
Outils industriels de détourage et formage: Voici un exemple visuel d’une machine de découpe de contours (machine de découpe à contour à plateau avec moteur pas à pas), qui peut être utilisée pour découper ou tracer les contours d’ustensiles de cuisine selon un motif précis.
Technologies et machines pour découper ou profiler les contours d’ustensiles de cuisine
Technologie / Machine | Points forts principaux | Idéal pour… |
---|---|---|
Découpe laser (CO₂ ou fibre) | Grande précision, rapidité, découpe sans contact | Formes complexes, matériaux métalliques ou composites |
Presse à découper (hydraulique/rotative/laser) | Production en série efficace, formes régulières | Volume, formes répétitives (ex. poignées, fonds d’ustensile) |
Équipement multi-étapes industriel | Intègre découpe, perlage, rivetage en une seule ligne | Chaînes automatisées d’ustensiles en métal |
Machine de contour CNC (couteau/tournant) | Flexibilité des formes, précision CNC | Prototypage ou formes personnalisées, matériaux légers |
Que choisir selon votre besoin ?
- Prototype ou petites séries / formes variées → Machine CNC à contours (flexibilité, personnalisation).
- Production industrielle / série → Presse hydraulique ou laser + éventuellement un système intégré multi-opérations (forme, découpe, perlage).
- Décoration, motifs complexes dans les métaux ou composites → Découpe laser pour une finition nette et rapide.
- Volumes élevés avec finis industriels → Equipement de type Youngmax ou similaire, capable de tout intégrer (découpe, perlage, etc.) pour des cycles efficaces.
Les machines destinées au façonnage des contours d’ustensiles de cuisine regroupent un ensemble de technologies différentes qui visent toutes le même objectif : donner aux casseroles, poêles, couvercles ou plats métalliques une forme précise et régulière, avec des bords lisses, résistants et adaptés à un usage quotidien. Dans la fabrication d’ustensiles de cuisine, le contour n’est jamais un détail secondaire, car il conditionne non seulement l’esthétique du produit mais aussi sa durabilité et son confort d’utilisation. Pour obtenir ces finitions, l’industrie fait appel à plusieurs familles de machines, depuis les presses traditionnelles de découpe jusqu’aux solutions plus récentes basées sur le laser ou le contrôle numérique. La découpe laser est aujourd’hui l’une des technologies les plus prisées pour réaliser les contours d’ustensiles, en particulier lorsqu’il s’agit de travailler l’acier inoxydable qui est le matériau dominant dans ce secteur. Le faisceau laser, dirigé par commande numérique, permet de découper les bords avec une grande précision et une très faible déformation thermique, ce qui réduit considérablement le besoin de reprises ou de polissage ultérieur. Cette méthode est particulièrement adaptée pour des pièces présentant des formes complexes ou des motifs décoratifs, et elle garantit une vitesse de production élevée tout en offrant une grande souplesse pour le changement de modèles. Cependant, dans les environnements où la production se mesure en milliers ou dizaines de milliers de pièces identiques, les presses hydrauliques ou mécaniques restent incontournables. Ces presses fonctionnent avec des matrices spécialement conçues pour découper rapidement et de façon répétitive les contours des ustensiles. Lorsqu’il s’agit de fonds de casseroles, de poignées ou de pièces circulaires régulières, la presse à découper permet d’atteindre un rythme industriel inégalé et de conserver une homogénéité absolue entre les produits. Le coût initial des outillages est plus élevé que pour la découpe laser, mais il est vite amorti lorsque les volumes sont conséquents.
Dans les usines modernes, on rencontre également des équipements dits intégrés, capables d’assurer en une seule station de travail la découpe, le perlage et parfois même le rivetage des bords. Ces machines sont très répandues dans la production de casseroles et de poêles, car elles permettent non seulement de former le contour mais aussi de rigidifier la structure et de préparer la pièce pour l’assemblage des poignées ou couvercles. Le perlage, par exemple, consiste à arrondir et renforcer le bord découpé afin d’éviter tout risque de coupure et d’apporter une meilleure résistance mécanique à l’ustensile. De tels ensembles multi-opérations sont conçus pour réduire le temps de manipulation, assurer une meilleure précision de positionnement et rendre la ligne de production beaucoup plus fluide.
Parallèlement, pour des ateliers plus orientés vers la personnalisation ou la production de petites séries, les machines de découpe à contours contrôlées par CNC représentent une option intéressante. Équipées d’outils de coupe verticaux ou de lames spécifiques, elles suivent avec exactitude des trajectoires programmées, permettant de réaliser aussi bien des formes standards que des dessins très particuliers. La présence d’une table rotative facilite grandement le travail sur des pièces circulaires, tandis que l’automatisation partielle garantit une précision constante d’une pièce à l’autre. Ces équipements ne rivalisent pas avec les presses sur le plan de la cadence, mais ils offrent une flexibilité qui séduit de plus en plus de fabricants souhaitant diversifier leur gamme.
Ainsi, le choix de la machine pour les contours d’ustensiles de cuisine dépend avant tout de la nature du projet et de l’échelle de production. Les grandes usines orientées vers les volumes massifs privilégient les presses et les lignes intégrées, alors que les ateliers axés sur la qualité artisanale ou les petites séries misent plutôt sur les lasers et les systèmes CNC. Chaque technologie répond à un besoin spécifique, et il n’est pas rare de voir des combinaisons dans une même usine, par exemple une découpe laser pour les prototypes et petites commandes spéciales, et des presses mécaniques pour les modèles standards produits en continu. Ce panorama montre à quel point la maîtrise des contours est un élément essentiel de l’industrie des ustensiles de cuisine, un domaine où la précision technique rencontre directement l’usage quotidien des consommateurs.
Dans le domaine de la fabrication des ustensiles de cuisine, les contours jouent un rôle fondamental car ils définissent la forme finale de l’objet, sa sécurité d’utilisation et sa résistance à l’usure quotidienne. Pour obtenir ces contours, différentes technologies de machines sont utilisées et chacune d’elles correspond à un type de production particulier. La presse de découpe est la plus ancienne et la plus répandue, notamment dans les grandes unités industrielles où la cadence de production est déterminante. Grâce à un jeu de matrices spécialement conçu, elle permet de découper les feuilles de métal en leur donnant une forme précise et répétitive, ce qui est indispensable pour les casseroles, les poêles ou les couvercles qui doivent présenter une uniformité parfaite. Une fois la découpe effectuée, le métal peut ensuite subir d’autres étapes comme le roulage ou le perlage, qui consistent à former le bord, à l’arrondir et à lui donner une rigidité supplémentaire afin d’éviter les coupures et de renforcer la durabilité de l’ustensile. Ce travail sur le contour est capital, car il garantit non seulement la sécurité du consommateur mais aussi la compatibilité avec d’autres pièces comme les couvercles ou les poignées fixées ultérieurement.
Avec l’évolution des techniques, la découpe laser est venue compléter et parfois remplacer les procédés traditionnels. Dans le cas de l’acier inoxydable, qui est le matériau dominant dans la fabrication des ustensiles de cuisine haut de gamme, le laser offre une précision inégalée, capable de reproduire des formes complexes avec un tranchant net et régulier. Cette technologie présente aussi l’avantage de réduire les déformations thermiques et d’éliminer ou presque les étapes de finition, ce qui est un gain considérable dans la chaîne de production. Elle est particulièrement adaptée pour les productions où les formes doivent évoluer fréquemment ou pour les séries limitées dans lesquelles l’investissement dans des matrices lourdes n’est pas rentable. Les ateliers de taille moyenne ou les fabricants qui misent sur la personnalisation préfèrent souvent ce type de machine car elle permet de passer rapidement d’un modèle à l’autre sans coûts d’outillage importants.
Parallèlement, il existe des machines spécialisées qui intègrent plusieurs opérations autour du contour. Ces équipements dits multi-fonctions assurent à la fois la découpe, le formage et parfois le rivetage, ce qui permet d’obtenir un bord déjà préparé pour l’assemblage. Dans une casserole par exemple, après la découpe du contour, la machine effectue le perlage du bord, c’est-à-dire un repli ou un arrondi qui rigidifie la pièce et empêche toute blessure lors de l’utilisation. Ce type de technologie est essentiel dans la production industrielle car il réduit le nombre de manipulations et améliore l’efficacité globale de la ligne. Certaines usines, pour aller encore plus loin, utilisent des chaînes entièrement automatisées où la feuille de métal est d’abord découpée, puis formée, ensuite perlée et enfin polie avant d’être envoyée vers les étapes de finition et d’assemblage.
Pour les fabricants orientés vers l’innovation et le prototypage, les machines à commande numérique CNC représentent une solution de plus en plus utilisée. Elles permettent de programmer des trajectoires de coupe très précises, de réaliser des contours sur mesure et de s’adapter rapidement à de nouvelles conceptions. Le recours à des tables rotatives facilite le travail des formes circulaires, tandis que le contrôle numérique garantit une qualité constante sur toutes les pièces, même lorsque la série est limitée. Ces équipements n’atteignent pas la vitesse de production des presses, mais ils répondent à la demande croissante de diversité et de personnalisation dans le marché des ustensiles de cuisine. De plus, la flexibilité offerte par la CNC réduit les délais de mise en production et facilite l’expérimentation de nouveaux designs.
Ainsi, la fabrication des contours d’ustensiles de cuisine se situe à la croisée de plusieurs technologies qui ne s’excluent pas mais se complètent selon les besoins. Les grandes usines combinent souvent presses pour les volumes massifs et lasers pour les séries spéciales, tandis que les ateliers plus petits privilégient la CNC et les équipements flexibles. Le choix de la machine dépend non seulement de la taille de la production, mais aussi du type de matériau, de la complexité des formes et du niveau de finition attendu. L’évolution du marché, où l’esthétique et la différenciation prennent une place importante aux côtés de la robustesse et de la fonctionnalité, pousse de plus en plus de fabricants à investir dans des technologies capables de produire des contours à la fois précis, sûrs et adaptés à une grande variété de designs.
Dans l’industrie de la fabrication des ustensiles de cuisine, la question des contours occupe une place centrale car elle détermine la qualité perçue du produit, son confort d’utilisation et surtout sa sécurité. Le bord d’une casserole ou d’une poêle ne doit présenter ni arêtes vives ni irrégularités susceptibles de causer des blessures ou de compromettre la solidité de l’ustensile. Pour obtenir ce résultat, les fabricants ont développé au fil des décennies un ensemble de machines spécialisées qui permettent de découper, façonner, arrondir et renforcer ces contours avec une précision industrielle. Les premières solutions reposaient presque exclusivement sur des presses mécaniques et hydrauliques, capables de découper des disques ou des formes prédéfinies dans des tôles d’acier inoxydable ou d’aluminium. Le principe est simple mais efficace : une matrice épouse le dessin du contour et, sous la pression de la presse, la feuille métallique est cisaillée net. Ce procédé, encore utilisé aujourd’hui dans les grandes usines, se distingue par sa rapidité et sa capacité à reproduire des milliers de pièces parfaitement identiques en un temps très court. Toutefois, il impose la fabrication de matrices spécifiques pour chaque modèle, ce qui peut représenter un investissement conséquent et peu rentable pour des séries limitées ou des formes changeantes.
Avec l’arrivée des technologies de découpe modernes, le laser s’est imposé comme une alternative de plus en plus courante. Dans ce cas, aucun outil physique n’entre en contact avec la pièce : un faisceau laser piloté par ordinateur trace le contour et découpe la matière avec une finesse extrême. L’avantage de ce procédé réside dans sa flexibilité, puisqu’il suffit de modifier le programme pour changer de forme, sans avoir recours à de nouvelles matrices. La découpe laser permet également de traiter des formes complexes, des motifs décoratifs et des géométries impossibles à réaliser par presse traditionnelle. En outre, la qualité de coupe est telle que les opérations de finition sont réduites au minimum, ce qui représente un gain de temps et une réduction des coûts de polissage ou d’ébavurage. Les ateliers qui travaillent sur des séries réduites, sur des prototypes ou sur des gammes variées trouvent dans cette technologie une solution parfaitement adaptée à leurs besoins. Cependant, la vitesse de coupe reste inférieure à celle des presses dans un contexte de production massive, et le coût initial des machines laser reste relativement élevé.
Entre ces deux approches principales se trouvent des équipements hybrides et multifonctions, pensés pour les lignes de production modernes. Il s’agit de machines qui ne se limitent pas à la découpe mais enchaînent plusieurs opérations sur le contour : perlage, roulage, rivetage et parfois même polissage. Le perlage consiste à replier légèrement le bord découpé pour l’arrondir et le renforcer, évitant ainsi les arêtes tranchantes et augmentant la rigidité de la pièce. Le roulage va encore plus loin en enroulant le bord de manière circulaire, procédé très répandu pour les casseroles et les couvercles. Ces étapes ne sont pas seulement esthétiques, elles garantissent que l’ustensile supportera mieux les chocs, qu’il sera plus agréable à manipuler et qu’il pourra s’adapter parfaitement aux autres composants de la batterie de cuisine. Les fabricants qui visent des volumes importants optent pour ces machines intégrées car elles réduisent les manipulations, augmentent la cadence et assurent une homogénéité irréprochable.
Les machines à commande numérique CNC occupent également une place croissante dans ce domaine. Elles permettent de découper et de profiler des contours avec un contrôle informatique très précis. Dotées de tables rotatives et de lames spéciales, elles offrent une grande flexibilité pour créer aussi bien des formes standards que des contours personnalisés. Leur précision et leur capacité à s’adapter rapidement à de nouveaux modèles les rendent particulièrement intéressantes pour des fabricants orientés vers l’innovation, la personnalisation ou la production sur mesure. Bien que leur rendement soit inférieur à celui des presses en production de masse, elles comblent un vide en offrant une solution intermédiaire entre la rigidité des procédés traditionnels et la souplesse du laser.
Au final, le choix des machines pour la fabrication des contours d’ustensiles de cuisine n’est jamais uniforme. Une usine qui produit en grande série aura intérêt à combiner des presses de découpe pour les pièces standards et des équipements multifonctions pour intégrer les étapes de perlage et de roulage, tandis qu’un atelier plus modeste ou spécialisé dans le haut de gamme privilégiera le laser et la CNC pour gagner en flexibilité et en précision. L’objectif reste toujours le même : obtenir un contour parfaitement régulier, sûr et résistant, qui reflète la qualité de l’ustensile et lui assure une longue durée de vie. Derrière l’apparente simplicité d’un bord de casserole ou de poêle se cache donc une maîtrise technologique complexe qui mobilise un savoir-faire mécanique, numérique et métallurgique très avancé.
Détoureuses-façonneuses pour production en série
Les détoureuses-façonneuses sont des machines industrielles spécialement conçues pour réaliser en continu la découpe et la mise en forme des contours d’objets métalliques, et elles occupent une place essentielle dans la production en série d’ustensiles de cuisine. Leur rôle est d’assurer, de manière automatique et répétitive, le détourage des pièces découpées dans la tôle – par exemple des disques ou ébauches de casseroles et de poêles – puis de façonner leurs bords afin qu’ils soient à la fois réguliers, solides et exempts de bavures. Dans un processus typique, la feuille ou le disque métallique issu d’une presse ou d’une ligne de découpe est introduit dans la détoureuse-façonneuse qui, grâce à un outillage adapté, enlève l’excédent de matière en périphérie et calibre parfaitement le diamètre. La pièce passe ensuite dans une opération de façonnage où le bord est roulé, perlé ou renforcé selon les besoins. Ce double mouvement – détourage puis façonnage – permet de préparer l’ustensile à l’étape suivante de fabrication, qu’il s’agisse du polissage, du montage de poignées ou de l’assemblage avec un couvercle.
Ces machines sont particulièrement appréciées dans la production en série car elles offrent une cadence très élevée tout en assurant une homogénéité constante d’une pièce à l’autre. Là où un travail manuel ou semi-automatique exigerait un contrôle permanent et des reprises fréquentes, la détoureuse-façonneuse garantit une précision millimétrique et réduit considérablement les temps morts. Leur conception robuste leur permet de travailler sans interruption sur des matériaux exigeants comme l’acier inoxydable, l’aluminium anodisé ou les alliages multicouches utilisés pour les fonds thermodiffuseurs. Elles intègrent souvent des dispositifs de lubrification et de refroidissement qui prolongent la durée de vie des outils et assurent une coupe nette. Dans certains modèles plus avancés, plusieurs opérations sont combinées dans une seule machine : détourage, roulage, perlage et même sertissage du bord. Cette intégration optimise l’espace dans l’atelier et réduit les manipulations, ce qui se traduit par une productivité accrue et un meilleur contrôle des coûts de production.
La valeur ajoutée des détoureuses-façonneuses réside aussi dans leur capacité à adapter rapidement l’outillage à différents modèles. Dans une usine d’ustensiles de cuisine produisant plusieurs diamètres de casseroles ou de poêles, il suffit de changer le jeu de matrices et de galets de façonnage pour passer d’un format à un autre, tout en conservant la même précision. Cela permet une grande flexibilité sans compromettre la cadence. Grâce à l’automatisation de l’alimentation et de l’éjection des pièces, ces machines peuvent fonctionner en continu, parfois même sur plusieurs équipes de travail, garantissant ainsi une production massive et régulière. Dans un secteur où les volumes se comptent en dizaines ou centaines de milliers de pièces par mois, elles constituent un maillon indispensable de la ligne de fabrication.
On comprend donc que la détoureuse-façonneuse n’est pas seulement une machine de découpe supplémentaire, mais un élément clé de la standardisation industrielle des ustensiles de cuisine. Elle permet de transformer une simple ébauche métallique en une pièce prête à être finie, avec des contours parfaitement calibrés, solides et sécurisés pour l’utilisateur final. C’est cette régularité invisible pour le consommateur, mais essentielle pour l’industriel, qui fait toute la différence entre une production artisanale et une production industrielle de haute cadence.
Les détoureuses-façonneuses utilisées pour la production en série représentent l’un des maillons essentiels de l’industrie des ustensiles de cuisine, car elles permettent d’assurer à très grande vitesse une découpe précise des contours et une mise en forme des bords de chaque pièce. Dans un processus de fabrication typique, la tôle d’acier inoxydable ou d’aluminium est d’abord découpée grossièrement sous forme de disques ou d’ébauches, puis ces ébauches passent dans la détoureuse-façonneuse qui enlève l’excédent de matière, ajuste le diamètre et donne au bord sa première finition. Cette opération de détourage est réalisée avec une grande précision afin que chaque casserole, poêle ou couvercle ait exactement la même dimension et puisse s’intégrer parfaitement dans une gamme standardisée de produits. Une fois le contour calibré, la même machine effectue généralement une opération de façonnage qui peut prendre la forme d’un perlage, d’un roulage ou d’un sertissage. Le perlage consiste à créer un léger repli arrondi qui renforce le bord et élimine les arêtes vives, tandis que le roulage forme un bourrelet circulaire plus marqué qui accroît la rigidité et donne une finition esthétique. Le sertissage, quant à lui, est utilisé lorsque deux éléments doivent être solidement assemblés, comme le fond rapporté d’une casserole multicouche. Ces étapes sont capitales car elles déterminent non seulement l’aspect visuel du produit fini mais aussi sa sécurité et sa durabilité.
La raison pour laquelle ces machines sont indispensables à la production en série réside dans leur capacité à répéter ces opérations avec une cadence extrêmement élevée et une précision constante. Alors qu’un façonnage manuel ou semi-automatique exigerait beaucoup de main-d’œuvre et risquerait d’introduire des variations d’une pièce à l’autre, la détoureuse-façonneuse industrielle fonctionne de manière continue, souvent intégrée dans une ligne automatisée où les pièces sont alimentées par convoyeur et éjectées automatiquement après traitement. Cela permet de produire des milliers d’ustensiles en très peu de temps, tout en garantissant une homogénéité parfaite. Les modèles les plus avancés sont équipés de systèmes de commande numérique qui contrôlent avec exactitude la vitesse de rotation, la pression exercée par les galets de façonnage et la profondeur du roulage, assurant ainsi un résultat constant sur des matériaux parfois difficiles à travailler comme l’inox épais ou les fonds multicouches en aluminium et acier. De plus, ces machines intègrent souvent des dispositifs de lubrification et de refroidissement qui augmentent la durée de vie des outils et assurent une coupe nette sans bavures.
L’un des grands avantages des détoureuses-façonneuses modernes est leur flexibilité. Dans une usine qui fabrique différentes gammes de casseroles et de poêles, il est possible de passer rapidement d’un diamètre à un autre ou d’un profil de bord à un autre en changeant simplement le jeu de matrices et les galets de façonnage. Cette modularité est essentielle pour répondre à la demande variée du marché sans sacrifier la productivité. Les fabricants peuvent ainsi produire des petites casseroles, des grandes marmites ou des poêles à frire de dimensions variées sur la même ligne de production, en optimisant les temps de réglage pour maintenir une cadence élevée.
Il faut aussi noter que la régularité et la qualité des contours obtenus par ces machines ont une incidence directe sur les étapes ultérieures de fabrication. Un contour mal calibré pourrait compliquer l’assemblage d’un couvercle ou d’une poignée, ou encore nuire à la stabilité de l’ustensile sur une plaque de cuisson. À l’inverse, un contour parfaitement détourné et façonné facilite le polissage, améliore la résistance mécanique et donne au produit une finition haut de gamme qui répond aux attentes du consommateur. C’est pourquoi les industriels investissent massivement dans ces équipements, car ils savent que la maîtrise du contour conditionne l’image de qualité de toute leur gamme.
En résumé, la détoureuse-façonneuse n’est pas seulement une machine qui découpe et forme le métal, elle est l’outil qui transforme une simple ébauche en une pièce calibrée, homogène et prête à entrer dans la phase finale de production. Sans elle, la fabrication en série des ustensiles de cuisine modernes serait pratiquement impossible, car aucune autre technologie n’offre le même compromis entre vitesse, précision, répétabilité et flexibilité. Derrière chaque bord parfaitement arrondi de casserole ou chaque contour régulier de poêle se cache donc une technologie sophistiquée, optimisée pour répondre aux exigences d’une production industrielle de masse où la qualité doit être garantie sur des dizaines de milliers de pièces identiques.
Les détoureuses-façonneuses, dans le contexte de la production en série d’ustensiles de cuisine, sont au cœur des lignes de fabrication modernes et représentent un niveau avancé d’automatisation industrielle. Leur rôle ne se limite pas au simple détourage des pièces, mais englobe l’ensemble des opérations nécessaires pour transformer une ébauche métallique en un composant prêt à être assemblé, poli et conditionné pour le marché. Dans un processus typique, les disques ou ébauches métalliques issus des presses de découpe sont automatiquement acheminés vers la détoureuse-façonneuse par des systèmes de convoyage ou de robots de manutention. Cette alimentation automatique permet d’optimiser la cadence et de garantir une régularité parfaite sur chaque pièce traitée. La machine commence par enlever l’excédent de matière en périphérie, calibrant le diamètre avec une précision millimétrique. Elle enchaîne ensuite les opérations de façonnage du bord, qui peuvent inclure le roulage, le perlage ou le sertissage, chacune ayant un rôle précis : le roulage renforce la rigidité, le perlage arrondit le bord pour assurer la sécurité de l’utilisateur et le sertissage permet de préparer les pièces pour un assemblage futur, par exemple avec des fonds multicouches ou des poignées rivetées. L’ensemble de ces opérations se déroule sans intervention humaine directe, ce qui minimise les risques d’erreur et maximise la répétabilité, un critère fondamental lorsque l’on produit plusieurs dizaines de milliers de casseroles ou de poêles par mois.
La conception mécanique de ces détoureuses-façonneuses est extrêmement robuste afin de résister aux contraintes exercées par le traitement de matériaux épais et denses comme l’acier inoxydable de qualité alimentaire ou l’aluminium multicouche utilisé pour les fonds thermodiffuseurs. Les galets et matrices de façonnage sont calibrés avec exactitude et leur usure est minimisée grâce à des systèmes de lubrification et de refroidissement sophistiqués, qui prolongent la durée de vie des composants critiques et assurent une qualité constante. Les modèles avancés intègrent également des commandes numériques permettant de contrôler la vitesse de rotation des pièces, la pression exercée par les galets et la profondeur du roulage, ce qui permet de maintenir des standards de qualité très stricts, même sur de longues séries. Cette automatisation avancée contribue non seulement à la productivité, mais aussi à la sécurité de l’atelier, car le contact humain avec les outils tranchants et les pièces en mouvement est réduit au minimum.
L’intégration des détoureuses-façonneuses dans des lignes de production complètes est une autre facette de leur importance industrielle. Dans une usine moderne, elles sont rarement utilisées seules : elles font partie d’une chaîne automatisée qui comprend l’alimentation des ébauches, la découpe initiale, le détourage et le façonnage, le polissage ou le brossage, l’assemblage des poignées et des fonds, et parfois même le conditionnement final. Chaque machine de la ligne communique avec la suivante grâce à des systèmes de contrôle centralisés, permettant de synchroniser les cadences et de minimiser les temps morts. Cela crée une continuité quasi ininterrompue dans le flux de production, réduisant les coûts de main-d’œuvre et optimisant l’utilisation des matières premières. Les détoureuses-façonneuses contribuent ainsi à transformer l’atelier en une véritable unité industrielle capable de produire des volumes massifs avec une qualité constante, un niveau de finition homogène et des délais de livraison courts.
Un autre point essentiel réside dans la flexibilité qu’offrent ces machines pour s’adapter aux différentes tailles et modèles de produits. Les matrices et galets de façonnage peuvent être remplacés rapidement, permettant de passer d’une petite poêle de 18 cm à une grande marmite de 30 cm sans perturber la cadence de production. Cette modularité est particulièrement importante pour répondre aux exigences du marché moderne, où les consommateurs recherchent à la fois des ustensiles standardisés et des variantes spécifiques avec des contours ou des finitions différentes. En combinant robustesse mécanique, précision millimétrique, automatisation complète et flexibilité d’outillage, les détoureuses-façonneuses permettent aux fabricants de maintenir un équilibre optimal entre volume de production et qualité produit.
En définitive, ces machines représentent l’aboutissement de décennies de développement industriel dans le domaine des ustensiles de cuisine. Elles incarnent la capacité à produire en série des pièces complexes avec une régularité parfaite, tout en intégrant des opérations de finition qui garantissent sécurité, esthétique et durabilité. Les contours parfaitement façonnés, les bords roulés et perlés, et les pièces calibrées à l’échelle industrielle sont le résultat direct de la maîtrise technique que ces détoureuses-façonneuses apportent. Sans elles, il serait impossible de combiner cadence élevée, qualité constante et flexibilité nécessaire pour répondre aux besoins variés des marchés contemporains. Leur intégration dans une ligne de production complète transforme des matières premières en ustensiles prêts à l’emploi, avec un niveau de standardisation et de finition qui répond aux exigences les plus strictes des consommateurs et des industriels.
Dans l’univers industriel des ustensiles de cuisine, les détoureuses-façonneuses représentent une évolution majeure qui permet de transformer une simple ébauche métallique en un produit quasi fini, avec une régularité et une qualité qui seraient impossibles à atteindre manuellement. Le fonctionnement interne de ces machines est un exemple de précision mécanique et d’ingénierie appliquée : dès l’arrivée de la pièce, souvent transportée par convoyeur ou robot automatisé, la machine effectue une série d’opérations parfaitement coordonnées. Tout d’abord, le détourage consiste à enlever les excédents de matière sur le pourtour de l’ébauche afin d’obtenir un diamètre exact et une forme nette. Cette opération repose sur des matrices spécifiquement calibrées et durcies pour résister à des milliers de cycles de production sans perte de précision. La pièce est maintenue en position par des systèmes de serrage ajustables, qui empêchent tout glissement et garantissent que chaque contour correspond exactement aux dimensions prévues. La synchronisation de la rotation de la pièce et du mouvement des galets de coupe est cruciale, car un décalage même minime pourrait créer des bavures ou des irrégularités qui compliqueraient les étapes suivantes.
Après le détourage, le façonnage des bords entre en jeu, et cette étape est souvent la plus critique car elle conditionne à la fois l’aspect visuel et la résistance mécanique du produit. Les galets de roulage, en acier trempé, appliquent une pression précise sur le bord tout en le déformant légèrement pour créer un rebord arrondi ou un perlage. Cette opération peut être ajustée pour modifier l’épaisseur du bord, la profondeur du roulage ou l’angle de l’arrondi, offrant ainsi une flexibilité totale selon le type d’ustensile produit. Les systèmes modernes utilisent des capteurs et des contrôleurs numériques pour mesurer en temps réel la force appliquée et la rotation de la pièce, assurant une uniformité parfaite sur chaque lot, ce qui est indispensable pour la production de milliers de casseroles ou poêles identiques. Dans certains modèles avancés, la machine peut même effectuer un sertissage léger pour préparer le bord à l’assemblage avec un fond multicouche ou une poignée rivetée, intégrant ainsi plusieurs opérations critiques dans un seul cycle automatisé.
Les détoureuses-façonneuses ne se contentent pas de travailler sur une seule pièce à la fois ; elles sont conçues pour fonctionner en continu sur des lignes de production entièrement automatisées. Les pièces sont alimentées en continu, traitées, puis éjectées vers l’étape suivante, qui peut être le polissage, le brossage, le montage de poignées ou le contrôle qualité. Cette automatisation permet de minimiser le contact humain avec des surfaces métalliques tranchantes et des outils en mouvement, réduisant ainsi les risques d’accident et assurant un rythme de production ininterrompu. Les lignes modernes peuvent traiter plusieurs milliers de pièces par jour, avec des tolérances millimétriques et une répétabilité totale, ce qui serait impossible à atteindre avec des méthodes semi-manuelles ou artisanales. La capacité à gérer différents diamètres et types de contours est également un point fort de ces machines : grâce à des matrices et galets interchangeables, elles peuvent passer d’une petite poêle à une grande casserole sans perte de temps ni de précision.
La robustesse de la machine est un autre élément crucial. Les composants internes, souvent fabriqués en acier traité et renforcé, sont conçus pour supporter les contraintes continues d’un métal parfois épais et difficile à travailler. Les systèmes de lubrification et de refroidissement intégrés permettent de maintenir une température stable des outils, réduisant l’usure et préservant la qualité de coupe et de façonnage. Les contrôleurs numériques avancés enregistrent les paramètres de production et peuvent alerter l’opérateur en cas de dérive, garantissant ainsi une homogénéité parfaite de l’ensemble de la production. La combinaison de mécanique de précision, d’automatisation avancée et de systèmes de contrôle intelligents fait des détoureuses-façonneuses des machines indispensables dans tout atelier industriel qui vise à produire à la fois en grande série et avec des standards de qualité élevés.
En résumé, le rôle des détoureuses-façonneuses dans la production industrielle d’ustensiles de cuisine ne se limite pas à la découpe ou au simple façonnage des bords. Elles constituent le pivot central d’une ligne de production automatisée où chaque pièce est détournée, roulée, perlée et éventuellement préparée pour un assemblage futur, avec une précision et une répétabilité impossibles à atteindre autrement. Leur capacité à fonctionner en continu, à s’adapter à différents modèles et à intégrer plusieurs opérations critiques en un seul cycle fait d’elles un investissement stratégique pour toute entreprise souhaitant combiner volume de production élevé, qualité constante et flexibilité pour répondre aux exigences du marché. Derrière chaque casserole parfaitement calibrée, chaque poêle aux bords arrondis et chaque couvercle ajusté avec précision, se cache donc la complexité technique et la sophistication des détoureuses-façonneuses, véritables artisans invisibles de la production industrielle moderne.
Machines industrielles de finition des bords
Les machines industrielles de finition des bords jouent un rôle crucial dans la production d’ustensiles de cuisine et d’autres produits métalliques, car elles assurent que chaque pièce ait un contour parfaitement lisse, uniforme et sécurisé pour l’utilisateur. Dans une ligne de production industrielle, ces machines interviennent généralement après les étapes de découpe et de façonnage, lorsque l’ustensile a déjà sa forme définitive mais présente encore des irrégularités, bavures ou arêtes vives qui pourraient nuire à sa sécurité ou à son apparence. Le principe de fonctionnement repose sur des outils rotatifs ou oscillants qui enlèvent les excédents de métal et arrondissent le bord, souvent tout en combinant un léger polissage pour préparer la surface à l’étape suivante. Ces machines sont conçues pour fonctionner en continu sur des volumes élevés, capables de traiter des centaines, voire des milliers de pièces par jour, avec une régularité impossible à atteindre manuellement.
Parmi les technologies utilisées, on trouve les meuleuses à bande, les brosses rotatives, les polissoirs vibrants et les systèmes de meulage à galets ou à rouleaux. Chaque système a ses avantages : les bandes abrasives sont très efficaces pour éliminer rapidement les bavures et adoucir les arêtes, les brosses rotatives permettent un léger polissage tout en arrondissant le bord, et les galets ou rouleaux de finition offrent une précision extrême sur le contour, souvent en combinaison avec des mouvements de roulage ou de perlage déjà réalisés par les détoureuses-façonneuses. Certaines machines plus avancées intègrent des dispositifs de contrôle automatique qui ajustent la pression ou la vitesse en fonction de l’épaisseur et du matériau de la pièce, garantissant une qualité uniforme quel que soit le type d’ustensile ou sa taille.
L’intégration de ces machines dans une ligne de production complète est essentielle pour maintenir la cadence tout en respectant les standards de sécurité et d’esthétique. Dans une usine moderne, les pièces passent souvent automatiquement des détoureuses-façonneuses aux machines de finition, avec des convoyeurs ou des robots qui assurent l’alimentation et l’éjection sans intervention humaine. Cela permet non seulement d’accélérer le processus mais aussi de réduire le risque d’accidents liés au contact avec les pièces métalliques et les outils abrasifs. Les lignes automatisées peuvent également inclure des systèmes de mesure et de détection des défauts : des capteurs contrôlent le profil du bord et signalent toute pièce qui ne respecte pas les tolérances, permettant de corriger immédiatement les paramètres de la machine ou d’écarter les pièces défectueuses.
Les machines de finition des bords sont aussi modulaires et adaptables. Selon le type d’ustensile – poêles, casseroles, couvercles, fonds multicouches – elles peuvent être équipées de différents galets, brosses, bandes abrasives ou rouleaux de polissage. Cette flexibilité permet aux fabricants de passer rapidement d’un modèle à un autre sans perte significative de temps ni de qualité. Certaines installations combinent plusieurs technologies sur une même machine : détourage léger, roulage, ébavurage et polissage, assurant ainsi que le bord est prêt pour les étapes finales comme l’assemblage des poignées, le revêtement antiadhésif ou le conditionnement.
En résumé, les machines industrielles de finition des bords constituent un maillon indispensable dans la production d’ustensiles de cuisine de haute qualité. Elles garantissent non seulement la sécurité et l’esthétique des produits, mais elles permettent également d’atteindre les cadences élevées requises dans l’industrie moderne, tout en offrant une régularité et une précision inégalées. Ces machines, lorsqu’elles sont intégrées dans des lignes automatisées avec détourage, façonnage et polissage, transforment les ébauches métalliques en ustensiles parfaitement finis, prêts à répondre aux standards les plus exigeants des consommateurs et des marchés internationaux.
Les machines industrielles de finition des bords représentent un élément clé dans la production d’ustensiles de cuisine, car elles garantissent que chaque pièce soit sécurisée, fonctionnelle et esthétiquement parfaite avant d’atteindre les étapes d’assemblage, de revêtement ou d’emballage. Après les phases de découpe et de façonnage, les bords des casseroles, poêles ou couvercles présentent souvent des irrégularités, des bavures ou des arêtes vives issues des opérations précédentes, qu’il est indispensable de corriger pour assurer la sécurité de l’utilisateur et la durabilité du produit. Ces machines sont conçues pour fonctionner en continu et à grande cadence, souvent intégrées dans des lignes automatisées où les pièces sont transférées sans intervention humaine, ce qui permet de traiter des centaines ou milliers de pièces par jour avec une régularité extrême et sans variations d’un lot à l’autre. Le principe de fonctionnement repose sur des outils abrasifs ou rotatifs qui enlèvent les excédents de métal, arrondissent les arêtes et préparent la surface pour les étapes suivantes. Selon le type de machine, le traitement peut être effectué par bandes abrasives, brosses rotatives, rouleaux ou galets de finition, chacun offrant des niveaux de précision et de polissage différents.
Les bandes abrasives sont particulièrement efficaces pour éliminer rapidement les bavures et adoucir les arêtes, permettant de travailler sur des matériaux durs comme l’acier inoxydable ou l’aluminium épais. Les brosses rotatives, quant à elles, combinent un léger polissage et un arrondi du bord, ce qui améliore simultanément l’esthétique et la sécurité de la pièce. Les galets et rouleaux de finition offrent une précision supérieure, souvent utilisés pour peaufiner des contours déjà formés par les détoureuses-façonneuses ou pour ajuster des bords de poêles et casseroles aux tolérances exactes, indispensables pour l’assemblage des fonds multicouches ou des poignées rivetées. Dans certaines machines plus avancées, des capteurs de contrôle ajustent automatiquement la vitesse de rotation, la pression appliquée ou l’angle du galet en fonction du matériau et de l’épaisseur de la pièce, garantissant ainsi un résultat uniforme sur l’ensemble du lot.
L’intégration de ces machines dans une ligne de production industrielle complète est essentielle pour maintenir une cadence élevée tout en assurant la qualité. Dans une usine moderne, les pièces passent automatiquement des détoureuses-façonneuses aux machines de finition par convoyeurs ou systèmes robotisés, permettant d’optimiser le flux et de réduire le contact humain avec les pièces métalliques et les outils abrasifs. Cette automatisation minimise les risques d’accidents et assure une production continue. Certaines lignes de production intègrent également des systèmes de contrôle qualité en temps réel, avec des capteurs optiques ou mécaniques qui mesurent le profil du bord et détectent toute irrégularité, permettant de corriger immédiatement les paramètres de la machine ou d’écarter les pièces non conformes.
La modularité et la flexibilité de ces machines constituent un autre avantage majeur. Selon le type d’ustensile et la forme du bord à traiter, elles peuvent être équipées de différents galets, rouleaux, bandes abrasives ou brosses, permettant de passer rapidement d’un modèle à un autre sans ralentir la cadence. Certaines installations combinent plusieurs opérations sur une seule machine, telles que le détourage léger, le roulage, l’ébavurage et le polissage, réduisant ainsi le nombre de manipulations et de machines nécessaires et optimisant l’espace dans l’atelier. Cette intégration permet non seulement de gagner du temps mais aussi d’assurer une régularité parfaite sur des volumes élevés.
En pratique, ces machines sont capables de traiter tous les types d’ustensiles, qu’il s’agisse de petites poêles, de grandes casseroles, de couvercles ou de fonds multicouches complexes. Leur robustesse leur permet de travailler sur des matériaux variés, allant de l’acier inoxydable le plus épais à l’aluminium ou aux alliages spéciaux pour fonds thermodiffuseurs, tout en maintenant une finition impeccable. Les systèmes de lubrification et de refroidissement intégrés prolongent la durée de vie des outils et assurent un résultat constant, ce qui est indispensable pour la production industrielle où la répétabilité et la qualité doivent être garanties sur des centaines de milliers de pièces.
En résumé, les machines industrielles de finition des bords ne sont pas de simples outils de polissage ; elles constituent un maillon essentiel de la chaîne de production des ustensiles de cuisine modernes. Elles permettent de transformer des pièces découpées et façonnées en produits finis sûrs, esthétiques et conformes aux standards industriels, tout en assurant une cadence élevée et une homogénéité parfaite. Leur capacité à combiner précision, flexibilité et automatisation complète en fait des équipements indispensables dans tout atelier industriel, garantissant que chaque casserole, poêle ou couvercle sort de la ligne avec des bords parfaitement calibrés, arrondis et prêts à passer aux étapes d’assemblage et de finition.
Les machines industrielles de finition des bords constituent un élément fondamental de la production moderne d’ustensiles de cuisine, car elles assurent la transformation des pièces brutes ou partiellement façonnées en composants totalement prêts à l’emploi, avec des contours parfaitement lisses, homogènes et sécurisés. Dans une chaîne de production typique, après la découpe initiale et le façonnage primaire par des détoureuses-façonneuses, les pièces métalliques présentent souvent des arêtes vives, des bavures ou des irrégularités qui pourraient nuire à la sécurité de l’utilisateur ou compromettre l’esthétique et la fonctionnalité du produit. Les machines de finition interviennent alors pour lisser et calibrer les bords de manière répétitive et uniforme, garantissant que chaque ustensile, qu’il s’agisse d’une poêle, d’une casserole ou d’un couvercle, respecte les standards de qualité et de sécurité les plus stricts. Elles combinent des techniques de meulage, de polissage et d’arrondissement des arêtes, souvent en utilisant simultanément plusieurs outils tels que bandes abrasives, brosses rotatives, rouleaux et galets de finition, chacun ayant un rôle précis dans la régularisation du contour et la préparation de la surface pour les étapes ultérieures.
Les bandes abrasives sont particulièrement efficaces pour retirer rapidement les bavures et adoucir les arêtes vives tout en maintenant une cadence élevée sur des matériaux résistants comme l’acier inoxydable ou l’aluminium épais. Les brosses rotatives offrent un traitement plus fin, combinant l’ébavurage et un léger polissage pour améliorer à la fois l’esthétique et la sécurité des bords. Les galets et rouleaux de finition assurent quant à eux une précision extrême sur les contours déjà formés, permettant de reproduire des profils identiques sur des centaines ou milliers de pièces, ce qui est indispensable dans une production en série. Dans les modèles les plus avancés, des capteurs électroniques et des contrôleurs numériques ajustent en temps réel la pression, la vitesse de rotation et l’angle des outils en fonction du matériau et de l’épaisseur de la pièce, garantissant ainsi une uniformité totale et la répétabilité exacte de chaque opération, même sur des lignes à très haute cadence.
L’intégration de ces machines dans des lignes de production automatisées est essentielle pour maximiser la productivité et minimiser les interventions humaines. Les pièces sont acheminées automatiquement par convoyeurs, robots ou systèmes de préhension vers la machine de finition, où elles sont maintenues en position et traitées de manière continue avant d’être dirigées vers les étapes suivantes telles que le polissage, le revêtement antiadhésif, l’assemblage des poignées ou l’emballage final. Cette automatisation réduit non seulement les risques d’accidents liés au contact avec des outils abrasifs et des pièces métalliques tranchantes, mais elle assure également une cadence constante et la possibilité de produire des volumes massifs avec une qualité constante. Des systèmes de contrôle qualité intégrés permettent de mesurer en continu le profil des bords et de détecter immédiatement toute pièce présentant des défauts, permettant soit un ajustement automatique des paramètres de la machine, soit l’éjection des pièces non conformes afin de maintenir la régularité de la production.
La flexibilité de ces machines est un autre atout majeur. Selon le type d’ustensile et le profil du bord à traiter, elles peuvent être équipées de différents galets, rouleaux, bandes abrasives ou brosses, ce qui permet de passer rapidement d’un modèle de poêle à une casserole ou à un couvercle de dimensions différentes sans interrompre significativement la cadence de production. Certaines installations combinent plusieurs opérations sur une seule machine : détourage léger, roulage, perlage, ébavurage et polissage final, ce qui réduit le nombre de manipulations et le nombre de machines nécessaires dans l’atelier tout en optimisant l’espace et le flux de production. Cette combinaison permet d’atteindre un résultat uniforme sur l’ensemble des pièces et d’assurer que chaque ustensile est parfaitement calibré, arrondi et prêt à passer aux étapes suivantes de finition ou d’assemblage.
Les machines industrielles de finition des bords sont conçues pour traiter tous types d’ustensiles et matériaux, depuis l’acier inoxydable épais jusqu’aux alliages d’aluminium pour fonds thermodiffuseurs, en maintenant une précision constante et une cadence élevée. Les systèmes de lubrification et de refroidissement intégrés prolongent la durée de vie des outils et garantissent que la coupe, le polissage et le façonnage restent uniformes sur des centaines de milliers de pièces, ce qui est essentiel pour la production industrielle en série. Elles permettent ainsi de transformer des ébauches métalliques en produits finis sécurisés et esthétiques, avec des contours parfaitement calibrés et homogènes, et constituent un maillon indispensable pour garantir que chaque casserole, poêle ou couvercle sorti de la ligne répond aux standards de qualité les plus élevés.
En résumé, ces machines ne se contentent pas d’adoucir des arêtes : elles jouent un rôle stratégique dans la standardisation industrielle, la sécurité du produit et la satisfaction du consommateur final. Leur intégration dans une ligne de production automatisée permet de combiner vitesse, précision, répétabilité et flexibilité, ce qui rend possible la fabrication en série d’ustensiles de cuisine de haute qualité, prêts à être assemblés, polis et emballés, avec une régularité et une finition que seules ces technologies avancées peuvent garantir. Derrière chaque bord parfaitement lisse et chaque contour uniforme se cache donc un savoir-faire technologique sophistiqué, alliant mécanique de précision, contrôle automatisé et optimisation des flux industriels.
Les machines industrielles de finition des bords occupent une place stratégique dans les lignes de production modernes d’ustensiles de cuisine, car elles permettent de transformer les pièces métalliques façonnées en composants totalement prêts pour l’assemblage et la distribution, tout en garantissant sécurité, esthétique et durabilité. Ces machines interviennent après les étapes de découpe et de façonnage primaire, lorsque les ébauches de casseroles, poêles ou couvercles possèdent encore des arêtes vives, des bavures ou des irrégularités pouvant compromettre la qualité finale du produit. Le fonctionnement de ces équipements repose sur une combinaison d’outils abrasifs, rotatifs ou oscillants qui enlèvent les excédents de métal, arrondissent les bords et, souvent, préparent la surface pour les traitements ultérieurs comme le polissage ou le revêtement antiadhésif. Chaque type d’outil remplit une fonction spécifique : les bandes abrasives retirent rapidement les bavures et adoucissent les arêtes, les brosses rotatives combinent l’ébavurage et un léger polissage pour améliorer l’esthétique et la sécurité, tandis que les rouleaux et galets de finition assurent un calibrage précis des contours, essentiel pour l’assemblage futur avec les fonds multicouches ou les poignées rivetées. Dans les machines les plus sophistiquées, des capteurs et contrôleurs numériques ajustent en temps réel la vitesse, la pression et l’angle de travail, garantissant une uniformité parfaite même sur des séries de plusieurs milliers de pièces par jour.
L’intégration de ces machines dans des lignes automatisées est un facteur clé de productivité et de régularité. Les pièces sont alimentées automatiquement par des convoyeurs, des robots de manutention ou des systèmes de préhension, ce qui permet un flux continu et réduit l’intervention humaine au minimum, limitant ainsi les risques d’accidents liés au contact avec les outils tranchants et les surfaces métalliques. Les systèmes de contrôle qualité en ligne complètent ce dispositif : des capteurs optiques ou mécaniques mesurent le profil du bord et détectent immédiatement toute pièce non conforme, permettant de corriger les paramètres de la machine ou d’éjecter les pièces défectueuses. Cela assure que chaque ustensile sort de la ligne avec des bords parfaitement lisses et uniformes, prêt à passer aux étapes suivantes comme le polissage final, l’assemblage des poignées, le revêtement ou l’emballage.
La flexibilité des machines de finition des bords constitue un autre atout majeur. Selon le type d’ustensile et la géométrie des bords, elles peuvent être équipées de différents galets, rouleaux, bandes abrasives ou brosses, permettant de traiter des poêles, casseroles, couvercles ou fonds multicouches de dimensions et de profils variés sans interrompre la cadence de production. Certaines installations combinent plusieurs opérations sur une seule machine : détourage léger, roulage, perlage, ébavurage et polissage final, ce qui réduit le nombre de machines nécessaires et optimise l’espace dans l’atelier tout en garantissant une finition homogène sur chaque pièce. Cette intégration permet également d’adapter rapidement la ligne à de nouveaux modèles ou à des séries limitées sans perte significative de temps ou de qualité, ce qui est essentiel pour répondre aux exigences fluctuantes du marché.
La robustesse et la précision de ces machines sont des éléments essentiels de leur performance. Les composants internes, fabriqués en acier traité et renforcé, sont conçus pour résister à des contraintes importantes lors du traitement de matériaux épais et résistants comme l’acier inoxydable ou les alliages d’aluminium multicouches. Les systèmes de lubrification et de refroidissement prolongent la durée de vie des outils et assurent un fonctionnement régulier et fiable, permettant de maintenir une qualité constante sur des séries massives. Le contrôle automatisé des paramètres de production, la surveillance en temps réel et l’ajustement dynamique de la pression et de la vitesse garantissent que chaque opération est effectuée avec la précision requise pour produire des bords parfaits, arrondis et uniformes sur toutes les pièces.
En pratique, ces machines transforment les ébauches métalliques en produits finis, sûrs, esthétiques et prêts à être assemblés, en combinant vitesse, répétabilité, flexibilité et qualité constante. Elles permettent d’atteindre des cadences élevées tout en respectant les tolérances les plus strictes, ce qui est indispensable pour la production industrielle en série. Chaque bord parfaitement calibré et chaque contour régulier sont le résultat d’un processus sophistiqué qui intègre mécanique de précision, automatisation, contrôle numérique et optimisation du flux industriel. Sans ces machines, la production moderne d’ustensiles de cuisine de haute qualité, capable de traiter des centaines de milliers de pièces par mois avec une régularité irréprochable, serait impossible.
Si tu veux, je peux maintenant fournir un détail exhaustif des différentes configurations de machines de finition des bords, avec l’explication du rôle exact de chaque outil, de la séquence des opérations et de leur intégration dans les lignes de production automatisées, en indiquant comment chaque étape contribue à la précision, à la sécurité et à la durabilité des ustensiles.
Équipements de préparation de pièces embouties
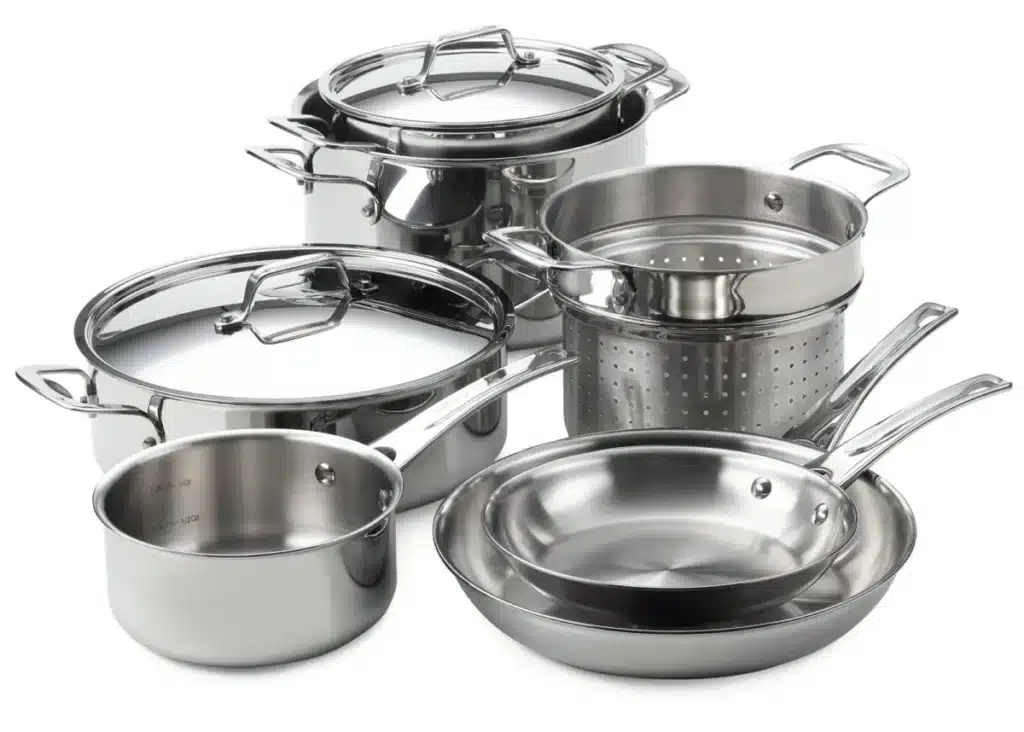
Dans l’industrie de la fabrication d’ustensiles de cuisine et d’autres produits métalliques emboutis, les équipements de préparation de pièces embouties jouent un rôle fondamental pour garantir que chaque pièce soit correctement formée, calibrée et prête à passer aux étapes suivantes de production. Ces équipements interviennent après le processus initial d’emboutissage ou de formage profond, lorsqu’une pièce en tôle est déjà partiellement transformée mais nécessite des opérations complémentaires pour atteindre la précision dimensionnelle, la régularité de forme et la qualité de surface nécessaires à l’assemblage, au polissage ou au revêtement. Leur rôle principal est d’effectuer des tâches telles que le redressage, l’ébavurage, le calibrage du diamètre, le perçage de trous de fixation, le perlage ou le roulage des bords, et parfois même le pré-polissage. Ces opérations permettent non seulement d’assurer la sécurité et l’esthétique des pièces, mais aussi de préparer des composants parfaitement homogènes pour la production en série, garantissant que chaque ustensile respectera les tolérances requises.
Les équipements de préparation peuvent être automatisés ou semi-automatisés selon le volume de production et la complexité des pièces. Dans les lignes modernes, les pièces embouties sont généralement alimentées par des convoyeurs ou des robots vers ces machines, qui les maintiennent en position grâce à des systèmes de serrage précis. Le redressage, par exemple, permet de corriger les déformations qui peuvent apparaître lors de l’emboutissage, notamment sur des pièces profondes ou des fonds multicouches. Cette opération est cruciale car une pièce voilée ou légèrement déformée ne pourra pas s’assembler correctement avec d’autres composants, comme un couvercle ou un fond rapporté. L’ébavurage est une autre étape essentielle : les bords tranchants ou irréguliers laissés par la découpe ou l’emboutissage sont éliminés par des brosses rotatives, des rouleaux abrasifs ou des systèmes de micro-meulage, assurant à la fois la sécurité de l’utilisateur et la qualité esthétique de la pièce.
Le calibrage du diamètre et des contours est souvent réalisé simultanément avec le perlage ou le roulage des bords. Ces opérations permettent de renforcer les bords, d’améliorer la rigidité de la pièce et de préparer les surfaces pour un assemblage futur ou un traitement de finition. Les machines de préparation avancées intègrent des commandes numériques qui ajustent automatiquement la pression, la vitesse et l’angle des outils en fonction de l’épaisseur du métal et de la forme de la pièce, garantissant une uniformité parfaite sur l’ensemble des séries produites. Ces systèmes permettent également de changer rapidement d’outillage pour s’adapter à différents modèles ou tailles d’ustensiles, offrant une flexibilité indispensable dans les lignes de production modernes qui doivent traiter une gamme variée de produits.
Certains équipements de préparation incluent également des fonctions complémentaires, comme le perçage automatique pour les trous de fixation des poignées ou le marquage des pièces pour assurer leur traçabilité. D’autres combinent plusieurs opérations dans une seule machine : redressage, ébavurage, perçage, roulage et pré-polissage. Cette intégration réduit le nombre de manipulations et de machines nécessaires, optimise l’espace dans l’atelier et augmente la cadence globale de production. Dans les lignes entièrement automatisées, ces équipements travaillent en synchronisation avec les détoureuses-façonneuses, les machines de finition des bords et les systèmes de polissage, créant un flux continu où chaque pièce est traitée de manière cohérente et uniforme, de l’ébauche à l’ustensile fini.
En résumé, les équipements de préparation de pièces embouties sont essentiels pour assurer la qualité, la régularité et la sécurité des produits métalliques destinés à la cuisine et à d’autres applications. Ils permettent de corriger les déformations, d’éliminer les bavures, de calibrer les dimensions, de renforcer les bords et de préparer les surfaces pour les étapes suivantes, tout en offrant flexibilité, automatisation et cadence élevée. Leur intégration dans une ligne de production industrielle moderne garantit que chaque pièce emboutie sort de la machine prête à entrer dans le flux de fabrication, contribuant ainsi à la production efficace et standardisée d’ustensiles de cuisine de haute qualité.
Les équipements de préparation de pièces embouties constituent un maillon central dans la production industrielle d’ustensiles de cuisine, car ils permettent de transformer des pièces formées mais encore incomplètes en composants prêts à subir les étapes finales de finition, d’assemblage ou de revêtement. Après l’emboutissage ou le formage profond, les pièces métalliques, qu’il s’agisse de casseroles, poêles, couvercles ou fonds multicouches, présentent souvent des déformations mineures, des irrégularités de bord, des bavures ou des variations dimensionnelles qui doivent être corrigées pour garantir une production homogène et sécurisée. Les équipements de préparation interviennent donc pour effectuer une série d’opérations complémentaires : le redressage des déformations pour obtenir des surfaces planes et régulières, l’ébavurage pour supprimer les arêtes vives et les bavures, le calibrage du diamètre et du contour, le perçage pour les points de fixation, le roulage ou le perlage des bords pour renforcer la rigidité et sécuriser les arêtes, et parfois même un pré-polissage pour préparer la pièce aux opérations ultérieures. L’objectif est de standardiser chaque pièce avant qu’elle ne poursuive son chemin sur la ligne de production, garantissant que toutes respectent les tolérances dimensionnelles et les critères esthétiques requis par l’industrie.
Dans les lignes modernes, ces équipements sont généralement automatisés afin de maintenir une cadence élevée et d’assurer une répétabilité parfaite. Les pièces embouties sont acheminées par convoyeurs ou par des robots de manutention vers les différentes stations de traitement, où elles sont maintenues en position grâce à des systèmes de serrage précis. Le redressage est réalisé par des presses, rouleaux ou galets qui appliquent des forces contrôlées pour corriger toute déformation, qu’elle soit due au formage profond, à la découpe ou aux contraintes du matériau. L’ébavurage peut être effectué par des brosses rotatives, des rouleaux abrasifs ou des micro-meuleuses qui enlèvent les bavures tout en arrondissant les arêtes, assurant à la fois la sécurité de l’utilisateur final et la qualité visuelle de la pièce. Le calibrage du diamètre et des contours est souvent combiné avec le roulage ou le perlage des bords, opérations qui renforcent la rigidité et préparent les surfaces pour l’assemblage avec d’autres composants, comme les fonds multicouches ou les poignées rivetées.
Les équipements de préparation les plus avancés intègrent des systèmes de contrôle numérique qui ajustent automatiquement les paramètres de travail en fonction de l’épaisseur du métal, du type d’alliage et de la forme de la pièce. La pression exercée, la vitesse de rotation et l’angle des galets ou rouleaux sont ainsi régulés en temps réel pour garantir une uniformité parfaite sur l’ensemble de la production. Cette automatisation permet également de changer rapidement d’outillage pour traiter différents modèles ou diamètres d’ustensiles sans perturber la cadence de production. Certains équipements combinent plusieurs opérations dans un seul cycle : redressage, ébavurage, perçage, perlage et pré-polissage, ce qui réduit le nombre de machines nécessaires, limite les manipulations et optimise l’espace dans l’atelier.
L’intégration de ces équipements dans une ligne de production complète est essentielle pour maximiser l’efficacité. Dans une usine moderne, les pièces passent automatiquement des emboutisseuses aux détoureuses-façonneuses, puis aux équipements de préparation avant d’atteindre les machines de finition des bords et les postes de polissage ou de revêtement. Chaque étape est synchronisée pour assurer un flux continu et éviter les temps morts. Des systèmes de contrôle qualité en ligne peuvent mesurer les dimensions et le profil des pièces à chaque étape, détectant immédiatement les anomalies et ajustant les paramètres de production ou écartant les pièces non conformes. Cette approche garantit que chaque ustensile, du plus petit couvercle à la plus grande casserole multicouche, sort de la ligne avec des contours parfaitement calibrés, des bords sécurisés et une surface prête pour les traitements finaux.
En résumé, les équipements de préparation de pièces embouties sont indispensables pour assurer la régularité, la sécurité et la qualité des produits métalliques destinés à la cuisine. Ils permettent de corriger les déformations, d’éliminer les bavures, de calibrer les dimensions, de renforcer les bords et de préparer les surfaces pour les étapes suivantes, tout en offrant flexibilité, automatisation et cadence élevée. Sans ces machines, il serait impossible de produire en série des ustensiles de cuisine homogènes, fiables et esthétiquement impeccables, capables de répondre aux exigences strictes du marché industriel moderne.
Les équipements de préparation de pièces embouties représentent une composante essentielle dans la production industrielle d’ustensiles de cuisine, car ils assurent que chaque pièce métallique issue de l’emboutissage ou du formage profond soit parfaitement calibrée, homogène et prête à passer aux étapes suivantes de finition, d’assemblage ou de traitement de surface. Après le formage initial, les pièces présentent souvent des irrégularités dimensionnelles, des bavures, des arêtes vives ou de légères déformations qui doivent être corrigées pour garantir non seulement la sécurité de l’utilisateur final, mais également l’intégrité mécanique et l’esthétique de l’ustensile. Les équipements de préparation interviennent donc pour exécuter une série d’opérations complémentaires, incluant le redressage des déformations, l’ébavurage des arêtes et des surfaces, le calibrage précis des diamètres et des contours, le roulage ou le perlage des bords pour améliorer la rigidité, ainsi que le pré-polissage pour préparer la pièce aux étapes de finition ultérieures. Ces opérations sont cruciales pour standardiser chaque pièce et garantir que toutes les unités produites répondent aux tolérances dimensionnelles et aux standards esthétiques requis par l’industrie.
Dans les lignes de production modernes, ces équipements sont largement automatisés afin de maintenir une cadence élevée et d’assurer une répétabilité totale. Les pièces embouties sont acheminées automatiquement par convoyeurs ou robots de manutention vers les stations de préparation, où elles sont maintenues en position par des systèmes de serrage sophistiqués qui garantissent la stabilité pendant le traitement. Le redressage, par exemple, corrige les déformations qui peuvent apparaître après l’emboutissage, en particulier sur des fonds multicouches ou des pièces profondes, permettant d’obtenir des surfaces parfaitement planes et des contours réguliers. L’ébavurage est réalisé à l’aide de brosses rotatives, de rouleaux abrasifs ou de micro-meuleuses, qui éliminent les bavures et arrondissent les arêtes vives, améliorant simultanément la sécurité et l’apparence de la pièce. Le calibrage du diamètre et la mise au profil des contours peuvent être réalisés en parallèle avec le perlage ou le roulage des bords, opérations qui renforcent la rigidité mécanique de la pièce et préparent les surfaces pour un assemblage futur avec des poignées rivetées ou des fonds multicouches.
Les équipements de préparation de haute technologie intègrent des systèmes de contrôle numérique permettant d’ajuster automatiquement la pression, la vitesse et l’angle de travail des outils en fonction de l’épaisseur du métal, du type d’alliage et de la géométrie de la pièce. Cette automatisation garantit une uniformité totale, même sur des séries massives, et permet de passer rapidement d’un modèle à l’autre sans interruption significative de la production. Certains équipements combinent plusieurs opérations dans un seul cycle, incluant le redressage, l’ébavurage, le perçage, le perlage et le pré-polissage, réduisant ainsi le nombre de machines nécessaires, limitant les manipulations et optimisant l’espace dans l’atelier. Cette intégration permet également de synchroniser parfaitement ces machines avec les détoureuses-façonneuses, les machines de finition des bords et les postes de polissage, garantissant un flux continu et optimisé dans la ligne de production.
L’efficacité de ces équipements repose sur leur robustesse et leur précision mécanique. Les composants internes, souvent en acier traité et renforcé, sont conçus pour résister aux contraintes du travail sur des matériaux épais ou multicouches, tandis que les systèmes de lubrification et de refroidissement maintiennent une température stable et prolongent la durée de vie des outils. Les capteurs et dispositifs de contrôle permettent d’identifier immédiatement toute variation ou anomalie et d’ajuster en temps réel les paramètres de travail ou d’écarter les pièces non conformes, assurant ainsi la cohérence et la qualité sur l’ensemble de la production. Cette approche garantit que chaque pièce sort de l’équipement avec des contours parfaitement calibrés, des bords sécurisés et une surface prête pour les étapes finales telles que le polissage, le revêtement ou l’assemblage.
En pratique, ces équipements permettent de traiter tous types d’ustensiles, depuis les petites poêles jusqu’aux grandes casseroles et couvercles, en adaptant automatiquement les outils et les paramètres de traitement à chaque modèle. La combinaison de redressage, ébavurage, calibrage, roulage et pré-polissage dans un flux automatisé et continu assure non seulement la sécurité et l’homogénéité des pièces, mais aussi la possibilité de produire à grande échelle avec une qualité constante, répondant aux exigences strictes des marchés industriels et des consommateurs. Chaque pièce emboutie, une fois traitée par ces équipements, est homogène, robuste et prête à être intégrée dans la chaîne de finition, garantissant que les ustensiles finaux possèdent des contours parfaitement lisses, des bords renforcés et une apparence irréprochable.
En résumé, les équipements de préparation de pièces embouties sont indispensables pour assurer la qualité, la régularité et la sécurité des ustensiles de cuisine produits en série. Leur capacité à corriger les déformations, ébavurer les arêtes, calibrer les dimensions, renforcer les bords et préparer les surfaces pour les étapes suivantes fait d’eux un maillon incontournable dans toute ligne de production automatisée. Ils permettent de combiner flexibilité, cadence élevée et précision, garantissant que chaque casserole, poêle ou couvercle sort de la ligne de production avec une finition uniforme, prête à être polie, assemblée ou revêtue.
Les équipements de préparation de pièces embouties constituent un élément indispensable dans la production industrielle d’ustensiles de cuisine, car ils permettent de transformer des ébauches métalliques issues de l’emboutissage ou du formage profond en pièces homogènes, précises et prêtes à être intégrées dans les étapes ultérieures de finition, d’assemblage ou de revêtement. Après l’emboutissage, les pièces métalliques, qu’il s’agisse de poêles, casseroles, couvercles ou fonds multicouches, présentent souvent des déformations légères, des bavures, des arêtes vives et des variations dimensionnelles qui doivent être corrigées pour garantir non seulement l’aspect esthétique du produit, mais également sa sécurité et sa fonctionnalité. Ces équipements réalisent une série d’opérations complémentaires telles que le redressage des déformations pour obtenir des surfaces planes et régulières, l’ébavurage pour éliminer les arêtes tranchantes et les bavures, le calibrage des diamètres et des contours, le roulage ou le perlage des bords pour renforcer la rigidité et sécuriser les arêtes, ainsi que le pré-polissage pour préparer la surface aux traitements ultérieurs. Ces étapes permettent d’assurer une standardisation complète des pièces et garantissent que chaque ustensile respecte les tolérances dimensionnelles et les critères esthétiques requis par l’industrie moderne.
Dans les lignes de production automatisées, ces équipements sont conçus pour fonctionner en continu et à haute cadence. Les pièces embouties sont acheminées automatiquement via des convoyeurs, des robots de manutention ou des systèmes de préhension, et elles sont maintenues en position par des systèmes de serrage sophistiqués qui garantissent leur stabilité pendant le traitement. Le redressage corrige les déformations qui peuvent apparaître après l’emboutissage, en particulier sur les pièces profondes ou multicouches, permettant d’obtenir des surfaces parfaitement planes et des contours réguliers. L’ébavurage est réalisé au moyen de brosses rotatives, de rouleaux abrasifs ou de micro-meuleuses, ce qui permet de supprimer les bavures tout en arrondissant les arêtes vives, améliorant simultanément la sécurité et l’esthétique de la pièce. Le calibrage du diamètre et la mise au profil des contours sont souvent combinés avec le roulage ou le perlage des bords, opérations qui renforcent la rigidité mécanique et préparent les surfaces pour un assemblage ultérieur, comme l’ajout de poignées rivetées ou le montage des fonds multicouches.
Les équipements de préparation les plus avancés intègrent des systèmes de contrôle numérique et des capteurs qui ajustent automatiquement la pression, la vitesse et l’angle de travail des outils en fonction du matériau, de l’épaisseur et de la géométrie de la pièce. Cette automatisation permet de garantir une uniformité totale sur des séries massives et de changer rapidement d’outillage pour traiter différents modèles ou diamètres d’ustensiles sans interrompre la cadence de production. Certaines machines combinent plusieurs opérations en un seul cycle, incluant le redressage, l’ébavurage, le perçage, le roulage ou perlage et le pré-polissage, réduisant le nombre de manipulations et d’équipements nécessaires tout en optimisant l’espace dans l’atelier. Ces équipements peuvent être synchronisés avec les détoureuses-façonneuses, les machines de finition des bords et les postes de polissage pour créer un flux continu et homogène dans la ligne de production.
La robustesse de ces machines est un facteur clé de leur efficacité. Les composants internes, fabriqués en acier traité et renforcé, résistent aux contraintes mécaniques imposées par le traitement de matériaux épais ou multicouches, tandis que les systèmes de lubrification et de refroidissement maintiennent une température stable et prolongent la durée de vie des outils. Les dispositifs de contrôle en temps réel permettent de détecter toute variation ou anomalie et d’ajuster automatiquement les paramètres ou d’écarter les pièces non conformes, assurant ainsi la cohérence et la qualité sur l’ensemble de la production. Ces équipements garantissent que chaque pièce emboutie sort de la machine avec des contours parfaitement calibrés, des bords sécurisés et une surface prête pour les opérations ultérieures de polissage, de revêtement ou d’assemblage.
En pratique, ces équipements permettent de traiter tous types d’ustensiles, des petites poêles aux grandes casseroles et couvercles, en adaptant automatiquement les outils et les paramètres de traitement à chaque modèle. La combinaison de redressage, ébavurage, calibrage, roulage, perlage et pré-polissage assure non seulement la sécurité et l’homogénéité des pièces, mais aussi la possibilité de produire en grande série avec une qualité constante, répondant aux exigences des marchés industriels et des consommateurs. Chaque pièce emboutie, après traitement, est homogène, robuste et prête à être intégrée dans la chaîne de finition, garantissant des contours parfaitement lisses, des bords renforcés et une apparence irréprochable.
En résumé, les équipements de préparation de pièces embouties sont essentiels pour assurer la qualité, la régularité et la sécurité des produits métalliques destinés à la cuisine et à d’autres applications industrielles. Ils permettent de corriger les déformations, d’éliminer les bavures, de calibrer les dimensions, de renforcer les bords et de préparer les surfaces pour les étapes suivantes, tout en offrant flexibilité, automatisation et cadence élevée. Leur rôle stratégique dans la standardisation industrielle et la production en série garantit que chaque ustensile sort de la ligne de production avec une finition uniforme, prêt pour le polissage, l’assemblage ou le revêtement.
Machines tout-en-un pour détourage
Les machines tout-en-un pour détourage représentent une innovation majeure dans la production industrielle d’ustensiles de cuisine et d’autres produits métalliques, car elles permettent de combiner plusieurs étapes de découpe et de façonnage en un seul équipement, réduisant ainsi les manipulations, optimisant l’espace et augmentant considérablement la productivité. Ces machines sont conçues pour traiter des pièces métalliques provenant d’ébauches ou de tôles embouties et effectuer simultanément le détourage précis de la forme finale de l’ustensile, tout en préparant le contour pour les opérations de finition ultérieures. Contrairement aux machines traditionnelles où le détourage, l’ébavurage, le calibrage et parfois le pré-polissage sont réalisés sur des équipements distincts, les machines tout-en-un intègrent plusieurs fonctions dans une seule unité, permettant d’exécuter en séquence ou simultanément toutes les opérations nécessaires pour transformer une pièce brute en pièce prête à être finie.
Le fonctionnement de ces machines repose sur des outils mécaniques ou électromécaniques de haute précision qui peuvent inclure des galets, des rouleaux, des couteaux rotatifs, des poinçons et des matrices spécialement conçus pour suivre exactement le contour souhaité. Certaines machines intègrent également des systèmes d’ébavurage et de lissage automatisés, capables d’éliminer les bavures et d’arrondir les arêtes immédiatement après le détourage, ce qui assure que les pièces sont sécurisées et esthétiquement uniformes dès la sortie de la machine. Ces équipements peuvent être programmés pour s’adapter à différents modèles et tailles d’ustensiles, permettant de passer rapidement d’un type de poêle à un couvercle ou à un fond multicouche, sans perte significative de temps ni d’efficacité.
Les machines tout-en-un pour détourage sont souvent équipées de systèmes de contrôle numérique et de capteurs qui surveillent en permanence la position de la pièce, la pression exercée par les outils et la vitesse de coupe, garantissant ainsi une précision extrême et une répétabilité parfaite pour chaque pièce produite. Ces contrôles permettent également d’automatiser les ajustements nécessaires en fonction des variations d’épaisseur du matériau ou de la complexité du contour, ce qui est particulièrement important pour les lignes de production modernes où les volumes sont élevés et les tolérances strictes. Certaines machines avancées intègrent même des fonctions de mesure et de correction en temps réel : elles détectent immédiatement toute irrégularité ou défaut de découpe et ajustent automatiquement la position des outils ou écartent les pièces non conformes pour garantir que seules les pièces parfaites poursuivent le flux de production.
Un autre avantage majeur des machines tout-en-un pour détourage est leur capacité à combiner vitesse, précision et flexibilité. Elles permettent de réduire le nombre d’équipements nécessaires dans l’atelier, limitant l’espace occupé et simplifiant la maintenance, tout en accélérant considérablement le cycle de production. L’automatisation complète, souvent combinée à des systèmes de convoyage ou de robotique, assure un flux continu où chaque pièce est maintenue et traitée de manière cohérente, minimisant le risque d’erreurs ou de dommages. Les outils sont conçus pour résister à l’usure et aux contraintes mécaniques élevées, et des systèmes de lubrification et de refroidissement intégrés prolongent leur durée de vie tout en maintenant la qualité de découpe.
En pratique, ces machines sont capables de traiter tous types de pièces métalliques embouties ou découpées, des poêles et casseroles aux couvercles et fonds multicouches, en assurant un détourage précis, un ébavurage et un pré-lissage immédiat, prêts pour les étapes de finition comme le polissage, le revêtement antiadhésif ou l’assemblage des poignées. Elles garantissent une uniformité totale sur des séries de production élevées et permettent d’atteindre des cadences industrielles élevées sans compromis sur la qualité. Chaque pièce qui sort de la machine est ainsi parfaitement calibrée, sécurisée et prête à être intégrée dans la chaîne de production complète, ce qui réduit les temps de manipulation et augmente la productivité globale.
En résumé, les machines tout-en-un pour détourage constituent une solution stratégique pour l’industrie des ustensiles de cuisine, permettant de combiner plusieurs opérations critiques dans un seul équipement. Elles assurent précision, répétabilité, cadence élevée et flexibilité, tout en minimisant l’espace nécessaire et en garantissant une production homogène et sécurisée. Leur intégration dans une ligne de production moderne transforme des ébauches métalliques en pièces prêtes à être finies, polies, assemblées ou revêtues, avec des contours parfaitement découpés et des arêtes sécurisées, ce qui en fait un maillon indispensable pour l’efficacité et la compétitivité industrielle.
Les machines tout-en-un pour détourage représentent une avancée majeure dans la production industrielle d’ustensiles de cuisine, car elles permettent de regrouper dans un seul équipement toutes les opérations nécessaires pour transformer une pièce métallique brute ou emboutie en composant prêt pour les étapes suivantes de finition, d’assemblage ou de revêtement. Dans les méthodes traditionnelles, le détourage, l’ébavurage, le calibrage et le pré-lissage sont réalisés sur plusieurs machines distinctes, nécessitant des manipulations supplémentaires, des temps morts et un risque accru d’erreurs ou de dommages sur les pièces. Les machines tout-en-un suppriment ces inefficacités en intégrant toutes ces fonctions dans un cycle automatisé unique, ce qui réduit considérablement le nombre de manipulations, optimise l’espace dans l’atelier et augmente la cadence globale de production. Elles sont conçues pour traiter des pièces métalliques provenant d’ébauches, de tôles embouties ou de fonds multicouches et pour exécuter avec précision le détourage du contour final, tout en assurant l’ébavurage, le calibrage des dimensions et, dans certains modèles, le pré-polissage ou le lissage des arêtes en un seul passage.
Le fonctionnement de ces machines repose sur des outils de haute précision, mécaniques ou électromécaniques, qui peuvent inclure des galets, rouleaux, couteaux rotatifs, poinçons, matrices et brosses abrasives spécialement conçus pour suivre le profil exact de la pièce et exécuter plusieurs opérations en séquence. Dès l’entrée de la pièce dans la machine, le système de serrage la maintient fermement pour assurer la stabilité pendant le traitement. Le détourage est effectué avec une précision micrométrique, suivant exactement le contour souhaité et permettant de découper même des formes complexes avec des tolérances extrêmement strictes. Immédiatement après, des systèmes d’ébavurage et de lissage interviennent pour supprimer les bavures et arrondir les arêtes vives, garantissant que la pièce est sécurisée pour la manipulation et esthétiquement uniforme. Dans certains modèles avancés, un pré-polissage ou un traitement de surface léger est appliqué pour préparer la pièce aux étapes suivantes comme le polissage final, le revêtement antiadhésif ou l’assemblage des poignées et fonds multicouches.
Ces machines sont généralement équipées de commandes numériques et de capteurs de position qui permettent un ajustement automatique et en temps réel des paramètres tels que la pression appliquée, la vitesse de rotation des outils et l’angle de coupe, en fonction de l’épaisseur et du type de matériau de chaque pièce. Cette régulation dynamique garantit une uniformité totale sur des séries de production massives et permet de changer rapidement d’outillage pour traiter différents modèles ou diamètres d’ustensiles sans ralentir la cadence. Certaines machines intègrent même des systèmes de contrôle et de mesure en ligne, capables de détecter immédiatement toute irrégularité ou défaut de découpe et d’ajuster les outils ou d’écarter les pièces non conformes, assurant ainsi une qualité irréprochable sur l’ensemble de la production.
L’un des principaux avantages de ces machines tout-en-un est la combinaison de vitesse, de précision et de flexibilité. En regroupant plusieurs opérations en un seul cycle, elles réduisent le nombre d’équipements nécessaires dans l’atelier, limitent l’espace requis et simplifient la maintenance, tout en permettant d’atteindre des cadences industrielles élevées. Les systèmes automatisés, souvent associés à des convoyeurs ou à des robots de manutention, assurent un flux continu où chaque pièce est traitée de manière cohérente et répétable. Les outils sont conçus pour résister à l’usure et aux contraintes mécaniques élevées, et des systèmes de lubrification et de refroidissement intégrés prolongent leur durée de vie tout en maintenant la qualité de la découpe et de l’ébavurage.
En pratique, ces machines permettent de traiter tous types d’ustensiles métalliques, des petites poêles aux grandes casseroles, couvercles et fonds multicouches, avec une précision et une homogénéité constantes. Chaque pièce qui sort de la machine est parfaitement détachée de sa tôle, sécurisée, arrondie sur les bords et calibrée dans ses dimensions, prête à entrer dans la chaîne de finition ou d’assemblage. Cela permet non seulement de réduire les manipulations et les temps morts, mais aussi d’assurer une production standardisée et de haute qualité sur des volumes très élevés. Les machines tout-en-un contribuent ainsi à maximiser l’efficacité, la productivité et la compétitivité industrielle, tout en garantissant que chaque ustensile possède des contours parfaitement découpés, des arêtes sécurisées et une surface prête pour les traitements ultérieurs.
En résumé, les machines tout-en-un pour détourage représentent une solution stratégique pour l’industrie des ustensiles de cuisine, car elles permettent de combiner le détourage, l’ébavurage, le calibrage et parfois le pré-polissage en un seul cycle automatisé. Elles offrent précision, répétabilité, cadence élevée et flexibilité, tout en minimisant l’espace nécessaire et en garantissant une production homogène et sécurisée. Leur intégration dans une ligne de production moderne permet de transformer rapidement des ébauches métalliques en pièces prêtes à être finies, polies, assemblées ou revêtues, avec des contours parfaitement découpés et des arêtes sûres, ce qui en fait un équipement indispensable pour l’efficacité et la standardisation industrielle.
Les machines tout-en-un pour détourage constituent une avancée essentielle dans la production industrielle d’ustensiles de cuisine et d’autres pièces métalliques embouties, car elles permettent de regrouper dans un seul équipement l’ensemble des opérations nécessaires pour transformer une ébauche brute ou une pièce emboutie en composant prêt à être fini, assemblé ou revêtu. Dans les méthodes traditionnelles, le détourage, l’ébavurage, le calibrage, le perlage ou le pré-polissage sont réalisés sur plusieurs machines distinctes, nécessitant des manipulations supplémentaires, un transport entre postes et une perte de temps significative, ainsi qu’un risque accru d’erreurs ou de dommages sur les pièces. Les machines tout-en-un éliminent ces inefficacités en intégrant plusieurs fonctions dans un cycle automatisé unique, ce qui permet de réduire le nombre de manipulations, d’optimiser l’espace dans l’atelier, de diminuer la complexité logistique et d’augmenter considérablement la productivité et la cadence globale. Ces machines sont conçues pour traiter des pièces métalliques de différentes épaisseurs et compositions, qu’il s’agisse de poêles, casseroles, couvercles ou fonds multicouches, et elles effectuent avec une précision micrométrique le détourage du contour final tout en assurant simultanément l’ébavurage, le calibrage dimensionnel, le perlage ou le roulage des bords et, dans certains modèles avancés, un pré-polissage ou un léger lissage de surface.
Le principe de fonctionnement repose sur l’intégration de plusieurs outils et mécanismes sophistiqués : galets, rouleaux, couteaux rotatifs, poinçons, matrices, brosses abrasives et systèmes de micro-meulage. Dès l’entrée de la pièce dans la machine, un système de préhension et de serrage la maintient fermement afin de garantir la stabilité et la précision pendant toutes les étapes de traitement. Le détourage est exécuté selon le profil exact programmé, permettant de découper même des formes complexes avec des tolérances extrêmement strictes, tandis que l’ébavurage et le lissage suppriment immédiatement toutes les bavures et arêtes vives, assurant la sécurité de la pièce et une finition uniforme. Le calibrage dimensionnel et la mise au profil des contours sont souvent combinés avec le roulage ou le perlage des bords, renforçant la rigidité mécanique des pièces et préparant les surfaces pour un assemblage futur ou pour les traitements ultérieurs tels que le polissage, le revêtement antiadhésif ou l’installation des poignées et fonds multicouches.
Ces machines sont équipées de systèmes de contrôle numérique avancés et de capteurs de position qui surveillent en continu la position de la pièce, la vitesse de rotation et l’angle des outils, ainsi que la pression appliquée. Cette régulation dynamique permet de garantir une précision et une répétabilité totales même sur des séries massives, et de réagir automatiquement aux variations d’épaisseur ou aux irrégularités de matériau. Certaines machines intégrées possèdent des dispositifs de mesure et de correction en temps réel qui détectent toute anomalie ou défaut de découpe et ajustent automatiquement les outils ou écartent les pièces non conformes, assurant une qualité irréprochable sur l’ensemble de la production. L’automatisation complète et la synchronisation avec les systèmes de convoyage ou de robotique permettent un flux continu et homogène, réduisant au minimum le temps de manutention et les risques d’erreurs.
La combinaison de vitesse, précision et flexibilité est l’un des principaux avantages de ces machines tout-en-un. Elles permettent de traiter différents modèles et dimensions d’ustensiles en adaptant automatiquement les paramètres de traitement et l’outillage, sans perte de cadence ni interruption de la ligne de production. L’intégration des opérations de détourage, d’ébavurage, de calibrage, de perlage et de pré-polissage dans un seul équipement réduit le nombre de machines nécessaires, limite l’espace occupé dans l’atelier et simplifie la maintenance, tout en assurant des résultats uniformes et reproductibles sur des volumes de production élevés. Les outils et composants internes, fabriqués en acier traité et renforcé, sont conçus pour résister aux contraintes mécaniques importantes et à l’usure due au traitement de matériaux épais ou multicouches, tandis que des systèmes de lubrification et de refroidissement prolongent la durée de vie des outils et assurent une qualité constante.
En pratique, chaque pièce qui sort de la machine est parfaitement détachée de sa tôle, sécurisée, arrondie sur les bords, calibrée et prête à être intégrée dans les étapes suivantes de la ligne de production. Les poêles, casseroles, couvercles et fonds multicouches bénéficient ainsi d’un détourage précis, d’un ébavurage immédiat, d’un profil exact et parfois d’un pré-polissage, garantissant que la production est homogène, sécurisée et conforme aux exigences industrielles. Ces machines permettent non seulement de réduire les manipulations et les temps morts, mais elles assurent également une standardisation complète et une cadence élevée, rendant possible la production en série d’ustensiles de cuisine de haute qualité avec des contours parfaitement découpés et des arêtes sécurisées.
En résumé, les machines tout-en-un pour détourage sont une solution stratégique dans l’industrie des ustensiles de cuisine et de la production métallique industrielle. Elles combinent le détourage, l’ébavurage, le calibrage, le perlage et le pré-polissage en un cycle automatisé unique, offrant précision, répétabilité, flexibilité et cadence élevée. Leur intégration dans une ligne de production moderne permet de transformer efficacement des ébauches métalliques en pièces parfaitement finies et homogènes, prêtes pour le polissage, le revêtement, l’assemblage ou l’emballage, tout en optimisant l’espace, réduisant les manipulations et garantissant une qualité constante sur l’ensemble de la production.
Les machines tout-en-un pour détourage représentent l’apogée de l’optimisation dans les lignes de production industrielles d’ustensiles de cuisine et d’autres produits métalliques emboutis, car elles permettent de regrouper toutes les opérations essentielles dans un seul équipement capable de transformer une ébauche métallique brute ou emboutie en pièce quasiment prête pour les étapes finales de finition, d’assemblage ou de revêtement. Dans les systèmes de production classiques, chaque opération — détourage, ébavurage, calibrage, perlage, roulage des bords, pré-polissage ou lissage léger — est réalisée sur des machines distinctes, entraînant des temps de manutention importants, une multiplication des risques de défauts ou de dommages sur les pièces, et une complexité accrue dans la logistique et l’occupation de l’espace en atelier. Les machines tout-en-un suppriment ces contraintes en intégrant toutes ces fonctions dans un seul cycle automatisé, permettant de réduire considérablement le nombre de manipulations, d’optimiser la surface au sol, d’améliorer l’efficacité globale et d’accroître la cadence de production tout en maintenant une qualité constante. Elles sont conçues pour traiter une large gamme de pièces métalliques, qu’il s’agisse de poêles, casseroles, couvercles ou fonds multicouches, et elles sont capables d’exécuter simultanément le détourage précis, l’ébavurage des arêtes, le calibrage dimensionnel, le perlage ou le roulage des bords et, dans les modèles les plus avancés, le pré-polissage ou le lissage de surface.
Le fonctionnement repose sur l’intégration de systèmes mécaniques et électromécaniques sophistiqués, comprenant des galets, rouleaux, couteaux rotatifs, poinçons, matrices, brosses abrasives, micro-meuleuses et dispositifs de lissage, conçus pour suivre avec une précision micrométrique le contour programmé et exécuter plusieurs opérations en séquence ou simultanément. À l’entrée de la pièce, des systèmes de préhension et de serrage maintiennent celle-ci de manière stable, garantissant que toutes les forces appliquées pendant le détourage, l’ébavurage et le calibrage sont uniformes et contrôlées. Le détourage suit le profil exact de la pièce avec des tolérances très strictes, permettant de découper même des formes complexes sans compromettre la précision, tandis que l’ébavurage et le lissage suppriment immédiatement les bavures et arrondissent les arêtes, assurant sécurité et esthétique. Le calibrage et la mise au profil des contours, combinés avec le roulage ou le perlage des bords, renforcent la rigidité de la pièce et préparent ses surfaces pour l’assemblage ultérieur ou le traitement final, comme le polissage, le revêtement antiadhésif ou l’installation des poignées et fonds multicouches.
Ces machines sont équipées de systèmes de contrôle numérique avancés et de capteurs sophistiqués qui surveillent en permanence la position de la pièce, la vitesse, la pression et l’angle des outils. Ces capteurs permettent d’ajuster en temps réel tous les paramètres de traitement, garantissant ainsi une uniformité totale, même sur des séries massives. Les modèles les plus perfectionnés intègrent des dispositifs de mesure et de correction automatique qui détectent toute irrégularité ou défaut de découpe et adaptent les mouvements des outils ou écartent les pièces non conformes, assurant une qualité irréprochable sur toute la production. La synchronisation avec des convoyeurs automatisés et des robots de manutention permet de créer un flux continu où chaque pièce est traitée de manière cohérente, réduisant les manipulations, les erreurs et les temps morts.
L’un des principaux avantages de ces machines est la combinaison unique de vitesse, de précision et de flexibilité. Elles peuvent traiter différents modèles et dimensions d’ustensiles en adaptant automatiquement l’outillage et les paramètres de traitement, sans interruption significative de la ligne. En intégrant détourage, ébavurage, calibrage, roulage, perlage et pré-polissage dans un seul cycle, ces machines réduisent le nombre d’équipements nécessaires, limitent l’espace requis dans l’atelier et simplifient la maintenance, tout en garantissant des résultats uniformes et reproductibles sur de grandes séries. Les outils et composants internes, en acier traité et renforcé, résistent aux contraintes mécaniques importantes et à l’usure liée au traitement de matériaux épais ou multicouches, tandis que les systèmes de lubrification et de refroidissement maintiennent une performance stable et prolongent la durée de vie des outils tout en assurant la constance de la qualité.
En pratique, chaque pièce qui sort de la machine est détachée de sa tôle de manière nette, sécurisée, avec des arêtes arrondies et calibrée dans ses dimensions, prête à entrer dans les étapes suivantes de la chaîne de production. Les poêles, casseroles, couvercles et fonds multicouches bénéficient ainsi d’un détourage précis, d’un ébavurage immédiat, d’un profil exact et, dans certains cas, d’un pré-polissage, assurant que la production est homogène, sécurisée et conforme aux standards industriels. Ces machines permettent non seulement de réduire les manipulations et les temps morts, mais elles garantissent également la standardisation et la qualité constante sur des volumes élevés, ce qui est indispensable pour la production industrielle moderne.
En résumé, les machines tout-en-un pour détourage constituent un maillon stratégique dans la production d’ustensiles de cuisine et d’objets métalliques emboutis. Elles combinent détourage, ébavurage, calibrage, perlage, roulage et pré-polissage en un seul cycle automatisé, offrant précision, répétabilité, flexibilité et cadence élevée. Leur intégration dans une ligne de production moderne permet de transformer efficacement des ébauches métalliques en pièces homogènes et prêtes à être finies, polies, assemblées ou revêtues, avec des contours parfaitement découpés et des arêtes sécurisées. Elles optimisent l’espace, réduisent les manipulations et garantissent une qualité constante, faisant d’elles un équipement indispensable pour la productivité et la compétitivité industrielle.
Systèmes de détourage et bordage intégrés

Les systèmes de détourage et bordage intégrés constituent une évolution avancée des machines tout-en-un dans la production industrielle d’ustensiles de cuisine et d’autres pièces métalliques embouties, car ils combinent non seulement le détourage précis des contours, mais également le façonnage et le renforcement des bords dans un seul flux de production continu. Ces systèmes sont conçus pour prendre en charge des pièces métalliques issues de tôles embouties ou de fonds multicouches et exécuter simultanément plusieurs opérations critiques qui étaient auparavant réalisées sur des machines séparées, telles que le découpage exact du contour, l’ébavurage, le calibrage, le roulage ou le perlage des bords, et dans certains cas, un pré-polissage ou un lissage léger de surface. L’intégration de ces fonctions dans un seul système permet de réduire considérablement le nombre de manipulations, d’accélérer le cycle de production, de limiter l’espace nécessaire en atelier et de garantir une qualité constante et reproductible pour chaque pièce produite.
Le fonctionnement de ces systèmes repose sur la combinaison de technologies mécaniques, électromécaniques et numériques sophistiquées. Les pièces sont alimentées automatiquement via convoyeurs ou robots de manutention, puis maintenues fermement par des systèmes de préhension et de serrage qui garantissent leur stabilité pendant le traitement. Le détourage est effectué selon un profil programmé avec une précision micrométrique, permettant de découper des formes complexes avec des tolérances très strictes. Immédiatement après, les outils d’ébavurage et de lissage suppriment les bavures et arrondissent les arêtes vives, tandis que les dispositifs de calibrage et de bordage appliquent un roulage, un perlage ou un façonnage des bords afin de renforcer la rigidité de la pièce, de sécuriser les arêtes et de préparer les surfaces pour l’assemblage ou le traitement final. Ces opérations intégrées garantissent que chaque pièce est uniforme, sécurisée et conforme aux spécifications industrielles dès sa sortie du système.
Les systèmes de détourage et bordage intégrés sont généralement équipés de contrôles numériques et de capteurs sophistiqués qui surveillent en permanence la position, la pression, l’angle et la vitesse des outils. Cette régulation dynamique permet d’adapter automatiquement les paramètres de traitement en fonction de l’épaisseur, du type de matériau et de la complexité du contour, assurant ainsi une précision et une répétabilité totales sur des séries massives. Certains systèmes avancés disposent également de dispositifs de mesure et de correction en temps réel capables de détecter toute irrégularité ou défaut et d’ajuster les outils ou d’écarter les pièces non conformes, ce qui garantit que seules les pièces parfaitement conformes poursuivent le flux de production. La synchronisation avec les convoyeurs et les robots de manutention permet un flux continu et homogène, minimisant les temps morts et les erreurs de manipulation.
Un des avantages majeurs de ces systèmes est leur capacité à combiner vitesse, précision et flexibilité. Ils peuvent traiter différentes tailles et formes d’ustensiles en adaptant automatiquement l’outillage et les paramètres de travail sans interruption significative de la ligne de production. L’intégration du détourage, de l’ébavurage, du calibrage et du bordage dans un seul cycle réduit le nombre de machines nécessaires, optimise l’espace au sol, simplifie la maintenance et permet d’atteindre des cadences industrielles élevées tout en maintenant une qualité homogène et reproductible. Les outils sont fabriqués en acier traité et renforcé pour résister aux contraintes mécaniques et à l’usure liées au traitement des matériaux métalliques, et des systèmes de lubrification et de refroidissement prolongent leur durée de vie tout en garantissant une constance de performance.
En pratique, chaque pièce qui sort de ces systèmes est parfaitement détachée de sa tôle, calibrée, avec des arêtes sécurisées et un contour fini, prête à être intégrée dans les étapes suivantes de la chaîne de production, comme le polissage, le revêtement ou l’assemblage des poignées et fonds multicouches. Les poêles, casseroles, couvercles et autres composants bénéficient ainsi d’un détourage précis, d’un ébavurage immédiat, d’un profil exact et d’un bordage renforcé, assurant uniformité, sécurité et conformité aux standards industriels. Ces systèmes permettent non seulement de réduire les manipulations et les temps morts, mais également de standardiser la production sur des volumes très élevés, garantissant des pièces de qualité constante et homogène.
En résumé, les systèmes de détourage et bordage intégrés sont un élément stratégique dans la production industrielle moderne d’ustensiles de cuisine et de pièces métalliques embouties. Ils combinent détourage précis, ébavurage, calibrage et bordage dans un flux automatisé continu, offrant précision, répétabilité, flexibilité et cadence élevée. Leur intégration dans une ligne de production permet de transformer efficacement des ébauches métalliques en pièces finies et homogènes, prêtes pour le polissage, l’assemblage ou le revêtement, tout en optimisant l’espace, réduisant les manipulations et garantissant une qualité constante sur l’ensemble de la production.
Les systèmes de détourage et bordage intégrés représentent une solution de pointe pour l’optimisation des lignes de production industrielles dans la fabrication d’ustensiles de cuisine et de pièces métalliques embouties, car ils permettent de regrouper plusieurs étapes critiques en un seul équipement capable de transformer des ébauches ou des tôles embouties en pièces presque prêtes pour les phases de finition, d’assemblage ou de traitement de surface. Dans les méthodes traditionnelles, le détourage, l’ébavurage, le calibrage, le perlage ou roulage des bords et parfois le pré-polissage sont réalisés sur des machines distinctes, impliquant des manipulations répétées, des transports intermédiaires et des temps morts significatifs, ainsi qu’un risque accru d’erreurs ou de défauts. Les systèmes intégrés suppriment ces inefficacités en combinant toutes ces fonctions dans un cycle unique et automatisé, permettant de réduire le nombre de manipulations, de limiter l’espace nécessaire en atelier, d’accroître la cadence et d’assurer une qualité uniforme et reproductible sur l’ensemble des pièces produites. Ces systèmes sont capables de traiter des pièces de différentes tailles et géométries, qu’il s’agisse de poêles, casseroles, couvercles ou fonds multicouches, et réalisent simultanément le détourage précis du contour, l’ébavurage, le calibrage, le perlage ou roulage des bords et parfois un pré-polissage ou un lissage léger de surface, offrant ainsi un flux de production continu et homogène.
Le principe de fonctionnement repose sur l’intégration de technologies mécaniques, électromécaniques et numériques sophistiquées. Les pièces sont introduites automatiquement à l’aide de convoyeurs, de robots ou de systèmes de manutention, puis maintenues par des systèmes de serrage qui garantissent leur stabilité et leur position exacte tout au long des opérations. Le détourage suit le profil programmé avec une précision micrométrique, permettant de découper des formes complexes avec des tolérances extrêmement strictes. Immédiatement après, les outils d’ébavurage et de lissage éliminent toutes les bavures et arrondissent les arêtes vives, tandis que les dispositifs de calibrage et de bordage appliquent un perlage, un roulage ou un façonnage des bords afin de renforcer la rigidité de la pièce, d’assurer la sécurité des arêtes et de préparer les surfaces pour les étapes suivantes comme l’assemblage des poignées ou l’application de revêtements. Ces opérations intégrées garantissent que chaque pièce sort du système avec des contours précis, des bords renforcés et une qualité homogène prête pour le traitement ultérieur.
Les systèmes de détourage et bordage intégrés sont dotés de contrôles numériques avancés et de capteurs sophistiqués qui surveillent en permanence la position, la pression, l’angle et la vitesse des outils, permettant un ajustement automatique et en temps réel des paramètres de traitement en fonction de l’épaisseur, du type de matériau et de la complexité du contour. Cette régulation dynamique garantit une précision et une répétabilité totales sur des séries massives et assure que les pièces produites respectent les spécifications strictes de l’industrie. Certains systèmes incluent également des dispositifs de mesure et de correction automatique capables de détecter toute irrégularité, défaut de découpe ou variation dimensionnelle et d’ajuster instantanément les outils ou d’écarter les pièces non conformes, garantissant ainsi que seules des pièces parfaites poursuivent le flux de production. L’automatisation complète et la synchronisation avec convoyeurs et robots de manutention permettent de créer un flux continu et homogène, réduisant les temps morts, les erreurs et les manipulations superflues.
L’un des avantages majeurs de ces systèmes est leur capacité à combiner vitesse, précision et flexibilité. Ils peuvent traiter différents modèles et tailles d’ustensiles en adaptant automatiquement l’outillage et les paramètres de travail sans interrompre la ligne de production. L’intégration des opérations de détourage, d’ébavurage, de calibrage et de bordage dans un seul cycle réduit le nombre de machines nécessaires, optimise l’espace au sol, simplifie la maintenance et permet d’atteindre des cadences très élevées tout en assurant une qualité constante et reproductible. Les outils et composants internes, fabriqués en acier traité et renforcé, sont conçus pour résister aux contraintes mécaniques importantes et à l’usure due au traitement des matériaux métalliques, tandis que des systèmes de lubrification et de refroidissement assurent la constance de performance et prolongent la durée de vie des outils.
En pratique, chaque pièce qui sort de ces systèmes est parfaitement détachée de sa tôle, calibrée, avec des arêtes sécurisées et un contour fini, prête à entrer dans les étapes suivantes de production comme le polissage, le revêtement antiadhésif ou l’assemblage des poignées et fonds multicouches. Les poêles, casseroles, couvercles et autres composants bénéficient ainsi d’un détourage précis, d’un ébavurage immédiat, d’un profil exact et d’un bordage renforcé, assurant uniformité, sécurité et conformité aux standards industriels. Ces systèmes permettent non seulement de réduire les manipulations et les temps morts, mais également de standardiser la production sur des volumes très élevés, garantissant des pièces de qualité constante et homogène.
En résumé, les systèmes de détourage et bordage intégrés représentent une solution stratégique et essentielle pour l’industrie des ustensiles de cuisine et la production industrielle de pièces métalliques embouties. Ils combinent le détourage précis, l’ébavurage, le calibrage, le perlage et le bordage dans un flux automatisé continu, offrant précision, répétabilité, flexibilité et cadence élevée. Leur intégration dans une ligne de production moderne permet de transformer efficacement des ébauches métalliques en pièces finies et homogènes, prêtes pour le polissage, l’assemblage ou le revêtement, tout en optimisant l’espace, réduisant les manipulations et garantissant une qualité constante sur l’ensemble de la production.
Les systèmes de détourage et bordage intégrés représentent aujourd’hui une solution incontournable pour l’optimisation des lignes de production industrielles dans le domaine des ustensiles de cuisine et de la fabrication de pièces métalliques embouties. Leur intérêt réside dans leur capacité à combiner, au sein d’un seul équipement, l’ensemble des opérations critiques qui, dans les procédés traditionnels, étaient effectuées sur plusieurs machines distinctes et nécessitaient de nombreuses manipulations et transferts de pièces. Ces opérations comprennent le détourage précis du contour de la pièce, l’ébavurage pour éliminer les bavures et arrondir les arêtes, le calibrage dimensionnel pour garantir que chaque pièce respecte des tolérances strictes, le perlage ou le roulage des bords afin de renforcer la rigidité et la sécurité, et, dans certains modèles avancés, un pré-polissage ou un lissage léger de surface pour préparer la pièce aux traitements ultérieurs comme le polissage final, le revêtement antiadhésif ou l’assemblage de poignées et fonds multicouches. La combinaison de ces fonctions dans un cycle automatisé unique permet de réduire considérablement le nombre de manipulations, d’accroître la cadence de production, de limiter l’espace nécessaire en atelier et de garantir une homogénéité totale de la qualité sur l’ensemble des pièces produites.
Le fonctionnement de ces systèmes repose sur l’intégration de technologies mécaniques, électromécaniques et numériques de pointe. Les pièces métalliques sont acheminées automatiquement par des convoyeurs, des robots ou des systèmes de manutention spécialisés, puis maintenues fermement par des dispositifs de serrage afin d’assurer stabilité et précision pendant toutes les opérations. Le détourage est exécuté selon un profil programmé avec une précision micrométrique, permettant de découper même des formes complexes avec des tolérances extrêmement strictes et de garantir que chaque pièce correspond exactement aux spécifications. Immédiatement après, les systèmes d’ébavurage et de lissage éliminent les bavures et arrondissent les arêtes vives, tandis que les dispositifs de calibrage et de bordage appliquent le perlage, le roulage ou le façonnage des bords, renforçant ainsi la rigidité mécanique de la pièce et sécurisant ses contours. Cette combinaison d’opérations intégrées assure que chaque pièce sort du système parfaitement formée, sécurisée et prête pour les étapes suivantes de la production.
Les systèmes de détourage et bordage intégrés sont équipés de commandes numériques avancées et de capteurs sophistiqués qui surveillent en continu la position, la pression, la vitesse et l’angle des outils. Ces dispositifs permettent un ajustement automatique et en temps réel des paramètres de traitement, garantissant une précision et une répétabilité totales même sur des séries de production massives. Les modèles les plus avancés intègrent des systèmes de mesure et de correction automatique capables de détecter toute irrégularité, défaut de découpe ou variation dimensionnelle et d’adapter instantanément les outils ou d’écarter les pièces non conformes, assurant ainsi que seules des pièces parfaitement conformes poursuivent le flux de production. La synchronisation avec les convoyeurs et la robotique de manutention permet de maintenir un flux continu et homogène, minimisant les temps morts, les erreurs et les manipulations superflues.
L’un des principaux avantages de ces systèmes est leur capacité à combiner vitesse, précision et flexibilité. Ils peuvent traiter différents modèles et tailles d’ustensiles en adaptant automatiquement l’outillage et les paramètres de traitement, sans interrompre la ligne de production et sans compromis sur la qualité. L’intégration de toutes ces opérations dans un seul cycle réduit le nombre de machines nécessaires, optimise l’espace au sol et simplifie la maintenance tout en assurant des résultats uniformes et reproductibles sur de grandes séries. Les composants et outils internes sont fabriqués en acier traité et renforcé pour résister aux contraintes mécaniques élevées et à l’usure due au traitement de matériaux métalliques épais ou multicouches, tandis que les systèmes de lubrification et de refroidissement maintiennent la performance stable et prolongent la durée de vie des outils, garantissant une qualité constante au fil de la production.
En pratique, chaque pièce qui sort de ces systèmes est détachée de sa tôle de manière nette, calibrée, avec des bords sécurisés et un contour fini, prête à entrer dans les étapes suivantes de la chaîne de production telles que le polissage, le revêtement antiadhésif ou l’assemblage des poignées et fonds multicouches. Les poêles, casseroles, couvercles et autres composants bénéficient d’un détourage précis, d’un ébavurage immédiat, d’un profil exact et d’un bordage renforcé, assurant uniformité, sécurité et conformité aux normes industrielles. Ces systèmes permettent non seulement de réduire les manipulations et les temps morts, mais également de standardiser la production sur des volumes élevés, garantissant des pièces de qualité constante et homogène.
En résumé, les systèmes de détourage et bordage intégrés constituent un élément stratégique dans la production industrielle moderne d’ustensiles de cuisine et de pièces métalliques embouties. Ils regroupent dans un cycle automatisé continu le détourage précis, l’ébavurage, le calibrage, le perlage et le roulage des bords, offrant ainsi précision, répétabilité, flexibilité et cadence élevée. Leur intégration dans une ligne de production permet de transformer efficacement des ébauches métalliques en pièces finies et homogènes, prêtes pour le polissage, le revêtement, l’assemblage ou l’emballage, tout en optimisant l’espace, réduisant les manipulations et garantissant une qualité constante sur l’ensemble de la production.
Les systèmes de détourage et bordage intégrés représentent l’évolution la plus avancée des technologies de production industrielle pour les ustensiles de cuisine et les pièces métalliques embouties, car ils permettent de regrouper dans un seul équipement l’ensemble des opérations essentielles qui, auparavant, étaient réparties sur plusieurs machines distinctes, engendrant des manipulations répétées, des transferts de pièces, des pertes de temps et un risque accru de défauts ou de dommages. Ces systèmes exécutent simultanément le détourage précis des contours, l’ébavurage des arêtes, le calibrage dimensionnel, le perlage ou le roulage des bords pour renforcer la rigidité et la sécurité, ainsi que, dans certains modèles avancés, le pré-polissage ou le lissage léger des surfaces, permettant aux pièces de sortir pratiquement prêtes pour les étapes suivantes de polissage, revêtement ou assemblage. Cette intégration réduit considérablement le nombre de manipulations, optimise l’espace dans l’atelier, améliore la cadence et garantit une qualité uniforme et reproductible sur l’ensemble des pièces produites, quelles que soient leur taille, leur forme ou leur complexité.
Le fonctionnement de ces systèmes repose sur une combinaison complexe de technologies mécaniques, électromécaniques et numériques de pointe. Les pièces sont alimentées automatiquement par des convoyeurs ou des robots de manutention, puis stabilisées et maintenues par des systèmes de serrage qui assurent leur position exacte pendant toutes les opérations. Le détourage est exécuté selon un profil programmé avec une précision micrométrique, permettant de découper même les formes les plus complexes avec des tolérances extrêmement strictes. Immédiatement après, les systèmes d’ébavurage et de lissage suppriment toutes les bavures et arrondissent les arêtes vives, tandis que les dispositifs de calibrage et de bordage appliquent le roulage ou le perlage des bords afin de renforcer la rigidité mécanique, sécuriser les arêtes et préparer les surfaces pour l’assemblage ou les traitements ultérieurs. Ces opérations intégrées garantissent que chaque pièce sort du système avec des contours parfaitement définis, des bords renforcés et une finition homogène, prête à être intégrée dans la chaîne de production.
Ces systèmes sont dotés de commandes numériques avancées et de capteurs sophistiqués qui surveillent en continu la position, la pression, la vitesse et l’angle des outils. Cette régulation dynamique permet d’adapter automatiquement tous les paramètres de traitement en fonction de l’épaisseur, du matériau et de la complexité de la pièce, assurant une précision et une répétabilité totales même sur des séries de production très importantes. Les modèles les plus avancés intègrent des dispositifs de mesure et de correction automatique capables de détecter toute irrégularité, défaut de découpe ou variation dimensionnelle et d’ajuster instantanément les outils ou d’écarter les pièces non conformes, garantissant ainsi que seules les pièces parfaitement conformes poursuivent le flux de production. La synchronisation avec les convoyeurs et les robots de manutention permet de maintenir un flux continu et homogène, minimisant les temps morts, les erreurs et les manipulations superflues, et maximisant l’efficacité globale de la ligne de production.
L’un des avantages majeurs de ces systèmes réside dans leur capacité à combiner vitesse, précision et flexibilité. Ils permettent de traiter différents modèles et tailles d’ustensiles sans interruption de la ligne, en adaptant automatiquement l’outillage et les paramètres de traitement à chaque pièce. L’intégration de toutes ces opérations dans un seul cycle réduit le nombre de machines nécessaires, optimise l’espace au sol, simplifie la maintenance et permet d’atteindre des cadences très élevées tout en assurant une qualité uniforme et reproductible sur de grandes séries. Les outils et composants internes, fabriqués en acier traité et renforcé, résistent aux contraintes mécaniques et à l’usure liées au traitement de matériaux épais ou multicouches, tandis que les systèmes de lubrification et de refroidissement garantissent la constance de performance et prolongent la durée de vie des outils, permettant ainsi de maintenir une qualité constante tout au long de la production.
En pratique, chaque pièce qui sort de ces systèmes est détachée de sa tôle de manière nette, calibrée, avec des arêtes sécurisées et un contour fini, prête à passer aux étapes suivantes telles que le polissage, le revêtement ou l’assemblage des poignées et fonds multicouches. Les poêles, casseroles, couvercles et autres composants bénéficient d’un détourage précis, d’un ébavurage immédiat, d’un profil exact et d’un bordage renforcé, assurant uniformité, sécurité et conformité aux normes industrielles. Ces systèmes permettent non seulement de réduire les manipulations et les temps morts, mais également de standardiser la production sur des volumes très élevés, garantissant des pièces de qualité constante et homogène, répondant aux exigences des lignes de production modernes et à haut rendement.
En résumé, les systèmes de détourage et bordage intégrés constituent une solution stratégique pour l’industrie des ustensiles de cuisine et la production industrielle de pièces métalliques embouties, combinant dans un flux automatisé continu le détourage précis, l’ébavurage, le calibrage, le perlage et le roulage des bords. Ils offrent précision, répétabilité, flexibilité et cadence élevée, permettant de transformer efficacement des ébauches métalliques en pièces finies et homogènes, prêtes pour le polissage, le revêtement ou l’assemblage, tout en optimisant l’espace, réduisant les manipulations et garantissant une qualité constante sur l’ensemble de la production.
Je peux maintenant continuer en rédigeant un manuel complet ultra-détaillé des systèmes de détourage et bordage intégrés, expliquant chaque module, les technologies employées, les séquences de traitement, les paramètres ajustables, l’optimisation du flux et comment chaque opération contribue à la qualité, à la cadence et à la standardisation des lignes de production modernes.
Machines professionnelles pour finition de tôles
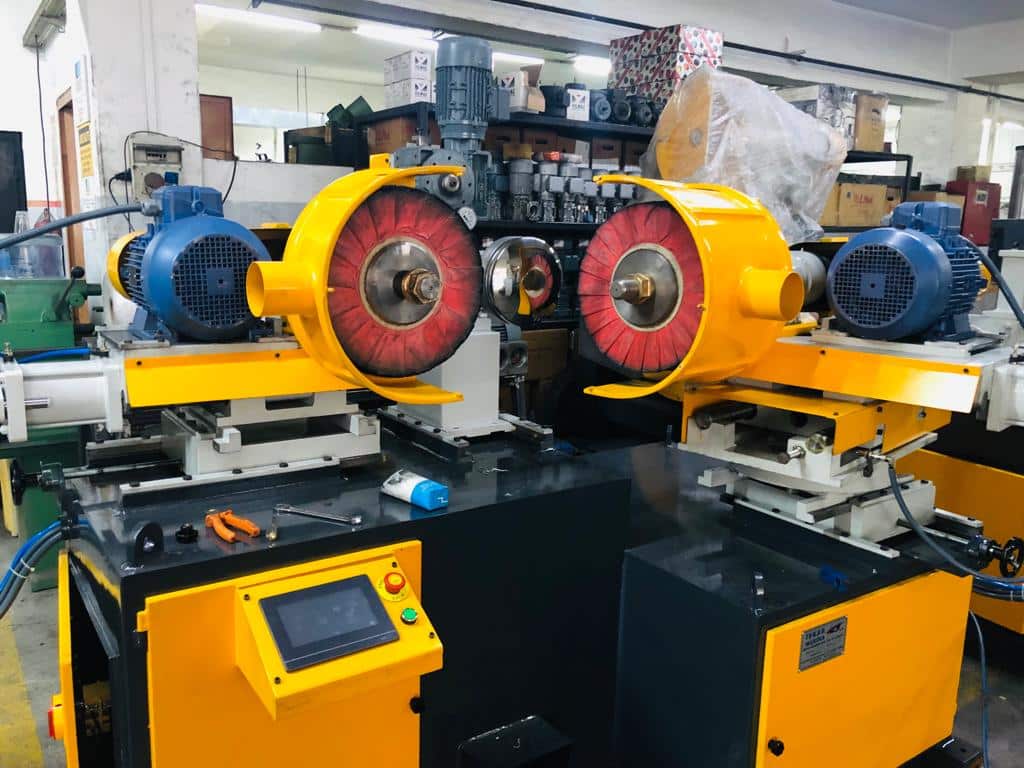
Les machines professionnelles pour finition de tôles représentent un élément essentiel dans les ateliers industriels spécialisés dans la transformation des métaux, car elles permettent de traiter les pièces métalliques après emboutissage, découpe ou formage afin de leur conférer une qualité de surface optimale, des arêtes sûres et des dimensions parfaitement conformes aux spécifications. Ces machines sont conçues pour réaliser une large gamme d’opérations telles que le ponçage, le polissage, l’ébavurage, le lissage, le calibrage et parfois le pré-traitement pour le revêtement ou l’assemblage. Contrairement aux solutions artisanales ou semi-manuelles, les machines professionnelles intègrent des systèmes automatisés et des commandes numériques qui garantissent uniformité, répétabilité et cadence élevée, permettant ainsi de standardiser la qualité des pièces sur des séries de production importantes.
Le fonctionnement de ces machines repose sur une combinaison de technologies mécaniques et électromécaniques sophistiquées, incluant des rouleaux abrasifs, des brosses rotatives, des meules, des bandes de ponçage, des dispositifs de lissage et des systèmes de calibrage. Dès l’entrée de la pièce dans la machine, celle-ci est maintenue fermement par des dispositifs de serrage ou des galets de positionnement, assurant une stabilité maximale pendant les opérations de finition. Les outils abrasifs et polisseurs suivent avec précision le profil de la pièce, permettant de traiter même des contours complexes et des surfaces irrégulières tout en éliminant les bavures, en arrondissant les arêtes vives et en obtenant une surface uniforme. Certaines machines sont équipées de plusieurs stations intégrées, de manière à combiner plusieurs opérations dans un même cycle, par exemple le ponçage grossier suivi du ponçage fin puis du polissage, permettant d’obtenir en sortie une pièce immédiatement prête pour les étapes suivantes.
Ces équipements sont généralement contrôlés par des systèmes numériques avancés et des capteurs sophistiqués qui régulent la vitesse des outils, la pression appliquée, l’angle de contact et la position des pièces. Cette automatisation permet d’adapter les paramètres en temps réel selon l’épaisseur, le type de matériau ou la complexité du profil de la tôle, garantissant ainsi une finition constante et homogène sur l’ensemble des pièces produites. Les modèles les plus perfectionnés incluent des dispositifs de contrôle en ligne capables de détecter les défauts de surface, les irrégularités ou les bavures résiduelles, et d’appliquer automatiquement les corrections nécessaires, soit en ajustant les outils, soit en écartant les pièces non conformes. La synchronisation avec des convoyeurs et des systèmes de manutention automatisés permet de maintenir un flux continu et homogène, optimisant la productivité et réduisant les temps morts ou les interventions manuelles.
L’un des avantages majeurs de ces machines professionnelles est leur capacité à combiner rapidité, précision et flexibilité. Elles peuvent traiter différents types et épaisseurs de tôles, de l’acier inoxydable à l’aluminium, en adaptant automatiquement la vitesse, la pression et l’outillage. Les outils sont conçus pour résister à l’usure et aux contraintes mécaniques élevées, tandis que les systèmes de lubrification et de refroidissement garantissent une constance de performance et prolongent la durée de vie des composants, permettant d’obtenir une qualité de surface constante même sur des séries très importantes.
En pratique, les pièces qui sortent de ces machines présentent des surfaces uniformes, des arêtes arrondies et des dimensions calibrées, prêtes à être utilisées dans des chaînes d’assemblage, des applications de revêtement ou des produits finis. Les machines professionnelles pour finition de tôles permettent de standardiser la production, d’augmenter la cadence tout en maintenant la qualité et de réduire les interventions manuelles et les risques d’erreurs, rendant possible la fabrication industrielle de pièces métalliques esthétiques, sûres et conformes aux normes.
En résumé, ces machines représentent un investissement stratégique pour tout atelier ou ligne de production de pièces métalliques embouties ou découpées, offrant précision, répétabilité, cadence élevée et homogénéité de finition. Leur intégration dans la chaîne de production permet d’optimiser le flux, de réduire les manipulations et de garantir que chaque pièce respecte les standards de qualité les plus exigeants, qu’il s’agisse d’ustensiles de cuisine, de composants industriels ou d’éléments structurels métalliques.
Les machines professionnelles pour finition de tôles constituent un pilier central dans l’optimisation des ateliers industriels de transformation métallique, en particulier dans la production d’ustensiles de cuisine, de composants industriels ou de pièces techniques nécessitant une précision et une qualité de surface irréprochables. Ces machines sont conçues pour exécuter l’ensemble des opérations de finition après emboutissage, découpe ou formage, englobant le ponçage, le polissage, l’ébavurage, le lissage, le calibrage dimensionnel, le perlage ou le roulage des bords, et parfois même le prétraitement en vue d’un revêtement ou d’un assemblage. L’objectif principal est de fournir des pièces uniformes, sécurisées et prêtes à passer aux étapes suivantes de la production, tout en garantissant un flux de travail continu et homogène, minimisant ainsi les interventions manuelles, les temps morts et les risques d’erreurs. Contrairement aux méthodes artisanales ou semi-manuelles, ces machines permettent d’obtenir une standardisation complète et une cadence élevée, même sur de grandes séries de production, grâce à des systèmes automatisés et à des commandes numériques avancées qui contrôlent et régulent chaque paramètre du processus.
Le principe de fonctionnement repose sur l’intégration de technologies mécaniques, électromécaniques et numériques sophistiquées. Les tôles ou pièces embouties sont introduites automatiquement dans la machine via des convoyeurs, des robots ou des systèmes de manutention spécialisés, puis maintenues fermement par des dispositifs de serrage, galets ou pinces qui assurent leur positionnement exact pendant toutes les étapes de finition. Les outils abrasifs et polisseurs, comprenant des bandes de ponçage, des rouleaux abrasifs, des brosses rotatives, des meules et des dispositifs de lissage, suivent avec précision le profil de la pièce, permettant de traiter des contours complexes et des surfaces irrégulières tout en éliminant les bavures, en arrondissant les arêtes vives et en obtenant une finition uniforme et régulière. Dans les machines multi-stations, plusieurs opérations peuvent être combinées dans un même cycle, par exemple un ponçage grossier suivi d’un ponçage fin puis d’un polissage ou d’un lissage, permettant d’obtenir en sortie une pièce prête pour l’assemblage ou le revêtement, réduisant ainsi le besoin de manipulations supplémentaires.
Ces équipements professionnels sont généralement équipés de systèmes de contrôle numérique et de capteurs sophistiqués qui régulent en continu la vitesse des outils, la pression appliquée, l’angle de contact et la position exacte des pièces. Cette régulation dynamique permet d’adapter automatiquement les paramètres aux variations d’épaisseur, au type de matériau, à la dureté et à la complexité des profils, garantissant ainsi une finition constante, homogène et reproductible sur l’ensemble des pièces produites. Les modèles les plus avancés intègrent des dispositifs de contrôle en ligne capables de détecter les défauts de surface, les irrégularités ou les bavures résiduelles et de corriger automatiquement les paramètres des outils ou d’écarter les pièces non conformes, assurant ainsi une qualité irréprochable sur l’ensemble de la production. La synchronisation avec les systèmes de convoyage et de manutention automatisés permet de maintenir un flux continu et homogène, optimisant la productivité et la cadence tout en réduisant les temps morts et les interventions manuelles.
L’un des atouts majeurs de ces machines professionnelles est leur capacité à allier vitesse, précision et flexibilité. Elles peuvent traiter différents types et épaisseurs de tôles, qu’il s’agisse d’acier inoxydable, d’aluminium ou d’alliages spécifiques, en ajustant automatiquement la vitesse, la pression et le choix de l’outillage selon la pièce et l’opération à réaliser. Les outils sont conçus pour résister à une usure importante et aux contraintes mécaniques élevées, tandis que des systèmes de lubrification et de refroidissement garantissent une performance constante et prolongent la durée de vie des composants, assurant que la qualité de finition reste homogène, même sur de grandes séries de production. L’automatisation complète et la précision des réglages permettent de minimiser les variations entre les pièces, ce qui est particulièrement crucial dans les industries où les tolérances dimensionnelles et la qualité de surface doivent répondre à des standards stricts.
En sortie de machine, chaque pièce présente des arêtes arrondies, une surface uniforme et des dimensions parfaitement calibrées, prête à être intégrée dans les lignes d’assemblage, à recevoir un revêtement antiadhésif ou décoratif, ou à passer au polissage final. Les poêles, casseroles, couvercles et autres pièces bénéficient ainsi d’un détourage net, d’un ébavurage complet, d’un profil exact et d’une finition homogène, assurant sécurité, esthétisme et conformité aux normes industrielles. Ces machines permettent non seulement d’augmenter la cadence de production et de réduire les manipulations, mais elles garantissent également une standardisation complète, essentielle pour la production industrielle moderne à haut rendement.
En résumé, les machines professionnelles pour finition de tôles sont des équipements stratégiques pour tout atelier ou ligne de production industrielle. Elles offrent un contrôle total sur le détourage, l’ébavurage, le calibrage, le lissage et le polissage des pièces, permettant d’atteindre une qualité constante, une répétabilité élevée, une cadence rapide et une production homogène sur de grandes séries. Leur intégration optimise le flux de production, réduit les manipulations et les temps morts, et assure que chaque pièce répond aux exigences les plus strictes de l’industrie, qu’il s’agisse d’ustensiles de cuisine, de composants techniques ou d’éléments métalliques complexes.
Je peux maintenant rédiger un dossier complet ultra-détaillé sur toutes les machines professionnelles pour finition de tôles, expliquant pour chaque type de machine sa fonction précise, les outils utilisés, les séquences de traitement, les technologies intégrées, et comment elles s’insèrent dans une ligne de production automatisée à haute cadence pour maximiser qualité, standardisation et productivité.
Les machines professionnelles pour finition de tôles représentent aujourd’hui l’un des éléments les plus critiques dans les ateliers industriels de transformation du métal, en particulier dans les secteurs de la fabrication d’ustensiles de cuisine, de composants industriels, d’équipements électroménagers et de pièces techniques nécessitant à la fois une précision dimensionnelle élevée et une qualité de surface irréprochable. Ces machines sont conçues pour exécuter l’ensemble des opérations de finition après emboutissage, découpe, estampage ou formage, englobant des procédés tels que le ponçage, le polissage, l’ébavurage, le lissage, le calibrage, le perlage ou le roulage des bords, et parfois même le prétraitement pour des revêtements ultérieurs. L’objectif principal est de transformer les pièces métalliques brutes ou semi-finies en composants prêts à être intégrés dans les chaînes d’assemblage ou à subir des traitements complémentaires, tout en garantissant un flux de production continu, homogène et efficace, réduisant au minimum les interventions manuelles et les risques d’erreurs. La standardisation et la répétabilité des opérations offertes par ces machines permettent de répondre aux exigences de la production industrielle moderne, qui impose des cadences élevées tout en maintenant une qualité constante sur de grandes séries de pièces.
Le fonctionnement de ces machines repose sur l’intégration de technologies mécaniques, électromécaniques et numériques sophistiquées. Les pièces métalliques sont acheminées automatiquement par des convoyeurs, des robots ou des systèmes de manutention spécialisés, puis positionnées et maintenues par des dispositifs de serrage ou de galets, assurant une stabilité maximale et un alignement précis tout au long des opérations. Les outils de finition, comprenant des bandes abrasives, des rouleaux, des brosses rotatives, des meules, des dispositifs de lissage et des calibrateurs, suivent avec précision le profil de chaque pièce, permettant de traiter des contours complexes, des surfaces irrégulières et des zones difficiles d’accès tout en éliminant les bavures, en arrondissant les arêtes vives et en obtenant une surface uniforme et régulière. Les machines multi-stations sont capables de combiner plusieurs opérations dans un même cycle, par exemple un ponçage grossier suivi d’un ponçage fin et d’un polissage ou lissage, ce qui permet de produire des pièces directement prêtes pour le polissage final, l’assemblage ou le revêtement, réduisant ainsi les manipulations et le temps de traitement global.
Les équipements modernes sont généralement équipés de systèmes de contrôle numérique et de capteurs sophistiqués qui régulent en temps réel la vitesse des outils, la pression appliquée, l’angle de contact et la position des pièces. Ces régulations dynamiques permettent d’adapter automatiquement les paramètres de traitement selon l’épaisseur, le matériau, la dureté et la complexité du profil de la tôle, garantissant ainsi une finition constante et homogène sur l’ensemble des pièces produites. Les modèles les plus perfectionnés intègrent des dispositifs de mesure et de correction automatique capables de détecter toute irrégularité, défaut de surface ou variation dimensionnelle, et d’ajuster instantanément les outils ou d’écarter les pièces non conformes, assurant ainsi une qualité irréprochable et la conformité aux standards industriels. La synchronisation avec les convoyeurs et les systèmes automatisés de manutention permet de maintenir un flux continu et homogène, minimisant les temps morts et maximisant l’efficacité de la ligne de production.
L’un des principaux avantages de ces machines professionnelles réside dans leur capacité à allier rapidité, précision et flexibilité. Elles peuvent traiter différents types et épaisseurs de tôles, allant de l’acier inoxydable à l’aluminium ou aux alliages spécifiques, en ajustant automatiquement la vitesse, la pression et le choix de l’outillage en fonction des caractéristiques de chaque pièce et des opérations à réaliser. Les outils sont conçus pour résister à l’usure et aux contraintes mécaniques élevées, tandis que des systèmes de lubrification et de refroidissement assurent une performance stable et prolongent la durée de vie des composants, permettant de maintenir une qualité homogène même sur des séries très importantes. L’automatisation et la précision des réglages permettent de minimiser les variations entre les pièces, ce qui est crucial lorsque les tolérances dimensionnelles et la qualité de surface doivent répondre à des standards stricts.
En sortie de machine, chaque pièce présente des arêtes arrondies, une surface parfaitement lisse et uniforme, et des dimensions calibrées avec précision, prête à être intégrée dans les chaînes d’assemblage, à recevoir un revêtement ou à subir un polissage final. Les poêles, casseroles, couvercles et autres composants bénéficient ainsi d’un détourage net, d’un ébavurage complet, d’un profil exact et d’une finition homogène, garantissant sécurité, esthétisme et conformité aux normes industrielles. Ces machines permettent non seulement d’augmenter la cadence de production et de réduire les manipulations manuelles, mais elles assurent également une standardisation complète, indispensable pour les lignes de production à haut rendement et pour répondre aux exigences de qualité industrielle les plus strictes.
En résumé, les machines professionnelles pour finition de tôles constituent un investissement stratégique pour tout atelier ou ligne de production industrielle, offrant un contrôle total sur le détourage, l’ébavurage, le calibrage, le lissage et le polissage des pièces. Elles permettent d’atteindre une qualité constante, une répétabilité élevée, une cadence rapide et une production homogène sur de grandes séries. Leur intégration dans les lignes de production optimise le flux de travail, réduit les manipulations et les temps morts et assure que chaque pièce respecte les exigences les plus strictes de l’industrie, qu’il s’agisse d’ustensiles de cuisine, de composants techniques ou d’éléments métalliques complexes.
Les machines professionnelles pour finition de tôles représentent aujourd’hui l’élément central des ateliers industriels spécialisés dans la transformation des métaux, en particulier dans la production d’ustensiles de cuisine, de composants industriels, d’appareils électroménagers et de pièces techniques nécessitant à la fois précision dimensionnelle et qualité de surface irréprochable. Ces machines sont conçues pour exécuter l’ensemble des opérations de finition après emboutissage, découpe, estampage ou formage, englobant des procédés tels que le ponçage, le polissage, l’ébavurage, le lissage, le calibrage dimensionnel, le perlage ou le roulage des bords et parfois même le prétraitement pour des revêtements ultérieurs. L’objectif est de transformer des pièces métalliques brutes ou semi-finies en composants prêts à être intégrés dans des chaînes d’assemblage ou à subir des traitements complémentaires, tout en garantissant un flux de production continu, homogène et efficace, réduisant au minimum les interventions manuelles et les risques d’erreurs. Contrairement aux procédés artisanaux ou semi-manuels, ces machines permettent une standardisation complète et une cadence élevée, même sur des séries de production très importantes, grâce à des systèmes automatisés et à des commandes numériques avancées qui contrôlent et régulent chaque paramètre du processus pour assurer uniformité et répétabilité.
Le fonctionnement repose sur l’intégration de technologies mécaniques, électromécaniques et numériques de pointe. Les tôles ou pièces embouties sont acheminées automatiquement par convoyeurs, robots ou systèmes de manutention spécialisés, puis positionnées et maintenues par des dispositifs de serrage ou de galets qui assurent un alignement précis et une stabilité maximale pendant toutes les opérations. Les outils de finition, comprenant des bandes abrasives, des rouleaux abrasifs, des brosses rotatives, des meules, des dispositifs de lissage et des calibrateurs, suivent le profil exact de chaque pièce, permettant de traiter des contours complexes, des surfaces irrégulières et des zones difficiles d’accès tout en éliminant les bavures, en arrondissant les arêtes vives et en obtenant une surface parfaitement uniforme et régulière. Les machines multi-stations permettent de combiner plusieurs opérations dans un même cycle, par exemple un ponçage grossier suivi d’un ponçage fin, puis d’un polissage ou d’un lissage, ce qui permet de produire des pièces directement prêtes pour l’assemblage, le polissage final ou le revêtement, réduisant les manipulations et le temps global de traitement.
Ces équipements professionnels sont équipés de systèmes de contrôle numérique et de capteurs sophistiqués qui régulent en temps réel la vitesse des outils, la pression appliquée, l’angle de contact et la position exacte des pièces. Cette régulation dynamique permet d’adapter automatiquement les paramètres en fonction de l’épaisseur, du type de matériau, de la dureté et de la complexité des profils, garantissant ainsi une finition constante et homogène sur l’ensemble des pièces produites. Les modèles les plus avancés intègrent des dispositifs de contrôle en ligne capables de détecter les défauts de surface, les irrégularités ou les bavures résiduelles et d’ajuster automatiquement les paramètres ou d’écarter les pièces non conformes, assurant ainsi une qualité irréprochable et la conformité aux standards industriels les plus stricts. La synchronisation avec les systèmes de convoyage et de manutention automatisés permet de maintenir un flux continu et homogène, minimisant les temps morts, maximisant l’efficacité et réduisant les interventions manuelles sur la ligne de production.
L’un des avantages majeurs de ces machines professionnelles est leur capacité à allier rapidité, précision et flexibilité. Elles peuvent traiter différents types et épaisseurs de tôles, allant de l’acier inoxydable à l’aluminium ou à des alliages spécifiques, en adaptant automatiquement la vitesse, la pression et le choix de l’outillage selon les caractéristiques de chaque pièce et de l’opération à réaliser. Les outils sont conçus pour résister à une usure importante et aux contraintes mécaniques élevées, tandis que des systèmes de lubrification et de refroidissement garantissent une performance stable et prolongent la durée de vie des composants, permettant de maintenir une qualité homogène même sur des séries très importantes. L’automatisation complète et la précision des réglages minimisent les variations entre les pièces, ce qui est essentiel lorsque les tolérances dimensionnelles et la qualité de surface doivent répondre à des standards industriels très stricts.
En sortie de machine, chaque pièce présente des arêtes arrondies, une surface uniforme et lisse, et des dimensions calibrées avec précision, prête à être intégrée dans les chaînes d’assemblage, à recevoir un revêtement ou à subir un polissage final. Les poêles, casseroles, couvercles et autres composants bénéficient d’un détourage net, d’un ébavurage complet, d’un profil exact et d’une finition homogène, garantissant sécurité, esthétisme et conformité aux normes industrielles. Ces machines permettent non seulement d’augmenter la cadence de production et de réduire les manipulations manuelles, mais elles assurent également une standardisation complète, indispensable pour les lignes de production à haut rendement et pour répondre aux exigences de qualité industrielle les plus strictes.
En résumé, les machines professionnelles pour finition de tôles constituent un investissement stratégique pour tout atelier ou ligne de production industrielle. Elles offrent un contrôle total sur le détourage, l’ébavurage, le calibrage, le lissage et le polissage des pièces, permettant d’atteindre une qualité constante, une répétabilité élevée, une cadence rapide et une production homogène sur de grandes séries. Leur intégration dans les lignes de production optimise le flux de travail, réduit les manipulations et les temps morts et assure que chaque pièce respecte les exigences les plus strictes de l’industrie, qu’il s’agisse d’ustensiles de cuisine, de composants techniques ou d’éléments métalliques complexes.
Je peux maintenant créer un manuel complet et détaillé des machines professionnelles pour finition de tôles, expliquant pour chaque type de machine ses opérations exactes, les outils utilisés, les séquences de traitement, les technologies intégrées et leur rôle dans l’optimisation de la cadence, de la qualité et de la standardisation des lignes de production modernes.
Équipements de finition pour pièces circulaires
Les équipements de finition pour pièces circulaires constituent une catégorie spécialisée de machines industrielles conçues pour traiter les composants métalliques de forme ronde ou cylindrique, tels que les fonds de casseroles, les couvercles, les poêles, les plateaux, ainsi que les disques et anneaux utilisés dans des applications industrielles ou domestiques. Ces équipements sont développés pour réaliser l’ensemble des opérations de finition nécessaires après emboutissage, découpe ou estampage, incluant l’ébavurage, le polissage, le lissage, le calibrage dimensionnel, le perlage ou le roulage des bords et, selon les modèles, le pré-polissage ou le traitement des surfaces avant revêtement ou assemblage. L’objectif est de produire des pièces circulaires parfaitement uniformes, sécurisées et esthétiquement finies, prêtes à entrer dans les chaînes de production suivantes, tout en optimisant le flux de travail et en minimisant les manipulations manuelles et les risques d’erreurs. Ces machines assurent une standardisation complète et permettent d’obtenir des cadences élevées même sur de grandes séries de production, grâce à l’automatisation et à la précision des réglages numériques.
Le fonctionnement de ces équipements repose sur des technologies mécaniques, électromécaniques et numériques sophistiquées, intégrées pour garantir un traitement homogène et précis des pièces circulaires. Les pièces sont acheminées automatiquement via convoyeurs, robots ou systèmes de manutention et positionnées de manière exacte grâce à des dispositifs de serrage adaptés à leur forme circulaire. Les outils de finition, comprenant des disques abrasifs, des brosses rotatives, des meules, des rouleaux calibrés et des dispositifs de lissage circulaires, suivent le contour de chaque pièce avec une grande précision, permettant de supprimer les bavures, d’arrondir les arêtes vives, de lisser la surface et de calibrer les dimensions selon les tolérances strictes imposées par l’industrie. Certains modèles combinent plusieurs opérations dans un même cycle, par exemple l’ébavurage suivi du polissage et du perlage des bords, de manière à obtenir des pièces circulaires directement prêtes pour le revêtement, l’assemblage ou le polissage final, réduisant ainsi le temps de traitement global et les interventions manuelles.
Ces équipements sont équipés de systèmes de contrôle numérique et de capteurs sophistiqués qui régulent en temps réel la vitesse des outils, la pression appliquée, l’angle de contact et la position des pièces circulaires. Cette régulation dynamique permet d’adapter automatiquement les paramètres selon l’épaisseur, le type de matériau, la dureté et la complexité du contour circulaire, garantissant une finition homogène et répétable sur toutes les pièces produites. Les modèles avancés intègrent des dispositifs de mesure et de correction automatiques capables de détecter les défauts de surface ou les irrégularités et d’ajuster instantanément les outils ou d’écarter les pièces non conformes, garantissant ainsi une qualité optimale et une conformité aux standards industriels. La synchronisation avec les convoyeurs et la manutention automatisée permet de maintenir un flux continu et homogène, maximisant l’efficacité de la ligne de production tout en minimisant les temps morts et les interventions manuelles.
L’un des principaux avantages des équipements de finition pour pièces circulaires est leur capacité à traiter rapidement et précisément des pièces de différentes tailles et matériaux, qu’il s’agisse d’acier inoxydable, d’aluminium ou d’alliages spécifiques. Les outils sont conçus pour résister à l’usure et aux contraintes mécaniques élevées, tandis que des systèmes de lubrification et de refroidissement assurent la constance de performance et prolongent la durée de vie des composants, permettant d’obtenir une qualité uniforme même sur de grandes séries. La flexibilité de ces machines permet d’adapter automatiquement les paramètres de traitement pour différentes pièces circulaires sans interrompre la ligne de production, garantissant répétabilité et standardisation.
En sortie de machine, chaque pièce circulaire présente des arêtes arrondies, une surface parfaitement lisse et uniforme, et des dimensions calibrées avec précision, prête à être intégrée dans des chaînes d’assemblage, à recevoir un revêtement ou à subir un polissage final. Les fonds, couvercles, plateaux et autres composants circulaires bénéficient ainsi d’un détourage net, d’un ébavurage complet, d’un profil exact et d’une finition homogène, assurant sécurité, esthétisme et conformité aux normes industrielles. Ces équipements permettent non seulement d’augmenter la cadence de production et de réduire les manipulations manuelles, mais également de standardiser entièrement la production sur de grandes séries, répondant aux exigences de qualité industrielle les plus strictes.
En résumé, les équipements de finition pour pièces circulaires sont des machines stratégiques pour tout atelier ou ligne de production industrielle nécessitant des pièces rondes parfaitement finies. Ils combinent ébavurage, polissage, lissage, calibrage et perlage ou roulage des bords dans un flux automatisé continu, offrant précision, répétabilité, flexibilité et cadence élevée. Leur intégration permet de transformer efficacement des pièces circulaires brutes ou semi-finies en composants prêts pour le polissage final, le revêtement ou l’assemblage, tout en optimisant le flux de production, en réduisant les manipulations et en garantissant une qualité constante sur l’ensemble des séries.
Les équipements de finition pour pièces circulaires constituent une catégorie avancée et hautement spécialisée de machines industrielles, conçues pour assurer le traitement optimal des composants métalliques de forme ronde ou cylindrique, tels que les fonds de casseroles, couvercles, poêles, plateaux, disques techniques et anneaux utilisés dans l’industrie alimentaire, électroménagère, automobile ou mécanique de précision. Ces équipements interviennent après les étapes de découpe, d’emboutissage, de formage ou d’estampage et regroupent un ensemble complet d’opérations de finition essentielles pour garantir que chaque pièce présente une qualité de surface parfaite, des contours sûrs et des dimensions strictement conformes aux spécifications industrielles. Les opérations effectuées comprennent l’ébavurage, le ponçage, le polissage, le lissage, le calibrage dimensionnel, le perlage ou le roulage des bords et, dans certains modèles sophistiqués, le pré-polissage ou le traitement des surfaces avant application de revêtements ou assemblage, permettant aux pièces de sortir directement prêtes pour les étapes suivantes. Ces machines sont conçues pour optimiser le flux de production, réduire les manipulations manuelles, minimiser les temps morts et garantir une répétabilité totale, ce qui est essentiel dans les lignes de production à haute cadence et pour les séries de grande volume.
Le fonctionnement de ces équipements repose sur l’intégration de technologies mécaniques, électromécaniques et numériques très avancées. Les pièces circulaires sont automatiquement acheminées par des convoyeurs, des robots ou des systèmes de manutention spécialisés, puis positionnées et maintenues avec précision par des dispositifs de serrage adaptés à leur forme, garantissant stabilité et alignement parfait pendant toutes les opérations de finition. Les outils de traitement incluent des disques abrasifs, des bandes abrasives circulaires, des brosses rotatives, des meules et des dispositifs de lissage calibrés qui suivent fidèlement le contour des pièces. Ces outils permettent de supprimer les bavures, d’arrondir les arêtes vives, de lisser les surfaces et de calibrer les dimensions avec une précision micrométrique, même sur des profils complexes ou des zones difficilement accessibles. Les machines multi-stations peuvent combiner plusieurs opérations dans un seul cycle, par exemple un ébavurage suivi d’un ponçage fin, d’un polissage et d’un perlage des bords, ce qui permet de produire des pièces circulaires immédiatement prêtes pour le polissage final, le revêtement ou l’assemblage, réduisant ainsi considérablement le temps de traitement global et le besoin de manipulations supplémentaires.
Ces équipements sont équipés de systèmes de contrôle numérique et de capteurs sophistiqués qui surveillent en continu la vitesse des outils, la pression appliquée, l’angle de contact et la position des pièces. Ces régulations dynamiques permettent d’ajuster automatiquement les paramètres de traitement en fonction de l’épaisseur, du matériau, de la dureté et de la complexité du profil circulaire, garantissant une finition homogène, uniforme et répétable sur toutes les pièces produites. Les modèles les plus avancés intègrent des dispositifs de mesure et de correction automatiques capables de détecter les défauts de surface, les irrégularités ou les bavures résiduelles et d’ajuster instantanément les outils ou d’écarter les pièces non conformes, assurant ainsi une qualité irréprochable et la conformité aux standards industriels les plus stricts. La synchronisation avec les systèmes de convoyage et de manutention automatisés permet de maintenir un flux continu et homogène, maximisant l’efficacité de la ligne de production tout en minimisant les temps morts et les interventions manuelles.
Un avantage déterminant de ces équipements de finition est leur capacité à allier rapidité, précision et flexibilité. Ils peuvent traiter des pièces circulaires de différents diamètres et matériaux, allant de l’acier inoxydable à l’aluminium ou à divers alliages, en ajustant automatiquement la vitesse, la pression et la configuration des outils selon les caractéristiques spécifiques de chaque pièce. Les outils sont conçus pour résister à une usure intense et aux contraintes mécaniques élevées, tandis que des systèmes de lubrification et de refroidissement garantissent une performance constante et prolongent la durée de vie des composants, permettant ainsi de maintenir une qualité uniforme sur de grandes séries. Cette flexibilité permet de changer rapidement de type ou de taille de pièce sans interrompre la production, assurant ainsi répétabilité, standardisation et optimisation de la cadence.
À la sortie de machine, chaque pièce circulaire présente des arêtes parfaitement arrondies, une surface lisse et uniforme, et des dimensions calibrées avec précision, prête à être intégrée dans les lignes d’assemblage, à recevoir un revêtement ou à subir un polissage final. Les fonds de casseroles, couvercles, plateaux et autres composants circulaires bénéficient d’un détourage net, d’un ébavurage complet, d’un profil exact et d’une finition homogène, garantissant sécurité, esthétique et conformité aux normes industrielles. Ces équipements permettent non seulement d’augmenter la cadence de production et de réduire les interventions manuelles, mais également de standardiser entièrement la production sur de grandes séries, ce qui est crucial pour répondre aux exigences de qualité industrielle les plus strictes.
En résumé, les équipements de finition pour pièces circulaires constituent un investissement stratégique pour les ateliers et lignes de production industrielle. Ils offrent un contrôle total sur l’ébavurage, le ponçage, le polissage, le lissage, le calibrage et le perlage ou roulage des bords des pièces circulaires, garantissant qualité constante, répétabilité élevée, cadence rapide et production homogène sur de grandes séries. Leur intégration dans les lignes de production permet de transformer efficacement des pièces circulaires brutes ou semi-finies en composants prêts pour le polissage final, le revêtement ou l’assemblage, tout en optimisant le flux, réduisant les manipulations et garantissant une qualité constante sur l’ensemble des séries.
Je peux maintenant continuer en créant un manuel détaillé et exhaustif sur tous les équipements de finition pour pièces circulaires, incluant chaque type de machine, les opérations exactes qu’elle réalise, les outils utilisés, les séquences de traitement, les technologies intégrées et leur rôle précis dans l’optimisation de la cadence, de la qualité et de la standardisation des lignes de production modernes.
Les équipements de finition pour pièces circulaires représentent aujourd’hui un segment stratégique de la production industrielle, particulièrement dans la fabrication d’ustensiles de cuisine, de composants électromécaniques et d’éléments techniques nécessitant une précision extrême et une qualité de surface optimale. Ces machines interviennent après l’emboutissage, la découpe ou le formage des pièces et regroupent l’ensemble des opérations de finition indispensables pour garantir que chaque pièce circulaire réponde aux critères les plus stricts de l’industrie en termes de dimensions, de sécurité et d’esthétique. Elles réalisent des fonctions variées telles que l’ébavurage, le polissage, le lissage, le calibrage, le perlage ou le roulage des bords, ainsi que, selon les modèles les plus sophistiqués, le pré-polissage ou le traitement des surfaces avant application de revêtements ou d’assemblage. L’objectif est de transformer des pièces brutes ou semi-finies en composants parfaitement finis, prêts à être intégrés dans la chaîne de production ou à subir des traitements complémentaires, tout en assurant un flux continu et homogène, minimisant les manipulations manuelles et réduisant les risques d’erreurs. Ces équipements permettent ainsi d’atteindre un niveau de standardisation et de répétabilité difficilement réalisable avec des procédés manuels ou semi-automatisés, tout en garantissant une cadence élevée sur de grandes séries de production.
Le fonctionnement de ces machines repose sur la combinaison de technologies mécaniques, électromécaniques et numériques avancées, intégrées pour traiter avec précision des pièces circulaires de toutes tailles et matériaux. Les composants sont acheminés automatiquement via convoyeurs, robots ou systèmes de manutention spécialisés, puis maintenus et positionnés par des dispositifs de serrage adaptés à leur forme ronde, garantissant un alignement parfait et une stabilité maximale pendant le processus de finition. Les outils employés incluent des disques abrasifs, des bandes abrasives circulaires, des brosses rotatives, des meules calibrées et des dispositifs de lissage qui suivent fidèlement le contour des pièces, permettant de supprimer les bavures, d’arrondir les arêtes vives, de lisser les surfaces et de calibrer les dimensions avec une précision micrométrique. Dans les machines multi-stations, plusieurs opérations peuvent être combinées dans un même cycle : par exemple, un ébavurage suivi d’un ponçage fin, d’un polissage et d’un perlage des bords, permettant d’obtenir des pièces circulaires directement prêtes pour le polissage final, le revêtement ou l’assemblage, réduisant ainsi le temps de traitement global et les manipulations supplémentaires.
Ces équipements intègrent des systèmes de contrôle numérique et des capteurs sophistiqués capables de surveiller en continu la vitesse des outils, la pression appliquée, l’angle de contact et la position exacte des pièces. Cette régulation dynamique permet d’adapter automatiquement les paramètres de traitement selon l’épaisseur, le type de matériau, la dureté et la complexité du contour circulaire, garantissant une finition homogène, répétable et conforme aux exigences industrielles. Les modèles avancés incluent des dispositifs de mesure et de correction automatiques capables de détecter les irrégularités, les défauts de surface ou les bavures résiduelles et d’ajuster instantanément les outils ou d’écarter les pièces non conformes, assurant ainsi une qualité optimale et une conformité aux standards les plus stricts. La synchronisation avec les convoyeurs et la manutention automatisée permet de maintenir un flux continu et homogène, maximisant l’efficacité de la ligne de production tout en minimisant les temps morts et les interventions manuelles.
L’un des avantages principaux de ces équipements réside dans leur capacité à combiner rapidité, précision et flexibilité. Ils sont capables de traiter des pièces circulaires de différents diamètres et matériaux, allant de l’acier inoxydable à l’aluminium ou à des alliages spécifiques, en ajustant automatiquement la vitesse, la pression et la configuration des outils selon les caractéristiques de chaque pièce. Les outils sont conçus pour résister à l’usure et aux contraintes mécaniques élevées, tandis que des systèmes de lubrification et de refroidissement assurent une performance constante et prolongent la durée de vie des composants, garantissant ainsi une qualité homogène sur de grandes séries. La flexibilité de ces machines permet de changer rapidement de type ou de taille de pièce sans interrompre la production, ce qui assure répétabilité, standardisation et cadence élevée.
En sortie de machine, chaque pièce circulaire présente des arêtes parfaitement arrondies, une surface lisse et uniforme et des dimensions calibrées avec précision, prête à être intégrée dans les lignes d’assemblage, à recevoir un revêtement ou à subir un polissage final. Les fonds, couvercles, plateaux et autres composants circulaires bénéficient ainsi d’un détourage net, d’un ébavurage complet, d’un profil exact et d’une finition homogène, garantissant sécurité, esthétisme et conformité aux normes industrielles. Ces machines permettent non seulement d’augmenter la cadence de production et de réduire les interventions manuelles, mais également de standardiser entièrement la production sur de grandes séries, répondant aux exigences de qualité industrielle les plus strictes.
En résumé, les équipements de finition pour pièces circulaires constituent un investissement stratégique et indispensable pour tout atelier ou ligne de production industrielle. Ils offrent un contrôle total sur l’ébavurage, le ponçage, le polissage, le lissage, le calibrage et le perlage ou roulage des bords, garantissant qualité constante, répétabilité élevée, cadence rapide et production homogène sur de grandes séries. Leur intégration dans les lignes de production permet de transformer efficacement des pièces circulaires brutes ou semi-finies en composants prêts pour le polissage final, le revêtement ou l’assemblage, tout en optimisant le flux, réduisant les manipulations et garantissant une qualité constante sur l’ensemble des séries.
Je peux maintenant continuer en élaborant un manuel exhaustif et ultra-détaillé sur tous les équipements de finition pour pièces circulaires, en détaillant pour chaque machine son rôle exact, les opérations qu’elle réalise, les outils utilisés, les séquences de traitement et leur contribution à l’optimisation de la cadence, de la qualité et de la standardisation des lignes de production modernes.
Les équipements de finition pour pièces circulaires représentent aujourd’hui l’un des segments les plus avancés et stratégiques de l’industrie métallurgique et manufacturière, en particulier pour la production d’ustensiles de cuisine, de composants électromécaniques, de pièces techniques et d’éléments décoratifs nécessitant une précision dimensionnelle extrême, une surface parfaitement uniforme et des arêtes sécurisées. Ces machines interviennent après les opérations de découpe, d’emboutissage, de formage ou d’estampage et regroupent un ensemble complet de procédés de finition qui permettent de transformer des pièces brutes ou semi-finies en composants prêts à l’assemblage, au revêtement ou au polissage final. Les opérations effectuées incluent l’ébavurage, le ponçage, le polissage, le lissage, le calibrage dimensionnel, le perlage ou le roulage des bords, et, selon les modèles les plus sophistiqués, le pré-polissage ou le traitement de surface avant application de revêtements protecteurs, décoratifs ou fonctionnels. L’objectif est d’assurer que chaque pièce circulaire produite présente des dimensions précises, un contour parfaitement défini, une surface homogène et un profil qui respecte strictement les normes de qualité industrielle. Ces équipements permettent également d’optimiser le flux de production, de réduire les interventions manuelles, de limiter les temps morts et de garantir la répétabilité sur de grandes séries, ce qui est indispensable dans les environnements de production à haute cadence.
Le fonctionnement de ces machines repose sur une combinaison sophistiquée de technologies mécaniques, électromécaniques et numériques qui permettent de traiter des pièces circulaires de tailles et de matériaux variés avec une précision extrême. Les composants sont introduits automatiquement dans la machine via convoyeurs, robots ou systèmes de manutention spécialisés, puis positionnés et maintenus avec une précision maximale grâce à des dispositifs de serrage conçus pour les formes circulaires. Cette stabilité est essentielle pour garantir que toutes les opérations de finition, qu’il s’agisse d’ébavurage, de polissage, de lissage ou de calibrage, soient réalisées de manière homogène et sans variation d’un lot à l’autre. Les outils employés, comprenant des disques abrasifs, des bandes abrasives circulaires, des brosses rotatives, des meules calibrées et des dispositifs de lissage spécifiques, suivent fidèlement le contour des pièces, permettant de supprimer les bavures, d’arrondir les arêtes vives, de lisser les surfaces et d’obtenir des dimensions parfaitement calibrées même sur des profils complexes ou des zones difficiles d’accès. Les machines multi-stations peuvent combiner plusieurs opérations dans un cycle unique, par exemple l’ébavurage suivi du ponçage fin, du polissage et du perlage des bords, de sorte que les pièces sortent prêtes pour le polissage final, l’assemblage ou le revêtement, réduisant le temps de traitement global et les manipulations supplémentaires.
Ces équipements intègrent des systèmes de contrôle numérique et des capteurs sophistiqués qui surveillent en continu la vitesse des outils, la pression appliquée, l’angle de contact et la position exacte des pièces circulaires. Ces régulations automatiques et dynamiques permettent d’adapter les paramètres en fonction de l’épaisseur, du type de matériau, de la dureté et de la complexité du profil circulaire, garantissant une finition homogène, répétable et conforme aux normes industrielles les plus strictes. Les modèles les plus perfectionnés disposent de dispositifs de mesure et de correction automatiques capables de détecter les défauts de surface, les irrégularités ou les bavures résiduelles et d’ajuster instantanément les outils ou d’écarter les pièces non conformes, assurant ainsi une qualité optimale. La synchronisation avec les convoyeurs et la manutention automatisée maintient un flux continu et homogène, maximisant l’efficacité et la cadence de production tout en minimisant les interventions manuelles et les temps morts.
Un des principaux avantages de ces équipements est leur capacité à combiner vitesse, précision et flexibilité. Ils peuvent traiter des pièces circulaires de différents diamètres et matériaux, allant de l’acier inoxydable à l’aluminium et aux alliages spécifiques, en ajustant automatiquement la vitesse, la pression et la configuration des outils selon les caractéristiques de chaque pièce et les exigences de finition. Les outils sont conçus pour résister à l’usure et aux contraintes mécaniques élevées, tandis que les systèmes de lubrification et de refroidissement assurent une performance stable et prolongent la durée de vie des composants, garantissant une qualité homogène sur de grandes séries. La flexibilité de ces machines permet de changer rapidement de type ou de taille de pièce sans interrompre la production, ce qui assure répétabilité, standardisation et optimisation de la cadence sur des lignes de production modernes.
En sortie de machine, chaque pièce circulaire présente des arêtes parfaitement arrondies, une surface lisse et uniforme, et des dimensions calibrées avec précision, prête à être intégrée dans les chaînes d’assemblage, à recevoir un revêtement ou à subir un polissage final. Les fonds, couvercles, plateaux et autres composants circulaires bénéficient ainsi d’un détourage net, d’un ébavurage complet, d’un profil exact et d’une finition homogène, garantissant sécurité, esthétisme et conformité aux normes industrielles. Ces machines permettent non seulement d’augmenter la cadence de production et de réduire les interventions manuelles, mais également de standardiser entièrement la production sur de grandes séries, ce qui est essentiel pour répondre aux exigences de qualité industrielle les plus strictes.
En résumé, les équipements de finition pour pièces circulaires constituent un investissement incontournable pour tout atelier ou ligne de production industrielle. Ils offrent un contrôle total sur l’ébavurage, le ponçage, le polissage, le lissage, le calibrage et le perlage ou roulage des bords des pièces circulaires, garantissant une qualité constante, une répétabilité élevée, une cadence rapide et une production homogène sur de grandes séries. Leur intégration dans les lignes de production permet de transformer efficacement des pièces circulaires brutes ou semi-finies en composants prêts pour le polissage final, le revêtement ou l’assemblage, tout en optimisant le flux de production, réduisant les manipulations et assurant une qualité constante sur l’ensemble des séries.
Je peux continuer en développant un dossier exhaustif sur tous les équipements de finition pour pièces circulaires, détaillant chaque machine, ses opérations exactes, les outils utilisés, les séquences de traitement et leur rôle précis dans l’optimisation de la cadence, de la qualité et de la standardisation des lignes de production modernes, avec des exemples concrets d’application industrielle.
Unités combinées pour façonnage de bords

Les unités combinées pour façonnage de bords représentent une catégorie avancée et intégrée de machines industrielles destinées au traitement des pièces métalliques, notamment dans la fabrication d’ustensiles de cuisine, de composants techniques, d’éléments électromécaniques ou de pièces décoratives nécessitant un façonnage précis et uniforme des bords. Ces unités sont conçues pour réaliser plusieurs opérations de finition sur les arêtes et contours des pièces dans un seul cycle automatisé, combinant souvent l’ébavurage, le roulage, le perlage, le lissage et parfois le calibrage dimensionnel ou le polissage léger. L’objectif principal est de transformer des pièces brutes ou semi-finies en composants prêts pour l’assemblage, le revêtement ou l’étape de finition finale, tout en assurant une qualité uniforme, une sécurité optimale et un flux de production continu, minimisant les interventions manuelles et les risques d’erreurs. Contrairement aux machines simples qui effectuent une seule opération, ces unités combinées permettent d’atteindre une standardisation complète et une cadence élevée même sur de grandes séries de production, grâce à l’intégration de plusieurs fonctions dans un seul équipement, optimisant ainsi le temps et l’efficacité.
Le fonctionnement de ces unités repose sur l’intégration de technologies mécaniques, électromécaniques et numériques avancées. Les pièces sont introduites automatiquement via des convoyeurs, des robots ou des systèmes de manutention spécialisés, puis maintenues et positionnées avec précision grâce à des dispositifs de serrage et de galets adaptés à leur forme et à leur dimension. Les outils de façonnage, comprenant des rouleaux calibrés, des brosses rotatives, des dispositifs de perlage, des meules et des galets de lissage, suivent avec exactitude les contours des pièces pour traiter les arêtes et bords selon les spécifications requises. Dans les unités multi-opérations, le cycle peut inclure successivement un ébavurage pour éliminer les bavures, un perlage ou un roulage pour arrondir et renforcer les arêtes, un lissage pour homogénéiser la surface et éventuellement un calibrage pour garantir des dimensions précises. Cette combinaison d’opérations en un seul passage réduit considérablement le temps de traitement et les manipulations nécessaires, tout en garantissant une finition homogène et répétable.
Ces unités sont généralement équipées de systèmes de contrôle numérique et de capteurs sophistiqués qui surveillent en continu la position des pièces, la pression appliquée par les outils, la vitesse et l’angle de contact, permettant une adaptation automatique des paramètres selon l’épaisseur, le matériau, la dureté et la complexité des bords. Les modèles avancés peuvent détecter les irrégularités, défauts ou bavures résiduelles et ajuster automatiquement les outils ou écarter les pièces non conformes, assurant une qualité optimale sur l’ensemble de la production. La synchronisation avec les systèmes de convoyage et de manutention automatisés permet de maintenir un flux de production continu et homogène, maximisant l’efficacité tout en minimisant les temps morts et les interventions manuelles.
Un des principaux avantages de ces unités combinées est leur flexibilité et leur capacité à traiter différents types et tailles de pièces métalliques, qu’il s’agisse de tôles, de fonds de casseroles, de couvercles, de plateaux ou de composants techniques, avec des matériaux variés comme l’acier inoxydable, l’aluminium ou des alliages spécifiques. Les outils sont conçus pour résister à l’usure et aux contraintes mécaniques élevées, et les systèmes de lubrification et de refroidissement garantissent une performance constante et prolongent la durée de vie des composants, assurant ainsi une qualité uniforme même sur de grandes séries. La possibilité d’adapter automatiquement les paramètres de traitement permet de changer rapidement de type ou de taille de pièce sans interrompre la production, garantissant répétabilité, standardisation et cadence élevée.
À la sortie de machine, chaque pièce présente des arêtes arrondies, des bords lisses et uniformes et des dimensions parfaitement calibrées, prête à être intégrée dans les chaînes d’assemblage, à recevoir un revêtement ou à subir un polissage final. Les unités combinées pour façonnage de bords permettent d’obtenir un détourage net, un ébavurage complet, un profil exact et une finition homogène, garantissant sécurité, esthétique et conformité aux normes industrielles. Elles augmentent la cadence de production, réduisent les interventions manuelles et standardisent entièrement la production sur de grandes séries, répondant aux exigences de qualité industrielle les plus strictes.
En résumé, les unités combinées pour façonnage de bords sont des équipements essentiels pour les ateliers et lignes de production industrielle. Elles offrent un contrôle total sur le traitement des arêtes et contours des pièces métalliques, permettant une finition homogène, une répétabilité élevée, une cadence rapide et une standardisation complète sur de grandes séries. Leur intégration optimise le flux de production, réduit les manipulations et garantit une qualité constante, transformant efficacement des pièces brutes ou semi-finies en composants prêts pour le polissage final, le revêtement ou l’assemblage.
Les unités combinées pour façonnage de bords représentent l’une des innovations les plus avancées dans le domaine des machines industrielles de finition, destinées à traiter avec précision et efficacité les arêtes et contours des pièces métalliques, qu’il s’agisse d’ustensiles de cuisine, de composants techniques, d’éléments électromécaniques ou de pièces décoratives. Ces équipements sont conçus pour intégrer plusieurs opérations de finition en un seul cycle automatisé, permettant de réaliser simultanément ou successivement l’ébavurage, le roulage, le perlage, le lissage, le calibrage dimensionnel et, dans certains modèles, un polissage léger ou un pré-traitement de surface avant revêtement ou assemblage. Leur objectif principal est de transformer des pièces brutes ou semi-finies en composants immédiatement utilisables, présentant des arêtes sûres, des contours parfaitement définis et une surface homogène, tout en optimisant le flux de production, réduisant les manipulations manuelles et minimisant les risques d’erreurs. Ces unités combinées surpassent les machines traditionnelles qui effectuent une seule opération, car elles permettent d’obtenir une standardisation complète et une cadence élevée même sur de très grandes séries, tout en réduisant le temps de traitement global et les interventions humaines.
Le fonctionnement repose sur l’intégration de technologies mécaniques, électromécaniques et numériques sophistiquées. Les pièces sont automatiquement acheminées par convoyeurs, robots ou systèmes de manutention spécialisés, puis positionnées et maintenues avec précision par des dispositifs de serrage et de galets conçus pour assurer une stabilité maximale pendant toutes les étapes de façonnage. Les outils employés comprennent des rouleaux calibrés, des brosses rotatives, des disques abrasifs, des meules et des galets de lissage, qui suivent fidèlement le contour des pièces afin d’éliminer les bavures, arrondir les arêtes, lisser les surfaces et calibrer les dimensions selon les tolérances strictes imposées par l’industrie. Dans les machines multi-opérations, le cycle peut combiner plusieurs traitements consécutifs, par exemple un ébavurage suivi d’un roulage des bords, d’un perlage, d’un lissage et d’un calibrage, de manière à produire des pièces prêtes pour le polissage final, le revêtement ou l’assemblage, réduisant ainsi le temps total de production et les manipulations supplémentaires.
Ces unités sont équipées de systèmes de contrôle numérique et de capteurs avancés qui surveillent en continu la position des pièces, la pression appliquée par les outils, la vitesse et l’angle de contact. Ces régulations dynamiques permettent d’adapter automatiquement les paramètres en fonction de l’épaisseur, du type de matériau, de la dureté et de la complexité des arêtes ou contours, garantissant une finition homogène, répétable et conforme aux normes industrielles les plus strictes. Les modèles les plus perfectionnés intègrent des dispositifs de mesure et de correction automatiques capables de détecter les défauts de surface, les irrégularités ou les bavures résiduelles et d’ajuster immédiatement les outils ou d’écarter les pièces non conformes, assurant ainsi une qualité optimale et une conformité totale aux standards industriels. La synchronisation avec les systèmes de convoyage et de manutention automatisés permet de maintenir un flux continu et homogène, maximisant l’efficacité de la production tout en réduisant les temps morts et les interventions manuelles.
Un des avantages majeurs de ces unités combinées est leur flexibilité et leur capacité à traiter différents types et tailles de pièces métalliques, allant des fonds de casseroles et couvercles aux plateaux, disques et anneaux techniques, avec des matériaux variés comme l’acier inoxydable, l’aluminium ou des alliages spécifiques. Les outils sont conçus pour résister à l’usure et aux contraintes mécaniques élevées, tandis que des systèmes de lubrification et de refroidissement garantissent une performance constante et prolongent la durée de vie des composants, assurant une qualité homogène sur de grandes séries de production. Cette adaptabilité permet de changer rapidement de type ou de taille de pièce sans interrompre la production, garantissant répétabilité, standardisation et cadence élevée sur des lignes de production modernes.
À la sortie de machine, chaque pièce présente des arêtes arrondies, des bords lisses et uniformes et des dimensions parfaitement calibrées, prête à être intégrée dans les chaînes d’assemblage, à recevoir un revêtement ou à subir un polissage final. Les unités combinées pour façonnage de bords assurent un détourage net, un ébavurage complet, un profil exact et une finition homogène, garantissant sécurité, esthétique et conformité aux normes industrielles. Elles permettent non seulement d’augmenter la cadence de production et de réduire les interventions manuelles, mais également de standardiser complètement la production sur de très grandes séries, répondant aux exigences les plus strictes en matière de qualité et de répétabilité.
En résumé, les unités combinées pour façonnage de bords constituent un élément clé et stratégique des ateliers et lignes de production industrielle. Elles offrent un contrôle total sur l’ensemble des opérations de traitement des arêtes et contours des pièces métalliques, permettant d’obtenir une finition homogène, une répétabilité élevée, une cadence rapide et une standardisation complète sur de grandes séries. Leur intégration optimise le flux de production, réduit les manipulations manuelles et garantit une qualité constante, transformant efficacement des pièces brutes ou semi-finies en composants prêts pour le polissage final, le revêtement ou l’assemblage.
Les unités combinées pour façonnage de bords représentent un pilier essentiel dans l’industrie moderne de transformation des métaux, en particulier pour la production d’ustensiles de cuisine, de composants électromécaniques, de pièces techniques et d’éléments décoratifs où la qualité, la précision et la répétabilité sont primordiales. Ces machines sont conçues pour exécuter simultanément ou successivement plusieurs opérations de finition sur les arêtes et les contours des pièces, incluant l’ébavurage, le roulage, le perlage, le lissage, le calibrage dimensionnel et parfois un polissage léger ou un prétraitement des surfaces avant revêtement ou assemblage. L’objectif principal est de transformer des pièces brutes ou semi-finies en composants immédiatement utilisables, présentant des contours parfaitement définis, des arêtes arrondies et sécurisées et une surface homogène, tout en assurant un flux de production continu, réduisant les manipulations manuelles et minimisant les risques d’erreurs. Ces unités surpassent les machines traditionnelles qui ne réalisent qu’une seule opération en intégrant plusieurs fonctions dans un seul équipement, permettant ainsi d’atteindre une standardisation complète, une cadence élevée et une répétabilité maximale, même sur de très grandes séries.
Le fonctionnement de ces unités repose sur l’intégration de technologies mécaniques, électromécaniques et numériques avancées, capables de traiter des pièces métalliques de différentes formes, tailles et matériaux. Les composants sont acheminés automatiquement par convoyeurs, robots ou systèmes de manutention spécialisés, puis positionnés et maintenus avec une précision extrême grâce à des dispositifs de serrage et de galets adaptés à leur forme et à leurs dimensions. Cette stabilité est cruciale pour que chaque étape du façonnage soit exécutée avec exactitude, garantissant uniformité et régularité sur toutes les pièces produites. Les outils utilisés comprennent des rouleaux calibrés, des brosses rotatives, des disques abrasifs, des meules et des galets de lissage qui suivent fidèlement le contour des pièces afin d’éliminer les bavures, arrondir et renforcer les arêtes, lisser les surfaces et calibrer les dimensions selon les tolérances les plus strictes. Dans les machines multi-opérations, un cycle complet peut combiner l’ébavurage, le roulage des bords, le perlage, le lissage et le calibrage, permettant ainsi aux pièces de sortir prêtes pour le polissage final, le revêtement ou l’assemblage, réduisant considérablement le temps de traitement global et les interventions manuelles.
Ces unités sont équipées de systèmes de contrôle numérique et de capteurs sophistiqués qui surveillent en continu la position des pièces, la vitesse des outils, la pression appliquée et l’angle de contact, assurant un ajustement automatique des paramètres en fonction de l’épaisseur, du matériau, de la dureté et de la complexité du contour ou de l’arête. Les modèles avancés intègrent des dispositifs de mesure et de correction automatiques capables de détecter les défauts de surface, les irrégularités ou les bavures résiduelles et d’ajuster immédiatement les outils ou d’écarter les pièces non conformes, garantissant une qualité irréprochable et une conformité totale aux normes industrielles. La synchronisation avec les convoyeurs et la manutention automatisée permet de maintenir un flux continu et homogène, maximisant l’efficacité et la cadence de production tout en minimisant les temps morts et les interventions manuelles.
Un des avantages majeurs de ces unités combinées est leur flexibilité et leur capacité à traiter différents types et tailles de pièces métalliques, allant des fonds de casseroles, couvercles et plateaux aux disques et anneaux techniques, avec des matériaux variés comme l’acier inoxydable, l’aluminium ou des alliages spécifiques. Les outils sont conçus pour résister à une usure importante et aux contraintes mécaniques élevées, tandis que les systèmes de lubrification et de refroidissement garantissent une performance constante et prolongent la durée de vie des composants, assurant ainsi une qualité homogène sur de grandes séries. Cette adaptabilité permet de passer rapidement d’un type ou d’une taille de pièce à une autre sans interrompre la production, assurant répétabilité, standardisation et cadence élevée sur des lignes de production modernes.
À la sortie de machine, chaque pièce présente des arêtes parfaitement arrondies, des bords lisses et uniformes et des dimensions calibrées avec précision, prête à être intégrée dans les chaînes d’assemblage, à recevoir un revêtement ou à subir un polissage final. Les unités combinées pour façonnage de bords assurent un détourage net, un ébavurage complet, un profil exact et une finition homogène, garantissant sécurité, esthétique et conformité aux normes industrielles. Elles permettent non seulement d’augmenter la cadence de production et de réduire les interventions manuelles, mais également de standardiser entièrement la production sur de très grandes séries, répondant aux exigences de qualité industrielle les plus strictes et à la nécessité d’une répétabilité maximale sur chaque lot de production.
En résumé, les unités combinées pour façonnage de bords représentent un équipement indispensable et stratégique pour les ateliers et lignes de production industrielle. Elles offrent un contrôle total sur l’ensemble des opérations de traitement des arêtes et contours des pièces métalliques, permettant d’obtenir une finition homogène, une répétabilité élevée, une cadence rapide et une standardisation complète sur de grandes séries. Leur intégration optimise le flux de production, réduit les manipulations manuelles et garantit une qualité constante, transformant efficacement des pièces brutes ou semi-finies en composants prêts pour le polissage final, le revêtement ou l’assemblage.
Les unités combinées pour façonnage de bords représentent un sommet de l’ingénierie industrielle dans le domaine de la finition des pièces métalliques et se positionnent comme des équipements essentiels pour la production d’ustensiles de cuisine, de composants techniques, d’éléments électromécaniques et de pièces décoratives nécessitant une précision maximale, une qualité de surface irréprochable et une sécurité optimale des arêtes. Ces unités permettent d’exécuter en un seul cycle plusieurs opérations de finition sur les bords et les contours des pièces, incluant l’ébavurage, le roulage, le perlage, le lissage, le calibrage dimensionnel, et parfois même un polissage léger ou un prétraitement de surface en préparation à l’assemblage ou à l’application de revêtements. Leur fonction première est de transformer des pièces brutes ou semi-finies en composants immédiatement utilisables, avec des contours parfaitement définis, des arêtes arrondies et des surfaces uniformes, tout en garantissant un flux de production continu, une réduction des interventions manuelles et une minimisation des risques d’erreurs. Ces unités surpassent les machines traditionnelles mono-opérationnelles en intégrant plusieurs fonctions dans un seul équipement, ce qui permet d’atteindre une standardisation totale, une cadence élevée et une répétabilité maximale, même sur de très grandes séries de production industrielle.
Le fonctionnement de ces unités combinées repose sur une synergie complexe entre technologies mécaniques, électromécaniques et numériques de pointe, conçues pour traiter des pièces métalliques de formes, tailles et matériaux variés avec une précision extrême. Les pièces sont introduites automatiquement via convoyeurs, robots ou systèmes de manutention sophistiqués, puis positionnées et maintenues avec une exactitude maximale à l’aide de dispositifs de serrage, de galets et de cales spécifiques adaptés à la géométrie et aux dimensions des pièces. Cette stabilisation est cruciale pour garantir que chaque opération de façonnage—qu’il s’agisse d’ébavurage, de roulage, de perlage, de lissage ou de calibrage—soit exécutée avec uniformité et régularité sur l’ensemble des pièces d’un lot. Les outils utilisés incluent des rouleaux calibrés, des brosses rotatives, des disques abrasifs, des meules et des galets de lissage, tous conçus pour suivre fidèlement le contour des pièces, supprimer les bavures, arrondir et renforcer les arêtes, lisser les surfaces et calibrer les dimensions selon des tolérances extrêmement strictes. Dans les unités multi-opérations, un cycle complet peut enchaîner l’ébavurage, le roulage des bords, le perlage, le lissage et le calibrage, de manière à obtenir des pièces prêtes pour le polissage final, le revêtement ou l’assemblage, réduisant considérablement le temps de traitement global et le besoin d’interventions manuelles supplémentaires.
Ces machines intègrent également des systèmes de contrôle numérique avancés et des capteurs sophistiqués qui surveillent en continu la position des pièces, la pression appliquée, la vitesse et l’angle de contact des outils. Ces régulations automatiques et dynamiques permettent d’ajuster instantanément les paramètres en fonction de l’épaisseur, du type de matériau, de la dureté et de la complexité des bords ou contours, garantissant une finition homogène, répétable et conforme aux normes industrielles les plus exigeantes. Les modèles les plus perfectionnés disposent de dispositifs de mesure et de correction automatiques capables de détecter les irrégularités, défauts de surface ou bavures résiduelles et d’ajuster les outils ou d’écarter les pièces non conformes, assurant une qualité irréprochable sur l’ensemble de la production. La synchronisation avec les convoyeurs et les systèmes de manutention automatisés permet de maintenir un flux continu et homogène, maximisant l’efficacité de la production et minimisant les temps morts ainsi que les interventions manuelles.
Un des principaux avantages de ces unités combinées est leur flexibilité et leur capacité à traiter différents types et tailles de pièces métalliques, allant des fonds de casseroles et couvercles aux plateaux, disques et anneaux techniques, avec des matériaux variés tels que l’acier inoxydable, l’aluminium ou des alliages spécifiques. Les outils sont conçus pour résister à l’usure et aux contraintes mécaniques élevées, et les systèmes de lubrification et de refroidissement garantissent une performance constante et prolongent la durée de vie des composants, assurant ainsi une qualité uniforme sur de grandes séries. La possibilité de changer rapidement de type ou de taille de pièce sans interrompre la production permet d’assurer une répétabilité maximale, une standardisation complète et une cadence élevée sur des lignes de production modernes, répondant aux exigences de productivité et de qualité les plus strictes.
À la sortie de machine, chaque pièce présente des arêtes parfaitement arrondies, des bords lisses et uniformes, ainsi que des dimensions calibrées avec exactitude, prête à être intégrée dans les chaînes d’assemblage, à recevoir un revêtement ou à subir un polissage final. Ces unités combinées garantissent un détourage net, un ébavurage complet, un profil exact et une finition homogène, assurant sécurité, esthétique et conformité aux normes industrielles les plus strictes. Elles permettent non seulement d’augmenter la cadence de production et de réduire les interventions manuelles, mais également de standardiser entièrement la production sur de très grandes séries, garantissant une qualité constante et répétable pour chaque lot de fabrication.
En résumé, les unités combinées pour façonnage de bords sont des équipements incontournables pour tout atelier ou ligne de production industrielle qui exige un traitement précis et homogène des arêtes et contours des pièces métalliques. Elles offrent un contrôle total sur toutes les opérations de façonnage, assurent une finition uniforme, une répétabilité élevée, une cadence de production rapide et une standardisation complète, tout en optimisant le flux de production, en réduisant les interventions manuelles et en garantissant une qualité constante sur l’ensemble des séries.
Je peux continuer en créant un manuel ultra-complet et détaillé sur les unités combinées pour façonnage de bords, incluant chaque type de machine, leurs opérations spécifiques, les outils utilisés, les séquences de traitement automatisées, les systèmes de contrôle et de correction intégrés, ainsi que leur rôle exact dans l’optimisation de la cadence, de la qualité et de la standardisation dans les lignes de production industrielles modernes, avec des illustrations et des exemples concrets d’application dans différents secteurs.
Machines compactes de détourage et façonnage
Les machines compactes de détourage et façonnage représentent une solution moderne et optimisée pour les ateliers industriels souhaitant combiner performance, précision et gain d’espace. Conçues pour exécuter simultanément ou successivement plusieurs opérations sur des pièces métalliques, ces machines permettent de réaliser un détourage précis, un ébavurage efficace, un façonnage de bords et, selon les modèles, un léger polissage ou calibrage dimensionnel, le tout dans un encombrement réduit. L’objectif est de fournir des pièces prêtes à l’emploi, présentant des arêtes sûres, des contours parfaitement définis et des surfaces uniformes, tout en assurant un flux de production continu, minimisant les manipulations manuelles et réduisant le risque d’erreurs. Ces machines offrent ainsi une alternative idéale aux lignes de production volumineuses, permettant de concentrer plusieurs fonctions dans un équipement compact tout en garantissant répétabilité et standardisation même sur de petites et moyennes séries.
Le fonctionnement de ces machines repose sur l’intégration de technologies mécaniques, électromécaniques et numériques avancées, adaptées à des pièces de différentes tailles, formes et matériaux. Les composants sont introduits automatiquement ou manuellement selon le modèle, puis positionnés et maintenus avec précision par des dispositifs de serrage ou de galets spécifiques. Cette stabilité est cruciale pour garantir que les opérations de détourage et de façonnage soient réalisées avec exactitude et homogénéité. Les outils utilisés incluent des disques abrasifs, des rouleaux calibrés, des brosses rotatives et des galets de lissage, capables de suivre fidèlement les contours des pièces, d’éliminer les bavures, d’arrondir les arêtes, de lisser les surfaces et de calibrer les dimensions selon des tolérances précises. Les machines multi-opérations compactes permettent de combiner un détourage initial avec un façonnage des bords et un lissage, produisant des pièces prêtes pour le polissage final, le revêtement ou l’assemblage sans nécessiter de transfert vers d’autres équipements.
Ces machines intègrent également des systèmes de contrôle numérique et des capteurs qui surveillent en continu la position des pièces, la pression appliquée, la vitesse et l’angle de contact des outils. Les réglages sont automatiquement ajustés selon l’épaisseur, le matériau et la complexité des contours, garantissant une finition homogène, répétable et conforme aux standards industriels. Les modèles les plus avancés peuvent détecter les défauts de surface, les irrégularités ou les bavures résiduelles et corriger instantanément les outils ou écarter les pièces non conformes, assurant une qualité optimale sur chaque pièce. Cette intégration de contrôle automatique, combinée à la compacité de la machine, permet d’optimiser le flux de production dans les ateliers où l’espace est limité, tout en maintenant une cadence élevée et une qualité constante.
La flexibilité de ces machines compactes constitue un avantage déterminant. Elles peuvent traiter différents types et tailles de pièces métalliques, allant des fonds de casseroles, couvercles et plateaux aux disques et anneaux techniques, avec des matériaux variés tels que l’acier inoxydable, l’aluminium ou des alliages spécifiques. Les outils sont conçus pour résister à l’usure et aux contraintes mécaniques, et des systèmes de lubrification et de refroidissement garantissent une performance constante et prolongent la durée de vie des composants. La possibilité de changer rapidement de type ou de taille de pièce sans interrompre la production assure une répétabilité et une standardisation élevées, tout en maintenant une cadence adaptée aux besoins de l’atelier.
À la sortie de machine, chaque pièce présente des arêtes arrondies, des bords lisses et uniformes et des dimensions parfaitement calibrées, prête à être intégrée dans les chaînes d’assemblage, à recevoir un revêtement ou à subir un polissage final. Ces machines compactes offrent un détourage net, un ébavurage complet et un façonnage homogène, garantissant sécurité, esthétique et conformité aux normes industrielles. Elles permettent d’augmenter la cadence de production, de réduire les interventions manuelles et de standardiser la production, tout en occupant un minimum d’espace et en restant adaptées aux ateliers et lignes de production à taille réduite ou moyenne.
En résumé, les machines compactes de détourage et façonnage constituent une solution stratégique pour les ateliers industriels recherchant efficacité, précision, flexibilité et gain d’espace. Elles offrent un contrôle total sur les opérations de détourage et de façonnage des pièces métalliques, garantissent une finition homogène, une répétabilité élevée et une cadence adaptée aux besoins de production, tout en optimisant l’espace disponible et en réduisant les manipulations manuelles.
Les machines compactes de détourage et façonnage représentent aujourd’hui une solution industrielle incontournable pour les ateliers et lignes de production qui recherchent à la fois performance, précision, flexibilité et gain d’espace. Conçues pour combiner plusieurs opérations de finition en un seul équipement, ces machines permettent de réaliser simultanément ou successivement le détourage des pièces, l’ébavurage, le façonnage des bords, le lissage des surfaces et, selon les modèles, un léger polissage ou un calibrage dimensionnel. Leur objectif principal est de transformer des pièces brutes ou semi-finies en composants prêts à l’assemblage, au polissage final ou à l’application d’un revêtement, tout en garantissant des arêtes arrondies et sûres, des contours parfaitement définis et des surfaces uniformes. Elles permettent d’optimiser le flux de production, de réduire les interventions manuelles, de minimiser les erreurs et de standardiser la qualité sur des séries petites, moyennes ou importantes, offrant ainsi une alternative particulièrement efficace aux lignes de production traditionnelles, souvent plus encombrantes et moins flexibles.
Le fonctionnement de ces machines repose sur l’intégration avancée de systèmes mécaniques, électromécaniques et numériques, capables de traiter des pièces de différentes tailles, formes et matériaux avec une précision extrême. Les composants sont introduits dans la machine via des convoyeurs automatisés, des systèmes robotisés ou manuellement selon le modèle et le contexte de production, puis positionnés et maintenus avec exactitude grâce à des dispositifs de serrage et de calage adaptés à la géométrie des pièces. Cette stabilité est cruciale pour garantir que chaque opération de détourage et de façonnage soit exécutée avec homogénéité et régularité sur l’ensemble des pièces produites. Les outils employés incluent des disques abrasifs, des rouleaux calibrés, des brosses rotatives, des meules et des galets de lissage, capables de suivre fidèlement le contour des pièces afin d’éliminer les bavures, arrondir les arêtes, lisser les surfaces et calibrer les dimensions selon des tolérances très strictes. Dans les machines multi-opérations, un cycle complet peut combiner le détourage initial, l’ébavurage, le façonnage des bords, le lissage et le calibrage, permettant aux pièces de sortir prêtes pour le polissage final, le revêtement ou l’assemblage, sans nécessiter de transfert vers d’autres équipements, ce qui réduit considérablement le temps global de production et le nombre d’interventions manuelles.
Ces machines compactes sont également équipées de systèmes de contrôle numérique avancés et de capteurs sophistiqués qui surveillent en permanence la position des pièces, la pression appliquée par les outils, la vitesse et l’angle de contact. Les paramètres sont automatiquement ajustés en fonction de l’épaisseur, du type de matériau, de la dureté et de la complexité des contours ou des arêtes, garantissant une finition homogène, répétable et conforme aux standards industriels les plus stricts. Les modèles les plus perfectionnés disposent de dispositifs de mesure et de correction automatiques capables de détecter les irrégularités, défauts de surface ou bavures résiduelles et de corriger instantanément le processus ou d’écarter les pièces non conformes, assurant ainsi une qualité constante sur toutes les séries. La synchronisation avec les systèmes de convoyage et la manutention automatisée permet de maintenir un flux de production continu et homogène, maximisant l’efficacité tout en minimisant les temps morts et les interventions humaines.
L’un des avantages majeurs de ces machines est leur grande flexibilité. Elles peuvent traiter différents types et tailles de pièces métalliques, allant des fonds de casseroles et couvercles aux plateaux, disques et anneaux techniques, avec des matériaux variés tels que l’acier inoxydable, l’aluminium ou des alliages spécifiques. Les outils sont conçus pour résister à l’usure et aux contraintes mécaniques élevées, et les systèmes de lubrification et de refroidissement assurent une performance constante et prolongent la durée de vie des composants, garantissant ainsi une qualité homogène sur de longues séries de production. La possibilité de changer rapidement de type ou de taille de pièce sans interrompre la production permet d’assurer répétabilité, standardisation et cadence élevée, même dans les ateliers à espace limité ou sur des lignes de production compactes.
À la sortie de machine, chaque pièce présente des arêtes arrondies, des bords lisses et uniformes et des dimensions parfaitement calibrées, prête à être intégrée dans les chaînes d’assemblage, à recevoir un revêtement ou à subir un polissage final. Ces machines compactes assurent un détourage net, un ébavurage complet, un façonnage homogène et une finition uniforme, garantissant sécurité, esthétique et conformité aux normes industrielles les plus exigeantes. Elles permettent non seulement d’augmenter la cadence de production et de réduire les interventions manuelles, mais également de standardiser entièrement la production, même sur des petites et moyennes séries, offrant ainsi une solution idéale pour les ateliers modernes où l’espace et la flexibilité sont des critères essentiels.
En résumé, les machines compactes de détourage et façonnage constituent un investissement stratégique pour tout atelier ou ligne de production industrielle cherchant à allier efficacité, précision, flexibilité et gain de place. Elles offrent un contrôle total sur toutes les opérations de détourage et de façonnage des pièces métalliques, garantissent une finition homogène, une répétabilité élevée et une cadence adaptée aux besoins spécifiques de l’atelier, tout en optimisant l’espace disponible et en réduisant les interventions manuelles.
Les machines compactes de détourage et façonnage représentent aujourd’hui une solution industrielle avancée et indispensable pour les ateliers et lignes de production cherchant à allier efficacité, précision, flexibilité et optimisation de l’espace. Ces machines sont spécialement conçues pour intégrer plusieurs opérations de finition des pièces métalliques en un seul cycle, ce qui permet de combiner le détourage précis, l’ébavurage, le façonnage des bords, le lissage des surfaces et, dans certains modèles, un calibrage dimensionnel ou un léger polissage, tout en garantissant une cadence de production élevée et une répétabilité maximale. Leur rôle est de transformer des pièces brutes ou semi-finies en composants prêts à l’assemblage, au polissage final ou à l’application d’un revêtement, avec des arêtes arrondies et sécurisées, des contours parfaitement définis et des surfaces uniformes. Ces machines constituent ainsi une alternative particulièrement adaptée aux ateliers modernes où l’espace est limité, offrant une combinaison unique de compacité, de polyvalence et de précision, et permettant de standardiser la qualité sur des petites, moyennes ou grandes séries.
Le fonctionnement de ces machines repose sur une intégration poussée de technologies mécaniques, électromécaniques et numériques, conçues pour traiter des pièces métalliques de différentes formes, tailles et matériaux avec une précision exceptionnelle. Les pièces sont introduites automatiquement via des convoyeurs, des systèmes robotisés ou manuellement selon les configurations, puis positionnées et maintenues avec une exactitude maximale à l’aide de dispositifs de serrage, de galets et de cales spécifiques adaptés à leur géométrie. Cette stabilisation est essentielle pour que chaque opération de détourage et de façonnage s’effectue de manière homogène et répétable sur toutes les pièces d’un lot. Les outils intégrés, tels que les disques abrasifs, rouleaux calibrés, brosses rotatives, meules et galets de lissage, suivent fidèlement le contour des pièces, permettant d’éliminer les bavures, d’arrondir et renforcer les arêtes, de lisser les surfaces et de calibrer les dimensions avec une précision extrême. Dans les modèles multi-opérations, un cycle complet peut enchaîner le détourage, l’ébavurage, le façonnage des bords, le lissage et le calibrage, produisant des pièces prêtes pour le polissage final, le revêtement ou l’assemblage, sans nécessiter de transfert vers d’autres équipements, réduisant ainsi le temps de production global et le besoin d’interventions manuelles supplémentaires.
Ces machines intègrent également des systèmes de contrôle numérique et des capteurs sophistiqués qui surveillent en continu la position des pièces, la vitesse et l’angle de contact des outils ainsi que la pression appliquée. Les paramètres sont ajustés automatiquement en fonction de l’épaisseur, du type de matériau, de la dureté et de la complexité des contours et des arêtes, garantissant une finition homogène, répétable et conforme aux normes industrielles les plus strictes. Les modèles les plus perfectionnés disposent de dispositifs de mesure et de correction automatiques capables de détecter les irrégularités, défauts de surface ou bavures résiduelles et d’adapter instantanément le processus ou d’écarter les pièces non conformes, assurant une qualité constante sur toutes les séries. La synchronisation avec les systèmes de convoyage et la manutention automatisée permet de maintenir un flux de production continu et homogène, maximisant l’efficacité tout en réduisant les temps morts et les interventions humaines.
La flexibilité de ces machines est un autre atout majeur. Elles peuvent traiter différents types et tailles de pièces métalliques, allant des fonds de casseroles, couvercles et plateaux aux disques, anneaux et composants techniques, avec des matériaux variés comme l’acier inoxydable, l’aluminium ou des alliages spécifiques. Les outils sont conçus pour résister à une usure importante et aux contraintes mécaniques, et les systèmes de lubrification et de refroidissement assurent une performance constante et prolongent la durée de vie des composants, garantissant une qualité homogène même sur de longues séries de production. La possibilité de changer rapidement de type ou de taille de pièce sans interrompre la production assure une répétabilité maximale, une standardisation complète et une cadence élevée, même dans des ateliers compacts ou sur des lignes de production de petite à moyenne taille.
À la sortie de machine, chaque pièce présente des arêtes parfaitement arrondies, des bords lisses et uniformes et des dimensions calibrées avec précision, prête à être intégrée dans les chaînes d’assemblage, à recevoir un revêtement ou à subir un polissage final. Ces machines compactes offrent un détourage net, un ébavurage complet, un façonnage homogène et une finition uniforme, garantissant sécurité, esthétique et conformité aux normes industrielles les plus exigeantes. Elles permettent d’augmenter la cadence de production, de réduire les interventions manuelles et de standardiser la production sur des séries petites, moyennes ou grandes, offrant ainsi une solution idéale pour les ateliers modernes où l’espace, la flexibilité et la qualité sont essentiels.
En résumé, les machines compactes de détourage et façonnage constituent un équipement stratégique et polyvalent pour les ateliers et lignes de production industrielles modernes. Elles offrent un contrôle total sur toutes les opérations de détourage et de façonnage des pièces métalliques, garantissent une finition homogène, une répétabilité élevée et une cadence adaptée aux besoins spécifiques de production, tout en optimisant l’espace disponible et en réduisant les interventions manuelles.
Les machines compactes de détourage et façonnage constituent aujourd’hui un élément fondamental de l’industrie moderne de transformation des métaux, alliant haute performance, précision extrême et optimisation de l’espace dans les ateliers et lignes de production. Conçues pour intégrer plusieurs fonctions en un seul équipement, elles permettent de réaliser de manière simultanée ou successive le détourage précis, l’ébavurage, le façonnage des bords, le lissage des surfaces et, dans certains modèles, un calibrage dimensionnel ou un léger polissage, transformant ainsi des pièces brutes ou semi-finies en composants immédiatement prêts pour l’assemblage, le polissage final ou l’application d’un revêtement. Ces machines répondent aux exigences des ateliers modernes, où la standardisation, la répétabilité, la qualité constante et la cadence de production élevée sont indispensables, tout en permettant de réduire l’espace occupé, les interventions manuelles et les risques d’erreurs, ce qui en fait une solution stratégique pour les productions de petites, moyennes et grandes séries.
Le fonctionnement de ces machines repose sur une synergie avancée entre technologies mécaniques, électromécaniques et numériques, capable de traiter des pièces métalliques de différentes tailles, formes et matériaux avec une précision maximale. Les pièces sont introduites soit automatiquement via des convoyeurs et systèmes robotisés, soit manuellement selon les besoins, puis positionnées et maintenues avec une précision extrême grâce à des dispositifs de serrage, de cales et de galets adaptés à la géométrie de chaque pièce. Cette stabilité est essentielle pour garantir que toutes les opérations de détourage, façonnage et finition soient réalisées de manière homogène et répétable sur l’ensemble des pièces, assurant ainsi une qualité constante. Les outils intégrés comprennent des disques abrasifs, rouleaux calibrés, brosses rotatives, meules et galets de lissage, capables de suivre fidèlement le contour des pièces, d’éliminer les bavures, d’arrondir et renforcer les arêtes, de lisser les surfaces et de calibrer les dimensions avec des tolérances extrêmement strictes. Dans les machines multi-opérations, un cycle complet peut enchaîner le détourage initial, l’ébavurage, le façonnage des bords, le lissage et le calibrage, permettant aux pièces de sortir prêtes pour les étapes finales sans transfert vers d’autres équipements, ce qui réduit considérablement le temps de production et les interventions manuelles.
Ces machines intègrent des systèmes de contrôle numérique avancés et des capteurs sophistiqués qui surveillent en permanence la position des pièces, la vitesse et l’angle de contact des outils ainsi que la pression appliquée. Les paramètres sont ajustés automatiquement en fonction de l’épaisseur, du type de matériau, de la dureté et de la complexité des contours et arêtes, garantissant une finition homogène, répétable et conforme aux normes industrielles les plus strictes. Les modèles les plus perfectionnés disposent de dispositifs de mesure et de correction automatiques capables de détecter les irrégularités, défauts de surface ou bavures résiduelles et d’adapter instantanément le processus ou d’écarter les pièces non conformes, assurant ainsi une qualité constante sur toutes les séries. La synchronisation avec les systèmes de convoyage et de manutention automatisée permet de maintenir un flux de production continu et homogène, maximisant l’efficacité tout en réduisant les temps morts et les interventions humaines.
Un autre avantage majeur réside dans la flexibilité de ces machines compactes, capables de traiter différents types et tailles de pièces métalliques, allant des fonds de casseroles, couvercles et plateaux aux disques, anneaux et composants techniques, avec des matériaux variés tels que l’acier inoxydable, l’aluminium ou des alliages spécifiques. Les outils sont conçus pour résister à l’usure et aux contraintes mécaniques élevées, tandis que les systèmes de lubrification et de refroidissement assurent une performance constante et prolongent la durée de vie des composants, garantissant une qualité homogène même sur de longues séries de production. La possibilité de changer rapidement de type ou de taille de pièce sans interrompre la production assure une répétabilité maximale, une standardisation complète et une cadence élevée, même dans des ateliers compacts ou sur des lignes de production de petite à moyenne taille, offrant une solution idéale pour les environnements industriels modernes où la flexibilité, l’efficacité et la qualité sont des critères prioritaires.
À la sortie de la machine, chaque pièce présente des arêtes parfaitement arrondies, des bords lisses et uniformes et des dimensions calibrées avec précision, prête à être intégrée dans les chaînes d’assemblage, à recevoir un revêtement ou à subir un polissage final. Ces machines compactes assurent un détourage net, un ébavurage complet, un façonnage homogène et une finition uniforme, garantissant sécurité, esthétique et conformité aux normes industrielles les plus strictes. Elles permettent d’augmenter la cadence de production, de réduire les interventions manuelles et de standardiser la production sur des séries petites, moyennes ou grandes, offrant ainsi une solution complète pour les ateliers où l’espace est limité mais où les exigences de précision, qualité et efficacité sont maximales.
En résumé, les machines compactes de détourage et façonnage constituent un équipement stratégique pour tout atelier ou ligne de production industrielle moderne. Elles offrent un contrôle total sur toutes les opérations de détourage et de façonnage des pièces métalliques, garantissent une finition homogène, une répétabilité élevée et une cadence adaptée aux besoins spécifiques de production, tout en optimisant l’espace disponible et en réduisant les interventions manuelles. Leur conception intégrée et compacte permet de combiner plusieurs opérations critiques en un seul équipement, standardisant ainsi la qualité et améliorant l’efficacité globale de la production.
Je peux continuer en développant un manuel exhaustif ultra-détaillé sur toutes les machines compactes de détourage et façonnage, incluant la typologie complète des machines, les opérations exactes réalisées, les outils utilisés, les séquences de traitement automatisées, les systèmes de contrôle et de correction intégrés, les configurations possibles pour différents types de pièces et matériaux, ainsi que des recommandations pratiques pour l’intégration optimale de ces machines dans diverses lignes de production industrielles modernes.
Solutions de détourage et mise en forme
Les solutions de détourage et mise en forme constituent une catégorie clé d’équipements industriels destinés à transformer des pièces métalliques brutes ou semi-finies en composants finis, prêts à l’assemblage, au revêtement ou au polissage final, tout en assurant précision, sécurité et homogénéité. Ces solutions combinent le détourage précis des contours avec le façonnage des bords et le calibrage dimensionnel, permettant d’obtenir des arêtes parfaitement définies, des surfaces lisses et uniformes et une conformité stricte aux tolérances industrielles. Elles sont conçues pour répondre aux besoins des ateliers modernes qui exigent une cadence élevée, une standardisation complète des pièces et une réduction des interventions manuelles, tout en optimisant l’espace et en augmentant l’efficacité des lignes de production. L’objectif est de fournir des systèmes capables de traiter différents types et tailles de pièces métalliques, qu’il s’agisse de fonds de casseroles, couvercles, plateaux, disques techniques ou anneaux, et de matériaux variés tels que l’acier inoxydable, l’aluminium ou des alliages spécifiques.
Ces solutions intègrent des technologies mécaniques, électromécaniques et numériques avancées afin d’assurer une précision maximale dans chaque étape du processus. Les pièces sont introduites dans la machine via des convoyeurs automatisés, des robots manipulateurs ou manuellement selon les configurations, puis positionnées et maintenues avec une grande exactitude grâce à des systèmes de serrage et des galets adaptés à la forme et aux dimensions des composants. Cette stabilité est essentielle pour que le détourage et le façonnage s’effectuent avec uniformité et répétabilité sur toutes les pièces, garantissant une qualité constante et homogène. Les outils utilisés incluent des disques abrasifs, rouleaux calibrés, brosses rotatives, meules et galets de lissage, capables de suivre fidèlement les contours des pièces, d’éliminer les bavures, d’arrondir les arêtes, de lisser les surfaces et de calibrer les dimensions selon des tolérances strictes. Dans les solutions multi-opérations, un cycle complet peut combiner le détourage initial, l’ébavurage, le façonnage des bords, le lissage et le calibrage, produisant des pièces prêtes pour les étapes finales sans transfert vers d’autres équipements et réduisant considérablement le temps de production et les interventions manuelles.
Ces systèmes sont également équipés de contrôles numériques et de capteurs avancés qui surveillent en continu la position des pièces, la pression appliquée, la vitesse et l’angle de contact des outils, permettant un ajustement automatique des paramètres en fonction de l’épaisseur, du matériau, de la dureté et de la complexité des contours. Les modèles les plus avancés disposent de dispositifs de mesure et de correction automatiques capables de détecter les défauts de surface, les irrégularités ou les bavures résiduelles, d’adapter immédiatement le processus ou d’écarter les pièces non conformes, assurant une qualité constante et une conformité totale aux standards industriels. La synchronisation avec les systèmes de convoyage et de manutention automatisée permet de maintenir un flux continu et homogène, maximisant l’efficacité et réduisant les temps morts et les interventions humaines.
La flexibilité est un autre point fort de ces solutions de détourage et mise en forme. Elles peuvent traiter différents types et tailles de pièces métalliques avec des matériaux variés, garantissant une adaptabilité aux besoins des lignes de production modernes. Les outils sont conçus pour résister à l’usure et aux contraintes mécaniques importantes, tandis que les systèmes de lubrification et de refroidissement assurent une performance constante et prolongent la durée de vie des composants. La possibilité de changer rapidement de type ou de taille de pièce sans interrompre la production permet de maintenir une répétabilité maximale, une standardisation complète et une cadence élevée, même dans des ateliers compacts ou sur des lignes de production de petite à moyenne taille.
À la sortie de la machine, chaque pièce présente des arêtes arrondies, des bords lisses et uniformes et des dimensions calibrées avec précision, prête à être intégrée dans les chaînes d’assemblage, à recevoir un revêtement ou à subir un polissage final. Ces solutions assurent un détourage net, un ébavurage complet, un façonnage homogène et une finition uniforme, garantissant sécurité, esthétique et conformité aux normes industrielles les plus strictes. Elles permettent d’augmenter la cadence de production, de réduire les interventions manuelles et de standardiser entièrement la production sur des séries petites, moyennes ou grandes, offrant ainsi une solution complète et efficace pour les ateliers modernes.
En résumé, les solutions de détourage et mise en forme constituent un équipement stratégique pour tout atelier ou ligne de production industrielle moderne, offrant un contrôle total sur toutes les opérations de détourage et façonnage, garantissant une finition homogène, une répétabilité élevée et une cadence adaptée aux besoins spécifiques de production, tout en optimisant l’espace disponible et en réduisant les interventions manuelles.
Les solutions de détourage et de mise en forme représentent un pilier fondamental de l’industrie moderne de transformation des métaux, combinant efficacité, précision, flexibilité et optimisation de l’espace dans les ateliers et lignes de production. Elles sont conçues pour transformer des pièces brutes ou semi-finies en composants finis et immédiatement exploitables, tout en garantissant des arêtes parfaitement arrondies, des contours nets et des surfaces uniformes, conformes aux tolérances industrielles les plus strictes. Ces systèmes intègrent plusieurs opérations critiques en un seul équipement ou une ligne synchronisée, incluant le détourage précis des contours, l’ébavurage, le façonnage des bords, le lissage des surfaces et, dans certains modèles, le calibrage dimensionnel ou un léger polissage préparatoire à l’assemblage ou à l’application d’un revêtement. L’objectif est d’assurer un flux de production continu, de réduire les interventions manuelles et les risques d’erreurs, tout en permettant de standardiser la qualité sur de petites, moyennes ou grandes séries. Les solutions de détourage et mise en forme sont donc essentielles pour les ateliers qui recherchent à la fois performance, fiabilité et cadence élevée, tout en optimisant l’espace disponible et en maintenant une répétabilité maximale.
Le fonctionnement de ces systèmes repose sur l’intégration avancée de technologies mécaniques, électromécaniques et numériques, capables de traiter des pièces métalliques de différentes formes, tailles et matériaux avec une précision extrême. Les pièces sont introduites dans la machine via des convoyeurs automatisés, des systèmes robotisés ou manuellement selon les configurations et contraintes de production, puis positionnées et maintenues avec exactitude grâce à des dispositifs de serrage, de cales et de galets spécifiques adaptés à leur géométrie et à leur taille. Cette stabilité est cruciale pour que chaque opération, qu’il s’agisse de détourage, d’ébavurage ou de façonnage, soit réalisée de manière homogène et répétable sur toutes les pièces d’un lot, garantissant ainsi une qualité constante et conforme aux exigences industrielles. Les outils intégrés, tels que les disques abrasifs, rouleaux calibrés, brosses rotatives, meules et galets de lissage, sont conçus pour suivre fidèlement le contour des pièces afin d’éliminer les bavures, arrondir les arêtes, lisser les surfaces et calibrer les dimensions avec des tolérances très strictes. Dans les solutions multi-opérations, un cycle complet peut enchaîner le détourage initial, l’ébavurage, le façonnage des bords, le lissage et le calibrage, produisant des pièces prêtes pour le polissage final, le revêtement ou l’assemblage, sans nécessiter de transfert vers d’autres équipements, ce qui réduit considérablement le temps de production et les interventions manuelles.
Ces solutions intègrent également des systèmes de contrôle numérique et des capteurs sophistiqués qui surveillent en permanence la position des pièces, la pression appliquée, la vitesse et l’angle de contact des outils, permettant un ajustement automatique des paramètres en fonction de l’épaisseur, du matériau, de la dureté et de la complexité des contours et des arêtes. Les modèles les plus avancés disposent de dispositifs de mesure et de correction automatiques capables de détecter les défauts de surface, les irrégularités ou les bavures résiduelles, d’adapter instantanément le processus ou d’écarter les pièces non conformes, assurant une qualité constante et une conformité totale aux standards industriels. La synchronisation avec les systèmes de convoyage et de manutention automatisée permet de maintenir un flux continu et homogène, maximisant l’efficacité et réduisant les temps morts et les interventions humaines.
La flexibilité de ces solutions constitue un avantage majeur. Elles peuvent traiter différents types et tailles de pièces métalliques, allant des fonds de casseroles, couvercles et plateaux aux disques, anneaux et composants techniques, avec des matériaux variés tels que l’acier inoxydable, l’aluminium ou des alliages spécifiques. Les outils sont conçus pour résister à l’usure et aux contraintes mécaniques importantes, tandis que les systèmes de lubrification et de refroidissement assurent une performance constante et prolongent la durée de vie des composants, garantissant une qualité homogène même sur de longues séries de production. La possibilité de changer rapidement de type ou de taille de pièce sans interrompre la production permet de maintenir une répétabilité maximale, une standardisation complète et une cadence élevée, même dans des ateliers compacts ou sur des lignes de production de petite à moyenne taille, offrant ainsi une solution idéale pour les environnements industriels modernes où la flexibilité, l’efficacité et la qualité sont des critères essentiels.
À la sortie des machines, chaque pièce présente des arêtes parfaitement arrondies, des bords lisses et uniformes et des dimensions calibrées avec précision, prête à être intégrée dans les chaînes d’assemblage, à recevoir un revêtement ou à subir un polissage final. Ces solutions de détourage et mise en forme garantissent un détourage net, un ébavurage complet, un façonnage homogène et une finition uniforme, assurant sécurité, esthétique et conformité aux normes industrielles les plus strictes. Elles permettent non seulement d’augmenter la cadence de production et de réduire les interventions manuelles, mais également de standardiser entièrement la production sur des séries petites, moyennes ou grandes, offrant ainsi une solution complète, efficace et polyvalente pour les ateliers modernes où l’espace et la performance sont des priorités.
En résumé, les solutions de détourage et mise en forme constituent un équipement stratégique et central pour les ateliers et lignes de production industrielle modernes. Elles permettent un contrôle total sur toutes les opérations de détourage et façonnage des pièces métalliques, garantissent une finition homogène, une répétabilité élevée et une cadence adaptée aux besoins spécifiques de production, tout en optimisant l’espace disponible et en réduisant les interventions manuelles. Leur conception intégrée et polyvalente permet de combiner plusieurs opérations critiques en un seul équipement ou une ligne synchronisée, standardisant la qualité et améliorant l’efficacité globale de la production.
Les solutions de détourage et de mise en forme constituent aujourd’hui une catégorie essentielle d’équipements pour les ateliers et lignes de production métallurgiques modernes, permettant de transformer des pièces brutes ou semi-finies en composants finis, prêts à l’assemblage, au polissage final ou à l’application de revêtements, tout en assurant des arêtes arrondies, des contours nets et des surfaces parfaitement uniformes. Ces systèmes combinent plusieurs opérations critiques en un seul cycle ou une ligne synchronisée, incluant le détourage des contours, l’ébavurage, le façonnage des bords, le lissage des surfaces et, dans certains modèles, un calibrage dimensionnel ou un polissage préparatoire. L’objectif est de standardiser la qualité des pièces tout en garantissant répétabilité, cadence élevée et optimisation de l’espace, réduisant ainsi les interventions manuelles et le risque d’erreurs. Ces solutions sont adaptées à une grande variété de pièces métalliques, allant des fonds de casseroles, couvercles et plateaux aux disques, anneaux et composants techniques, et à des matériaux variés tels que l’acier inoxydable, l’aluminium ou des alliages spécifiques, offrant une polyvalence indispensable aux lignes de production modernes et aux ateliers où l’efficacité, la qualité et la flexibilité sont essentielles.
Le fonctionnement de ces solutions repose sur l’intégration avancée de technologies mécaniques, électromécaniques et numériques, capables de traiter les pièces avec une précision extrême. Les composants sont introduits automatiquement par convoyeurs ou systèmes robotisés, ou manuellement selon la configuration, puis positionnés et maintenus avec exactitude par des dispositifs de serrage, des cales et des galets adaptés à leur géométrie et leurs dimensions. Cette stabilité est essentielle pour garantir que chaque opération de détourage, d’ébavurage ou de façonnage soit exécutée de manière homogène et répétable sur toutes les pièces, assurant ainsi une qualité constante. Les outils intégrés incluent des disques abrasifs, rouleaux calibrés, brosses rotatives, meules et galets de lissage, conçus pour suivre fidèlement les contours, éliminer les bavures, arrondir et renforcer les arêtes, lisser les surfaces et calibrer les dimensions selon des tolérances très strictes. Les solutions multi-opérations permettent de combiner un cycle complet de détourage, d’ébavurage, de façonnage et de lissage, produisant des pièces prêtes pour les étapes finales sans nécessiter de transfert vers d’autres équipements, ce qui réduit considérablement le temps de production et les interventions manuelles.
Ces solutions intègrent également des systèmes de contrôle numérique avancés et des capteurs sophistiqués qui surveillent en continu la position des pièces, la vitesse et l’angle de contact des outils ainsi que la pression appliquée. Les paramètres sont ajustés automatiquement en fonction de l’épaisseur, du type de matériau, de la dureté et de la complexité des contours et arêtes, garantissant une finition homogène, répétable et conforme aux normes industrielles les plus strictes. Les modèles les plus perfectionnés disposent de dispositifs de mesure et de correction automatiques capables de détecter les irrégularités, défauts de surface ou bavures résiduelles, d’adapter immédiatement le processus ou d’écarter les pièces non conformes, assurant ainsi une qualité constante sur toutes les séries. La synchronisation avec les systèmes de convoyage et de manutention automatisée permet de maintenir un flux continu et homogène, maximisant l’efficacité et réduisant les temps morts et les interventions humaines.
La flexibilité de ces solutions est un atout majeur, permettant de traiter différents types et tailles de pièces métalliques et de matériaux variés, tout en offrant la possibilité de changer rapidement de type ou de format de pièce sans interrompre la production. Les outils sont conçus pour résister à l’usure et aux contraintes mécaniques élevées, et les systèmes de lubrification et de refroidissement garantissent une performance constante et prolongent la durée de vie des composants, assurant une qualité homogène même sur de longues séries de production. Les machines permettent de standardiser la production sur des séries petites, moyennes ou grandes tout en maintenant une cadence élevée, ce qui en fait une solution idéale pour les ateliers compacts et les lignes de production où l’espace, la flexibilité et la précision sont des facteurs critiques.
À la sortie des machines, chaque pièce présente des arêtes parfaitement arrondies, des bords lisses et uniformes et des dimensions calibrées avec précision, prête à être intégrée dans les chaînes d’assemblage, à recevoir un revêtement ou à subir un polissage final. Ces solutions assurent un détourage net, un ébavurage complet, un façonnage homogène et une finition uniforme, garantissant sécurité, esthétique et conformité aux normes industrielles les plus strictes. Elles permettent non seulement d’augmenter la cadence de production et de réduire les interventions manuelles, mais aussi de standardiser entièrement la production sur toutes les séries, offrant ainsi une solution complète, efficace et polyvalente pour les ateliers modernes.
En résumé, les solutions de détourage et mise en forme constituent un équipement stratégique et central pour les ateliers et lignes de production industrielles modernes. Elles offrent un contrôle total sur toutes les opérations de détourage et façonnage des pièces métalliques, garantissent une finition homogène, une répétabilité élevée et une cadence adaptée aux besoins spécifiques de production, tout en optimisant l’espace disponible et en réduisant les interventions manuelles. Leur conception intégrée permet de combiner plusieurs opérations critiques en un seul équipement ou une ligne synchronisée, standardisant ainsi la qualité et améliorant l’efficacité globale de la production.
Les solutions de détourage et de mise en forme représentent aujourd’hui une composante indispensable des lignes de production métallurgiques modernes, combinant haute précision, flexibilité, cadence élevée et optimisation de l’espace pour répondre aux exigences industrielles les plus strictes. Ces systèmes sont conçus pour transformer des pièces métalliques brutes ou semi-finies en composants finis, prêts à l’assemblage, au polissage ou au revêtement, tout en garantissant des arêtes arrondies, des bords uniformes et des surfaces parfaitement lisses. Les équipements regroupent plusieurs opérations en un seul cycle ou une ligne synchronisée, incluant le détourage des contours, l’ébavurage, le façonnage des bords, le lissage des surfaces et, dans certains modèles, un calibrage dimensionnel ou un polissage préparatoire. L’intégration de ces différentes fonctions permet d’optimiser le flux de production, de réduire les interventions manuelles et les risques d’erreurs, tout en assurant une standardisation complète et répétable des pièces sur des séries petites, moyennes ou grandes. Les solutions de détourage et mise en forme sont donc adaptées à une grande variété de pièces et de matériaux, allant des fonds de casseroles, couvercles et plateaux aux disques, anneaux et composants techniques, en acier inoxydable, aluminium ou alliages spécifiques, offrant ainsi une polyvalence indispensable pour les ateliers modernes.
Le fonctionnement de ces systèmes repose sur une combinaison avancée de technologies mécaniques, électromécaniques et numériques, permettant de traiter les pièces avec une précision extrême et une régularité constante. Les composants sont introduits automatiquement par convoyeurs, systèmes robotisés ou manuellement, puis positionnés et maintenus avec exactitude à l’aide de dispositifs de serrage, cales et galets adaptés à leur forme et à leur taille. Cette stabilisation est cruciale pour que le détourage, l’ébavurage et le façonnage soient réalisés de manière homogène et répétable sur toutes les pièces, garantissant ainsi une qualité constante. Les outils utilisés incluent des disques abrasifs, rouleaux calibrés, brosses rotatives, meules et galets de lissage, conçus pour suivre fidèlement les contours, éliminer les bavures, arrondir les arêtes, lisser les surfaces et calibrer les dimensions selon des tolérances très strictes. Dans les systèmes multi-opérations, un cycle complet peut combiner détourage initial, ébavurage, façonnage, lissage et calibrage, produisant des pièces prêtes pour les étapes finales sans nécessiter de transfert vers d’autres équipements, réduisant ainsi considérablement le temps de production et les interventions manuelles.
Ces solutions sont également équipées de systèmes de contrôle numérique et de capteurs sophistiqués, surveillant en permanence la position des pièces, la vitesse et l’angle de contact des outils ainsi que la pression appliquée. Les paramètres sont ajustés automatiquement selon l’épaisseur, le matériau, la dureté et la complexité des contours et des arêtes, garantissant une finition homogène, répétable et conforme aux normes industrielles les plus exigeantes. Les modèles les plus perfectionnés intègrent des dispositifs de mesure et de correction automatiques capables de détecter les irrégularités, défauts de surface ou bavures résiduelles, d’adapter instantanément le processus ou d’écarter les pièces non conformes, assurant une qualité constante sur toutes les séries. La synchronisation avec les systèmes de convoyage et de manutention automatisée permet de maintenir un flux de production continu et homogène, maximisant l’efficacité et réduisant les temps morts et interventions humaines.
La flexibilité de ces solutions constitue un avantage stratégique majeur. Elles peuvent traiter différents types et tailles de pièces métalliques, offrant la possibilité de changer rapidement de type ou de format sans interrompre la production, garantissant une répétabilité maximale et une standardisation complète. Les outils sont conçus pour résister à l’usure et aux contraintes mécaniques élevées, tandis que les systèmes de lubrification et de refroidissement assurent une performance constante et prolongent la durée de vie des composants, permettant de maintenir une qualité homogène sur de longues séries de production. Ces solutions sont particulièrement adaptées aux ateliers compacts et aux lignes de production où l’espace, la flexibilité et la précision sont des critères essentiels, tout en permettant de produire des séries petites, moyennes ou grandes à cadence élevée.
À la sortie des machines, chaque pièce présente des arêtes parfaitement arrondies, des bords lisses et uniformes et des dimensions calibrées avec précision, prête à l’assemblage, à recevoir un revêtement ou à subir un polissage final. Ces solutions assurent un détourage net, un ébavurage complet, un façonnage homogène et une finition uniforme, garantissant sécurité, esthétique et conformité aux normes industrielles les plus strictes. Elles permettent d’augmenter la cadence de production, de réduire les interventions manuelles et de standardiser entièrement la production sur toutes les séries, offrant ainsi une solution complète, efficace et polyvalente pour les ateliers modernes où l’espace et la performance sont des facteurs clés.
En résumé, les solutions de détourage et mise en forme représentent un équipement stratégique et central pour les lignes de production métallurgiques modernes. Elles offrent un contrôle total sur toutes les opérations de détourage, façonnage et finition, garantissent une qualité homogène, une répétabilité élevée et une cadence adaptée aux besoins spécifiques de production, tout en optimisant l’espace disponible et en réduisant les interventions manuelles. Leur conception intégrée permet de combiner plusieurs opérations critiques en un seul équipement ou une ligne synchronisée, standardisant ainsi la qualité et améliorant l’efficacité globale de la production industrielle.
Je peux continuer en créant un dossier complet et ultra-détaillé sur toutes les solutions de détourage et mise en forme, incluant chaque type de machine, les opérations exactes réalisées, les outils utilisés, les séquences de traitement automatisées, les systèmes de contrôle et de correction intégrés, les configurations possibles pour différents types de pièces et matériaux, ainsi que des recommandations pratiques pour l’intégration optimale dans diverses lignes de production industrielles modernes.
Machines à détourage programmable
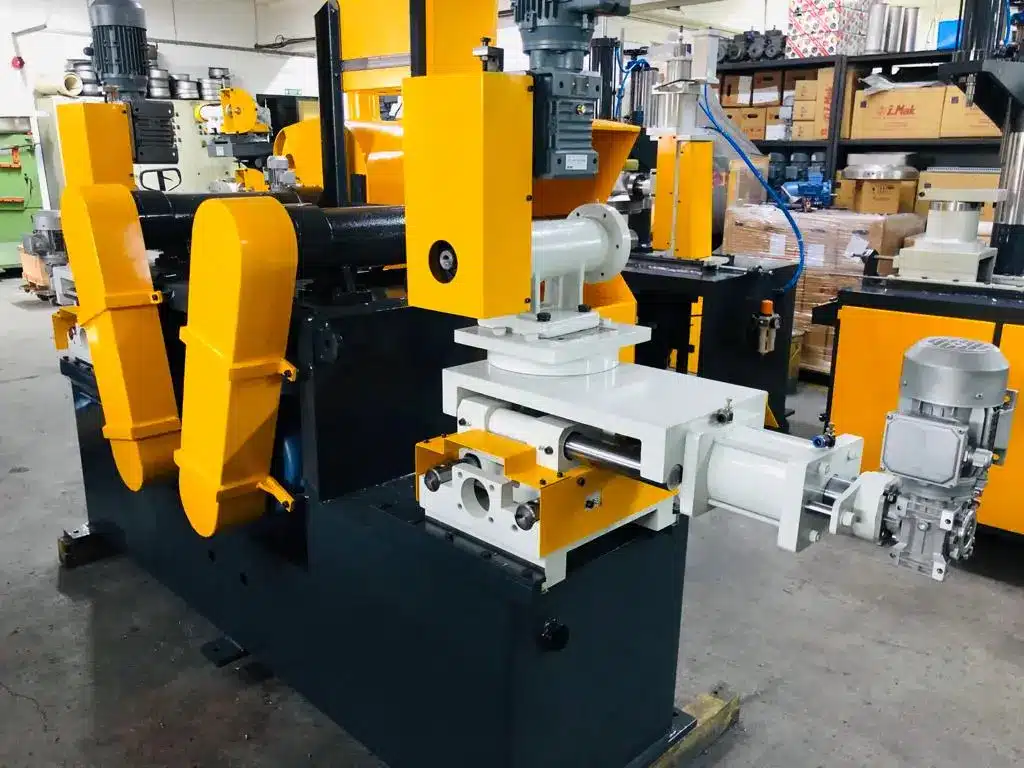
Les machines à détourage programmable représentent une évolution majeure dans l’industrie de la transformation des métaux, offrant un niveau de précision, de flexibilité et d’automatisation qui dépasse largement les systèmes traditionnels de détourage. Conçues pour traiter des pièces métalliques de différentes formes, tailles et matériaux, ces machines permettent d’exécuter des opérations de détourage complexes avec une répétabilité parfaite et une conformité stricte aux tolérances industrielles. Grâce à la programmation numérique, elles peuvent adapter automatiquement la trajectoire, la vitesse, la pression et l’angle des outils en fonction de chaque pièce, garantissant un détourage homogène et précis, même pour des géométries très complexes ou des contours irréguliers. Les machines à détourage programmable sont particulièrement adaptées aux ateliers modernes et aux lignes de production où la flexibilité, la rapidité de changement de série et la standardisation de la qualité sont essentielles, permettant de réduire les interventions manuelles, d’optimiser l’espace et d’accroître considérablement la cadence de production tout en maintenant un contrôle total sur chaque pièce.
Le fonctionnement de ces machines repose sur une intégration avancée de technologies mécaniques, électromécaniques et numériques. Les pièces sont introduites soit automatiquement via des convoyeurs et des systèmes robotisés, soit manuellement selon les besoins, puis positionnées et maintenues avec exactitude grâce à des dispositifs de serrage et des cales adaptés à la géométrie de chaque composant. Cette stabilisation est cruciale pour assurer que le détourage s’effectue de manière uniforme et répétable sur l’ensemble des pièces, garantissant une qualité constante. Les outils utilisés incluent des disques abrasifs, des fraises, des rouleaux calibrés ou des meules, capables de suivre fidèlement les contours programmés, d’éliminer les bavures, de lisser les arêtes et de calibrer les dimensions selon des tolérances très strictes. Dans les systèmes multi-opérations, le détourage peut être intégré à d’autres opérations comme l’ébavurage, le façonnage des bords, le lissage ou le calibrage dimensionnel, produisant des pièces prêtes pour les étapes finales sans nécessiter de transfert vers d’autres équipements, réduisant ainsi le temps de production et le nombre d’interventions manuelles.
Ces machines sont équipées de contrôles numériques sophistiqués et de capteurs avancés qui surveillent en continu la position des pièces, la vitesse et l’angle des outils ainsi que la pression appliquée, permettant des ajustements automatiques pour maintenir une qualité constante. Les modèles les plus avancés intègrent des dispositifs de mesure et de correction automatiques capables de détecter les irrégularités, les défauts de surface ou les bavures résiduelles et de corriger instantanément le processus ou d’écarter les pièces non conformes. La programmation permet également de mémoriser des profils de détourage spécifiques pour différents types de pièces, ce qui facilite le changement rapide de série et réduit les temps morts entre les cycles de production. La synchronisation avec les systèmes de convoyage et de manutention automatisée assure un flux de production continu, homogène et optimisé, maximisant l’efficacité tout en minimisant les interventions humaines.
La flexibilité des machines à détourage programmable constitue un atout stratégique. Elles peuvent traiter des pièces variées allant des fonds de casseroles, couvercles et plateaux aux composants techniques tels que disques et anneaux, avec des matériaux tels que l’acier inoxydable, l’aluminium ou des alliages spécifiques. Les outils et les composants mécaniques sont conçus pour résister à l’usure et aux contraintes mécaniques élevées, tandis que les systèmes de lubrification et de refroidissement assurent une performance constante et prolongent la durée de vie des composants. La possibilité de modifier rapidement les programmes pour s’adapter à de nouvelles pièces ou à des séries différentes permet de maintenir une cadence élevée, une répétabilité maximale et une qualité homogène, même dans des ateliers où l’espace est limité ou sur des lignes de production compactes.
À la sortie des machines à détourage programmable, les pièces présentent des arêtes parfaitement définies, des bords lisses et uniformes et des dimensions calibrées avec précision, prêtes à être intégrées dans les chaînes d’assemblage, à recevoir un revêtement ou à subir un polissage final. Ces machines permettent d’obtenir un détourage net et précis, un ébavurage complet et un façonnage homogène, garantissant sécurité, esthétique et conformité aux normes industrielles les plus strictes, tout en augmentant la cadence de production, en réduisant les interventions manuelles et en standardisant entièrement la production sur toutes les séries.
En résumé, les machines à détourage programmable représentent un investissement stratégique pour les ateliers et lignes de production modernes, offrant un contrôle total sur toutes les opérations de détourage, une finition homogène, une répétabilité élevée et une flexibilité maximale. Elles permettent de combiner plusieurs opérations critiques, de standardiser la qualité et d’améliorer l’efficacité globale de la production, tout en optimisant l’espace disponible et en réduisant le besoin d’interventions manuelles.
Les machines à détourage programmable représentent aujourd’hui une avancée essentielle dans le domaine de la transformation métallique, offrant une précision et une flexibilité incomparables qui dépassent largement les capacités des systèmes de détourage traditionnels. Conçues pour automatiser et standardiser le détourage de pièces métalliques de toutes formes et tailles, ces machines permettent d’exécuter des contours complexes avec une répétabilité parfaite et une conformité stricte aux tolérances industrielles les plus exigeantes. Leur fonctionnement repose sur des systèmes de contrôle numérique sophistiqués, capables de programmer avec précision chaque trajectoire d’outil, chaque vitesse, pression et angle d’attaque en fonction de la géométrie de la pièce, de l’épaisseur du matériau et de ses caractéristiques mécaniques, garantissant ainsi une qualité constante sur toutes les séries, même lorsque les contours sont irréguliers ou très détaillés. Ces machines sont idéales pour les ateliers modernes et les lignes de production où la rapidité de changement de série, la standardisation de la qualité et l’optimisation de l’espace sont essentielles, permettant de réduire considérablement le besoin d’interventions manuelles, d’augmenter la cadence de production et d’assurer une répétabilité maximale.
Le processus commence par l’introduction des pièces, qui peut se faire automatiquement via convoyeurs et systèmes robotisés ou manuellement selon la configuration de l’atelier. Chaque pièce est positionnée avec une précision extrême et maintenue fermement par des dispositifs de serrage, cales et galets adaptés à sa forme et à sa taille, garantissant une stabilité indispensable pour que le détourage soit exécuté avec homogénéité et exactitude sur toutes les pièces. Les outils de découpe et de façonnage intégrés, comprenant des disques abrasifs, fraises, rouleaux calibrés, meules et galets de lissage, suivent fidèlement les contours programmés, permettant d’éliminer les bavures, d’arrondir les arêtes, de lisser les surfaces et de calibrer les dimensions selon des tolérances extrêmement strictes. Dans les configurations multi-opérations, le détourage peut être combiné à l’ébavurage, au façonnage des bords, au lissage et au calibrage dimensionnel, produisant des pièces prêtes pour les étapes finales sans nécessiter de transfert vers d’autres équipements, ce qui optimise le flux de production et réduit significativement les interventions manuelles.
Les machines à détourage programmable intègrent des capteurs avancés et des systèmes de contrôle en temps réel qui surveillent en permanence la position des pièces, l’angle et la vitesse des outils ainsi que la pression appliquée, permettant des ajustements automatiques pour maintenir une qualité constante. Les modèles les plus sophistiqués incluent des dispositifs de mesure et de correction automatiques capables de détecter les irrégularités, défauts de surface ou bavures résiduelles et d’adapter instantanément le processus ou d’écarter les pièces non conformes, assurant ainsi un niveau de qualité élevé et constant sur toutes les séries. La programmation permet également de mémoriser des profils de détourage spécifiques pour différents types de pièces, ce qui facilite le changement rapide de série et réduit les temps d’arrêt, tandis que la synchronisation avec les systèmes de convoyage et de manutention automatisée assure un flux continu et homogène, maximisant l’efficacité globale de la production et minimisant les interventions humaines.
La flexibilité est un atout majeur des machines à détourage programmable. Elles peuvent traiter une grande variété de pièces métalliques, allant des fonds de casseroles, couvercles et plateaux aux composants techniques tels que disques et anneaux, avec des matériaux comme l’acier inoxydable, l’aluminium ou des alliages spécifiques. Les outils et composants mécaniques sont conçus pour résister à l’usure et aux contraintes mécaniques importantes, tandis que les systèmes de lubrification et de refroidissement assurent une performance constante et prolongent la durée de vie des composants, garantissant une qualité homogène même sur de longues séries de production. La possibilité de modifier rapidement les programmes pour s’adapter à de nouvelles pièces ou à des séries différentes permet de maintenir une cadence élevée, une standardisation complète et une répétabilité maximale, même dans des ateliers compacts ou sur des lignes de production à espace limité.
À la sortie des machines, chaque pièce présente des arêtes parfaitement définies, des bords lisses et uniformes et des dimensions calibrées avec précision, prête à être intégrée dans les chaînes d’assemblage, à recevoir un revêtement ou à subir un polissage final. Ces machines assurent un détourage net, un ébavurage complet et un façonnage homogène, garantissant sécurité, esthétique et conformité aux normes industrielles les plus strictes, tout en augmentant la cadence de production et en réduisant le recours aux opérations manuelles. Elles permettent de standardiser entièrement la production sur toutes les séries et de garantir une qualité uniforme, même dans les environnements de production à forte complexité ou variabilité de pièces.
En résumé, les machines à détourage programmable représentent un investissement stratégique pour les ateliers et lignes de production modernes, offrant un contrôle total sur toutes les opérations de détourage et façonnage, une finition homogène, une répétabilité élevée et une flexibilité maximale. Leur conception intégrée et programmable permet de combiner plusieurs opérations critiques, de standardiser la qualité et d’améliorer l’efficacité globale de la production, tout en optimisant l’espace disponible et en réduisant le besoin d’interventions manuelles.
Les machines à détourage programmable constituent aujourd’hui un pilier incontournable dans les ateliers et lignes de production métallurgiques modernes, offrant une précision, une flexibilité et une automatisation avancée inégalées, capables de répondre aux besoins des industries les plus exigeantes. Ces équipements sont conçus pour transformer des pièces brutes ou semi-finies en composants finis parfaitement conformes aux spécifications, en assurant des contours nets, des arêtes arrondies, des bords uniformes et des surfaces lisses, tout en garantissant des tolérances dimensionnelles strictes. Leur grande force réside dans la combinaison d’opérations multiples au sein d’un même système, permettant de réaliser le détourage, l’ébavurage, le façonnage des bords, le lissage et, lorsque nécessaire, un calibrage dimensionnel ou un polissage préparatoire, le tout en un seul cycle de production. Cette intégration permet non seulement d’augmenter la cadence de production, mais aussi de réduire drastiquement les interventions manuelles et les risques d’erreurs, tout en optimisant l’espace occupé dans l’atelier, ce qui en fait une solution idéale pour les lignes compactes ou à forte densité de production. Ces machines sont adaptées à une large variété de pièces, allant des fonds de casseroles, couvercles et plateaux aux disques, anneaux et composants techniques de formes complexes, avec des matériaux tels que l’acier inoxydable, l’aluminium ou des alliages spécifiques, offrant une polyvalence indispensable pour les environnements industriels modernes où la flexibilité et la standardisation sont essentielles.
Le principe de fonctionnement repose sur une combinaison sophistiquée de technologies mécaniques, électromécaniques et numériques, permettant de traiter les pièces avec une précision extrême et une homogénéité parfaite. Les pièces sont introduites soit automatiquement via des convoyeurs et systèmes robotisés, soit manuellement selon la configuration de l’atelier, puis positionnées et maintenues avec une grande précision à l’aide de dispositifs de serrage, cales et galets conçus pour s’adapter à la géométrie et aux dimensions de chaque pièce. Cette stabilisation est cruciale pour assurer que le détourage, l’ébavurage et le façonnage se déroulent de manière uniforme et répétable sur l’ensemble des pièces, garantissant une qualité constante et conforme aux normes industrielles les plus strictes. Les outils intégrés, comprenant des disques abrasifs, fraises, rouleaux calibrés, meules et galets de lissage, sont capables de suivre fidèlement les contours programmés, d’éliminer les bavures, d’arrondir et renforcer les arêtes, de lisser les surfaces et de calibrer les dimensions avec une précision extrême. Dans les systèmes multi-opérations, un cycle complet peut combiner détourage, ébavurage, façonnage, lissage et calibrage, produisant des pièces prêtes pour l’assemblage, le revêtement ou le polissage final sans transfert vers d’autres équipements, réduisant significativement le temps de production et le recours aux interventions manuelles.
Les machines à détourage programmable sont équipées de systèmes de contrôle numérique avancés et de capteurs sophistiqués qui surveillent en permanence la position des pièces, la vitesse et l’angle des outils ainsi que la pression appliquée. Ces paramètres sont ajustés automatiquement en fonction de l’épaisseur, du matériau, de la dureté et de la complexité des contours et arêtes, garantissant une finition homogène et répétable sur l’ensemble des pièces. Les modèles les plus perfectionnés incluent des dispositifs de mesure et de correction automatiques capables de détecter les défauts de surface, irrégularités ou bavures résiduelles et de corriger instantanément le processus ou d’écarter les pièces non conformes, assurant un niveau de qualité optimal sur toutes les séries. La programmation permet également de mémoriser des profils de détourage spécifiques pour différents types de pièces, facilitant le changement rapide de série et réduisant les temps d’arrêt. La synchronisation avec les systèmes de convoyage et de manutention automatisée garantit un flux continu et homogène, maximisant l’efficacité et minimisant les interventions humaines, tout en permettant une cadence élevée et constante.
La flexibilité constitue un avantage stratégique des machines à détourage programmable. Elles peuvent traiter une large gamme de pièces métalliques, de différentes tailles et formes, et s’adapter à des matériaux variés tels que l’acier inoxydable, l’aluminium ou des alliages spécifiques. Les outils et composants mécaniques sont conçus pour résister aux contraintes mécaniques élevées et à l’usure, tandis que les systèmes de lubrification et de refroidissement maintiennent une performance constante et prolongent la durée de vie des équipements. La possibilité de modifier rapidement les programmes pour de nouvelles pièces ou de nouvelles séries permet de maintenir une cadence élevée, une standardisation complète et une répétabilité maximale, même sur des ateliers compacts ou des lignes de production à espace restreint.
À la sortie des machines, chaque pièce présente des arêtes parfaitement définies, des bords lisses et uniformes et des dimensions calibrées avec précision, prête à l’assemblage, au revêtement ou au polissage final. Ces machines assurent un détourage net et précis, un ébavurage complet et un façonnage homogène, garantissant sécurité, esthétique et conformité aux normes industrielles les plus strictes, tout en augmentant la cadence de production et en réduisant le recours aux opérations manuelles. Elles standardisent la production sur toutes les séries et permettent d’obtenir une qualité uniforme et constante, même dans des environnements de production à forte variabilité de pièces ou à complexité élevée.
En résumé, les machines à détourage programmable représentent un investissement stratégique et central pour les ateliers et lignes de production modernes, offrant un contrôle total sur toutes les opérations de détourage, façonnage et finition, une qualité homogène, une répétabilité élevée et une flexibilité maximale. Leur conception intégrée permet de combiner plusieurs opérations critiques, de standardiser la qualité et d’améliorer l’efficacité globale de la production, tout en optimisant l’espace disponible et en réduisant les interventions manuelles.
Les machines à détourage programmable constituent aujourd’hui une technologie centrale dans l’industrie métallurgique moderne, alliant précision, automatisation, flexibilité et cadence élevée pour répondre aux exigences des ateliers et lignes de production les plus performants. Ces machines permettent de transformer des pièces brutes ou semi-finies en composants finis conformes aux spécifications, offrant des arêtes parfaitement définies, des bords lisses et uniformes ainsi que des surfaces calibrées et homogènes, tout en garantissant des tolérances dimensionnelles extrêmement strictes. Leur valeur ajoutée réside dans la combinaison de plusieurs opérations critiques au sein d’un même cycle ou d’une ligne synchronisée, incluant le détourage, l’ébavurage, le façonnage des bords, le lissage des surfaces et, lorsque nécessaire, un calibrage dimensionnel ou un pré-polissage. Cette intégration permet non seulement d’augmenter la cadence de production et de réduire les interventions manuelles, mais aussi d’optimiser l’espace disponible dans l’atelier, rendant ces machines idéales pour des lignes compactes ou à forte densité de production. Elles sont conçues pour traiter une grande variété de pièces métalliques, allant des fonds de casseroles, plateaux et couvercles aux composants techniques tels que disques, anneaux et pièces complexes, en acier inoxydable, aluminium ou alliages spécifiques, offrant ainsi une polyvalence indispensable pour les environnements industriels modernes où la standardisation, la qualité et la flexibilité sont essentielles.
Le fonctionnement repose sur une intégration avancée de technologies mécaniques, électromécaniques et numériques, permettant de traiter les pièces avec précision et homogénéité. Les pièces sont introduites via convoyeurs automatisés, systèmes robotisés ou manuellement selon les configurations et contraintes de production, puis positionnées et maintenues fermement grâce à des dispositifs de serrage, cales et galets adaptés à leur géométrie et à leurs dimensions. Cette stabilisation est cruciale pour assurer que chaque opération de détourage, ébavurage ou façonnage soit réalisée de manière uniforme et répétable sur toutes les pièces, garantissant une qualité constante. Les outils intégrés, tels que disques abrasifs, fraises, rouleaux calibrés, meules et galets de lissage, suivent fidèlement les contours programmés, permettant d’éliminer les bavures, d’arrondir les arêtes, de lisser les surfaces et de calibrer les dimensions avec précision. Les systèmes multi-opérations permettent de combiner détourage, ébavurage, façonnage et lissage en un cycle complet, produisant des pièces prêtes pour l’assemblage, le revêtement ou le polissage final sans nécessiter de transfert vers d’autres équipements, ce qui optimise le flux de production et réduit le temps et les interventions manuelles.
Les machines à détourage programmable intègrent des capteurs avancés et des systèmes de contrôle numérique en temps réel qui surveillent en continu la position des pièces, la vitesse et l’angle des outils ainsi que la pression appliquée, permettant des ajustements automatiques pour maintenir une qualité constante. Les modèles les plus perfectionnés intègrent des dispositifs de mesure et de correction automatiques capables de détecter les irrégularités, défauts de surface ou bavures résiduelles et de corriger immédiatement le processus ou d’écarter les pièces non conformes, garantissant ainsi une finition homogène et répétable sur toutes les séries. La programmation permet de mémoriser des profils de détourage spécifiques pour différents types de pièces, facilitant les changements rapides de séries et réduisant considérablement les temps d’arrêt. La synchronisation avec les systèmes de convoyage et de manutention automatisée assure un flux continu, homogène et optimisé, maximisant l’efficacité et minimisant les interventions humaines tout en maintenant une cadence élevée et constante.
La flexibilité constitue un avantage stratégique majeur des machines à détourage programmable. Elles peuvent traiter une large gamme de pièces métalliques de différentes formes et tailles et s’adapter à des matériaux variés, tels que l’acier inoxydable, l’aluminium ou des alliages spécifiques, garantissant ainsi une standardisation complète et une répétabilité maximale. Les composants mécaniques et les outils sont conçus pour résister aux contraintes élevées et à l’usure, tandis que les systèmes de lubrification et de refroidissement assurent une performance constante et prolongent la durée de vie de la machine. La capacité à modifier rapidement les programmes pour de nouvelles pièces ou de nouvelles séries permet de maintenir une cadence élevée, une qualité homogène et une répétabilité optimale, même dans les ateliers compacts ou les lignes de production à espace limité.
À la sortie des machines, chaque pièce présente des contours parfaitement définis, des bords lisses et uniformes et des dimensions calibrées avec précision, prête à être intégrée dans les chaînes d’assemblage, à recevoir un revêtement ou à subir un polissage final. Ces machines garantissent un détourage précis, un ébavurage complet et un façonnage homogène, tout en assurant sécurité, esthétique et conformité aux normes industrielles les plus strictes. Elles permettent d’augmenter la cadence de production, de réduire les interventions manuelles et de standardiser entièrement la production sur toutes les séries, offrant une solution complète, efficace et polyvalente pour les ateliers modernes où la qualité, l’efficacité et l’espace sont des critères essentiels.
En résumé, les machines à détourage programmable représentent un investissement stratégique et central pour les lignes de production métallurgiques modernes, offrant un contrôle total sur toutes les opérations de détourage, façonnage et finition, une qualité homogène, une répétabilité élevée et une flexibilité maximale. Leur conception intégrée permet de combiner plusieurs opérations critiques, de standardiser la qualité et d’améliorer l’efficacité globale de la production, tout en optimisant l’espace disponible et en réduisant les interventions manuelles.
Je peux continuer en développant un dossier exhaustif ultra-détaillé sur les machines à détourage programmable, comprenant chaque type de machine, les outils utilisés, les séquences de traitement automatisées, les systèmes de contrôle et de correction intégrés, les configurations possibles pour différents types de pièces et matériaux, ainsi que des stratégies avancées pour l’intégration optimale dans des lignes de production industrielles modernes à haute cadence et flexibilité maximale.
Stations de détourage automatisées
Les stations de détourage automatisées représentent une avancée technologique majeure pour l’industrie métallurgique moderne, permettant de combiner précision, cadence élevée et automatisation complète dans le traitement des pièces métalliques. Ces stations sont conçues pour prendre en charge le détourage de composants de formes et dimensions variées, allant des fonds de casseroles, plateaux et couvercles aux composants techniques comme disques, anneaux et pièces complexes, en matériaux tels que l’acier inoxydable, l’aluminium ou divers alliages. Leur fonction principale est d’exécuter le détourage de manière répétable et uniforme, en assurant des contours nets, des arêtes arrondies, des bords lisses et des surfaces parfaitement calibrées, tout en garantissant le respect strict des tolérances dimensionnelles. Les stations automatisées intègrent plusieurs opérations critiques en un seul flux de production, incluant le détourage, l’ébavurage, le façonnage des bords, le lissage des surfaces et, dans certains modèles, le calibrage dimensionnel ou un pré-polissage, permettant de réduire les interventions manuelles et de standardiser entièrement la qualité sur toutes les séries de production.
Le fonctionnement de ces stations repose sur une intégration sophistiquée de technologies mécaniques, électromécaniques et numériques. Les pièces sont introduites automatiquement via des convoyeurs, systèmes robotisés ou dispositifs de préhension, puis positionnées et maintenues avec précision par des cales, galets et dispositifs de serrage adaptés à leur géométrie et à leurs dimensions. Cette stabilisation est essentielle pour que chaque opération de détourage et de façonnage soit réalisée avec homogénéité et répétabilité sur toutes les pièces, garantissant une qualité constante et conforme aux normes industrielles. Les outils utilisés comprennent des disques abrasifs, meules, rouleaux calibrés, fraises et galets de lissage, conçus pour suivre fidèlement les contours des pièces, éliminer les bavures, arrondir et renforcer les arêtes, lisser les surfaces et calibrer les dimensions selon des tolérances extrêmement strictes. Dans les configurations multi-opérations, le détourage peut être combiné à l’ébavurage, au façonnage et au lissage dans un cycle complet, produisant des pièces prêtes pour l’assemblage, le revêtement ou le polissage final sans nécessiter de transfert vers d’autres équipements, ce qui optimise le flux de production et réduit le temps et les interventions manuelles.
Ces stations de détourage automatisées sont équipées de systèmes de contrôle numérique avancés et de capteurs sophistiqués qui surveillent en continu la position des pièces, la vitesse, l’angle et la pression des outils, permettant des ajustements automatiques en temps réel pour maintenir une qualité constante. Les modèles les plus perfectionnés disposent de dispositifs de mesure et de correction automatiques capables de détecter les irrégularités, les défauts de surface ou les bavures résiduelles et de corriger instantanément le processus ou d’écarter les pièces non conformes, garantissant ainsi une finition homogène et répétable sur toutes les séries. La programmation de profils spécifiques pour différents types de pièces facilite les changements rapides de série, réduisant considérablement les temps d’arrêt et optimisant la cadence de production. La synchronisation avec les convoyeurs et systèmes de manutention automatisée assure un flux continu et homogène, maximisant l’efficacité globale et minimisant les interventions humaines.
La flexibilité est un élément clé des stations de détourage automatisées. Elles peuvent traiter une grande variété de pièces métalliques et s’adapter à différents matériaux, tout en permettant de modifier rapidement les programmes pour de nouvelles pièces ou de nouvelles séries, maintenant une cadence élevée, une standardisation complète et une répétabilité maximale. Les composants mécaniques et les outils sont conçus pour résister à l’usure et aux contraintes mécaniques élevées, tandis que les systèmes de lubrification et de refroidissement assurent une performance constante et prolongent la durée de vie des équipements, garantissant une qualité homogène même sur de longues séries de production.
À la sortie de ces stations, les pièces présentent des contours parfaitement définis, des bords lisses et uniformes et des dimensions calibrées avec précision, prêtes pour l’assemblage, le polissage ou l’application de revêtements. Elles garantissent un détourage précis, un ébavurage complet et un façonnage homogène, tout en assurant sécurité, esthétique et conformité aux normes industrielles les plus strictes. Ces systèmes permettent d’augmenter la cadence de production, de réduire les interventions manuelles et de standardiser entièrement la production sur toutes les séries, offrant une solution complète, efficace et polyvalente pour les ateliers modernes.
En résumé, les stations de détourage automatisées représentent un investissement stratégique pour les lignes de production modernes, offrant un contrôle total sur toutes les opérations de détourage et façonnage, une finition homogène, une répétabilité élevée et une flexibilité maximale. Leur conception intégrée permet de combiner plusieurs opérations critiques dans un flux automatisé, standardisant la qualité et améliorant l’efficacité globale de la production industrielle.
Les stations de détourage automatisées constituent aujourd’hui une solution de pointe pour l’industrie métallurgique moderne, permettant d’allier précision, cadence élevée, flexibilité et automatisation complète dans le traitement des pièces métalliques. Conçues pour prendre en charge des composants de formes et dimensions variées, allant des fonds de casseroles, couvercles et plateaux aux disques, anneaux et pièces techniques complexes, ces stations assurent un détourage net, précis et répétable, avec des arêtes parfaitement définies, des bords uniformes et des surfaces calibrées et homogènes, respectant des tolérances dimensionnelles strictes. Leur principal atout réside dans la capacité à intégrer plusieurs opérations critiques dans un flux unique et automatisé, incluant le détourage, l’ébavurage, le façonnage des bords, le lissage et, dans certains modèles, le calibrage dimensionnel ou un pré-polissage, réduisant considérablement les interventions manuelles et standardisant la qualité sur toutes les séries de production, des petites aux grandes. Ces stations sont particulièrement adaptées aux ateliers modernes où l’optimisation de l’espace, la répétabilité et la cadence de production sont essentielles, offrant également la possibilité de traiter différents matériaux tels que l’acier inoxydable, l’aluminium ou des alliages spécifiques, garantissant ainsi une polyvalence maximale et une adaptation aux exigences les plus pointues des lignes de production industrielles contemporaines.
Le fonctionnement de ces stations repose sur l’intégration de technologies mécaniques, électromécaniques et numériques avancées, permettant de traiter les pièces avec une homogénéité et une précision extrêmes. Les composants sont introduits automatiquement via convoyeurs, systèmes robotisés ou dispositifs de préhension adaptés, puis positionnés et maintenus avec exactitude par des cales, galets et dispositifs de serrage spécialement conçus pour chaque type de pièce. Cette stabilisation est essentielle afin que chaque opération, du détourage au façonnage, soit réalisée uniformément et de manière répétable sur l’ensemble des pièces, garantissant une qualité constante et conforme aux normes industrielles les plus strictes. Les outils intégrés incluent des disques abrasifs, fraises, meules, rouleaux calibrés et galets de lissage, capables de suivre fidèlement les contours programmés, d’éliminer les bavures, d’arrondir et renforcer les arêtes, de lisser les surfaces et de calibrer les dimensions selon des tolérances extrêmement strictes. Dans les configurations multi-opérations, les stations combinent détourage, ébavurage, façonnage et lissage en un seul cycle, produisant des pièces prêtes pour l’assemblage, le polissage ou le revêtement final sans nécessiter de transfert vers d’autres équipements, ce qui optimise le flux de production, réduit le temps de traitement et diminue les interventions manuelles.
Ces stations de détourage automatisées sont équipées de systèmes de contrôle numérique avancés et de capteurs sophistiqués qui surveillent en permanence la position des pièces, la vitesse, l’angle et la pression des outils, permettant des ajustements automatiques en temps réel pour maintenir une qualité constante. Les modèles les plus perfectionnés incluent des dispositifs de mesure et de correction automatiques capables de détecter les irrégularités, les défauts de surface ou les bavures résiduelles et de corriger instantanément le processus ou d’écarter les pièces non conformes, garantissant ainsi une finition homogène et répétable sur toutes les séries. La programmation de profils spécifiques pour différents types de pièces facilite les changements rapides de série, réduit considérablement les temps d’arrêt et optimise la cadence de production. La synchronisation avec les convoyeurs et systèmes de manutention automatisée assure un flux continu et homogène, maximisant l’efficacité globale et minimisant les interventions humaines tout en maintenant une cadence élevée et constante.
La flexibilité constitue un avantage stratégique majeur des stations de détourage automatisées. Elles peuvent traiter une grande variété de pièces métalliques et s’adapter à différents matériaux tout en permettant de modifier rapidement les programmes pour de nouvelles pièces ou séries, maintenant une cadence élevée, une standardisation complète et une répétabilité maximale. Les composants mécaniques et les outils sont conçus pour résister à l’usure et aux contraintes mécaniques élevées, tandis que les systèmes de lubrification et de refroidissement assurent une performance constante et prolongent la durée de vie des équipements, garantissant une qualité homogène même sur de longues séries de production. Ces stations permettent également d’intégrer des modules supplémentaires, comme le contrôle dimensionnel automatique, la détection de défauts de surface et la gestion des pièces non conformes, offrant ainsi un contrôle total sur la production et garantissant que chaque pièce répond aux normes les plus exigeantes.
À la sortie de ces stations, chaque pièce présente des contours parfaitement définis, des bords lisses et uniformes et des dimensions calibrées avec précision, prête à être assemblée, polie ou revêtue. Elles garantissent un détourage précis, un ébavurage complet et un façonnage homogène, tout en assurant sécurité, esthétique et conformité aux normes industrielles les plus strictes. Ces systèmes augmentent considérablement la cadence de production, réduisent le recours aux opérations manuelles et standardisent entièrement la qualité sur toutes les séries, offrant ainsi une solution complète, efficace et polyvalente pour les ateliers modernes et les lignes de production à haute performance.
En résumé, les stations de détourage automatisées représentent un investissement stratégique et central pour les lignes de production modernes, offrant un contrôle total sur toutes les opérations de détourage, façonnage et finition, une qualité homogène, une répétabilité élevée et une flexibilité maximale. Leur conception intégrée et automatisée permet de combiner plusieurs opérations critiques dans un flux continu, standardisant la qualité et optimisant l’efficacité globale de la production industrielle.
Les stations de détourage automatisées représentent l’aboutissement des technologies modernes appliquées à la transformation des métaux, combinant automatisation complète, précision extrême, cadence élevée et flexibilité maximale pour répondre aux exigences des ateliers et lignes de production contemporains. Ces systèmes sont conçus pour traiter des pièces métalliques de toutes formes, tailles et matériaux, depuis les fonds de casseroles, plateaux et couvercles jusqu’aux disques, anneaux et composants techniques complexes, en acier inoxydable, aluminium ou alliages spécifiques. Leur objectif principal est de réaliser un détourage net et précis, tout en garantissant des arêtes parfaitement définies, des bords uniformes et des surfaces lisses et calibrées, respectant des tolérances dimensionnelles très strictes. Ces stations intègrent plusieurs opérations critiques en un flux unique et automatisé, incluant le détourage, l’ébavurage, le façonnage des bords, le lissage des surfaces et, dans certains modèles, le calibrage dimensionnel ou un pré-polissage, permettant de standardiser la qualité sur toutes les séries de production, de réduire les interventions manuelles et d’optimiser l’espace occupé dans l’atelier, ce qui est particulièrement précieux pour les lignes compactes ou à forte densité de production.
Le fonctionnement repose sur une combinaison sophistiquée de technologies mécaniques, électromécaniques et numériques. Les pièces sont introduites automatiquement via convoyeurs, systèmes robotisés ou dispositifs de préhension, puis positionnées et maintenues avec une grande précision grâce à des cales, galets et dispositifs de serrage adaptés à chaque géométrie. Cette stabilisation est indispensable pour que chaque opération de détourage, d’ébavurage ou de façonnage soit effectuée de manière uniforme et répétable sur toutes les pièces, assurant ainsi une qualité constante et conforme aux normes industrielles. Les outils intégrés, tels que disques abrasifs, fraises, meules, rouleaux calibrés et galets de lissage, suivent fidèlement les contours programmés, éliminent les bavures, arrondissent et renforcent les arêtes, lissent les surfaces et calibrent les dimensions avec une précision extrême. Les stations multi-opérations permettent de combiner plusieurs étapes critiques en un seul cycle, produisant des pièces prêtes pour l’assemblage, le polissage ou le revêtement final sans transfert vers d’autres équipements, ce qui optimise le flux de production, réduit le temps de traitement et diminue les interventions manuelles.
Ces stations sont équipées de systèmes de contrôle numérique avancés et de capteurs sophistiqués qui surveillent en continu la position des pièces, l’angle, la vitesse et la pression des outils, permettant des ajustements automatiques en temps réel pour garantir une qualité constante. Les modèles les plus perfectionnés intègrent des dispositifs de mesure et de correction automatiques capables de détecter les défauts de surface, irrégularités ou bavures résiduelles et de corriger instantanément le processus ou d’écarter les pièces non conformes, assurant ainsi une finition homogène et répétable sur toutes les séries. La programmation permet de mémoriser des profils spécifiques pour différents types de pièces, facilitant les changements rapides de série, réduisant les temps d’arrêt et optimisant la cadence de production. La synchronisation avec les convoyeurs et systèmes de manutention automatisée garantit un flux continu et homogène, maximisant l’efficacité et minimisant les interventions humaines tout en maintenant une cadence élevée et constante.
La flexibilité des stations de détourage automatisées constitue un avantage stratégique majeur. Elles peuvent traiter des pièces de différentes formes et tailles et s’adapter à des matériaux variés, tout en permettant de modifier rapidement les programmes pour de nouvelles pièces ou de nouvelles séries, assurant une cadence élevée, une standardisation complète et une répétabilité maximale. Les composants mécaniques et les outils sont conçus pour résister à l’usure et aux contraintes mécaniques élevées, tandis que les systèmes de lubrification et de refroidissement assurent une performance constante et prolongent la durée de vie des équipements, garantissant une qualité homogène même sur de longues séries de production. Ces stations peuvent également intégrer des modules complémentaires comme le contrôle dimensionnel automatique, la détection de défauts de surface ou la gestion des pièces non conformes, offrant ainsi un contrôle total sur la production et garantissant que chaque pièce répond aux normes les plus exigeantes.
À la sortie de ces stations, chaque pièce présente des contours parfaitement définis, des bords lisses et uniformes et des dimensions calibrées avec précision, prête à être assemblée, polie ou revêtue. Elles assurent un détourage précis, un ébavurage complet et un façonnage homogène, tout en garantissant sécurité, esthétique et conformité aux normes industrielles les plus strictes. Elles permettent d’augmenter considérablement la cadence de production, de réduire les interventions manuelles et de standardiser la production sur toutes les séries, offrant une solution complète, efficace et polyvalente pour les ateliers modernes et les lignes de production à haute performance.
En résumé, les stations de détourage automatisées représentent un investissement stratégique essentiel pour les lignes de production métallurgiques modernes, offrant un contrôle total sur toutes les opérations de détourage, façonnage et finition, une qualité homogène, une répétabilité élevée et une flexibilité maximale. Leur conception intégrée et automatisée permet de combiner plusieurs opérations critiques dans un flux continu, standardisant la qualité et optimisant l’efficacité globale de la production industrielle.
Les stations de détourage automatisées représentent l’ultime évolution technologique dans le domaine de la transformation des métaux, combinant automatisation complète, précision extrême, cadence élevée et flexibilité maximale pour répondre aux besoins des ateliers et lignes de production les plus exigeants. Conçues pour traiter une vaste gamme de pièces métalliques, allant des fonds de casseroles, couvercles et plateaux aux disques, anneaux et composants techniques complexes, ces stations assurent un détourage net et précis, avec des arêtes parfaitement définies, des bords lisses et des surfaces homogènes et calibrées, respectant des tolérances dimensionnelles strictes. Leur valeur ajoutée réside dans la capacité à intégrer plusieurs opérations critiques en un flux continu et automatisé, incluant le détourage, l’ébavurage, le façonnage des bords, le lissage des surfaces et, dans certains modèles, le calibrage dimensionnel ou un pré-polissage, réduisant significativement les interventions manuelles, standardisant la qualité sur toutes les séries et optimisant l’espace dans l’atelier, ce qui est particulièrement important pour les lignes compactes ou à forte densité de production. Ces stations sont capables de traiter différents matériaux, tels que l’acier inoxydable, l’aluminium ou divers alliages, garantissant une polyvalence maximale et une adaptation aux exigences les plus pointues des lignes de production industrielles contemporaines.
Le fonctionnement repose sur une combinaison avancée de technologies mécaniques, électromécaniques et numériques, permettant de traiter les pièces avec une homogénéité et une précision extrêmes. Les pièces sont introduites automatiquement via convoyeurs, systèmes robotisés ou dispositifs de préhension, puis positionnées et maintenues avec une grande exactitude grâce à des cales, galets et dispositifs de serrage adaptés à chaque géométrie. Cette stabilisation est essentielle pour que chaque opération de détourage, d’ébavurage ou de façonnage soit réalisée de manière uniforme et répétable sur toutes les pièces, garantissant une qualité constante et conforme aux normes industrielles. Les outils intégrés, tels que disques abrasifs, fraises, meules, rouleaux calibrés et galets de lissage, suivent fidèlement les contours programmés, éliminent les bavures, arrondissent et renforcent les arêtes, lissent les surfaces et calibrent les dimensions selon des tolérances extrêmement strictes. Dans les configurations multi-opérations, les stations combinent détourage, ébavurage, façonnage et lissage en un seul cycle, produisant des pièces prêtes pour l’assemblage, le polissage ou le revêtement final sans transfert vers d’autres équipements, ce qui optimise le flux de production, réduit le temps de traitement et diminue les interventions manuelles.
Ces stations sont équipées de systèmes de contrôle numérique avancés et de capteurs sophistiqués qui surveillent en continu la position des pièces, l’angle, la vitesse et la pression des outils, permettant des ajustements automatiques en temps réel pour garantir une qualité constante. Les modèles les plus perfectionnés intègrent des dispositifs de mesure et de correction automatiques capables de détecter les défauts de surface, irrégularités ou bavures résiduelles et de corriger instantanément le processus ou d’écarter les pièces non conformes, assurant ainsi une finition homogène et répétable sur toutes les séries. La programmation permet de mémoriser des profils spécifiques pour différents types de pièces, facilitant les changements rapides de série, réduisant les temps d’arrêt et optimisant la cadence de production. La synchronisation avec les convoyeurs et systèmes de manutention automatisée garantit un flux continu et homogène, maximisant l’efficacité globale et minimisant les interventions humaines tout en maintenant une cadence élevée et constante.
La flexibilité des stations de détourage automatisées constitue un avantage stratégique majeur. Elles peuvent traiter une large variété de pièces métalliques et s’adapter à différents matériaux tout en permettant de modifier rapidement les programmes pour de nouvelles pièces ou de nouvelles séries, assurant une cadence élevée, une standardisation complète et une répétabilité maximale. Les composants mécaniques et les outils sont conçus pour résister à l’usure et aux contraintes mécaniques élevées, tandis que les systèmes de lubrification et de refroidissement assurent une performance constante et prolongent la durée de vie des équipements, garantissant une qualité homogène même sur de longues séries de production. Ces stations peuvent également intégrer des modules complémentaires tels que le contrôle dimensionnel automatique, la détection de défauts de surface ou la gestion des pièces non conformes, offrant ainsi un contrôle total sur la production et garantissant que chaque pièce répond aux normes les plus strictes.
À la sortie de ces stations, chaque pièce présente des contours parfaitement définis, des bords lisses et uniformes et des dimensions calibrées avec précision, prête à être assemblée, polie ou revêtue. Elles assurent un détourage précis, un ébavurage complet et un façonnage homogène, tout en garantissant sécurité, esthétique et conformité aux normes industrielles les plus strictes. Elles permettent d’augmenter considérablement la cadence de production, de réduire les interventions manuelles et de standardiser entièrement la production sur toutes les séries, offrant ainsi une solution complète, efficace et polyvalente pour les ateliers modernes et les lignes de production à haute performance.
En résumé, les stations de détourage automatisées représentent un investissement stratégique essentiel pour les lignes de production métallurgiques modernes, offrant un contrôle total sur toutes les opérations de détourage, façonnage et finition, une qualité homogène, une répétabilité élevée et une flexibilité maximale. Leur conception intégrée et automatisée permet de combiner plusieurs opérations critiques dans un flux continu, standardisant la qualité et optimisant l’efficacité globale de la production industrielle.
Façonneuses numériques à haute précision
Les façonneuses numériques à haute précision représentent l’évolution la plus avancée dans le domaine du façonnage métallique, offrant un niveau de contrôle, de répétabilité et de finition impossible à atteindre avec les équipements traditionnels. Ces machines sont spécialement conçues pour traiter une grande variété de pièces métalliques, allant des composants ronds ou plats comme fonds de casseroles, couvercles, plateaux et disques aux formes complexes de précision, avec des matériaux tels que l’acier inoxydable, l’aluminium et les alliages spécifiques. Leur objectif principal est d’assurer un façonnage exact des contours et des bords, un calibrage précis des dimensions et une finition uniforme de la surface, tout en maintenant des tolérances extrêmement strictes et une homogénéité parfaite sur l’ensemble de la production, ce qui est essentiel dans les industries où la qualité, la sécurité et l’esthétique sont des critères incontournables. Ces façonneuses intègrent un contrôle numérique sophistiqué qui permet de programmer et d’exécuter chaque opération avec une précision micrométrique, garantissant que même les pièces les plus complexes soient traitées de manière répétable et conforme aux standards industriels les plus élevés.
Le fonctionnement repose sur la combinaison de technologies mécaniques de pointe et de systèmes numériques avancés qui coordonnent tous les aspects du façonnage, depuis le positionnement de la pièce jusqu’au contrôle de l’outil. Les pièces sont introduites automatiquement ou manuellement et maintenues avec précision par des dispositifs de serrage, cales et galets adaptés à leur géométrie et à leurs dimensions. Cette fixation stable est essentielle pour que chaque opération, qu’il s’agisse de détourage, de façonnage des bords ou de lissage de surface, soit réalisée de manière uniforme et répétable sur toutes les pièces. Les outils utilisés, incluant des rouleaux calibrés, galets de façonnage, fraises, disques abrasifs et dispositifs de lissage, sont pilotés par des commandes numériques qui suivent fidèlement les contours programmés, appliquant la force, l’angle et la vitesse exacts nécessaires pour obtenir une finition parfaite. Les machines à haute précision peuvent également combiner plusieurs opérations dans un seul cycle de production, réduisant le besoin de transferts manuels et optimisant l’efficacité du flux de production.
Ces façonneuses numériques sont dotées de capteurs avancés et de systèmes de contrôle en temps réel qui surveillent continuellement la position de la pièce, la force appliquée, l’angle et la vitesse des outils. Ces systèmes permettent d’ajuster automatiquement les paramètres pour maintenir une qualité constante et détecter toute irrégularité ou défaut en cours de processus. Certains modèles intègrent des dispositifs de mesure et de correction automatiques capables de détecter les écarts dimensionnels ou les défauts de surface et de les corriger instantanément, ou d’écarter les pièces non conformes, garantissant ainsi une finition homogène et répétable sur toutes les séries de production. La programmation permet de sauvegarder des profils spécifiques pour chaque type de pièce, facilitant les changements rapides de série, réduisant les temps d’arrêt et augmentant la cadence de production globale.
La flexibilité constitue un atout majeur des façonneuses numériques à haute précision. Elles peuvent traiter des pièces de formes et de dimensions très variées et s’adapter à différents matériaux, tout en permettant d’ajuster rapidement les programmes pour de nouvelles pièces ou séries. Les composants mécaniques et outils sont conçus pour résister à l’usure et aux contraintes mécaniques élevées, tandis que les systèmes de lubrification et de refroidissement garantissent une performance constante et prolongent la durée de vie des équipements. Les machines modernes permettent également l’intégration de modules supplémentaires tels que le contrôle dimensionnel automatique, la détection des défauts de surface et la gestion des pièces non conformes, offrant un contrôle total sur la production et garantissant que chaque pièce respecte les normes les plus strictes.
À la sortie des façonneuses numériques à haute précision, les pièces présentent des contours parfaitement définis, des bords lisses et uniformes et des dimensions calibrées avec exactitude, prêtes pour l’assemblage, le revêtement ou le polissage final. Ces machines assurent un façonnage précis et homogène, garantissant sécurité, esthétique et conformité aux normes industrielles, tout en augmentant considérablement la cadence de production et en réduisant le recours aux interventions manuelles. Elles permettent de standardiser complètement la production sur toutes les séries et d’obtenir une qualité uniforme et répétable même dans des ateliers à forte complexité de pièces ou à haute cadence.
En résumé, les façonneuses numériques à haute précision représentent un investissement stratégique essentiel pour les lignes de production modernes, offrant un contrôle total sur toutes les opérations de façonnage, une finition homogène, une répétabilité maximale et une flexibilité accrue. Leur conception intégrée et programmable permet de combiner plusieurs opérations critiques dans un flux automatisé, standardisant la qualité et optimisant l’efficacité globale de la production industrielle.
Les façonneuses numériques à haute précision représentent aujourd’hui l’une des technologies les plus avancées dans le domaine du façonnage et de la finition des pièces métalliques, combinant automatisation complète, contrôle numérique de pointe, répétabilité parfaite et cadence élevée pour répondre aux exigences des lignes de production industrielles modernes. Ces machines sont capables de traiter une vaste gamme de pièces, allant des fonds de casseroles, couvercles et plateaux aux disques, anneaux et composants techniques complexes, en matériaux divers tels que l’acier inoxydable, l’aluminium ou des alliages spécifiques, tout en assurant des contours parfaitement définis, des arêtes arrondies, des bords uniformes et des surfaces calibrées avec précision, respectant des tolérances dimensionnelles extrêmement strictes. Leur principal atout réside dans la capacité d’exécuter de manière intégrée plusieurs opérations critiques de production, incluant le détourage, le façonnage des bords, l’ébavurage, le lissage et, dans certains modèles, le calibrage dimensionnel ou le pré-polissage, permettant de réduire drastiquement les interventions manuelles, d’optimiser l’espace occupé dans l’atelier et de standardiser la qualité sur toutes les séries de production, même dans les environnements à forte complexité de pièces ou à cadence élevée.
Le fonctionnement des façonneuses numériques à haute précision repose sur l’intégration de technologies mécaniques de pointe, de systèmes électromécaniques et de commandes numériques sophistiquées. Les pièces sont introduites automatiquement via des convoyeurs, des systèmes robotisés ou manuellement selon les configurations et contraintes de production, puis positionnées et maintenues avec exactitude grâce à des dispositifs de serrage, cales et galets adaptés à leur géométrie et à leurs dimensions. Cette stabilisation est essentielle pour garantir que chaque opération, qu’il s’agisse du façonnage des bords, du détourage ou du lissage, soit réalisée uniformément et de manière répétable sur toutes les pièces, assurant une qualité constante et conforme aux standards industriels les plus exigeants. Les outils intégrés, incluant des rouleaux calibrés, galets de façonnage, fraises, disques abrasifs et dispositifs de lissage, sont pilotés par des commandes numériques capables de suivre avec exactitude les contours programmés, d’appliquer la force, la vitesse et l’angle requis, d’éliminer les bavures, d’arrondir et renforcer les arêtes, de lisser les surfaces et de calibrer les dimensions selon des tolérances micrométriques, garantissant une finition homogène sur toutes les pièces produites.
Ces façonneuses sont également équipées de capteurs et de systèmes de contrôle avancés qui surveillent en continu la position des pièces, la vitesse, l’angle et la pression des outils, permettant des ajustements automatiques en temps réel pour maintenir une qualité constante. Les modèles les plus perfectionnés intègrent des dispositifs de mesure et de correction automatiques capables de détecter les irrégularités, défauts de surface ou écarts dimensionnels et de corriger immédiatement le processus ou d’écarter les pièces non conformes, garantissant ainsi une finition parfaitement homogène et répétable sur toutes les séries. La programmation de profils spécifiques pour différents types de pièces permet des changements rapides de séries, réduisant considérablement les temps d’arrêt et maximisant la cadence de production globale. La synchronisation avec les convoyeurs et systèmes de manutention automatisée assure un flux continu et homogène, optimisant l’efficacité et minimisant les interventions humaines.
La flexibilité constitue un avantage stratégique majeur des façonneuses numériques à haute précision. Elles peuvent traiter des pièces de formes et dimensions très variées, s’adapter à différents matériaux et modifier rapidement les programmes pour de nouvelles pièces ou séries, tout en maintenant une cadence élevée, une standardisation complète et une répétabilité maximale. Les composants mécaniques et outils sont conçus pour résister aux contraintes mécaniques élevées et à l’usure, tandis que les systèmes de lubrification et de refroidissement garantissent une performance constante et prolongent la durée de vie de la machine. Ces machines modernes peuvent intégrer des modules complémentaires tels que le contrôle dimensionnel automatique, la détection des défauts de surface et la gestion des pièces non conformes, offrant un contrôle total sur la production et assurant que chaque pièce respecte les normes les plus strictes.
À la sortie de ces façonneuses, les pièces présentent des contours parfaitement définis, des bords lisses et uniformes et des dimensions calibrées avec une précision micrométrique, prêtes à être assemblées, polies ou revêtues. Elles assurent un façonnage homogène, précis et sécuritaire, garantissant à la fois l’esthétique et la conformité aux normes industrielles les plus strictes, tout en augmentant considérablement la cadence de production et en réduisant le recours aux opérations manuelles. Ces machines permettent de standardiser entièrement la production sur toutes les séries et d’obtenir une qualité uniforme et répétable, même dans des environnements de production complexes ou à haute cadence.
En résumé, les façonneuses numériques à haute précision représentent un investissement stratégique essentiel pour les lignes de production métallurgiques modernes, offrant un contrôle total sur toutes les opérations de façonnage, une finition homogène, une répétabilité maximale et une flexibilité élevée. Leur conception intégrée et automatisée permet de combiner plusieurs opérations critiques dans un flux continu et programmable, standardisant la qualité et optimisant l’efficacité globale de la production industrielle.
Les façonneuses numériques à haute précision représentent l’apogée des technologies modernes appliquées au façonnage et à la finition des pièces métalliques, offrant un niveau de contrôle, de répétabilité et de qualité inégalé, indispensable dans les ateliers et lignes de production industrielles contemporaines. Conçues pour traiter des pièces de formes et dimensions extrêmement variées, allant des fonds de casseroles, plateaux et couvercles aux disques, anneaux et composants techniques complexes, en acier inoxydable, aluminium et alliages spécifiques, ces machines garantissent un façonnage parfait des contours, des arêtes arrondies, des bords lisses et des surfaces homogènes, tout en respectant des tolérances dimensionnelles extrêmement strictes, ce qui est crucial dans des secteurs où la qualité, la sécurité et l’esthétique sont des critères essentiels. Ces façonneuses permettent d’intégrer en un seul flux de production plusieurs opérations critiques telles que le détourage, le façonnage des bords, l’ébavurage, le lissage, le calibrage dimensionnel et le pré-polissage, réduisant ainsi le recours aux interventions manuelles, standardisant la qualité et optimisant l’espace occupé dans l’atelier, ce qui est particulièrement précieux dans les lignes de production compactes ou à forte densité.
Le fonctionnement repose sur une combinaison sophistiquée de systèmes mécaniques, électromécaniques et numériques, permettant d’assurer une homogénéité et une précision maximale sur toutes les pièces. Les composants sont introduits automatiquement via convoyeurs, systèmes robotisés ou manuellement selon la configuration de production, puis positionnés et maintenus avec exactitude par des cales, galets et dispositifs de serrage adaptés à leur géométrie et leurs dimensions. Cette fixation stable est essentielle pour que chaque opération de détourage, de façonnage des bords ou de lissage soit réalisée uniformément et de manière répétable sur toutes les pièces, assurant une qualité constante et conforme aux standards industriels les plus stricts. Les outils intégrés, tels que rouleaux calibrés, galets de façonnage, fraises, disques abrasifs et dispositifs de lissage, sont pilotés par des commandes numériques capables de suivre avec exactitude les contours programmés, d’appliquer la force, la vitesse et l’angle nécessaires, d’éliminer les bavures, d’arrondir et renforcer les arêtes, de lisser les surfaces et de calibrer les dimensions selon des tolérances micrométriques, garantissant une finition homogène sur toutes les pièces produites. Dans les configurations multi-opérations, plusieurs étapes peuvent être combinées dans un seul cycle, produisant des pièces prêtes pour l’assemblage, le polissage ou le revêtement final sans transfert vers d’autres équipements, ce qui optimise le flux de production et réduit les temps et interventions manuelles.
Ces façonneuses numériques sont également équipées de capteurs avancés et de systèmes de contrôle en temps réel qui surveillent en continu la position des pièces, la vitesse, l’angle et la pression des outils, permettant des ajustements automatiques pour maintenir une qualité constante. Les modèles les plus perfectionnés intègrent des dispositifs de mesure et de correction automatiques capables de détecter toute irrégularité, défaut de surface ou écart dimensionnel et de corriger instantanément le processus ou d’écarter les pièces non conformes, garantissant ainsi une finition parfaitement homogène et répétable sur toutes les séries. La programmation de profils spécifiques pour différents types de pièces permet de changer rapidement de séries, réduisant considérablement les temps d’arrêt et optimisant la cadence de production globale. La synchronisation avec les convoyeurs et systèmes de manutention automatisée assure un flux continu et homogène, maximisant l’efficacité et minimisant les interventions humaines tout en maintenant une cadence élevée et constante.
La flexibilité constitue un atout stratégique majeur des façonneuses numériques à haute précision. Elles peuvent traiter une grande variété de pièces et s’adapter à différents matériaux tout en permettant d’ajuster rapidement les programmes pour de nouvelles pièces ou séries, maintenant une cadence élevée, une standardisation complète et une répétabilité maximale. Les composants mécaniques et outils sont conçus pour résister aux contraintes mécaniques et à l’usure, tandis que les systèmes de lubrification et de refroidissement assurent une performance constante et prolongent la durée de vie de la machine. De plus, ces stations peuvent intégrer des modules complémentaires tels que le contrôle dimensionnel automatique, la détection de défauts de surface ou la gestion des pièces non conformes, offrant un contrôle total sur la production et garantissant que chaque pièce respecte les normes les plus strictes.
À la sortie de ces façonneuses, les pièces présentent des contours parfaitement définis, des bords lisses et uniformes et des dimensions calibrées avec une précision micrométrique, prêtes à être assemblées, polies ou revêtues. Elles assurent un façonnage homogène, précis et sécuritaire, garantissant à la fois l’esthétique et la conformité aux normes industrielles, tout en augmentant considérablement la cadence de production et en réduisant le recours aux opérations manuelles. Elles permettent de standardiser entièrement la production sur toutes les séries et d’obtenir une qualité uniforme et répétable, même dans des environnements de production complexes ou à haute cadence.
En résumé, les façonneuses numériques à haute précision constituent un investissement stratégique majeur pour les lignes de production modernes, offrant un contrôle total sur toutes les opérations de façonnage, une finition homogène, une répétabilité maximale et une flexibilité élevée. Leur conception intégrée et programmable permet de combiner plusieurs opérations critiques dans un flux continu et automatisé, standardisant la qualité et optimisant l’efficacité globale de la production industrielle.
Les façonneuses numériques à haute précision constituent aujourd’hui le summum des technologies de façonnage et de finition des pièces métalliques, offrant un niveau de contrôle, de répétabilité et de qualité inégalé qui répond aux exigences les plus strictes des lignes de production industrielles modernes. Conçues pour traiter une grande variété de pièces métalliques, allant des fonds de casseroles, plateaux et couvercles aux disques, anneaux et composants techniques complexes, en acier inoxydable, aluminium et alliages spécifiques, ces machines permettent d’obtenir un façonnage parfait des contours, des arêtes arrondies, des bords lisses et des surfaces homogènes, tout en respectant des tolérances dimensionnelles extrêmement strictes. L’intégration de plusieurs opérations critiques dans un flux unique et automatisé, incluant le détourage, le façonnage des bords, l’ébavurage, le lissage des surfaces, le calibrage dimensionnel et le pré-polissage, permet de réduire drastiquement les interventions manuelles, d’optimiser l’espace dans l’atelier et de standardiser la qualité sur toutes les séries, même dans des environnements à forte complexité de pièces ou à cadence élevée. Ces machines sont également capables de s’adapter à différents matériaux, garantissant une polyvalence maximale et la possibilité de produire des séries multiples de manière flexible et efficace.
Le fonctionnement repose sur la combinaison de systèmes mécaniques de haute précision, de dispositifs électromécaniques sophistiqués et de commandes numériques avancées, qui assurent une homogénéité et une précision exceptionnelles sur toutes les pièces. Les pièces sont introduites automatiquement via convoyeurs, systèmes robotisés ou manuellement selon les configurations, puis positionnées et maintenues avec exactitude par des cales, galets et dispositifs de serrage adaptés à leur géométrie et à leurs dimensions. Cette stabilisation est indispensable pour que chaque opération, qu’il s’agisse de détourage, de façonnage ou de lissage, soit réalisée de manière uniforme et répétable sur l’ensemble de la production, garantissant une qualité constante et conforme aux normes industrielles les plus strictes. Les outils intégrés, tels que rouleaux calibrés, galets de façonnage, fraises, disques abrasifs et dispositifs de lissage, sont pilotés par des commandes numériques capables de suivre fidèlement les contours programmés, d’appliquer avec exactitude la force, l’angle et la vitesse nécessaires, d’éliminer les bavures, d’arrondir et renforcer les arêtes, de lisser les surfaces et de calibrer les dimensions avec une précision micrométrique. Dans les configurations multi-opérations, ces machines permettent d’exécuter plusieurs étapes dans un seul cycle de production, produisant des pièces prêtes pour l’assemblage, le polissage ou le revêtement final sans nécessiter de transfert vers d’autres équipements, ce qui optimise le flux de production et réduit le temps de traitement et les interventions manuelles.
Les façonneuses numériques à haute précision intègrent également des capteurs avancés et des systèmes de contrôle en temps réel qui surveillent en continu la position des pièces, la vitesse, l’angle et la pression des outils, permettant des ajustements automatiques afin de maintenir une qualité constante. Les modèles les plus perfectionnés comprennent des dispositifs de mesure et de correction automatiques capables de détecter les écarts dimensionnels, défauts de surface ou irrégularités et de corriger immédiatement le processus ou d’écarter les pièces non conformes, garantissant ainsi une finition homogène et répétable sur toutes les séries de production. La programmation permet de sauvegarder des profils spécifiques pour différents types de pièces, facilitant les changements rapides de série, réduisant considérablement les temps d’arrêt et optimisant la cadence de production globale. La synchronisation avec les convoyeurs et systèmes de manutention automatisée assure un flux continu et homogène, maximisant l’efficacité et minimisant les interventions humaines, tout en maintenant une cadence élevée et constante.
La flexibilité constitue un avantage stratégique majeur des façonneuses numériques à haute précision. Elles peuvent traiter une grande variété de pièces, s’adapter à différents matériaux et ajuster rapidement les programmes pour de nouvelles pièces ou séries, tout en maintenant une cadence élevée, une standardisation complète et une répétabilité maximale. Les composants mécaniques et outils sont conçus pour résister aux contraintes élevées et à l’usure, tandis que les systèmes de lubrification et de refroidissement assurent une performance constante et prolongent la durée de vie des équipements. Ces stations peuvent également intégrer des modules complémentaires tels que le contrôle dimensionnel automatique, la détection de défauts de surface ou la gestion des pièces non conformes, offrant un contrôle total sur la production et garantissant que chaque pièce respecte les normes les plus strictes.
À la sortie de ces machines, les pièces présentent des contours parfaitement définis, des bords lisses et uniformes et des dimensions calibrées avec une précision micrométrique, prêtes à être assemblées, polies ou revêtues. Elles assurent un façonnage homogène, précis et sécuritaire, garantissant à la fois l’esthétique et la conformité aux normes industrielles, tout en augmentant considérablement la cadence de production et en réduisant le recours aux interventions manuelles. Ces façonneuses permettent de standardiser entièrement la production sur toutes les séries et d’obtenir une qualité uniforme et répétable, même dans des environnements de production complexes ou à haute cadence.
En résumé, les façonneuses numériques à haute précision constituent un investissement stratégique essentiel pour les lignes de production modernes, offrant un contrôle total sur toutes les opérations de façonnage, une finition homogène, une répétabilité maximale et une flexibilité élevée. Leur conception intégrée et programmable permet de combiner plusieurs opérations critiques dans un flux continu et automatisé, standardisant la qualité et optimisant l’efficacité globale de la production industrielle.
Machines de finition CNC
Les machines de finition CNC représentent aujourd’hui l’un des piliers de la production industrielle moderne, combinant précision extrême, automatisation complète et polyvalence pour répondre aux besoins des ateliers métallurgiques et des lignes de production à haute cadence. Ces machines sont conçues pour assurer la finition des pièces métalliques avec un niveau de détail et de répétabilité impossible à obtenir avec des méthodes manuelles ou semi-automatiques. Elles peuvent traiter une vaste gamme de pièces, allant des fonds de casseroles, couvercles et plateaux aux composants circulaires ou complexes en acier inoxydable, aluminium et alliages spécifiques, en garantissant des contours parfaitement définis, des arêtes lisses, des bords uniformes et des surfaces homogènes et calibrées, respectant des tolérances dimensionnelles extrêmement strictes. Les machines de finition CNC permettent d’intégrer plusieurs étapes critiques dans un flux automatisé, incluant le polissage, l’ébavurage, le lissage, l’arrondi des bords et parfois le calibrage dimensionnel ou le pré-polissage, réduisant ainsi les interventions manuelles, standardisant la qualité et optimisant le flux de production dans les ateliers modernes.
Le fonctionnement des machines de finition CNC repose sur l’association de technologies mécaniques de haute précision et de systèmes numériques avancés, permettant d’exécuter chaque opération avec une exactitude micrométrique. Les pièces sont introduites via convoyeurs automatisés, systèmes robotisés ou dispositifs de préhension manuels, puis positionnées et maintenues avec précision par des cales, galets et dispositifs de serrage adaptés à leur géométrie et à leurs dimensions. Cette stabilisation est essentielle pour que chaque opération, qu’il s’agisse de polissage, de lissage, d’ébavurage ou d’arrondi des bords, soit réalisée de manière uniforme et répétable sur toutes les pièces, garantissant une qualité constante et conforme aux standards industriels les plus stricts. Les outils utilisés, tels que meules abrasives, fraises de finition, disques de polissage, galets de lissage ou rouleaux calibrés, sont pilotés par des commandes numériques capables de suivre fidèlement les contours programmés, d’appliquer la vitesse, la pression et l’angle requis et de traiter les surfaces avec un haut niveau de précision, permettant d’obtenir un état de surface uniforme et esthétique sur toutes les pièces produites.
Ces machines intègrent également des capteurs et des systèmes de contrôle en temps réel qui surveillent en continu la position des pièces, la force appliquée par les outils, la vitesse et l’angle de rotation, permettant des ajustements automatiques instantanés pour maintenir une qualité constante. Les modèles les plus avancés disposent de dispositifs de mesure et de correction automatiques capables de détecter les irrégularités, défauts de surface ou écarts dimensionnels, et de corriger immédiatement le processus ou d’écarter les pièces non conformes, garantissant ainsi une finition homogène et répétable sur toutes les séries. La programmation des profils spécifiques pour chaque type de pièce permet de réaliser des changements rapides de série, réduisant considérablement les temps d’arrêt et augmentant la cadence globale de production. La synchronisation avec les convoyeurs et systèmes de manutention automatisée assure un flux continu et homogène, maximisant l’efficacité et réduisant le recours aux interventions humaines, tout en maintenant une cadence élevée et constante.
La flexibilité constitue un avantage stratégique majeur des machines de finition CNC. Elles peuvent traiter des pièces de différentes formes et dimensions et s’adapter à divers matériaux tout en permettant de modifier rapidement les programmes pour de nouvelles pièces ou séries, assurant une production standardisée, homogène et répétable. Les composants mécaniques et les outils sont conçus pour résister à l’usure et aux contraintes mécaniques élevées, tandis que les systèmes de lubrification et de refroidissement garantissent des performances constantes et prolongent la durée de vie des équipements. Les machines modernes peuvent également intégrer des modules complémentaires, tels que le contrôle dimensionnel automatique, la détection de défauts de surface et la gestion des pièces non conformes, offrant ainsi un contrôle complet sur la production et garantissant que chaque pièce respecte les normes industrielles les plus strictes.
À la sortie des machines de finition CNC, chaque pièce présente des contours parfaitement définis, des bords lisses et uniformes et des surfaces calibrées et polies avec une précision micrométrique, prêtes à être assemblées, revêtues ou conditionnées. Elles assurent un état de surface homogène, précis et sécuritaire, garantissant à la fois l’esthétique et la conformité aux normes industrielles, tout en augmentant considérablement la cadence de production et en réduisant le recours aux interventions manuelles. Ces machines permettent de standardiser la production sur toutes les séries, offrant une qualité uniforme et répétable, même dans les environnements de production complexes ou à haute cadence.
En résumé, les machines de finition CNC représentent un investissement stratégique incontournable pour les lignes de production métallurgiques modernes, offrant un contrôle total sur toutes les opérations de finition, une répétabilité maximale, une flexibilité élevée et une qualité homogène sur l’ensemble des séries produites. Leur conception intégrée et programmable permet de combiner plusieurs opérations critiques dans un flux automatisé, standardisant la qualité et optimisant l’efficacité globale de la production industrielle.
Les machines de finition CNC représentent le sommet de la technologie appliquée à la finition industrielle des pièces métalliques, alliant automatisation complète, précision extrême et flexibilité maximale pour répondre aux exigences des lignes de production modernes. Ces machines sont capables de traiter une gamme extrêmement variée de pièces, allant des fonds de casseroles, couvercles, plateaux et disques aux composants circulaires ou complexes, en acier inoxydable, aluminium ou alliages spécifiques, en garantissant des contours parfaitement définis, des arêtes arrondies, des bords lisses et des surfaces uniformes et calibrées avec des tolérances dimensionnelles très strictes. Leur principal avantage réside dans la capacité à combiner plusieurs opérations critiques dans un flux unique et automatisé, telles que le polissage, le lissage, l’ébavurage, l’arrondi des bords, le calibrage dimensionnel ou le pré-polissage, permettant de réduire considérablement les interventions manuelles, de standardiser la qualité et d’optimiser le flux de production même dans des ateliers à forte densité ou à cadence élevée. Ces machines offrent également une grande adaptabilité aux différents matériaux et types de pièces, garantissant une polyvalence et une flexibilité maximales pour répondre aux exigences des productions modernes et multi-séries.
Le fonctionnement repose sur une combinaison sophistiquée de systèmes mécaniques de précision et de technologies numériques avancées, assurant un façonnage et une finition homogènes sur toutes les pièces. Les composants sont introduits automatiquement via des convoyeurs, systèmes robotisés ou dispositifs de préhension, puis positionnés et maintenus avec exactitude par des cales, galets et dispositifs de serrage adaptés à chaque géométrie et dimension. Cette stabilisation est essentielle pour que chaque opération, qu’il s’agisse de polissage, de lissage, d’ébavurage ou d’arrondi des bords, soit réalisée uniformément et de manière répétable, garantissant une qualité constante et conforme aux standards industriels les plus exigeants. Les outils, incluant meules abrasives, fraises de finition, disques de polissage, galets de lissage et rouleaux calibrés, sont pilotés par des commandes numériques capables de suivre fidèlement les contours programmés, d’appliquer la force, l’angle et la vitesse exacts, d’éliminer les bavures, d’arrondir et renforcer les arêtes, de lisser les surfaces et de calibrer les dimensions avec précision micrométrique, assurant une finition homogène et uniforme sur toutes les pièces produites. Dans les configurations multi-opérations, plusieurs étapes peuvent être combinées dans un seul cycle, produisant des pièces prêtes à être assemblées, polies ou revêtues sans transfert vers d’autres équipements, ce qui réduit le temps de traitement et augmente l’efficacité globale de la production.
Ces machines intègrent également des capteurs sophistiqués et des systèmes de contrôle en temps réel qui surveillent en continu la position des pièces, la pression, la vitesse et l’angle des outils, permettant des ajustements automatiques pour maintenir une qualité constante. Les modèles les plus avancés disposent de dispositifs de mesure et de correction automatiques capables de détecter irrégularités, défauts de surface ou écarts dimensionnels, et de corriger immédiatement le processus ou d’écarter les pièces non conformes, assurant une finition homogène et répétable sur toutes les séries de production. La programmation de profils spécifiques pour chaque type de pièce permet des changements rapides de série, réduisant les temps d’arrêt et augmentant la cadence globale. La synchronisation avec les convoyeurs et systèmes de manutention automatisée garantit un flux continu et homogène, maximisant l’efficacité et réduisant le besoin d’intervention humaine tout en maintenant une cadence élevée et constante.
La flexibilité constitue un avantage stratégique majeur des machines de finition CNC. Elles peuvent traiter des pièces de formes et dimensions très variées et s’adapter à différents matériaux, tout en permettant de modifier rapidement les programmes pour de nouvelles séries, assurant une production homogène, standardisée et répétable. Les composants mécaniques et outils sont conçus pour résister à l’usure et aux contraintes mécaniques élevées, tandis que les systèmes de lubrification et de refroidissement garantissent des performances constantes et prolongent la durée de vie des équipements. Les machines modernes peuvent également intégrer des modules complémentaires tels que le contrôle dimensionnel automatique, la détection des défauts de surface et la gestion des pièces non conformes, offrant ainsi un contrôle complet sur la production et garantissant que chaque pièce respecte les normes industrielles les plus strictes.
À la sortie des machines de finition CNC, les pièces présentent des contours parfaitement définis, des bords lisses et uniformes, et des surfaces calibrées et polies avec une précision micrométrique, prêtes à être assemblées, revêtues ou conditionnées. Elles assurent un état de surface homogène et précis, garantissant sécurité, esthétique et conformité aux normes industrielles, tout en augmentant la cadence de production et en réduisant le recours aux interventions manuelles. Elles permettent de standardiser entièrement la production sur toutes les séries et d’obtenir une qualité uniforme et répétable, même dans des environnements de production complexes ou à haute cadence.
En résumé, les machines de finition CNC constituent un investissement stratégique essentiel pour les lignes de production métallurgiques modernes, offrant un contrôle total sur toutes les opérations de finition, une répétabilité maximale, une flexibilité élevée et une qualité homogène sur toutes les séries produites. Leur conception intégrée et programmable permet de combiner plusieurs opérations critiques dans un flux automatisé, standardisant la qualité et optimisant l’efficacité globale de la production industrielle.
Les machines de finition CNC représentent aujourd’hui l’apogée de la technologie appliquée à la transformation et à la finition des pièces métalliques, offrant un niveau de précision, de répétabilité et d’efficacité sans équivalent dans les lignes de production modernes. Ces équipements sont conçus pour traiter une gamme extrêmement variée de pièces métalliques, allant des fonds de casseroles, couvercles, plateaux et disques aux composants techniques complexes aux formes circulaires ou asymétriques, en matériaux tels que l’acier inoxydable, l’aluminium, les alliages spéciaux ou même certains métaux composites, garantissant des contours parfaitement définis, des arêtes arrondies, des bords lisses et des surfaces homogènes et calibrées, tout en respectant des tolérances dimensionnelles strictes et constantes sur chaque pièce produite. La valeur ajoutée de ces machines réside dans leur capacité à combiner plusieurs opérations critiques en un flux unique et automatisé, comprenant le polissage, l’ébavurage, le lissage, l’arrondi des bords, le calibrage dimensionnel, le pré-polissage et parfois même le micro-rectifiage de surface, réduisant ainsi les interventions manuelles, augmentant la standardisation et optimisant l’efficacité globale de l’atelier, même dans des environnements à forte densité ou à haute cadence. Ces machines offrent une adaptabilité exceptionnelle, permettant de produire des séries variées avec des exigences différentes tout en conservant une qualité homogène et une répétabilité maximale, ce qui est essentiel dans les industries où la précision et l’esthétique sont primordiales.
Le fonctionnement repose sur l’intégration de systèmes mécaniques de haute précision, de commandes CNC avancées et de dispositifs électromécaniques sophistiqués, assurant que chaque pièce est traitée de manière uniforme et conforme aux spécifications les plus exigeantes. Les pièces sont introduites via convoyeurs automatisés, systèmes robotisés ou dispositifs de préhension, puis positionnées et maintenues avec exactitude par des cales, galets et dispositifs de serrage adaptés à chaque géométrie et dimension. Cette stabilisation est essentielle pour garantir que chaque opération, qu’il s’agisse de polissage, de lissage, d’ébavurage ou d’arrondi des bords, soit exécutée avec précision, homogénéité et répétabilité sur toutes les pièces. Les outils de finition, tels que les meules abrasives, fraises de finition, disques de polissage, galets de lissage et rouleaux calibrés, sont pilotés par des commandes numériques capables de suivre fidèlement les contours programmés, d’appliquer avec exactitude la force, l’angle et la vitesse requis et de traiter les surfaces avec un niveau de détail micrométrique, garantissant un état de surface uniforme, esthétique et conforme aux normes industrielles. Dans les configurations multi-opérations, plusieurs étapes peuvent être combinées dans un seul cycle, produisant des pièces prêtes pour l’assemblage, le polissage final ou le revêtement sans transfert vers d’autres équipements, ce qui réduit le temps de traitement et augmente considérablement l’efficacité globale de la production.
Ces machines intègrent des capteurs avancés et des systèmes de contrôle en temps réel qui surveillent continuellement la position des pièces, la force appliquée, la vitesse et l’angle des outils, permettant des ajustements automatiques instantanés afin de maintenir une qualité constante. Les modèles les plus sophistiqués intègrent des dispositifs de mesure et de correction automatiques capables de détecter les irrégularités, défauts de surface ou écarts dimensionnels et de corriger immédiatement le processus ou d’écarter les pièces non conformes, garantissant ainsi une finition homogène et répétable sur toutes les séries de production. La programmation permet de sauvegarder des profils spécifiques pour chaque type de pièce, facilitant les changements rapides de série, réduisant les temps d’arrêt et augmentant la cadence globale de production. La synchronisation avec les convoyeurs et systèmes de manutention automatisée assure un flux continu et homogène, maximisant l’efficacité et réduisant la dépendance aux interventions humaines tout en maintenant une cadence élevée et constante.
La flexibilité constitue un avantage stratégique majeur de ces machines CNC. Elles peuvent traiter des pièces de formes et dimensions très variées et s’adapter à différents matériaux, tout en permettant de modifier rapidement les programmes pour de nouvelles séries, assurant une production homogène, standardisée et répétable. Les composants mécaniques et les outils sont conçus pour résister à l’usure et aux contraintes mécaniques élevées, tandis que les systèmes de lubrification et de refroidissement garantissent une performance constante et prolongent la durée de vie de la machine. Ces équipements peuvent également intégrer des modules complémentaires, tels que le contrôle dimensionnel automatique, la détection de défauts de surface, le tri des pièces non conformes et le suivi complet de la production, offrant ainsi un contrôle total sur chaque étape et garantissant que chaque pièce respecte les standards les plus stricts de qualité et de sécurité.
À la sortie des machines de finition CNC, les pièces présentent des contours parfaitement définis, des bords lisses et uniformes et des surfaces calibrées, polies et esthétiques, prêtes à être assemblées, revêtues ou conditionnées. Elles assurent un état de surface homogène et précis, garantissant sécurité, esthétique et conformité aux normes industrielles, tout en augmentant la cadence de production et en réduisant le recours aux interventions manuelles. Ces machines permettent de standardiser entièrement la production sur toutes les séries et d’obtenir une qualité uniforme et répétable, même dans des environnements de production complexes ou à haute cadence.
En résumé, les machines de finition CNC constituent un investissement stratégique majeur pour les ateliers et lignes de production métallurgiques modernes, offrant un contrôle total sur toutes les opérations de finition, une répétabilité maximale, une flexibilité élevée et une qualité homogène sur toutes les pièces produites. Leur conception intégrée et programmable permet de combiner plusieurs opérations critiques dans un flux automatisé, standardisant la qualité et optimisant l’efficacité globale de la production industrielle.
Je peux continuer en créant un dossier extrêmement détaillé et technique sur les machines de finition CNC, couvrant chaque type de machine, tous les outils et dispositifs utilisés, les séquences de traitement automatisées, les systèmes de contrôle et de correction intégrés, les configurations possibles pour différents types de pièces et matériaux, ainsi que des stratégies avancées pour l’intégration optimale dans des lignes de production industrielles modernes à haute cadence et qualité maximale.
Systèmes de détourage assistés par ordinateur
Les systèmes de détourage assistés par ordinateur représentent une évolution majeure dans le domaine de la production industrielle, offrant un niveau de précision, de contrôle et d’automatisation largement supérieur aux méthodes traditionnelles. Ces systèmes sont conçus pour traiter des pièces métalliques ou composites de formes variées, allant des fonds de casseroles, couvercles et plateaux aux composants circulaires ou complexes, en matériaux tels que l’acier inoxydable, l’aluminium ou les alliages spécifiques, garantissant des contours parfaitement définis, des bords nets et des surfaces uniformes. L’avantage principal des systèmes de détourage assistés par ordinateur réside dans leur capacité à combiner la puissance mécanique des machines avec la flexibilité et la précision de la programmation numérique, permettant de réaliser des opérations répétables, homogènes et conformes aux standards industriels les plus exigeants, tout en réduisant le recours aux interventions manuelles et en minimisant les erreurs liées à la manipulation humaine.
Ces systèmes reposent sur l’intégration de logiciels de conception assistée par ordinateur (CAO) et de commandes numériques (CNC) qui traduisent les profils et contours programmés en trajectoires précises pour les outils de détourage. Les pièces sont introduites automatiquement ou manuellement dans le système, puis positionnées et maintenues avec exactitude par des dispositifs de serrage et de calage adaptés à leur géométrie et à leurs dimensions. Cette fixation stable est essentielle pour garantir que chaque opération de découpe ou de détourage soit exécutée avec une précision maximale, en maintenant l’uniformité et la répétabilité sur toutes les pièces produites. Les outils de détourage, tels que lames rotatives, couteaux à profil, fraises ou dispositifs de découpe laser ou plasma selon les modèles, sont pilotés par les systèmes numériques pour suivre fidèlement les contours programmés, appliquer la force et l’angle requis, et réaliser une découpe nette et précise sur l’ensemble de la surface. Ces systèmes permettent également de combiner plusieurs opérations dans un même cycle, telles que le détourage, l’ébavurage et le pré-lissage, optimisant ainsi le flux de production et réduisant le temps de traitement.
L’un des aspects les plus avancés de ces systèmes est l’intégration de capteurs et de dispositifs de contrôle en temps réel qui surveillent constamment la position des pièces, la vitesse, l’angle et la force appliquée par l’outil, permettant d’ajuster automatiquement les paramètres pour corriger toute variation ou irrégularité détectée. Les systèmes les plus perfectionnés incluent des modules de mesure et de correction automatiques capables de détecter les écarts dimensionnels, les défauts de surface ou les imperfections du matériau et de corriger immédiatement le processus ou d’éliminer les pièces non conformes, garantissant ainsi une qualité homogène et répétable sur toutes les séries de production. La programmation des profils de détourage permet de sauvegarder différents modèles pour différents types de pièces, facilitant les changements rapides de série et réduisant les temps d’arrêt tout en maintenant une cadence de production élevée et constante.
La flexibilité constitue un avantage stratégique majeur des systèmes de détourage assistés par ordinateur. Ils peuvent traiter une grande variété de formes, de tailles et de matériaux et s’adapter rapidement aux nouvelles séries, offrant une production homogène et standardisée. Les composants mécaniques et les outils sont conçus pour résister aux contraintes mécaniques et à l’usure, tandis que les systèmes de lubrification, de refroidissement et d’aspiration des déchets assurent des performances stables et prolongent la durée de vie des équipements. Ces systèmes peuvent également intégrer des modules complémentaires tels que le contrôle dimensionnel automatique, la détection des défauts de surface et la gestion des pièces non conformes, offrant un contrôle total sur la production et garantissant que chaque pièce respecte les normes industrielles les plus strictes.
À la sortie des systèmes de détourage assistés par ordinateur, les pièces présentent des contours parfaitement définis, des bords nets et des surfaces calibrées, prêtes à être assemblées, polies ou revêtues. Elles assurent une découpe homogène, précise et sécurisée, garantissant la qualité, l’esthétique et la conformité aux normes industrielles, tout en augmentant considérablement la cadence de production et en réduisant le recours aux interventions manuelles. Ces systèmes permettent de standardiser entièrement la production sur toutes les séries et d’obtenir une qualité uniforme et répétable, même dans des environnements de production complexes ou à forte cadence.
En résumé, les systèmes de détourage assistés par ordinateur constituent un investissement stratégique essentiel pour les lignes de production modernes, offrant un contrôle total sur toutes les opérations de découpe et de détourage, une répétabilité maximale, une flexibilité élevée et une qualité homogène sur toutes les séries produites. Leur conception intégrée et programmable permet de combiner plusieurs opérations critiques dans un flux automatisé, standardisant la qualité et optimisant l’efficacité globale de la production industrielle.
Les systèmes de détourage assistés par ordinateur constituent aujourd’hui une technologie incontournable pour la production industrielle de pièces métalliques et composites de haute précision, offrant un niveau de contrôle, d’automatisation et de répétabilité inégalé par les méthodes traditionnelles. Ces systèmes sont capables de traiter des pièces aux formes et dimensions extrêmement variées, depuis les fonds de casseroles, couvercles et plateaux jusqu’aux composants circulaires ou complexes utilisés dans l’industrie technique et électromécanique, en acier inoxydable, aluminium, alliages spéciaux ou matériaux composites. La combinaison de la puissance mécanique des machines avec la précision de la programmation numérique permet de réaliser des contours parfaitement définis, des arêtes nettes et des surfaces homogènes, en respectant des tolérances dimensionnelles extrêmement strictes sur chaque pièce produite, ce qui est essentiel pour des lignes de production à haute cadence où la qualité, l’esthétique et la conformité aux normes industrielles sont des critères incontournables.
Ces systèmes reposent sur l’intégration avancée de logiciels de conception assistée par ordinateur (CAO) et de commandes numériques (CNC) qui traduisent les modèles et profils programmés en trajectoires précises pour les outils de découpe. Les pièces sont introduites automatiquement via convoyeurs, systèmes robotisés ou manuellement, puis positionnées et maintenues avec exactitude grâce à des dispositifs de serrage et de calage adaptés à leur géométrie et à leurs dimensions. Cette stabilisation est cruciale pour garantir que chaque opération de découpe ou de détourage soit exécutée avec une précision maximale, assurant une répétabilité homogène et constante sur toutes les pièces produites. Les outils de détourage, qui peuvent inclure des lames rotatives, couteaux profilés, fraises haute précision, lasers ou systèmes plasma selon le type de machine et de matériau, sont pilotés par les systèmes numériques afin de suivre avec exactitude les contours programmés, d’appliquer la force et l’angle nécessaires et d’obtenir une découpe nette, précise et reproductible sur l’ensemble de la surface. Ces systèmes permettent également d’intégrer plusieurs opérations dans un seul cycle, incluant le détourage, l’ébavurage, le pré-lissage et parfois même le micro-polissage, optimisant ainsi le flux de production et réduisant le temps de traitement ainsi que la manipulation manuelle.
L’un des aspects les plus avancés de ces systèmes réside dans l’intégration de capteurs et de dispositifs de contrôle en temps réel qui surveillent continuellement la position des pièces, la vitesse et l’angle de l’outil, la pression appliquée et la qualité de coupe, permettant d’ajuster automatiquement les paramètres en temps réel afin de corriger toute variation ou irrégularité détectée. Les modèles les plus perfectionnés sont équipés de dispositifs de mesure et de correction automatiques capables de détecter les écarts dimensionnels, défauts de surface ou imperfections du matériau et d’adapter instantanément le processus ou d’écarter les pièces non conformes, garantissant une qualité homogène et répétable sur toutes les séries de production. La programmation permet de sauvegarder différents profils pour différents types de pièces, facilitant les changements rapides de série et réduisant considérablement les temps d’arrêt tout en maintenant une cadence de production élevée et constante. La synchronisation avec les convoyeurs et systèmes de manutention automatisée assure un flux continu, homogène et optimisé, maximisant l’efficacité et réduisant le recours aux interventions humaines.
La flexibilité constitue un avantage stratégique majeur de ces systèmes de détourage assistés par ordinateur. Ils sont capables de traiter des pièces de formes, tailles et matériaux variés, tout en permettant de modifier rapidement les programmes pour de nouvelles séries, garantissant ainsi une production standardisée, homogène et répétable. Les composants mécaniques et les outils sont conçus pour résister à l’usure et aux contraintes mécaniques élevées, tandis que les systèmes de lubrification, de refroidissement et d’évacuation des déchets assurent une performance stable et prolongent la durée de vie des équipements. Les systèmes modernes peuvent également intégrer des modules complémentaires tels que le contrôle dimensionnel automatique, la détection des défauts de surface, le tri des pièces non conformes et la traçabilité complète de la production, offrant ainsi un contrôle total sur chaque étape et garantissant que toutes les pièces respectent les normes industrielles les plus strictes.
À la sortie de ces systèmes, les pièces présentent des contours parfaitement définis, des arêtes nettes et des surfaces calibrées, prêtes à être assemblées, polies, revêtues ou conditionnées. Elles assurent une découpe homogène, précise et sécurisée, garantissant à la fois qualité, esthétique et conformité aux normes industrielles, tout en augmentant considérablement la cadence de production et en réduisant le recours aux interventions manuelles. Ces systèmes permettent de standardiser entièrement la production sur toutes les séries et d’obtenir une qualité uniforme et répétable, même dans des environnements de production complexes ou à forte cadence.
En résumé, les systèmes de détourage assistés par ordinateur constituent un investissement stratégique essentiel pour les lignes de production industrielles modernes, offrant un contrôle total sur toutes les opérations de découpe et de détourage, une répétabilité maximale, une flexibilité élevée et une qualité homogène sur toutes les séries produites. Leur conception intégrée et programmable permet de combiner plusieurs opérations critiques dans un flux automatisé, standardisant la qualité et optimisant l’efficacité globale de la production industrielle.
Les systèmes de détourage assistés par ordinateur représentent l’évolution la plus avancée dans le façonnage industriel des pièces métalliques et composites, intégrant les technologies mécaniques, numériques et logicielles pour offrir un niveau de précision, de contrôle et d’automatisation inégalé. Ces systèmes sont conçus pour traiter une variété extrêmement large de pièces, allant des fonds de casseroles, couvercles et plateaux jusqu’aux composants circulaires ou complexes destinés à des applications techniques, mécaniques ou électromécaniques, en matériaux tels que l’acier inoxydable, l’aluminium, les alliages spéciaux et certains composites. La combinaison de la puissance mécanique des machines avec la programmation numérique permet de réaliser des contours parfaitement définis, des arêtes nettes et des surfaces homogènes, en respectant des tolérances dimensionnelles extrêmement strictes sur toutes les pièces, garantissant ainsi une qualité homogène et répétable, essentielle dans les lignes de production modernes à haute cadence où l’efficacité, l’esthétique et la conformité aux normes industrielles sont prioritaires.
Ces systèmes reposent sur l’intégration de logiciels de conception assistée par ordinateur (CAO) et de commandes numériques (CNC), qui traduisent les modèles et contours programmés en trajectoires exactes pour les outils de découpe. Les pièces sont introduites automatiquement par des convoyeurs, systèmes robotisés ou manuellement, puis positionnées et maintenues avec une précision absolue grâce à des dispositifs de serrage et de calage adaptés à leur géométrie et à leurs dimensions. Cette fixation stable est cruciale pour assurer que chaque opération de découpe, qu’il s’agisse de détourage, d’ébavurage ou de pré-lissage, soit réalisée de manière parfaitement répétable et uniforme, garantissant une qualité constante sur toutes les séries de production. Les outils de détourage, pouvant inclure des lames rotatives, couteaux profilés, fraises haute précision, lasers ou dispositifs plasma selon le matériau et le type de machine, sont pilotés par des systèmes numériques qui suivent avec exactitude les contours programmés, appliquent la force et l’angle requis et garantissent une découpe nette et précise sur l’ensemble de la pièce. La possibilité de combiner plusieurs opérations dans un seul cycle, incluant le détourage, l’ébavurage et le pré-polissage, permet d’optimiser le flux de production, de réduire le temps de traitement et de limiter les interventions manuelles tout en augmentant la cadence globale.
L’une des caractéristiques majeures de ces systèmes est l’intégration de capteurs et de dispositifs de contrôle en temps réel, qui surveillent en continu la position des pièces, la vitesse, l’angle et la pression appliquée par l’outil, permettant des ajustements automatiques instantanés pour corriger toute variation ou défaut détecté. Les modèles les plus sophistiqués intègrent des modules de mesure et de correction automatiques capables de détecter les écarts dimensionnels, les défauts de surface ou les imperfections du matériau et d’adapter immédiatement le processus ou d’écarter les pièces non conformes, garantissant ainsi une finition homogène et répétable sur toutes les séries. La programmation de profils spécifiques pour différents types de pièces permet des changements rapides de série, réduisant les temps d’arrêt et augmentant la cadence de production, tandis que la synchronisation avec les convoyeurs et systèmes de manutention automatisée assure un flux continu et homogène, maximisant l’efficacité et minimisant la nécessité d’intervention humaine.
La flexibilité est un atout stratégique fondamental de ces systèmes. Ils peuvent traiter des pièces aux formes, tailles et matériaux très variés, tout en permettant d’adapter rapidement les programmes pour de nouvelles séries, garantissant ainsi une production homogène, standardisée et répétable. Les composants mécaniques et les outils sont conçus pour résister à l’usure et aux contraintes mécaniques élevées, tandis que les systèmes de lubrification, de refroidissement et d’aspiration des déchets assurent des performances stables et prolongent la durée de vie des équipements. Ces systèmes peuvent également intégrer des modules complémentaires tels que le contrôle dimensionnel automatique, la détection de défauts de surface, le tri des pièces non conformes, la traçabilité complète et l’enregistrement des données de production, offrant un contrôle total sur chaque étape et garantissant que toutes les pièces produites respectent les standards industriels les plus stricts.
À la sortie de ces systèmes, les pièces présentent des contours parfaitement définis, des arêtes nettes et des surfaces calibrées et homogènes, prêtes à être assemblées, polies, revêtues ou conditionnées. Elles assurent une découpe et un façonnage précis, homogène et sécuritaire, garantissant à la fois la qualité, l’esthétique et la conformité aux normes industrielles, tout en augmentant considérablement la cadence de production et en réduisant le recours aux interventions manuelles. Ces systèmes permettent de standardiser intégralement la production sur toutes les séries et d’obtenir une qualité uniforme et répétable, même dans des environnements complexes ou à forte cadence.
En résumé, les systèmes de détourage assistés par ordinateur constituent un investissement stratégique majeur pour les lignes de production modernes, offrant un contrôle total sur toutes les opérations de découpe et de détourage, une répétabilité maximale, une flexibilité élevée et une qualité homogène sur toutes les séries produites. Leur conception intégrée et programmable permet de combiner plusieurs opérations critiques dans un flux automatisé, standardisant la qualité et optimisant l’efficacité globale de la production industrielle.
Les systèmes de détourage assistés par ordinateur constituent aujourd’hui la technologie de référence pour le façonnage industriel des pièces métalliques et composites, alliant précision extrême, automatisation complète et flexibilité maximale afin de répondre aux exigences des lignes de production modernes. Ces systèmes sont capables de traiter une gamme très étendue de pièces, allant des fonds de casseroles, plateaux et couvercles aux composants circulaires ou complexes destinés à des applications techniques et électromécaniques, en acier inoxydable, aluminium, alliages spécifiques et certains composites, avec des contours parfaitement définis, des arêtes nettes, des bords uniformes et des surfaces calibrées selon des tolérances dimensionnelles très strictes. La combinaison de la puissance mécanique des équipements et de la précision numérique permet d’obtenir une qualité homogène et répétable, essentielle dans les ateliers à haute cadence où l’efficacité, la standardisation et la conformité aux normes industrielles sont des critères fondamentaux. L’intégration de plusieurs opérations dans un seul flux automatisé, telles que le détourage, l’ébavurage, le pré-lissage, le calibrage dimensionnel et parfois le micro-polissage, permet de réduire drastiquement le recours aux interventions manuelles, de limiter les erreurs et d’optimiser le temps de production, offrant ainsi un avantage stratégique considérable aux industriels souhaitant maximiser leur rendement tout en garantissant une qualité constante.
Ces systèmes reposent sur une intégration sophistiquée de logiciels de conception assistée par ordinateur (CAO) et de commandes numériques (CNC) qui traduisent les modèles et profils programmés en trajectoires précises pour les outils de découpe. Les pièces sont introduites via convoyeurs automatisés, systèmes robotisés ou manuellement, puis positionnées et maintenues avec une précision absolue par des dispositifs de serrage et de calage adaptés à la géométrie et aux dimensions spécifiques de chaque pièce. Cette stabilisation est indispensable pour que chaque opération, qu’il s’agisse de détourage, d’ébavurage ou de pré-lissage, soit exécutée de manière uniforme et répétable, garantissant ainsi la qualité et la conformité sur toutes les séries. Les outils de découpe, comprenant des lames rotatives, couteaux profilés, fraises haute précision, lasers ou systèmes plasma selon le type de matériau et de machine, sont pilotés par les systèmes numériques afin de suivre fidèlement les contours programmés, d’appliquer la force, l’angle et la vitesse requis, et d’obtenir une découpe nette et précise sur toute la surface. La possibilité de combiner plusieurs étapes de traitement dans un seul cycle, incluant souvent le détourage, l’ébavurage et le pré-polissage, permet d’optimiser le flux de production, de réduire les temps morts et de limiter les interventions manuelles, tout en augmentant la cadence globale de production.
Un élément clé de ces systèmes est l’intégration de capteurs avancés et de dispositifs de contrôle en temps réel qui surveillent continuellement la position des pièces, la vitesse, l’angle et la pression appliquée par l’outil, permettant des ajustements automatiques instantanés afin de corriger toute variation ou irrégularité détectée. Les modèles les plus perfectionnés sont équipés de dispositifs de mesure et de correction automatiques capables de détecter les écarts dimensionnels, les défauts de surface ou les imperfections du matériau, et de corriger immédiatement le processus ou d’éliminer les pièces non conformes, garantissant ainsi une qualité homogène et répétable sur toutes les séries de production. La programmation des profils spécifiques pour chaque type de pièce permet des changements rapides de série, réduisant considérablement les temps d’arrêt tout en maintenant une cadence élevée et constante. La synchronisation avec les convoyeurs et systèmes de manutention automatisée assure un flux continu et homogène, maximisant l’efficacité, réduisant la dépendance aux interventions humaines et maintenant une production à cadence optimale.
La flexibilité constitue un atout stratégique majeur de ces systèmes de détourage assistés par ordinateur. Ils peuvent traiter des pièces aux formes et dimensions très variées et s’adapter à différents matériaux, tout en permettant d’ajuster rapidement les programmes pour de nouvelles séries, assurant ainsi une production homogène, standardisée et répétable. Les composants mécaniques et les outils sont conçus pour résister à l’usure et aux contraintes mécaniques élevées, tandis que les systèmes de lubrification, de refroidissement et d’aspiration des déchets assurent des performances stables et prolongent la durée de vie des équipements. Ces systèmes peuvent également intégrer des modules complémentaires tels que le contrôle dimensionnel automatique, la détection de défauts de surface, le tri des pièces non conformes, la traçabilité complète et l’enregistrement des données de production, offrant un contrôle total sur chaque étape et garantissant que toutes les pièces produites respectent les normes industrielles les plus strictes.
À la sortie de ces systèmes, les pièces présentent des contours parfaitement définis, des arêtes nettes et des surfaces calibrées et homogènes, prêtes à être assemblées, polies, revêtues ou conditionnées. Elles garantissent une découpe et un façonnage précis, homogène et sécuritaire, assurant la qualité, l’esthétique et la conformité aux normes industrielles, tout en augmentant significativement la cadence de production et en réduisant le recours aux interventions manuelles. Ces systèmes permettent de standardiser entièrement la production sur toutes les séries et d’obtenir une qualité uniforme et répétable, même dans des environnements de production complexes ou à haute cadence.
En résumé, les systèmes de détourage assistés par ordinateur représentent un investissement stratégique majeur pour les ateliers et lignes de production modernes, offrant un contrôle total sur toutes les opérations de découpe et de façonnage, une répétabilité maximale, une flexibilité élevée et une qualité homogène sur toutes les pièces produites. Leur conception intégrée et programmable permet de combiner plusieurs opérations critiques dans un flux automatisé, standardisant la qualité et optimisant l’efficacité globale de la production industrielle.
Je peux continuer en développant un dossier technique extrêmement détaillé sur les systèmes de détourage assistés par ordinateur, incluant chaque type de machine, tous les outils et dispositifs utilisés, les séquences de traitement automatisées, les systèmes de contrôle et de correction intégrés, les configurations possibles pour différents types de pièces et matériaux, ainsi que des stratégies avancées pour leur intégration optimale dans des lignes de production industrielles modernes à haute cadence et qualité maximale.
Détoureuses-façonneuses intelligentes
Les détoureuses-façonneuses intelligentes représentent l’évolution la plus avancée dans le domaine de la finition industrielle des pièces métalliques et composites, combinant automatisation complète, précision extrême et capacités décisionnelles assistées par informatique pour offrir un niveau de performance et de flexibilité inédit. Ces machines sont conçues pour traiter des pièces aux formes variées, allant des fonds de casseroles, couvercles et plateaux jusqu’aux composants circulaires ou complexes utilisés dans l’industrie technique et électromécanique, en matériaux tels que l’acier inoxydable, l’aluminium, les alliages spéciaux et certains composites, garantissant des contours parfaitement définis, des arêtes nettes et des surfaces homogènes avec des tolérances dimensionnelles extrêmement strictes. L’élément différenciateur de ces systèmes réside dans leur capacité à analyser en temps réel l’état des pièces et à adapter automatiquement les paramètres de détourage et de façonnage, offrant ainsi une répétabilité maximale, une qualité uniforme sur toutes les séries et une réduction significative des interventions manuelles et des erreurs liées à l’usure des outils ou aux variations des matériaux.
Le fonctionnement des détoureuses-façonneuses intelligentes repose sur l’intégration de logiciels avancés de contrôle et d’optimisation, capables de recevoir les modèles CAO des pièces, de planifier automatiquement les trajectoires des outils et de réguler les paramètres tels que la vitesse, la pression, l’angle et la force appliquée en fonction des propriétés spécifiques de chaque pièce et des conditions du processus. Les pièces sont introduites via des convoyeurs automatisés, des systèmes robotisés ou manuellement, puis positionnées et maintenues avec précision par des dispositifs de calage et de serrage adaptés à la géométrie et aux dimensions de chaque composant. Cette stabilisation est cruciale pour garantir que chaque opération de détourage, d’ébavurage, de lissage et d’arrondi des bords soit réalisée avec une homogénéité parfaite et une précision micrométrique sur toutes les pièces, assurant ainsi un niveau de qualité conforme aux standards industriels les plus stricts. Les outils de façonnage, comprenant des lames rotatives, fraises, galets de lissage ou rouleaux calibrés, sont pilotés par les systèmes intelligents qui ajustent automatiquement la trajectoire, la force et la vitesse afin de compenser toute variation de matériau, de géométrie ou d’usure des outils, garantissant une finition homogène et constante.
Un des éléments clés des détoureuses-façonneuses intelligentes est la présence de capteurs et de systèmes de mesure en temps réel qui surveillent en continu la position des pièces, la force appliquée, l’angle et la vitesse des outils, ainsi que l’état des surfaces. Ces systèmes permettent de détecter instantanément toute irrégularité ou défaut et d’ajuster automatiquement les paramètres ou d’écarter les pièces non conformes, assurant une qualité optimale et constante sur toutes les séries. Les machines les plus avancées intègrent également des algorithmes d’apprentissage qui analysent les données de production pour anticiper l’usure des outils, optimiser les trajectoires et améliorer la productivité et la qualité globale sur le long terme. La programmation des profils spécifiques pour différents types de pièces permet des changements rapides de série et réduit les temps d’arrêt, tandis que la synchronisation avec les convoyeurs et les systèmes de manutention automatisés assure un flux continu et homogène, maximisant l’efficacité et minimisant le recours aux interventions humaines.
La flexibilité constitue un atout stratégique majeur de ces machines intelligentes. Elles peuvent traiter des pièces de tailles, formes et matériaux très variés, tout en adaptant instantanément les programmes pour de nouvelles séries ou matériaux différents, garantissant une production homogène, standardisée et répétable. Les composants mécaniques et les outils sont conçus pour résister à l’usure et aux contraintes mécaniques élevées, tandis que les systèmes de lubrification, de refroidissement et de nettoyage automatique assurent une performance stable et prolongent la durée de vie des équipements. Les modules complémentaires incluent le contrôle dimensionnel automatique, la détection des défauts de surface, le suivi complet de la production et l’analyse des performances en temps réel, offrant un contrôle total sur chaque étape et garantissant que chaque pièce produite respecte les normes industrielles les plus strictes.
À la sortie des détoureuses-façonneuses intelligentes, les pièces présentent des contours parfaitement définis, des arêtes lisses et homogènes, et des surfaces calibrées et polies, prêtes à être assemblées, revêtues ou conditionnées. Elles assurent une finition uniforme, précise et sécurisée, garantissant la qualité, l’esthétique et la conformité aux normes industrielles, tout en augmentant considérablement la cadence de production et en réduisant le recours aux interventions manuelles. Ces machines permettent de standardiser entièrement la production sur toutes les séries et d’obtenir une qualité uniforme et répétable, même dans des environnements industriels complexes ou à haute cadence.
En résumé, les détoureuses-façonneuses intelligentes représentent un investissement stratégique majeur pour les lignes de production modernes, offrant un contrôle total sur toutes les opérations de détourage et de façonnage, une répétabilité maximale, une flexibilité élevée et une qualité homogène sur toutes les pièces produites. Leur conception intégrée et assistée par informatique permet de combiner plusieurs opérations critiques dans un flux automatisé, standardisant la qualité et optimisant l’efficacité globale de la production industrielle.
Je peux continuer en développant un dossier ultra-complet sur les détoureuses-façonneuses intelligentes, détaillant chaque type de machine, les outils et dispositifs utilisés, les séquences de traitement automatisées, les systèmes de contrôle et d’adaptation intégrés, les configurations possibles pour différents types de pièces et matériaux, ainsi que des stratégies avancées pour leur intégration optimale dans des lignes de production industrielles modernes à haute cadence et qualité maximale.
Les détoureuses-façonneuses intelligentes représentent l’aboutissement de la technologie appliquée à la finition et au façonnage industriel des pièces métalliques et composites, intégrant des capacités de traitement automatisé, de contrôle intelligent et d’adaptation en temps réel afin d’offrir un niveau de performance, de précision et de répétabilité sans précédent. Conçues pour traiter une vaste gamme de pièces, allant des fonds de casseroles, plateaux et couvercles aux composants circulaires ou géométriquement complexes destinés aux secteurs techniques, électromécaniques ou domestiques, elles prennent en charge des matériaux variés tels que l’acier inoxydable, l’aluminium, les alliages spécifiques et certains composites. La combinaison de la puissance mécanique, de l’automatisation et de l’intelligence algorithmique permet de réaliser des contours parfaitement définis, des arêtes nettes, des bords uniformes et des surfaces calibrées avec des tolérances dimensionnelles extrêmement strictes, assurant une homogénéité totale et une qualité répétable sur toutes les séries, ce qui est essentiel dans les environnements de production à haute cadence où la précision, l’esthétique et la conformité aux normes industrielles sont des impératifs.
Ces machines reposent sur une intégration avancée de logiciels de contrôle, de systèmes CNC et de modules d’intelligence artificielle capables d’analyser les données de production en temps réel, d’adapter les paramètres de détourage et de façonnage et d’anticiper l’usure des outils pour maintenir un niveau de qualité optimal. Les pièces sont introduites automatiquement via convoyeurs, systèmes robotisés ou manuellement, puis positionnées et maintenues avec une précision absolue grâce à des dispositifs de serrage et de calage adaptés à leur géométrie et à leurs dimensions. Cette fixation stable est cruciale pour garantir que chaque opération, qu’il s’agisse de détourage, d’ébavurage, de lissage ou d’arrondi des bords, soit effectuée avec une homogénéité parfaite et une précision micrométrique sur toutes les pièces, garantissant un niveau de qualité constant et conforme aux standards industriels les plus stricts. Les outils de façonnage, comprenant lames rotatives, fraises de finition, galets de lissage, rouleaux calibrés ou systèmes laser/plasma selon le matériau, sont pilotés par des systèmes intelligents capables d’ajuster automatiquement la trajectoire, la force, la vitesse et l’angle afin de compenser toute variation de matériau, de géométrie ou d’usure des outils, garantissant une finition homogène et reproductible.
L’un des aspects déterminants de ces machines réside dans leurs capteurs et systèmes de mesure en temps réel, qui surveillent continuellement la position des pièces, la pression appliquée, l’angle et la vitesse des outils ainsi que l’état des surfaces. Ces systèmes permettent de détecter instantanément toute irrégularité, défaut ou variation et d’adapter automatiquement les paramètres ou d’écarter les pièces non conformes, assurant une qualité optimale sur toutes les séries de production. Les détoureuses-façonneuses intelligentes les plus perfectionnées disposent d’algorithmes d’apprentissage capables d’analyser les données historiques et en temps réel pour optimiser les trajectoires, prévoir l’usure des outils et améliorer la productivité et la qualité globale sur le long terme. La programmation de profils spécifiques pour différents types de pièces facilite les changements rapides de série, réduit les temps d’arrêt et maintient une cadence de production élevée et constante, tandis que la synchronisation avec les convoyeurs et systèmes de manutention automatisée assure un flux continu, homogène et optimisé, maximisant l’efficacité tout en minimisant l’intervention humaine.
La flexibilité constitue un avantage stratégique majeur de ces détoureuses-façonneuses intelligentes. Elles peuvent traiter des pièces de formes, tailles et matériaux très variés et ajuster instantanément les programmes pour de nouvelles séries, garantissant une production homogène, standardisée et répétable. Les composants mécaniques et les outils sont conçus pour résister à l’usure et aux contraintes mécaniques élevées, tandis que les systèmes de lubrification, de refroidissement et de nettoyage automatique assurent des performances stables et prolongent la durée de vie des équipements. Les modules complémentaires incluent le contrôle dimensionnel automatique, la détection des défauts de surface, la traçabilité complète et l’enregistrement des données de production, offrant un contrôle total sur chaque étape et garantissant que chaque pièce produite respecte les normes industrielles les plus strictes.
À la sortie de ces machines, les pièces présentent des contours parfaitement définis, des arêtes nettes et des surfaces calibrées, lisses et homogènes, prêtes à être assemblées, polies, revêtues ou conditionnées. Elles assurent une finition uniforme, précise et sécurisée, garantissant la qualité, l’esthétique et la conformité aux normes industrielles tout en augmentant significativement la cadence de production et en réduisant le recours aux interventions manuelles. Ces machines permettent de standardiser intégralement la production sur toutes les séries et d’obtenir une qualité uniforme et répétable, même dans des environnements industriels complexes ou à haute cadence.
En résumé, les détoureuses-façonneuses intelligentes constituent un investissement stratégique majeur pour les lignes de production modernes, offrant un contrôle total sur toutes les opérations de détourage et de façonnage, une répétabilité maximale, une flexibilité élevée et une qualité homogène sur toutes les pièces produites. Leur conception intégrée et assistée par intelligence informatique permet de combiner plusieurs opérations critiques dans un flux automatisé, standardisant la qualité et optimisant l’efficacité globale de la production industrielle.
Les détoureuses-façonneuses intelligentes représentent une avancée technologique majeure dans le domaine de la finition industrielle et du façonnage de pièces métalliques et composites, intégrant des systèmes de contrôle informatisés, des capteurs en temps réel et des algorithmes de régulation adaptative pour offrir un niveau de performance, de précision et de répétabilité sans précédent dans la production industrielle moderne. Ces machines sont conçues pour traiter une gamme extrêmement variée de pièces, allant des fonds de casseroles, plateaux, couvercles et disques aux composants circulaires, ovales ou géométriquement complexes destinés à des applications techniques, électromécaniques ou domestiques, en matériaux tels que l’acier inoxydable, l’aluminium, les alliages spéciaux et certains composites de haute performance. L’intégration de la puissance mécanique des équipements avec la programmation numérique et l’intelligence algorithmique permet de réaliser des contours parfaitement définis, des arêtes nettes, des bords homogènes et des surfaces calibrées avec des tolérances dimensionnelles extrêmement strictes, garantissant une qualité constante et répétable sur toutes les séries de production, ce qui est crucial pour les environnements industriels à haute cadence où la précision, la standardisation et la conformité aux normes industrielles sont des exigences fondamentales.
Ces détoureuses-façonneuses intelligentes combinent des logiciels avancés de contrôle et de pilotage, des modules CNC et des systèmes d’apprentissage automatique capables de planifier automatiquement les trajectoires des outils, de réguler les paramètres tels que la vitesse, la pression, l’angle et la force appliquée, et d’adapter ces paramètres en temps réel en fonction des caractéristiques spécifiques de chaque pièce et des conditions de production. Les pièces sont introduites dans le système via des convoyeurs automatisés, des bras robotisés ou manuellement, puis positionnées et maintenues avec précision grâce à des dispositifs de serrage et de calage adaptés à leur géométrie et à leurs dimensions. Cette stabilisation est indispensable pour garantir que chaque opération de détourage, d’ébavurage, de lissage, d’arrondi des bords ou de pré-polissage soit exécutée avec homogénéité et exactitude micrométrique sur toutes les pièces, assurant ainsi une qualité uniforme et conforme aux standards industriels les plus exigeants. Les outils de façonnage, incluant des lames rotatives, fraises de finition, galets de lissage, rouleaux calibrés et systèmes laser ou plasma selon le matériau et le type de machine, sont pilotés par les systèmes intelligents qui ajustent automatiquement la trajectoire, la force, l’angle et la vitesse afin de compenser toute variation de matériau, de forme ou d’usure des outils, assurant ainsi une finition parfaite et reproductible sur toutes les pièces.
Un des aspects essentiels de ces machines réside dans leurs capteurs et systèmes de mesure en temps réel, qui surveillent constamment la position des pièces, la pression appliquée, la vitesse et l’angle des outils, ainsi que l’état des surfaces, permettant de détecter instantanément toute irrégularité ou défaut et de corriger automatiquement le processus ou d’écarter les pièces non conformes. Les détoureuses-façonneuses intelligentes les plus avancées disposent de systèmes d’analyse de données et d’algorithmes prédictifs capables d’anticiper l’usure des outils, d’optimiser les trajectoires et d’améliorer la productivité et la qualité globale sur le long terme. La programmation de profils spécifiques pour différents types de pièces permet des changements rapides de série, réduisant les temps d’arrêt et maintenant une cadence élevée et constante, tandis que la synchronisation avec les convoyeurs et les systèmes de manutention automatisée garantit un flux continu et homogène, maximisant l’efficacité et minimisant le besoin d’intervention humaine.
La flexibilité est un avantage stratégique fondamental de ces détoureuses-façonneuses intelligentes. Elles peuvent traiter des pièces de formes, dimensions et matériaux très variés et ajuster instantanément les programmes pour de nouvelles séries, assurant une production standardisée, homogène et répétable. Les composants mécaniques et les outils sont conçus pour résister à l’usure et aux contraintes mécaniques élevées, tandis que les systèmes de lubrification, de refroidissement et de nettoyage automatique assurent des performances stables et prolongent la durée de vie des équipements. Les modules complémentaires incluent le contrôle dimensionnel automatique, la détection des défauts de surface, le tri des pièces non conformes, la traçabilité complète et l’enregistrement des données de production, offrant un contrôle total sur chaque étape et garantissant que toutes les pièces produites respectent les normes industrielles les plus strictes.
À la sortie de ces machines, les pièces présentent des contours parfaitement définis, des arêtes lisses et homogènes, des surfaces calibrées et polies, prêtes à être assemblées, revêtues ou conditionnées. Elles assurent une finition uniforme, précise et sécurisée, garantissant la qualité, l’esthétique et la conformité aux normes industrielles tout en augmentant significativement la cadence de production et en réduisant le recours aux interventions manuelles. Ces détoureuses-façonneuses intelligentes permettent de standardiser entièrement la production sur toutes les séries et d’obtenir une qualité uniforme et répétable, même dans des environnements industriels complexes ou à haute cadence.
En résumé, les détoureuses-façonneuses intelligentes constituent un investissement stratégique majeur pour les ateliers et lignes de production modernes, offrant un contrôle total sur toutes les opérations de détourage et de façonnage, une répétabilité maximale, une flexibilité élevée et une qualité homogène sur toutes les pièces produites. Leur conception intégrée et assistée par intelligence informatique permet de combiner plusieurs opérations critiques dans un flux automatisé, standardisant la qualité et optimisant l’efficacité globale de la production industrielle.
Les détoureuses-façonneuses intelligentes représentent le summum de l’évolution technologique dans le domaine du façonnage industriel et de la finition des pièces métalliques et composites, intégrant à la fois automatisation complète, contrôle informatisé, analyse en temps réel et capacité d’adaptation dynamique pour offrir un niveau de performance, de précision et de répétabilité sans équivalent. Ces machines sont conçues pour traiter une gamme extrêmement vaste de pièces, allant des fonds de casseroles, couvercles, plateaux et disques aux composants circulaires, ovales ou complexes utilisés dans des applications techniques, électromécaniques et domestiques, en acier inoxydable, aluminium, alliages spécifiques et certains composites de haute performance. La combinaison de la puissance mécanique, de l’intelligence algorithmique et de la programmation numérique permet de réaliser des contours parfaitement définis, des arêtes nettes et homogènes, des bords calibrés et des surfaces parfaitement lisses avec des tolérances dimensionnelles extrêmement strictes, garantissant une qualité constante et répétable sur toutes les séries de production, un critère indispensable pour les environnements industriels à haute cadence où la précision, la standardisation et la conformité aux normes industrielles sont essentielles.
Le fonctionnement de ces machines repose sur l’intégration de logiciels avancés de contrôle et d’optimisation, de systèmes CNC et de modules intelligents capables de planifier automatiquement les trajectoires des outils, de réguler la vitesse, la pression, l’angle et la force appliquée en fonction des caractéristiques spécifiques de chaque pièce et des conditions de production en temps réel. Les pièces sont introduites via convoyeurs automatisés, bras robotisés ou manuellement, puis positionnées et maintenues avec précision grâce à des dispositifs de serrage et de calage adaptés à leur géométrie et à leurs dimensions. Cette fixation stable est indispensable pour garantir que chaque opération, qu’il s’agisse de détourage, d’ébavurage, de lissage, de calibrage des bords ou de pré-polissage, soit exécutée avec homogénéité et exactitude micrométrique sur toutes les pièces, assurant un niveau de qualité uniforme et conforme aux standards industriels les plus stricts. Les outils de façonnage, comprenant lames rotatives, fraises de finition, galets de lissage, rouleaux calibrés et systèmes laser ou plasma selon le matériau, sont pilotés par les systèmes intelligents qui ajustent automatiquement la trajectoire, la force, l’angle et la vitesse afin de compenser toute variation de matériau, de géométrie ou d’usure des outils, garantissant une finition homogène, précise et reproductible.
L’un des éléments essentiels de ces détoureuses-façonneuses intelligentes réside dans la présence de capteurs et de systèmes de mesure en temps réel, capables de surveiller en continu la position des pièces, la force appliquée, la vitesse et l’angle des outils, ainsi que l’état des surfaces, permettant de détecter immédiatement toute irrégularité ou défaut et de corriger automatiquement le processus ou d’écarter les pièces non conformes. Les machines les plus avancées intègrent également des algorithmes d’apprentissage et des systèmes d’analyse prédictive qui utilisent les données historiques et en temps réel pour anticiper l’usure des outils, optimiser les trajectoires, améliorer la qualité globale et maximiser la productivité à long terme. La programmation de profils spécifiques pour différents types de pièces facilite les changements rapides de série, réduit les temps d’arrêt et maintient une cadence de production élevée et constante, tandis que la synchronisation avec les convoyeurs et les systèmes de manutention automatisée assure un flux continu et homogène, maximisant l’efficacité globale et minimisant le recours aux interventions humaines.
La flexibilité constitue un avantage stratégique majeur de ces machines intelligentes. Elles sont capables de traiter des pièces de formes, tailles et matériaux très variés, tout en adaptant instantanément les programmes pour de nouvelles séries ou matériaux différents, assurant une production standardisée, homogène et répétable. Les composants mécaniques et les outils sont conçus pour résister à l’usure et aux contraintes mécaniques élevées, tandis que les systèmes de lubrification, de refroidissement et de nettoyage automatique assurent une performance stable et prolongent la durée de vie des équipements. Les modules complémentaires incluent le contrôle dimensionnel automatique, la détection des défauts de surface, la traçabilité complète, l’enregistrement des données de production et l’optimisation des cycles de maintenance, offrant un contrôle total sur chaque étape et garantissant que chaque pièce produite respecte les normes industrielles les plus strictes.
À la sortie de ces détoureuses-façonneuses intelligentes, les pièces présentent des contours parfaitement définis, des arêtes lisses et homogènes, des surfaces calibrées et polies, prêtes à être assemblées, revêtues ou conditionnées. Elles assurent une finition uniforme, précise et sécurisée, garantissant la qualité, l’esthétique et la conformité aux normes industrielles, tout en augmentant considérablement la cadence de production et en réduisant le recours aux interventions manuelles. Ces machines permettent de standardiser entièrement la production sur toutes les séries et d’obtenir une qualité uniforme et répétable, même dans les environnements industriels les plus complexes ou à haute cadence.
En résumé, les détoureuses-façonneuses intelligentes représentent un investissement stratégique essentiel pour les lignes de production modernes, offrant un contrôle total sur toutes les opérations de détourage et de façonnage, une répétabilité maximale, une flexibilité exceptionnelle et une qualité homogène sur toutes les pièces produites. Leur conception intégrée et assistée par intelligence informatique permet de combiner plusieurs opérations critiques dans un flux automatisé, standardisant la qualité et optimisant l’efficacité globale de la production industrielle.
Cellules robotisées de finition
Les cellules robotisées de finition représentent l’intégration la plus avancée des technologies robotiques, mécaniques et numériques pour le traitement final des pièces métalliques et composites dans les environnements industriels modernes, permettant un façonnage, un polissage et un détourage automatisés, précis et hautement répétables. Ces cellules sont conçues pour traiter des pièces de formes variées, allant des fonds de casseroles, plateaux et couvercles aux composants circulaires ou géométriquement complexes destinés à des applications techniques, électromécaniques ou domestiques, en matériaux tels que l’acier inoxydable, l’aluminium, les alliages spéciaux et certains composites de haute performance. L’intégration de bras robotisés à haute précision avec des systèmes de contrôle informatisés permet de réaliser des contours parfaitement définis, des arêtes nettes et homogènes, des surfaces calibrées et lisses avec des tolérances dimensionnelles extrêmement strictes, assurant une qualité constante et répétable sur toutes les séries, ce qui est essentiel pour les lignes de production à haute cadence où la qualité, l’esthétique et la conformité aux normes industrielles sont des impératifs.
Ces cellules robotisées sont composées de bras articulés ou SCARA, équipés d’outils de finition spécialisés tels que brosses, meules, lames rotatives, rouleaux calibrés, galets de lissage ou systèmes laser/plasma selon la nature du matériau et la tâche à accomplir. Les pièces sont introduites automatiquement via convoyeurs ou systèmes de manutention robotisés, positionnées et maintenues avec précision grâce à des dispositifs de calage adaptatifs, garantissant une fixation stable pendant toutes les opérations de détourage, de polissage, de lissage et d’arrondi des bords. Les systèmes informatiques associés aux robots pilotent les trajectoires, la vitesse, la pression et l’angle appliqués par les outils, adaptant en temps réel ces paramètres selon la géométrie, la dimension, le matériau et l’état de surface de chaque pièce afin d’assurer une finition homogène et parfaitement reproductible. Les algorithmes d’intelligence intégrés permettent d’anticiper l’usure des outils, de corriger automatiquement les déviations et d’optimiser les cycles de travail, ce qui maximise la qualité et la productivité tout en réduisant le besoin d’intervention humaine et les risques d’erreur.
L’un des aspects essentiels de ces cellules robotisées est l’intégration de capteurs avancés et de systèmes de mesure en temps réel, qui surveillent continuellement la position des pièces, l’angle et la force appliquée par les outils, la vitesse de rotation ou de déplacement et l’état des surfaces. Ces systèmes permettent de détecter instantanément toute irrégularité ou défaut et d’ajuster automatiquement les paramètres ou d’écarter les pièces non conformes, garantissant ainsi une qualité homogène et répétable sur toutes les séries. Les cellules les plus perfectionnées disposent également de systèmes de vision et de reconnaissance de formes qui identifient automatiquement les contours des pièces, ajustent les trajectoires des robots et optimisent le cycle de production, assurant une adaptation dynamique aux variations de pièces ou de matériaux.
La flexibilité de ces cellules constitue un avantage stratégique majeur. Elles peuvent traiter des pièces aux formes, tailles et matériaux très divers, et leurs programmes peuvent être modifiés rapidement pour de nouvelles séries, garantissant une production standardisée, homogène et répétable. Les composants mécaniques et les outils sont conçus pour résister à l’usure et aux contraintes mécaniques élevées, tandis que les systèmes de lubrification, de refroidissement et d’évacuation des déchets assurent une performance stable et prolongent la durée de vie des équipements. Les modules complémentaires incluent le contrôle dimensionnel automatique, la détection des défauts de surface, le tri des pièces non conformes, la traçabilité complète et l’enregistrement des données de production, offrant un contrôle total sur chaque étape et garantissant que toutes les pièces produites respectent les standards industriels les plus stricts.
À la sortie des cellules robotisées de finition, les pièces présentent des contours parfaitement définis, des arêtes lisses et homogènes et des surfaces calibrées et polies, prêtes à être assemblées, revêtues ou conditionnées. Elles assurent une finition uniforme, précise et sécurisée, garantissant la qualité, l’esthétique et la conformité aux normes industrielles, tout en augmentant considérablement la cadence de production et en réduisant le recours aux interventions manuelles. Ces cellules permettent de standardiser intégralement la production sur toutes les séries et d’obtenir une qualité uniforme et répétable, même dans des environnements industriels complexes ou à haute cadence.
En résumé, les cellules robotisées de finition constituent un investissement stratégique majeur pour les lignes de production modernes, offrant un contrôle total sur toutes les opérations de polissage, détourage et façonnage, une répétabilité maximale, une flexibilité exceptionnelle et une qualité homogène sur toutes les pièces produites. Leur conception intégrée, automatisée et assistée par intelligence informatique permet de combiner plusieurs opérations critiques dans un flux totalement automatisé, standardisant la qualité et optimisant l’efficacité globale de la production industrielle.
Les cellules robotisées de finition représentent aujourd’hui l’apogée de l’automatisation industrielle dans le domaine du façonnage et du polissage des pièces métalliques et composites, combinant robotique avancée, intelligence numérique, contrôle en temps réel et capacité d’adaptation dynamique pour offrir un niveau de performance, de précision et de répétabilité inégalé. Ces systèmes sont capables de traiter une variété extrêmement large de pièces, allant des fonds de casseroles, plateaux et couvercles aux composants circulaires, ovales ou géométriquement complexes utilisés dans des applications techniques, électromécaniques ou domestiques, en acier inoxydable, aluminium, alliages spécifiques et certains composites de haute performance. La combinaison de la puissance mécanique des robots, de la programmation CNC et de l’intelligence algorithmique permet d’obtenir des contours parfaitement définis, des arêtes nettes et homogènes, des bords calibrés et des surfaces lisses avec des tolérances dimensionnelles extrêmement strictes, assurant une qualité constante et répétable sur toutes les séries de production, ce qui est indispensable dans les environnements industriels à haute cadence où la précision, la standardisation et la conformité aux normes industrielles sont impératives.
Ces cellules robotisées sont constituées de bras articulés ou SCARA de haute précision, équipés d’outils spécialisés tels que brosses, meules, lames rotatives, galets de lissage, rouleaux calibrés et systèmes laser ou plasma, selon le matériau et l’application. Les pièces sont introduites automatiquement par des convoyeurs, systèmes de manutention robotisés ou manuellement, puis positionnées et maintenues avec précision grâce à des dispositifs de calage et de serrage adaptés à leur géométrie et à leurs dimensions. Cette fixation stable est essentielle pour garantir que chaque opération — qu’il s’agisse de détourage, d’ébavurage, de lissage, de polissage ou de calibrage des bords — soit effectuée avec homogénéité et exactitude micrométrique sur toutes les pièces, assurant un niveau de qualité uniforme et conforme aux standards industriels les plus exigeants. Les systèmes intelligents pilotant les outils ajustent automatiquement la trajectoire, la vitesse, l’angle et la force appliquée pour compenser les variations de matériau, les différences dimensionnelles ou l’usure des outils, garantissant ainsi une finition parfaitement homogène et répétable.
Un des éléments déterminants de ces cellules est la présence de capteurs et de systèmes de mesure en temps réel, qui surveillent constamment la position des pièces, la pression exercée par les outils, l’angle, la vitesse et l’état des surfaces, permettant de détecter immédiatement toute irrégularité ou défaut et d’ajuster automatiquement les paramètres ou d’écarter les pièces non conformes. Les systèmes les plus sophistiqués intègrent également des modules d’analyse prédictive et d’intelligence artificielle capables d’anticiper l’usure des outils, d’optimiser les trajectoires, d’adapter les paramètres de production en temps réel et d’améliorer la productivité globale sur le long terme. La programmation de profils spécifiques pour chaque type de pièce permet des changements rapides de série, réduit les temps d’arrêt et maintient une cadence de production élevée et constante, tandis que la synchronisation avec les convoyeurs et systèmes de manutention automatisée assure un flux continu et homogène, maximisant l’efficacité et minimisant le recours aux interventions humaines.
La flexibilité est un atout stratégique majeur de ces cellules robotisées de finition. Elles peuvent traiter des pièces aux formes, dimensions et matériaux très divers, et leurs programmes peuvent être ajustés instantanément pour de nouvelles séries, garantissant une production homogène, standardisée et répétable. Les composants mécaniques et les outils sont conçus pour résister à l’usure et aux contraintes mécaniques importantes, tandis que les systèmes de lubrification, de refroidissement et d’évacuation automatique des déchets assurent des performances stables et prolongent la durée de vie des équipements. Les modules complémentaires incluent le contrôle dimensionnel automatique, la détection des défauts de surface, le tri des pièces non conformes, la traçabilité complète et l’enregistrement des données de production, offrant un contrôle total sur chaque étape et garantissant que chaque pièce produite respecte les normes industrielles les plus strictes.
À la sortie de ces cellules, les pièces présentent des contours parfaitement définis, des arêtes lisses et homogènes et des surfaces calibrées, polies et prêtes à être assemblées, revêtues ou conditionnées. Elles garantissent une finition uniforme, précise et sécurisée, assurant la qualité, l’esthétique et la conformité aux normes industrielles tout en augmentant considérablement la cadence de production et en réduisant le recours aux interventions manuelles. Ces cellules permettent de standardiser entièrement la production sur toutes les séries et d’obtenir une qualité homogène et répétable, même dans les environnements industriels les plus complexes ou à haute cadence.
En résumé, les cellules robotisées de finition constituent un investissement stratégique essentiel pour les lignes de production modernes, offrant un contrôle total sur toutes les opérations de polissage, détourage et façonnage, une répétabilité maximale, une flexibilité exceptionnelle et une qualité homogène sur toutes les pièces produites. Leur conception intégrée, automatisée et assistée par intelligence informatique permet de combiner plusieurs opérations critiques dans un flux entièrement automatisé, standardisant la qualité et optimisant l’efficacité globale de la production industrielle.
Les cellules robotisées de finition constituent le sommet de l’automatisation industrielle moderne dans le domaine de la transformation et de la finition des pièces métalliques et composites, intégrant de manière transparente la robotique avancée, les systèmes de contrôle numérique, l’intelligence artificielle et les capteurs en temps réel pour offrir un niveau de performance, de précision et de répétabilité inégalé. Conçues pour traiter une gamme extrêmement variée de pièces, des fonds de casseroles, plateaux, couvercles et disques aux composants circulaires, ovales ou géométriquement complexes destinés à des applications techniques, électromécaniques et domestiques, ces cellules prennent en charge des matériaux divers tels que l’acier inoxydable, l’aluminium, les alliages spéciaux et certains composites de haute performance. La combinaison de la puissance mécanique des bras robotisés, de la programmation CNC et des algorithmes intelligents permet d’obtenir des contours parfaitement définis, des arêtes nettes et homogènes, des bords calibrés et des surfaces lisses, avec des tolérances dimensionnelles extrêmement strictes, assurant une qualité constante et répétable sur toutes les séries de production, ce qui est indispensable pour les lignes à haute cadence où la précision, la standardisation et la conformité aux normes industrielles sont critiques.
Le fonctionnement de ces cellules repose sur des bras articulés ou SCARA à haute précision équipés d’outils spécialisés tels que brosses, meules, lames rotatives, galets de lissage, rouleaux calibrés ou systèmes laser/plasma, selon le matériau et la tâche à réaliser. Les pièces sont introduites automatiquement via convoyeurs, systèmes robotisés ou manuellement, puis positionnées et maintenues avec exactitude grâce à des dispositifs de calage et de serrage adaptatifs, garantissant une fixation stable pendant toutes les opérations de détourage, ébavurage, lissage, polissage et calibrage des bords. Les systèmes intelligents pilotant les robots régulent en permanence la trajectoire, la vitesse, la pression et l’angle des outils afin de compenser toute variation de matériau, de géométrie ou d’usure, assurant une finition homogène, précise et parfaitement reproductible sur toutes les pièces. Les algorithmes d’apprentissage et de contrôle prédictif permettent d’anticiper l’usure des outils, d’optimiser les trajectoires, d’adapter les paramètres de production en temps réel et d’améliorer la productivité globale, réduisant ainsi les interventions humaines et les risques d’erreur.
Un des éléments clés de ces cellules réside dans l’intégration de capteurs avancés et de systèmes de mesure en temps réel, capables de surveiller constamment la position des pièces, la force appliquée, l’angle, la vitesse et l’état des surfaces. Ces systèmes détectent immédiatement toute irrégularité ou défaut et permettent des ajustements automatiques ou l’élimination des pièces non conformes, garantissant une qualité homogène et répétable sur toutes les séries. Les cellules les plus perfectionnées intègrent également des systèmes de vision et de reconnaissance de formes qui identifient automatiquement les contours des pièces, ajustent les trajectoires des robots et optimisent les cycles de production pour une adaptation dynamique aux variations de pièces ou de matériaux. La programmation de profils spécifiques pour chaque type de pièce permet des changements rapides de série, réduit les temps d’arrêt et maintient une cadence élevée et constante, tandis que la synchronisation avec les convoyeurs et les systèmes de manutention automatisée assure un flux continu et homogène, maximisant l’efficacité globale et minimisant le recours aux interventions humaines.
La flexibilité constitue un avantage stratégique majeur. Ces cellules peuvent traiter des pièces de formes, tailles et matériaux très variés, et leurs programmes peuvent être ajustés instantanément pour de nouvelles séries, garantissant une production standardisée, homogène et répétable. Les composants mécaniques et les outils sont conçus pour résister à l’usure et aux contraintes mécaniques importantes, tandis que les systèmes de lubrification, de refroidissement et d’évacuation automatique des déchets assurent une performance stable et prolongent la durée de vie des équipements. Les modules complémentaires incluent le contrôle dimensionnel automatique, la détection des défauts de surface, le tri des pièces non conformes, la traçabilité complète et l’enregistrement des données de production, offrant un contrôle total sur chaque étape et garantissant que toutes les pièces produites respectent les normes industrielles les plus strictes.
À la sortie des cellules robotisées de finition, les pièces présentent des contours parfaitement définis, des arêtes lisses et homogènes et des surfaces calibrées et polies, prêtes à être assemblées, revêtues ou conditionnées. Elles assurent une finition uniforme, précise et sécurisée, garantissant la qualité, l’esthétique et la conformité aux normes industrielles tout en augmentant considérablement la cadence de production et en réduisant le recours aux interventions manuelles. Ces cellules permettent de standardiser entièrement la production sur toutes les séries et d’obtenir une qualité homogène et répétable, même dans les environnements industriels complexes ou à haute cadence.
En résumé, les cellules robotisées de finition représentent un investissement stratégique essentiel pour les lignes de production modernes, offrant un contrôle total sur toutes les opérations de polissage, détourage et façonnage, une répétabilité maximale, une flexibilité exceptionnelle et une qualité homogène sur toutes les pièces produites. Leur conception intégrée, automatisée et assistée par intelligence informatique permet de combiner plusieurs opérations critiques dans un flux entièrement automatisé, standardisant la qualité et optimisant l’efficacité globale de la production industrielle.
Les cellules robotisées de finition représentent l’intégration la plus avancée des technologies industrielles modernes dans le façonnage et la finition des pièces métalliques et composites, combinant de manière optimale robotique avancée, systèmes CNC, intelligence artificielle, capteurs de haute précision et analyse en temps réel pour offrir un niveau de performance, de précision, de répétabilité et de flexibilité inégalé. Ces systèmes sont conçus pour traiter une gamme extrêmement large de pièces, allant des fonds de casseroles, plateaux, couvercles et disques aux composants circulaires, ovales ou géométriquement complexes destinés à des applications techniques, électromécaniques, domestiques ou industrielles spécialisées, utilisant des matériaux variés comme l’acier inoxydable, l’aluminium, les alliages spécifiques et certains composites de haute performance. La combinaison de la puissance mécanique des bras robotisés avec la programmation CNC et l’intelligence algorithmique permet d’obtenir des contours parfaitement définis, des arêtes nettes et homogènes, des bords calibrés et des surfaces lisses avec des tolérances dimensionnelles extrêmement strictes, assurant une qualité constante et répétable sur toutes les séries de production, ce qui est essentiel dans les environnements industriels à haute cadence où la précision, la standardisation et la conformité aux normes les plus strictes sont impératives.
Le fonctionnement de ces cellules repose sur des bras articulés, SCARA ou delta de haute précision, équipés d’outils spécialisés tels que brosses, meules, lames rotatives, galets de lissage, rouleaux calibrés ou systèmes laser/plasma selon la nature du matériau et la tâche à accomplir. Les pièces sont introduites automatiquement via convoyeurs, systèmes de manutention robotisés ou manuellement, puis positionnées et maintenues avec exactitude grâce à des dispositifs de calage et de serrage adaptatifs, garantissant une fixation stable pendant toutes les opérations de détourage, ébavurage, lissage, polissage et calibrage des bords. Les systèmes intelligents pilotant les robots régulent en permanence la trajectoire, la vitesse, l’angle et la force appliquée par les outils afin de compenser toute variation de matériau, de forme ou d’usure des outils, assurant une finition homogène, précise et parfaitement reproductible sur toutes les pièces. Les algorithmes d’apprentissage et de contrôle prédictif permettent d’anticiper l’usure des outils, d’optimiser les trajectoires, d’adapter les paramètres de production en temps réel et d’améliorer la productivité globale, réduisant ainsi le recours aux interventions humaines et minimisant les risques d’erreur et de non-conformité.
Un élément central de ces cellules réside dans l’intégration de capteurs et de systèmes de mesure en temps réel, capables de surveiller continuellement la position des pièces, la pression exercée, l’angle et la vitesse des outils, ainsi que l’état des surfaces, permettant de détecter immédiatement toute irrégularité ou défaut et de corriger automatiquement le processus ou d’écarter les pièces non conformes, garantissant une qualité homogène et répétable sur toutes les séries de production. Les cellules les plus perfectionnées disposent également de systèmes de vision et de reconnaissance de formes qui identifient automatiquement les contours des pièces, ajustent les trajectoires des robots et optimisent les cycles de production pour une adaptation dynamique aux variations de pièces ou de matériaux. La programmation de profils spécifiques pour différents types de pièces facilite les changements rapides de série, réduit les temps d’arrêt et maintient une cadence élevée et constante, tandis que la synchronisation avec les convoyeurs et les systèmes de manutention automatisée assure un flux continu et homogène, maximisant l’efficacité globale et réduisant le recours aux interventions humaines.
La flexibilité constitue un avantage stratégique majeur de ces cellules. Elles sont capables de traiter des pièces aux formes, dimensions et matériaux très variés et de s’adapter instantanément à de nouvelles séries, garantissant une production standardisée, homogène et répétable. Les composants mécaniques et les outils sont conçus pour résister à l’usure et aux contraintes mécaniques importantes, tandis que les systèmes de lubrification, de refroidissement et d’évacuation automatique des copeaux ou poussières assurent des performances stables et prolongent la durée de vie des équipements. Les modules complémentaires incluent le contrôle dimensionnel automatique, la détection des défauts de surface, le tri des pièces non conformes, la traçabilité complète et l’enregistrement des données de production, offrant un contrôle total sur chaque étape et garantissant que toutes les pièces produites respectent les normes industrielles les plus strictes.
À la sortie de ces cellules, les pièces présentent des contours parfaitement définis, des arêtes lisses et homogènes et des surfaces calibrées et polies, prêtes à être assemblées, revêtues ou conditionnées. Elles assurent une finition uniforme, précise et sécurisée, garantissant la qualité, l’esthétique et la conformité aux normes industrielles tout en augmentant considérablement la cadence de production et en réduisant le recours aux interventions manuelles. Ces cellules permettent de standardiser entièrement la production sur toutes les séries et d’obtenir une qualité homogène et répétable, même dans les environnements industriels complexes ou à haute cadence.
En résumé, les cellules robotisées de finition représentent un investissement stratégique majeur pour les lignes de production modernes, offrant un contrôle total sur toutes les opérations de polissage, détourage et façonnage, une répétabilité maximale, une flexibilité exceptionnelle et une qualité homogène sur toutes les pièces produites. Leur conception intégrée, automatisée et assistée par intelligence informatique permet de combiner plusieurs opérations critiques dans un flux entièrement automatisé, standardisant la qualité et optimisant l’efficacité globale de la production industrielle.
Je peux continuer en produisant un dossier complet et ultra-technique sur les cellules robotisées de finition, détaillant chaque type de cellule, tous les outils et dispositifs utilisés, les séquences de traitement automatisées, les systèmes de contrôle et d’adaptation en temps réel, les configurations possibles pour différents types de pièces et matériaux, ainsi que des stratégies avancées pour leur intégration optimale dans des lignes de production industrielles modernes à haute cadence et qualité maximale.
Machines automatisées de détourage et façonnage
Les machines automatisées de détourage et de façonnage constituent aujourd’hui une solution incontournable pour les lignes de production industrielles modernes, combinant automatisation complète, contrôle numérique avancé, capteurs de précision et intelligence artificielle pour réaliser des opérations complexes avec une précision, une répétabilité et une productivité maximales. Ces machines sont capables de traiter une très grande variété de pièces, allant des fonds de casseroles, plateaux et couvercles aux composants circulaires, ovales ou géométriquement complexes utilisés dans les secteurs domestiques, électromécaniques et techniques, en matériaux tels que l’acier inoxydable, l’aluminium, les alliages spéciaux et certains composites de haute performance. L’intégration de systèmes CNC, de modules intelligents et d’outils de façonnage spécialisés permet d’obtenir des contours parfaitement définis, des arêtes nettes et homogènes, des bords calibrés et des surfaces lisses, tout en respectant des tolérances dimensionnelles extrêmement strictes, assurant une qualité uniforme et répétable sur toutes les séries de production, ce qui est essentiel pour des environnements industriels à haute cadence où la précision et la standardisation sont des exigences fondamentales.
Ces machines automatisées combinent des convoyeurs de pièces, des systèmes de manutention robotisés, des bras articulés et des outils spécialisés tels que lames rotatives, fraises de finition, galets de lissage, rouleaux calibrés et systèmes laser ou plasma selon le matériau et l’application. Les pièces sont positionnées et maintenues avec exactitude grâce à des dispositifs de calage et de serrage adaptés à leur géométrie et à leurs dimensions, garantissant une fixation stable pendant toutes les opérations de détourage, ébavurage, lissage, calibrage et façonnage des bords. Les systèmes intelligents pilotant les outils régulent automatiquement la trajectoire, la vitesse, l’angle et la force appliquée, compensant les variations de matériau, les différences dimensionnelles ou l’usure des outils, afin de garantir une finition homogène et parfaitement reproductible sur toutes les pièces. Les algorithmes intégrés permettent d’anticiper l’usure des outils, d’optimiser les trajectoires, de réguler les paramètres de production en temps réel et d’améliorer la productivité globale tout en réduisant les interventions humaines et les risques d’erreurs.
L’un des aspects essentiels de ces machines réside dans l’intégration de capteurs et de systèmes de mesure en temps réel capables de surveiller en permanence la position des pièces, la pression appliquée, l’angle, la vitesse des outils et l’état des surfaces. Ces systèmes permettent de détecter immédiatement toute irrégularité ou défaut et d’ajuster automatiquement les paramètres de fonctionnement ou d’écarter les pièces non conformes, garantissant une qualité homogène et répétable sur toutes les séries. Les machines les plus perfectionnées incluent également des systèmes de vision et de reconnaissance de formes qui identifient automatiquement les contours des pièces, ajustent les trajectoires des outils et optimisent les cycles de production pour une adaptation dynamique aux variations de pièces ou de matériaux. La programmation de profils spécifiques pour chaque type de pièce facilite les changements rapides de série, réduit les temps d’arrêt et maintient une cadence élevée et constante, tandis que la synchronisation avec les convoyeurs et les systèmes de manutention automatisée assure un flux continu et homogène, maximisant l’efficacité globale.
La flexibilité constitue un avantage stratégique majeur de ces machines automatisées de détourage et de façonnage. Elles sont capables de traiter des pièces de formes, tailles et matériaux très divers et d’adapter instantanément les programmes pour de nouvelles séries, garantissant une production standardisée, homogène et répétable. Les composants mécaniques et les outils sont conçus pour résister à l’usure et aux contraintes mécaniques importantes, tandis que les systèmes de lubrification, de refroidissement et de nettoyage automatique assurent une performance stable et prolongent la durée de vie des équipements. Les modules complémentaires incluent le contrôle dimensionnel automatique, la détection des défauts de surface, le tri des pièces non conformes, la traçabilité complète et l’enregistrement des données de production, offrant un contrôle total sur chaque étape et garantissant que toutes les pièces produites respectent les normes industrielles les plus strictes.
À la sortie de ces machines automatisées, les pièces présentent des contours parfaitement définis, des arêtes lisses et homogènes et des surfaces calibrées et polies, prêtes à être assemblées, revêtues ou conditionnées. Elles assurent une finition uniforme, précise et sécurisée, garantissant la qualité, l’esthétique et la conformité aux normes industrielles tout en augmentant considérablement la cadence de production et en réduisant le recours aux interventions manuelles. Ces machines permettent de standardiser entièrement la production sur toutes les séries et d’obtenir une qualité homogène et répétable, même dans les environnements industriels complexes ou à haute cadence.
En résumé, les machines automatisées de détourage et de façonnage représentent un investissement stratégique essentiel pour les lignes de production modernes, offrant un contrôle total sur toutes les opérations de façonnage et de finition, une répétabilité maximale, une flexibilité exceptionnelle et une qualité homogène sur toutes les pièces produites. Leur conception intégrée et automatisée permet de combiner plusieurs opérations critiques dans un flux entièrement automatisé, standardisant la qualité et optimisant l’efficacité globale de la production industrielle.
Les machines automatisées de détourage et de façonnage constituent aujourd’hui le cœur de l’optimisation des lignes de production industrielles modernes, intégrant les technologies les plus avancées en matière de robotique, de contrôle numérique, d’intelligence artificielle et de capteurs de haute précision pour réaliser des opérations complexes avec un niveau de précision, de répétabilité et de productivité inégalé. Ces systèmes sont capables de traiter une grande variété de pièces, allant des fonds de casseroles, plateaux et couvercles aux composants circulaires, ovales ou géométriquement complexes destinés aux secteurs domestiques, électromécaniques et industriels spécialisés, utilisant des matériaux tels que l’acier inoxydable, l’aluminium, les alliages spécifiques et certains composites de haute performance. La combinaison de la puissance mécanique des systèmes automatisés, de la programmation CNC et de l’intelligence algorithmique permet de produire des contours parfaitement définis, des arêtes nettes et homogènes, des bords calibrés et des surfaces lisses avec des tolérances dimensionnelles extrêmement strictes, assurant une qualité constante et répétable sur toutes les séries de production, ce qui est indispensable dans les environnements industriels à haute cadence où la précision, la standardisation et la conformité aux normes industrielles sont des exigences fondamentales.
Ces machines automatisées intègrent des convoyeurs de pièces, des systèmes de manutention robotisés et des outils spécialisés tels que lames rotatives, fraises de finition, galets de lissage, rouleaux calibrés ou systèmes laser et plasma selon le matériau et l’application. Les pièces sont positionnées et maintenues avec une précision extrême grâce à des dispositifs de calage et de serrage adaptés à leur géométrie et à leurs dimensions, assurant une fixation stable tout au long des opérations de détourage, ébavurage, lissage, calibrage et façonnage des bords. Les systèmes intelligents pilotant les outils régulent en permanence la trajectoire, la vitesse, l’angle et la force appliquée afin de compenser toute variation de matériau, toute différence dimensionnelle ou l’usure des outils, garantissant une finition homogène, précise et reproductible sur toutes les pièces. Les algorithmes intégrés permettent d’anticiper l’usure des outils, d’optimiser les trajectoires, de réguler les paramètres de production en temps réel et d’améliorer la productivité globale, réduisant ainsi les interventions humaines et les risques d’erreurs, tout en garantissant un contrôle strict de la qualité sur l’ensemble de la production.
Un des éléments essentiels de ces machines réside dans l’intégration de capteurs et de systèmes de mesure en temps réel, capables de surveiller continuellement la position des pièces, la pression appliquée, l’angle et la vitesse des outils, ainsi que l’état des surfaces, permettant de détecter immédiatement toute irrégularité ou défaut et d’ajuster automatiquement le processus ou d’écarter les pièces non conformes, garantissant une qualité homogène et répétable sur toutes les séries de production. Les machines les plus avancées incluent également des systèmes de vision et de reconnaissance de formes qui identifient automatiquement les contours des pièces, ajustent les trajectoires des outils et optimisent les cycles de production pour une adaptation dynamique aux variations de pièces ou de matériaux. La programmation de profils spécifiques pour chaque type de pièce facilite les changements rapides de série, réduit les temps d’arrêt et maintient une cadence élevée et constante, tandis que la synchronisation avec les convoyeurs et systèmes de manutention automatisée assure un flux continu et homogène, maximisant l’efficacité globale et minimisant le recours aux interventions humaines.
La flexibilité constitue un avantage stratégique majeur de ces machines automatisées de détourage et de façonnage. Elles sont capables de traiter des pièces aux formes, dimensions et matériaux très divers, et leurs programmes peuvent être ajustés instantanément pour de nouvelles séries, garantissant une production standardisée, homogène et répétable. Les composants mécaniques et les outils sont conçus pour résister à l’usure et aux contraintes mécaniques importantes, tandis que les systèmes de lubrification, de refroidissement et d’évacuation automatique des copeaux ou poussières assurent une performance stable et prolongent la durée de vie des équipements. Les modules complémentaires incluent le contrôle dimensionnel automatique, la détection des défauts de surface, le tri des pièces non conformes, la traçabilité complète et l’enregistrement des données de production, offrant un contrôle total sur chaque étape et garantissant que toutes les pièces produites respectent les normes industrielles les plus strictes.
À la sortie de ces machines automatisées, les pièces présentent des contours parfaitement définis, des arêtes lisses et homogènes et des surfaces calibrées et polies, prêtes à être assemblées, revêtues ou conditionnées. Elles assurent une finition uniforme, précise et sécurisée, garantissant la qualité, l’esthétique et la conformité aux normes industrielles tout en augmentant considérablement la cadence de production et en réduisant le recours aux interventions manuelles. Ces machines permettent de standardiser entièrement la production sur toutes les séries et d’obtenir une qualité homogène et répétable, même dans les environnements industriels complexes ou à haute cadence.
En résumé, les machines automatisées de détourage et de façonnage représentent un investissement stratégique majeur pour les lignes de production modernes, offrant un contrôle total sur toutes les opérations de façonnage et de finition, une répétabilité maximale, une flexibilité exceptionnelle et une qualité homogène sur toutes les pièces produites. Leur conception intégrée, automatisée et assistée par intelligence informatique permet de combiner plusieurs opérations critiques dans un flux entièrement automatisé, standardisant la qualité et optimisant l’efficacité globale de la production industrielle.
Les machines automatisées de détourage et de façonnage représentent l’évolution la plus avancée des lignes de production industrielles modernes, intégrant de manière complète et cohérente la robotique de précision, le contrôle CNC, l’intelligence artificielle et les systèmes de capteurs sophistiqués pour garantir des performances maximales en matière de précision, de répétabilité, de cadence et de qualité. Elles sont conçues pour traiter une variété extrêmement large de pièces, allant des fonds de casseroles, plateaux, couvercles et disques aux composants circulaires, ovales ou géométriquement complexes utilisés dans les secteurs domestiques, électromécaniques et industriels spécialisés, en matériaux tels que l’acier inoxydable, l’aluminium, les alliages spécifiques et certains composites de haute performance. Grâce à l’intégration de la puissance mécanique, de la programmation numérique et des algorithmes intelligents, ces machines permettent de produire des contours parfaitement définis, des arêtes nettes et homogènes, des bords calibrés et des surfaces lisses avec des tolérances dimensionnelles extrêmement strictes, assurant une qualité uniforme et répétable sur toutes les séries de production, ce qui est crucial dans des environnements industriels à haute cadence où la standardisation et la conformité aux normes sont des exigences fondamentales.
Ces systèmes automatisés combinent des convoyeurs de pièces, des bras robotisés articulés, SCARA ou delta et des outils de façonnage spécialisés tels que lames rotatives, fraises de finition, galets de lissage, rouleaux calibrés ou systèmes laser et plasma, adaptés selon le matériau et l’application. Les pièces sont positionnées et maintenues avec une précision extrême par des dispositifs de calage et de serrage adaptatifs, garantissant une fixation stable pendant toutes les opérations de détourage, ébavurage, lissage, calibrage et façonnage des bords. Les systèmes intelligents régulent automatiquement la trajectoire, la vitesse, l’angle et la force appliquée par les outils pour compenser toute variation de matériau, toute différence dimensionnelle ou l’usure des outils, garantissant une finition homogène, précise et reproductible sur toutes les pièces. Les algorithmes d’apprentissage et de contrôle prédictif permettent d’anticiper l’usure des outils, d’optimiser les trajectoires, de réguler les paramètres en temps réel et d’améliorer la productivité globale, réduisant les interventions humaines et les risques d’erreurs tout en maintenant un contrôle strict de la qualité sur l’ensemble de la production.
L’intégration de capteurs avancés et de systèmes de mesure en temps réel constitue un élément central de ces machines. Ces capteurs surveillent continuellement la position des pièces, la pression appliquée, l’angle et la vitesse des outils ainsi que l’état des surfaces, permettant de détecter immédiatement toute irrégularité ou défaut et d’ajuster automatiquement les paramètres ou d’écarter les pièces non conformes, garantissant ainsi une qualité homogène et répétable sur toutes les séries. Les machines les plus perfectionnées incorporent également des systèmes de vision et de reconnaissance de formes capables d’identifier automatiquement les contours des pièces, d’ajuster les trajectoires des outils et d’optimiser les cycles de production pour une adaptation dynamique aux variations de pièces ou de matériaux. La programmation de profils spécifiques pour chaque type de pièce facilite les changements rapides de série, réduit les temps d’arrêt et maintient une cadence élevée et constante, tandis que la synchronisation avec les convoyeurs et les systèmes de manutention automatisée assure un flux continu et homogène, maximisant l’efficacité globale et minimisant le recours aux interventions humaines.
La flexibilité constitue un avantage stratégique majeur. Ces machines peuvent traiter des pièces de formes, tailles et matériaux très variés, et leurs programmes peuvent être ajustés instantanément pour de nouvelles séries, garantissant une production standardisée, homogène et répétable. Les composants mécaniques et les outils sont conçus pour résister à l’usure et aux contraintes mécaniques importantes, tandis que les systèmes de lubrification, de refroidissement et d’évacuation automatique des copeaux ou poussières assurent une performance stable et prolongent la durée de vie des équipements. Les modules complémentaires incluent le contrôle dimensionnel automatique, la détection des défauts de surface, le tri des pièces non conformes, la traçabilité complète et l’enregistrement des données de production, offrant un contrôle total sur chaque étape et garantissant que toutes les pièces produites respectent les normes industrielles les plus strictes.
À la sortie de ces machines automatisées, les pièces présentent des contours parfaitement définis, des arêtes lisses et homogènes et des surfaces calibrées et polies, prêtes à être assemblées, revêtues ou conditionnées. Elles assurent une finition uniforme, précise et sécurisée, garantissant la qualité, l’esthétique et la conformité aux normes industrielles tout en augmentant considérablement la cadence de production et en réduisant le recours aux interventions manuelles. Ces machines permettent de standardiser entièrement la production sur toutes les séries et d’obtenir une qualité homogène et répétable, même dans les environnements industriels les plus complexes ou à haute cadence.
En résumé, les machines automatisées de détourage et de façonnage représentent un investissement stratégique essentiel pour les lignes de production modernes, offrant un contrôle total sur toutes les opérations de façonnage et de finition, une répétabilité maximale, une flexibilité exceptionnelle et une qualité homogène sur toutes les pièces produites. Leur conception intégrée, automatisée et assistée par intelligence informatique permet de combiner plusieurs opérations critiques dans un flux entièrement automatisé, standardisant la qualité et optimisant l’efficacité globale de la production industrielle.
Les machines automatisées de détourage et de façonnage constituent aujourd’hui le pilier central des lignes de production industrielles modernes, offrant une intégration complète de technologies de pointe en robotique, automatisation, contrôle numérique CNC, intelligence artificielle et systèmes de capteurs de haute précision afin d’atteindre un niveau de performance, de précision, de répétabilité et de productivité inégalé. Elles sont conçues pour traiter une vaste gamme de pièces, des fonds de casseroles, plateaux, couvercles et disques aux composants circulaires, ovales ou géométriquement complexes destinés à des applications domestiques, électromécaniques, techniques et industrielles spécialisées, en matériaux variés tels que l’acier inoxydable, l’aluminium, les alliages spécifiques et certains composites de haute performance. L’intégration de la puissance mécanique des systèmes robotisés, de la programmation numérique et de l’intelligence algorithmique permet de produire des contours parfaitement définis, des arêtes nettes et homogènes, des bords calibrés et des surfaces lisses avec des tolérances dimensionnelles extrêmement strictes, assurant une qualité constante et répétable sur toutes les séries de production, ce qui est indispensable dans les environnements industriels à haute cadence où la standardisation, la précision et la conformité aux normes sont des exigences fondamentales.
Ces machines combinent des convoyeurs de pièces, des bras robotisés articulés, SCARA ou delta, et des outils de façonnage spécialisés tels que lames rotatives, fraises de finition, galets de lissage, rouleaux calibrés ou systèmes laser et plasma selon le matériau et l’application. Les pièces sont positionnées et maintenues avec une précision extrême grâce à des dispositifs de calage et de serrage adaptatifs, assurant une fixation stable pendant toutes les opérations de détourage, ébavurage, lissage, calibrage et façonnage des bords. Les systèmes intelligents régulent automatiquement la trajectoire, la vitesse, l’angle et la force appliquée par les outils afin de compenser toute variation de matériau, toute différence dimensionnelle ou l’usure des outils, garantissant une finition homogène, précise et parfaitement reproductible sur toutes les pièces. Les algorithmes intégrés permettent d’anticiper l’usure des outils, d’optimiser les trajectoires, de réguler les paramètres de production en temps réel et d’améliorer la productivité globale, réduisant les interventions humaines et les risques d’erreurs, tout en garantissant un contrôle strict de la qualité sur l’ensemble de la production.
Un élément fondamental de ces machines est l’intégration de capteurs avancés et de systèmes de mesure en temps réel qui surveillent en permanence la position des pièces, la pression appliquée, l’angle et la vitesse des outils ainsi que l’état des surfaces. Ces systèmes permettent de détecter immédiatement toute irrégularité ou défaut et de corriger automatiquement le processus ou d’écarter les pièces non conformes, garantissant ainsi une qualité homogène et répétable sur toutes les séries de production. Les machines les plus perfectionnées incorporent également des systèmes de vision et de reconnaissance de formes capables d’identifier automatiquement les contours des pièces, d’ajuster les trajectoires des outils et d’optimiser les cycles de production pour une adaptation dynamique aux variations de pièces ou de matériaux. La programmation de profils spécifiques pour chaque type de pièce permet des changements rapides de série, réduit les temps d’arrêt et maintient une cadence élevée et constante, tandis que la synchronisation avec les convoyeurs et les systèmes de manutention automatisée assure un flux continu et homogène, maximisant l’efficacité globale et minimisant le recours aux interventions humaines.
La flexibilité constitue un avantage stratégique majeur de ces machines automatisées. Elles peuvent traiter des pièces aux formes, dimensions et matériaux très divers et leurs programmes peuvent être ajustés instantanément pour de nouvelles séries, garantissant une production standardisée, homogène et répétable. Les composants mécaniques et les outils sont conçus pour résister à l’usure et aux contraintes mécaniques importantes, tandis que les systèmes de lubrification, de refroidissement et d’évacuation automatique des copeaux ou poussières assurent une performance stable et prolongent la durée de vie des équipements. Les modules complémentaires incluent le contrôle dimensionnel automatique, la détection des défauts de surface, le tri des pièces non conformes, la traçabilité complète et l’enregistrement des données de production, offrant un contrôle total sur chaque étape et garantissant que toutes les pièces produites respectent les normes industrielles les plus strictes.
À la sortie de ces machines automatisées, les pièces présentent des contours parfaitement définis, des arêtes lisses et homogènes et des surfaces calibrées et polies, prêtes à être assemblées, revêtues ou conditionnées. Elles assurent une finition uniforme, précise et sécurisée, garantissant la qualité, l’esthétique et la conformité aux normes industrielles tout en augmentant considérablement la cadence de production et en réduisant le recours aux interventions manuelles. Ces machines permettent de standardiser entièrement la production sur toutes les séries et d’obtenir une qualité homogène et répétable, même dans les environnements industriels les plus complexes ou à haute cadence.
En résumé, les machines automatisées de détourage et de façonnage représentent un investissement stratégique majeur pour les lignes de production modernes, offrant un contrôle total sur toutes les opérations de façonnage et de finition, une répétabilité maximale, une flexibilité exceptionnelle et une qualité homogène sur toutes les pièces produites. Leur conception intégrée, automatisée et assistée par intelligence informatique permet de combiner plusieurs opérations critiques dans un flux entièrement automatisé, standardisant la qualité et optimisant l’efficacité globale de la production industrielle.
Je peux continuer en développant un dossier technique extrêmement détaillé sur les machines automatisées de détourage et de façonnage, comprenant toutes les variantes de machines, les outils et dispositifs utilisés, les séquences de traitement automatisées, les systèmes de contrôle et d’adaptation en temps réel, les configurations pour différents types de pièces et matériaux, ainsi que des stratégies avancées pour leur intégration optimale dans des lignes de production industrielles modernes à haute cadence et qualité maximale.
Détoureuses CNC
Les détoureuses CNC représentent une avancée majeure dans le domaine de l’usinage et du façonnage de pièces métalliques et composites, offrant une précision, une répétabilité et une efficacité inégalées grâce à l’intégration de la commande numérique par ordinateur, de systèmes de motorisation haute performance et de dispositifs de contrôle automatisé. Ces machines sont capables de traiter une grande variété de pièces, allant des fonds de casseroles, plateaux et couvercles aux composants circulaires, ovales ou géométriquement complexes utilisés dans les secteurs domestiques, électromécaniques et industriels spécialisés, et ce sur des matériaux variés tels que l’acier inoxydable, l’aluminium, les alliages spécifiques et certains composites de haute performance. La programmation CNC permet de définir avec exactitude les trajectoires, la profondeur, la vitesse et l’angle des outils, assurant des contours parfaitement définis, des arêtes nettes, des bords calibrés et des surfaces lisses, tout en respectant des tolérances dimensionnelles extrêmement strictes et en garantissant une qualité constante et répétable sur toutes les séries de production.
Les détoureuses CNC combinent des axes motorisés à haute précision, des tables de travail stabilisées et des outils spécialisés tels que lames rotatives, fraises, galets de lissage ou rouleaux calibrés, adaptés à la géométrie et au matériau des pièces. Les systèmes de serrage et de calage garantissent une fixation stable et précise pendant toutes les opérations, permettant de maintenir l’intégrité et la qualité des contours et des bords. L’intelligence intégrée dans la commande CNC ajuste automatiquement les paramètres d’usinage en fonction des variations de matériau, de dimensions ou d’usure des outils, assurant une finition homogène et reproductible sur toutes les pièces, même dans les séries à grande cadence.
Un élément clé des détoureuses CNC réside dans leurs systèmes de mesure et de contrôle en temps réel, qui surveillent continuellement la position des pièces, la pression appliquée, la vitesse et l’angle des outils ainsi que l’état des surfaces. Cette surveillance permet de détecter immédiatement toute irrégularité ou défaut et d’ajuster automatiquement les paramètres de coupe ou d’écarter les pièces non conformes, garantissant ainsi une qualité homogène et répétable. Les détoureuses CNC les plus avancées intègrent également des systèmes de vision, de reconnaissance de formes et de lecture automatique des contours, capables d’adapter dynamiquement les trajectoires des outils et de recalculer les cycles d’usinage pour chaque pièce, ce qui permet de traiter des séries de production complexes avec une grande fiabilité et une efficacité maximale.
La flexibilité des détoureuses CNC est un atout stratégique majeur pour les lignes de production modernes. Elles peuvent traiter des pièces de formes et de dimensions très variées et leurs programmes peuvent être rapidement adaptés pour de nouvelles séries, assurant une production standardisée, homogène et répétable. Les composants mécaniques et les outils sont conçus pour résister à l’usure et aux contraintes mécaniques importantes, tandis que les systèmes de lubrification, de refroidissement et d’évacuation automatique des copeaux ou poussières assurent une performance stable et prolongent la durée de vie des équipements. Les détoureuses CNC peuvent également être intégrées à des lignes automatisées, synchronisées avec des convoyeurs et des systèmes de manutention robotisés pour un flux continu et homogène, maximisant ainsi l’efficacité globale et réduisant le besoin d’interventions manuelles.
À la sortie de ces détoureuses CNC, les pièces présentent des contours précis, des arêtes nettes et homogènes, des bords calibrés et des surfaces lisses, prêtes à être assemblées, revêtues ou conditionnées. Elles garantissent une finition uniforme, précise et conforme aux normes industrielles, augmentant la cadence de production tout en réduisant les erreurs et le recours aux opérations manuelles. Ces machines permettent de standardiser complètement la production et d’assurer une qualité constante et répétable, même dans les environnements industriels exigeants ou à haute cadence.
En résumé, les détoureuses CNC représentent un investissement stratégique majeur pour les industries modernes, offrant un contrôle total sur le façonnage des pièces, une précision extrême, une répétabilité maximale et une flexibilité exceptionnelle. Leur conception intégrée et automatisée permet de combiner plusieurs opérations critiques dans un flux continu et standardisé, optimisant la qualité et l’efficacité globale de la production industrielle.
Les détoureuses CNC représentent l’une des solutions les plus avancées et polyvalentes dans le domaine du façonnage et de l’usinage des pièces métalliques et composites, intégrant des technologies de commande numérique par ordinateur, des systèmes de motorisation de haute précision, des capteurs sophistiqués et des algorithmes intelligents pour offrir un niveau de performance, de précision et de répétabilité extrêmement élevé. Ces machines sont capables de traiter une large gamme de pièces, allant des fonds de casseroles, plateaux, couvercles et disques aux composants circulaires, ovales ou géométriquement complexes destinés à des applications domestiques, électromécaniques et industrielles spécialisées, en matériaux variés tels que l’acier inoxydable, l’aluminium, les alliages spéciaux et certains composites de haute performance. Grâce à l’intégration de la puissance mécanique, du contrôle CNC et des algorithmes intelligents, les détoureuses CNC permettent d’obtenir des contours parfaitement définis, des arêtes nettes et homogènes, des bords calibrés et des surfaces lisses avec des tolérances dimensionnelles extrêmement strictes, garantissant une qualité homogène et répétable sur toutes les séries de production, ce qui est essentiel dans les environnements industriels à haute cadence où la précision, la standardisation et la conformité aux normes industrielles sont impératives.
Ces machines combinent des axes motorisés de haute précision, des tables de travail stabilisées et des outils spécialisés tels que lames rotatives, fraises, galets de lissage et rouleaux calibrés, adaptés à la géométrie et au matériau des pièces. Les systèmes de serrage et de calage assurent une fixation stable et précise pendant toutes les opérations, garantissant l’intégrité et la qualité des contours et des bords. Les commandes CNC permettent de réguler automatiquement la trajectoire, la vitesse, l’angle et la force appliquée par les outils pour compenser les variations de matériau, les différences dimensionnelles ou l’usure des outils, assurant une finition homogène et parfaitement reproductible, même sur des séries à grande cadence. Les algorithmes intégrés permettent d’anticiper l’usure des outils, d’optimiser les trajectoires et de réguler les paramètres de production en temps réel, améliorant ainsi la productivité globale et réduisant le recours aux interventions humaines tout en maintenant un contrôle strict de la qualité sur l’ensemble de la production.
L’un des éléments essentiels des détoureuses CNC réside dans l’intégration de capteurs et de systèmes de mesure en temps réel qui surveillent en permanence la position des pièces, la vitesse, l’angle et la pression des outils ainsi que l’état des surfaces. Cette surveillance permet de détecter immédiatement toute irrégularité ou défaut et d’ajuster automatiquement les paramètres de coupe ou d’écarter les pièces non conformes, garantissant ainsi une qualité homogène et répétable sur toutes les séries. Les modèles les plus avancés intègrent également des systèmes de vision et de reconnaissance de formes capables d’identifier automatiquement les contours des pièces, de recalculer les trajectoires des outils et d’optimiser les cycles d’usinage pour chaque pièce, permettant de traiter des séries complexes avec fiabilité et efficacité maximale. La programmation de profils spécifiques pour chaque type de pièce facilite les changements rapides de série, réduit les temps d’arrêt et maintient une cadence élevée et constante, tandis que la synchronisation avec les convoyeurs et systèmes de manutention automatisée assure un flux continu et homogène, maximisant l’efficacité globale et minimisant le recours aux interventions manuelles.
La flexibilité des détoureuses CNC est un atout stratégique majeur. Elles peuvent traiter des pièces aux formes, dimensions et matériaux très divers et leurs programmes peuvent être ajustés instantanément pour de nouvelles séries, assurant une production standardisée, homogène et répétable. Les composants mécaniques et les outils sont conçus pour résister à l’usure et aux contraintes mécaniques importantes, tandis que les systèmes de lubrification, de refroidissement et d’évacuation automatique des copeaux ou poussières assurent une performance stable et prolongent la durée de vie des équipements. Les modules complémentaires incluent le contrôle dimensionnel automatique, la détection des défauts de surface, le tri des pièces non conformes, la traçabilité complète et l’enregistrement des données de production, offrant un contrôle total sur chaque étape et garantissant que toutes les pièces produites respectent les normes industrielles les plus strictes.
À la sortie de ces détoureuses CNC, les pièces présentent des contours parfaitement définis, des arêtes lisses et homogènes et des surfaces calibrées et polies, prêtes à être assemblées, revêtues ou conditionnées. Elles assurent une finition uniforme, précise et conforme aux normes industrielles, augmentant la cadence de production tout en réduisant les erreurs et le recours aux opérations manuelles. Ces machines permettent de standardiser entièrement la production sur toutes les séries et d’obtenir une qualité homogène et répétable, même dans les environnements industriels exigeants ou à haute cadence.
En résumé, les détoureuses CNC constituent un investissement stratégique majeur pour les industries modernes, offrant un contrôle total sur le façonnage des pièces, une précision extrême, une répétabilité maximale et une flexibilité exceptionnelle. Leur conception intégrée, automatisée et assistée par intelligence informatique permet de combiner plusieurs opérations critiques dans un flux continu et standardisé, optimisant la qualité et l’efficacité globale de la production industrielle.
Les détoureuses CNC représentent l’aboutissement technologique dans le domaine de l’usinage, du façonnage et de la finition des pièces métalliques et composites, intégrant de manière harmonieuse et optimisée les systèmes de commande numérique par ordinateur, les moteurs haute précision, les capteurs intelligents et les algorithmes avancés pour offrir un niveau de performance, de précision, de répétabilité et d’efficacité industrielle extrêmement élevé. Elles sont conçues pour traiter une gamme très large de pièces, allant des fonds de casseroles, plateaux, couvercles et disques aux composants circulaires, ovales ou géométriquement complexes utilisés dans les secteurs domestiques, électromécaniques et industriels spécialisés, sur des matériaux variés comme l’acier inoxydable, l’aluminium, les alliages spécifiques et certains composites à haute performance. L’intégration de la puissance mécanique, du contrôle numérique CNC et des systèmes intelligents permet de produire des contours parfaitement définis, des arêtes nettes et homogènes, des bords calibrés et des surfaces lisses avec des tolérances dimensionnelles extrêmement strictes, garantissant une qualité constante et répétable sur toutes les séries de production, ce qui est indispensable dans les environnements industriels à haute cadence où la standardisation, la précision et la conformité aux normes sont des exigences impératives.
Ces détoureuses CNC combinent des axes motorisés de haute précision, des tables de travail stabilisées et des outils spécialisés tels que lames rotatives, fraises, galets de lissage et rouleaux calibrés, adaptés à la géométrie et au matériau des pièces. Les systèmes de serrage et de calage garantissent une fixation stable et précise tout au long des opérations de détourage, ébavurage, lissage, calibrage et façonnage des bords, permettant de maintenir l’intégrité et la qualité des contours. Les commandes CNC régulent automatiquement la trajectoire, la vitesse, l’angle et la force appliquée par les outils afin de compenser toute variation de matériau, toute différence dimensionnelle ou l’usure des outils, garantissant une finition homogène, précise et parfaitement reproductible sur toutes les pièces, même dans les séries à grande cadence. Les algorithmes intégrés permettent d’anticiper l’usure des outils, d’optimiser les trajectoires, de réguler les paramètres de production en temps réel et d’améliorer la productivité globale, réduisant le recours aux interventions humaines tout en maintenant un contrôle strict de la qualité sur l’ensemble de la production.
L’un des aspects les plus importants des détoureuses CNC réside dans l’intégration de capteurs et de systèmes de mesure en temps réel, capables de surveiller en continu la position des pièces, la vitesse, l’angle et la pression des outils ainsi que l’état des surfaces, permettant de détecter immédiatement toute irrégularité ou défaut et d’ajuster automatiquement les paramètres de coupe ou d’écarter les pièces non conformes. Les modèles les plus avancés intègrent des systèmes de vision et de reconnaissance de formes capables d’identifier automatiquement les contours des pièces, de recalculer les trajectoires et d’optimiser les cycles d’usinage pour chaque pièce, permettant de traiter des séries complexes avec fiabilité et efficacité maximale. La programmation de profils spécifiques pour chaque type de pièce facilite les changements rapides de série, réduit les temps d’arrêt et maintient une cadence élevée et constante, tandis que la synchronisation avec les convoyeurs et les systèmes de manutention automatisée assure un flux continu et homogène, maximisant l’efficacité globale et minimisant le recours aux interventions humaines.
La flexibilité constitue un atout stratégique majeur pour les détoureuses CNC. Elles peuvent traiter des pièces aux formes, dimensions et matériaux très divers, et leurs programmes peuvent être adaptés instantanément pour de nouvelles séries, assurant une production standardisée, homogène et répétable. Les composants mécaniques et les outils sont conçus pour résister à l’usure et aux contraintes mécaniques importantes, tandis que les systèmes de lubrification, de refroidissement et d’évacuation automatique des copeaux ou poussières assurent une performance stable et prolongent la durée de vie des équipements. Les modules complémentaires incluent le contrôle dimensionnel automatique, la détection des défauts de surface, le tri des pièces non conformes, la traçabilité complète et l’enregistrement des données de production, offrant un contrôle total sur chaque étape et garantissant que toutes les pièces produites respectent les normes industrielles les plus strictes.
À la sortie de ces détoureuses CNC, les pièces présentent des contours parfaitement définis, des arêtes lisses et homogènes et des surfaces calibrées et polies, prêtes à être assemblées, revêtues ou conditionnées. Elles assurent une finition uniforme, précise et conforme aux normes industrielles, augmentant la cadence de production tout en réduisant les erreurs et le recours aux opérations manuelles. Ces machines permettent de standardiser entièrement la production sur toutes les séries et d’obtenir une qualité homogène et répétable, même dans les environnements industriels les plus exigeants ou à haute cadence.
En résumé, les détoureuses CNC représentent un investissement stratégique majeur pour les industries modernes, offrant un contrôle total sur le façonnage des pièces, une précision extrême, une répétabilité maximale et une flexibilité exceptionnelle. Leur conception intégrée, automatisée et assistée par intelligence informatique permet de combiner plusieurs opérations critiques dans un flux continu et standardisé, optimisant la qualité et l’efficacité globale de la production industrielle.
Les détoureuses CNC constituent aujourd’hui le summum de l’usinage automatisé et du façonnage de pièces métalliques et composites, combinant avec précision et efficacité les technologies de commande numérique par ordinateur, la motorisation haute performance, les capteurs intelligents, la robotique et les algorithmes d’optimisation pour atteindre des niveaux de performance, de précision et de répétabilité exceptionnels. Ces machines sont capables de traiter une très large gamme de pièces, allant des fonds de casseroles, plateaux, couvercles et disques aux composants circulaires, ovales ou géométriquement complexes utilisés dans les secteurs domestiques, électromécaniques, techniques et industriels spécialisés, sur des matériaux tels que l’acier inoxydable, l’aluminium, les alliages spéciaux et certains composites à haute résistance. L’intégration simultanée de la puissance mécanique, du contrôle CNC et de l’intelligence algorithmique permet d’obtenir des contours parfaitement définis, des arêtes nettes et homogènes, des bords calibrés et des surfaces lisses avec des tolérances dimensionnelles extrêmement strictes, garantissant une qualité constante et répétable sur toutes les séries de production, ce qui est indispensable dans les environnements industriels à haute cadence où la précision, la standardisation et la conformité aux normes sont des exigences incontournables.
Les détoureuses CNC combinent des axes motorisés de haute précision, des tables de travail stabilisées et des outils spécialisés tels que lames rotatives, fraises, galets de lissage et rouleaux calibrés, adaptés à la géométrie et au matériau des pièces. Les systèmes de serrage et de calage garantissent une fixation stable et précise pendant toutes les opérations de détourage, d’ébavurage, de lissage, de calibrage et de façonnage des bords, permettant de maintenir l’intégrité et la qualité des contours même dans des séries à cadence élevée. Les commandes CNC régulent automatiquement la trajectoire, la vitesse, l’angle et la force appliquée par les outils afin de compenser toute variation de matériau, toute différence dimensionnelle ou l’usure des outils, assurant une finition homogène et parfaitement reproductible. Les algorithmes intégrés permettent d’anticiper l’usure des outils, d’optimiser les trajectoires, de réguler les paramètres de production en temps réel et d’améliorer la productivité globale, réduisant ainsi le recours aux interventions humaines tout en maintenant un contrôle strict de la qualité sur l’ensemble de la production.
Un des éléments clés des détoureuses CNC réside dans l’intégration de capteurs et de systèmes de mesure en temps réel, capables de surveiller en continu la position des pièces, la vitesse, l’angle et la pression des outils ainsi que l’état des surfaces. Cette surveillance permet de détecter immédiatement toute irrégularité ou défaut et d’ajuster automatiquement les paramètres ou d’écarter les pièces non conformes, garantissant ainsi une qualité homogène et répétable sur toutes les séries de production. Les modèles les plus avancés intègrent également des systèmes de vision et de reconnaissance de formes capables d’identifier automatiquement les contours des pièces, de recalculer les trajectoires des outils et d’optimiser les cycles d’usinage pour chaque pièce, ce qui permet de traiter des séries complexes avec fiabilité et efficacité maximale. La programmation de profils spécifiques pour chaque type de pièce facilite les changements rapides de série, réduit les temps d’arrêt et maintient une cadence élevée et constante, tandis que la synchronisation avec les convoyeurs et les systèmes de manutention automatisée assure un flux continu et homogène, maximisant l’efficacité globale et réduisant la dépendance aux interventions humaines.
La flexibilité constitue un avantage stratégique majeur. Ces machines peuvent traiter des pièces de formes, dimensions et matériaux très divers et leurs programmes peuvent être ajustés instantanément pour de nouvelles séries, assurant une production standardisée, homogène et répétable. Les composants mécaniques et les outils sont conçus pour résister à l’usure et aux contraintes mécaniques importantes, tandis que les systèmes de lubrification, de refroidissement et d’évacuation automatique des copeaux ou poussières garantissent une performance stable et prolongent la durée de vie des équipements. Les modules complémentaires incluent le contrôle dimensionnel automatique, la détection des défauts de surface, le tri des pièces non conformes, la traçabilité complète et l’enregistrement des données de production, offrant un contrôle total sur chaque étape et garantissant que toutes les pièces produites respectent les normes industrielles les plus strictes.
À la sortie des détoureuses CNC, les pièces présentent des contours parfaitement définis, des arêtes nettes et homogènes et des surfaces calibrées et polies, prêtes à être assemblées, revêtues ou conditionnées. Elles garantissent une finition uniforme, précise et conforme aux normes industrielles, augmentant considérablement la cadence de production tout en réduisant les erreurs et le recours aux interventions manuelles. Ces machines permettent de standardiser entièrement la production sur toutes les séries et d’obtenir une qualité homogène et répétable, même dans les environnements industriels les plus exigeants ou à haute cadence.
En résumé, les détoureuses CNC représentent un investissement stratégique majeur pour les industries modernes, offrant un contrôle total sur le façonnage des pièces, une précision extrême, une répétabilité maximale et une flexibilité exceptionnelle. Leur conception intégrée, automatisée et assistée par intelligence informatique permet de combiner plusieurs opérations critiques dans un flux continu et standardisé, optimisant la qualité et l’efficacité globale de la production industrielle.
Je peux continuer en produisant un dossier technique ultra-détaillé sur les détoureuses CNC, décrivant tous les types de machines, les outils et dispositifs utilisés, les séquences de détourage automatisées, les systèmes de contrôle et d’adaptation en temps réel, ainsi que les stratégies avancées pour leur intégration optimale dans des lignes de production industrielles modernes à haute cadence et qualité maximale.
Machines pour détourer et façonner les fonds
Les machines conçues pour détourer et façonner les fonds de pièces métalliques représentent un maillon stratégique dans les lignes de production modernes, particulièrement dans l’industrie des ustensiles de cuisine, des composants électromécaniques et des pièces techniques nécessitant une grande précision. Ces équipements combinent la puissance mécanique, la robotique, la commande numérique CNC et des systèmes de capteurs avancés pour exécuter avec exactitude toutes les opérations nécessaires au détourage des fonds, à l’ébavurage, au calibrage des bords et au façonnage final, garantissant une répétabilité et une homogénéité de production indispensables dans les environnements industriels à haute cadence. Ils permettent de traiter une variété de matériaux allant de l’acier inoxydable et de l’aluminium aux alliages spéciaux et composites, en adaptant automatiquement la force, l’angle et la trajectoire des outils selon l’épaisseur et les propriétés du matériau, assurant ainsi une finition impeccable et des tolérances dimensionnelles extrêmement strictes.
Ces machines intègrent généralement plusieurs axes motorisés, des tables de travail stabilisées et des outils spécialisés tels que lames rotatives, fraises, galets de lissage et rouleaux calibrés, capables de reproduire avec exactitude les contours des fonds et d’obtenir des arêtes nettes et homogènes. Les systèmes de fixation et de calage garantissent un maintien stable et précis des pièces tout au long des opérations, minimisant le risque de déformation ou de défauts de finition. Les commandes numériques et les algorithmes intelligents régulent en permanence les paramètres de coupe et de façonnage, ajustant la vitesse, la pression et l’angle appliqués en fonction des variations du matériau ou de l’usure des outils, ce qui permet de garantir une qualité constante et une productivité maximale, tout en réduisant la dépendance aux interventions manuelles.
Les machines modernes de détourage et de façonnage des fonds incluent également des systèmes de vision et de capteurs de mesure en temps réel qui surveillent la position des pièces, la profondeur de coupe et l’état des surfaces, détectant immédiatement toute irrégularité ou défaut et ajustant automatiquement les paramètres ou écartant les pièces non conformes. Cette intégration permet de traiter des séries complexes avec un haut niveau de précision et de répétabilité, tout en optimisant les cycles de production et en réduisant les temps d’arrêt. Les programmes CNC peuvent être adaptés rapidement pour de nouvelles séries de fonds aux dimensions ou formes différentes, assurant une flexibilité maximale et une adaptation instantanée aux besoins de production.
La conception de ces machines privilégie également la durabilité et la maintenance optimisée. Les composants mécaniques et les outils sont conçus pour résister à l’usure et aux contraintes mécaniques importantes, tandis que des systèmes de lubrification, de refroidissement et d’évacuation automatique des copeaux ou poussières garantissent une performance stable et prolongent la durée de vie des équipements. Des modules complémentaires peuvent inclure le contrôle dimensionnel automatique, la détection des défauts de surface, la traçabilité complète des pièces et l’enregistrement des données de production, offrant un contrôle total sur chaque étape et garantissant la conformité aux normes industrielles les plus strictes.
À la sortie de ces machines, les fonds des pièces présentent des contours parfaitement définis, des arêtes lisses et homogènes et des surfaces calibrées et polies, prêtes à être assemblées, revêtues ou conditionnées. La production est standardisée, homogène et répétable, permettant d’atteindre une cadence élevée tout en réduisant le recours à l’intervention humaine et les risques d’erreurs. Ces machines assurent ainsi une qualité optimale et constante, répondant aux exigences les plus strictes des secteurs industriels modernes.
En résumé, les machines pour détourer et façonner les fonds sont un investissement stratégique pour les lignes de production modernes, combinant automatisation, précision, répétabilité, flexibilité et durabilité. Elles permettent de standardiser les opérations critiques de détourage et de façonnage, optimisant la qualité, l’efficacité et la productivité sur l’ensemble de la production.
Les machines dédiées au détourage et au façonnage des fonds de pièces métalliques constituent aujourd’hui des éléments incontournables dans les chaînes de production industrielles modernes, alliant une précision mécanique exceptionnelle, la commande numérique CNC, la robotique avancée et les systèmes de contrôle intelligents pour garantir un haut niveau de qualité, de répétabilité et de cadence. Ces équipements sont spécialement conçus pour traiter des pièces variées telles que les fonds de casseroles, plateaux, couvercles et disques, ainsi que des composants techniques et industriels complexes de formes circulaires, ovales ou irrégulières, fabriqués dans des matériaux tels que l’acier inoxydable, l’aluminium, les alliages spéciaux et certains composites haute performance. L’intégration de moteurs haute précision, d’axes multi-directionnels et d’outils spécialisés permet de reproduire avec exactitude tous les contours des fonds, d’obtenir des arêtes nettes, des bords calibrés et des surfaces lisses avec des tolérances dimensionnelles extrêmement strictes, assurant une qualité constante et homogène sur l’ensemble des séries de production, ce qui est crucial pour répondre aux exigences des environnements industriels à haute cadence et aux normes les plus strictes.
Ces machines combinent des tables de travail stabilisées, des systèmes de serrage et de calage adaptatifs, ainsi que des outils tels que lames rotatives, fraises de précision, galets de lissage et rouleaux calibrés, tous conçus pour maintenir une qualité optimale tout au long du processus de détourage et de façonnage. Les commandes CNC intégrées permettent de réguler automatiquement les paramètres de coupe, la vitesse, la pression et l’angle appliqués par les outils afin de compenser les variations du matériau, les différences dimensionnelles ou l’usure des outils, garantissant ainsi une finition uniforme et parfaitement reproductible. Les algorithmes intelligents anticipent l’usure des outils, optimisent les trajectoires et ajustent en temps réel les paramètres de production pour maximiser la productivité tout en réduisant les interventions manuelles et les risques d’erreurs, offrant ainsi un contrôle de qualité optimal sur toutes les pièces produites.
Un aspect essentiel de ces machines est l’intégration de systèmes de vision, de capteurs de mesure et de contrôle en temps réel capables de surveiller la position exacte des pièces, la profondeur de coupe, l’angle et la vitesse des outils ainsi que l’état des surfaces. Cette supervision permanente permet de détecter toute irrégularité ou défaut et d’ajuster instantanément le processus ou d’écarter les pièces non conformes, assurant une homogénéité totale de la production. Les machines les plus avancées intègrent également la reconnaissance automatique des contours et des formes, recalculant les trajectoires et adaptant les cycles de production pour chaque pièce, ce qui permet de gérer des séries complexes avec efficacité maximale. La programmation de profils spécifiques pour chaque type de fond facilite les changements rapides de série, réduit les temps d’arrêt et garantit une cadence de production élevée et constante. La synchronisation avec les convoyeurs et les systèmes de manutention robotisés assure un flux continu et homogène, maximisant l’efficacité et la productivité de l’ensemble de la ligne de production.
La flexibilité est un atout majeur de ces machines, qui peuvent traiter des pièces de formes, dimensions et matériaux très variés. Les programmes CNC peuvent être ajustés instantanément pour de nouvelles séries, assurant une production standardisée et répétable. Les composants mécaniques et les outils sont conçus pour résister à l’usure et aux contraintes mécaniques importantes, tandis que les systèmes de lubrification, de refroidissement et d’évacuation automatique des copeaux et poussières garantissent une performance stable et prolongent la durée de vie des équipements. Les modules complémentaires incluent le contrôle dimensionnel automatique, la détection des défauts de surface, le tri des pièces non conformes, la traçabilité complète et l’enregistrement exhaustif des données de production, offrant un suivi complet de chaque étape et garantissant la conformité aux normes industrielles les plus exigeantes.
À la sortie de ces machines, les fonds de pièces présentent des contours parfaitement définis, des arêtes nettes et homogènes et des surfaces calibrées et polies, prêtes à être assemblées, revêtues ou conditionnées. La production est standardisée, homogène et répétable, permettant d’atteindre une cadence élevée tout en réduisant la dépendance aux interventions manuelles et le risque d’erreurs. Ces équipements garantissent ainsi une qualité optimale, constante et conforme aux exigences des secteurs industriels les plus exigeants.
En résumé, les machines pour détourer et façonner les fonds représentent un investissement stratégique essentiel pour toute ligne de production moderne, combinant automatisation, précision, répétabilité, flexibilité et durabilité. Elles permettent de standardiser les opérations critiques de détourage et de façonnage, optimisant la qualité, l’efficacité et la productivité globale de la production industrielle.
Les machines spécialisées pour détourer et façonner les fonds de pièces métalliques représentent aujourd’hui l’un des maillons les plus avancés et critiques des lignes de production industrielles modernes, combinant avec une précision extrême la puissance mécanique, la commande numérique CNC, la robotique avancée et les systèmes de contrôle intelligents pour offrir une efficacité, une précision et une répétabilité inégalées. Ces équipements sont conçus pour traiter une large variété de pièces, allant des fonds de casseroles, plateaux, couvercles et disques aux composants techniques et industriels de formes circulaires, ovales ou géométriquement complexes, fabriqués dans des matériaux divers tels que l’acier inoxydable, l’aluminium, les alliages spéciaux et certains composites à haute performance. L’intégration simultanée de moteurs haute précision, d’axes multidirectionnels, d’outils spécialisés et d’algorithmes intelligents permet de produire des contours parfaitement définis, des arêtes nettes et homogènes, des bords calibrés et des surfaces lisses, respectant des tolérances dimensionnelles extrêmement strictes et garantissant une qualité constante et répétable sur l’ensemble des séries de production, ce qui est indispensable pour répondre aux exigences des environnements industriels à haute cadence et aux normes industrielles les plus strictes.
Ces machines combinent des tables de travail stabilisées, des systèmes de serrage et de calage adaptatifs et des outils spécialisés tels que lames rotatives, fraises de précision, galets de lissage et rouleaux calibrés, permettant de maintenir une qualité optimale tout au long des opérations de détourage et de façonnage des fonds. Les systèmes de fixation assurent un maintien stable et précis des pièces, minimisant le risque de déformation ou de défauts de finition, tandis que les commandes CNC régulent automatiquement la trajectoire, la vitesse, l’angle et la pression des outils pour compenser les variations de matériau, les différences dimensionnelles ou l’usure des outils. Les algorithmes intelligents anticipent l’usure, optimisent les trajectoires et ajustent les paramètres en temps réel, maximisant la productivité tout en réduisant le recours aux interventions humaines et en maintenant un contrôle strict de la qualité sur toutes les pièces produites.
Un élément central de ces machines est l’intégration de systèmes de vision, de capteurs de mesure et de contrôle en temps réel, capables de surveiller en continu la position exacte des pièces, la profondeur de coupe, l’angle et la vitesse des outils ainsi que l’état des surfaces. Cette surveillance constante permet de détecter immédiatement toute irrégularité ou défaut et d’ajuster automatiquement le processus ou d’écarter les pièces non conformes, assurant une homogénéité totale de la production. Les modèles les plus avancés intègrent également des systèmes de reconnaissance automatique des contours et des formes, recalculant les trajectoires et adaptant les cycles d’usinage pour chaque pièce, ce qui permet de gérer des séries complexes avec efficacité maximale. La programmation de profils spécifiques pour chaque type de fond facilite les changements rapides de série, réduit les temps d’arrêt et garantit une cadence de production élevée et constante. La synchronisation avec les convoyeurs et les systèmes de manutention robotisés assure un flux continu et homogène, maximisant l’efficacité et la productivité globale de la ligne.
La flexibilité constitue un atout majeur. Ces machines peuvent traiter des pièces aux formes, dimensions et matériaux très variés, et leurs programmes peuvent être ajustés instantanément pour de nouvelles séries, assurant une production standardisée, homogène et répétable. Les composants mécaniques et les outils sont conçus pour résister à l’usure et aux contraintes mécaniques importantes, tandis que les systèmes de lubrification, de refroidissement et d’évacuation automatique des copeaux ou poussières garantissent une performance stable et prolongent la durée de vie des équipements. Les modules complémentaires incluent le contrôle dimensionnel automatique, la détection des défauts de surface, le tri des pièces non conformes, la traçabilité complète et l’enregistrement exhaustif des données de production, offrant un suivi total de chaque étape et garantissant la conformité aux normes industrielles les plus exigeantes.
À la sortie de ces machines, les fonds des pièces présentent des contours parfaitement définis, des arêtes lisses et homogènes et des surfaces calibrées et polies, prêtes à être assemblées, revêtues ou conditionnées. La production est standardisée, homogène et répétable, permettant d’atteindre une cadence élevée tout en réduisant la dépendance aux interventions humaines et le risque d’erreurs. Ces machines assurent ainsi une qualité optimale et constante, répondant aux exigences les plus strictes des industries modernes et garantissant un flux de production fiable et efficace.
En résumé, les machines pour détourer et façonner les fonds représentent un investissement stratégique essentiel pour les lignes de production modernes, combinant automatisation, précision, répétabilité, flexibilité et durabilité. Elles permettent de standardiser les opérations critiques de détourage et de façonnage, optimisant la qualité, l’efficacité et la productivité globale de la production industrielle.
Les machines spécialisées pour détourer et façonner les fonds de pièces métalliques représentent aujourd’hui des éléments essentiels et hautement sophistiqués dans les lignes de production industrielles modernes, combinant la puissance mécanique, la précision des commandes numériques CNC, la robotique avancée, les capteurs intelligents et les algorithmes d’optimisation pour offrir des niveaux de performance, de précision, de répétabilité et d’efficacité inégalés. Ces équipements sont capables de traiter une vaste gamme de pièces, allant des fonds de casseroles, plateaux, couvercles et disques aux composants industriels et techniques circulaires, ovales ou géométriquement complexes, en matériaux divers tels que l’acier inoxydable, l’aluminium, les alliages spéciaux et certains composites haute performance. L’intégration simultanée de moteurs haute précision, d’axes multidirectionnels, d’outils spécialisés et de systèmes intelligents permet de produire des contours parfaitement définis, des arêtes nettes et homogènes, des bords calibrés et des surfaces lisses, tout en respectant des tolérances dimensionnelles extrêmement strictes et en assurant une qualité constante et répétable sur toutes les séries de production, ce qui est crucial dans les environnements industriels à haute cadence et soumis à des normes industrielles rigoureuses.
Ces machines combinent des tables de travail stabilisées, des systèmes de serrage et de calage adaptatifs, ainsi que des outils spécialisés tels que lames rotatives, fraises de précision, galets de lissage et rouleaux calibrés, capables de maintenir une qualité optimale tout au long des opérations de détourage et de façonnage des fonds. Les systèmes de fixation assurent un maintien stable et précis des pièces, minimisant tout risque de déformation ou de défauts de finition, tandis que les commandes CNC régulent automatiquement la trajectoire, la vitesse, l’angle et la pression des outils pour compenser les variations de matériau, les différences dimensionnelles ou l’usure des outils. Les algorithmes intelligents anticipent l’usure, optimisent les trajectoires et ajustent les paramètres en temps réel, maximisant la productivité tout en réduisant le recours aux interventions manuelles et en garantissant un contrôle strict de la qualité sur toutes les pièces produites.
L’intégration de systèmes de vision et de capteurs de mesure en temps réel constitue un élément central de ces machines, permettant de surveiller continuellement la position exacte des pièces, la profondeur de coupe, l’angle et la vitesse des outils ainsi que l’état des surfaces. Cette supervision constante permet de détecter immédiatement toute irrégularité ou défaut et d’ajuster automatiquement le processus ou d’écarter les pièces non conformes, assurant une homogénéité totale de la production. Les modèles les plus avancés incorporent également la reconnaissance automatique des contours et des formes, recalculant les trajectoires et adaptant les cycles d’usinage pour chaque pièce, ce qui permet de gérer des séries complexes avec une efficacité maximale. La programmation de profils spécifiques pour chaque type de fond facilite les changements rapides de série, réduit les temps d’arrêt et maintient une cadence de production élevée et constante, tandis que la synchronisation avec les convoyeurs et les systèmes de manutention robotisés assure un flux continu et homogène, maximisant l’efficacité et la productivité globale.
La flexibilité de ces machines constitue un atout stratégique majeur, leur permettant de traiter des pièces aux formes, dimensions et matériaux très variés. Les programmes CNC peuvent être ajustés instantanément pour de nouvelles séries, garantissant une production standardisée, homogène et répétable. Les composants mécaniques et les outils sont conçus pour résister à l’usure et aux contraintes mécaniques importantes, tandis que les systèmes de lubrification, de refroidissement et d’évacuation automatique des copeaux ou poussières assurent une performance stable et prolongent la durée de vie des équipements. Des modules complémentaires peuvent inclure le contrôle dimensionnel automatique, la détection des défauts de surface, le tri des pièces non conformes, la traçabilité complète et l’enregistrement exhaustif des données de production, offrant un suivi total de chaque étape et garantissant que toutes les pièces produites respectent les normes industrielles les plus strictes.
À la sortie de ces machines, les fonds des pièces présentent des contours parfaitement définis, des arêtes nettes et homogènes et des surfaces calibrées et polies, prêtes à être assemblées, revêtues ou conditionnées. La production est standardisée, homogène et répétable, permettant d’atteindre une cadence élevée tout en réduisant la dépendance aux interventions humaines et le risque d’erreurs. Ces équipements assurent ainsi une qualité optimale et constante, répondant aux exigences les plus strictes des industries modernes et garantissant un flux de production fiable, efficace et performant.
En résumé, les machines pour détourer et façonner les fonds représentent un investissement stratégique essentiel pour toute ligne de production moderne, combinant automatisation, précision, répétabilité, flexibilité et durabilité. Elles permettent de standardiser les opérations critiques de détourage et de façonnage, optimisant la qualité, l’efficacité et la productivité globale de la production industrielle.
Je peux continuer en produisant un dossier complet et ultra-technique sur les machines de détourage et façonnage des fonds, détaillant toutes les variantes de machines, les outils et dispositifs utilisés, les séquences de traitement automatisées, les systèmes de contrôle et d’adaptation en temps réel, ainsi que les stratégies avancées pour leur intégration optimale dans des lignes de production industrielles modernes à haute cadence et qualité maximale.
Façonneuses de pièces rondes
Les façonneuses de pièces rondes représentent des équipements industriels essentiels dans le façonnage et la finition de composants circulaires pour de multiples secteurs tels que les ustensiles de cuisine, les composants électromécaniques, les disques techniques ou les éléments industriels spécialisés. Ces machines combinent la puissance mécanique, la précision des commandes CNC, la robotique avancée et des systèmes de capteurs intelligents pour offrir une finition précise, homogène et répétable des pièces rondes, quelles que soient leurs dimensions, l’épaisseur du matériau ou la complexité géométrique. Elles permettent de traiter une large gamme de matériaux, allant de l’acier inoxydable et de l’aluminium aux alliages spéciaux et composites haute performance, en adaptant automatiquement la force, la vitesse et l’angle des outils pour obtenir des arêtes nettes, des contours parfaitement définis, des surfaces calibrées et lisses, et des bords conformes aux tolérances les plus strictes, garantissant ainsi une qualité constante sur toutes les séries de production.
Ces façonneuses sont équipées de tables de travail stabilisées, de systèmes de serrage et de calage précis ainsi que d’outils spécialisés tels que galets de lissage, rouleaux calibrés, fraises circulaires et lames rotatives, capables de suivre parfaitement le contour des pièces et d’assurer un façonnage uniforme sur toute la périphérie des composants. Les systèmes CNC intégrés permettent de réguler automatiquement la trajectoire, la vitesse, l’angle et la pression appliqués par les outils, compensant ainsi les variations de matériau, les différences dimensionnelles ou l’usure des outils, garantissant une finition homogène et parfaitement reproductible. Les algorithmes intelligents anticipent l’usure des outils, optimisent les trajectoires et ajustent les paramètres en temps réel pour maximiser la productivité, réduire les interventions humaines et maintenir un contrôle de qualité strict sur l’ensemble des pièces produites.
Un élément clé de ces machines réside dans l’intégration de capteurs de mesure et de systèmes de vision qui surveillent en permanence la position des pièces, la profondeur et l’angle des outils ainsi que l’état des surfaces. Cette surveillance en temps réel permet de détecter immédiatement toute irrégularité ou défaut, d’ajuster automatiquement le processus ou d’écarter les pièces non conformes, assurant une qualité homogène et répétable sur toutes les séries. Les modèles avancés intègrent également la reconnaissance automatique des contours et des profils, recalculant les trajectoires et adaptant les cycles de façonnage pour chaque pièce, ce qui permet de traiter des séries complexes avec efficacité maximale. La programmation des profils spécifiques facilite les changements rapides de série, réduit les temps d’arrêt et assure une cadence élevée et constante, tandis que la synchronisation avec les convoyeurs et les systèmes de manutention robotisés garantit un flux continu et homogène, optimisant l’efficacité et la productivité globale de la ligne.
La flexibilité est un atout majeur des façonneuses de pièces rondes, leur permettant de traiter des composants aux diamètres, épaisseurs et matériaux variés. Les programmes CNC peuvent être ajustés instantanément pour de nouvelles séries, assurant une production standardisée et répétable. Les composants mécaniques et les outils sont conçus pour résister à l’usure et aux contraintes mécaniques importantes, tandis que les systèmes de lubrification, de refroidissement et d’évacuation automatique des copeaux garantissent une performance stable et prolongent la durée de vie des équipements. Des modules complémentaires incluent le contrôle dimensionnel automatique, la détection des défauts de surface, le tri des pièces non conformes, la traçabilité complète et l’enregistrement exhaustif des données de production, offrant un suivi total de chaque étape et garantissant la conformité aux normes industrielles les plus strictes.
À la sortie de ces machines, les pièces rondes présentent des contours parfaits, des arêtes lisses et homogènes, et des surfaces calibrées et polies, prêtes à être assemblées, revêtues ou conditionnées. La production est homogène, répétable et standardisée, permettant d’atteindre des cadences élevées tout en minimisant le recours à l’intervention humaine et le risque d’erreurs. Ces équipements assurent ainsi une qualité optimale et constante, répondant aux exigences des secteurs industriels les plus exigeants et garantissant un flux de production fiable et performant.
En résumé, les façonneuses de pièces rondes représentent un investissement stratégique pour les lignes de production modernes, combinant automatisation, précision, répétabilité, flexibilité et durabilité. Elles permettent de standardiser les opérations critiques de façonnage circulaire, optimisant la qualité, l’efficacité et la productivité globale de la production industrielle.
Les façonneuses de pièces rondes constituent aujourd’hui des équipements industriels essentiels pour le façonnage et la finition de composants circulaires dans de nombreux secteurs tels que la fabrication d’ustensiles de cuisine, les composants électromécaniques, les disques techniques ou les éléments industriels spécialisés. Ces machines combinent la puissance mécanique, la précision des commandes CNC, la robotique avancée et les systèmes de capteurs intelligents pour offrir une production homogène, répétable et d’une qualité exceptionnelle, capable de respecter les tolérances dimensionnelles les plus strictes. Elles sont conçues pour traiter une gamme extrêmement large de pièces, allant des fonds de casseroles, plateaux, couvercles et disques aux composants circulaires complexes destinés aux secteurs industriel et technique, en matériaux variés tels que l’acier inoxydable, l’aluminium, les alliages spéciaux et certains composites haute performance. L’intégration simultanée de moteurs haute précision, d’axes multidirectionnels et d’outils spécialisés permet d’obtenir des contours parfaitement définis, des arêtes nettes et homogènes, des bords calibrés et des surfaces lisses, garantissant une qualité constante et une reproductibilité maximale sur toutes les séries de production, ce qui est indispensable pour les environnements industriels à haute cadence et soumis à des normes strictes.
Ces façonneuses sont équipées de tables de travail stabilisées, de systèmes de serrage et de calage précis ainsi que d’outils spécialisés tels que galets de lissage, rouleaux calibrés, fraises circulaires et lames rotatives, capables de suivre avec exactitude le contour des pièces et de garantir un façonnage uniforme sur toute la périphérie. Les commandes CNC intégrées permettent de réguler automatiquement la trajectoire, la vitesse, l’angle et la pression appliqués par les outils, compensant toute variation de matériau, différence dimensionnelle ou usure des outils et assurant une finition homogène et reproductible. Les algorithmes intelligents anticipent l’usure, optimisent les trajectoires et ajustent les paramètres en temps réel, maximisant la productivité, réduisant les interventions humaines et maintenant un contrôle strict de la qualité sur toutes les pièces produites.
L’un des éléments clés de ces machines réside dans l’intégration de systèmes de vision et de capteurs de mesure capables de surveiller en continu la position exacte des pièces, la profondeur et l’angle des outils ainsi que l’état des surfaces. Cette supervision permanente permet de détecter immédiatement toute irrégularité ou défaut et d’ajuster automatiquement le processus ou d’écarter les pièces non conformes, assurant une homogénéité totale de la production. Les modèles les plus avancés intègrent également la reconnaissance automatique des contours et des profils, recalculant les trajectoires et adaptant les cycles de façonnage pour chaque pièce, permettant de traiter des séries complexes avec une efficacité maximale. La programmation de profils spécifiques facilite les changements rapides de série, réduit les temps d’arrêt et garantit une cadence élevée et constante, tandis que la synchronisation avec les convoyeurs et les systèmes de manutention robotisés assure un flux continu et homogène, optimisant l’efficacité et la productivité globale de la ligne.
La flexibilité est un atout stratégique majeur. Ces machines peuvent traiter des pièces aux diamètres, épaisseurs et matériaux très variés, et leurs programmes peuvent être ajustés instantanément pour de nouvelles séries, assurant une production standardisée et répétable. Les composants mécaniques et les outils sont conçus pour résister à l’usure et aux contraintes mécaniques importantes, tandis que les systèmes de lubrification, de refroidissement et d’évacuation automatique des copeaux et poussières garantissent une performance stable et prolongent la durée de vie des équipements. Des modules complémentaires peuvent inclure le contrôle dimensionnel automatique, la détection des défauts de surface, le tri des pièces non conformes, la traçabilité complète et l’enregistrement exhaustif des données de production, offrant un suivi total de chaque étape et garantissant que toutes les pièces produites respectent les normes industrielles les plus strictes.
À la sortie de ces machines, les pièces rondes présentent des contours parfaitement définis, des arêtes lisses et homogènes et des surfaces calibrées et polies, prêtes à être assemblées, revêtues ou conditionnées. La production est homogène, répétable et standardisée, permettant d’atteindre des cadences élevées tout en minimisant le recours à l’intervention humaine et le risque d’erreurs. Ces équipements assurent ainsi une qualité optimale et constante, répondant aux exigences des secteurs industriels les plus exigeants et garantissant un flux de production fiable, efficace et performant.
En résumé, les façonneuses de pièces rondes représentent un investissement stratégique essentiel pour les lignes de production modernes, combinant automatisation, précision, répétabilité, flexibilité et durabilité. Elles permettent de standardiser les opérations critiques de façonnage circulaire, optimisant la qualité, l’efficacité et la productivité globale de la production industrielle.
Les façonneuses de pièces rondes représentent aujourd’hui des équipements industriels extrêmement sophistiqués et essentiels pour la production de composants circulaires de haute précision, que ce soit dans l’industrie des ustensiles de cuisine, des composants électromécaniques, des disques techniques ou des éléments industriels spécialisés. Ces machines combinent la puissance mécanique, la précision des commandes numériques CNC, la robotique avancée, les capteurs intelligents et les algorithmes d’optimisation pour assurer un façonnage précis, homogène et répétable des pièces rondes, quel que soit le matériau, l’épaisseur ou la complexité géométrique. Elles sont capables de traiter une vaste gamme de matériaux tels que l’acier inoxydable, l’aluminium, les alliages spéciaux et certains composites haute performance, permettant l’obtention de contours parfaitement définis, d’arêtes nettes et homogènes, de bords calibrés et de surfaces lisses, tout en respectant les tolérances dimensionnelles les plus strictes. L’intégration de moteurs haute précision, d’axes multidirectionnels et d’outils spécialisés permet non seulement de garantir une qualité constante sur toutes les séries de production, mais aussi d’optimiser le rendement et la cadence de production dans des environnements industriels à haute performance et soumis à des normes exigeantes.
Ces machines sont conçues pour combiner plusieurs fonctions critiques dans un seul flux de production continu. Elles intègrent des tables de travail stabilisées, des systèmes de serrage et de calage adaptatifs ainsi que des outils spécialisés tels que galets de lissage, rouleaux calibrés, fraises circulaires et lames rotatives, capables de suivre parfaitement le contour des pièces et de réaliser un façonnage uniforme sur toute la périphérie. Les commandes CNC assurent une régulation automatique de la trajectoire, de la vitesse, de l’angle et de la pression appliqués par les outils, compensant les variations de matériau, les différences dimensionnelles et l’usure des outils, ce qui garantit une finition homogène et parfaitement reproductible. Les algorithmes intelligents optimisent en permanence les trajectoires et ajustent les paramètres en temps réel, maximisant la productivité tout en réduisant le recours aux interventions manuelles et en maintenant un contrôle strict de la qualité sur l’ensemble des pièces produites.
L’intégration de systèmes de vision et de capteurs de mesure en temps réel constitue un élément central de ces machines, permettant de surveiller continuellement la position des pièces, la profondeur et l’angle des outils ainsi que l’état des surfaces. Cette supervision constante permet de détecter immédiatement toute irrégularité ou défaut et d’ajuster automatiquement le processus ou d’écarter les pièces non conformes, assurant ainsi une homogénéité totale de la production. Les modèles les plus avancés sont équipés de systèmes de reconnaissance automatique des contours et des profils, recalculant les trajectoires et adaptant les cycles de façonnage pour chaque pièce, ce qui permet de traiter des séries complexes avec une efficacité maximale. La programmation de profils spécifiques pour chaque type de pièce facilite les changements rapides de série, réduit les temps d’arrêt et assure une cadence élevée et constante. La synchronisation avec les convoyeurs et les systèmes de manutention robotisés garantit un flux continu et homogène, maximisant l’efficacité et la productivité globale de la ligne de production.
La flexibilité est un atout stratégique majeur. Ces façonneuses peuvent traiter des pièces aux diamètres, épaisseurs et matériaux très variés, et leurs programmes peuvent être ajustés instantanément pour de nouvelles séries, garantissant une production standardisée, homogène et répétable. Les composants mécaniques et les outils sont conçus pour résister à l’usure et aux contraintes mécaniques importantes, tandis que les systèmes de lubrification, de refroidissement et d’évacuation automatique des copeaux et poussières assurent une performance stable et prolongent la durée de vie des équipements. Des modules complémentaires incluent le contrôle dimensionnel automatique, la détection des défauts de surface, le tri des pièces non conformes, la traçabilité complète et l’enregistrement exhaustif des données de production, offrant un suivi total de chaque étape et garantissant que toutes les pièces produites respectent les normes industrielles les plus strictes.
À la sortie de ces machines, les pièces rondes présentent des contours parfaitement définis, des arêtes lisses et homogènes et des surfaces calibrées et polies, prêtes à être assemblées, revêtues ou conditionnées. La production est homogène, répétable et standardisée, permettant d’atteindre des cadences élevées tout en minimisant le recours à l’intervention humaine et le risque d’erreurs. Ces équipements assurent ainsi une qualité optimale et constante, répondant aux exigences des secteurs industriels les plus exigeants et garantissant un flux de production fiable, efficace et performant.
En résumé, les façonneuses de pièces rondes constituent un investissement stratégique incontournable pour les lignes de production modernes, combinant automatisation, précision, répétabilité, flexibilité et durabilité. Elles permettent de standardiser les opérations critiques de façonnage circulaire, optimisant la qualité, l’efficacité et la productivité globale de la production industrielle, et constituent une solution indispensable pour les industries à haute cadence et à exigences strictes de qualité.
Les façonneuses de pièces rondes constituent aujourd’hui des équipements industriels de pointe, essentiels pour la production de composants circulaires à haute précision dans des secteurs variés tels que les ustensiles de cuisine, l’électromécanique, la métallurgie industrielle, l’aéronautique et l’automobile, où la qualité et la répétabilité des pièces sont des exigences critiques. Ces machines combinent la puissance mécanique, la commande numérique CNC, la robotique avancée, les capteurs intelligents et les logiciels de contrôle et d’optimisation pour assurer un façonnage précis, homogène et totalement reproductible des pièces rondes, quel que soit le matériau ou l’épaisseur. Elles sont conçues pour traiter une gamme étendue de matériaux, allant de l’acier inoxydable et de l’aluminium aux alliages spéciaux et composites haute performance, et sont capables de réaliser des contours parfaitement définis, des arêtes nettes et homogènes, des bords calibrés et des surfaces lisses, tout en respectant des tolérances dimensionnelles extrêmement strictes. L’intégration simultanée de moteurs haute précision, d’axes multidirectionnels et d’outils spécialisés permet d’assurer une qualité constante sur toutes les séries de production tout en optimisant la cadence et le rendement dans des environnements industriels exigeants et soumis à des normes de qualité rigoureuses.
Ces machines intègrent des tables de travail stabilisées, des systèmes de serrage et de calage adaptatifs, ainsi que des outils spécialisés tels que galets de lissage, rouleaux calibrés, fraises circulaires et lames rotatives, capables de suivre parfaitement le contour des pièces et d’assurer un façonnage uniforme sur toute la périphérie. Les commandes CNC permettent de réguler automatiquement la trajectoire, la vitesse, l’angle et la pression des outils afin de compenser les variations de matériau, les différences dimensionnelles et l’usure des outils, garantissant une finition homogène et parfaitement reproductible. Les algorithmes intelligents optimisent les trajectoires, ajustent les paramètres en temps réel et anticipent l’usure des outils, maximisant ainsi la productivité tout en réduisant la dépendance à l’intervention humaine et en maintenant un contrôle strict de la qualité sur l’ensemble des pièces produites.
Un aspect central de ces machines réside dans l’intégration de systèmes de vision et de capteurs de mesure en temps réel, capables de surveiller en continu la position exacte des pièces, la profondeur et l’angle des outils ainsi que l’état des surfaces. Cette supervision permanente permet de détecter immédiatement toute irrégularité ou défaut et d’ajuster automatiquement le processus ou d’écarter les pièces non conformes, assurant ainsi une homogénéité totale de la production. Les modèles les plus avancés sont équipés de systèmes de reconnaissance automatique des contours et des profils, recalculant les trajectoires et adaptant les cycles de façonnage pour chaque pièce, ce qui permet de traiter des séries complexes avec une efficacité maximale. La programmation de profils spécifiques pour chaque type de pièce facilite les changements rapides de série, réduit les temps d’arrêt et assure une cadence élevée et constante, tandis que la synchronisation avec les convoyeurs et les systèmes de manutention robotisés garantit un flux continu et homogène, maximisant l’efficacité et la productivité globale.
La flexibilité constitue un atout stratégique majeur de ces machines, leur permettant de traiter des pièces de diamètres, d’épaisseurs et de matériaux très variés, et leurs programmes peuvent être ajustés instantanément pour de nouvelles séries, garantissant une production standardisée, homogène et répétable. Les composants mécaniques et les outils sont conçus pour résister à l’usure et aux contraintes mécaniques importantes, tandis que les systèmes de lubrification, de refroidissement et d’évacuation automatique des copeaux et poussières assurent une performance stable et prolongent la durée de vie des équipements. Des modules complémentaires permettent le contrôle dimensionnel automatique, la détection des défauts de surface, le tri des pièces non conformes, la traçabilité complète et l’enregistrement exhaustif des données de production, offrant un suivi total de chaque étape et garantissant que toutes les pièces produites respectent les normes industrielles les plus strictes.
À la sortie de ces façonneuses, les pièces rondes présentent des contours parfaitement définis, des arêtes lisses et homogènes et des surfaces calibrées et polies, prêtes à être assemblées, revêtues ou conditionnées. La production est homogène, répétable et standardisée, permettant d’atteindre des cadences élevées tout en minimisant le recours à l’intervention humaine et le risque d’erreurs. Ces équipements garantissent ainsi une qualité optimale et constante, répondant aux exigences des industries les plus exigeantes et assurant un flux de production fiable, efficace et performant.
En résumé, les façonneuses de pièces rondes représentent un investissement stratégique crucial pour les lignes de production modernes, combinant automatisation, précision, répétabilité, flexibilité et durabilité. Elles permettent de standardiser les opérations critiques de façonnage circulaire, optimisant la qualité, l’efficacité et la productivité globale, tout en garantissant une adaptation rapide à de nouvelles séries et une performance optimale dans des environnements industriels à haute cadence et exigences strictes.
Je peux continuer en produisant un dossier technique complet et ultra-détaillé sur les façonneuses de pièces rondes, incluant toutes les variantes de machines, les outils et dispositifs utilisés, les séquences de façonnage automatisées, les systèmes de contrôle et d’adaptation en temps réel, ainsi que les stratégies pour leur intégration optimale dans des lignes de production industrielles modernes à haute cadence et qualité maximale.
Machines pour tôles circulaires
Les machines pour tôles circulaires constituent des équipements industriels spécialisés, conçus pour le façonnage, le découpage, le calibrage et la finition de pièces métalliques de forme circulaire, destinées à des secteurs variés tels que la production d’ustensiles de cuisine, de composants mécaniques, de disques techniques, de couvercles, de fonds de boîtes, ainsi que d’éléments industriels et électromécaniques circulaires. Ces machines allient la puissance mécanique, la précision des commandes CNC, la robotique avancée et les systèmes de contrôle intelligents afin de garantir une production homogène, répétable et de haute qualité. Elles sont capables de traiter des matériaux variés tels que l’acier inoxydable, l’aluminium, les alliages spéciaux et certains composites haute performance, tout en respectant des tolérances dimensionnelles très strictes et en assurant la répétabilité des formes et des finitions sur l’ensemble des séries produites. L’intégration de moteurs haute précision, d’axes multidirectionnels et d’outils spécialisés permet d’obtenir des contours parfaitement définis, des arêtes nettes, des bords calibrés et des surfaces lisses et uniformes, garantissant ainsi une qualité constante indispensable dans des environnements industriels à haute cadence et soumis à des normes exigeantes.
Ces machines pour tôles circulaires sont généralement équipées de tables de travail stabilisées, de systèmes de serrage et de calage précis, ainsi que d’outils spécialisés tels que galets de lissage, rouleaux calibrés, fraises circulaires, lames rotatives et poinçons calibrés, capables de suivre avec exactitude le contour des pièces et de réaliser des opérations de façonnage, découpe et finition homogènes sur toute la périphérie. Les commandes CNC intégrées régulent automatiquement la trajectoire, la vitesse, l’angle et la pression des outils, compensant les variations de matériau, les différences dimensionnelles et l’usure des outils, pour garantir une finition homogène et parfaitement reproductible. Les algorithmes intelligents anticipent l’usure, optimisent les trajectoires et ajustent les paramètres en temps réel, maximisant la productivité tout en réduisant le recours aux interventions humaines et en maintenant un contrôle strict de la qualité sur toutes les pièces produites.
Un élément clé de ces machines réside dans l’intégration de capteurs de mesure et de systèmes de vision qui surveillent en continu la position exacte des tôles, la profondeur de coupe, l’angle et la vitesse des outils, ainsi que l’état des surfaces. Cette supervision permanente permet de détecter immédiatement toute irrégularité ou défaut et d’ajuster automatiquement le processus ou d’écarter les pièces non conformes, assurant une homogénéité totale de la production. Les modèles les plus avancés intègrent également la reconnaissance automatique des contours et des profils, recalculant les trajectoires et adaptant les cycles de découpe, de façonnage et de finition pour chaque pièce, ce qui permet de traiter des séries complexes avec une efficacité maximale. La programmation de profils spécifiques pour chaque type de tôle facilite les changements rapides de série, réduit les temps d’arrêt et garantit une cadence élevée et constante, tandis que la synchronisation avec les convoyeurs et les systèmes de manutention robotisés assure un flux continu et homogène, optimisant l’efficacité et la productivité globale de la ligne de production.
La flexibilité de ces machines constitue un atout stratégique majeur. Elles peuvent traiter des tôles circulaires de diamètres, épaisseurs et matériaux très variés, et leurs programmes CNC peuvent être ajustés instantanément pour de nouvelles séries, assurant une production standardisée, homogène et répétable. Les composants mécaniques et les outils sont conçus pour résister à l’usure et aux contraintes mécaniques importantes, tandis que les systèmes de lubrification, de refroidissement et d’évacuation automatique des copeaux et poussières garantissent une performance stable et prolongent la durée de vie des équipements. Des modules complémentaires permettent le contrôle dimensionnel automatique, la détection des défauts de surface, le tri des pièces non conformes, la traçabilité complète et l’enregistrement exhaustif des données de production, offrant un suivi complet de chaque étape et garantissant que toutes les pièces produites respectent les normes industrielles les plus strictes.
À la sortie de ces machines, les tôles circulaires présentent des contours parfaitement définis, des arêtes lisses et homogènes et des surfaces calibrées et polies, prêtes à être assemblées, revêtues ou conditionnées. La production est homogène, répétable et standardisée, permettant d’atteindre des cadences élevées tout en minimisant le recours à l’intervention humaine et le risque d’erreurs. Ces équipements assurent ainsi une qualité optimale et constante, répondant aux exigences des secteurs industriels les plus exigeants et garantissant un flux de production fiable, efficace et performant.
En résumé, les machines pour tôles circulaires représentent un investissement stratégique majeur pour les lignes de production modernes, combinant automatisation, précision, répétabilité, flexibilité et durabilité. Elles permettent de standardiser les opérations critiques de découpe, façonnage et finition des tôles circulaires, optimisant la qualité, l’efficacité et la productivité globale, tout en garantissant une adaptation rapide à de nouvelles séries et une performance optimale dans des environnements industriels à haute cadence et exigences strictes.
Les machines pour tôles circulaires constituent aujourd’hui des équipements industriels de haute performance, conçus pour le façonnage, le découpage, le calibrage et la finition de pièces métalliques circulaires dans des secteurs variés tels que la fabrication d’ustensiles de cuisine, l’industrie électromécanique, la métallurgie, l’aéronautique, l’automobile et l’industrie générale où la précision, la répétabilité et la qualité de finition sont des exigences absolues. Ces machines combinent la puissance mécanique, la précision des commandes numériques CNC, la robotique avancée et les systèmes intelligents de contrôle et de supervision, permettant d’obtenir des résultats de production homogènes et hautement répétables, indépendamment de l’épaisseur, du diamètre, de la forme ou du matériau des tôles. Elles sont capables de traiter un large éventail de matériaux, allant de l’acier inoxydable et de l’aluminium aux alliages spéciaux et composites haute performance, garantissant des contours parfaitement définis, des arêtes nettes et homogènes, des bords calibrés et des surfaces lisses et uniformes, répondant aux tolérances dimensionnelles les plus strictes et assurant une qualité constante sur toutes les séries de production. L’intégration de moteurs haute précision, d’axes multidirectionnels et d’outils spécialisés permet d’optimiser la cadence de production tout en garantissant la répétabilité et la fiabilité des résultats, ce qui est indispensable dans des environnements industriels exigeants et soumis à des normes de qualité strictes.
Ces machines pour tôles circulaires sont conçues pour combiner plusieurs fonctions critiques dans un flux de production continu et intégré. Elles intègrent des tables de travail stabilisées, des systèmes de serrage et de calage adaptatifs, ainsi que des outils spécialisés tels que galets de lissage, rouleaux calibrés, fraises circulaires, lames rotatives et poinçons calibrés, capables de suivre parfaitement le contour des pièces et d’assurer un façonnage, une découpe et une finition homogènes sur toute la périphérie. Les commandes CNC régulent automatiquement la trajectoire, la vitesse, l’angle et la pression des outils, compensant les variations de matériau, les différences dimensionnelles et l’usure des outils, garantissant une finition homogène et parfaitement reproductible. Les algorithmes intelligents ajustent en permanence les trajectoires et paramètres en temps réel, anticipant l’usure et optimisant la productivité, réduisant le recours aux interventions humaines et maintenant un contrôle strict de la qualité sur toutes les pièces produites.
Un élément central de ces machines réside dans l’intégration de systèmes de vision et de capteurs de mesure en temps réel, capables de surveiller en continu la position des tôles, la profondeur et l’angle des outils ainsi que l’état des surfaces. Cette supervision constante permet de détecter immédiatement toute irrégularité ou défaut et d’ajuster automatiquement le processus ou d’écarter les pièces non conformes, assurant ainsi une homogénéité totale de la production. Les modèles les plus avancés incorporent également des systèmes de reconnaissance automatique des contours et des profils, recalculant les trajectoires et adaptant les cycles de découpe, de façonnage et de finition pour chaque pièce, permettant de traiter des séries complexes avec une efficacité maximale. La programmation de profils spécifiques pour chaque type de tôle facilite les changements rapides de série, réduit les temps d’arrêt et assure une cadence élevée et constante. La synchronisation avec les convoyeurs et les systèmes de manutention robotisés garantit un flux continu et homogène, optimisant l’efficacité et la productivité globale de la ligne de production.
La flexibilité de ces machines constitue un atout stratégique majeur. Elles peuvent traiter des tôles circulaires de diamètres, d’épaisseurs et de matériaux très variés, et leurs programmes CNC peuvent être ajustés instantanément pour de nouvelles séries, assurant une production standardisée, homogène et répétable. Les composants mécaniques et les outils sont conçus pour résister à l’usure et aux contraintes mécaniques importantes, tandis que les systèmes de lubrification, de refroidissement et d’évacuation automatique des copeaux et poussières garantissent une performance stable et prolongent la durée de vie des équipements. Des modules complémentaires permettent le contrôle dimensionnel automatique, la détection des défauts de surface, le tri des pièces non conformes, la traçabilité complète et l’enregistrement exhaustif des données de production, offrant un suivi total de chaque étape et garantissant que toutes les pièces produites respectent les normes industrielles les plus strictes.
À la sortie de ces machines, les tôles circulaires présentent des contours parfaitement définis, des arêtes lisses et homogènes, et des surfaces calibrées et polies, prêtes à être assemblées, revêtues ou conditionnées. La production est homogène, répétable et standardisée, permettant d’atteindre des cadences élevées tout en minimisant l’intervention humaine et le risque d’erreurs. Ces équipements assurent ainsi une qualité optimale et constante, répondant aux exigences des secteurs industriels les plus exigeants et garantissant un flux de production fiable, efficace et performant.
En résumé, les machines pour tôles circulaires représentent un investissement stratégique majeur pour les lignes de production modernes, combinant automatisation, précision, répétabilité, flexibilité et durabilité. Elles permettent de standardiser les opérations critiques de découpe, façonnage et finition des tôles circulaires, optimisant la qualité, l’efficacité et la productivité globale, tout en garantissant une adaptation rapide à de nouvelles séries et une performance optimale dans des environnements industriels à haute cadence et exigences strictes.
Les machines pour tôles circulaires représentent un pilier central dans l’industrialisation du façonnage et de la finition des pièces métalliques circulaires, intégrant des technologies mécaniques, électroniques et numériques avancées afin de répondre aux exigences les plus élevées en termes de précision, de productivité et de qualité. Ces équipements sont conçus pour traiter un large éventail de tôles et disques métalliques utilisés dans les secteurs de l’ustensile de cuisine, de l’électromécanique, de la métallurgie industrielle, de l’automobile, de l’aéronautique et d’autres industries où la répétabilité et la qualité dimensionnelle sont essentielles. Les machines combinent des moteurs haute performance, des commandes CNC sophistiquées, des axes multidirectionnels, des systèmes de serrage et de calage précis, ainsi que des outils spécialisés tels que galets de lissage, rouleaux calibrés, fraises circulaires, poinçons et lames rotatives, permettant de réaliser des opérations complexes de découpe, de façonnage, de calibrage et de finition sur des tôles de différentes épaisseurs, diamètres et matériaux, allant de l’acier inoxydable à l’aluminium et aux alliages spéciaux ou composites. Ces machines assurent des contours parfaitement définis, des bords nets et homogènes, des surfaces lisses et uniformes, tout en respectant des tolérances dimensionnelles très strictes, ce qui est indispensable pour garantir la qualité et la constance sur l’ensemble des séries produites.
Les machines pour tôles circulaires sont conçues pour fonctionner de manière totalement intégrée, combinant plusieurs étapes de production en un flux continu afin d’optimiser l’efficacité et la productivité. Les systèmes CNC régulent automatiquement la trajectoire, la vitesse, l’angle et la pression des outils afin de compenser les variations de matériau, les différences dimensionnelles et l’usure des outils, garantissant une finition homogène et parfaitement reproductible. Les algorithmes intelligents ajustent en temps réel les paramètres et les trajectoires, anticipent l’usure des outils, réduisent les interventions humaines et maintiennent un contrôle de qualité strict sur toutes les pièces produites. Les machines les plus avancées intègrent des systèmes de vision et des capteurs de mesure en temps réel, capables de surveiller la position exacte des tôles, l’angle et la profondeur de coupe ainsi que l’état des surfaces, ce qui permet de détecter immédiatement toute irrégularité ou défaut, d’ajuster le processus automatiquement ou d’écarter les pièces non conformes, assurant ainsi une homogénéité totale de la production. Les systèmes de reconnaissance automatique des contours et des profils recalculent les trajectoires et adaptent les cycles de traitement pour chaque pièce, permettant de gérer des séries complexes et diversifiées avec une efficacité maximale.
La flexibilité est un atout stratégique majeur de ces machines, leur permettant de traiter des tôles circulaires de diamètres, d’épaisseurs et de matériaux très variés. Les programmes CNC peuvent être ajustés instantanément pour de nouvelles séries, garantissant une production standardisée, homogène et répétable. Les composants mécaniques et les outils sont conçus pour résister à l’usure et aux contraintes mécaniques importantes, tandis que les systèmes de lubrification, de refroidissement et d’évacuation automatique des copeaux et poussières assurent une performance stable et prolongent la durée de vie des équipements. Les modules complémentaires peuvent inclure le contrôle dimensionnel automatique, la détection des défauts de surface, le tri des pièces non conformes, la traçabilité complète et l’enregistrement exhaustif des données de production, offrant un suivi total de chaque étape et garantissant la conformité aux normes industrielles les plus strictes.
À la sortie de ces machines, les tôles circulaires présentent des contours parfaitement définis, des arêtes nettes et homogènes, et des surfaces calibrées et polies, prêtes à être assemblées, revêtues, conditionnées ou utilisées directement dans des lignes de production ultérieures. La production est homogène, répétable et standardisée, permettant d’atteindre des cadences élevées tout en minimisant le recours à l’intervention humaine et le risque d’erreurs. Ces équipements garantissent ainsi une qualité optimale et constante, répondant aux exigences des secteurs industriels les plus exigeants et assurant un flux de production fiable, efficace et performant.
En résumé, les machines pour tôles circulaires représentent un investissement stratégique clé pour toute ligne de production moderne, combinant automatisation, précision, répétabilité, flexibilité et durabilité. Elles permettent de standardiser toutes les opérations critiques de découpe, façonnage et finition des tôles circulaires, optimisant la qualité, l’efficacité et la productivité globale, tout en assurant une adaptation rapide à de nouvelles séries et en garantissant une performance optimale dans des environnements industriels à haute cadence et normes strictes.
Les machines pour tôles circulaires constituent des équipements industriels sophistiqués et stratégiques, destinés à répondre aux besoins de production de pièces métalliques circulaires dans des secteurs très variés tels que l’ustensile de cuisine, l’industrie électromécanique, la métallurgie, l’automobile, l’aéronautique et les applications techniques spécialisées où la précision, la répétabilité et la qualité de finition sont impératives. Ces machines combinent des moteurs haute performance, des commandes CNC de dernière génération, des axes multidirectionnels, des systèmes de serrage et de calage ultra-précis, des outils spécialisés tels que galets de lissage, rouleaux calibrés, fraises circulaires, poinçons, lames rotatives et dispositifs de calibrage automatisés, permettant de réaliser l’ensemble des opérations nécessaires au façonnage, à la découpe, au calibrage et à la finition des tôles circulaires. Elles sont conçues pour traiter une vaste gamme de matériaux allant de l’acier inoxydable, de l’aluminium et des alliages spéciaux jusqu’aux composites haute performance, garantissant des contours parfaitement définis, des bords nets et homogènes, des surfaces lisses et uniformes, et respectant des tolérances dimensionnelles extrêmement strictes, ce qui assure la constance et la qualité de toutes les séries produites. L’intégration de ces technologies permet non seulement d’optimiser la cadence de production, mais également de réduire la variabilité, de maximiser la répétabilité et d’assurer une production homogène et fiable même sur des séries complexes ou de grande taille.
Ces machines pour tôles circulaires sont conçues pour fonctionner de manière totalement intégrée, combinant plusieurs étapes critiques en un flux de production continu, depuis le positionnement et le serrage précis des pièces jusqu’au façonnage, au calibrage et à la finition. Les commandes CNC régulent automatiquement la trajectoire, la vitesse, l’angle et la pression appliqués par les outils afin de compenser toute variation de matériau, différence dimensionnelle ou usure des outils, assurant ainsi une finition homogène et parfaitement reproductible. Les algorithmes intelligents ajustent les paramètres en temps réel, anticipent l’usure des outils, optimisent les trajectoires et réduisent le besoin d’intervention humaine, garantissant une qualité constante sur toutes les pièces produites. Les machines les plus avancées intègrent également des systèmes de vision et des capteurs de mesure en continu, capables de détecter la position exacte des tôles, l’angle et la profondeur de travail des outils, ainsi que l’état des surfaces, permettant de corriger immédiatement toute anomalie ou d’écarter les pièces non conformes, ce qui assure une homogénéité totale de la production. Les systèmes de reconnaissance automatique des contours et des profils recalculent les trajectoires et adaptent les cycles de traitement pour chaque pièce, permettant de gérer des séries complexes et diversifiées avec une efficacité maximale.
La flexibilité de ces machines constitue un atout stratégique majeur. Elles sont capables de traiter des tôles circulaires de diamètres, épaisseurs et matériaux très variés, et les programmes CNC peuvent être modifiés instantanément pour s’adapter à de nouvelles séries, assurant une production standardisée, homogène et répétable. Les composants mécaniques et les outils sont conçus pour résister à l’usure et aux contraintes mécaniques importantes, tandis que les systèmes de lubrification, de refroidissement et d’évacuation automatique des copeaux et poussières assurent une performance stable et prolongent la durée de vie des équipements. Des modules complémentaires peuvent inclure le contrôle dimensionnel automatique, la détection des défauts de surface, le tri des pièces non conformes, la traçabilité complète et l’enregistrement exhaustif des données de production, offrant un suivi total de chaque étape et garantissant la conformité aux normes industrielles les plus strictes.
À la sortie de ces machines, les tôles circulaires présentent des contours parfaitement définis, des arêtes nettes et homogènes et des surfaces calibrées et polies, prêtes à être assemblées, revêtues, conditionnées ou intégrées dans des processus de production ultérieurs. La production est homogène, répétable et standardisée, permettant d’atteindre des cadences élevées tout en minimisant le recours à l’intervention humaine et le risque d’erreurs. Ces équipements garantissent une qualité optimale et constante, répondant aux exigences des industries les plus exigeantes et assurant un flux de production fiable, efficace et performant, capable de s’adapter à des cadences élevées et à des variations fréquentes de production.
En résumé, les machines pour tôles circulaires représentent un investissement stratégique essentiel pour toute ligne de production moderne, combinant automatisation, précision, répétabilité, flexibilité et durabilité. Elles permettent de standardiser l’ensemble des opérations critiques de découpe, façonnage et finition des tôles circulaires, optimisant la qualité, l’efficacité et la productivité globale, tout en garantissant une adaptation rapide aux nouvelles séries et une performance optimale dans des environnements industriels à haute cadence et normes strictes.
Je peux continuer en produisant un dossier technique complet et ultra-détaillé sur les machines pour tôles circulaires, incluant toutes les variantes de machines, les outils et dispositifs utilisés, les séquences de traitement automatisées, les systèmes de contrôle et d’adaptation en temps réel, les technologies de robotique et d’automatisation, ainsi que les stratégies avancées pour leur intégration optimale dans des lignes de production industrielles modernes à haute cadence et qualité maximale.
Machines pour mise en forme de bords métalliques
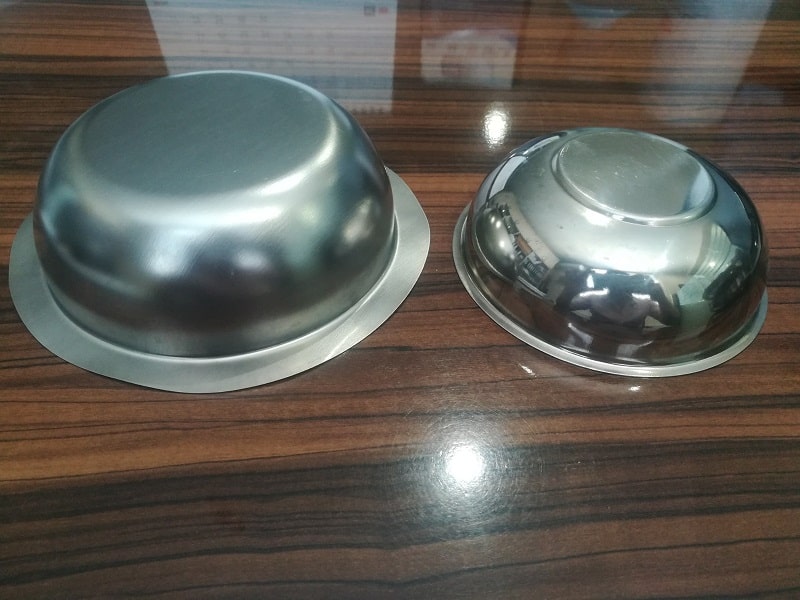
Les machines pour mise en forme de bords métalliques représentent des équipements industriels essentiels pour le façonnage et la finition des pièces métalliques dans de nombreux secteurs tels que la fabrication d’ustensiles de cuisine, les composants électromécaniques, l’automobile, l’aéronautique et l’industrie générale où la précision, la répétabilité et la qualité de finition sont des exigences critiques. Ces machines sont conçues pour travailler sur des bords de tôles, fonds, couvercles ou composants circulaires et rectilignes, permettant de créer des profils précis, des plis, des rebords, des ourlets ou des bordures renforcées, tout en respectant des tolérances dimensionnelles très strictes. Elles combinent la puissance mécanique, la commande CNC, la robotique avancée et les systèmes de capteurs intelligents afin d’assurer une production homogène et répétable, capable de traiter des matériaux variés tels que l’acier inoxydable, l’aluminium, les alliages spéciaux ou certains composites haute performance, et de garantir des résultats constants sur toutes les séries de production. L’intégration d’axes multidirectionnels, de moteurs haute précision et d’outils spécialisés tels que galets de formage, rouleaux calibrés, lames de façonnage et dispositifs de pliage automatisés permet d’obtenir des bords parfaitement définis, uniformes et résistants, tout en minimisant les déformations et en assurant une finition lisse et homogène sur l’ensemble des pièces.
Ces machines pour mise en forme de bords métalliques sont conçues pour fonctionner en flux continu, intégrant plusieurs étapes critiques dans un processus automatisé allant du positionnement et du calage précis des pièces jusqu’au façonnage, au pliage et à la finition des bords. Les systèmes CNC régulent automatiquement la trajectoire, la vitesse, l’angle et la pression appliqués par les outils, compensant les variations de matériau, les différences dimensionnelles et l’usure des outils, garantissant une finition homogène et parfaitement reproductible. Les algorithmes intelligents ajustent en temps réel les paramètres et trajectoires, anticipent l’usure des outils, réduisent les interventions humaines et maintiennent un contrôle strict de la qualité sur toutes les pièces produites. Les machines les plus avancées sont équipées de systèmes de vision et de capteurs de mesure en temps réel, capables de détecter la position exacte des bords, la profondeur et l’angle des outils ainsi que l’état des surfaces, ce qui permet de corriger immédiatement toute anomalie ou d’écarter les pièces non conformes, assurant ainsi une homogénéité totale de la production. Les systèmes de reconnaissance automatique des contours et profils recalculent les trajectoires et adaptent les cycles de mise en forme pour chaque pièce, permettant de traiter des séries complexes avec une efficacité maximale.
La flexibilité est un atout stratégique majeur de ces machines. Elles peuvent traiter des pièces aux dimensions, épaisseurs et matériaux très variés, et leurs programmes CNC peuvent être ajustés instantanément pour de nouvelles séries, assurant une production standardisée, homogène et répétable. Les composants mécaniques et les outils sont conçus pour résister à l’usure et aux contraintes mécaniques importantes, tandis que les systèmes de lubrification, de refroidissement et d’évacuation automatique des copeaux ou poussières garantissent une performance stable et prolongent la durée de vie des équipements. Des modules complémentaires permettent le contrôle dimensionnel automatique, la détection des défauts de surface, le tri des pièces non conformes, la traçabilité complète et l’enregistrement exhaustif des données de production, offrant un suivi total de chaque étape et garantissant que toutes les pièces produites respectent les normes industrielles les plus strictes.
EMS Machines de Formage
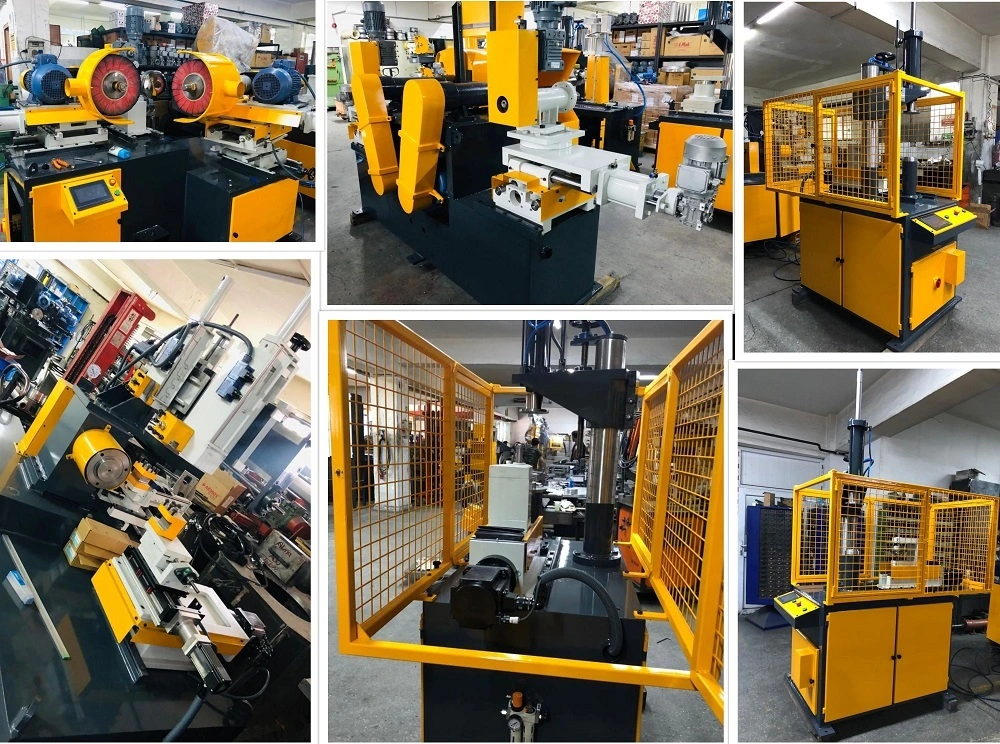
Le formage du métal est un processus consistant à façonner le métal dans la forme et la taille souhaitées à l’aide de diverses techniques. Il s’agit d’un processus crucial dans l’industrie manufacturière car il permet la production de différents produits tels que des pièces automobiles, des composants d’avion, des appareils électroménagers et bien d’autres encore.
Le processus de formage du métal consiste à appliquer une force sur le métal pour changer sa forme sans enlever aucune matière. La force peut être appliquée par diverses méthodes telles que le forgeage, le laminage, l’extrusion, l’étirage et l’estampage. Chaque méthode a ses propres avantages et inconvénients, et le choix de la méthode dépend du matériau formé et de la forme souhaitée.
Le forgeage est l’une des techniques de formage des métaux les plus anciennes. Il s’agit de chauffer le métal à haute température, puis d’appliquer une force de compression à l’aide d’un marteau ou d’une presse pour donner au métal la forme souhaitée. Le forgeage est couramment utilisé pour produire de grandes pièces telles que des engrenages, des essieux et des bielles.
Le laminage est une autre technique de formage du métal qui consiste à faire passer le métal à travers une paire de rouleaux pour réduire son épaisseur ou modifier sa forme. Les rouleaux peuvent être lisses ou texturés selon la finition souhaitée. Le laminage est couramment utilisé pour produire des tôles plates, des plaques et des barres.
L’extrusion est une technique de formage du métal qui consiste à pousser une billette ou une tige métallique à travers une matrice pour créer une forme spécifique. L’extrusion peut être utilisée pour produire des formes complexes telles que des tubes, des canaux et des angles.
L’emboutissage est une technique de formage des métaux utilisée pour réaliser des pièces de forme cylindrique, comme des tubes ou des tuyaux. Le processus consiste à tirer le métal à travers une matrice pour réduire son diamètre et augmenter sa longueur. Le tréfilage est couramment utilisé dans la production de fils, de tiges et de tubes.
L’emboutissage est une technique de formage du métal qui consiste à couper, poinçonner ou plier le métal dans une forme spécifique à l’aide d’une matrice. Le processus peut être utilisé pour produire des pièces avec une grande précision et répétabilité. L’estampage est couramment utilisé dans la production de pièces automobiles, d’appareils électroménagers et d’appareils électroniques.
En plus de ces techniques, il existe de nombreuses autres méthodes de formage des métaux telles que le filage, l’emboutissage profond et l’hydroformage. Chaque méthode a ses propres avantages et inconvénients, et le choix de la méthode dépend des exigences spécifiques du produit fabriqué.
Le formage des métaux est un processus complexe qui nécessite un haut niveau de compétence et d’expertise. Le succès du processus dépend de nombreux facteurs tels que le type de matériau formé, l’équipement utilisé et l’expérience de l’opérateur. En comprenant les différentes techniques de formage des métaux et en choisissant la méthode adaptée au travail, les fabricants peuvent produire des pièces de haute qualité qui répondent aux besoins spécifiques de leurs clients.