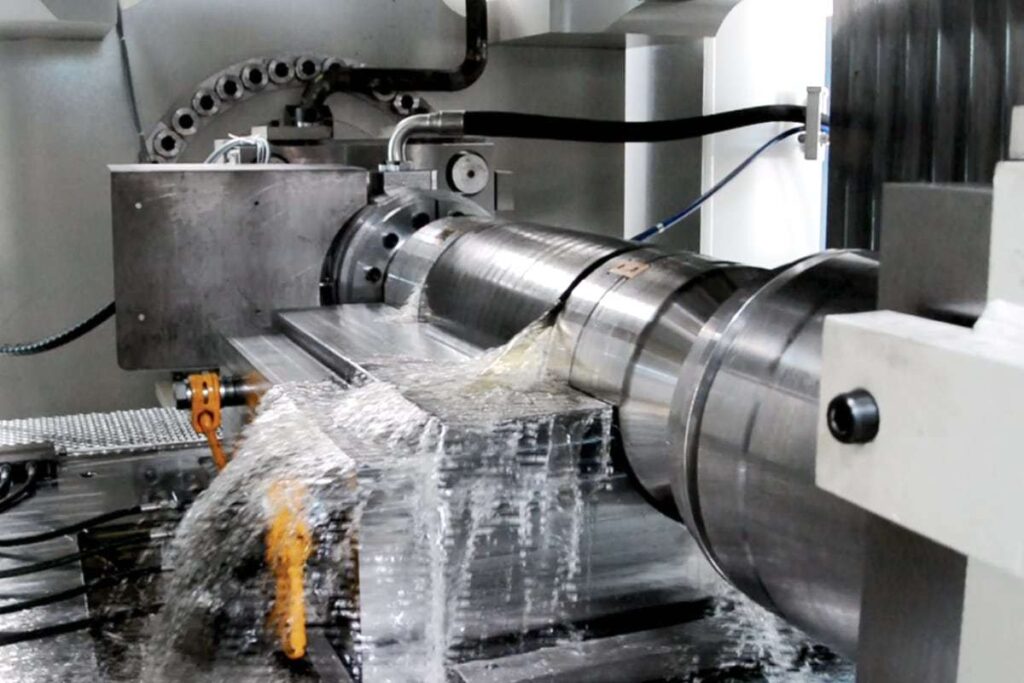
Hydroformage France: L’hydroformage est une technique de fabrication innovante utilisée principalement dans les industries automobile et aérospatiale pour former des pièces métalliques complexes. Ce procédé repose sur l’utilisation d’un fluide sous haute pression pour façonner le métal dans un moule. Contrairement aux méthodes traditionnelles comme le pressage ou l’emboutissage, l’hydroformage permet d’obtenir des formes plus complexes avec une meilleure répartition des contraintes et une finition de surface supérieure. Le processus commence généralement par la préparation d’une pièce de métal, souvent sous forme de tube ou de feuille. Cette pièce est ensuite placée dans un moule spécifique conçu pour la forme finale souhaitée. Un fluide, souvent de l’huile, est alors injecté à haute pression à l’intérieur du métal, ce qui le pousse à épouser les contours du moule.
L’un des principaux avantages de l’hydroformage est la possibilité de réduire le poids des composants tout en conservant leur solidité structurelle. Cela en fait une solution particulièrement prisée dans le domaine de l’automobile, où la réduction de poids contribue à améliorer l’efficacité énergétique des véhicules. Les constructeurs automobiles utilisent cette technique pour produire des éléments tels que les cadres de carrosserie, les montants de toit et les traverses. Dans l’aéronautique, l’hydroformage est utilisé pour fabriquer des composants complexes des structures d’avion, où chaque gramme compte en termes de performance et de consommation de carburant. En plus des avantages structurels, l’hydroformage permet également de réduire les coûts de production en diminuant le nombre de pièces nécessaires pour une structure donnée, ce qui simplifie l’assemblage et diminue les besoins en soudures ou en fixations mécaniques.
Cette méthode présente également des défis, notamment en termes de conception des moules et des machines nécessaires pour générer les hautes pressions requises. Les moules doivent être conçus avec une grande précision pour garantir une répartition uniforme de la pression sur la pièce de métal, et les équipements doivent pouvoir supporter des pressions extrêmement élevées, parfois supérieures à 1000 bars. Malgré ces défis techniques, les avantages de l’hydroformage en termes de qualité et de performance l’emportent largement, ce qui en fait une technologie incontournable dans les secteurs industriels modernes. Au fil des années, des innovations ont permis d’étendre les applications de l’hydroformage, incluant maintenant des matériaux tels que l’aluminium, l’acier inoxydable et même certains alliages spéciaux.
L’impact environnemental de l’hydroformage est également un point positif, car cette méthode génère moins de déchets que les procédés traditionnels. En effet, le métal est formé de manière plus efficace, ce qui réduit les pertes de matériau. De plus, la capacité de créer des structures légères et robustes contribue indirectement à réduire les émissions de gaz à effet de serre, notamment dans le domaine des transports. Cependant, la mise en œuvre de l’hydroformage nécessite une expertise spécialisée, tant pour le développement des moules que pour le contrôle du processus. L’évolution des technologies numériques, telles que la simulation informatique, a grandement facilité cette tâche, permettant de prévoir avec précision le comportement du métal sous pression et d’optimiser les paramètres de fabrication avant même de lancer la production réelle.
En résumé, l’hydroformage est une technologie clé qui combine efficacité, précision et respect de l’environnement, répondant aux besoins des industries modernes tout en ouvrant la voie à de nouvelles possibilités de conception et de fabrication.
Hydroformage France
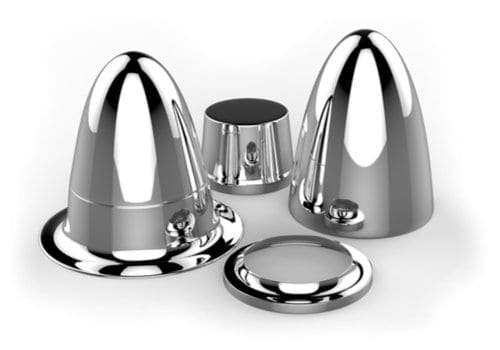
L’hydroformage continue d’évoluer grâce à l’intégration de nouvelles technologies et à l’exploration de nouveaux matériaux. Par exemple, les avancées dans la métallurgie ont permis de développer des alliages spécifiques qui se prêtent particulièrement bien à ce procédé. Les matériaux légers comme l’aluminium, le titane et les alliages de magnésium sont de plus en plus utilisés, notamment dans les secteurs où la réduction de poids est cruciale. Ces alliages offrent un excellent rapport résistance/poids, ce qui les rend idéaux pour les applications exigeantes. De plus, l’hydroformage peut être adapté pour manipuler ces matériaux, même ceux qui présentent des propriétés mécaniques complexes, comme une faible ductilité ou une haute résistance.
Un autre domaine de progrès concerne l’automatisation et la numérisation des processus. Les systèmes de contrôle intelligents permettent de surveiller en temps réel les paramètres critiques tels que la pression, la température et la déformation du matériau. Cela réduit les risques d’erreurs et garantit une meilleure répétabilité des pièces produites. En parallèle, l’utilisation de la simulation numérique pour modéliser le processus d’hydroformage a transformé la manière dont les ingénieurs conçoivent les outils et optimisent les processus. Les logiciels modernes permettent de simuler des conditions de pression extrême et de prédire le comportement du matériau, ce qui réduit le besoin de prototypes physiques et accélère le développement des produits.
L’intégration de l’hydroformage dans des chaînes de production durables est également un sujet d’intérêt croissant. Certaines industries explorent des moyens d’utiliser des fluides plus respectueux de l’environnement ou même des fluides recyclables pour limiter l’impact écologique du processus. En parallèle, la réduction des déchets de matière première, une caractéristique intrinsèque de l’hydroformage, s’inscrit parfaitement dans les stratégies de fabrication éco-responsable. À l’avenir, l’adoption de matériaux recyclés dans le processus d’hydroformage pourrait renforcer son rôle dans une économie circulaire.
Malgré ses nombreux avantages, le processus d’hydroformage comporte des défis qui nécessitent des solutions innovantes. Par exemple, la gestion de la fatigue des moules sous des conditions de pression répétées reste un enjeu technique majeur. Les ingénieurs travaillent sur des matériaux et des traitements de surface capables d’améliorer la durabilité des moules. De plus, pour élargir les possibilités offertes par l’hydroformage, des techniques hybrides sont en cours de développement, combinant l’hydroformage avec d’autres procédés, tels que l’emboutissage profond ou le forgeage. Ces techniques hybrides permettent de surmonter certaines limitations et d’atteindre des niveaux de complexité encore plus élevés dans les conceptions finales.
L’impact de l’hydroformage se fait également sentir au-delà des applications industrielles traditionnelles. Par exemple, dans le domaine médical, cette technologie est utilisée pour fabriquer des implants et des instruments chirurgicaux précis et résistants. De même, dans le secteur de l’énergie, des composants pour les turbines, les échangeurs de chaleur et les réservoirs haute pression sont produits grâce à l’hydroformage. Ces exemples illustrent la polyvalence du procédé et sa capacité à répondre à des exigences strictes de performance et de fiabilité.
Avec l’intensification des efforts de recherche et développement, il est probable que l’hydroformage jouera un rôle encore plus important dans les années à venir. Les innovations pourraient inclure l’introduction de matériaux composites, qui combinent les avantages des métaux et des polymères pour créer des pièces encore plus performantes. Par ailleurs, les progrès dans les sources d’énergie renouvelables, comme l’énergie solaire ou éolienne, pourraient s’appuyer sur l’hydroformage pour produire des composants clés avec une efficacité accrue.
Ainsi, l’hydroformage, tout en étant un procédé relativement mature, continue de repousser les limites de la fabrication industrielle. Ses applications variées, associées à des avantages tels que la réduction des coûts, l’amélioration des performances structurelles et l’impact environnemental positif, en font une technologie incontournable pour relever les défis du futur.
L’avenir de l’hydroformage s’annonce prometteur, soutenu par des innovations qui élargissent sans cesse ses domaines d’application. L’un des axes de développement les plus fascinants concerne l’introduction de matériaux intelligents dans le processus. Ces matériaux, capables de s’adapter aux contraintes mécaniques ou thermiques en temps réel, pourraient révolutionner la manière dont les pièces hydroformées sont conçues et utilisées. Par exemple, des alliages à mémoire de forme ou des matériaux dotés de propriétés autoréparatrices pourraient être façonnés via l’hydroformage pour créer des composants capables de s’ajuster à leur environnement ou de prolonger leur durée de vie.
Par ailleurs, la miniaturisation croissante des dispositifs dans de nombreux secteurs, tels que l’électronique ou la robotique, pousse les ingénieurs à développer des techniques d’hydroformage à micro-échelle. Ce micro-hydroformage permet de produire des pièces de très petite taille avec une précision extrême, répondant aux besoins des technologies miniaturisées. Par exemple, dans le domaine des microcapteurs ou des micro-actionneurs, l’hydroformage pourrait jouer un rôle clé dans la fabrication de composants complexes et légers tout en maintenant des tolérances très serrées.
Dans le secteur automobile, la transition vers les véhicules électriques stimule également de nouvelles applications pour l’hydroformage. Les batteries et leurs composants associés, tels que les boîtiers, les systèmes de refroidissement et les structures de soutien, nécessitent des solutions légères, robustes et économes en matériaux. L’hydroformage est particulièrement adapté pour répondre à ces exigences. Il permet de fabriquer des structures optimisées qui maximisent l’espace disponible tout en minimisant le poids total, un facteur essentiel pour améliorer l’autonomie des véhicules électriques. De plus, les progrès dans la conception de pièces hybrides intégrant des métaux et des polymères ouvrent de nouvelles possibilités pour les fabricants, avec des pièces qui combinent rigidité, légèreté et isolation thermique ou électrique.
Le rôle de l’hydroformage dans l’aéronautique continue également de croître, notamment en raison de la nécessité de concevoir des avions plus économes en carburant. Des composants comme les réservoirs de carburant, les pièces structurelles ou les conduits de fluides sont de plus en plus souvent fabriqués à l’aide de cette technologie. Les progrès dans la simulation numérique et l’impression 3D des moules permettent d’accélérer les cycles de développement et de production, rendant l’hydroformage encore plus attractif pour les fabricants d’aéronefs.
Dans le domaine des énergies renouvelables, l’hydroformage trouve des applications dans la fabrication de composants pour les éoliennes, les piles à combustible et les systèmes solaires thermiques. Les structures complexes et les matériaux résistants aux conditions extrêmes, nécessaires pour ces applications, peuvent être produits de manière efficace grâce à ce procédé. Par exemple, les turbines des éoliennes, soumises à des contraintes mécaniques importantes, bénéficient de l’utilisation de pièces hydroformées qui garantissent leur solidité et leur durabilité.
Enfin, l’intégration de l’intelligence artificielle (IA) dans les systèmes de contrôle de l’hydroformage représente une avancée significative. L’IA permet d’optimiser automatiquement les paramètres du processus, comme la pression, la vitesse et la température, en fonction des spécificités de chaque pièce. Ces systèmes intelligents peuvent également anticiper les défaillances potentielles, réduire les temps d’arrêt et garantir une qualité constante tout au long de la production. Couplés à l’analyse des données, ces outils permettent de mieux comprendre les interactions complexes entre les matériaux, les outils et les fluides, ouvrant ainsi la voie à des innovations encore plus poussées.
En somme, l’hydroformage ne cesse d’évoluer, porté par les défis et les opportunités des industries modernes. Ses avantages en termes de précision, de flexibilité et de durabilité en font une technologie indispensable dans une large gamme d’applications. À mesure que de nouveaux matériaux, outils et techniques émergent, l’hydroformage continuera de repousser les frontières de ce qui est possible dans la fabrication industrielle, consolidant son rôle comme un pilier des technologies du futur.
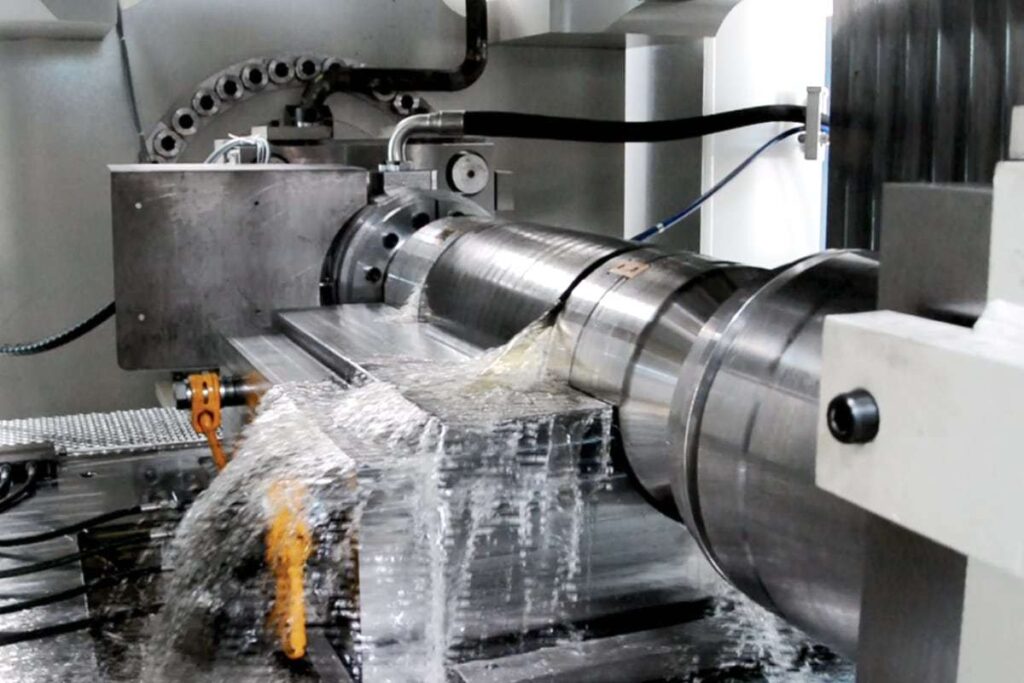
L’hydroformage, bien que déjà mature dans de nombreux secteurs, reste une technologie pleine de potentiel pour répondre aux exigences de plus en plus complexes de la fabrication moderne. À mesure que les défis industriels évoluent, cette méthode s’impose comme une solution clé pour associer performances élevées et durabilité. L’un des domaines les plus prometteurs pour l’expansion de l’hydroformage est celui de la fabrication additive, ou impression 3D. La combinaison de ces deux technologies permet de concevoir des moules ou des structures préliminaires complexes, que l’hydroformage peut ensuite affiner ou renforcer. Cette synergie ouvre la voie à la production de pièces aux géométries inédites, tout en réduisant les coûts et les délais de fabrication.
De plus, l’hydroformage est désormais exploré dans le contexte de matériaux composites et multicouches. Ces matériaux, qui intègrent des combinaisons de métaux, de polymères ou même de fibres, offrent des propriétés mécaniques et physiques uniques. En adaptant les techniques d’hydroformage, les ingénieurs peuvent produire des composants avec des caractéristiques telles qu’une résistance accrue, une absorption des vibrations ou une isolation thermique améliorée. Ces innovations sont particulièrement pertinentes pour les industries du transport, où chaque gramme économisé peut se traduire par des économies substantielles en carburant ou en énergie.
Un autre aspect fascinant est l’utilisation croissante de l’hydroformage dans des environnements extrêmes, tels que les applications spatiales et sous-marines. Dans ces contextes, les composants doivent résister à des conditions extrêmes de pression, de température ou de corrosion. L’hydroformage permet de fabriquer des structures telles que des réservoirs de carburant cryogéniques pour les fusées ou des coques résistantes à la pression pour les véhicules sous-marins habités. Les caractéristiques de précision et de robustesse obtenues grâce à cette méthode en font une solution privilégiée pour ces environnements exigeants.
Dans les domaines médicaux et biomédicaux, l’hydroformage joue également un rôle croissant. Des implants métalliques personnalisés, comme des prothèses articulaires ou des plaques osseuses, peuvent être fabriqués avec une précision extrême grâce à cette technologie. L’ajustement parfait à l’anatomie du patient est essentiel pour garantir la réussite des interventions chirurgicales et améliorer la qualité de vie des patients. Par ailleurs, la capacité de l’hydroformage à travailler avec des matériaux biocompatibles comme le titane ou les alliages cobalt-chrome est un atout majeur.
En termes d’infrastructure, des innovations ont été introduites pour rendre l’hydroformage plus accessible et adaptable aux entreprises de toutes tailles. Des machines modulaires et compactes permettent désormais aux petites et moyennes entreprises d’adopter cette technologie sans nécessiter des investissements massifs. De plus, les efforts visant à réduire la consommation énergétique du processus d’hydroformage le rendent encore plus attrayant, notamment dans un contexte où les entreprises cherchent à limiter leur empreinte carbone.
Enfin, il est important de noter le rôle de la collaboration internationale dans le développement continu de l’hydroformage. Des consortiums de recherche, réunissant des universités, des entreprises et des centres technologiques, travaillent ensemble pour repousser les limites de cette technologie. Ces partenariats permettent non seulement de résoudre des problèmes techniques complexes, mais aussi de standardiser les pratiques, ce qui facilite son adoption dans des secteurs variés et à l’échelle mondiale.
L’hydroformage est donc bien plus qu’un simple procédé industriel : il s’agit d’une plateforme technologique qui façonne les innovations de demain. Sa capacité à évoluer et à s’adapter aux besoins émergents garantit qu’il continuera à jouer un rôle central dans les progrès de la fabrication, tout en répondant aux attentes croissantes en matière de durabilité, d’efficacité et de précision.
Introduction à l’hydroformage
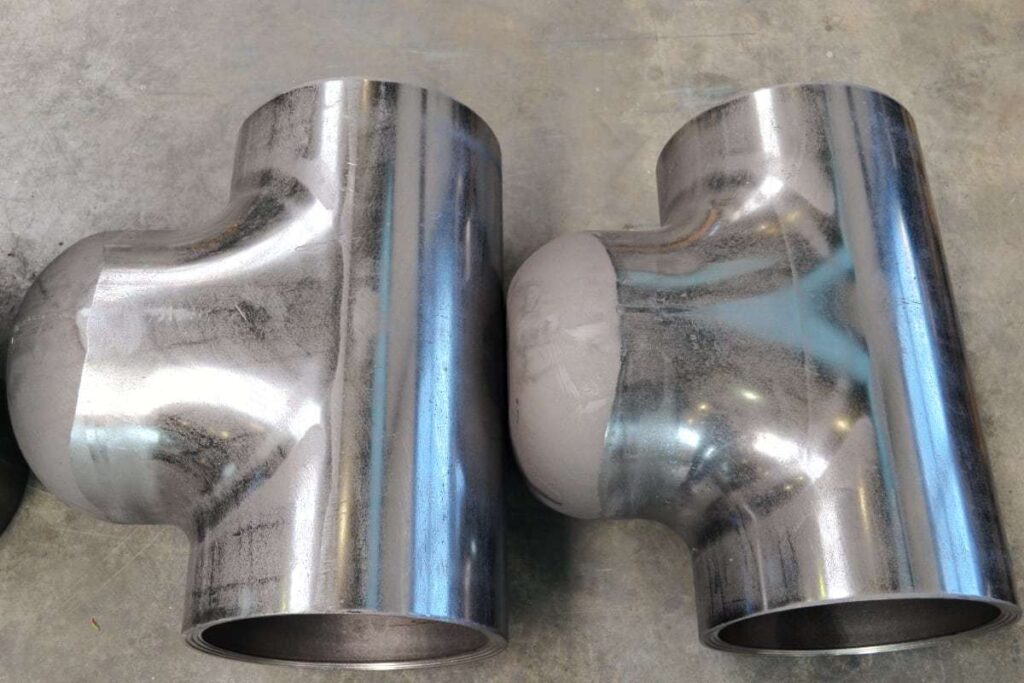
L’hydroformage est une technologie de fabrication avancée qui utilise un fluide sous haute pression pour façonner des pièces métalliques dans des moules. Appréciée pour sa capacité à produire des géométries complexes, des pièces légères et des surfaces homogènes, cette méthode est largement utilisée dans l’industrie automobile, aérospatiale et énergétique. Ce procédé se distingue par une réduction significative des déchets de matériaux et une amélioration des propriétés mécaniques des pièces formées.
Principe de fonctionnement
Le processus d’hydroformage repose sur l’application de pression hydraulique pour déformer un matériau métallique. Ce matériau, sous forme de tube ou de feuille, est inséré dans un moule et pressé jusqu’à ce qu’il épouse parfaitement la forme de ce dernier. La pression peut atteindre des niveaux extrêmes, souvent supérieurs à 1000 bars, nécessitant des équipements sophistiqués et des matériaux résistants. Ce procédé permet une déformation uniforme du métal, évitant les défauts courants comme les plis ou les fissures.
Avantages techniques et économiques
L’hydroformage présente plusieurs avantages :
- Réduction des coûts de production : Il diminue le besoin d’assemblages complexes et réduit les étapes de fabrication.
- Amélioration des performances structurelles : Les pièces formées présentent une meilleure répartition des contraintes et une résistance accrue.
- Légèreté : Idéal pour produire des pièces légères mais robustes, contribuant à une efficacité énergétique accrue dans les transports.
- Précision : Les tolérances serrées et les surfaces homogènes améliorent la qualité globale des produits.
Applications industrielles
Automobile
L’industrie automobile utilise l’hydroformage pour produire des cadres de châssis, des montants de toit et des traverses. Ces composants légers permettent de réduire la consommation de carburant tout en augmentant la sécurité.
Aérospatiale
Dans ce secteur, l’hydroformage est utilisé pour fabriquer des pièces structurelles complexes, comme des cadres ou des conduits, où chaque gramme économisé est essentiel pour les performances des aéronefs.
Énergies renouvelables
Les structures pour les turbines éoliennes, les réservoirs d’hydrogène et les échangeurs de chaleur bénéficient de l’hydroformage, qui permet de produire des composants robustes capables de résister à des conditions extrêmes.
Secteur médical
L’hydroformage est exploité pour concevoir des implants sur mesure et des instruments chirurgicaux complexes. Les pièces produites répondent aux exigences de biocompatibilité et de précision nécessaires dans ce domaine.
Défis et limites
Malgré ses nombreux avantages, l’hydroformage comporte des défis :
- Coûts initiaux élevés : Les équipements et les moules sont coûteux, nécessitant un investissement important.
- Complexité des matériaux : Certains alliages difficiles à former requièrent des ajustements précis des paramètres de pression et de température.
- Durabilité des moules : Les hautes pressions entraînent une usure rapide des équipements, nécessitant des matériaux et des traitements spécifiques.
Innovations et perspectives
Les recherches actuelles visent à intégrer des matériaux composites et intelligents dans le processus d’hydroformage, élargissant ainsi ses applications. Par ailleurs, les techniques hybrides combinant hydroformage et fabrication additive ouvrent des possibilités pour produire des géométries complexes à moindre coût. L’intégration de l’intelligence artificielle pour optimiser les paramètres en temps réel est également une voie prometteuse pour améliorer l’efficacité et la qualité du processus.
L’avenir de l’hydroformage semble également lié à des objectifs de durabilité, notamment par l’utilisation de fluides écologiques et la réduction de l’énergie consommée. Ces efforts s’inscrivent dans une stratégie globale visant à répondre aux besoins des industries modernes tout en respectant les impératifs environnementaux.
Conclusion
L’hydroformage s’impose comme une technologie essentielle pour répondre aux défis croissants de l’industrie moderne. Sa capacité à produire des pièces légères, robustes et complexes, tout en minimisant les déchets, en fait un choix privilégié pour les secteurs automobile, aérospatial, médical et énergétique. Grâce aux innovations constantes, cette technique continuera d’évoluer pour relever les défis techniques et environnementaux de demain, consolidant son rôle clé dans la fabrication avancée.
Introduction à l’hydroformage
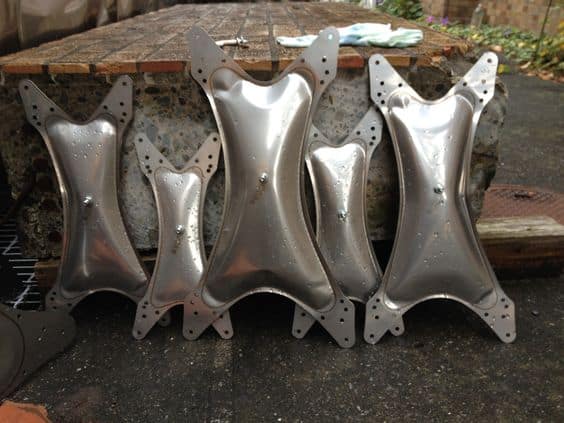
L’hydroformage est une technologie de fabrication avancée qui utilise un fluide sous haute pression pour façonner des pièces métalliques dans des moules. Appréciée pour sa capacité à produire des géométries complexes, des pièces légères et des surfaces homogènes, cette méthode est largement utilisée dans l’industrie automobile, aérospatiale et énergétique. Ce procédé se distingue par une réduction significative des déchets de matériaux et une amélioration des propriétés mécaniques des pièces formées. Le principe repose sur l’application de pressions hydrauliques élevées qui déforment uniformément le matériau, garantissant une précision accrue et une distribution optimale des contraintes. En favorisant l’efficacité énergétique et la durabilité, l’hydroformage joue un rôle clé dans le développement de solutions de fabrication adaptées aux exigences modernes.
Le processus d’hydroformage est particulièrement adapté à la production de pièces aux formes complexes et aux tolérances serrées, qui seraient difficiles ou coûteuses à obtenir avec des méthodes conventionnelles. Il est largement utilisé pour former des tubes et des plaques métalliques dans des configurations variées, permettant de créer des composants structurels robustes et légers. Ce procédé offre des avantages notables, notamment la réduction du nombre de pièces nécessaires dans les assemblages, ce qui simplifie les conceptions et améliore les performances globales des produits. Par exemple, dans l’industrie automobile, l’hydroformage permet de fabriquer des cadres de châssis intégrés, augmentant la rigidité et réduisant le poids des véhicules.
Un autre aspect essentiel de l’hydroformage est sa compatibilité avec une large gamme de matériaux, notamment l’aluminium, l’acier inoxydable, le titane et les alliages avancés. Cette polyvalence en fait un choix de prédilection pour les secteurs nécessitant des matériaux légers, résistants ou biocompatibles. L’utilisation croissante de l’aluminium et des alliages légers dans les industries automobile et aéronautique, en raison de leurs propriétés exceptionnelles, s’aligne parfaitement avec les capacités offertes par l’hydroformage.
De plus, ce procédé s’inscrit dans une démarche de fabrication durable. En réduisant les pertes de matière et en minimisant le besoin de procédés de finition, l’hydroformage contribue à des économies significatives en ressources et en énergie. Cela répond aux préoccupations environnementales croissantes et aux exigences réglementaires visant à limiter l’empreinte écologique des processus industriels.
Cependant, l’hydroformage n’est pas sans défis. Les coûts initiaux élevés, liés à l’achat d’équipements spécialisés et à la fabrication de moules adaptés, peuvent représenter une barrière pour certaines entreprises. De plus, les contraintes techniques, telles que la gestion de la fatigue des moules sous des pressions répétées ou l’optimisation des paramètres pour des matériaux spécifiques, nécessitent une expertise avancée et des technologies de pointe. Ces limitations sont néanmoins atténuées par les avantages économiques et techniques à long terme, ainsi que par les innovations constantes dans ce domaine.
L’hydroformage continue de se développer grâce à l’intégration de nouvelles technologies telles que l’intelligence artificielle, la simulation numérique et les matériaux composites. Ces progrès permettent d’améliorer la précision, de réduire les coûts et d’étendre les possibilités d’application à des secteurs émergents. L’intelligence artificielle, par exemple, joue un rôle clé dans l’optimisation des paramètres en temps réel, garantissant une qualité constante et minimisant les risques de défaillance.
En conclusion, l’hydroformage est une méthode de fabrication essentielle, offrant des solutions innovantes aux défis des industries modernes. Sa capacité à combiner précision, efficacité et durabilité en fait une technologie incontournable pour répondre aux besoins actuels et futurs de la fabrication industrielle.
Principe de fonctionnement
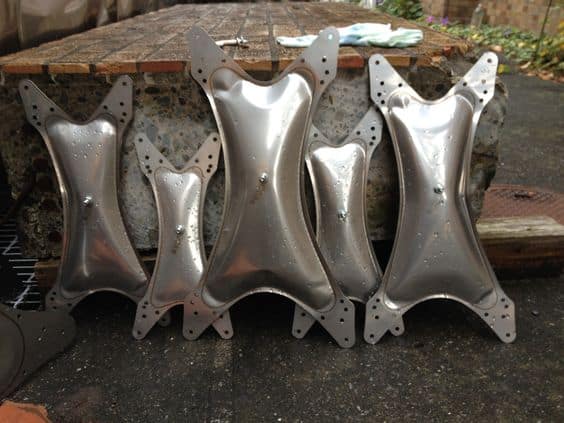
Le principe de fonctionnement de l’hydroformage repose sur l’utilisation d’un fluide sous haute pression pour déformer un matériau métallique, généralement sous forme de tube ou de feuille, afin qu’il épouse la forme d’un moule. Le matériau est placé dans un moule préalablement conçu pour la forme finale désirée. Une fois le matériau positionné, le fluide hydraulique est introduit à haute pression, souvent supérieure à 1000 bars, ce qui force le matériau à se conformer aux parois du moule. Cette pression uniforme permet d’obtenir des formes complexes avec des tolérances précises et des propriétés mécaniques améliorées.
Le procédé se divise en plusieurs étapes clés. Tout d’abord, la pièce brute est chargée dans un moule spécialement conçu pour résister à la pression élevée. Ensuite, une force mécanique initiale peut être appliquée pour positionner correctement le matériau et commencer une préformage. Ensuite, le fluide hydraulique est introduit, exerçant une pression uniforme qui déforme progressivement le métal. Pendant cette phase, la distribution homogène de la pression évite les plis ou les zones faibles, assurant une déformation contrôlée. Enfin, après la formation complète, la pression est relâchée et la pièce finie est extraite du moule.
Ce procédé est particulièrement adapté pour travailler avec des métaux ductiles comme l’aluminium, l’acier inoxydable, le cuivre ou certains alliages légers. Il permet de produire des pièces avec des parois minces tout en conservant une grande résistance mécanique. L’avantage majeur du principe d’hydroformage réside dans sa capacité à répartir uniformément les contraintes à travers le matériau, ce qui améliore ses propriétés structurelles et réduit le risque de fissures ou de défaillances.
En outre, le contrôle précis des paramètres, tels que la pression appliquée, la température et la vitesse de déformation, est essentiel pour garantir des résultats optimaux. Ces paramètres sont souvent ajustés en fonction des propriétés spécifiques du matériau utilisé et de la complexité de la géométrie souhaitée. Des simulations numériques avancées sont souvent employées pour optimiser ces réglages avant la production, réduisant ainsi les coûts et le temps de mise au point.
Le principe de fonctionnement de l’hydroformage, simple en théorie mais sophistiqué en pratique, le rend indispensable pour produire des pièces complexes, légères et robustes, répondant aux besoins des industries modernes, notamment l’automobile, l’aéronautique et l’énergie.
Avantages techniques et économiques
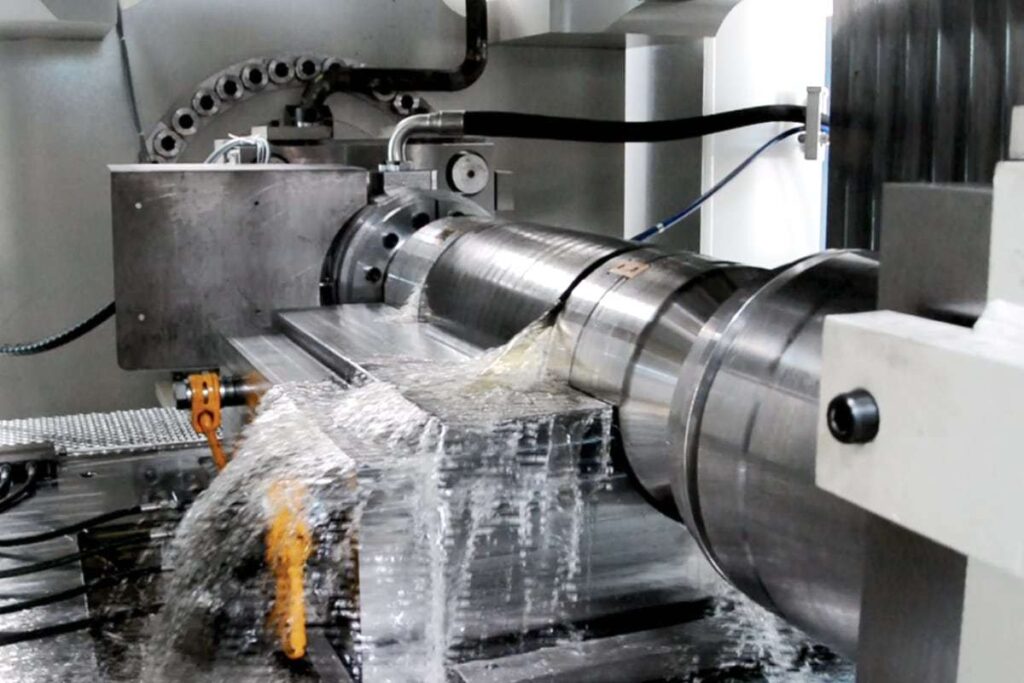
L’hydroformage offre de nombreux avantages techniques et économiques qui en font un procédé de fabrication prisé dans diverses industries. Ces avantages découlent de sa capacité à produire des pièces complexes avec une grande précision tout en réduisant les coûts et les impacts environnementaux. Voici les principaux bénéfices associés à cette technologie :
1. Réduction des coûts de fabrication
L’hydroformage simplifie la production en réduisant le nombre de pièces nécessaires pour assembler un composant complexe. Par exemple, dans l’industrie automobile, un cadre de châssis réalisé par hydroformage peut remplacer plusieurs pièces soudées ou assemblées. Cela réduit le besoin de processus secondaires tels que le soudage, le rivetage ou l’usinage, ce qui diminue les coûts de main-d’œuvre et de matériel.
2. Optimisation de l’utilisation des matériaux
Ce procédé minimise les pertes de matière, car la déformation est précisément contrôlée et conforme à la géométrie souhaitée. Contrairement aux techniques de découpe ou d’enlèvement de matière, l’hydroformage exploite pleinement le matériau de départ, ce qui est particulièrement bénéfique pour les métaux coûteux comme le titane ou les alliages légers.
3. Fabrication de pièces légères et robustes
L’hydroformage permet de produire des pièces aux parois minces mais extrêmement solides, répondant ainsi à la demande croissante pour des structures légères dans les secteurs comme l’automobile et l’aéronautique. Cette réduction de poids contribue directement à l’efficacité énergétique, réduisant la consommation de carburant et les émissions de CO₂.
4. Production de formes complexes
Grâce à l’application uniforme de la pression hydraulique, il est possible de réaliser des formes géométriques complexes qui seraient difficiles ou impossibles à obtenir avec des procédés traditionnels. Cela inclut des pièces avec des courbes complexes, des variations d’épaisseur ou des détails fonctionnels intégrés.
5. Amélioration des propriétés mécaniques
L’hydroformage améliore les propriétés structurelles des pièces fabriquées. La répartition homogène des contraintes pendant le formage élimine les zones faibles et améliore la résistance aux charges mécaniques. Cela se traduit par une durabilité accrue des composants, même dans des environnements exigeants.
6. Finition de surface supérieure
Les pièces fabriquées par hydroformage ont des surfaces lisses et homogènes, ce qui réduit le besoin de traitements de finition comme le polissage ou l’usinage. Cela accélère les cycles de production et diminue les coûts supplémentaires.
7. Flexibilité des matériaux
Ce procédé est compatible avec une large gamme de matériaux, notamment les alliages d’aluminium, l’acier inoxydable, le cuivre et même certains métaux exotiques. Cette polyvalence permet son adoption dans des secteurs variés aux exigences spécifiques.
8. Réduction de l’empreinte écologique
En minimisant les déchets de matière et les étapes de production, l’hydroformage contribue à une fabrication plus durable. De plus, la légèreté des pièces produites permet des économies d’énergie dans leur utilisation, particulièrement dans les transports.
9. Réduction des délais de production
Avec des techniques avancées de simulation numérique et de conception des moules, les cycles de production peuvent être optimisés. Une fois que les moules sont prêts, l’hydroformage permet une production rapide et reproductible, ce qui est particulièrement utile pour les séries à grand volume.
En conclusion, les avantages techniques et économiques de l’hydroformage en font une technologie incontournable pour les industries cherchant à concilier performance, efficacité et durabilité. Ses capacités à réduire les coûts, à produire des pièces légères et complexes et à minimiser les impacts environnementaux le placent au cœur des stratégies de fabrication modernes.
Applications industrielles
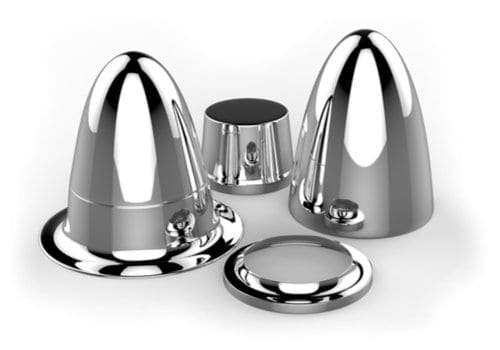
L’hydroformage est une technologie polyvalente utilisée dans de nombreux secteurs industriels en raison de sa capacité à produire des pièces complexes, légères et résistantes. Voici les principales applications industrielles où l’hydroformage joue un rôle clé :
1. Industrie automobile
Dans l’automobile, l’hydroformage est principalement utilisé pour fabriquer des composants structurels critiques, tels que :
- Châssis et cadres : Les cadres de châssis et les traverses sont souvent produits par hydroformage, car cette méthode permet de réduire le poids tout en augmentant la rigidité et la sécurité.
- Montants de toit et structures de carrosserie : Ces pièces bénéficient des propriétés mécaniques améliorées obtenues grâce à l’hydroformage, ce qui contribue à une meilleure absorption des chocs en cas de collision.
- Composants d’échappement : Les systèmes d’échappement, y compris les collecteurs, tirent parti de la précision et de la résistance des pièces formées par hydroformage pour résister à des températures élevées et à des pressions internes.
2. Industrie aérospatiale
Dans ce domaine, où le poids et la performance sont essentiels, l’hydroformage est utilisé pour fabriquer des pièces légères avec des géométries complexes :
- Structures internes : Des cadres, des longerons et des nervures sont formés avec précision pour offrir une résistance maximale tout en minimisant le poids.
- Conduits et canalisations : Les composants de gestion des fluides dans les avions, comme les conduites d’air ou de carburant, sont souvent produits par hydroformage, assurant une résistance élevée aux pressions internes et une étanchéité parfaite.
- Réservoirs cryogéniques : Utilisés dans les fusées ou les satellites, ces réservoirs nécessitent des matériaux résistants aux pressions extrêmes et aux basses températures, une exigence parfaitement satisfaite par l’hydroformage.
3. Énergies renouvelables
L’hydroformage est de plus en plus adopté pour fabriquer des composants dans le secteur de l’énergie propre :
- Réservoirs d’hydrogène : Ces réservoirs, essentiels pour les véhicules à hydrogène, nécessitent des structures légères et résistantes aux pressions élevées.
- Structures pour turbines éoliennes : Des pièces formées par hydroformage contribuent à l’efficacité et à la durabilité des éoliennes.
- Échangeurs de chaleur : Dans les systèmes solaires thermiques et les centrales électriques, les échangeurs de chaleur produits par hydroformage offrent une meilleure gestion thermique grâce à des géométries optimisées.
4. Secteur médical
L’hydroformage joue un rôle crucial dans la fabrication de dispositifs médicaux et d’implants sur mesure :
- Prothèses et implants : Les matériaux biocompatibles, comme le titane, peuvent être formés pour produire des implants osseux ou dentaires avec une précision adaptée à l’anatomie du patient.
- Instruments chirurgicaux : Les instruments nécessitant une précision et une résistance accrues, tels que les pinces et les forceps, sont souvent fabriqués à l’aide de cette technologie.
5. Construction et architecture
Dans ce domaine, l’hydroformage est utilisé pour créer des structures métalliques esthétiques et fonctionnelles :
- Façades et éléments décoratifs : Les architectes exploitent les formes complexes et les finitions de haute qualité obtenues par hydroformage pour concevoir des façades modernes et des structures métalliques.
- Structures de soutien : Les poutres creuses et les structures tubulaires sont fabriquées pour combiner légèreté et robustesse.
6. Industrie des biens de consommation
Les fabricants de produits de consommation utilisent l’hydroformage pour produire des articles innovants et durables :
- Meubles métalliques : Les formes complexes et légères des meubles modernes, comme les chaises ou les tables, sont souvent le résultat de l’hydroformage.
- Équipements sportifs : Les cadres de vélos, les clubs de golf et autres équipements utilisent cette technologie pour réduire le poids tout en maintenant la performance.
7. Secteur ferroviaire et transport lourd
Les trains et les véhicules industriels bénéficient de l’hydroformage pour la fabrication de pièces comme les poutres de châssis, les conduits d’air et les réservoirs de carburant, où robustesse et légèreté sont essentielles pour l’efficacité énergétique.
En résumé, l’hydroformage s’impose comme une technologie indispensable pour les industries exigeant des pièces précises, légères et robustes. Grâce à ses applications variées, il contribue à améliorer la performance, la durabilité et l’efficacité des produits tout en répondant aux exigences de durabilité et d’innovation.
L’hydroformage est une technologie utilisée dans de nombreux secteurs industriels en raison de ses avantages en matière de production de pièces légères, résistantes et complexes. Dans l’industrie automobile, il est largement employé pour fabriquer des composants structuraux, comme les châssis, les montants de toit et les pièces de carrosserie. Ces composants sont souvent soumis à des contraintes importantes, et l’hydroformage permet de réduire le poids tout en augmentant la sécurité et la rigidité. Les composants d’échappement, comme les collecteurs, bénéficient également de ce procédé en raison de sa capacité à créer des pièces avec des parois fines et une grande résistance à la chaleur et aux pressions internes.
Dans le secteur aérospatial, l’hydroformage est utilisé pour produire des structures internes légères mais robustes, comme les longerons et les cadres, qui sont essentiels pour maintenir la stabilité des aéronefs tout en réduisant le poids. Les conduits d’air et de carburant, ainsi que les réservoirs cryogéniques, sont également formés à l’aide de cette technologie pour répondre aux exigences strictes de pression et de température. En énergies renouvelables, l’hydroformage est de plus en plus utilisé pour fabriquer des réservoirs d’hydrogène et des composants pour turbines éoliennes, en raison de ses capacités à créer des pièces résistantes aux pressions élevées et aux conditions extrêmes. Les échangeurs de chaleur, utilisés dans les systèmes solaires thermiques et les centrales électriques, bénéficient également de l’hydroformage, qui permet de maximiser l’efficacité thermique.
Le secteur médical tire parti de l’hydroformage pour fabriquer des implants sur mesure et des instruments chirurgicaux de haute précision. Les matériaux biocompatibles, comme le titane, sont formés pour produire des implants osseux ou dentaires avec une grande précision, tout en garantissant leur solidité. Les instruments chirurgicaux, tels que les pinces ou les forceps, nécessitent des composants robustes et précis, ce qui est facilité par l’hydroformage.
Dans le domaine de la construction et de l’architecture, l’hydroformage est utilisé pour créer des façades modernes et des structures métalliques esthétiques, tout en offrant une résistance mécanique élevée. Les poutres creuses et autres éléments de soutien sont fabriqués grâce à cette technologie, alliant légèreté et solidité. L’industrie des biens de consommation, notamment pour les meubles métalliques et les équipements sportifs, utilise également l’hydroformage pour produire des pièces légères et performantes, comme les cadres de vélos et les clubs de golf, qui bénéficient de la réduction de poids sans compromis sur la solidité.
Enfin, dans le secteur ferroviaire et du transport lourd, l’hydroformage est utilisé pour la fabrication de pièces structurelles comme les poutres de châssis, les réservoirs de carburant et les conduits d’air, où la résistance et la légèreté sont essentielles pour l’efficacité énergétique et la sécurité. Ces applications variées montrent à quel point l’hydroformage est devenu une technologie indispensable dans les industries modernes, offrant une combinaison unique de précision, de durabilité et de réduction des coûts. Grâce à ses capacités à produire des pièces complexes tout en optimisant l’utilisation des matériaux, l’hydroformage répond aux exigences de performance et d’innovation de nombreux secteurs industriels.
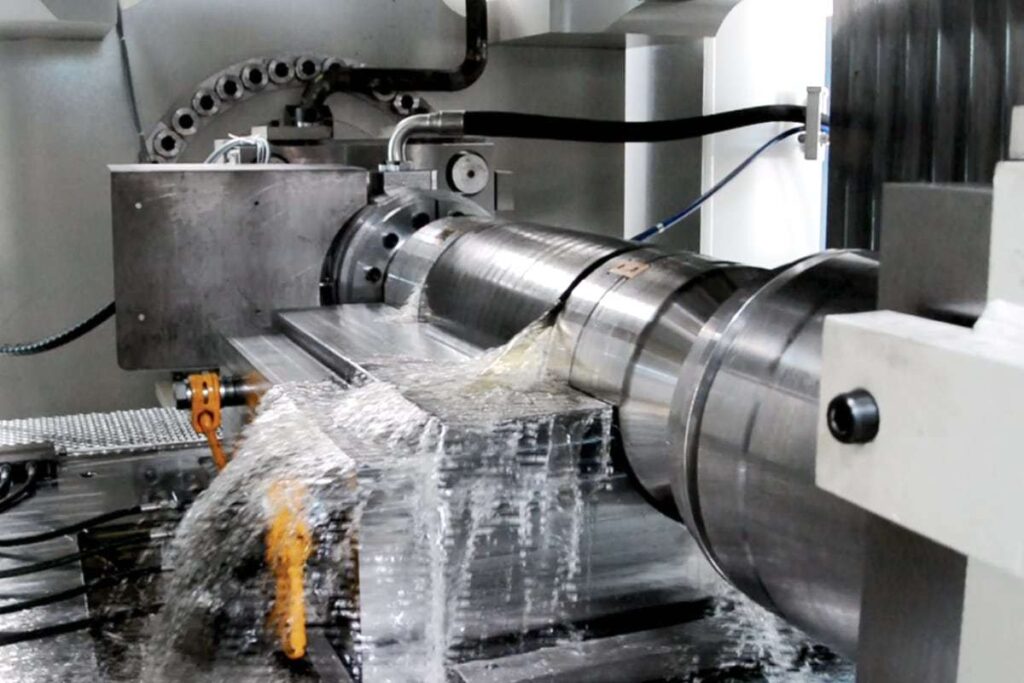
L’hydroformage continue d’évoluer et de se développer, en particulier dans des secteurs où l’innovation et la réduction des coûts de production sont des priorités majeures. Les technologies associées, comme la simulation numérique et la modélisation avancée, permettent d’améliorer constamment la précision et l’efficacité du processus. Cela facilite la fabrication de pièces encore plus complexes, avec des tolérances serrées et des géométries novatrices, tout en réduisant les déchets et les coûts associés à la production.
La flexibilité de l’hydroformage, combinée à la capacité de traiter une large gamme de matériaux, permet également de répondre à des besoins industriels variés, allant de la production de pièces légères pour l’automobile à des composants de haute performance pour des applications aérospatiales. Les industries de l’énergie, notamment celles engagées dans la transition énergétique, profitent également de cette technologie pour fabriquer des réservoirs et des composants pour les systèmes de stockage d’énergie, comme ceux utilisés dans les véhicules électriques ou dans les infrastructures de recharge.
En outre, l’hydroformage joue un rôle clé dans les efforts visant à réduire l’empreinte écologique des processus industriels. En produisant moins de déchets et en utilisant moins d’énergie par rapport à d’autres méthodes de fabrication, ce procédé contribue à des pratiques de production plus durables. Les avantages environnementaux sont encore amplifiés par le fait que l’hydroformage est compatible avec des matériaux recyclables, ce qui permet une réduction continue de l’impact environnemental tout au long du cycle de vie des produits fabriqués.
L’intégration de l’intelligence artificielle et de l’apprentissage machine dans les systèmes de contrôle de l’hydroformage ouvre de nouvelles perspectives, en permettant une gestion optimisée des processus de production en temps réel. Cela permet de réagir rapidement aux variations dans les matériaux ou dans les conditions de production, garantissant des résultats constants et de haute qualité. À l’avenir, ces technologies devraient rendre le procédé encore plus flexible et efficace, en offrant la possibilité de personnaliser des pièces à des niveaux de complexité inédits.
En conclusion, l’hydroformage est une méthode de fabrication de plus en plus utilisée et incontournable pour les industries qui recherchent une production précise, efficace, et respectueuse de l’environnement. À mesure que la technologie continue de se perfectionner et que de nouveaux matériaux et applications émergent, l’hydroformage restera un élément central des processus industriels modernes, contribuant à l’innovation dans une variété de secteurs, de l’automobile à l’aérospatial, en passant par les énergies renouvelables et le secteur médical.
L’hydroformage, en tant que technologie de fabrication avancée, continue de s’étendre au-delà de ses applications traditionnelles, avec de nouvelles possibilités d’utilisation dans des domaines tels que la fabrication additive et les matériaux composites. Alors que l’hydroformage était initialement limité aux métaux et alliages conventionnels, les chercheurs explorent des moyens de l’adapter aux matériaux composites et aux alliages à haute performance pour répondre à la demande croissante de composants plus légers, plus résistants et plus durables. Cela pourrait ouvrir la voie à des applications dans des secteurs comme la fabrication de pièces pour véhicules électriques, où la légèreté et la performance sont essentielles.
En parallèle, le développement de nouvelles méthodes d’hydroformage à froid offre des avantages supplémentaires en termes de coûts et d’efficacité. L’hydroformage traditionnel est souvent associé à des températures élevées, ce qui nécessite des équipements coûteux et énergivores. Cependant, l’hydroformage à froid permet de formuler des matériaux de manière plus économe en énergie tout en réduisant les coûts d’exploitation, ce qui est particulièrement avantageux pour la production de grandes séries de petites pièces ou pour des applications plus sensibles aux coûts de fabrication.
La capacité de l’hydroformage à fabriquer des pièces avec une précision exceptionnelle et des propriétés mécaniques supérieures offre également un fort potentiel dans le domaine des pièces de remplacement ou de personnalisation. Dans le secteur automobile, par exemple, l’hydroformage permet de produire des pièces sur mesure pour des véhicules spécifiques, offrant ainsi une flexibilité accrue aux constructeurs automobiles et permettant la fabrication de composants adaptés à des besoins particuliers. Cette personnalisation est également prometteuse pour les petites séries, notamment dans les secteurs de l’aéronautique ou des équipements sportifs.
L’évolution des processus de contrôle, notamment grâce à l’automatisation et à l’utilisation de capteurs intelligents, permet également de garantir une qualité constante tout au long de la production. L’intégration de ces systèmes dans les lignes de production permet une surveillance continue et une adaptation en temps réel des paramètres de pression et de déformation, ce qui garantit une performance optimale et réduit les risques de défauts de fabrication. Ce niveau de contrôle accru contribue à la réduction des taux de rejets et optimise l’utilisation des ressources, rendant le processus encore plus rentable et écologique.
À mesure que les industries continuent de se tourner vers des solutions plus durables et économiquement viables, l’hydroformage, avec ses nombreux avantages, est appelé à jouer un rôle croissant dans la fabrication de produits de haute performance tout en répondant aux impératifs écologiques et économiques actuels. Les innovations technologiques, qu’elles soient liées à l’automatisation, aux matériaux ou à la numérisation des processus, permettront à l’hydroformage de rester compétitif face à d’autres méthodes de fabrication et d’ouvrir de nouvelles perspectives dans un large éventail d’industries.
En résumé, l’hydroformage est une méthode qui continue de se réinventer et d’évoluer, avec des applications toujours plus larges et un potentiel d’innovation important. Elle répond à la demande croissante pour des pièces complexes, légères et durables, tout en s’adaptant aux nouvelles exigences environnementales et économiques des secteurs industriels. Grâce à ses avantages uniques en matière de réduction de poids, d’optimisation des matériaux et de production à haute précision, l’hydroformage reste une technologie clé pour les industries modernes.
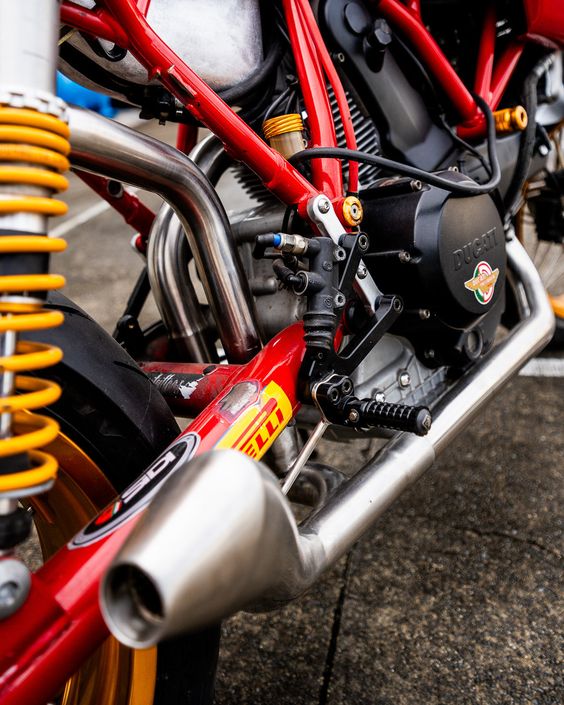
L’avenir de l’hydroformage semble prometteur, car la technologie continue de se perfectionner et de s’adapter aux défis industriels contemporains. Un domaine particulièrement intéressant concerne l’intégration de l’hydroformage avec d’autres technologies de fabrication avancée, comme la fabrication additive et l’impression 3D. En combinant ces techniques, il est possible de produire des composants métalliques et composites à la fois légers, complexes et sur mesure, tout en maintenant un haut niveau de précision. Cette convergence pourrait permettre la fabrication de pièces aux formes et aux fonctions encore plus avancées, adaptées à des applications spécialisées dans des secteurs comme l’aérospatiale, la médecine et les technologies de pointe.
Les progrès dans les matériaux jouent également un rôle clé dans l’avenir de l’hydroformage. Le développement de nouveaux alliages métalliques et composites, ainsi que l’amélioration des propriétés des matériaux existants, permet une plus grande flexibilité dans les applications. Les matériaux à haute performance, comme les alliages à mémoire de forme ou les métaux superalliés, peuvent désormais être formés à l’aide de l’hydroformage pour créer des pièces qui résistent mieux aux conditions extrêmes tout en étant légères. Cela est particulièrement utile dans les secteurs où les conditions de travail sont sévères, comme l’aéronautique, l’automobile de performance, et même dans les applications militaires.
Un autre aspect de l’évolution de l’hydroformage est la réduction continue des coûts associés à l’installation et à l’exploitation des équipements. L’amélioration des technologies de contrôle et des capteurs, ainsi que l’optimisation des processus de production, permettent de rendre les installations de plus en plus accessibles à une variété d’industries. De plus, les techniques d’optimisation basées sur l’intelligence artificielle (IA) et l’apprentissage automatique permettent de concevoir des pièces encore plus complexes tout en réduisant les risques de défaillances pendant la production. Ces avancées rendent l’hydroformage plus rentable, même pour les petites et moyennes séries de production.
L’hydroformage est également un atout pour les stratégies d’économie circulaire, un domaine où l’optimisation de l’utilisation des matériaux et la réduction des déchets sont primordiales. Par sa capacité à recycler et à réutiliser certains matériaux, comme l’aluminium ou l’acier, cette technologie soutient les objectifs de durabilité. Par exemple, en permettant la fabrication de pièces avec moins de matière tout en maintenant leur performance, l’hydroformage contribue directement à la réduction de l’empreinte carbone de nombreux secteurs. De plus, l’utilisation de matériaux recyclés dans les processus de production permet de minimiser l’impact environnemental, un aspect crucial à mesure que les industries cherchent à respecter des réglementations de plus en plus strictes en matière de durabilité.
L’adaptabilité de l’hydroformage aux nouvelles demandes du marché est également renforcée par sa capacité à évoluer rapidement pour répondre aux besoins spécifiques des clients. Dans des industries comme l’automobile, où la personnalisation et les séries limitées gagnent en popularité, l’hydroformage permet de produire des pièces uniques ou adaptées à des configurations particulières sans nécessiter des investissements massifs dans des outils ou des équipements spécialisés. Cela ouvre la porte à une plus grande flexibilité dans la production, permettant aux entreprises de s’adapter plus rapidement aux tendances du marché et aux demandes spécifiques des consommateurs.
En somme, l’hydroformage, grâce à ses avantages uniques en termes de légèreté, de résistance et de précision, continue de transformer les méthodes de fabrication dans une variété de secteurs. La combinaison avec de nouvelles technologies et matériaux, ainsi que les innovations en matière de contrôle et de production, garantit que cette technologie restera au cœur des processus industriels de demain. Alors que les industries continuent de chercher des solutions plus efficaces, plus écologiques et plus rentables, l’hydroformage est bien positionné pour jouer un rôle central dans la fabrication de composants complexes, durables et de haute performance.
EMS Machines de Formage
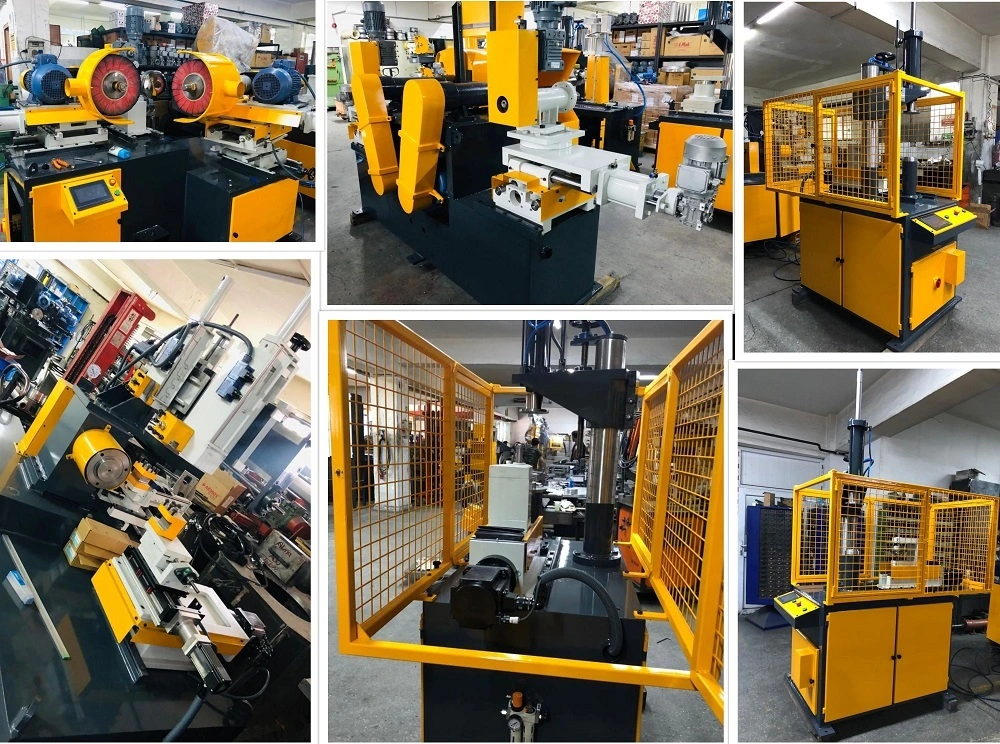
Le formage du métal est un processus consistant à façonner le métal dans la forme et la taille souhaitées à l’aide de diverses techniques. Il s’agit d’un processus crucial dans l’industrie manufacturière car il permet la production de différents produits tels que des pièces automobiles, des composants d’avion, des appareils électroménagers et bien d’autres encore.
Le processus de formage du métal consiste à appliquer une force sur le métal pour changer sa forme sans enlever aucune matière. La force peut être appliquée par diverses méthodes telles que le forgeage, le laminage, l’extrusion, l’étirage et l’estampage. Chaque méthode a ses propres avantages et inconvénients, et le choix de la méthode dépend du matériau formé et de la forme souhaitée.
Le forgeage est l’une des techniques de formage des métaux les plus anciennes. Il s’agit de chauffer le métal à haute température, puis d’appliquer une force de compression à l’aide d’un marteau ou d’une presse pour donner au métal la forme souhaitée. Le forgeage est couramment utilisé pour produire de grandes pièces telles que des engrenages, des essieux et des bielles.
Le laminage est une autre technique de formage du métal qui consiste à faire passer le métal à travers une paire de rouleaux pour réduire son épaisseur ou modifier sa forme. Les rouleaux peuvent être lisses ou texturés selon la finition souhaitée. Le laminage est couramment utilisé pour produire des tôles plates, des plaques et des barres.
L’extrusion est une technique de formage du métal qui consiste à pousser une billette ou une tige métallique à travers une matrice pour créer une forme spécifique. L’extrusion peut être utilisée pour produire des formes complexes telles que des tubes, des canaux et des angles.
L’emboutissage est une technique de formage des métaux utilisée pour réaliser des pièces de forme cylindrique, comme des tubes ou des tuyaux. Le processus consiste à tirer le métal à travers une matrice pour réduire son diamètre et augmenter sa longueur. Le tréfilage est couramment utilisé dans la production de fils, de tiges et de tubes.
L’emboutissage est une technique de formage du métal qui consiste à couper, poinçonner ou plier le métal dans une forme spécifique à l’aide d’une matrice. Le processus peut être utilisé pour produire des pièces avec une grande précision et répétabilité. L’estampage est couramment utilisé dans la production de pièces automobiles, d’appareils électroménagers et d’appareils électroniques.
En plus de ces techniques, il existe de nombreuses autres méthodes de formage des métaux telles que le filage, l’emboutissage profond et l’hydroformage. Chaque méthode a ses propres avantages et inconvénients, et le choix de la méthode dépend des exigences spécifiques du produit fabriqué.
Le formage des métaux est un processus complexe qui nécessite un haut niveau de compétence et d’expertise. Le succès du processus dépend de nombreux facteurs tels que le type de matériau formé, l’équipement utilisé et l’expérience de l’opérateur. En comprenant les différentes techniques de formage des métaux et en choisissant la méthode adaptée au travail, les fabricants peuvent produire des pièces de haute qualité qui répondent aux besoins spécifiques de leurs clients.