage de tôle sont équipés de capteurs intelligents capables de surveiller l’état des machines en temps réel. Ces capteurs collectent des données sur des paramètres comme la pression, la température, l’usure des outils et d’autres aspects cruciaux pour la performance des machines. Grâce à l’analyse des données et à l’intelligence artificielle, il devient possible de prévoir l’usure des composants ou d’identifier des anomalies avant qu’elles ne conduisent à une panne, réduisant ainsi les temps d’arrêt et optimisant l’efficacité de la production.
Les usines intelligentes, souvent décrites sous l’appellation d’Industrie 4.0, sont un autre domaine d’évolution des systèmes de formage de tôle. L’intégration de l’Internet des objets (IoT), des big data et des systèmes cyber-physiques dans les lignes de production permet une gestion de la production en temps réel. Chaque machine peut communiquer ses données avec un système centralisé, permettant une planification dynamique, une gestion plus fluide des stocks et une optimisation des processus de production. Ces usines connectées permettent également une amélioration continue, en analysant les données de production pour identifier des pistes d’amélioration en termes de qualité, de rendement et de coûts.
Du côté de la durabilité et de la réduction de l’empreinte carbone, les innovations ne cessent de croître. Les matériaux métalliques, comme l’acier et l’aluminium, peuvent être recyclés efficacement, et les machines modernes de formage de tôle sont conçues pour minimiser les déchets et maximiser l’utilisation des ressources. Par exemple, des systèmes de récupération des déchets sont installés pour collecter les chutes de métal et les réintroduire dans le cycle de production. Les machines sont également de plus en plus écoénergétiques, utilisant des moteurs à haut rendement et des technologies de réduction de la consommation d’énergie.
En matière de sécurité, les systèmes de formage de tôle de demain intégreront davantage de fonctionnalités pour protéger les opérateurs. Les robots collaboratifs (cobots) travailleront aux côtés des humains, en effectuant des tâches dangereuses ou répétitives tout en garantissant un environnement de travail plus sûr. Les technologies de vision et de détection, associées à des algorithmes d’intelligence artificielle, permettront d’identifier les risques en temps réel et d’arrêter automatiquement les machines en cas de danger imminent.
L’avenir des systèmes de formage de tôle est donc marqué par une transformation profonde, alimentée par des technologies avancées qui permettront une production plus rapide, plus précise et plus durable. En combinant l’automatisation, la robotisation, l’intelligence artificielle et la numérisation, ces systèmes seront plus flexibles, réactifs et capables de s’adapter à des besoins de production variés et de plus en plus complexes. Ces avancées contribueront non seulement à améliorer l’efficacité et la rentabilité des processus industriels, mais aussi à répondre aux défis environnementaux et sociaux actuels.
Machines de mise en forme de tôle

Les machines de mise en forme de tôle sont des équipements essentiels dans les processus industriels de transformation de tôles métalliques. Elles permettent de réaliser une variété de déformations mécaniques pour produire des pièces aux formes et aux dimensions spécifiques. Ces machines sont utilisées dans de nombreuses industries, telles que l’automobile, la construction, l’aéronautique, l’électroménager, et bien d’autres secteurs qui nécessitent des composants métalliques.
Les principales machines utilisées pour la mise en forme de tôle sont :
1. Plieuses
Les plieuses sont utilisées pour plier les tôles métalliques selon un angle précis. Ce processus est souvent effectué à l’aide d’une plieuse hydraulique ou mécanique, selon les exigences du projet. Une plieuse hydraulique est équipée de deux poutres qui exercent une pression sur la tôle pour la déformer sans rompre le métal. Les plieuses modernes sont souvent CNC (commande numérique), permettant de programmer des angles de pliage précis et des ajustements rapides en fonction des exigences de production. Elles sont couramment utilisées pour créer des angles ou des formes géométriques spécifiques dans des tôles plates.
2. Presse à Emboutir
Les presses à emboutir sont des machines utilisées pour créer des pièces profondes ou des formes tridimensionnelles complexes à partir de tôles métalliques. Elles utilisent une matrice et un poinçon pour exercer une pression sur la tôle, la déformant ainsi pour obtenir la forme souhaitée. Ce procédé est couramment utilisé pour des pièces automobiles, des réservoirs, des coques et d’autres composants métalliques. Les presses à emboutir peuvent être hydrauliques ou mécaniques, selon les besoins de force et de précision. Les presses modernes sont souvent équipées de commandes numériques (CNC) pour garantir une précision maximale.
3. Rouleuses à Tôle
Les rouleuses à tôle, ou machines de roulage, sont utilisées pour former des courbes ou des cylindres à partir de tôles métalliques. Ces machines fonctionnent en faisant passer la tôle entre des rouleaux qui la déforment progressivement en la courbant. Les rouleuses à trois rouleaux sont les plus courantes et conviennent pour des courbures simples, tandis que les rouleuses à quatre rouleaux offrent une plus grande précision pour des courbes plus complexes. Elles sont utilisées pour fabriquer des tubes, des cônes, des arcs et des structures cylindriques ou coniques dans des matériaux comme l’acier, l’aluminium et d’autres métaux.
4. Machines à Découpe
Les machines à découper jouent un rôle essentiel dans la mise en forme de la tôle. Il existe différentes méthodes de découpe, chacune adaptée à des applications spécifiques :
- Découpe laser : Utilise un faisceau laser à haute intensité pour découper des tôles métalliques avec une grande précision. Ce type de découpe est idéal pour les formes complexes et les tolérances serrées.
- Découpe plasma : Utilise un jet de plasma pour découper des tôles métalliques, particulièrement pour des matériaux plus épais. Bien que moins précis que la découpe laser, ce procédé est plus rapide et plus économique pour des matériaux plus épais.
- Découpe à jet d’eau : Cette méthode utilise un jet d’eau haute pression, souvent mélangé à un abrasif, pour couper des tôles. Elle est idéale pour les matériaux sensibles à la chaleur et pour des découpes de haute précision.
- Cisaillage : Procédé de découpe où une lame tranche directement la tôle, souvent utilisé pour des découpes droites et des formes simples.
5. Machines de Profilage
Les machines de profilage sont utilisées pour déformer les tôles en une forme particulière, comme des profilés métalliques. Elles sont souvent utilisées dans la construction pour fabriquer des tôles ondulées, des profilés de charpente ou des éléments de couverture. Les lignes de profilage utilisent des rouleaux pour guider et déformer la tôle tout au long du processus, permettant une production continue et rapide de profils métalliques avec une grande précision. Ce type de machine est souvent utilisé pour produire des pièces en grandes quantités, comme des éléments de toiture ou des rails.
6. Machines de Formage à Froid
Les machines de formage à froid sont utilisées pour transformer la tôle métallique sans recourir à la chaleur. Ce procédé de déformation est effectué à température ambiante et est particulièrement utilisé pour les métaux ductiles tels que l’acier, l’aluminium et le cuivre. Les machines de formage à froid incluent des plieuses, des presses à emboutir, et des machines de découpe, qui peuvent être utilisées dans diverses configurations pour créer des pièces de forme complexe sans altérer les propriétés mécaniques du matériau.
7. Machines à Fileter et à Tarauder
Les machines à fileter et à tarauder sont utilisées pour créer des filets ou des trous filetés dans des tôles métalliques, généralement pour des applications nécessitant des assemblages mécaniques. Ces machines sont essentielles dans la fabrication de pièces destinées à être vissées ou assemblées, comme dans l’industrie automobile ou dans la construction de machines.
8. Machines de Formage Magnétique
Les machines de formage magnétique utilisent des champs magnétiques pour déformer la tôle métallique. Ce type de procédé est moins courant, mais il peut être utilisé dans des applications spécialisées où une déformation uniforme est nécessaire sans contact direct avec la surface de la tôle. Il est particulièrement utile pour des matériaux sensibles ou dans des environnements où un formage rapide et sans contact est requis.
9. Machines de Formage à Haute Pression
Les machines de formage à haute pression sont utilisées pour déformer des tôles métalliques en appliquant une pression extrêmement élevée. Ces machines sont adaptées pour travailler avec des matériaux plus épais ou résistants, qui nécessitent une force plus importante pour être formés correctement. Le formage à haute pression est utilisé dans des applications industrielles lourdes, comme la fabrication de pièces pour l’aéronautique, l’automobile et la construction.
10. Presses Plieuses Hydraulique et Mécanique
Les presses plieuses peuvent être soit hydrauliques, soit mécaniques, et sont utilisées pour plier la tôle métallique selon des angles définis. Les presses hydrauliques offrent généralement plus de puissance et de contrôle sur le processus de pliage, tandis que les presses mécaniques sont plus adaptées à des applications nécessitant des séries de production plus rapides et moins complexes.
Conclusion
Les machines de mise en forme de tôle jouent un rôle central dans la fabrication moderne, permettant de transformer efficacement les tôles métalliques en produits finis ou semi-finis. Ces machines varient en fonction de la technique de formage, des matériaux traités, et des exigences de production. L’évolution des technologies, telles que l’automatisation et la commande numérique (CNC), continue d’améliorer la précision, la vitesse et la flexibilité des processus de formage de tôle, offrant ainsi des solutions plus efficaces pour les industries qui dépendent de composants métalliques.
Les machines de mise en forme de tôle sont essentielles pour transformer des feuilles de métal en produits finis ou semi-finis. Elles sont utilisées dans divers secteurs industriels, allant de l’automobile à l’aéronautique, en passant par la construction, l’électroménager et bien d’autres. Ces machines permettent de réaliser une gamme variée d’opérations, telles que le pliage, le découpage, l’emboutissage, le profilage, le roulage, et bien d’autres. Chaque type de machine est conçu pour répondre à des besoins spécifiques de production, en fonction des matériaux à transformer, des formes à obtenir, et des quantités à produire.
Certaines machines, comme les plieuses et les presses à emboutir, utilisent des forces mécaniques ou hydrauliques pour déformer la tôle. Les machines de découpe, telles que les machines à découper au laser, à plasma ou à jet d’eau, permettent de réaliser des découpes précises et de grandes dimensions. Elles sont particulièrement utiles lorsque des formes complexes ou des tolérances serrées sont requises. Les rouleuses et les machines de profilage sont utilisées pour fabriquer des courbes et des formes profilées à partir de tôles, et sont couramment utilisées pour produire des éléments de toiture, des tuyaux, des rails et des pièces de structure métallique.
En plus de ces machines traditionnelles, il existe des technologies plus récentes, telles que les presses à haute pression et les machines de formage magnétique. Ces technologies permettent de travailler avec des matériaux plus résistants et d’effectuer des déformations plus complexes, en appliquant une pression extrêmement élevée ou des champs magnétiques pour transformer la tôle sans contact direct. Cela peut être utile pour produire des pièces nécessitant des propriétés mécaniques particulières ou lorsque la déformation doit être réalisée de manière rapide et précise.
Les machines modernes sont souvent équipées de systèmes de commande numérique (CNC) qui permettent une plus grande précision, une automatisation accrue et une flexibilité dans le processus de fabrication. Cela permet de réaliser des ajustements rapides pour répondre à des exigences de production changeantes ou pour produire des séries de pièces avec une grande cohérence. Les commandes CNC permettent également une surveillance en temps réel de la production, ce qui permet d’optimiser les processus et de réduire les erreurs humaines.
L’intégration de la robotique dans le formage de tôle est une autre tendance émergente. Les robots peuvent être utilisés pour effectuer des tâches répétitives ou dangereuses, comme l’assemblage de pièces ou le transport de tôles entre les différentes machines. Cela permet de libérer les opérateurs des tâches manuelles et d’augmenter la productivité tout en réduisant les risques d’accidents du travail.
L’automatisation des lignes de production est également en croissance. Les systèmes automatisés permettent de rationaliser les processus de production, d’optimiser l’utilisation des matériaux et de réduire les coûts. Cela est particulièrement important dans des secteurs comme l’automobile, où la production de grandes séries de pièces doit être rapide, précise et rentable. L’utilisation d’intelligence artificielle et de systèmes de gestion de la production en temps réel permet de suivre l’évolution de la production et d’identifier rapidement les problèmes potentiels, ce qui permet d’optimiser les opérations.
Le développement de matériaux avancés et l’évolution des normes de durabilité influencent également la conception des machines de mise en forme de tôle. Les machines doivent être capables de travailler avec une variété de matériaux, tels que les alliages à haute résistance, l’aluminium, et même des matériaux composites, chacun ayant des caractéristiques différentes qui peuvent affecter le processus de formage. Les pressions pour réduire l’empreinte carbone et la consommation d’énergie des processus industriels ont également conduit à la conception de machines plus écoénergétiques, avec des moteurs plus efficaces et des systèmes de contrôle plus intelligents qui minimisent les gaspillages d’énergie.
Dans le même temps, l’industrie cherche à améliorer l’efficacité des processus en réduisant les déchets de matériaux. De plus en plus de machines sont équipées de systèmes de récupération des chutes de tôle, permettant de recycler les matériaux directement sur le site de production. Cela aide à réduire le gaspillage et à améliorer la rentabilité en réutilisant les matériaux excédentaires dans la production de nouvelles pièces.
Les tendances actuelles de l’industrie du formage de tôle se concentrent sur l’augmentation de la flexibilité et de la productivité, tout en garantissant une qualité constante des pièces produites. L’intégration de nouvelles technologies et le passage à des systèmes plus automatisés permettent non seulement de produire des pièces de plus en plus complexes, mais aussi de le faire plus rapidement et à moindre coût. Les machines de mise en forme de tôle sont ainsi en constante évolution pour répondre aux besoins d’une industrie en perpétuelle mutation, dans un environnement de plus en plus axé sur la durabilité, la précision et l’efficacité.
L’évolution des machines de mise en forme de tôle s’oriente également vers des processus de production plus intelligents et connectés, intégrant des technologies avancées telles que l’Internet des objets (IoT), l’intelligence artificielle (IA) et le big data. Ces technologies permettent aux machines de collecter, analyser et partager des données en temps réel pour optimiser les processus de production et améliorer la prise de décision. Par exemple, les machines peuvent être équipées de capteurs intelligents qui mesurent en continu des paramètres comme la température, la pression, la vitesse et l’usure des outils. Ces données sont ensuite analysées pour détecter les anomalies avant qu’elles ne deviennent des problèmes, permettant ainsi une maintenance prédictive et une réduction des temps d’arrêt non planifiés.
Les systèmes de vision industrielle sont également de plus en plus utilisés dans les machines de mise en forme de tôle. Ces systèmes permettent d’inspecter automatiquement les pièces produites, de vérifier leur conformité aux spécifications et de détecter des défauts ou des imperfections. L’utilisation de caméras haute résolution et de logiciels de traitement d’image avancés permet de réaliser un contrôle qualité en temps réel, ce qui améliore la précision des produits finis et réduit le besoin de contrôles manuels.
De plus, le contrôle numérique avancé (CNC) offre une flexibilité et une précision accrues dans la production. Les machines de mise en forme de tôle avec CNC permettent non seulement de programmer les mouvements des outils avec une grande précision, mais elles peuvent aussi ajuster automatiquement les paramètres en fonction des variations de l’environnement ou du matériau. Cela permet d’optimiser le processus de fabrication et de garantir une qualité constante des produits, même dans des conditions de production variables.
Les systèmes de simulation jouent également un rôle croissant dans le développement des machines de mise en forme de tôle. Avant de lancer la production réelle, des simulations numériques permettent de modéliser les processus de formage pour anticiper les problèmes potentiels, ajuster les paramètres de production et optimiser la conception des pièces. Ces outils de simulation sont utilisés pour prédire comment les matériaux se comporteront lors du processus de formage, ce qui permet de réduire les risques d’erreurs coûteuses et d’améliorer l’efficacité du processus de fabrication.
Les roboticiens continuent également à jouer un rôle clé dans la mise en forme de tôle. L’intégration de robots collaboratifs (cobots) dans les lignes de production permet de renforcer la sécurité et de réduire la pénibilité des tâches pour les opérateurs humains. Les cobots, souvent utilisés pour des tâches répétitives ou dangereuses, travaillent en étroite collaboration avec les opérateurs humains, en permettant une interaction en temps réel et en garantissant un environnement de travail plus sûr. Par exemple, un robot peut être utilisé pour manipuler des tôles lourdes ou pour effectuer des tâches précises de découpe ou de soudage, tandis que les opérateurs humains supervisent le processus et effectuent des ajustements si nécessaire.
L’intégration de l’automatisation flexible dans les systèmes de formage de tôle permet aux entreprises de produire des séries de pièces variées sans avoir à reconfigurer entièrement la ligne de production. Cela permet de répondre plus rapidement aux demandes du marché, tout en maintenant une productivité élevée. Par exemple, les machines à commande numérique peuvent être reprogrammées facilement pour produire différentes pièces en fonction des besoins du client, sans avoir besoin de changements physiques majeurs dans les machines.
Un autre aspect important de l’innovation dans le domaine des machines de mise en forme de tôle réside dans la durabilité et la réduction de l’impact environnemental des processus de fabrication. Les nouvelles générations de machines sont conçues pour être plus écoénergétiques et moins polluantes, réduisant ainsi les coûts opérationnels tout en répondant aux exigences croissantes en matière de durabilité. Des solutions telles que l’utilisation de matériaux recyclés, l’optimisation de la consommation énergétique et la gestion des déchets jouent un rôle essentiel dans cette transition vers des processus de production plus écologiques.
Les marchés émergents, notamment en Asie et en Afrique, présentent un potentiel de croissance pour les machines de mise en forme de tôle, notamment en raison de l’urbanisation croissante et de l’augmentation des investissements dans les infrastructures. Ces régions adoptent des technologies avancées pour moderniser leur industrie de la métallurgie et répondre à la demande croissante de biens de consommation, d’automobiles, d’appareils électroménagers, et d’autres produits métalliques. Cela entraîne une forte demande pour des machines plus efficaces, capables de produire une grande variété de pièces métalliques dans des délais plus courts et à des coûts compétitifs.
La recherche de solutions de fabrication personnalisées et à petite échelle est un autre aspect qui influence l’évolution des machines de mise en forme de tôle. Dans certains secteurs, comme celui de la construction de petits appareils électroniques ou la fabrication d’outils de précision, les entreprises cherchent des machines capables de produire des pièces uniques ou des séries de petite taille à des coûts abordables. Cette tendance favorise l’adoption de technologies telles que l’impression 3D métallique ou des systèmes de formage plus modulaires, permettant une grande flexibilité dans la production tout en minimisant les investissements nécessaires.
Finalement, l’avenir des machines de mise en forme de tôle s’oriente vers une production intelligente, intégrant des systèmes de gestion avancés, des capteurs connectés et des analyses en temps réel pour optimiser tous les aspects du processus de fabrication. Cette évolution permettra non seulement de réduire les coûts et d’augmenter la productivité, mais aussi de répondre aux exigences de plus en plus strictes en matière de qualité, de personnalisation, et de durabilité. Les avancées technologiques et les innovations dans le domaine des machines de mise en forme de tôle continueront de transformer l’industrie manufacturière, offrant de nouvelles possibilités pour la production de pièces métalliques complexes et de haute qualité.
Équipements de formage de tôle
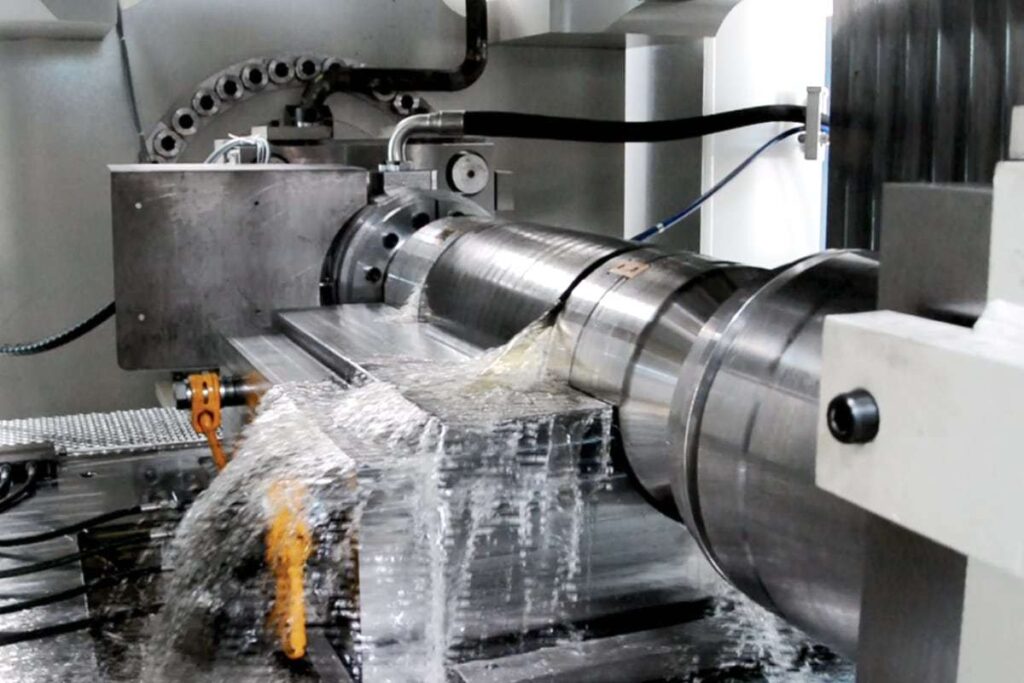
Les équipements de formage de tôle sont des machines et des dispositifs utilisés pour transformer des tôles métalliques en produits finis ou semi-finis à travers divers procédés de déformation. Ces équipements sont essentiels dans des industries telles que l’automobile, l’aéronautique, la construction, et la fabrication de biens de consommation. Ils permettent de réaliser des pièces aux formes complexes, tout en garantissant la précision et l’efficacité des processus de production. Voici une vue d’ensemble des principaux types d’équipements utilisés pour le formage de tôle.
1. Plieuses
Les plieuses sont utilisées pour plier les tôles métalliques selon un angle spécifique. Elles peuvent être hydrauliques, mécaniques, ou à commande numérique (CNC) pour une meilleure précision. Les plieuses hydrauliques sont particulièrement adaptées pour les tôles épaisses et offrent une grande flexibilité en termes d’angles de pliage. Les plieuses CNC permettent des ajustements rapides et des changements de paramètres sans reconfiguration physique.
2. Presses à emboutir
Les presses à emboutir ou presses de formage sont utilisées pour produire des pièces à partir de tôles métalliques par emboutissage, un procédé qui déforme la tôle à l’aide d’une matrice et d’un poinçon. Ce procédé permet de réaliser des pièces à géométrie complexe, comme des coques ou des carrosseries de voitures. Les presses peuvent être hydrauliques ou mécaniques, et sont équipées de contrôles numériques pour plus de précision.
3. Rouleuses à tôle
Les rouleuses à tôle, ou machines de roulage, permettent de courber les tôles métalliques. Ces machines fonctionnent en faisant passer la tôle entre plusieurs rouleaux qui la déforment progressivement en une forme courbe ou cylindrique. Elles sont principalement utilisées pour fabriquer des tuyaux, des cônes, des arcs et des profils de couverture métallique.
4. Cisailles
Les cisailles sont des machines de découpe qui utilisent deux lames pour trancher les tôles métalliques. Elles sont souvent utilisées pour couper des tôles plates en lignes droites. Les cisailles peuvent être manuelles, électriques ou hydrauliques, et sont particulièrement efficaces pour des découpes simples et des grandes séries de production.
5. Machines à découpe au laser
Les machines à découpe au laser utilisent un faisceau laser très concentré pour découper des tôles métalliques avec une grande précision. Ce procédé est particulièrement adapté pour la découpe de formes complexes, de petites pièces, ou de tolérances serrées. Les machines à découpe laser peuvent être utilisées sur des matériaux tels que l’acier inoxydable, l’aluminium et d’autres métaux.
6. Machines de découpe au plasma
Les machines de découpe au plasma utilisent un jet de gaz ionisé pour couper des tôles métalliques. Le procédé est plus rapide que la découpe au laser, mais il peut être moins précis pour des matériaux fins. La découpe au plasma est idéale pour couper des tôles plus épaisses et est largement utilisée dans l’industrie du métal et de la construction.
7. Machines de découpe à jet d’eau
Les machines de découpe à jet d’eau utilisent un jet d’eau à haute pression, souvent mélangé à un abrasif, pour découper des tôles métalliques. Ce procédé est particulièrement utile pour les matériaux sensibles à la chaleur, comme les alliages métalliques ou les matériaux composites. La découpe à jet d’eau permet des découpes nettes et précises sans affecter les propriétés du matériau.
8. Machines de profilage
Les machines de profilage ou lignes de profilage sont utilisées pour produire des profilés métalliques (par exemple, des tôles ondulées ou des profils de toiture). Elles fonctionnent en faisant passer la tôle entre une série de rouleaux qui lui donnent la forme souhaitée. Les machines de profilage sont souvent utilisées pour la production en série de pièces de construction, de charpentes métalliques, ou d’éléments de couverture.
9. Machines de formage à froid
Le formage à froid est une méthode de transformation qui déforme la tôle métallique à température ambiante, ce qui permet d’éviter les coûts et les complications associés à l’utilisation de chaleur. Les machines de formage à froid incluent des plieuses, des presses et des machines de découpe, qui peuvent être adaptées pour des applications comme l’emboutissage, le profilage, ou le pliage de tôles minces.
10. Machines de formage à haute pression
Les machines de formage à haute pression sont utilisées pour appliquer des pressions extrêmement élevées sur les tôles métalliques. Elles sont adaptées pour les matériaux très résistants et les applications où une déformation importante est nécessaire, comme dans la fabrication de pièces automobiles ou d’aéronautique.
11. Machines de formage magnétique
Les machines de formage magnétique utilisent un champ magnétique pour déformer les tôles métalliques. Elles sont particulièrement utilisées pour des applications spécifiques où un formage précis est nécessaire sans contact direct avec la tôle. Ce procédé est encore relativement rare, mais il peut offrir des avantages dans certains secteurs où des matériaux sensibles doivent être traités sans dommage.
12. Systèmes robotisés
Les robots industriels sont de plus en plus utilisés dans les lignes de formage de tôle pour effectuer des tâches telles que la manipulation de tôles, le soudage, ou l’assemblage de pièces. Les robots collaboratifs (cobots) travaillent en étroite collaboration avec les opérateurs humains, offrant une sécurité accrue tout en automatisant des tâches répétitives.
13. Machines de formage à haute fréquence
Les machines de formage à haute fréquence utilisent des courants électriques à haute fréquence pour chauffer localement la tôle, facilitant ainsi sa déformation. Ce procédé est souvent utilisé dans la fabrication de certains types de tubes métalliques et dans la production de composants pour l’industrie automobile.
14. Machines à emboutir rotatives
Les machines à emboutir rotatives sont utilisées dans des applications de haute production, où plusieurs emboutissages sont réalisés en série. Ces machines fonctionnent en tournant la tôle pendant l’opération d’emboutissage, ce qui permet de réaliser des pièces complexes à des cadences très élevées.
Conclusion
Les équipements de formage de tôle sont essentiels pour transformer des tôles métalliques en une multitude de pièces utilisées dans des secteurs variés. Du pliage à la découpe, en passant par l’emboutissage et le profilage, chaque machine est conçue pour répondre à des besoins spécifiques en termes de précision, de complexité des formes, de vitesse de production et de coût. L’intégration de technologies avancées telles que la commande numérique, l’automatisation, la robotique et la connectivité permet d’optimiser ces processus de manière significative, tout en répondant aux exigences croissantes en matière de qualité et d’efficacité dans les industries modernes.
Les équipements de formage de tôle sont utilisés pour transformer les tôles métalliques en produits finis ou semi-finis, grâce à une série de procédés mécaniques et thermiques. Ces machines sont utilisées dans diverses industries comme l’automobile, la construction, l’aéronautique, et la fabrication de biens de consommation. Le formage de tôle comprend des techniques telles que le pliage, l’emboutissage, la découpe, le roulage, et le profilage, chacune adaptée à des besoins spécifiques de production.
Les plieuses permettent de réaliser des pliages de tôle avec une grande précision, et peuvent être mécaniques, hydrauliques ou numériques, offrant une flexibilité importante dans les réglages de l’angle et de la profondeur de pliage. Les presses à emboutir, quant à elles, utilisent des matrices et des poinçons pour déformer la tôle, permettant ainsi de produire des pièces complexes comme des carrosseries automobiles ou des composants d’aéronefs. Le processus est souvent accompagné de presses hydrauliques ou mécaniques capables d’appliquer de fortes pressions sur la tôle.
Les rouleuses à tôle, également appelées machines de roulage, sont utilisées pour donner une forme courbe ou cylindrique à la tôle, ce qui est utile pour la fabrication de tuyaux, de courbes de structure, et d’éléments de toiture. En parallèle, les cisailles sont utilisées pour couper les tôles métalliques, qu’elles soient manuelles, hydrauliques, ou électriques, et sont particulièrement efficaces pour des découpes droites et simples.
Les machines à découpe au laser et au plasma sont des équipements modernes utilisés pour découper des tôles métalliques avec une précision extrême. Le laser permet de réaliser des découpes fines et complexes, tandis que le plasma est plus adapté pour des découpes plus rapides, souvent sur des tôles plus épaisses. Les machines de découpe à jet d’eau utilisent un jet d’eau haute pression mélangé à un abrasif, ce qui permet de découper des métaux sans générer de chaleur, évitant ainsi toute déformation thermique du matériau.
Les machines de profilage sont spécifiquement conçues pour fabriquer des profilés métalliques, comme des tôles ondulées ou des poutrelles. Ce processus implique de faire passer la tôle entre des rouleaux de forme spécifique pour obtenir le profil souhaité. Les machines de formage à froid, en revanche, sont utilisées pour déformer des tôles métalliques à température ambiante, ce qui permet d’éviter l’utilisation d’énergie thermique et est particulièrement adapté aux tôles minces et aux formes moins complexes.
Les machines de formage à haute pression et à haute fréquence utilisent des pressions ou des courants électriques élevés pour déformer les tôles métalliques. Ces équipements sont utiles pour les matériaux très résistants ou lorsque des déformations importantes sont nécessaires. Certaines machines de formage magnétique utilisent un champ magnétique pour déformer la tôle sans contact direct, une technologie qui reste relativement peu courante mais qui offre des avantages spécifiques dans certaines applications.
L’intégration de la robotique dans les lignes de production est une tendance croissante, avec l’utilisation de robots pour manipuler les tôles, assembler les pièces ou effectuer des tâches répétitives. Les robots collaboratifs (cobots) travaillent aux côtés des opérateurs humains pour effectuer des tâches dangereuses ou difficiles, permettant ainsi d’augmenter la productivité tout en réduisant les risques pour les employés. Les systèmes automatisés permettent également de réduire les erreurs humaines et d’augmenter l’efficacité générale des lignes de production.
En parallèle, les technologies de contrôle numérique (CNC) sont de plus en plus utilisées pour garantir la précision des opérations. Grâce à la commande numérique, les machines peuvent être programmées pour effectuer des ajustements fins pendant le processus de fabrication, ce qui permet de produire des pièces complexes avec une grande précision et une répétabilité élevée. Les machines CNC sont également capables d’effectuer des ajustements en temps réel pour répondre aux variations des matériaux ou de l’environnement.
Les systèmes de vision industrielle et d’intelligence artificielle permettent également d’automatiser et de contrôler la qualité des pièces en temps réel, réduisant ainsi le besoin de contrôles manuels. Ces technologies permettent de détecter les défauts de fabrication, d’ajuster les paramètres de production et d’assurer que chaque pièce respectera les spécifications requises, augmentant ainsi le rendement de la production et réduisant les déchets.
Dans les années récentes, l’accent a également été mis sur l’éco-conception et l’efficience énergétique des équipements de formage de tôle. Les machines modernes sont conçues pour réduire la consommation énergétique et minimiser les déchets, en optimisant l’utilisation des matériaux et en favorisant le recyclage des chutes de métal. Cela est particulièrement important dans un contexte où les préoccupations environnementales deviennent un facteur clé dans l’industrie de la fabrication.
Les équipements de formage de tôle sont donc essentiels pour produire une large gamme de produits métalliques, allant des pièces automobiles aux composants de construction, en passant par des éléments d’aéronefs ou des biens de consommation. Leur évolution constante, guidée par les innovations technologiques, permet non seulement d’améliorer la précision et la productivité, mais aussi de répondre à des exigences croissantes en termes de durabilité et de rentabilité dans un environnement industriel de plus en plus automatisé et connecté.
L’évolution continue des équipements de formage de tôle est influencée par plusieurs tendances clés, notamment la numérisation, l’automatisation avancée, et l’intégration de l’Internet des objets (IoT). Ces technologies permettent d’optimiser les processus de production, d’améliorer la précision des pièces et de réduire les coûts de fabrication. L’Industrie 4.0 transforme les équipements de formage de tôle en machines intelligentes capables de collecter des données en temps réel, d’analyser les performances et de prendre des décisions autonomes pour ajuster les paramètres de production.
Les machines connectées permettent de surveiller l’état des équipements à distance et de détecter les anomalies avant qu’elles n’affectent la production. Par exemple, des capteurs intégrés dans les machines peuvent suivre l’usure des outils, la température de fonctionnement, et la pression appliquée pendant les processus de formage. Ces données sont ensuite envoyées à un système de gestion centralisé où des algorithmes d’intelligence artificielle analysent les informations pour prédire des pannes potentielles, optimiser les cycles de maintenance et prévenir des arrêts de production non planifiés. Cela permet une approche de maintenance prédictive, qui réduit les temps d’arrêt et améliore l’efficacité opérationnelle.
La fabrication additive, bien qu’encore en développement pour le formage de tôle, commence à influencer les processus de fabrication traditionnels. L’impression 3D métallique et d’autres techniques de fabrication additive permettent de créer des pièces métalliques complexes qui étaient auparavant difficiles ou impossibles à produire avec des méthodes de formage conventionnelles. Cette technologie pourrait compléter ou même remplacer certaines opérations de formage traditionnelles, en particulier pour des petites séries ou des pièces sur mesure nécessitant une grande précision.
Le contrôle qualité automatisé devient également de plus en plus sophistiqué grâce à l’utilisation de systèmes de vision par ordinateur et de capteurs intelligents. Ces systèmes permettent de vérifier la qualité des pièces en temps réel tout au long du processus de fabrication, en détectant des défauts invisibles à l’œil nu, tels que des fissures microscopiques ou des variations dimensionnelles. Les logiciels de vision industrielle analysent les images capturées par les caméras haute résolution et comparent les pièces produites aux modèles numériques pour s’assurer qu’elles respectent les spécifications exactes. Les erreurs sont ainsi détectées et corrigées instantanément, ce qui réduit le taux de rebuts et améliore la qualité des produits finaux.
L’optimisation énergétique est un autre domaine d’innovation. Les machines modernes sont conçues pour être plus économes en énergie, ce qui permet aux entreprises de réduire leur empreinte écologique et leurs coûts de production. L’utilisation de moteurs à haut rendement, de systèmes de récupération de chaleur et d’optimisation des cycles de travail permet de minimiser la consommation d’énergie pendant les phases de production. De plus, les processus de formage peuvent être ajustés pour utiliser moins de matériaux, ce qui contribue à la réduction des déchets et à la gestion durable des ressources.
Le recyclage des matériaux est également au cœur des préoccupations actuelles. Les équipements de formage de tôle intègrent souvent des systèmes qui permettent de réutiliser les chutes de métal ou les pièces non conformes, réduisant ainsi la nécessité d’acheter de nouvelles matières premières. Ces machines sont conçues pour être plus flexibles, capables de traiter des matériaux recyclés ou des alliages spéciaux tout en maintenant des niveaux de qualité élevés.
L’adoption de technologies de simulation avancées permet de tester et d’optimiser les processus de formage avant la production réelle. Par exemple, des logiciels de simulation peuvent modéliser le comportement des matériaux sous différentes contraintes de pression, de température et de déformation. Ces outils de simulation permettent de concevoir des outils de formage plus efficaces, d’optimiser les paramètres de production et de prédire les défauts avant même qu’ils ne surviennent sur le terrain, améliorant ainsi la rentabilité des projets et réduisant le coût des prototypes physiques.
La modularité des équipements de formage est également un aspect qui se développe. Les machines peuvent être configurées ou adaptées en fonction des besoins spécifiques des fabricants, ce qui leur permet de répondre à des demandes de production plus flexibles. Par exemple, les lignes de production peuvent être reconfigurées rapidement pour produire différentes pièces ou changer d’outils sans nécessiter un arrêt prolongé de la production. Cette flexibilité est particulièrement précieuse dans les secteurs où les exigences du marché changent fréquemment, comme dans l’automobile ou la production de biens de consommation.
Les robots collaboratifs (cobots) jouent un rôle de plus en plus important dans les environnements de production de tôles. Ces robots sont conçus pour travailler en toute sécurité aux côtés des opérateurs humains, prenant en charge des tâches répétitives ou dangereuses tout en permettant une collaboration étroite avec l’humain. Les cobots peuvent être utilisés pour manipuler des tôles, effectuer des tâches de soudage, de découpe ou d’assemblage, tout en s’adaptant à des changements dans le processus de production. Cette coopération homme-machine permet de maximiser l’efficacité tout en garantissant un environnement de travail plus sûr.
Les marchés émergents dans des régions comme l’Asie, l’Afrique et l’Amérique Latine voient une forte demande pour des équipements de formage de tôle. Ces régions, en plein développement industriel, cherchent à moderniser leurs infrastructures et à adopter des technologies avancées pour soutenir une croissance rapide. Les équipements de formage de tôle y jouent un rôle essentiel, car ils permettent de produire à grande échelle des pièces pour la construction, l’automobile, l’aéronautique, et d’autres secteurs en plein essor.
Enfin, l’avenir des équipements de formage de tôle est intrinsèquement lié à la transition vers des pratiques de fabrication plus durables. L’augmentation de la demande pour des solutions écologiques et plus efficaces pousse les fabricants à développer des équipements qui non seulement optimisent les coûts, mais contribuent également à la réduction de l’empreinte carbone. Cela inclut des innovations dans la récupération et le recyclage des matériaux, la réduction des déchets et de l’énergie, et l’utilisation de technologies de production respectueuses de l’environnement.
En conclusion, les équipements de formage de tôle évoluent vers des machines plus intelligentes, plus flexibles, plus écologiques et plus connectées. L’impact de ces innovations est profond, non seulement en termes d’efficacité de production, mais aussi en matière de durabilité et de qualité des produits finis. L’avenir des équipements de formage de tôle s’annonce prometteur, avec un fort accent sur l’intégration de la technologie et de la durabilité dans les processus de fabrication.
Équipements pour la production de pièces en tôle
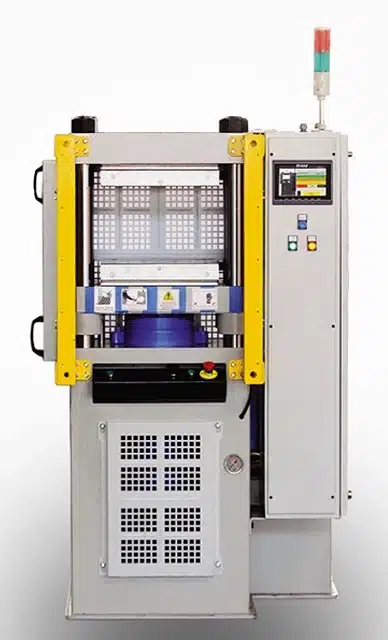
Les équipements pour la production de pièces en tôle sont utilisés pour transformer les tôles métalliques en pièces finies ou semi-finies, qui sont utilisées dans diverses industries, telles que l’automobile, l’aéronautique, la construction, l’électroménager, et d’autres secteurs nécessitant des pièces métalliques de précision. Ces équipements varient en fonction des processus de production et des caractéristiques des pièces à produire, et ils peuvent combiner différentes technologies pour obtenir des résultats optimaux en termes de qualité, de rapidité et d’efficacité. Voici un aperçu des principaux équipements utilisés dans la production de pièces en tôle.
1. Plieuses
Les plieuses sont utilisées pour plier la tôle métallique selon un angle spécifique. Elles peuvent être manuelles, hydrauliques ou à commande numérique (CNC). Les plieuses CNC offrent une grande précision et permettent d’automatiser les ajustements, ce qui est particulièrement utile pour des séries de production de pièces complexes et pour garantir une grande uniformité des pièces produites. Elles sont largement utilisées pour la fabrication de composants tels que des panneaux, des boîtiers, des châssis, et d’autres pièces nécessitant des plis nets et réguliers.
2. Presses à emboutir
Les presses à emboutir (ou presses de formage) sont utilisées pour déformer les tôles métalliques à l’aide d’une matrice et d’un poinçon, permettant de produire des pièces de formes complexes comme des boîtiers, des coques ou des composants automobiles. Ces presses sont souvent hydrauliques ou mécaniques, et peuvent être équipées de commandes numériques pour offrir plus de flexibilité dans les réglages et une plus grande précision de formage. Elles sont idéales pour la production de grandes séries de pièces avec une forme constante.
3. Machines de découpe (cisaille, laser, plasma, jet d’eau)
Les machines de découpe sont utilisées pour séparer des pièces de tôle des grandes plaques métalliques. Elles peuvent utiliser différentes technologies, chacune ayant ses avantages spécifiques :
- Cisailles : pour des découpes droites simples de tôles fines ou épaisses.
- Découpe au laser : pour des découpes de haute précision, particulièrement adaptées pour des formes complexes et des matériaux plus fins.
- Découpe au plasma : plus rapide que la découpe au laser, idéale pour les tôles épaisses, bien que moins précise pour des découpes fines.
- Découpe à jet d’eau : permet une découpe sans chaleur, ce qui évite toute déformation thermique et est adapté aux matériaux sensibles à la chaleur ou aux pièces complexes.
4. Rouleuses à tôle
Les rouleuses à tôle (ou machines de roulage) sont utilisées pour plier ou courber les tôles en des formes arrondies ou cylindriques, ce qui est couramment requis pour fabriquer des pièces comme des tuyaux, des cônes, ou des éléments de toiture. Ces machines passent la tôle entre plusieurs rouleaux qui l’accolent progressivement jusqu’à obtenir la forme souhaitée. Elles sont idéales pour la production de pièces de formes circulaires ou courbes.
5. Machines à emboutir rotatives
Les machines à emboutir rotatives sont une version plus spécialisée des presses à emboutir, où la tôle est tournée pendant l’emboutissage. Ce type de machine est utilisé pour produire des pièces complexes à un rythme rapide, et il est souvent utilisé dans des environnements de production de masse. Ces machines sont particulièrement adaptées à la production de pièces automobiles et électroniques.
6. Machines de profilage
Les machines de profilage sont utilisées pour produire des profilés métalliques, comme des tôles ondulées ou des poutres en acier. Elles font passer la tôle entre des rouleaux qui lui donnent la forme souhaitée. Ce procédé est souvent utilisé pour la fabrication de tôles pour la construction, des panneaux de toiture, ou des éléments de charpente métallique. Les machines de profilage peuvent être configurées pour produire une grande variété de profils de tôle en fonction des besoins spécifiques.
7. Machines de formage à froid
Les machines de formage à froid sont utilisées pour déformer les tôles métalliques sans les chauffer, ce qui permet de maintenir l’intégrité du matériau tout en le modifiant en termes de forme. Ces machines sont souvent utilisées pour produire des pièces simples ou des profilés métalliques, et elles sont particulièrement adaptées pour travailler avec des matériaux minces et légers. Le formage à froid est couramment utilisé pour les composants automobiles, les équipements de construction, et les produits électroniques.
8. Machines de formage à chaud
Le formage à chaud est utilisé pour des tôles plus épaisses ou des matériaux plus résistants. Dans ce procédé, la tôle est chauffée à une température spécifique avant d’être formée, ce qui permet de réduire la résistance du matériau et de faciliter sa déformation. Ce procédé est couramment utilisé dans la fabrication de pièces automobiles, aéronautiques et dans l’industrie de la construction pour produire des éléments structurels solides.
9. Soudage et assemblage
Les machines de soudage sont utilisées pour assembler des pièces de tôle entre elles, ce qui est nécessaire lorsque la pièce en tôle doit être reliée à d’autres éléments pour former une structure complète. Les procédés de soudage les plus couramment utilisés incluent :
- Soudage MIG/MAG (Métal Inert Gas / Métal Active Gas) : pour assembler des tôles minces.
- Soudage TIG (Tungsten Inert Gas) : pour des soudures de haute précision et de qualité.
- Soudage par résistance : utilisé pour l’assemblage de tôles fines, notamment dans l’automobile.
10. Machines de découpe et de marquage laser
Les machines de découpe et de marquage laser sont une évolution des technologies de découpe classiques. Elles permettent de découper, mais aussi de marquer ou d’inscrire des informations sur les pièces en tôle. Ce marquage peut inclure des codes QR, des numéros de série, ou des spécifications techniques. Ces machines sont très utiles dans des industries où la traçabilité et le marquage des pièces sont nécessaires, comme dans l’aéronautique ou la production d’équipements de haute technologie.
11. Presses plieuses de grande capacité
Les presses plieuses de grande capacité sont utilisées dans des applications industrielles où des tôles épaisses doivent être pliées avec des forces importantes. Ces presses peuvent traiter des tôles d’épaisseur considérable, et sont souvent utilisées dans la fabrication de pièces lourdes pour les secteurs de la construction ou de l’industrie pétrolière et gazière.
12. Robotisation et automatisation
L’automatisation et la robotisation des lignes de production de tôle sont devenues essentielles pour optimiser la productivité et réduire les coûts de main-d’œuvre. Les robots sont souvent utilisés pour des tâches telles que la manipulation de pièces, le soudage, ou même la découpe et le pliage. Les systèmes automatisés permettent une production continue et précise de grandes séries de pièces.
13. Machines de traitement de surface
Les machines de traitement de surface, telles que les sablanes, les machines de polissage, et les machines de galvanisation, sont utilisées pour améliorer les propriétés de surface des pièces en tôle, comme la résistance à la corrosion, l’aspect esthétique ou la finition de surface. Ces équipements sont particulièrement utilisés dans les industries où l’apparence et la durabilité des pièces en tôle sont essentielles, comme dans l’automobile et les produits de consommation.
En résumé, les équipements utilisés pour la production de pièces en tôle couvrent une large gamme de technologies et de procédés, chacun étant conçu pour répondre aux besoins spécifiques de l’industrie, du type de matériau à transformer, des caractéristiques des pièces à produire, et du volume de production. Ces équipements permettent de fabriquer des pièces métalliques variées avec une grande précision et une efficacité optimale.
Les équipements pour la production de pièces en tôle sont essentiels pour transformer les tôles métalliques en composants utilisés dans divers secteurs industriels, notamment l’automobile, la construction, l’aéronautique et l’électroménager. Ces machines sont conçues pour effectuer une variété d’opérations de transformation sur les tôles métalliques, y compris la découpe, le formage, le pliage, l’emboutissage, le profilage et l’assemblage.
Les plieuses sont des équipements incontournables dans la production de pièces en tôle. Elles permettent de plier la tôle selon un angle précis, offrant ainsi des solutions pour la fabrication de boîtiers, de châssis, de panneaux et d’autres pièces qui nécessitent des formes angulées. Avec l’avènement des plieuses à commande numérique (CNC), ces machines offrent une grande précision, permettant une production rapide et répétitive de pièces complexes avec des tolérances strictes.
Les presses à emboutir sont également largement utilisées pour produire des pièces complexes. Ce type de machine utilise une matrice et un poinçon pour déformer la tôle, et il est idéal pour des applications où des formes complexes sont requises. Ces presses peuvent être hydrauliques ou mécaniques, et de plus en plus, elles sont équipées de technologies CNC pour un contrôle plus précis des paramètres de production. Cela est particulièrement important dans des secteurs tels que l’automobile, où des pièces aux formes variées et complexes doivent être fabriquées à grande échelle.
La découpe est une autre étape clé dans la production de pièces en tôle. Les cisailles, qui sont utilisées pour des découpes simples et rapides de tôles fines ou épaisses, font partie des équipements les plus courants dans ce domaine. D’autres technologies comme la découpe au laser, la découpe au plasma et la découpe à jet d’eau permettent de réaliser des découpes plus complexes, de haute précision, et sont particulièrement utiles pour les formes détaillées ou les matériaux plus épais. Le laser, par exemple, permet une découpe extrêmement précise et propre, tandis que le plasma est plus rapide et peut traiter des tôles plus épaisses. Le jet d’eau, quant à lui, offre l’avantage de ne pas générer de chaleur, évitant ainsi toute déformation thermique du matériau.
Le formage de tôle comprend également des opérations comme le roulage, qui est utilisé pour produire des pièces courbes ou cylindriques, telles que des tuyaux, des cônes ou des éléments de toiture. Les rouleuses à tôle sont utilisées pour ce processus, où la tôle passe entre plusieurs rouleaux pour lui donner la forme souhaitée. C’est un procédé fondamental dans des industries comme la construction et la fabrication d’équipements industriels.
En plus du formage et de la découpe, les équipements de soudage sont cruciaux pour assembler les pièces en tôle. Les robots de soudage sont de plus en plus utilisés dans la production automatisée de pièces, notamment pour les soudures de précision dans des secteurs comme l’automobile ou l’aéronautique. Ces robots sont capables d’effectuer des soudures cohérentes et de haute qualité, tout en réduisant les erreurs humaines et en augmentant la vitesse de production.
L’automatisation des lignes de production devient également un élément clé dans la production moderne de pièces en tôle. De nombreuses usines utilisent des robots collaboratifs (cobots) qui travaillent aux côtés des opérateurs humains pour effectuer des tâches répétitives ou dangereuses. Cela permet de réduire la fatigue des employés et d’augmenter la productivité. L’intégration de systèmes de vision industrielle et de contrôles automatisés permet de détecter et corriger en temps réel les défauts de fabrication, garantissant ainsi une qualité constante tout au long de la production.
Les équipements modernes de traitement de surface, tels que les machines de galvanisation, les sablanes et les polisseuses, jouent également un rôle important dans la finition des pièces en tôle. Ces machines permettent d’améliorer la résistance à la corrosion, l’apparence esthétique et la durabilité des pièces métalliques. Dans l’industrie automobile, par exemple, les pièces en tôle sont souvent traitées pour garantir leur longévité et leur résistance aux intempéries.
En parallèle, les innovations dans le recyclage des matériaux sont également un aspect important du processus de production de pièces en tôle. De plus en plus d’équipements sont conçus pour optimiser l’utilisation des matériaux et minimiser les déchets, par exemple, en récupérant et en réutilisant les chutes de tôle. Cette approche est essentielle pour réduire l’empreinte écologique des industries métallurgiques et répondre aux exigences croissantes en matière de durabilité.
Enfin, l’industrie 4.0 transforme la manière dont ces équipements fonctionnent en intégrant des technologies comme l’Internet des objets (IoT), l’intelligence artificielle et la maintenance prédictive. Les machines sont désormais capables de collecter et d’analyser des données en temps réel, ce qui permet d’optimiser les performances, de réduire les pannes et d’améliorer la qualité des produits finis. La simulation numérique permet également de tester les processus de fabrication avant même qu’ils ne soient réalisés, réduisant ainsi les coûts liés aux erreurs de production et aux prototypes physiques.
En conclusion, la production de pièces en tôle repose sur un large éventail d’équipements spécialisés qui permettent de réaliser des opérations complexes telles que le formage, la découpe, le soudage et le traitement de surface. L’automatisation, la robotisation, ainsi que les avancées en matière de technologies de contrôle et d’analyse, permettent d’améliorer la productivité, la précision et la qualité des pièces tout en réduisant les coûts de production et l’impact environnemental. Les évolutions technologiques en cours promettent de transformer encore davantage le secteur de la fabrication de pièces en tôle, rendant ces processus plus efficaces et plus durables.
Les progrès continus dans la fabrication de pièces en tôle ouvrent la voie à des technologies de production plus avancées et des solutions plus personnalisées pour répondre aux besoins de divers secteurs. Ces nouvelles innovations permettent de répondre à des exigences de plus en plus strictes en matière de qualité, de durabilité et de flexibilité dans la production de pièces métalliques. Les équipements de production de pièces en tôle évoluent pour intégrer des solutions de fabrication souples, permettant une réponse rapide aux besoins changeants du marché et la capacité de produire des petites séries ou des pièces sur mesure avec une grande précision.
Une tendance notable dans l’industrie des équipements de production de tôle est le renforcement de la connectivité entre les machines. Grâce à des systèmes intégrés de gestion de la production, les machines intelligentes peuvent échanger des informations en temps réel pour ajuster automatiquement les paramètres de production. Par exemple, une machine de découpe laser peut ajuster sa puissance et sa vitesse de coupe en fonction des spécifications exactes de chaque pièce à produire, tout en minimisant les erreurs humaines et en réduisant le gaspillage de matériaux. Cela crée un environnement de production flexible et réactif, capable de s’adapter aux demandes de production personnalisées et aux changements fréquents de design ou de matériau.
Les technologies de simulation numérique jouent également un rôle croissant dans l’optimisation de la production de pièces en tôle. Grâce à des logiciels de simulation de formage, les fabricants peuvent tester et affiner leurs procédés de production avant de lancer une série de fabrication. Cela permet de prédire les comportements des matériaux, de tester les outils de formage, d’évaluer les forces nécessaires et d’identifier des défauts potentiels dans la conception avant qu’ils ne surviennent dans le monde réel. Cela réduit le besoin de prototypes physiques, accélère le développement de produits, et permet de garantir une meilleure rentabilité.
Le contrôle qualité devient également plus sophistiqué avec l’intégration de systèmes automatisés. Des technologies telles que la vision industrielle, combinées à des logiciels d’analyse de données et à des capteurs intelligents, permettent de surveiller la qualité des pièces à chaque étape du processus de production. Ces systèmes peuvent détecter automatiquement les défauts, comme les déformations, les fissures ou les imperfections de surface, et ajuster les machines en conséquence pour corriger le problème en temps réel. Cette surveillance continue améliore considérablement la qualité des pièces et réduit les erreurs humaines, ce qui est crucial dans des secteurs comme l’aéronautique ou l’automobile, où la précision et la sécurité sont des priorités absolues.
L’optimisation énergétique et la réduction des coûts d’exploitation sont d’autres priorités majeures pour les équipements modernes de production de pièces en tôle. La consommation d’énergie est un facteur clé dans les processus de formage, et de nombreux équipements sont désormais conçus pour être plus économes en énergie. Les systèmes de récupération d’énergie, comme ceux utilisés dans les presses hydrauliques et les machines de découpe, permettent de récupérer et de réutiliser l’énergie qui serait autrement gaspillée. Les moteurs à haute efficacité et les technologies de régulation de la vitesse permettent également d’optimiser les performances des équipements tout en réduisant leur consommation énergétique.
En ce qui concerne la durabilité, les fabricants d’équipements de production de pièces en tôle s’efforcent de rendre leurs machines plus écologiques en utilisant des matériaux recyclables et en intégrant des procédés qui minimisent les déchets. Par exemple, les machines de découpe au laser permettent une découpe nette qui génère moins de déchets par rapport aux méthodes plus traditionnelles, tout en maintenant une qualité de coupe élevée. L’utilisation de matériaux recyclés dans la production des tôles métalliques, combinée à des processus de fabrication plus efficaces, contribue également à une fabrication plus durable et à la réduction de l’empreinte carbone des usines.
Le recyclage des matériaux est un autre domaine d’innovation majeur dans la fabrication de pièces en tôle. L’industrie métallurgique cherche constamment à améliorer ses techniques de gestion des matériaux en optimisant les taux de recyclage. Par exemple, les chutes de tôle provenant de la découpe ou de l’emboutissage peuvent être récupérées et réutilisées dans la production d’autres pièces. Cela permet non seulement de réduire les déchets, mais aussi de diminuer la dépendance aux ressources naturelles et de réduire l’impact environnemental de la production de tôle.
Les robots collaboratifs (cobots) et la robotisation avancée jouent également un rôle clé dans la production de pièces en tôle. Ces robots, qui peuvent travailler en toute sécurité aux côtés des opérateurs humains, sont utilisés pour des tâches répétitives et physiques, telles que le soudage, l’assemblage, la manipulation de pièces lourdes ou la peinture. Leur adoption améliore non seulement l’efficacité de la production, mais aussi la sécurité des travailleurs, en les libérant des tâches dangereuses ou pénibles. Les cobots sont facilement intégrables dans des environnements de production existants, ce qui permet d’augmenter la productivité sans nécessiter de modifications majeures dans les installations de production.
L’industrie 4.0 est un facteur clé de transformation dans la fabrication de pièces en tôle, avec des technologies comme les systèmes cyber-physiques, l’analyse des données massives (big data), et l’intelligence artificielle. Ces technologies permettent non seulement une meilleure gestion de la production, mais aussi une personnalisation accrue des pièces en tôle. Les usines intelligentes, où les machines et les systèmes sont interconnectés, peuvent ainsi ajuster leurs paramètres en fonction des données collectées, optimisant ainsi les cycles de production, la qualité des pièces et la gestion des ressources.
Les marchés émergents jouent également un rôle de plus en plus important dans l’évolution des équipements pour la production de pièces en tôle. Des régions comme l’Asie et l’Afrique, qui connaissent un développement industriel rapide, ont des besoins croissants en équipements de formage et de découpe de tôle. Ces marchés recherchent des solutions de production efficaces et flexibles pour soutenir leur expansion dans des secteurs clés comme la construction, l’automobile, et l’électronique. Les équipements doivent donc être conçus pour être à la fois rentables, flexibles et capables de produire une large gamme de pièces à des coûts compétitifs.
En somme, l’industrie de la production de pièces en tôle continue d’évoluer, avec des équipements toujours plus intelligents, écologiques et flexibles. L’intégration de technologies avancées permet aux fabricants de répondre aux demandes croissantes du marché, d’améliorer la qualité des pièces, de réduire les coûts de production et de rendre les processus plus durables. L’avenir semble prometteur pour ce secteur, avec des innovations qui devraient encore transformer les méthodes de production et accroître l’efficacité et la durabilité des processus de fabrication de tôle.
Machines pour transformation plastique de la tôle
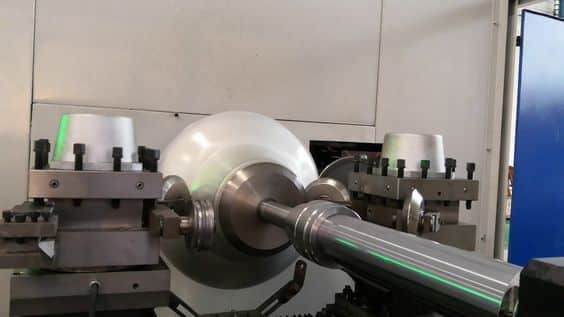
Les machines pour la transformation plastique de la tôle sont des équipements spécialisés utilisés dans les processus de formage des métaux qui modifient la forme des tôles métalliques sans provoquer de rupture ou de fissure du matériau. Le terme “plastique” dans ce contexte fait référence à la capacité du matériau à se déformer de manière permanente sans se casser, ce qui se distingue des autres formes de transformation, comme l’élasticité. Ces machines exploitent des principes mécaniques, thermiques ou combinés pour transformer les tôles métalliques en pièces fonctionnelles ou esthétiques. Voici un aperçu des principaux types de machines utilisées dans ces procédés.
1. Presses à emboutir
Les presses à emboutir (ou presses de formage) sont utilisées pour réaliser des pièces en tôle de formes complexes, telles que des boîtiers ou des composants automobiles. Ces presses peuvent être mécaniques ou hydrauliques et fonctionnent en appliquant une force de compression sur la tôle à l’aide d’un poinçon et d’une matrice. Le procédé implique la déformation plastique de la tôle sous l’action de la pression, permettant de produire des formes tridimensionnelles complexes. Les presses à emboutir sont particulièrement efficaces pour des productions en grande série, notamment pour les pièces nécessitant des détails fins et précis.
2. Plieuses
Les plieuses sont des machines qui permettent de plier des tôles métalliques de manière plastique, créant des angles ou des courbes spécifiques. Le processus de pliage est effectué en exerçant une pression sur la tôle entre deux outils (la matrice et le poinçon), ce qui permet de modifier l’angle ou la forme de la tôle sans qu’elle ne se casse. Les plieuses à commande numérique (CNC) permettent des ajustements très précis pour fabriquer des pièces avec des tolérances strictes. Ce procédé est couramment utilisé pour des pièces comme des panneaux, des boîtiers ou des composants de châssis.
3. Machines de formage par traction (emboutissage profond)
Les machines de formage par traction, également appelées presses à emboutir profond, sont utilisées pour des applications où des formes très profondes doivent être créées à partir de tôles fines. Ce procédé consiste à étirer la tôle métallique en l’amenant dans une cavité, de manière à former des pièces comme des coques, des cuves ou des carrosseries de voiture. Ces machines appliquent une force de traction qui provoque une déformation plastique de la tôle. Elles sont particulièrement utiles pour la production de grandes quantités de pièces métalliques complexes et de formes 3D.
4. Rouleuses à tôle
Les rouleuses à tôle sont des machines utilisées pour former des pièces courbes ou cylindriques à partir de tôles métalliques. Le processus consiste à faire passer la tôle entre plusieurs rouleaux, ce qui la déforme plastiquement pour lui donner une forme cylindrique ou courbée. Ces machines sont couramment utilisées dans la fabrication de tuyaux, de cônes ou d’autres pièces nécessitant une forme arrondie, comme des éléments de toiture, des réservoirs ou des structures métalliques.
5. Machines de profilage
Les machines de profilage sont utilisées pour produire des pièces métalliques à partir de tôles plates, en leur donnant des formes profilées spécifiques, comme des tôles ondulées, des canaux ou des poutres. Ces machines travaillent en faisant passer la tôle à travers une série de rouleaux qui la façonnent progressivement. Le profilage est particulièrement utilisé dans la production de matériaux de construction, de panneaux de toiture, ou de structures en acier.
6. Machines à emboutir rotatives
Les machines à emboutir rotatives sont une forme avancée de presse à emboutir qui permet de réaliser des pièces en tôle en effectuant un emboutissage sous rotation. Ce procédé est utilisé pour la production de pièces complexes à grande vitesse, comme des composants automobiles. L’avantage de la machine rotative est qu’elle peut traiter des grandes quantités de pièces rapidement, tout en offrant une précision élevée.
7. Machines à étirer la tôle
Les machines à étirer la tôle sont utilisées pour effectuer un étirement de la tôle métallique, ce qui modifie sa forme et son épaisseur sans la casser. Ce procédé est particulièrement utile pour produire des pièces minces et uniformes, telles que des parois de boîtiers ou des composants de carrosserie automobile. L’étirement est généralement réalisé en appliquant une force de traction sur la tôle, souvent dans des environnements contrôlés pour éviter la déformation excessive ou la rupture du matériau.
8. Machines de formage à chaud
Le formage à chaud est un procédé dans lequel la tôle métallique est chauffée à une température élevée avant d’être formée. Cette chaleur réduit la résistance du matériau, ce qui permet une déformation plus facile et plus contrôlée. Les machines de formage à chaud sont utilisées pour des matériaux plus épais ou des pièces qui nécessitent une forme plus complexe. Ce procédé est souvent utilisé dans l’industrie automobile pour la fabrication de pièces comme des pare-chocs ou des éléments de châssis.
9. Machines de découpe et de formage combinées
Certaines machines combinent à la fois des opérations de découpe et de formage. Ces machines permettent de découper une tôle à une forme spécifique, puis de la transformer plastiquement pour créer la pièce finale. Elles sont particulièrement utiles dans les applications où la production de pièces de forme complexe nécessite à la fois une découpe et un formage. Ces machines peuvent être équipées de plusieurs outils interchangeables pour effectuer une gamme variée d’opérations sur une même pièce.
10. Soudage et assemblage plastique
Le soudage plastique dans la transformation de tôle peut également être intégré aux machines de formage pour assembler des pièces métalliques après leur transformation. Par exemple, dans la fabrication de pièces automobiles ou d’éléments de structure métallique, le soudage permet d’assembler des parties formées séparément. Le soudage est souvent utilisé après le formage plastique pour garantir la solidité et l’intégrité de la pièce finale.
11. Robotisation et automatisation des processus de formage
L’automatisation et la robotisation dans la transformation plastique de la tôle permettent de réduire les coûts de main-d’œuvre, d’augmenter la précision et d’améliorer la répétabilité des opérations de formage. Les robots industriels sont utilisés pour manipuler des tôles métalliques, réaliser des soudures ou des tâches de formage, et même pour assurer la finition des pièces. Cette automatisation est couramment utilisée dans les environnements de production à grande échelle, où la rapidité et la précision sont essentielles.
En résumé, les machines utilisées pour la transformation plastique de la tôle couvrent une large gamme de technologies, adaptées à des applications variées allant de la production en série de pièces complexes à la fabrication de composants de grande taille. Chaque machine et chaque procédé présente des avantages spécifiques en termes de flexibilité, de précision, de coûts et de volume de production, et peut être choisi en fonction des exigences du projet. Ces technologies de formage plastique permettent une grande variété de produits finis, allant des petites pièces fines aux grandes structures métalliques.
Les machines pour la transformation plastique de la tôle sont un élément clé de l’industrie de la fabrication, permettant de produire une variété de pièces métalliques destinées à des applications spécifiques. Ces machines utilisent des procédés mécaniques, thermiques et combinés pour déformer plastiquement les tôles métalliques, modifiant ainsi leur forme sans les casser. Elles permettent de réaliser des pièces complexes avec une grande précision, et peuvent être utilisées dans de nombreux secteurs tels que l’automobile, l’aéronautique, la construction, l’électroménager, et bien d’autres.
Les presses à emboutir, par exemple, sont couramment utilisées pour produire des formes tridimensionnelles complexes. Elles fonctionnent en appliquant une pression sur la tôle entre un poinçon et une matrice, provoquant une déformation plastique du métal. Ces machines peuvent être hydrauliques ou mécaniques, et leur capacité à traiter des tôles fines ou épaisses en fait un choix privilégié pour des applications de grande série. Elles sont capables de réaliser des pièces avec des détails fins et des tolérances strictes, ce qui est essentiel pour des secteurs comme l’automobile ou l’électronique, où la qualité des pièces est cruciale.
Les plieuses, de leur côté, sont utilisées pour créer des angles et des courbes sur les tôles métalliques. Elles exercent une pression sur la tôle entre deux outils, la matrice et le poinçon, ce qui permet de plier la tôle de manière contrôlée. L’utilisation de plieuses CNC permet une plus grande précision dans la production de pièces complexes, ce qui est particulièrement utile pour la fabrication de panneaux, de boîtiers ou de structures métalliques. Ces machines permettent également de réaliser des plis très serrés sans compromettre la qualité du matériau, ce qui est important pour des applications où l’esthétique et la fonctionnalité doivent être optimisées.
Le formage par traction, ou emboutissage profond, est un autre procédé utilisé pour produire des pièces à partir de tôles métalliques. Ce procédé consiste à appliquer une force de traction sur la tôle pour l’étirer dans une cavité, créant ainsi des formes complexes et profondes. Il est utilisé pour la production de pièces comme des coques, des cuves ou des éléments de carrosserie automobile. Les machines de formage par traction sont souvent équipées de contrôles de force sophistiqués et de systèmes de lubrification pour garantir la qualité de la pièce tout en réduisant l’usure des outils.
Les rouleuses à tôle sont utilisées pour donner des formes cylindriques ou courbes aux tôles. Elles fonctionnent en faisant passer la tôle entre plusieurs rouleaux ajustables, permettant de produire des éléments comme des tuyaux, des réservoirs, des cônes ou des éléments de toiture. Ce procédé est particulièrement utile dans l’industrie de la construction, où des formes complexes sont souvent nécessaires. La flexibilité des rouleuses à tôle permet de traiter une large gamme de matériaux et d’épaisseurs de tôles, offrant ainsi une solution polyvalente pour la fabrication de structures métalliques de différentes tailles.
Les machines de profilage sont utilisées pour produire des formes spécifiques en passant la tôle à travers une série de rouleaux qui modifient progressivement sa forme. Ce procédé est idéal pour la production de pièces comme des tôles ondulées, des poutres ou des profilés utilisés dans la construction ou la fabrication de structures métalliques. Les machines de profilage sont capables de produire des pièces à grande vitesse, ce qui les rend particulièrement efficaces pour les lignes de production en continu.
Le formage à chaud est une autre technologie importante dans la transformation plastique de la tôle. Dans ce procédé, la tôle est chauffée à une température élevée avant d’être formée. La chaleur réduit la résistance du métal et facilite sa déformation, ce qui est particulièrement utile pour les matériaux plus épais ou les formes complexes. Les machines de formage à chaud sont souvent utilisées dans l’industrie automobile pour produire des pièces de carrosserie ou de châssis, où des matériaux épais doivent être façonnés avec une grande précision.
Les machines combinées de découpe et de formage permettent de réaliser des opérations multiples sur une même pièce, ce qui est particulièrement utile pour les productions de séries limitées ou personnalisées. Ces machines permettent de découper une tôle à une forme spécifique, puis de la transformer plastiquement pour obtenir la forme finale. Elles sont souvent équipées de différents outils interchangeables pour réaliser une variété d’opérations sur une même pièce.
Dans de nombreux cas, des machines de robotisation et d’automatisation sont intégrées dans les lignes de production pour augmenter l’efficacité, la précision et la flexibilité. Les robots industriels peuvent effectuer des tâches telles que le soudage, la manipulation des pièces, et même le formage ou l’assemblage des pièces. Cette automatisation permet de réduire les coûts de main-d’œuvre, d’améliorer la sécurité en réduisant l’exposition des opérateurs à des tâches dangereuses, et d’augmenter la rapidité des processus de production.
Le soudage joue également un rôle clé dans l’assemblage des pièces formées. Après le formage plastique, les pièces peuvent être assemblées par soudage, ce qui garantit la solidité et l’intégrité structurelle de l’ensemble. Les robots de soudage sont de plus en plus utilisés pour réaliser des soudures de haute précision sur les pièces en tôle formées, notamment dans les secteurs automobile et aéronautique, où des tolérances strictes sont essentielles pour garantir la sécurité et la performance des produits finis.
Les machines de traitement de surface sont également utilisées dans la transformation plastique de la tôle pour améliorer les propriétés des pièces finies. Ces machines permettent de traiter la surface de la tôle pour augmenter sa résistance à la corrosion, améliorer son apparence esthétique, ou préparer la surface pour une meilleure adhérence des peintures et des revêtements. Les machines de galvanisation, les sablanes et les polisseuses sont couramment utilisées pour ces traitements.
Les progrès technologiques dans l’industrie 4.0 permettent aux machines de transformation plastique de la tôle d’être de plus en plus intelligentes et interconnectées. Grâce à des systèmes cyber-physiques, ces machines peuvent collecter et analyser des données en temps réel, ce qui permet d’optimiser les paramètres de production, de prévoir les défaillances et de maintenir la qualité tout au long de la production. L’intégration de capteurs intelligents et de logiciels d’analyse avancée permet également d’ajuster les paramètres de production pour maximiser l’efficacité énergétique et réduire les déchets.
En résumé, les machines pour la transformation plastique de la tôle couvrent un large éventail de technologies qui permettent de produire une variété de pièces métalliques pour des applications diverses. Ces machines sont utilisées pour des procédés tels que le formage, le découpage, l’emboutissage, le profilage, et bien d’autres, et elles sont équipées de technologies modernes qui améliorent la précision, la flexibilité, l’efficacité et la durabilité des opérations de fabrication.
Les machines pour la transformation plastique de la tôle, en plus de leur capacité à fabriquer des pièces complexes et de grande précision, offrent aussi des avantages considérables en termes de réduction des coûts et d’amélioration de la productivité. En particulier, l’automatisation des processus permet une gestion plus efficace des ressources, un meilleur contrôle de la qualité et une réduction significative des erreurs humaines. L’intégration des technologies de l’industrie 4.0, telles que l’Internet des objets (IoT) et l’intelligence artificielle (IA), joue un rôle clé dans l’optimisation de la production. Ces technologies permettent une surveillance en temps réel des machines et des processus de production, facilitent la maintenance prédictive et assurent des ajustements instantanés des paramètres pour maximiser la rentabilité et la qualité des produits finis.
Les systèmes d’automatisation avancés permettent aussi de réduire les délais de fabrication. Par exemple, les robots de manutention peuvent déplacer les tôles métalliques entre les différentes étapes de production, de l’alimentation en matière première à l’assemblage final, tout en minimisant les risques de dommages ou d’erreurs. Cela augmente non seulement la sécurité des opérateurs, mais aussi la rapidité des cycles de production, ce qui est essentiel dans des secteurs où les demandes sont élevées et où les délais sont serrés.
Les machines modernes de transformation plastique de la tôle sont également conçues pour être flexibles et capables de traiter différents types de matériaux, y compris des alliages métalliques spécialisés, des tôles fines ou épaisses, et des matériaux de différentes épaisseurs et duretés. Cela permet aux fabricants d’adapter leurs lignes de production à une large gamme de produits tout en conservant une haute précision et des coûts de production compétitifs. De plus, les machines récentes sont capables de s’adapter à des séries de production variables, ce qui est particulièrement avantageux pour les entreprises qui doivent jongler entre des séries de grande échelle et des productions sur mesure.
L’un des développements majeurs dans ce domaine est l’introduction des machines à commande numérique (CNC). Ces machines sont capables de réaliser des opérations de formage très précises avec des tolérances extrêmement serrées, ce qui est essentiel dans des secteurs comme l’aéronautique ou l’électronique, où des ajustements fins sont souvent nécessaires. Les machines CNC permettent également une plus grande flexibilité de conception, car les paramètres de production peuvent être facilement modifiés pour réaliser différentes pièces sans nécessiter de changements majeurs dans les outils ou l’équipement.
L’un des défis actuels dans la transformation plastique de la tôle est la gestion des déchets et de l’efficacité énergétique. Les machines modernes intègrent de plus en plus des technologies écologiques, comme des systèmes de recyclage des copeaux métalliques ou des systèmes de filtration des gaz et poussières. Les procédés comme la découpe au laser, l’emboutissage ou la plieuse peuvent générer des déchets, mais de nombreuses machines actuelles sont conçues pour minimiser ces pertes et optimiser l’utilisation des matériaux. Par exemple, des systèmes de découpe au laser peuvent offrir une précision accrue tout en réduisant les chutes de matériau et, par conséquent, les coûts de production.
Les machines de formage de tôle sont également de plus en plus intelligentes, avec des capteurs qui mesurent en temps réel les contraintes et déformations du métal pendant le processus. Ces informations sont ensuite utilisées pour ajuster les paramètres de la machine, garantissant que la qualité du produit final respecte les exigences strictes des clients. Les capteurs de température, de force et de position aident à contrôler chaque étape du processus, évitant ainsi les erreurs humaines et réduisant les risques de pièces défectueuses.
Un autre développement intéressant dans ce domaine est l’intégration de la simulation numérique dans le processus de conception des pièces en tôle. Avant même que la production ne commence, les ingénieurs peuvent utiliser des logiciels de simulation pour prédire comment une pièce se comportera pendant le processus de formage. Cela permet de prévoir les éventuels défauts, comme la fissuration, la déformation ou le gauchissement, et d’optimiser la conception des matrices et des outils avant même le lancement de la production. Cette approche préventive permet de réduire le nombre de prototypes physiques, d’optimiser les ressources et de garantir une meilleure efficacité dans la production en série.
L’évolution vers l’industrie 4.0 dans le secteur du formage de tôle permet également un meilleur suivi des performances des machines. Des systèmes d’analyse de données avancées peuvent être utilisés pour recueillir des informations détaillées sur la consommation énergétique, les cycles de production, et même les tendances de panne ou de dégradation des équipements. Ces informations peuvent être utilisées pour programmer des interventions de maintenance avant que des problèmes majeurs ne surviennent, ce qui réduit les arrêts de production imprévus et améliore la rentabilité.
Enfin, les fabricants de machines pour la transformation plastique de la tôle continuent de chercher des solutions innovantes pour répondre aux besoins du marché, y compris des systèmes plus modulaires qui peuvent être facilement adaptés à différents types de produits et de processus. Les machines à usages multiples, qui peuvent alterner entre plusieurs procédés de formage ou qui permettent de réaliser plusieurs étapes de transformation dans une seule opération, sont de plus en plus populaires. Cela permet aux fabricants d’optimiser leur espace de production, de réduire les coûts d’investissement en équipements multiples, et d’améliorer la flexibilité de leurs lignes de production.
En résumé, les machines de transformation plastique de la tôle continuent d’évoluer avec l’introduction de technologies de pointe qui améliorent la productivité, la précision, et la durabilité des produits. Grâce à l’automatisation, la robotisation, la simulation numérique et les avancées dans le domaine de l’analyse des données, ces machines sont devenues des instruments essentiels pour les industries modernes.
Cellules de formage de tôle

Les cellules de formage de tôle sont des systèmes automatisés ou semi-automatisés utilisés pour effectuer des processus de transformation de tôles métalliques. Ces cellules sont généralement composées de plusieurs machines et équipements interconnectés, permettant de réaliser différentes étapes de formage de la tôle dans un environnement intégré et contrôlé. Elles sont conçues pour améliorer l’efficacité, réduire les coûts de production et garantir une qualité constante des pièces fabriquées.
Les cellules de formage de tôle sont couramment utilisées dans des industries comme l’automobile, l’aéronautique, la construction métallique, l’électroménager et d’autres secteurs où la production de pièces en métal est essentielle. Elles permettent une automatisation complète ou partielle du processus de transformation des tôles, en passant par des étapes comme la découpe, le formage, le pliage, l’assemblage et même le contrôle de qualité.
1. Composition d’une cellule de formage de tôle
Une cellule de formage de tôle se compose généralement de plusieurs équipements qui travaillent ensemble pour transformer la tôle métallique. Les principales machines que l’on retrouve dans ces cellules sont :
- Machines de découpe : Les tôles sont d’abord découpées selon les dimensions souhaitées avant d’être envoyées vers les autres machines pour leur transformation. Les découpes peuvent être réalisées par des machines de découpe laser, de découpe à jet d’eau, de découpe par poinçon ou de découpe par cisaillement, selon les exigences de production.
- Presses à emboutir : Ces presses sont utilisées pour réaliser des formes tridimensionnelles complexes sur la tôle, en appliquant une pression sur le métal avec un poinçon et une matrice. Elles sont essentielles pour fabriquer des pièces complexes comme des composants de carrosserie automobile, des boîtiers électroniques ou des éléments de mobilier métallique.
- Plieuses : Les machines à plier, souvent intégrées dans les cellules de formage, permettent de plier les tôles pour leur donner une forme spécifique, comme des angles droits ou des courbes.
- Machines de formage par traction ou emboutissage profond : Elles sont utilisées pour transformer la tôle en forme de pièces profondes, telles que des coques ou des réservoirs. Ces machines permettent de créer des formes complexes qui nécessitent une déformation plastique du métal.
- Systèmes de soudage et d’assemblage : Parfois, des étapes de soudage sont nécessaires pour assembler les pièces formées ou pour réaliser des structures complexes. Les robots de soudage et d’assemblage peuvent être intégrés à la cellule pour garantir une précision et une efficacité optimales.
2. Caractéristiques des cellules de formage de tôle
- Automatisation : L’automatisation est un élément clé des cellules de formage modernes. Les machines sont souvent équipées de robots industriels et de systèmes de contrôle numériques qui assurent le transport automatique des tôles entre les différentes étapes du processus. Cela permet de réduire les erreurs humaines et d’augmenter la vitesse et la constance de la production.
- Flexibilité : Les cellules de formage modernes sont conçues pour être flexibles. Elles peuvent être configurées pour traiter différents types de matériaux, d’épaisseurs et de formes. Certaines cellules peuvent également être modifiées pour intégrer de nouveaux procédés de formage ou pour produire de nouvelles gammes de pièces sans nécessiter un changement majeur dans l’équipement.
- Intégration de la gestion des données : De nombreuses cellules de formage de tôle modernes sont connectées à des systèmes de gestion des données de production, qui permettent de suivre en temps réel les performances des machines, les consommations d’énergie et les progrès de la production. Cela permet d’ajuster les processus pour optimiser l’efficacité, la qualité et les coûts de production.
- Réduction des temps de cycle : L’un des principaux avantages des cellules de formage est la réduction des temps de cycle. Grâce à l’automatisation et à la synchronisation des machines, les cellules permettent de réaliser plusieurs étapes de formage et de transformation en un temps réduit, ce qui augmente la productivité.
3. Avantages des cellules de formage de tôle
- Productivité accrue : L’intégration de machines automatisées et de robots dans une cellule permet de traiter un grand volume de tôles sans intervention humaine constante. Cela augmente la productivité et réduit les erreurs liées à la manipulation manuelle.
- Précision et qualité : Les cellules de formage de tôle permettent d’atteindre un haut niveau de précision, ce qui est essentiel pour des applications qui exigent des tolérances strictes, comme l’automobile et l’aéronautique. Les systèmes de contrôle et les capteurs intégrés permettent de garantir la qualité des pièces produites.
- Réduction des coûts : L’automatisation permet de réduire les coûts de main-d’œuvre tout en augmentant la vitesse de production. De plus, les cellules de formage sont conçues pour minimiser les déchets de matériau, en utilisant des techniques de découpe et de formage plus efficaces.
- Amélioration de la sécurité : En automatisant des processus potentiellement dangereux, comme le soudage ou la manipulation de tôles lourdes, les cellules de formage contribuent à améliorer la sécurité des opérateurs. Les robots et les machines à commande numérique sont souvent équipés de systèmes de sécurité avancés pour prévenir les accidents.
- Suivi et maintenance prédictive : Les cellules de formage modernes sont équipées de systèmes de surveillance en temps réel qui permettent de suivre l’état de chaque machine et de prédire les besoins de maintenance avant que des défaillances majeures ne se produisent. Cela permet de planifier les interventions de maintenance de manière proactive, réduisant ainsi les arrêts imprévus.
4. Applications des cellules de formage de tôle
Les cellules de formage de tôle sont utilisées dans de nombreuses industries, notamment :
- Automobile : La fabrication de pièces complexes, telles que des panneaux de carrosserie, des châssis, des composants de moteur et des éléments de sécurité, est un domaine clé d’application des cellules de formage. Les processus automatisés permettent une production rapide et précise de ces pièces essentielles.
- Aéronautique : Les pièces pour les avions, comme les ailes, les panneaux de fuselage et d’autres composants structuraux, nécessitent des procédés de formage très précis, ce qui rend les cellules de formage adaptées pour ce secteur.
- Construction : Les structures métalliques pour les bâtiments, les ponts et les infrastructures nécessitent souvent des tôles formées de manière spécifique, ce qui peut être réalisé efficacement dans des cellules de formage.
- Électroménager : Les fabricants d’appareils électroménagers, comme les réfrigérateurs, les lave-linge et les fours, utilisent également des cellules de formage pour fabriquer des boîtiers, des panneaux et des pièces métalliques complexes.
Conclusion
Les cellules de formage de tôle représentent une avancée importante dans le domaine de la fabrication de pièces métalliques. En intégrant des machines spécialisées et des technologies avancées d’automatisation et de contrôle, elles permettent de produire des pièces de haute qualité de manière rapide, flexible et rentable. Leur capacité à intégrer différentes étapes du processus de fabrication dans une seule unité de production fait d’elles un choix privilégié pour les industries modernes exigeant des solutions de production efficaces et à grande échelle.
Les cellules de formage de tôle sont des systèmes intégrés qui permettent de transformer des tôles métalliques de manière automatisée ou semi-automatisée. Elles combinent plusieurs machines et équipements pour réaliser différentes étapes de fabrication, telles que la découpe, le pliage, l’emboutissage, le profilage et même l’assemblage, dans un espace de production cohérent et efficace. Ces cellules sont particulièrement utilisées dans des secteurs comme l’automobile, l’aéronautique, l’électroménager, la construction et d’autres industries qui nécessitent des pièces métalliques de haute précision.
Les machines dans une cellule de formage de tôle sont souvent interconnectées et synchronisées pour effectuer des opérations successives sans intervention manuelle. Cela permet d’augmenter la productivité, de réduire les coûts de main-d’œuvre et d’améliorer la précision des pièces produites. Par exemple, une cellule peut inclure une presse à emboutir pour réaliser des formes complexes, une plieuse pour façonner des angles et des courbes, ainsi qu’un système de découpe pour ajuster la taille et la forme des tôles. Certaines cellules intègrent également des systèmes de soudage pour assembler les pièces ou de robots pour manipuler et transporter les tôles entre les différentes étapes.
L’automatisation au sein de ces cellules permet de réduire les erreurs humaines et de garantir une production constante de pièces de haute qualité. L’intégration de technologies comme l’Internet des objets (IoT) et l’intelligence artificielle (IA) permet aux machines de collecter et d’analyser des données en temps réel pour optimiser les processus de fabrication, ajuster les paramètres et prévoir la maintenance des équipements. Cette gestion intelligente aide à minimiser les déchets de matériau et les arrêts non planifiés.
Les cellules de formage de tôle peuvent être flexibles et adaptables, traitant divers types de matériaux et de formes. Les avancées en robotisation permettent également de réduire les délais de production et d’améliorer la sécurité des opérateurs en automatisant les tâches dangereuses, telles que le soudage et la manipulation de tôles lourdes. Ces cellules sont conçues pour répondre à des besoins spécifiques, qu’il s’agisse de productions de masse ou de petites séries personnalisées. Grâce à leur modularité, elles sont capables de s’ajuster à différents processus et exigences de production sans nécessiter de réajustements majeurs dans l’infrastructure.
Les avantages des cellules de formage de tôle incluent une meilleure efficacité énergétique, un meilleur contrôle de la qualité et des temps de cycle réduits. L’intégration des capteurs et des systèmes de surveillance permet de suivre l’état de chaque machine et de détecter les anomalies avant qu’elles ne deviennent des problèmes majeurs. Cela contribue à la réduction des arrêts de production et à la prolongation de la durée de vie des équipements. Les données recueillies pendant la production peuvent également être utilisées pour améliorer la conception des pièces et optimiser les processus de fabrication dans le futur.
En résumé, les cellules de formage de tôle sont un élément essentiel dans la fabrication moderne, permettant de combiner différentes technologies pour une production rapide, flexible et de haute qualité. Leur capacité à automatiser plusieurs étapes du processus et à intégrer des technologies avancées de contrôle et d’analyse fait d’elles un outil indispensable pour répondre aux exigences des industries actuelles.
Les cellules de formage de tôle, grâce à leur conception intégrée, sont capables de gérer une grande variété de processus tout en maintenant une flexibilité optimale. Elles sont adaptées à des productions de séries petites ou grandes, ce qui est essentiel pour les industries où la demande peut fluctuer rapidement. Cette flexibilité est rendue possible grâce à des systèmes de réglage automatisés qui ajustent les paramètres de production, comme la pression, la température, ou la vitesse de fabrication, en fonction des besoins spécifiques des pièces à produire.
L’une des avancées notables dans les cellules de formage est l’utilisation de robots collaboratifs (ou cobots), qui travaillent aux côtés des opérateurs humains pour effectuer des tâches de manipulation, de contrôle qualité ou d’assemblage. Ces robots augmentent non seulement la productivité mais aussi la sécurité en effectuant des tâches répétitives ou à risque, tout en réduisant la fatigue des travailleurs. Ils peuvent aussi être facilement reprogrammés ou reconfigurés pour s’adapter à de nouveaux processus, rendant ainsi les cellules plus polyvalentes.
Les systèmes de vision et les capteurs intelligents jouent également un rôle crucial dans les cellules de formage de tôle. Ils permettent de surveiller en continu les pièces pendant la production, détectant des défauts ou des imperfections dès qu’elles apparaissent. Les caméras et les capteurs laser sont utilisés pour mesurer avec précision les dimensions des pièces et ajuster en temps réel les paramètres des machines afin de garantir que chaque pièce respecte les tolérances définies. Cela assure un niveau de contrôle qualité très élevé tout en réduisant le gaspillage de matériaux, puisque seules les pièces conformes sont mises en production.
De plus, les cellules de formage de tôle modernes sont souvent intégrées dans des réseaux de production plus larges, où elles sont connectées à des systèmes de gestion de la production (MES, Manufacturing Execution System) ou à des systèmes ERP (Enterprise Resource Planning). Cette interconnexion permet un suivi en temps réel de l’ensemble de la chaîne de production, du stockage des matières premières jusqu’à la livraison des produits finis. Les données recueillies tout au long du processus peuvent être analysées pour identifier des opportunités d’amélioration continue, optimiser l’utilisation des ressources et réduire les coûts de production.
Une autre caractéristique intéressante des cellules de formage modernes est leur capacité à réduire l’impact environnemental. L’optimisation des processus de fabrication permet de diminuer la consommation d’énergie et de matières premières, tout en maximisant la recyclabilité des matériaux. Les systèmes de récupération de chaleur et de filtration des gaz d’échappement, par exemple, contribuent à réduire l’empreinte carbone de la production. De plus, la réduction des déchets et des pertes de matériau, combinée à des processus de fabrication plus précis, permet de rendre les cellules de formage plus durables sur le plan écologique.
Dans un environnement industriel où les exigences sont de plus en plus complexes et où la compétition est accrue, les cellules de formage de tôle jouent un rôle clé pour garantir la compétitivité des entreprises. Elles permettent d’offrir une qualité constante, une production rapide, et une capacité à s’adapter aux demandes variées des clients, tout en minimisant les coûts d’exploitation et les risques. Leur rôle est donc central dans l’industrie 4.0, où l’automatisation, la flexibilité et l’optimisation sont des facteurs déterminants pour le succès des fabricants.
En conclusion, les cellules de formage de tôle constituent une solution hautement efficace pour répondre aux défis modernes de la production de pièces métalliques. Grâce à leur capacité à intégrer plusieurs technologies avancées, elles permettent aux fabricants de gagner en productivité, en flexibilité et en durabilité tout en réduisant les coûts et les risques associés aux erreurs humaines. Ces systèmes représentent l’avenir de la fabrication de pièces métalliques, en offrant des solutions de plus en plus sophistiquées et écologiques dans un environnement de plus en plus exigeant.
Machines pour mise en forme de tôles métalliques

Les machines pour la mise en forme de tôles métalliques sont des équipements industriels conçus pour transformer les tôles métalliques en pièces ou composants avec des formes et des dimensions spécifiques. Ces machines permettent de réaliser une variété de procédés, allant du simple découpage à des opérations complexes telles que l’emboutissage, le pliage, ou le formage tridimensionnel. Elles jouent un rôle clé dans des secteurs industriels comme l’automobile, l’aéronautique, la construction métallique, l’électroménager, et bien d’autres.
Types de machines pour la mise en forme des tôles métalliques
- Presses à emboutir : Ces presses sont utilisées pour former des pièces métalliques en appliquant une pression sur la tôle avec un poinçon et une matrice. Ce procédé, appelé emboutissage, permet de produire des pièces de formes complexes et de tailles variées, comme des pièces de carrosserie automobile, des coques, ou des boîtiers d’appareils électroniques. L’emboutissage peut être effectué à froid ou à chaud, selon le matériau et les exigences de la pièce.
- Plieuses : Les machines de pliage, ou plieuses, sont utilisées pour réaliser des courbes ou des angles dans les tôles métalliques. Elles permettent de plier les tôles avec précision, ce qui est essentiel pour la fabrication de pièces comme des panneaux de carrosserie ou des éléments structurels. Les plieuses modernes sont souvent à commande numérique (CNC), offrant ainsi une grande précision et une flexibilité dans les angles et les dimensions de pliage.
- Cisailles et machines de découpe : Les cisailles et les machines de découpe sont utilisées pour découper les tôles métalliques en fonction de dimensions spécifiques. La découpe peut être réalisée par cisaillement, découpe laser, découpe plasma ou découpe au jet d’eau, selon les matériaux et la précision requise. Ces machines sont souvent utilisées pour produire des pièces plates ou des éléments de structure de base.
- Machines de formage à chaud : Ces machines sont utilisées pour former des tôles métalliques en les chauffant à des températures élevées avant de les façonner sous pression ou par traction. Ce procédé est utilisé pour des matériaux difficiles à former à froid ou pour obtenir des formes tridimensionnelles complexes, comme des coques ou des réservoirs. Les presses à chaud et les machines à emboutir à chaud sont des exemples typiques dans ce domaine.
- Machines de déformation par traction (emboutissage profond) : L’emboutissage profond est un processus qui consiste à tirer une tôle métallique à travers une matrice pour lui donner une forme tridimensionnelle. Ce procédé est utilisé pour produire des pièces comme des réservoirs, des coques, ou des éléments de carrosserie automobile. Les machines de formage par traction appliquent une force importante pour étirer la tôle sans la rompre.
- Machines de découpe et de formage par laser : Les machines à découpe laser permettent de découper des tôles métalliques avec une précision extrême. Elles utilisent un faisceau laser concentré pour chauffer et découper la tôle. Ce procédé est particulièrement adapté pour des formes complexes et des matériaux fins. La découpe au laser est idéale pour la production de pièces de haute précision, utilisées dans des secteurs comme l’aéronautique, l’automobile, et l’électronique.
- Machines à emboutir rotatif : Ces machines permettent de réaliser des formes cylindriques et coniques sur des tôles métalliques. Le formage rotatif est utilisé pour la fabrication de pièces comme des réservoirs, des tuyaux ou des pièces de carrosserie automobile. Ce procédé permet de traiter des matériaux plus épais que l’emboutissage traditionnel, tout en offrant une grande précision.
- Machines de redressage et de finition : Après la mise en forme des tôles, il est souvent nécessaire de redresser les pièces ou d’effectuer des opérations de finition pour éliminer les déformations ou les irrégularités. Les machines de redressage et de finition permettent d’ajuster les pièces métalliques pour qu’elles respectent les tolérances dimensionnelles et esthétiques.
Technologies associées aux machines de mise en forme de tôles
Les machines modernes de mise en forme de tôles métalliques sont souvent équipées de technologies avancées qui améliorent la précision, la flexibilité et l’efficacité de la production :
- Commande numérique (CNC) : Les machines à commande numérique permettent de contrôler les paramètres de mise en forme avec une grande précision. Les utilisateurs peuvent programmer des angles de pliage, des pressions de découpe, et d’autres paramètres, ce qui permet de produire des pièces avec une précision constante.
- Automatisation et robotisation : L’automatisation est de plus en plus courante dans les ateliers de mise en forme de tôles. Les robots peuvent manipuler les tôles entre les différentes étapes de production, réduire les risques d’erreurs humaines et augmenter la vitesse de production. L’automatisation permet également de traiter des séries plus grandes tout en conservant la flexibilité nécessaire pour des séries plus petites et personnalisées.
- Systèmes de vision et de contrôle de qualité : Les machines de mise en forme modernes intègrent souvent des systèmes de vision pour surveiller en temps réel la qualité des pièces produites. Ces systèmes détectent les défauts, mesurent les dimensions des pièces, et ajustent les paramètres des machines en fonction des résultats. Cela garantit un contrôle qualité constant tout au long du processus de production.
Avantages des machines pour la mise en forme de tôles métalliques
Les machines de mise en forme de tôles métalliques offrent plusieurs avantages :
- Précision et répétabilité : Les machines modernes sont capables de produire des pièces avec une grande précision, respectant des tolérances strictes. Cela est particulièrement important dans des secteurs comme l’aéronautique et l’automobile, où les exigences de qualité sont extrêmement élevées.
- Réduction des coûts de production : L’automatisation, la flexibilité des machines, et la réduction des erreurs humaines contribuent à réduire les coûts de production. De plus, l’utilisation efficace des matériaux, grâce à des procédés comme la découpe laser, minimise les déchets.
- Flexibilité : Les machines de mise en forme de tôles peuvent être configurées pour traiter différents types de matériaux, d’épaisseurs et de formes. Cela permet aux fabricants de répondre à des demandes variées, qu’il s’agisse de grandes séries ou de productions plus petites et personnalisées.
- Efficacité énergétique : Les machines modernes sont de plus en plus efficaces sur le plan énergétique, ce qui permet de réduire la consommation d’énergie et d’améliorer la rentabilité des processus de production.
Conclusion
Les machines pour la mise en forme des tôles métalliques sont des équipements essentiels dans de nombreux secteurs industriels. Elles permettent de transformer des tôles plates en pièces complexes, tout en garantissant une grande précision et une productivité élevée. Les avancées technologiques, telles que l’automatisation, la commande numérique et l’intégration de systèmes de contrôle qualité, continuent de rendre ces machines plus efficaces, flexibles et adaptées aux exigences modernes de production.
Les machines pour la mise en forme des tôles métalliques jouent un rôle fondamental dans la fabrication moderne en permettant la production de pièces métalliques complexes avec une grande précision et à des coûts optimisés. La diversité des machines, allant des presses à emboutir aux machines de découpe laser, permet de traiter une large gamme de matériaux et d’applications. Ces machines sont souvent intégrées dans des processus automatisés et interconnectés pour maximiser l’efficacité de la production tout en maintenant une qualité constante.
L’automatisation des lignes de production, avec l’intégration de robots et de systèmes de contrôle numérique, permet non seulement de réduire les erreurs humaines, mais aussi d’améliorer la rapidité des cycles de production. En utilisant des technologies comme la commande numérique (CNC), les entreprises peuvent programmer des opérations complexes pour fabriquer des pièces avec des tolérances strictes, réduisant ainsi les erreurs et les coûts de retouche. Les systèmes de vision et de contrôle qualité intégrés permettent un suivi en temps réel de la production, garantissant ainsi que chaque pièce produite respecte les standards de qualité définis. Cela est particulièrement important dans des industries telles que l’automobile et l’aéronautique, où des exigences rigoureuses en matière de précision et de performance sont indispensables.
L’un des avantages clés des machines modernes pour la mise en forme de tôles métalliques est leur capacité à produire une grande variété de pièces, qu’il s’agisse de petites séries personnalisées ou de grandes productions en série. Cela donne aux entreprises la flexibilité nécessaire pour répondre aux besoins du marché tout en maintenant une productivité élevée. Par exemple, une cellule de fabrication automatisée peut gérer une production continue de pièces métalliques tout en permettant des ajustements rapides en fonction des spécifications de production.
De plus, les machines de mise en forme modernes sont conçues pour minimiser les déchets et maximiser l’utilisation des matériaux. Des procédés comme la découpe au laser permettent de découper des tôles avec une précision extrême, réduisant ainsi les pertes matérielles. Cela contribue non seulement à la réduction des coûts mais aussi à une production plus durable sur le plan environnemental. Les progrès en matière de recyclage des matériaux et d’efficacité énergétique rendent les machines de mise en forme de tôles plus écologiques, tout en contribuant à une meilleure rentabilité des entreprises.
Dans le cadre de l’industrie 4.0, l’intégration des technologies IoT (Internet des objets) et de l’intelligence artificielle permet d’aller encore plus loin dans l’optimisation des processus de fabrication. Ces technologies permettent de collecter et d’analyser des données en temps réel pour ajuster les processus de production, prévoir les besoins en maintenance, et détecter les anomalies avant qu’elles n’affectent la qualité ou la productivité. L’analyse des données recueillies durant la production offre une vue d’ensemble permettant d’identifier les zones d’amélioration et de prendre des décisions informées pour optimiser les opérations.
Les machines de mise en forme des tôles ne sont plus seulement des outils de fabrication, mais des éléments intégrés à un écosystème de production avancé, où chaque étape de la production est connectée et optimisée. Elles offrent aux fabricants une combinaison de précision, de flexibilité, d’automatisation et de réduction des coûts qui leur permet de rester compétitifs dans un marché mondial de plus en plus exigeant. Par conséquent, ces machines deviennent de plus en plus sophistiquées, capables de s’adapter aux évolutions des besoins du marché et des technologies, et de répondre aux défis contemporains en matière de production de pièces métalliques.
Les machines de mise en forme de tôles métalliques sont au cœur de l’évolution industrielle, avec une tendance croissante vers l’automatisation, la précision et l’efficacité énergétique. Elles permettent de réaliser une large gamme d’opérations sur les tôles, allant de la découpe à des formes complexes jusqu’à des processus de finition sophistiqués. L’innovation continue dans le domaine des matériaux et des technologies de fabrication permet d’offrir des solutions encore plus flexibles et performantes pour répondre aux besoins variés des industries modernes.
L’un des aspects les plus marquants de cette évolution est l’introduction de technologies hybrides qui combinent plusieurs procédés de fabrication dans une seule machine. Par exemple, des machines combinant découpe au laser et formage, ou encore découpe plasma et emboutissage, permettent de rationaliser la chaîne de production, d’économiser de l’espace et de réduire les coûts d’investissement. Ces systèmes hybrides optimisent le temps de cycle tout en offrant une qualité constante, car chaque procédé peut être ajusté pour s’assurer que la pièce finie respecte les spécifications.
Les machines à commande numérique (CNC), qui étaient autrefois limitées aux grandes productions en série, deviennent de plus en plus courantes dans les environnements de production plus petites ou personnalisées. Cela permet de répondre aux besoins de clients exigeant des produits spécifiques tout en maintenant un haut niveau de qualité. Les machines CNC permettent non seulement de piloter des processus de formage complexes, mais aussi de gérer plusieurs étapes de fabrication dans une séquence entièrement automatisée, réduisant ainsi les coûts de main-d’œuvre et minimisant les erreurs humaines.
En parallèle, la robotisation continue de transformer la production de tôles métalliques. Les robots peuvent prendre en charge des tâches telles que le chargement et déchargement des tôles, la manipulation des pièces après leur découpe ou formage, et même l’assemblage des composants. L’intégration de robots collaboratifs (cobots) permet aux opérateurs humains de travailler en synergie avec les machines, augmentant ainsi la productivité sans compromettre la sécurité. Cela permet également d’automatiser des processus dans des environnements où la flexibilité et la personnalisation sont cruciales.
L’aspect durabilité est de plus en plus au centre des préoccupations des fabricants. La réduction de l’empreinte écologique des processus de fabrication devient essentielle, tant pour des raisons économiques qu’écologiques. Les machines modernes permettent de réduire le gaspillage de matériaux, d’optimiser la consommation d’énergie, et de gérer efficacement les déchets produits. Les technologies comme les systèmes de récupération de chaleur et l’optimisation énergétique des machines sont intégrées pour réduire l’impact environnemental de la production. Par ailleurs, les matériaux utilisés dans le formage des tôles, comme les alliages métalliques plus légers et résistants, permettent de produire des pièces avec une consommation réduite de ressources, tout en maintenant des propriétés de performance élevées.
Les logiciels de simulation et de conception jouent un rôle clé dans l’amélioration des processus de formage de tôles. Avant même de lancer la production, les concepteurs peuvent simuler le comportement des matériaux sous différentes contraintes pour prédire le résultat du formage, et ainsi optimiser les paramètres de la machine. Cela permet de réduire les essais et erreurs sur le terrain, minimisant ainsi les coûts et les retards de production. Ces logiciels permettent également de concevoir des pièces plus complexes tout en garantissant qu’elles respectent les exigences techniques et esthétiques tout au long du processus de fabrication.
Un autre aspect crucial est l’amélioration continue et l’optimisation des processus de maintenance. Les systèmes de maintenance prédictive, qui utilisent des capteurs et des données en temps réel pour surveiller l’état des machines, deviennent de plus en plus courants. Ces systèmes peuvent prédire les défaillances avant qu’elles ne se produisent, réduisant ainsi les temps d’arrêt non planifiés et les coûts associés à la maintenance réactive. Cela garantit que les machines fonctionnent toujours à leur niveau optimal et permet de maximiser la durée de vie des équipements.
En somme, les machines pour la mise en forme des tôles métalliques sont un élément fondamental de l’industrie moderne, combinant efficacité, flexibilité et technologies avancées pour répondre aux exigences de la fabrication contemporaine. Leur évolution continue, alimentée par l’automatisation, la robotisation, l’analyse des données et l’optimisation énergétique, garantit non seulement une amélioration de la qualité et de la productivité, mais aussi une réduction des coûts et de l’impact environnemental. Ces machines jouent ainsi un rôle clé dans l’avenir de la fabrication, en permettant aux industries de s’adapter aux défis futurs tout en restant compétitives et durables.
Systèmes industriels de mise en forme de tôle
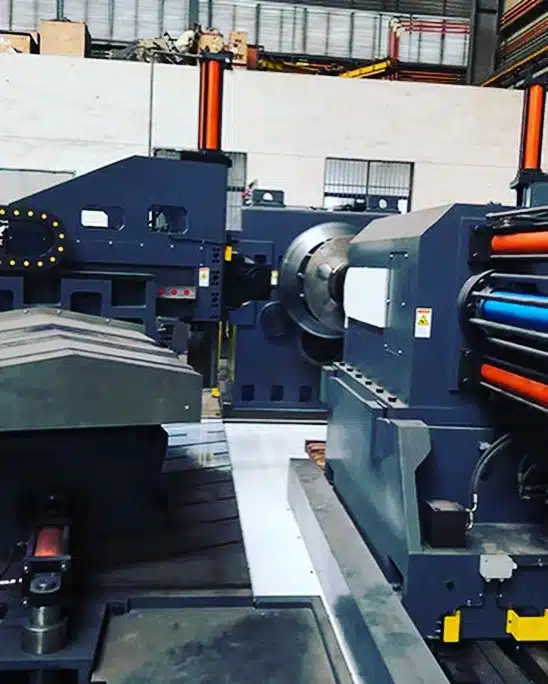
Les systèmes industriels de mise en forme de tôle désignent un ensemble de technologies, de machines et d’équipements utilisés pour transformer des tôles métalliques en pièces spécifiques par des procédés de formage. Ces systèmes intègrent souvent plusieurs étapes de fabrication, allant de la découpe à l’emboutissage, en passant par le pliage, le redressage et la finition. L’objectif est de produire des composants métalliques avec une précision élevée et une efficacité optimisée, tout en réduisant les coûts et les temps de production.
Intégration des systèmes industriels
Les systèmes industriels de mise en forme de tôle sont généralement conçus pour maximiser la flexibilité et l’efficacité. Pour ce faire, ils intègrent souvent des technologies avancées comme la commande numérique (CNC), l’automatisation robotique, et les systèmes de contrôle qualité en temps réel. Voici un aperçu des principaux éléments qui composent ces systèmes :
- Machines de formage : Les systèmes de mise en forme comprennent une gamme de machines spécifiques qui permettent d’appliquer différentes forces mécaniques aux tôles métalliques pour les transformer en pièces. Ces machines incluent des presses à emboutir, des plieuses, des cisailles, et des équipements de formage à chaud. Elles peuvent fonctionner individuellement ou être intégrées dans des lignes de production automatisées. Les machines de formage utilisent souvent des matrices et des poinçons pour créer des pièces aux formes spécifiques, comme des boîtiers ou des éléments de carrosserie automobile.
- Systèmes de commande numérique (CNC) : La commande numérique est l’une des pierres angulaires des systèmes modernes de mise en forme de tôle. Elle permet une grande précision dans le contrôle des mouvements des machines, ce qui permet de produire des pièces de haute qualité tout en réduisant les erreurs humaines. La CNC est utilisée pour gérer les réglages des machines de formage, en ajustant les paramètres tels que la pression, la température ou la vitesse de travail pour correspondre aux exigences de chaque pièce.
- Automatisation et robotisation : L’intégration de robots et d’automatisation est essentielle pour améliorer l’efficacité et la sécurité dans les systèmes industriels de mise en forme de tôle. Les robots peuvent être utilisés pour charger et décharger les tôles, manipuler les pièces formées, ou réaliser des tâches de montage. Cela permet de réduire les risques d’accidents et de faciliter le travail sur des opérations répétitives. Les systèmes automatisés peuvent être reprogrammés rapidement pour traiter différentes tailles et types de pièces, ce qui est crucial pour la flexibilité de la production.
- Systèmes de vision et de contrôle qualité : Les systèmes de vision et les capteurs jouent un rôle central dans l’inspection et la surveillance de la qualité dans les systèmes industriels de mise en forme. Des caméras et des capteurs laser sont souvent utilisés pour mesurer les dimensions des pièces et détecter toute imperfection ou défaut. Ces données sont analysées en temps réel, ce qui permet d’ajuster immédiatement les paramètres de la machine pour garantir que chaque pièce produite respecte les spécifications.
- Intégration dans des lignes de production : Les systèmes de mise en forme de tôle sont souvent intégrés dans des lignes de production automatisées et interconnectées, où différentes étapes du processus de fabrication sont synchronisées. Cela permet de créer des processus de production continus, où les pièces passent d’une machine à l’autre sans interruption, et où les temps d’arrêt sont minimisés. Ces lignes de production sont souvent contrôlées par des systèmes de gestion de la production (MES), qui supervisent l’ensemble du processus, du traitement des matériaux à l’assemblage des pièces.
- Maintenance prédictive et gestion des ressources : L’une des caractéristiques des systèmes industriels modernes est la maintenance prédictive, rendue possible par l’intégration de capteurs IoT et de l’analyse de données. Ces systèmes permettent de suivre en temps réel l’état des machines, de prédire les pannes avant qu’elles ne surviennent, et ainsi d’éviter des interruptions coûteuses. Par ailleurs, la gestion des ressources, comme les matériaux et l’énergie, est optimisée pour réduire les coûts de production et limiter l’impact environnemental.
Avantages des systèmes industriels de mise en forme de tôle
L’intégration de ces systèmes dans les processus de fabrication présente plusieurs avantages significatifs pour les industries :
- Précision et qualité constante : Grâce aux technologies de commande numérique et de contrôle en temps réel, les systèmes de mise en forme de tôle garantissent une qualité constante et une grande précision, même lors de la production de pièces complexes.
- Réduction des coûts de production : L’automatisation et l’intégration des processus permettent d’augmenter la productivité et de réduire les erreurs humaines, ce qui contribue à réduire les coûts de production. De plus, l’optimisation de la consommation d’énergie et de matériaux contribue également à la réduction des coûts.
- Flexibilité : Les systèmes modernes de mise en forme de tôle sont capables de s’adapter à une variété de tailles de production et de types de matériaux. Cela permet aux entreprises de répondre rapidement aux exigences changeantes du marché, qu’il s’agisse de petites séries ou de grandes productions.
- Efficacité énergétique et durabilité : Les machines modernes sont conçues pour être plus efficaces énergétiquement. De plus, elles intègrent souvent des procédés de recyclage des matériaux et des systèmes de gestion des déchets qui permettent de minimiser l’impact environnemental de la production.
- Sécurité améliorée : L’automatisation et la robotisation réduisent l’exposition des opérateurs aux risques physiques, en particulier lors de tâches répétitives ou dangereuses, contribuant ainsi à un environnement de travail plus sûr.
Tendances et innovations
L’innovation dans les systèmes industriels de mise en forme de tôle est en constante évolution. Parmi les tendances récentes, on trouve :
- Fabrication additive (impression 3D) : Bien que l’impression 3D de métal ne soit pas encore couramment utilisée pour la mise en forme de tôles, elle offre un potentiel énorme pour la production de pièces métalliques complexes avec des géométries impossibles à réaliser avec des méthodes traditionnelles. Cela pourrait transformer certaines étapes du processus de fabrication.
- Analyse avancée des données : L’intégration de l’intelligence artificielle et de l’apprentissage automatique dans les systèmes de contrôle permet une optimisation continue des processus, notamment pour la prédiction des défauts, l’ajustement automatique des machines et l’amélioration des performances globales.
- Personnalisation de masse : Les systèmes de mise en forme de tôle deviennent de plus en plus capables de gérer des commandes de petite série tout en maintenant une haute efficacité. La personnalisation de masse, qui permet de produire des pièces sur mesure tout en maintenant des coûts similaires à ceux des grandes séries, devient un facteur clé pour les fabricants modernes.
En conclusion, les systèmes industriels de mise en forme de tôle représentent la convergence de plusieurs technologies avancées, allant de la robotisation à la commande numérique, en passant par les systèmes de contrôle qualité. Leur intégration dans les chaînes de production permet aux entreprises de produire des pièces métalliques de haute qualité, avec une grande flexibilité et une efficacité accrue, tout en réduisant les coûts et l’impact environnemental. Ces systèmes évoluent rapidement et continueront de jouer un rôle crucial dans la fabrication de demain.
Les systèmes industriels de mise en forme de tôle ont connu une évolution majeure ces dernières années, devenant des éléments essentiels pour les industries modernes. L’intégration de nouvelles technologies a permis d’améliorer la productivité, la flexibilité et la précision des processus de fabrication. Les machines utilisées dans ces systèmes sont désormais plus intelligentes, avec des capacités d’automatisation poussées et une gestion avancée des ressources, ce qui permet aux entreprises de répondre aux demandes complexes et diversifiées du marché.
L’un des principaux avantages de ces systèmes est la capacité d’optimiser le processus de production à chaque étape. Grâce à l’intégration de systèmes de contrôle en temps réel, les machines peuvent ajuster instantanément les paramètres pour s’adapter aux variations du matériau, aux tolérances de production et aux conditions environnementales. Cette adaptabilité permet non seulement d’assurer une qualité constante mais aussi d’éviter les erreurs et les défauts qui peuvent survenir pendant le processus de formage. De plus, la réduction des déchets et des pertes de matériaux est un autre aspect clé, car les systèmes modernes permettent de maximiser l’utilisation des tôles tout en minimisant l’empreinte écologique.
Le contrôle de la qualité en temps réel, avec l’aide de systèmes de vision avancés et de capteurs intelligents, est une autre caractéristique marquante des systèmes industriels modernes. Ces technologies permettent une inspection continue et une détection immédiate des anomalies, permettant des ajustements avant même que les pièces ne soient jugées non conformes. En conséquence, les temps d’arrêt sont réduits, et la productivité générale est maximisée, car il n’est plus nécessaire de repasser par un processus de validation manuelle des pièces après leur production. Les machines de mise en forme sont donc capables de fonctionner de manière plus autonome, tout en maintenant des standards de qualité stricts.
L’intégration de la robotique et de l’automatisation dans ces systèmes permet de transformer radicalement les lignes de production. Non seulement cela améliore la sécurité en réduisant l’interaction humaine avec les machines, mais cela augmente également la flexibilité des processus de fabrication. Les robots peuvent accomplir des tâches telles que le chargement et le déchargement des tôles, la manipulation des pièces finies, et même l’assemblage de composants, le tout sans interruption. De plus, ces robots collaboratifs (cobots) peuvent travailler en harmonie avec les opérateurs humains, augmentant ainsi l’efficacité sans compromettre la sécurité ni la qualité. Ces évolutions rendent la production plus fluide, plus rapide, et plus rentable, en particulier dans des environnements où la demande de flexibilité et de personnalisation est élevée.
Les systèmes de mise en forme de tôle sont aussi devenus plus intelligents avec l’utilisation des données massives (big data) et de l’intelligence artificielle. L’analyse en temps réel des données recueillies tout au long de la production permet aux entreprises de prendre des décisions plus éclairées et de réagir plus rapidement aux fluctuations du marché ou aux défis imprévus. Par exemple, l’intelligence artificielle peut être utilisée pour prédire les défaillances des machines avant qu’elles ne se produisent, permettant ainsi une maintenance préventive plutôt que réactive. Cela permet de réduire les temps d’arrêt imprévus et d’augmenter la durée de vie des équipements.
Les technologies d’impression 3D métallique sont une autre évolution qui pourrait avoir un impact significatif sur les systèmes industriels de mise en forme de tôle. Bien que cette technologie ne remplace pas encore complètement les méthodes traditionnelles de formage, elle offre de nouvelles possibilités pour la fabrication de pièces complexes qui seraient autrement difficiles ou impossibles à produire avec des techniques de formage classiques. La combinaison des processus traditionnels et des technologies d’impression 3D pourrait révolutionner certains secteurs, en particulier dans des industries comme l’aéronautique et l’automobile, où des pièces à géométrie complexe sont de plus en plus demandées.
Enfin, le passage à des solutions de fabrication plus écologiques et durables devient une priorité pour de nombreuses entreprises. Les systèmes de mise en forme de tôle modernes incluent souvent des solutions pour réduire la consommation d’énergie et améliorer l’efficacité énergétique des machines. Par exemple, les machines à faible consommation d’énergie, les récupérateurs de chaleur et les processus de recyclage des matériaux sont devenus des standards dans les environnements de production modernes. Cette tendance à une fabrication plus responsable et à la réduction de l’impact environnemental est également encouragée par les régulations de plus en plus strictes dans le monde entier.
En conclusion, les systèmes industriels de mise en forme de tôle ont évolué pour devenir des solutions de production extrêmement avancées, où l’automatisation, l’intelligence artificielle, la robotique et l’efficacité énergétique jouent un rôle clé. Ces technologies permettent non seulement d’améliorer la productivité et la flexibilité des processus de fabrication, mais aussi de répondre aux demandes croissantes du marché pour des produits plus complexes, personnalisés et de haute qualité. Ces systèmes représentent une véritable révolution dans la manière dont les pièces métalliques sont fabriquées, avec des impacts significatifs sur l’industrie et l’économie mondiale.
Les systèmes industriels de mise en forme de tôle continuent d’évoluer avec l’innovation technologique, ce qui ouvre la voie à des applications encore plus diversifiées et à des performances améliorées. À mesure que les demandes du marché deviennent plus complexes et que les industries cherchent à réduire les coûts tout en améliorant la qualité, les systèmes de production doivent s’adapter à de nouvelles exigences. Cette adaptation passe par l’intégration de technologies avancées et par l’optimisation des processus existants.
Un aspect clé de cette évolution est la flexibilité accrue des systèmes de fabrication. Alors que dans le passé, les machines étaient souvent conçues pour des séries de production longues et uniformes, les systèmes modernes permettent désormais une grande variété de configurations de production. Cela permet aux entreprises de répondre rapidement à la demande de petites séries ou de pièces personnalisées, sans compromettre l’efficacité de la production. Les machines capables de changer rapidement de configuration, grâce à des systèmes automatisés ou semi-automatisés, permettent de minimiser les coûts de reconfiguration, rendant les processus plus agiles.
Les systèmes de contrôle avancés, y compris l’intégration de la réalité augmentée (RA) et de la réalité virtuelle (RV), permettent d’améliorer l’expérience des opérateurs. Par exemple, dans le cadre des opérations de maintenance, la réalité augmentée peut être utilisée pour guider les techniciens à travers des procédures complexes, en superposant des instructions visuelles sur les équipements réels. Cela réduit le risque d’erreurs humaines et accélère les interventions de maintenance. De plus, les plateformes de simulation virtuelle permettent aux concepteurs et aux ingénieurs de tester et d’optimiser les processus de mise en forme de tôle dans un environnement virtuel avant de les déployer sur le terrain, réduisant ainsi les coûts liés aux erreurs en production et à l’expérimentation physique.
La gestion des flux de production est également une priorité. Les technologies de traçabilité des pièces, alimentées par des systèmes comme la RFID (identification par radiofréquence) ou des capteurs IoT, permettent de suivre chaque pièce tout au long de son cycle de production. Cela garantit une transparence totale, ce qui facilite l’identification rapide des goulots d’étranglement dans la chaîne de production et permet d’optimiser les cycles de fabrication en fonction des données recueillies en temps réel.
La fabrication numérique continue également de se développer, notamment avec l’avènement de la fabrication additive (impression 3D), qui permet la production de pièces métalliques directement à partir de modèles numériques. Bien que cette technologie soit encore en développement dans l’industrie de la mise en forme de tôle, elle offre un potentiel énorme pour la création de pièces complexes avec des géométries optimisées, difficilement réalisables avec des méthodes de formage traditionnelles. L’impression 3D métallique, en particulier, permet d’éliminer de nombreux processus intermédiaires tout en produisant des pièces légères, solides et souvent plus durables, tout en offrant des options de personnalisation de masse.
Les systèmes d’analyse des données jouent un rôle crucial dans l’amélioration continue des processus de production. L’utilisation de big data et de l’intelligence artificielle pour analyser les performances des machines, les conditions de production et les retours clients permet aux entreprises d’anticiper les problèmes avant qu’ils ne surviennent. Par exemple, l’analyse prédictive peut estimer la durée de vie des composants des machines, permettant une planification plus précise des maintenances et une meilleure gestion des stocks de pièces de rechange.
Un autre aspect fondamental de ces systèmes est la capacité à réduire l’impact environnemental des processus de fabrication. Les nouvelles technologies, comme les systèmes de gestion de l’énergie, visent à réduire la consommation d’énergie des machines tout en garantissant une efficacité optimale. De plus, les procédés de mise en forme modernes permettent de maximiser l’utilisation des matériaux en réduisant les pertes et les déchets. Par exemple, la découpe laser et la découpe plasma permettent des découpes plus nettes et plus précises, ce qui réduit la quantité de matière première nécessaire et les rebuts produits.
Dans un contexte économique de plus en plus tourné vers la durabilité, les matériaux recyclés deviennent également un élément clé dans les systèmes industriels de mise en forme de tôle. L’utilisation de métaux recyclés dans la fabrication des tôles permet de réduire les coûts et d’abaisser l’empreinte carbone. Les machines sont de plus en plus adaptées pour traiter ces matériaux, avec des technologies permettant de maintenir une qualité de production élevée tout en utilisant des métaux provenant de filières de recyclage.
Enfin, la synchronisation des systèmes de production avec la gestion de la chaîne d’approvisionnement devient essentielle pour améliorer les performances globales de la fabrication. La mise en place de systèmes ERP (Enterprise Resource Planning) et MES (Manufacturing Execution Systems) permet de coordonner en temps réel les opérations de production, la gestion des stocks et les prévisions de la demande. Cela permet de réduire les coûts liés aux inventaires excédentaires ou à la rupture de stock, en ajustant les flux de production aux besoins exacts du marché.
Les systèmes industriels de mise en forme de tôle sont en constante évolution et deviennent de plus en plus sophistiqués. L’intégration des technologies de l’Industrie 4.0, y compris l’automatisation, l’intelligence artificielle, l’IoT, et l’analyse de données, transforme les processus de fabrication en environnements hautement intelligents et interconnectés. Ces systèmes permettent aux fabricants de répondre rapidement aux exigences croissantes de personnalisation et de qualité tout en maintenant une production efficace, durable et rentable. Dans ce contexte, les entreprises capables d’intégrer ces technologies et d’optimiser leurs processus seront mieux positionnées pour réussir sur le marché mondial.
Machines de traitement de tôle
Les machines de traitement de tôle sont des équipements utilisés pour transformer les tôles métalliques brutes en pièces finies ou semi-finies, en utilisant des procédés de fabrication variés comme la découpe, le formage, le pliage, l’emboutissage, la perforation, et le redressage. Ces machines sont essentielles dans les industries telles que l’automobile, l’aérospatiale, la construction, l’électroménager, et bien d’autres, où les pièces métalliques doivent être précises, solides et adaptées aux besoins spécifiques de chaque application. Voici un aperçu des principaux types de machines utilisées dans le traitement de la tôle.
Machines de découpe de tôle
La découpe est l’une des étapes de base dans le traitement de la tôle, consistant à séparer une ou plusieurs tôles métalliques en fonction des spécifications requises pour les pièces finies. Il existe plusieurs types de machines pour la découpe des tôles, en fonction de la méthode utilisée :
- Cisailles mécaniques ou hydrauliques : Ces machines utilisent des lames pour couper les tôles en lignes droites. Les cisailles mécaniques sont généralement utilisées pour les découpes simples, tandis que les cisailles hydrauliques sont plus puissantes et adaptées à des découpes de tôles plus épaisses.
- Découpe au laser : Les machines de découpe au laser utilisent un faisceau laser concentré pour couper des tôles métalliques avec une grande précision. Ce procédé est idéal pour des formes complexes et des découpes fines, et est très utilisé dans la fabrication de pièces de haute précision.
- Découpe plasma : Ce procédé utilise un jet de plasma pour couper les tôles métalliques. Il est plus rapide que la découpe au laser et est souvent utilisé pour couper des tôles d’épaisseur moyenne à épaisse. Il est particulièrement adapté pour les métaux conducteurs, comme l’acier, l’aluminium, et le cuivre.
- Découpe au jet d’eau : Une autre méthode précise consiste à utiliser un jet d’eau haute pression, souvent avec des abrasifs, pour découper les tôles. Cela permet de travailler sur des matériaux sensibles à la chaleur, car le procédé ne génère pas de chaleur, ce qui empêche la déformation du métal.
Machines de formage de tôle
Le formage de tôle implique de plier ou de modeler la tôle métallique sous l’effet de forces externes. Ce processus est couramment utilisé pour produire des boîtiers, des structures, et des composants à partir de tôles. Les machines de formage les plus courantes sont :
- Plieuses (ou plieuses hydrauliques) : Ces machines sont utilisées pour plier des tôles métalliques selon des angles spécifiques. Le processus se fait généralement par l’application d’une pression hydraulique, qui permet de manipuler les tôles avec précision et sans risque de déformation indésirable. Elles peuvent être équipées de divers outils pour réaliser des plis de différents types.
- Emboutisseuses (ou presses d’emboutissage) : L’emboutissage est un processus qui permet de former des pièces à partir de tôles plates par l’application d’une pression de l’outillage sur la tôle. Cela permet de réaliser des formes complexes comme des boîtiers de véhicules ou des pièces de carrosserie.
- Machines à cintrer : Utilisées pour plier des tôles métalliques dans des courbes complexes, ces machines permettent de créer des formes circulaires ou semi-circulaires avec une grande précision.
- Presses plieuses CNC (Commande Numérique par Calculateur) : Ces machines sont équipées de contrôles numériques qui permettent de programmer des opérations de pliage avec une grande précision, en ajustant automatiquement la position et la pression de la machine en fonction de chaque pièce. Elles sont particulièrement utiles pour les productions de pièces complexes ou de petites séries.
Machines de perforation
Les machines de perforation de tôle sont utilisées pour créer des trous ou des motifs perforés dans les tôles métalliques. Ces machines peuvent être manuelles ou automatisées et sont souvent utilisées dans la fabrication de pièces destinées à des applications spécifiques, comme les filtres, les grilles, ou les composants de ventilation.
- Perceuses à commande numérique (CNC) : Ces machines sont capables de percer des trous avec une grande précision dans des tôles de diverses épaisseurs. Grâce à leur commande numérique, elles permettent de réaliser des perforations multiples et complexes à des vitesses élevées.
- Perforatrices à poinçons : Ces machines utilisent des poinçons pour percer des trous dans la tôle. Elles sont souvent utilisées pour créer des trous ou des motifs réguliers dans des tôles plus épaisses, comme celles utilisées pour les pièces d’automobiles ou d’appareils électroménagers.
Machines de redressage
Le redressage est un procédé visant à corriger les déformations ou ondulations dans les tôles qui se produisent pendant leur fabrication ou leur stockage. Cela permet d’obtenir une surface plane et régulière, essentielle pour de nombreux processus de fabrication ultérieurs.
- Redresseuses à rouleaux : Ces machines utilisent des rouleaux pour aplatir les tôles courbées. Elles sont souvent utilisées pour corriger les défauts de planéité des tôles avant qu’elles ne soient utilisées dans d’autres processus de fabrication.
- Redresseuses hydrauliques : Ces machines utilisent la pression hydraulique pour redresser les tôles. Elles peuvent être réglées pour effectuer des ajustements fins et adaptés à des tôles de différentes épaisseurs et dimensions.
Machines de soudage et assemblage
Le soudage est une autre étape importante dans le traitement de la tôle, particulièrement pour les applications où les pièces métalliques doivent être unies pour former une structure ou un composant plus large.
- Machines de soudage MIG/MAG : Ces machines sont utilisées pour effectuer un soudage par fusion de métaux, généralement dans les industries automobile et aéronautique. Elles permettent de souder les tôles ensemble de manière efficace et rapide, en utilisant un gaz de protection pour éviter l’oxydation pendant le processus.
- Soudage TIG : Plus adapté pour les métaux fins et pour des applications nécessitant des soudures très propres et de haute qualité, cette méthode utilise un arc électrique pour chauffer et fusionner les tôles métalliques.
- Soudage par points : Ce procédé de soudage est couramment utilisé dans la fabrication de carrosseries de voitures et d’autres structures en tôle. Il consiste à appliquer une pression localisée à l’endroit où les tôles se rejoignent, ce qui crée une soudure solide.
Machines de finition et de contrôle
Enfin, après les procédés de formage, découpe, et assemblage, il est souvent nécessaire d’effectuer des opérations de finition et de contrôle qualité.
- Machines de polissage et de meulage : Ces machines sont utilisées pour nettoyer les bords des pièces découpées, éliminer les bavures et améliorer la finition des surfaces métalliques.
- Contrôles dimensionnels et inspection visuelle : L’inspection de la qualité des pièces finies est réalisée à l’aide de machines de mesure et de dispositifs de contrôle. Cela inclut des machines de mesure tridimensionnelle (CMM) qui permettent de vérifier avec une grande précision les dimensions des pièces par rapport aux spécifications de conception.
En conclusion, les machines de traitement de tôle jouent un rôle fondamental dans l’industrie moderne en permettant la transformation de tôles métalliques en pièces finies. Grâce à une gamme diversifiée de technologies allant de la découpe à l’assemblage, ces machines permettent de produire des composants complexes, de haute précision, et de grande qualité, adaptés aux besoins spécifiques de chaque secteur. Les innovations constantes dans le domaine des machines de traitement de tôle, telles que l’automatisation, la robotisation, et l’intégration de la commande numérique, continuent de pousser les limites de ce qui est possible dans le traitement des métaux.
Les machines de traitement de tôle, avec leurs diverses applications, jouent un rôle crucial dans la fabrication moderne. Leur capacité à transformer des tôles métalliques brutes en pièces finies de qualité, tout en répondant aux besoins variés des industries, en fait un pilier de la production industrielle. En plus de leur rôle dans le formage et la découpe, ces machines intègrent des innovations technologiques qui permettent d’améliorer leur efficacité, leur précision et leur flexibilité.
Une des grandes avancées dans le domaine des machines de traitement de tôle a été l’intégration de la robotisation et de l’automatisation. Ces technologies permettent de réduire l’intervention humaine dans les processus répétitifs, réduisant ainsi les risques d’erreurs, améliorant la sécurité et augmentant la vitesse de production. Les robots sont souvent utilisés pour le chargement et déchargement des tôles, le positionnement des pièces dans les machines de découpe ou encore l’assemblage de pièces par soudure. Cette automatisation des tâches répétitives permet de libérer du temps pour des opérations à plus forte valeur ajoutée, tout en optimisant les coûts de production.
L’utilisation de systèmes de contrôle numérique (CNC) est une autre évolution importante dans les machines de traitement de tôle. Ces systèmes permettent de contrôler avec une grande précision les paramètres de fonctionnement des machines, comme la vitesse de coupe, l’angle de pliage ou la pression appliquée. Grâce à la CNC, les machines peuvent être programmées pour effectuer des opérations complexes et variées, ce qui réduit les besoins en main-d’œuvre qualifiée tout en augmentant la production de manière plus constante et uniforme.
Le suivi en temps réel des opérations grâce aux technologies de l’Internet des objets (IoT) est également une caractéristique de plus en plus répandue dans les systèmes modernes. Les capteurs intégrés dans les machines peuvent collecter des données en continu sur des variables telles que la température, la pression ou l’humidité. Ces informations sont ensuite envoyées à un système centralisé qui analyse les données et fournit des rapports de performance. Cela permet aux opérateurs de prendre des décisions informées en temps réel pour ajuster les paramètres de production et prévenir les éventuels dysfonctionnements. De plus, ces systèmes peuvent aider à la maintenance prédictive en détectant les signes avant-coureurs de pannes, réduisant ainsi les temps d’arrêt imprévus et augmentant la fiabilité des équipements.
L’adoption croissante de la fabrication additive, ou impression 3D, dans les processus de traitement de tôle représente également une avancée majeure. Bien que l’impression 3D des métaux soit encore principalement utilisée pour des applications spécifiques ou des prototypes, elle commence à trouver sa place dans des secteurs comme l’aéronautique ou l’automobile, où des pièces de géométrie complexe et de haute performance sont nécessaires. Les machines de fabrication additive permettent de créer des pièces sans les contraintes des méthodes traditionnelles de formage ou de découpe. Cela permet, en outre, de réduire le gaspillage de matériaux, car l’impression 3D est un procédé très précis qui ne nécessite pas de découper ou d’éliminer des morceaux de métal comme dans les procédés classiques.
Dans le cadre de la durabilité, les machines de traitement de tôle modernes intègrent de plus en plus des technologies visant à minimiser leur impact environnemental. Les procédés de production sont de plus en plus optimisés pour réduire la consommation d’énergie et limiter les déchets. Par exemple, les machines de découpe au laser utilisent un faisceau de lumière concentré, ce qui permet des découpes très fines, réduisant ainsi les chutes de matériau. De même, les systèmes de récupération de chaleur et d’optimisation de la consommation énergétique permettent de réduire l’empreinte carbone des usines de fabrication. En parallèle, des initiatives de recyclage des matériaux sont mises en place pour réduire l’usage de nouvelles ressources et encourager l’utilisation de tôles recyclées.
L’intégration de la réalité augmentée (RA) et de la réalité virtuelle (RV) dans les machines de traitement de tôle ouvre également de nouvelles perspectives. Ces technologies sont particulièrement utiles pour la formation des opérateurs, la maintenance à distance et même la conception. Par exemple, les opérateurs peuvent utiliser la RA pour visualiser les étapes de montage d’un composant ou être guidés dans les réglages des machines en superposant des informations utiles sur l’environnement de travail réel. De plus, les concepteurs peuvent tester virtuellement les processus de fabrication avant de passer à la production réelle, ce qui permet d’éviter les erreurs coûteuses et d’optimiser les procédés.
Dans un environnement de plus en plus connecté et numérique, les systèmes ERP (Enterprise Resource Planning) et MES (Manufacturing Execution Systems) sont de plus en plus intégrés aux machines de traitement de tôle. Ces systèmes permettent de synchroniser l’ensemble des opérations de production, de la gestion des stocks à l’ordonnancement des tâches, tout en offrant une visibilité en temps réel sur l’état de la production. Cela facilite la gestion des flux de travail, optimise l’utilisation des ressources et réduit les coûts liés à la gestion des stocks ou aux inefficacités dans la chaîne de production.
Les machines de traitement de tôle modernes, avec l’avènement de l’industrie 4.0, sont devenues des éléments hautement intelligents et interconnectés. Grâce à l’intégration des technologies de big data, IoT, IA et robotique, elles permettent de produire des pièces de manière plus rapide, plus précise et plus économique, tout en étant capables de s’adapter à des besoins de production de plus en plus variés et personnalisés. Ces machines contribuent ainsi à transformer les environnements industriels en des systèmes de production plus flexibles, réactifs et durables, répondant aux défis actuels de la fabrication.
L’évolution continue des machines de traitement de tôle est directement influencée par les exigences croissantes des industries, qui recherchent des solutions permettant non seulement d’augmenter la productivité, mais aussi de répondre à des normes de qualité strictes tout en minimisant les coûts et l’impact environnemental. Dans ce contexte, l’adoption des technologies avancées, comme l’intelligence artificielle (IA), la robotique et la gestion en temps réel, est primordiale pour optimiser la fabrication et rendre les processus plus intelligents et autonomes.
Innovation dans la robotisation et l’automatisation
Les robots industriels jouent un rôle de plus en plus important dans le traitement des tôles, en particulier pour des tâches répétitives et lourdes. Par exemple, dans les lignes de production automatisées, des robots peuvent effectuer des opérations de chargement et déchargement des tôles, d’assemblage de pièces, ainsi que d’inspection visuelle. Ces robots sont équipés de caméras intelligentes et de capteurs pour inspecter les pièces à la recherche de défauts ou d’anomalies avant qu’elles ne passent à l’étape suivante du processus de production. Cette automatisation permet non seulement d’améliorer la vitesse de production, mais aussi de garantir un niveau de qualité constant et d’éviter les erreurs humaines.
Dans le domaine de la robotique collaborative (cobots), ces systèmes de robots peuvent travailler en toute sécurité à côté des opérateurs humains. Contrairement aux robots traditionnels, qui nécessitent souvent des protections et des barrières de sécurité, les cobots sont conçus pour interagir directement avec les opérateurs humains sans risques de blessures, tout en optimisant les processus de production. Par exemple, un cobot peut aider un opérateur en soulevant des pièces lourdes ou en réalisant des tâches de précision répétitives, améliorant ainsi la productivité et réduisant la fatigue des travailleurs.
La fabrication prédictive avec l’IA
L’intelligence artificielle joue un rôle clé dans l’évolution des machines de traitement de tôle, notamment par l’introduction de systèmes de maintenance prédictive. Grâce aux algorithmes d’IA et aux capteurs intelligents, les machines peuvent être équipées pour surveiller en temps réel leur état de fonctionnement. Ces capteurs mesurent des variables comme la température, la pression, l’humidité et l’usure des pièces, puis transmettent ces informations à un système centralisé qui utilise l’IA pour analyser les données et prévoir les défaillances potentielles avant qu’elles ne se produisent. Cette approche permet de réduire les temps d’arrêt non planifiés et d’optimiser la durée de vie des équipements, ce qui peut se traduire par des économies importantes et une meilleure efficacité opérationnelle.
L’IA est également utilisée pour améliorer le contrôle qualité en temps réel. Par exemple, des systèmes basés sur l’apprentissage automatique peuvent être appliqués pour analyser les pièces métalliques pendant leur fabrication, identifier des défauts invisibles à l’œil nu, et même ajuster les paramètres de production pour garantir que chaque pièce fabriquée respecte les spécifications de qualité exigées.
L’impact de l’Internet des Objets (IoT)
L’intégration de l’IoT dans les machines de traitement de tôle permet une collecte de données en temps réel, qui peut ensuite être utilisée pour des ajustements immédiats et une prise de décision optimisée. Grâce à l’IoT, les machines sont capables de communiquer entre elles et avec un système centralisé, ce qui facilite la gestion des stocks, le suivi des pièces en production, et la planification des opérations. Cela améliore la traçabilité, réduit les erreurs humaines, et optimise la gestion de la chaîne de production. Par exemple, une machine peut alerter les opérateurs dès que des anomalies sont détectées, ou encore ajuster automatiquement ses réglages pour optimiser la découpe ou le formage de la tôle.
Optimisation de la consommation énergétique
Les machines modernes de traitement de tôle intègrent de plus en plus de solutions pour optimiser la consommation d’énergie. Les procédés de découpe, en particulier ceux utilisant des technologies telles que le laser ou le plasma, sont énergivores, mais des innovations récentes ont permis d’améliorer leur efficacité énergétique. Par exemple, les systèmes de gestion de l’énergie intégrés permettent de suivre la consommation énergétique des machines en temps réel, et des algorithmes peuvent être utilisés pour ajuster automatiquement les cycles de production afin de maximiser l’efficacité tout en minimisant l’empreinte énergétique. Cela s’inscrit dans un objectif global de durabilité, où les entreprises cherchent à réduire leur impact environnemental tout en maintenant une productivité élevée.
Maintenance prédictive et réduction des coûts
La maintenance prédictive s’impose comme une solution indispensable pour les entreprises désireuses de prolonger la durée de vie de leurs machines de traitement de tôle tout en réduisant les coûts de maintenance imprévus. En combinant les données des capteurs IoT avec des algorithmes d’IA, il est possible de prévoir les défaillances avant qu’elles n’affectent la production. Par exemple, une machine de découpe laser peut être équipée de capteurs mesurant l’intensité du faisceau lumineux, et si l’intensité commence à diminuer de manière anormale, le système peut signaler qu’une maintenance est nécessaire pour nettoyer ou ajuster les composants avant qu’ils ne tombent en panne. Cette approche réduit non seulement les coûts de réparation, mais elle permet également d’augmenter le temps de fonctionnement des machines, ce qui améliore l’efficacité globale de la production.
Fabrication durable et recyclage
Les préoccupations environnementales occupent une place de plus en plus importante dans l’industrie de la tôle. Les entreprises cherchent à réduire leur empreinte carbone en utilisant des matériaux recyclés et en optimisant les procédés pour minimiser le gaspillage. Le recyclage des métaux joue un rôle clé dans cette démarche, et les machines de traitement de tôle doivent être capables de traiter efficacement des matériaux recyclés tout en garantissant la même qualité que celle obtenue avec des matériaux vierges.
Certaines machines modernes de traitement de tôle, notamment les systèmes de découpe au laser, ont été optimisées pour travailler avec des tôles issues du recyclage, tout en réduisant le taux de rejet des matériaux. De plus, les nouvelles méthodes de découpe et de formage génèrent moins de déchets et permettent d’exploiter pleinement la matière première. Les technologies de gestion des déchets dans les usines permettent de récupérer et de recycler les chutes de métal générées pendant le processus de production, contribuant ainsi à une approche circulaire de la fabrication.
Intégration des chaînes de production et flexibilité
Les avancées dans l’automatisation et l’interconnexion des machines permettent une intégration plus fluide des chaînes de production. Les systèmes modernes permettent à différentes machines de travailler de manière coordonnée, offrant une plus grande flexibilité dans les lignes de production. Par exemple, une ligne de fabrication entièrement automatisée peut être configurée pour produire à la fois de grandes séries de produits identiques et de petites séries de produits personnalisés, tout en maintenant un haut niveau de productivité. Cela permet de mieux répondre à la demande variable des clients, ce qui est essentiel dans un monde où les cycles de production et de consommation sont de plus en plus rapides.
Ces systèmes flexibles et interconnectés permettent également de réagir rapidement aux changements dans la demande ou aux problèmes de production, ce qui est essentiel pour maintenir une compétitivité élevée. Dans un contexte mondial de plus en plus incertain, la capacité d’adaptation est une des principales forces de ces systèmes industriels modernes de traitement de tôle.
En résumé, les machines de traitement de tôle ne cessent d’évoluer grâce à l’intégration de technologies avancées comme la robotique, l’IA, l’IoT, et la fabrication additive. Ces innovations permettent de rendre les processus de production plus rapides, précis, flexibles, et durables, tout en optimisant les coûts et en minimisant l’impact environnemental. Les entreprises qui sauront tirer parti de ces avancées seront mieux équipées pour faire face aux défis de l’industrie moderne et se positionner comme des leaders sur leurs marchés.
Équipements pour modelage de tôle
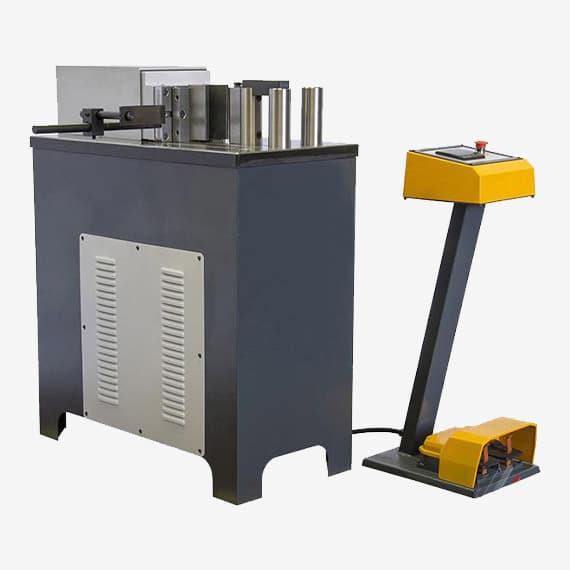
Les équipements pour le modelage de tôle sont essentiels pour transformer des tôles métalliques brutes en pièces finies qui répondent aux spécifications précises demandées par divers secteurs industriels. Ces équipements couvrent un large éventail de technologies et de procédés permettant de former, plier, découper ou assembler des tôles métalliques. En fonction du type de traitement et de la complexité des pièces à réaliser, différents types d’équipements peuvent être utilisés. Voici un aperçu des principaux équipements utilisés pour le modelage de tôle :
1. Plieuses et Poinçonneuses
Les plieuses et poinçonneuses sont des machines largement utilisées pour le modelage de tôles métalliques. Elles permettent de plier et de perforer les tôles avec précision.
- Plieuses : Ces machines sont utilisées pour plier des tôles métalliques afin de leur donner des formes angulaires spécifiques. Elles peuvent être hydrauliques, mécaniques ou à commande numérique (CNC) pour des plis plus complexes et plus précis. Les plieuses modernes sont capables de réaliser des plis très fins et réguliers, tout en maintenant une excellente précision dimensionnelle.
- Poinçonneuses : Les poinçonneuses sont utilisées pour percer des trous ou effectuer des découpes dans les tôles métalliques. Elles peuvent être équipées de matrices et de poinçons interchangeables pour réaliser des trous de différentes formes et tailles. Certaines poinçonneuses sont également dotées de fonctions CNC permettant de programmer des motifs complexes.
2. Machines de découpe au laser
Les machines de découpe au laser utilisent un faisceau laser intense pour découper des tôles métalliques avec une grande précision. Ce procédé est très apprécié pour sa capacité à réaliser des découpes complexes et nettes, avec des tolérances extrêmement serrées. Les machines de découpe laser sont souvent utilisées pour des applications nécessitant une grande précision, comme la production de pièces pour l’aéronautique, l’automobile et l’électronique.
- Laser à CO2 : Ce type de laser est couramment utilisé pour la découpe de tôles métalliques, en particulier pour les métaux plus fins et de haute épaisseur.
- Laser à fibre optique : Ce laser est de plus en plus populaire car il offre une meilleure efficacité énergétique et peut découper des matériaux métalliques plus épais que les lasers CO2.
3. Découpe plasma
La découpe plasma est un autre procédé couramment utilisé pour découper des tôles métalliques. Elle utilise un jet de plasma (gaz ionisé) chauffé à très haute température pour couper à travers le métal. Bien que ce procédé soit généralement moins précis que la découpe au laser, il reste très efficace pour découper des tôles métalliques épaisses et est souvent utilisé dans des environnements industriels à haute production.
4. Machines de formage à froid
Les machines de formage à froid permettent de modeler des tôles métalliques sans nécessiter de chauffage préalable. Ce procédé est couramment utilisé pour la production de pièces métalliques comme des boîtiers, des tôles ondulées ou des pièces de carrosserie automobile. Parmi les machines utilisées dans ce type de formage, on trouve :
- Les presses de formage : Ces presses exercent une pression sur la tôle pour la faire prendre la forme souhaitée, comme le moulage ou l’emboutissage.
- Les rouleuses : Ces machines permettent de courber les tôles métalliques en appliquant une pression graduée entre des rouleaux, permettant ainsi de créer des formes arrondies ou cylindriques.
5. Machines de découpe par jet d’eau
Les machines de découpe par jet d’eau utilisent un jet d’eau à haute pression, souvent mélangé à des abrasifs, pour couper des tôles métalliques. Ce procédé est particulièrement utile pour les matériaux sensibles à la chaleur, car il ne génère pas de chaleur. Il est également capable de découper des tôles épaisses tout en préservant des bords nets et sans déformation thermique.
6. Machines de cintrage
Les machines de cintrage sont utilisées pour plier les tôles métalliques en leur appliquant une pression mécanique. Contrairement aux plieuses qui effectuent des plis avec des angles spécifiques, les cintrages servent à donner à la tôle une forme courbée continue. Ce procédé est couramment utilisé pour la fabrication de tuyauteries ou de structures en métal.
7. Presses hydrauliques
Les presses hydrauliques sont utilisées pour un large éventail d’applications dans le modelage des tôles, notamment pour des opérations de formage, de coupe, ou de déformation. Elles utilisent une force hydraulique pour appliquer une pression sur la tôle métallique, ce qui permet de réaliser des formes complexes ou de couper des tôles avec une grande force. Ce type de machine est particulièrement utile dans la production de grandes séries de pièces ou de pièces de grandes dimensions.
8. Machines de formage par emboutissage
L’emboutissage est un procédé de formage de tôle qui consiste à déformer une tôle métallique en utilisant une matrice et un poinçon. Ce processus permet de créer des pièces complexes avec des formes concaves. Il est couramment utilisé pour la production de pièces automobiles, telles que des panneaux de carrosserie. Les machines utilisées pour l’emboutissage peuvent être équipées de presses mécaniques ou hydrauliques.
9. Machines de découpe par scie
Les scies à ruban ou scies circulaires sont parfois utilisées pour couper des tôles métalliques. Bien que ces machines soient généralement moins précises que les découpeurs laser ou plasma, elles peuvent être utilisées pour des découpes simples et de faibles épaisseurs de métal.
10. Soudage et assemblage
Le soudage est une technique complémentaire au modelage de tôle, utilisée pour assembler différentes pièces en métal. Les techniques de soudage, telles que le soudage TIG (Tungsten Inert Gas) ou MIG (Metal Inert Gas), sont couramment utilisées pour assembler des pièces de tôle métallique après leur modelage. Les robots de soudage sont également utilisés pour automatiser ce processus dans les industries où une grande précision est requise.
11. Presses à découper et presses à emboutir
Les presses à découper sont utilisées pour couper des formes spécifiques dans les tôles métalliques, tandis que les presses à emboutir servent à façonner ou déformer la tôle métallique en appliquant une pression à l’aide de matrices.
Conclusion
Le modelage de tôle est une étape cruciale dans de nombreux secteurs industriels, et les équipements associés varient en fonction des exigences de production, de la complexité des pièces à fabriquer, et du type de métal utilisé. L’intégration de technologies avancées, telles que la robotisation, la CNC, et la gestion numérique, transforme les procédés de modelage de tôle en processus plus rapides, plus précis et plus rentables. Avec l’évolution continue de la technologie, ces machines deviennent de plus en plus intelligentes, offrant une flexibilité accrue et une meilleure efficacité dans la production de pièces métalliques de haute qualité.
Les équipements pour le modelage de tôle sont conçus pour transformer les tôles métalliques en pièces finies avec des formes, des tailles et des caractéristiques spécifiques. Ces équipements intègrent diverses technologies et procédés permettant de plier, couper, perforer ou assembler les tôles selon les besoins de l’industrie. L’un des principaux types d’équipements est la plieuse, utilisée pour plier les tôles à différents angles. Certaines plieuses sont équipées de commandes numériques (CNC) qui offrent une précision accrue pour des plis complexes. Les poinçonneuses servent à perforer les tôles, créant des trous ou des motifs avec une grande exactitude.
La découpe au laser est une autre technologie courante utilisée pour créer des découpes nettes et complexes. Les machines de découpe laser peuvent couper des tôles métalliques de manière précise et rapide, tout en réduisant les risques de déformation thermique. Un autre procédé important est la découpe plasma, qui utilise un jet de plasma à haute température pour couper des tôles métalliques épaisses. Bien qu’elle soit généralement moins précise que la découpe au laser, elle est plus économique pour couper des matériaux plus épais.
Les machines de formage à froid sont utilisées pour transformer les tôles sans nécessiter de chauffage préalable, par exemple à travers des presses de formage ou des rouleuses. Ces machines permettent de donner à la tôle une forme courbée ou angulaire sans altérer ses propriétés métallurgiques. De plus, les machines de découpe par jet d’eau, utilisant un jet haute pression mélangé à des abrasifs, offrent une alternative pour découper les tôles sans générer de chaleur, ce qui est utile pour des matériaux sensibles.
Le cintrage est également un processus essentiel dans le modelage de tôle, où les machines appliquent une pression pour donner à la tôle une forme arrondie ou courbée. Les presses hydrauliques, utilisées dans des opérations de formage, de coupe ou de déformation, permettent de travailler avec des tôles de grandes dimensions ou de matériaux très épais. L’emboutissage, un procédé de déformation plastique, est souvent utilisé pour produire des pièces métalliques complexes telles que des composants de carrosserie automobile.
Les machines de soudage et les équipements associés sont également essentiels dans la phase finale du modelage des tôles, où différentes pièces métalliques sont assemblées pour créer un produit fini. Les robots de soudage, qui assurent un assemblage précis et rapide, sont particulièrement populaires dans les environnements de production automatisée. Le soudage TIG ou MIG est souvent utilisé pour l’assemblage des tôles après leur déformation.
Le recyclage des métaux et l’optimisation énergétique sont également des considérations importantes dans le choix des équipements modernes. Les systèmes modernes de gestion de l’énergie et les technologies de découpe avancées permettent de réduire la consommation d’énergie et le gaspillage de matériaux, contribuant ainsi à une production plus durable et moins coûteuse. De plus, l’intégration de technologies telles que l’intelligence artificielle et l’Internet des objets (IoT) dans ces machines permet de mieux suivre la production, optimiser les performances et réduire les temps d’arrêt. Cela améliore la productivité globale tout en maintenant des standards de qualité élevés.
En somme, le modelage de tôle repose sur une large gamme de technologies qui permettent de produire des pièces métalliques avec des caractéristiques spécifiques. Les équipements de transformation de tôle continuent d’évoluer, en particulier avec les avancées en automatisation, robotisation, et intégration numérique, qui permettent aux industries de produire des pièces avec une précision, une vitesse et une efficacité accrues.
L’évolution des équipements pour le modelage de tôle s’inscrit dans un contexte d’innovation continue visant à répondre à des exigences de plus en plus strictes en matière de qualité, de coût et de durabilité. L’intégration de technologies telles que l’intelligence artificielle (IA), la robotique avancée et les systèmes de gestion des données en temps réel joue un rôle crucial dans l’amélioration des processus de production.
Les systèmes de maintenance prédictive sont devenus un atout majeur pour les équipements de modelage de tôle. Grâce à l’utilisation de capteurs intelligents et à l’analytique des données, ces systèmes permettent de surveiller les performances des machines en temps réel. Ils peuvent détecter les signes de défaillances potentielles avant qu’elles ne surviennent, ce qui permet aux entreprises de planifier des réparations sans interruption de la production. Cela conduit à une réduction des coûts de maintenance imprévus, une augmentation du temps de fonctionnement des machines et une prolongation de leur durée de vie utile.
Les progrès dans les matériaux et les procédés de fabrication sont également un facteur clé. Par exemple, les machines modernes de découpe et de formage peuvent maintenant travailler avec des matériaux plus résistants ou plus fins, tout en maintenant une précision élevée. Cela permet aux industries de répondre à des demandes de plus en plus complexes, notamment dans des secteurs tels que l’aérospatial, l’automobile, l’électronique et la construction.
Une autre évolution importante est l’utilisation croissante des technologies de fabrication additive, comme l’impression 3D. Bien que principalement utilisée pour la création de prototypes, cette technologie trouve également sa place dans le modelage de tôle pour des applications très spécifiques, telles que la fabrication de matrices et d’outils de formage. L’intégration de l’impression 3D avec des équipements de transformation de tôle permet de réaliser des outils personnalisés et des pièces complexes à un coût réduit et dans des délais plus courts. Cette approche offre une plus grande flexibilité et un meilleur contrôle sur les caractéristiques des produits finis.
L’automatisation est un autre domaine où les équipements de modelage de tôle ont considérablement évolué. Les lignes de production modernes peuvent être entièrement automatisées, avec des robots collaboratifs (cobots) qui travaillent en synergie avec les opérateurs humains. Ces cobots peuvent effectuer des tâches telles que la manipulation des tôles, le positionnement des pièces, ou même le contrôle de la qualité, tout en réduisant les risques d’erreurs humaines et en augmentant la cadence de production.
Les systèmes de contrôle qualité automatisés sont également de plus en plus utilisés pour garantir que chaque pièce produite respecte les normes strictes de qualité. Grâce à des caméras haute résolution, des capteurs et des logiciels d’IA, ces systèmes peuvent inspecter les pièces tout au long du processus de production et ajuster automatiquement les paramètres des machines en cas de détection de défauts, garantissant ainsi des pièces parfaitement conformes aux exigences.
L’impact environnemental est également un facteur de plus en plus important dans l’optimisation des équipements de modelage de tôle. De nombreux fabricants cherchent à réduire leur empreinte carbone en adoptant des technologies qui consomment moins d’énergie, produisent moins de déchets et permettent de recycler davantage de matériaux. Par exemple, des systèmes de découpe plus efficaces, tels que ceux utilisant la technologie au laser ou au jet d’eau, génèrent moins de déchets et utilisent l’énergie de manière plus ciblée, contribuant ainsi à une production plus écologique.
Les matériaux composites gagnent aussi en popularité, car ils combinent la légèreté du métal et la résistance de matériaux non métalliques. Les équipements de transformation de tôle modernes peuvent maintenant être utilisés pour travailler avec ces matériaux composites, offrant une plus grande flexibilité dans la production de pièces légères mais robustes, particulièrement dans l’industrie aéronautique et automobile.
Enfin, l’interconnexion des machines via l’Internet des Objets (IoT) permet aux fabricants d’accéder à des données en temps réel provenant des équipements de production. Ces données peuvent être utilisées pour surveiller la performance, ajuster les paramètres des machines et optimiser les processus de fabrication de manière dynamique. Les systèmes de gestion intégrée permettent une planification et un suivi en temps réel de la production, améliorant ainsi la réactivité et l’efficacité des lignes de production.
En conclusion, l’avenir des équipements pour le modelage de tôle repose sur l’intégration des technologies avancées qui permettent d’améliorer la précision, la rapidité et la flexibilité des processus de production. L’automatisation, la maintenance prédictive, l’IA, l’IoT, la robotisation et l’utilisation de matériaux innovants transforment ces équipements pour répondre aux défis croissants de l’industrie. Alors que les exigences des marchés deviennent plus complexes et que les pressions pour réduire l’impact environnemental s’intensifient, ces équipements devront évoluer pour offrir des solutions de plus en plus intelligentes, durables et rentables.
À mesure que les équipements de modelage de tôle continuent d’évoluer, plusieurs tendances et innovations se dessinent qui redéfinissent la manière dont ces machines sont utilisées et intégrées dans les chaînes de production. Les machines intelligentes sont à la pointe de cette transformation, intégrant des fonctionnalités avancées qui améliorent non seulement la performance mais aussi la durabilité et la réactivité des processus de fabrication.
L’intelligence artificielle (IA) et l’apprentissage automatique (machine learning) commencent à jouer un rôle crucial dans la gestion des lignes de production. Ces technologies permettent d’optimiser les processus de modelage de tôle en analysant des quantités massives de données en temps réel. Par exemple, l’IA peut être utilisée pour prédire des défaillances des machines, ajuster automatiquement les paramètres des équipements en fonction des conditions de production, et améliorer la planification de la production en anticipant les demandes du marché. Ces systèmes peuvent apprendre des erreurs passées et des conditions de production pour ajuster les processus de manière autonome, réduisant ainsi les coûts et améliorant la qualité.
Une autre tendance importante est l’intégration de technologies de simulation numérique dans la conception et la planification des processus de formage de tôle. Grâce aux logiciels de simulation, les ingénieurs peuvent modéliser virtuellement les opérations de formage avant la production réelle. Cela permet de tester différents scénarios, de prévoir les résultats et d’optimiser les configurations des machines, des matrices et des outillages avant même le début de la fabrication. Ces simulations permettent de minimiser les erreurs de fabrication et d’optimiser l’utilisation des matériaux.
Les systèmes de vision industrielle sont également de plus en plus présents dans les lignes de production. Ces systèmes utilisent des caméras et des capteurs pour inspecter les pièces tout au long du processus de formage de tôle. Grâce à des algorithmes avancés de traitement d’image, ces systèmes peuvent détecter des défauts tels que des fissures, des bosses ou des irrégularités de surface. Lorsqu’un défaut est détecté, le système peut immédiatement ajuster les paramètres de la machine ou alerter l’opérateur, garantissant ainsi une qualité constante et réduisant le gaspillage de matériaux.
Dans un contexte de production de grande échelle, l’automatisation devient un impératif pour augmenter la productivité et réduire les coûts de main-d’œuvre. Les robots industriels jouent un rôle central dans la manipulation des tôles et dans l’assemblage de pièces après leur formage. Ces robots peuvent travailler avec une précision élevée et dans des conditions de travail difficiles, réduisant ainsi les risques de blessures et améliorant l’efficacité. De plus, les robots peuvent être intégrés avec des systèmes de vision et des capteurs pour effectuer des tâches telles que le contrôle de la qualité, le tri des pièces, et le stockage.
Les robots collaboratifs (cobots) sont également de plus en plus utilisés dans des environnements de production où l’humain et la machine doivent travailler ensemble. Contrairement aux robots traditionnels qui opèrent souvent dans des environnements isolés pour des raisons de sécurité, les cobots peuvent interagir directement avec les opérateurs humains. Cela permet une flexibilité accrue dans la production et facilite l’adaptation des lignes de production à des besoins changeants.
L’optimisation énergétique est un autre domaine d’innovation. Les équipements modernes sont conçus pour réduire leur consommation d’énergie, un objectif crucial dans un environnement industriel où les coûts énergétiques sont une part importante du budget. Des technologies telles que les moteurs à haute efficacité, les systèmes de récupération d’énergie, et l’utilisation d’énergies renouvelables pour alimenter les machines de formage de tôle deviennent de plus en plus courantes. Ces efforts contribuent à rendre la production plus durable tout en réduisant les coûts opérationnels.
Une attention particulière est également accordée à l’optimisation des matériaux. Les machines modernes sont capables de traiter des matériaux de plus en plus divers, y compris des alliages métalliques avancés et des composites métalliques. Par exemple, des matériaux comme l’aluminium, les alliages à haute résistance, et même les métaux composites sont de plus en plus utilisés dans des industries comme l’automobile et l’aérospatial, où la légèreté et la résistance sont cruciales. Ces matériaux nécessitent souvent des technologies de transformation spécialisées pour obtenir la forme et les propriétés mécaniques souhaitées.
Le recyclage des matériaux dans le cadre du modelage de tôle est également un domaine de plus en plus intégré dans les processus de production. De nombreuses entreprises adoptent des systèmes de récupération des chutes de métal pour les réutiliser dans la production de nouvelles pièces. Cela contribue non seulement à réduire le gaspillage mais aussi à diminuer les coûts liés à l’achat de matières premières. Le recyclage est désormais un aspect essentiel des stratégies de durabilité des entreprises manufacturières.
Dans l’industrie automobile, par exemple, les progrès dans le formage de tôle haute résistance ont permis de créer des pièces plus légères et plus solides, contribuant à la réduction de la consommation de carburant et des émissions de CO2. Les équipements de pressage à chaud et de formage superplastique permettent désormais de produire des pièces métalliques complexes tout en maintenant des standards de performance élevés.
En conclusion, les équipements de modelage de tôle sont en constante évolution pour répondre aux défis contemporains de précision, de durabilité, et de flexibilité. L’adoption de technologies avancées, telles que l’IA, l’automatisation, la simulation numérique, et les systèmes de maintenance prédictive, permet non seulement de maximiser la productivité mais aussi d’améliorer la qualité et la durabilité des produits finis. Ces innovations jouent un rôle clé dans la transformation de l’industrie manufacturière, en la rendant plus intelligente, écologique et réactive aux exigences du marché mondial.
Presses de formage de tôle
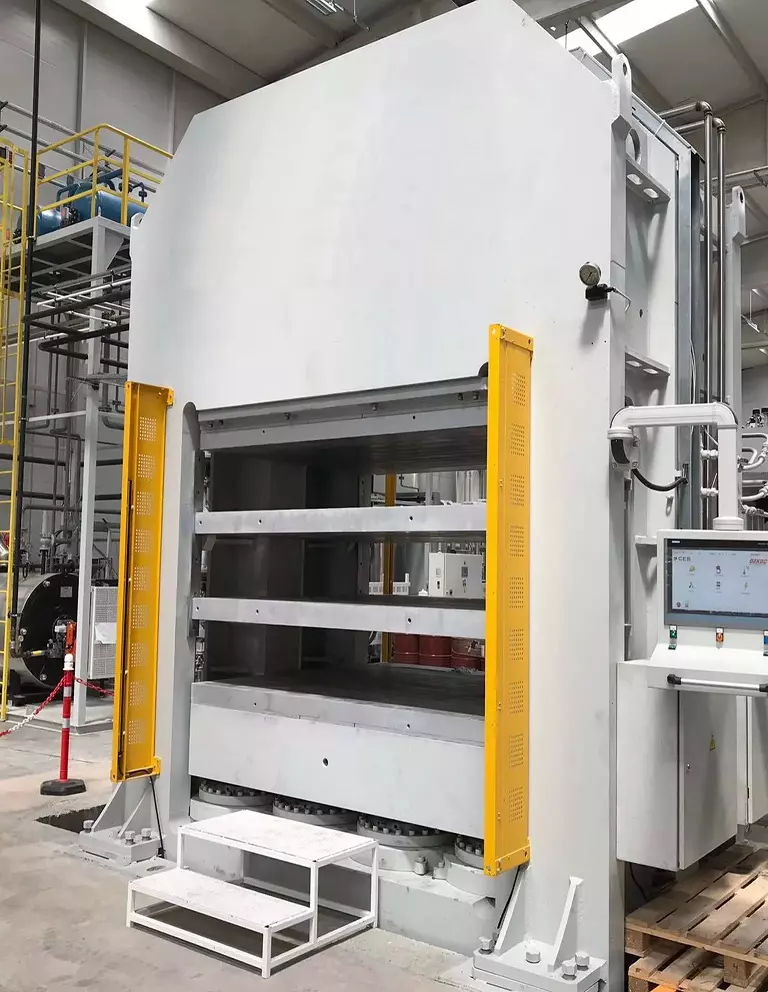
Les presses de formage de tôle sont des machines essentielles dans l’industrie de la transformation des métaux, utilisées pour façonner des tôles métalliques en différentes formes en appliquant une pression élevée. Ces presses jouent un rôle crucial dans de nombreux secteurs industriels, notamment l’automobile, l’aérospatial, la construction, et la production d’appareils électroménagers. Leur fonction principale est de modifier la forme et la structure des tôles métalliques, en utilisant des techniques de formage à froid ou formage à chaud, selon le type de processus utilisé.
Types de presses de formage de tôle
- Presses à vérins (ou presses mécaniques) :
- Ces presses sont alimentées par un moteur qui entraîne un volant ou un système à vis, créant ainsi un mouvement rotatif converti en pression verticale. Les presses à vérins sont souvent utilisées pour des opérations rapides, telles que le poinçonnage, le découpage ou le pliage de tôles métalliques.
- Les presses mécaniques peuvent générer des forces élevées pour réaliser des opérations de formage rapide avec une grande précision. Elles sont couramment utilisées pour produire des pièces simples ou des composants de taille moyenne.
- Les modèles à battement rapide sont conçus pour des applications nécessitant un mouvement rapide et répétitif, comme les lignes de production de grande échelle.
- Presses hydrauliques :
- Ces presses utilisent des vérins hydrauliques pour exercer une force de pression, ce qui permet d’atteindre une grande puissance de formage avec un contrôle précis. Contrairement aux presses mécaniques, qui sont souvent limitées à des charges spécifiques, les presses hydrauliques peuvent ajuster facilement la force de pression pour répondre aux besoins de différentes applications.
- Ces presses sont idéales pour des opérations de formage complexes, comme l’emboutissage profond de tôles, où une pression constante et uniforme est nécessaire pour éviter toute déformation non désirée.
- Les presses hydrauliques sont couramment utilisées dans l’industrie automobile pour la fabrication de panneaux de carrosserie, ainsi que dans la fabrication d’outillage complexe.
- Presses à cames :
- Les presses à cames sont équipées d’un système de came qui convertit un mouvement rotatif en un mouvement linéaire. Ce type de presse est particulièrement adapté pour des applications où il est nécessaire d’avoir un contrôle précis de la vitesse et de la force appliquée sur la tôle pendant le formage.
- Les presses à cames sont souvent utilisées dans la fabrication de petites pièces ou pour des opérations répétitives, comme le poinçonnage ou l’assemblage de composants métalliques.
- Presses à excentrique :
- Ces presses sont un type particulier de presse mécanique, où l’entraînement excentrique crée un mouvement de levée et de descente de la matrice. Elles sont souvent utilisées pour des applications nécessitant des vitesse de travail élevée et un cycle de production rapide.
- Ce type de presse est couramment utilisé dans des processus comme le coup de poinçonnage ou des emboutissages simples de tôles. Elles sont efficaces pour les travaux de découpe et de poinçonnage dans des séries de production moyenne à grande.
Processus de formage avec les presses de tôle
Le processus de formage de tôle implique plusieurs étapes, que la presse de formage aide à réaliser efficacement :
- Poinçonnage et découpe : La presse est utilisée pour perforer la tôle, créant des trous ou des motifs spécifiques. Les presses de formage peuvent aussi être utilisées pour découper des pièces de forme complexe, permettant une flexibilité de conception.
- Emboutissage : L’emboutissage est un processus où une tôle est formée pour donner des pièces profondes ou en trois dimensions, comme des boîtiers ou des panneaux de carrosserie. Cela nécessite une pression élevée pour tirer et étirer la tôle sans la déchirer. Les presses hydrauliques sont souvent utilisées pour ce processus.
- Pliage : Ce processus est utilisé pour donner une forme angulaire à la tôle. Une presse peut être équipée de matrices et de poinçons pour plier la tôle dans des formes spécifiques selon l’application.
- Découpe à froid : Certaines presses sont utilisées pour couper des tôles métalliques en utilisant des matrices et des poinçons conçus pour créer des bords nets et précis sans recourir à des techniques de découpe thermique.
- Repoussage : Un procédé similaire à l’emboutissage, mais où la tôle est poussée ou repoussée dans un moule pour former des formes profondes, comme des éléments décoratifs ou des pièces structurées.
Avantages des presses de formage de tôle
- Précision : Les presses modernes permettent un haut niveau de précision, essentiel pour des applications de haute qualité et des industries exigeantes comme l’aérospatiale et l’automobile.
- Flexibilité : Les presses peuvent être adaptées pour traiter une grande variété de matériaux, tels que l’acier, l’aluminium, et même des matériaux composites, ce qui les rend polyvalentes pour différentes applications.
- Efficacité : Ces machines sont capables de produire des pièces en grande série avec une cadence rapide, optimisant ainsi les coûts de production.
- Économie d’énergie : Les presses hydrauliques modernes et les presses à cames offrent des solutions énergétiques efficaces, surtout lorsqu’elles sont équipées de systèmes de contrôle intelligents qui ajustent automatiquement la force appliquée en fonction des caractéristiques de la tôle.
- Capacité de production en masse : Les presses de formage de tôle sont particulièrement adaptées à la production de grandes quantités de pièces, ce qui est crucial dans des industries à forte demande, comme l’automobile.
Tendances récentes et innovations
Les presses de formage de tôle évoluent constamment pour répondre aux exigences du marché. Voici quelques tendances récentes :
- Automatisation et robotisation : L’intégration de robots industriels dans les lignes de presses permet une gestion autonome des pièces, une manipulation plus précise et une productivité accrue. Les robots peuvent charger et décharger automatiquement les tôles, réduisant ainsi le besoin de main-d’œuvre et augmentant la vitesse de production.
- Presses intelligentes : Grâce à l’intelligence artificielle (IA) et à la connectivité IoT, les presses de formage modernes peuvent effectuer des ajustements automatiques en fonction de la production en temps réel, ce qui permet de détecter des anomalies et de minimiser les défauts.
- Matériaux plus légers et plus résistants : Les presses doivent être capables de traiter des matériaux métalliques avancés, y compris les alliages à haute résistance et les composites métalliques, qui nécessitent des forces de formage plus importantes sans compromettre la qualité du produit final.
- Fabrication additive et pressage hybride : L’intégration des technologies de fabrication additive (impression 3D) dans les presses permet de produire des outillages ou des pièces hybrides qui combinent les avantages de la fabrication traditionnelle et de l’impression 3D, offrant ainsi plus de flexibilité dans la production de pièces complexes.
En résumé, les presses de formage de tôle jouent un rôle central dans la transformation de métaux et la production de pièces métalliques. Leur capacité à offrir des solutions de haute précision, combinée avec des innovations technologiques, continue d’en faire des équipements incontournables pour une large gamme d’industries.
Les presses de formage de tôle, qu’elles soient mécaniques, hydrauliques ou à cames, sont essentielles dans de nombreuses applications industrielles. Elles permettent non seulement de façonner des tôles métalliques en différentes formes, mais aussi d’assurer une grande précision et répétabilité dans la production. Ces presses sont de plus en plus équipées de technologies avancées pour améliorer leur efficacité, leur précision et leur capacité à travailler avec des matériaux variés et complexes.
Les presses hydrauliques, par exemple, sont particulièrement adaptées aux opérations nécessitant une force continue et uniforme, ce qui est idéal pour des processus comme l’emboutissage profond. Elles offrent une grande flexibilité, car la pression peut être ajustée pour répondre aux besoins de chaque tâche spécifique. Par contraste, les presses mécaniques, qui génèrent une force par un système de volant ou de vis, sont idéales pour des applications rapides et à haute cadence, comme le poinçonnage ou le découpage de tôles de petite à moyenne taille. Ces presses sont souvent utilisées dans les lignes de production en série, où la rapidité et l’efficacité sont cruciales.
Une autre tendance importante dans le domaine des presses de formage de tôle est l’intégration de l’automatisation. Les robots industriels et les systèmes automatisés permettent d’optimiser les chaînes de production, réduisant ainsi le besoin de main-d’œuvre manuelle et augmentant la vitesse de fabrication. Les robots peuvent manipuler les tôles métalliques, charger et décharger les presses, et même effectuer des inspections en temps réel pour assurer la qualité des pièces produites. L’automatisation permet également de réduire les erreurs humaines, d’améliorer la précision des opérations et d’augmenter la sécurité sur les lignes de production.
Les presses de formage de tôle modernes sont également dotées de systèmes intelligents et de capteurs qui permettent une surveillance en temps réel des paramètres de production. Ces machines sont capables de détecter des anomalies et d’ajuster automatiquement les paramètres de pressage en fonction des conditions de travail. Cette capacité d’adaptation en temps réel est cruciale pour garantir que chaque pièce produite respecte les normes de qualité strictes, même dans des environnements de production de grande envergure.
L’impact environnemental est un autre facteur qui influence la conception des presses de formage de tôle. Les fabricants cherchent de plus en plus à réduire leur consommation d’énergie, à diminuer les déchets générés lors du processus de formage et à maximiser le recyclage des matériaux. De nouvelles technologies, comme les systèmes de récupération d’énergie et l’utilisation de moteurs à haute efficacité, permettent d’optimiser l’énergie consommée pendant le fonctionnement des presses. Cela non seulement réduit les coûts d’exploitation mais aide également à répondre aux attentes croissantes en matière de durabilité.
Enfin, l’évolution des matériaux traités par ces presses représente un défi et une opportunité. Les alliages métalliques avancés, les matériaux composites et les métaux à haute résistance nécessitent des forces de formage accrues et des technologies de pressage plus sophistiquées pour garantir une production de haute qualité. Les presses de formage de tôle doivent donc être conçues pour travailler avec ces matériaux de manière efficace, tout en maintenant des tolérances serrées et des propriétés mécaniques optimales. En parallèle, les machines doivent être capables de s’adapter rapidement aux changements dans la production et de répondre à des besoins de personnalisation accrue, comme cela est souvent demandé dans les secteurs de l’aérospatial, de l’automobile et de la fabrication de composants électroniques.
L’avenir des presses de formage de tôle semble prometteur avec l’innovation continue en matière de matériaux, technologies de fabrication, et automatisation intelligente. Ces évolutions permettent d’améliorer non seulement les processus de production mais aussi de répondre aux défis de la durabilité, de la flexibilité et de la compétitivité qui marquent les industries modernes. L’intégration de ces technologies pourrait également rendre les presses de formage de tôle plus accessibles aux petites et moyennes entreprises, leur offrant la possibilité d’adopter des processus de fabrication plus efficaces et plus écologiques.
Les presses de formage de tôle continuent de se perfectionner grâce aux avancées technologiques dans plusieurs domaines. Parmi celles-ci, l’intégration de la connectivité et de l’Internet des objets (IoT) représente une évolution majeure. Grâce à la collecte de données en temps réel, ces machines peuvent désormais être surveillées à distance, permettant aux opérateurs et aux ingénieurs de suivre les performances de la presse, de prédire les pannes potentielles et de maintenir un niveau de performance optimal. Les capteurs IoT intégrés peuvent détecter des anomalies telles que des fluctuations de température, des vibrations excessives ou des niveaux de pression incorrects, et alerter le personnel de maintenance avant que des pannes majeures ne surviennent. Cela minimise les temps d’arrêt imprévus, réduisant ainsi les coûts de maintenance et améliorant l’efficacité des lignes de production.
Les presses modernes sont également équipées de systèmes de gestion de la production (MES), qui aident à optimiser l’ensemble du processus de fabrication. Ces systèmes permettent d’améliorer la planification des tâches, le suivi des matériaux et la gestion des stocks. En intégrant la presse dans un réseau de fabrication intelligent, les entreprises peuvent réduire les erreurs humaines, améliorer la qualité du produit final, et ajuster rapidement la production en fonction des demandes du marché ou des fluctuations de la chaîne d’approvisionnement.
L’adaptation aux matériaux nouveaux et spécialisés reste une priorité pour les presses de formage de tôle. Avec la demande croissante de matériaux légers mais résistants, comme l’aluminium, les alliages à haute résistance, ou même des métaux comme le titane, les presses doivent pouvoir appliquer des forces spécifiques sans compromettre la structure du matériau. De plus, avec l’essor des composites métalliques, qui combinent les propriétés de matériaux métalliques et non métalliques, les presses doivent pouvoir s’adapter à des comportements mécaniques parfois complexes. Par exemple, certains composites peuvent se déformer différemment en fonction de la direction du fil ou de l’orientation des fibres, ce qui nécessite des ajustements précis du processus de formage.
L’utilisation de presses pour des applications de formage à chaud a également gagné en popularité, en particulier pour les matériaux résistants à la chaleur, comme les alliages métalliques utilisés dans l’industrie aérospatiale. Dans ces applications, les tôles sont chauffées à des températures très élevées avant d’être formées, ce qui permet de réduire la contrainte exercée sur le métal et d’obtenir des formes complexes sans endommager le matériau. Les presses à formage à chaud peuvent intégrer des systèmes de contrôle thermique avancés, garantissant que chaque pièce est chauffée de manière homogène, réduisant ainsi les risques de déformation et de défauts dans la pièce finale.
La simulation numérique devient un outil de plus en plus important dans la conception des presses de formage de tôle. Avant même de fabriquer la machine, les ingénieurs peuvent utiliser des logiciels de simulation pour modéliser le processus de formage, tester différentes configurations de matrices et de poinçons, et prévoir les effets des forces appliquées sur la tôle. Cela permet non seulement de réduire les coûts de prototypage, mais aussi de mieux comprendre les comportements des matériaux et de prévoir des solutions pour éviter les défauts. La simulation est particulièrement utile dans les processus de formage complexe, où les pièces nécessitent des formes géométriques complexes et où la précision est essentielle.
Dans un monde de plus en plus tourné vers la durabilité, les presses de formage de tôle jouent également un rôle clé dans la réduction des déchets. Les pressions croissantes pour rendre la production industrielle plus écologique ont conduit à une plus grande adoption du recyclage des matériaux et de la réutilisation des chutes de métal. Les presses modernes sont conçues pour minimiser les pertes de matériaux, en intégrant des systèmes de recueil et de recyclage des chutes de métal, qui peuvent être renvoyées dans le processus de production pour être refondues ou utilisées pour d’autres applications. Ce processus non seulement aide à réduire l’impact environnemental, mais aussi à diminuer les coûts des matériaux.
Les presses de formage de tôle sont également plus silencieuses et plus sûres grâce aux améliorations technologiques dans les systèmes de contrôle du bruit et dans l’ergonomie des machines. Les avancées dans les matériaux de construction des machines et les systèmes de réduction des vibrations contribuent à un environnement de travail plus confortable, tout en réduisant l’usure des machines et en prolongeant leur durée de vie. Les dispositifs de sécurité, tels que les systèmes de détection de présence et les capteurs de sécurité, ont également été améliorés pour garantir que les opérateurs ne se trouvent pas dans des zones dangereuses pendant le fonctionnement de la machine, augmentant ainsi la sécurité des travailleurs.
En somme, l’avenir des presses de formage de tôle semble être axé sur une combinaison de flexibilité, d’intelligence et de durabilité. L’introduction de systèmes connectés, l’optimisation des matériaux, l’intégration des technologies de simulation et d’automatisation, ainsi que l’accent mis sur la réduction des déchets, permettent de transformer ces équipements en solutions encore plus efficaces et adaptées aux défis de l’industrie moderne. Ces machines ne sont plus seulement des outils de production; elles deviennent des éléments clés de systèmes de fabrication intelligents, contribuant à une production plus rapide, plus précise et plus durable.
Machines de travail des tôle
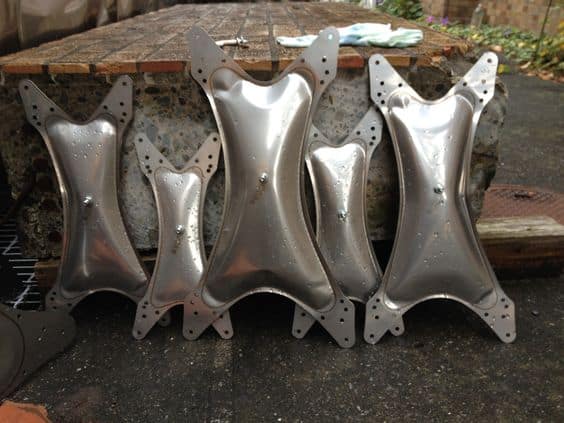
Les machines de travail des tôles sont des équipements utilisés pour transformer, façonner et modifier des tôles métalliques dans divers processus industriels. Ces machines sont essentielles dans une large gamme de secteurs, notamment l’automobile, l’aéronautique, la construction, et l’électroménager, où elles permettent de produire des pièces métalliques de formes et tailles variées à partir de feuilles ou plaques de métal.
Il existe plusieurs types de machines utilisées pour travailler les tôles, chacune étant adaptée à des applications spécifiques. Ces machines peuvent réaliser des opérations telles que le découpage, le pliage, l’emboutissage, le poinçonnage et le décapage, selon les besoins de production.
1. Cisaille à tôle
La cisaille à tôle est une machine utilisée pour couper des tôles métalliques avec une grande précision. Elle est souvent utilisée pour des découpes droites dans des tôles de différentes épaisseurs. Ce type de machine peut couper les tôles en longues bandes ou en petites sections, selon les besoins. Les modèles modernes sont souvent équipés de contrôles numériques permettant une gestion automatisée de la coupe, garantissant des découpes régulières et sans déformation.
2. Presse-plieuse
Une presse-plieuse est une machine utilisée pour plier les tôles métalliques sous un angle donné. Elle fonctionne en appliquant une pression sur une tôle à l’aide d’un poinçon et d’une matrice, créant ainsi des plis ou des angles spécifiques. Cette machine est couramment utilisée pour créer des pièces telles que des boîtes, des panneaux et des composants de carrosserie dans l’industrie automobile. Les presses-plieuses modernes peuvent être contrôlées numériquement pour offrir une précision élevée dans le pliage complexe de pièces.
3. Poinçonneuse
La poinçonneuse est une machine utilisée pour perforer ou découper des motifs dans des tôles métalliques. Elle fonctionne en faisant pénétrer un poinçon dans la tôle à travers une matrice pour créer des trous, des formes complexes, ou des découpes personnalisées. Les poinçonneuses sont couramment utilisées pour des applications de perforation, de découpage de formes complexes et de marquage dans des secteurs tels que l’automobile, l’aéronautique, et la construction métallique.
4. Machine de découpe laser
Les machines de découpe laser utilisent un faisceau laser très précis pour couper des tôles métalliques. Ces machines offrent une précision de coupe extrêmement élevée et sont capables de découper des matériaux de diverses épaisseurs avec une finition nette. La découpe laser est idéale pour des applications où une grande précision est nécessaire, telles que la production de composants électroniques, de structures métalliques complexes, ou de pièces de petite taille. La rapidité et la flexibilité du laser en font également un choix populaire pour les environnements de production à grande échelle.
5. Machine de découpe à jet d’eau
La découpe à jet d’eau utilise un jet d’eau à haute pression, parfois mélangé à des abrasifs, pour couper des tôles métalliques. Ce procédé est particulièrement adapté pour les matériaux sensibles à la chaleur, comme les métaux tendres ou les matériaux composites. Il est également utilisé pour découper des tôles épaisses avec une précision de coupe et une faible zone de chaleur affectée. Les machines de découpe à jet d’eau sont idéales pour des découpes de précision dans des environnements où la chaleur générée par d’autres procédés pourrait endommager la pièce.
6. Machine d’emboutissage
Les machines d’emboutissage sont utilisées pour transformer une tôle métallique plate en une pièce tridimensionnelle. Cela se fait en utilisant une matrice et un poinçon pour appliquer une pression sur la tôle, la formant dans des formes profondes ou des formes complexes comme des coques, des réservoirs, ou des boîtiers métalliques. Ce processus est souvent utilisé dans la production de pièces de carrosserie automobile, de composants électroniques, et de nombreux autres produits nécessitant des formes précises et profondes.
7. Machine de formage à froid
Les machines de formage à froid sont utilisées pour plier, rouler ou aplatir des tôles métalliques sans les chauffer. Ce procédé est généralement utilisé pour des modifications de forme simples mais essentielles dans des applications où les propriétés du métal doivent être préservées, comme dans la fabrication de pièces structurées et précises. Les machines de formage à froid incluent des rouleuses pour effectuer des courbes ou des torsions sur les tôles métalliques, et des laminoirs pour les aplatir ou les étirer.
8. Laminoirs
Les laminoirs sont des machines utilisées pour réduire l’épaisseur des tôles métalliques ou pour les donner des formes spécifiques, comme des rouleaux ou des plaques épaisses. En utilisant des cylindres qui exercent une pression sur la tôle, les laminages permettent de réaliser des pièces métalliques uniformes, fines et de grande qualité. Ce processus est couramment utilisé dans la production de feuilles métalliques, de bandelettes et d’autres composants dans l’industrie lourde.
9. Tôlerie robotisée
La tôlerie robotisée implique l’utilisation de robots pour effectuer diverses opérations de travail de tôle telles que la découpe, le poinçonnage, l’emboutissage, et le soudage. Ces systèmes sont particulièrement utiles pour des productions à grande échelle, où l’automatisation peut améliorer l’efficacité et réduire le temps de cycle de production. De plus, les robots peuvent être équipés de capteurs et de caméras pour effectuer des contrôles de qualité en temps réel, garantissant ainsi une production sans défaut.
10. Fraiseuses et meuleuses
Les fraiseuses et meuleuses sont des machines utilisées pour usiner les tôles métalliques en leur donnant des formes spécifiques. Elles sont utilisées pour retirer du matériau de la tôle pour créer des détails fins, des entures, des alésages, ou des découpes spécifiques. Ces machines sont idéales pour des applications nécessitant une précision extrême et un fraisage sur des matériaux difficiles à traiter avec d’autres machines de travail de tôle.
Ces machines de travail des tôles sont des éléments clés dans la production industrielle, permettant de produire une variété de pièces métalliques essentielles pour différents secteurs. Grâce aux évolutions technologiques, de nombreuses machines sont désormais équipées de systèmes de contrôle numérique et d’automatisation, ce qui permet de gagner en efficacité, de réduire les coûts et d’améliorer la précision des pièces produites.
Les machines de travail des tôles ont un rôle crucial dans l’industrie moderne, car elles permettent de transformer les tôles métalliques en pièces complexes et précises, adaptées aux besoins spécifiques de chaque secteur. La diversité des équipements disponibles garantit une flexibilité maximale dans les processus de fabrication, permettant aux fabricants de répondre à une large gamme d’exigences. Que ce soit pour de la découpe, du pliage, de l’emboutissage, ou de l’usinage, chaque type de machine offre des avantages uniques en termes de vitesse, de précision et de capacité à traiter divers matériaux.
Avec les avancées technologiques, la connectivité et l’intégration de systèmes automatisés, ces machines sont devenues plus intelligentes et plus efficaces. Les logiciels de contrôle numérique (CNC) permettent aux opérateurs de programmer les machines avec une grande précision, d’optimiser les processus et d’assurer des productions répétitives avec des résultats constants. En outre, les capteurs et la maintenance prédictive permettent une gestion proactive des machines, réduisant les risques de pannes inattendues et garantissant un taux de production élevé.
Les machines modernes sont également équipées de systèmes de gestion de la qualité qui surveillent en permanence les tolérances dimensionnelles des pièces produites, assurant ainsi que chaque produit respecte des normes strictes. L’automatisation permet non seulement de minimiser les erreurs humaines, mais aussi de réduire les coûts de main-d’œuvre, augmentant ainsi la compétitivité des entreprises qui adoptent ces technologies.
Les tendances actuelles mettent également l’accent sur la durabilité et l’écologie. De nombreuses machines de travail des tôles sont désormais conçues pour réduire leur consommation d’énergie, minimiser les déchets et optimiser le recyclage des matériaux. Les fabricants de machines de formage et de traitement des tôles mettent en œuvre des solutions pour limiter l’impact environnemental tout en maintenant une productivité élevée. L’intégration de moteurs à haute efficacité et de systèmes de récupération d’énergie est un exemple de cette approche.
En parallèle, la recherche sur de nouveaux matériaux et la demande croissante de matériaux de haute performance pousse les fabricants de machines à développer des équipements capables de traiter des tôles de plus en plus fines, mais également des matériaux plus résistants, comme les alliages à haute résistance ou les composites métalliques. Ces matériaux exigent souvent des technologies de formage et de découpe plus avancées pour éviter toute déformation ou rupture pendant le traitement.
Le développement de nouvelles technologies de découpe comme la découpe au laser et au jet d’eau a transformé la capacité de traitement des tôles, offrant des solutions extrêmement précises pour des applications de plus en plus complexes. Ces technologies, qui ne génèrent presque pas de chaleur, permettent de travailler des matériaux sensibles sans compromettre leurs propriétés. Elles ouvrent également la voie à des formes géométriques plus complexes et à des détails fins qui étaient autrefois impossibles à réaliser avec des machines traditionnelles.
Un autre aspect de cette évolution technologique réside dans l’intégration de robots industriels et d’outils collaboratifs (cobots). Ces robots travaillent en tandem avec les opérateurs pour réaliser des tâches répétitives et de précision, augmentant la productivité tout en améliorant la sécurité sur le lieu de travail. Les robots peuvent être utilisés pour des tâches comme la manutention des tôles, le chargement et déchargement des machines, ainsi que pour le contrôle de la qualité des pièces fabriquées.
Le futur des machines de travail des tôles semble être tourné vers une intégration accrue des technologies de l’industrie 4.0, avec l’utilisation de l’intelligence artificielle, du big data, et de l’analyse prédictive pour optimiser les processus de production. Ces technologies permettent non seulement de rendre les machines plus autonomes, mais aussi de créer des systèmes de production plus flexibles, capables de s’adapter à des changements rapides dans les demandes du marché. Par exemple, un système intelligent pourrait ajuster en temps réel les paramètres de fonctionnement des machines en fonction des caractéristiques spécifiques du matériau ou des variations de température, garantissant ainsi des pièces de haute qualité à chaque cycle de production.
Les machines de travail des tôles sont donc en constante évolution, et avec les avancées continues en matière de technologie de fabrication, elles permettent de produire des pièces métalliques de plus en plus complexes et adaptées aux besoins spécifiques de chaque secteur. Elles sont des éléments essentiels dans le processus de fabrication, contribuant à rendre les productions plus rapides, plus précises et plus écologiques, tout en augmentant la compétitivité des entreprises qui les utilisent.
Les machines de travail des tôles continuent d’évoluer avec l’introduction de nouvelles fonctionnalités et capacités, notamment grâce à l’intégration des technologies intelligentes et de robotique avancée. Le principal objectif des fabricants de ces machines est de garantir non seulement des gains de productivité, mais aussi une flexibilité accrue dans la fabrication. Par exemple, avec l’essor des usines connectées, les machines peuvent maintenant être reliées à des systèmes de gestion de la production (MES) et à des plateformes cloud. Cela permet de collecter et d’analyser des données en temps réel sur chaque phase de production, optimisant ainsi les processus et permettant une gestion plus agile des lignes de production.
Le contrôle de la qualité est devenu un domaine central dans le développement des machines de travail des tôles. Des systèmes de vision industrielle, alimentés par des technologies telles que l’intelligence artificielle et l’apprentissage automatique, sont de plus en plus utilisés pour surveiller la qualité des pièces produites à chaque étape du processus. Ces systèmes peuvent détecter des anomalies comme des imperfections de surface, des écarts dimensionnels ou des déformations qui ne sont pas immédiatement visibles à l’œil nu. Ils permettent ainsi d’augmenter le taux de rendement de la production et de réduire le gaspillage en permettant des ajustements en temps réel.
Les machines hybrides, qui combinent plusieurs technologies dans un même système, sont également de plus en plus courantes. Par exemple, une machine de découpe laser peut être couplée avec un système de poinçonnage ou un pliage robotisé, permettant une production continue et sans interruption. Cette approche multifonctionnelle permet d’augmenter la flexibilité et de réduire les coûts liés à la maintenance et à l’entretien, tout en permettant de traiter une large gamme de matériaux et de formes complexes.
Les machines de travail des tôles doivent également répondre à des normes strictes en matière de sécurité et d’ergonomie. Les équipements modernes intègrent des dispositifs de sécurité avancés, comme des barrières photoélectriques, des systèmes de détection de mouvement et des arrêts d’urgence automatiques. Parallèlement, les améliorations en matière de confort opératoire garantissent que les machines sont plus faciles à utiliser, avec des interfaces utilisateur intuitives et des commandes à distance. L’ergonomie a été pensée pour réduire la fatigue des opérateurs et limiter les risques d’accidents, en intégrant des commandes et des écrans de contrôle accessibles et faciles à lire.
Les évolutions dans les matériaux utilisés pour la fabrication des machines elles-mêmes sont également notables. De nombreux composants sont désormais fabriqués en alliages composites ou en matériaux à haute résistance pour augmenter la durabilité des machines et les rendre plus résistantes aux conditions de travail intenses et aux vibrations. Ces matériaux réduisent l’usure des pièces et augmentent la longévité des machines, tout en réduisant leur poids et leur consommation d’énergie.
L’un des autres défis majeurs auquel les fabricants de machines doivent faire face est celui de la modularité. En réponse à la demande croissante pour des lignes de production flexibles, certaines machines de travail des tôles sont désormais conçues pour être facilement modulaires et adaptables aux besoins de production spécifiques. Par exemple, il est désormais possible d’ajouter des modules de poinçonnage, de découpe laser ou de pliage selon les exigences du processus de fabrication, permettant aux entreprises de faire évoluer leur équipement en fonction des nouvelles demandes du marché ou des changements de conception des pièces à produire.
La durabilité environnementale est un autre aspect crucial pour l’avenir des machines de travail des tôles. Les machines sont désormais conçues pour être plus écoénergétiques et moins polluantes, intégrant des technologies pour réduire la consommation énergétique et minimiser l’empreinte carbone de la production. L’utilisation de systèmes de récupération d’énergie dans les presses ou les découpeuses, l’intégration de moteurs à haute efficacité énergétique, et la réduction des pertes de chaleur pendant les processus de fabrication contribuent à rendre l’industrie plus verte et moins gourmande en ressources.
Un autre aspect qui se développe rapidement dans les machines de travail des tôles est la personnalisation à grande échelle. Grâce à l’intégration de la fabrication additive (impression 3D) et d’autres technologies de production avancées, il est désormais possible de créer des pièces métalliques très spécifiques en petites séries tout en conservant un coût compétitif. Cette flexibilité dans la production permet aux entreprises de répondre plus rapidement aux demandes spécifiques de leurs clients, notamment dans des secteurs comme l’aérospatiale, où des pièces sur mesure sont souvent nécessaires.
Les perspectives d’avenir pour les machines de travail des tôles s’orientent clairement vers une intégration toujours plus poussée des technologies numériques et de l’automatisation, combinant réalité augmentée (RA), intelligence artificielle (IA) et internet des objets (IoT) pour une production plus intelligente, plus flexible et plus écologique. Les machines intelligentes de demain devraient pouvoir s’ajuster automatiquement en fonction des données collectées en temps réel, tout en permettant aux entreprises de réagir rapidement aux fluctuations du marché et d’optimiser les coûts de production.
En résumé, les machines de travail des tôles sont en pleine transformation, intégrant des technologies avancées pour répondre à des exigences de plus en plus complexes. L’automatisation, la connectivité, la durabilité et la flexibilité sont désormais des caractéristiques essentielles de ces équipements, qui permettent aux entreprises de rester compétitives dans un monde en constante évolution.
Équipements de mise en forme de tôle métallique
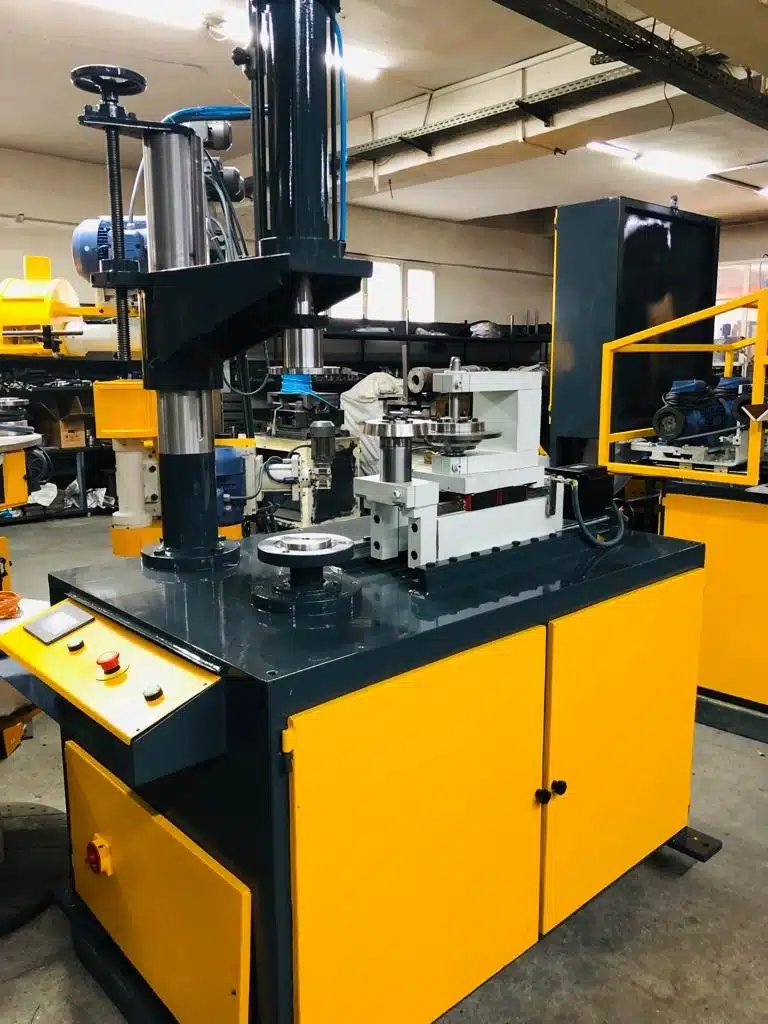
Les équipements de mise en forme de tôle métallique sont des machines utilisées dans l’industrie pour transformer des tôles métalliques plates en formes tridimensionnelles ou en pièces spécifiques en fonction des besoins de production. Ces équipements permettent de réaliser une gamme d’opérations, telles que le pliage, l’emboutissage, le poinçonnage, et le roulage, afin de produire des pièces métalliques de forme et de taille variées.
Voici un aperçu des principaux équipements utilisés pour la mise en forme des tôles métalliques :
1. Presse-plieuse
La presse-plieuse est un équipement essentiel pour le pliage des tôles métalliques. Elle est utilisée pour appliquer une force sur une tôle afin de la plier sous un angle précis. La presse-plieuse fonctionne généralement à l’aide d’un poinçon et d’une matrice, qui déterminent l’angle de pliage et la forme souhaitée de la pièce. Les presses-plieuses modernes sont équipées de commandes numériques (CNC) pour une précision maximale et permettent de réaliser des plis complexes dans des tôles de différentes épaisseurs et tailles.
2. Rouleurs de tôle
Les rouleurs de tôle sont utilisés pour courber ou rouler des tôles métalliques pour leur donner une forme cylindrique ou incurvée. Ce processus est couramment utilisé dans la fabrication de tuyaux, de coques, ou d’autres pièces circulaires. Les rouleuses utilisent des cylindres rotatifs pour appliquer une pression uniforme sur la tôle, lui donnant ainsi une forme continue et régulière. Elles peuvent être utilisées pour des matériaux de diverses épaisseurs et sont essentielles dans l’industrie du bâtiment, de la construction navale, et de la fabrication de réservoirs.
3. Machine d’emboutissage
Les machines d’emboutissage sont utilisées pour transformer une tôle métallique plate en une forme tridimensionnelle en utilisant une matrice et un poinçon. Ce processus est utilisé pour créer des pièces telles que des coques, des réservoirs, des boîtiers électroniques, ou des pièces de carrosserie automobile. L’emboutissage est un processus crucial dans la fabrication de pièces métalliques profondes et complexes. Les machines modernes peuvent être équipées de systèmes de contrôle automatisé pour améliorer la précision et la vitesse du processus.
4. Poinçonneuse
Les poinçonneuses sont des machines utilisées pour réaliser des découpes ou des perforations dans des tôles métalliques. Ce processus est essentiel pour produire des trous, des formes spécifiques, ou des motifs dans des tôles. La poinçonneuse utilise un poinçon qui pénètre dans la tôle, créant ainsi des perforations. Elle peut être utilisée pour des applications allant de la production de pièces automobiles à la création de composants électroniques. Les poinçonneuses à commande numérique permettent d’effectuer des découpes très précises et complexes.
5. Machine de découpe laser
Les machines de découpe laser utilisent un faisceau laser pour couper avec une grande précision des tôles métalliques. Ce procédé est particulièrement adapté pour des découpes complexes ou de petites pièces nécessitant une précision extrême. Le laser est capable de découper des tôles de différentes épaisseurs et matériaux, avec une finition nette et sans déformation. Ce type de machine est largement utilisé dans des secteurs tels que l’automobile, l’aéronautique, et la production de composants industriels.
6. Machine de découpe à jet d’eau
La découpe à jet d’eau est une méthode qui utilise un jet d’eau à haute pression, parfois mélangé à un abrasif, pour découper des tôles métalliques. Cette technique est idéale pour les matériaux sensibles à la chaleur ou ceux qui ne peuvent pas être coupés à l’aide d’autres méthodes de découpe, comme les métaux tendres ou les matériaux composites. La découpe à jet d’eau est également utilisée pour découper des tôles métalliques épaisses, offrant une précision de coupe et une zone de chaleur affectée minimisée.
7. Plieuse hydraulique
La plieuse hydraulique est similaire à la presse-plieuse, mais elle utilise un système hydraulique pour appliquer la force nécessaire pour plier la tôle. Ces machines sont particulièrement adaptées pour plier des tôles de grande épaisseur et permettent d’obtenir des plis très nets et réguliers. Elles sont souvent utilisées dans la production de pièces métalliques pour des applications de construction, de fabrication de meubles, et dans l’industrie automobile.
8. Plieuse à rouleaux
La plieuse à rouleaux est utilisée pour plier des tôles métalliques de manière à leur donner une courbure précise. Ce processus est couramment utilisé pour des applications où une forme continue est nécessaire, comme dans la fabrication de réservoirs, de tuyaux et d’autres pièces rondes ou cylindriques. Ce type de machine est particulièrement utile pour le travail de tôles de grande taille et de matériaux plus épais.
9. Fraiseuse pour tôles
Les fraiseuses pour tôles sont des machines utilisées pour usinage ou finishing des tôles métalliques, permettant de créer des détails fins comme des entures ou des cavités dans les pièces métalliques. Ces machines utilisent des outils rotatifs pour enlever de la matière et peuvent être équipées de différentes têtes de coupe pour des applications spécifiques. Les fraiseuses sont couramment utilisées dans les industries aéronautique, automobile, et électronique.
10. Laminoirs
Les laminoirs sont utilisés pour réduire l’épaisseur des tôles métalliques ou pour les façonner sous des formes spécifiques, comme des plaques, des bandes, ou des feuilles métalliques. Les laminages permettent d’obtenir des tôles métalliques de différentes épaisseurs tout en préservant leur intégrité structurale. Les machines de laminoir sont couramment utilisées dans la production de métaux de construction, aluminium, et acier pour diverses applications industrielles.
11. Machine de formage à froid
Les machines de formage à froid sont utilisées pour appliquer des formes spécifiques aux tôles métalliques sans les chauffer. Ce processus est utilisé pour plier, rouler ou étirer les tôles en des formes précises. Le formage à froid est particulièrement avantageux pour des matériaux qui ne doivent pas être chauffés pour conserver leurs propriétés mécaniques. Ce type de machine est utilisé dans des secteurs tels que l’automobile et l’équipement industriel.
12. Robot de manipulation de tôle
Les robots de manipulation de tôle sont utilisés pour automatiser les tâches de chargement et déchargement des machines de travail des tôles, ainsi que pour positionner les pièces pendant le processus de formage. Ces robots peuvent être programmés pour effectuer des tâches spécifiques telles que le placement des tôles dans les machines, le retour des pièces finies ou la manutention de tôles grandes dimensions. L’utilisation de robots dans la mise en forme des tôles permet de réduire les risques d’accidents et d’améliorer la productivité.
Ces équipements de mise en forme de tôle sont essentiels pour de nombreux secteurs industriels et permettent de fabriquer une large gamme de produits allant de composants automobiles à des structures métalliques complexes. Les progrès dans les technologies de fabrication, y compris l’automatisation, la robotique et l’intégration des systèmes numériques, continuent d’améliorer la précision, la vitesse, et la flexibilité de ces équipements, tout en réduisant les coûts de production et les risques d’erreurs.
Les équipements de mise en forme de tôle métallique continuent de jouer un rôle essentiel dans la production industrielle, facilitant la transformation de matériaux plats en pièces complexes utilisées dans divers secteurs. Au fur et à mesure que les technologies avancent, ces machines deviennent de plus en plus sophistiquées, intégrant des capacités automatisées, des contrôles numériques et des matériaux innovants pour améliorer l’efficacité et la qualité des produits finis. L’un des aspects majeurs des machines modernes est la capacité d’intégration avec des systèmes de gestion de la production (MES) et des outils de contrôle qualité automatisés, permettant une surveillance continue des performances des machines et une optimisation des processus en temps réel. Cela garantit non seulement une production plus rapide, mais aussi une précision accrue et une réduction des erreurs humaines.
Les avancées en matière de contrôle numérique (CNC) permettent une programmation plus intuitive des équipements de mise en forme, ce qui facilite la création de pièces avec des géométries complexes. Ces systèmes offrent des fonctionnalités avancées telles que la simulation des processus de fabrication avant la production réelle, ce qui permet de détecter les problèmes potentiels et de les corriger à l’avance, réduisant ainsi le gaspillage de matériel et le temps de mise en production. L’utilisation de capteurs intelligents dans les machines de formage de tôle permet également de surveiller en temps réel les paramètres de production, comme la température, la pression et la force appliquée sur la tôle, garantissant une homogénéité des produits tout au long du processus.
Les machines de mise en forme de tôle bénéficient aussi d’améliorations en matière de maintenance prédictive. Grâce à l’intégration de systèmes IoT (Internet of Things), il est possible de collecter et d’analyser des données en temps réel sur l’état de la machine, anticipant ainsi les pannes avant qu’elles ne surviennent. Cela permet aux entreprises de planifier des interventions de maintenance de manière plus efficace, de prolonger la durée de vie de leurs équipements et de réduire les coûts associés aux arrêts de production non planifiés.
En outre, avec la demande croissante de produits plus personnalisés, les équipements de mise en forme de tôle sont devenus plus flexibles, permettant une adaptation rapide aux modifications des spécifications des produits. Par exemple, dans le secteur automobile, où la production de pièces sur mesure est fréquente, les machines de formage de tôle peuvent facilement être reconfigurées pour produire des composants de différentes tailles et formes sans nécessiter de changement complet de configuration. Ce degré de flexibilité est possible grâce à l’automatisation et aux contrôles numériques avancés, permettant aux entreprises de répondre plus rapidement aux demandes des clients tout en maintenant des coûts de production compétitifs.
La durabilité est également un facteur clé dans l’évolution des équipements de mise en forme de tôle. Avec une prise de conscience accrue des enjeux environnementaux, les fabricants se concentrent sur la réduction de la consommation d’énergie et l’optimisation de l’usage des matériaux. Les technologies telles que le recyclage des chutes de métal, l’optimisation de la coupe et la réduction des émissions de gaz à effet de serre sont intégrées dans de plus en plus de machines. Cela permet non seulement de rendre la production plus écologique, mais aussi de réduire les coûts associés à l’achat de nouveaux matériaux et à l’élimination des déchets.
Le secteur des matériaux utilisés pour la fabrication des machines est aussi en pleine évolution. De plus en plus, les fabricants de machines utilisent des alliages spéciaux, des matériaux composites et des revêtements innovants pour augmenter la résistance à l’usure et à la corrosion des équipements, ce qui permet d’étendre leur durée de vie tout en réduisant les coûts d’entretien. Ces matériaux de haute performance sont particulièrement importants pour les machines qui doivent supporter des conditions de travail extrêmes, comme les presses de formage ou les poinçonneuses utilisées pour traiter des tôles épaisses ou des matériaux particulièrement abrasifs.
L’évolution des interfaces utilisateurs est un autre aspect de la modernisation des machines de mise en forme de tôle. De plus en plus, les machines intègrent des écrans tactiles interactifs, des tableaux de bord intuitifs et des systèmes de commande à distance permettant aux opérateurs de contrôler et de superviser plusieurs machines à partir d’un seul poste de travail. Cela réduit la complexité de l’opération et permet d’augmenter l’efficacité des processus, en particulier dans les environnements de production à grande échelle. Par ailleurs, l’intégration de réalité augmentée dans la formation et la maintenance des machines permet d’offrir une assistance en temps réel pour diagnostiquer des problèmes ou optimiser les réglages des équipements, améliorant ainsi la productivité et la réduction des erreurs.
À mesure que les besoins industriels évoluent, les équipements de mise en forme de tôle s’adaptent également aux nouvelles exigences en matière de produits complexes et de performance. Les industries aérospatiale, automobile, et électronique demandent des pièces de plus en plus petites, légères, mais aussi d’une grande précision. Les machines de formage de tôle doivent donc être capables de répondre à ces exigences tout en maintenant des normes de qualité élevées et en respectant des délais de production serrés. Dans ce contexte, les avancées en matière de technologie de formage, telles que l’intégration de procédés hybrides (comme l’emboutissage combiné à la découpe laser) ou la capacité de former des matériaux composites, ouvrent de nouvelles perspectives pour la fabrication de composants de plus en plus complexes.
En somme, l’innovation continue dans les équipements de mise en forme de tôle permet d’améliorer non seulement la productivité et la qualité, mais aussi de répondre aux défis modernes, comme l’automatisation, la flexibilité, l’efficacité énergétique, et la durabilité. Ces machines sont devenues des outils incontournables dans un environnement de production en constante évolution, où la compétitivité et la rapidité de réaction aux besoins du marché sont essentielles.
Les équipements de mise en forme de tôle ne se limitent pas simplement à des outils de transformation physique des matériaux. Ils jouent également un rôle crucial dans l’optimisation des processus de fabrication grâce à l’intégration de technologies avancées. L’un des progrès les plus notables réside dans l’utilisation croissante de l’automatisation et de l’intelligence artificielle pour superviser et ajuster les paramètres de production en temps réel. Grâce à des algorithmes d’optimisation basés sur des données en provenance de capteurs intelligents, ces machines peuvent ajuster automatiquement les vitesses de coupe, les températures, ou les pressions appliquées, ce qui améliore la précision des pièces tout en réduisant les déchets et en augmentant le rendement.
La maintenance prédictive, qui repose sur l’analyse de données provenant des machines, devient également un aspect essentiel de l’industrie moderne de la mise en forme de tôle. Grâce à la surveillance continue des conditions de fonctionnement des machines et à l’utilisation de modèles analytiques, il est désormais possible de prédire les pannes avant qu’elles ne surviennent. Par exemple, les capteurs de vibration ou de température installés sur les presses ou les rouleuses peuvent fournir des informations qui permettent de détecter des signes précoces de défaillance. Cette approche réduit non seulement les coûts liés à des arrêts imprévus, mais elle améliore aussi la durée de vie des équipements et garantit une production continue et fluide.
La demande croissante pour des produits plus légers et plus résistants a également conduit à l’évolution des matériaux utilisés dans les processus de mise en forme de tôle. De nouvelles alliages métalliques, comme les alliages à haute résistance ou les composites métalliques, sont de plus en plus utilisés, nécessitant des machines capables de travailler sur ces matériaux complexes. Les équipements de formage doivent être conçus pour offrir une flexibilité maximale et s’adapter rapidement aux nouveaux matériaux tout en maintenant des niveaux de qualité stricts. Par exemple, des presses de formage plus robustes et plus puissantes sont capables de travailler sur des tôles métalliques très résistantes tout en préservant les caractéristiques mécaniques et structurelles du matériau.
Les machines de formage de tôle à grande échelle, utilisées dans les industries telles que l’automobile, l’aérospatiale et la construction navale, ont vu des avancées significatives en matière de production de pièces complexes. Ces machines sont capables de produire des composants avec des formes géométriques très compliquées et des tolérances extrêmement serrées, nécessaires pour des applications exigeantes. Dans l’automobile, par exemple, les pièces de carrosserie sont de plus en plus fabriquées à partir de tôles métalliques à haute résistance, qui doivent être formées avec une grande précision pour répondre aux exigences strictes en matière de sécurité et de performance. L’introduction de matériaux légers, comme l’aluminium et les alliages en magnésium, a également conduit à la mise au point de nouvelles techniques de formage adaptées, telles que le formage superplastique ou le formage à haute température.
Un autre domaine dans lequel les équipements de mise en forme de tôle ont évolué est l’intégration de systèmes robotisés. L’automatisation des processus, notamment grâce à l’utilisation de robots industriels, permet d’effectuer des tâches répétitives, comme le chargement/déchargement des tôles, ou de manipuler des pièces de manière plus sûre et plus efficace. Les robots de soudage et les robots de manipulation de pièces sont désormais utilisés pour exécuter des opérations de mise en forme et de finition sur des tôles métalliques avec une précision accrue, réduisant ainsi le risque d’erreurs humaines et augmentant la vitesse de production. Les robots peuvent aussi être équipés de systèmes visuels intelligents qui leur permettent de détecter et de traiter des défauts sur les pièces, garantissant ainsi une qualité constante des produits finis.
Les équipements modernes de mise en forme de tôle intègrent également des technologies de simulation qui permettent de tester et d’optimiser les processus de production avant de commencer la fabrication réelle. La simulation par éléments finis (FEM) est utilisée pour prédire la déformation des tôles sous l’effet de forces appliquées, permettant ainsi de concevoir des processus de formage plus efficaces et d’éviter les défauts de fabrication. En simulant les différents stades de l’opération de formage, les ingénieurs peuvent optimiser les paramètres de processus, tels que la vitesse, la pression et la température, et anticiper les déformations ou les ruptures potentielles. Cette approche préventive réduit non seulement les coûts liés aux erreurs, mais elle permet aussi d’améliorer la durabilité des pièces produites.
En matière de flexibilité de production, les équipements modernes sont de plus en plus capables de s’adapter rapidement à des séries de production de petites tailles. Cela est particulièrement important dans des secteurs comme l’automobile, où la demande de personnalisation des véhicules augmente. Les machines peuvent maintenant changer de configuration et d’outils de manière plus rapide et plus efficace grâce à des systèmes de commande automatisés, permettant ainsi une adaptation plus souple aux besoins du marché tout en réduisant le temps de mise en place entre les séries de production.
Les équipements de mise en forme de tôle sont également en train de se transformer sous l’influence de la fabrication additive (impression 3D). Bien que les machines de formage de tôle restent dominantes pour la production de grandes séries de pièces métalliques, la fabrication additive permet de fabriquer des outils ou des composants personnalisés avec des géométries complexes qui ne peuvent être réalisées avec des méthodes traditionnelles de formage. De plus en plus, des machines hybrides, combinant le formage traditionnel avec des techniques de fabrication additive, commencent à émerger, permettant la production de pièces métalliques de manière plus flexible et avec moins de gaspillage de matériaux.
Les préoccupations environnementales influencent également la conception des machines de mise en forme de tôle. Les fabricants cherchent à améliorer l’efficacité énergétique des équipements et à réduire leur empreinte écologique. Des technologies comme le récupération de chaleur et les systèmes de filtration améliorés sont de plus en plus utilisés pour réduire la consommation d’énergie et minimiser les émissions de gaz à effet de serre, contribuant ainsi à rendre les processus de fabrication plus durables.
Enfin, avec la montée des marchés mondiaux et la concurrence croissante, les entreprises investissent dans des équipements de mise en forme de tôle plus rapides, précis, et économiques. Le contrôle de la chaîne d’approvisionnement et la réduction des coûts de production sont des facteurs cruciaux, et l’innovation technologique dans les machines de formage de tôle est devenue un levier stratégique pour maintenir la compétitivité. Les entreprises cherchent à rationaliser leur production tout en offrant une plus grande variété de produits personnalisés, tout en optimisant la durée de vie de leurs équipements et en maintenant des coûts d’entretien réduits.
En conclusion, les équipements de mise en forme de tôle continuent d’évoluer dans un monde où la demande de produits plus complexes, personnalisés et durables augmente. L’intégration de technologies avancées, telles que l’automatisation, l’intelligence artificielle, et la fabrication additive, ainsi que la prise en compte des enjeux environnementaux, assurent que ces machines restent à la pointe de l’innovation industrielle.
Machines de mise en forme de tôles fines

Les machines de mise en forme de tôles fines sont spécifiquement conçues pour travailler des matériaux métalliques d’une épaisseur réduite, souvent utilisées dans des secteurs comme l’automobile, l’électronique, l’aérospatiale, et la fabrication de composants fins pour des appareils électroménagers. Ces tôles fines nécessitent des équipements spécialisés afin d’assurer une précision extrême et une qualité de surface impeccable.
Voici un aperçu des différents types de machines utilisées pour le formage de tôles fines et des techniques associées :
1. Presses à estampe (Presses à emboutir)
Les presses à estampe sont des équipements essentiels dans le formage des tôles fines. Elles sont utilisées pour réaliser des emboutissements, des poinçonnages et des pliages. Ces presses utilisent une matrice et un poinçon pour appliquer une force importante sur la tôle, modifiant sa forme selon la géométrie de l’outil. Ces presses peuvent être de différents types :
- Presses mécaniques : Utilisent un moteur pour générer une force qui est transmise au poinçon.
- Presses hydrauliques : Utilisent la pression hydraulique pour appliquer une force plus régulière et contrôlable, idéale pour des tôles plus fines.
2. Machines de découpe au laser
La découpe au laser est une technique très utilisée pour la découpe de tôles fines, particulièrement lorsqu’une précision extrême est nécessaire. Les machines de découpe au laser utilisent un faisceau laser à haute température pour fondre ou vaporiser le métal, créant des coupes nettes et complexes. Cette méthode est très efficace pour les tôles fines car elle minimise les déformations thermiques et permet une grande flexibilité dans la conception des pièces.
3. Poinçonneuses
Les poinçonneuses sont couramment utilisées pour perforer, découper, et façonner les tôles fines. Elles sont capables de créer des trous, des formes complexes ou des découpes de contour à grande vitesse et avec une grande précision. Ces machines sont particulièrement adaptées aux séries de production en grande quantité. Le processus est généralement très rapide et peut être automatisé avec des changeurs de tourelle pour intégrer différentes matrices et poinçons sans interruption de la production.
4. Machines à plier (Plieuse)
Les plieuses sont utilisées pour plier les tôles fines à des angles précis. Elles peuvent être hydrauliques ou électriques et permettent de créer des bords nets et réguliers sans endommager la tôle. La précision du pliage est particulièrement cruciale pour les tôles fines, car des déformations ou des irrégularités peuvent affecter la fonctionnalité des pièces finales. Certaines plieuses intègrent également des systèmes CNC (commande numérique par ordinateur) pour automatiser les réglages et permettre des ajustements en temps réel, ce qui garantit une grande précision sur de grandes séries de production.
5. Machines de laminage
Les machines de laminage sont utilisées pour réduire l’épaisseur des tôles fines, en les faisant passer entre deux cylindres rotatifs. Ce processus est essentiel dans la production de tôles de très fine épaisseur et permet de créer des matériaux avec des propriétés mécaniques spécifiques, comme la résistance à la traction ou à la flexibilité. Le laminage est généralement une étape préalable avant d’autres opérations de formage.
6. Formage par traction
Le formage par traction est un procédé où la tôle est tirée sur une matrice à l’aide d’une force de traction. Ce procédé est utilisé pour obtenir des formes profondes et complexes, comme des boîtiers, des panneaux et des coques. Il est souvent utilisé pour des matériaux métalliques fins dans l’industrie automobile, où des pièces comme les carrosseries de voitures doivent être formées avec une grande précision tout en maintenant une légèreté.
7. Machines de formage rotatif
Les machines de formage rotatif utilisent un système de rotation pour appliquer une pression sur la tôle, la déformant de manière uniforme. Ce procédé est couramment utilisé pour former des pièces cylindriques ou courbées, comme des tuyaux ou des réservoirs. L’un des avantages de cette technologie est qu’elle permet de travailler sur des tôles fines tout en maintenant des tolérances serrées.
8. Soudage par points (et autres techniques de soudage)
Bien que le soudage ne soit pas un procédé de formage à proprement parler, de nombreuses machines de mise en forme de tôles fines intègrent des techniques de soudage par points, utilisées pour assembler les tôles métalliques entre elles après leur formage. Le soudage par points est particulièrement adapté aux tôles fines, car il permet de joindre les pièces sans trop affecter leur structure ou leur forme.
9. Équipements de contrôle de qualité
Lors de la mise en forme de tôles fines, il est essentiel de garantir que la qualité de surface et les dimensions des pièces respectent des tolérances très strictes. Pour ce faire, les machines modernes sont souvent équipées de systèmes de contrôle de qualité automatisés, tels que des capteurs de vision, des dispositifs de mesure laser ou des systèmes de mesure 3D. Ces outils permettent de vérifier en temps réel la qualité des pièces, détectant immédiatement toute déviation par rapport aux spécifications.
Avantages de la mise en forme des tôles fines :
- Précision élevée : Les machines modernes permettent un contrôle de précision minutieux, garantissant des tolérances très serrées.
- Flexibilité : Grâce à des systèmes CNC et des ajustements automatisés, ces machines sont capables de s’adapter rapidement à des séries de production de tailles variables.
- Réduction des déchets : Les techniques comme la découpe au laser ou le poinçonnage sont très efficaces, minimisant le gaspillage de matériel.
- Automatisation : Les machines modernes permettent de réduire l’intervention humaine, ce qui réduit les risques d’erreurs et augmente la vitesse de production.
- Qualité de surface : Les équipements de mise en forme de tôles fines sont conçus pour garantir une qualité de surface lisse et sans défaut, essentiel dans des secteurs comme l’électronique ou l’automobile.
Conclusion
Les machines de mise en forme de tôles fines jouent un rôle clé dans de nombreuses industries, en particulier celles où la précision et la qualité de surface sont cruciales. Grâce aux progrès de la technologie, ces machines deviennent de plus en plus flexibles, efficaces et précises, permettant aux fabricants de produire des pièces de plus en plus complexes tout en maintenant des coûts de production compétitifs. Les avancées en automatisation, en contrôle qualité, et en intégration de systèmes intelligents ouvrent des perspectives prometteuses pour l’avenir du formage des tôles métalliques fines.
Les machines de mise en forme de tôles fines jouent un rôle essentiel dans divers secteurs industriels. Elles sont utilisées pour créer des pièces métalliques de petite épaisseur avec des tolérances serrées et une haute précision. Parmi les procédés les plus courants, on retrouve la découpe, l’emboutissage, le pliage et le formage par traction, chacun nécessitant des équipements spécifiques pour répondre aux exigences des applications. Les presses à estampe, par exemple, sont très courantes pour la transformation de tôles fines et permettent de réaliser des pièces complexes avec des contours bien définis. De même, la découpe au laser permet une grande précision, surtout pour des géométries complexes et des contours très détaillés. Cette technique, utilisée avec des machines de découpe laser haute puissance, fait fondre ou vaporise la tôle par un faisceau laser concentré, permettant des découpes nettes et sans distorsion thermique.
Le poinçonnage est également un procédé largement utilisé, où des poinçons viennent perforer la tôle pour y créer des trous ou des formes complexes, avec une précision qui reste constante même sur de grandes séries. Les poinçonneuses modernes sont dotées de tourelles rotatives, permettant de changer rapidement les outils de coupe et d’optimiser le temps de production. Les plieuses, quant à elles, permettent de réaliser des angles précis sur les tôles fines, une étape essentielle dans de nombreuses fabrications, notamment pour des pièces utilisées dans l’industrie de la carrosserie automobile ou pour la fabrication de composants électroniques. Ces machines peuvent être automatisées à l’aide de systèmes CNC pour une plus grande flexibilité et une plus grande précision dans la gestion des commandes.
Le formage par traction, utilisé pour transformer des tôles fines en pièces plus profondes et complexes, est essentiel pour la production de composants avec des courbes ou des formes spécifiques. Ce procédé est souvent employé dans des secteurs où les pièces doivent être légères tout en étant suffisamment solides, comme dans l’industrie automobile ou aéronautique. Les machines de formage rotatif, utilisées pour des pièces cylindriques ou courbées, sont aussi très populaires pour travailler sur des tôles fines, notamment dans la fabrication de tuyaux, réservoirs ou autres structures tubulaires.
Le laminage est une autre étape importante dans la transformation de la tôle fine. Ce procédé consiste à faire passer la tôle entre des cylindres rotatifs pour la réduire à une épaisseur uniforme, tout en modifiant ses propriétés mécaniques. Les tôles obtenues sont souvent utilisées comme matériau de base pour d’autres processus de formage, assurant une grande uniformité de matière avant d’être façonnées en produits finis.
Les équipements modernes intègrent souvent des systèmes de contrôle de qualité en temps réel, qui mesurent automatiquement les dimensions et la surface des pièces afin d’assurer leur conformité aux spécifications. Ces systèmes peuvent utiliser des capteurs laser ou des caméras de vision pour détecter toute déviation par rapport aux normes, permettant ainsi d’ajuster rapidement les paramètres de la machine et de garantir un produit final sans défaut. Grâce à l’automatisation et à l’optimisation des paramètres de production, les machines de mise en forme de tôles fines permettent une production à grande échelle tout en réduisant le risque d’erreurs humaines et en maximisant l’efficacité du processus.
En parallèle, l’industrie se dirige de plus en plus vers des machines hybrides qui intègrent des technologies de fabrication additive, comme l’impression 3D, pour créer des composants métalliques complexes avec des propriétés spécifiques tout en minimisant les déchets. Ces technologies permettent d’élargir les possibilités de conception et de fabrication, ouvrant la voie à une personnalisation accrue des pièces. Les progrès en matière de robotisation, avec des robots automatisés intégrés dans la chaîne de production, ont également permis d’améliorer l’efficacité des machines de mise en forme de tôles fines en optimisant les opérations de manipulation et d’assemblage des pièces.
Ainsi, les machines de mise en forme de tôles fines continuent d’évoluer grâce à l’intégration de technologies avancées et à l’amélioration constante des processus industriels. Ces progrès permettent non seulement de répondre aux besoins croissants de production à grande échelle, mais aussi d’assurer une plus grande précision, une réduction des coûts et une meilleure durabilité des équipements, tout en répondant aux standards de qualité de plus en plus stricts dans des secteurs comme l’aérospatiale, l’automobile et l’électronique.
Avec l’évolution continue des technologies, les machines de mise en forme de tôles fines intègrent de plus en plus des systèmes intelligents qui permettent une gestion optimisée des processus de production. Ces systèmes incluent des algorithmes d’intelligence artificielle (IA) et des capteurs avancés qui surveillent en permanence les conditions de travail des machines. Par exemple, les systèmes d’intelligence artificielle peuvent analyser les données en temps réel pour ajuster automatiquement les paramètres de pression, de température ou de vitesse de découpe, permettant ainsi de réduire les erreurs humaines et d’optimiser la consommation d’énergie.
Les machines de formage de tôles fines, qui étaient autrefois principalement contrôlées manuellement, deviennent ainsi de plus en plus autonomes. Cela est particulièrement vrai pour les presses hydrauliques et les plieuses modernes qui intègrent des systèmes CNC (commande numérique par ordinateur) avancés. Ces systèmes permettent non seulement un réglage très précis des outils, mais également la possibilité de créer des programmes de production entièrement automatisés, capables de produire une grande variété de pièces à partir de différentes géométries et matériaux, le tout avec un minimum d’intervention humaine.
Les capteurs de vision et les caméras haute définition intégrés dans ces machines permettent d’inspecter les tôles à chaque étape du processus de fabrication. Cela inclut des inspections en temps réel pour détecter des défauts de surface, des erreurs dimensionnelles ou des irrégularités dans les découpes. L’inspection automatique améliore non seulement la qualité du produit final, mais elle permet également de détecter des anomalies dès les premières étapes de la production, évitant ainsi des gaspillages importants et des coûts de production liés à des erreurs non détectées.
L’utilisation des systèmes de maintenance prédictive fait également partie de l’arsenal technologique des machines modernes de mise en forme de tôles fines. Ces systèmes collectent des données à partir de différents capteurs placés sur les machines, tels que des capteurs de vibration, des capteurs de température, ou encore des compteurs de cycles, afin de prévoir les pannes avant qu’elles ne surviennent. Cela permet aux entreprises de planifier des maintenances régulières et de minimiser les arrêts imprévus. Cette approche permet d’optimiser le rendement de la production tout en augmentant la durée de vie des machines.
En matière de flexibilité de production, les machines actuelles de mise en forme de tôles fines sont capables de travailler non seulement sur des matériaux métalliques classiques comme l’acier, l’aluminium ou le cuivre, mais aussi sur des alliages plus sophistiqués, tels que les matériaux à haute résistance ou les composites métalliques. Ces matériaux, bien qu’ayant des propriétés mécaniques supérieures, présentent souvent des défis supplémentaires lors du formage, notamment en termes de contrôle de la température ou de vitesse de formage. Les machines modernes sont donc de plus en plus polyvalentes et capables de s’adapter à une grande variété de matériaux, ce qui permet aux entreprises de rester compétitives dans des marchés de plus en plus diversifiés.
L’un des principaux défis dans le formage des tôles fines réside dans le contrôle des déformations qui peuvent se produire pendant le processus. Par exemple, dans le pliage, une déformation excessive peut entraîner des écarts de tolérances ou des casses. Les machines de formage modernes intègrent des mécanismes de compensation automatisés qui ajustent en temps réel les forces appliquées, compensant les variations qui peuvent survenir en raison de l’élasticité du matériau ou des variations de température.
Le formage multi-étapes est également une tendance croissante. Plutôt que de se limiter à une seule opération, les équipements modernes permettent de réaliser plusieurs opérations sur une même machine, en réduisant les cycles de production. Par exemple, une presse peut être équipée de plusieurs modules de formage permettant non seulement d’effectuer des emboutissements mais aussi des pliages ou des découpes, le tout en une seule passe. Cela non seulement augmente l’efficacité de la production, mais améliore également la précision des pièces, car les différents processus sont réalisés dans une séquence contrôlée, réduisant les risques d’erreurs entre les étapes.
Dans les industries de haute technologie comme l’aérospatiale, le contrôle de la qualité est particulièrement rigoureux, et les machines de mise en forme de tôles fines doivent répondre à des normes strictes en matière de tolérances et de propriétés mécaniques des matériaux. Pour répondre à ces exigences, les machines sont de plus en plus équipées de systèmes de mesure en ligne qui permettent de vérifier en temps réel la qualité des produits finis sans interrompre la production. Ces systèmes de mesure peuvent analyser la dureté, la résistance et la composabilité des matériaux, garantissant ainsi que chaque pièce respecte les critères techniques nécessaires à son utilisation finale.
En parallèle, l’optimisation énergétique devient un enjeu majeur dans la conception des machines de mise en forme de tôles fines. Les machines à faible consommation énergétique sont non seulement plus écologiques, mais elles permettent également de réduire les coûts de production. Des technologies comme le récupérateur de chaleur ou l’utilisation de systèmes à fréquence variable pour les moteurs sont de plus en plus courantes. Ces innovations permettent de limiter l’empreinte carbone des processus industriels tout en augmentant l’efficacité globale des machines.
Enfin, l’aspect durabilité et la réduction des déchets sont des objectifs croissants dans l’industrie. Les machines modernes sont conçues pour minimiser les pertes de matériaux grâce à des procédés de découpe ultra-précis et à des techniques de recyclage des chutes. Les matériaux recyclés peuvent être réintégrés dans le processus de production, contribuant ainsi à la durabilité et à la réduction des coûts de fabrication.
Ainsi, avec la convergence des technologies avancées, les machines de mise en forme de tôles fines deviennent de plus en plus intelligentes, flexibles et écologiques. Elles permettent de produire des pièces métalliques d’une qualité et d’une précision exceptionnelles tout en optimisant les coûts, les délais et l’impact environnemental. Dans un monde où les exigences des consommateurs évoluent constamment et où la compétitivité est clé, ces avancées technologiques sont essentielles pour permettre aux industries de répondre aux défis du marché global.
Outils de production pour le formage de tôle
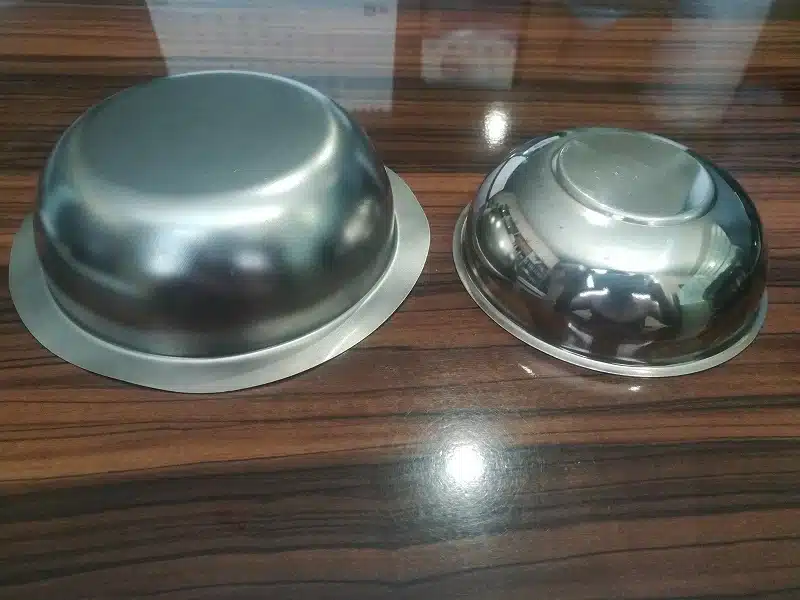
Les outils de production pour le formage de tôle sont des équipements spécialisés utilisés dans les processus de transformation des tôles métalliques. Ces outils sont conçus pour effectuer des opérations de découpe, de pliage, d’emboutissage, de perforation et d’autres formes de déformation plastique des tôles métalliques. Ils sont essentiels pour la production de pièces aux formes variées et complexes, avec des tolérances très strictes. Voici un aperçu des principaux outils utilisés dans la production de tôles métalliques :
1. Matrices et poinçons
Les matrices et poinçons sont des éléments clés dans le processus de découpe et de poinçonnage. Ils sont utilisés dans des machines comme les poinçonneuses ou les presses à estampe pour couper ou perforer des tôles métalliques.
- Poinçon : Il s’agit d’un outil de coupe qui applique une pression pour perforer la tôle. Il est généralement en forme de cône ou de cylindre et peut être ajusté pour créer des trous, des formes spécifiques ou des contours.
- Matrice : La matrice est la pièce qui reçoit la tôle et guide le poinçon pour créer la forme désirée. Les matrices peuvent être de différentes formes, permettant des coupes ou des perforations avec des géométries variées.
2. Outils de pliage
Les outils de pliage sont utilisés pour déformer la tôle afin de lui donner un angle ou une forme spécifique. Ils sont utilisés dans les plieuses pour créer des angles ou des courbes.
- Matrice de pliage : Cette matrice est conçue pour recevoir la tôle et permettre un pliage précis sans déformation excessive. Elle est souvent fabriquée en acier pour résister aux forces élevées pendant le pliage.
- Poinçon de pliage : Utilisé en conjonction avec la matrice, il applique la force nécessaire pour plier la tôle à l’angle souhaité.
3. Couteaux de découpe
Les couteaux de découpe sont des outils de coupe utilisés dans les machines de découpe pour couper les tôles selon des formes géométriques précises. Ces outils sont utilisés pour des découpes simples ou des découpes complexes.
- Couteaux de cisaillement : Ils sont souvent utilisés dans des machines de cisaillement pour couper les tôles en lignes droites ou dans des configurations définies.
- Lames de découpe : Spécialisées pour les découpes de précision dans des matériaux fins, elles sont utilisées dans des machines comme les scies à ruban ou les ciseaux mécaniques.
4. Rouleaux de formage
Les rouleaux de formage sont utilisés dans des machines de formage à froid, telles que les laminoirs et les machines de profilage, pour appliquer une pression sur la tôle afin de lui donner une forme spécifique. Ces outils sont utilisés pour des opérations comme la fabrication de tuyaux, de profilés et de tôles ondulées.
- Rouleaux de profilage : Ces rouleaux sont utilisés pour donner aux tôles une forme profilée continue. Chaque rouleau applique une pression spécifique pour créer une forme particulière, comme des ondulations ou des formes cylindriques.
5. Outils de découpe au laser
Les outils de découpe au laser sont des lasers haute puissance utilisés pour découper les tôles avec une précision extrême. Ces outils sont généralement intégrés dans des machines de découpe au laser et utilisent un faisceau laser pour chauffer, fondre ou vaporiser le métal, créant des découpes nettes et précises. Bien que ce ne soit pas un outil physique traditionnel comme les poinçons ou les matrices, l’outil ici est le faisceau laser et le système optique qui guide et concentre le faisceau pour la découpe.
6. Outils de formage par emboutissage
Les outils utilisés dans le formage par emboutissage sont essentiels pour produire des pièces métalliques profondes, comme des coques ou des boîtiers. Ces outils comprennent des matrices et des poinçons qui exercent une pression sur la tôle pour lui donner une forme concave ou convexe.
- Matrice d’emboutissage : La matrice est conçue pour recevoir la tôle et lui donner une forme spécifique à chaque étape du processus.
- Poinçon d’emboutissage : Le poinçon pousse la tôle dans la matrice, formant une dépression ou une cavité selon les exigences du design.
7. Outils de soudage
Les outils de soudage sont utilisés pour assembler les pièces métalliques formées ensemble. Bien que le soudage ne soit pas un procédé de formage à proprement parler, il joue un rôle important dans l’assemblage des pièces formées. Les machines de soudage, comme les soudeuses à points et les soudeuses TIG (Tungsten Inert Gas), utilisent des outils qui génèrent une chaleur localisée pour fusionner les bords des tôles métalliques.
- Pince de soudage à point : Utilisée pour effectuer des soudages par points, ce type d’outil applique une pression sur les tôles pour chauffer les surfaces et les faire fondre ensemble.
- Électrode de soudage : Dans les procédés TIG, l’électrode est utilisée pour fournir l’arc de chaleur nécessaire au soudage.
8. Outils de redressage
Les outils de redressage sont utilisés pour corriger les déformations indésirables sur les tôles formées. Parfois, les tôles peuvent se courber ou se tordre lors des opérations de formage, et ces outils sont utilisés pour les ramener à une forme plane.
- Redresseurs : Les redresseurs sont utilisés pour aplatir ou remettre en forme des tôles tordues ou courbées après leur formage. Ces machines appliquent une force pour remettre la tôle à sa forme d’origine.
9. Outils de finition
Après que les tôles ont été formées, découpées et pliées, il est souvent nécessaire de procéder à des opérations de finition pour garantir la qualité du produit. Ces outils sont utilisés pour éliminer les bavures, les arêtes vives et les défauts de surface.
- Meules et meules abrasives : Elles sont utilisées pour enlever les excédents de matériau et lisser les surfaces après des opérations de découpe.
- Brosses et outils de polissage : Utilisés pour donner une finition lisse et brillante aux pièces formées.
Conclusion
Les outils de production pour le formage de tôle sont essentiels pour garantir que les pièces métalliques respectent les normes de précision et de qualité dans la fabrication. Chaque outil est conçu pour une opération spécifique, que ce soit pour découper, plier, emboutir ou souder les tôles, et chaque machine peut intégrer plusieurs outils pour optimiser les processus de fabrication. Avec les avancées technologiques, l’intégration de systèmes automatisés et de contrôle numérique permet d’améliorer l’efficacité, la précision et la répétabilité de la production, tout en réduisant les erreurs et les coûts.
Les outils de production pour le formage de tôle sont au cœur des processus industriels de transformation des métaux. Ils permettent de façonner les tôles métalliques en différentes formes et dimensions pour répondre aux besoins spécifiques des industries de fabrication. Les machines de formage de tôle sont de plus en plus sophistiquées, intégrant des technologies avancées pour améliorer la précision, l’efficacité et la flexibilité de la production. Les outils utilisés dans ces machines sont variés et spécialisés en fonction du type de transformation à réaliser.
L’un des principaux outils utilisés dans les machines de formage est le poinçon, qui est utilisé pour perforer la tôle ou pour réaliser des découpes spécifiques. Ce poinçon est souvent couplé à une matrice, qui soutient la tôle pendant l’opération de découpe. La combinaison du poinçon et de la matrice permet d’obtenir des formes précises, avec une grande régularité de répétition. Ce système est largement utilisé dans les presses à estampe ou les poinçonneuses, qui permettent de réaliser des opérations de perforation, de découpe et de formage complexes sur des tôles de différentes épaisseurs.
Les outils de pliage jouent également un rôle central dans le formage de tôle. Les plieuses et autres équipements de pliage utilisent des matrices et des poinçons adaptés pour créer des angles spécifiques sur les tôles. Ces outils sont conçus pour appliquer une pression suffisante afin de déformer la tôle sans la casser ou provoquer des distorsions excessives. Le pliage est souvent utilisé pour produire des pièces comme des boîtiers, des châssis ou des composants structuraux dans l’industrie automobile, aérospatiale et de la construction. Les machines CNC permettent une programmation de ces outils pour une précision et une répétabilité exceptionnelles.
Les machines de découpe au laser et les outils de découpe plasma sont également de plus en plus utilisés pour des applications de formage de tôle fines. Ces outils permettent de réaliser des découpes extrêmement précises, avec une tolérance d’usinage serrée. Les lasers utilisent un faisceau concentré pour chauffer et vaporiser la matière, permettant des coupes nettes et fines, souvent sur des tôles très minces ou des matériaux spéciaux. Le plasma, quant à lui, est utilisé pour couper des tôles plus épaisses et est particulièrement adapté aux matériaux résistants comme l’acier inoxydable ou les alliages spéciaux. Les outils de découpe à jet d’eau, qui utilisent un jet haute pression pour découper des matériaux sans chaleur, trouvent également leur place dans des applications spécifiques où la chaleur pourrait endommager les pièces.
Les outils de redressage sont essentiels pour corriger les déformations qui peuvent survenir pendant le processus de formage. Ils sont utilisés pour aplanir les tôles courbées ou tordues, ce qui est crucial pour garantir que les pièces finies respectent les tolérances dimensionnelles strictes. Les machines de redressage appliquent une pression ou utilisent des rouleaux pour remettre la tôle dans une forme plane. Ce processus est particulièrement important dans des industries comme l’aérospatiale, où la précision est essentielle, ou dans la fabrication de panneaux métalliques utilisés dans les bâtiments.
Les outils d’emboutissage sont utilisés pour des opérations de formage profond, où la tôle est poussée dans une matrice pour créer des formes complexes. Ces outils sont utilisés pour fabriquer des pièces comme des coques, des boîtiers, des réservoirs, ou même des composants automobiles. L’emboutissage permet de transformer des tôles plates en pièces tridimensionnelles avec une profondeur et une géométrie spécifiques. Il est particulièrement utile pour la production en grande série de pièces métalliques.
Dans un contexte de production automatisée, les outils sont souvent intégrés dans des systèmes de contrôle numérique (CNC), permettant un contrôle précis et automatisé des paramètres de chaque opération de formage. Ces systèmes offrent la possibilité de programmer les machines pour réaliser des opérations de formage complexes avec une grande répétabilité. Ils permettent aussi de minimiser les erreurs humaines et de réduire le gaspillage de matériaux, ce qui améliore l’efficacité de la production et réduit les coûts.
Les machines modernes de formage de tôle sont également équipées de systèmes de maintenance prédictive, permettant de surveiller en temps réel l’état des outils et des machines. Ces systèmes utilisent des capteurs pour détecter les anomalies de fonctionnement, comme une usure excessive des outils ou des vibrations anormales. Cela permet de planifier des interventions de maintenance avant qu’une panne ne survienne, réduisant ainsi les temps d’arrêt et améliorant la productivité globale des lignes de production.
Les outils de finition jouent aussi un rôle essentiel après que la tôle a été formée. Ils permettent de retirer les bavures, de lisser les bords et de préparer les pièces pour l’assemblage ou le montage. Les meules et autres équipements de polissage sont utilisés pour ces opérations de finition, qui sont nécessaires pour garantir une qualité de surface optimale et une bonne ergonomie des pièces. Ces outils permettent de donner à la tôle un aspect lisse et sans défaut, tout en respectant les spécifications dimensionnelles finales.
Le contrôle de la qualité est aussi intégré aux outils modernes de formage de tôle. Des systèmes de vision automatisés, basés sur des caméras et des capteurs, sont utilisés pour inspecter les pièces en temps réel pendant le processus de fabrication. Ces systèmes peuvent détecter des défauts, tels que des irrégularités dimensionnelles ou des défauts de surface, permettant une correction rapide avant que les pièces ne soient envoyées à l’étape suivante du processus de production. Cela améliore la qualité du produit final et réduit les déchets.
En somme, les outils de production pour le formage de tôle sont essentiels pour répondre aux exigences complexes des industries modernes. Qu’il s’agisse de découpe, de pliage, d’emboutissage ou de finition, chaque outil est conçu pour optimiser un aspect spécifique du processus de fabrication. Grâce à des technologies avancées, ces outils sont de plus en plus précis, rapides et efficaces, permettant ainsi une production de pièces métalliques de haute qualité avec des coûts réduits et une flexibilité accrue.
Le formage de tôle est un domaine en constante évolution, et avec l’intégration de technologies avancées, la capacité des équipements de production s’est améliorée de manière significative au fil du temps. Les outils et machines modernes permettent non seulement de produire des pièces complexes avec des tolérances très strictes, mais également d’améliorer la productivité, de réduire les coûts de production et de garantir une qualité constante.
L’utilisation de robots industriels dans les lignes de production de formage de tôle est de plus en plus courante. Ces robots peuvent manipuler les tôles, les placer dans les machines et effectuer des tâches répétitives, ce qui réduit la dépendance à la main-d’œuvre humaine et augmente la vitesse de production. De plus, l’intégration de systèmes de vision artificielle permet aux robots d’inspecter en temps réel les pièces fabriquées, détectant ainsi toute anomalie ou imperfection qui pourrait affecter la qualité des produits finis. Les robots peuvent ajuster les paramètres des machines en fonction de ces inspections, ce qui contribue à maintenir la qualité de production sans intervention humaine.
En parallèle, les systèmes de contrôle numérique (CNC) et de programmation assistée par ordinateur (CAO/FAO) jouent un rôle clé dans l’optimisation des processus de formage. La programmation informatique permet de concevoir et de simuler des pièces avant leur fabrication, réduisant ainsi le risque d’erreurs de production. Les commandes CNC permettent également de contrôler précisément chaque étape du processus de formage, qu’il s’agisse de découpe, de pliage ou d’emboutissage. Ce niveau de contrôle améliore non seulement la précision mais aussi la flexibilité des lignes de production, permettant de passer d’un produit à un autre sans perte de temps.
Les machines hybrides sont un autre exemple de progrès technologique dans le domaine du formage de tôle. Ces machines combinent différentes technologies de formage, telles que le pliage hydraulique, le découpage au laser, et parfois même l’emboutissage, dans un seul équipement. Cela permet de rationaliser le processus de fabrication, réduisant ainsi le nombre de machines nécessaires et la complexité du flux de travail. Ces machines permettent également de réduire le temps de cycle de production, ce qui se traduit par des coûts de production plus faibles et une meilleure efficacité globale.
Les matériaux avancés jouent également un rôle de plus en plus important dans le formage de tôle. Les tôles métalliques traditionnelles, telles que l’acier doux et l’aluminium, sont toujours largement utilisées, mais des alliages plus complexes et des matériaux à haute résistance, comme les aciers haute résistance et les composites métalliques, sont de plus en plus présents. Ces matériaux offrent une meilleure résistance à la traction, une durabilité accrue et une meilleure performance dans des conditions extrêmes. Cependant, ils présentent également des défis supplémentaires en termes de formage, car ils peuvent être plus difficiles à manipuler ou à découper en raison de leurs propriétés mécaniques particulières. Les outils et machines doivent donc être adaptés pour gérer ces matériaux de manière efficace et sûre.
Le recyclage des matériaux est un autre aspect clé du formage de tôle dans le contexte industriel actuel. Les entreprises cherchent de plus en plus à réduire leur empreinte écologique et à adopter des pratiques plus durables. Cela inclut le recyclage des chutes de tôle et des pièces usagées. Le recyclage permet non seulement de réduire la consommation de matériaux, mais aussi de minimiser les déchets. Les entreprises qui utilisent des systèmes de gestion de matériaux avancés peuvent optimiser l’utilisation des tôles, réduisant ainsi les coûts tout en respectant les normes environnementales.
Les innovations en matière de revêtements de surface sont également cruciales pour le formage de tôle. Les traitements de surface, tels que la galvanisation, le revêtement en poudre, ou les traitements anti-corrosion, sont utilisés pour protéger les tôles contre la rouille et l’usure. Ces traitements augmentent la durée de vie des pièces formées et améliorent leur apparence. De plus, les revêtements spéciaux peuvent améliorer les propriétés de la tôle, comme la résistance à la chaleur, aux produits chimiques ou à l’usure mécanique, ce qui est essentiel dans des secteurs comme l’automobile, l’aérospatiale, et la construction.
Enfin, l’avenir du formage de tôle semble de plus en plus tourné vers l’intégration de l’IA (intelligence artificielle) et des algorithmes de machine learning pour optimiser les processus de fabrication. Ces technologies permettent d’analyser de grandes quantités de données provenant des machines et des capteurs pour prévoir des pannes, ajuster les paramètres en temps réel, et optimiser les cycles de production. Par exemple, l’IA peut aider à prédire l’usure des outils, permettant ainsi une maintenance préventive avant que les problèmes ne surviennent. Elle peut également optimiser les trajectoires des robots ou ajuster automatiquement la vitesse de découpe et de formage pour maximiser l’efficacité tout en maintenant la qualité.
Dans ce contexte d’évolution technologique, les tendances vers l’automatisation et la digitalisation se poursuivent. Les entreprises qui adoptent ces technologies se retrouvent non seulement avec des processus de production plus efficaces, mais également capables de répondre aux besoins de personnalisation croissante des produits. Les lignes de production flexibles permettent aux fabricants de produire une plus large gamme de pièces, parfois même en petites séries, sans sacrifier l’efficacité ou la rentabilité.
Ainsi, l’avenir du formage de tôle repose sur une combinaison d’innovations matérielles, technologiques et procédurales qui permettent aux industries de continuer à évoluer tout en répondant aux exigences croissantes de performance, de durabilité et de flexibilité. L’intégration de nouveaux matériaux, l’adoption de technologies avancées et l’optimisation des processus de production garantiront que le formage de tôle reste un pilier fondamental dans la fabrication industrielle du futur.
Machines pour le traitement de tôle
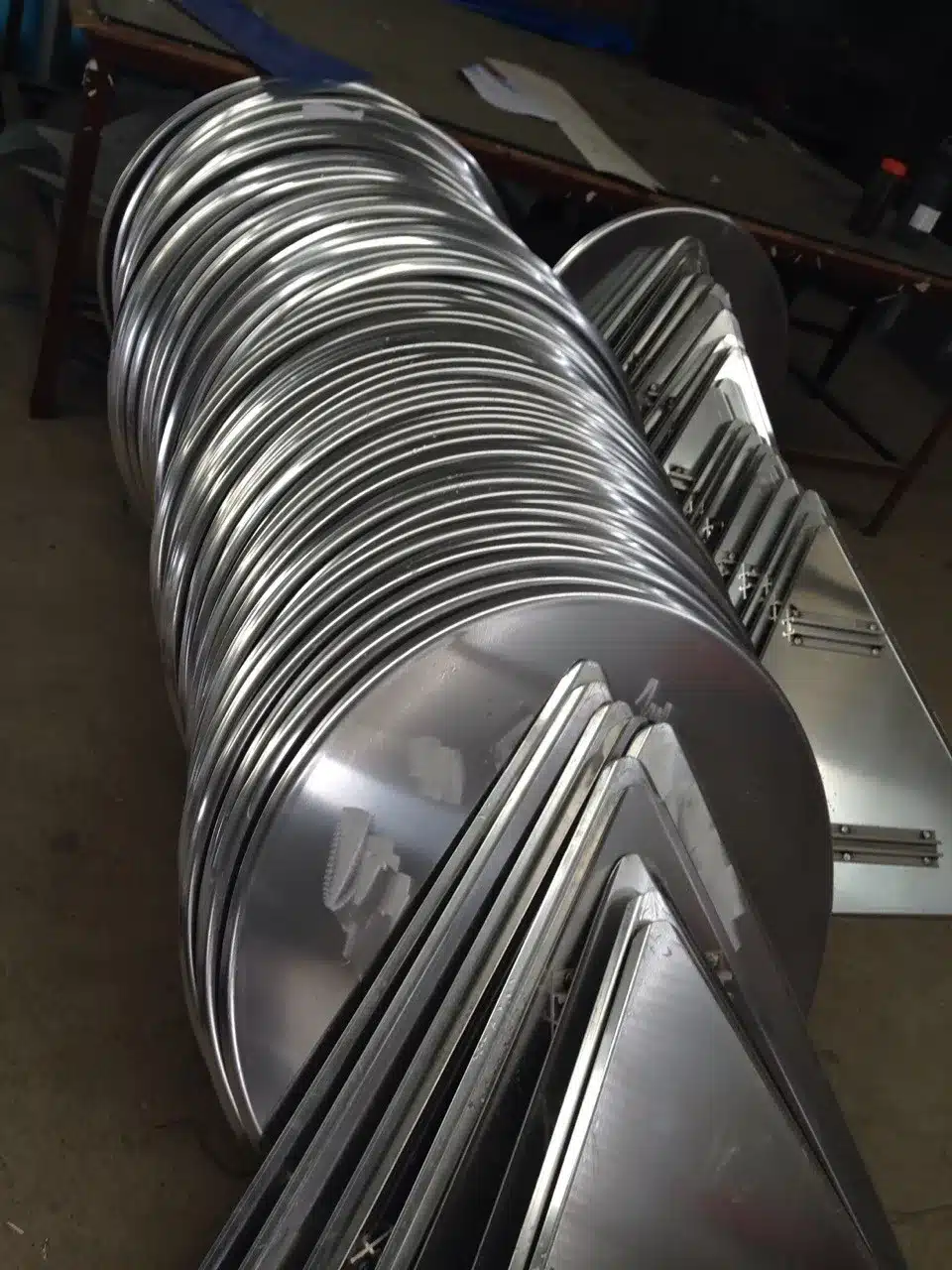
Les machines pour le traitement de tôle sont utilisées dans de nombreux secteurs industriels pour transformer les tôles métalliques en produits finis ou semi-finis. Ces machines sont conçues pour effectuer une large gamme de traitements, allant de la découpe, au pliage, au soudage, au formage, à la finition, et à d’autres opérations spécialisées. Elles peuvent être automatisées pour offrir des capacités de production de masse ou être utilisées pour des productions plus petites et spécifiques, selon les besoins de l’industrie. Voici un aperçu des principales machines utilisées pour le traitement de tôle :
1. Presse-plieuse (ou plieuse hydraulique)
La presse-plieuse est utilisée pour plier des tôles métalliques à des angles spécifiques. Elle fonctionne en appliquant une force de compression sur la tôle entre un poinçon et une matrice. Ces machines peuvent être équipées de commandes numériques (CNC), permettant un pliage précis et répétitif. Elles sont souvent utilisées dans la fabrication de boîtiers, de châssis, et d’autres composants en métal.
2. Poinçonneuse
La poinçonneuse est utilisée pour perforer des tôles métalliques. Cette machine utilise un poinçon pour découper des formes spécifiques dans la tôle, créant des trous ou des motifs selon les besoins du design. La poinçonneuse est particulièrement utile pour les productions en série où des milliers de pièces identiques doivent être fabriquées. Ces machines sont souvent équipées de systèmes CNC pour une plus grande précision.
3. Cisaille
La cisaille est une machine de découpe utilisée pour couper des tôles métalliques en lignes droites. Elle est idéale pour des coupes rapides et nettes sur des tôles de grande dimension. Les cisailles peuvent être manuelles ou motorisées, et sont largement utilisées dans les industries de la construction, de l’automobile et de la métallurgie pour découper les tôles à la longueur ou à la forme souhaitée.
4. Machine de découpe au laser
Les machines de découpe au laser utilisent un faisceau laser haute précision pour découper ou graver des tôles métalliques. Ces machines sont particulièrement adaptées pour la découpe de formes complexes, avec des tolérances très fines et des bords nets. Le processus de découpe au laser est très rapide et permet de traiter des matériaux très fins ou des matériaux plus épais avec une grande efficacité. C’est un outil essentiel dans l’industrie de l’aérospatiale, de l’automobile, et de la production de composants électroniques.
5. Découpe plasma
Les machines de découpe plasma sont utilisées pour couper des tôles métalliques de différentes épaisseurs, en particulier les métaux tels que l’acier inoxydable, l’aluminium, et d’autres alliages. Elles fonctionnent en utilisant un jet de gaz ionisé (plasma) pour chauffer et couper le métal. Ce type de découpe est rapide et efficace, particulièrement pour des applications nécessitant des coupes en grandes séries, mais il peut laisser des bords légèrement rugueux qui nécessitent parfois un traitement de finition.
6. Découpe au jet d’eau
Les machines de découpe au jet d’eau utilisent un jet d’eau haute pression, souvent mélangé à des abrasifs, pour couper des tôles métalliques. Ce procédé ne génère pas de chaleur, ce qui permet de couper des matériaux sensibles à la chaleur sans les altérer. Il est particulièrement utile pour couper des matériaux épais ou des matériaux sensibles, comme les composites, sans compromettre leur structure.
7. Machine de formage à froid
Les machines de formage à froid sont utilisées pour transformer des tôles métalliques par déformation, sans chauffage préalable. Ces machines peuvent être utilisées pour des opérations de pliage, de roulage, de repliement, ou même de profilage. Elles sont couramment utilisées pour produire des composants tels que des tubes, des profilés, et des tôles formées pour la construction, la fabrication automobile, ou d’autres secteurs où la résistance mécanique et la précision des formes sont essentielles.
8. Machine de redressage
Les machines de redressage sont utilisées pour corriger les déformations ou courbures qui peuvent se produire pendant les étapes précédentes du traitement de la tôle. Ces machines appliquent des forces pour aplatir ou redresser les tôles métalliques et assurer une géométrie correcte avant qu’elles ne soient envoyées aux étapes suivantes de fabrication. Elles sont souvent utilisées dans la production de pièces de haute précision ou pour garantir que les tôles restent plates après de multiples opérations de formage.
9. Machines de soudage (par points, MIG/TIG)
Les machines de soudage sont utilisées pour assembler des pièces de tôle métallique entre elles. Le soudage peut être effectué par différentes techniques, telles que le soudage par points, le soudage MIG (Métal Inert Gas), ou le soudage TIG (Tungsten Inert Gas). Le soudage par points est particulièrement utilisé pour l’assemblage de tôles fines, comme dans l’industrie automobile, où des joints solides et rapides sont nécessaires. Les machines de soudage MIG/TIG sont utilisées pour des applications où des soudures de haute qualité et une finition propre sont requises.
10. Plieuse à commande numérique (CNC)
Les plieuses à commande numérique sont des machines avancées qui utilisent des commandes informatiques pour effectuer des plis précis dans les tôles métalliques. Elles permettent de programmer des séries complexes de plis, ce qui est essentiel dans la production de pièces métalliques personnalisées ou à grande échelle. Ces machines peuvent travailler avec des tôles métalliques d’épaisseurs et de matériaux variés, offrant une flexibilité de production tout en maintenant une grande précision.
11. Machines de finition (meulage, polissage, etc.)
Une fois les tôles formées, découpées, ou soudées, des machines de finition sont utilisées pour éliminer les imperfections et améliorer la surface des pièces. Les meuleuses, polisseuses et autres équipements de finition sont utilisés pour lisser les bords, éliminer les bavures, et rendre la surface de la tôle plus esthétique ou adaptée à des exigences techniques spécifiques.
Conclusion
Les machines de traitement de tôle jouent un rôle essentiel dans l’industrie moderne en permettant de transformer des tôles métalliques brutes en produits finis, souvent en grande série et avec des exigences de qualité strictes. Grâce à l’automatisation, aux technologies avancées comme le CNC, et à l’intégration de techniques de découpe sophistiquées, ces machines permettent de réaliser une large variété d’opérations de manière précise, rapide et efficace.
Les machines de traitement de tôle jouent un rôle central dans la fabrication de pièces métalliques complexes et de haute précision. Grâce aux avancées technologiques, elles permettent d’effectuer des tâches variées allant de la découpe, du formage, du soudage, à la finition, tout en maintenant un haut niveau d’efficacité et de précision. Parmi les plus courantes, la presse-plieuse permet de réaliser des plis sur des tôles métalliques en appliquant une pression, souvent à l’aide d’un système hydraulique. Cette machine est essentielle pour la fabrication de pièces qui nécessitent des angles précis et une finition nette. La poinçonneuse, de son côté, est utilisée pour perforer des tôles métalliques, une opération courante dans des secteurs comme l’automobile ou l’électronique, où des trous ou des motifs réguliers sont nécessaires dans les pièces. En parallèle, les cisailles, utilisées pour couper des tôles en lignes droites, sont souvent équipées de mécanismes motorisés ou hydrauliques et sont capables de traiter des matériaux de diverses épaisseurs.
Le découpage au laser est une méthode populaire dans le traitement de tôle en raison de sa précision et de sa rapidité. Grâce à un faisceau laser, cette technique permet de découper des tôles en formes complexes tout en minimisant les risques de déformation du matériau. Les machines de découpe au plasma, quant à elles, sont idéales pour couper des tôles métalliques plus épaisses, en utilisant un jet de gaz ionisé pour chauffer et découper le métal. Cela permet de réaliser des coupes rapides, mais nécessite parfois des traitements supplémentaires pour améliorer les bords coupés. La découpe au jet d’eau est une autre méthode de découpe, qui utilise un jet d’eau haute pression mélangé à un abrasif pour couper des matériaux sans générer de chaleur. Cette méthode est particulièrement utile pour traiter des matériaux sensibles à la chaleur ou pour couper des tôles très épaisses.
Les machines de formage à froid, qui comprennent des plieuses, des rouleuses et des machines de profilage, sont utilisées pour donner forme à des tôles sans les chauffer, ce qui permet de maintenir les propriétés mécaniques du matériau tout en créant des formes complexes comme des tubes, des profilés ou des boîtiers. Les machines de redressage, quant à elles, sont conçues pour éliminer les courbures ou déformations des tôles métalliques qui peuvent se produire lors des étapes précédentes de traitement, assurant ainsi que les pièces restent géométriquement correctes et prêtes pour l’assemblage ou la finition. Le soudage, qu’il soit effectué par points, MIG (Métal Inert Gas) ou TIG (Tungsten Inert Gas), est également une étape clé dans le traitement de tôle. Ces techniques permettent de joindre plusieurs pièces métalliques entre elles, qu’il s’agisse de tôles fines ou de composants plus complexes. Le soudage par points est particulièrement courant dans l’industrie automobile pour l’assemblage rapide de pièces, tandis que les méthodes MIG et TIG sont utilisées pour des soudures plus fines et de haute qualité.
Une fois que les pièces de tôle ont été formées, découpées ou soudées, des machines de finition telles que les meuleuses ou les polisseuses sont utilisées pour améliorer l’apparence de la surface des pièces et éliminer toute irrégularité. Ces machines permettent de lisser les bords des pièces ou d’éliminer les bavures, assurant ainsi une finition propre et professionnelle. Enfin, les machines modernes de traitement de tôle sont souvent équipées de commandes numériques (CNC), ce qui permet une grande précision et une flexibilité dans les opérations de fabrication. Les systèmes CNC permettent de programmer des séquences complexes d’opérations, de manière à optimiser la production, tout en garantissant une qualité constante sur de grandes séries de pièces. L’automatisation joue un rôle crucial dans cette évolution, permettant aux machines de fonctionner avec peu ou pas d’intervention humaine, tout en améliorant la sécurité, la vitesse et la précision des processus de production. Grâce à ces technologies avancées, le traitement de tôle est devenu un processus plus rapide, plus flexible et plus précis, permettant aux industries de répondre aux demandes de production modernes tout en respectant des normes de qualité de plus en plus exigeantes.
Le traitement de tôle a continué à évoluer avec l’intégration de nouvelles technologies, augmentant ainsi l’efficacité, la flexibilité et la qualité des produits finis. L’une des avancées majeures a été l’intégration de l’intelligence artificielle (IA) et du machine learning dans les systèmes de production de tôles. Ces technologies permettent de prédire les problèmes de qualité, de suivre les conditions des machines en temps réel, et de procéder à des ajustements automatiques sans intervention humaine, optimisant ainsi la performance de l’ensemble du processus. Par exemple, des algorithmes d’IA peuvent analyser des images de la production pour détecter des défauts invisibles à l’œil nu ou prévoir l’usure des outils, ce qui réduit le nombre d’erreurs et améliore la durée de vie des équipements.
En plus de cela, l’automatisation avancée a permis la mise en place de cellules de production complètes pour le traitement de tôle. Ces cellules comprennent un ensemble de machines connectées et autonomes qui peuvent effectuer plusieurs opérations simultanément, telles que la découpe, le pliage, le soudage et la finition. L’automatisation garantit non seulement une production plus rapide mais aussi une réduction des coûts de main-d’œuvre et une amélioration de la sécurité, en minimisant l’intervention humaine dans les tâches potentiellement dangereuses. Ces cellules permettent également une production flexible, où des modifications rapides peuvent être apportées pour répondre à des commandes personnalisées ou à des séries limitées de produits.
Le recyclage des matériaux est une autre tendance importante dans le traitement de tôle. De nombreuses industries, en particulier celles travaillant avec des métaux, cherchent à réduire leur impact environnemental en réutilisant les chutes de métal ou en intégrant davantage de matériaux recyclés dans leur production. Les machines de récupération et de tri de métaux jouent un rôle essentiel en permettant de récupérer les métaux des déchets ou des pièces défectueuses et de les réintroduire dans le cycle de production. Cela contribue à diminuer la dépendance aux matériaux vierges et à réduire les coûts de fabrication tout en respectant les normes environnementales de plus en plus strictes.
Les machines modernes pour le traitement de tôle sont également équipées de technologies de monitoring et de maintenance prédictive. Par exemple, les capteurs installés sur les machines collectent en continu des données relatives à la température, à la pression, à la vibration et à d’autres paramètres critiques du processus de production. Ces données sont ensuite analysées pour prédire quand les pièces de machine risquent de s’user ou de tomber en panne, ce qui permet aux entreprises de procéder à une maintenance préventive avant qu’une panne ne se produise. Cela minimise les interruptions de production et prolonge la durée de vie des équipements.
Le traitement des tôles métalliques fines, comme celles utilisées dans l’industrie automobile ou aérospatiale, est également facilité par l’avancée des technologies de découpe ultraprécise et de poinçonnage à haute vitesse. Ces machines permettent d’obtenir des tolérances extrêmement fines et de traiter des matériaux plus délicats, réduisant ainsi les déchets de production tout en augmentant le rendement des matériaux.
L’adaptation aux matériaux nouveaux est aussi un facteur clé dans l’évolution des machines de traitement de tôle. Les métaux de haute performance comme les alliages à haute résistance, les titanes, les alliages légers et les composites sont de plus en plus utilisés, notamment dans l’aéronautique, l’automobile et l’industrie de l’énergie. Ces matériaux, plus difficiles à travailler en raison de leur résistance ou de leur fragilité, nécessitent des machines de traitement plus spécialisées qui intègrent des technologies avancées pour garantir une manipulation correcte sans dégradation.
En ce qui concerne la production à faible coût et à haute efficacité, les machines sont conçues pour fonctionner à des vitesses accrues tout en maintenant une faible consommation d’énergie. Les technologies de gestion de l’énergie sont utilisées pour optimiser l’utilisation de l’énergie pendant le processus de production, ce qui permet de réduire l’empreinte carbone et les coûts d’exploitation. Ces solutions sont particulièrement importantes dans un contexte où la durabilité et la réduction des coûts sont des priorités pour les entreprises industrielles.
L’amélioration des interfaces utilisateurs a également été un axe d’évolution majeur. Les machines de traitement de tôle modernes sont désormais équipées de systèmes de commande intuitifs et de tableaux de bord numériques qui permettent aux opérateurs de suivre en temps réel l’état des machines, les performances de la production et les éventuelles anomalies. Ces interfaces sont généralement dotées de systèmes de diagnostic automatisé qui offrent aux opérateurs des recommandations précises pour corriger rapidement les problèmes, sans avoir besoin de faire appel à un technicien spécialisé.
L’intégration des technologies de réalité augmentée (RA) et de réalité virtuelle (RV) commence également à apparaître dans les environnements de fabrication. Ces technologies permettent aux ingénieurs et aux opérateurs d’effectuer des inspections virtuelles des pièces, de tester des prototypes numériques ou de visualiser des données complexes en temps réel, ce qui facilite la prise de décision et améliore l’efficacité des processus de conception et de fabrication.
Dans un avenir proche, il est probable que les machines de traitement de tôle deviendront de plus en plus intelligentes et autonomes, grâce à l’intégration continue de l’IA, du big data et de l’automatisation avancée. Cela permettra aux usines de fonctionner de manière plus agile, plus réactive et plus éco-efficiente. Ces développements permettront aux industriels de répondre plus efficacement aux exigences du marché, telles que la personnalisation de masse, la réduction des délais de production, l’amélioration de la qualité, et la gestion durable des ressources.
Machines pour la déformation de tôle
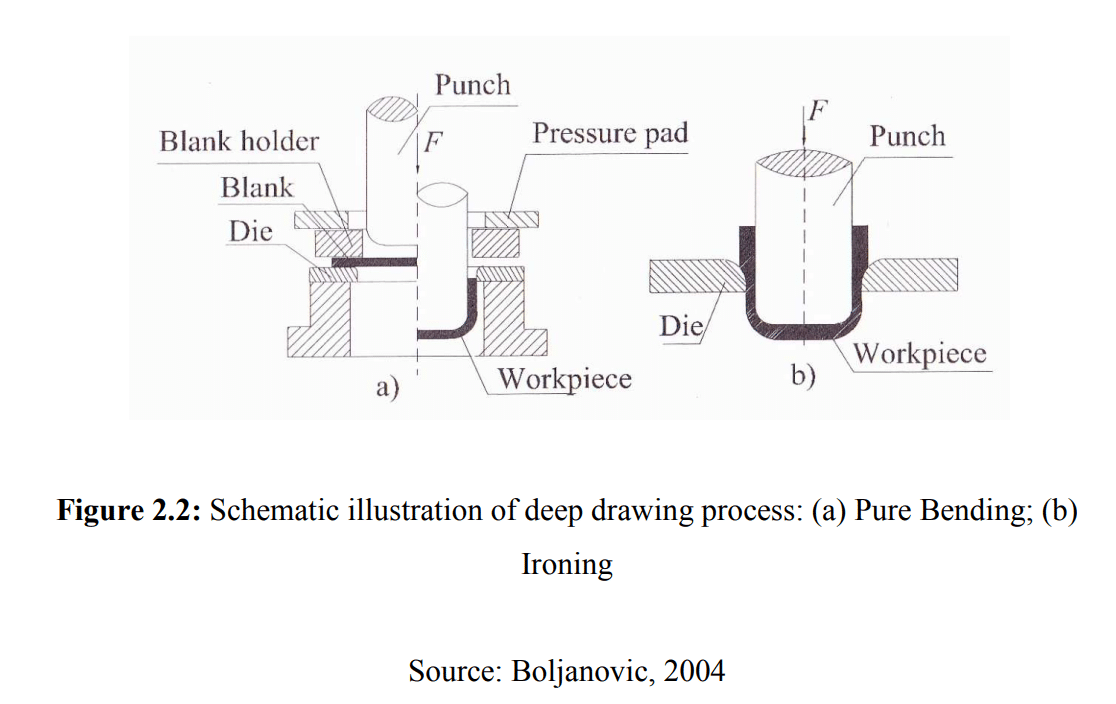
Les machines pour la déformation de tôle sont des équipements industriels essentiels utilisés pour transformer les tôles métalliques en pièces ayant des formes spécifiques sans altérer leur intégrité ou leurs propriétés mécaniques. La déformation de tôle implique des processus physiques qui modifient la forme de la tôle par des actions de compression, de traction ou de flexion, tout en conservant la cohésion du matériau. Ces machines sont largement utilisées dans l’industrie automobile, aérospatiale, de la construction, de la métallurgie et dans d’autres secteurs nécessitant des composants métalliques formés sur mesure. Voici un aperçu des principales machines utilisées pour la déformation de tôle :
- Plieuses et presses-plieuses : Ces machines sont utilisées pour plier des tôles métalliques à des angles spécifiques. Elles exercent une pression sur la tôle entre une matrice et un poinçon. Les presses-plieuses peuvent être manuelles, hydrauliques, ou à commande numérique (CNC), et sont idéales pour réaliser des plis précis sur des tôles de différentes épaisseurs. Elles sont essentielles pour la fabrication de boîtiers, de châssis et d’autres pièces métalliques de forme angulaire.
- Cisailles et machines de coupe : Les cisailles sont utilisées pour couper les tôles métalliques en ligne droite, en utilisant des lames rotatives ou fixes. Elles sont souvent équipées de systèmes motorisés ou hydrauliques pour effectuer des coupes nettes et rapides. Ces machines sont particulièrement utiles pour des travaux de découpe de tôles en grandes dimensions. Certaines cisailles sont aussi équipées de coupeurs à jet d’eau ou plasma, qui peuvent couper des tôles plus épaisses ou des matériaux plus résistants.
- Poinçonneuses : Les poinçonneuses sont utilisées pour perforer des tôles métalliques en créant des trous ou des motifs dans le métal. Elles utilisent un poinçon qui appuie sur la tôle pour créer une perforation. Ce processus est couramment utilisé dans la fabrication de pièces pour des secteurs tels que l’automobile, la construction et l’électronique. Les poinçonneuses peuvent être à commande numérique, ce qui permet de perforer avec une grande précision.
- Rouleurs et machines de cintrage : Les rouleurs sont utilisés pour courber les tôles métalliques en formes circulaires ou ovales. Les tôles sont alimentées dans des rouleaux qui exercent une pression progressive pour donner à la tôle une courbure homogène. Ce processus est utilisé pour fabriquer des tubes, des cylindres ou d’autres formes arrondies. Les machines de cintrage sont une forme de rouleur plus spécialisée pour des pièces plus complexes ou des cintrages plus serrés.
- Machines de formage à froid : Les machines de formage à froid sont utilisées pour créer des formes complexes en tôle métallique sans chauffage préalable. Ces machines travaillent sur des tôles à température ambiante et peuvent être utilisées pour des opérations telles que le profilage, le repliement et le façonnage. Ces processus sont particulièrement courants dans la fabrication de tuyaux, de profilés et d’autres composants métalliques utilisés dans la construction et l’industrie automobile.
- Rouleuses à commandes numériques (CNC) : Les rouleuses CNC sont des machines de formage à froid de haute précision, équipées de commandes numériques pour garantir des courbures uniformes et des formes complexes. Ces machines sont utilisées pour des productions en série, garantissant une répétabilité parfaite et une flexibilité dans le design. Les rouleuses CNC sont essentielles dans des industries où des tolérances serrées et des courbes spécifiques sont nécessaires.
- Machines à emboutir : Les machines à emboutir sont utilisées pour effectuer des opérations de formage profond, où la tôle est poussée dans une matrice pour obtenir une forme tridimensionnelle, comme des boîtiers ou des pièces complexes. L’emboutissage peut être effectué à chaud ou à froid, en fonction du matériau de la tôle et des exigences de conception. Ces machines sont couramment utilisées dans l’industrie automobile pour produire des pièces comme les panneaux de carrosserie.
- Machines de matriçage : Les machines de matriçage sont utilisées pour créer des formes complexes en tôle métallique à l’aide de matrices. Cela inclut des processus tels que l’emboutissage, l’estampage et le formage. Ces machines exercent une pression importante sur la tôle pour la faire prendre la forme de la matrice, souvent utilisée pour créer des pièces avec des détails fins ou des formes géométriques complexes.
- Machines de déformation rotative : Ce type de machine permet de déformer des tôles métalliques en les faisant tourner autour d’un axe fixe. Ces machines sont souvent utilisées pour la fabrication de pièces cylindriques ou coniques, comme des réservoirs ou des conduits. L’action de déformation est généralement douce et permet de créer des formes sans compromettre la résistance du métal.
- Emboutisseuses à haute vitesse : Les emboutisseuses à haute vitesse sont des machines spéciales qui peuvent effectuer des opérations d’emboutissage rapide et de haute précision, adaptées aux grandes séries de production. Elles sont particulièrement utilisées pour la fabrication de pièces fines, telles que des composants pour l’électronique ou des éléments décoratifs pour l’industrie automobile.
- Machines de formage par soufflage : Bien que principalement utilisées pour les matériaux plastiques, certaines machines de formage par soufflage peuvent être adaptées au traitement de tôles métalliques légères. Ce processus implique l’utilisation d’air comprimé pour modeler la tôle autour d’une matrice. Cette technique est utilisée dans des applications spécifiques, telles que la fabrication de coques ou de pièces à parois minces.
- Machines de filetage et de vissage : Les machines de filetage sont utilisées pour créer des filetages dans les tôles métalliques. Ce processus est souvent nécessaire lorsqu’une pièce métallique doit être fixée ou assemblée avec d’autres composants à l’aide de vis ou de boulons. Certaines machines peuvent combiner plusieurs opérations, y compris l’emboutissage et le filetage, dans une seule étape de production.
Toutes ces machines sont souvent intégrées dans des lignes de production automatisées qui peuvent effectuer plusieurs opérations en chaîne, réduisant ainsi les besoins en main-d’œuvre et augmentant la vitesse de production tout en maintenant des normes de qualité élevées. Grâce à l’évolution de la robotisation et de l’intelligence artificielle, ces machines peuvent désormais être configurées pour produire des pièces sur mesure à grande échelle, ce qui en fait un élément crucial dans la fabrication de composants métalliques modernes.
Les machines pour la déformation de tôle sont des équipements essentiels dans l’industrie moderne, permettant de transformer des tôles métalliques en pièces de formes diverses tout en maintenant leurs propriétés mécaniques intactes. Ces machines sont conçues pour répondre aux exigences de production à grande échelle tout en garantissant une précision élevée et une répétabilité constante. Les plieuses et presses-plieuses, par exemple, sont cruciales pour créer des angles et des plis précis sur les tôles métalliques. Elles utilisent une pression importante pour plier la tôle entre deux outils, un poinçon et une matrice, afin d’obtenir la forme souhaitée. Les presses-plieuses à commande numérique (CNC) permettent d’automatiser ce processus, garantissant une répétabilité parfaite pour les séries de production complexes. Ces machines sont souvent utilisées dans des secteurs tels que l’automobile et la construction, où les formes complexes et les tolérances strictes sont essentielles.
Les poinçonneuses, quant à elles, perforent des tôles métalliques pour créer des trous ou des motifs dans des matériaux fins. En utilisant des poinçons et des matrices, ces machines permettent de réaliser des perforations très précises, essentielles pour la fabrication de pièces comme les panneaux de carrosserie, les composants électroniques ou même les filtres. Certaines poinçonneuses sont équipées de commandes numériques, permettant d’adapter rapidement les paramètres de perforation pour des designs variés et complexes. D’autre part, les rouleuses, utilisées pour former des tôles métalliques en courbes ou en cylindres, sont courantes pour la fabrication de tuyaux, de réservoirs et d’autres pièces cylindriques. Elles fonctionnent en faisant passer la tôle entre des rouleaux qui exercent une pression progressive, permettant ainsi de plier la tôle sans l’endommager. Ces machines sont idéales pour la production de pièces avec une grande uniformité de forme.
Les machines de déformation à froid, telles que les machines de formage par emboutissage, utilisent des matrices pour transformer des tôles métalliques en formes complexes. Ce processus est effectué sans chauffer la tôle, ce qui permet de maintenir ses propriétés mécaniques tout en obtenant des détails fins dans la pièce finale. L’emboutissage est souvent utilisé pour des composants automobiles, comme des panneaux de carrosserie, ou dans des applications aérospatiales et électroniques. En complément, les machines de formage rotatif ou à déformation par soufflage permettent de traiter des tôles métalliques de manière à produire des formes cylindriques ou coniques. Ces technologies sont utilisées dans la fabrication de réservoirs ou de conduits et sont idéales pour des matériaux qui doivent être manipulés avec soin pour éviter toute déformation ou faiblesse dans le métal.
La maintenance et l’amélioration continue des machines de déformation de tôle sont essentielles pour garantir une production sans faille. L’introduction de capteurs intelligents, de systèmes de contrôle automatisés et d’algorithmes d’intelligence artificielle dans les équipements permet de prédire l’usure des outils, d’ajuster en temps réel les paramètres de production et de maximiser le rendement des machines. Ces avancées permettent de réduire les arrêts imprévus et d’augmenter l’efficacité de la production, tout en garantissant la qualité constante des pièces fabriquées. De plus, l’intégration des technologies numériques dans ces machines permet une grande flexibilité de production, rendant possible la fabrication de petites séries personnalisées à un coût compétitif, tout en maintenant une qualité homogène et une rapidité d’exécution.
Les machines pour la déformation de tôle sont également dotées de systèmes de surveillance et de contrôle à distance, permettant aux opérateurs de suivre en temps réel l’état des machines, d’identifier rapidement tout problème potentiel et de procéder à des ajustements sans avoir besoin d’une intervention physique sur place. Cela est particulièrement important dans les usines modernes, où les processus de production sont souvent automatisés et où une surveillance constante est nécessaire pour assurer la continuité des opérations. La mise en réseau des machines permet aussi de collecter des données de performance, qui peuvent être utilisées pour optimiser les processus de fabrication et prévoir les besoins en maintenance.
En somme, les machines de déformation de tôle sont essentielles pour la production de composants métalliques de haute précision, jouant un rôle clé dans divers secteurs industriels, de l’automobile à l’aérospatial. Grâce à l’automatisation, à l’intégration de l’intelligence artificielle et à l’amélioration des technologies de contrôle et de surveillance, ces machines deviennent plus efficaces, plus flexibles et plus adaptées aux besoins de production modernes.
La technologie continue d’évoluer dans le domaine du formage de tôle, avec une attention particulière portée à l’amélioration des performances et de la précision des machines. L’un des aspects clés de cette évolution est l’intégration accrue des systèmes automatisés et des robotisations. Les robots industriels, souvent associés à des machines de déformation de tôle, sont capables d’effectuer des tâches répétitives et de grande précision, comme la manipulation des tôles, le positionnement des pièces dans les machines, ou encore le contrôle de la qualité en cours de production. Cela permet non seulement de réduire les erreurs humaines, mais aussi d’augmenter la vitesse et la fiabilité des processus de fabrication.
L’un des principaux avantages de cette automatisation est la réduction des temps de cycle. Les machines de déformation de tôle modernes, équipées de systèmes de commande numérique (CNC) et de logiciels de simulation, permettent d’optimiser les processus en ajustant automatiquement les paramètres de production pour chaque pièce fabriquée. Cela est particulièrement utile pour les petites séries ou les pièces complexes, où chaque ajustement de forme ou de taille doit être effectué avec une grande précision. Les logiciels de simulation peuvent également prévoir l’impact des différentes stratégies de formage sur la tôle, permettant ainsi de déterminer la meilleure approche avant même de commencer la production, ce qui réduit les essais physiques et les coûts associés.
L’usage de matériaux innovants et de tôles de haute performance dans la fabrication de pièces nécessite des machines de formage capables de traiter des matériaux plus durs ou plus légers, tout en maintenant des tolérances précises. Par exemple, le traitement des alliages spéciaux, des métaux légers comme l’aluminium ou des matériaux composites nécessite des équipements dotés de caractéristiques particulières. Des machines dotées de systèmes de chauffage localisé ou de revêtements spéciaux pour outils de coupe permettent de traiter ces matériaux sans compromettre leur résistance ou leur qualité.
L’éco-efficacité est également un domaine d’innovation dans les machines de formage de tôle. L’accent est mis sur l’amélioration de l’efficacité énergétique des équipements, tout en réduisant les déchets de production. Les machines modernes sont conçues pour fonctionner de manière plus écologique, avec des systèmes de récupération de chaleur, des moteurs plus efficaces et des processus qui minimisent les chutes de matière. Les technologies de recyclage interne permettent de récupérer les restes de tôle ou les chutes pour les réintroduire dans le cycle de production, réduisant ainsi la consommation de matériaux neufs.
L’optimisation des flux de production dans les usines de traitement de tôle est également un aspect crucial du développement des machines modernes. L’intégration de la fabrication flexible permet aux usines de s’adapter rapidement à la demande, que ce soit pour des productions de grande envergure ou des séries limitées. Les machines de déformation de tôle sont désormais capables de s’adapter à des commandes spécifiques et à des exigences de personnalisation. Les systèmes de fabrication juste-à-temps (JAT), couplés à une gestion intelligente de l’inventaire, permettent d’optimiser les coûts en réduisant les stocks et en produisant uniquement ce qui est nécessaire, lorsque c’est nécessaire.
Le domaine de la maintenance prédictive a aussi connu une avancée notable. L’intégration de capteurs intelligents et de technologies de surveillance à distance dans les machines de formage de tôle permet de détecter les anomalies avant qu’elles ne se transforment en pannes majeures. Ces capteurs mesurent des paramètres tels que la température, la pression, les vibrations et l’usure des composants clés. En analysant ces données en temps réel, les systèmes de maintenance prédictive peuvent alerter les opérateurs ou planifier des interventions avant qu’une défaillance ne se produise, ce qui permet de réduire les temps d’arrêt et d’améliorer la disponibilité des machines.
Le marché des machines de déformation de tôle continue de croître, avec une forte demande pour des solutions modulaires et modifiables qui peuvent être adaptées aux besoins spécifiques des clients. Les fournisseurs de machines se concentrent sur la création de plateformes flexibles qui permettent de configurer différentes options en fonction des exigences de production, qu’il s’agisse de la taille des tôles, de la complexité des formes à produire ou des matériaux utilisés. Ce type de machine modulaire permet aux entreprises de faire évoluer leurs installations de production en fonction des changements dans la demande, des matériaux disponibles ou des technologies émergentes.
L’avenir de la technologie de déformation de tôle se dirige vers des solutions encore plus intelligentes, connectées et flexibles, avec des systèmes d’intelligence artificielle (IA) capables d’optimiser les paramètres de production en temps réel et d’apprendre des données générées par chaque cycle de fabrication. Ces systèmes intelligents permettront une adaptation dynamique des processus, des matériaux et des outils utilisés, en fonction des conditions réelles de production, tout en maintenant un niveau élevé de qualité et d’efficacité.
Enfin, la collaboration entre machines et opérateurs restera un aspect essentiel de l’industrie du formage de tôle. L’interaction entre les machines, les opérateurs et les technologies avancées de contrôle permettra de maintenir une production efficace, tout en garantissant des conditions de travail sûres et ergonomiques. Des interfaces utilisateur simplifiées et des assistants virtuels (par exemple, via réalité augmentée) aideront les opérateurs à gérer les processus de manière plus intuitive et à résoudre les problèmes plus rapidement, facilitant ainsi la transition vers des usines de plus en plus autonomes et intelligentes.
Unités de formage de tôle
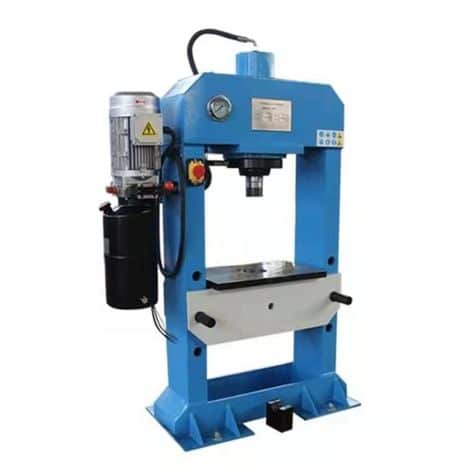
Les unités de formage de tôle sont des ensembles de machines et d’équipements industriels dédiés à la transformation de tôles métalliques en pièces de formes spécifiques, tout en respectant des normes de qualité strictes. Ces unités sont conçues pour optimiser les processus de production en série, garantissant une efficacité maximale et des résultats précis. Elles combinent diverses machines spécialisées dans des étapes successives de transformation de la tôle, allant de la coupe à la déformation, en passant par le pliage et l’emboutissage. Voici les principaux composants d’une unité de formage de tôle :
- Chargeurs de tôles : Ce sont des dispositifs qui permettent de manipuler et de positionner les tôles métalliques sur la ligne de production. Les chargeurs de tôles peuvent être automatiques ou manuels, et ils facilitent le passage fluide du matériau entre les différentes machines de la ligne de formage. Ils sont souvent équipés de rouleaux ou de ventouses pour soulever et déplacer les tôles sans les endommager.
- Machines de coupe (cisailles, scies, laser) : Dans le processus de formage de tôle, il est souvent nécessaire de découper les tôles à des dimensions spécifiques avant de les envoyer vers d’autres machines pour leur transformation. Les cisailles hydrauliques ou mécaniques sont couramment utilisées pour couper des tôles de manière droite ou en formes spécifiques. Les machines de découpe au laser et plasma sont également populaires pour leur capacité à couper avec une grande précision des tôles plus épaisses ou des matériaux spéciaux.
- Plieuses et presses-plieuses : Ces machines sont utilisées pour plier les tôles métalliques et leur donner des formes angulaires. Elles exercent une pression sur la tôle entre un poinçon et une matrice pour créer des plis dans la tôle. Les plieuses hydrauliques, les presses à commande numérique (CNC) ou les machines à commande manuelle sont utilisées en fonction de la complexité des formes et de la taille des pièces à produire. Elles sont généralement utilisées pour fabriquer des pièces en tôle qui doivent être pliées en angles précis, comme des boîtiers, des châssis ou des panneaux.
- Poinçonneuses : Les poinçonneuses sont utilisées pour percer des trous ou pour créer des motifs complexes dans les tôles métalliques. Elles fonctionnent en appuyant un poinçon sur la tôle pour créer des trous d’un diamètre précis. Les poinçonneuses à commande numérique (CNC) permettent d’effectuer des opérations de perforation de manière automatisée et rapide. Elles sont particulièrement efficaces pour la fabrication de pièces avec des perforations multiples et régulières, telles que des grilles, des filtres ou des panneaux perforés.
- Machines de formage à froid : Ces unités de formage sont utilisées pour déformer les tôles métalliques à température ambiante. Le formage à froid permet de créer des formes complexes sans nécessiter de chauffage préalable, ce qui préserve les propriétés mécaniques du matériau. Cela comprend des processus comme le profilage, le repliement, le façonnage ou l’emboutissage. Ces machines sont souvent utilisées pour produire des pièces métalliques telles que des profilés, des conduits ou des composants pour l’industrie automobile.
- Emboutisseuses et machines à emboutir : Ces machines sont conçues pour effectuer des opérations de formage profond, où une tôle est enfoncée dans une matrice pour en faire une pièce à forme tridimensionnelle. L’emboutissage à froid est couramment utilisé pour des applications comme la fabrication de panneaux de carrosserie, de coques ou d’autres pièces métalliques complexes dans l’automobile et l’aérospatial. L’emboutissage peut être effectué par une seule machine ou intégré dans une ligne de production de formage de tôle.
- Rouleuses à commande numérique (CNC) : Les rouleuses CNC sont utilisées pour former des tôles métalliques en courbes ou en cylindres. Elles exercent une pression sur la tôle, qui est ensuite manipulée pour lui donner la forme souhaitée. Ces machines permettent de réaliser des pièces à forme circulaire ou conique, telles que des tuyaux, des réservoirs ou des pièces arrondies. Les rouleuses CNC offrent une grande flexibilité et précision, permettant de réaliser des courbes serrées ou des arcs complexes.
- Machines de matriçage et de formage rotatif : Ces unités sont utilisées pour réaliser des formes complexes à l’aide de matrices. Le matriçage permet de créer des formes précises avec un minimum de déformation, tandis que le formage rotatif est une méthode spécifique pour traiter des matériaux en utilisant un mouvement rotatif qui façonne la tôle en une forme spécifique, souvent conique ou cylindrique. Ces techniques sont utilisées dans des applications comme la fabrication de coques ou de pièces avec une forme régulière mais complexe.
- Machines de déformation à chaud : Bien que la plupart des processus de déformation de tôle soient effectués à froid, certains matériaux nécessitent un traitement thermique avant leur déformation. Les machines de déformation à chaud sont utilisées pour travailler des tôles métalliques chauffées à des températures élevées, facilitant leur transformation en formes complexes tout en réduisant la résistance du matériau. Ce processus est particulièrement utile pour les métaux durs comme l’acier.
- Systèmes de contrôle et de surveillance : Les unités modernes de formage de tôle sont souvent équipées de systèmes de contrôle automatisés pour optimiser les processus de production. Ces systèmes assurent la gestion des paramètres de la machine, la synchronisation des différentes étapes de production et la détection en temps réel des anomalies. L’utilisation de technologies de capteurs intelligents et d’analyse de données permet de prévoir l’usure des outils, d’ajuster automatiquement les machines et d’optimiser la production.
- Systèmes de manutention automatisée : Dans les grandes unités de formage de tôle, les systèmes de manutention automatisée sont utilisés pour déplacer les tôles à travers les différentes étapes de production. Cela peut inclure des convoyeurs, des bras robotiques ou des systèmes à vide qui permettent de manipuler les tôles sans contact direct, réduisant ainsi le risque de dommages et améliorant l’efficacité des flux de travail.
Les unités de formage de tôle modernes sont de plus en plus intégrées et automatisées, permettant des cycles de production plus courts, une précision accrue et une réduction des coûts. La combinaison de machines de formage spécialisées et de systèmes de contrôle avancés permet d’optimiser chaque étape du processus de production tout en garantissant une qualité constante des pièces fabriquées.
Les unités de formage de tôle modernes se caractérisent par une intégration poussée des technologies automatisées, permettant de rendre les processus de fabrication plus efficaces, flexibles et précis. Elles sont conçues pour répondre aux exigences des industries où les pièces métalliques doivent être produites à grande échelle tout en maintenant des standards de qualité stricts. Grâce à l’automatisation, ces unités permettent une gestion optimisée de la production, réduisant les erreurs humaines, augmentant la productivité et garantissant des tolérances serrées. Le contrôle de qualité est intégré tout au long du processus, avec des technologies de vision industrielle et des capteurs de haute précision qui détectent toute déviation dans la forme ou la dimension des pièces fabriquées, permettant ainsi de corriger immédiatement toute non-conformité.
Une des avancées majeures dans les unités de formage de tôle est l’utilisation des systèmes de fabrication flexibles. Ces systèmes permettent de passer rapidement d’une production en grande série à des petites séries, ou même des pièces uniques personnalisées, sans nécessiter des modifications substantielles des équipements. Cette flexibilité est obtenue grâce à l’automatisation et aux machines modulaires qui peuvent être configurées selon les besoins spécifiques de chaque production. Par exemple, une même unité peut être utilisée pour produire des composants automobile de grande série, puis être reconfigurée pour fabriquer des pièces complexes pour l’industrie aérospatiale, avec des ajustements minimes dans les paramètres de production.
En outre, l’adoption des systèmes de simulation avant même la mise en production permet aux ingénieurs de tester virtuellement les étapes de formage, optimisant ainsi les cycles de production. Ces logiciels permettent de simuler le comportement des matériaux sous différentes conditions de pression, température et déformation, ce qui aide à anticiper les problèmes avant qu’ils n’apparaissent dans la production réelle. L’analyse des simulations offre aussi des informations précieuses sur la durée de vie des outils et des matrices, ce qui permet de planifier une maintenance préventive et d’éviter les arrêts imprévus.
L’utilisation des systèmes de maintenance prédictive basés sur l’IoT (Internet des objets) permet de suivre en temps réel l’état de chaque machine. Grâce aux capteurs intelligents installés sur les équipements, des données précieuses sont collectées sur des paramètres tels que la température, l’humidité, les vibrations et la pression. Ces informations sont ensuite envoyées à une plateforme de gestion qui analyse les performances et détecte d’éventuelles anomalies. Si une machine commence à présenter des signes d’usure ou de défaillance, une alerte est envoyée, ce qui permet aux opérateurs de prendre des mesures avant que des pannes coûteuses ne se produisent. Cette technologie contribue à améliorer la fiabilité des équipements, à prolonger leur durée de vie et à réduire les coûts de maintenance.
Les équipements de traitement thermique sont également essentiels dans certaines unités de formage, car certains matériaux nécessitent un chauffage préalable avant d’être formés pour éviter la fissuration ou d’autres défauts. Cela inclut des processus comme le recuit, qui est utilisé pour ramollir la tôle avant de la soumettre à des opérations de déformation. Le chauffage localisé par induction ou par four est souvent utilisé dans ces cas pour assurer une chaleur uniforme et précise. Ce traitement permet de réduire la dureté du matériau et d’améliorer sa malléabilité sans compromettre sa résistance une fois refroidi.
Les unités de formage de tôle sont souvent interconnectées à des systèmes de gestion de la production (MES – Manufacturing Execution Systems), qui assurent une coordination optimale entre les différentes machines et le flux de matériaux. Ces systèmes surveillent l’ensemble de la production, optimisent les processus en temps réel et permettent une traçabilité complète de chaque pièce fabriquée. Cela est particulièrement important pour les industries où les exigences de qualité et de traçabilité sont strictes, comme l’aérospatiale ou l’automobile, où chaque pièce doit être enregistrée et contrôlée pour répondre aux normes réglementaires.
Les évolutions récentes dans les technologies de formage de tôle ont également permis l’introduction de machines de formage hybrides qui combinent plusieurs techniques en une seule unité. Par exemple, des machines qui combinent l’emboutissage et le formage à froid permettent de réaliser des pièces complexes en une seule étape, réduisant ainsi les coûts et le temps de cycle de fabrication. Ces machines sont capables de traiter différents types de métaux et d’alliages, offrant ainsi une polyvalence importante dans la production.
Les unités de formage de tôle modernes tendent également à être plus écologiques. L’accent est mis sur la réduction de la consommation d’énergie et de matériaux. Des systèmes de récupération d’énergie et de recyclage des chutes sont de plus en plus utilisés pour minimiser l’impact environnemental. De plus, certaines machines sont équipées de systèmes de filtration pour réduire les émissions de poussières et d’autres contaminants produits lors des processus de découpe et de formage. Les usines de formage de tôle de demain seront donc de plus en plus respectueuses de l’environnement, tout en répondant aux exigences de production et de qualité des clients.
Les tendances futures dans ce domaine incluent également le développement de machines encore plus intelligentes, utilisant des technologies avancées comme l’intelligence artificielle pour optimiser les processus de fabrication en temps réel. Ces machines pourraient analyser les données de production pour prévoir les ajustements nécessaires et même améliorer la conception des pièces en fonction des retours d’expérience. L’intégration des technologies de réalité augmentée et de réalité virtuelle pour l’assistance à la maintenance et à la formation des opérateurs est également une direction prometteuse pour améliorer encore l’efficacité des unités de formage de tôle.
En conclusion, les unités de formage de tôle continuent de se transformer grâce à l’intégration des technologies de pointe, permettant non seulement de produire des pièces métalliques plus rapidement et avec une précision accrue, mais aussi de répondre à des exigences de durabilité, de flexibilité et de rentabilité. Ces avancées technologiques permettent aux industries de s’adapter à des marchés de plus en plus exigeants, tout en optimisant les coûts et en garantissant une qualité constante.
Les innovations continues dans le domaine des unités de formage de tôle apportent des changements significatifs dans la manière dont les entreprises abordent la fabrication. L’un des développements les plus remarquables est l’intégration croissante des technologies de l’intelligence artificielle (IA) et du machine learning dans les processus de production. Grâce à ces technologies, les machines sont capables d’apprendre et d’adapter leurs opérations en fonction des conditions de fabrication et des variations des matériaux. Cela permet non seulement d’optimiser les performances de chaque machine, mais aussi de prédire et de corriger les défauts avant qu’ils ne se produisent, réduisant ainsi les rebuts et augmentant la rentabilité globale des lignes de production.
Les systèmes de vision industrielle associés à l’IA sont utilisés pour inspecter les pièces en temps réel tout au long du processus de fabrication. Les caméras et capteurs sophistiqués sont capables de détecter des défauts microscopiques, tels que des irrégularités dans les dimensions, des fissures superficielles ou des écarts par rapport aux tolérances, et d’envoyer immédiatement un signal aux opérateurs ou aux machines pour ajuster les paramètres de production. Cela permet d’améliorer la qualité des produits finis et de réduire les coûts liés aux erreurs humaines et aux défauts de production.
Dans le même esprit d’optimisation, l’adoption de l’automatisation robotique dans les unités de formage de tôle est de plus en plus courante. Les robots collaboratifs ou cobots, qui interagissent directement avec les opérateurs humains, sont utilisés pour effectuer des tâches répétitives ou dangereuses, comme le chargement et le déchargement des tôles, la manipulation des pièces ou l’assemblage des composants. Ces cobots sont dotés de capteurs de sécurité et d’une grande flexibilité, ce qui leur permet de travailler aux côtés des humains sans risquer de causer des accidents. Leur capacité à s’adapter à des environnements de travail variés et à effectuer des tâches complexes les rend particulièrement adaptés à des lignes de production flexibles, où la demande varie fréquemment.
Les progrès en matière de numérisation et de connectivité permettent aux entreprises de suivre l’ensemble de leur production grâce à des systèmes de gestion de la production en temps réel (MES) et des plateformes de cloud computing. Ces systèmes permettent une gestion à distance des lignes de production, une optimisation des flux de matières et de personnel, ainsi qu’une gestion des stocks améliorée. De plus, l’utilisation du cloud permet de collecter et d’analyser des volumes massifs de données issues des différentes machines de formage de tôle. Ces données peuvent être utilisées pour anticiper les besoins de maintenance, optimiser les performances des machines et même prévoir les tendances de la demande.
La fabrication additive ou impression 3D commence également à jouer un rôle dans la production de pièces métalliques pour certaines applications spécifiques. Bien que l’impression 3D ne remplace pas les processus traditionnels de formage de tôle dans la production de masse, elle offre des possibilités intéressantes pour créer des prototypes, des pièces complexes ou des petites séries de manière plus économique. Les pièces en métal peuvent être imprimées couche par couche à partir de poudres métalliques, offrant une liberté de conception qui dépasse celle des méthodes de fabrication conventionnelles. Cela est particulièrement utile pour l’industrie aérospatiale et la fabrication de pièces très spécifiques, où des géométries complexes sont nécessaires.
Les machines de formage de tôle sont également de plus en plus capables de traiter des matériaux composites, en plus des métaux traditionnels. Les matériaux composites, qui combinent différents matériaux pour obtenir des propriétés spécifiques (comme la légèreté, la résistance ou la flexibilité), trouvent une application croissante dans l’industrie automobile et aérospatiale. Ces matériaux exigent des machines spécialisées qui peuvent traiter à la fois la tôle métallique et les matériaux composites, permettant ainsi une production hybride de pièces métalliques et composites dans une même ligne de production.
L’optimisation énergétique est une priorité pour de nombreuses entreprises, en particulier dans un contexte où les préoccupations environnementales et les coûts énergétiques sont de plus en plus importants. Les unités de formage de tôle modernes intègrent des technologies de gestion de l’énergie afin de réduire leur empreinte carbone. Cela peut inclure l’utilisation d’énergies renouvelables, des systèmes de récupération thermique pour récupérer et réutiliser la chaleur excédentaire générée pendant le processus de fabrication, ainsi que des moteurs à haute efficacité énergétique pour réduire la consommation d’énergie globale. Les systèmes intelligents de gestion de l’énergie permettent aussi d’optimiser l’utilisation de l’énergie en fonction des besoins de la production en temps réel, ce qui permet de réaliser des économies substantielles.
De plus, la durabilité et l’écoconception sont des aspects de plus en plus pris en compte dans la conception des machines de formage de tôle. Les fabricants s’efforcent de concevoir des équipements qui consomment moins de ressources et qui sont plus facilement recyclables en fin de vie. Par exemple, certaines machines sont fabriquées à partir de matériaux plus légers ou de composants modulaires qui facilitent leur réparation et leur mise à niveau, prolongeant ainsi leur durée de vie. Les fabricants adoptent également des pratiques de recyclage des chutes de tôle, en intégrant ces matériaux dans la production afin de réduire le gaspillage.
Les nouvelles méthodes de fabrication de tôles métalliques se concentrent également sur la possibilité de manipuler des tôles de plus en plus fines et de plus en plus résistantes. Les progrès dans le domaine des matériaux, comme les alliages métalliques avancés ou les traitements thermiques innovants, permettent de produire des tôles plus légères tout en augmentant leur résistance. Ces tôles peuvent être utilisées dans des applications où le poids est un facteur critique, comme dans l’industrie automobile, aéronautique et dans la fabrication de dispositifs électroniques.
Enfin, les défis futurs dans le domaine du formage de tôle comprennent la gestion de la complexité croissante des pièces à produire. Les demandes de personnalisation des produits finis augmentent, et les fabricants doivent être capables de s’adapter rapidement aux nouvelles exigences tout en optimisant les coûts. Cela nécessite des investissements dans des technologies plus avancées, de meilleurs systèmes de gestion de la production et une amélioration continue des compétences des opérateurs. Le développement de machines plus modulaires et flexibles, capables de traiter une variété de matériaux et de types de pièces, sera essentiel pour répondre à ces nouveaux défis.
En somme, les unités de formage de tôle continuent de progresser grâce à l’intégration des technologies avancées, offrant ainsi des solutions de production plus efficaces, écologiques et intelligentes.
L’évolution des unités de formage de tôle ne se limite pas uniquement aux technologies de production, mais touche également l’aspect gestion et organisation de la chaîne de valeur. L’optimisation de la supply chain devient un facteur clé dans la réussite des entreprises qui fabriquent des pièces métalliques. Grâce à des outils comme l’intelligence artificielle et l’apprentissage automatique, les fabricants peuvent prévoir plus précisément les besoins en matières premières, optimiser les stocks et gérer les délais de production en fonction des demandes du marché.
Les logistiques internes au sein des usines sont également impactées par ces évolutions. Les robots autonomes de transport et de stockage (AGV – Automated Guided Vehicles) sont utilisés pour déplacer les tôles métalliques ou les pièces semi-finies d’une machine à une autre sans intervention humaine. Cela permet de réduire les risques de dommages aux pièces et améliore la sécurité des opérateurs. Ces systèmes de transport sont souvent couplés avec des systèmes de gestion de la production (MES) pour assurer que chaque pièce est traitée dans le bon ordre, à la bonne machine et au bon moment, minimisant ainsi les temps d’attente et améliorant le flux global de production.
Les systèmes de traçabilité deviennent également de plus en plus sophistiqués. La traçabilité en temps réel des pièces de tôle au sein de la chaîne de production permet une meilleure gestion des stocks et une réponse plus rapide aux problèmes de qualité. Les données sont collectées à chaque étape du processus de fabrication et sont accessibles en temps réel par les opérateurs, les responsables de la production et même les clients dans certains cas. Cela permet une gestion plus transparente et plus réactive des processus, contribuant ainsi à une amélioration continue de la qualité et à la satisfaction client.
Un autre aspect important de l’évolution des unités de formage de tôle est la gestion du cycle de vie des machines. En plus de la maintenance prédictive déjà mentionnée, les fabricants mettent en place des contrats de service ou des programmes de maintenance à distance. Ces contrats garantissent qu’une équipe d’experts suit l’état des équipements à distance, assure les mises à jour nécessaires et intervient dès qu’une anomalie est détectée. Cela permet d’améliorer l’efficacité des machines tout en réduisant les coûts de maintenance. L’utilisation de plateformes cloud permet de stocker et d’analyser les données issues des machines de manière centralisée, rendant ainsi la gestion des équipements plus simple et plus fluide.
Les méthodes de gestion de la qualité deviennent également de plus en plus rigoureuses. Les normes de qualité ISO et autres certifications sont essentielles dans des industries telles que l’aérospatiale, l’automobile ou l’électronique. Afin d’assurer la conformité, les entreprises mettent en place des systèmes de contrôle statistique de processus (SPC) et des tests de validation avancés. Ces systèmes permettent de détecter et de corriger les dérives de production avant qu’elles n’affectent les produits finis. En plus des inspections visuelles et des contrôles dimensionnels, l’intégration de l’impression 3D pour créer des prototypes numériques avant le lancement de la production peut également permettre de tester les pièces dans des conditions réelles de fonctionnement avant leur fabrication.
Le développement durable reste au cœur des préoccupations, et l’industrie du formage de tôle met en œuvre des stratégies de recyclage avancées. Non seulement les chutes de métal sont recyclées dans des processus fermés pour être réutilisées dans la production, mais des technologies de recyclage énergétique sont également mises en place pour récupérer l’énergie excédentaire des machines. Cela comprend les systèmes de récupération de chaleur qui utilisent l’énergie thermique générée par les processus de formage pour alimenter d’autres parties du processus de production, ce qui permet de réduire la consommation énergétique globale des usines.
Les technologies vertes et écologiques se développent également au sein des machines elles-mêmes. Par exemple, de nouvelles techniques de lubrification et de refroidissement qui utilisent des fluides biodégradables et non-toxiques sont mises en place pour réduire l’impact environnemental. De plus, les fabricants investissent dans la réduction de l’empreinte carbone de leurs machines, en utilisant des matériaux et des composants plus durables et en optimisant la consommation d’énergie. Les machines de formage de tôle de demain intégreront probablement des solutions éco-efficientes, non seulement pour respecter des réglementations environnementales de plus en plus strictes, mais aussi pour répondre aux attentes des consommateurs et des partenaires commerciaux en matière de responsabilité sociétale.
L’impact de la digitalisation est également majeur dans la conception des unités de formage de tôle. Les logiciels de conception assistée par ordinateur (CAO) et de fabrication assistée par ordinateur (FAO) sont désormais utilisés pour optimiser la conception des pièces et le processus de fabrication en même temps. En utilisant des modèles numériques et des simulations de processus, les ingénieurs peuvent prévoir comment une pièce se comportera sous pression, quelle sera la déformation à chaque étape, et comment les machines doivent être ajustées pour obtenir le meilleur résultat. Ces outils permettent de réduire les erreurs de conception et de fabrication, augmentant ainsi l’efficacité et la qualité du produit final.
Enfin, l’exploration de nouvelles applications des matériaux s’est intensifiée. Les alliages métalliques légers, les matériaux à haute résistance et les nouvelles générations de revêtements métalliques ouvrent des horizons nouveaux pour l’industrie. Par exemple, les tôles de titane, d’aluminium ou les matériaux composites à base de fibres de carbone nécessitent des processus de formage spécialement adaptés. De même, le développement de nouveaux types de traitements thermiques et de recuits contrôlés permet de mieux exploiter les caractéristiques de ces matériaux avancés et d’obtenir des pièces encore plus résistantes tout en conservant leur légèreté.
Le formage de tôle se dirige donc vers une révolution technologique, où l’automatisation, l’intelligence artificielle, et l’écologie ne sont plus de simples tendances, mais des composantes fondamentales d’une production industrielle moderne. Ces évolutions permettent non seulement de répondre aux besoins actuels des industries, mais aussi d’anticiper les défis de demain, offrant ainsi des solutions de fabrication plus efficaces, plus flexibles et plus durables.
Machines de pliage et formage de tôle

Les machines de pliage et de formage de tôle jouent un rôle essentiel dans le processus de transformation de tôles métalliques, permettant de donner aux pièces métalliques une forme spécifique pour des applications variées dans les industries automobile, aéronautique, électronique, et bien d’autres secteurs. Ces machines sont utilisées pour créer des angles, des bords, des courbes ou des formes complexes à partir de tôles plates, et sont capables de traiter une grande variété de métaux, y compris l’acier, l’aluminium, l’inox, et même certains matériaux composites.
Voici une vue d’ensemble des principaux types de machines de pliage et de formage de tôle, ainsi que leurs caractéristiques et applications :
1. Plieuses (ou Plieuses à tablier)
Les plieuses sont des machines utilisées principalement pour plier des tôles métalliques sur un axe, créant ainsi des angles ou des bords. Ce type de machine est utilisé pour produire des pièces ayant des angles droits ou des plis simples. Les tôles sont maintenues en place sur la table de travail tandis qu’une presse pousse une lame ou un poinçon vers le bas pour effectuer le pliage.
- Plieuses manuelles : Conviennent pour des travaux de faible volume ou des applications simples.
- Plieuses CNC (contrôle numérique par ordinateur) : Ces machines sont automatiques et peuvent effectuer des plis très précis avec un contrôle numérique, ce qui permet des plis complexes à grande échelle. Elles sont largement utilisées pour des productions en série et de haute précision.
2. Plieuses à cintre (ou presses à plier)
Les plieuses à cintre permettent de former des tôles métalliques par un mouvement de cintre qui déforme la tôle dans une courbure souhaitée. La presse appuie contre la tôle pour l’amener à la forme désignée.
- Ces machines sont particulièrement adaptées pour créer des courbes complexes ou des formes plus élaborées, comme des profilés ou des canaux.
- Elles sont utilisées pour des applications où les tôles doivent être pliées selon des angles variés, et non seulement des plis droits.
3. Presses plieuses à commande numérique (CNC)
Les presses plieuses CNC sont une évolution des plieuses traditionnelles, où le mouvement et les paramètres de pliage sont contrôlés électroniquement à l’aide d’un système informatique. Cela permet de réaliser des pliages complexes avec des tolérances extrêmement précises, offrant une flexibilité maximale dans la production de pièces.
- La commande numérique permet à l’opérateur d’entrer directement des données pour des angles et des configurations spécifiques, ce qui augmente la productivité et la précision.
- Ces presses peuvent être équipées de systèmes de détection de pression, garantissant une uniformité dans chaque pliage et réduisant les risques de déformation non désirée de la tôle.
4. Machines de formage rotatif
Le formage rotatif est une méthode utilisée pour plier ou façonner des tôles par rotation, en utilisant un ensemble de rouleaux. Ce processus est utilisé pour produire des formes cylindriques ou coniques à partir de tôles métalliques.
- Ces machines sont utilisées pour produire des pièces cylindriques, comme des tuyaux ou des conduits, et sont couramment utilisées dans les industries aérospatiale et automobile.
- Elles sont capables de travailler avec des matériaux fins et épais tout en préservant la forme désirée avec des tolérances serrées.
5. Rouleuses (ou rouleuses de tôle)
Les rouleuses sont utilisées pour courber des tôles métalliques. Elles fonctionnent avec des rouleaux qui appliquent une pression uniforme sur la tôle, la faisant se plier selon un rayon donné. Cette machine est essentielle pour fabriquer des courbes douces ou des formes arrondies.
- Il existe plusieurs types de rouleuses, dont les rouleuses à 3 rouleaux et les rouleuses à 4 rouleaux, chacune ayant une configuration différente pour contrôler le type de courbure.
- Ces machines sont très polyvalentes et adaptées pour réaliser des cylindres, des boudins, ou des coques pour des applications comme des cuves, des réservoirs ou des pièces d’architecture.
6. Cisailles de coupe et machines de découpe
Les cisailles de coupe sont utilisées pour couper des tôles métalliques avant ou après le processus de pliage, souvent en combinaison avec des machines de formage. Les lames de la cisaille coupent la tôle avec une grande précision et sont idéales pour produire des bords nets.
- Les cisailles peuvent être utilisées pour découper des tôles de différents types de métaux, comme l’acier ou l’aluminium.
- Elles sont souvent intégrées dans des lignes de production automatisées, où la tôle est d’abord découpée puis pliée ou formée.
7. Machines de formage à emboutissage profond
Le formage à emboutissage profond est un procédé de déformation qui permet de créer des pièces complexes à partir de tôles plates en les emboutissant dans des moules. Cette méthode est couramment utilisée pour créer des formes profondes comme des boîtiers, des composants automobiles ou des pièces de mobilier.
- Ces machines utilisent des matrices et des poinçons pour appliquer une pression localisée sur la tôle afin de la déformer de manière contrôlée.
- Elles sont particulièrement adaptées pour produire des pièces dont les dimensions sont complexes et qui nécessitent des formes profondes et précises.
8. Formage à chaud (ou formage thermique)
Le formage à chaud est une méthode où la tôle est chauffée à une température élevée avant d’être déformée, ce qui réduit la résistance du matériau et facilite sa manipulation. Ce processus est utilisé pour former des tôles épaisses ou des matériaux ayant une dureté élevée.
- Il est couramment utilisé pour fabriquer des pièces de grande taille, comme des tôles de voitures, des pièces aérospatiales, et dans l’industrie du moulage de métaux.
- Le formage à chaud nécessite des équipements spécialisés pour maintenir et contrôler la température, tout en assurant que la déformation se fasse de manière uniforme et contrôlée.
Applications courantes des machines de pliage et de formage de tôle :
- Industrie automobile : Fabrication de pièces carrossées, pare-chocs, châssis, etc.
- Aéronautique : Fabrication de structures légères mais solides, pièces de fuselage.
- Construction métallique : Conception de structures en métal pour des bâtiments, des ponts, des infrastructures.
- Fabrication de mobilier métallique : Composants métalliques pour meubles industriels, étagères, armoires, etc.
Conclusion :
Les machines de pliage et de formage de tôle représentent un secteur crucial de l’industrie manufacturière, offrant des solutions pour transformer des tôles métalliques en pièces finies à partir de concepts de design sophistiqués. Avec les évolutions technologiques, notamment l’intégration de la robotisation, du contrôle numérique et des systèmes intelligents de production, ces machines permettent de répondre à des exigences de précision, de flexibilité et de productivité toujours plus importantes.
Les machines de pliage et de formage de tôle continuent d’évoluer avec les avancées technologiques, permettant une amélioration continue en matière de productivité, de qualité et de flexibilité des processus de fabrication. L’automatisation des machines de formage de tôle est devenue un impératif dans l’industrie moderne, permettant de réduire les coûts de production tout en augmentant la précision et la rapidité des processus. Ces machines, qu’elles soient manuelles ou automatisées, sont conçues pour répondre à des besoins spécifiques qui varient en fonction de la nature de la pièce à produire, des matériaux utilisés, et des volumes de production.
L’intégration de la robotisation dans ces machines permet de réaliser des tâches de manière plus rapide et efficace. Par exemple, des robots de manipulation peuvent être utilisés pour charger et décharger automatiquement les tôles dans les presses et plieuses, améliorant ainsi le flux de production et réduisant les risques d’erreurs humaines. De plus, les robots peuvent travailler en collaboration avec les opérateurs humains dans des environnements de fabrication de plus en plus automatisés, ce qui permet de maximiser la productivité et de réduire le temps d’attente entre les différentes étapes de la production.
L’intelligence artificielle (IA) et les systèmes de contrôle numériques jouent également un rôle crucial dans la gestion des machines de pliage et de formage de tôle. Les logiciels CNC (Contrôle Numérique par Ordinateur) permettent de programmer les machines avec une grande précision, et les systèmes d’apprentissage automatique peuvent analyser les données en temps réel pour ajuster les paramètres de fabrication en fonction des conditions de production, des variations des matériaux ou des exigences du client. Ces systèmes offrent une grande flexibilité, permettant des ajustements rapides pour répondre à des commandes de production personnalisées tout en maintenant un niveau élevé de qualité.
Les technologies de maintenance prédictive et de surveillance à distance sont également de plus en plus courantes. Grâce à des capteurs intelligents et à des systèmes connectés, les performances des machines peuvent être surveillées en temps réel. Cela permet de détecter les problèmes avant qu’ils ne deviennent critiques, de planifier les interventions de maintenance de manière proactive et de réduire ainsi les temps d’arrêt imprévus. Ces technologies aident également à prolonger la durée de vie des équipements, à optimiser leur efficacité énergétique et à garantir une production continue sans interruption.
Les matériaux utilisés dans la fabrication des tôles et dans les machines elles-mêmes sont également en constante évolution. Les matériaux allégés, tels que les alliages d’aluminium, et les nouveaux composites, comme les matériaux composites renforcés de fibres de carbone, sont de plus en plus utilisés dans l’industrie de la tôle. Ces matériaux permettent de créer des pièces plus légères et plus résistantes, tout en réduisant les coûts énergétiques pendant la fabrication. Les revêtements de protection innovants sont également développés pour améliorer la durabilité et la résistance à la corrosion des pièces en métal, en particulier pour les applications extérieures ou les environnements industriels difficiles.
Le recyclage des matériaux est un autre aspect essentiel dans l’industrie du formage de tôle. En réponse aux préoccupations environnementales croissantes, de nombreuses entreprises mettent en place des processus de recyclage pour réutiliser les chutes et les restes de tôle. Cela non seulement permet de réduire les déchets, mais aussi de réduire les coûts de production, tout en répondant aux normes environnementales strictes. Les usines intègrent des systèmes de gestion des déchets plus sophistiqués, garantissant que les matériaux non utilisés sont récupérés et réintégrés dans le cycle de production.
Les machines de formage de tôle deviennent également plus ergonomiques et plus sûres pour les opérateurs. L’intégration de dispositifs de sécurité tels que les capteurs de proximité, les barrières automatiques et les arrêts d’urgence réduit les risques d’accidents sur le lieu de travail. De plus, les environnements de travail deviennent plus confortables et accessibles, permettant aux opérateurs de travailler pendant de longues périodes sans fatigue excessive.
Un autre domaine où l’innovation est en plein essor est celui de l’optimisation des cycles de production. Les machines modernes sont capables de travailler avec une grande rapidité tout en maintenant une qualité de production constante. Les machines de formage de tôle peuvent être programmées pour optimiser les séquences de fabrication, ce qui permet de réduire les délais de production et d’augmenter le rendement global des équipements. L’utilisation de logiciels de gestion de production avancés permet de planifier de manière plus stratégique la répartition des tâches, le suivi de la production et la gestion des stocks, assurant ainsi une meilleure organisation de la chaîne de fabrication.
Les marchés mondiaux exigent également des solutions de formage de tôle plus flexibles et adaptables. Les entreprises qui utilisent ces machines doivent répondre à des demandes personnalisées tout en restant compétitives. De nouvelles tendances de production à la demande, où les clients exigent des pièces métalliques spécifiques en petites séries, ont émergé, ce qui met la pression sur les fabricants pour qu’ils offrent des délais de production plus courts, sans sacrifier la qualité. L’adaptabilité des machines de formage de tôle aux nouveaux designs et matériaux est donc essentielle pour rester compétitif sur le marché.
En conclusion, l’industrie des machines de pliage et de formage de tôle est en pleine transformation. Grâce à l’introduction de technologies telles que l’automatisation, l’intelligence artificielle, la maintenance prédictive et l’optimisation des matériaux, la production devient plus rapide, plus précise et plus respectueuse de l’environnement. Ces évolutions permettent aux fabricants de répondre aux exigences croissantes du marché tout en maximisant la qualité, la sécurité et l’efficacité des processus de production.
L’industrie des machines de formage de tôle continue de s’adapter aux besoins croissants de flexibilité, de durabilité et d’efficacité énergétique. En plus des innovations technologiques, il y a une tendance vers la personnalisation des solutions de formage. Les entreprises doivent être en mesure de produire des pièces métalliques plus complexes et diversifiées tout en respectant des délais de fabrication réduits et des coûts de production optimisés. L’un des aspects clés de cette évolution est la possibilité de fabrication agile, où les machines peuvent être reconfigurées rapidement pour répondre aux nouvelles demandes des clients sans nécessiter de longs temps d’arrêt ou de changements coûteux dans la chaîne de production.
Développement des matériaux
Les matériaux utilisés dans les tôles métalliques sont devenus plus diversifiés et sophistiqués, ce qui impose des exigences accrues aux machines de formage. En particulier, les alliages haute performance, comme les alliages à haute résistance, sont désormais utilisés pour créer des composants qui doivent résister à des contraintes mécaniques et thermiques plus sévères. Cela exige des machines capables de traiter des matériaux plus durs et plus complexes sans compromettre la qualité des pièces produites.
Les avancées dans le domaine des matériaux composites sont également notables. Des matériaux comme les composites à fibres de carbone ou les alliages légers renforcés sont de plus en plus utilisés, notamment dans des secteurs comme l’automobile ou l’aéronautique, où la légèreté et la résistance sont cruciales. Les machines de formage doivent donc être conçues pour travailler avec ces nouveaux matériaux tout en maintenant une productivité élevée et une qualité de finition optimale.
Réduction de l’impact environnemental
Un autre domaine d’évolution des machines de formage de tôle concerne la durabilité et la réduction de l’empreinte carbone des processus de production. De plus en plus de fabricants intègrent des pratiques respectueuses de l’environnement, que ce soit par l’utilisation de matériaux recyclés, la réduction des déchets ou l’optimisation de l’utilisation de l’énergie. La recyclabilité des tôles métalliques devient un enjeu clé, et il est primordial que les machines de formage soient capables de traiter efficacement des matériaux recyclés tout en maintenant des standards de performance.
Les systèmes de contrôle de l’énergie et la gestion des ressources naturelles deviennent essentiels pour les fabricants soucieux de leur empreinte écologique. Par exemple, l’utilisation de technologies comme les moteurs à faible consommation d’énergie, ou l’optimisation des processus de chauffage et de refroidissement pour le formage à chaud, contribue à diminuer les coûts énergétiques tout en répondant aux normes environnementales.
Évolutions vers l’industrie 4.0
L’émergence de l’industrie 4.0 transforme considérablement la façon dont les machines de formage de tôle fonctionnent. L’intégration de capteurs intelligents, de technologies de connectivité et d’outils de gestion de la production basés sur le cloud permet aux fabricants de gérer et d’optimiser en temps réel leurs équipements et leurs processus de production. Par exemple, grâce aux systèmes de gestion de production intelligents, il est possible de suivre l’efficacité des machines et de prendre des décisions basées sur des données en temps réel, réduisant ainsi les risques d’erreurs humaines, améliorant la traçabilité des opérations, et augmentant la rentabilité globale.
Les machines sont désormais souvent équipées de systèmes d’auto-diagnostic qui permettent d’anticiper les problèmes mécaniques ou techniques avant qu’ils n’entraînent des arrêts de production. De plus, l’analyse des données de production permet de déterminer des zones d’amélioration et de prédire les tendances de production, contribuant à une gestion proactive des équipements.
La sécurité des travailleurs
L’amélioration de la sécurité des opérateurs reste une priorité majeure pour les fabricants de machines de formage de tôle. L’introduction de systèmes de sécurité avancés, tels que les capteurs de présence, les dispositifs d’arrêt d’urgence automatiques et les protections anti-chocs, permet de protéger les opérateurs contre les risques mécaniques. Les technologies d’interface homme-machine (IHM) et les systèmes de contrôle à distance facilitent également le travail des opérateurs en leur permettant de superviser le processus de production tout en réduisant leur exposition aux dangers physiques.
En outre, l’ergonomie des machines de formage devient un aspect essentiel du design, pour permettre aux opérateurs de travailler dans des conditions optimales. Les machines modernes sont donc conçues pour réduire la fatigue et le stress des opérateurs, en incorporant des postes de travail réglables, des commandes intuitives et des systèmes de visibilité optimale pour une surveillance facile des machines.
Formation et compétences
Avec l’avancement des technologies, les opérateurs doivent acquérir de nouvelles compétences. La formation continue est devenue indispensable pour les techniciens et les ingénieurs de production afin de rester à jour avec les évolutions des machines et des systèmes de production. De nombreuses entreprises investissent dans des programmes de formation spécialisés pour enseigner la gestion des machines CNC, l’analyse des données de production, et la maintenance préventive, tout en intégrant les meilleures pratiques en matière de sécurité et de durabilité.
Les simulateurs et les réalités augmentée et virtuelle deviennent également des outils populaires dans la formation des opérateurs. Ces technologies permettent aux employés de se familiariser avec le fonctionnement des machines sans risquer de causer des erreurs sur le terrain, augmentant ainsi l’efficacité et la sécurité des environnements de production.
Conclusion
L’industrie des machines de formage de tôle se trouve à un carrefour entre tradition et innovation. Les évolutions technologiques en matière d’automatisation, de connectivité, de matériaux et de respect de l’environnement permettent une amélioration continue des performances des machines tout en répondant aux défis croissants d’une production flexible et responsable. Ces machines permettent de répondre aux exigences de productivité, de qualité, de durabilité, et de sécurité dans un environnement industriel en constante évolution. L’adoption de solutions intelligentes, couplées à une approche de fabrication durable, fait de cette industrie un pilier central de la production moderne, apte à répondre aux besoins des générations futures tout en respectant les défis écologiques et sociaux de notre époque.
Machines de fabrication de pièces en tôle
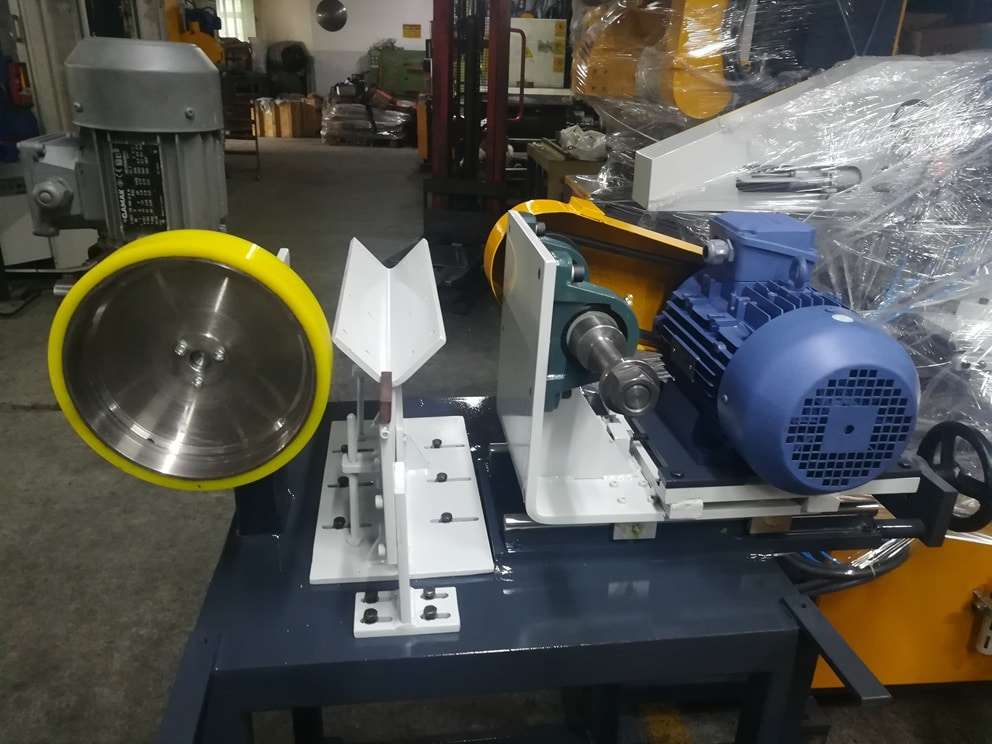
Les machines de fabrication de pièces en tôle jouent un rôle essentiel dans de nombreux secteurs industriels, tels que l’automobile, l’aéronautique, la construction, l’électroménager, et bien d’autres. Ces machines permettent de transformer des tôles métalliques brutes en pièces finies avec des formes complexes et des dimensions précises. Il existe plusieurs types de machines utilisées pour la fabrication de pièces en tôle, chacune étant adaptée à des processus spécifiques de production.
Types de machines pour la fabrication de pièces en tôle :
- Plieuses de tôle (plieuses CNC)
Les plieuses sont utilisées pour plier des tôles métalliques selon des angles précis. Elles peuvent être équipées de commandes numériques (CNC) pour une gestion automatisée des angles et des dimensions de pliage. Ces machines sont idéales pour la production de pièces avec des formes géométriques complexes, telles que des boîtes, des cadres ou des tôles pliées pour des composants de carrosserie automobile. Les plieuses modernes offrent une grande flexibilité et précision grâce à des systèmes de contrôle avancés. - Cisailles (machines de découpe)
Les cisailles sont des machines utilisées pour découper des tôles métalliques à une taille spécifique, en utilisant une force de cisaillement. Les cisailles peuvent être manuelles, hydrauliques ou mécaniques, et sont utilisées pour des coupes droites ou courbes. Les cisailles modernes sont souvent équipées de contrôles numériques permettant une découpe plus rapide et plus précise. Elles sont couramment utilisées dans la fabrication de pièces de grande série. - Presse-plieuses (presses de formage)
Les presse-plieuses sont des machines puissantes utilisées pour plier ou former des tôles métalliques à l’aide de matrices et de poinçons. Ces machines peuvent appliquer une pression très élevée, permettant de former des pièces métalliques plus épaisses ou plus résistantes. Elles sont utilisées pour la production de pièces telles que des châssis, des boîtiers, des panneaux de carrosserie, et d’autres composants métalliques. - Machines de découpe laser
Les machines de découpe laser sont utilisées pour couper des tôles métalliques avec une grande précision. Le laser permet une découpe fine, même pour des matériaux très épais. Ce type de machine est largement utilisé pour produire des pièces complexes avec des détails fins. Les machines de découpe laser sont extrêmement polyvalentes et peuvent être utilisées pour couper des formes simples ou complexes avec une grande exactitude. De plus, elles génèrent moins de chaleur et créent moins de déformations thermiques, ce qui est un avantage pour certains types de matériaux. - Machines de découpe au jet d’eau (Waterjet)
La découpe au jet d’eau est une autre méthode de découpe qui utilise un jet d’eau à haute pression, souvent mélangé à un abrasif, pour découper des tôles métalliques. Cette méthode est particulièrement utile pour les matériaux sensibles à la chaleur, tels que les métaux légers, les alliages et les matériaux composites. Le jet d’eau permet une découpe précise sans compromettre la structure du matériau. - Machines de formage à froid
Les machines de formage à froid sont utilisées pour modeler des tôles métalliques sans les chauffer. Ces machines comprennent des équipements tels que les matrices et poinçons, qui sont utilisés pour réaliser des emboutissages, des découpes, des pliages et des profilages. Les machines de formage à froid permettent de créer des pièces métalliques avec une grande précision et sont utilisées pour produire des composants comme des boîtes, des embouts et des pièces de structure. - Machines de roulage de tôle
Les machines de roulage sont utilisées pour courber les tôles métalliques afin de leur donner des formes cylindriques ou coniques. Elles sont souvent utilisées dans la fabrication de réservoirs, de tuyaux, de silos ou d’autres composants nécessitant des formes rondes ou arquées. Le processus de roulage peut être effectué à froid ou à chaud, selon les propriétés du matériau. - Machines de déformation par emboutissage
L’emboutissage est un procédé qui consiste à former une pièce métallique à partir d’une tôle plate par déformation plastique. Ce processus est effectué à l’aide de matrices et de poinçons, et est couramment utilisé pour produire des pièces telles que des capots de voiture, des boîtiers, et des composants de structures métalliques. L’emboutissage permet de produire des pièces avec des formes complexes tout en réduisant le gaspillage de matière. - Machines de découpe par plasma
La découpe plasma est une méthode de découpe utilisant un jet de plasma extrêmement chaud pour couper des tôles métalliques. Cette technique est adaptée pour les métaux conducteurs de chaleur tels que l’acier, l’aluminium et l’acier inoxydable. Les machines de découpe plasma sont rapides, efficaces et peuvent découper des tôles d’épaisseurs variées avec une précision élevée. - Machines de soudage de tôle
Le soudage est utilisé pour assembler des pièces en tôle métallique. Les machines de soudage peuvent être manuelles ou automatisées et sont utilisées pour assembler des tôles métalliques en une seule pièce. Des procédés comme le soudage MIG, TIG, soudage par résistance, ou soudage à l’arc sont utilisés selon le type de métal et la nature des pièces à souder.
Applications des machines de fabrication de pièces en tôle
Les machines de fabrication de pièces en tôle sont largement utilisées dans de nombreuses industries pour créer des pièces métalliques utilisées dans une variété d’applications. Par exemple :
- Automobile : production de panneaux de carrosserie, de châssis, de supports et de pièces internes.
- Aéronautique : fabrication de structures légères, de pièces pour moteurs et d’éléments de carrosserie.
- Construction : production de tôles pour la fabrication de structures métalliques, de panneaux de toiture, de fenêtres, de portes, et de cloisons.
- Électroménager : fabrication de composants pour des appareils tels que des réfrigérateurs, des machines à laver et des cuisinières.
- Énergie : production de réservoirs, de tuyauterie et d’autres composants utilisés dans les centrales électriques et les installations industrielles.
Conclusion
Les machines de fabrication de pièces en tôle sont indispensables dans le secteur industriel pour transformer les tôles métalliques en pièces finies. Elles permettent de répondre aux besoins d’une production de masse tout en offrant la précision et la flexibilité nécessaires pour produire des pièces complexes. L’évolution technologique, notamment avec l’intégration de l’automatisation et des outils de contrôle numériques, a amélioré les performances de ces machines, rendant les processus de production plus efficaces et plus durables.
Les machines de fabrication de pièces en tôle ont évolué pour répondre aux exigences croissantes en termes de précision, de productivité et de flexibilité. À mesure que les matériaux se diversifient et que les besoins industriels se complexifient, ces machines s’adaptent aux nouveaux défis. La technologie numérique joue un rôle de plus en plus important dans l’automatisation des processus, permettant une production plus rapide et plus précise tout en réduisant les risques d’erreurs humaines.
Les machines modernes sont équipées de systèmes de commande numérique (CNC) qui facilitent le réglage des paramètres de production. Ces systèmes permettent de programmer des formes complexes et d’ajuster en temps réel les paramètres de la machine pour optimiser la qualité de la production. Cela permet également de réduire les temps d’arrêt pour reconfigurer la machine, ce qui est particulièrement utile dans des environnements où des séries courtes de pièces différentes sont produites.
Le processus de fabrication de pièces en tôle a également bénéficié des progrès dans le domaine de la robotisation. Les robots sont désormais utilisés pour effectuer des tâches telles que le chargement et le déchargement des tôles, la manipulation des pièces en cours de fabrication, ainsi que des opérations de soudage et d’assemblage. Ces robots augmentent l’efficacité des lignes de production tout en améliorant la sécurité en réduisant le contact humain avec des machines potentiellement dangereuses.
Les machines de découpe laser et plasma, en particulier, ont radicalement transformé la façon dont les pièces en tôle sont produites. La découpe laser, par exemple, permet une précision extrême et une grande vitesse de découpe, ce qui est crucial pour des applications nécessitant une tolérance stricte. Ce type de machine peut couper des matériaux épais tout en minimisant les distorsions thermiques, offrant ainsi une qualité de coupe supérieure par rapport aux méthodes traditionnelles.
En parallèle, la fabrication de pièces en tôle bénéficie de l’introduction de matériaux plus performants et légers, notamment des alliages et des composites métalliques. Ces matériaux sont de plus en plus utilisés pour répondre à la demande d’efficacité énergétique et de légèreté dans des secteurs comme l’aéronautique et l’automobile. Les machines de formage doivent être capables de traiter ces matériaux sans compromettre la qualité ou la fiabilité des pièces produites.
Dans un contexte où la durabilité et la réduction des déchets sont des priorités, l’industrie du formage de tôle met également l’accent sur des solutions écologiques. Par exemple, de nombreuses machines de fabrication de pièces en tôle intègrent des systèmes d’optimisation pour réduire la consommation d’énergie et minimiser les rebuts de matière. Les systèmes de récupération de chaleur ou de recyclage des matériaux sont également de plus en plus courants, ce qui contribue à rendre la production plus respectueuse de l’environnement.
Un autre domaine clé de l’évolution des machines de fabrication de pièces en tôle est la connectivité et l’intégration dans le cadre de l’industrie 4.0. L’intégration de capteurs intelligents et de systèmes de surveillance permet une gestion en temps réel des performances des machines, ainsi qu’une maintenance prédictive qui peut anticiper les pannes avant qu’elles ne surviennent. Cela permet de réduire les temps d’arrêt non planifiés et d’augmenter la durée de vie des équipements.
Dans le même temps, la formation des opérateurs devient un aspect crucial de la gestion des machines de formage. Les systèmes de formation utilisant des réalités augmentée et virtuelle permettent aux opérateurs de se former à l’utilisation des machines sans risques, tout en simulant des scénarios de production pour mieux comprendre les processus complexes. Ces technologies d’apprentissage aident les travailleurs à se familiariser avec les nouvelles machines et à optimiser leur gestion, ce qui augmente la productivité globale et réduit les erreurs.
L’évolution des machines de fabrication de pièces en tôle, couplée à une meilleure compréhension des matériaux et des technologies de production, offre de nouvelles perspectives dans des secteurs clés comme l’aéronautique, l’automobile, et même la fabrication de composants pour l’électronique. L’amélioration continue des machines permet de produire des pièces de plus en plus complexes tout en réduisant les coûts de production et l’impact environnemental.
En somme, l’avenir de la fabrication de pièces en tôle semble prometteur grâce à des innovations constantes en termes de technologie, de matériaux, et de durabilité. Les machines de formage de tôle deviennent de plus en plus sophistiquées, capables de répondre aux exigences élevées de précision, de flexibilité, et de durabilité dans des environnements industriels modernes.
L’évolution continue des machines de fabrication de pièces en tôle ouvre la voie à des possibilités encore plus vastes en termes d’automatisation, de personnalisation et de sustainabilité. Les entreprises cherchent de plus en plus à intégrer des solutions innovantes pour améliorer la compétitivité et répondre aux exigences de production modernes.
L’un des axes majeurs de développement est la digitalisation de la production. Les systèmes de gestion de production assistée par ordinateur (PDM) et les logiciels de conception assistée par ordinateur (CAO) sont désormais utilisés pour simuler et optimiser les processus de fabrication. Ces outils permettent non seulement de créer des modèles numériques détaillés des pièces en tôle, mais aussi de simuler l’ensemble du processus de production avant de lancer la fabrication physique. Cela minimise les erreurs de production, optimise l’utilisation des matériaux et améliore l’efficacité générale du processus.
Dans le cadre de la personnalisation, les machines de formage de tôle offrent une flexibilité accrue grâce à l’intégration de technologies comme la fabrication additive ou des procédés de soudage à haute précision. Cela permet de répondre à des demandes spécifiques des clients pour des pièces de tailles et de formes non standards, souvent dans des délais très courts. Par exemple, dans l’industrie aéronautique, des pièces de tôle très complexes et légères peuvent être fabriquées sur mesure pour répondre aux spécifications strictes des aéronefs, tout en maintenant une haute performance.
En parallèle, l’industrie s’oriente de plus en plus vers des matériaux intelligents ou composites qui nécessitent des machines capables de gérer des propriétés mécaniques variées. L’utilisation de métaux composites ou de matériaux à haute conductivité thermique peut permettre d’améliorer les performances des produits tout en réduisant le poids et la consommation d’énergie. Les machines de formage doivent donc être équipées pour travailler avec ces nouveaux matériaux, qui peuvent se comporter différemment des métaux traditionnels, et cela nécessite des ajustements dans les paramètres de formage, de découpe et de soudage.
Le suivi de la qualité en temps réel est également un domaine d’innovation clé dans la fabrication de pièces en tôle. Les capteurs intégrés dans les machines permettent de surveiller continuellement des aspects tels que l’épaisseur du matériau, la température de déformation ou encore la pression appliquée. Ces données sont analysées pour garantir la conformité des pièces aux spécifications techniques, tout en permettant des ajustements automatiques ou des alertes en cas de déviation par rapport aux normes. Cela réduit considérablement le taux de rebut et augmente la fiabilité des pièces produites.
En outre, la soutenabilité est devenue une priorité pour l’industrie du formage de tôle. Les entreprises se tournent de plus en plus vers des procédés qui utilisent moins d’énergie, génèrent moins de déchets et ont un impact environnemental réduit. Les machines de formage de tôle modernes sont conçues pour maximiser l’efficacité énergétique, en utilisant des moteurs et des systèmes hydrauliques à faible consommation d’énergie, ainsi que des matériaux recyclés ou recyclables. Les technologies comme la recyclabilité des chutes de métal, la réduction des émissions et la gestion des fluides de découpe sont de plus en plus courantes pour minimiser l’empreinte écologique de la production.
Dans ce cadre, les mécanismes d’optimisation de la production, tels que l’intelligence artificielle (IA), l’apprentissage automatique et l’analyse prédictive, se sont intégrés dans les systèmes de contrôle des machines. Ces technologies permettent de prévoir des pannes potentielles avant qu’elles ne surviennent, de prédire les besoins en maintenance et de planifier les opérations de manière plus efficace. Cela se traduit par une réduction des coûts de maintenance, un meilleur rendement des machines et une réduction des temps d’arrêt.
Les entreprises qui réussissent à intégrer ces nouvelles technologies peuvent non seulement augmenter leur productivité mais aussi offrir une meilleure réactivité face aux demandes du marché. Les petites séries de production, qui étaient historiquement plus coûteuses et difficiles à réaliser, deviennent désormais plus accessibles grâce à l’automatisation et aux machines flexibles.
L’avenir des machines de formage de tôle réside également dans leur capacité à collaborer avec d’autres technologies avancées, telles que les drones et les cobots (robots collaboratifs). Par exemple, dans un environnement de fabrication moderne, un robot collaboratif pourrait être utilisé pour assister un opérateur humain dans l’assemblage de pièces de tôle après leur formage, tandis qu’un drone pourrait effectuer des inspections visuelles pour vérifier la qualité des pièces ou la conformité des dimensions.
À terme, l’objectif de l’industrie du formage de tôle est de rendre la production plus intelligente, plus connectée et plus efficace, tout en garantissant une plus grande flexibilité et une réduction des coûts. Les machines de formage de tôle seront plus que de simples outils de production : elles deviendront des acteurs intelligents dans un système de fabrication interconnecté, capables de s’adapter et d’optimiser leur fonctionnement de manière autonome tout en collaborant avec d’autres machines et opérateurs.
Ainsi, l’avenir de la fabrication de pièces en tôle semble prometteur, avec des machines toujours plus sophistiquées, intégrées dans des systèmes de production ultra-modernes, où l’automatisation, la précision, l’optimisation des ressources et la durabilité seront au cœur de l’innovation.
Équipements industriels de formage de tôle
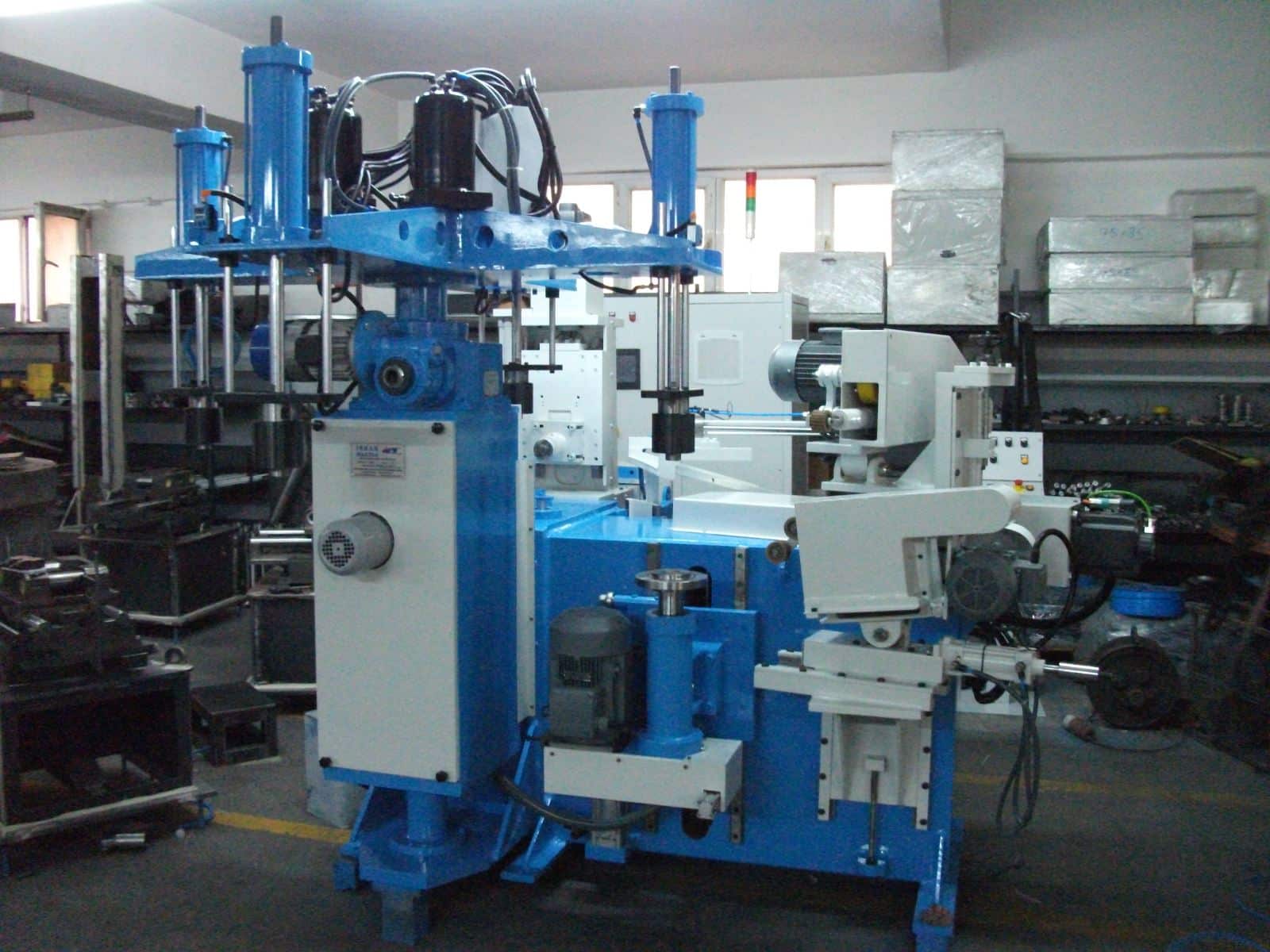
Les équipements industriels de formage de tôle occupent une place centrale dans de nombreux secteurs de production, notamment l’automobile, l’aéronautique, la construction, l’électroménager et l’énergie. Ces équipements sont conçus pour transformer des feuilles métalliques planes en pièces tridimensionnelles aux formes précises, en utilisant divers procédés comme le pliage, l’emboutissage, le roulage, le poinçonnage ou encore le découpage. Grâce à une combinaison de puissance mécanique, d’ingénierie de précision et de technologies numériques avancées, ils permettent une production rapide, reproductible et conforme aux exigences les plus strictes en matière de qualité et de performance.
L’évolution des équipements industriels de formage de tôle s’est accélérée avec l’introduction des systèmes de commande numérique, de la robotique et des capteurs intelligents. Les presses mécaniques ou hydrauliques, autrefois manuelles ou semi-automatiques, sont désormais commandées par des interfaces numériques sophistiquées capables de mémoriser des configurations, d’adapter les paramètres de formage en temps réel, et de garantir une grande homogénéité dans la fabrication en série. Les lignes de production modernes peuvent intégrer plusieurs opérations successives sur une seule plateforme, réduisant ainsi les manipulations manuelles, les temps de cycle et les erreurs potentielles.
Dans une logique d’automatisation poussée, ces équipements sont souvent intégrés à des cellules de production robotisées où chaque étape du processus – depuis le chargement de la tôle brute jusqu’à l’évacuation de la pièce finie – est assurée par des machines interconnectées. Les robots manipulateurs, bras articulés et convoyeurs intelligents assurent un flux constant et optimisé des pièces à travers les différents postes de formage. Cela permet non seulement de produire en grande quantité, mais aussi d’assurer une traçabilité complète des pièces grâce à des systèmes de suivi par codes-barres, QR codes ou puces RFID.
Le contrôle qualité intégré dans ces équipements est un autre atout majeur. Grâce à des capteurs de force, des caméras de vision industrielle et des dispositifs de mesure laser, chaque pièce formée peut être inspectée en ligne pour vérifier sa conformité géométrique, l’absence de défauts de surface ou encore la précision des perçages et découpes. Cette vérification instantanée permet d’éviter que des pièces non conformes poursuivent leur parcours dans la chaîne de production, réduisant ainsi les coûts de reprise ou de rebut.
Les matériaux utilisés dans le formage de tôle ont également évolué, et les équipements industriels doivent désormais être capables de travailler une gamme très large d’alliages : aciers doux ou à haute résistance, inox, aluminium, cuivre, titane ou encore alliages composites. Chaque matériau présente des caractéristiques mécaniques spécifiques (élasticité, limite d’écoulement, ductilité) qui nécessitent des réglages particuliers et des outillages adaptés pour garantir un formage sans fissuration, sans retour élastique excessif et avec une précision dimensionnelle constante.
La tendance actuelle à la fabrication flexible et à la personnalisation impose également aux équipements de pouvoir traiter des séries variées avec des temps de changement de production très courts. Les systèmes à outils interchangeables, les matrices ajustables automatiquement et les plateformes de programmation intuitive permettent de passer rapidement d’une référence à une autre, tout en maintenant des standards élevés de qualité et de rendement.
Enfin, les préoccupations environnementales et énergétiques influencent de plus en plus la conception de ces équipements. Des systèmes de récupération d’énergie, de lubrification minimale, de réduction du bruit et de limitation des déchets sont intégrés dès la conception des lignes de formage. L’objectif est d’allier performance industrielle et responsabilité écologique, en créant des machines économes, durables et capables d’intégrer les principes de l’économie circulaire.
Souhaitez-vous que je développe plus spécifiquement un type d’équipement (comme les presses hydrauliques, les rouleuses ou les plieuses CNC) ?
L’intégration croissante de l’intelligence artificielle dans les équipements industriels de formage de tôle marque une étape décisive vers une production autonome et prédictive. Grâce à des algorithmes capables d’apprendre des cycles précédents et d’ajuster les paramètres de production en temps réel, les machines sont désormais en mesure de détecter des anomalies subtiles avant qu’elles n’impactent la qualité des pièces produites. Cette intelligence embarquée permet une maintenance prédictive, où les systèmes surveillent leurs propres composants mécaniques et électroniques, identifient des signes d’usure ou de fatigue, et alertent automatiquement les techniciens pour planifier les interventions sans interrompre la production. Par conséquent, les arrêts imprévus sont réduits, la durée de vie des machines est prolongée et la fiabilité globale des lignes de production est améliorée.
La connectivité est également au cœur de ces évolutions. Les équipements industriels sont désormais interconnectés dans des écosystèmes de production intelligents, appelés usines 4.0. Dans ces environnements, chaque machine transmet en temps réel ses données à des plateformes centralisées qui les analysent, les croisent et les utilisent pour optimiser l’ensemble du processus de fabrication. Cette approche permet une coordination instantanée entre les différentes étapes de production, une gestion fine des stocks de matières premières, une adaptation rapide aux changements de la demande, et une réaction immédiate en cas de problème détecté sur une ligne. De plus, les données historiques recueillies au fil du temps nourrissent des modèles d’optimisation qui peuvent prédire les performances futures et guider les décisions stratégiques.
L’ergonomie et la sécurité des opérateurs ont également bénéficié de ces avancées. Les interfaces homme-machine modernes sont conçues pour être intuitives, tactiles et personnalisables, facilitant ainsi la prise en main même pour des opérateurs peu expérimentés. Des systèmes de sécurité active, tels que des capteurs de présence, des scanners de zones dangereuses ou des dispositifs de verrouillage automatique, assurent une protection optimale lors des interventions de maintenance ou des changements d’outils. En outre, les bras collaboratifs, ou cobots, permettent aux opérateurs de travailler en interaction directe avec les machines, sans cages de sécurité, tout en réduisant la pénibilité des tâches physiques et en améliorant la productivité globale.
Les avancées technologiques permettent également une grande précision dans le formage de pièces complexes, avec des tolérances très serrées, même pour des géométries irrégulières. Cela est particulièrement crucial dans les secteurs de pointe comme l’aéronautique, la microélectronique ou le médical, où la moindre imperfection peut compromettre la sécurité ou la fonctionnalité d’un composant. Les machines sont capables d’adapter en continu la pression de formage, la vitesse de déplacement, ou la température appliquée, pour compenser les variations de matériau, d’humidité ou de tension interne dans la tôle. Ce niveau de contrôle permet une reproductibilité parfaite, même dans des conditions de production variables.
L’intégration de technologies complémentaires, comme le découpage laser, le soudage par friction-malaxage ou la découpe à jet d’eau, dans une seule ligne de formage, favorise une approche modulaire et complète de la fabrication. Cela permet de transformer une simple feuille de métal en une pièce finie, prête à être assemblée, sans nécessiter d’étapes intermédiaires ou de transferts entre différentes stations. Ce regroupement des opérations réduit les délais de production, les coûts de logistique interne, et les risques de détérioration des pièces lors de la manipulation.
Enfin, l’impact environnemental des équipements industriels de formage de tôle fait l’objet d’une attention croissante. Les constructeurs développent des solutions écoénergétiques qui réduisent la consommation d’électricité, récupèrent l’énergie cinétique des opérations de presse, utilisent des lubrifiants biodégradables et minimisent les chutes de matière grâce à une optimisation des découpes et à la réutilisation des rebuts. La conception des machines elles-mêmes évolue vers une modularité facilitant la réparation, la mise à jour ou le recyclage en fin de vie, selon les principes de l’éco-conception industrielle.
Cette transformation du paysage industriel repose sur une collaboration étroite entre fabricants de machines, utilisateurs finaux, intégrateurs de systèmes et développeurs de logiciels. Ensemble, ils façonnent une nouvelle génération d’équipements capables de produire mieux, plus vite, de manière plus flexible et plus respectueuse de l’environnement. Dans ce contexte, les équipements industriels de formage de tôle ne sont plus de simples outils mécaniques, mais deviennent les éléments centraux d’un système de production intelligent, durable et agile, au service d’une industrie résolument tournée vers l’avenir.
L’évolution constante des matériaux à mettre en forme impose également une adaptation rapide des équipements industriels de formage de tôle. L’apparition de tôles multicouches, de composites métalliques, ou encore de matériaux hybrides associant métaux et polymères demande aux machines non seulement une puissance accrue, mais aussi une capacité à moduler leur comportement selon les propriétés locales de la tôle. Les systèmes de formage deviennent alors plus complexes, intégrant des mécanismes de compensation dynamiques pour éviter les déformations indésirables, les plissements, ou les microfissures qui peuvent apparaître dans les zones contraintes. Des techniques comme le formage à chaud assisté par induction ou par infrarouge gagnent en popularité, notamment dans l’automobile et l’aéronautique, car elles permettent de travailler des alliages légers à haute résistance tout en assurant une ductilité suffisante durant la déformation.
Par ailleurs, la personnalisation croissante des produits finit par se répercuter sur les lignes de production. Les équipements doivent pouvoir répondre à des demandes de séries courtes, voire de pièces uniques, tout en conservant l’efficacité d’une production en série. Cela passe par une numérisation poussée des chaînes de valeur, où chaque pièce est identifiée, traçable, et son parcours entièrement piloté par un jumeau numérique. Le modèle virtuel de la pièce est simulé en amont pour optimiser les séquences de formage, éviter les défauts, et adapter automatiquement les réglages des machines. Ce flux de données permet d’avoir une interaction étroite entre la conception et la fabrication, rendant les ateliers de formage plus réactifs et moins dépendants des changements physiques d’outillage.
Le développement de solutions de formage souples, comme le formage incrémental ou l’hydroformage, permet de repousser encore les limites de la mise en forme de tôle. Ces procédés autorisent la création de formes complexes à partir de modèles CAO, avec un minimum d’outillage spécifique. Le formage incrémental, en particulier, qui déplace un poinçon selon un chemin contrôlé pour déformer progressivement la tôle, offre une flexibilité remarquable pour la production de prototypes ou de pièces sur mesure. Ces technologies, autrefois cantonnées aux laboratoires ou à la R&D, gagnent du terrain dans les ateliers industriels, portées par la demande croissante de produits personnalisés, de réparations sur mesure et de délais de mise sur le marché réduits.
La coopération homme-machine évolue elle aussi. Les postes de travail hybrides, où un opérateur supervise ou intervient ponctuellement sur une ligne automatisée, se multiplient. Ces postes sont conçus pour maximiser la sécurité, l’efficacité gestuelle et la réduction des efforts physiques. Ils tirent parti de l’analyse ergonomique, de la réalité augmentée, et de systèmes d’aide à la décision intégrés dans les interfaces. L’opérateur devient un superviseur stratégique, capable d’intervenir rapidement sur des réglages complexes, d’interpréter des anomalies détectées par la machine, ou d’adapter un programme à une situation imprévue.
Enfin, l’exportation et l’internationalisation des équipements de formage de tôle posent de nouveaux défis en matière de normalisation, d’interopérabilité et de formation. Les machines doivent s’adapter à des standards techniques et réglementaires très variés selon les pays, tout en assurant une maintenance et une mise en route facilitées. La documentation technique, les tutoriels interactifs, la formation à distance et la réalité virtuelle deviennent des outils indispensables pour assurer une prise en main rapide par des opérateurs localisés aux quatre coins du monde. L’assistance à distance par des experts connectés via des lunettes intelligentes ou des systèmes immersifs devient une norme dans les services après-vente des fabricants d’équipements.
Les machines de formage de tôle d’aujourd’hui sont ainsi bien plus que de simples dispositifs mécaniques. Elles représentent l’aboutissement d’un effort collectif d’innovation, d’intégration technologique et de vision industrielle, au service d’une fabrication à la fois plus intelligente, plus humaine et plus durable. Voulez-vous que je continue en explorant les tendances futures ou les exemples d’applications concrètes dans des secteurs spécifiques ?
Solutions de formage de tôle

Les solutions de formage de tôle englobent un ensemble de technologies, de procédés et de dispositifs destinés à transformer une feuille métallique plane en un objet tridimensionnel répondant à des exigences précises de forme, de résistance et de fonctionnalité. Ces solutions s’adaptent à une grande variété d’industries, allant de la fabrication automobile à l’électroménager, en passant par l’aéronautique, la construction, la défense ou encore les dispositifs médicaux. Elles incluent des procédés traditionnels comme le pliage, le découpage ou l’emboutissage, mais aussi des approches plus avancées comme le formage par impulsion électromagnétique, l’hydroformage ou le formage incrémental, qui permettent une flexibilité accrue, une réduction des coûts d’outillage et une meilleure qualité de pièce.
Ces solutions ne se limitent pas aux machines elles-mêmes, mais s’étendent à tout l’écosystème de production, y compris les logiciels de simulation, les systèmes de contrôle qualité, les outils de programmation hors ligne et les interfaces homme-machine intelligentes. La tendance vers des solutions de plus en plus intégrées se traduit par la mise en œuvre de cellules de formage automatisées capables de réaliser plusieurs opérations en un seul cycle, avec un minimum d’intervention humaine. Cela comprend le chargement automatisé des tôles, le positionnement précis, le contrôle dimensionnel en ligne et l’évacuation des pièces finies, le tout orchestré par un système centralisé de gestion de production.
L’optimisation des solutions de formage repose aussi sur l’analyse et la simulation numérique. Les logiciels de CAO/FAO couplés aux outils de simulation de formage permettent de prédire les comportements des matériaux sous contrainte, d’identifier les zones à risque de fissuration ou de plissement, et d’ajuster les paramètres de formage avant même la fabrication du premier prototype. Cette approche permet d’accélérer le développement de nouveaux produits, de réduire les essais physiques coûteux et de garantir une mise en production plus fluide.
L’aspect environnemental est également pris en compte dans les solutions modernes de formage de tôle. Des approches visant à réduire les pertes de matière, la consommation énergétique et l’utilisation de lubrifiants nocifs sont intégrées dès la conception des lignes de production. Des systèmes de découpe optimisée, de recyclage des chutes et de récupération d’énergie pendant les cycles de presse sont de plus en plus répandus. Par ailleurs, la montée en puissance des matériaux légers – tels que l’aluminium et les aciers à ultra-haute résistance – dans les industries sensibles aux performances énergétiques pousse les fabricants à développer des procédés spécifiques capables de former ces matériaux exigeants sans les endommager.
En somme, les solutions de formage de tôle représentent bien plus qu’un ensemble de machines : elles constituent une réponse globale, technique et stratégique, aux défis de la production moderne. Elles permettent de concilier productivité, personnalisation, qualité et durabilité dans un contexte industriel toujours plus exigeant et concurrentiel.
L’évolution des solutions de formage de tôle s’inscrit dans une dynamique où la flexibilité, la précision et l’automatisation sont devenues des impératifs industriels majeurs. Dans les ateliers modernes, les chaînes de production sont conçues pour s’adapter à des cycles de fabrication de plus en plus courts, à des changements de séries fréquents et à des géométries de pièces toujours plus complexes. Cela nécessite des machines capables de se reconfigurer rapidement, de traiter différents types de matériaux sans nécessiter de longues interruptions, et de garantir une reproductibilité parfaite même sur des pièces uniques. Cette agilité est rendue possible grâce à l’intégration de capteurs intelligents, de logiciels de pilotage évolués et de systèmes de rétroaction continue qui permettent d’ajuster les efforts, les vitesses et les trajectoires de formage en temps réel, en fonction du comportement du matériau.
Dans cette logique, les presses servo-électriques ou servo-hydrauliques ont largement remplacé les systèmes traditionnels dans de nombreux secteurs, car elles offrent une maîtrise extrêmement fine du cycle de formage. Leur capacité à moduler la force appliquée à chaque instant, combinée à leur efficacité énergétique, en fait des solutions idéales pour des applications exigeant à la fois précision et performance. Parallèlement, des technologies de formage alternatives, comme le formage par explosion, le formage électromagnétique ou le formage thermique localisé, sont explorées pour répondre à des cas particuliers, notamment dans le travail de matériaux à très haute résistance ou dans la production de formes non développables par les procédés conventionnels.
L’impact de la numérisation et de l’industrie 4.0 est omniprésent dans la nouvelle génération de solutions de formage. Chaque composant de la ligne de production, du convoyeur à la matrice de presse, est connecté à un réseau interne qui centralise les données, les analyse en temps réel et les met à disposition des opérateurs, des ingénieurs ou des systèmes automatisés. Cette capacité à surveiller et à interpréter en continu les paramètres de production permet non seulement d’éviter les défauts mais aussi de proposer des ajustements proactifs pour améliorer les performances globales. Les solutions de formage deviennent ainsi auto-adaptatives, apprenant des campagnes précédentes pour affiner leurs réglages et anticiper les dérives.
Par ailleurs, la personnalisation des équipements en fonction des besoins spécifiques de chaque client est une tendance forte. Les constructeurs de machines-outils proposent des plateformes modulaires où les composants mécaniques, les actionneurs, les commandes numériques, les périphériques de manutention ou de contrôle qualité peuvent être assemblés en fonction du type de production visé, de la cadence attendue, ou du niveau d’automatisation souhaité. Cette modularité permet de concevoir des cellules de formage uniques, dimensionnées au plus juste, tout en conservant une évolutivité future. Elle ouvre aussi la voie à des modèles économiques fondés sur la reconfiguration de l’existant plutôt que sur l’achat systématique de nouvelles machines.
La formation des opérateurs et des techniciens joue un rôle déterminant dans le succès de ces solutions. Les équipements sont souvent accompagnés de simulateurs, d’environnements de réalité virtuelle ou d’interfaces pédagogiques permettant de former le personnel sans risque ni perte de matière. Ces outils facilitent la prise en main, renforcent la compréhension des phénomènes de formage et permettent une montée en compétence rapide, même pour des utilisateurs peu familiarisés avec ces technologies avancées. Ainsi, les solutions de formage de tôle ne reposent pas uniquement sur la performance technique des machines, mais aussi sur la capacité à en faire un usage optimal, sécurisé et intelligent.
En définitive, l’ensemble de ces avancées convergent vers une même finalité : produire des pièces en tôle toujours plus complexes, dans des délais plus courts, avec moins de gaspillage, plus de flexibilité, et une qualité maîtrisée dès la première pièce. Les solutions de formage de tôle deviennent des éléments clés dans les stratégies industrielles de différenciation, d’agilité et de durabilité. Elles incarnent la fusion entre la mécanique de précision, la science des matériaux, l’informatique industrielle et l’intelligence humaine.
Cette évolution continue des solutions de formage de tôle s’inscrit également dans un contexte plus large de transformation écologique et sociale de l’industrie. L’un des objectifs majeurs des fabricants d’équipements est de proposer des technologies capables de réduire significativement l’empreinte carbone, tout en augmentant l’efficacité énergétique globale du processus. Cela passe notamment par l’utilisation de moteurs à haut rendement, de systèmes de récupération d’énergie sur les vérins ou les entraînements, ou encore par l’optimisation des séquences de production pour réduire le nombre de cycles inutiles. De plus, la réduction des rebuts, grâce à un contrôle qualité intégré à chaque étape du processus, contribue à un meilleur usage de la matière première, qui est souvent la composante la plus coûteuse et la plus énergivore dans la fabrication d’une pièce en tôle.
L’émergence de matériaux dits « intelligents » ou « adaptatifs », comme les alliages à mémoire de forme ou les composites métalliques multicouches, pousse également les systèmes de formage à se réinventer. Ces matériaux réagissent de façon complexe aux efforts mécaniques et thermiques, ce qui nécessite une maîtrise fine de tous les paramètres du procédé, notamment la température, la vitesse de déformation, ou la pression appliquée à chaque instant. Ainsi, le formage devient un acte coordonné à l’échelle microscopique, où la connaissance des propriétés métallurgiques du matériau est aussi importante que la robustesse mécanique de la machine elle-même.
L’intelligence artificielle et l’apprentissage automatique commencent aussi à jouer un rôle dans l’optimisation des procédés de formage. En analysant de grandes quantités de données issues des capteurs, des systèmes de vision ou des historiques de production, les algorithmes peuvent détecter des corrélations invisibles à l’œil humain, proposer des réglages plus efficaces, ou prédire l’apparition de défauts avant qu’ils ne se produisent. Dans certaines usines pilotes, des systèmes auto-correcteurs sont déjà en place, capables de modifier en temps réel les paramètres de formage pour corriger les dérives liées à l’usure des outils, aux variations de matière ou aux changements climatiques dans l’atelier. Cette autonomie croissante des systèmes de production transforme le rôle des opérateurs, qui deviennent de véritables chefs d’orchestre des données, garants de la cohérence du processus plus que simples exécutants.
Enfin, les collaborations entre les fabricants de machines, les éditeurs de logiciels, les laboratoires de recherche et les industriels utilisateurs permettent d’accélérer l’innovation. Des plateformes collaboratives émergent, où les données de formage sont partagées dans un cadre sécurisé pour alimenter des modèles prédictifs communs, améliorer les outils de simulation ou tester virtuellement de nouveaux procédés avant leur mise en œuvre réelle. Ce travail collectif ouvre la voie à une standardisation accrue des bonnes pratiques, à la mutualisation des développements, et à une réduction importante du temps de mise sur le marché pour les nouvelles solutions de formage.
Ainsi, les solutions de formage de tôle s’imposent aujourd’hui comme un pilier technologique essentiel pour répondre aux exigences de l’industrie moderne : produire vite, avec précision, dans le respect de l’environnement, et en s’adaptant en permanence aux évolutions du marché, des matériaux et des attentes sociétales. Souhaitez-vous que je poursuive avec des exemples d’applications industrielles concrètes ou des innovations spécifiques par procédé ?
Machines de façonnage de tôle
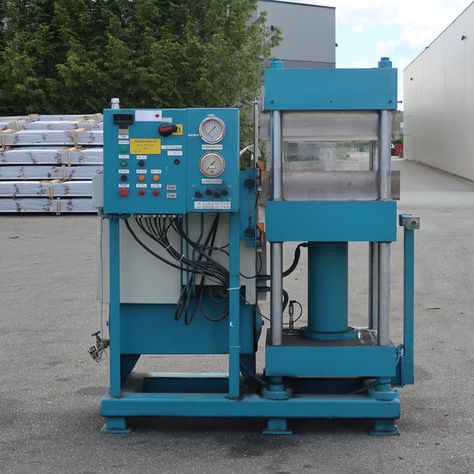
Les machines de façonnage de tôle jouent un rôle fondamental dans l’industrie manufacturière, car elles permettent de transformer une matière première plane – la tôle – en composants de forme complexe, fonctionnelle et souvent structurelle. Ces machines englobent une grande diversité de technologies, allant des presses mécaniques ou hydrauliques aux rouleuses, plieuses, cisailles, poinçonneuses, et jusqu’aux équipements les plus avancés comme les centres de formage automatisés ou les systèmes de formage par impulsions. Elles sont conçues pour travailler une grande variété de matériaux, notamment l’acier, l’aluminium, l’inox, le laiton ou encore des alliages plus spécifiques selon les besoins de performance, de poids ou de résistance à la corrosion.
L’efficacité de ces machines repose sur leur capacité à appliquer avec précision des efforts mécaniques – souvent très importants – sur la tôle pour en modifier la géométrie sans rompre sa continuité. Selon la nature de l’opération (pliage, roulage, découpe, emboutissage, cintrage), les machines sont équipées d’outils ou de matrices spécifiques, souvent interchangeables, et réglées selon des paramètres rigoureux pour garantir la répétabilité et la qualité de la pièce produite. Dans les versions les plus récentes, ces machines sont souvent intégrées à des lignes automatisées où la tôle est acheminée, positionnée, façonnée, contrôlée et évacuée sans intervention humaine directe, ce qui améliore la cadence de production, la sécurité et la traçabilité.
Les machines de façonnage modernes sont également conçues pour offrir un haut degré de flexibilité. Grâce à des interfaces numériques, des systèmes de contrôle intelligent, et parfois des robots collaboratifs, elles peuvent s’adapter à des séries de production variées, en changeant rapidement d’outillage ou de programme. Cela répond à la demande croissante pour des lots de fabrication plus courts, des pièces personnalisées et des délais de production réduits. Les progrès en mécatronique, en hydraulique proportionnelle, en moteurs linéaires et en capteurs de haute précision contribuent également à cette évolution, en permettant un contrôle dynamique des efforts, des vitesses et des positions pendant toute la durée du cycle.
En résumé, les machines de façonnage de tôle incarnent l’alliance entre robustesse mécanique, précision technologique et intelligence numérique. Elles sont au cœur des processus industriels modernes qui visent la compétitivité, la qualité et la réactivité dans la fabrication de pièces métalliques aux formes complexes et aux tolérances serrées. Souhaitez-vous que je poursuive sur un type de machine en particulier ou sur les critères de sélection d’un équipement de façonnage ?
Les machines de façonnage de tôle forment un ensemble technologique indispensable à la transformation du métal en feuilles en objets utiles, qu’ils soient industriels, architecturaux ou utilitaires. Leur rôle principal est d’imprimer une géométrie à la tôle, par des actions mécaniques qui n’enlèvent pas de matière mais la déplacent, la plient, la compriment ou l’étirent. Ce façonnage peut prendre la forme de pliages nets, de galbes doux, de profils complexes ou de formes embossées, selon la finalité de la pièce et le procédé utilisé. Dans les environnements industriels, ces machines sont non seulement des outils de transformation mais également des instruments de précision, capables de respecter des tolérances inférieures au dixième de millimètre et de garantir une homogénéité sur des milliers de pièces.
Leur conception repose sur une parfaite synergie entre les composants mécaniques (châssis rigide, systèmes de guidage, outils formant), les actionneurs (hydrauliques, pneumatiques ou électromécaniques), et les systèmes de contrôle. Ces derniers, devenus numériques, assurent la répétabilité des gestes, la coordination des axes de mouvement et la synchronisation des étapes successives. Dans certains cas, une seule machine peut réaliser plusieurs opérations de façonnage : par exemple, une presse plieuse dotée d’un changeur d’outils automatique peut enchaîner des pliages de formes différentes sans intervention manuelle, ce qui favorise la production en flux tendu. D’autres machines comme les rouleuses, les cintreuses ou les machines à former les bords sont plus spécialisées, mais trouvent leur place dans des chaînes hybrides intégrant plusieurs technologies de façonnage complémentaires.
La tendance actuelle pousse au développement de solutions modulaires, évolutives, et connectées. Une machine de façonnage moderne est souvent dotée d’un système de surveillance en temps réel de l’usure des outils, de la consommation énergétique ou de la qualité de la pièce en cours. Elle peut être reliée à un système MES (Manufacturing Execution System) qui coordonne l’ensemble de la production à l’échelle de l’usine, ou bien alimentée par des modèles de simulation prédictifs intégrés au jumeau numérique de la ligne. Grâce à cela, les réglages sont optimisés en permanence, les arrêts non planifiés réduits, et les temps de changement de série raccourcis. Ce niveau de sophistication permet aux entreprises de répondre à des commandes plus complexes tout en maîtrisant leurs coûts et leurs délais.
Le façonnage de la tôle, bien que souvent perçu comme une opération purement mécanique, devient ainsi une discipline multidisciplinaire, à la croisée de la mécanique, de la métallurgie, de l’automatisation et de la science des données. Les machines qui l’exécutent sont de plus en plus intelligentes, communicantes et autonomes, capables non seulement de produire mais aussi de s’auto-contrôler, de s’ajuster, voire de s’auto-diagnostiquer. Dans ce contexte, elles constituent un pilier stratégique pour toute entreprise engagée dans la fabrication de produits métalliques performants, compétitifs et conformes aux exigences normatives les plus élevées.
Prenons l’exemple d’une ligne de production dédiée à la fabrication de capots métalliques pour l’industrie automobile, qui illustre de manière concrète l’intégration de différentes machines de façonnage de tôle dans une chaîne automatisée et intelligente. À l’entrée de la ligne, de grandes bobines de tôle en acier galvanisé sont déroulées par un dérouleur motorisé. Cette tôle passe ensuite dans une ligne de redressage qui élimine les contraintes résiduelles et assure une planéité parfaite, indispensable pour éviter toute déformation imprévue lors des opérations ultérieures.
La tôle redressée est ensuite acheminée vers une presse de découpe automatique équipée de matrices interchangeables. Cette étape permet de donner à la tôle un contour brut proche de la forme finale du capot. La précision de cette découpe est cruciale : elle conditionne l’efficacité des opérations de formage qui suivent et la qualité esthétique de la pièce. La tôle pré-découpée est ensuite prise en charge par un robot manipulateur qui la dépose dans une presse hydraulique d’emboutissage. Cette machine, équipée d’un outillage complexe, réalise une opération de déformation plastique contrôlée en trois dimensions. C’est à cette étape que la tôle acquiert sa forme incurvée et sa rigidité finale.
La pièce emboutie passe ensuite sur une station de refendage et d’ébavurage automatisée, qui corrige les bords, supprime les bavures éventuelles et ajuste les dimensions avec une grande précision. Puis elle est convoyée vers une plieuse numérique à commande CNC, qui effectue les plis secondaires nécessaires à l’assemblage ou à la fixation sur le véhicule. Cette plieuse peut s’adapter automatiquement à différents programmes selon le modèle de capot, ce qui permet une grande flexibilité de production. Un système de vision industrielle contrôle chaque pli et alerte le superviseur en cas d’écart, ce qui limite les rebuts.
La pièce façonnée est ensuite contrôlée dimensionnellement par un scanner 3D, puis marquée par un système de gravure laser qui inscrit un code de traçabilité. Elle est enfin évacuée vers une ligne de finition ou de peinture, prête à être assemblée. Tout au long de la chaîne, des capteurs enregistrent la température de l’outillage, la pression exercée, le retour élastique du matériau, ou encore la consommation énergétique. Ces données sont centralisées sur une interface de supervision qui permet d’analyser la performance de la ligne en temps réel et d’anticiper les besoins de maintenance.
Ce type d’organisation illustre comment les machines de façonnage de tôle, combinées intelligemment, permettent une production à la fois rapide, personnalisable et contrôlée. La coordination entre les différentes étapes est essentielle, de même que la compatibilité entre les équipements. Des logiciels de simulation sont souvent utilisés dès la phase de conception de la ligne pour tester virtuellement les séquences de formage, détecter les risques de froissement, de rupture ou de déformation excessive, et valider les trajectoires des robots.
En résumé, une ligne moderne de façonnage de tôle n’est plus un simple assemblage de machines, mais un système intégré et intelligent, capable de s’adapter aux exigences d’un marché en constante évolution. Le façonnage devient alors un processus fluide, prévisible et optimisé, au service de l’innovation produit et de la performance industrielle.
EMS Machines de Formage
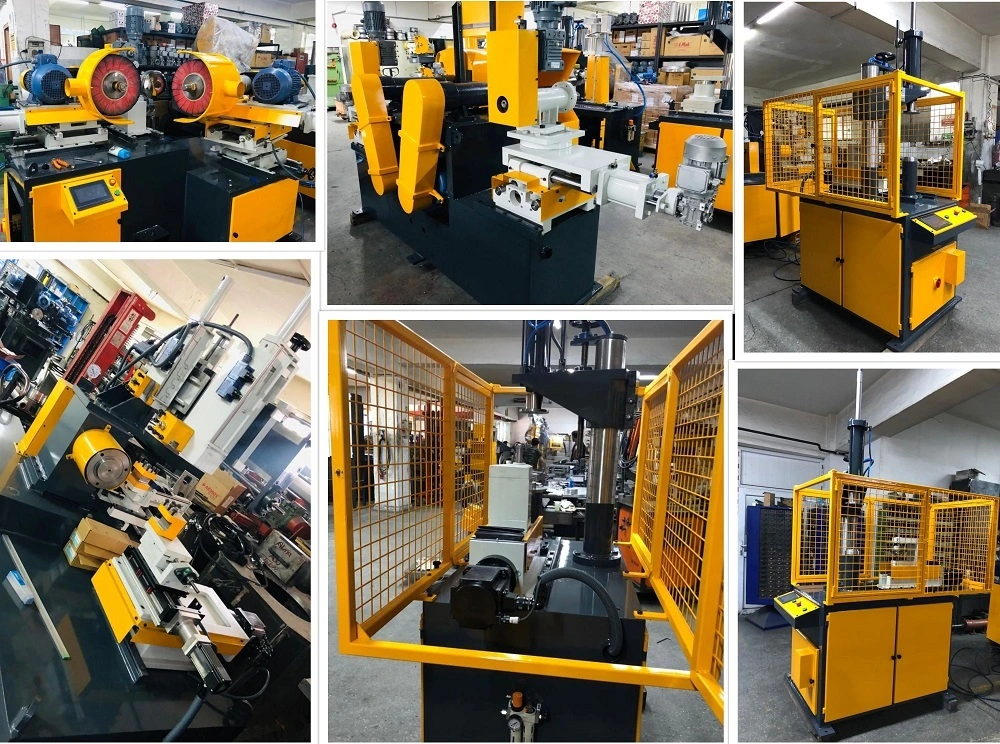
Le formage du métal est un processus consistant à façonner le métal dans la forme et la taille souhaitées à l’aide de diverses techniques. Il s’agit d’un processus crucial dans l’industrie manufacturière car il permet la production de différents produits tels que des pièces automobiles, des composants d’avion, des appareils électroménagers et bien d’autres encore.
Le processus de formage du métal consiste à appliquer une force sur le métal pour changer sa forme sans enlever aucune matière. La force peut être appliquée par diverses méthodes telles que le forgeage, le laminage, l’extrusion, l’étirage et l’estampage. Chaque méthode a ses propres avantages et inconvénients, et le choix de la méthode dépend du matériau formé et de la forme souhaitée.
Le forgeage est l’une des techniques de formage des métaux les plus anciennes. Il s’agit de chauffer le métal à haute température, puis d’appliquer une force de compression à l’aide d’un marteau ou d’une presse pour donner au métal la forme souhaitée. Le forgeage est couramment utilisé pour produire de grandes pièces telles que des engrenages, des essieux et des bielles.
Le laminage est une autre technique de formage du métal qui consiste à faire passer le métal à travers une paire de rouleaux pour réduire son épaisseur ou modifier sa forme. Les rouleaux peuvent être lisses ou texturés selon la finition souhaitée. Le laminage est couramment utilisé pour produire des tôles plates, des plaques et des barres.
L’extrusion est une technique de formage du métal qui consiste à pousser une billette ou une tige métallique à travers une matrice pour créer une forme spécifique. L’extrusion peut être utilisée pour produire des formes complexes telles que des tubes, des canaux et des angles.
L’emboutissage est une technique de formage des métaux utilisée pour réaliser des pièces de forme cylindrique, comme des tubes ou des tuyaux. Le processus consiste à tirer le métal à travers une matrice pour réduire son diamètre et augmenter sa longueur. Le tréfilage est couramment utilisé dans la production de fils, de tiges et de tubes.
L’emboutissage est une technique de formage du métal qui consiste à couper, poinçonner ou plier le métal dans une forme spécifique à l’aide d’une matrice. Le processus peut être utilisé pour produire des pièces avec une grande précision et répétabilité. L’estampage est couramment utilisé dans la production de pièces automobiles, d’appareils électroménagers et d’appareils électroniques.
En plus de ces techniques, il existe de nombreuses autres méthodes de formage des métaux telles que le filage, l’emboutissage profond et l’hydroformage. Chaque méthode a ses propres avantages et inconvénients, et le choix de la méthode dépend des exigences spécifiques du produit fabriqué.
Le formage des métaux est un processus complexe qui nécessite un haut niveau de compétence et d’expertise. Le succès du processus dépend de nombreux facteurs tels que le type de matériau formé, l’équipement utilisé et l’expérience de l’opérateur. En comprenant les différentes techniques de formage des métaux et en choisissant la méthode adaptée au travail, les fabricants peuvent produire des pièces de haute qualité qui répondent aux besoins spécifiques de leurs clients.