
Les presses de compression jouent un rôle crucial dans diverses industries, allant de l’automobile à l’aéronautique, en passant par la construction et les équipements sportifs. Elles permettent la fabrication de pièces de haute qualité à des coûts compétitifs, tout en offrant une grande flexibilité en termes de matériaux et de formes. Ce texte vise à fournir une vue d’ensemble complète des presses de compression, en mettant l’accent sur les matériaux SMC (Sheet Molding Compound), BMC (Bulk Molding Compound) et GMT (Glass Mat Thermoplastic). Nous explorerons leur fonctionnement, leurs applications, ainsi que les avantages et inconvénients associés à ces technologies.
Qu’est-ce que les Presses de Compression ?
Les presses de compression sont des machines utilisées pour mouler des matériaux composites en appliquant chaleur et pression. Ce procédé est particulièrement adapté pour la fabrication de pièces en matériaux composites thermodurcissables et thermoplastiques. Le concept de base repose sur le placement d’un matériau brut dans un moule préchauffé, qui est ensuite fermé sous haute pression. Ce processus permet de produire des pièces avec des caractéristiques mécaniques et physiques précises.
Historiquement, les presses de compression ont évolué pour répondre aux besoins croissants de diverses industries. Initialement développées pour la production de pièces simples, ces machines sont désormais capables de fabriquer des composants complexes avec des tolérances strictes et des finitions de surface de haute qualité.
Les matériaux utilisés dans les presses de compression varient en fonction des exigences spécifiques du produit final. Les composés de moulage en feuille (SMC), en vrac (BMC) et les thermoplastiques renforcés de tapis de verre (GMT) sont parmi les matériaux les plus couramment utilisés. Chaque type de matériau offre des avantages uniques, ce qui permet de choisir le composite le plus adapté à une application particulière.
Les Matériaux Utilisés
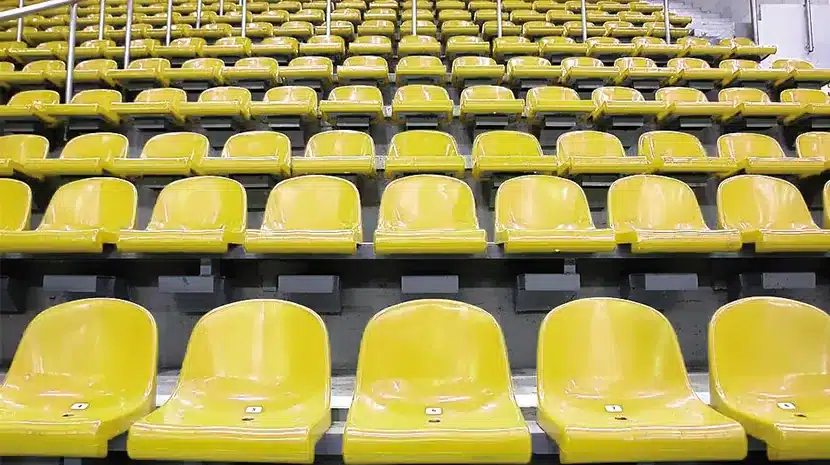
SMC (Sheet Molding Compound)
Le SMC est un composite thermodurcissable constitué de résine polyester, de fibres de verre et de charges diverses. Il est présenté sous forme de feuilles prêtes à l’emploi. Ce matériau est réputé pour sa haute résistance mécanique, sa stabilité dimensionnelle et sa capacité à produire des pièces complexes avec des détails fins. Les avantages du SMC incluent une bonne résistance aux produits chimiques, une haute performance mécanique et une faible densité, ce qui le rend idéal pour les applications nécessitant un rapport résistance/poids élevé. Cependant, le SMC peut être plus coûteux à produire en raison de la complexité du procédé de fabrication et de la nécessité de moules spécifiques.
BMC (Bulk Molding Compound)
Le BMC est similaire au SMC, mais il est fourni sous forme de masse pâteuse, facilitant ainsi son moulage dans des formes complexes et détaillées. Il est composé de résine polyester, de fibres de verre courtes, de charges minérales et d’additifs divers. Le BMC est largement utilisé dans les applications électriques et électroniques en raison de ses excellentes propriétés isolantes et de sa résistance à la chaleur. Les avantages du BMC comprennent une bonne résistance à la chaleur, des propriétés isolantes électriques élevées et une excellente résistance mécanique. Toutefois, comme le SMC, le BMC nécessite des moules précis et peut être coûteux en termes de production initiale.
GMT (Glass Mat Thermoplastic)
Le GMT est un composite thermoplastique renforcé de fibres de verre continues, offrant une combinaison unique de légèreté et de haute résistance. Ce matériau est particulièrement apprécié dans l’industrie automobile pour la fabrication de pièces structurelles et semi-structurelles. Les avantages du GMT incluent une haute résistance aux chocs, une excellente capacité de recyclage et une grande flexibilité de conception. Cependant, le GMT peut être moins résistant aux températures élevées comparé aux composites thermodurcissables.
Fonctionnement des Presses de Compression
Les presses de compression fonctionnent selon un principe relativement simple mais extrêmement efficace. Le matériau brut, sous forme de SMC, BMC ou GMT, est placé dans un moule préchauffé. Ce moule est ensuite fermé, et une pression élevée est appliquée pour conformer le matériau à la forme du moule. La chaleur permet de durcir ou de fondre le matériau, selon qu’il s’agit d’un thermodurcissable ou d’un thermoplastique, et la pression assure une répartition uniforme du matériau et l’élimination des bulles d’air.
Les étapes clés de ce processus incluent :
- Préparation du moule et du matériau : Le moule est nettoyé et préchauffé, et le matériau est préparé selon les spécifications requises.
- Placement du matériau : Le matériau brut est placé dans le moule ouvert.
- Fermeture et compression : Le moule est fermé, et une pression élevée est appliquée pour former la pièce.
- Cure ou refroidissement : Le matériau est chauffé pour le durcissement (pour les thermodurcissables) ou refroidi (pour les thermoplastiques).
- Démoulage : La pièce finie est retirée du moule.
Les innovations récentes dans ce domaine incluent l’automatisation des presses, l’utilisation de capteurs pour un contrôle précis du processus et le développement de nouveaux matériaux composites offrant des performances améliorées.
Applications et Utilisations
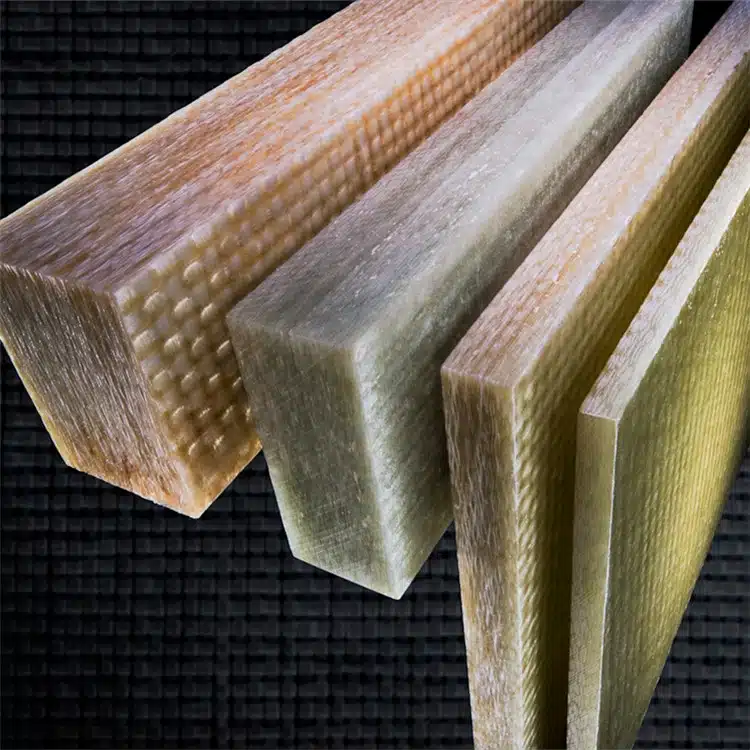
Les presses de compression trouvent des applications dans divers secteurs industriels en raison de leur capacité à produire des pièces complexes avec une grande précision. Dans l’industrie automobile, elles sont utilisées pour fabriquer des composants tels que des panneaux de carrosserie, des tableaux de bord et des supports de moteur. L’industrie aéronautique utilise ces presses pour produire des pièces structurelles légères mais robustes, comme des éléments de fuselage et des revêtements intérieurs. Le secteur de la construction bénéficie également de cette technologie pour la fabrication de panneaux muraux, de toits et d’autres éléments structurels.
Exemples concrets de produits fabriqués avec des presses de compression :
- Panneaux de porte et capots pour automobiles en SMC.
- Boîtiers de distribution électrique en BMC.
- Supports de siège et structures de renforcement en GMT.
Des études de cas montrent que l’utilisation des presses de compression peut réduire les coûts de production, améliorer la qualité des produits finis et augmenter la flexibilité de conception.
Avantages et Inconvénients des Presses de Compression
Avantages :
- Coût : Les presses de compression permettent de produire des pièces à des coûts compétitifs, surtout pour les grandes séries.
- Efficacité : Le processus est rapide et permet une production en masse.
- Qualité du produit final : Les pièces produites sont de haute qualité, avec des tolérances précises et une excellente finition de surface.
- Flexibilité des matériaux : Possibilité d’utiliser divers matériaux composites pour répondre à des exigences spécifiques.
Inconvénients :
- Limitations de conception : Certaines formes complexes peuvent être difficiles à réaliser.
- Coût des moules : Les moules utilisés doivent être très précis, ce qui peut entraîner des coûts initiaux élevés.
- Maintenance et sécurité : Les presses nécessitent un entretien régulier et des mesures de sécurité strictes pour prévenir les accidents.
Comparées à d’autres méthodes de moulage, comme l’injection ou le thermoformage, les presses de compression offrent des avantages spécifiques mais peuvent être limitées par des coûts initiaux plus élevés et des restrictions de conception.
Maintenance et Sécurité des Presses de Compression
Pour assurer une performance optimale et prolonger la durée de vie des presses de compression, un entretien régulier est essentiel. Cela inclut le nettoyage des moules, la vérification des systèmes de chauffage et de pression, et l’inspection des composants mécaniques. La prévention des pannes par des inspections régulières et des réparations proactives peut réduire les temps d’arrêt et augmenter l’efficacité de la production.
La sécurité est également un aspect crucial. Les opérateurs doivent suivre des protocoles stricts pour éviter les accidents, comme le port d’équipements de protection individuelle, l’utilisation de dispositifs de verrouillage de sécurité et la formation régulière sur les procédures de sécurité.
Innovations et Développements Futurs
L’industrie des presses de compression continue d’évoluer avec des innovations technologiques visant à améliorer l’efficacité et la qualité de production. Les tendances actuelles incluent l’intégration de l’automatisation et de l’intelligence artificielle pour optimiser le processus de moulage, le développement de nouveaux composites plus performants et respectueux de l’environnement, et l’adoption de techniques de fabrication additive pour des conceptions plus complexes et personnalisées.
Les perspectives pour l’avenir sont prometteuses, avec des recherches en cours sur des matériaux composites encore plus légers et résistants, et des procédés de moulage plus rapides et plus écologiques.
Conclusion
En conclusion, les presses de compression jouent un rôle indispensable dans la fabrication de pièces en matériaux composites pour divers secteurs industriels. Leur capacité à produire des pièces complexes et de haute qualité, combinée aux avantages économiques et à la flexibilité des matériaux, en fait une technologie précieuse pour l’avenir. En investissant dans l’innovation et en adoptant des pratiques de maintenance et de sécurité rigoureuses, l’industrie peut continuer à tirer parti des nombreux avantages offerts par les presses de compression.
EMS Machines de Formage
Le formage du métal est un processus consistant à façonner le métal dans la forme et la taille souhaitées à l’aide de diverses techniques. Il s’agit d’un processus crucial dans l’industrie manufacturière car il permet la production de différents produits tels que des pièces automobiles, des composants d’avion, des appareils électroménagers et bien d’autres encore.
Le processus de formage du métal consiste à appliquer une force sur le métal pour changer sa forme sans enlever aucune matière. La force peut être appliquée par diverses méthodes telles que le forgeage, le laminage, l’extrusion, l’étirage et l’estampage. Chaque méthode a ses propres avantages et inconvénients, et le choix de la méthode dépend du matériau formé et de la forme souhaitée.
Le forgeage est l’une des techniques de formage des métaux les plus anciennes. Il s’agit de chauffer le métal à haute température, puis d’appliquer une force de compression à l’aide d’un marteau ou d’une presse pour donner au métal la forme souhaitée. Le forgeage est couramment utilisé pour produire de grandes pièces telles que des engrenages, des essieux et des bielles.
Le laminage est une autre technique de formage du métal qui consiste à faire passer le métal à travers une paire de rouleaux pour réduire son épaisseur ou modifier sa forme. Les rouleaux peuvent être lisses ou texturés selon la finition souhaitée. Le laminage est couramment utilisé pour produire des tôles plates, des plaques et des barres.
L’extrusion est une technique de formage du métal qui consiste à pousser une billette ou une tige métallique à travers une matrice pour créer une forme spécifique. L’extrusion peut être utilisée pour produire des formes complexes telles que des tubes, des canaux et des angles.
L’emboutissage est une technique de formage des métaux utilisée pour réaliser des pièces de forme cylindrique, comme des tubes ou des tuyaux. Le processus consiste à tirer le métal à travers une matrice pour réduire son diamètre et augmenter sa longueur. Le tréfilage est couramment utilisé dans la production de fils, de tiges et de tubes.
L’emboutissage est une technique de formage du métal qui consiste à couper, poinçonner ou plier le métal dans une forme spécifique à l’aide d’une matrice. Le processus peut être utilisé pour produire des pièces avec une grande précision et répétabilité. L’estampage est couramment utilisé dans la production de pièces automobiles, d’appareils électroménagers et d’appareils électroniques.
En plus de ces techniques, il existe de nombreuses autres méthodes de formage des métaux telles que le filage, l’emboutissage profond et l’hydroformage. Chaque méthode a ses propres avantages et inconvénients, et le choix de la méthode dépend des exigences spécifiques du produit fabriqué.
Le formage des métaux est un processus complexe qui nécessite un haut niveau de compétence et d’expertise. Le succès du processus dépend de nombreux facteurs tels que le type de matériau formé, l’équipement utilisé et l’expérience de l’opérateur. En comprenant les différentes techniques de formage des métaux et en choisissant la méthode adaptée au travail, les fabricants peuvent produire des pièces de haute qualité qui répondent aux besoins spécifiques de leurs clients.