Machine à Tarauder pour Radiateurs en Aluminium et en Fonte: La machine à tarauder pour radiateurs en aluminium et en fonte est un équipement industriel spécialement conçu pour réaliser des filets internes ou externes sur les composants des radiateurs. Ces machines sont essentielles dans l’industrie de la fabrication de radiateurs, notamment ceux utilisés dans le chauffage central. Le processus de taraudage permet de créer des pas de vis pour assembler les différentes pièces du radiateur, comme les connecteurs et les tuyaux, tout en garantissant une étanchéité parfaite et une fixation solide.
Dans le cas des radiateurs en aluminium et en fonte, le choix des matériaux pour la machine à tarauder est crucial. L’aluminium, étant un métal léger et bon conducteur de chaleur, est souvent préféré pour sa capacité à chauffer rapidement et efficacement. Cependant, il est plus fragile que la fonte, qui est robuste et durable, mais moins performante en termes de conductivité thermique. Ces différences de propriétés nécessitent des machines à tarauder adaptées aux particularités de chaque matériau.
Le processus de taraudage dans la fabrication de radiateurs en aluminium et en fonte est effectué sous des conditions contrôlées. L’opérateur doit veiller à la vitesse de rotation de la machine, à la profondeur du taraudage et à l’utilisation de lubrifiants spécifiques afin d’assurer une coupe nette et précise. Le taraudage est réalisé par une série d’outils de coupe qui sont souvent réalisés en acier haute résistance ou en carbure pour résister aux contraintes imposées par les matériaux durs comme la fonte.
En fonction du type de radiateur et des spécifications du client, la machine à tarauder peut être équipée de différents types de tarauds, qui sont choisis en fonction du diamètre et du type de filetage requis. L’aluminium, bien que plus malléable, nécessite des réglages précis pour éviter toute déformation du matériau, tandis que la fonte, plus dure, nécessite des outils de coupe plus résistants et une vitesse de travail plus lente pour éviter l’usure prématurée des outils.
L’automatisation de ces machines à tarauder a considérablement amélioré l’efficacité et la précision des processus de fabrication. Les machines modernes peuvent effectuer des séries de taraudages sans intervention manuelle, ce qui réduit les risques d’erreurs humaines et augmente la productivité. De plus, ces machines sont souvent équipées de systèmes de contrôle numérique, permettant de programmer des paramètres de travail spécifiques et de suivre en temps réel l’état de la production.
Le contrôle de qualité est une étape cruciale dans le processus de fabrication des radiateurs. Après le taraudage, chaque pièce est soigneusement inspectée pour s’assurer que les filets sont correctement formés et qu’il n’y a pas de défauts. Des tests de résistance à la pression sont également réalisés pour garantir que les radiateurs ne présenteront pas de fuites une fois installés.
En résumé, la machine à tarauder pour radiateurs en aluminium et en fonte est un outil indispensable dans la fabrication de radiateurs modernes. Son rôle est de garantir la précision et la fiabilité des assemblages, ce qui contribue à l’efficacité et à la longévité des systèmes de chauffage. Les avancées technologiques, telles que l’automatisation et l’utilisation de matériaux de coupe de haute qualité, permettent de produire des radiateurs de haute performance tout en optimisant les coûts de production.
Machine à Tarauder pour Radiateurs en Aluminium et en Fonte

Les machines à tarauder pour radiateurs en aluminium et en fonte sont souvent intégrées dans des lignes de production automatisées. Cette intégration permet non seulement une production rapide mais aussi une réduction des erreurs humaines. L’automatisation de ces machines comprend des systèmes de réglage automatique des paramètres, des capteurs pour vérifier la qualité des taraudages, ainsi que des contrôles informatisés qui assurent une constance parfaite dans chaque série produite.
En outre, la gestion de la chaleur et des contraintes mécaniques lors du taraudage est un aspect important dans la conception des machines. Lorsqu’un matériau comme l’aluminium ou la fonte est traité, il y a un échauffement de l’outil et du composant, ce qui peut entraîner une usure prématurée si ce phénomène n’est pas correctement géré. Par conséquent, les machines à tarauder modernes sont souvent équipées de systèmes de refroidissement efficaces, comme des buses qui pulvérisent des fluides de coupe ou des lubrifiants pour réduire la friction et la chaleur générée.
Le choix du système de lubrification est également important pour le résultat final du taraudage. L’utilisation de lubrifiants de haute qualité permet non seulement de protéger les outils de coupe, mais aussi d’améliorer la finition des filets, en réduisant la formation de bavures ou de copeaux résiduels qui pourraient compromettre la qualité du filet. Les machines sont parfois dotées de systèmes de filtration des fluides pour éviter que des impuretés ne nuisent à la précision du taraudage.
En plus des aspects mécaniques et techniques, l’ergonomie de la machine à tarauder est un facteur clé dans l’amélioration de la productivité et de la sécurité des opérateurs. Les machines modernes sont conçues pour être faciles à utiliser et à maintenir, avec des interfaces numériques intuitives qui permettent aux opérateurs de contrôler et de surveiller chaque étape du processus de production. Cela inclut la possibilité de modifier les paramètres de taraudage, de lancer des cycles de nettoyage ou de maintenance, et de réaliser des diagnostics pour prévenir toute panne.
Les radiateurs en fonte, bien que plus lourds et plus robustes, sont souvent utilisés dans des applications où la longévité et la résistance aux chocs thermiques sont primordiales. Leur fabrication nécessite un taraudage particulièrement minutieux, car la fonte est un matériau fragile qui peut se fissurer sous des contraintes mal gérées. Par conséquent, la machine à tarauder doit être équipée de moteurs puissants capables de supporter les forces nécessaires pour travailler ce matériau tout en minimisant le risque de déformation ou de cassure.
De l’autre côté, les radiateurs en aluminium, qui sont plus légers et dotés d’une meilleure conductivité thermique, sont largement utilisés dans les systèmes modernes de chauffage central, où la rapidité de réponse thermique est un avantage. Le processus de taraudage pour l’aluminium nécessite une attention particulière afin de ne pas endommager le matériau, qui est plus tendre et susceptible aux marques de l’outil.
Il est important de noter que, même si l’automatisation réduit les risques d’erreur, la surveillance continue et l’entretien des machines restent essentiels. Cela permet d’éviter des pannes coûteuses et d’assurer une production fluide. Les opérateurs doivent être formés non seulement pour piloter les machines mais aussi pour effectuer des contrôles de qualité réguliers, vérifier les niveaux de lubrifiants et d’autres paramètres, ainsi que pour intervenir rapidement en cas d’anomalie.
Enfin, l’impact environnemental des machines à tarauder ne doit pas être négligé. De plus en plus, les fabricants cherchent à réduire leur empreinte écologique en optant pour des équipements plus économes en énergie et des méthodes de production qui génèrent moins de déchets. Les lubrifiants écologiques, les systèmes de recyclage des fluides de coupe et les matériaux de coupe durables sont des exemples d’initiatives prises pour répondre à ces préoccupations. De même, les machines modernes sont souvent conçues pour être moins bruyantes et moins polluantes, contribuant ainsi à un environnement de travail plus sain pour les employés.
En somme, la machine à tarauder pour radiateurs en aluminium et en fonte représente un équipement clé dans la chaîne de production des radiateurs modernes. Elle combine des technologies avancées de précision, de contrôle de la température, de gestion des matériaux et d’automatisation pour produire des composants fiables, durables et de haute qualité. Grâce à des innovations continues, ces machines permettent de répondre à la demande croissante de radiateurs performants et écologiques, tout en maintenant des standards élevés de sécurité et de productivité.
Introduction
La machine à tarauder pour radiateurs en aluminium et en fonte est un équipement industriel spécialisé dans la création de filets de vis internes et externes sur les composants des radiateurs. Le taraudage est une opération essentielle pour l’assemblage de pièces de radiateurs, permettant de réaliser des connexions solides et étanches. Cet équipement est adapté pour différents matériaux, chacun ayant des exigences techniques spécifiques, notamment l’aluminium et la fonte, qui présentent des caractéristiques distinctes en termes de résistance, de conductivité thermique et de durabilité.
Matériaux et Spécificités
Aluminium
L’aluminium est un métal léger, apprécié pour sa capacité à transférer la chaleur rapidement, ce qui le rend idéal pour des radiateurs performants. Cependant, il est plus malléable et peut se déformer si les conditions de taraudage ne sont pas optimisées. Pour éviter cela, les machines à tarauder destinées à ce matériau doivent offrir un contrôle précis de la vitesse et de la pression appliquées. Les outils de coupe utilisés sont souvent en acier haute vitesse ou en carbure de tungstène, offrant un compromis entre résistance à l’usure et performance de coupe.
Fonte
La fonte, en revanche, est un matériau plus dur et plus robuste, souvent utilisé dans des radiateurs nécessitant une résistance élevée à la pression et aux températures extrêmes. Cependant, la fonte est également plus fragile sous des contraintes mal gérées et peut se fissurer si les outils de coupe sont trop agressifs. Les machines à tarauder pour la fonte doivent être dotées de moteurs puissants et de systèmes de refroidissement efficaces pour maintenir une température contrôlée et éviter toute dégradation du matériau pendant l’opération de taraudage.
Processus de Taraudage
Le taraudage est un processus mécanique qui permet de créer des filets dans un trou préexistant. Dans le cas des radiateurs, ces filets sont utilisés pour assembler les différentes pièces du radiateur, comme les tuyaux et les connecteurs. Le processus comprend plusieurs étapes, dont :
- Préparation du trou : Avant le taraudage, un trou est percé dans le composant du radiateur. La taille et la profondeur du trou dépendent du type de filetage requis.
- Taraudage proprement dit : Le taraudage est réalisé à l’aide d’un outil appelé taraud, qui est inséré dans le trou et tourné pour couper le filetage. Ce processus peut être effectué manuellement ou de manière automatisée, selon la configuration de la machine.
- Contrôle de la qualité : Après le taraudage, les pièces sont inspectées pour s’assurer que les filets sont uniformes et exempts de défauts. Des tests de résistance et des contrôles dimensionnels sont effectués pour garantir que le produit final respecte les standards de qualité.
Automatisation et Contrôle Numérique
Les machines modernes à tarauder pour radiateurs sont souvent automatisées, ce qui permet une production plus rapide et plus précise. Ces machines sont équipées de systèmes de contrôle numérique (CNC) qui permettent de programmer les paramètres de taraudage, tels que la vitesse de rotation, la profondeur du filet et la pression appliquée. L’automatisation permet également de réduire les erreurs humaines et d’augmenter la productivité, tout en garantissant une qualité constante des produits fabriqués.
Les systèmes de contrôle avancés peuvent ajuster en temps réel les paramètres de la machine en fonction des caractéristiques du matériau ou des conditions de production, assurant ainsi une précision maximale. De plus, certains systèmes peuvent surveiller en continu l’état des outils de coupe, détectant l’usure et optimisant les cycles de production en fonction de l’état de l’équipement.
Systèmes de Lubrification et de Refroidissement
Le refroidissement et la lubrification sont des éléments cruciaux dans le processus de taraudage, particulièrement lors du travail avec des matériaux comme la fonte, qui génèrent beaucoup de chaleur. La lubrification réduit la friction entre l’outil de coupe et le matériau, ce qui permet de prolonger la durée de vie de l’outil et d’améliorer la qualité du taraudage. En outre, le refroidissement permet de dissiper la chaleur générée lors de la coupe, évitant ainsi que la pièce ne se déforme ou que l’outil ne s’use prématurément.
Les machines à tarauder modernes sont souvent équipées de systèmes de lubrification automatisés, qui pulvérisent un fluide de coupe sur les zones de contact pendant le processus. Ces fluides sont parfois recyclés grâce à des filtres intégrés, ce qui permet de réduire les déchets et de diminuer les coûts d’exploitation. Les systèmes de refroidissement, tels que les buses de refroidissement ou les bains d’immersion, aident à maintenir une température optimale pendant l’opération de taraudage.
Maintenance et Ergonomie
Les machines à tarauder pour radiateurs sont conçues pour être robustes et faciles à maintenir. Les opérations de maintenance régulières incluent la vérification de l’état des outils de coupe, des systèmes de lubrification et de refroidissement, ainsi que l’inspection des composants mécaniques pour détecter toute usure prématurée. Les machines modernes sont dotées de systèmes de diagnostic automatisés qui permettent de repérer les pannes potentielles avant qu’elles ne causent des interruptions dans la production.
L’ergonomie des machines est également un aspect important pour garantir la sécurité et le confort des opérateurs. Les interfaces utilisateur modernes sont intuitives et permettent un contrôle facile des paramètres de la machine. De plus, des dispositifs de sécurité, tels que des capteurs et des systèmes d’arrêt d’urgence, sont intégrés pour prévenir les accidents et garantir un environnement de travail sûr.
Impact Environnemental et Écologique
L’impact environnemental des machines à tarauder est de plus en plus pris en compte dans la conception des équipements. Les fabricants cherchent à réduire la consommation d’énergie et à minimiser les déchets produits pendant le processus. Par exemple, l’utilisation de lubrifiants écologiques, la réduction de la consommation d’eau pour le refroidissement, ainsi que la mise en place de systèmes de recyclage des fluides de coupe contribuent à une production plus respectueuse de l’environnement.
De plus, les machines modernes sont conçues pour être plus efficaces en termes d’énergie, réduisant ainsi leur empreinte carbone. L’utilisation de matériaux durables pour les composants des machines et la mise en place de programmes de maintenance préventive permettent d’allonger la durée de vie des équipements et de réduire les besoins en remplacement de pièces.
Conclusion
La machine à tarauder pour radiateurs en aluminium et en fonte est un outil fondamental dans la fabrication des radiateurs modernes. Grâce aux avancées technologiques en matière d’automatisation, de contrôle numérique, de lubrification et de refroidissement, ces machines permettent de produire des composants de haute qualité et de garantir la fiabilité des systèmes de chauffage. L’intégration de solutions plus écologiques et d’une meilleure gestion de l’impact environnemental montre que l’industrie continue d’évoluer pour répondre aux défis du XXIe siècle, tout en optimisant la productivité et la durabilité des produits fabriqués.
Matériaux et Spécificités
Les matériaux utilisés pour la fabrication des radiateurs, qu’ils soient en aluminium ou en fonte, jouent un rôle essentiel dans les performances thermiques, la durabilité et la facilité de fabrication de ces composants. Chaque matériau présente des caractéristiques spécifiques qui influencent le choix du processus de fabrication, y compris le taraudage, et la conception des machines utilisées pour produire ces radiateurs. L’aluminium, en particulier, est apprécié pour sa légèreté et sa conductivité thermique, ce qui le rend idéal pour des radiateurs capables de diffuser la chaleur rapidement et efficacement. Toutefois, bien que l’aluminium soit un excellent conducteur thermique, il est également plus malléable, ce qui peut rendre sa manipulation et son usinage plus délicats. Les machines utilisées pour travailler l’aluminium doivent donc être réglées avec une grande précision afin d’éviter tout endommagement du matériau, notamment lors des opérations de taraudage. Ce matériau, bien que relativement plus facile à usiner que la fonte, nécessite des outils de coupe spécifiques, souvent en acier haute vitesse ou en carbure, pour garantir des résultats nets et précis.
D’autre part, la fonte est un matériau beaucoup plus dense et plus dur, ce qui lui confère une résistance à la pression et une capacité à maintenir la chaleur plus longtemps. Cette durabilité fait de la fonte un choix privilégié pour les radiateurs destinés à des environnements plus exigeants, tels que les systèmes de chauffage central. Cependant, la dureté de la fonte rend l’usinage plus complexe et plus exigeant. Le taraudage des radiateurs en fonte, par exemple, demande une grande attention, car une mauvaise gestion de la vitesse ou de la pression pendant le processus pourrait entraîner des fissures ou une usure prématurée des outils de coupe. En raison de la fragilité relative de la fonte sous certaines contraintes mécaniques, il est essentiel que les machines à tarauder destinées à ce matériau soient équipées de moteurs puissants et de systèmes de refroidissement sophistiqués pour prévenir la surchauffe et garantir une coupe efficace. Ce processus est souvent plus lent que celui de l’aluminium, car la fonte nécessite un contrôle minutieux pour éviter la fissuration du matériau.
Bien que l’aluminium et la fonte soient utilisés pour des applications similaires, leur traitement dans les machines à tarauder nécessite des approches distinctes en raison de leurs différences notables. L’aluminium, étant plus léger et plus souple, peut parfois être plus facilement usiné, mais il reste sensible aux défauts si les conditions de fabrication ne sont pas optimisées. Par exemple, les machines doivent être équipées de mécanismes de lubrification efficaces pour réduire les risques de déformation ou de mauvaise finition des filets. La fonte, en revanche, peut supporter des conditions de travail plus rigoureuses mais requiert un entretien plus fréquent des outils de coupe en raison de sa dureté. Les matériaux de coupe utilisés dans le travail de la fonte doivent être extrêmement résistants, et des systèmes de refroidissement sophistiqués sont nécessaires pour garantir que l’outil ne surchauffe pas pendant l’opération.
Ainsi, bien que les deux matériaux aient des avantages en termes de performance thermique et de durabilité, le choix du matériau influe considérablement sur le processus de fabrication, en particulier le taraudage. Le passage d’un matériau à l’autre dans les lignes de production peut impliquer des ajustements techniques précis sur les machines utilisées, allant de la vitesse de coupe à la température et à l’utilisation de lubrifiants spécifiques. Cela nécessite une expertise approfondie dans le domaine des matériaux et des machines de fabrication, afin de garantir que les radiateurs produits soient à la fois efficaces, durables et faciles à assembler.
Processus de Taraudage
Le processus de taraudage est une opération cruciale dans la fabrication de radiateurs, en particulier pour ceux fabriqués à partir de matériaux comme l’aluminium et la fonte. Le taraudage permet de créer des filets de vis dans des pièces de métal, qui sont ensuite utilisées pour assembler différentes parties du radiateur, comme les tuyaux et les connecteurs. Cette opération est essentielle pour garantir une fixation solide et une étanchéité parfaite des éléments du radiateur, ce qui est primordial pour leur fonctionnement et leur sécurité.
Le taraudage commence par la préparation du matériau, où un trou est percé dans le composant à l’aide d’un foret. Ce trou doit avoir un diamètre précis en fonction du type de filet requis. La précision de cette étape est essentielle, car elle conditionne la qualité du taraudage à venir. Si le trou est trop grand ou trop petit, il peut affecter la forme du filet ou la solidité de la fixation une fois le filet formé.
Une fois le trou percé, l’outil principal du taraudage, appelé “taraud”, est utilisé pour couper les filets. Un taraud est un outil de coupe à plusieurs arêtes qui tourne dans le trou pour créer le filet. Selon les spécifications du radiateur et le type de matériau, différents types de tarauds peuvent être utilisés. Les tarauds pour les matériaux plus tendres, comme l’aluminium, sont généralement fabriqués à partir d’acier haute vitesse ou d’autres matériaux résistants à l’usure. En revanche, pour les matériaux plus durs, comme la fonte, des tarauds en carbure de tungstène ou d’autres matériaux extrêmement résistants peuvent être nécessaires pour garantir un usinage précis et efficace.
Le processus de taraudage lui-même se déroule sous une rotation de l’outil, qui coupe progressivement le matériau en suivant le contour du trou. Ce processus est parfois assisté par des machines automatisées, qui permettent de réguler de manière précise la vitesse de rotation du taraud, ainsi que la profondeur du filet, pour s’assurer que chaque pièce est réalisée selon les spécifications exactes. L’automatisation permet d’éviter les erreurs humaines et assure une production plus rapide et plus constante. Cependant, ce processus nécessite également un contrôle minutieux pour éviter la formation de défauts comme les bavures ou les déformations des filets, qui pourraient compromettre l’étanchéité du radiateur.
Le lubrifiant est également un élément clé du processus de taraudage. Lors du travail avec des matériaux comme l’aluminium ou la fonte, une friction importante se produit entre le taraud et le matériau, générant de la chaleur. Pour éviter la surchauffe et réduire l’usure prématurée des outils de coupe, des fluides de coupe ou des lubrifiants sont utilisés. Ces fluides servent également à éliminer les copeaux générés pendant le taraudage, permettant ainsi de maintenir l’outil propre et d’augmenter sa durée de vie. Le choix du lubrifiant est donc crucial, car il doit être compatible avec le matériau travaillé et la machine utilisée, tout en offrant un refroidissement et une lubrification efficaces.
Après que le taraudage est effectué, les pièces doivent être inspectées pour s’assurer que les filets sont parfaitement formés. Des tests dimensionnels sont réalisés pour vérifier la précision des dimensions du filet et s’assurer qu’elles correspondent aux tolérances spécifiées. Il est également courant de réaliser des essais de résistance pour s’assurer que le radiateur ne présentera pas de fuites une fois assemblé. Les contrôles de qualité sont essentiels pour garantir que chaque pièce répond aux exigences de sécurité et de performance, notamment en termes de résistance à la pression et à la chaleur.
Une fois les pièces vérifiées, elles sont prêtes à être assemblées. Le taraudage assure non seulement une fixation mécanique solide, mais aussi une étanchéité optimale grâce à la précision des filets formés. Il est donc primordial que le processus soit effectué avec soin et selon des normes strictes de qualité. Tout manquement à cette étape pourrait entraîner des défauts dans les radiateurs, affectant leur efficacité et leur sécurité.
Le processus de taraudage peut également varier en fonction de l’outillage utilisé et de la configuration de la machine. Par exemple, certaines machines à tarauder modernes sont équipées de commandes numériques qui permettent d’ajuster avec précision la profondeur de coupe, la vitesse de rotation et d’autres paramètres en fonction du matériau et de la taille du filet souhaité. Ces ajustements garantissent une précision maximale et contribuent à une production plus rapide et plus uniforme des pièces.
Le taraudage, en tant qu’étape clé dans la production de radiateurs, nécessite donc une expertise technique approfondie et un équipement de haute précision. Bien qu’il puisse être effectué manuellement, les machines automatisées ont considérablement amélioré l’efficacité et la précision de cette opération, tout en réduisant les risques d’erreurs humaines. Grâce à ces avancées, il est possible de produire des radiateurs de haute qualité, à la fois fiables et durables, répondant aux exigences modernes de performance thermique et de sécurité.
Automatisation et Contrôle Numérique
L’automatisation et le contrôle numérique ont révolutionné le processus de fabrication des radiateurs, en particulier lorsqu’il s’agit de taraudage pour des matériaux comme l’aluminium et la fonte. Ces technologies permettent non seulement de garantir une précision et une répétabilité exceptionnelles, mais aussi d’améliorer considérablement l’efficacité de la production. Le contrôle numérique des machines de taraudage repose sur l’utilisation de systèmes informatisés qui supervisent et régulent toutes les étapes du processus, offrant ainsi une flexibilité accrue et un contrôle en temps réel sur chaque paramètre de fabrication.
Les machines à tarauder modernes, équipées de commandes numériques, permettent d’ajuster avec une grande précision la vitesse de rotation de l’outil, la profondeur de coupe, ainsi que les mouvements de la machine pendant l’opération de taraudage. Grâce à ces ajustements fins, il devient possible d’optimiser chaque étape du processus, que ce soit pour des matériaux plus tendres comme l’aluminium ou des matériaux plus durs comme la fonte. Ces systèmes sont conçus pour s’adapter aux spécifications exactes de chaque projet, ce qui permet une production de pièces parfaitement conformes aux exigences de qualité.
Le contrôle numérique permet également de programmer les cycles de production en fonction des besoins spécifiques de chaque série de fabrication. Par exemple, le taraudage de radiateurs en aluminium peut nécessiter des paramètres différents de ceux utilisés pour la fonte, notamment en termes de vitesse de coupe et de lubrification. Les opérateurs peuvent ainsi entrer ces paramètres dans la machine, qui les ajuste automatiquement, minimisant ainsi les risques d’erreur humaine. Une fois les paramètres programmés, la machine exécute le processus de manière autonome, ce qui permet de réduire le temps de production et d’améliorer la constance des résultats.
En plus de la programmation des paramètres, l’automatisation permet un suivi en temps réel de l’état de la machine et du processus de taraudage. Des capteurs et des dispositifs de surveillance intégrés mesurent en permanence des variables telles que la température de l’outil, la pression exercée sur la pièce, ou la quantité de lubrifiant utilisé. Ces données sont ensuite envoyées à un système central qui peut alerter les opérateurs en cas de problème, permettant ainsi une maintenance prédictive et prévenant toute panne ou dysfonctionnement avant qu’il n’affecte la production. Cela réduit les arrêts imprévus et optimise l’efficacité globale des machines.
L’intégration du contrôle numérique ne se limite pas à la régulation des paramètres de taraudage, elle inclut également la gestion de l’ensemble du flux de production. Les machines modernes peuvent être connectées à des systèmes de gestion de la production qui permettent de suivre l’état des pièces en temps réel, de planifier la production en fonction des demandes et d’analyser les données de performance pour optimiser les futurs processus de fabrication. Cette approche centralisée permet de coordonner plusieurs machines et lignes de production, ce qui est particulièrement utile dans des environnements de production de grande envergure, où de nombreux composants doivent être fabriqués simultanément.
L’automatisation a également un impact positif sur la réduction des coûts de production. En minimisant l’intervention humaine et en augmentant la vitesse de fabrication, les machines automatisées réduisent les coûts associés à la main-d’œuvre et à la gestion des erreurs. De plus, grâce à l’automatisation, les machines peuvent fonctionner de manière continue, 24 heures sur 24, sans avoir besoin de pauses pour les ajustements manuels ou les recalibrages fréquents. Cette capacité à maintenir une production ininterrompue contribue à une augmentation significative des volumes de fabrication tout en maintenant une qualité constante.
En ce qui concerne la maintenance, les machines à contrôle numérique offrent une assistance considérable. Les systèmes informatisés permettent une surveillance continue de l’état des outils de coupe, détectant ainsi l’usure et prévoyant les moments où un remplacement ou un affûtage des outils est nécessaire. Cela permet de garantir que les outils de coupe restent efficaces et performants tout au long de leur cycle de vie, ce qui augmente la durée de vie de la machine et réduit le besoin d’interventions manuelles fréquentes. En cas de problème technique, les systèmes numériques peuvent fournir des diagnostics détaillés pour aider les techniciens à résoudre rapidement les dysfonctionnements, minimisant ainsi les temps d’arrêt et optimisant la production.
L’automatisation et le contrôle numérique facilitent également l’intégration de méthodes de production plus écologiques. Grâce à l’optimisation des cycles de production, il est possible de réduire la consommation de ressources telles que l’énergie et les fluides de coupe. Les machines sont programmées pour fonctionner de manière plus efficiente, ce qui permet de réduire les déchets et de mieux gérer les lubrifiants et autres matériaux consommables. De plus, les systèmes de surveillance permettent de détecter immédiatement toute anomalie dans l’utilisation des fluides ou de l’énergie, permettant ainsi d’intervenir rapidement pour rectifier le problème et éviter tout gaspillage.
En conclusion, l’automatisation et le contrôle numérique ont profondément transformé la fabrication des radiateurs, en particulier dans des processus complexes comme le taraudage. Ces technologies permettent non seulement d’améliorer la précision et l’efficacité, mais aussi de garantir une qualité constante et d’optimiser la production à grande échelle. Avec la possibilité d’ajuster les paramètres de manière fine, de surveiller en temps réel le processus et de planifier efficacement la production, les entreprises peuvent répondre aux exigences de qualité élevées tout en réduisant les coûts et en augmentant leur compétitivité sur le marché.
Systèmes de Lubrification et de Refroidissement
Les systèmes de lubrification et de refroidissement jouent un rôle crucial dans le processus de fabrication des radiateurs, en particulier lors de l’opération de taraudage, où des températures élevées et des frottements intenses peuvent se produire. Ces systèmes sont indispensables pour garantir la durabilité des outils de coupe, la qualité des pièces produites et la performance globale du processus de fabrication. Le lubrifiant et le refroidisseur agissent ensemble pour réduire la chaleur générée par les frottements entre l’outil de coupe et le matériau, tout en facilitant l’évacuation des copeaux et en préservant l’intégrité des pièces usinées.
Le refroidissement est nécessaire pour dissiper la chaleur produite par l’outil de coupe pendant le taraudage, surtout lorsque l’on travaille avec des matériaux durs comme la fonte. Lorsque l’outil de coupe entre en contact avec le matériau, une friction intense se produit, générant de la chaleur. Cette chaleur peut entraîner une dégradation de la qualité du taraudage, une usure prématurée des outils et même des déformations du matériau. Le système de refroidissement sert à maintenir une température optimale, permettant ainsi une coupe plus nette et plus précise, tout en évitant l’endommagement de la pièce ou de l’outil. Les systèmes de refroidissement peuvent être intégrés directement dans la machine et sont souvent équipés de buses qui pulvérisent un liquide de refroidissement sur la zone de coupe.
Les fluides de refroidissement utilisés peuvent être des huiles ou des liquides spécifiques, qui sont souvent formulés pour résister à des températures élevées et offrir une viscosité idéale pour une lubrification optimale. Ces fluides sont également conçus pour minimiser les frottements et garantir un écoulement facile des copeaux, évitant ainsi qu’ils ne s’accumulent autour de l’outil de coupe et ne gênent le processus. En plus d’éliminer la chaleur, les fluides de refroidissement contribuent également à prolonger la durée de vie des outils de coupe en réduisant leur usure due à la friction continue avec le matériau.
Les systèmes de lubrification, quant à eux, jouent un rôle complémentaire essentiel en réduisant le frottement entre l’outil de coupe et la pièce. Lors du taraudage, un lubrifiant de haute qualité est utilisé pour faciliter l’opération en diminuant la friction qui se produit à l’interface entre l’outil et le matériau. Une lubrification insuffisante peut entraîner une surchauffe de l’outil, une usure prématurée et une dégradation de la qualité du filetage. Le lubrifiant forme une couche protectrice qui permet à l’outil de glisser plus facilement sur la surface du matériau, ce qui améliore la qualité du taraudage et prolonge la durée de vie de l’outil.
L’une des principales préoccupations liées à l’utilisation des lubrifiants et des systèmes de refroidissement est l’entretien et la gestion des fluides. Dans de nombreuses machines modernes, les fluides de refroidissement et de lubrification sont recyclés grâce à des systèmes de filtration sophistiqués. Cela permet non seulement de réduire les coûts en diminuant la consommation de nouveaux fluides, mais aussi de limiter l’impact environnemental de la production. Les systèmes de filtration éliminent les impuretés, les copeaux métalliques et les résidus qui peuvent affecter l’efficacité du refroidissement et de la lubrification. De plus, l’utilisation de lubrifiants écologiques a gagné en popularité, car ils permettent de réduire les risques pour l’environnement tout en offrant des performances similaires aux fluides traditionnels.
Le choix du type de lubrifiant et de refroidisseur dépend largement du matériau à traiter et des spécifications du processus de taraudage. Par exemple, pour des matériaux comme l’aluminium, qui sont plus tendres, des fluides de coupe moins visqueux peuvent être utilisés, tandis que pour des matériaux plus durs comme la fonte, des lubrifiants plus épais et des systèmes de refroidissement plus puissants peuvent être nécessaires pour maintenir une température stable et éviter la surchauffe. En outre, la quantité de fluide appliquée doit être soigneusement contrôlée, car trop de lubrifiant peut entraîner des éclaboussures et une accumulation sur la pièce, tandis que trop peu peut provoquer une usure rapide de l’outil et un échauffement excessif.
Les systèmes modernes de lubrification et de refroidissement peuvent également être équipés de capteurs et de dispositifs de surveillance qui permettent de vérifier en temps réel le niveau et la température des fluides. Ces technologies permettent aux opérateurs de s’assurer que le système fonctionne de manière optimale et de détecter tout dysfonctionnement ou défaillance avant qu’il n’affecte la production. Par exemple, des capteurs peuvent surveiller la température du fluide de refroidissement pour s’assurer qu’il ne dépasse pas une température critique, ce qui pourrait nuire à l’efficacité du refroidissement et à la qualité du travail. De même, des capteurs peuvent vérifier le débit de lubrifiant pour garantir une application suffisante tout au long du processus de taraudage.
En conclusion, les systèmes de lubrification et de refroidissement sont essentiels pour garantir une performance optimale dans le processus de taraudage, en particulier lors du travail avec des matériaux comme l’aluminium et la fonte. Leur rôle dans la réduction de la chaleur, la diminution de la friction et l’élimination des copeaux est fondamental pour maintenir la qualité des pièces usinées et assurer une durée de vie prolongée des outils de coupe. Grâce aux avancées technologiques, ces systèmes sont devenus de plus en plus efficaces et écologiques, contribuant ainsi à une production de radiateurs plus durable, plus rapide et plus précise.
Taraudage
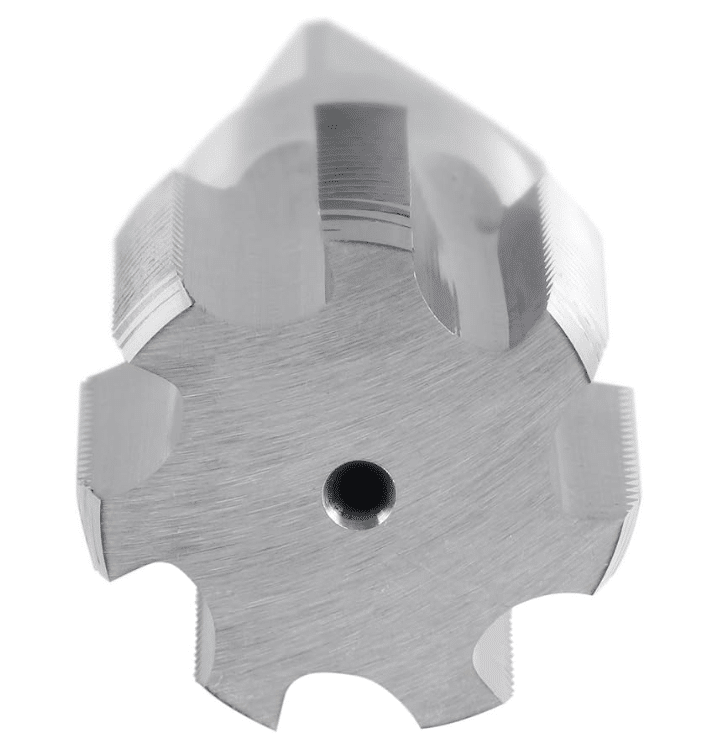
Le taraudage est un processus essentiel dans la fabrication de nombreuses pièces métalliques, en particulier lorsqu’il s’agit de créer des filetages internes dans des composants tels que des radiateurs. Ce procédé consiste à utiliser un outil appelé taraud, qui, en tournant dans un trou préalablement percé, découpe des filets à l’intérieur du matériau, permettant ainsi de créer des zones de fixation pour des vis ou des boulons. Le taraudage est utilisé dans une variété d’applications, notamment dans l’industrie automobile, la mécanique de précision et, bien sûr, la fabrication de radiateurs en fonte et en aluminium, où la création de filetages précis est cruciale pour assurer des assemblages solides et étanches.
Le processus commence généralement par le perçage d’un trou dans la pièce métallique, dont le diamètre est légèrement plus petit que celui du filetage à créer. Ce trou sert de base pour l’outil de taraudage. Il est essentiel que ce trou soit percé à la bonne profondeur et avec un diamètre précis pour garantir que le filetage sera bien formé et compatible avec les vis ou les boulons destinés à y être insérés. Une fois le trou prêt, l’outil de taraudage, un dispositif rotatif équipé de plusieurs arêtes de coupe, est introduit dans le trou. En tournant, il découpe des spirales à l’intérieur du trou, formant ainsi les filets nécessaires.
Le taraudage peut être réalisé de manière manuelle ou automatisée, selon les besoins de production. Dans un contexte industriel, le processus est généralement automatisé, avec des machines équipées de moteurs puissants et de systèmes de contrôle numériques pour ajuster la vitesse de rotation et la profondeur du taraudage. Les machines modernes permettent de réaliser le taraudage de manière rapide et précise, minimisant ainsi les erreurs humaines et augmentant la productivité. La possibilité d’automatiser ces tâches permet également de maintenir une qualité constante tout au long de la production, réduisant ainsi le risque de défauts et améliorant l’efficacité du processus.
Pendant l’opération de taraudage, la friction générée entre l’outil de coupe et le matériau peut entraîner une élévation de la température. C’est pourquoi un système de lubrification et de refroidissement est souvent utilisé pour réduire la chaleur et faciliter l’évacuation des copeaux métalliques produits pendant l’opération. Un lubrifiant est appliqué sur la zone de coupe pour minimiser la friction et éviter l’usure prématurée des outils. Ce lubrifiant joue également un rôle crucial dans l’évacuation des copeaux, permettant ainsi un travail plus propre et plus fluide.
Le choix du type de taraud dépend du matériau à travailler. Par exemple, le taraudage de l’aluminium, un métal relativement tendre, peut être réalisé avec des outils plus fins et des vitesses de coupe plus rapides, tandis que la fonte, plus dure et plus fragile, nécessite des tarauds plus robustes et des vitesses plus lentes. Le taraudage de la fonte doit être effectué avec une grande précision pour éviter de provoquer des fissures ou des déformations dans le matériau. De même, l’angle et la forme des arêtes de coupe du taraud peuvent varier en fonction du type de filet souhaité, qu’il soit standard, profond ou très précis.
Une fois le processus de taraudage terminé, un contrôle minutieux est effectué pour vérifier la qualité des filets. Cela inclut des mesures précises de la profondeur, de la forme et de la taille des filets pour s’assurer qu’ils correspondent aux spécifications requises. Un mauvais taraudage peut entraîner des problèmes d’assemblage, comme des vis mal fixées ou des fuites dans les radiateurs, ce qui peut nuire à leur performance et à leur sécurité. C’est pourquoi des tests de résistance et de compatibilité sont souvent effectués pour garantir que les pièces fabriquées sont adaptées à leur fonction.
Le taraudage est un processus délicat qui exige non seulement des outils appropriés, mais aussi une gestion efficace de la production pour garantir que chaque pièce soit réalisée avec la plus grande précision. Dans de nombreux cas, la qualité du taraudage peut avoir un impact direct sur la durabilité du produit final, comme dans le cas des radiateurs, où un filetage bien réalisé est nécessaire pour assurer des connexions solides et sans fuite. Ce processus de fabrication est donc un élément clé de l’industrie métallurgique et de la production de composants mécaniques, et il continue d’évoluer grâce aux innovations technologiques, permettant de répondre aux exigences de précision, de rapidité et de rentabilité.
Le taraudage est un processus qui exige une grande précision et une compréhension approfondie des matériaux et des outils utilisés. Un aspect important du processus de taraudage est la gestion de la profondeur de coupe. Une profondeur de taraudage incorrecte peut entraîner un filetage trop court ou trop long, ce qui peut affecter la solidité de la fixation ou la capacité à y insérer des vis et des boulons. Les machines modernes dotées de contrôle numérique permettent de régler précisément la profondeur, garantissant ainsi que chaque pièce est traitée de manière uniforme et selon les tolérances strictes.
De plus, le taraudage nécessite une attention particulière à la direction du taraudage. Lorsque l’on travaille sur des matériaux comme la fonte ou l’aluminium, les tarauds doivent être orientés de manière à créer des filets dans le sens le plus efficace pour le matériau, tout en minimisant les risques d’endommagement ou de déformation de la pièce. Les outils de taraudage sont conçus avec des arêtes de coupe qui se déplacent en spirale dans le trou pour former des filets qui s’enroulent autour du diamètre interne du trou. Cela garantit que les filets sont bien formés et offrent une prise solide pour les vis ou boulons à insérer.
Un autre facteur clé à prendre en compte lors du taraudage est le type de filet que l’on souhaite créer. Il existe différents types de filet, tels que les filets triangulaires, carrés ou à pas fin, qui sont utilisés selon les exigences spécifiques de l’application. Par exemple, pour des applications de haute pression ou des environnements soumis à des températures extrêmes, des filets plus fins et plus précis peuvent être nécessaires pour garantir une étanchéité parfaite et une fixation robuste. Le choix du type de filet dépend largement des spécifications du projet, du matériau du radiateur et des performances attendues.
L’entretien des outils de taraudage est également crucial pour maintenir la qualité du travail. Les tarauds, comme tous les outils de coupe, s’usent avec le temps, et une usure excessive peut affecter la précision du processus de taraudage. Un outil mal entretenu peut créer des filets irréguliers ou endommager la pièce. Il est donc essentiel de surveiller régulièrement l’état des tarauds, de les aiguiser ou de les remplacer lorsque nécessaire. Certains ateliers de production utilisent des machines de diagnostic pour mesurer l’usure des outils et s’assurer qu’ils sont encore capables de fournir des performances optimales.
Dans le cadre de la production industrielle, la gestion des copeaux générés par le taraudage est également un aspect important. Les copeaux métalliques peuvent obstruer les outils et les systèmes de refroidissement, réduisant ainsi l’efficacité du processus. Des systèmes de collecte et d’évacuation des copeaux sont utilisés pour maintenir la zone de travail propre et éviter l’accumulation de résidus qui pourraient endommager les outils ou la machine elle-même. Les copeaux sont souvent récupérés pour être recyclés ou éliminés de manière appropriée, réduisant ainsi l’impact environnemental de la production.
L’intégration du taraudage dans des processus automatisés est un autre domaine où des progrès considérables ont été réalisés. L’automatisation permet non seulement de réduire les erreurs humaines, mais aussi d’augmenter la vitesse de production tout en maintenant une qualité constante. Grâce à des systèmes de contrôle numérique, les machines peuvent être programmées pour effectuer des cycles de taraudage continus, ajustant automatiquement les paramètres en fonction des besoins spécifiques de chaque pièce. Cela est particulièrement bénéfique dans les environnements de production de masse, où des milliers de pièces doivent être fabriquées avec la même précision et le même soin.
Le contrôle qualité post-taraudage est essentiel pour s’assurer que les pièces fabriquées respectent les normes les plus élevées. Après le processus de taraudage, des inspections visuelles et dimensionnelles sont réalisées pour vérifier l’intégrité des filets. Les instruments de mesure, tels que les micromètres, les jauges de filetage et les testeurs de profondeur, sont utilisés pour s’assurer que les dimensions des filets sont conformes aux spécifications. De plus, des tests de résistance peuvent être effectués pour vérifier que les pièces peuvent supporter les contraintes mécaniques auxquelles elles seront soumises.
Enfin, la traçabilité des pièces est une autre étape importante dans le processus de taraudage, surtout dans des secteurs comme l’automobile, l’aérospatiale ou la production d’équipements lourds. Chaque pièce peut être identifiée par un numéro de lot, permettant de suivre son parcours tout au long de la production et de vérifier la qualité à chaque étape. Cela facilite non seulement la gestion de la production, mais aussi le suivi en cas de défauts ou de retours de produits.
En résumé, le taraudage est une opération de fabrication fondamentale qui nécessite un haut niveau de précision et de contrôle pour garantir des résultats de qualité. Que ce soit pour des applications simples ou pour des pièces complexes telles que des radiateurs en fonte ou en aluminium, le processus de taraudage est essentiel pour assurer des assemblages solides et durables. L’évolution technologique dans le domaine du taraudage, en particulier avec l’intégration de systèmes automatisés et de contrôle numérique, a permis d’améliorer considérablement la vitesse, la précision et l’efficacité de ce processus, tout en répondant aux exigences strictes de qualité et de performance.
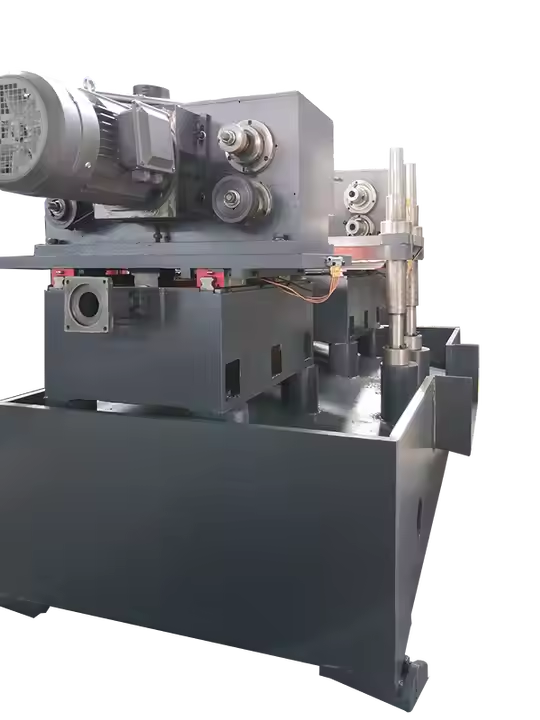
Le processus de taraudage continue de s’adapter aux défis modernes de l’industrie, où la recherche de plus grande efficacité, de réduction des coûts et d’amélioration de la durabilité est constante. À mesure que la technologie évolue, des innovations permettent de rendre le taraudage encore plus rapide et plus précis, tout en répondant aux exigences de qualité toujours plus strictes des clients. L’utilisation de machines à commande numérique par ordinateur (CNC) est l’une de ces avancées, car elle permet une gestion intégrée et automatisée des processus de taraudage. Cela inclut la programmation de cycles complexes, l’ajustement précis des paramètres de coupe et la surveillance en temps réel de l’état de l’outil, garantissant ainsi une qualité constante dans la production des pièces.
La numérisation et la collecte de données ont également changé la donne en matière de contrôle de la qualité. Grâce aux capteurs intégrés aux machines et aux systèmes d’analyse des performances en temps réel, les fabricants peuvent détecter des anomalies ou des variations de performance avant qu’elles n’affectent la production à grande échelle. Par exemple, une usure prématurée des outils peut être détectée par des capteurs de pression ou de température, permettant ainsi un remplacement anticipé des tarauds avant que des défauts de filetage ne se produisent. Cette approche proactive améliore la qualité des produits tout en réduisant les arrêts imprévus et les coûts liés aux réparations ou à la remise en état des pièces.
Les matériaux utilisés pour les tarauds ont également évolué, avec des alliages plus résistants et des revêtements améliorés qui augmentent la durée de vie des outils et permettent d’améliorer les performances du taraudage. Les revêtements en nitrure de titane (TiN), par exemple, sont largement utilisés pour leur capacité à résister à l’usure, à réduire la friction et à améliorer la résistance à la chaleur. Ces revêtements permettent d’effectuer le taraudage à des vitesses plus élevées tout en réduisant la production de chaleur et la friction, ce qui augmente la durée de vie des outils tout en maintenant la qualité des filets. Cette amélioration des matériaux de taraudage joue un rôle majeur dans l’efficacité globale de la production.
La possibilité d’adapter les outils de taraudage à des conditions de travail spécifiques est une autre caractéristique importante des progrès technologiques. En fonction du matériau à traiter, du type de filetage nécessaire et des caractéristiques du processus, des outils spécialisés peuvent être choisis pour optimiser la performance. Par exemple, pour les matériaux plus durs comme les alliages d’acier inoxydable ou certains types de fonte, des tarauds plus robustes et plus résistants aux conditions extrêmes peuvent être utilisés. De même, pour des applications spécifiques, comme le taraudage de pièces de précision dans l’aérospatiale, des outils de taraudage à haute performance, dotés de géométries de coupe spéciales, peuvent être employés pour garantir la précision nécessaire.
L’optimisation du processus de taraudage inclut également la gestion des conditions de coupe. Les paramètres tels que la vitesse de rotation de l’outil, la pression d’avance et la profondeur de coupe sont souvent ajustés en fonction de l’état du matériau et des caractéristiques spécifiques de la pièce. Un contrôle précis de ces paramètres permet de réduire l’usure des outils, de garantir des filets uniformes et d’améliorer la qualité de la finition. Dans certains cas, des techniques comme le taraudage sec ou semi-sec sont utilisées pour réduire la dépendance aux fluides de coupe, en particulier lorsque des fluides sont difficiles à gérer ou lorsqu’il y a des préoccupations environnementales. Ces techniques nécessitent cependant des machines de haute précision et des matériaux de coupe très résistants pour maintenir la performance du processus sans lubrification.
L’impact environnemental du processus de taraudage est également un aspect important de la production moderne. Les fabricants cherchent de plus en plus à réduire la consommation de fluides et à recycler les matériaux pour minimiser l’empreinte écologique. Par exemple, l’utilisation de systèmes de filtration et de recyclage des fluides permet de prolonger leur durée de vie et de réduire les déchets produits. De plus, l’amélioration des systèmes de gestion des copeaux permet non seulement d’évacuer plus efficacement les résidus métalliques, mais aussi de les recycler pour réutiliser les matériaux dans d’autres processus de fabrication.
Les exigences en matière de qualité et de précision dans des industries comme l’automobile, l’aérospatiale ou la fabrication d’équipements lourds ont renforcé la nécessité de méthodes de taraudage rigoureuses et fiables. Le contrôle strict des tolérances et la gestion des fichiers numériques permettent aujourd’hui de fabriquer des composants qui respectent des critères de performance très élevés. Dans ces secteurs, un petit défaut de filetage peut entraîner des défaillances graves, compromettant la sécurité des produits et la réputation des fabricants. Cela a conduit à une meilleure standardisation des processus et à une traçabilité complète des pièces fabriquées, permettant une inspection rigoureuse et la mise en œuvre de contrôles de qualité tout au long de la chaîne de production.
En conclusion, bien que le taraudage soit un procédé qui existe depuis longtemps, il continue d’évoluer avec les progrès technologiques. L’automatisation, l’optimisation des matériaux et des outils, ainsi que l’amélioration des systèmes de contrôle et de lubrification ont permis de rendre ce processus plus rapide, plus précis et plus respectueux de l’environnement. Ces avancées ont des implications profondes sur la qualité des produits finaux, notamment dans des secteurs industriels exigeants, et permettent de répondre aux besoins d’une production de plus en plus sophistiquée et efficace. L’innovation continue dans ce domaine ouvre de nouvelles possibilités pour améliorer la productivité tout en garantissant des normes de qualité élevées.
It seems you’re interested in continuing with sections or further detail. Could you clarify which aspect you’d like to explore next or if you’d prefer to break down the content into specific sections? Here’s a brief outline of possible sections based on the previous discussions:
- Introduction au Taraudage
- Matériaux Utilisés dans le Taraudage
- Types de Tarauds et Outils de Coupe
- Processus de Taraudage et Paramètres de Coupe
- Technologies et Automatisation du Taraudage
- Gestion des Copeaux et Systèmes de Refroidissement
- Contrôle de Qualité et Inspection
- Applications Industrielles du Taraudage
- Innovations et Développements Futurs dans le Taraudage
Le taraudage est un processus mécanique essentiel dans de nombreux secteurs industriels, notamment dans la fabrication de pièces nécessitant des filetages internes pour y insérer des vis, des boulons ou d’autres types de fixations. Il s’agit d’une opération de coupe réalisée à l’aide d’un outil appelé taraud, qui sert à créer des filets dans un trou préalablement percé. Ces filets permettent d’assurer une connexion solide et stable entre différentes pièces d’un assemblage. Le taraudage est utilisé dans des applications variées, allant des équipements automobiles aux composants d’avion, en passant par des systèmes de chauffage et de refroidissement, comme les radiateurs en fonte ou en aluminium.
Le processus de taraudage commence par la réalisation d’un trou pilote, qui est légèrement plus petit que le diamètre du filetage final. Ce trou est ensuite agrandi et façonné par le taraud, qui tourne dans le sens horaire pour couper les arêtes du filet à l’intérieur du trou. Les machines modernes permettent d’automatiser cette opération, assurant ainsi une grande précision dans la formation des filetages. L’outil utilisé pour cette opération est conçu avec des arêtes de coupe qui, lorsqu’elles entrent en contact avec le matériau, génèrent des filets internes parfaitement adaptés à la fixation de vis ou de boulons.
Le taraudage est souvent associé à des applications de précision, où la qualité du filetage est cruciale pour garantir une fixation fiable et sécurisée. Un mauvais taraudage peut entraîner des problèmes de fixation, des fuites dans des systèmes sous pression, ou des défaillances mécaniques dans des structures complexes. Par conséquent, le processus nécessite une attention particulière à la fois au choix des matériaux et à la conception des outils de coupe. De plus, la gestion de la vitesse de coupe, de la profondeur du taraudage et de la lubrification joue un rôle important pour obtenir un résultat optimal.
Dans l’industrie moderne, le taraudage est généralement effectué à l’aide de machines à commande numérique par ordinateur (CNC), qui permettent de régler avec précision tous les paramètres du processus. Cette automatisation du processus de taraudage a permis d’augmenter l’efficacité de la production tout en garantissant une qualité constante. Les machines CNC permettent également d’effectuer des ajustements en temps réel, offrant ainsi une flexibilité accrue dans la production de différentes pièces avec des spécifications variées.
Le choix des matériaux pour le taraudage dépend en grande partie du type de pièce à fabriquer. Par exemple, l’aluminium, qui est un métal relativement tendre, nécessite des tarauds avec une géométrie spécifique pour éviter l’usure prématurée, tandis que des matériaux plus durs, comme l’acier inoxydable ou la fonte, nécessitent des outils de coupe plus résistants et des vitesses de coupe plus lentes. Le contrôle de la qualité du taraudage est également une étape cruciale, et des inspections sont souvent réalisées pour garantir que les filets sont conformes aux spécifications et aux tolérances de l’industrie.
En somme, le taraudage est une technique essentielle dans la fabrication de composants mécaniques. Son objectif est de créer des filetages internes précis et durables, nécessaires à la fixation d’autres éléments dans un assemblage. Bien que simple en apparence, ce processus nécessite une maîtrise approfondie des outils, des matériaux et des paramètres de coupe pour assurer un résultat optimal et une production efficace. Grâce à l’automatisation et aux innovations technologiques, le taraudage est devenu une étape clé dans la fabrication de pièces de haute qualité pour une large gamme d’industries.
Matériaux Utilisés dans le Taraudage
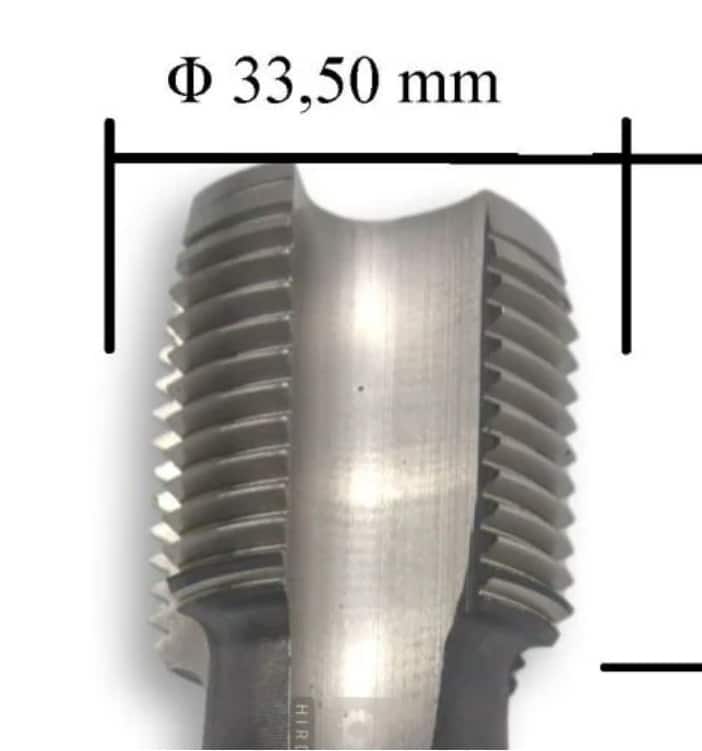
Les matériaux utilisés dans le taraudage jouent un rôle crucial dans la qualité, la précision et la durabilité du processus. Le choix des matériaux dépend largement du type de taraudage à effectuer et des propriétés du métal ou de la pièce à traiter. Chaque matériau présente des défis et des exigences spécifiques en termes de résistance, de ténacité et de réactivité à l’usure. L’objectif est d’assurer non seulement la réalisation de filetages de qualité, mais aussi d’optimiser la durée de vie des outils et la performance globale de l’opération.
Les matériaux de base pour le taraudage incluent une gamme de métaux allant des alliages d’aluminium aux aciers inoxydables et aux fontes, chacun ayant des caractéristiques uniques qui influencent la manière dont il réagit aux outils de coupe. Les matériaux les plus couramment utilisés pour les taraudages comprennent des métaux légers comme l’aluminium, des alliages métalliques plus durs comme l’acier et l’acier inoxydable, ainsi que des matériaux plus complexes tels que les fontes et les alliages de nickel.
L’aluminium est l’un des matériaux les plus faciles à tarauder en raison de sa relative douceur. Il est largement utilisé dans les secteurs automobile, aéronautique et de la fabrication de radiateurs en raison de sa légèreté et de sa conductivité thermique. Lors du taraudage de l’aluminium, il est essentiel d’utiliser des tarauds spécialement conçus pour éviter que le métal ne s’accumule dans les arêtes du taraud, ce qui peut entraîner des erreurs dans les filetages. Le choix d’un taraud adapté et une lubrification adéquate sont donc essentiels pour obtenir des filetages propres et nets.
L’acier, en particulier l’acier au carbone et l’acier allié, est un autre matériau couramment utilisé dans les opérations de taraudage. L’acier est plus résistant que l’aluminium, ce qui signifie qu’il nécessite des outils de coupe plus robustes. En fonction de sa composition, l’acier peut être plus ou moins difficile à tarauder. Les aciers inoxydables, en raison de leur résistance à la corrosion et de leur durabilité, sont utilisés dans des environnements où la résistance à l’humidité ou à des produits chimiques est nécessaire. Toutefois, l’acier inoxydable, en raison de sa dureté, peut entraîner une usure plus rapide des outils de taraudage. De plus, ce matériau génère davantage de chaleur durant le processus de taraudage, ce qui augmente les exigences en matière de lubrification et de refroidissement pour éviter l’endommagement des tarauds.
Les alliages spéciaux, tels que les alliages de nickel, sont également utilisés dans des applications spécifiques, notamment dans les environnements à haute température ou sous haute pression, où la résistance à la chaleur et à la corrosion est primordiale. Le taraudage de ces matériaux exige une attention particulière, car leur dureté et leur élasticité les rendent difficiles à traiter. Des outils de coupe spéciaux, souvent en carbure de tungstène ou d’autres matériaux ultra-résistants, sont nécessaires pour garantir des filets précis et durables.
La fonte, utilisée dans la fabrication de composants lourds comme les radiateurs en fonte, est un matériau plus fragile et plus difficile à tarauder en raison de sa structure cristalline. Bien qu’elle soit relativement facile à usiner dans des conditions de coupe optimales, elle peut se fissurer ou se casser si elle est mal manipulée. Le taraudage de la fonte nécessite des outils avec des arêtes de coupe plus robustes et une gestion précise de la vitesse et de la profondeur de coupe pour éviter toute déformation ou fissuration du matériau. Il est également important de maintenir une lubrification adéquate pour réduire la friction et minimiser l’usure de l’outil.
En ce qui concerne les matériaux à forte teneur en nickel ou en titane, qui sont souvent utilisés dans des secteurs de pointe tels que l’aérospatiale ou l’industrie de la défense, les exigences pour le taraudage sont encore plus strictes. Ces matériaux sont extrêmement résistants à la chaleur et à la corrosion, mais ils sont également très durs et peuvent générer beaucoup de chaleur pendant le taraudage. Par conséquent, des outils de taraudage revêtus, comme ceux en nitrure de titane (TiN), sont souvent utilisés pour prolonger la durée de vie de l’outil et améliorer les performances du processus.
Les matériaux composites, tels que ceux utilisés dans l’aéronautique ou l’automobile, sont également parfois soumis à des opérations de taraudage. Ces matériaux sont souvent constitués de fibres renforcées par des résines, et leur taraudage exige une grande précision afin de ne pas endommager les fibres ou la matrice. De plus, les matériaux composites peuvent être sensibles à la chaleur, ce qui nécessite une gestion soignée de la température de coupe.
Les outils de taraudage eux-mêmes sont fabriqués à partir de matériaux très résistants, car le processus implique une forte pression et une friction élevée. Les tarauds sont généralement fabriqués à partir d’acier rapide (HSS – High Speed Steel), qui est un matériau suffisamment dur pour résister à l’usure tout en étant capable de maintenir une coupe nette et précise. Pour les applications plus exigeantes, des tarauds en carbure de tungstène ou des alliages céramiques peuvent être utilisés, car ces matériaux offrent une résistance exceptionnelle à la chaleur et à l’usure, ce qui permet de traiter des matériaux plus durs avec une plus grande efficacité.
Le choix des matériaux pour le taraudage est donc un facteur clé dans la réussite du processus, car il influence directement la qualité du filetage, l’usure des outils, ainsi que la vitesse et l’efficacité du travail. En fonction des exigences spécifiques de chaque projet, qu’il s’agisse de fabrication de pièces automobiles, de composants industriels ou de systèmes de chauffage, les fabricants choisissent soigneusement les matériaux et les outils de taraudage pour répondre aux besoins de performance, de durabilité et de sécurité.
Types de Tarauds et Outils de Coupe
Le choix des tarauds et des outils de coupe est essentiel pour garantir la qualité et la précision du processus de taraudage. Les tarauds sont des outils spécialisés utilisés pour couper des filets internes dans un trou préalablement percé, et leur sélection dépend du type de matériau à traiter, de la taille et du type de filetage désiré, ainsi que des conditions de coupe. Il existe différents types de tarauds et d’outils de coupe, chacun conçu pour répondre à des besoins spécifiques de production, permettant ainsi d’optimiser les performances tout en minimisant l’usure des outils.
Les tarauds les plus courants sont les tarauds à pas normal, les tarauds à filetage fin et les tarauds à filetage spécial, qui se distinguent principalement par la configuration de leurs arêtes de coupe et la forme des filets qu’ils génèrent. Les tarauds à pas normal sont utilisés pour des applications générales, tandis que les tarauds à filetage fin sont spécifiquement conçus pour créer des filets plus serrés et plus fins, offrant une meilleure résistance à l’usure et une plus grande capacité de charge. Les tarauds à filetage spécial, quant à eux, sont utilisés pour des applications très spécifiques où des caractéristiques particulières sont nécessaires, comme la création de filets à une certaine géométrie ou une profondeur de coupe précise.
Les tarauds peuvent être classés en fonction de la façon dont ils coupent. On distingue ainsi les tarauds à main, qui sont utilisés pour des applications manuelles ou de faible production, et les tarauds de machine, qui sont utilisés dans des environnements de production plus automatisés, où la vitesse et la répétabilité sont cruciales. Les tarauds à main sont souvent utilisés pour des travaux de petite envergure, comme dans les réparations ou les travaux d’entretien, tandis que les tarauds de machine sont conçus pour des opérations plus rapides et de plus grande précision.
Dans le cadre des tarauds de machine, on distingue plusieurs types de géométries de tarauds, comme les tarauds à filetage métrique, les tarauds à filetage UNC (Unified National Coarse), les tarauds à filetage UNF (Unified National Fine) et les tarauds à filetage BSP (British Standard Pipe), qui sont utilisés pour des applications spécifiques. Les tarauds à filetage métrique, par exemple, sont utilisés principalement dans les applications européennes, tandis que les tarauds à filetage UNC et UNF sont utilisés dans les systèmes impériaux et dans les applications américaines. Le choix du type de filetage dépend des normes de l’industrie et des exigences du projet.
Les tarauds peuvent également différer en fonction de la méthode de coupe qu’ils utilisent. Les tarauds à coupe droite, par exemple, sont conçus pour couper directement dans le matériau en formant les filets à chaque révolution du taraud. Ce type de taraud est principalement utilisé dans les matériaux tendres, comme l’aluminium ou l’acier doux. Les tarauds à coupe spirale, quant à eux, sont utilisés dans les matériaux plus durs et permettent de réduire la friction en dirigeant les copeaux vers l’extérieur. Ces tarauds sont particulièrement adaptés pour des matériaux comme l’acier inoxydable, les alliages d’aluminium ou de cuivre, et les matériaux composites. Ils permettent un travail plus rapide et plus propre tout en réduisant l’usure des outils.
Les outils de coupe associés au taraudage sont également d’une grande importance pour la précision et la durabilité du processus. Parmi les plus utilisés, on trouve les forets, les alésoirs et les fraises. Les forets sont utilisés pour créer le trou de base dans lequel le taraud sera inséré. Le diamètre de ce trou est essentiel pour assurer une bonne adhérence du taraud et garantir que les filets soient créés avec la bonne forme et la bonne profondeur. Les alésoirs, quant à eux, sont utilisés pour affiner la forme du trou et garantir que les dimensions du trou soient parfaitement adaptées aux spécifications du filetage. Enfin, les fraises, qui peuvent être utilisées pour les opérations de fraisage en complément du taraudage, permettent de créer des rainures ou des surfaces planes sur la pièce, souvent avant ou après le taraudage, pour ajouter de la précision ou de la résistance à l’assemblage.
Les matériaux utilisés pour fabriquer les tarauds et les outils de coupe jouent également un rôle clé dans la performance. Les tarauds sont généralement fabriqués à partir d’acier rapide (HSS), qui est un matériau robuste offrant une bonne résistance à la chaleur et à l’usure. Toutefois, pour les applications les plus exigeantes, notamment dans le travail des matériaux durs comme les aciers inoxydables ou les alliages de titane, des outils en carbure de tungstène ou en céramique sont parfois utilisés. Ces matériaux sont plus résistants à l’usure et permettent des vitesses de coupe plus élevées, mais ils sont aussi plus fragiles et nécessitent des précautions particulières lors de l’utilisation. De plus, les outils de coupe sont parfois recouverts de revêtements spéciaux, comme le nitrure de titane (TiN), pour améliorer leur durabilité et réduire la friction, ce qui permet d’augmenter la longévité des tarauds tout en maintenant des performances optimales.
Le processus de taraudage lui-même peut être influencé par d’autres outils et accessoires, tels que les guides et les adaptateurs, qui aident à maintenir la stabilité de la pièce et de l’outil pendant le travail. Des systèmes de lubrification ou de refroidissement sont souvent utilisés pour réduire la chaleur générée pendant la coupe et pour éliminer les copeaux, ce qui permet de maintenir une qualité constante des filetages tout en évitant l’usure prématurée des outils.
En conclusion, le choix des tarauds et des outils de coupe est un élément clé dans le processus de taraudage. La géométrie, les matériaux et le type de coupe influencent directement la qualité des filets créés, ainsi que l’efficacité et la longévité des outils. Chaque projet de taraudage nécessite des outils spécifiques adaptés aux matériaux à traiter et aux exigences de production, et il est crucial de sélectionner les outils appropriés pour garantir des résultats optimaux et une fabrication de qualité.
Processus de Taraudage et Paramètres de Coupe
Le processus de taraudage est une opération de coupe de précision réalisée pour créer des filetages internes dans un trou préalablement percé. Cette opération est essentielle pour de nombreuses applications industrielles, où des fixations ou des composants doivent être reliés par des vis, des boulons ou d’autres types de fixations filetées. Le processus de taraudage implique l’utilisation d’un outil appelé taraud, qui est conçu pour découper les arêtes du filetage dans le matériau. Ce processus nécessite une maîtrise de plusieurs paramètres de coupe pour assurer la qualité du filetage et éviter l’usure prématurée de l’outil.
Le taraudage commence par la préparation du trou dans lequel le taraud va travailler. Ce trou, appelé trou pilote, est généralement percé à l’aide d’un foret. Le diamètre de ce trou est crucial, car il doit être légèrement plus petit que celui du filetage désiré pour permettre au taraud de former les arêtes du filet avec précision. La taille du trou dépend du type de filetage à réaliser ainsi que du matériau dans lequel le taraudage est effectué. Si le trou est trop grand, les filetages peuvent être imprécis, tandis que si le trou est trop petit, il peut être difficile de réaliser un filetage de qualité.
Une fois le trou préparé, le taraud, qui peut être monté sur une machine manuelle ou une machine à commande numérique (CNC), est inséré dans le trou pilote. Le taraud tourne dans le sens horaire et découpe le matériau autour de son axe pour créer les filets internes. Ce processus génère des copeaux qu’il est nécessaire d’évacuer régulièrement pour éviter qu’ils n’endommagent l’outil ou la pièce. Les machines modernes utilisent souvent des systèmes de lubrification ou de refroidissement pour maintenir la température de coupe et assurer une évacuation efficace des copeaux.
Le contrôle des paramètres de coupe est essentiel pour la réussite du taraudage. Parmi ces paramètres, la vitesse de coupe, la profondeur de coupe, la pression appliquée et le type de lubrification sont des éléments clés qui influencent le résultat final. La vitesse de coupe est déterminée par la combinaison de la vitesse de rotation du taraud et de la vitesse d’avance. Une vitesse trop élevée peut entraîner une usure rapide du taraud et un échauffement excessif du matériau, ce qui peut altérer la qualité du filetage. À l’inverse, une vitesse trop basse peut rendre le processus de coupe plus lent et moins efficace, tout en augmentant la charge sur l’outil.
La profondeur de coupe est également un paramètre important, car elle détermine la quantité de matériau retiré à chaque passe. Les tarauds sont souvent utilisés pour couper les filetages sur plusieurs passes, en augmentant progressivement la profondeur à chaque passe pour éviter des contraintes excessives sur l’outil. La profondeur de coupe doit être adaptée en fonction du type de filetage et du matériau à travailler. Par exemple, dans des matériaux durs comme l’acier inoxydable, il peut être nécessaire de réduire la profondeur de coupe pour éviter l’usure prématurée du taraud.
La pression appliquée pendant le taraudage est un autre paramètre critique. Trop de pression peut entraîner des déformations du matériau ou des dommages à l’outil, tandis qu’une pression insuffisante peut rendre le processus de coupe inefficace. Il est important de maintenir une pression constante et contrôlée, en particulier dans les opérations de taraudage de précision où la géométrie du filetage doit être parfaitement respectée.
Le type de lubrification utilisé est essentiel pour assurer une coupe de qualité et prolonger la durée de vie de l’outil. La lubrification réduit la friction entre le taraud et le matériau, ce qui permet de diminuer l’échauffement et d’améliorer l’efficacité du processus de coupe. Elle permet également d’évacuer les copeaux de manière plus efficace, réduisant ainsi le risque d’encrassement des arêtes de coupe. Selon le matériau à tarauder, différentes solutions de lubrification peuvent être utilisées, allant des huiles de coupe aux fluides de refroidissement plus complexes. Dans certains cas, le recours à des systèmes de refroidissement à haute pression est nécessaire pour maintenir des conditions de coupe optimales.
Les machines utilisées pour le taraudage peuvent être manuelles ou automatisées. Dans les environnements de production à grande échelle, les machines à commande numérique (CNC) sont couramment utilisées, car elles permettent un contrôle précis et automatisé des paramètres de coupe. Ces machines peuvent ajuster automatiquement la vitesse, la profondeur de coupe et d’autres variables, ce qui garantit une grande précision et une reproductibilité des opérations de taraudage. Les machines CNC sont également capables de réaliser des taraudages dans des configurations complexes ou des matériaux difficiles à travailler, ce qui permet d’optimiser le processus de fabrication.
Un autre aspect important du processus de taraudage est la gestion des copeaux. L’évacuation des copeaux est cruciale pour maintenir une coupe propre et éviter que les copeaux ne se coincent dans le taraud ou la pièce. Des systèmes d’aspiration ou de filtration sont souvent utilisés pour éliminer les copeaux et améliorer l’efficacité du processus. L’accumulation de copeaux peut non seulement entraîner une usure prématurée de l’outil, mais aussi dégrader la qualité du filetage.
Le contrôle de la qualité des filetages obtenus est une étape finale importante dans le processus de taraudage. Des instruments de mesure, tels que des jauges de filetages ou des micromètres, sont utilisés pour vérifier la précision et la conformité des filetages avec les spécifications requises. La précision des filetages est essentielle pour assurer l’assemblage correct des pièces et garantir la fiabilité de l’ensemble du système.
En résumé, le processus de taraudage et les paramètres de coupe sont des éléments essentiels pour garantir la qualité, la précision et la durabilité des filetages. La gestion de la vitesse de coupe, de la profondeur de coupe, de la pression et de la lubrification, ainsi que l’utilisation de machines appropriées, sont toutes des considérations cruciales pour obtenir un résultat optimal. Une maîtrise approfondie de ces paramètres permet de produire des filetages de haute qualité et de maximiser l’efficacité du processus de taraudage.
Technologies et Automatisation du Taraudage
Les technologies et l’automatisation du taraudage ont considérablement évolué au fil des années, transformant ce processus manuel en une opération précise, rapide et extrêmement efficace. Aujourd’hui, le taraudage automatisé, particulièrement dans les industries de production de masse, est essentiel pour garantir des filetages de haute qualité tout en réduisant les coûts et en améliorant la productivité. L’automatisation du taraudage repose sur l’intégration de technologies avancées, qui permettent de réaliser des opérations de taraudage complexes avec une grande précision, tout en optimisant la gestion des ressources et des outils.
Une des principales technologies utilisées dans l’automatisation du taraudage est l’utilisation des machines à commande numérique (CNC). Ces machines permettent un contrôle précis des mouvements de l’outil, ce qui est essentiel pour réaliser des filetages de qualité constante sur une large gamme de matériaux et de tailles de pièces. Les machines CNC, grâce à leur capacité de programmation, peuvent ajuster automatiquement des paramètres tels que la vitesse de coupe, la profondeur de coupe et la vitesse d’avance en fonction des spécifications de chaque projet. Cela permet d’obtenir des résultats homogènes, même dans des séries de production élevées, tout en minimisant les risques d’erreur humaine.
L’automatisation du taraudage implique également l’utilisation de robots pour le chargement et le déchargement des pièces. Ces robots sont capables de prendre en charge les pièces de manière autonome, ce qui permet d’intégrer le processus de taraudage dans une ligne de production entièrement automatisée. Cette automatisation des manipulations élimine les risques liés aux interventions humaines, améliore la sécurité et réduit le temps d’arrêt des machines, ce qui permet d’augmenter le rendement global de la production.
Les systèmes de contrôle et de surveillance numériques jouent également un rôle clé dans l’automatisation du taraudage. Les capteurs et les systèmes de vision intégrés aux machines CNC peuvent suivre en temps réel les performances de l’outil, détecter l’usure et ajuster les paramètres de coupe en conséquence. Par exemple, certains systèmes peuvent mesurer l’épaisseur du copeau généré et ajuster la vitesse d’avance ou la pression exercée par le taraud pour éviter des déformations ou des erreurs dans les filetages. Ces systèmes permettent également d’alerter l’opérateur si un défaut est détecté, comme un blocage de l’outil ou un excès de chaleur, ce qui permet de prévenir les pannes et de garantir une qualité constante.
L’automatisation du taraudage n’est pas limitée à l’aspect mécanique. Les logiciels de gestion de production jouent un rôle crucial dans la planification et la gestion des tâches de taraudage. Ces logiciels permettent de définir des cycles de production optimisés, de gérer les stocks d’outils et de prélever des données en temps réel sur la production. Grâce à l’intégration des systèmes ERP (Enterprise Resource Planning) et MES (Manufacturing Execution System), les fabricants peuvent surveiller l’ensemble de la chaîne de production, planifier les entretiens des machines et garantir l’efficacité des processus.
En parallèle, l’innovation dans les outils de coupe eux-mêmes contribue grandement à l’automatisation du taraudage. Les tarauds modernes sont fabriqués avec des matériaux extrêmement durables, comme les alliages de carbure ou les revêtements en nitrure de titane (TiN), qui prolongent la durée de vie des outils et permettent des vitesses de coupe plus élevées. Ces outils sont conçus pour résister à des conditions de travail intensives tout en maintenant une performance optimale. Les outils de coupe automatiques peuvent être changés automatiquement grâce à des systèmes de gestion d’outils intégrés, ce qui améliore encore la productivité.
L’introduction des technologies de refroidissement et de lubrification avancées a également permis d’optimiser le taraudage automatisé. Des systèmes de lubrification à haute pression ou à jet dirigé sont utilisés pour réduire la friction et la chaleur générée pendant le processus de coupe. Ces technologies permettent non seulement de maintenir la température à un niveau optimal, mais aussi de garantir une évacuation efficace des copeaux, ce qui réduit le risque d’usure prématurée de l’outil et améliore la qualité du filetage. Dans certains cas, des systèmes de lubrification et de refroidissement intégrés dans la machine CNC peuvent être programmés pour s’ajuster automatiquement en fonction des conditions de coupe.
Une autre avancée technologique importante dans l’automatisation du taraudage est l’utilisation de la simulation numérique avant la production. Les logiciels de simulation permettent de modéliser le processus de taraudage et de tester différents paramètres, tels que la vitesse de coupe, la profondeur de coupe et les angles de coupe, avant de procéder à la fabrication réelle. Cela permet d’optimiser le processus, de prévenir les erreurs et de réduire le temps nécessaire pour trouver les bons réglages. Cette simulation peut également aider à déterminer le choix optimal des outils et à prévoir leur usure, ce qui réduit les temps d’arrêt liés au changement d’outils.
L’automatisation du taraudage contribue également à la réduction des coûts de production en augmentant l’efficacité, en réduisant le nombre d’erreurs et en limitant l’intervention humaine. Les robots et les machines CNC permettent de produire des filetages à des vitesses élevées, avec une précision constante, et ce, sur une grande variété de matériaux, allant des métaux non ferreux aux alliages d’acier, en passant par des matériaux plus complexes comme les composites. De plus, l’automatisation permet d’améliorer la sécurité des travailleurs, car elle réduit le besoin d’interventions manuelles dans des environnements potentiellement dangereux.
En conclusion, les technologies et l’automatisation du taraudage ont permis d’atteindre des niveaux de précision, d’efficacité et de productivité sans précédent. L’intégration des machines CNC, des robots, des systèmes de contrôle intelligents, des outils de coupe de haute performance et des solutions de lubrification avancées a non seulement optimisé les processus de production, mais a aussi amélioré la qualité des filetages et prolongé la durée de vie des outils. Ces avancées technologiques permettent aux entreprises de répondre aux exigences croissantes de l’industrie tout en maintenant des standards élevés de performance et de rentabilité.
Gestion des Copeaux et Systèmes de Refroidissement
La gestion des copeaux et les systèmes de refroidissement sont deux éléments essentiels pour optimiser le processus de taraudage et garantir la qualité du travail effectué. Dans toute opération de taraudage, les copeaux générés lors de la coupe du matériau peuvent rapidement devenir un facteur limitant, affectant la précision du filetage, l’efficacité du processus et la durée de vie des outils de coupe. De même, la gestion thermique joue un rôle crucial dans la réduction de l’usure des outils et la prévention des déformations du matériau. Ainsi, l’intégration de systèmes efficaces de gestion des copeaux et de refroidissement est indispensable pour maintenir une productivité élevée et des résultats constants dans le taraudage, en particulier dans les environnements de production de grande échelle.
Les copeaux sont générés pendant le processus de coupe, lorsqu’une partie du matériau est enlevée par l’outil de taraudage pour former le filetage interne. Ces copeaux peuvent varier en taille, forme et quantité selon le matériau travaillé, le type de taraud et les paramètres de coupe. Si les copeaux ne sont pas correctement gérés, ils peuvent se coincer entre l’outil et la pièce, ce qui peut entraîner des défauts de filetage, une augmentation de la friction et une usure prématurée de l’outil. L’accumulation de copeaux peut également obstruer la machine, ralentir le processus de production et causer des pannes. C’est pourquoi il est crucial de mettre en place des systèmes adaptés pour l’évacuation et le traitement des copeaux pendant et après l’opération de taraudage.
La gestion des copeaux commence dès le début de l’opération de taraudage, lorsqu’ils sont générés. La conception des outils de coupe joue un rôle déterminant dans cette gestion. Les tarauds modernes sont souvent conçus avec des canaux spécialement intégrés, appelés canaux de déchappement, qui permettent aux copeaux de s’évacuer plus facilement de la zone de coupe. Cela réduit la probabilité que les copeaux ne s’accumulent et ne perturbent l’opération. Ces canaux sont d’autant plus efficaces lorsqu’ils sont associés à un système de lubrification ou de refroidissement, car ces derniers permettent de maintenir les copeaux en suspension dans le liquide de coupe et de les évacuer plus facilement. De plus, certains tarauds sont conçus pour réduire la formation de copeaux longs ou fragiles qui risquent de se coincer dans les machines.
L’évacuation des copeaux peut se faire de différentes manières, en fonction de l’équipement utilisé et du type de production. Dans les environnements de production automatisée, des systèmes d’aspiration ou de ventilation sont souvent employés pour aspirer les copeaux à partir de la zone de travail. Ces systèmes sont connectés à des filtres ou à des réservoirs de collecte qui permettent de récupérer les copeaux pour les recycler ou les éliminer de manière adéquate. D’autres systèmes utilisent des convoyeurs à vis ou à bande pour transporter les copeaux vers des zones de stockage ou de traitement, garantissant ainsi que la production se poursuit sans interruption.
Le rôle des systèmes de refroidissement est tout aussi crucial dans le processus de taraudage. Lors de l’opération de coupe, une chaleur significative est générée au point de contact entre l’outil de coupe et le matériau. Si cette chaleur n’est pas dissipée de manière efficace, elle peut entraîner une usure accélérée des outils, une déformation de la pièce, voire des erreurs dans le filetage. Les systèmes de refroidissement et de lubrification sont donc essentiels pour contrôler la température et garantir la durabilité des outils ainsi que la qualité du filetage.
Les fluides de refroidissement et de lubrification sont utilisés pour réduire la friction entre le taraud et le matériau, ce qui permet de diminuer la chaleur générée pendant la coupe. Ces fluides facilitent également l’évacuation des copeaux, tout en améliorant la qualité de la coupe. Selon le type de matériau traité et la configuration de la machine, différents types de fluides peuvent être utilisés. Les lubrifiants à base d’huile sont couramment utilisés pour leur capacité à lubrifier efficacement et à dissiper la chaleur. Les émulsions, qui combinent de l’huile et de l’eau, sont également populaires car elles offrent une meilleure dissipation thermique tout en étant plus écologiques. En outre, les fluides de coupe à haute pression, comme les jets de lubrifiant ou d’air comprimé, peuvent être utilisés pour renforcer l’efficacité du refroidissement, en particulier lors du travail de matériaux durs ou difficiles à couper.
Les systèmes de refroidissement peuvent également être équipés de dispositifs à haute pression qui dirigent les fluides de manière ciblée vers la zone de coupe, réduisant ainsi la température et permettant d’améliorer les conditions de coupe. Cette approche est particulièrement efficace dans les machines à commande numérique (CNC), où des jets de fluide peuvent être programmés pour s’ajuster en fonction de la vitesse de coupe, de la profondeur et d’autres paramètres. Certains systèmes intègrent des capteurs thermiques qui mesurent la température de l’outil et ajustent automatiquement la pression du fluide pour éviter la surchauffe et garantir une performance optimale.
En plus des systèmes de refroidissement et de lubrification externes, certains outils de taraudage sont conçus pour intégrer des canaux de refroidissement à l’intérieur même de l’outil. Ces canaux permettent au fluide de circuler directement autour de l’outil, apportant ainsi un refroidissement constant et ciblé là où il est le plus nécessaire. Ce type de système est particulièrement utile pour les taraudages effectués dans des matériaux de haute résistance thermique, où les températures de coupe peuvent rapidement devenir critiques.
En résumé, la gestion des copeaux et l’utilisation de systèmes de refroidissement efficaces sont essentiels pour le bon déroulement du processus de taraudage. Une gestion adéquate des copeaux permet non seulement d’éviter des défaillances dans le processus de production, mais elle contribue également à prolonger la durée de vie des outils et à maintenir la précision des filetages. De plus, les systèmes de refroidissement et de lubrification garantissent une réduction de la chaleur et de la friction, ce qui permet de préserver l’intégrité des outils et des matériaux tout en optimisant la qualité et l’efficacité de l’opération. Ces technologies, intégrées correctement dans les machines de taraudage, permettent de garantir des résultats constants et une productivité élevée dans les environnements de production industrielle.
Contrôle de Qualité et Inspection
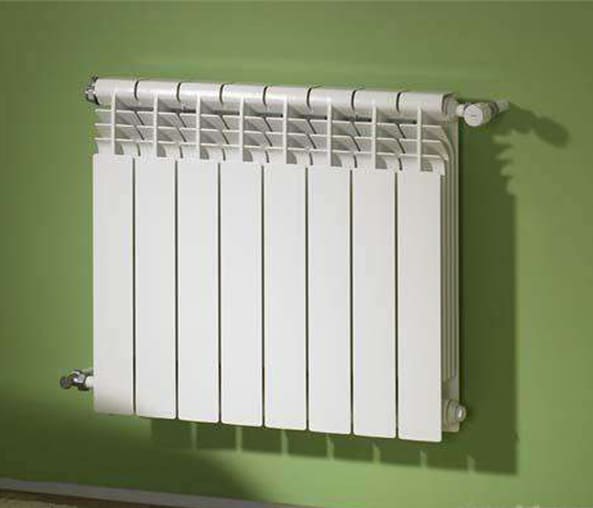
Le contrôle de qualité et l’inspection sont des éléments essentiels dans le processus de taraudage, garantissant que les filetages obtenus répondent aux spécifications techniques et aux exigences des clients. Ces étapes permettent de s’assurer que les pièces fabriquées sont conformes aux normes de précision, de résistance et de fiabilité, et qu’elles peuvent être utilisées dans des applications exigeantes. Un contrôle rigoureux est nécessaire non seulement pour assurer la fonctionnalité des filetages, mais aussi pour optimiser la durée de vie des outils, minimiser les défauts de fabrication et garantir la sécurité des produits finaux.
Le contrôle de qualité dans le taraudage commence dès la phase de préparation des matériaux. La vérification du matériau avant le taraudage est cruciale, car des imperfections ou des variations dans les propriétés du matériau peuvent affecter le processus de taraudage et, par conséquent, la qualité des filetages. Des tests de dureté, de résistance à la traction ou des contrôles visuels peuvent être effectués pour s’assurer que le matériau répond aux spécifications requises. Ces vérifications sont particulièrement importantes lorsqu’on travaille avec des matériaux spécifiques tels que l’acier inoxydable, les alliages d’aluminium ou des matériaux composites, qui peuvent avoir des comportements très différents lors du taraudage.
Une fois que le taraudage est effectué, l’inspection du filetage est une étape cruciale pour vérifier qu’il respecte les critères dimensionnels et fonctionnels. Les mesures de précision sont réalisées à l’aide de différents instruments de mesure tels que des micromètres, des jauges de filetages, des pieds à coulisse ou des machines de mesure tridimensionnelle (CMM). Ces instruments permettent de mesurer des paramètres comme le diamètre interne, la profondeur, l’angle du filetage, ainsi que la précision du profil. Des écarts par rapport aux tolérances spécifiées peuvent compromettre la capacité du filetage à recevoir des vis ou des boulons correctement, ce qui peut entraîner des dysfonctionnements mécaniques ou des problèmes d’assemblage.
Les contrôles de qualité comprennent également l’inspection visuelle, qui permet de détecter tout défaut apparent dans le filetage, comme des fissures, des bavures ou des irrégularités. Cette inspection visuelle peut être réalisée à l’œil nu ou à l’aide de microscopes, d’optical ou de systèmes de vision automatisée, particulièrement dans les environnements de production à grande échelle. L’identification de tels défauts est essentielle pour éviter la propagation de défauts dans les séries de production et garantir que les pièces répondent aux exigences fonctionnelles.
Les tests de résistance sont également une partie intégrante du contrôle de qualité dans le processus de taraudage. En fonction de l’application finale de la pièce taraudée, des tests mécaniques peuvent être nécessaires pour s’assurer que le filetage résiste à des contraintes telles que des forces de torsion ou de traction. Ces tests peuvent inclure des essais de traction pour vérifier la résistance du filetage sous charge, des essais de fatigue pour évaluer la performance des filetages sous conditions de cycles répétés ou des essais de résistance à la corrosion pour des applications dans des environnements sévères.
Dans certaines industries, telles que l’aéronautique, l’automobile ou la production d’équipements de haute précision, la conformité aux normes de qualité est particulièrement rigoureuse. Des normes comme ISO 9001, les spécifications ASME ou les directives de l’industrie automobile peuvent imposer des critères stricts de contrôle de qualité et d’inspection pour chaque pièce produite. Pour répondre à ces exigences, des audits internes et externes sont souvent réalisés pour garantir la conformité des processus de fabrication et des contrôles de qualité aux normes en vigueur.
Une autre méthode d’inspection utilisée dans le contrôle de qualité est la vérification par échantillonnage. Dans des productions à grande échelle, où il est impraticable de contrôler chaque pièce individuellement, des échantillons de pièces sont prélevés à intervalles réguliers pour être soumis à un contrôle de qualité approfondi. Les échantillons sont inspectés en fonction de critères spécifiés et, si un défaut est détecté, des mesures correctives sont prises, telles que l’ajustement des paramètres de machine, l’entretien des outils de coupe ou même le remplacement d’une partie de la production. Cette méthode permet de maintenir un niveau de qualité constant sans avoir à tester chaque pièce individuellement.
L’intégration de technologies avancées dans le processus d’inspection, telles que les systèmes de vision automatisés et l’intelligence artificielle (IA), a amélioré l’efficacité du contrôle de qualité. Les systèmes de vision automatisés sont capables de détecter des défauts microscopiques et d’effectuer des mesures complexes de manière plus rapide et plus précise que l’œil humain. L’IA peut analyser des images de manière intelligente pour identifier des défauts non seulement visibles, mais aussi ceux qui pourraient être difficiles à détecter, comme des microfissures ou des irrégularités dans la structure du filetage.
Le contrôle de la qualité dans le processus de taraudage s’étend également à la maintenance des machines et des outils de coupe. Un entretien préventif régulier est nécessaire pour garantir que les machines de taraudage et les outils de coupe restent dans un état optimal de fonctionnement. Cela inclut la vérification régulière des paramètres de coupe, la calibration des machines CNC et le remplacement des outils de coupe usés. L’usure des outils est particulièrement importante dans le processus de taraudage, car des outils émoussés ou mal ajustés peuvent affecter la qualité du filetage, entraînant des erreurs de dimensions ou des défauts dans la surface du filetage.
En conclusion, le contrôle de qualité et l’inspection sont des étapes fondamentales dans le processus de taraudage, car elles assurent la conformité des filetages produits aux exigences techniques, dimensionnelles et fonctionnelles. L’utilisation d’instruments de mesure de précision, de systèmes d’inspection visuelle, de tests de résistance et de technologies de contrôle automatisées permet de maintenir un haut niveau de qualité, d’assurer la fiabilité des pièces et de garantir la sécurité des produits finaux. Ces processus sont essentiels pour répondre aux exigences des clients et aux normes industrielles, en particulier dans des secteurs où la précision et la performance des filetages sont cruciales.
Applications Industrielles du Taraudage
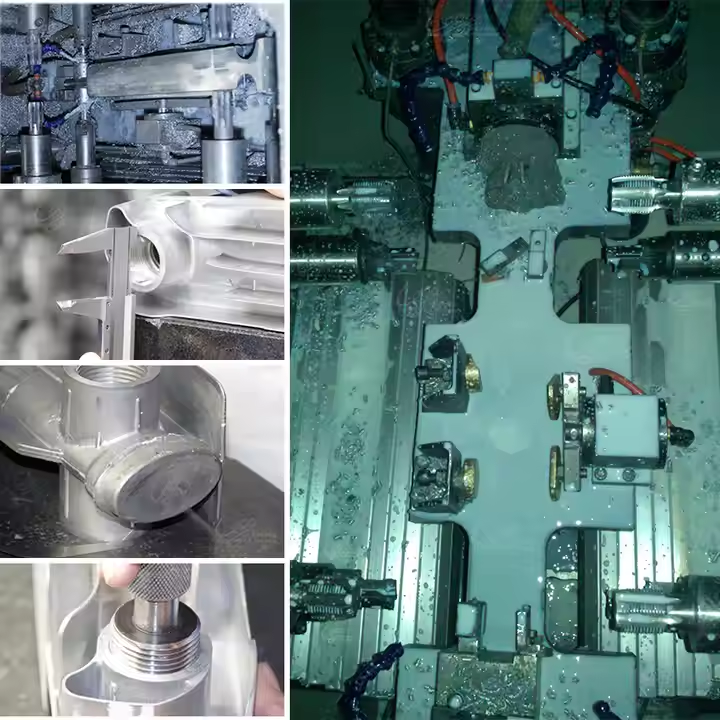
Le taraudage est une opération de fabrication cruciale utilisée dans de nombreuses industries pour produire des filetages internes sur des pièces métalliques et autres matériaux. Cette technique est indispensable dans des secteurs variés, tels que l’aéronautique, l’automobile, la construction, la mécanique de précision, ainsi que dans la fabrication de dispositifs médicaux et d’équipements électroniques. Chaque application industrielle du taraudage nécessite des spécifications particulières en termes de matériaux, de tolérances dimensionnelles et de conditions de coupe. En raison de sa polyvalence et de sa capacité à offrir des solutions de fixation robustes, le taraudage est un procédé clé pour l’assemblage de composants, le montage de pièces et la création de produits de haute qualité.
Dans l’industrie automobile, par exemple, le taraudage est utilisé pour la production de moteurs, de boîtes de vitesses, de suspensions et d’autres composants essentiels. Les filetages internes créés par le taraudage permettent d’assembler des vis, des boulons et d’autres éléments de fixation, qui sont essentiels pour assurer la robustesse et la sécurité des véhicules. Les pièces automobiles doivent répondre à des critères stricts de résistance mécanique, ce qui nécessite l’utilisation de matériaux durables comme l’acier allié, l’aluminium ou même des composites avancés. Le processus de taraudage dans cette industrie doit garantir une précision dimensionnelle et une tolérance serrée pour assurer une fixation sûre et fiable.
Dans l’aéronautique, le taraudage est une technique incontournable pour la fabrication de pièces de moteurs, de structures d’avions, de composants hydrauliques et d’assemblages d’avions. Les exigences de performance dans ce secteur sont particulièrement élevées, car les pièces doivent résister à des contraintes extrêmes de température, de pression et de vibrations. Par conséquent, les filetages doivent être d’une grande précision, et les matériaux utilisés doivent offrir une résistance exceptionnelle à la fatigue, à la corrosion et aux contraintes mécaniques. Le taraudage dans l’aéronautique est souvent effectué sur des matériaux légers et résistants, tels que les alliages d’aluminium, le titane et des matériaux composites haute performance.
Dans l’industrie de la construction, le taraudage est utilisé pour la fabrication de raccords, de fixations et d’autres composants structurels. Les pièces fabriquées à l’aide du taraudage sont souvent utilisées dans des applications nécessitant une fixation solide et durable, comme dans la construction de bâtiments, de ponts et d’autres infrastructures. Les matériaux employés dans ce secteur incluent des aciers doux, des alliages de cuivre et des aciers inoxydables, qui doivent être traités avec des paramètres de taraudage adaptés pour garantir une résistance maximale. Le processus de taraudage dans la construction doit non seulement produire des filetages de haute qualité mais aussi permettre des économies de temps et de coûts, étant donné la large échelle de production.
Dans le secteur de la mécanique de précision, le taraudage est utilisé pour produire des composants et des dispositifs nécessitant des tolérances très strictes et une finition de surface parfaite. Les équipements de haute précision, tels que les instruments de mesure, les machines-outils, et les dispositifs de contrôle, dépendent de l’utilisation du taraudage pour créer des filetages internes sur des pièces métalliques complexes. La qualité des filetages dans ces applications doit être extrêmement précise, car même de petites variations peuvent compromettre la fonctionnalité des composants. En outre, les matériaux utilisés dans la mécanique de précision, comme les aciers inoxydables, les alliages spéciaux et les matériaux non ferreux, nécessitent un taraudage adapté pour éviter les défauts et garantir la durabilité des pièces finies.
Dans l’industrie électronique, le taraudage joue également un rôle essentiel, en particulier pour la fabrication de boîtiers, de composants électroniques et d’équipements de communication. Les pièces en plastique, en métal et en céramique utilisées dans les dispositifs électroniques sont souvent soumises à des opérations de taraudage pour permettre l’assemblage de vis, de boulons et d’autres éléments de fixation. Les exigences de précision dans l’industrie électronique sont élevées, en raison de la petite taille des composants et de la nécessité d’un assemblage précis pour garantir le bon fonctionnement des appareils. Les matériaux utilisés dans ce domaine, tels que les alliages légers, le cuivre, l’aluminium et les plastiques renforcés, nécessitent un taraudage réalisé avec des outils de coupe de haute qualité pour éviter l’endommagement des pièces et assurer la conformité aux normes industrielles.
Le secteur médical utilise également le taraudage dans la fabrication de dispositifs chirurgicaux, d’équipements dentaires, d’implants et d’autres produits médicaux. Les matériaux utilisés dans ces applications doivent être biocompatibles et résister à des conditions extrêmes de stérilisation, de température et de pression. Le taraudage est utilisé pour produire des filetages internes dans les implants médicaux, tels que les vis, les broches et les fixations, afin d’assurer leur fixation sécurisée dans le corps humain. Les spécifications strictes de qualité et de tolérances dans le secteur médical exigent une précision maximale et une qualité de surface élevée, ce qui rend le processus de taraudage particulièrement critique dans ce domaine.
En plus de ces industries principales, le taraudage est également utilisé dans d’autres secteurs tels que l’équipement de production, l’électronique automobile, l’industrie pétrolière et gazière, et la fabrication de biens de consommation. Dans le secteur de l’énergie, par exemple, le taraudage est utilisé pour produire des composants de turbines, de générateurs et de pompes, qui nécessitent une précision extrême et une résistance à des conditions de travail sévères. Les filetages créés lors du taraudage sont souvent utilisés dans des applications nécessitant une étanchéité parfaite et une fixation sûre sous des pressions et des températures élevées.
En conclusion, les applications industrielles du taraudage sont vastes et variées, touchant des secteurs allant de l’automobile à l’aéronautique, de la construction à la mécanique de précision, et des équipements médicaux à l’électronique. Dans chaque cas, le taraudage permet de produire des filetages internes d’une précision essentielle, tout en garantissant la résistance et la fiabilité des pièces. Les progrès technologiques dans les outils de coupe, les machines et les fluides de coupe continuent d’améliorer les performances du taraudage, permettant aux industries de répondre à des demandes de production toujours plus complexes et exigeantes.
Innovations et Développements Futurs dans le Taraudage
Les innovations et les développements futurs dans le taraudage se concentrent sur l’amélioration de l’efficacité, de la précision, et de la durabilité des processus de fabrication. Alors que les industries exigent des filetages toujours plus fins et précis, la recherche et le développement dans ce domaine visent à répondre à ces besoins croissants tout en réduisant les coûts et l’impact environnemental. Les progrès technologiques dans les outils de coupe, les machines de taraudage, les matériaux, ainsi que l’intégration de l’automatisation et de l’intelligence artificielle, transforment rapidement cette industrie.
L’une des principales innovations concerne les matériaux utilisés pour la fabrication des outils de taraudage. Les nouveaux alliages métalliques et les revêtements de surface avancés permettent de prolonger la durée de vie des tarauds et d’améliorer la qualité des filetages. Par exemple, les revêtements en nitrure de titane ou en carbure cémenté sont de plus en plus utilisés pour améliorer la résistance à l’usure et à la corrosion des outils de taraudage. Ces revêtements permettent également de réduire la friction pendant l’opération de taraudage, ce qui entraîne une diminution de la chaleur générée et une usure moins rapide des outils. De plus, les matériaux composites et les alliages à haute performance, qui étaient autrefois difficiles à tarauder, deviennent plus accessibles grâce à l’évolution des outils et des techniques de coupe.
Les technologies de commande numérique (CNC) et de fabrication assistée par ordinateur (FAO) ont également un impact significatif sur le taraudage. L’introduction des machines CNC avec des capacités de contrôle avancées permet d’atteindre des tolérances beaucoup plus strictes qu’auparavant, ce qui est essentiel pour répondre aux exigences de précision des industries modernes. Ces machines permettent une programmation flexible et une gestion en temps réel des paramètres de coupe, ce qui permet d’optimiser les cycles de production et d’éviter les erreurs humaines. À mesure que les systèmes CNC deviennent plus sophistiqués, il devient possible d’adapter les paramètres de taraudage, tels que la vitesse de coupe, la profondeur et l’alimentation, en fonction des conditions réelles de coupe et du type de matériau. Cela permet d’améliorer la productivité tout en garantissant la qualité du filetage.
L’automatisation et l’intégration de l’intelligence artificielle (IA) ouvrent de nouvelles perspectives pour l’avenir du taraudage. L’intelligence artificielle peut analyser en temps réel les données générées lors du processus de taraudage et ajuster automatiquement les paramètres pour optimiser la coupe. Par exemple, l’IA peut détecter les anomalies de coupe ou les signes d’usure des outils avant qu’ils n’affectent la qualité du produit final, ce qui permet une maintenance prédictive et une gestion proactive des machines. Ces technologies permettent de réduire le temps de cycle, d’augmenter la production et d’améliorer la cohérence des résultats, tout en minimisant les erreurs humaines et en garantissant la précision des filetages.
L’innovation dans les systèmes de refroidissement et de lubrification est également un domaine clé de développement. Les fluides de coupe traditionnels, tels que les huiles et émulsions, sont de plus en plus remplacés par des solutions plus écologiques et efficaces, comme les lubrifiants secs ou les systèmes de refroidissement à haute pression. Les systèmes de refroidissement améliorés permettent de maintenir des températures de coupe plus basses, ce qui réduit l’usure des outils et améliore la qualité du filetage, surtout lors du traitement de matériaux difficiles tels que les alliages d’acier inoxydable ou les titanes. Les innovations dans le domaine des microjets ou des lubrifiants à base d’aérosols permettent de réduire la consommation de liquide et de garantir un refroidissement ciblé sans gaspillage, ce qui contribue à l’efficacité énergétique et à la durabilité des processus.
Une autre tendance importante est l’utilisation des technologies de vision artificielle et des capteurs intelligents pour surveiller et contrôler le processus de taraudage. Les systèmes de vision peuvent analyser le filetage pendant sa fabrication pour détecter toute irrégularité, comme des bavures, des fissures ou des défauts de forme, et fournir un retour instantané sur la qualité du travail effectué. Ces systèmes permettent d’identifier et de corriger rapidement les problèmes, évitant ainsi des erreurs coûteuses ou des rebuts de production. De plus, les capteurs de force et de température intégrés aux machines de taraudage permettent de surveiller les conditions de coupe en temps réel, ce qui permet d’ajuster automatiquement les paramètres pour optimiser la qualité du filetage et prolonger la durée de vie des outils.
Les innovations dans les matériaux et les procédés de fabrication continuent d’améliorer la capacité de production des machines de taraudage. Par exemple, l’impression 3D et la fabrication additive commencent à être explorées pour créer des outils de coupe personnalisés ou des pièces à géométrie complexe qui ne seraient pas possibles à réaliser par des méthodes de fabrication conventionnelles. L’impression 3D permet de fabriquer des tarauds sur mesure adaptés à des applications spécifiques, ce qui pourrait ouvrir de nouvelles possibilités dans des industries comme l’aéronautique, où des formes complexes et des matériaux spéciaux sont souvent requis. Cette approche offre également des avantages en termes de réduction des coûts de production et de délais de livraison.
En outre, la durabilité et la réduction de l’impact environnemental du taraudage font l’objet d’une attention croissante. La recherche sur les solutions de réduction des déchets, la gestion des fluides de coupe et l’optimisation des cycles de production s’intensifie. Par exemple, des initiatives visant à réutiliser les fluides de coupe ou à récupérer les copeaux métalliques pour les recycler sont de plus en plus mises en œuvre. Ces démarches écologiques permettent de réduire les coûts de production tout en minimisant l’empreinte écologique de l’industrie du taraudage.
En somme, l’avenir du taraudage se dirige vers une automatisation accrue, une meilleure précision grâce à l’intelligence artificielle, et l’optimisation des matériaux et des processus. Les machines plus intelligentes, les outils plus résistants, et les systèmes de production plus écologiques permettront de répondre aux défis de production de plus en plus complexes dans les industries modernes. Ces innovations permettent non seulement d’améliorer l’efficacité des processus de taraudage, mais aussi de répondre aux exigences croissantes en matière de qualité, de coûts et de durabilité.
EMS Machines de Formage
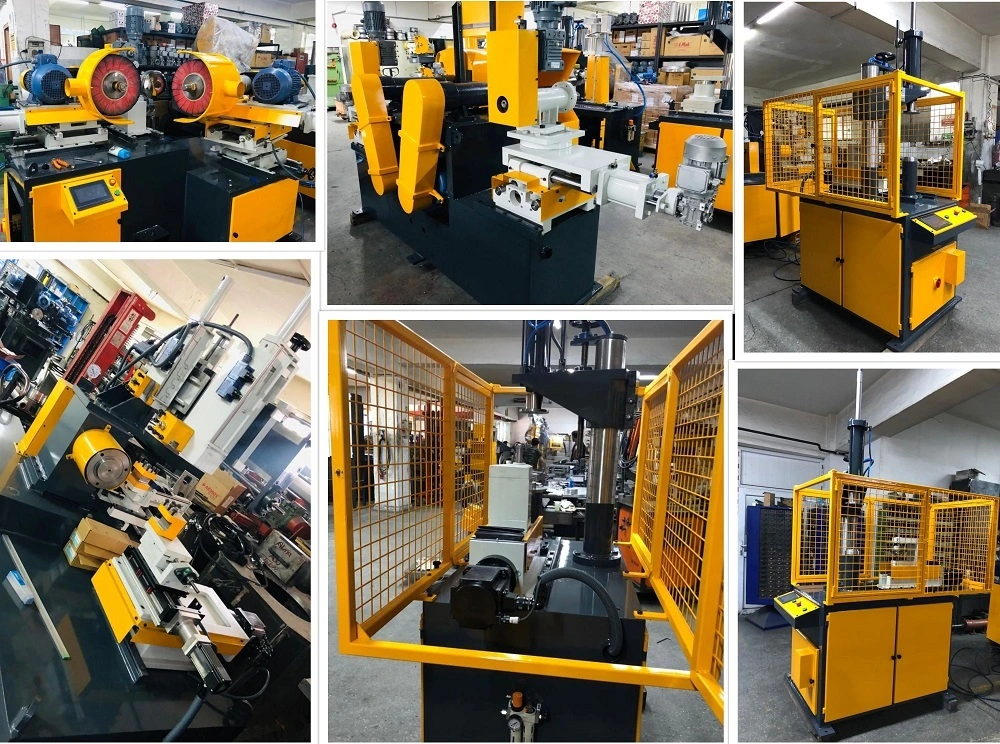
Le formage du métal est un processus consistant à façonner le métal dans la forme et la taille souhaitées à l’aide de diverses techniques. Il s’agit d’un processus crucial dans l’industrie manufacturière car il permet la production de différents produits tels que des pièces automobiles, des composants d’avion, des appareils électroménagers et bien d’autres encore.
Le processus de formage du métal consiste à appliquer une force sur le métal pour changer sa forme sans enlever aucune matière. La force peut être appliquée par diverses méthodes telles que le forgeage, le laminage, l’extrusion, l’étirage et l’estampage. Chaque méthode a ses propres avantages et inconvénients, et le choix de la méthode dépend du matériau formé et de la forme souhaitée.
Le forgeage est l’une des techniques de formage des métaux les plus anciennes. Il s’agit de chauffer le métal à haute température, puis d’appliquer une force de compression à l’aide d’un marteau ou d’une presse pour donner au métal la forme souhaitée. Le forgeage est couramment utilisé pour produire de grandes pièces telles que des engrenages, des essieux et des bielles.
Le laminage est une autre technique de formage du métal qui consiste à faire passer le métal à travers une paire de rouleaux pour réduire son épaisseur ou modifier sa forme. Les rouleaux peuvent être lisses ou texturés selon la finition souhaitée. Le laminage est couramment utilisé pour produire des tôles plates, des plaques et des barres.
L’extrusion est une technique de formage du métal qui consiste à pousser une billette ou une tige métallique à travers une matrice pour créer une forme spécifique. L’extrusion peut être utilisée pour produire des formes complexes telles que des tubes, des canaux et des angles.
L’emboutissage est une technique de formage des métaux utilisée pour réaliser des pièces de forme cylindrique, comme des tubes ou des tuyaux. Le processus consiste à tirer le métal à travers une matrice pour réduire son diamètre et augmenter sa longueur. Le tréfilage est couramment utilisé dans la production de fils, de tiges et de tubes.
L’emboutissage est une technique de formage du métal qui consiste à couper, poinçonner ou plier le métal dans une forme spécifique à l’aide d’une matrice. Le processus peut être utilisé pour produire des pièces avec une grande précision et répétabilité. L’estampage est couramment utilisé dans la production de pièces automobiles, d’appareils électroménagers et d’appareils électroniques.
En plus de ces techniques, il existe de nombreuses autres méthodes de formage des métaux telles que le filage, l’emboutissage profond et l’hydroformage. Chaque méthode a ses propres avantages et inconvénients, et le choix de la méthode dépend des exigences spécifiques du produit fabriqué.
Le formage des métaux est un processus complexe qui nécessite un haut niveau de compétence et d’expertise. Le succès du processus dépend de nombreux facteurs tels que le type de matériau formé, l’équipement utilisé et l’expérience de l’opérateur. En comprenant les différentes techniques de formage des métaux et en choisissant la méthode adaptée au travail, les fabricants peuvent produire des pièces de haute qualité qui répondent aux besoins spécifiques de leurs clients.